质量看板
《质量看板》PPT课件
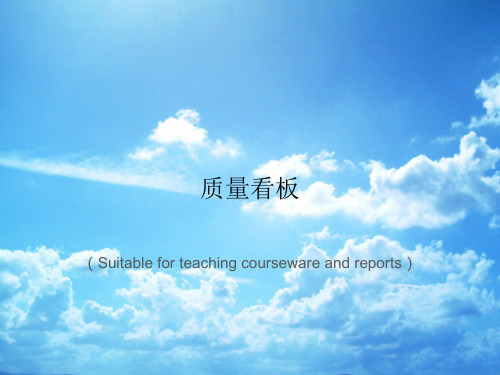
(Suitable for teaching courseware and reports)
QC活动8步骤
质量问题处理方法
1.选课题
8.反省及今 后的计划
2.现状调查 和目标设定
P
A
7.标准化和管 理的常规化
3.活动计划
目标未达成 目标达成 C
4. 原因分析
6.确认效果
5.对策实施
D
检验指导书的内容
对设备要实行“TPM”管理
“设备”的管理
这里所说的“设备”,包括设备,机械及装置以外的 夹具和工具等。设备的管理是要尽早发现设备运转不良及 分析其原因,采取适当的措施;而且还要进行预防性维护, 以防患于未然。对设备和机械,包括夹具、工具等,都需 要工人的日常检修,以及依据一定的标准进行定期的检修 和调整。
绿色-------放行
白色----配制零件
注:标识时统一使用油漆记号笔或油漆,标识“○”时 的直径大小约为30㎜。
“设备”的管理
这里所说的“设备”,包括设备,机械及装置以外的 夹具和工具等。设备的管理是要尽早发现设备运转不良及 分析其原因,采取适当的措施;而且还要进行预防性维护, 以防患于未然。对设备和机械,包括夹具、工具等,都需 要工人的日常检修,以及依据一定的标准进行定期的检修 和调整。
“人”的管理
在5M1E中,人是最重要的因素。不论是设备的操作、检修、保养、还是材料的验收 把关,以及作业方法的遵守和改进等等,都依靠工人的智能和积极性。因此,对“人” 的管理要做好以下几方面工作: 1)加强对工人的技能训练
a、让工人充分理解质量标准和作业标准 b、按要求进行充分训练 c、进行个别而具体的指导 2)提高工人的质量意识 a、加强对自己作业质量的控制 b、提高对自己工作重要性的认识 c、加强全面质量管理思想和方法的宣传教育
质量看板模板

质量看板模板质量看板模板。
1. 项目名称,(在此处填写项目名称)。
2. 质量目标,(在此处填写项目的质量目标,例如,产品合格率达到98%)。
3. 关键指标:每日产量,(在此处填写每日产量目标,例如,1000件)。
不合格品数量,(在此处填写每日不合格品数量目标,例如,不超过10件)。
完工率,(在此处填写项目的完工率目标,例如,95%)。
4. 质量问题记录:日期,(在此处填写日期)。
问题描述,(在此处描述当日出现的质量问题)。
原因分析,(在此处分析导致质量问题的原因)。
改进措施,(在此处描述针对质量问题采取的改进措施)。
5. 质量改进计划:改进内容,(在此处填写需要改进的内容,例如,工艺流程优化、设备更新等)。
负责人,(在此处填写负责改进的人员)。
完成期限,(在此处填写改进计划的完成期限)。
6. 质量看板更新记录:日期,(在此处填写更新日期)。
更新内容,(在此处描述对质量看板的更新内容,例如,新增关键指标、调整质量目标等)。
质量看板模板的使用方法:1. 根据项目实际情况填写项目名称和质量目标。
2. 每日根据生产情况填写关键指标,如每日产量、不合格品数量和完工率等。
3. 每日记录质量问题,包括问题描述、原因分析和改进措施。
4. 制定质量改进计划,包括改进内容、负责人和完成期限。
5. 定期更新质量看板,记录更新内容和日期。
通过使用质量看板模板,可以帮助企业实时了解生产质量状况,及时发现和解决质量问题,提高产品质量和生产效率。
同时,质量看板还可以促进团队间的沟通和协作,提高团队的执行力和协作效率。
希望这份质量看板模板能够帮助您更好地实施质量管理,提升企业的竞争力和持续发展能力。
在实际应用中,质量看板模板可以根据项目实际情况进行调整和优化,以更好地满足企业的管理需求。
通过不断地改进和优化,可以使质量看板模板更加贴合企业的实际情况,发挥出更大的管理效益。
总之,质量看板作为一种重要的管理工具,对于企业提高生产效率和产品质量具有重要意义。
质量宣传看板内容
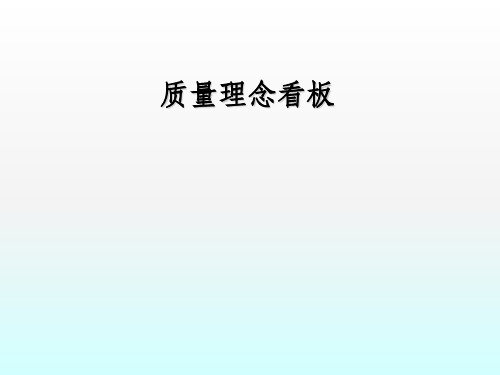
• 采购部门:购得的产品次品量下降。 • 客户部门:12小时内处理投诉并提供满意的解决办法。 • 销售部门:检测客户的满意程度,及早收集汽车原设备制造商 开发计划的信息。在不同的层次还有特定的目标
如:生产小组次品率/返工率/废品率下降一半
理想的道路由公司文化开始
• 有一件事比任何其他事情更重要 —— “文化”技能的开发
• 文化渗入到价值体系、生产能力中去 • 文化渗入到员工个人行为
—— 企业发展过程中的长期持久的动力 • 运用文化攻势,一家企业可以取得至少在短期内别家无法仿效 的持续的竞争优势 • 这一优势要通过一个大规模的、系统化的、动员力强的方案才 能建立或达到
用户满意度=100%
E、持续改进观念
不断改进和不断发掘
彻底杜绝此缺陷 缺陷
预防
缺陷
解决
临时
发现缺陷后的不断改进
有止境的改进过程
潜因 潜因 潜因 潜因
不断发掘潜因的不断改进 引起质量缺陷的潜因是无止境的
E、持续改进观念
FMEA
8D报告
P AD
C
不断改进的方法、 分析工具、运作 形式
Poka-Yoke
➢ 以超常的质量目标为引导,将整个业务系统重组为核心流程。 ➢ 一步研究问题症结,将精力集中在核心业务上。 ➢ 精简体制并外购所有模件或子系统。 ➢ 与供应商和客户共同实施联合项目。 ➢ 建立新的观念,工人参加自我检验小组,对生产线负责。
通向优质企业的不同途径
为整个业务系统制订了质量目标
示例2:一家日本供应商是这样做的: • 营销部门:弄清客户需求,以进行质量功能展开(QFD)分析 。
质量管理看板模板
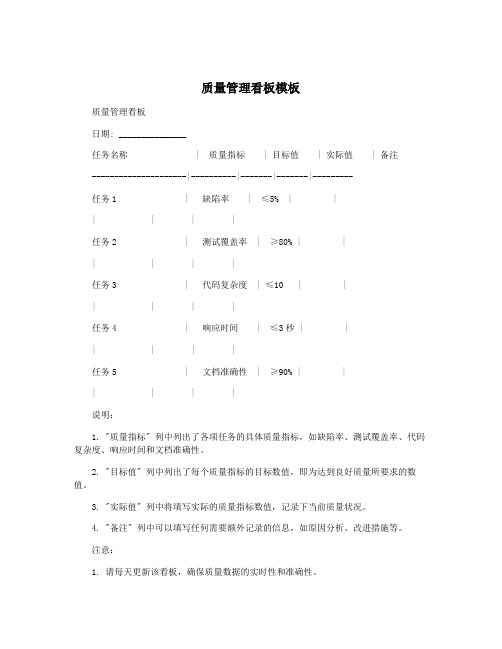
质量管理看板模板
质量管理看板
日期: _______________
任务名称 | 质量指标 | 目标值 | 实际值 | 备注
---------------------|----------|-------|-------|---------
任务1 | 缺陷率| ≤5% | |
| | | |
任务2 | 测试覆盖率| ≥80% | |
| | | |
任务3 | 代码复杂度| ≤10 | |
| | | |
任务4 | 响应时间| ≤3秒 | |
| | | |
任务5 | 文档准确性| ≥90% | |
| | | |
说明:
1. "质量指标" 列中列出了各项任务的具体质量指标,如缺陷率、测试覆盖率、代码复杂度、响应时间和文档准确性。
2. "目标值" 列中列出了每个质量指标的目标数值,即为达到良好质量所要求的数值。
3. "实际值" 列中将填写实际的质量指标数值,记录下当前质量状况。
4. "备注" 列中可以填写任何需要额外记录的信息,如原因分析、改进措施等。
注意:
1. 请每天更新该看板,确保质量数据的实时性和准确性。
2. 尽量保持各项任务的目标值在合理范围内,以确保任务的可实现性和质量的持续改进性。
每日质量管理报告:
- 当前共有X个任务,分别是任务1、任务2、任务3、任务4和任务5。
- 目标质量指标以及实际数值的对比,可根据实际情况评估质量状况,并采取相应的措施进行质量改进和问题修复。
请尽快行动并同时更新看板中的数据。
感谢您的配合与努力!。
工厂质量看板管理制度

工厂质量看板管理制度第一章总则第一条为加强工厂质量管理,提高产品质量,确保客户满意度,制定本制度。
第二条本制度适用于工厂所有部门。
第三条质量看板是工厂质量管理的重要工具,通过看板能够有效地监控生产过程和产品质量。
第二章管理责任第四条工厂质量看板由质量管理部门负责制定、更新和维护。
第五条各部门负责人要加强对质量看板的重视,确保各项指标的准确记录和及时更新。
第六条生产班组长要认真执行质量看板制度,确保生产过程中的质量问题能够及时发现和解决。
第三章看板内容第七条质量看板需要包含以下内容:1. 生产计划:包括生产任务、生产进度、产量等信息。
2. 质量指标:包括产品的合格率、不良品率、返工率等。
3. 工艺参数:包括设备参数、工艺流程等信息。
4. 安全生产:包括事故记录、安全检查等信息。
5. 人员配置:包括各班组人员数量、班次安排等信息。
第八条质量看板要根据实际情况进行定制化,确保符合工厂的管理需求。
第四章看板管理第九条每天上班前,各班组要进行看板汇报,对前一天的工作进行总结,并根据情况调整当天工作计划。
第十条质量管理部门定期对质量看板进行审核,发现问题及时进行整改。
第十一条发现问题要及时上报,制定纠正措施,并在质量看板上进行记录。
第五章培训与考核第十二条新员工入职前要接受质量看板管理培训,了解质量看板的重要性和使用方法。
第十三条定期对员工进行质量看板管理考核,根据考核结果进行奖惩。
第六章附则第十四条本制度自发布之日起生效,如有需要修改,应经质量管理部门审核。
第十五条对违反本制度的行为,质量管理部门有权进行处罚。
第十六条本制度之解释权归质量管理部门所有。
以上为工厂质量看板管理制度,希望各部门认真遵守,确保工厂质量管理工作顺利进行。
质量看板ppt课件

8;
10)检验结果和质量状况反馈及纠正程序;
11)经检验确认不符合规定质量要求的物料、产品组成部分、成品的处理程序。
4
不合格品的控制流程:
发现不合格品
标识、记录、隔离、报告
组织评审
返工/返修
让步接收
不
合
格
合格
检验
入库
退货/报废 财务结算
6.换模的
更改生产项目 时的时间
换模方式之改进表的设计
19
一句话 S
中文
关键意义
整理 “扔”的智慧
整顿 易取、易放、易存
典型例子
倒掉垃圾、长期不用的东西放 仓库 30秒内就可以找到要找的东西
清扫 清洁
点检,找出问题,解决问 题
标准化
谁使用谁清洁(管理) 管理的公开化、透明化
修养 养成一种好的习惯 安全 消灭一切安全隐患
15
什么是6S管理?(5S+1S)
• 1 S整理– 分离及丢弃 (“Seiri”)
SEIRI
• 2 S整顿–排序及识别 (“Seiton”)
SEISO
5S
S•EIT3ONS清扫– 清扫及日检 (“Seiso”) • 4 S清洁– 标准化 (“Seiketsu”)
SEIKETSUSHITSU•KE5 素养– 主动保持(“Shitsuke”)
9
现场质量管理
全面质量管理的一个重要特点是“预防性”,即变仅靠“事后把关”为加 强“事前预防”,变管理结果为管理因素。从微观角度看,引起产品质量波动 的原因主要来自6个方面: 人(Man):操作者的质量意识、技术水平、文化素养、熟练程度和身体素质 等。 机器(Machine):机器设备、工夹具的精度和维护保养状况等。 材料(Material):材料的化学成分、物理性能和外观质量等。 方法(Method):加工工艺、操作规程和作业指导书的正确程度等。 测量(Measure):测量设备、试验手段和测试方法等。 环境(Enviroment):工作地的温度、湿度、含尘度、照明、噪音和震动等。 通常把上述因素称为引起产品质量波动的6大因素或简称“5M1E”因素。
品管部质量宣传看板
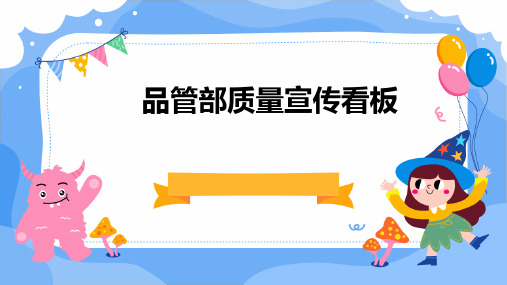
持续改进
质量目标
制定明确的质量目标,并分解到各个部门和岗位,确 保全员参与。
数据分析
收集质量数据,进行统计分析,找出潜在问题,提出 改进措施。
质量培训
定期开展质量意识培训,提高员工对质量的认识和重 视程度。
05
质量工具
鱼骨图
定义
鱼骨图是一种用于问题分析的图形化工具,因其形状类似鱼骨而得 名。
使用方法
主要内容
ISO9001标准包括质量管理体系的建立、实施、维护和持 续改进,涵盖了产品质量策划、质量控制、质量保证和质 量改进等方面的要求。
作用
通过ISO9001质量管理体系认证,企业可以提升自身质量 管理水平,增强市场竞争力,提高客户信任度和忠诚度。
全面质量管理(TQM)
01 02
定义
全面质量管理是一种以质量为核心,以全员参与为基础,通过持续改进 和不断创新,旨在提供满足或超越顾客期望的高品质产品和服务的管理 理念。
特点
能够提供准确的质量数据,帮助 团队及时发现和解决问题,提高 产品质量和生产效率。
06
质量案例
产品案例
01
产品A
在生产过程中,通过严格控制原 材料和生产工艺,确保产品性能 稳定,满足客户要求。
产品B
02
03
产品C
针对市场反馈,改进产品设计, 提高产品使用寿命,赢得客户信 赖。
在品质检测中,发现潜在问题并 及时解决,避免批量不良,降低 损失。
主要内容
全面质量管理强调全员参与、全过程控制和全方位管理,注重预防和持 续改进,通过不断优化管理流程和改进生产工艺来提高产品质量。
03
作用
全面质量管理可以帮助企业提高产品质量、降低生产成本、增强员工质
质量理念看板
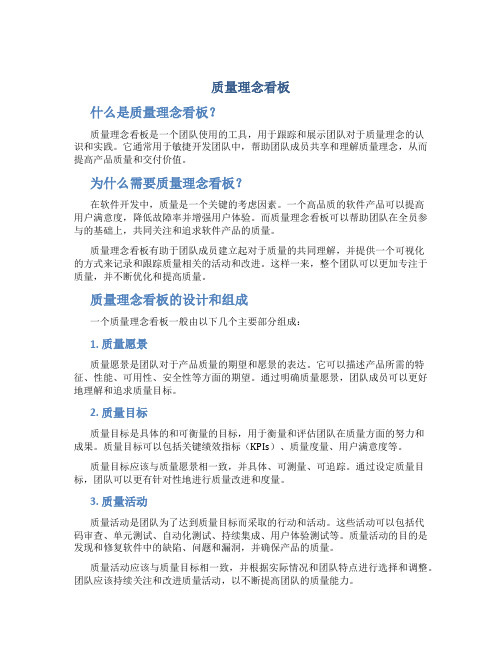
质量理念看板什么是质量理念看板?质量理念看板是一个团队使用的工具,用于跟踪和展示团队对于质量理念的认识和实践。
它通常用于敏捷开发团队中,帮助团队成员共享和理解质量理念,从而提高产品质量和交付价值。
为什么需要质量理念看板?在软件开发中,质量是一个关键的考虑因素。
一个高品质的软件产品可以提高用户满意度,降低故障率并增强用户体验。
而质量理念看板可以帮助团队在全员参与的基础上,共同关注和追求软件产品的质量。
质量理念看板有助于团队成员建立起对于质量的共同理解,并提供一个可视化的方式来记录和跟踪质量相关的活动和改进。
这样一来,整个团队可以更加专注于质量,并不断优化和提高质量。
质量理念看板的设计和组成一个质量理念看板一般由以下几个主要部分组成:1. 质量愿景质量愿景是团队对于产品质量的期望和愿景的表达。
它可以描述产品所需的特征、性能、可用性、安全性等方面的期望。
通过明确质量愿景,团队成员可以更好地理解和追求质量目标。
2. 质量目标质量目标是具体的和可衡量的目标,用于衡量和评估团队在质量方面的努力和成果。
质量目标可以包括关键绩效指标(KPIs)、质量度量、用户满意度等。
质量目标应该与质量愿景相一致,并具体、可测量、可追踪。
通过设定质量目标,团队可以更有针对性地进行质量改进和度量。
3. 质量活动质量活动是团队为了达到质量目标而采取的行动和活动。
这些活动可以包括代码审查、单元测试、自动化测试、持续集成、用户体验测试等。
质量活动的目的是发现和修复软件中的缺陷、问题和漏洞,并确保产品的质量。
质量活动应该与质量目标相一致,并根据实际情况和团队特点进行选择和调整。
团队应该持续关注和改进质量活动,以不断提高团队的质量能力。
4. 质量改进质量改进是团队在质量方面所做的持续改进和优化。
质量改进可以基于团队成员的经验和反馈,也可以借鉴行业和标准的最佳实践。
质量改进需要团队成员的参与和支持,并通过经验总结、持续学习和反思来推进。
质量改进是一个持续的过程,并应该持续关注和持续改进。
质量管理看板
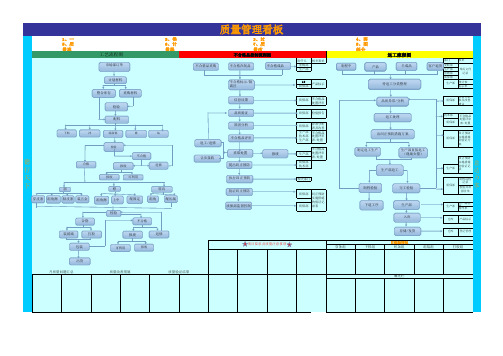
生产部
表单
相关文件 记录
统计表 标示单
异常分析 质保部 表及改善
建议
返工处理
出纠正预防措施方案
制定返工生产
生产部直接返工 (现场少量)
生产部返工
制程检验
完工检验
技术部 质保部
不合格品 处置评审 表/处置
质保部
纠正预防 实施措施 的验证方 案
生产部 质保部
纠正预防
意 实施措施
的验证记
录
达
万 制程巡检 家 记录
检验异常 报告单
下道工序
生产部 入库
生产流程 生产部 单
转序单
仓库 产品标示
穿条组Biblioteka 下料组存储/发货日检验情况 机加组
组装组
仓库 登记管理 打胶组
出货 月质量问题汇总
质量改善措施
质量验证结果
曝光栏
质保部
生产部 技术部 生产部
异常分析 表及改善
不合格品 处置评审 表/处置
生产部
质保部 技术部
不合格品 处置评审 表/处置
相关部门
质保部 质保部
纠正预防 实施措施 的验证记 录表
4、客 8、图
纸分
制程制中程中
产品产品
返工流程图
半成半品成品
待返工分待类返整工理分类整理
品质品异质常异/常分/析分析
部门 客户退货 采购部
1、一 5、质
量事
工艺流程图
市场部订单
2、供 6、计
量器
计划材料
整合库存
采购材料
检验 配料
下料
冲
端面铣
铣
钻
检验
不合格
生产质量看板维护方案
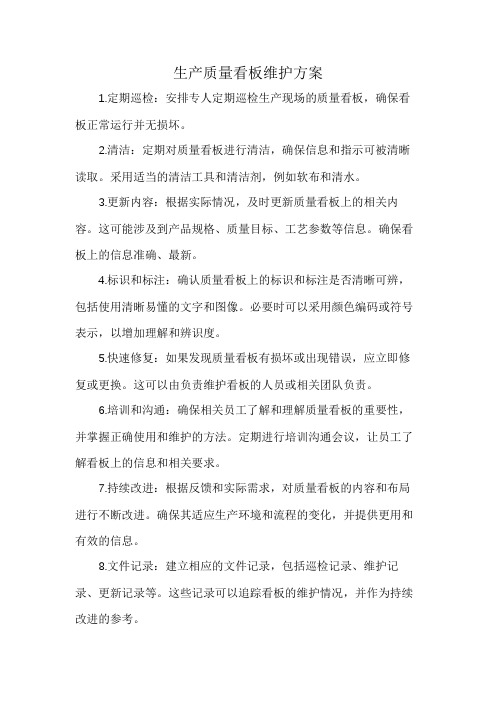
生产质量看板维护方案
1.定期巡检:安排专人定期巡检生产现场的质量看板,确保看板正常运行并无损坏。
2.清洁:定期对质量看板进行清洁,确保信息和指示可被清晰读取。
采用适当的清洁工具和清洁剂,例如软布和清水。
3.更新内容:根据实际情况,及时更新质量看板上的相关内容。
这可能涉及到产品规格、质量目标、工艺参数等信息。
确保看板上的信息准确、最新。
4.标识和标注:确认质量看板上的标识和标注是否清晰可辨,包括使用清晰易懂的文字和图像。
必要时可以采用颜色编码或符号表示,以增加理解和辨识度。
5.快速修复:如果发现质量看板有损坏或出现错误,应立即修复或更换。
这可以由负责维护看板的人员或相关团队负责。
6.培训和沟通:确保相关员工了解和理解质量看板的重要性,并掌握正确使用和维护的方法。
定期进行培训沟通会议,让员工了解看板上的信息和相关要求。
7.持续改进:根据反馈和实际需求,对质量看板的内容和布局进行不断改进。
确保其适应生产环境和流程的变化,并提供更用和有效的信息。
8.文件记录:建立相应的文件记录,包括巡检记录、维护记录、更新记录等。
这些记录可以追踪看板的维护情况,并作为持续改进的参考。
外企的质量看板

外企的质量看板摘要:一、外企质量看板的概念与作用1.定义与组成2.提升质量管理的意义二、外企质量看板的特点1.国际化标准2.实时数据分析3.严格的执行流程三、外企质量看板在各行业的应用1.制造业2.服务业3.信息技术产业四、外企质量看板的优势与挑战1.优势a.提升工作效率b.降低成本c.提高客户满意度2.挑战a.适应不同国家和地区的法规b.保障数据安全c.持续创新与改进正文:外企质量看板是一种应用于外企的质量管理工具,它通过可视化的方式展示企业的质量状况,以实现实时监控、数据分析和持续改进。
质量看板起源于日本,并在全球范围内得到广泛应用,特别是在外企中。
本文将对外企质量看板的概念、特点、应用及优势与挑战进行详细阐述。
一、外企质量看板的概念与作用外企质量看板是一种将企业的质量数据进行可视化展示的工具,通常包括关键绩效指标(KPI)、实时数据、趋势分析等。
它可以帮助企业及时发现质量问题,提高工作效率,降低成本,提高客户满意度。
二、外企质量看板的特点1.国际化标准:外企质量看板遵循国际化的标准,使得企业在全球范围内都能保持一致的质量管理。
2.实时数据分析:外企质量看板能够实时展示质量数据,使企业能够快速响应市场变化,调整战略。
3.严格的执行流程:外企质量看板具有严格的执行流程,确保数据准确性和质量管理的有效性。
三、外企质量看板在各行业的应用1.制造业:在制造业中,外企质量看板可以实时监控生产线的质量状况,以便快速发现和解决问题。
2.服务业:在服务业中,外企质量看板可以展示客户满意度、服务质量和业务运营等方面的数据,以提升服务质量。
3.信息技术产业:在信息技术产业中,外企质量看板可以关注软件开发、测试和运维等环节的质量,以提高产品的稳定性。
四、外企质量看板的优势与挑战1.优势:a.提升工作效率:通过实时数据分析,企业可以快速发现问题并采取措施,提高工作效率。
b.降低成本:外企质量看板可以帮助企业发现潜在的质量问题,从而降低返工、召回等成本。
车间质量看板模板

显示当前时间点的产品合格数量 和合格率,以便了解生产线的稳 定性和产品质量。
通过实时数据展示,可以及时发 现异常情况,采取相应措施,避 免问题扩大。
历史数据展示
历史报错率
展示一段时间内的报错数量和报错率,以便分析 问题原因和制定改进措施。
历史合格率
展示一段时间内的产品合格数量和合格率,以便 分析生产线的稳定性和产品质量变化趋势。
车间质量看板模板
目录
• 引言 • 质量目标与指标 • 质量数据展示 • 质量异常处理 • 质量改进与提升 • 结论与展望
01
引言
ห้องสมุดไป่ตู้
目的和背景
01
车间质量看板是用于监控和展示 生产过程中质量信息的工具,旨 在提高生产效率和产品质量。
02
在制造业中,质量看板被广泛应 用于实时监控生产流程、预防质 量问题、提高员工质量意识等方 面。
历史监控数据
通过历史数据展示,可以了解生产过程中的变化 趋势,为后续生产提供参考。
数据趋势分析
报错率趋势
分析报错率的变化趋势,以便及时发现和解决潜在问题。
合格率趋势
分析合格率的变化趋势,以便了解生产线的稳定性和产品质量的变 化情况。
监控数据趋势
通过数据趋势分析,可以预测未来的变化趋势,提前采取应对措施。
建立跨部门的质量协作机制
加强与其他部门的沟通和协作,共同推动质量改进工作。
THANKS
感谢观看
质量看板鼓励员工积极参与质量改进, 提高员工的质量意识和责任感。
未来质量改进的方向与计划
持续优化质量管理体系
根据质量看板的反馈,不断完善和优化质量管理体系,确保持续改进。
引入先进的质量管理工具和技术
质量看板资料
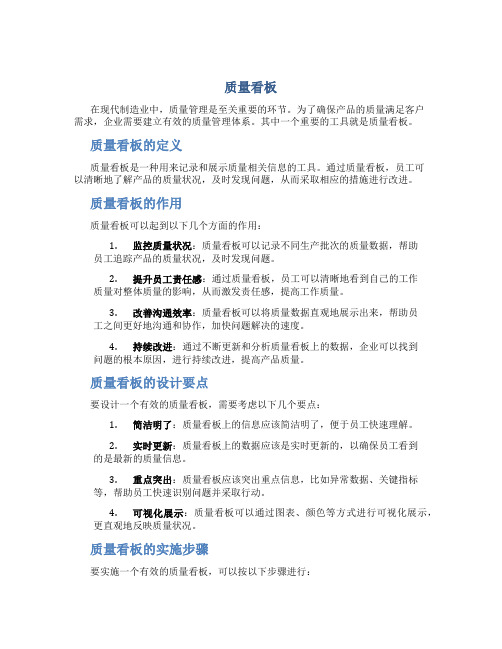
质量看板在现代制造业中,质量管理是至关重要的环节。
为了确保产品的质量满足客户需求,企业需要建立有效的质量管理体系。
其中一个重要的工具就是质量看板。
质量看板的定义质量看板是一种用来记录和展示质量相关信息的工具。
通过质量看板,员工可以清晰地了解产品的质量状况,及时发现问题,从而采取相应的措施进行改进。
质量看板的作用质量看板可以起到以下几个方面的作用:1.监控质量状况:质量看板可以记录不同生产批次的质量数据,帮助员工追踪产品的质量状况,及时发现问题。
2.提升员工责任感:通过质量看板,员工可以清晰地看到自己的工作质量对整体质量的影响,从而激发责任感,提高工作质量。
3.改善沟通效率:质量看板可以将质量数据直观地展示出来,帮助员工之间更好地沟通和协作,加快问题解决的速度。
4.持续改进:通过不断更新和分析质量看板上的数据,企业可以找到问题的根本原因,进行持续改进,提高产品质量。
质量看板的设计要点要设计一个有效的质量看板,需要考虑以下几个要点:1.简洁明了:质量看板上的信息应该简洁明了,便于员工快速理解。
2.实时更新:质量看板上的数据应该是实时更新的,以确保员工看到的是最新的质量信息。
3.重点突出:质量看板应该突出重点信息,比如异常数据、关键指标等,帮助员工快速识别问题并采取行动。
4.可视化展示:质量看板可以通过图表、颜色等方式进行可视化展示,更直观地反映质量状况。
质量看板的实施步骤要实施一个有效的质量看板,可以按以下步骤进行:1.确定质量指标:首先需要确定需要监控的质量指标,比如产品合格率、不良品率等。
2.设计看板布局:根据质量指标的重要性和关联性,设计质量看板的布局,将重点信息放在显眼的位置。
3.收集数据:建立数据收集机制,确保质量数据能够及时准确地录入到质量看板上。
4.培训员工:对员工进行培训,教会他们如何使用质量看板,并理解其中的信息。
5.持续改进:定期分析质量看板上的数据,找到问题所在,采取措施进行改进。
质量看板

排孔标准:所有孔径、孔位、孔深符合工艺标准。
公差:孔径±0.1mm;孔位、孔距±0.3mm;孔深±0.5mm。
板件外观:无撞伤碰坏,孔四周无残留胶丝及连体崩缺,单个崩缺大小≤1mm,一个孔最多允许一个单体崩缺。
质量问题:水平孔排浅
原因:活动靠档调太大;更换钻头时安装不均匀;气压不稳;钻头长短不一致。
质量问题:垂直孔排浅
原因:气压不稳定;控制开关调太下;钻头长短不一致。
质量问题:排孔错
原因:对产品工艺不熟悉;钻头脱落未及时发现;自检不到位。
钻头脱落未及时发现;自检不到位。
质量问题:多排孔
原因:对产品工艺不熟悉;机器故障;钻头脱落未发现。
质量问题:孔崩缺
原因:钻头没紧固或者有磨损;原材料贴面太脆;排夹板速度太快。
质量问题:水平孔排深
原因:活动靠档调太小;更换钻头时安装不均匀;钻头长短不一致。
质量问题:垂直孔排深
原因:控制开关调太上;钻头长短不一致。
质量问题:漏排孔
原因:对产品工艺不熟悉;钻头脱落未及时发现;自检不到位。
钻头脱落未及时发现;自检不到位。
质量问题:孔距偏差
原因:板件尺寸偏小或偏大;对角线不相等;靠档磨损误差。
质量管理看板模板

质量管理看板模板质量管理是企业生产经营中非常重要的一环,而看板则是一种直观、简单的管理工具,能够帮助企业管理者及时了解生产情况,发现问题,及时解决。
因此,质量管理看板模板的设计和使用对于企业的质量管理具有重要意义。
接下来,我们将介绍一种质量管理看板模板的设计方案,希望能够为您的质量管理工作提供一些参考。
首先,我们来看看这个质量管理看板模板的整体结构。
整个看板分为四个主要部分,问题汇报区、问题分析区、问题解决区和改进措施区。
每个区域都有相应的标识和内容,方便员工和管理者快速了解当前的质量管理情况。
在问题汇报区,员工可以记录发现的质量问题,包括问题的描述、发现时间等信息。
问题分析区则是对问题进行分析,找出问题的根本原因。
问题解决区是用来记录问题的解决过程和结果。
最后,改进措施区则是用来记录针对问题制定的改进措施和实施情况。
在设计这个质量管理看板模板时,我们需要考虑到一些重要的原则。
首先,要保持看板的简洁和直观,让员工和管理者一目了然。
其次,要注重信息的及时性和准确性,确保看板上的信息能够及时反映实际情况。
另外,还要注重看板的可操作性,让员工能够方便地记录和查阅信息。
最后,要注重看板的持续改进,根据实际使用情况不断优化和调整看板的设计和内容。
在使用这个质量管理看板模板时,我们还需要注意一些细节。
首先,要保持看板的更新,及时记录和更新看板上的信息。
其次,要注重看板的使用培训,确保员工能够正确地使用和理解看板。
另外,还要注重看板的定期检查,发现问题及时进行纠正。
最后,要注重看板的反馈和改进,根据使用情况和反馈意见不断改进和优化看板的设计和内容。
总的来说,质量管理看板模板是质量管理工作中非常重要的一部分,它能够帮助企业管理者及时了解生产情况,发现问题并及时解决。
因此,设计和使用一个合理、实用的质量管理看板模板对于企业的质量管理工作具有重要意义。
希望我们提供的质量管理看板模板能够为您的质量管理工作提供一些帮助,也希望您能够根据实际情况进行调整和优化,使之更好地适应您的企业实际情况。
- 1、下载文档前请自行甄别文档内容的完整性,平台不提供额外的编辑、内容补充、找答案等附加服务。
- 2、"仅部分预览"的文档,不可在线预览部分如存在完整性等问题,可反馈申请退款(可完整预览的文档不适用该条件!)。
- 3、如文档侵犯您的权益,请联系客服反馈,我们会尽快为您处理(人工客服工作时间:9:00-18:30)。
5.整修品、不良 出现不良品 品、退货的 更改生产项目 6.换模的 换模方式之改进表的设计 时的时间
一句话 S
中文 整理 整顿 清扫 关键意义 “扔”的智慧 易取、易放、易存 点检,找出问题,解决问 题 典型例子 倒掉垃圾、长期不用的东西放 仓库 30秒内就可以找到要找的东西 谁使用谁清洁(管理)
生产的态度的改善
从【不行的说辞】到【努力的意见】的转变 通过5个转变来实施改善
①现在没法做。 ②只能做这么多。 ③以前没做过。 ④因为不清楚所以做不了。 ⑤太费时间而不愿做。
马上开始做。 试着做更多。 做做看。 主动要求去做。 即使花时间也要做。
制造・生产的改善体系
技术改善 作业改善 生产能力 品质改善 能力改善 作业人改善 设备改善
对设备要实行“TPM”管理
7
“设备”的管理
这里所说的“设备”,包括设备,机械及装置以外的 夹具和工具等。设备的管理是要尽早发现设备运转不良及 分析其原因,采取适当的措施;而且还要进行预防性维护, 以防患于未然。对设备和机械,包括夹具、工具等,都需 要工人的日常检修,以及依据一定的标准进行定期的检修 和调整。
①检查改善→管理体制、②标准化→消灭不合格 ①目标改善→、目标设定定、②技能→评价训练
①机械改善→改良、②工艺改善→单纯化
①作业方法改善→标准化、②作业缩短→搬运、工装
①工人作业→时间管理、②工人能力→技术教育 ①运行效率→持续运行、②设备管理→TPM实施 ①进度管理→点检巡察、②效率管理→8大浪费的消除 ①保养维修管理、②故障解决→修理的简单化
不合格品的控制流程:
发现不合格品
标识、记录、隔离、报告
组织评审
返工/返修 不 合 格 检验
让步接收
退货/报废
合格 入库 财务结算
5
不合格品的标识方法 依据产品特点可分别采用下列方法之一: A、用红色记号笔在不合格品的醒目位置做标识; B、附不合格品标签; C、置于不合格品区(或隔离区、退货区)。 油漆颜色标识: 红色-------废品 绿色-------放行 黄色----待处理 白色----配制零件
清洁
修养 安全
标准化
养成一种好的习惯 消灭一切安全隐患
管理的公开化、透明化
按标准作业、自发、改善创新 、客户意识 三不伤害
• 5 SEIKETSUSHITSUKE
• 安全:消灭一切安全隐患
1.小心你的思想,它会改变你的行为; 2.小心你的行为,它会改变你的习惯; 3.小心你的习惯,它会改变你的性格;
4.小心你的性格,它会改变你的命运;
12种的浪费及改善提示
浪 费 的 型 态 例 7.搬运的 流程不顺 无意义的作业 8.加工方法的 方法 9.材料、副料的 材料用量过多 各种报表的整 10.转记的 理、重记 11.未清扫、 废料、半成品 未整理的 堆积现象 12.传达、联络 规 格 变 更 时 之 方式不良的 联络 改 善 提 搬运器具之设计 改良加工方法 标准用量之决定 表格之重新设计、有效利用 不用物品立刻丢弃,每项物品 均需定位 联络、确认方法之重新检讨 示
运转能力
效率改善 保养改善
什么是6S管理?(5S+1S)
• 1 S整理– 分离及丢弃 (“Seiri”) • 2 S整顿–排序及识别 (“Seiton”)
SEISO SEITON
SEIRI
5S
• 3 S清扫– 清扫及日检 (“Seiso”) • 4 S清洁– 标准化 (“Seiketsu”) 素养– 主动保持(“Shitsuke”)
9
现场质量管理
全面质量管理的一个重要特点是“预防性”,即变仅靠“事后把关”为加 强“事前预防”,变管理结果为管理因素。从微观角度看,引起产品质量波动 的原因主要来自6个方面:
人(Man):操作者的质量意识、技术水平、文化素养、熟练程度和身体素质 等。 机器(Machine):机器设备、工夹具的精度和维护保养状况等。 材料(Material):材料的化学成分、物理性能和外观质量等。 方法(Method):加工工艺、操作规程和作业指导书的正确程度等。 测量(Measure):测量设备、试验手段和测试方法等。 环境(Enviroment):工作地的温度、湿度、含尘度、照明、噪音和震动等。 通常把上述因素称为引起产品质量波动的6大因素或简称“5M1E”因素。
注:标识时统一使用油漆记号笔或油漆,标识“○”时 的直径大小约为30㎜。
6
“设备”的管理
这里所说的“设备”,包括设备,机械及装置以外的 夹具和工具等。设备的管理是要尽早发现设备运转不良及 分析其原因,采取适当的措施;而且还要进行预防性维护, 以防患于未然。对设备和机械,包括夹具、工具等,都需 要工人的日常检修,以及依据一定的标准进行定期的检修 和调整。
8
“人”的管理
在5M1E中,人是最重要的因素。不论是设备的操作、检修、保养、还是材料的验收 把关,以及作业方法的遵守和改进等等,都依靠工人的智能和积极性。因此,对“人” 的管理要做好以下几方面工作: 1)加强对工人的技能训练 a、让工人充分理解质量标准和作业标准
b、按要求进行充分训练
c、进行个别而具体的指导 2)提高工人的质量意识 a、加强对自己作业质量的控制 b、提高对自己工作重要性的认识 c、加强全面质量管理思想和方法的宣传教育
不良原因 不良情况 对策 改善 点检
制造・生产的改善的问题解决与对策(实施例)
在中国进行工厂改善时的教训
小组活动取得成效的做法②
1.改善对象 2.改善方法
品质、工艺、作业者、生产量、在库、机械、 设备、作业场地、整个生产线。 对每个对象确定达成目标。在改善现场张贴改善 记录看板(红牌)。Байду номын сангаас
确定Q、C、D、S、E各项基准
12种的浪费及改善提示
浪 费 的 型 态 1.取放时的 2.等待的 3.动作的 4.生产过多的 例 材料、工具的 取放位置 出现等待时间 材料、工具等 的放置方法 预行生产 改 善 提 示 使易取、易放并标准化 多能化之训练 材料、工具放置方法之重新检 讨,两手同时作业 设定标准中间制品量,到达标 准量后即停止 工具、夹具之重新设计、防呆 装置(Fool proof)
检验手册的内容
1)质量检验体系和机构,包括机构框图,机构职能(职责、权限)的规定; 2)质量检验的管理制度和工作制度; 3)进货检验程序; 4)过程(工序)检验程序; 5)成品检验程序; 6)计量控制程序(包括通用仪器设备及计量器具的检定、校验周期表); 7)检验有关的原始记录表格格式、样本及必要的文字说明; 8)不合格产品审核和鉴别程序; 9)检验标志的发放和控制程序; 10)检验结果和质量状况反馈及纠正程序; 11)经检验确认不符合规定质量要求的物料、产品组成部分、成品的处理程序。
10
制造・生产的改善
1.品质并不是在产品完成后进行检查。 不是制造产品,要制造品质。 2.生产、制造相关的全体人员要每天进行改善。 改善的日积月累会带来课题的最终解决。
3.所谓改善、就是:品质管理 成本管理 交货期管理 安全管理 环境管理
制造・生产的不良品对策
不良品在哪里制作的? 是人的错误还是机器的错误? 不良是在什么样的作业中发生的? 不良品的出现是什么时候开始发生的? 什么时候,是怎样被发现的? 数量是多少? 不良产品多还是少? 产生不良产品的原因:是一时的,还是连 续的? 不良产品的对策、改善能不能够马上 进行?
《8D》的问题处理图
质量问题处理方法
QC活动8步骤 1.选课题 8.反省及今 后的计划 A 2.现状调查 和目标设定 P 3.活动计划
7.标准化和管 理的常规化 目标未达成 目标达成
C
6.确认效果 4. 原因分析 5.对策实施 D
检验指导书的内容
(1)检测对象:受检产品名称、型号、图号、工序(流程)名称及编号; (2)质量特性值:按产品质量要求转化的技术要求,规定检验的项目; (3)检验方法:规定检测的基准(或基面)、检验的程序和方法、有关计 算(换算)方法、检测频次、抽样检验时有关规定和数据; (4)检测手段,检测使用的计量器具、仪器、仪表及设备、工装卡具的 名称和编号: (5)检验判定:规定数据处理、判定比较的方法、判定的准则; (6)记录和报告:规定记录的事项、方法和表格,规定报告的内容与方 式、 程序与时间; (7)其他说明。