ERSA选择性波峰焊LAYOUT规范
波峰焊作业规范标准
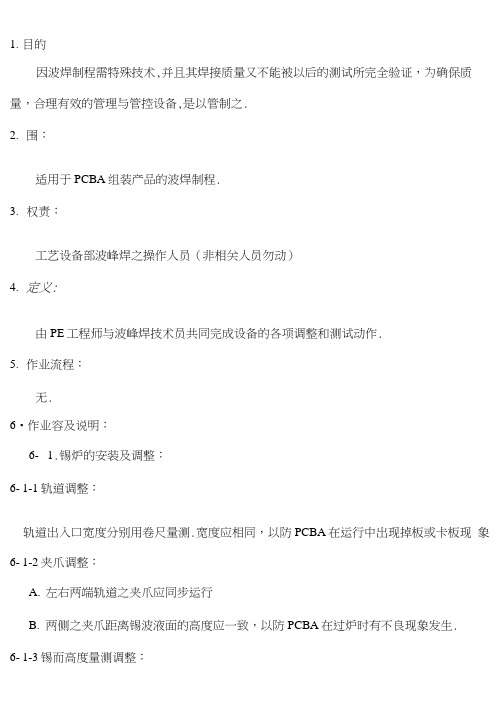
1.目的因波焊制程需特殊技术,并且其焊接质量又不能被以后的测试所完全验证,为确保质量,合理有效的管理与管控设备,是以管制之.2.围:适用于PCBA组装产品的波焊制程.3.权责:工艺设备部波峰焊之操作人员(非相关人员勿动)4.定义:由PE工程师与波峰焊技术员共同完成设备的各项调整和测试动作.5.作业流程:无.6•作业容及说明:6-1.锡炉的安装及调整:6-1-1轨道调整:轨道出入口宽度分别用卷尺量测.宽度应相同,以防PCBA在运行中岀现掉板或卡板现象6-1-2夹爪调整:A.左右两端轨道之夹爪应同步运行B.两侧之夹爪距离锡波液面的高度应一致,以防PCBA在过炉时有不良现象发生.6-1-3锡而高度量测调整:锡而高度量测应在波峰开启的状态下,用钢尺下量至液面,锡面距锡槽边的距离应控制在20±2mm.生产中每两小时量测一次,如高于上述标准.则需添加锡棒拼记录于vv波峰焊日常保养点检表>>•6-1-4锡波高度量测:A.用钢尺垂直于波峰喷口向下量测锡波高度,平视钢尺刻度.高度应在10±3mm以下, 以防波而落差过大造成焊锡大量氧化和吃锡不良.B.PCB吃锡深度控制在其板(或过炉载具)厚的1/2-2/3之间,以防溢锡或漏焊.6-15锡炉传送带测试调整:A.新设备进厂后,在锡炉传送带导轨两端用红色高温胶带标出1000MM长的标示段, 用秒表计算PCBA通过此标示段所耗用的时间,然后用标示段长度除以PCBA通过标示段所耗用的时间,即得到锡炉标准传送带传送速度.B.以A所述的标准传送带速度为参照,校正锡炉自检系统测得的传送带速度,使两者保持一致,即得出正确的锡炉自检速度,一般控制在1700mm±200mm/min之间,生产中每一天读取锡炉自检传送速度一次,并记录于vv波峰焊炉温与链速记录表>>.6-16输送带仰角量测:设备上所安装的角度测量仪所显示的实际输送带仰角,应控制在5° -7°6-1-7.锡炉熔锡温度量测:将温度测试仪电源开关瘤歹至劇上显示数字,然后将温度测试仪之感温头插入锡波而约5mm的位置.待温度测试仪数字显示稳定后,表面所显示数值即为所要测试锡炉熔锡的实际温度.温度应控制在250±10°C,测试完毕,将测试结果(正常生产需每天检测一次)填写在vv波峰焊炉温与链速记录表 >>上.(备注:也可以使用其它温度计进行量测). 6-1-8.锡炉预热温度测试:A.新设备进厂后,在预热区每一个发热段中部各选取一个测试点,设定其预热参数为a,机台自检测得的温度为b,用温度测试仪测试各测试点之温度值为标准预热段温度值c.B.以A所述的标准预热段温度值c为参照,校正锡炉自检系统测得的预热段温度b,使两者保持一致,得到正确的锡炉自检预热段温度值,生产中每两小时读取锡炉自检预热段温度一次,并记录于VV波峰焊预热区记录表».Profile测试所得预热最高温度以产品也指导书为准. 62锡炉Profile测试:6-2-1.测温点的选择参照《Profile制作规》.如客户有特殊需求.依客户要求为准.6-2-1.测试方法及步骤请参照profile炉温测试仪使用说明书.6-2-2profile 测试时机:6-2-2-1.新设备进厂时,由锡炉工程师对锡炉进行Profile测试,以检测设备工作性能及技术指标.相关数据标准及测试点选取由锡炉工程师参照业界标准,结合公司实际情况确定各项参数的设定及测试点选取.6-2-22新机种上线,由锡炉工程师参照客供标准Profile,并结合本公司实际情况测得该机种在本公司生产环境下之标准Profile,如客户有特殊要求,请以客户要求为准.622-3.每周对每台波峰焊用测温仪测试一次Profile并存档,.并确实以Profile反映数据为参照来设定锡炉工作参数,达到合理有效的管控锡炉各项参数、监测锡炉工作状态的目的, 以此来保证良好的焊接质量.6-2-24测试基木参数要求:6-2-2-5如在生产过程中出现品质异常需重新测试Profile.6-2-2-6设备在维修后.为确保其温控系统未受到影响.也需测试Profile.6-3.锡炉助焊剂比重测试: 将所要测试的助焊剂用吸管吸入测试量杯中,然后将比重计轻轻放入测试量杯中,待液面 与比重计皆静止不动时读取比重计所显示的数值,即得到所测试助焊剂的比重.(读取数 据时以液面的凹而为准)•每天开线前对锡炉所使用之助焊剂进行量测并把量测结果填写 在v 波峰焊机每天点检报告>> 上.6-5.锡炉PPM 值管控: 6-5-1.锡炉PPM 值管控由工程单位实施执行,并持续改善.6- 52每日锡炉工程师需对炉后补焊段不良进行统计,分析其不良原因并写出改善说明.7. 生产注意事项:7- 1.生产前注意事项:7- 1-1.查看锡炉锡液温度是否在设定温度.7- 12锡炉液位是否在要求围. 设备型号「 链速(ram/min)-助焊剂济虽 预热卜” 预热二・ 预热三卩 披峰一丿波峰二卩 焊接时间(S )「 NK-350< 1700 (rm/rTdnj< 0.张1 (nun)*3 1300 150t>25l)t<> 250匕 3・5 (S) ~ 注释…首先训节彼堆焊链速为1700 (mm/min ) ± 200(«!n/.in ),当PCBA 经过助焊剂区时流虽喷芻 为0.4ml±0. lml/min,经过第一预热区时其温度 达到13CTC 土5匸,当PCBA 经过笫二预热区时其 温度达到1509土5£,当PCBA 经过第三预热区 时其温度达到17()9 ±59,当经过焊接区时其温 度达到2509土 10t 打波躍焊接时间为3 5(S )土 0.5(S ),焊接完成后经过冷却区羯度逐渐下降到 509以下。
波峰焊操作规程

波峰焊操作规程
《波峰焊操作规程》
一、目的
本规程的目的是为了规范波峰焊操作流程,保障焊接质量,提高生产效率。
二、适用范围
本规程适用于公司内进行波峰焊操作的所有员工。
三、操作规程
1. 检查设备和工具
在进行波峰焊操作前,必须检查焊接设备和工具的运行状态,确保设备正常运转。
2. 准备焊接材料
根据工艺要求,准备好焊接材料,确保其质量符合要求。
3. 准备工件
对需要进行波峰焊的工件进行清洁、涂敷焊接剂等前期准备工作。
4. 设置焊接参数
根据工艺要求,设置好波峰焊设备的参数,包括预热温度、焊锡温度、焊锡速度等。
5. 进行焊接作业
根据工艺要求和设备参数,进行波峰焊操作,确保焊接质量。
6. 检验焊接质量
在焊接完成后,对焊接质量进行检验,确保焊接完好无损。
7. 清理工作区
工作完成后,清理工作区域,妥善保管焊接设备和工具。
四、安全注意事项
1. 在进行波峰焊操作时,必须佩戴防护眼镜和手套,确保人身安全。
2. 使用完毕的焊接设备和工具必须妥善存放,确保设备完好。
3. 禁止在焊接过程中进行其他无关操作,确保焊接作业的安全。
五、特殊情况处理
在进行波峰焊操作过程中,如遇到异常情况,必须及时向主管报告,并做出相应处理。
六、操作规程的执行和监督
对本规程的执行和监督由公司主管负责,员工必须严格按照本规程执行。
七、附则
对于本规程未尽事宜的处理,由公司主管负责解释。
以上为《波峰焊操作规程》,请所有员工严格遵守。
layout注意事项

Layout注意问题一:ESD 器件由于ESD器件选择和摆放位置同具体的产品相关,下面是一些通用规则:1.让元器件尽量远离板边。
2.敏感线(Reset,PBINT)走板内层不要太靠近板边;RTC部分电路不要靠近板边。
3.可能的话,PCB四周保留一圈露铜的地线。
4. ESD器件接地良好,直接(通过VIA)连接到地平面。
5. 受保护的信号线保证先通过ESD器件,路径尽量短。
二:天线13MHz泄漏,会导致其谐波所在的Channel: Chan5, Chan70,Chan521、586、651、716、781、846等灵敏度明显下降;13MHz相关线需要充分屏蔽。
一般FPC和LCDM离天线较近,容易产生干扰,对FPC上的线需要采取滤波(RC 滤波)措施和屏蔽FPC,并可靠接地。
靠近天线部分的板上线(不管什么类型)尽量要走到内层或采取一定的屏蔽措施,来降低其辐射。
(板内的其他信号可能耦合到走在表层的信号线上,产生辐射干扰。
)三.LCD注意FPC连接器的信号定义:音频信号线最好两边有地线保护;音频信号线与电平变换频繁的信号线要有足够间距;FPC上的时钟信号及其他电平变换频繁的信号要有地线保护减少EMI影响;LCD的数据线格式是否和BB芯片匹配?例如i80或M68在时序上要求不一致等问题。
设计中对LCM 上的JPEG IC时钟信号的频率,幅值要满足需求。
如果时钟幅度不够可能导致JPEG不工作或不正常;注意Camera的输入时钟对Preview的影响,通常较高的Preview刷新帧数要求时钟频率高。
布局上,升压电路远离天线;音频器件和音频走线;给Camera供电的LDO靠近Camera放置;主板上Hall器件的位置要恰当,不能对应上盖LCD屏的位置,否则上盖的磁铁不能正对着Hall器件。
四.音频设计PCB布局音频器件远离天线、RF、数字部分,防止天线辐射对音频器件(音频功放等)的干扰;如果靠的很近,应该考虑使用屏蔽罩。
选择性波峰焊工艺设计指南

选择性波峰焊工艺设计指南1.简介实现最佳焊接结果,需满足特殊工艺条件高标准工艺可靠性取决于以下几点:●pad设计(pad类型,pad之间距离)●pad及周边元件pad距离(如,不应触碰SMD器件)●PIN脚长度不应超过电路板板下PIN脚长度●PIN脚间距(如,连接器间距)这些影响系数直接影响流动焊料的剥离。
为了避免产生锡桥,需要重复剥离。
锡桥是导致焊接失败的主要原 因(占80%以上)。
通常来说,小型拖焊工艺和浸焊工艺存在明显区别。
每道工艺都需特殊的印刷电路板设计。
如下设计指南可确保最佳工艺条件。
如果您不采纳如下建议,工艺窗口将会受到局限,而且需额外步骤稳定 此工艺。
这些额外步骤所需维护要求更高,并会增加模具零件的磨损。
> 3.0 mm> 5.0 mm2. 浸焊工艺最佳布局●优先使用圆垫●圆垫之间距离: >0.60mm ●PIN脚距离: >2.54mm2.2 PIN脚长度不应超过电路板板下PIN脚长度2.3 焊料喷嘴间隙 - 到邻垫距离(不被焊接)●在3面上: > 3.0mm ●在第四面上: > 5.0mm> 1.9 mm3. 微波/拖焊焊接工艺最佳布局3.1 pad之间的间隙●优先使用圆垫●圆垫之间距离: >0.60mm ●PIN脚距离: > 1.9mm3.2 PIN脚长度不应超过电路板3.3 微波间隙 - 到邻垫距离(不被焊接)●在3面上: > 2.0mm ●在第四面上: > 5.0mmØ 3.0 mm4. 焊料喷嘴最小尺寸4.1 矩形焊料喷嘴●焊接面积 <40mm ²4.2 圆形焊料喷嘴●焊接区 <7mm ²5. 相邻元件最大高度底部(焊接面)所能容纳的最大元件高度受限于焊料喷嘴的高度。
标准焊料喷嘴高度为32mm。
因此, 最大元件高度不应超过25mm。
更高的元件需要更高的焊料喷嘴设计,我们可根据您的要求设计。
波峰焊治具设计规范

工程管理華東地區波峰焊治具設計規範PAGE4 OF 21 REV B6. 作業流程與內容6.1波峰焊治具分類6.1.1試產波峰焊治具分類為: (1)一般試產波峰焊治具 (2)特殊試產波峰焊治具 6.1.2 一般試產波峰焊治具材質:FR4或電木.治具尺寸:如下圖所示(1).治具結構﹕底框架+托邊框架. (2).治具四周需要加軌道邊.(3).S0階段(sample run)治具不需要製作壓條,S0後之試產時需要都I/O 零件 製作壓條.A:承載邊厚度=2.6±0.1mm B:檔錫牆高度=4±0.2mm C:治具厚度=4±0.2mmD:PCB 承載邊深度=PCB 厚度*3/4 側視圖俯視圖FGHHGAB C D E工程管理華東地區波峰焊治具設計規範PAGE 5 OF 21REV B E:軌道邊寬度=9±0.2mmF:PCB板與板之間距離=15±0.2mmG:PCB與治具檔錫牆之間距離=15±0.2mmH:治具檔牆寬度+治具承載邊寬度=7+10=17±0.2mm6.1.3 特殊試產波峰焊(可旋轉角度)主要應用於驗證特殊,異形零件,Pin腳Pitch較小零件,或新性零件沒有把握控制wave solder 良率時, 在試產階段確認產品過爐最佳角度. 確認量產治具的開設.(1).治具結構﹕底框架+托邊框架.(2).治具四周需要加軌道邊.(3).S0階段(sample run 治具不需要製作壓扣,S0後之試產時需要都I/O 零件製作壓扣.(4).外框材質:合成石;套板材質: FR4或電木.可旋轉角度治具組合圖外框套板PCB板刻度工程管理 華東地區波峰焊治具設計規範PAGE6 OF 21 REV BA:承載邊厚度=2.6±0.1mm B.檔錫牆高度=5±0.2mm C:檔錫牆高度=5±0.2mm D:治具厚度=5±0.2mm E:套板支撐臺階=5±0.2mm F:軌道邊寬度-9±0.2mm G: 檔錫牆寬度=7±0.2mmH:套板支撐臺階厚度=2.5±0.2mmI:治具長寬尺寸=318mm. J:尺寸=17mm.300mm I=318mm 300mm 318mmJ=17m俯視圖266mm 側視圖D=5mmG=2.5mmC=5mm E=9mmF=7mmB=8mmA=3mm工程管理華東地區波峰焊治具設計規範PAGE 7 OF 21REV B 6.1.4量產波峰焊治具結構與尺寸定義:6.1.4.1量產波峰焊治具材質:6.1.4.1.1底板、搭載邊條選用合成石.6.1.4.1.2 方向邊框可選用合成石/FR4.6.1.4.2量產波峰焊治具尺寸:如下圖所示治具結構:底框架+托邊框架A: 檔錫牆高度=5±0.2mmB: 軌道邊寬度=9±0.2mmC:治具厚度=5±0.2mmD: PCB與治具檔錫牆之間距離=20±0.2mmE:治具牛角擋錫牆固定於治具的寬度E1為7±0.2mm,E2為12±0.2mmF:擋錫牆到牛角之間距離30±0.2mmG:牛角導圓角半徑R=10±0.2mmH:PCB板與PCB板放置間距15±0.2mmI:PCB板到擋錫牆之間的距離15±0.2mmJ:治具檔牆寬度+治具承載邊寬度=7+9=16±0.2mmK:牛角墊塊長度20±0.2mmL:牛角墊塊寬度20±0.2mmM:牛角墊塊厚度5±0.2mmN:PCB放板導角直徑3±0.2mmO:治具邊框寬度:10±0.2mmP:軌道承載邊厚度3±0.2mmQ:牛角內長15±0.2mmR:牛角內寬15±0.2mm注:圖中橢圓形為5*2.5 mm導圓角,如右圖所示.工程管理華東地區波峰焊治具設計規範PAGE8 OF 21 REV B6.1.5錫波平整度波峰焊治具主要應用于測量錫波峰平整度﹐以檢驗錫槽是否有異常. 6.1.5.1治具材質: 合成石+玻璃6.1.5.2 治具具體尺寸與普通試產波峰焊治具尺寸定義相同. 6.1.5.3 治具結構:底框架+托邊框架+耐溫刻度玻璃.(單位:mm)6.1.6錫槽高度校正波峰焊治具最大特點在於承載邊底部到治具底部距離H 為13mm, 比試產及量產波峰焊治具多3mm, 通過此治具可以調試錫槽高度,保證試產及量產波峰焊治具與錫槽至少3mm 間隙. (具體使用方法參見波峰焊操作規範) 6.1.6.1 治具材質:合成石+ 45鋼+不銹鋼 6.1.6.2 治具結構及具體尺寸如下圖所示.(單位:mm) 6.2 波峰焊治具排版所有波峰焊治具排版遵循應遵循以下原則: 6.2.1 PCB 放置于波峰焊治具方向判定依據: 6.2.1.1 淚滴PAD 及盜錫塊考慮:當PCB 中有Ring 與Ring 之間距離小於0.8mm,並且設計淚滴PAD,則PCB 放置于波峰焊治具時﹐須保證淚滴PAD 與波峰焊過錫爐方向相同.如下圖:450 350 H3工程管理華東地區波峰焊治具設計規範PAGE9 OF 21 REV B過錫爐方向 A<0.8mma. Connector ,CBL(排線)過錫爐方向 b. two row pin connector:A<0.8mm過錫爐方向 A<0.8mm c. RJ45,RJ11過錫爐方向d. Connector工程管理華東地區波峰焊治具設計規範PAGE 10 OF 21 REVB當PCB 中有Ring 與 Ring 之間距離小於0.6mm,並且設計盜錫塊,則PCB 放置于波峰焊治具時﹐須保證盜錫塊最後與錫波接觸.如下圖:6.2.1.2 多Pin 腳Connector Ring 與Ring 之間距離小於1mm,則過錫爐方向須特別定義.如下圖:6.2.1.3 當PCB Layout 中都無以上過波峰焊方向限制,則考慮將Connector 零件放置於治具前端﹐以便於插件.過錫爐方向A<1mmB<1mm 過錫爐方向A<0.6mmConnector 前置與波峰焊方向一致工程管理華東地區波峰焊治具設計規範PAGE 12 OF 21REV B 6.3.3 治具的環保標示要求:為滿足不同客戶稽核要求,治具上所標識的“GP RoHS LF”均表示為環保產品治具.環保標識適用於無鉛機種,有鉛機種只需刻上廠內編碼.6.3.4 治具編碼申請管理:治具製作前需向鋼板治具系統管理員申請編號,製作後由管理員錄入系統,並且治具管理員根據廠內編碼追蹤治具製作進度.6.4 治具壓扣設計標準.6.4.1壓扣分類:普通單邊壓扣(圖A),普通雙邊壓扣(圖B),材質均為賽鋼.圖A 圖B6.4.2普通單邊壓扣,和普通雙邊壓扣工程尺寸圖.普通單邊壓扣工程圖普通雙邊壓扣工程圖工程管理華東地區波峰焊治具設計規範PAGE 13 OF 21REV B 6.4.3 波峰焊壓扣佈局原則:(1)壓扣一般分佈在PCB板四個角,並保證壓扣壓住PCB板邊至少3±0.5mm.(2)所有壓扣放置位置須保證其周圍3mm內無SMD零件.(3)在空間允許情況下, PCB板與PCB板連接處,採用普通雙邊壓扣設計以節省工時.6.5 壓條設計標準化6.5.1 壓條製作時機: 由波峰焊試產組統計試產過程中易浮高偏位元零件位置及浮高不良率﹐並最終確定開設壓條.6.4.2 壓條壓扣設計原則: (1) 壓條設計功能滿足要求.(2) 壓條材質須滿足防靜電要求,及耐高溫性.(3) 壓條放置方向須有防呆及定位設計.(4) 壓條放置動作最簡化性.6.5.3 現有壓條結構設計類型:6.5.3.1普通壓浮壓條結構設計(1)壓浮零件在2個以內﹐採用類壓扣設計.須壓浮高PCBA如下圖工程管理華東地區波峰焊治具設計規範PAGE 14 OF 21 REVB壓條採用類壓扣設計如下圖所示:(2) 壓浮高零件在2個以上﹐則採用整體式壓條設計. 須製作壓條PCBA 板上零件結構如下:壓條結構設計根據零件結構設計成長條式﹐其結構如下圖所示:壓條與零件壓浮配合為過盈配合﹐其過盈量為0.2mm. 6.5.3.2 特殊壓條結構設計----彈簧壓浮設計.適用條件:零件極易浮高﹐且與PCB 板無卡鉤設計的零件類型. 例如長條彈簧壓條結構就是典型的彈簧壓浮設計﹕1.其結構與普通單邊壓扣類似2.尺寸須保證與零件0.2mm 過盈量易浮高零件定位孔螺絲耐溫塑膠 彈簧工程管理華東地區波峰焊治具設計規範PAGE 15 OF 21REV B6.5.3.3 限位元壓條結構設計適用條件:零件易偏位元﹐且周圍50mm無須壓浮高零件.例如排阻結構易偏位元﹐其本體結構如下:限位壓條設計如下﹕6.5.3.4 治具壓條的材質:電木/FR46.6 治具螺絲標準化.6.6.1固定擋錫條、承載邊採用M3×16的六角螺釘,並且上下鎖緊, 螺帽在上平面固定螺絲;固定牛角的螺絲採用M3×10,且須開槽保證螺絲與治具本體的下表面齊平.6.6.2 M3螺絲的佈置方式參照PCB排版圖.6.6.3壓扣所採用的螺絲按照其工程圖選擇.6.6.4所有的波峰焊治具螺絲均需點螺絲膠,(為便於維修,一般都採用可拆卸試螺勢較)如未點螺絲膠而造成治具易鬆動﹐供應商應無償修復.6.7波峰焊治具局部結構設計要點.6.7.1(1)治具厚度為5mm,PCB承載深度為板厚的3/4.(2)支撐板托臺階寬度至少是1mm以上.針對緊貼板邊DIP件此距離可以考慮再縮小.PCB承載深度=¾*PCB板厚托臺階寬度至少為1mm工程管理華東地區波峰焊治具設計規範PAGE 16 OF 21 REVB6.7.2.(1)治具開設保護SMT 零件槽的擋牆至少為1.0mm.(2)Bottom SMT 螺絲孔已上錫﹐須開1mm 保護槽. (3)保護槽底部厚度至少1mm ﹐以增加治具強度及壽命.6.7.3 DIP 零件開孔標準化. (L 為SMD 零件距PTH 孔PAD 距離,h 為SMD 零件高度) 6.7.3.1.當L ≥3.0mm 、h <0.6mm 時,採用如下圖開孔方式.6.7.3.2當L<3.0mm 時,不利於上錫,則更改設計,可採用45 ∘過爐或增加導錫塊1.045度45度1.01.0~位置范圍極限1.0~1.01.0~5.01.0~1.0fixtureDIPSMDSMDSMDPCB>=1mm>=1mm\工程管理華東地區波峰焊治具設計規範PAGE 18 OF 21 REVB6.7.4開設導錫槽時機.(1)當DIP 零件與SMD 零件距離小於3mm. (2)當DIP 周圍SMD 零件高度小於1.5mm. 其導錫槽開設如下:6.7.5 波峰焊治具開孔大小原則:(1)在空間允許下,DIP 零件至波峰焊治具開孔邊緣保持5mm,脫錫空間.fixture導錫槽 PCB 須開設導錫槽難以開設導錫槽PCBFixture工程管理華東地區波峰焊治具設計規範PAGE 19 OF 21 REVB(2)如果空間有限制,則治具開孔大小最大限度滿足DIP 零件與開孔邊緣5mm 的要求.6.7.6 Bottom 面SMT 零件開槽圖解及要求.6.7.8治具壓條之壓扣須加導10*5*300mm 角便操作員作業.6.7.9治具開設須保護塑膠Pin 條件:(1) PTH 孔與塑膠Pin 距離大於等於3mm ﹐則塑膠Pin 須開槽保護住. (2) PTH 孔與塑膠Pin 距離小於3mm, 則塑膠Pin 無須開槽保護.KLH<3mm>=3mm10*5mm*30°壓合時 壓合後30°位置K L H 范圍(mm)1~1.51~1.50.3~0.5優選(mm)1.51.50.5工程管理華東地區波峰焊治具設計規範PAGE 20 OF 21 REVB6.7.10產品有Flux 污染風險﹐如Bottom 面天線介面,按鍵彈片等Flux 敏感元件,Bottom 須開設防Flux 槽.即在所有插件零件治具開孔的位置周圍開出一道槽, 將治具內外隔開,其設計尺寸為: A(槽的寬度)*B(槽的深度)=2mm*2mm.6.7.11治具結構設計中儘量避免出現以下情況:(1) 沿波峰焊過爐方向﹐出現10mm 以上只有單邊加強肋保護塊.要求:保護塊至少在兩個方向有加強肋.(2) 治具加強肋寬度小於3mm,易產生變形而影響治具強度及壽命. 要求:加強肋寬度至少大於3mm.6.7.12對於 QFN 零件及BGA 等熱敏感SMD 零件,波峰焊治具須保護住其Bottom 面,以防止 出現過波峰焊二次熔錫等不良現象.此保護塊只有單邊受力, 且其長度大於10mm,易造成治具變形而造成溢錫.槽寬2mm 槽深2mmBGAQFN系統名稱SYSTEM:主題SUBJECT: 文件編號DOCUMENT NO.: 工程管理 華東地區波峰焊治具設計規範PAGE 21 OF 21 REV B※ ※ ※ ※ 6.5.13治具須有取板設計以便操作員取板順利,取板設計一般為板邊長方形槽深2.5mm 設計.7. 修訂許可權本規範由製造工程單位ME 工程師撰寫,經製造單位最高主管同意後實施,修改時亦同.保管單位﹕ME 保存期限: 三個月取板設計。
8-3选择性波峰焊

8-3选择性波峰焊选择性波峰焊(⼜称机器⼈焊接)在现代电⼦焊接技术的发展历程中,经历了两次历史性的变⾰:第⼀次是从通孔焊接技术向表⾯贴装焊接技术的转变;第⼆次便是我们正在经历的从有铅焊接技术向⽆铅焊接技术的转变。
焊接技术的演变直接带来了两个结果:⼀是线路板上所需焊接的通孔元器件越来越少;⼆是通孔元器件(尤其是⼤热容量或细间距元器件)的焊接难度越来越⼤,特别是对⽆铅和⾼可靠性要求的产品。
再来看看全球电⼦组装⾏业⽬前所⾯临的新挑战:全球竞争迫使⽣产⼚商必须在更短时间⾥将产品推向市场,以满⾜客户不断变化的要求;产品需求的季节性变化,要求灵活的⽣产制造理念;全球竞争迫使⽣产⼚商在提升品质的前提下降低运⾏成本;⽆铅⽣产已是⼤势所趋。
上述挑战都⾃然地反映在⽣产⽅式和设备的选择上,这也是为什么选择性波峰焊(以下简称选择焊)在近年来⽐其他焊接⽅式发展得都要快的主要原因;当然,⽆铅时代的到来也是推动其发展的另⼀个重要因素。
通孔元器件的焊接主要采⽤⼿⼯焊、波峰焊和选择焊等⼏种焊接技术,它们的特点各不相同,下⾯我们进⾏⼀下简单的介绍:⼿⼯焊接⼿⼯焊接由于具有历史悠久、成本低、灵活性⾼等优势,⾄今仍被⼴泛采⽤。
但是,在可靠性要求⾼、焊接难度⼤的⼀些应⽤中,由于下述原因受到相当的制约:1、烙铁头的温度难以精确控制,这是⼀个最根本的问题。
如果烙铁头温度过低,容易造成焊接温度低于⼯艺窗⼝的下限⽽形成冷焊或虚焊;同时,由于烙铁的热回复性毕竟有限,⾮常容易导致⾦属化通孔内透锡不良。
烙铁头温度过⾼,容易使焊接温度⾼于⼯艺窗⼝上限⽽形成过厚的⾦属间化合物层,从⽽导致焊点变脆、强度下降,并可能导致焊盘脱落使线路板报废;2、焊点质量的好坏往往受到操作者的知识、技能和情绪的影响,很难进⾏控制;3、劳动⼒较机器设备的成本优势正在逐渐丧失。
波峰焊波峰焊设备发明⾄今已有50多年的历史了,在通孔元器件电路板的制造中具有⽣产效率⾼和产量⼤等优点,因此曾经是电⼦产品⾃动化⼤批量⽣产中最主要的焊接设备。
ERSA选择性波峰焊培训2

Page 4
ERSA Versaflow Application Training
General • Path to creating a solder joint =
Rev 2.0 – Mar. 08
Function of a solder joint Electrical and mechanical connection
Rev 2.0 – Mar. 08
Page 2
ERSA Versaflow Application Training
General Process Description
• Different types of PCB’s influence the process
Q = c ·m ·∆T
Q = Heat absorbtion capacity c = Constant for PCB material m = mass ∆T= Ambient to flux activation a aaaatemperature
FR 2
Phenol Resin
FR 4
Epoxy
Single layer boards, does not always require preheating, can get enough heat from nitrogen of solder pot Multi-layer boards, need more accuracy with flux to be able to penetrate into PTH, increased preheat with more layers / copper inside board, higher solder dwell times
波峰焊参数设定标准

波峰焊参数设定标准波峰焊是一种常用的电弧焊接技术,也被称为电渣焊。
它通过产生一系列的电弧波峰来完成焊接过程,具有高效、高质量和高可靠性的特点。
在波峰焊的参数设定中,有几个关键因素需要考虑,包括焊接电流、焊接电压、焊接速度和焊接时间等。
焊接电流是决定焊接过程中熔化金属的主要参数之一。
合适的焊接电流可以保证焊接强度和质量,同时避免出现焊接缺陷。
一般来说,焊接电流应根据焊接材料的种类和厚度来设定。
对于较薄的材料,适宜选择较小的焊接电流,而较厚的材料则需要较大的焊接电流。
焊接电压是控制焊接过程中电弧稳定性的重要参数。
合适的焊接电压可以保证电弧的稳定燃烧,避免产生飞溅和焊接缺陷。
一般来说,焊接电压应根据焊接电流来设定。
当焊接电流较小时,适宜选择较低的焊接电压,而焊接电流较大时则需要较高的焊接电压。
焊接速度是控制焊接过程中熔化金属流动的重要参数。
合适的焊接速度可以保证焊接焊缝的形状和质量,避免产生焊接缺陷。
一般来说,焊接速度应根据焊接材料和厚度来设定。
对于较薄的材料,适宜选择较快的焊接速度,而较厚的材料则需要较慢的焊接速度。
焊接时间是控制焊接过程中熔化金属凝固的重要参数。
合适的焊接时间可以保证焊接焊缝的完整性和质量,避免产生焊接缺陷。
一般来说,焊接时间应根据焊接材料和焊接速度来设定。
对于较薄的材料和较快的焊接速度,适宜选择较短的焊接时间,而较厚的材料和较慢的焊接速度则需要较长的焊接时间。
总结起来,波峰焊的参数设定标准包括焊接电流、焊接电压、焊接速度和焊接时间等。
合理设定这些参数可以保证焊接过程的稳定性和焊接质量,提高焊接效率和生产效益。
在实际操作中,需要根据具体的焊接要求和材料特性来选择合适的参数设定。
同时,还需要通过实验和实践来不断优化和调整参数,以达到最佳的焊接效果。
ersa选择波峰焊培训计划

ersa选择波峰焊培训计划培训目标:1.了解波峰焊的原理和工艺流程;2.掌握波峰焊的操作技巧;3.能够熟练应用波峰焊设备进行实际焊接;4.掌握波峰焊的质量控制方法。
培训内容:1.波峰焊的基本原理1.1 熔化焊接原理1.2 焊接材料和设备1.3 波峰焊工艺参数设置2.波峰焊的操作技巧2.1 设备启动和停止2.2 工件固定和预热2.3 焊接电流和速度控制2.4 焊缝跟踪3.波峰焊设备的维护和维修3.1 日常保养和维护3.2 设备故障排除4.波峰焊实践操作4.1 根据实际工件进行波峰焊实验4.2 对焊接质量进行评估和改进5.波峰焊质量控制5.1 焊接质量标准5.2 质量检测方法5.3 质量控制措施培训方式:1.理论讲解1.1 通过PPT、视频等多媒体教学手段,讲解波峰焊的基本原理、工艺参数设置、操作技巧等内容。
2.操作实践2.1 提供波峰焊设备和工件,让学员进行实际操作练习,熟练掌握波峰焊操作技巧。
3.实例分析3.1 分析波峰焊实际应用中遇到的问题和解决方法,让学员从实际案例中学习经验。
4.质量控制4.1 培训结束时进行质量考核,确保学员掌握了波峰焊的质量控制方法。
培训师资力量:1.具有丰富波峰焊实践经验的专业人士,能够结合实际案例进行讲解和指导;2.具有教学经验和培训能力的专业讲师,能够通过多种教学手段提高学员的学习效果。
培训时间和地点:1.培训时间:为期三天,每天8小时,共计24小时;2.培训地点:ERSA公司内部培训室或者客户指定的场所。
培训效果评估:1.通过培训结束的质量考核,评估学员是否掌握了波峰焊的基本原理、操作技巧和质量控制方法;2.实施跟踪调研,对学员在实际工作中应用波峰焊技术的效果进行评估。
培训后续服务:1.提供波峰焊技术支持和咨询服务,解决学员在实际工作中遇到的问题;2.定期举办波峰焊技术交流会,分享最新的波峰焊技术和案例经验。
通过以上波峰焊培训计划,我们相信可以培养更多的波峰焊专业人才,提升焊接工作者的技术水平和工作质量,为企业的发展壮大提供有力的技术支持。
波峰焊治具设计规范流程

俯視圖HPCB板套板外框可旋轉角度治具組合圖J=17m300mmI=318mm俯視圖D=5mmA: 檔錫牆高度=5±0.2mm B: 軌道邊寬度=9±0.2mm C:治具厚度=5±0.2mm4503506.1.6錫槽高度校正波峰焊治具最大特點在於承載邊底部到治具底部距離H及量產波峰焊治具多3mm, 通過此治具可以調試錫槽高度,保證試產及量產波峰焊治具與錫槽至少3mm間隙. (具體使用方法參見波峰焊操作規範)6.1.6.1 治具材質:合成石+ 45鋼+不銹鋼6.1.6.2 治具結構及具體尺寸如下圖所示3H(單位:mm)0.8mm,並且設計淚滴PAD,則PCB放置于波峰焊與波峰焊過錫爐方向相同.如下圖:A<0.8mm 過錫爐方向A<0.8mm過錫爐方向6.2.1.2 多Pin腳Connector Ring與Ring 之間距離小於過錫爐方向A<1mmB<1mm過錫爐方向A<0.6mm圖A 圖B 6.4.2普通單邊壓扣,和普通雙邊壓扣工程尺寸圖.壓條設計標準化6.5.1 壓條製作時機: 由波峰焊試產組統計試產過程中易浮高偏位元零件位置及浮高不良率﹐並最終確定開設壓條.6.4.2 壓條壓扣設計原則: (1) 壓條設計功能滿足要求.(2) 壓條材質須滿足防靜電要求,及耐高溫性.(2)壓浮高零件在2個以上﹐則採用整體式壓條設計須製作壓條PCBA板上零件結構如下:壓條結構設計根據零件結構設計成長條式﹐其結構如下圖所示定位孔壓條與零件壓浮配合為過盈配合﹐其過盈量為0.2mm.6.5.3.2 特殊壓條結構設計----彈簧壓浮設計.適用條件:零件極易浮高﹐且與PCB板無卡鉤設計的零件類型例如長條彈簧壓條結構就是典型的彈簧壓浮設計﹕螺絲彈簧耐溫塑膠例如排阻結構易偏位元﹐其本體結構如下限位壓條設計如下﹕6.5.3.4 治具壓條的材質:電木/FR4治具螺絲標準化.6.6.1固定擋錫條、承載邊採用M3×16的六角螺釘定牛角的螺絲採用M3×10,且須開槽保證螺絲與治具本體的下表面齊平PCB承載深度托臺階寬度至少為1mmfixture DIPSMD SMD SMDPCB>=1mm\6.7.3 DIP零件開孔標準化. (L為SMD零件距PTH孔PAD距離,h為PCB須開設導錫槽難以開設導錫槽PCBfixture導錫槽6.7.5 波峰焊治具開孔大小原則:(1)在空間允許下,DIP零件至波峰焊治具開孔邊緣保持5mm,FixtureKLH6.7.8治具壓條之壓扣須加導10*5*300mm10*5mm*30°30°壓合時壓合後6.7.9治具開設須保護塑膠Pin條件:>=3mm<3mm6.7.11治具結構設計中儘量避免出現以下情況(1)沿波峰焊過爐方向﹐出現要求:保護塊至少在兩個方向有加強肋(2) 治具加強肋寬度小於3mm,易產生變形而影響治具強度及壽命要求:加強肋寬度至少大於3mm.6.7.12對於QFN 零件及BGA等熱敏感出現過波峰焊二次熔錫等不良現象.BGA QFN修訂許可權本規範由製造工程單位ME工程師撰寫,經製造單位最高主管同意後實施,修改時亦同保管單位﹕ME。
波峰焊制程规范

波峰焊制程规范1.生产前设备机器的设置:1.1.调整传送PCBA的轨道宽度,保证波峰焊链爪在运送PCBA时安全并不至于导致PCBA板或托盘弯曲1.2.检查阻焊剂是否足够,不足则添加足够的助焊剂1.3.检查锡槽锡量是否足够,不足则添加适量的锡棒1.4.技术人员参照《波峰焊参数设定表》调整波峰焊参数,同时要有足够的时间使预热及锡槽温度达到参数设定值1.5.有特殊要求的产品和客户指定的作业,需要根据对应的SAP进行作业2.生产程序:2.1.完成生产前设备设置后才可以开始生产,具体流程为:基板载入基板感应延时触发喷助焊剂结束喷助焊剂预热加热波峰焊接冷却基板流出2.2.更具SIP要求是否使用产品对应的波峰焊托盘装载PCBA过波峰焊,波峰焊托盘治具有生产到工装室领取2.3.生产当线组长待技术员将波峰焊参数调整好后,确认没有问题后,开始试过1PCS产品,确认焊锡性是否良好,如有问题反映给当线工程师调机处理,如无问题,则可正常开线。
2.4.正常生产后,技术人员应随时观察产品焊接品质,并且需要观察辅料是否需要添加。
2.5.波峰焊预热温度界限应该设定为设定温度±10℃,当预热温度超出设定值界限时,设备要能报警提示,应立即通知工程师查看是否有设备异常,出现设备异常则需要停线处理,带处理完成后,重新测温,温度达到制程要求后方可继续生产。
2.6.波峰焊锡槽温度界限应该控制在设定温度±5℃,当锡槽温度超出设定值界限时,设备要能报警提示,应立即通知工程师查看是否有设备异常,出现设备异常则需要停线处理,带处理完成后,重新测温,温度达到制程要求后方可继续生产。
2.7.有特殊要求的产品或客户指定的作业,需要根据对应的SOP进行操作。
3.锡成分检验3.1.对于锡槽中锡合金成分,每隔半年从锡槽中取样检测一次,其中合金锡成分比例控制在60%~65%,合金铅成分比例控制在35%~40%之间。
3.2.由于波峰焊长期的使用,锡槽内的锡中各种金属杂质会越来越多,故:对各条波峰焊线锡槽内的锡样成分,每隔半年取样送相关部门进行成分分析测试,各杂质金属含量需要控制在如下范围之内:3.3主要合金比例或杂质合金比例超过控制范围,则要立即停线通知相关技术部门处理。
波峰焊操作规范

波峰焊操作规范一、通电前的准备1.检查电气线路是否老化破损,检查供电电源3相380v是否正常。
2.检查各传动、调整机构是否正常,将本批次焊件的试样基板上爪调准运输件的宽度。
3.添加松香水至箱体2/3位置;排气管、接驳气嘴应无泄露,将气压调至5bar(此时启动配套的空压机送风)。
4.添加酒精至洗爪箱4/5位置,将流量调到适量的位置(流量不得过大,以免酒精溅出起火)。
5.将锅炉调至适当高度5mm—10mm(端口两边应与爪的高度一致)。
二、通电调整、运转1.检查急停按钮是否按下,打开电源开关。
2.将锅炉温度定在250℃,锡炉报警温度定在高于锅炉温度10℃, 待充分熔锡后,达250℃到才能进行其它功能操作(约1小时)。
3.开启预热键,设定预热温度:a.酚醛板80℃—100℃b.环氧板100℃—120℃。
以试样基板上锡状况取值,设定预热报警温度为高于预热温度10℃。
4.开启运输键,调整速度到1.2米/分钟(约在20至30之间具体情况及时修正)。
5.查看锡容量(距炉面10mm)及时加条状锡料;启动波峰, 以试样基板为参照,调整焊锡角度和波峰高度,使锡波在基板厚度的1/2~2/3。
6.按下“喷雾”键,调节流量,调节气压,调整横移速度,使喷雾至最佳状态。
7.设定波峰1手动,波峰2自动。
按下“波峰2”键和“冷却”键。
8.完成上述步骤后,方可送板件入波峰焊导轨。
送入波峰焊导轨时把乱了的元件稍稍整理下。
9.根据送板件的焊点质量情况,调整参数。
直至送板件的焊点质量合格,方可进行生产。
发现异常应立即停机报修。
三、停机关断电源(若选用自动控制,则不能直接关掉电源。
需清除锡渣,清洗爪键后才能关断电源)。
波峰焊常见焊接质量问题及解决方法。
波峰焊操作规程

波峰焊操作规程一、引言波峰焊是一种常见的电子产品焊接方式,它通过将插件的引脚浸入熔化的焊锡中,实现焊接与固定。
为了保证焊接质量的稳定性和一致性,有必要制定一套详尽的波峰焊操作规程。
本文将介绍波峰焊操作规程的主要内容及步骤。
二、设备准备1. 检查设备在开始波峰焊操作之前,需要检查设备的工作状态。
确保焊接机、热风机和冷却装置等设备运行正常。
2. 准备焊锡及助焊剂选择合适的焊锡丝以及助焊剂,并保证其质量符合相关标准。
焊锡丝的直径、成分和熔点应根据焊接任务而确定。
三、钢网准备1. 检查钢网确保钢网的孔径、厚度和平整度符合要求。
检查钢网是否有损坏或变形,并及时更换。
2. 调整钢网高度根据焊接任务需求,调整钢网的高度。
确保钢网与插件引脚之间的距离符合要求,通常为2-3mm。
四、波峰焊操作步骤1. 设定焊接程序根据焊接任务的要求,在焊接机上设定相应的焊接程序。
确定焊接温度、波峰高度、预热时间等参数。
2. 开始预热启动焊接机,让其进行预热。
预热时间通常为5-10分钟,待设定温度达到后方可进行下一步操作。
3. 调整波峰高度根据焊接任务的要求,调整波峰高度。
通常情况下,波峰高度应略高于插件引脚的高度。
4. 准备插件将焊锡丝和助焊剂涂抹在插件的焊盘上,确保焊点涂覆均匀。
5. 插件定位将准备好的插件放置在钢网上,并调整位置,使其与焊点对齐。
6. 开始焊接将钢网缓慢地下移,插件的引脚将被浸入焊锡中。
要保持匀速下移,以确保焊接质量的稳定性。
7. 波峰焊完成当焊点完全浸入焊锡中后,继续下移一段距离,以确保焊点形成一定的柱状形态。
待上升时,焊点会被波峰除锡剂清除。
8. 冷却焊接完成后,打开冷却装置,将焊点快速冷却。
冷却时间通常为2-3分钟。
五、注意事项1. 运行时的注意事项在进行波峰焊操作时,操作人员应站立在稳定的位置上,并戴上相应的防护设备,如防静电手套、护目镜等。
2. 设备维护定期对波峰焊设备进行维护和保养,保持其正常工作状态,清理焊接头、钢网和焊炉等部件。
ERSA选择性波峰焊LAYOUT规范
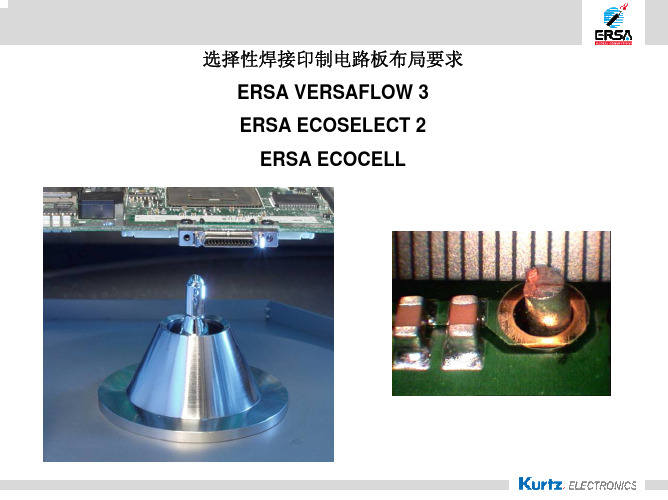
Seite 18
零件布局建议 VERSAFLOW 3
焊接面的零件高度及喷嘴与边缘的距离需求
传输系统(滚轮)
X Y
不适用于 ECOSELECT 2 + ECOCELL
*
焊接面零件的最大高度X为30mm*
焊接喷嘴以外的零件高度是受距离的限制的,请参考第20页的尺寸描述 从滚轮边缘到喷嘴中心的最小距离取决于所选择的喷嘴外直径 Y = 喷嘴外直径/2 + 1 mm * 如有更高的零件请咨询ERSA
Seite 15
焊接过程对零件布局的要求 VERSAFLOW 3 / ECOSELECT 2 / ECOCELL 单排或多排焊点到印制电路板边的最小距离
B 焊点 焊接区域 非焊接限制区域
非焊接限制区域与印制电路板边缘的最小距离B 为4 mm 最小的限制区域请参考第14~15页的描述 焊点可不在焊接区域的中心位置,但以中心为 最佳。
Seite 22
载具/夹具设计要求 VERSAFLOW 3 / ECOSELECT 2 / ECOCELL
当使用载具或夹具的时候,需要确保轨道传输平面A与印制电路板底面B处于同一高度 。如有其它特殊情况时也要以这个要求为原则,与其基本保持一致。
传输平面 A = 印制电路板底面B 加工精度 +/- 0,05 mm
载具/夹具
© by ERSA GmbH • VF_LAYOUT_DT_V401_200dpi.ppt • AT/jfr.01.2011
© by ERSA GmbH • VF_LAYOUT_DT_V401_200dpi.ppt • AT/jfr.01.2011
Seite 3
轨道传输系统对产品的要求 VERSAFLOW 3 传输系统截面图
LAYOUT规范(电气、安规EMC)

山特电子(深圳)有限公司
附图: TRACE宽度与电流承载量的关系图
1-3K机型FLY-BACK电路LAYOUT示范
①功率电流路径原则:初级:BulkCap→变压器→功率开关→ BulkCap / 次
级:变压器→整流二极管→输出电容→变压器两极回路应粗短化;输入输出电容直接于此两路径。
感的路经)
用于保护开关管的Clamp&SnubberRCD电
路紧靠开关。
而且其与开
关管构成的回路面积须最小,路径须粗短
1-3K机型PFC电路LAYOUT示范
①功率电流路径原则:输入→Boost电感→整流桥→功率开关→电流感
应器→整流桥→输入地/ Boost电感→整流二极管→BUS电容→输入两路经应粗短化;BUS电容直接接于输出路径上。
ersa selective soldering

ersa selective soldering标题:ERSA Selective Soldering:深度解析与应用指南一、引言ERSA selective soldering,即ERSA选择性焊接技术,是一种先进的电子制造工艺,主要用于复杂电路板的精细焊接。
本文将详细解析ERSA选择性焊接的原理、设备、工艺流程、优势及其在电子制造业中的应用。
二、ERSA选择性焊接原理ERSA选择性焊接是一种精确的焊接方法,主要通过精确控制焊锡的施加位置和量,只对需要焊接的部位进行焊接,避免对不需要焊接或者敏感部件造成影响。
其工作原理主要包括以下步骤:1. 预热:首先,电路板经过预热区,使得电路板和元器件达到合适的焊接温度,减少热冲击并提高焊接质量。
2. 焊接定位:然后,通过视觉系统或机械定位系统,精确地将电路板定位到焊接头下方。
3. 焊接:焊接头在精确的位置上施加适量的焊锡,只对需要焊接的部位进行焊接。
4. 冷却:焊接完成后,电路板进入冷却区,快速冷却以稳定焊接效果并防止元器件因温度变化而受损。
三、ERSA选择性焊接设备ERSA公司的选择性焊接设备主要包括以下几个部分:1. 运输系统:用于承载和输送电路板。
2. 预热系统:包括红外线或热风预热,用于加热电路板和元器件。
3. 定位系统:包括视觉系统和机械定位系统,用于精确地定位电路板。
4. 焊接系统:包括焊锡喷嘴和焊锡供应系统,用于施加焊锡。
5. 冷却系统:用于快速冷却电路板。
6. 控制系统:包括软件和硬件,用于控制整个焊接过程。
四、ERSA选择性焊接工艺流程以下是ERSA选择性焊接的一般工艺流程:1. 电路板装载:将待焊接的电路板放入运输系统。
2. 预热:电路板通过预热区,达到合适的焊接温度。
3. 定位:通过视觉或机械定位系统,精确地将电路板定位到焊接头下方。
4. 焊接:焊接头在精确的位置上施加适量的焊锡,只对需要焊接的部位进行焊接。
5. 冷却:焊接完成后,电路板进入冷却区,快速冷却。
ERSA多喷嘴选择性焊接培训资料

ERSA VERSAFLOW 3选择性波峰焊培训资料焊接类型介绍浸焊波峰焊选择焊选择焊工作原理系统Versaflow 3 的焊接流程一般包括以下几个步骤:进板→选择位置喷助焊剂→停下预热→选择位置焊接→出板 整个系统是一个闭环的处理系統。
Infeed Outfeed 闭环处理控制 工作过程 设备功能设备操作设备保养设备维护喷雾系统◎喷雾模块的工作原理:基板在喷雾区定位以后,喷头在程序的控制下开始工作。
助焊剂的喷雾是靠压缩气的压力將其由喷嘴射出,并每间隔一段時间后,机器自动对喷头位置的准确性进行检测。
助焊剂喷嘴 助焊剂压力罐工作过程 设备功能 设备操作设备保养设备维护喷雾系统◎助焊剂检测控制: 自动感测助焊剂喷头喷雾的位置。
◎喷雾头的结构:工作原理----喷头在不工作时,內部的电磁阀会处于关闭的状,这时液体被堵住;开始工作以后,电磁阀得到打开的脉冲号下,电磁阀打开,在气压的作用下,助焊剂由喷嘴射出,因为喷嘴的孔径在: 100μm ~ 130μm之间,助焊剂在高压之下经由喷嘴后形成雾状。
工作过程设备功能设备操作设备保养设备维护喷雾系统◎喷雾量的测试:下图是在PCB 上贴张热敏纸,编写点喷测试程序,执行喷雾动作后,将会在紙上留下如下的图案,显示出每小滴的痕跡。
工作过程 设备功能 设备操作设备保养设备维护预热系统预热区工作原理: 基板在助焊剂喷雾区被喷过助焊剂后,將到达预热区加热使助焊剂活化。
热源是IR 加热管,同时,客戶可以根据需要加裝顶部热风回流加热模块。
在底部加热模块的上方和里边各裝一个温度感应器,对基板加热时间的温度进行监测及超温保护.底部红外线加热模块 顶部热风回流加热模块 工作过程设备功能 设备操作 设备保养 设备维护焊接系统◎single nozzle 锡炉焊接区:基板由预热区进入焊接区后,机器对基板进行定位便开始焊接。
在焊接完几块基板或间隔一定的时间后,机器自动对焊锡波的高度进行测试并根据测試結果自动调整。
波峰焊接工艺对PCB布局组见设计要求

焊盘和孔的同心度
• 在单面PCB中,焊盘和孔不同心几乎能 100%造成孔穴,气孔或者焊点吃锡不均匀 等缺陷.(我们公司的TP9206表现的极为明 显).如下图所示.
工艺设备科2008
Jiangsu Toppower Automotive Electronics Co., Ltd.
江苏天宝汽车电子有限公司
焊接面贴片的排列
波峰焊接中有一种能够导致虚焊的重要原 因,叫做阴影效应,所谓阴影效应,简单的讲 就是器件在传送方向上挡住了焊盘. 在一定程度上波峰焊设备通过开启乱波能 够适当解决这种效应的产生,但最根本的是 从元件布局上面解决这问题.
工艺设备科2008
Jiangsu Toppower Automotive Electronics Co., Ltd.
工艺设备科2008
Jiangsu Toppower Automotive Electronics Co., Ltd.
江苏天宝汽车电子有限公司
上两图分别为CD1019A和C D1023R在波峰焊接后机芯插 座的焊接效果,箭头为焊接方向.
工艺设备科2008
Jiangsu Toppower Automotive Electronics Co., Ltd.
江苏天宝汽车电子有限公司
难题
• 对于USB线束插座(CD1037 CD1038 CD1039等机 型),焊接时出现桥接的几率近100%. • 因为各管脚功能定义不一样,对于某些不用的管脚, 可以采取去除无用管脚焊盘的方式减少焊点的密 集度来降低桥接几率. • 但是有的机型的此插座的每一个管脚都有其必要 的作用.
•
•
•
工艺设备科2008
Jiangsu Toppower Automotive Electronics Co., Ltd.
波峰焊治具设计规范

工程管理華東地區波峰焊治具設計規範PAGE4 OF 21 REV B6. 作業流程與內容6.1波峰焊治具分類6.1.1試產波峰焊治具分類為: (1)一般試產波峰焊治具 (2)特殊試產波峰焊治具 6.1.2 一般試產波峰焊治具材質:FR4或電木.治具尺寸:如下圖所示(1).治具結構﹕底框架+托邊框架. (2).治具四周需要加軌道邊.(3).S0階段(sample run)治具不需要製作壓條,S0後之試產時需要都I/O 零件 製作壓條.A:承載邊厚度=2.6±0.1mm B:檔錫牆高度=4±0.2mm C:治具厚度=4±0.2mmD:PCB 承載邊深度=PCB 厚度*3/4 側視圖俯視圖FGHHGAB C D E工程管理華東地區波峰焊治具設計規範PAGE 5 OF 21REV B E:軌道邊寬度=9±0.2mmF:PCB板與板之間距離=15±0.2mmG:PCB與治具檔錫牆之間距離=15±0.2mmH:治具檔牆寬度+治具承載邊寬度=7+10=17±0.2mm6.1.3 特殊試產波峰焊(可旋轉角度)主要應用於驗證特殊,異形零件,Pin腳Pitch較小零件,或新性零件沒有把握控制wave solder 良率時, 在試產階段確認產品過爐最佳角度. 確認量產治具的開設.(1).治具結構﹕底框架+托邊框架.(2).治具四周需要加軌道邊.(3).S0階段(sample run 治具不需要製作壓扣,S0後之試產時需要都I/O 零件製作壓扣.(4).外框材質:合成石;套板材質: FR4或電木.可旋轉角度治具組合圖外框套板PCB板刻度工程管理 華東地區波峰焊治具設計規範PAGE6 OF 21 REV BA:承載邊厚度=2.6±0.1mm B.檔錫牆高度=5±0.2mm C:檔錫牆高度=5±0.2mm D:治具厚度=5±0.2mm E:套板支撐臺階=5±0.2mm F:軌道邊寬度-9±0.2mm G: 檔錫牆寬度=7±0.2mmH:套板支撐臺階厚度=2.5±0.2mmI:治具長寬尺寸=318mm. J:尺寸=17mm.300mm I=318mm 300mm 318mmJ=17m俯視圖266mm 側視圖D=5mmG=2.5mmC=5mm E=9mmF=7mmB=8mmA=3mm工程管理華東地區波峰焊治具設計規範PAGE 7 OF 21REV B 6.1.4量產波峰焊治具結構與尺寸定義:6.1.4.1量產波峰焊治具材質:6.1.4.1.1底板、搭載邊條選用合成石.6.1.4.1.2 方向邊框可選用合成石/FR4.6.1.4.2量產波峰焊治具尺寸:如下圖所示治具結構:底框架+托邊框架A: 檔錫牆高度=5±0.2mmB: 軌道邊寬度=9±0.2mmC:治具厚度=5±0.2mmD: PCB與治具檔錫牆之間距離=20±0.2mmE:治具牛角擋錫牆固定於治具的寬度E1為7±0.2mm,E2為12±0.2mmF:擋錫牆到牛角之間距離30±0.2mmG:牛角導圓角半徑R=10±0.2mmH:PCB板與PCB板放置間距15±0.2mmI:PCB板到擋錫牆之間的距離15±0.2mmJ:治具檔牆寬度+治具承載邊寬度=7+9=16±0.2mmK:牛角墊塊長度20±0.2mmL:牛角墊塊寬度20±0.2mmM:牛角墊塊厚度5±0.2mmN:PCB放板導角直徑3±0.2mmO:治具邊框寬度:10±0.2mmP:軌道承載邊厚度3±0.2mmQ:牛角內長15±0.2mmR:牛角內寬15±0.2mm注:圖中橢圓形為5*2.5 mm導圓角,如右圖所示.工程管理華東地區波峰焊治具設計規範PAGE8 OF 21 REV B6.1.5錫波平整度波峰焊治具主要應用于測量錫波峰平整度﹐以檢驗錫槽是否有異常. 6.1.5.1治具材質: 合成石+玻璃6.1.5.2 治具具體尺寸與普通試產波峰焊治具尺寸定義相同. 6.1.5.3 治具結構:底框架+托邊框架+耐溫刻度玻璃.(單位:mm)6.1.6錫槽高度校正波峰焊治具最大特點在於承載邊底部到治具底部距離H 為13mm, 比試產及量產波峰焊治具多3mm, 通過此治具可以調試錫槽高度,保證試產及量產波峰焊治具與錫槽至少3mm 間隙. (具體使用方法參見波峰焊操作規範) 6.1.6.1 治具材質:合成石+ 45鋼+不銹鋼 6.1.6.2 治具結構及具體尺寸如下圖所示.(單位:mm) 6.2 波峰焊治具排版所有波峰焊治具排版遵循應遵循以下原則: 6.2.1 PCB 放置于波峰焊治具方向判定依據: 6.2.1.1 淚滴PAD 及盜錫塊考慮:當PCB 中有Ring 與Ring 之間距離小於0.8mm,並且設計淚滴PAD,則PCB 放置于波峰焊治具時﹐須保證淚滴PAD 與波峰焊過錫爐方向相同.如下圖:450 350 H3工程管理華東地區波峰焊治具設計規範PAGE9 OF 21 REV B過錫爐方向 A<0.8mma. Connector ,CBL(排線)過錫爐方向 b. two row pin connector:A<0.8mm過錫爐方向 A<0.8mm c. RJ45,RJ11過錫爐方向d. Connector工程管理華東地區波峰焊治具設計規範PAGE 10 OF 21 REVB當PCB 中有Ring 與 Ring 之間距離小於0.6mm,並且設計盜錫塊,則PCB 放置于波峰焊治具時﹐須保證盜錫塊最後與錫波接觸.如下圖:6.2.1.2 多Pin 腳Connector Ring 與Ring 之間距離小於1mm,則過錫爐方向須特別定義.如下圖:6.2.1.3 當PCB Layout 中都無以上過波峰焊方向限制,則考慮將Connector 零件放置於治具前端﹐以便於插件.過錫爐方向A<1mmB<1mm 過錫爐方向A<0.6mmConnector 前置與波峰焊方向一致工程管理華東地區波峰焊治具設計規範PAGE 12 OF 21REV B 6.3.3 治具的環保標示要求:為滿足不同客戶稽核要求,治具上所標識的“GP RoHS LF”均表示為環保產品治具.環保標識適用於無鉛機種,有鉛機種只需刻上廠內編碼.6.3.4 治具編碼申請管理:治具製作前需向鋼板治具系統管理員申請編號,製作後由管理員錄入系統,並且治具管理員根據廠內編碼追蹤治具製作進度.6.4 治具壓扣設計標準.6.4.1壓扣分類:普通單邊壓扣(圖A),普通雙邊壓扣(圖B),材質均為賽鋼.圖A 圖B6.4.2普通單邊壓扣,和普通雙邊壓扣工程尺寸圖.普通單邊壓扣工程圖普通雙邊壓扣工程圖工程管理華東地區波峰焊治具設計規範PAGE 13 OF 21REV B 6.4.3 波峰焊壓扣佈局原則:(1)壓扣一般分佈在PCB板四個角,並保證壓扣壓住PCB板邊至少3±0.5mm.(2)所有壓扣放置位置須保證其周圍3mm內無SMD零件.(3)在空間允許情況下, PCB板與PCB板連接處,採用普通雙邊壓扣設計以節省工時.6.5 壓條設計標準化6.5.1 壓條製作時機: 由波峰焊試產組統計試產過程中易浮高偏位元零件位置及浮高不良率﹐並最終確定開設壓條.6.4.2 壓條壓扣設計原則: (1) 壓條設計功能滿足要求.(2) 壓條材質須滿足防靜電要求,及耐高溫性.(3) 壓條放置方向須有防呆及定位設計.(4) 壓條放置動作最簡化性.6.5.3 現有壓條結構設計類型:6.5.3.1普通壓浮壓條結構設計(1)壓浮零件在2個以內﹐採用類壓扣設計.須壓浮高PCBA如下圖工程管理華東地區波峰焊治具設計規範PAGE 14 OF 21 REVB壓條採用類壓扣設計如下圖所示:(2) 壓浮高零件在2個以上﹐則採用整體式壓條設計. 須製作壓條PCBA 板上零件結構如下:壓條結構設計根據零件結構設計成長條式﹐其結構如下圖所示:壓條與零件壓浮配合為過盈配合﹐其過盈量為0.2mm. 6.5.3.2 特殊壓條結構設計----彈簧壓浮設計.適用條件:零件極易浮高﹐且與PCB 板無卡鉤設計的零件類型. 例如長條彈簧壓條結構就是典型的彈簧壓浮設計﹕1.其結構與普通單邊壓扣類似2.尺寸須保證與零件0.2mm 過盈量易浮高零件定位孔螺絲耐溫塑膠 彈簧工程管理華東地區波峰焊治具設計規範PAGE 15 OF 21REV B6.5.3.3 限位元壓條結構設計適用條件:零件易偏位元﹐且周圍50mm無須壓浮高零件.例如排阻結構易偏位元﹐其本體結構如下:限位壓條設計如下﹕6.5.3.4 治具壓條的材質:電木/FR46.6 治具螺絲標準化.6.6.1固定擋錫條、承載邊採用M3×16的六角螺釘,並且上下鎖緊, 螺帽在上平面固定螺絲;固定牛角的螺絲採用M3×10,且須開槽保證螺絲與治具本體的下表面齊平.6.6.2 M3螺絲的佈置方式參照PCB排版圖.6.6.3壓扣所採用的螺絲按照其工程圖選擇.6.6.4所有的波峰焊治具螺絲均需點螺絲膠,(為便於維修,一般都採用可拆卸試螺勢較)如未點螺絲膠而造成治具易鬆動﹐供應商應無償修復.6.7波峰焊治具局部結構設計要點.6.7.1(1)治具厚度為5mm,PCB承載深度為板厚的3/4.(2)支撐板托臺階寬度至少是1mm以上.針對緊貼板邊DIP件此距離可以考慮再縮小.PCB承載深度=¾*PCB板厚托臺階寬度至少為1mm工程管理華東地區波峰焊治具設計規範PAGE 16 OF 21 REVB6.7.2.(1)治具開設保護SMT 零件槽的擋牆至少為1.0mm.(2)Bottom SMT 螺絲孔已上錫﹐須開1mm 保護槽. (3)保護槽底部厚度至少1mm ﹐以增加治具強度及壽命.6.7.3 DIP 零件開孔標準化. (L 為SMD 零件距PTH 孔PAD 距離,h 為SMD 零件高度) 6.7.3.1.當L ≥3.0mm 、h <0.6mm 時,採用如下圖開孔方式.6.7.3.2當L<3.0mm 時,不利於上錫,則更改設計,可採用45 ∘過爐或增加導錫塊1.045度45度1.01.0~位置范圍極限1.0~1.01.0~5.01.0~1.0fixtureDIPSMDSMDSMDPCB>=1mm>=1mm\工程管理華東地區波峰焊治具設計規範PAGE 18 OF 21 REVB6.7.4開設導錫槽時機.(1)當DIP 零件與SMD 零件距離小於3mm. (2)當DIP 周圍SMD 零件高度小於1.5mm. 其導錫槽開設如下:6.7.5 波峰焊治具開孔大小原則:(1)在空間允許下,DIP 零件至波峰焊治具開孔邊緣保持5mm,脫錫空間.fixture導錫槽 PCB 須開設導錫槽難以開設導錫槽PCBFixture工程管理華東地區波峰焊治具設計規範PAGE 19 OF 21 REVB(2)如果空間有限制,則治具開孔大小最大限度滿足DIP 零件與開孔邊緣5mm 的要求.6.7.6 Bottom 面SMT 零件開槽圖解及要求.6.7.8治具壓條之壓扣須加導10*5*300mm 角便操作員作業.6.7.9治具開設須保護塑膠Pin 條件:(1) PTH 孔與塑膠Pin 距離大於等於3mm ﹐則塑膠Pin 須開槽保護住. (2) PTH 孔與塑膠Pin 距離小於3mm, 則塑膠Pin 無須開槽保護.KLH<3mm>=3mm10*5mm*30°壓合時 壓合後30°位置K L H 范圍(mm)1~1.51~1.50.3~0.5優選(mm)1.51.50.5工程管理華東地區波峰焊治具設計規範PAGE 20 OF 21 REVB6.7.10產品有Flux 污染風險﹐如Bottom 面天線介面,按鍵彈片等Flux 敏感元件,Bottom 須開設防Flux 槽.即在所有插件零件治具開孔的位置周圍開出一道槽, 將治具內外隔開,其設計尺寸為: A(槽的寬度)*B(槽的深度)=2mm*2mm.6.7.11治具結構設計中儘量避免出現以下情況:(1) 沿波峰焊過爐方向﹐出現10mm 以上只有單邊加強肋保護塊.要求:保護塊至少在兩個方向有加強肋.(2) 治具加強肋寬度小於3mm,易產生變形而影響治具強度及壽命. 要求:加強肋寬度至少大於3mm.6.7.12對於 QFN 零件及BGA 等熱敏感SMD 零件,波峰焊治具須保護住其Bottom 面,以防止 出現過波峰焊二次熔錫等不良現象.此保護塊只有單邊受力, 且其長度大於10mm,易造成治具變形而造成溢錫.槽寬2mm 槽深2mmBGAQFN系統名稱SYSTEM:主題SUBJECT: 文件編號DOCUMENT NO.: 工程管理 華東地區波峰焊治具設計規範PAGE 21 OF 21 REV B※ ※ ※ ※ 6.5.13治具須有取板設計以便操作員取板順利,取板設計一般為板邊長方形槽深2.5mm 設計.7. 修訂許可權本規範由製造工程單位ME 工程師撰寫,經製造單位最高主管同意後實施,修改時亦同.保管單位﹕ME 保存期限: 三個月取板設計。
选择性波峰焊工艺研究要点
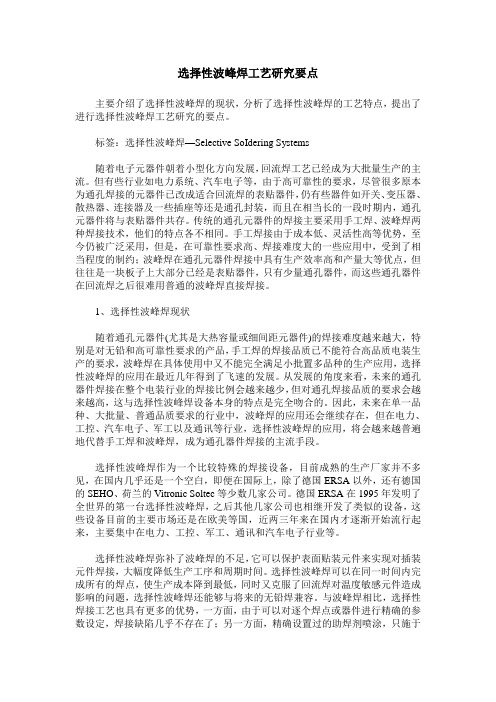
选择性波峰焊工艺研究要点主要介绍了选择性波峰焊的现状,分析了选择性波峰焊的工艺特点,提出了进行选择性波峰焊工艺研究的要点。
标签:选择性波峰焊—Selective SoIdering Systems随着电子元器件朝着小型化方向发展,回流焊工艺已经成为大批量生产的主流。
但有些行业如电力系统、汽车电子等,由于高可靠性的要求,尽管很多原本为通孔焊接的元器件已改成适合回流焊的表贴器件,仍有些器件如开关、变压器、散热器、连接器及一些插座等还是通孔封装,而且在相当长的一段时期内,通孔元器件将与表贴器件共存。
传统的通孔元器件的焊接主要采用手工焊、波峰焊两种焊接技术,他们的特点各不相同。
手工焊接由于成本低、灵活性高等优势,至今仍被广泛采用,但是,在可靠性要求高、焊接难度大的一些应用中,受到了相当程度的制约;波峰焊在通孔元器件焊接中具有生产效率高和产量大等优点,但往往是一块板子上大部分已经是表贴器件,只有少量通孔器件,而这些通孔器件在回流焊之后很难用普通的波峰焊直接焊接。
1、选择性波峰焊现状随着通孔元器件(尤其是大热容量或细间距元器件)的焊接难度越来越大,特别是对无铅和高可靠性要求的产品,手工焊的焊接品质已不能符合高品质电装生产的要求,波峰焊在具体使用中又不能完全满足小批置多品种的生产应用,选择性波峰焊的应用在最近几年得到了飞速的发展。
从发展的角度来看,未来的通孔器件焊接在整个电装行业的焊接比例会越来越少,但对通孔焊接品质的要求会越来越高,这与选择性波峰焊设备本身的特点是完全吻合的。
因此,未来在单一品种、大批量、普通品质要求的行业中,波峰焊的应用还会继续存在,但在电力、工控、汽车电子、军工以及通讯等行业,选择性波峰焊的应用,将会越来越普遍地代替手工焊和波峰焊,成为通孔器件焊接的主流手段。
选择性波峰焊作为一个比较特殊的焊接设备,目前成熟的生产厂家并不多见,在国内几乎还是一个空白,即便在国际上,除了德国ERSA以外,还有德国的SEHO、荷兰的Vitronic Soltec等少数几家公司。
- 1、下载文档前请自行甄别文档内容的完整性,平台不提供额外的编辑、内容补充、找答案等附加服务。
- 2、"仅部分预览"的文档,不可在线预览部分如存在完整性等问题,可反馈申请退款(可完整预览的文档不适用该条件!)。
- 3、如文档侵犯您的权益,请联系客服反馈,我们会尽快为您处理(人工客服工作时间:9:00-18:30)。
© by ERSA GmbH • VF_LAYOUT_DT_V401_200dpi.ppt • AT/jfr.01.2011
Seite 18
零件布局建议 VERSAFLOW 3
焊接面的零件高度及喷嘴与边缘的距离需求
传输系统(滚轮)
X *
不适用于
ECOSELECT 2 +
Y
ECOCELL
焊接面零件的最大高度X为30mm*
Seite 5
轨道传输系统对产品的要求 VERSAFLOW 3 / ECOSELECT 2 / ECOCELL 焊接面零件的最大高度及零件本体与边缘的距离
最大零件高度 30 mm
详细数据参考19-22 页
© by ERSA GmbH • VF_LAYOUT_DT_V401_200dpi.ppt • AT/jfr.01.2011
Seite 16
焊接过程对零件布局的要求 VERSAFLOW 3 / ECOSELECT 2 / ECOCELL 可用的圆形喷嘴
如下尺寸都是常用的喷嘴尺寸* 外径 6, 8, 10, 12, 14, 20mm, + 特殊订做
喷嘴的尺寸默认以2mm为增量制作,但可以根据实际需求订做在上述尺寸范围内 的喷嘴 如有更小的尺寸需要,请联系ERSA
如有更小的空间请向ERSA咨询
© by ERSA GmbH • VF_LAYOUT_DT_V401_200dpi.ppt • AT/jfr.01.2011
非焊接限制区域与印制电路板边缘的最小距离B 为4 mm 最小的限制区域请参考第14~15页的描述 焊点可不在焊接区域的中心位置,但以中心为 最佳。
1. 单点焊接 2. 拖焊
* 如有需求可提供更小的Nozzle.
© by ERSA GmbH • VF_LAYOUT_DT_V401_200dpi.ppt • AT/jfr.01.2011
Seite 9
焊接过程对零件布局的要求 VERSAFLOW 3 / ECOSELECT 2 / ECOCELL
© by ERSA GmbH • VF_LAYOUT_DT_V401_200dpi.ppt • AT/jfr.01.2011
非焊接限制区域与印制电路板边缘的最小距离 为B (4 mm) 最小的限制区域请参考第11页的描述 焊点可不在焊接区域的中心位置,但以中心为 最佳。
Seite 12
焊接过程对零件布局的要求 VERSAFLOW 3 / ECOSELECT 2 / ECOCELL 在只有一边SMD零件的时候可以采用不对称的焊接位置
长度
VF3 345 VF3 366 ECOSELECT ECOCELL
长度 [mm] 120 - 508 120 - 610 120 - 508* 120 - 356
宽度 [mm] 60 - 406 60 - 610 60 - 406 60 - 356
最大厚度 6 mm *长度略短也是可行的
Seite 2
© by ERSA GmbH • VF_LAYOUT_DT_V401_200dpi.ppt • AT/jfr.01.2011
Seite 15
焊接过程对零件布局的要求 VERSAFLOW 3 / ECOSELECT 2 / ECOCELL 单排或多排焊点到印制电路板边的最小距离
B
焊点
焊接区域 非焊接限制区域
不足够的空间
© by ERSA GmbH • VF_LAYOUT_DT_V401_200dpi.ppt • AT/jfr.01.2011
Good
Seite 8
焊接过程对零件布局的要求 VERSAFLOW 3 / ECOSELECT 2 / ECOCELL
选择性焊接点与周围零件的安全距离(基于选用最小的喷嘴-外径6mm)
Seite 10
焊接过程对零件布局的要求 VERSAFLOW 3 / ECOSELECT 2 / ECOCELL 焊点周围的最小距离
X
焊点
焊接区域
非焊接限制区域
X1
焊接区域与周围零件的最小的距离X= 2 mm 最小的可焊接区域X1= 6 mm 焊点可不在焊接区域的中心位置,但以中心为最 佳。
如有更小的可焊接区域请咨询ERSA
*喷嘴尺寸来源于喷嘴外部轮廓的直径
© by ERSA GmbH • VF_LAYOUT_DT_V401_200dpi.ppt • AT/jfr.01.2011
Seite 17
焊接过程对零件布局的要求 VERSAFLOW 3 / ECOSELECT 2 / ECOCELL 焊点区域的热量影响
由于焊接区域存在氮气保护环境,在氮气罩上方的红色区域可能存在100度左右的高 温,该区域不适合放置热敏感元器件
© by ERSA GmbH • VF_LAYOUT_DT_V401_200dpi.ppt • AT/jfr.01.2011
Seite 11
焊接过程对零件布局的要求 VERSAFLOW 3 / ECOSELECT 2 / ECOCELL
焊点周围的最小距离
B
焊点 焊接区域 非焊接限制区域
如有更小的可焊接区域请咨询ERSA
4 mm 印制电路板边缘和零件本体的距离
Seite 4
轨道传输系统对产品的要求 ECOSELECT 2 / ECOCELL 传输系统截面图
4 mm
4 mm
印制电路板边缘和零件本体的距离
© by ERSA GmbH • VF_LAYOUT_DT_V401_200dpi.ppt • AT/jfr.01.2011
当使用载具或夹具的时候,需要确保轨道传输平面A与印制电路板底面B处于同一高度 。如有其它特殊情况时也要以这个要求为原则,与其基本保持一致。
传输平面 A = 印制电路板底面B 加工精度 +/- 0,05 mm
© by ERSA GmbH • VF_LAYOUT_DT_V401_200dpi.ppt • AT/jfr.01.2011
轨道传输系统对产品的要求 VERSAFLOW 3 / ECOSELECT 2 / ECOCELL 零件面零件高度和与板边的距离要求
传输方向
零件高度
max. 120 mm
零件与印制电路板边缘的距离 min. 4 mm
印制电路板或载具厚度
max. 6 mm
*
BE 高度 (从板底开始量测)
零件与印制电路板边缘的距离
焊点 焊接区域 非焊接限制区域
X2 X‘
X2
最小的宽度X为6mm(pad到pad的距离).
焊接长度取决于零件的长度加上2*X2.
焊接区域到邻近pad的最小距离X1为1 mm.
拖焊开始和结束的边缘与邻近pad的最小距离 X2为3mm
焊点可不在焊接区域的中心位置,但以中心为 最佳。
如有更小的空间请向ERSA咨询
焊接和非焊接限制区域定义
焊点 焊接区域 非焊接限制区域
焊接区域: 能接触到焊料的区域.实际的焊点可能会比该区域要小,焊点可不在焊接区 域的中心位置,但以中心为最佳。
限制区域:
注意: 能。
周围没有需要焊接零件的区域。 以上的区域是应当优先考虑的,如超出这个尺寸,周围零件就有被冲掉的可
© by ERSA GmbH • VF_LAYOUT_DT_V401_200dpi.ppt • AT/jfr.01.2011
与焊接区域外缘垂直摆放的SMD 零件在选择性焊接时,即使接触 到焊锡也只会熔化一个Pad, 从而 避免零件被冲掉.
Seite 7
焊接过程对零件布局的要求 VERSAFLOW 3 / ECOSELECT 2 / ECOCELL
选择性焊接的一般要求
机械塑料固定脚或锁扣被接插件广泛地应用于将零件固定到印制电路板上,但大部分 塑料件是不能接触高温液态焊料的,所以要像对待SMD零件一样来对待它们。参照 SMD零件的布局要求。
单排焊点最小空间需求
X
X1
X1
焊点 焊接区域 非焊接限制区域
X2
X‘ X2
最小的宽度X为6mm(pad到pad的距离).
焊接长度取决于零件的长度加上2*X2.
焊接区域到邻近pad的最小距离X1为2 mm.
拖焊开始和结束的边缘与邻近pad的最小距离 X2为3mm
焊点可不在焊接区域的中心位置,但以中心为 最佳。
如有更小的空间请向ERSA咨询
© by ERSA GmbH • VF_LAYOUT_DT_V401_200dpi.ppt • AT/jfr.01.2011
Seite 14
焊接过程对零件布局的要求 VERSAFLOW 3 / ECOSELECT 2 / ECOCELL 多排焊点最小空间需求
X
X1
X1
焊接喷嘴以外的零件高度是受距离的限制的,请参考第20页的尺寸描述 从滚轮边缘到喷嘴中心的最小距离取决于所选择的喷嘴外直径 Y = 喷嘴外直径/2 + 1 mm * 如有更高的零件请咨询ERSA
© by ERSA GmbH • VF_LAYOUT_DT_V401_200dpi.ppt • AT/jfr.01.2011
© by ERSA GmbH • VF_LAYOUT_DT_V401_200dpi.ppt • AT/jfr.01.2011
Seite 3
轨道传输系统对产品的要求 VERSAFLOW 3 传输系统截面图
4 mm
© by ERSA GmbH • VF_LAYOUT_DT_V401_200dpi.ppt • AT/jfr.01.2011
选择性焊接点与周围零件的安全距离取决于: 1. 焊接喷嘴的尺寸 2. 与周围零件的距离
选择多大的焊接喷嘴来完成焊接, 取决于焊点与周围零件的距离。对于一个新的印制电路 板设计我们必须考虑以下页面所示的焊接喷嘴最小尺寸。 最小的焊接喷嘴是6mm* 基于这些喷嘴的外部尺寸,我们必须加一个安全距离来避免焊接时润湿到周围的SMD零 件。下几页会描述几种不同的情形。 如果我们使用单点焊接模组,有以下几种焊接方式: