回转窑煤粉制备及燃烧系统的改造
新型干法回转窑系统的节能提产改造
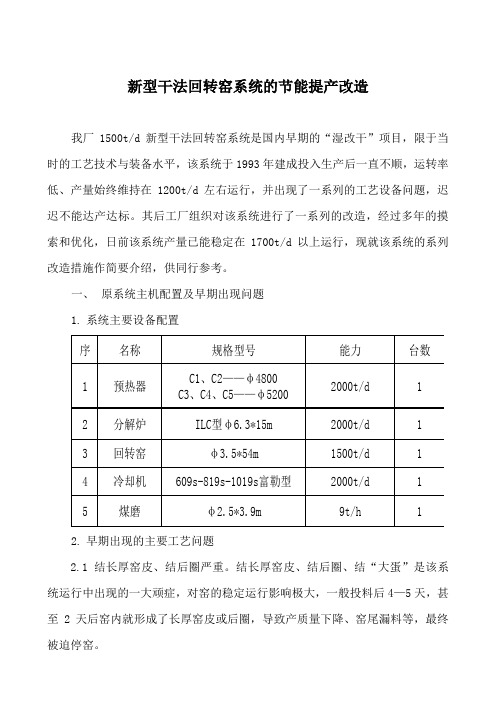
新型干法回转窑系统的节能提产改造我厂1500t/d新型干法回转窑系统是国内早期的“湿改干”项目,限于当时的工艺技术与装备水平,该系统于1993年建成投入生产后一直不顺,运转率低、产量始终维持在1200t/d左右运行,并出现了一系列的工艺设备问题,迟迟不能达产达标。
其后工厂组织对该系统进行了一系列的改造,经过多年的摸索和优化,日前该系统产量已能稳定在1700t/d以上运行,现就该系统的系列改造措施作简要介绍,供同行参考。
一、原系统主机配置及早期出现问题1.系统主要设备配置2.早期出现的主要工艺问题2.1 结长厚窑皮、结后圈严重。
结长厚窑皮、结后圈、结“大蛋”是该系统运行中出现的一大顽症,对窑的稳定运行影响极大,一般投料后4—5天,甚至2天后窑内就形成了长厚窑皮或后圈,导致产质量下降、窑尾漏料等,最终被迫停窑。
2.2 窑尾上升烟道结皮严重,严重影响了窑内通风。
2.3 一级筒出口温度高,通常达到370℃以上;气体粉尘浓度大,高达215g/Nm3。
2.4 篦冷机冷却效果差、运转率低、自身故障频繁,出篦冷机熟料温度高达150℃以上。
2.5 喂煤不稳定,波动幅度大且频繁,常出现断煤。
2.6 熟料产质量较差。
二、改造措施1.篦冷机的改造利用原有的水平推动式篦冷机框架及主梁,改为充气梁式篦冷机。
在高温区采用“固定式充气梁”装置最大的优点是大大降低了热端篦床的机械故障率,充分保证了篦冷机的运转率。
由于对窑下料口区域的篦床采用“固定式充气梁"装置,热熟料易于堆积,虽可调节冷却风量来对积料厚度加以控制,但为了防止堆“雪人”和大块熟料的堆积,在端墙安装了一组空气炮,按实际需要间断开炮,适时清理过多的积料,保证篦冷机安全稳定运行。
采用充气梁式冷却机,冷却风分布更为均匀,避免了“红河”现象,其热效率由原来的50—60%提高了到70%以上,三次风温提高了300℃左右。
2.分解炉的改造分解炉的改造与窑尾、冷却机等系统是密不可分的,因为原分解炉(如图1)的结构缺陷,物料在炉内停留时间过短,入窑分解率低,同时只靠窑尾废气不能把四级筒的来料完全带入炉内,一部分直接短路入窑,而为保证熟料质量,窑头必然加大燃煤量,这样又造成了窑尾温度过高、上升烟道结皮、窑内结后圈、窑内通风不良等不正常现象。
回转窑的改造
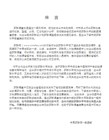
2 改造方案
此项目的改造目标、范围和内容如下:
(1) 改造目标。将窑生产能力从2100td提高到5500td。
(2) 改造范围。采用原料预均化库及最新的配料系统改善生料质量均一性,以提高熟料质量;提高过程控制自动化水平,以提高劳动生产率;进行环保配套改造,以最大限度地保护环境。
2.4 #3窑的改造
1999年2月1日,在马来西亚因经济萧条而水泥需求低时,进行#3窑的停窑改造,至2000年5月结束。窑系统的改造由伯力鸠斯公司承担,具体改造内容如下
(1) 保留原5.0m4.6m×81m回转窑。更换窑传动,采用2×550kW双传动;更换窑烧成带筒体和窑头及窑尾段筒体 更换2号窑墩的轮带和托轮。在保持窑斜度不变,将窑转速提高到最高4.8rmin。
系统改造后,原莱歇磨与新的混合原料喂料系统相连,烘干粉磨用热气体通过新的#3窑排风机继续从#3窑抽取。生料送入原间歇式均化库和储库(这些储库被保留,作为改造后的#3窑喂料系统的一部分)。
生料库总储量为20000t,以保证窑连续、平稳操作。原生料库和新生料库中的生料卸出后送入70m3的窑喂料小仓,仓下装有1台冲板流量计及1套标定用的旁路系统。
1996年8月TCB开始对#3窑生产线进行改造,增加窑系统的上游和下游设施,将生产能力由2100td提高到5500td,从而将全厂熟料和水泥总生产能力分别提高到250万t和300万t。由于金融危机,该改造工程被迫推迟,改造后的新线直到2000年才调试。本文就#3窑生产线的改造工作作一简要叙述。
该水泥终粉磨系统由1台HRP-W-2.0辊压机和1台4.2m×12.5m的UMS管磨组成的混合粉磨系统。出辊压机的料饼被送入1台SAPEX M-B3-400-450-C-V打散机打散,再送入只装细研磨介质的单仓UMS管磨粉磨。出管磨物料通过SAPEX-450 M-210高效变速选粉机(转子速度可在77rmin~230rmin之间调节)控制产品细度。如果UMS管磨由于某种原因不能运转,辊压机能够以84th的产量生产比表面积为320m2kg的普通硅酸盐水泥,此时电耗约为28.9kWht(辊压机+管磨混合粉磨时的电耗为3.1kWht),但水泥产品的需水量稍高。UMS磨也可不带辊压机单独使用,此时当生产320m2kg普通硅酸盐水泥时,其能力为90th,但应更换特殊级配的研磨介质。为满足上述需要,辊压机的两个辊子都装有带变频器的变速传动。
回转窑焙烧工艺流程

回转窑焙烧工艺流程回转窑焙烧工艺流程是一种常用于生产水泥和其他矿石材料的工艺。
下面为您详细介绍回转窑焙烧工艺流程。
回转窑焙烧工艺是通过旋转的锥形窑筒将原材料进行高温煅烧的过程。
主要包括下述几个阶段:1.预热区:原料进入回转窑的上部,在该区域受到火焰和热空气的预热。
温度约为600℃-800℃,这有助于降低能耗和提高焙烧效率。
2.煅烧区:原料在该区域的温度逐渐上升,达到煅烧温度。
这是回转窑的主要区域,温度一般在1200℃-1450℃之间。
煅烧的目的是将原料中的水分和化学结合物转化为水泥熟料中的主要组分,例如三氧化二铝、硅酸盐及其他矿物质。
3.冷却区:焙烧后的熟料进入回转窑的下部,通过外部冷却空气的循环进行快速冷却。
这有助于提高产品的质量和稳定性,避免因过热导致后续处理过程中的问题。
4.煤粉喷烧阶段:在鼓风机的作用下,将煤粉喷入回转窑中,与预热和煅烧区域中的气流混合燃烧。
煤粉的燃烧提供热量,使窑筒内温度保持在所需的范围内,确保焙烧过程的顺利进行。
5.尾部净化:对于煤粉燃烧产生的烟气,通过尾部净化装置进行处理,以减少对环境的污染,同时回收部分热量用于供能。
回转窑焙烧工艺流程中流程控制的关键是保持适当的温度和气氛。
同时,还需要定期进行维护和检修,以确保设备的正常运行和生产效率。
回转窑焙烧工艺流程是一个将原料高温煅烧以制备水泥的重要过程。
通过预热、煅烧、冷却和煤粉喷烧等阶段,将原料转化为水泥熟料,并对煤粉燃烧产生的烟气进行净化处理。
这个工艺流程在水泥和矿石材料的生产中起着至关重要的作用。
回转窑煤粉燃烧器技术进展
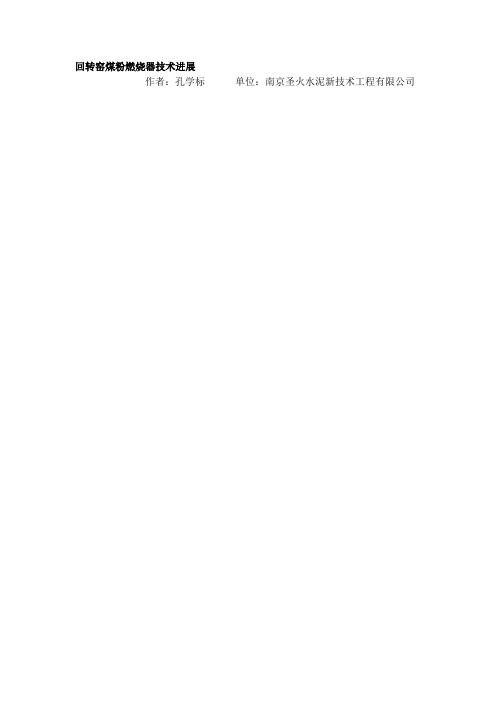
回转窑煤粉燃烧器技术进展作者:孔学标单位:南京圣火水泥新技术工程有限公司0 引言70年代中其国际上发展起来的水泥回转窑多通道煤粉燃烧器,使窑的一次风用量由传统的20%~30%下降至12%~15%,同时窑的操作及熟料煅烧情况得到明显改善。
经过20多年的技术进步,目前窑的一次净风用量已降低到6%~8%,大大改进了窑的燃烧效率和热效率。
与此同时,水泥窑对燃煤品质要求不断降低,无烟煤、劣质煤及再生燃料(即工业和民用可燃垃圾)的利用技术渐成热点,从而促使燃烧器结构形式不断的改进。
自传统的单通道燃烧器向多通道(如三通道、四通道等)燃烧器发展以后,新一代的双通道燃烧器,由于调节性能、火焰成形能力及燃烧效率等方面的优良性能正作为一种新的技术发展方向。
多相流及反应计算机数值模型技术的发展使燃烧器开发专家不再依赖传统的冷态气体模拟试验,以KILN FLAME SYSTEMS公司为代表的酸碱水模拟试验方法可使回转窑燃烧的流畅设计更加精确,从而确保了高风险的窑头燃烧器的投运调试顺利达到预期效果。
1 对回转窑煤粉燃烧认识的深入从工艺过程角度看,用于对回转窑烧成带提供热量的燃烧器应满足下述要求:1)对燃烧品质具有较强的适应性,特别是在燃烧无烟煤或劣质煤时,能确保在较低空气过剩系数下完全燃烧,其CO和NOx排放量降至最低限度。
2)火焰形状应是细而不长,使整个烧成带具有强而均匀的热辐射。
这一方面有利于熟料结粒、熟料矿物晶相正常发育,防止烧成带扬尘;另一方面有利于形成致密稳定的烧成带窑皮,延长耐火砖使用寿命。
3)一次风用量尽可能少,但必须保证在不正常的窑况下火焰燃烧的稳定。
值得指出的是,在上述要求中强调了火焰形成应是“细而不长”以形成合理的燃烧带长度,而不再象以往那样强调化燃烧以适应强化煅烧要求,这是因为强化燃烧所形成的局部高温对烧成带窑皮不利,从而影响耐火砖使用寿命,另一方面局部高温将增加NOx的排放量。
一般情况,来自冷却机的二次风温可达900℃以上,窑头燃烧火焰温度高达1800℃左右,其燃烧一般已进入扩散控制区。
发布版)旋窑工艺煤粉制备系统防火防爆隐患整改技术指导书
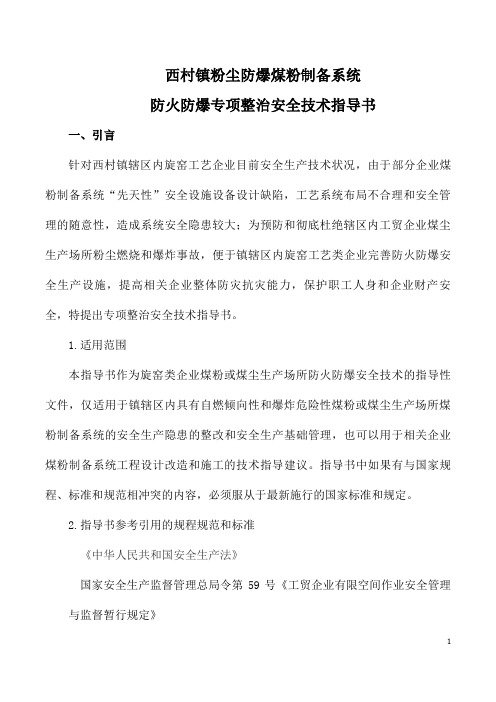
西村镇粉尘防爆煤粉制备系统防火防爆专项整治安全技术指导书一、引言针对西村镇辖区内旋窑工艺企业目前安全生产技术状况,由于部分企业煤粉制备系统“先天性”安全设施设备设计缺陷,工艺系统布局不合理和安全管理的随意性,造成系统安全隐患较大;为预防和彻底杜绝辖区内工贸企业煤尘生产场所粉尘燃烧和爆炸事故,便于镇辖区内旋窑工艺类企业完善防火防爆安全生产设施,提高相关企业整体防灾抗灾能力,保护职工人身和企业财产安全,特提出专项整治安全技术指导书。
1.适用范围本指导书作为旋窑类企业煤粉或煤尘生产场所防火防爆安全技术的指导性文件,仅适用于镇辖区内具有自燃倾向性和爆炸危险性煤粉或煤尘生产场所煤粉制备系统的安全生产隐患的整改和安全生产基础管理,也可以用于相关企业煤粉制备系统工程设计改造和施工的技术指导建议。
指导书中如果有与国家规程、标准和规范相冲突的内容,必须服从于最新施行的国家标准和规定。
2.指导书参考引用的规程规范和标准《中华人民共和国安全生产法》国家安全生产监督管理总局令第59号《工贸企业有限空间作业安全管理与监督暂行规定》国家安全生产监督管理总局令第68号《严防企业粉尘爆炸五条规定》西村镇人民政府西政【2016】32号《西村镇工贸企业深化粉尘防爆专项整治实施方案》GB12476.1— 2013《可燃性粉尘环境用电气通用要求》GB50058—2014《爆炸和火灾危险环境电力装置设计规范》 GB13532—92《干粉灭火剂通用技术条件》GB15577—2007《粉尘防爆安全规程》GB3836.1—2010《爆炸性环境第一部分通用要求》GB/T15605—1995《粉尘爆炸泄压指南》GB/T29304—2012《爆炸危险场所防爆安全导则》GB50016—2014《建筑设计防火规范》GB17919—2008 《粉尘爆炸危险场所用收尘器防爆导则》GBZ1—2010《工业企业设计卫生标准》GBZ188—2014《职业健康监护技术规范》GB16543—2008《高炉喷吹烟煤系统防爆安全规程》GB50057—2010《建筑物防雷设计规范》3.指导书采用下列定义3.1 煤粉:细微的煤颗粒。
水泥回转窑用煤技术的进步及其燃烧器的发展(一)

所 谓 低 质 煤 目前 还 没有 一 个准 确 的 定 义 , 主 要
是 因 用途 不 同 , 衡量 的 标 准 各 异 。 如 无 烟 煤 对 回转 窑 来说 是 非 常 低 劣 的煤 种 , 而对 立 窑 来 说 便 是 优 质 燃 料 优质 烟 煤 反 而还 不 能 用 于立 窑 煅 烧 熟料 。一 1 , 般 的概 念 是 指 灰 分 高 、挥 发分 低 、热 值 低 、水 分 大 和 硫 分高 的煤 种 。现 有两 种 观 点 :一 种 指 应 用基 低 1 位 发热值 在 1 6 l g30 0 cl g以下 的各 种牌 号 25 0k/ ( 0 a k ) k k /
关键词 低质煤 四风道煤粉燃烧器 扩散控制 化学控 制
0 引言
回 转 窑烧 廉 价 的低 质煤 可 以大 幅 度地 降 低水 泥 成 本 。
现 在 我 国不 少 水 泥 厂 都 看 准 了这 一 既可 增 强企 业 竞
在 工 业 窑 炉 中 ,水 泥 回 转 窑 是 最 早 应 用 煤 粉 为 燃 料 来 煅 烧 熟 料 的 , 而动 力 蒸 汽 锅 炉  ̄ 2 世 纪2 年 ] 10 0 代 才 开 始 使 用 煤 粉 为 燃 料 。 可 是 对 水 泥 窑 煤 粉 燃烧
及 火 焰 的 研 究 却 远 不 如 对 锅 炉 研 究 的 那 样 充 分 和 深
争 能 力 又 可提 高 经 济 效 益 的 目标 , 积极 酝酿 和 筹 划 , 并 且 有 少 部 分 已应用 成 功 , 促 进 了水 泥 回 转 窑用 煤 的进 步 , 为廉 价低 质 煤 的 利用开 辟 了一 条新 路 。 1 我 国煤炭 分 布 的特 点 我 国 的煤 炭 资 源 相 当 丰 富 , 目前 探 明储 量 已超
水泥厂煤粉制备系统的改造
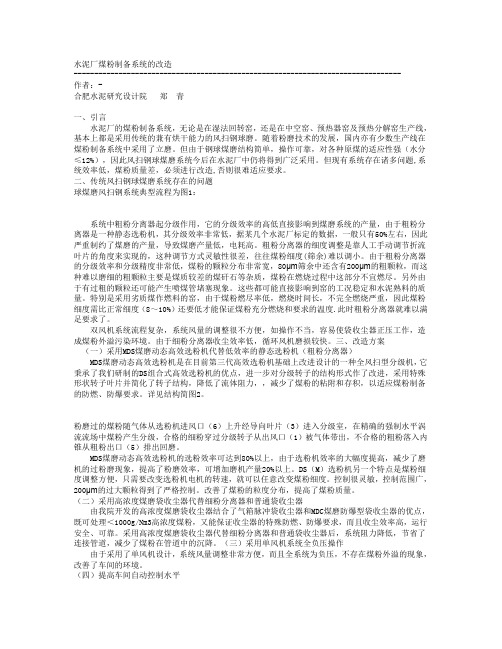
水泥厂煤粉制备系统的改造--------------------------------------------------------------------------------作者:-合肥水泥研究设计院郑青一、引言水泥厂的煤粉制备系统,无论是在湿法回转窑,还是在中空窑、预热器窑及预热分解窑生产线,基本上都是采用传统的兼有烘干能力的风扫钢球磨。
随着粉磨技术的发展,国内亦有少数生产线在煤粉制备系统中采用了立磨。
但由于钢球煤磨结构简单,操作可靠,对各种原煤的适应性强(水分≤12%),因此风扫钢球煤磨系统今后在水泥厂中仍将得到广泛采用。
但现有系统存在诸多问题,系统效率低,煤粉质量差,必须进行改造,否则很难适应要求。
二、传统风扫钢球煤磨系统存在的问题球煤磨风扫钢系统典型流程为图1:系统中粗粉分离器起分级作用,它的分级效率的高低直接影响到煤磨系统的产量,由于粗粉分离器是一种静态选粉机,其分级效率非常低,据某几个水泥厂标定的数据,一般只有50%左右,因此严重制约了煤磨的产量,导致煤磨产量低,电耗高。
粗粉分离器的细度调整是靠人工手动调节折流叶片的角度来实现的,这种调节方式灵敏性很差,往往煤粉细度(筛余)难以调小。
由于粗粉分离器的分级效率和分级精度非常低,煤粉的颗粒分布非常宽,80μm筛余中还含有200μm的粗颗粒,而这种难以磨细的粗颗粒主要是煤质较差的煤矸石等杂质,煤粉在燃烧过程中这部分不宜燃尽。
另外由于有过粗的颗粒还可能产生喷煤管堵塞现象。
这些都可能直接影响到窑的工况稳定和水泥熟料的质量。
特别是采用劣质煤作燃料的窑,由于煤粉燃尽率低,燃烧时间长,不完全燃烧严重,因此煤粉细度需比正常细度(8~10%)还要低才能保证煤粉充分燃烧和要求的温度.此时粗粉分离器就难以满足要求了。
双风机系统流程复杂,系统风量的调整很不方便,如操作不当,容易使袋收尘器正压工作,造成煤粉外溢污染环境。
由于细粉分离器收尘效率低,循环风机磨损较快。
金川回转窑低温焙烧煤粉燃烧技术的研究与应用
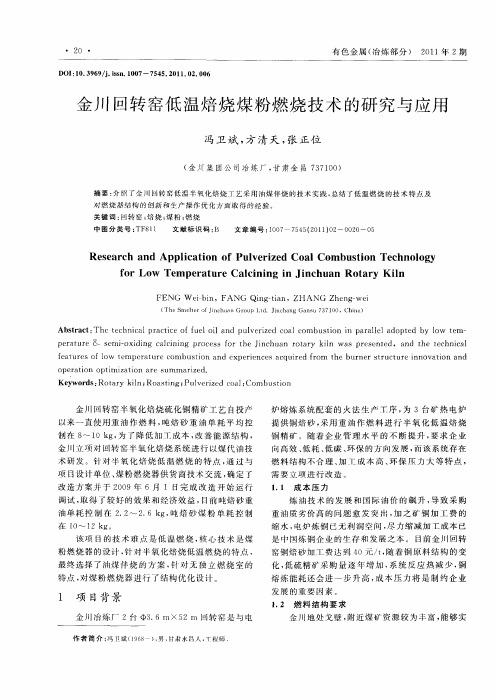
p r t r ea u e
s mi x d n a cn n r c s o h i c u n r t r i s p e e t d a d t e t c n c l e — i i g c li i g p o e s f r t e J n h a o a y k l wa r s n e . n h e h ia o n
金 川回转窑 半氧化 焙烧硫 化铜精 矿工艺 自投 产 以来一直 使用重 油作 燃 料 , 焙 砂重 油 单耗 平 均 控 吨 制 在 8 1 g 为 了降低 加工成 本 , ~ 0k , 改善 能源 结构 ,
金 川 立 项 对 回转 窑 半 氧 化 焙 烧 系 统 进 行 以煤 代 油 技 术 研 发 。针 对 半 氧 化 焙 烧 低 温 燃 烧 的 特 点 , 过 与 通
( 川 集 团公 司 冶 炼 厂 , 肃 金 昌 7 7 0 ) 金 甘 3 10
摘 要 : 绍 了金 川 【 转 窑 低温 半 氧 化 焙 烧 丁 艺 采 用油 煤 伴 烧 的 技 术 实 践 , 结 了 低 温燃 烧 的 技 术 特 点 及 介 旦 l 总 对 燃烧 器结 构 的创 新 和 生 产 操 作 优 化 方 面取 得 的经 验 。 关键词 : 回转 窑 ; 烧 ; 粉 ; 烧 焙 煤 燃
炉熔炼 系统配套 的火 法 生 产 丁序 , 3台矿热 电炉 为 提供铜 焙砂 , 用重 油 作 燃料 进 行半 氧化 低温 焙 烧 采
铜 精 矿 。随 着 企 业 管 理 水 平 的 不 断 提 升 , 求 企 业 要
向高效 、 低耗 、 低碳 、 保 的方 向发 展 , 该系统存 在 环 而
・
2 0・
有色 金属 ( 炼部 分 ) 21 冶 0 1年 2 期
水泥回转窑工艺流程图

水泥回转窑工艺流程图
水泥回转窑工艺流程图主要包括原料处理、煤磨和预均化、煤粉储备、回转窑系统、水泥磨和包装等几个环节。
首先是原料处理环节。
原料主要有石灰石、粘土、矾土、铁矿石等。
首先将这些原材料经过采矿、破碎、粉碎等工艺处理,获得合适的粒度的原材料。
接下来是煤磨和预均化环节。
在该环节中,将适量的煤磨碾碎并烧制成煤粉,同时也要把原料混合均匀。
煤粉和预均化的原料混合后,得到新鲜煤粉和原料均匀混合的原料,这样更有利于水泥回转窑中的热交换。
然后是煤粉储备环节。
在这个环节中,将煤粉储存在煤粉仓中,以备水泥回转窑需要的时候使用。
接下来是回转窑系统环节。
在这个环节中,将前面制备好的原料和煤粉供给回转窑中,进行煅烧过程。
通过高温煅烧,原料中的矿物质发生物理和化学反应,产生了“熟料”,即水泥石。
最后是水泥磨和包装环节。
在这个环节中,将煅烧后的熟料通过水泥磨进行细磨,使其达到所需的细度。
然后将细磨后的水泥通过包装机进行包装,分装成规定的包装袋或散装。
通过以上几个环节的工艺流程,完成了整个水泥回转窑的生产过程。
需要注意的是,该工艺流程图是一个简化的示意图,实际的工艺流程中还包括很多细节,例如温度控制、废气处理、
能量回收等等,这些细节对于水泥回转窑的生产效率和环境保护都是非常重要的。
同时,该工艺流程图中使用的原料和燃料也可以根据不同的工厂和产品要求进行调整,以满足不同的生产需求。
回转窑在运转中回转窑内煤粉燃烧状况分解

回转窑在运转中回转窑内煤粉燃烧状况分解煤粉在回转窑内的燃烧过程比较复杂,煤粉在燃烧的同时,还要向窑尾运动,并且在燃烧过程中,要进行传热,这几方面又相互影响,现由河南省荥阳市矿山机械制造厂对该过程分析如下:在回转窑内煤粉以分散状态由喷煤嘴喷出至开始燃烧的这段距离称黑火头,在正常生产时高温带温度很高,因此煤粉很容易着火燃烧,当开窑点火时,窑内无热源,就必须距窑口3-5m处放置木柴、费油棉纱等易燃物点火燃烧,使其湿度达到煤粉的着火温度后再喷进煤粉才能进行燃烧。
煤粉受热后首先被干燥,将所含1%-2%的水分排出,一般需要0.03-0.05s。
但在煤粉粗湿的情况下,干燥预热的时间要相应延长,干燥预热时间的长短,决定火焰黑火头的长短,温度升高到150-500℃时,挥发分开始透出,在700-800℃时全部溢出(煤粉中水分和挥发分溢出后剩下的是固定碳粒子和灰分)。
当挥发分遇到空气时使其着火燃烧,生成气态的CO2和H2O,他们包围在剩下的固定碳粒子周围,因此固定碳粒子的燃烧,除了要有足够高的温度外,还必须待空气中国的氧通过扩散透过包围在固定碳粒子周围的气膜。
与固定碳粒子接触后才能进行固定碳的燃烧。
挥发分燃烧时间长短,与挥发分含量多少,气体流速大小、温度高低有关,挥发分低,气体流速快,温度高,燃烧时间就短,否则相反,挥发分高的煤,着火早,燃烧快,黑火头短,白火焰长,挥发分低的煤则相反。
煤粉在回转窑内燃烧形成火焰示意图1.煤喷管;2-一儿风入口固定碳粒的燃烧是很缓慢的,它的燃烧速度不但与温度高低有关,且与气体扩散速度(包括燃烧产物扩散离开碳粒子表面和氧气扩散到固定碳粒子表面)有很大关系。
所以加强气流扰动,以增加气体扩散速度,将大大加速固定碳粒子的燃烧,煤粉的颗粒大小及含碳量多少也都影响着碳粒的燃烧速度。
煤粉喷出有一定速度,因此一出喷嘴首先是预热干燥,不可能立即燃烧,随着距喷嘴距离的增加,挥发分逐步溢出并燃烧,他们的位置分布如图所示。
回转窑焚烧处理系统技术方案

回转窑焚烧处理系统技术方案回转窑焚烧处理系统技术方案随着工业化的不断加速,我国的固体废弃物也在快速增长,废弃物的处理和综合利用已成为各地政府和企业关注的热点领域。
回转窑焚烧处理系统是一种综合利用固体废弃物的方法,主要通过高温烧烤来达到废弃物减量和资源化利用的目的。
本文将从技术方案、工程设计、设备选择和运行管理等方面探讨回转窑焚烧处理系统的技术应用。
一、技术方案回转窑烧结系统主要包括四部分:前端处理系统、烘干系统、烧结系统和排放处理系统。
前端处理系统主要负责废弃物的采集、分选、粉碎和成块处理,确保废弃物在烘干和烧结过程中具有相同的物理和化学性质。
进入烘干系统后,废弃物会被送往回转窑中进行干燥处理,使其水分含量降至5%以下。
经过烘干处理后,废弃物被送入回转窑进行烧结处理,达到减量和资源化利用的目的。
在冷却和排放处理系统中,烧结后的物料被送至降温塔进行冷却,过滤和净化后再排放至空气中。
二、工程设计根据处理规模和工艺流程等因素,设计一个具有满足处理能力、稳定性和可靠性的回转窑烧结系统,并考虑系统的容错性和后续维护的便利性。
设计将考虑回转窑的形状、尺寸和旋转速度等因素,以确保高温下的均匀加热和物料的均匀流动。
同时还需要考虑炉体与设备的耐腐蚀性、耐高温性以及防火安全等因素。
三、设备选择在采购设备时,需要选择符合生产需求、质量可靠和成本合理的设备。
主要设备包括回转窑、燃烧器和废气处理设备等。
回转窑的选择需考虑废弃物的物理特性和加热方式,确保其旋转速度和加热温度具有稳定性。
燃烧器的选择需根据燃烧物料类型和热量需求,选择适合的燃烧器类型并确保其燃烧效率高、排放尽量低。
废气处理设备主要包括旋流器、喷淋塔等,需要根据废气的化学性质和排放要求选择合适的处理设备。
四、运行管理回转窑处理系统不仅需要合理的设计和设备配合,更需要有效的运行管理来确保正常生产和减少环境污染。
在生产和运营中需要对系统进行定期维护和检修,确保设备安全稳定,以及对废气和废水进行有效地处理和排放。
回转窑内燃料燃烧

如图所示为 常用的几种 传统喷嘴。
二、煤粉燃烧过程:
回转窑煤粉的燃烧设备为单管式烧嘴。
在回转窑的烧成带,物料进行的主要物理化学反应是 C2 S 吸收 f CaO 生成 C3 S ,这是微吸热反应。为了使生成
C3 S
的反应完全,必须使物料在1400~1450℃的高温下停留
一定的时间。
(关于燃料的燃烧过程已在《硅酸盐工业热工基础》中燃烧学 部分讨论,要课程不再重复)
(2)火焰温度分布(火焰形状)
窑内火焰温度分布,通常是两头低、中间高Hale Waihona Puke 热端较低温度 区就是窑内的冷却带。
煤粉从喷管喷出后,须经过干燥预热至700~800℃才着 火燃烧,回转窑中所看到的黑火头就是煤粉从喷出后至着火 燃烧前气流所移动的距离。黑火头长则使回转窑的传热面积 减小,对产量、质量不利,黑火头过短则冷却带短,熟料离 窑的温度提高,增加冷却机的负荷。
回 转 窑 喂 煤 系 统
1、燃料在回转窑内燃烧应满足的要求
为了使生成 C3 S
的反应完全,使生料烧成熟料并获得
较高的产量,燃料在转窑内的燃烧必须满足一定的要求:
燃料燃烧的火焰温度要达到1600~1800℃;(保持高温) 火焰要有适当的长度;(保持物料高温时间) 处于适当的位置。(适合 C3 S 的形成的反应)
2、回转窑对入窑煤粉和助燃空气的要求
(1)对入窑煤粉的质量要求
低热值:
g QDW 20600 kJ / kg
挥发份:
灰分: 水分:
vg
Ag
回转窑无烟煤煤粉制备系统研究
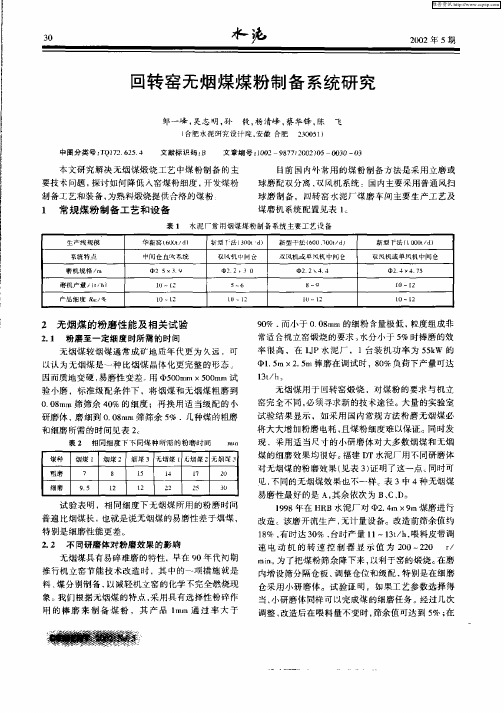
1 5
1 4
1 7
l细 9 磨 5
1 2
1 2
2 2
2 5
3 0
试 验 表 明 ,相 同细 度 下无 烟煤 所用 的粉 磨 时间 普遍 比烟煤 长 , 就是说 无烟 煤 的易磨性 差 于烟煤 , 也
特别是 细磨 性能 更差 。 2 2 不 同研磨 体对 粉磨 效果 的影 响 .
9%, 0 而小于 0 0 m 的细粉 含量极 低 , 8m 粒度 组成非
常适 台机 立窑煅 烧 的要求 。 分小 于 5 时棒磨 的效 水 % 率 很 高 ,在 kP水 泥 厂 ,1台装机 功 率 为 5 k 的 l 5W 中15 2 5 .m× .m棒 磨在 调试 时 ,8 %负荷 下产量 可达 0
1t 3 /h。
无烟 煤 较烟 煤通 常 成矿 地质 年代 更 为久 远 .可
以认为 无 烟煤是 一 种 比烟煤 晶体 化 更完 整 的形 态 。 因而质地变 硬 , 易磨性 变差 用  ̄5 0 m×5 0 m试 0r a 0r a
验 小磨 ,标准级 配 条件下 ,将 烟煤 和无 烟煤 粗磨 到 00 r 筛 筛余 4 % 的细 度 ;再 换用 适 当级 配 的小 8 m a 0
无烟 煤 用 于 回转窑煅 烧 ,对 煤 粉 的要求 与 机立 窑 完全不 同 , 必须 寻求新 的技术 途径 大 量 的实验室 试验 结 果显示 ,如 采用 国 内常 规方 法粉 磨 无烟煤 必 将大 大增 加粉 磨 电耗 , 且煤 粉细 度难 以保证 。同时发 现 ,采 用适 当尺 寸的小 研磨 体 对大 多数 烟 煤和 无烟 煤 的细磨 效果 均很好 建 D 福 T水泥 厂用 不 同研 磨体 对 无烟煤 的粉磨 效 果 ( 表 3 证 明了这一 点 。 见 ) 同时可 见 同的无 烟煤效 果也 不一样 表 3中 4种 无烟煤 不
回转窑内燃料的燃烧
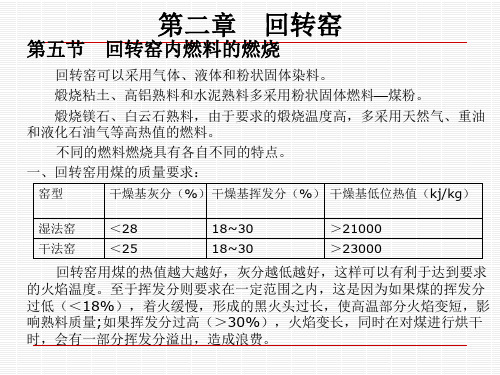
回 转 窑 喂 煤 系 统
1、燃料在回转窑内燃烧应满足的要求
为了使生成 C3 S
的反应完全,使生料烧成熟料并获得
较高的产量,燃料在转窑内的燃烧必须满足一定的要求:
燃料燃烧的火焰温度要达到1600~1800℃;(保持高温) 火焰要有适当的长度;(保持物料高温时间) 处于适当的位置。(适合 C3 S 的形成的反应)
气体流速:主要指一次风
一次空气主要供挥发分燃烧,因此一次风量主要决定 于煤粉中挥发的含量。挥发分多的煤粉,如一次风量少燃 烧速度就减慢,会使火焰拉长。
回转窑的直径愈大,一次风速愈高,直么2.5~4.0米 的回转窑,一次风速为50~70米/秒。一次风速增加,一 方面能增加煤粉单位时间的有效射程,另一方面又使煤粉 的燃烧速度加快,燃烧时间缩短,因此在实际操作中,一 次风速增加后,火焰变长或变短,应视两者的影响程度而 定。
L f =3.2 D f
烧成带长度:
燃烧带只是烧成带中温度最高的部分,烧成带长度 可按下式计算:
Ls
Ls
=(0.60~0.65) L f
(3)燃烧带的表面积热力强度(也称表面积热负荷) 和截面积热力强度(也称截面积热负荷)
表面积热力强度:燃烧带单位表面积上所发出的热量。
截面积热力强度:燃烧带单位截面积上所发出的热量。 计算公式分别为:
直管型 缩口型
拔哨型 风翅型
缩口型
风翅型
拔哨型:在缩口外再加一节平 头,能延长火焰,且使火焰平 衡。
直管型
拔哨型
风翅型:为加速风煤的混合,在 缩口型 喷煤管内加装风翅,翅片与管壁 中心线呈7~30°,角度大,火 焰短,但流股发生旋转,会扫伤 缩口型 窑皮。
直管型
拔哨型
煤粉燃烧系统的节能改造

加 大高 温风 的用量 ,减 小低温 风 的用量 ,是 降低煤
耗 的一个 重要 途径 。根 据这一 原则 ,在 满足火 焰稳 定 燃烧 的基础 上 ,尽 量 用较小 一次 风量 ,加 大窑 内 二 次 风量 的用 风 比例 ( 次风 温 约2 一 0,操 作灵 活 ,强化 了煅烧 ,产 品质 量稳定 。燃
2 1 年 第5 00 期
次 风温约 1 5 0℃ ),可有 效解 决这一 问题 。 0 改进 措施 :通 过计 算把 原来 的一 次净 风机 ( 全
压2 . k a 风 量 1 1 i, 0k )换成 一 台高风 9 P , 4 2 / n 9 W m m 压 、 低 风 量 净 风 机 (全 压 3 2 风 量 k a, 9. P 4 n 6m / ,功率5 W ),风量 减少 6 n 这 mi 5k 6m / , mi
为 五通 道 煤 粉 燃 烧 器 ,本 次 改 造 采 用 同产 某 五 通
由于 只是两 风道 与煤混 合 ,煤 粉混 燃效 果较差 ,热
量发挥 不集 中 ,烧 成带 温度相 对偏 低 ,物料反 应速
率下 降 ,一 定程度 上影 响熟料 的煅 烧 ;燃 烧器 头部 断面经 常 出现结焦 现象 造成火 焰分 叉 ;内外风 问 由 于受热 变形 ,风 出 口截 面 间隙不均 匀 ,造 成偏 火 ,
改进措施 :窑头喂煤 输送风机 ( 全压7 . k a 8 P , 4 风量4 n 4m/ ,功率9 W )改为 变频 控制 ,同时 mi 0k 把 煤输 送管 路 的内径 由15mm 为 10m 8 变 5 m。 ( 3)如何 更好 实 现 煤 粉 和空 气 的混合 ,加 快
回转窑的工作原理
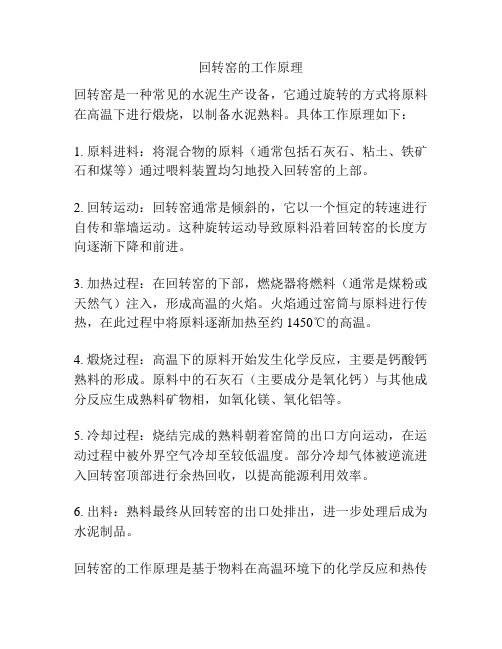
回转窑的工作原理
回转窑是一种常见的水泥生产设备,它通过旋转的方式将原料在高温下进行煅烧,以制备水泥熟料。
具体工作原理如下:
1. 原料进料:将混合物的原料(通常包括石灰石、粘土、铁矿石和煤等)通过喂料装置均匀地投入回转窑的上部。
2. 回转运动:回转窑通常是倾斜的,它以一个恒定的转速进行自传和靠墙运动。
这种旋转运动导致原料沿着回转窑的长度方向逐渐下降和前进。
3. 加热过程:在回转窑的下部,燃烧器将燃料(通常是煤粉或天然气)注入,形成高温的火焰。
火焰通过窑筒与原料进行传热,在此过程中将原料逐渐加热至约1450℃的高温。
4. 煅烧过程:高温下的原料开始发生化学反应,主要是钙酸钙熟料的形成。
原料中的石灰石(主要成分是氧化钙)与其他成分反应生成熟料矿物相,如氧化镁、氧化铝等。
5. 冷却过程:烧结完成的熟料朝着窑筒的出口方向运动,在运动过程中被外界空气冷却至较低温度。
部分冷却气体被逆流进入回转窑顶部进行余热回收,以提高能源利用效率。
6. 出料:熟料最终从回转窑的出口处排出,进一步处理后成为水泥制品。
回转窑的工作原理是基于物料在高温环境下的化学反应和热传
导机制,通过旋转的方式使原料充分接触并加热,以实现水泥生产过程中的煅烧和冷却等工序。
这种工作原理使得回转窑成为水泥工业中不可或缺的关键设备。
回转窑用煤粉燃烧器操作参数选用和优化
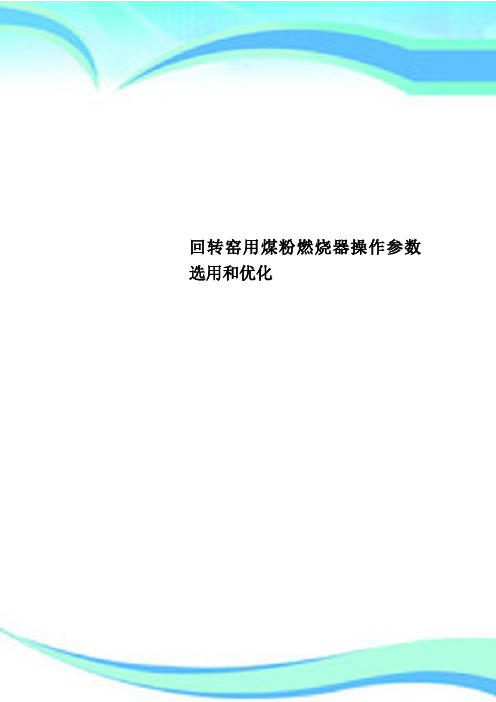
回转窑用煤粉燃烧器操作参数选用和优化————————————————————————————————作者:————————————————————————————————日期:浅谈回转窑用煤粉燃烧器操作参数的合理选择和优化1.研究意义回转窑工作原理是利用回转着的窑筒体,不断旋转带动固体物料不断翻滚,以其暴露的新表面与掠过的气体进行传热和传质并产生化学反应。由于回转窑内的物料是处于堆积态,窑内气-固、固-固之间的换热效率就相对较低,研究高温热处理条件下回转窑内发生的物质与能量的转化与传递,研究空气过剩系数、二次风温度、内外风量比等操作参数对窑内传热过程的影响,并对操作参数进行优化,从而求得烟气、物料、窑内外壁沿窑长方向的温度变化规律,借此了解煅烧窑内温度分布及炉窑热工特性,可为优化窑的操作参数提供理论依据。
并对煤粉燃烧器的操作参数进行优化,这对提高回转窑内换热效率、降低回转窑能耗具有重要的意义。
水泥熟料烧成反应是指硅酸二钙与氧化钙生成的液固相反应。
由于水泥熟料强度的主要组成来源是C3S,因此C2S+Ca O→C3S的烧成过程对整个煅烧过程具有至关重要的作用。
对C-S-A-F-MgO系统而言,该反应主要发生在熔融的液相中,液相出现的温度约为1550K(1277℃)。
烧结反应的机理可以这样描述:固相反应生成的C2S和之前未被反应的CaO在液相中溶解、扩散并在液相中发生反应、经液相的过饱和及反扩散,最后经过再结晶形成新相C3S。
从传热学的角度来说,窑内物料因入窑生料表观分解率为90~95%,分解吸热反应所需的热量很少,公斤熟料约200~100千焦,物料升温吸热量约为450~500千焦,而熟料矿物形成是以放热反应为主,设熟料中C2S占0.20%,C3S占0.60%,C3A占0.08%,C4AF占0.10%,反应过程放热量约为655千焦。
基于窑内熟料形成热基本是一个负值,所以可以认为窑内传热已不是主要矛盾,而熟料矿物生成的晶格形成和晶体生长所需维持的高温条件及在烧成带的停留时间成为矛盾的主要方面。
回转窑新型燃料结构的改变与使用

回转窑新型燃料结构的改变与使用在水泥行业、冶金行业、化工行业大型回转窑热力系统的燃烧方面,一般采用优质烟煤作为常用燃料,优质粉体烟煤在回转窑内喷燃时,能形成形状、热力强度可调节的火焰,从而达到物料热化学烧结的效果。
回转窑内的火焰形状与热力强度不仅与煤粉的细度、水份、挥发份、灰份、固定碳、热值等工业分析数值有关,还与燃料的C、H、O、N、S等化学元素分析数值有关,同时,燃烧用二次风风量与风温、一次风风量与风压、燃烧器端部的一次风风速与喷燃瞬间的燃烧动量等热工流体参数也直接影响着燃烧的效果。
研究燃料在回转窑内的燃烧效果主要研究燃料的易燃性、燃烬性、火焰形状稳定性、火力强度(热辐射与热传导的能量强度)与窑尾烟气的有害气体成份含量。
一、燃料工业分析、化学元素分析、热工流体参数对回转窑燃烧效果的影响。
1、燃料工业分析数值对回转窑燃烧效果的影响。
燃料细度越小、水分越低、挥发份越高,其易燃性与燃烬性越好;燃料灰份越低、固定碳与热值越高,其单位质量燃料的火力强度越高。
2、燃料化学元素分析数值对回转窑燃烧效果的影响。
燃料中C、H、O含量越高,其易燃性与燃烬性越好,同时其火力强度越高;燃料中N、S含量越高,其窑尾烟气中NxOy、SOx的有害气体成份含量越高。
3、燃料热工流体参数对回转窑燃烧效果的影响。
一次风风量随燃料挥发份增高而增高,对挥发份高的优质烟煤,由于其易燃性与燃烬性好,所以火焰短,火焰形状不能完全布满回转窑烧成带,导致温度前移,为调节火焰形状,只能通过增加一次风量与喷燃动量,使火焰拉长,布满烧成带;对挥发份很低的无烟煤,由于其易燃性与燃烬性很不好,火焰芯部黑火头很长,导致火焰很长,温度后移,使烧成带热力不集中,同时还使窑尾设备(如水泥厂预热器与分解炉)热工制度不稳定从而影响煅烧,所以只能减少一次风风量,但同时为改善无烟煤的易燃性与燃烬性,必须大幅度增大一次风压,使黑火头缩短。
一次风为冷风,会吸收燃烧时的热量,所以不论对烟煤还是无烟煤,应尽量少用,为保证喷燃动量,可通过提高一次风风速与风压、通过调节喷煤管的内外风风压与比例来改善燃料的易燃性与燃烬性。
回转窑内燃料的燃烧解读
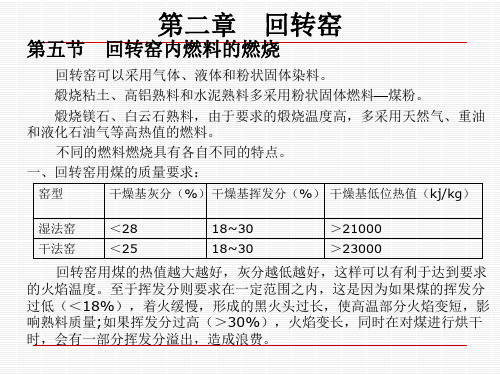
回 转 窑 喂 煤 系 统
1、燃料在回转窑内燃烧应满足的要求
为了使生成 C3 S
的反应完全,使生料烧成熟料并获得
较高的产量,燃料在转窑内的燃烧必须满足一定的要求:
燃料燃烧的火焰温度要达到1600~1800℃;(保持高温) 火焰要有适当的长度;(保持物料高温时间) 处于适当的位置。(适合 C3 S 的形成的反应)
影响窑内火焰长度的因素:有很多。主要有:燃烧速度和窑 内气体的流速。 燃烧速度:
粉煤的细度、煤粉与空气混合情况、一、二次风的温度
等因素有关。
煤粉粉愈细,或在喷煤管内加装风翅,以加还煤与空气
的混合,或提高一、二次空气的温度,均能提高燃烧速度, 而使火焰短。
风煤的混合速度和均匀程度也是影响燃烧速度的关键。
气体流速:主要指一次风
一次空气主要供挥发分燃烧,因此一次风量主要决定 于煤粉中挥发的含量。挥发分多的煤粉,如一次风量少燃 烧速度就减慢,会使火焰拉长。
回转窑的直径愈大,一次风速愈高,直么2.5~4.0米 的回转窑,一次风速为50~70米/秒。一次风速增加,一 方面能增加煤粉单位时间的有效射程,另一方面又使煤粉 的燃烧速度加快,燃烧时间缩短,因此在实际操作中,一 次风速增加后,火焰变长或变短,应视两者的影响程度而 定。
影响黑火头长度的因素有:
煤粉的组成与细度、一次空气的温度和流速、二次风量与 风温等。
煤粉愈细,煤粉中挥发分的含量越高,提高一次风温, 增加一次空气的比例,都会使黑火头缩短。
在窑的操作中,应形成适合烧成需要的好火焰,即高温 部分较长,黑火头较短,火焰平稳。
燃 烧 器
5、煤粉燃烧器(喷嘴)—喷煤管
3 =1.08N m / s
1.30V 1 d 1000 v
- 1、下载文档前请自行甄别文档内容的完整性,平台不提供额外的编辑、内容补充、找答案等附加服务。
- 2、"仅部分预览"的文档,不可在线预览部分如存在完整性等问题,可反馈申请退款(可完整预览的文档不适用该条件!)。
- 3、如文档侵犯您的权益,请联系客服反馈,我们会尽快为您处理(人工客服工作时间:9:00-18:30)。
回转窑煤粉制备及燃烧系统的改造
newmaker
中国铝业中州分公司年氧化铝生产能力
为137万t 。
其烧结法生产系统主要设备为6台Φ4.5×100m 回转窑,其中5#、6#窑采用转子称及多风道燃烧器喂煤,产量低,能耗高。
公司于2004年4月和10月分别对两台窑的煤粉制备及燃烧系统进行了改造,效果良好,达到了提产降耗的目的。
一、转子称配单风道燃烧器系统存在的问题
1、煤粉制备及燃烧系统基本配置煤粉制备及燃烧系统的工艺流程为:原煤从原煤仓进入磨煤机进行磨制,合格后通过管道输送到粗粉分离器进行分离,不合格的煤粒通过管道返回到磨煤机重新磨制,合格的煤粉随风进入细粉分离器进行分离。
分离出的合格煤粉进入煤粉仓,通过转子称进入到喷渠道,通过风喷入回转窑,而分离出的废气进入布袋收尘器,除尘后排入大气。
该系统的工艺流程见图1a 。
该系统主要设备参数如下:回转窑Φ4.5×100m ,安装斜度3.5%,设计产量55t /h ,烧结温度1200℃~1300℃,耐火材料寿命平均120天,耗煤量7.8t /h ,窑尾排烟温度220℃,火焰长度约7m 。
磨煤机DTMΦ2.9m×4.1m ,产量14t /h 排粉机M9-26No13DQ =
39910m3/h ,全压10045Pa 多风道喷煤管GD -10型,四风道转子称DRW3.1,PFISTER 公司布袋除尘器96LCPM -12,除尘面积231m2罗茨风机L73WDBQ =5754m3/h ,全压49500Pa
2、煤粉制备及燃烧系统存在的主要问题
采用转子称及多风道燃烧器喂煤具有喂煤量准确、稳定的优点,对稳定火焰形状有一定的帮助。
但存在一定的问题,主要表现在以下几个方面:
①采用多风道喂煤系统,回转窑的产量低于采用单风道喂煤系统窑的产量,按喂料系统油隔泵冲刺计算,平均低1冲刺/分。
②常规操作时,多风道喷煤管火力集中,火焰短,不易形成窑皮,容易造成炉体温度高,
影响提产,缩短耐火砖使用周期。
③由于5#、6#煤粉制备系统的废气没有入窑,故两套系统仍然保留袋式除尘器,在煤粉温度和环境温度高时,该除尘器易着火,不安全。
5目前5#、6#窑转子秤和多风道喷煤管采用罗茨风机供风,该风机安装在一楼磨煤主机厂房,其产生的噪声主要是气体动力性噪声和机械性噪声,最高可达110dB,严重影响员工工作。
二、改造方案
鉴于5#、6#窑多风道喂煤系统存在以上缺点,计划将多风道改为单风道,仍然采用转子秤喂煤,目的是既发挥单通道产量高、火力均衡的特点,又保留了转子喂煤量准确、火焰形状稳定的优点,同时可以基本解决罗茨风机噪音大、袋式除尘器易着火等问题。
1、实施方案采用比较成熟的单风道喷煤管模式替代原有的多风道喷煤管,增加一台M9-26No14D鼓风机做为喷煤管的一次风风源,该风机Q=58850m3/h,全压P=10045Pa,单风道喷煤管正常操作需要风量Q=30000m3/h,压力P=2000Pa,考虑到火焰调节的需要,计划新增加的鼓风机采用变频调速,因此在风量和压力上留有一定的余量,以满足挂窑皮、正常操作、提产等不同操作对风量和风压的需要,同时该型号风机使用可靠,维修费用低,故选用该型号鼓风机;保留转子秤,转子秤煤粉输送空气仍由一台罗茨风机提供,停用一台罗茨风机;煤粉制备系统停用袋式除尘器,废气一部分通过M9-26No14D 鼓风机入窑,一部分做为磨煤机的循环风从磨煤机的进料口入磨,在废气入窑和磨前的管道上均设有风门及配套的执行器,可以根据熟料窑火焰控制的需求来调整废气的入窑量,剩余入磨废气量大小对磨的操作不产生任何影响。
新增加的一台鼓风机和罗茨风机均采用变频调速,在操作上可实现对一次风和喷煤量的无级调控,满足生产需要。
具体工艺流程配置见图1b。
2、方案的可行性根据1#~4#回转窑运行情况来看,在回转窑正常操作时,M9-26No14D 鼓风机的转速为680~
720r/min,电流100~120A,喷煤管的一次风压力为2000Pa左右,新增加的鼓风机完全满足生产需要。
变频后的罗茨风机可以为转子秤提供18~40m/s风速的输送空气,来确保煤粉从各排转子室卸出。
同时由于电机采用变频调速,可以在生产过程中通过试验确
定满足转子秤输送煤粉的最低转速,确定后可保持该鼓风机的转速不变,通过调整转子秤电机转速来调整喷煤量,通过调整M9-26No14D鼓风机电机转速来调整一次风压力、风量,达到控制火焰形状的目的。
同时转子秤煤管与单风道喷煤管一次风流向之间夹角135°,通过文丘里管连接,采用负压操作,在两台风机出风口风道之间有转子秤转子相隔,因此,两台风机在运行过程中不会因出口风道并联和压力不平衡而产生“喘振”现象;煤粉制备系统停用布袋除尘器、废气分别入窑和磨煤机的方案在1#~4#窑已运行很长时间,有比较成熟的经验,不存在任何问题。
此外,离心风机的基础、设备、管网布置、煤粉制备系统的管网布置均可在不停回转窑的情况下提前进行,整个改造工作可随窑的检修同步进行施工,不需要额外增加改造时间。
三、改造效果
转子称系进口设备,单风道喷煤管配转子称作为熟料窑的煤燃烧系统使用,公司对其通过改造后,达到了提产降耗的目的,主要表现在以下几个方面:
①由于采用变频技术,窑前鼓风机和罗茨风机可以实现无级调速,其风量、压力同样可以实现无级调控,使得火焰形状的调整变得很容易。
②大幅度的改善窑况,使耐火砖的寿命得到很大的提高,其中5#窑的窑龄首次突破200天,改造前后窑龄对比见表1。
③改造后喷煤管火焰在正常操作时形状稳定,不易发散,在熟料烧结区可集中能量,均衡操作。
同时火焰长度增加近1m,可增加烧结反应长度,有利于稳定窑况和操作;产量大幅度提高,较改造前单台窑熟料产量提高4t/h,两台窑全年可多产氧化铝约2万t,经济效益显著。
另外,由于转子称和喷煤鼓风机采用变频调速,可任意调节火焰长度,在窑操作不稳定时,可迅速扭转、稳定窑况,条件具备时又可以迅速提产。
5去掉两台袋式除尘器,从根本上杜绝了发生煤粉着火的可能性,煤粉制备系统的安全可靠性大幅度提高。
⑤由于产量增加,单位熟料能源消耗由改造前的125kg标煤/t下降到101kg标煤/t,大大降低了能源消耗。
⑥停用两台罗茨风机,降低了噪声,有利于改善工作环境。
⑦整个技改投资约100万元,其中设备及备件费用为30万元,管道材料及制作费20万元,改造施工费30万元。
技改后年增产氧化铝2万t,按现行氧化铝价格4300元/t计算,除去各项成本,纯利润3000元/t,全年利润6000万元。
同时停用两台布袋收尘器,可降低运行及维护费用8万元,合计年获效益5908万元,改造后经济效益显著。
(end)。