第十三十四章铸造应力、变形及热裂
铸件应力及裂纹的种类

合理地调整合金成分(严格控制钢和铁中的硫、磷含量),合理地设计铸件结构,采用同时凝固的原则和改善型(芯)砂的退让性,都是防止热裂的有效措施。
(2)冷裂
① 冷裂的产生
冷裂是铸件冷却到低温处于弹性状态时所产生的热应力和收缩应力的总和,如果大于该温度下合金的强度,则产生冷裂。冷裂是在较低温度下形成的,其裂缝细小,呈连续直线状,缝内干净,有时呈轻微氧化色。壁厚差别大、形状复杂的铸件,尤其是大而薄的铸件易于发生冷裂。
② 冷裂的防止
凡是减小铸造内应力或降低合金脆性的措施,都能防止冷裂的形成。例如:钢和铸铁中的磷能显著降低合金的冲击韧性,增加脆性,容易产生冷裂倾向,因此在金属熔炼中必须严格加以限制。
3.铸件的变形与防止
如前所述,在热应力的作用下,铸件薄的部分受压应力,厚的部分受拉应力,但铸件总是力图通过变形来减缓其内应力。因此,铸件常发生不同程度的变形。铸件的变形往往使铸件精度降低,严重时可以使铸件报废,应予防止。因铸件变形是由铸造应力引起,减小和防止铸造应力的办法,是防止铸件变形的有效措施。
2.减小和消除铸造应力的措施
(1)合理地设计铸件的结构
铸件的形状愈复杂,各部分壁厚相差愈大,冷却时温度愈不均匀,铸造应力愈大。因此,在设计铸件时应尽量使铸件形状简单、对称、壁厚均匀。
(2)采用同时凝固的工艺
所谓同时凝固是指采取一些工艺措施,使铸件各部分温差很小,几乎同时进行凝固。因各部分温差小,不易产生热应力和热裂,铸件变形小。设法改善铸型、型芯的退让性,合理设置浇冒口等。同时凝固的示意图,该工艺是在工件厚壁处加冷铁,冒口设薄壁处。
(2)收缩应力
铸件在固态收缩时,因受铸型、型芯、浇冒口等外力的阻碍而产生的应力称收缩应力。、一般铸件冷却到弹性状态后,收缩受阻都会产生收缩应力。收缩应力常表现为拉应力。形成原因一经消除(如铸件落砂或去除浇口后)收缩应力也随之消之,因此收缩应力是一种临时应力。但在落砂前,如果铸件的收缩应力和热应力共同作用其瞬间应力大于铸件的抗拉强度时,铸件会产生裂纹。和共振时效等。所谓自然时效,是将铸件置于露天场地半年以上,让其内应力消除。热时效(人工时效)又称去应力退火,是将铸件加热到550-650℃,保温2-4h,随炉冷却至150-200T,然后出炉。共振法是将铸件在其共振频率下震动10-60ndn,以消除铸件中的残留应力。
铸造应力与变形169校标

铸件形成理论基础——铸造应力与变形铸造应力与变形1.铸造应力的形成2. 铸造应力的减小和消除3. 铸件的变形4. 变形的减小和消除内应力热应力机械应力由于铸件各部分冷却速度不同,以致在同一时期内收缩不一致,而且各部分之间存在约束作用,从而产生的内应力。
由于铸件的收缩受到机械阻碍而产生的,是暂时性的。
只要机械阻碍一消除,应力也随之消失。
相变应力合金在弹性状态下发生相变会引起体积变化。
若铸件各部分冷却速度不同,相变不同时进行,则由此而产生的应力称为相变应力。
铸造应力是热应力、机械应力和相变应力三者的代数和。
根据情况不同,三种应力有时相互叠加,有时相互抵消。
铸造应力的存在会带来一系列不良影响,诸如使铸件产生变形、裂纹,降低承载能力,影响加工精度等。
1. 铸造应力的形成1. 铸造应力的形成(1)热应力的形成过程厚壁部分或心部为拉应力,薄壁部分或表层为压应力。
铸件的壁厚差别越大(或壁厚越大),冷却速度越大,合金的线收缩系数越大,弹性模量越大,产生的热应力也越大。
1. 铸造应力的形成(2)机械应力的形成机械应力示意图1. 铸造应力的形成(2)机械应力的形成机械应力示意图(1)工艺方面a. 使铸件按“同时凝固”原则进行凝固。
b. 提高铸型和型芯的退让性,及早落砂、打箱以消除机械阻碍,将铸件放入保温坑中缓冷,减小铸造应力。
(2)结构设计方面尽量做到结构简单,壁厚均匀,薄、厚壁之间逐渐过渡,以减小各部分的温差,并使各部分能比较自由地进行收缩。
(3)时效处理 2. 铸造应力的减小和消除有缘学习更多+谓ygd3076考证资料或关注桃报:奉献教育(店铺)有缘学习更多+谓ygd3076考证资料或关注桃报:奉献教育(店铺)4. 变形的减小和消除(1)设计与铸造铸件壁厚设计要力求均匀;制定铸造工艺时,尽量使铸件各部分同时冷却,增加型(芯)砂的退让性等。
(2)反变形法(3)时效处理。
铸造变形与裂纹的原因分析【全面解析】

铸件在冷却过程中,其固态收缩受到阻碍时,就会在铸件内部产生应力,称为铸造应力,该应力是铸件产生变形、冷裂和热裂等缺陷的主要原因。
1.铸造应力的形成:铸造应力按产生原因的不同可分为热应力、相变应力和收缩应力。
(1)热应力:热应力是由于铸件壁厚不均匀,各部分的冷却速度不同,以致在同一时间内,铸件各部分收缩不一致而造成的.通常,热应力使铸件的厚壁处或心部受拉伸,薄壁处或表层受压缩.合金的固态收缩率越高、铸件的壁厚差越大,热应力也越大.预防产生热应力的基本途径是尽量减小铸件各部分的温度差,使铸件均匀地冷却.因此,设计铸件结构时,应尽量使铸件壁厚均匀,避免金属聚集,并在铸造工艺上采取必要的措施,如采取同时凝固原则.(2)相变应力:铸件各部位在不同的时间产生相变而引起的应力称为相变应力.(3)收缩应力:它是铸件收缩受到机械阻碍而形成的应力,因此又称为机械应力.形成机械阻碍的原因很多,如型砂舂得过紧,型砂或芯砂的高温强度太高、退让性差等.这种应力是暂时的,故又称为暂时应力.当机械阻碍的原因一经消失,应力即自行消失.由于铸件高温强度低,当应力超过其高温强度时,在应力集中的部位,容易产生裂纹(热裂).铸造应力是收缩应力、热应力和相变应力的综合.根据铸件的具体情况,三种应力有时互相抵消,有时互相叠加;有时是暂时存在,有时则残留下来.铸件冷却过程中所产生的铸造应力,如超过该温度下合金的屈服强度,则将产生残留变形;如超过其抗拉强度,则将产生裂纹.如在弹性强度范围内,则以残留应力的形式存在铸件内,这样就可能降低其机械强度;E——合金的弹性模量,MPa.测定铸件热处理后应力的消除程度时,可随铸件一起铸出两批应力框,其中一批不经热处理而测定其内应力值(如为σ1);另一批随铸件一起热处理,再测定其内应力值(如为σ2),应力消除的程度就可按下式算出:2.铸件的变形及其防止热应力是铸件产生变形和裂纹的内在原因.铸件的薄壁部分(或外层)冷却较快,残留有压应力,厚壁部分(或内层)冷却较慢,残留有拉应力.具有内应力的铸件处于不稳定状态,能自发地进行变形以减小内应力,使其趋于稳定状态.变形的结果将使铸件产生弯曲.细而长或大而薄的铸件,更易变形.为防止变形,应尽可能使铸件壁厚均匀或使之形状对称.对铸造工艺上应采取措施,力求使其同时凝固.有时,对长而易变形的铸件,在制模时,将木模制成与铸件变形相反的形状,用以抵消铸件产生的变形,这种方法称为反变形法.尽管铸件冷却时发生了一定的变形,但铸造应力仍难以彻底去除.经机械加工后,这些内应力将重新分布.铸件还会逐渐地发生变形,使加工后的零件丧失了应有的精度,严重影响机械产品质量.为此,不允许变形的重要铸件,必须采取自然时效或人工时效方法,将残留的内应力有效地去除.所谓人工时效是将铸件进行低温退火,它比自然时效节省时间,应用广泛.铸件的裂纹及其防止当铸造应力超过金属的强度极限时,铸件则发生裂纹.裂纹是铸件的严重缺陷,必须设法防止.1.热裂热裂是在凝固末期高温下形成的裂缝,其形状特征是裂纹短,缝隙宽,形状曲折,缝内金属呈氧化色(黄紫色).热裂是铸钢和铸铝合金件中常见的缺陷.为防止产生热裂,除了使铸件的结构设计合理外,还应合理地选择型砂或芯砂的黏结剂,以改善其退让性,大的型芯可制成中空的或内部填以焦炭.同时,应严格限制钢和铸铁中的含硫量,因为硫能增加热脆性,使合金的高温强度降低.2.冷裂冷裂是在较低温度下形成的,并常出现在受拉伸的部位,其裂缝细校呈连续直线状,缝内干净,有时呈轻微氧化色.壁厚差别大、形状复杂的铸件,尤其是大而薄的铸件容易发生冷裂.凡是减小铸造内应力或降低合金脆性的因素,均能防止冷裂的形成.钢和铸铁中,磷能显着降低合金的冲击韧性,增加脆性,因此,在熔炼金属过程中,必须对磷加以严格控制.。
3.3.2 铸件的变形、裂纹
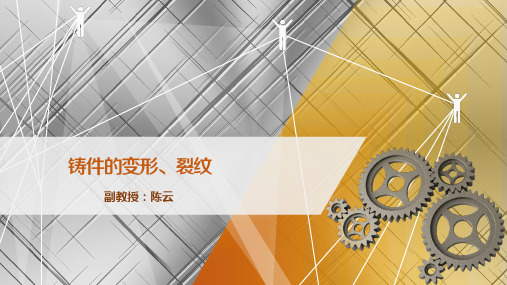
铸件的变形、裂纹副教授:陈云铸件的变形、裂纹变形裂纹残余热应力的存在,使铸件处在一种非稳定状态,将自发地通过铸件的变形来缓解其应力,以回到稳定的平衡状态。
当铸造内应力超过金属的强度极限时,铸件便产生裂纹(热裂纹与冷裂纹)。
一、铸件的变形具有残余应力的铸件是不稳定的,它将自发地通过变形来减缓其内应力,以便趋于稳定状态。
只有原来受拉伸部分产生压缩变形、受压缩部分产生拉伸变形,才能使残余内应力减小或消除。
厚部、心部受拉应力,出现内凹变形;薄部、表面受压应力,出现外凸变形车床床身的导轨部分厚,侧壁部分薄,铸造后导轨产生拉应力,侧壁产生压应力,往往发生导轨面下凹变形。
将一刚生产出来的圆柱体铸件,作如下加工:1、将铸件外表面车掉一层;2、将铸件心部钻一通孔;3、将铸件侧面切去一部分;问:在这三种情况下铸件会发生什么变化?防止变形的方法与防止铸造应力的方法基本相同。
此外,工艺上还可采取某些措施,如反变形法;对某些重要的易变形铸件,可采取提早落砂,落砂后立即将铸件放入炉内焖火的办法消除机械应力。
二、铸件的裂纹当铸造应力超过金属的强度极限时,铸件便产生裂纹,裂纹是严重的铸造缺陷,必须设法防止。
按裂纹形成的温度范围可分为热裂纹和冷裂纹两种。
1、热裂纹热裂纹是在凝固末期高温下形成的裂纹。
其形状特征是缝隙宽、形状曲折、缝内呈氧化色。
铝合金6061圆铸锭 100X热裂纹在金相分析上的形状表现为锯齿状裂开,裂纹弯曲、分叉或呈网状、圆弧状,断口位置处裂纹凹凸不平。
热裂纹一般分布在应力集中部位(尖角或断面突变处)或热节处。
防止热裂纹的方法:使铸件结构合理,减小浇、冒口对铸件收缩的机械阻碍,内浇口设置应符合同时凝固原则。
此外减少合金中有害杂质硫、磷含量,可提高合金高温强度,特别是硫增加合金的热脆性,使热裂倾向大大提高。
2、冷裂纹冷裂纹是铸件处于弹性状态即在较低温下形成的裂纹。
其形状特征是裂纹细小、连续直线状,有时缝内呈轻微氧化色。
铸件变形和裂纹

热裂纹的形成机理
液态金 属凝固 结晶
液固状态 固液状态
偏析
低熔点共晶 液态薄膜
脆性温 度区间
拘束
凝固收缩
应力与应变
凝固 裂纹
固相
固液
液固
塑 性δ
液相
a
b
T'S TS TB
T'H
TL
温度T
图11-47 金属凝固过程中的脆性温度区
TL-液相线 TS-固相线 TB-脆性温度区
凝固温度区间的影响
凝固温度区增大 温 度 /℃
中纹的的溶产解生度。比但在是δ当相中w 低>很0.多16, 16%(包晶点)时,磷的有害作用将超过硫,此时再增加wMn/wS比值对防止热裂纹已无意义。
碳在钢中是影响热裂纹的主要元素,并能加剧硫﹑磷及C其他元素的有害作用。
如%果(初包生晶相点为)γ时相,,磷则的析有出害作的 壁厚不均匀、形状复杂的大型铸件容易产生冷裂纹。
wC/%
凝固组织形态与偏析程度
增w加凝/w固比裂值纹对倾防向止。热裂纹已无 合理设置浇M冒口n ,尽S量使铸件各部分温度均匀。
意义。 它们既能增大凝固温度区间,与其他元素形成多种低熔点共晶,又是钢中极易偏析的元素。
热处理法 分析下列铸件内的纵向残余应力:
图11-54 Fe-C 相图的高温部分
提高铸型的预热温度可减小铸件各部分的温差;
铸件变形和裂纹
铸钢件生产技术课程
应力的形成
热膨胀 受阻 热应力(自身拘束)
温
或收缩
机 碍械 应阻 力(外部拘束)
度
受阻
变
固态相变
相变应力
化
(伴随比容变化)
加热
与冷 却
铸件开裂的原因

铸件开裂的原因
铸件开裂是在铸造过程中经常发生的问题,可能会造成产品质量下降甚至损坏。
下面将从几个方面分析铸件开裂的原因。
温度控制不当是导致铸件开裂的主要原因之一。
在铸造过程中,如果铸件冷却过快或温度变化过大,容易造成内部应力过大,从而导致铸件开裂。
因此,对于不同材料和结构的铸件,需要合理控制铸造温度和冷却速度,避免温度梯度过大造成应力集中。
金属液体的浇注方式也会影响铸件的质量。
如果浇注速度过快或浇注过程中存在气泡和气体混入,会导致铸件内部存在气孔和夹杂物,降低铸件的强度和韧性,容易发生开裂。
因此,在铸造过程中需要采取适当的浇注方式和控制浇注速度,确保金属液体充分填充模具且不受气体污染。
金属合金的成分和熔炼工艺也会影响铸件的质量。
如果金属合金成分不均匀或存在杂质,会导致铸件内部组织不均匀,容易出现晶粒过大或过小的情况,从而影响铸件的力学性能,导致开裂。
因此,在选择合金材料和熔炼工艺时,需要严格控制合金成分和熔炼温度,确保合金均匀混合且无杂质。
模具设计和制造也会对铸件开裂产生影响。
如果模具设计不合理或制造精度不高,会导致铸件表面粗糙或存在凹凸不平的情况,容易造成应力集中和裂纹产生。
因此,在模具设计和制造过程中,需要
考虑铸件的结构和形状,确保模具表面光洁度和精度要求,减少铸件在脱模过程中的变形和损伤。
铸件开裂是由多种因素综合作用导致的问题,需要在铸造过程中综合考虑温度控制、浇注方式、合金成分、模具设计等多个方面的因素,以避免铸件开裂的发生,提高铸件的质量和性能。
只有在铸造过程中严格控制每个环节,才能确保铸件的质量和稳定性,避免开裂等质量问题的发生。
铸造应力
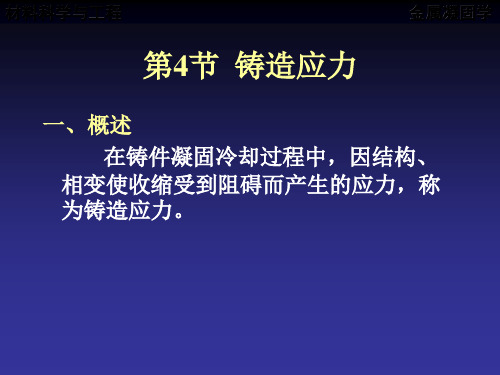
余热应力符号相同,而与铸件薄部或外部残余
热应力的符号相反,因此,冷裂容易在铸件厚 部和内部产生。 • 综合上述可见,铸造应力是热应力、相变应 力以及机械阻碍应力的总和。在某一瞬间,一
切应力的总和大于金属在该温度下的强度极限
时,铸件就要产生裂缝。
材料科学与工程
金属凝固学
五、减少及消除残余应力的方法
(一)减小措施和途径
材料科学与工程
金属凝固学
第5节 铸造变形
材料科学与工程
金属凝固学
材料科学与工程
金属凝固学
• 防止铸件产生变形的措施: • 提高铸型刚度,加大压铁重量,减小变 形; • 控制打箱时间; • 采取反变形措施; • 设置防变形箱(拉箱); • 改变铸件结构;
材料科学与工程
金属凝固学
第六节 冷裂纹
• 冷裂是铸件中应力超出合金的强度极限而产生的。 冷裂往往出现在铸件受拉伸的部位,特别是有应 力集中的地方。 冷裂纹的特征: • 温度:较低温度下产生; • 宏观:发亮、金属光泽的脆断特征; 裂口宽度0.001~0.01mm. 微观:一般晶间(或沿晶)断裂;
材料科学与工程
金属凝固学
二、铸件中的热应力
框形铸件中的动态应力分析
材料科学与工程
金属凝固学
影响残余热应力的因素
1. 合金性质方面 1) E , (1)弹性模量 2) , (2)膨胀系数 (3)合金的热导率 3) tH 2. 铸型性质 蓄热系数大,导致温差大,残余压力大 3. 浇注温度 t浇 铸件的冷却速度 t 4. 铸件结构 壁厚差 t
机械阻碍的来源大致有以下几个方面: (1)铸型和型芯有较高的强度和较低的退让性。 (2)砂箱内的箱档和型芯内的芯骨。 (3)设置在铸件上的拉杆,防裂筋,分型面上 的铸件飞边。 (4)浇冒口系统以及铸件上的一些突出部分。
铸造开裂原因及处理办法【实用版】

热裂纹常发生在铸件最后凝固并且容易产生应力集中的部位,如热节、拐角或靠近内浇口等处。
热裂纹分为内裂纹和外裂纹。
内裂纹产生在铸件内部最后凝固的地方,有时与晶间缩孔、缩松较难区别。
外裂纹在铸件的表面可以看见,其始于铸件的表面,由大到小逐渐向内部延伸,严重时裂纹将贯穿铸件的整个断面。
宏观裂纹:由于热裂纹是在高温下形成的,因此裂纹的表面与空气接触并被氧化而呈暗褐色甚至黑色,同时热裂纹呈弯曲状而不规则。
微观裂纹:沿晶界发生与发展,热裂纹的两侧有脱碳层并且裂纹附近的晶粒粗大,并伴有魏氏组织热裂纹形成的温度范围熔模铸件的热裂纹到底是在什么温度下发生的,长期以来说法不一.到目前为止归纳起来仍有两种:其一,热裂纹是在凝固温度范围内但接近于固相线温度时形成的,此时合金处于固-液态;其二,热裂纹是在稍低于固相线温度时形成的,此时合金处于固态。
热裂纹的防止措施1.提高铸件在高温时的强度与塑性(1)合理选材选材是一项极为复杂的技术和经济问题。
所渭合理选材就是选用的材质应该同时满足铸件的使用性、工艺性和经济性。
对于铸件而言,主要是铸造工艺性(热裂性、流动性和收缩性等)。
如果该材质的铸造工艺性能不佳,热裂倾向性大,那么浇注出来的铸件产生热裂纹的废品率就高。
(2)保证熔炼质量在铸钢合金成分中,最有害的化学成分是硫。
当wS>0.03%,以O.05%的临界铝含量脱氧,硫化物以链状共晶形式分布时,塑性很低,易引起热裂纹。
在熔炼时,可以加入适量的强脱硫剂稀土元素,以减少合金中的含硫量。
只要稀土元素的加入工艺合理,其脱硫效果为40%~50%:并且稀土元素能细化晶粒,改变夹杂物的形态与分布,从而减轻了热裂纹的程度(指裂纹的大小与深浅)和降低了热裂纹的数量。
另外,分布于铸钢晶界的低熔点夹杂物将降低它的强度和塑性,并且随着夹杂物的增多,强度和塑性下降,促使形成热裂纹。
在熔炼时,应选用干净、清洁的炉料;采用合理的熔炼工艺,加强操作,才能保证熔炼质量。
制品的应力、变形和裂纹

二、变形和裂纹
(一)铸件的变形 1.铸件中的挠曲变形 当铸件中的残余应力以热应力为主时, 铸件中冷却快的部分受压应力; 铸件中冷却慢的部分受拉应力。 受压部分产生拉伸变形,可减小应力; 受拉部分产生压缩变形,可减小应力。 因此产生挠曲变形。
二、变形和裂纹
(二) 铸件的裂纹 2. 冷裂 (1)特征:铸件处于弹性状态时,铸造应力超过了合金的强度
极限,裂纹呈连续直线或圆滑曲线形状,断口为穿晶断裂, 有金属光泽。 (2)影响因素: ➢ 合金性质:材质不同,强度不同,
增加脆性的元素和夹杂物,易冷裂 磷易在钢中形成磷共晶,易冷裂 ➢ 开箱时间:开箱早,温差大,热应力大,易冷裂 水爆清砂易产生冷裂纹
棒内存在残余拉应力。
谢 谢!
二、变形和裂纹
O
N
E
T字形梁铸件挠曲变形情况
机床床身变形示意图
二、变形和裂纹
铸件的变形示意图
释放应力 的过程伴 随着变形
过程
二、变形和裂纹
(一)铸件的变形 2. 防止变形的措施 (1)提高铸型的刚度 (2)延迟打箱时间 (3)采取反变形工艺 (4)设置变形筋 (5)改变铸件结构
二、变形和裂纹
当温度应力>σS ,冷却至室温
薄处先凝,受压 铸造应力框
厚处后凝 ,受拉
++-
t0~t1: t1~t2: t2~t3:
T T
1
H
1
2
T
塑性状态
临
T室 t
2 t t2
弹性状
态
t t3
11
01
铸造-应力、变形、冷裂
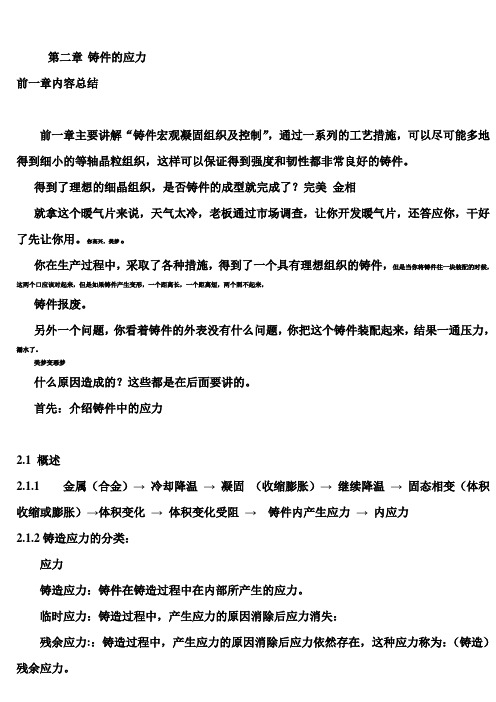
第二章铸件的应力前一章内容总结前一章主要讲解“铸件宏观凝固组织及控制”,通过一系列的工艺措施,可以尽可能多地得到细小的等轴晶粒组织,这样可以保证得到强度和韧性都非常良好的铸件。
得到了理想的细晶组织,是否铸件的成型就完成了?完美金相就拿这个暖气片来说,天气太冷,老板通过市场调查,让你开发暖气片,还答应你,干好了先让你用。
你高兴,美梦。
你在生产过程中,采取了各种措施,得到了一个具有理想组织的铸件,但是当你将铸件往一块装配的时候,这两个口应该对起来,但是如果铸件产生变形,一个距离长,一个距离短,两个照不起来,铸件报废。
另外一个问题,你看着铸件的外表没有什么问题,你把这个铸件装配起来,结果一通压力,漏水了。
美梦变恶梦什么原因造成的?这些都是在后面要讲的。
首先:介绍铸件中的应力2.1 概述2.1.1 金属(合金)→冷却降温→凝固(收缩膨胀)→继续降温→固态相变(体积收缩或膨胀)→体积变化→体积变化受阻→铸件内产生应力→内应力2.1.2铸造应力的分类:应力铸造应力:铸件在铸造过程中在内部所产生的应力。
临时应力:铸造过程中,产生应力的原因消除后应力消失:残余应力::铸造过程中,产生应力的原因消除后应力依然存在,这种应力称为:(铸造)残余应力。
以上两种应力是从时间上分类的。
按应力产生的原因有以下三种:热应力、相变应力、机械阻碍应力、关于这几种应力,我们在后面将逐一给以详细的介绍。
2.1.3应力对铸件的影响低于弹性极限:铸件中产生应力,同时在应力的作用下,产生有限的变形(弹性变形)高于屈服极限:铸件产生塑性变形;高于强度极限:铸件中出现裂纹。
因此,在这一章中,将应力、变形、裂纹放在一起讲解。
在应力的作用下,铸件如何变形和出现裂纹,也将在后面相应的章节中介绍。
2.2热应力:2.2.1概念热应力:铸件冷却过程中,由于各部分冷却速度不同,收缩时间及收缩量不同,铸件由于结构所限,相互制约,不能完成各自的理论变形,结果:在铸件内所产生的应力。
1.2.3 铸造应力、变形与裂纹解析

d) 设计结构时避免应力集中;
1.2.3 铸造内应力、变形及裂纹
本节内容回顾:
重点:铸造内应力的分布、形成及预防,变形和 裂纹的预防; 难点:铸造热应力的形成及分布规律,铸件的变 形规律——需理解 !
4)铸造内应力的预防 a)采用同时凝固的原则 同时凝固是指通过设置冷铁、 布置浇口等工艺措施,使铸件温差尽量变小,基本实现 铸件各部分在同一时间凝固,可有效降低4)铸造内应力的预防 b)提高铸型温度(对铸型进行预热) c)铸件壁厚设计均匀 d)改善铸型和型芯的退让性 e)进行去应力退火 预防热应力 预防机械应力
浇注温度 铸件结构 本节内容
铸造内应力、变形和裂纹
铸型条件
§1-2 金属液态成形的基本原理
1.2.3 铸造内应力、变形及裂纹
1、铸造内应力
铸造内应力——铸件固态收缩受到阻碍产生的内部应力。
铸件 冷却
受约束
完全冷却后 瞬时应力与 残余应力 应变 与变形
1)铸造内应力的种类
2)铸造内应力的形成原理 3)铸造内应力的预防
超过材料强度极限而引起的开裂。
冷裂常常出现在铸件形状复杂受拉
伸处,特别是应力集中部位。壁厚不均 匀、形状复杂的大型铸件容易产生冷裂 纹。
冷裂裂纹穿晶断裂,裂纹细小,外形呈 连续直线状或圆滑曲线状,裂纹缝内干 净,有时呈轻微氧化色。
铸件尖角部位的裂纹
1.2.3 铸造内应力、变形及裂纹
2)铸件裂纹的预防措施 a) 改善铸型的退让性;
§1-2 金属液态成形的基本原理
内容回顾
1)合金的流动性 2) 合金的充型能力
铸造热应力和热疲劳的产生、特点及其对构件使用性能的影响
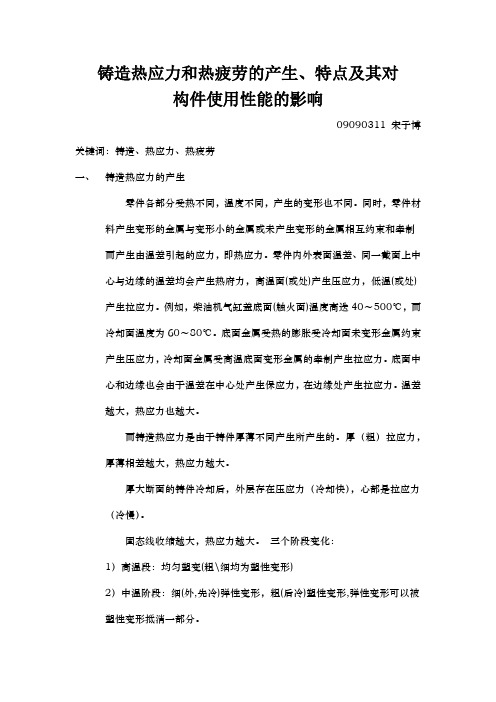
铸造热应力和热疲劳的产生、特点及其对构件使用性能的影响09090311 宋子博关键词:铸造、热应力、热疲劳一、铸造热应力的产生零件各部分受热不同,温度不同,产生的变形也不同。
同时,零件材料产生变形的金属与变形小的金属或未产生变形的金属相互约束和牵制而产生由温差引起的应力,即热应力。
零件内外表面温差、同一截面上中心与边缘的温差均会产生热府力,高温面(或处)产生压应力,低温(或处)产生拉应力。
例如,柴油机气缸盖底面(触火面)温度高迭40~500℃,而冷却面温度为60~80℃。
底面金属受热的膨胀受冷却面未变形金属约束产生压应力,冷却面金属受高温底面变形金属的牵制产生拉应力。
底面中心和边缘也会由于温差在中心处产生保应力,在边缘处产生拉应力。
温差越大,热应力也越大。
而铸造热应力是由于铸件厚薄不同产生所产生的。
厚(粗)拉应力,厚薄相差越大,热应力越大。
厚大断面的铸件冷却后,外层存在压应力(冷却快),心部是拉应力(冷慢)。
固态线收缩越大,热应力越大。
三个阶段变化:1)高温段:均匀塑变(粗\细均为塑性变形)2)中温阶段:细(外,先冷)弹性变形,粗(后冷)塑性变形,弹性变形可以被塑性变形抵消一部分。
3)低温段:均是弹性变形(温度不同,变形量不一致),导致残余应力的产生。
结果:残余应力的分布情况:细(先冷)的最后被压缩,粗的(后冷)被拉伸。
二、铸造热应力的特点对构件使用性能的影响1. 热应力随约束程度的增大而增大。
由于材料的线膨胀系数、弹性模量与泊桑比随温度变化而变化,热应力不仅与温度变化量有关,而且受初始温度的影响。
2. 热应力与零外载相平衡,是由热变形受约束引起的自平衡应力,在温度高处发生压缩,温度低处发生拉伸形变。
3. 热应力具有自限性,屈服流动或高温蠕变可使热应力降低。
对于塑性材料,热应力不会导致构件断裂,但交变热应力有可能导致构件发生疲劳失效或塑性变形累积。
4. 定向凝固时,由于铸件各部分冷却速度不一致,产生的热应力较大,铸件易出现变形和裂纹。
铸造应力的产生、危害及防治措施

金属在凝固冷却的状态时,热胀冷缩引起的体积变化受到来自外界或其来自于本身的制约,就会导致其变形过程受到阻碍,就会产生一个铸造应力。
铸造的方法就是将加热熔融为液体的合金倒入事先准备好的模具中去使其填充满,等到热的液体变冷凝固以后,就得到链初步的毛坯产品。
除此之外,在整个铸造生产的过程中,特别是对于单件进行小批量的生产,如果工人的劳动条件较差、且劳动强度大,铸造的应用过程也会受到一定程度的限制。
铸造应力是当一个铸件冷却到其弹性状态之后,在收缩过程中会受到阻碍,进而产生的一种弹性应力。
铸造应力如果存在于机械设备中,会导致设备的结构强度降低,承载能力下降,使用寿命缩短等。
但通常我们讲的铸造应力一般指的是残余应力。
当铸件有残余应力存在的时候,铸件经过机械加工之后就有可能产生一个新的变形,导致零件的精准度降低、尺寸变差;如果铸件的工作应力和残存应力进行叠加就会损坏到铸件;倘若残存应力一直存在与铸件之内,经过长时间的积累之后就会使得铸件发生形变;如果铸件长时期处的环境都是潮湿有腐蚀性的空气中,那么时间长了以后就可能会让铸件被腐蚀掉。
所以,在浇注完毕的冷却过程中对与铸件中残存的应力的消除的研究是十分有必要的,这对于提升铸件的工艺品质是极其重要的。
当一个铸件凝固之后,伴随着温度的下降,铸件都会变为固态在这个过程中会发生相变,随着铸件变为固态的相变过程,相变体也会发生收缩或者膨胀的过程,由于铸件较为厚的外壁存在,所以外层的温度下降的很快,内层的温度下降的慢,所以壁厚越厚冷却用时越长。
这种现象致使一个完整的铸件的内层和外层以及薄厚不一样的地方的收缩程度不一样,这样的现象会影响到铸件的薄厚和内外层之间发生相互牵制的作用,导致铸件拉深或者发生不可逆的形变。
热应力现象就是由于铸造过程中铸件壁的薄厚不一致在相同的单位时间内它们收缩的程度不同而产生的一种现象。
要去研究热应力形成的条件,需要对金属在冷却的进程中内部的应力是如何进行分布的。
铸造内应力、变形和裂纹
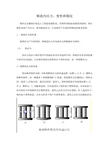
铸造内应力、变形和裂纹铸件完全凝固后便进入了固态收缩阶段,若铸件的固态收缩受到阻碍,将在铸件内部产生应力,称为铸造应力。
它是铸件产生变形和裂纹的基本原因。
1.铸造应力的形成按照应力产生的原因,将铸造应力分为热应力和机械应力两种。
(1)热应力热应力是由于铸件壁厚不均或各部分冷却速度不同,使铸件各部分的收缩不同步而引起的。
它在铸件落砂后仍然存在于铸件内部,是一种残留应力。
1)残留热应力的形成现以框形铸件为例,分析残留热应力的形成过程。
如图3.12中 1) 图所示的框形铸件,由一根粗杆I和两根细杆II组成。
假设铸件完全凝固后,两杆从同一温度T固开始冷却,最后达到同一温度T,两杆的固态冷却曲线如图3.12中2) 图所示。
Tk为临界温度,在此温度以上铸件处于塑性状态。
在此状态下,较小的应力可使铸件发生塑性变形,变形之后应力可自行消除;在Tk温度以下,铸件处于弹性状态,在应力作用下将产生弹性变形,变形之后应力还继续存在。
下面用图3.12中图2)所示的冷却曲线来分析热应力的形成过程。
当铸件处于高温阶段(t0-t1)时,两杆都处于塑性状态,尽管此时两杆的冷速不同、收缩也不同步,但瞬时的应力可通过塑性变形来自行消失,在铸件内无应力产生;继续冷却,冷速较快的杆II进入弹性状态,粗杆I仍然处于塑性状态(t1-t2),此时由于细杆II的冷速较快、收缩较大,所以细杆II会受到拉伸,粗杆I会受到压缩(图b),形成暂时内应力,但此内应力很快因粗杆I发生了微量的受压塑性变形而自行消失(图c);当进一步冷至更低温度时(t2-t3),两杆均进入了弹性状态,此时由于两杆的温度不同、冷却速度也不同,所以二者的收缩也不同步,粗杆I的温度较高,还要进行较大的收缩,细杆II的温度较低,收缩已趋于停止,因此粗杆I的收缩必定受到细杆II的阻碍,使其收缩不彻底,在部产生拉应力;而杆II则受到杆I因收缩而施与的压应力(图d)。
直到室温,残留热应力一直存在。
- 1、下载文档前请自行甄别文档内容的完整性,平台不提供额外的编辑、内容补充、找答案等附加服务。
- 2、"仅部分预览"的文档,不可在线预览部分如存在完整性等问题,可反馈申请退款(可完整预览的文档不适用该条件!)。
- 3、如文档侵犯您的权益,请联系客服反馈,我们会尽快为您处理(人工客服工作时间:9:00-18:30)。
§ 11.1.2 固态有相变的合金瞬时应力的发展过程
§ 11.1.3 铸件在冷却过程产生的机械阻碍应力
§ 11.1.4 影响残余应力因素
§ 11.1.5 减小或消除铸造应力的途径
东北大学材料加工工程
下一内容 上一内容 主目录
2020/4/10
5
§ 11.1.1 固态无相变的合金瞬时应力的发展过程
c. 机械阻碍应力(mechanism hindered stress):铸件收缩受 到铸型、型芯、箱挡和芯骨等机械阻碍所产生的应力。(临时)
B. 按应力存在的时间分:
a.临时应力(temporary stress):产生应力原因消失,应力便消 失。
b.残余应力(residual stress):产生应力原因消除后,仍然存在
的应力。
东北大学材料加工工程
下一内容 上一内容 主目录
2020/4/10
§ 11.1 铸件在冷却过程中产生的应力 4
早在1867年俄国学者卡拉库特斯基就研究了铸钢 锭内产生的应力。1907年德国学者Heyn对参与应力的 产生进行了系统的分析。我们站在前人研究的基础上 对他们的理论进行修正。下面从以下几个方面进行讲 解:
压应力,杆I 内为拉应力。
阶
应该指出,合金在高温时,特别是
段
在固相线以上,屈服极限很低,铸件内
产生的应力很容易超出屈服极限,发生
塑性变形,使完全卸载时刻早于τ3。
下一内容 上一内容 主目录
2020/4/10
§ 11.1.1 固态无相变的合金瞬时应力的发展过程 8
线收缩开始
温度
Байду номын сангаас第三阶段(τ2~τ3):两杆的温差逐渐减
小,到τ2时,温差又减小到Δt H。在此阶
段,杆I的冷却速度大于杆Ⅱ,即杆I的自
由线收缩速度大于杆Ⅱ。从τ2到τ3,两杆 自由线收缩量的差值为:
第 三
l2 (tH tmax )L l1
从上式可以看出,从τ1到τ3,两杆的 自由线收缩量相等。因为假定铸件只产
生弹性变形,所以到达τ3时,两杆中的应
阶
力值均为零。这样,在第三阶段,两杆
段
中的应力逐渐减小,到τ3时,铸件处于完 全卸载状态。
东北大学材料加工工程
下一内容 上一内容 主目录
2020/4/10
a. 热应力(thermal stress):铸件厚薄不同, 在凝固、冷却过程 中,冷速不同,造成各部分收缩量不一致,铸件各部分彼此制 约,产生的应力。
b. 相变应力(phase transformation stress):合金发生固态相 变,由于各部冷却条件不同,达到相变点的时刻不同,且相变 的程度也不同而产生的应力。
变化。 3) 铸件不产生挠曲变形。
Ⅲ
4) 铸件收缩不受铸型阻碍。 5) 横梁Ⅲ是刚性体。
ⅡI Ⅱ
东北大学材料加工工程
下一内容 上一内容 主目录
2020/4/10
6
§ 11.1.1 固态无相变的合金瞬时应力的发展过程
图b为杆I和杆Ⅱ的冷却曲线。开 始冷却时,两杆具有相同的温度tL, 最后又冷却到同一温度t0。由于杆 I较厚,冷却前期杆Ⅱ的冷却速度 大于杆I,而后期必然是杆I的冷却 速度比杆Ⅱ快。在整个冷却过程 中,两杆的温差变化如图c所示。 瞬时应力的发展过程可分四个阶 段加以说明,如图d所示。
在不考虑机械阻碍时,该合金铸件中的瞬时应力就是热应力。 以应力框为例(图),讨论瞬时应力的发展过程。
应力框由杆I,杆Ⅱ以及横梁Ⅲ组成。为便于讨论,作如下 假设:
1) 金属液充满铸型后,立即停止流动,杆I和杆Ⅱ从同一温
度tL开始冷却,最后冷却到室温t0。
2) 合金线收缩开始温度为ty,材料的收缩系数α不随温度
§ 11.1 铸件在冷裂过程中产生的应力 § 11.2 铸件的变形 § 11.3 铸件的冷裂
东北大学材料加工工程
下一内容 上一内容 主目录
2020/4/10
基础知识
3
铸造应力(casting stress):金属在凝固和冷却过程 中体积变化受到外界或其本身的制约,变形受阻,而 产生的应力。
A. 按应力形成的原因分:
§ 11.1.1 固态无相变的合金瞬时应力的发展过程 9
线收缩开始 温度
第四阶段(τ3~τ4):杆I的冷却速度仍 然比杆Ⅱ快,即杆I 的自由线收缩速度大
于杆Ⅱ。从τ3到τ4两杆自由线收缩的差值
为:
l3 tH gL
第
在此阶段,杆I 被拉长,故产生拉应
四
力,杆Ⅱ则相反,产生压应力。到τ4时 (室温),铸件内存在残余应力,杆Ⅱ内为
线收缩开始 温度
架尚未形成。显然,此时铸件的变形由
杆Ⅱ确定,杆Ⅱ带动杆I一起收缩。到τ1
时,两杆具有同一长度,温差为ΔtH,铸
第第
件不产生应力。
一二
第二阶段(τ1~τ2):tⅡ<ty ,tⅠ<ty。此时杆 I温度也已降到ty以下,开始线收缩,在τ1
时两杆具有相同长度。在以后的冷却过程
中,两杆的温差沿图c中ab变化,到τ2时
近期的研究工作表明,合金的温 度低于液相线以后,其变形由弹 性变形、塑性变形和粘弹性变形 组成,且以弹性变形为主。这样, 铸件在冷凝过程中,收缩一旦受 阻,就产生应力。
东北大学材料加工工程
下一内容 上一内容
主目录
2020/4/10
§ 11.1.1 固态无相变的合金瞬时应力的发展过程 7
第一阶段(τ0~τ1):tⅡ<ty ,tⅠ>ty。杆Ⅱ开始 线收缩,而杆I仍处于凝固初期,枝晶骨
2020/4/10
材料加工工程 林晓娉(教授)
材料加工工程 Material Processing
2
铸造应力、变形及冷裂
铸造应力和铸件的变形对铸件质量的影响很大。铸造应力是铸件生产 、存放、加工以及使用过程中产生变形和裂纹的主要原因,它降低铸件 的使用性能。因此对铸造应力的产生及释放过程进行研究,有助于我们 对铸造相关知识的认识,同时能够在一定程度上探索提高铸件质量,缓解 (防止)铸造应力所致缺陷的产生。本章将主要讲解以下内容:
两杆温差最大,为Δtmax。从τ1到τ2,两自 由线收缩量的差为:
阶阶 段段
l1 (tmax tH )L
杆Ⅱ要比杆I多收缩l1,但两杆彼此相连,
始终具有相同的长度。因此,杆Ⅱ被拉
长,杆I被压缩。这样在杆Ⅱ内产生拉应
力,在杆I内产生压应力。到τ2时,应力达
极大值,该阶段为应力增长阶段。
东北大学材料加工工程