流程模拟技术在常减压蒸馏装置上的应用
常减压装置仿真实训报告

常减压装置仿真实训报告一、引言常减压装置是石油化工企业中非常重要的设备之一,主要用于将原油进行减压蒸馏,分离成不同沸点的油品。
为了让我们更好地了解常减压装置的工作原理和操作流程,学校安排了常减压装置仿真实训课程。
通过仿真实训,我们能够在实际操作中掌握常减压装置的基本知识和技能,提高自己的实践能力和操作水平。
二、仿真实训内容在仿真实训中,我们首先通过计算机模拟软件了解了常减压装置的基本结构和流程。
随后,我们进行了以下操作:1. 原油的预处理:通过加入破乳剂和水,对原油进行破乳和脱水处理,以去除其中的水和杂质。
2. 加热和蒸馏:将处理后的原油加热,使其沸腾并分离成不同沸点的油品。
在这一过程中,我们需要注意控制温度和压力,保证分离效果和产品质量。
3. 冷却和收集:将蒸馏后的油品进行冷却,收集不同温度下的油品并进行检测。
4. 废水处理:对产生的废水进行处理,以去除其中的油和杂质,达到环保要求。
在操作过程中,我们需要注意安全问题,如防止火灾、爆炸和中毒等事故的发生。
同时,我们还需要关注设备的维护和保养,保证设备的正常运行和使用寿命。
三、实训收获通过这次仿真实训,我深刻认识到了常减压装置在石油化工企业中的重要性和作用。
同时,我也掌握了一些基本的操作技能和实践经验,对自己的专业素养和实践能力有了更进一步的提升。
此外,我也意识到了在操作过程中需要注意安全问题,增强了自己的安全意识和环保意识。
四、建议和展望在未来的学习和工作中,我希望能够进一步加强理论与实践的结合,不断提高自己的专业素养和实践能力。
同时,我也希望能够有更多的机会参与到实际操作中去,积累更多的实践经验。
最后,我希望学校能够继续加强仿真实训课程的建设和管理,提高实训效果和质量,为我们未来的职业发展打下坚实的基础。
常减压装置仿真实训系统操作说明书.

一、工艺流程1. 1装置概况本装置为石油常减压蒸馏装置,原油经原油泵(P-1/1. 2)送入装置,到装置内经两路换热器,换热至120℃,加入一定量的破乳剂和洗涤水,充分混合后进入电脱盐罐(V1)进行脱盐。
脱后原油经过两路换热器,换热至235℃进入初馏塔(T1)闪蒸。
闪蒸后的拔头原油经两路换热器,换热至310℃,分四股进入常压塔加热炉(F1)升至368℃进入常压塔(T2)。
常压塔塔底重组分经泵送到减压塔加热炉(F2)升温至395℃进入减压塔(T4)。
减压塔塔底渣油经两路换热器,送出装置。
1. 2工艺原理 1. 2. 1原油换热罐区原油(45℃)经原油泵P -1/1. 2进入装置,分两路进行换热。
一路原油与E -1(常顶气)、E-2(常二线)、E-3(减一线)、E-4(减三线、E-5(常一线、E-6(减渣油换热到120℃;二路原油与E -14(常顶气)、E -16(常二线、E -17(减二线换热到127. 3℃。
两路原油混合换热后温度为120℃,注入冷凝水,经混合阀(PD I C -306)充分混合后,进入电脱盐罐(V -1 进行脱盐脱水。
脱后原油分成两路进行换热,一路脱后原油与E -7(常二线、E-8(减二线、E -9/1. 2(减三线、E-10/1~4(渣油换热到239. 8℃;二路脱后原油与E -11/1. 2(减一中)、E-12/1. 2(常二线、E--13/1. 2(减渣换热到239. 7℃。
两路脱后原油换热升温到230℃合为一路进入初馏塔(T -1 汽化段。
初馏塔塔顶油气经空冷气(KN -5/1~5)冷凝到77℃,进入初顶回流罐(V-2)。
油气经分离后,液相用初顶回流泵(P-4/1. 2)打回初馏塔顶作回流,其余油气继续由初顶空冷器(KN -1/1~3)、初顶后冷器(N-1)冷却到40℃,进入初顶产品罐(V -3 。
初馏塔侧线油从初馏塔第10层用泵(P-6/1. 2)抽出与常一中返塔线合并送到常压塔第33层塔盘上。
流程模拟技术在生产计划优化系统中的应用

adPt c e cl dl g ytm ) ,这 些 系 统 为 n er hmia Moei s o nS e 等
石化企业在选购原油 、加工方案优化 、优化调合产 品结构 、制定生产计划和调度排产等方面起到 了重 要 作 用 ,为 石 化企 业 带 来 了很 大 的利 润 ¨’ 。 生产计划优化系统基于线性规划理论 ,其核心 是 生产计划模型 ,模 型涵盖原料进厂 、装置生产 、 产 品调 合 、产 品销 售 、多 周 期 库 存 、公 用 工 程 消 耗 等。计划模型 中,各装置 的侧线物料收率数据 以及 物料性质数据 的准确性是保证模型计算结果准确 的 基 础 。 尤 其是 常减 压 蒸 馏 装 置 ,作 为 炼 油 厂 生 产
理论板数为 1 。经过计算 调整 , 5 确定各物料进出塔
的位 置 。常 一 线 汽提 塔 设 置 为 4块 理 论板 ,常 二线 汽 提塔 设 置 为 3块 理论 板 ,常 三 线汽 提 塔 设置 为 2
块理论板 。按照 I 套蒸馏装置的实际生产流程 ,建 立模 型 ,选 择 装 置 的标 定 数 据 进 行 流程 模 拟模 型 的
选 取 陆 丰 、番 禺 、大 港 3种 原 油作 为可选 油 种 ,进
3 研 究 方 法
为解 决 这些 问题 ,提 出用 流 程模 拟 系统 P OI R / I 和 生 产计 划 优化 系统 R MS 相 结合 的解 决方 案 ~ P
“
。
行 计算 。 套 蒸 馏装 置 对 这 几 种原 油 没 有进 行 过 单 独 I 加 工 ,所 以确 定 其 中一 种 原 油 的侧 线 收率 和 性 质是
基于流程模拟软件的原油常压蒸馏塔的节能优化

对于求解一般 的线性 和非 线性 约束 函数 的效 率较
高, 能够解决一般的优化 问题 。 虽然 H ny e Q oe lS P优化器具 有很多优点 , w l 但是
还 存 在 以下 不 足 之处 :
() 1 优化器种类有 限 , 优化 方法不灵活 , 不能对 已有优化算法作改进 ; () 2 自身所 带的优化器经过一 次运行不能寻找
殷 卫兵 齐 , 峥 罗雄麟 赵 , , 辉
( . 国石 油 大 学 自动 化 系 , 京 124 2 中 国石 油 大 港 石 化 公 司 信 息 中心 , 津 30 8 ) 1中 北 0 29;. 天 0 20
摘 要 : 以 H ny e 公 司 流 程 模 拟 软 件 U ii 对 常 压 塔 进 行 流 程 模 拟 为 基 础 , 软 件 自带 的 H ny e o ew l l nSm 用 oew l l
优化 , 该方法可以达到更好 的优化 目标 。 2 常 压 塔 流 程模 拟 ( 图 1 见 )
BOt —D r t aw
图 1 常 压 塔 子 流 程
用 于优 化 的过 程 模 型 通 常 可 分 为 两 种 , 一 种 第
收稿日 21. - ( 期: 01- 修改稿) 0 23 0
系 统 , 置 数学 模 型 的建 立 非 常 复 杂 , 就 使 得 针 对 装 这
该装置的操作优 化极 为困难 , 流程模 拟的 出现很 好地解决了这一问题 , 利用 计算机 流程模 拟建 立常 减压蒸馏 装置 的模 型 , 在此 基础上进 行能量 目标 的
种改进的遗传算法应 用到常压塔模 型上进行流程
需要在工艺现场进行大量数据测试 , 时间周期较长。 此外 , 在建立数学模 型或进行模 型辨 识之前还 需要
模拟常减压蒸馏装置的物性计算方法和模型结构

模拟常减压蒸馏装置的物性计算方法和模型结构郑刚【摘要】Property calculation method has great effect on the accuracy of the CDU simulation re-sults,especially for the vacuum column. It is often observed that the simulated flow rate of vacuum resi-due is lower than the test-run data. This paper introduces a relatively more convinced methodology to simulate CDU using Aspen Plus. Based on a set of CDU test-run data,an Equation-Oriented model is built and solved in reconciliation mode on the Aspen Plus V10 Platform. Comparing the different results among the different property methods,the most accurate property method for CDU is presented. Finally the in-fluence of different property methods on the analog computation results of CDU is explained theoretically.%不同物性计算方法对常减压蒸馏装置的模拟,尤其对减压塔模拟的准确性影响较大.实践中常遇到模拟计算的减压渣油流量值低于现场实际数据的情况.采用 Aspen Plus 软件,结合某炼油厂常减压蒸馏装置的标定数据,建立了联立方程法(EO)模型.在数据整定(Reconciliation)模式下,通过选用不同的物性计算方法和建立特殊的减压蒸馏装置模型结构,给出了在Aspen Plus软件中模拟常减压蒸馏装置误差最小的物性计算方法,并从理论上解释了不同物性计算方法对常减压蒸馏装置模拟计算结果的影响.【期刊名称】《石油炼制与化工》【年(卷),期】2018(049)007【总页数】7页(P100-106)【关键词】常减压蒸馏;流程模拟;物性计算方法;Maxwell-Bonnell;序贯模块法;联立方程法;减压深拔【作者】郑刚【作者单位】中国石油化工股份有限公司炼油事业部,北京 100728【正文语种】中文随着计算机软硬件技术的高速发展,流程模拟技术已逐渐被大专院校、研究设计单位、企业各级管理部门及工艺工程师所掌握。
流程模拟技术在常减压装置上的应用

塔底油 5 %点馏出温度逐渐升高 , 常压拔 出率增 大; 随常压塔底吹汽量增大 , 常压塔底油 5 %点馏
出温度逐渐升高, 常压拔出率增大, 但常压炉 出口
温度提到一定温度 时 , 油 的 5 常底 %温 度变 化趋 于 平缓 , 从操作费 用和 经济效 益 综合 考虑 , 压炉 出 常 口温度 控制 在 35— 7 ̄ 6 30C比较合 适 , 底 吹 汽 为 塔 自产 03 a 汽 , .MP 蒸 塔底 吹 汽控 制在 6 0— .th . 70/
高, 油 5 渣 %点 温 度 逐 步 提 高 。但 过 高 的炉 温 将
馏 出 景 ,
图 2 减 压塔 主要产 品馏程标定分析数据与 模拟计算数据对 比图
增加装置的能耗 , 同时引起油品裂化。通过初步 模拟 , 得出减压炉 出口温度和塔顶真空度对减底
油5 %点馏 出温 度的影 响 曲线 , 图 4 见 。
4。 7
枷
合装置实际运行工况 , 初步确定 了优化 目标和具 体内容。
;
d0 5 一 … 一一 一 ~ 一一 一 —— —— …
2 1 常压炉 出 口温 度、 . 常压塔底 吹汽量与 常底油 5 %点馏 出温度之间的关系
从标 定数 据 看 , 置 目前 常底 重 油 中 30C 装 5  ̄
前 言
中国石化股份有限公司九江分公司 I 套常减 压装 置经过 技术 改造 于 20 0 8年 3月 1 7日一次 开
车成 功 , 加工 能力 达 到 50 / 。为进 一 步 优 化 .Mta
表 1 各塔实际操作数据与模 拟计 算数 据对 比
生产 , 降低装置能耗 , 提高轻油收率和经济效益 , 20 0 8年 4月 2 0日至 4月 2 9日在 石化盈 科上海 分
常减压蒸馏装置的常压系统流程模拟

1 模拟流程
常压 系统 的工 艺 流程 如 图 1 所示 , 主要 设 备有 原 油混合 器 ( M1 ) 、 常压加 热炉 ( E 1 ) 和常压 塔 ( T 1 ) 。 如 图 1所示 , 常 压塔 由 2 4层 塔板 构 成 , 常压 塔
的进 料 为常压 加 热炉 加热 到 3 6 2  ̄ C 的拔头 Байду номын сангаас 从 常压
( 天 津 渤 海 职 业技 术 学院 , 天津 3 0 0 4 0 2 )
摘要 : 常 减压 蒸馏 装置 是石 油 炼制过 程 的龙 头装 置 , 常减 压蒸馏 的操 作条 件 以及产 品 的馏 出率 不仅 影 响下 游的 生产过程 , 而且对 炼油厂 的 能耗 有很 大影 响 。针 对我 国某 常减压 蒸馏装 置 由于加 工的原 料 由国 内原 油 变为 国外原 油 , 原 有 的操 作条件 使得 常减压 蒸馏 装 置的馏 出率低且 能耗 高的特 点 , 对
常减压 蒸馏装 置进 行常压 系统的流 程模拟 , 模 拟结 果对 实际 生产过程 的优化 改 造起到 指 导作 用。
关键 词 : 常减 压蒸馏 ; 常 压塔 ; 流程模 拟 ; 中段取 热 d o i : 1 0 . 3 9 6 9 / j . i s s n . 1 0 0 8 - 1 2 6 7 . 2 0 1 3 . 0 4 . 0 1 3
热到一定温度后 ,再进到常压加热 炉加 热 到要求
的温 度 ,常 压 加 热 炉 出 口达 到 一 定 温 度 和 气 化 率 的原油 , 进 到常 压 塔 的进 料段 , 油气 往 上走 , 常压塔 侧线 抽 出 , 一至 四个左 右 的侧线 产 品 , 为
控 制侧 线产 品的干 点 ,抽 出的侧线 产 品进 到侧 线 产 品 汽 提 塔 中气 提 , 冷 却 后 出装 置 , 塔 底抽 出常
原油常减压蒸馏装置流程的参数模拟分析

Plus模拟 软件 实 现模 拟计算 ,实 现原有 常 减压 蒸馏 产 的柴 油 密 度 较 轻 。T 艺 流 程 为 :将 混 合 原 油在
装 置 能耗 的 降低 ,提 高生 产效 率 。
40 自 装 料 区 将 设 备 投 入 ,将 混 合 原 油 加 热
要想使装置满足不 同的操作需求 ,就要全面优化常减压蒸 馏装置操作参数 ,以此解决实 际生 产中的问题。基于
此 ,本文就分析原油常减压蒸馏装置 中的运行参数 ,之后实 现装 置的优化。
关 键 词 :原油 ;常减压蒸馏装置 ;流程 ;参数模拟
中图分类号 :TQ053 文献标 识码 : A
文章编 号: 1671—0460(2018)08—1749—04
Sim ulation A nalysis on the Process Param eters of Crude Oil Atm ospheric and Vacuum Distillation Unit
H UANG M ing—hui,CHIHong-yan (Ref ining& Chemical Plant ofYumen Oilf ield Company,Gansu Jiuquan 735200,China)
精 制 成为 合格 的产 品 。常减 压装 置 属 于炼 油厂 中最 加 工 的石油 为 四种 愿油 的组 合 。炼 油 厂 中设 备的蒸
大的耗能装置 ,占据炼油总耗能的 30%左右 ,所 以 馏工 艺 完善 ,能够 正 常运 行 ,设 备 主要 包括 初馏 塔 、
使此装置能耗进一步降低 ,对于炼油厂节能降耗具 常压 塔 和减 压 塔 。其 中的 产 品具 有 多种 种类 ,根据
第 47卷 第8期 2018年 8月
流程模拟技术在常减压蒸馏中的应用
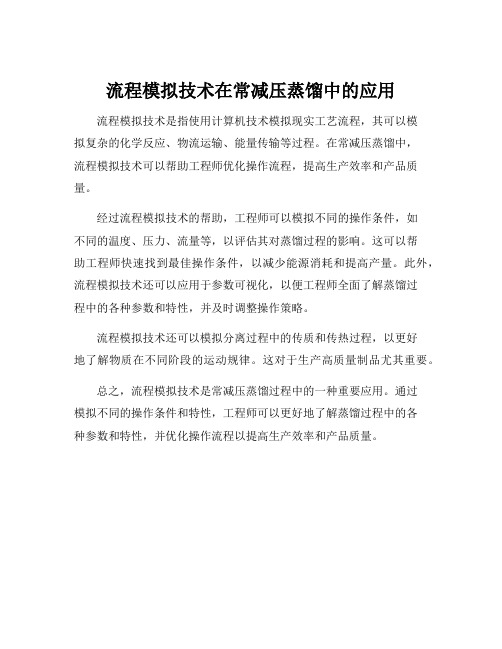
流程模拟技术在常减压蒸馏中的应用
流程模拟技术是指使用计算机技术模拟现实工艺流程,其可以模
拟复杂的化学反应、物流运输、能量传输等过程。
在常减压蒸馏中,
流程模拟技术可以帮助工程师优化操作流程,提高生产效率和产品质量。
经过流程模拟技术的帮助,工程师可以模拟不同的操作条件,如
不同的温度、压力、流量等,以评估其对蒸馏过程的影响。
这可以帮
助工程师快速找到最佳操作条件,以减少能源消耗和提高产量。
此外,流程模拟技术还可以应用于参数可视化,以便工程师全面了解蒸馏过
程中的各种参数和特性,并及时调整操作策略。
流程模拟技术还可以模拟分离过程中的传质和传热过程,以更好
地了解物质在不同阶段的运动规律。
这对于生产高质量制品尤其重要。
总之,流程模拟技术是常减压蒸馏过程中的一种重要应用。
通过
模拟不同的操作条件和特性,工程师可以更好地了解蒸馏过程中的各
种参数和特性,并优化操作流程以提高生产效率和产品质量。
常减压装置的全流程模拟

常减压装置的全流程模拟【摘要】本文介绍了使用Petro-SIM V3.0桌面炼油厂模拟软件构建公司Ⅰ常减压装置的主要过程,通过分析模型的优缺点,并结合当前加工新油种的需求,给出了模型的几个应用实例,从而表明严格精确的模型能够明显提高生产运行和管理水平。
【关键字】常减压流程模拟 Petro-SIM一、前言在炼油厂中,常减压装置处于加工链的最上端,常减压装置因为加工量大,加工方案和加工油种经常改变,因此确保常减压装置的稳定优化操作对于炼油企业总体技术经济指标以及下游装置来说意义重大。
随着现代计算技术的突飞猛进,使用软件来模拟蒸馏过程的技术也已经日益成熟。
目前设计部门已经普遍采用模拟软件来设计常减压装置,而生产、计划、调度、质检等部门也逐步开始使用这类工具指导和预测日常生产,分析和故障排除。
可以预计在不久的将来,软件模拟技术将在各炼厂得到迅速推广和应用。
二、模拟软件简介目前大型通用模拟软件有Aspen Plus,Aspen Hysys,SimSci ProII以及KBC Petro-SIM。
这些软件在模拟蒸馏设备方面都很成熟,而且各有优点。
本文采用KBC Petro-SIM软件进行常减压装置的全流程建模,因为采用这个软件能够很方便地预测原油及产品的性质分布,而这对于生产运行而言是比较重要的。
Petro-Sim软件是目前世界唯一能进行炼油厂全厂流程模拟的平台,它集Profimatics(包括催化,加氢裂化,重整,加氢,焦化,歧化,芳烃抽提等)动力学包和Hysys通用流程模拟平台于一体,这是上述其它软件不能比拟的。
三、原油评价数据的合成本文采用镇海公司原油评价数据为准,因为公司内部的原油评价数据各窄馏分分析数据有重叠,如果直接采用Petro-SIM系统提供的原油合成功能误差较大。
为此本文另辟蹊径提出了在流程图环境中合成原油评价的新方法。
经过验证,这个方法准确,可靠。
由于流程图环境的数据可以和Excel交互,通过进一步开发Excel原油评价数据输入界面,可使合成原油评价数据的工作迅速而简便。
探讨流程模拟技术在常减压装置换热网络优化中的应用
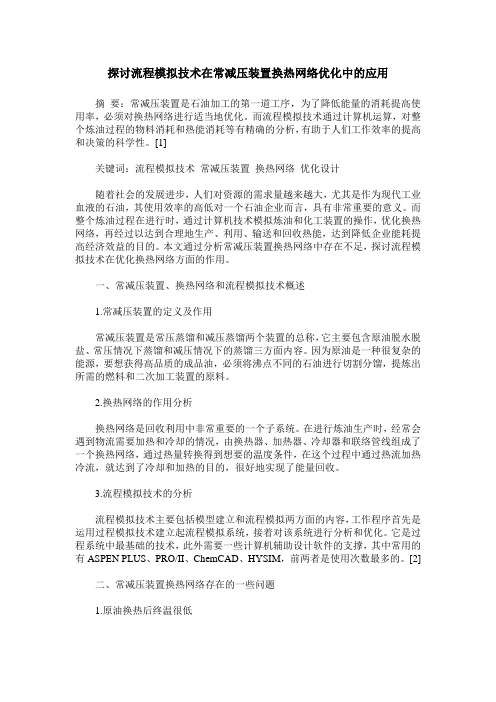
探讨流程模拟技术在常减压装置换热网络优化中的应用摘要:常减压装置是石油加工的第一道工序,为了降低能量的消耗提高使用率,必须对换热网络进行适当地优化。
而流程模拟技术通过计算机运算,对整个炼油过程的物料消耗和热能消耗等有精确的分析,有助于人们工作效率的提高和决策的科学性。
[1]关键词:流程模拟技术常减压装置换热网络优化设计随着社会的发展进步,人们对资源的需求量越来越大,尤其是作为现代工业血液的石油,其使用效率的高低对一个石油企业而言,具有非常重要的意义。
而整个炼油过程在进行时,通过计算机技术模拟炼油和化工装置的操作,优化换热网络,再经过以达到合理地生产、利用、输送和回收热能,达到降低企业能耗提高经济效益的目的。
本文通过分析常减压装置换热网络中存在不足,探讨流程模拟技术在优化换热网络方面的作用。
一、常减压装置、换热网络和流程模拟技术概述1.常减压装置的定义及作用常减压装置是常压蒸馏和减压蒸馏两个装置的总称,它主要包含原油脱水脱盐、常压情况下蒸馏和减压情况下的蒸馏三方面内容。
因为原油是一种很复杂的能源,要想获得高品质的成品油,必须将沸点不同的石油进行切割分馏,提炼出所需的燃料和二次加工装置的原料。
2.换热网络的作用分析换热网络是回收利用中非常重要的一个子系统。
在进行炼油生产时,经常会遇到物流需要加热和冷却的情况,由换热器、加热器、冷却器和联络管线组成了一个换热网络,通过热量转换得到想要的温度条件,在这个过程中通过热流加热冷流,就达到了冷却和加热的目的,很好地实现了能量回收。
3.流程模拟技术的分析流程模拟技术主要包括模型建立和流程模拟两方面的内容,工作程序首先是运用过程模拟技术建立起流程模拟系统,接着对该系统进行分析和优化。
它是过程系统中最基础的技术,此外需要一些计算机辅助设计软件的支撑,其中常用的有ASPEN PLUS、PRO/II、ChemCAD、HYSIM,前两者是使用次数最多的。
[2]二、常减压装置换热网络存在的一些问题1.原油换热后终温很低以某石厂为例,2013年12月,其常减压装置的主原油经过了常规的三次换热和蒸馏后,对比原油换热前后的温度发现,脱前原油经过换热后最终的温度只有118.4摄氏度,严重影响电脱盐工艺的进行;而脱后原油换热后的最终温度也只有225.1摄氏度,大大降低了初馏塔的拔出效率,使常压炉的工作量大大增加;而初底原油经过换热后最终温度也仅仅只有289.6摄氏度。
基于Aspen+Plus的原油蒸馏装置流程模拟及优化

明显,当汽提蒸汽量继续提高时,常底重油350℃馏 出量的变化幅度降低。
因此,根据模拟计算结果,建议装置在该加工
负荷下,将常压炉的出口温度控制在360~364℃之 间,将塔底汽提蒸汽量控制在3~4t/h之间,以保证 在尽可能提高装置常压拔出率的情况下,实现装置 的节能降耗。
万方数据
增刊1
水春贵.基于Aspen
因:一是目前装置加工的原油性质与建模时的原油
性质不一样;二是实际加工量偏小;三是受各中段 回流换热器换热面积的影响,其流量调整受到限
模块,每个塔内的关键参数设定见表l。表4【l】。利 用以上基础数据,建立装置稳态模型,各塔参数以 万方数据
E—mail:shuicg.jmh@sin叩ec.cⅢ
中外能源
・10・ SIN0一GLOBAL ENERGY
2011年第16卷
0.2l%;而在塔底汽提蒸汽量为8.0t/h情况下,常压 炉出口温度每升高2cC,常底重油350℃馏出量仅 降低0.05%。同理,在常压炉出口温度保持不变情
2 5 2 13 27 35 43
汽提塔l 减压塔 汽提塔2 汽提塔3
表5初馏塔操作数据与计算值对比
项目 初馏塔顶温度/℃ 初馏塔顶回流温度,℃ 初馏塔底温度,℃ 标定值
123 40 197 201 50
计算值
124-8 40 198 200 50 Nhomakorabea3
进料温度,℃
8
初馏塔顶压力,kPa
22 30
从图2还可以看出,塔底汽提蒸汽量控制在 2—4t/h之间,对常底重油350℃馏出量的影响较为
项目 初馏塔 常压塔 减压塔 塔板数
21 49
表4常压塔和减压塔汽提塔
再沸器选型
蒸馏装置负荷转移技术的模拟与优化

2005年12月炼油技术与工程PETROLEUMREFINERYENGINEERING第35卷第12期鬻獭常减压蒸馏装置负荷转移技术的模拟与优化赵晓军1陈伟军2杨敬一1徐心茹11.华东理工大学石油加工研究所(上海市200237)2.中国石化镇海炼油化工股份有限公司(浙江省宁渡市315200)摘要:用ASPENPLUS软件对卡宾达原油常减压蒸馏装置进行流程模拟计算,并通过灵敏度分析确定装置的最大加工负荷,并找出常压塔与减压塔之间关联操作的影响心素,提H{常减压装置负荷转移技术的扩能改造操作优化方案。
关键词:常减压蒸馏装置流程模拟计算机优化根据“十五规划”,镇海炼油化工股份有限公司的原油综合加工能力和生产技术水平要达到国际炼油企业的先进水平,并基本形成20Ml/a的综合加工能力,为此要对Ⅱ套常减压蒸馏装置进行扩能改造,由原来的原油处理能力3.0Mt/a改造到6.0Mt/a。
为节省投资和缩短改造周期,改造采用四级蒸馏的改造工艺——即负荷转移技术。
四级蒸馏新工艺是在原有的常减压蒸馏流程的基础上,通过新增一级减压炉和一级减压塔,前后分别转移部分常压负荷和减压负荷至一级减压塔,即采用初馏塔一常压炉一常压塔一一级减压炉一一级减压塔一二级减压炉一二级减压塔的新工艺,从而实现蒸馏装置扩能。
本研究采用ASPENPLUS软件对该公司Ⅱ套常减压蒸馏装置进行模拟,找出常压塔与减压塔之间关联操作的影响因素,对负荷转移技术的操作条件进行模拟优化。
1常减压蒸馏装置工艺模型的建立”。
11.1加工方案及控制指标产品方案为石脑油.喷气燃料一柴油-蜡油加氢裂化/精制方案,其中石脑油作为催化重整原料,常二线油作为军用柴油加氢精制原料,常一、三线作为柴油加氢精制原料;一级减一、二线油作为柴油加氢精制原料;一级减三线油、二级减一、二线油作为蜡油加氢精制/裂化原料;减压渣油(减渣)作为重油催化/焦化/溶剂脱沥青/氧化沥青原料。
生产方案及控制指标见表1。
常减压蒸馏装置模拟与操作优化

常减压蒸馏 装置模拟 与操作优化
装 置在运 行过程 中还存在圣金桥过程仿真模拟软件实现装置模拟
首先 , 对 初馏塔 、 常压塔 、 减 压塔 以及稳定塔 之间组成 的常
1装置中存在 的问题
炼 油厂 为我 们提 供装 置的模 拟数 据 , 进 分析 本 厂 常减 压 装 置 中存在 的 问题 , 找 出 流程 的 模拟 结 压蒸馏 装 置进行 模拟 , 果 。近年 来 , 本厂原 油性 质变 化较大 , 重 质化 劣质化加 剧 , 在供 行主 装 置的设 备参数 和 工艺参 数分 析 。如果 对原油 的进 料温 得 到的结果 与实际生 产的数据 进行 比 给上 一直 处于 不稳定 的状 态 , 由于 处于 被动 模式 , 所 以在 原油 度和压 力进行模 拟计算 , 较 。而 且利 用该 工具进 行夹点分析 , 从而优化换 热 网络 。对夹 种类 以及 比例 变化上 都给 工厂 的生 产造 成许 多问题 。在 大量
究。
性、 结果 合理性 以及计算机 的性能 上都要提 出要求 。在混合原 油 的 比值输 入上 , 主要 是 通过 化验 样 品或 调 和样 品混 合 规 定 的, 但在 灵敏 度工具 中没 有对 它变量 的选 项 , 所 以要 变成对 原 油输 入量 的方法 , 就要对模 拟流程 进行改造 。 由于运 用灵敏 度 工具 在生成 的变量组 合与模拟 结果是有 限的 , 只是对 反映变量 变化 上 产生 一定 的影 响 , 还 不能 完全 做 到变 量 完整 变化 的影
AspenPlus在常减压蒸馏装置中的应用
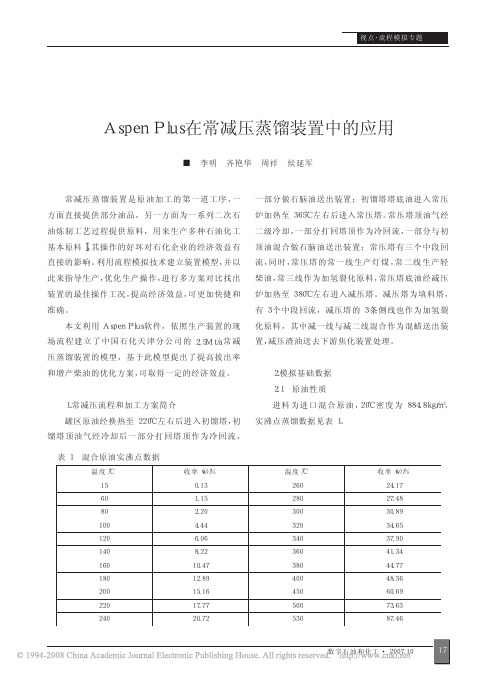
2.2 过程参数 在进行装置过程参数收集时, 按照先采集操作 数据, 再进行现场取油样的顺序进行。装置的实际操 作是动态的, 过程参数会在一定范围内波动, 因此, 在收集过程参数时, 不仅采集了即时数据, 对重要的 过程参数还收集了一段时间内的数据, 根据数据变 化趋势可以判断即时数据的合理性, 同时在合理范
Aspen Plus 在常减压蒸馏装置中的应用
■ 李明 齐艳华 周祥 侯延军
常减压蒸馏装置是原油加工的第一道工序, 一 方面直接提供部分油品, 另一方面为一系列二次石 油炼制工艺过程提供原料, 用来生产多种石油化工 基本原料[], 其操作的好坏对石化企业的经济效益有 直接的影响。利用流程模拟技术建立装置模型, 并以 此来指导生产, 优化生产操作, 进行多方案对比找出 装置的最佳操作工况, 提高经济效益, 可更加快捷和 准确。
5.2 增产柴油 为提高柴汽比以缓解国内消费柴汽比大于生产 柴汽比的局面, 增加柴油产量也是优化常减压装置 操作目标之一。其优化问题可表述为: 目标: Max flow( 常二线) 约束: 常一线干点≯240℃, 常二线 95%点≯365℃ 自变量: 塔顶温度, 常一线抽出量, 常三线抽出 量, 常塔底汽提蒸汽量
减压系统直接模拟的结果与产品实际馏程偏差 较大, 失去指导意义。初步分析主要有两个原因: 一 个重要的是, 530℃以前的原油实沸点蒸馏数据由实 验得到, 较为准确, 而 530℃以后的蒸馏数据由软件 自动外推, 有一定的误差; 另一个是, 常压塔底的渣 油在减压炉中发生部分高温裂解也是导致减压塔模 拟失真的一个主要原因。目前已有文献报道, 在常减 炉入口通过人为的加入一定组成的轻端组分后较好 的模拟了包括减压塔在内的常减压蒸馏流程。为此, 该模型在减压系统前加入模拟裂解气, 具体裂解气 组分见表 4。
HYSYSV10在常减压装置上的应用
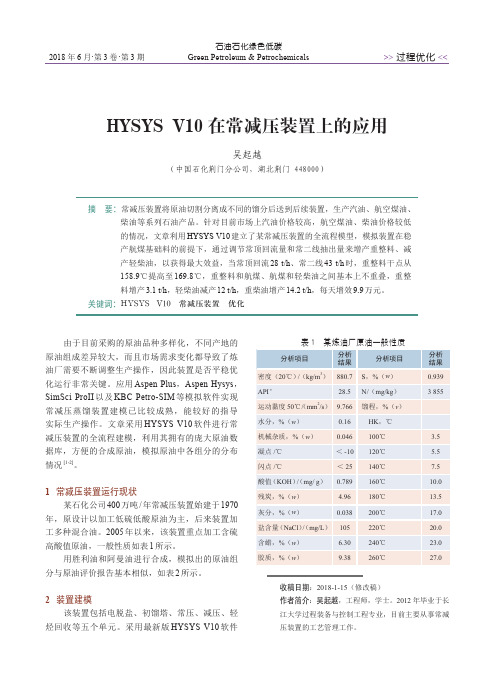
摘 要:常减压装置将原油切割分离成不同的馏分后送到后续装置,生产汽油、航空煤油、柴油等系列石油产品。
针对目前市场上汽油价格较高,航空煤油、柴油价格较低的情况,文章利用HYSYS V10建立了某常减压装置的全流程模型,模拟装置在稳产航煤基础料的前提下,通过调节常顶回流量和常二线抽出量来增产重整料、减产轻柴油,以获得最大效益,当常顶回流28 t/h 、常二线43 t/h 时,重整料干点从158.9℃提高至169.8℃,重整料和航煤、航煤和轻柴油之间基本上不重叠,重整料增产3.1 t/h ,轻柴油减产12 t/h ,重柴油增产14.2 t/h ,每天增效9.9万元。
关键词:HYSYS V10 常减压装置 优化HYSYS V10在常减压装置上的应用吴起越(中国石化荆门分公司,湖北荆门 448000)由于目前采购的原油品种多样化,不同产地的原油组成差异较大,而且市场需求变化都导致了炼油厂需要不断调整生产操作,因此装置是否平稳优化运行非常关键。
应用Aspen Plus ,Aspen Hysys ,SimSci ProII 以及KBC Petro-SIM 等模拟软件实现常减压蒸馏装置建模已比较成熟,能较好的指导 实际生产操作。
文章采用HYSYS V10软件进行常减压装置的全流程建模,利用其拥有的庞大原油数据库,方便的合成原油,模拟原油中各组分的分布 情况[1-2]。
1 常减压装置运行现状某石化公司400万吨/年常减压装置始建于1970年,原设计以加工低硫低酸原油为主,后来装置加工多种混合油。
2005年以来,该装置重点加工含硫高酸值原油,一般性质如表1所示。
用胜利油和阿曼油进行合成,模拟出的原油组分与原油评价报告基本相似,如表2所示。
2 装置建模该装置包括电脱盐、初馏塔、常压、减压、轻烃回收等五个单元。
采用最新版HYSYS V10软件收稿日期:2018-1-15(修改稿)作者简介:吴起越,工程师,学士。
2012年毕业于长江大学过程装备与控制工程专业,目前主要从事常减压装置的工艺管理工作。
流程模拟技术在常减压蒸馏装置上的应用
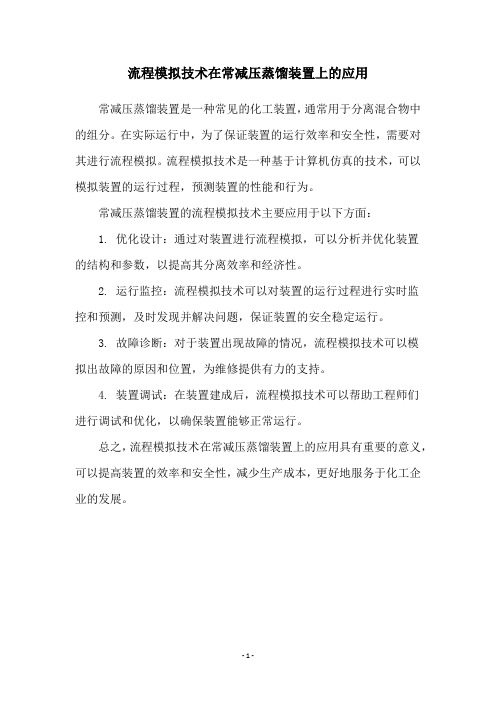
流程模拟技术在常减压蒸馏装置上的应用常减压蒸馏装置是一种常见的化工装置,通常用于分离混合物中的组分。
在实际运行中,为了保证装置的运行效率和安全性,需要对其进行流程模拟。
流程模拟技术是一种基于计算机仿真的技术,可以模拟装置的运行过程,预测装置的性能和行为。
常减压蒸馏装置的流程模拟技术主要应用于以下方面:
1. 优化设计:通过对装置进行流程模拟,可以分析并优化装置
的结构和参数,以提高其分离效率和经济性。
2. 运行监控:流程模拟技术可以对装置的运行过程进行实时监
控和预测,及时发现并解决问题,保证装置的安全稳定运行。
3. 故障诊断:对于装置出现故障的情况,流程模拟技术可以模
拟出故障的原因和位置,为维修提供有力的支持。
4. 装置调试:在装置建成后,流程模拟技术可以帮助工程师们
进行调试和优化,以确保装置能够正常运行。
总之,流程模拟技术在常减压蒸馏装置上的应用具有重要的意义,可以提高装置的效率和安全性,减少生产成本,更好地服务于化工企业的发展。
- 1 -。
原油蒸馏过程的工艺计算及模拟
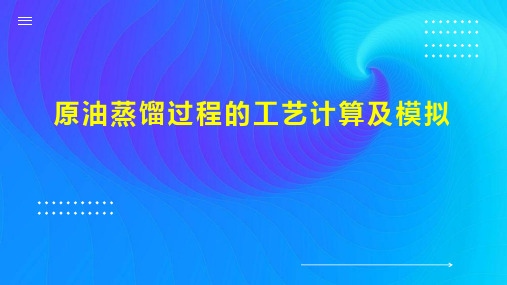
该软件包采用了以下关键技术和方法:
1、组分模型库的建立:收集各种原油的组成和性质数据,建立组分模型库, 以便快速查询和选用。
2、模拟软件的集成:将多种模拟软件集成到一起,实现多软件协同计算, 提高计算效率和精度。
3、标定算法优化:采用多种标定算法相结合的论
本次演示通过对柴油机燃油喷雾过程的模拟计算和实验研究,深入探讨了燃 油喷雾特性的影响因素。结果表明,喷嘴出口处的流体性质、燃烧室内的气体流 动等参数对柴油机燃油喷雾特性有着重要的影响。在今后的研究中,可以针对这 些影响因素,通过优化喷嘴设计、改善燃烧室内的气体流动等措施,进一步优化 柴油机燃油喷雾过程,从而提高发动机性能、降低排放。
背景
柴油机燃油喷雾过程是指将燃油喷入燃烧室,形成细小油滴和油膜的过程。 这个过程中,燃油被喷嘴喷出后,受到燃烧室内的气体流动和热辐射等作用,其 动力学行为和蒸发过程对发动机的性能和排放有着直接的影响。在过去的几十年 里,研究者们对柴油机燃油喷雾过程进行了广泛的研究,提出了许多理论和模型, 如液滴破碎模型、湍流混合模型等。这些理论和模型为进一步理解柴油机燃油喷 雾过程提供了有益的指导。
总之,本次演示开发的原油常减压蒸馏装置工艺计算和标定核算软件包,具 有功能完善、计算精度高、稳定性好、速度快、用户友好等优点,可以大大提高 常减压蒸馏装置的设计和操作水平,降低生产成本,提高企业效益。在石油化工 行业中具有广泛的应用前景。
引言
柴油机由于具有较高的热效率和燃油经济性,在汽车、船舶、发电机组等领 域得到了广泛应用。在柴油机燃油系统中,燃油喷雾过程是燃烧过程的关键环节 之一,对发动机的性能和排放有着重要影响。因此,对柴油机燃油喷雾过程进行 深入研究,对于提高发动机性能、降低排放具有重要意义。本次演示旨在通过模 拟计算和实验研究方法,探讨柴油机燃油喷雾过程的内在规律,为优化发动机设 计和降低排放提供理论支撑和实践依据。
流程模拟技术在天津石化3#常减压装置上的应用

流程模拟技术在天津石化3#常减压装置上的应用柳化增【摘要】以中国石化天津分公司1000wt/年常减压装置为研究对象,采用Aspen Plus流程模拟软件,建立了与实际工况相吻合的常减压装置稳态流程模拟模型,通过对闪蒸塔、常压塔和减压塔的模拟,了解各操作参数对装置性能的影响;通过蒸馏塔模型中的气液相负荷分布和温度梯度的分布情况,加深对蒸馏操作的理解。
随着重油加工工艺技术的发展,炼厂能够加工更加劣质的渣油,因此常减压装置轻油收率和总拔出率的提高,对提高原油的利用率及炼厂的经济效益极为重要。
为此,重点对影响常减压装置轻油收率的关键操作参数进行灵敏度分析,优化操作,实现提高常减压装置轻油收率的目的。
【期刊名称】《中国新技术新产品》【年(卷),期】2014(000)001【总页数】3页(P81-83)【关键词】Aspen Plus;流程模拟;常减压轻收能耗【作者】柳化增【作者单位】中国石油化工股份有限公司天津分公司炼油部,天津300271【正文语种】中文【中图分类】TQ02中国石油化工股份有限公司天津分公司100万吨/年乙烯及配套项目1000万吨/年常减压蒸馏装置由中国石油化工工程建设公司设计,燕华公司施工,2007年12月动工建设,预计2009年6月建成投产。
本装置加工沙特阿拉伯轻油和沙特阿拉伯重油的混合原油(混合比为1:1),处理能力为1000万吨/年,年开工时数按8400小时计。
随着重油深加工工艺技术的发展,使得炼厂可以加工更为劣质的减压渣油[1]。
因而减压蒸馏可以合理地提高拔出率,以降低减压渣油的产率,这样不仅可以有效提高原油利用率,同时还能增加炼厂的经济效益。
厂高原油的利用率及炼厂的经济效益均流程模拟技术的推广应用,为寻找装置生产瓶颈,优化装置操作条件,提高装置的轻油收率和总拔出率,降低能耗,离线培训操作人员创造了条件。
建模的主要目标是建立生产过程的流程模拟模型,并通过模型计算满足以下要求:(1)对常减压装置的闪蒸塔、常压塔和减压塔进行全流程模拟。
- 1、下载文档前请自行甄别文档内容的完整性,平台不提供额外的编辑、内容补充、找答案等附加服务。
- 2、"仅部分预览"的文档,不可在线预览部分如存在完整性等问题,可反馈申请退款(可完整预览的文档不适用该条件!)。
- 3、如文档侵犯您的权益,请联系客服反馈,我们会尽快为您处理(人工客服工作时间:9:00-18:30)。
第24卷 第6期2006年11月 石化技术与应用Petr oche m ical Technol ogy&App licati on Vol.24 No.6 Nov.2006工业技术(484~486)流程模拟技术在常减压蒸馏装置上的应用邓岗,孙琳娟,段永静(中国石油兰州石化分公司自动化研究院,甘肃兰州730060)摘要:针对常减压蒸馏的工艺特点,利用A s pen Plus流程模拟软件的速率模型Petr oFrac单元模块,通过构建基本模型来模拟初馏塔、常压塔和减压塔的实际运行工况。
同时,考虑装置物流的压力和热量变化,配合Fs p lit物流分离模块、Heater换热模块、Flash简单气液分离模块和Pu mp压力改变模块,共同构建了常减压装置的稳态模型。
结果表明,建立的模型可以较为准确地模拟常压工艺,但对于减压工艺存在一定误差;根据增产柴油的实际生产要求,用稳态模型对生产方案进行了模拟,发现常压三线的产品质量有一定裕度可以调节,因此可适当提高常压三线的侧线采出量。
关键词:工艺流程;计算机模拟;软件;常压蒸馏;减压蒸馏;工艺计算中图分类号:TE624.4 文献标识码:B 文章编号:1009-0045(2006)06-0484-03 20世纪90年代,国外石化企业普遍使用流程模拟技术对生产装置的日常操作进行指导,并在单装置或联合装置上进行全流程离线或在线模拟优化。
1990—1996年,国内各企业逐步引进国外流程模拟软件,将其用于设计、工艺计算、装置改造等工作中。
中国石油兰州石化分公司自动化研究院利用A spen Plus 流程模拟软件,对常减压蒸馏装置进行了模拟研究。
通过对模拟结果分析,发现操作中存在着问题,同时找出了装置的“瓶颈”所在,为技术改造提供了依据。
1 流程模拟稳态模型的建立① 针对常减压蒸馏工艺的特点,本工作利用A s pen Plus流程模拟软件的速率模型Petr oFrac单元模块,通过构建基本模型来模拟初馏塔、常压塔和减压塔的实际运行工况。
同时考虑装置物流的压力和热量变化,配合其他单元模块:Fs p lit 物流分离模块、Heater换热模块、Flash简单气液分离模块和Pu mp压力改变模块,共同构建了常减压装置的稳态模型。
其模拟工艺流程见图1。
构建的稳态模型没有利用单元模块本身所假设的塔顶冷凝器的操作条件,而是考虑到实际操作过程中,塔顶冷凝器不是在泡点温度下进行分离操作的因素,这样做增加了模型收敛的难度,但是计算结果更符合装置的实际运行状况。
常减压蒸馏工艺虽然比较成熟,但由于存在进料复杂,侧线产品切割馏分重叠等问题,若要非常精确地进行流程模拟难度较大,同时各个单元模块的进出物料相互关联,因此对全流程工艺模拟要分步进行。
在流程模拟中,板效率的改动或各塔操作条件的变动都会使计算难以收敛。
因此需要不断的实验,使最终的计算结果既能很好地收敛,也能尽量与所参照的实际数据相吻合。
2 流程模拟计算结果分析利用建立好的模型,可以对常减压装置进行流程模拟、物料衡算,也可以通过塔板水力学计算,得出各塔每层塔盘的泛点因子,塔板液相流速,以及气液相对密度、黏度和表面张力等结果。
本工作对常减压装置操作温度和馏程进行了模拟计算(见表1和表2)。
①收稿日期:2005-09-15;修回日期:2006-08-10作者简介:邓岗(1976—),男,甘肃武威人,学士,工程师。
已发表论文2篇。
CRUDE —原油;WATER1—初馏塔顶冷凝水;T2ST M —常压塔底吹汽;VACFEED —减压炉进料;T3ST M —减压塔底吹气;T3VAP —减压塔顶油气;T3G AS —减压塔顶瓦斯;VAC -COLD —减顶冷却油;T3ST M1—减压一线;T3ST M2—减压二线;T3ST M3—减压三线;T3ST M4—减压四线;T3BT M —减压渣油图1 常减压装置流程模拟表1 3塔操作温度℃塔名项目实测值模拟值初馏塔塔顶温度133129.1956侧线采出温度176177.5919塔底采出温度232232.6757常压塔塔顶温度123123.0000一线采出温度190188.0348二线采出温度262257.1133三线采出温度315320.1639塔底采出温度353354.7921减压塔塔顶温度4544.2257塔顶采出温度158177.9385一线采出温度215230.6453二线采出温度265279.5327三线采出温度312315.7294四线采出温度340344.2420五线采出温度375368.7816塔底采出温度360358.1298 由表1和表2可知,建立的模型可以较为准确地模拟常压工艺,但是对于减压工艺却存在一定的误差。
误差产生的原因有以下几点:(1)为简化流程,方便计算收敛,整个减压塔的计算以Mellapak 型填料为基准,将各段填料对应的理论塔板数进行换算,多次的估算造成误差产生并累加;(2)在模拟计算中,没有考虑到减压物料本身有一定程度的裂化;(3)连续流程计算中,前期的计算误差累积。
另外,还可以利用软件本身所带的一些功能作进一步的研究。
例如:利用基础模型,添加设计规定,以某个或者某些产品的质量指标作为控制目标,确定影响产品的调节变量和每个调节变量的操作范围。
在此基础上,寻找满足控制目标的最佳操作条件,通过指导现场操作,获取潜在的经济效益。
利用已有的基础模型,通过改变可调节的变量,进行过程的敏感性分析,得到相应变量的变化趋势。
表2 产品馏程实测值和模拟值℃物料结果10%30%50%70%90%95%~98%终馏点97%初馏塔塔顶采出石脑油实测值66.090.5107.5122.5144.0158.0模拟值60.680.4101.4117.4138.3148.7158.2初馏塔侧线采出物料实测值157.5171.5182.0189.0200.5212.5模拟值152.0172.0179.0187.1199.8208.4216.7・584・ 第6期 邓岗等1流程模拟技术在常减压蒸馏装置上的应用续表2℃物料结果10%30%50%70%90%95%~98%终馏点97%常压塔塔顶采出石脑油实测值65.089.0105.5123.0147.0165.0模拟值67.4108.5117.7127.8138.1147.9157.3常压一线采出物料实测值167.0177.0186.0194.0207.5219.0223.0模拟值168.9178.4186.3196.4209.5218.6227.2常压二线采出物料实测值232.0251.5263.5277.5298.5310.0329.5模拟值235.6250.5261.6274.7291.9302.6313.6常压三线采出物料实测值277.0321.0339.0354.5376.5386.0模拟值295.4321.5332.5345.6369.4383.0396.2减压塔塔顶冷却油实测值11710161.519310227.5275.530310模拟值165.1207.0234.5258.3290.1314.3336.4减压塔塔顶采出物料实测值256.5265.5276.5293103191033410349.5模拟值251.7283.9305.3320.9336.1349.6366.6减压一线采出物料实测值33510348103571037010386103921039910模拟值316.5341.8361.5378.1392.0406.1422.9减压二线采出物料实测值40010409104151042210433104391044410模拟值372.339510411.5424.4438.3463.8485.3减压三线采出物料实测值42810439104461045210466104771048610模拟值404.9426.244310452.2477.7495.6511.2减压四线采出物料实测值46010474104821049310511105211052910模拟值432.7463.448210497.3520.6528.8552.4减压五线采出物料实测值4701051410531105471057610模拟值466.3506.5529.8550.5584.6616.5652.13 工业应用根据增产柴油的实际生产要求,用稳态模型对生产方案进行了模拟,在满足常压三线柴油95%馏程不大于37510℃的条件下,最大量生产柴油的实际工况与模拟工况对比见表3。
表3 模拟增产柴油的方案(常压塔计算结果)项目增产柴油方案模拟结果实际工况模拟结果塔顶温度/℃120120塔顶不凝汽量/(m3・h-1)46.347.1常顶汽油量/(m3・h-1)206.7207.4一线采出温度/℃188.0187.6一线采出量/(m3・h-1)53.554.1二线采出温度/℃256.85257.00二线采出量/(m3・h-1)86.085.7三线采出温度/℃324.37323.50三线采出量/(m3・h-1)45.942.4塔底采出温度/℃354.7204354.7000塔底采出量/(m3・h-1)365.6367.5馏程/℃ 初馏点200.85199.89 5%265.63264.43 10%293.90292.70 30%319.78317.65 50%330.26327.95 70%341.65336.56 90%362.71354.85 95%374.03363.76 由表3可知,与实际情况对比,发现常压三线的产品质量有一定裕度可以调节,因此适当提高常压三线的侧线采出量,既保证了产品质量,又达到了增产柴油的目的。
4 结论a.针对常减压蒸馏工艺的特点,利用A s pen Plus流程模拟软件的速率模型Petr oFrac单元模块,通过构建基本模型来模拟初馏塔、常压塔和减压塔的实际运行工况。
同时考虑装置物流的压力和热量变化,配合其他单元模块:Fs p lit物流分离模块、Heater换热模块、Flash简单气液分离模块和Pump压力改变模块,共同构建了常减压装置的稳态模型。
b.建立的模型可以较为准确地模拟常压工艺,对于减压工艺存在一定误差。
c.根据增产柴油的生产要求,用稳态模型对生产方案进行了模拟。
发现常压三线的产品质量有一定裕度可以调节,因此适当提高常压三线的侧线采出量,既保证了产品质量,又达到了增产柴油的目的。
・684・石 化 技 术 与 应 用 第24卷 。