球化剂含镁量对镁吸收率的影响
影响球化效果的几方面因素及解决方法

影响球化效果的几方面因素及解决方法1、原材料。
使用废钢方面,由于货源不固定,因而造成成分的波动与偏差,如果是生产铁素体基体材质的铸件,则应选用碳素钢成分的废钢,例如A3钢、45钢等角钢、工字钢等;也可以适度用些不含Cr的合金钢。
在外观方面,最好不得有铁锈、油漆、油圬以及焊缝等,因为铁锈主要是FeO等,在球化反应时会消耗Mg元素,影响球化率;油漆尤其是橘黄色、绿色,是由含Pb约64%和Cr约16.1%的颜料配置而成;焊缝金属一般含有O、H、S、P、Sn、Pb等有害杂质,这些干扰杂质元素,尤其是Pb会进入铁液之中,直接会是石墨形态变异。
尽量少用表面附着较多的煤(煤中S、P含量高)、或铁锈的废钢,以及废钢中夹杂锌、铝、铅、铬、铜等反球化元素,上料工一定要多加注意不能用不明来源的废生铁铸件和玛钢件。
增碳剂一定要保持干燥,受潮后的增碳剂会导致铁水中含O、H等元素增加,造成铁水过度氧化,影响球化效果。
2、出炉温度出炉温度尽量控制在1480-1500℃,在球化包温度较低时,可以适当提高10-30℃。
但最高不能超过1538℃的临界温度。
否则会造成球化反应剧烈(过度烧损球化剂)、夹渣、冷隔等现象。
3、捣包捣包注意:①填充后应进行紧实,使合金之间的空隙或缝隙最小,堆积密度最大;也就是必须分层用力捣实,②必须有覆盖物,覆盖物可以说是千差万别,主要目的是延缓起爆、预处理等,③现场操作操作注意一定要覆盖严实,不要有缝隙,充分体现既覆又盖的目的;④覆盖后的体积最好和处理包凹槽相吻合。
4、扒渣扒渣应迅速和彻底,防止铁水回硫,第二次氧化5、覆盖扒渣后,覆盖足量的保温剂,保证铁水温度下降缓慢,利于浇注。
6、浇注时间尽量在12分钟内完成,以免温度过低和孕育衰退。
与球化剂有关的球铁件缺陷(1)石墨球异化:石墨球异化出现不规则石墨,如团块状、蝌蚪状、蠕虫状、角状或其他非圆球状。
这是由于球状石墨沿辐射方向生长时,局部晶体生长模式和生长速率偏离正常生长规律所致。
球化剂怎么选
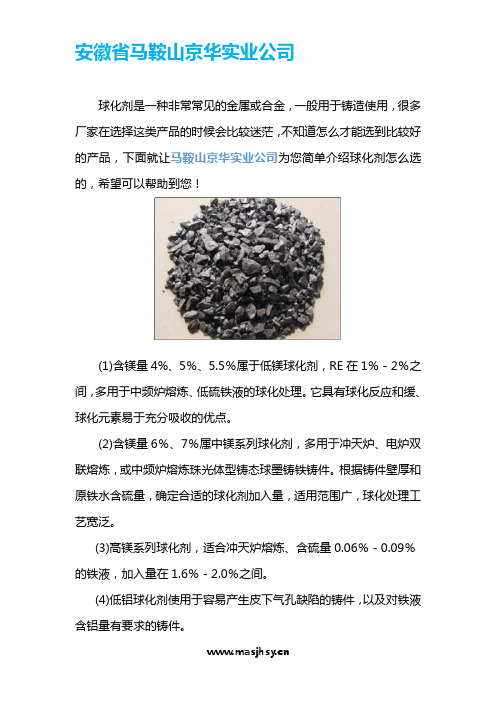
球化剂是一种非常常见的金属或合金,一般用于铸造使用,很多厂家在选择这类产品的时候会比较迷茫,不知道怎么才能选到比较好的产品,下面就让马鞍山京华实业公司为您简单介绍球化剂怎么选的,希望可以帮助到您!
(1)含镁量4%、5%、5.5%属于低镁球化剂,RE在1%-2%之间,多用于中频炉熔炼、低硫铁液的球化处理。
它具有球化反应和缓、球化元素易于充分吸收的优点。
(2)含镁量6%、7%属中镁系列球化剂,多用于冲天炉、电炉双联熔炼,或中频炉熔炼珠光体型铸态球墨铸铁铸件。
根据铸件壁厚和原铁水含硫量,确定合适的球化剂加入量,适用范围广,球化处理工艺宽泛。
(3)高镁系列球化剂,适合冲天炉熔炼、含硫量0.06%-0.09%的铁液,加入量在1.6%-2.0%之间。
(4)低铝球化剂使用于容易产生皮下气孔缺陷的铸件,以及对铁液含铝量有要求的铸件。
(5)纯Ce、纯La生产的球化剂,球化处理后铁液纯净夹杂物少、石墨球圆整。
钇基重稀土生产的球化剂适合于大断面铸件,延缓球化衰退、防止块状石墨。
含Sb球化剂用于珠光体型球墨铸铁。
(6)低硅球化剂适用于使用大量回炉料的铸造工厂;镍镁球化剂则用于高镍奥氏体球墨铸铁。
马鞍山京华实业公司是炼钢、铸造用增碳剂、煅后石油焦以及石墨化增碳剂,孕育剂,碳化硅等专业生产厂家。
公司能按增碳剂客户的要求加工成各种粒度规格的增碳剂,对产品高质量的追求户及对顾客称心满意的服务是马鞍山京华的经营宗旨。
马鞍山京华实业公司秉承着“凭质量铸造现在,靠信誉开拓未来”的经营理念,为客户提供最优质的增碳剂和贴心的服务。
如果您想进一步了解,可以直接点击官网马鞍山京华实业公司进行在线咨询。
我国球化剂与球化工艺的现状及发展
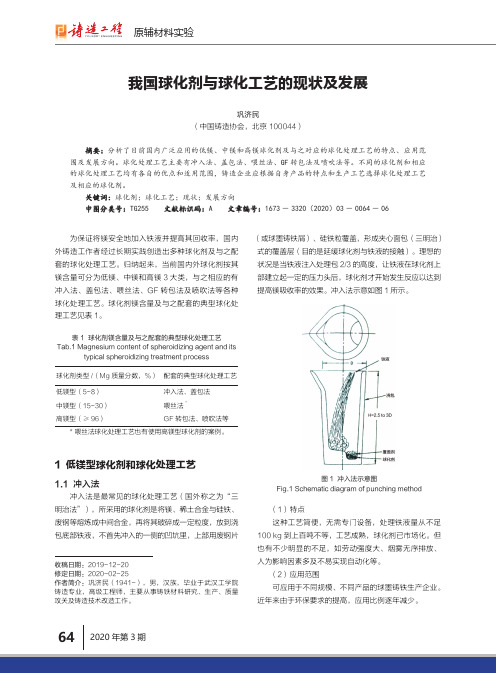
为保证将镁安全地加入铁液并提高其回收率,国内外铸造工作者经过长期实践创造出多种球化剂及与之配套的球化处理工艺。
归纳起来,当前国内外球化剂按其镁含量可分为低镁、中镁和高镁3大类,与之相应的有冲入法、盖包法、喂丝法、GF转包法及喷吹法等各种球化处理工艺。
球化剂镁含量及与之配套的典型球化处理工艺见表1。
表 1 球化剂镁含量及与之配套的典型球化处理工艺Tab.1 Magnesium content of spheroidizing agent and its typical spheroidizing treatment process球化剂类型/(Mg质量分数,%)配套的典型球化处理工艺低镁型(5~8)冲入法、盖包法中镁型(15~30)喂丝法*高镁型(≥96)GF转包法、喷吹法等* 喂丝法球化处理工艺也有使用高镁型球化剂的案例。
1 低镁型球化剂和球化处理工艺1.1 冲入法冲入法是最常见的球化处理工艺(国外称之为“三明治法”),所采用的球化剂是将镁、稀土合金与硅铁、废钢等熔炼成中间合金,再将其破碎成一定粒度,放到浇包底部铁液,不首先冲入的一侧的凹坑里,上部用废钢片(或球墨铸铁屑)、硅铁粒覆盖,形成夹心面包(三明治)式的覆盖层(目的是延缓球化剂与铁液的接触)。
理想的状况是当铁液注入处理包2/3的高度,让铁液在球化剂上部建立起一定的压力头后,球化剂才开始发生反应以达到提高镁吸收率的效果。
冲入法示意如图1所示。
图1 冲入法示意图Fig.1 Schematic diagram of punching method(1)特点这种工艺简便,无需专门设备,处理铁液量从不足100 kg到上百吨不等,工艺成熟,球化剂已市场化。
但也有不少明显的不足,如劳动强度大、烟雾无序排放、人为影响因素多及不易实现自动化等。
(2)应用范围可应用于不同规模、不同产品的球墨铸铁生产企业。
近年来由于环保要求的提高,应用比例逐年减少。
我国球化剂与球化工艺的现状及发展巩济民(中国铸造协会,北京 100044)摘要:摘要:分析了目前国内广泛应用的低镁、中镁和高镁球化剂及与之对应的球化处理工艺的特点、应用范围及发展方向。
REMg球化剂中MgO含量的影响因素

Mg O r e d u c e d t h e c o n t e n t o f t h e e f f e c t i v e Mg t h a t wo u l d i n l f u e n c e t h e n o d u l a r i z i n g c a p a b i l i t y o f t h e n o d u a l r i z i n g a l l o y . T h e s o u r c e o f Mg O i n n o d u l a r i z i n g a l l o y wa s a n a l y z e d a s f o l l o w s : t h e Mg O f o r me d d u i r n g t h e me h i n g p r o c e s s o f t h e n o d u l a r i z i n g
c o r r e c t s a mp l e p r e p a r i n g me t h o d .
Ke y wor d s: REMg ; n o d u l a r i z i n g a l l o y ; Mg O; n o d u l a r i z i n g t r e a t me n t
球化剂生产质量控制要点浅析
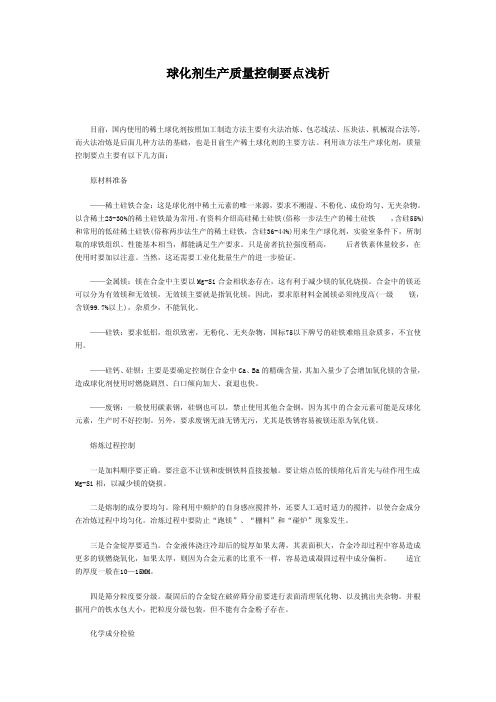
球化剂生产质量控制要点浅析目前,国内使用的稀土球化剂按照加工制造方法主要有火法冶炼、包芯线法、压块法、机械混合法等,而火法冶炼是后面几种方法的基础,也是目前生产稀土球化剂的主要方法。
利用该方法生产球化剂,质量控制要点主要有以下几方面:原材料准备——稀土硅铁合金:这是球化剂中稀土元素的唯一来源,要求不潮湿、不粉化、成份均匀、无夹杂物。
以含稀土23-30%的稀土硅铁最为常用。
有资料介绍高硅稀土硅铁(俗称一步法生产的稀土硅铁,含硅55%)和常用的低硅稀土硅铁(俗称两步法生产的稀土硅铁,含硅36-44%)用来生产球化剂,实验室条件下,所制取的球铁组织、性能基本相当,都能满足生产要求。
只是前者抗拉强度稍高,后者铁素体量较多,在使用时要加以注意。
当然,这还需要工业化批量生产的进一步验证。
——金属镁:镁在合金中主要以Mg-Si合金相状态存在,这有利于减少镁的氧化烧损。
合金中的镁还可以分为有效镁和无效镁,无效镁主要就是指氧化镁,因此,要求原材料金属镁必须纯度高(一级镁,含镁99.7%以上),杂质少,不能氧化。
——硅铁:要求低铝,组织致密,无粉化、无夹杂物,国标75以下牌号的硅铁难熔且杂质多,不宜使用。
——硅钙、硅钡:主要是要确定控制住合金中Ca、Ba的精确含量,其加入量少了会增加氧化镁的含量,造成球化剂使用时燃烧剧烈、白口倾向加大、衰退也快。
——废钢:一般使用碳素钢,硅钢也可以,禁止使用其他合金钢,因为其中的合金元素可能是反球化元素,生产时不好控制。
另外,要求废钢无油无锈无污,尤其是铁锈容易被镁还原为氧化镁。
熔炼过程控制一是加料顺序要正确。
要注意不让镁和废钢铁料直接接触。
要让熔点低的镁熔化后首先与硅作用生成Mg-Si相,以减少镁的烧损。
二是熔制的成分要均匀。
除利用中频炉的自身感应搅拌外,还要人工适时适力的搅拌,以使合金成分在冶炼过程中均匀化。
冶炼过程中要防止“跑镁”、“棚料”和“碰炉”现象发生。
三是合金锭厚要适当。
稀土球化剂知道

稀土球化剂知道稀土球化剂的质量和选用球墨铸铁现在几乎在所有的铸铁厂都有生产,而作为生产球墨铸铁必不可少的球化剂亦越来越受到普遍关注。
本文从球化剂的上产和使用两个角度来探讨说明什么样的球化剂是好的,应该在铸造过程中热核选用球化剂,也就是球化极品值得的判定和选用问题。
1、球化剂及球化元素的作用尽管国内外球化剂的种类很多,但在我们国内目前应用最多的还是稀土镁类合金,现主要论述该类合金及其球化元素的作用。
1、1球化元素及反球化元素1、1、1球化元素的作用素。
球化元素一般有以下共同性质:(1)元素最外电子层上有一个或两个价电子,次内层有8个电子。
这种电子结构使元素与硫、氧和碳有较强的亲和力,反映产物稳定,能显著减少贴水中的硫和氧。
(2)元素在铁水中溶解度低,凝固过程中有显著偏析倾向。
(3)虽然和碳有一定亲和力,但在石墨晶格内溶解度低。
根据以上特点,Mg,Ce,Y,Ca属于有效球化元素。
比铁水小,熔点650度,沸点1108度,在铁水的处理温度下,镁产生的蒸气压力很高(超过1Mpa).镁的熔解热为21J/g,蒸发潜热为406J/g。
因此,镁加入铁水时,要产生汽化,使铁水翻腾。
二是与硫、氧有很强的亲和力。
所生成的MgO和MgS熔点高,密度也远小于铁,容易与铁水分离,因此镁处理后的铁水,硫和氧的含量都很低;三是在铁水凝固过程中有偏析于石墨的倾向,当其在铁水中的残留量超过0.035%时,使末就可以球化,但当镁残留量超过0.07%时,一部分镁偏析于晶界,并于晶界中的碳、磷等发生放热反应,生成MgC2、Mg2C3、Mg3P2等。
残留镁量更多时,晶间碳化物增多。
重稀土中的钇。
一是稀土元素的沸点均比镁高,加入铁水中时,不会引起铁水的翻腾和喷溅;二是铈和钇基稀土元素有比镁更强的脱硫脱氧能力,生成的硫化稀土、氧化稀土等化合物熔点高、稳定性好;三是稀土元素与铁水中的球化干扰元素也能形成稳定的化合物,因此含稀土的球化剂比镁球化剂的抗干扰能力强。
球化处理与孕育处理
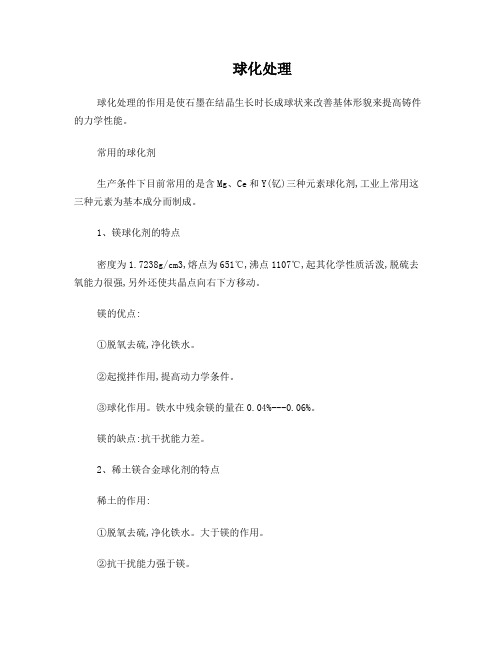
球化处理球化处理的作用是使石墨在结晶生长时长成球状来改善基体形貌来提高铸件的力学性能。
常用的球化剂生产条件下目前常用的是含Mg、Ce和Y(钇)三种元素球化剂,工业上常用这三种元素为基本成分而制成。
1、镁球化剂的特点密度为1.7238g/cm3,熔点为651℃,沸点1107℃,起其化学性质活泼,脱硫去氧能力很强,另外还使共晶点向右下方移动。
镁的优点:①脱氧去硫,净化铁水。
②起搅拌作用,提高动力学条件。
③球化作用。
铁水中残余镁的量在0.04%---0.06%。
镁的缺点:抗干扰能力差。
2、稀土镁合金球化剂的特点稀土的作用:①脱氧去硫,净化铁水。
大于镁的作用。
②抗干扰能力强于镁。
③球化作用。
小于镁的作用。
稀土的缺点:①白口倾向大②原子量大,动力学条件差③球化能力小于镁球化剂的处理方法:1.冲入法;该浇包分为凹坑式、堤坝式和复包式等。
2.型内球化法;该方法的优点是球化剂的吸收率高,所得球铁的性能比普通冲入法的高,特别是抗拉强度较高的情况下伸长率也高。
此外还克服了孕育衰退和球化衰退的问题。
3.盖包法。
优点:①比冲入法的镁利用率高10-20%;②球化剂加入的量少;③工作条件改善了。
4.自建压力加镁法;特点:①以纯镁作为球化剂,降低了成本;②镁的吸收率高,达到了60-80% ;③处理的铁液在3T以上。
④倒包补加铁液1/2-1/3,同时孕育处理。
⑤危险系数大5.转动包法;特点:①应用于含硫高的铁水,可处理含量为0.3%的铁液。
②镁的加入量为0.14-0.20%。
6.镁合金法;常用的合金有Si-Fe-Mg、Cu-Mg、Ni-Mg、Ni- Si-Mg等。
7.喂丝法;特点:①需要平底包,且H/D=1.5-2的细长包和加盖;②处理包有足够的空间供铁水沸腾;③处理的温度应尽可能的低;④要求有高的含镁量。
孕育处理孕育的目的是消除白口、增加共晶团和石墨球并细化、消除偏析、消除结晶过冷倾向等。
孕育效果的评定标准是:①白口倾向的减少。
2012。球化剂的选用及球化处理_2012-04-28 16.12
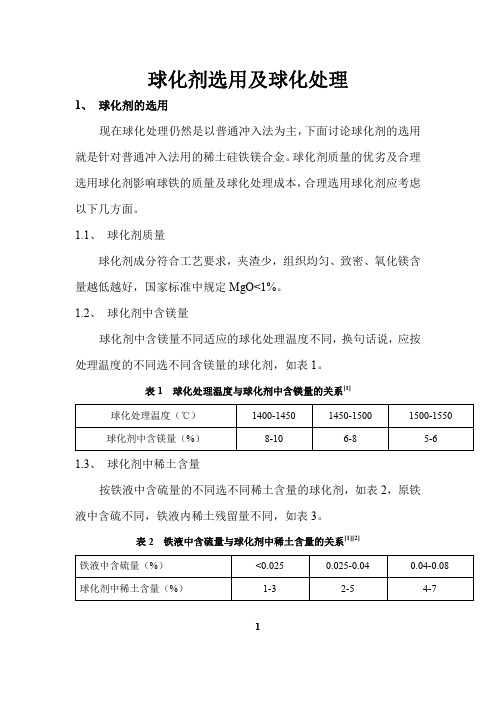
球化剂选用及球化处理1、球化剂的选用现在球化处理仍然是以普通冲入法为主,下面讨论球化剂的选用就是针对普通冲入法用的稀土硅铁镁合金。
球化剂质量的优劣及合理选用球化剂影响球铁的质量及球化处理成本,合理选用球化剂应考虑以下几方面。
1.1、球化剂质量球化剂成分符合工艺要求,夹渣少,组织均匀、致密、氧化镁含量越低越好,国家标准中规定MgO<1%。
1.2、球化剂中含镁量球化剂中含镁量不同适应的球化处理温度不同,换句话说,应按处理温度的不同选不同含镁量的球化剂,如表1。
表1 球化处理温度与球化剂中含镁量的关系[1]1.3、球化剂中稀土含量按铁液中含硫量的不同选不同稀土含量的球化剂,如表2,原铁液中含硫不同,铁液内稀土残留量不同,如表3。
表2 铁液中含硫量与球化剂中稀土含量的关系[1][2]表3 原铁液含硫量与稀土残留量的关系[1][2]1.4、球化剂的粒度球化剂的颗粒度与一次处理铁液量或与球化处理包的容量有关,如表4。
表4 球化剂的粒度与一次处理铁液量的关系[1][2]2、球化处理方法2.1、敞口包冲入法(普通冲入法)敞口包冲入法(以下简称冲入法)国内外早期应用均比较广泛,国内1965年以后逐渐用冲入法代替压力加镁法,直到现在,球铁的生产中仍然是冲入法比较普遍,特别是汽车零件、农机件等一般球铁件的生产中。
冲入法应用40多年至今还广泛应用,说明它有许多优点,现在看,冲入法也存在有不少问题或者说是缺点。
2.1.1、冲入法的优点冲入法的优点,主要有:能满足球铁生产的要求,生产出优质铸件;设备简单,投资少;操作简便、安全,工人容易掌握。
2.1.2、冲入法的缺点冲入法的缺点,主要有:球化质量的稳定性差,稳定生产高档球铁件需寻求球化质量更稳定的新的球化处理方法;镁的吸收率低,球化剂的加入量大,处理过程,铁液降温多;球化过程产生的烟尘处理比较困难,不能满足环保的要求。
2.2、盖包冲入法盖包冲入法(以下简称盖包法)是在冲入法铁液包上面设计一个带有注入孔的包盖。
铸造铁液球化处理常用方法介绍
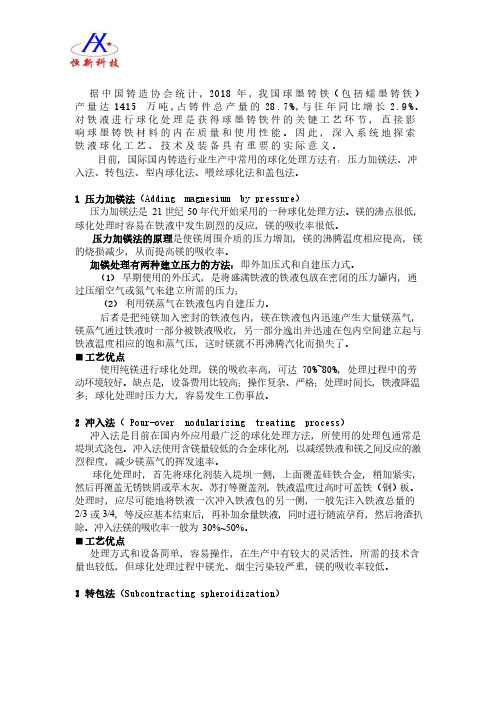
据中国铸造协会统计,2018年,我国球墨铸铁(包括蠕墨铸铁)产量达1415万吨,占铸件总产量的28.7%,与往年同比增长2.9%。
对铁液进行球化处理是获得球墨铸铁件的关键工艺环节,直接影响球墨铸铁材料的内在质量和使用性能。
因此,深入系统地探索铁液球化工艺、技术及装备具有重要的实际意义。
目前,国际国内铸造行业生产中常用的球化处理方法有:压力加镁法、冲入法、转包法、型内球化法、喂丝球化法和盖包法。
1压力加镁法(Adding magnesium by pressure)压力加镁法是21世纪50年代开始采用的一种球化处理方法。
镁的沸点很低,球化处理时容易在铁液中发生剧烈的反应,镁的吸收率很低。
压力加镁法的原理是使镁周围介质的压力增加,镁的沸腾温度相应提高,镁的烧损减少,从而提高镁的吸收率。
加镁处理有两种建立压力的方法:即外加压式和自建压力式。
(1)早期使用的外压式,是将盛满铁液的铁液包放在密闭的压力罐内,通过压缩空气或氮气来建立所需的压力;(2)利用镁蒸气在铁液包内自建压力。
后者是把纯镁加入密封的铁液包内,镁在铁液包内迅速产生大量镁蒸气,镁蒸气通过铁液时一部分被铁液吸收,另一部分逸出并迅速在包内空间建立起与铁液温度相应的饱和蒸气压,这时镁就不再沸腾汽化而损失了。
■工艺优点使用纯镁进行球化处理,镁的吸收率高,可达70%~80%,处理过程中的劳动环境较好。
缺点是,设备费用比较高;操作复杂、严格;处理时间长,铁液降温多;球化处理时压力大,容易发生工伤事故。
2冲入法(Pour-over nodularizing treating process)冲入法是目前在国内外应用最广泛的球化处理方法,所使用的处理包通常是堤坝式浇包。
冲入法使用含镁量较低的合金球化剂,以减缓铁液和镁之间反应的激烈程度,减少镁蒸气的挥发速率。
球化处理时,首先将球化剂装入堤坝一侧,上面覆盖硅铁合金,稍加紧实,然后再覆盖无锈铁屑或草木灰、苏打等覆盖剂,铁液温度过高时可盖铁(钢)板。
球化剂中氧化镁的控制!
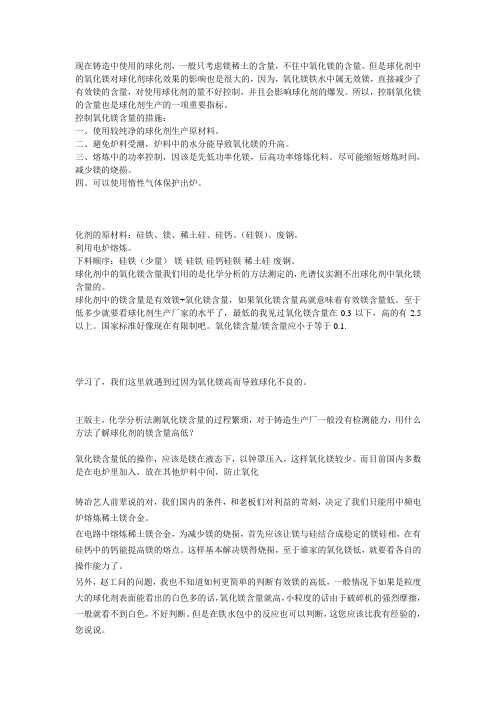
现在铸造中使用的球化剂,一般只考虑镁稀土的含量,不住中氧化镁的含量。
但是球化剂中的氧化镁对球化剂球化效果的影响也是很大的,因为,氧化镁铁水中属无效镁,直接减少了有效镁的含量,对使用球化剂的量不好控制,并且会影响球化剂的爆发。
所以,控制氧化镁的含量也是球化剂生产的一项重要指标。
控制氧化镁含量的措施:一、使用较纯净的球化剂生产原材料。
二、避免炉料受潮,炉料中的水分能导致氧化镁的升高。
三、熔炼中的功率控制,因该是先低功率化镁,后高功率熔炼化料。
尽可能缩短熔炼时间,减少镁的烧损。
四、可以使用惰性气体保护出炉。
化剂的原材料:硅铁、镁、稀土硅、硅钙、(硅钡)、废钢。
利用电炉熔炼。
下料顺序:硅铁(少量)-镁-硅铁-硅钙硅钡-稀土硅-废钢。
球化剂中的氧化镁含量我们用的是化学分析的方法测定的,光谱仪实测不出球化剂中氧化镁含量的。
球化剂中的镁含量是有效镁+氧化镁含量,如果氧化镁含量高就意味着有效镁含量低。
至于低多少就要看球化剂生产厂家的水平了,最低的我见过氧化镁含量在0.3以下,高的有2.5以上。
国家标准好像现在有限制吧。
氧化镁含量/镁含量应小于等于0.1.学习了,我们这里就遇到过因为氧化镁高而导致球化不良的。
王版主,化学分析法测氧化镁含量的过程繁琐,对于铸造生产厂一般没有检测能力,用什么方法了解球化剂的镁含量高低?氧化镁含量低的操作,应该是镁在液态下,以钟罩压入,这样氧化镁较少。
而目前国内多数是在电炉里加入,放在其他炉料中间,防止氧化铸冶艺人前辈说的对,我们国内的条件,和老板们对利益的苛刻,决定了我们只能用中频电炉熔炼稀土镁合金。
在电路中熔炼稀土镁合金,为减少镁的烧损,首先应该让镁与硅结合成稳定的镁硅相,在有硅钙中的钙能提高镁的熔点。
这样基本解决镁得烧损,至于谁家的氧化镁低,就要看各自的操作能力了。
另外,赵工问的问题,我也不知道如何更简单的判断有效镁的高低,一般情况下如果是粒度大的球化剂表面能看出的白色多的话,氧化镁含量就高,小粒度的话由于破碎机的强烈摩擦,一般就看不到白色,不好判断。
7.究竟是谁发明的球墨铸铁
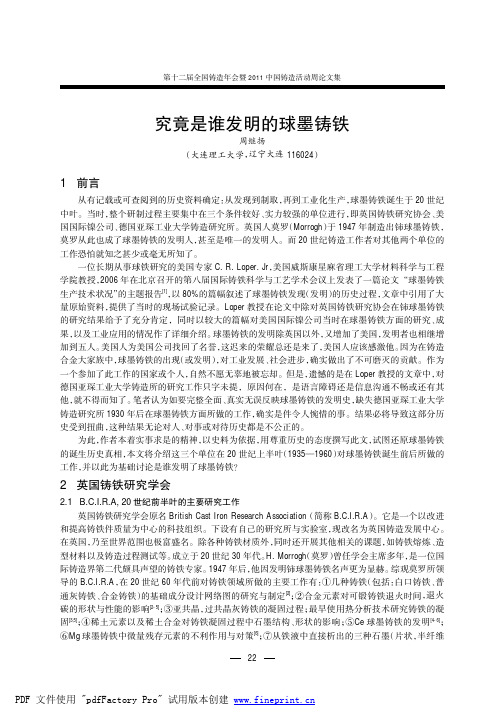
第十二届全国铸造年会暨2011中国铸造活动周论文集究竟是谁发明的球墨铸铁周继扬(大连理工大学,辽宁大连116024)1前言从有记载或可查阅到的历史资料确定:从发现到制取,再到工业化生产,球墨铸铁诞生于20世纪中叶。
当时,整个研制过程主要集中在三个条件较好、实力较强的单位进行,即英国铸铁研究协会、美国国际镍公司、德国亚琛工业大学铸造研究所。
英国人莫罗(Morrogh)于1947年制造出铈球墨铸铁,莫罗从此也成了球墨铸铁的发明人,甚至是唯一的发明人。
而20世纪铸造工作者对其他两个单位的工作恐怕就知之甚少或毫无所知了。
一位长期从事球铁研究的美国专家C.R.Loper.Jr,美国威斯康星麻省理工大学材料科学与工程学院教授,2006年在北京召开的第八届国际铸铁科学与工艺学术会议上发表了一篇论文“球墨铸铁生产技术状况”的主题报告[1],以80%的篇幅叙述了球墨铸铁发现(发明)的历史过程,文章中引用了大量原始资料,提供了当时的现场试验记录。
Loper教授在论文中除对英国铸铁研究协会在铈球墨铸铁的研究结果给予了充分肯定,同时以较大的篇幅对美国国际镍公司当时在球墨铸铁方面的研究、成果,以及工业应用的情况作了详细介绍。
球墨铸铁的发明除英国以外,又增加了美国,发明者也相继增加到五人。
美国人为美国公司找回了名誉,这迟来的荣耀总还是来了,美国人应该感激他。
因为在铸造合金大家族中,球墨铸铁的出现(或发明),对工业发展、社会进步,确实做出了不可磨灭的贡献。
作为一个参加了此工作的国家或个人,自然不愿无辜地被忘却。
但是,遗憾的是在Loper教授的文章中,对德国亚琛工业大学铸造所的研究工作只字未提,原因何在,是语言障碍还是信息沟通不畅或还有其他,就不得而知了。
笔者认为如要完整全面、真实无误反映球墨铸铁的发明史,缺失德国亚琛工业大学铸造研究所1930年后在球墨铸铁方面所做的工作,确实是件令人惋惜的事。
结果必将导致这部分历史受到扭曲,这种结果无论对人、对事或对待历史都是不公正的。
球墨铸铁喷吹球化工艺及优化实验研究

球墨铸铁喷吹球化工艺及优化实验研究作者:未永斌靳杰刘俊锋耿国锋来源:《河北工业科技》2022年第04期摘要:為进一步优化喷吹球化工艺,提高镁的吸收率,对球墨铸铁管的应用效果以及铁液温度、球化深度与镁球化剂吸收率之间的关系进行了研究。
结果表明:球化后的残余硫含量能够稳定降低至0.01%(质量分数)以下,且残余镁含量大于0.05%(质量分数)不会发生球化衰退现象;球化时铁液温度越低、球化深度越大,铁液对镁的吸收率越大;当喷吹球化铁液温度为1 460 ℃、球化深度为1.32 m时,可保证镁吸收率在50%以上。
喷吹球化工艺兼顾了设备简单可靠、易维护,球化剂量调整灵活等特点,将其应用于快节奏、大批量的球墨铸铁管生产领域,降低了喷吹球化工艺成本,可为喷吹球化工艺在球墨铸铁行业的推广应用提供一定的参考。
关键词:黑色金属及其合金;球墨铸铁;喷吹球化;镁处理;球墨铸铁管中图分类号:TG255 文献标识码:ADOI: 10.7535/hbgykj.2022yx04001Experimental research on spray-spheroidization process of ductile iron and its optimizationWEI Yongbin1,2,3,JIN Jie1,2,3,LIU Junfeng1,2,3,GENG Guofeng4,5(1.Xinxing Hebei Engineering Technology Company Limited,Handan,Hebei 056107,China;2.High Strength and High Plasticity Ductile Iron Pipe Engineering Research Center (Preparation),Handan,Hebei 056107,China;3.Hebei Ductile Iron Pipe Manufacturing Innovation Center(Preparation),Handan,Hebei 056107,China;4.School of Materials Science and Engineering,Hebei University of Science and Technology,Shijiazhuang,Hebei 050018,China;5.Hebei Key Laboratory of Material Near-Net Forming Technology,Shijiazhuang,Hebei 050018,China)Abstract:In order to further optimize the spray spheroidization process and improve the availability of Mg,the application effect of ductile iron pile and the relationship between molten iron temperature,spheroidization depth and the availability of Mg spheroidizing agent were studied.The results show that the residual S content after spheroidization can be steadily reduced to less than0.01%(mass fraction),and spheroidization degeneration doesn′t occur when the residual Mg content is greater than 0.05%(mass fraction).During spheroidization,the lower the temperature of molten iron and the greater the spheroidization depth are,the greater the availability of Mg by molten iron is.When the molten iron temperature is 1 460 ℃ and spheroidization depth is 1.32 m,the Mg availability can be over 50%.The spray spheroidization process takes into account the characteristics of simple and reliable equipment,easy maintenance and flexible adjustment of spheroidization dose.It is applied to the production field of fast-paced and large-scale ductile iron pipes to reduce the cost of spray spheroidization process,which provides a certain reference for the popularization and application of spray spheroidization process in the ductile iron industry.Keywords:ferrous metal and its alloy;ductile iron;spray spheroidization;Mg treatment;ductile iron pipe球墨铸铁以优异的性能、低廉的价格在铸铁件领域得到广泛应用。
提高喷镁吸收率与稳定残余镁量的分析研究
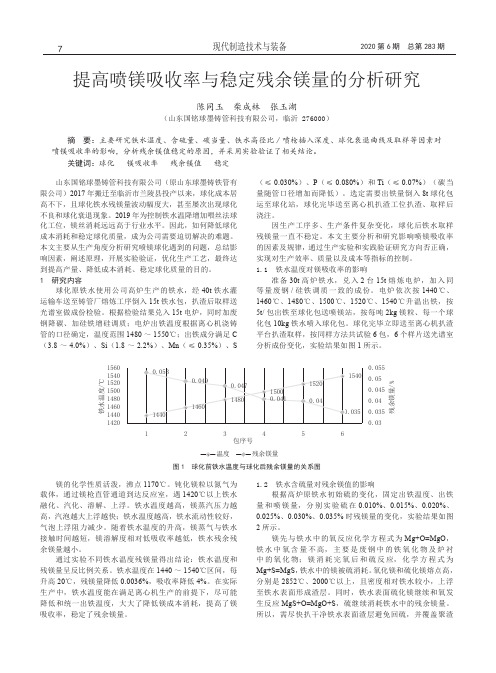
山东国铭球墨铸管科技有限公司(原山东球墨铸铁管有限公司)2017年搬迁至临沂市兰陵县投产以来,球化成本居高不下,且球化铁水残镁量波动幅度大,甚至屡次出现球化不良和球化衰退现象。
2019年为控制铁水温降增加喂丝法球化工位,镁丝消耗远远高于行业水平。
因此,如何降低球化成本消耗和稳定球化质量,成为公司需要迫切解决的难题。
本文主要从生产角度分析研究喷镁球化遇到的问题,总结影响因素,阐述原理,开展实验验证,优化生产工艺,最终达到提高产量、降低成本消耗、稳定球化质量的目的。
1 研究内容球化原铁水使用公司高炉生产的铁水,经40t 铁水灌运输车送至铸管厂熔炼工序倒入15t 铁水包,扒渣后取样送光谱室做成份检验。
根据检验结果兑入15t 电炉,同时加废钢降碳、加硅铁增硅调质;电炉出铁温度根据离心机浇铸管的口径确定,温度范围1480~1550℃;出铁成分满足C (3.8~4.0%)、Si (1.8~2.2%)、Mn (≤0.35%)、S(≤0.030%)、P (≤0.080%)和Ti (≤0.07%)(碳当量随管口径增加而降低)。
选定需要出铁量倒入8t 球化包运至球化站,球化完毕送至离心机扒渣工位扒渣、取样后浇注。
因生产工序多、生产条件复杂变化,球化后铁水取样残镁量一直不稳定。
本文主要分析和研究影响喷镁吸收率的因素及规律,通过生产实验和实践验证研究方向否正确,实现对生产效率、质量以及成本等指标的控制。
1.1 铁水温度对镁吸收率的影响准备30t 高炉铁水,兑入2台15t 熔炼电炉,加入同等量废钢/硅铁调质一致的成份。
电炉依次按1440℃、1460℃、1480℃、1500℃、1520℃、1540℃升温出铁,按5t/包出铁至球化包送喷镁站,按每吨2kg 镁粒、每一个球化包10kg 铁水喷入球化包。
球化完毕立即送至离心机扒渣平台扒渣取样,按同样方法共试验6包,6个样片送光谱室分析成份变化,实验结果如图1所示。
(山东国铭球墨铸管科技有限公司,临沂 276000)摘 要:主要研究铁水温度、含硫量、碳当量、铁水高径比/喷枪插入深度、球化衰退曲线及取样等因素对喷镁吸收率的影响,分析残余镁值稳定的原因,并采用实验验证了相关结论。
低硅球化剂使用的一些情况

低硅球化剂使用的一些情况
一、上汽集团圣德曼公司使用情况:
目前,圣德曼的球化工艺是:
铁水出炉温度:1500-1540摄氏度,原铁水含硫量0.02%左右。
每包出铁700公斤左右,使用盖包球化。
球化剂加入总量:1.5%-1.6%,其中低硅球化剂占0.4%。
残留镁量:0.035%-0.05%。
加入方式是低硅球化剂和普通球化剂简单混合,加入铁水包,用废钢片覆盖,然后马上进行球化。
二、嘉善晋亿公司使用情况
铁水出炉温度:1530摄氏度左右,原铁水含硫量0.02%左右。
每包出铁700-1000公斤左右,铁水包用的是普通堤坝包。
球化剂总加入量1.3%,低硅球化剂占0.4%。
残留镁量:0.04%左右。
低硅球化剂和普通球化剂简单混合后使用(在球化剂称量和加入的过程中即可完成混合),使用废钢片覆盖,然后球化即可。
几点注意事项:
1、球化剂加入铁水包后,拨平即可,不要捣实,如果铁水包是红的,温度很高,加入球化剂后应马上进行球化,否则低硅球化剂会有烧损,即在铁水出炉球化和球化剂加入时间越短越好,防止烧损。
2、低硅球化剂不能烘烤,低硅球化剂是纯镁球化剂,如果烘烤,镁会有烧损。
3、如果在球化剂中有碎块和粉末,不可加入,要单独放置作退货处理。
4、覆盖厚度以铁水液面有一定高度后开始球化反应为宜。
5在球化处理是如果铁水量太少球化效果会不好,因为液面较低,对低硅球化剂的镁吸收不太好,在球化时尽量提高铁水液面。
影响球化剂吸收率和球化稳定性的主要因素

影响球化剂吸收率和球化稳定性的主要因素冲入法处理球铁操作简便,安全可靠,处理铁水量灵活,而且冲入法无须特殊的工艺装备,容易上马,因而被越来越多地用于代替压力加镁法,成为目前应用最广泛的球化处理方法。
冲入法处理流程为:把球化剂(如块度15〜20毫米的稀土镁硅铁)堆放在铁水包一侧,稍加紧实,并根据铁水出炉温度不同加不同的覆盖剂(如硅铁粉、铁屑、铁板等),铁水包装载后预热至暗红色,将铁水包的另一侧对向出铁槽,球化示意图见图1。
球化处理时先出所需铁水总量的60%^75%待铁水与球化剂反应的翻腾基本结束后,再出余量铁水,同时冲入孕育剂,作孕育处理,然后搅拌、扒渣、浇注。
图1冲入法球化示意图1.铁水包2.球化剂3.覆盖剂对于处理少量铁水,可一次出完并作孕育处理,效果更好,温度损失也少。
冲入法球化工艺要保证铁水中残留适当含量的镁和稀土,并使二者有合适的比例,这是保证球化的必要条件。
铁水中残留镁量与稀土量的比例主要依靠球化剂中镁和稀土的比例来保证。
球化元素残留量的绝对值则取决于球化剂的加入量和吸收率。
在冲入法球化处理时,球化元素的主要损耗是氧化烧损和脱硫损耗。
影响球化剂吸收率和球化稳定性的主要因素如下:一、原铁水含硫量的影响原铁水含硫量越高,消耗在脱硫上的球化剂越多。
因此球化剂加入量必须随铁水含硫量增高而加大。
对于含Mg 8%〜10% Si 35%-40%勺稀土镁硅铁,在1380c〜1450c处理,对壁厚100毫米以下铸件,球化剂加入量与含硫量关系见表1。
表1 稀土镁硅铁加入量与原铁水含硫量的关系原铁水含硫量(衿<0.03 0.03〜0.05 0.05〜0.07 0.07〜0.10球化剂加入量(衿0.6〜0.8 0.8〜1.1 1.1〜1.3 1.3〜1.6二、处理温度的影响铁水温度是影响稀土镁硅铁冲入法处理球墨铸铁质量的一个重要因素。
由于球化剂、覆盖剂以及孕育剂的熔化需要耗费大量热量,使整个冲入法处理过程中铁水温度下降较大,1吨〜2吨包降低50c〜100C,大型浇包降温较少。
浅析提高喷镁球化吸收率的途径
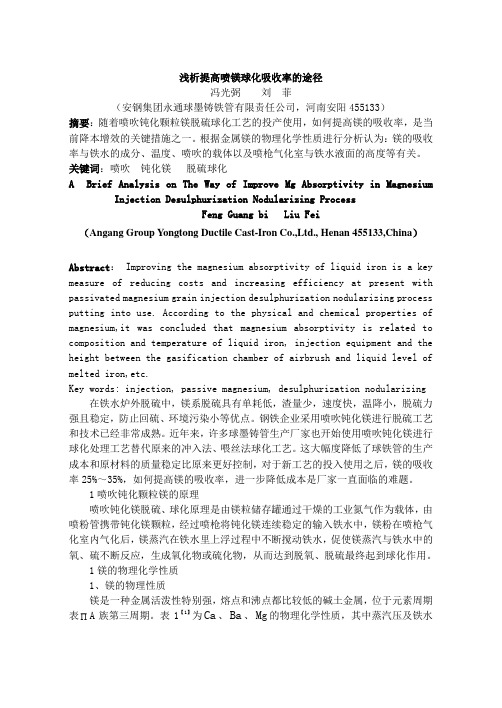
浅析提高喷镁球化吸收率的途径冯光弼刘菲(安钢集团永通球墨铸铁管有限责任公司,河南安阳455133)摘要:随着喷吹钝化颗粒镁脱硫球化工艺的投产使用,如何提高镁的吸收率,是当前降本增效的关键措施之一。
根据金属镁的物理化学性质进行分析认为:镁的吸收率与铁水的成分、温度、喷吹的载体以及喷枪气化室与铁水液面的高度等有关。
关键词:喷吹钝化镁脱硫球化A Brief Analysis on The Way of Improve Mg Absorptivity in MagnesiumInjection Desulphurization Nodularizing ProcessFeng Guang bi Liu Fei(Angang Group Yongtong Ductile Cast-Iron Co.,Ltd., Henan 455133,China)Abstract: Improving the magnesium absorptivity of liquid iron is a key measure of reducing costs and increasing efficiency at present with passivated magnesium grain injection desulphurization nodularizing process putting into use. According to the physical and chemical properties of magnesium,it was concluded that magnesium absorptivity is related to composition and temperature of liquid iron, injection equipment and the height between the gasification chamber of airbrush and liquid level of melted iron,etc.Key words: injection, passive magnesium, desulphurization nodularizing 在铁水炉外脱硫中,镁系脱硫具有单耗低,渣量少,速度快,温降小,脱硫力强且稳定,防止回硫、环境污染小等优点。
稳定球墨铸铁残余镁量的控制措施

稳定球墨铸铁残余镁量的控制措施球墨铸铁残余镁量的控制是保证质量的关键之一,残余镁量控制偏高,易导致渣眼、缩松、气孔等缺陷,同时会增加成本;残余镁量控制偏低,易导致球化不良、球化衰退等废品。
由于镁的活性较大,极易烧损,稳定控制残余镁量比较困难。
不过通过对技术标准、操作过程和检验进行优化改进,实际生产是可以较稳定控制的。
1 影响残余镁量波动的因素分析1.1 球化剂的选择选择合适的球化剂是稳定控制残余镁量最重要的环节,主要包括镁含量、稀土含量、氧化镁含量和粒度。
(1)镁和稀土含量:首先是牌号选择,根据生产的产品、球化包、球化温度等实际情况确定合适的牌号,可以是标准的Mg8Re5、Mg8Re3等,也可以是非标准的Mg8Re4、Mg8Re2、Mg6Re3等;其次是控制球化剂本身镁和稀土含量波动,国家标准允许的波动范围是±1%,有实力的厂家球化剂中镁和稀土含量(质量分数)波动可以分别稳定控制在±(O.020%-0.35%)和±(O.15%-0.025%)。
确定镁和稀土含量,是稳定控制残余镁量的基础。
(2)氧化镁含量:氧化镁含量变化会影响有效镁含量,进而影响残余镁量。
球化剂中的氧化镁含量要求小于1%。
(3)粒度:主要是粒度大小和粒度的均匀性,粒度过大或过小,都会影响镁的吸收,要根据生产的铸件、球化包、球化温度、装包等实际情况确定合适的粒度,并保证粒度的均匀性。
1.2 加入量控制除了关键材料如球化剂、孕育剂加入量外,容易忽视的辅助材料有:覆盖剂、压铁、珍珠岩等加入量不稳定,球化反应波动就会较大,镁的吸收就不稳定。
1.3 球化处理温度控制随着球化处理温度的提高,镁的吸收率先提高,后下降。
因此,必须要保证球化温度的稳定。
1.4 硫量控制由于铁液中的硫量会消耗一定的球化剂,硫量波动大会影响球化剂的最佳加入量。
1.5 球化出铁影响采用双联熔化工艺时,由于中频炉在每一包球化出铁时铁液面高度都不一样,加上中频炉在出铁过程中出铁槽在转动,铁液冲入球化包位置会不断变化,甚至会冲到合金导致合金上浮,球化起爆、反应时间、反应剧烈程度都会变化很大,影响镁的吸收。
- 1、下载文档前请自行甄别文档内容的完整性,平台不提供额外的编辑、内容补充、找答案等附加服务。
- 2、"仅部分预览"的文档,不可在线预览部分如存在完整性等问题,可反馈申请退款(可完整预览的文档不适用该条件!)。
- 3、如文档侵犯您的权益,请联系客服反馈,我们会尽快为您处理(人工客服工作时间:9:00-18:30)。
合 而成 的球化 剂 。我 国使 用最 多 的球 化剂 是稀 上镁 合 金l 1 l 。部分 元素 的物理 性能 见表 1_ _ 2 。当前 大多数球 化剂 是含有镁 的合金 。配 制球化 剂合金 的 目的除 了减 弱镁 的爆 发性 反应 外 ,由于合 金密 度 大于 纯镁 ,处 理时 不 易上 浮 至铁液 表 面 ,从 而 减少镁 的氧化 烧损 ,稳定 镁
c mp tie t x . e c mp n n fF Si 6 2 i s f I ws 6.% Mg, 7 RE, 9 5 Si .0 o e iv e t Th o o e to e Mg RE S a ol t o , 2 2_% 3 . % ,2 5 % Ca .% Ba ,23 ,0.9 Bi 0 % .As a r s l d ci r n o ih e a i 4 0 2 S o t ie n a t g e ut u te i f hg t n ct QT 5 . 2 i ba n d i c s i l o y n
c n i n teme h nc I rp r sfIws b5 .- 6 . a 6 22 2 .%. h b opit o dt ,h c a i o et i a l , 4 23 4 79MP 。 2 .% ̄ 60 T ea s rt i i o ap yS oo vy
元素部分球化元素的物理性质密度cm3table1physicalpropertyofpartspheroidzingelement17469155233787熔点65080485014121537沸点11083468144033102930熔化热888552432655汽化热125466809106试验目的及试验过程序号3898381438253825si1648164416631706mn0045006000587007400320031004000280043004600460044球化剂成分mg62807re27273si395426ca250149ba23bi009球化剂加入量铁液质量kgtable4additionofnodulizer588594质量kg1017011515mg铁液010544012226re铁液004609004128试验结果序号3724380737583855si2727268327362791mn010900570080009700100009000900090049004600510050mg残0048005800580065ce残0028002700310028序号物理性能分析屈服强度mpatable6analysisofmechanicalproperty34243408抗拉强度mpa4785463746794685伸长率228240242260球铁显微组织100fig1microscopicstructureofductileirona未浸蚀b硝酸酒精浸蚀foundryjun2006vol55no6624根据公式1可计算镁的吸收率目前对于镁的吸收率有不同的计算方法本文中引用此公式计算为了比较不同球化剂时镁的吸收率仅作为比较
a e s e il a ay e . Tu ds —o e s h r iia in r c s i r e p cal y n lz d n ih c v r p e ods t po e s S d p e i til a ua t r . o a o td n r — n f cu e a m
关键词 : 球化剂;镁;吸收率;球墨铸铁 中图分 类号 :T 25 文献标 识码 :A 文章编 号 :10—97 (0 6 6 02— 3 G5 0147 20 )0~ 63 0
E e t fMg Co t ti d l e h s r t i fMg f c nen No ui r t e Ab o p i t o o n z on vy
No l e F Si 6 dui r e Mg RE2 o O M g a d e Mg RE3 n n r a u e a e x e i e t l e i te z f IW n F Si 8 i o m I s r e p r m nai d I h z " 1
维普资讯
J n.2 0 u 06
VO , 5 NO 6 I 5 . ・6 3 ・ 2
球化剂含镁量对镁 吸收率的影响
郭振 廷 ,孙雅 心 ,李 蒙
( 郑州大学材料科 学与工程学院 ,河南郑 州 4 01 ) 5( 2 0
摘要: 介绍了球化剂中球化元素的性质及它们对球墨铸铁性能的影响,针对镁对石墨球化效果影响机理进行了分析。
试验 生产 中采 用盖包法球 化处理 ,分别采用低镁球 化剂 F SMg R 2和常规球 化剂 F SMg R 3进行对 比试验 ,其 中 ei 6 E ei 8E F SMg R 2成分 :62 ei 6 E . %Mg ,%R 、2 7 E、3 . S 、2 0 a _ 95 i . %C 、23 a , % B 。铸 态下获得 高韧性球铁 Q 4 0 2 , % 5 %B 、0 9 i 0 T 5 - 2 o4 23 479 a 2 ,%- 6O - 5 . 6 .MP ,3 2 b - 2 2. %。使镁 的吸收率 由常规球 化剂的 3 , %提高到 6 . %。 95 5 12 9
Ab ta t Ch r ce so p e od ig ee e t o uie n h i ef c n d ci r n p r r a c s rc : a a t r f h r izn lm nsi n d l r dt er fe t u te i e f m n e s n z a o l o o a eit d c d i h a e . h h r c e fMg a d t em e h ns o se f c ng a ht lb l g r r u e t e p p r T ec a a t r n h c a im fi fe t r p i go ui no n o t o e n
0 gi p o e o619 % f0 3 . 5 o o m a d l e . f i rv d t .2 M Sm r m 9 5 % f r I n No ui r z
K ywo d : d l e ; : b o pii ; u te i n e r s No ui r Mg a s r t t d c i o z vy l r
镁是最常用的球化元素 ,但由于镁 自身性质活泼 , 不易控制 。因此 对球 化处 理方 法 的研究 主要 是针 对球 化剂中镁吸收率的提高 ,减少镁的烧损 。随着球墨铸 铁 的发 展 ,已经 出现 几种 球 化 处理 方 法 作 者 认为 ,
加 盖法在 国内很 有应 用前 景 。为 了优化 加盖 处理 法参
GUO h nt g, Z e —i SUN Ya xn L n n — i, I Me g
(c o lf aeis c nea dE gn ei , h n z o n esy S h o o M tr lS i c n n i r g Z e g h uU i ri, a e e n v t Z e g h u 4 0 0 , e a , h a hnzo , 502 H n nC i ) n