复合材料的强韧化
第三章 材料强韧化设计的总结与实例

约作用。
(2)涂层硬质合金
在 韧 性 较 好 的 硬 质 合 金 基 体 上 , 通 过 CVD( 化 学 气 相 沉 积 ) 、 PVD(物理气相沉积)、HVOF(High Velocity Oxy Fuel Thermal Spraying)
等方法涂覆一层很薄的耐磨金属化合物,可使基体的强韧性与涂层的
性,以检验计算模型并对计算模型进行修正; 二是对复合材料的强度与韧性进行测试与评价。总之,在强韧指 标需求、损伤模式分析、材料微结构优化匹配、工艺参数控制之间可 以形成对强韧化设计原理和实验室实现的闭环体系,如下图所示。
3.2 材料界面增韧的力学机理及其强韧化设计:
1. 界面设计:
界面在工程材料中几乎无处不在:组合构件的搭接界面,复合材料 层合结构的层间界面,不同材料扩散连接形成的界面,多晶体材料中 不同晶粒之间的界面等。依不同的尺度划分,可将这些界面分别定义 为宏观界面,细观界面以及微观界面。然而,对于实际的材料系统, 往往不能严格区分不同层次界面的界限,它可以同时存在这些界面结 构,也可能只存在其中任何一种层次的界面。不同组分材料之间通过 物化或固化反应形成的界面,这样的界面往往不是一个单纯的几何面,
动控制;
涂层硬质合金刀具的基体经过钝化、精化处理后尺寸精度
较高,可满足自动化加工对换刀定位精度的要求。
上述特点决定了涂层硬质合金刀具特别适用于FMs、CIMS
(计算机集成制造系统)等自动化加工设备。但是,采用涂层方 法仍未能根本解决硬质合金基体材料韧性和抗冲击性较差的问 题。
(3)表面、整体热处理和循环热处理
m(微米级),超细晶粒硬质合金晶粒度可达0.5μm以下(亚微米、
纳米级)。超细晶粒硬质合金与成分相同的普通硬质合金相比, 硬度可提高2HRA以上,抗弯强度可提高600~800MPa。
金属材料的构型化复合与强韧化

金属材料的构型化复合与强韧化摘要:随着我国航空航天、交通运输和海洋装备等重大工程领域的快速发展,其装备对于结构材料提出了高性能、轻量化和高可靠性的迫切需求。
正所谓“一代材料,一代装备”,金属及其合金作为工业领域中不可或缺的结构材料,其综合服役性能的不断提高推动着相关工业技术的进步。
金属结构材料的力学性能指标的优异性和使役过程中的稳定性决定了上述工业领域的先进性和安全性。
关键词:金属材料;构型化复合;强韧化引言与陶瓷和有机高分子材料相比,金属结构材料具有最高的断裂韧性和较高的强度、失效强度可预测性、在中高温度范围内良好的综合力学性能以及可回收性等,因此,金属结构材料在很多工业领域,尤其是对高可靠性和高持久性有严格要求的应用领域是不可替代的材料。
1增强体宏观非均匀构型强韧化早期的构型化复合通过降低基体内部过高的硬化状态来达到提高金属基复合材料塑韧性的目的,将复合材料组织分化为硬相区和软相区,通过硬相-软相界面开裂和软相区塑性变形来偏转和钝化复合材料内部的裂纹,起到阻碍裂纹扩展的作用。
典型代表有叠层、多芯、梯度、环状等构型,其硬相区与软相区的尺度通常在毫米级以上,因此称为增强体宏观非均匀构型。
硬相与软相在尺寸、性能、空间分布等方面的匹配特性决定了复合构型的强韧化效果。
例如借鉴层合板结构设计理念的叠层构型,从宏观尺度不同载荷环境下的应力-应变响应行为研究,到细观、微观尺度的层间界面结合强度调控与强韧化机制揭示,再到基于应变梯度塑性理论的界面影响区-软相区尺寸匹配设计,结构尺度精细化与力学模型定量化推动着叠层构型的设计优化。
叠层构型的增韧效益显著,但是硬相对软相的束缚作用仅仅局限于界面法向,即使通过调整软层宽度至界面影响区宽度的2倍来弥补加工硬化,对软层提前颈缩失效的抑制效果也十分有限。
多芯构型通过设计增强体的富集分布,解除了叠层构型中硬相-软相界面对软相的束缚,但是仍具有良好的增韧效果,这得益于增强体含量高的硬质增强芯与基体之间的界面脱黏。
陶瓷基复合材料增韧机制的研究现状及展望
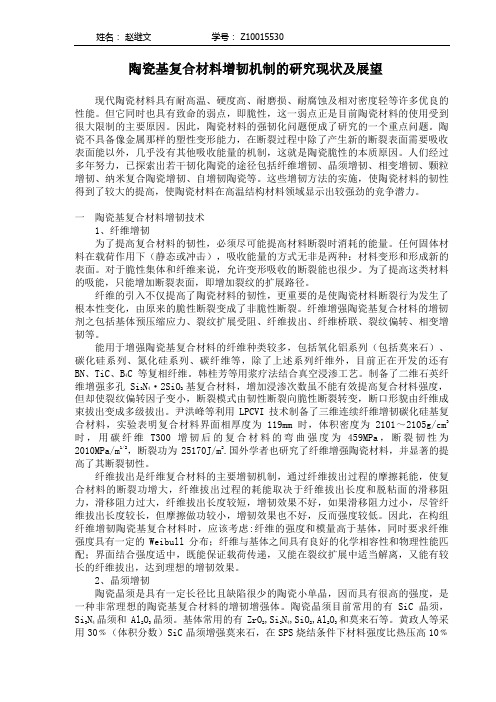
陶瓷基复合材料增韧机制的研究现状及展望现代陶瓷材料具有耐高温、硬度高、耐磨损、耐腐蚀及相对密度轻等许多优良的性能。
但它同时也具有致命的弱点,即脆性,这一弱点正是目前陶瓷材料的使用受到很大限制的主要原因。
因此,陶瓷材料的强韧化问题便成了研究的一个重点问题。
陶瓷不具备像金属那样的塑性变形能力,在断裂过程中除了产生新的断裂表面需要吸收表面能以外,几乎没有其他吸收能量的机制,这就是陶瓷脆性的本质原因。
人们经过多年努力,已探索出若干韧化陶瓷的途径包括纤维增韧、晶须增韧、相变增韧、颗粒增韧、纳米复合陶瓷增韧、自增韧陶瓷等。
这些增韧方法的实施,使陶瓷材料的韧性得到了较大的提高,使陶瓷材料在高温结构材料领域显示出较强劲的竞争潜力。
一陶瓷基复合材料增韧技术1、纤维增韧为了提高复合材料的韧性,必须尽可能提高材料断裂时消耗的能量。
任何固体材料在载荷作用下(静态或冲击),吸收能量的方式无非是两种:材料变形和形成新的表面。
对于脆性集体和纤维来说,允许变形吸收的断裂能也很少。
为了提高这类材料的吸能,只能增加断裂表面,即增加裂纹的扩展路径。
纤维的引入不仅提高了陶瓷材料的韧性,更重要的是使陶瓷材料断裂行为发生了根本性变化,由原来的脆性断裂变成了非脆性断裂。
纤维增强陶瓷基复合材料的增韧剂之包括基体预压缩应力、裂纹扩展受阻、纤维拔出、纤维桥联、裂纹偏转、相变增韧等。
能用于增强陶瓷基复合材料的纤维种类较多,包括氧化铝系列(包括莫来石)、碳化硅系列、氮化硅系列、碳纤维等,除了上述系列纤维外,目前正在开发的还有BN、TiC、B4C等复相纤维。
韩桂芳等用浆疗法结合真空浸渗工艺。
制备了二维石英纤维增强多孔Si3N4·2SiO2基复合材料,增加浸渗次数虽不能有效提高复合材料强度,但却使裂纹偏转因子变小,断裂模式由韧性断裂向脆性断裂转变,断口形貌由纤维成束拔出变成多级拔出。
尹洪峰等利用LPCVI技术制备了三维连续纤维增韧碳化硅基复合材料,实验表明复合材料界面相厚度为119mm时,体积密度为2101~2105g/cm3时,用碳纤维T300增韧后的复合材料的弯曲强度为459MPa,断裂韧性为2010MPa/m1/2,断裂功为25170J/m2.国外学者也研究了纤维增强陶瓷材料,并显著的提高了其断裂韧性。
MoSi_2材料的强韧化

似于高温结构陶瓷 SiC、Si3N4 等 ,其抗氧化温度可达 1600 ℃以上 ,与 SiC等硅基陶瓷相当 ; ③ 适中的密度
其室温增韧与高温补强成为主要研究方向 。本文综述 了 MoSi2 及其复合材料的强韧化研究成果及工业应用 , 以期为进一步研究提供参考 。
(6124 g / cm3 ) ,较低的热膨胀系数 (811 ×10- 6 K- 1 ) ,良 好的电热传导性 (电阻率 2115 ×10- 6 Ω ·cm ,热传导率 25 W /m·K) ; ④具有较高的脆性转变温度 (BDTT为
2 MoSi2 材料的强韧化及应用
211 M oS i2 作为高温发热元件材料 目前常用的高温发热元件有硅碳棒和硅钼棒两
种 。硅碳棒是以高纯 度的绿 色 SiC 为主 要原 料 , 经 2200 ℃高温再结晶制成的非金属发热体 ,最高使用温
32
《金属热处理 》2006年第 31卷第 8期
度为 1350 ℃,其电阻随使用温度和时间而变化 [3 ] 。硅 元件大多在 400 ℃~1200 ℃之间使用 ,然而在 450 ℃~
碳棒主要在电磁材料 、电子陶瓷 、工程陶瓷 、耐火材料 、 550 ℃间 ,MoSi2 在氧化性气氛中会出现加速氧化即 磨具等制造业 ;金属材料的热加工和粉末冶金工业 ;玻 pesting现象 ,使材料发生整体性破坏 。研究表明 ,这
璃工业的熔化 、精炼工序 ;石油化工 、纺织 、食品工业和 造纸工业的烘烤工序等领域获得应用 ,是应用最广和
表 1 具有 2000 ℃以上熔点的部分硅化物结构及其性能 [ 6] Table 1 Structure and properties of the silic ides ( m elting po in t > 2000 ℃)
粉末冶金原理
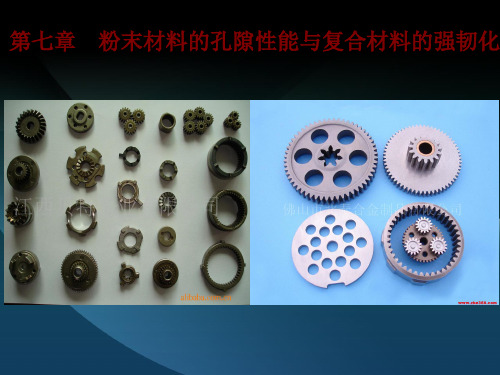
测定比表面的透过法是通过测定透过系数来求得比表 面的。这个方法的原理是根据柯-卡门公式:
测定比表面的透过法,通常是以气体(特别是空气) 为介质,操作简便、迅速,得到了广泛应用。但此法只适 用于层流而不适用于紊流,并且当孔道很细,接近气体分 子平均自由程时,也不适用。
四、粉末多孔材料的其他特性
粉末多孔材料易压缩变形的特性,是通过各种变形 方式使多孔体致密化的基础。关于多孔体的变形特性, 第六章已经详细讨论过,不再重复。在工业技术上也常 利用这一特性来制取密封材料。高孔隙度的多孔铁的柔 软性和易压缩变形特性接近于铅。德国曾用多孔铁代替 铜制造炮弹箍,以节约大量铜材,它具有和铸铜相同的 硬度,当炮弹沿炮身来复线射出时,炮弹箍由于易压缩 变形和孔隙中润滑剂的作用,不至于磨坏来复线。
一、粉末材料孔隙度和孔径的测定
孔隙度和密度是粉末冶金材料的基本特性,孔隙度和 密度的测定是控制粉末冶金材料质量的主要方法之一。试 样的体积可采用量度几何尺寸的方法,也可采用液体静力 学称量方法来测定。对于致密材料,可直接将试样放在水 中称重,其残留孔隙度也可以采用显微镜法进行定量估算。 对于具有开孔隙的材料,用液体静力学法称量时,为了不 让液体介质进入孔隙,可浸渍熔融石蜡、石蜡泵油、无水 乙醇液体明胶溶液和凡士林等物质,使烧结体的 开孔隙饱和或堵塞。
在多孔材料中,层流时比能损失较小(和流速的一次 方成正比),而且在流体流过很细的孔道时,流速一般不 会很高。下面着重研究在层流条件下流体的透过规律。 当有层流的流体通过多孔材料时,在单位面积上的流速与 其压力梯度成正比,通常以达尔西公式表示:
为了工程上使用方便,在实际测量中多采用相对 透过系数 对于气体叫相对透气系数;对于液 体叫相对渗透系数。则式(7-3)可变为:
第三章 材料强韧化设计的总结与实例汇总

和断口形貌的显微组织观测,提出复合材料的损伤与失效机理,
提出复合材料增强与增韧的途径;
(2) 增强相、基体及其界面的损伤与失效准则研究 参数的选择与计算,破坏临界值的测量方法等; (3) 应力-应变分析、损伤与断裂参量计算 指以数值计算 (尤 包括控制
其是有限元 )为基础的复合材料细观计算力学分析,通过发展破
制备复合材料,进行力学性能试验,以对复合材料的强韧力学
性能进行评价,对强韧化设计准则和模型进行检验和修正后再 反馈到复合材料设计与制备中去。这种强韧化设计的总体思路 可由下图来简单表示。
复合材料强韧化力学设计准则与模型的建立过程分五项工作 内容(见上图): (1) 复合材料强韧化机理研究 指通过对复合材料的损伤演化
1 硬质合金刀具材料的研究现状
由于硬质合金刀具材料的耐磨性和强韧性不易兼顾,
这给硬质合金刀具的选用和管理带来诸多不便。为进
坏单元技术模拟多相复合材料的破裂与界面损伤临界行为并定
量计算出其临界值;
(4) 复合材料的损伤、扩展与失效过程的模拟。指在应力 与断裂参量分析、损伤与失效准则研究的基础上,模拟复合材 料在外力、温度、电磁场等作用下的应力-应变变化的相应过
程,微缺陷的形核、长大、汇聚与扩展直至断裂的整个过程;
(5) 复合材料微结构优化设计。由于应力分析、损伤与失 效破坏准则都涉及材料组元的物理力学性能和几何特性(如几 何尺寸、形貌、分布状态、体分率以及界面结合状态等),所 以可优化分析复合材料微结构对力学性能的影响,实现复合材
类:物理因素和化学因素。物理因素包括吸附、扩散、机械等作用,
而化学因素则主要是化学键结合。无论是物理因素还是化学因素, 都与形成界面的组分材料及其工艺条件有。
工艺、界面以及材料宏观性能三者之间有着不可分割的联系。 由于界面两侧材料的失配使连接界面产生应力应变集中,且界面 形成过程中会不同程度地留有连接的工艺性缺陷,使得界面往往成为 发生断裂的源泉:
不饱和聚酯树脂增强增韧的研究

不饱和聚酯树脂增强增韧的研究不饱和聚酯树脂(UP)作为一种复合材料的树脂基体,具有较高的比强度和比刚度,且机械性能高、成型工艺简单、产品质量轻等优点,在复合材料地板领域具有广泛的应用前景。
但UP的固化物一般存在强度低、收缩率大、韧性差、容易开裂等缺点,因此对UP的增强增韧改性仍然吸引着很多研究者的目光。
本文以通用型UP为基体,用二氧化硅(Si O2)、碳酸钙(Ca CO3)、聚乙二醇(PEG)、短切玻璃纤维(SGF)对UP进行增强增韧研究。
然后以玻璃纤维布(GF)增强UP(FRUP)为面层,以改性UP(MUP)为芯层,通过手糊成型的方法制备夹层板复合材料。
并在此基础上制备了以FRUP为面层,以混杂短纤维增强MUP为芯层的夹层板复合材料。
对制备的复合材料进行了力学性能测试、动态热机械性能测试、耐热性能测试;使用扫描电镜对复合材料的冲击断面进行观察,初步研究了填料的含量对复合材料冲击韧性的影响。
1、UP基体增强增韧改性研究无机填料/UP复合材料性能研究结果表明:(1)与Si O2改性的UP相比,用Ca CO3改性的UP复合材料性能更加优越,当Ca CO3质量分数为10%时,复合材料拉伸强度和冲击强度均达到最大值34.71MPa和8.2KJ/m2,与纯UP相比分别提高了21.3%和46.4%。
(2)无机填料的加入可以降低UP的收缩性能,当填料含量为10%时,收缩性能降低最明显。
PEG增韧改性Ca CO3/UP复合材料性能研究结果表明:(1)PEG的加入能够显著提高复合材料的冲击性能,加入30%PEG复合材料与未添加PEG的复合材料相比冲击强度从7.9k J/m2提高到11.2k J/m2,冲击强度提高了42.7%。
(2)PEG的加入降低了复合材料的动态储能模量,提高了复合材料的韧性。
SGF增强PEG/Ca CO3/UP(MUP)复合材料性能研究结果表明:(1)SGF的加入,可以提高复合材料冲击强度,当SGF含量为50%时,冲击强度达到17.3k J/m2,与未添加SGF的复合材料相比冲击强度提高了54.4%。
复合增韧双马来酰亚胺原理_概述说明以及解释_
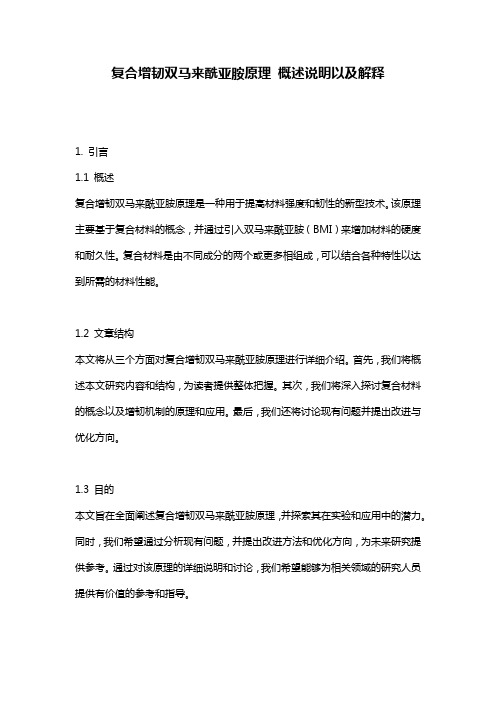
复合增韧双马来酰亚胺原理概述说明以及解释1. 引言1.1 概述复合增韧双马来酰亚胺原理是一种用于提高材料强度和韧性的新型技术。
该原理主要基于复合材料的概念,并通过引入双马来酰亚胺(BMI)来增加材料的硬度和耐久性。
复合材料是由不同成分的两个或更多相组成,可以结合各种特性以达到所需的材料性能。
1.2 文章结构本文将从三个方面对复合增韧双马来酰亚胺原理进行详细介绍。
首先,我们将概述本文研究内容和结构,为读者提供整体把握。
其次,我们将深入探讨复合材料的概念以及增韧机制的原理和应用。
最后,我们还将讨论现有问题并提出改进与优化方向。
1.3 目的本文旨在全面阐述复合增韧双马来酰亚胺原理,并探索其在实验和应用中的潜力。
同时,我们希望通过分析现有问题,并提出改进方法和优化方向,为未来研究提供参考。
通过对该原理的详细说明和讨论,我们希望能够为相关领域的研究人员提供有价值的参考和指导。
以上是“1. 引言”部分的内容。
2. 复合增韧双马来酰亚胺原理:2.1 复合材料概念:复合材料是由两种或更多种不同组分组成的,具有明显界面和协调工作的材料。
通常是将一种或多种纤维或颗粒状增强相与连续相(基体)结合在一起形成的。
复合材料具有优异的力学性能、减轻重量、提高刚度和强度等特点,因此被广泛应用于航空航天、汽车工程、建筑结构等领域。
2.2 增韧机制介绍:增韧是指通过对复合材料进行改性,使其能够在拉伸或冲击等载荷下表现出更好的韧性。
常见的增韧机制包括斜交层、吸能微裂纹和位错抗行进等。
- 斜交层: 通过在复合材料中引入不同方向的纤维层,使其在受到外力时能够产生微小的位移,从而吸收冲击力并阻碍裂纹扩展。
- 吸能微裂纹: 在复合材料中添加一些可拉断的微裂纹,以吸收能量并阻止裂纹扩展。
- 位错抗行进: 将位错线引入到复合材料中,增加了其变形能力和韧性。
2.3 双马来酰亚胺引入与作用:双马来酰亚胺(BMI)是一种高性能的热固性树脂,具有优异的耐高温、耐化学品和机械性能。
钛-铝-碳复合材料的结构调控、性能及强韧化机理研究
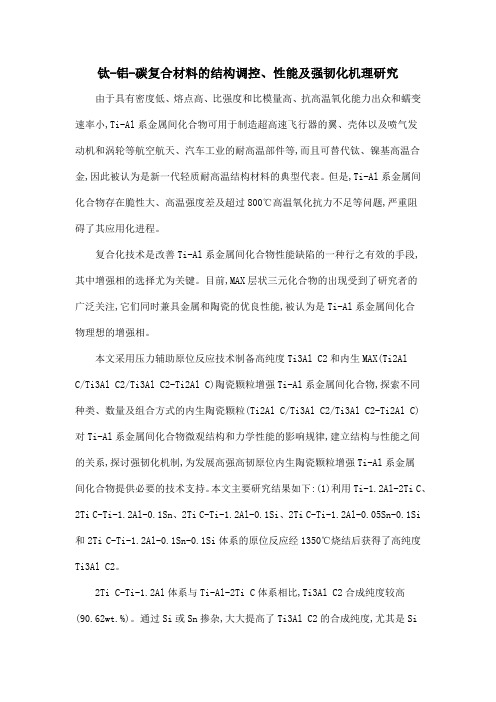
钛-铝-碳复合材料的结构调控、性能及强韧化机理研究由于具有密度低、熔点高、比强度和比模量高、抗高温氧化能力出众和蠕变速率小,Ti-Al系金属间化合物可用于制造超高速飞行器的翼、壳体以及喷气发动机和涡轮等航空航天、汽车工业的耐高温部件等,而且可替代钛、镍基高温合金,因此被认为是新一代轻质耐高温结构材料的典型代表。
但是,Ti-Al系金属间化合物存在脆性大、高温强度差及超过800℃高温氧化抗力不足等问题,严重阻碍了其应用化进程。
复合化技术是改善Ti-Al系金属间化合物性能缺陷的一种行之有效的手段,其中增强相的选择尤为关键。
目前,MAX层状三元化合物的出现受到了研究者的广泛关注,它们同时兼具金属和陶瓷的优良性能,被认为是Ti-Al系金属间化合物理想的增强相。
本文采用压力辅助原位反应技术制备高纯度Ti3Al C2和内生MAX(Ti2AlC/Ti3Al C2/Ti3Al C2-Ti2Al C)陶瓷颗粒增强Ti-Al系金属间化合物,探索不同种类、数量及组合方式的内生陶瓷颗粒(Ti2Al C/Ti3Al C2/Ti3Al C2-Ti2Al C)对Ti-Al系金属间化合物微观结构和力学性能的影响规律,建立结构与性能之间的关系,探讨强韧化机制,为发展高强高韧原位内生陶瓷颗粒增强Ti-Al系金属间化合物提供必要的技术支持。
本文主要研究结果如下:(1)利用Ti-1.2Al-2Ti C、2Ti C-Ti-1.2Al-0.1Sn、2Ti C-Ti-1.2Al-0.1Si、2Ti C-Ti-1.2Al-0.05Sn-0.1Si 和2Ti C-Ti-1.2Al-0.1Sn-0.1Si体系的原位反应经1350℃烧结后获得了高纯度Ti3Al C2。
2Ti C-Ti-1.2Al体系与Ti-Al-2Ti C体系相比,Ti3Al C2合成纯度较高(90.62wt.%)。
通过Si或Sn掺杂,大大提高了Ti3Al C2的合成纯度,尤其是Si和Sn协同掺杂后,Ti3Al C2的合成纯度最高达98.94wt.%。
聚合物复合材料中的分散和增韧

聚合物复合材料中的分散和增韧聚合物复合材料是一种重要的材料,广泛用于汽车、飞机、船舶、建筑等领域。
这种材料具有重量轻、强度高、成型性好等优点,但是也有一些缺点,如脆性、易碎等。
为了克服聚合物复合材料的缺点,科学家们开发了各种方法,其中最重要的是分散和增韧。
下面我们将分别介绍这两种方法,并探讨它们的作用和应用。
一、分散分散是指将纳米颗粒、碳纤维等增强材料均匀地分散在聚合物基体中。
这样可以提高材料的强度、刚度和耐热性,同时还可以改善材料的耐磨性、耐腐蚀性等性能。
分散技术主要有两种:一种是机械分散,另一种是化学分散。
机械分散是指利用高剪切力将增强材料分散在聚合物基体中,常用的设备有搅拌器、超声波器等。
化学分散是指利用界面活性剂、增溶剂等化学剂来增进材料分散性。
分散技术的主要作用是改善复合材料的力学性能和热稳定性。
例如,碳纤维分散在聚合物基体中可以提高材料的强度和刚度,增强材料的分散还可以提高材料的耐磨性和耐腐蚀性。
二、增韧增韧是指在聚合物基体中添加吸收能量的增韧剂,以提高材料的韧性和断裂韧性。
增韧技术主要有两种:一种是弹性增韧,另一种是粘弹性增韧。
弹性增韧是指在聚合物基体中添加弹性剂,以吸收能量并防止裂纹扩展。
常用的弹性剂有SBS、SEBS、EPDM等。
粘弹性增韧是指在聚合物基体中添加粘弹性剂,在材料拉伸和断裂时吸收能量,保持断裂韧性。
常用的粘弹性剂有PVC、PMMA等。
增韧技术的主要作用是提高材料的韧性和断裂韧性,防止裂纹扩展。
例如,在增韧剂的作用下,聚碳酸酯等材料的断裂韧性可以提高数倍以上。
结语:聚合物复合材料中的分散和增韧是重要的技术,可以提高复合材料的强度、刚度、耐热性、耐磨性、耐腐蚀性等性能,从而扩大它们的应用范围。
虽然这些技术非常有用,但是它们之间也存在一些相互影响和制约的关系。
因此,在设计和制备复合材料时,需要综合考虑它们的分散和增韧问题,以达到最佳的性能和经济效益。
复合材料的强韧化
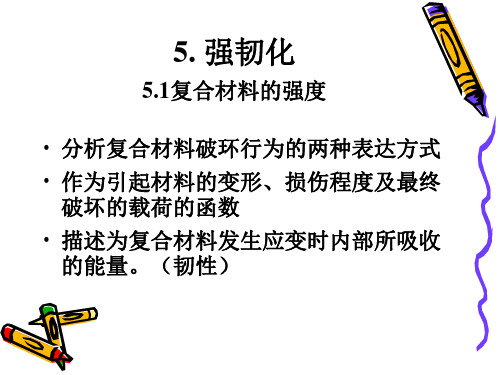
5. 强韧化5.1复合材料的强度•分析复合材料破环行为的两种表达方式•作为引起材料的变形、损伤程度及最终破坏的载荷的函数•描述为复合材料发生应变时内部所吸收的能量。
(韧性)纤维与基体的断裂基体的开裂基体的切变5.1.1 长纤维复合材料的断裂模式纤维的断裂应变大于基体的断裂应变纤维的断裂应变小于基体的断裂应变f '复合体系弹性模量(GPa )断裂应变(%)断裂应力(MPa )σmfu(MPa)σfmu (MPa)f (体积% )σ1u(MPa)高模量碳纤维3500.7250035- 2.51267环氧树脂基体4 2.0100玻璃纤维71 2.82000-143010.91000聚酯基体3 2.070Nicalon 纤维1300.81000-17510.8500玻璃基体700.14100f '与纤维平行的载荷最初的断裂通常发生在最弱处应力值增加发生材料全体的断裂两个类型累积损伤模型纤维断裂传播模型与纤维平行的应力σ在裂纹1附近增长较快在裂纹的传播方向上也存在显著的横向应力纤维与基体的刚性比越大,应力集中越严重;界面剪切强度接近0时,应力集中可以忽略不计;相邻纤维之间的距离增大(纤维的体积分数减少),则应力集中会减轻。
聚酯/玻璃环氧树脂/碳纤维界面强度较大产生大的应力集中呈现出贯通大的纤维束的倾向聚酯/Kevlar纤维连接较弱,发生了大范围的纤维拔出有害的环境,沿裂纹进行浸透,纤维强度显著下降横向拉伸断裂强度及应变都显著降低局部应力纤维对横向强度没有贡献对于横向载荷,泊松比有下降的倾向()[]2/12/21πσσf m u u -=剪切断裂复合材料轴向强度σ1u (MPa)横向强度σ2u(MPa)剪切强度τ12u(MPa)轴向断裂应变ε1u(%)横向断裂应变ε2u(%)聚酯/50%玻璃7002050 2.00.3环氧树脂/50%碳(高弹)100035700.50.3环氧树脂/50%Kevlar12002050 2.00.4压缩断裂Ym /c στϕ*=∆5.1.2 受到非轴向载荷的单层板的断裂•1)最大应力学说•在单纯的最大应力学说中,假定与纤维平行或垂直的应力达到某一极限值时,发生断裂。
2、3讲陶瓷基复合材料的强韧化机理

2) 韧化机理
• 均匀无限大基体中存在第二相颗粒时,颗粒将 受到一个压力 2TE m p 1 m 2 1 2 p • 式中,=p-m,、E为泊松比和弹性模量; 下标m、p分别表示基体和颗粒;T为基体的塑 性变形可忽略时的温度Tp冷却到室温TR时的温 度差,=Em/Ep。 • 这一内压力在基体中距球形颗粒中心为R处产生 径向正应力及切向正应力t(图) 3 r p R
陶瓷基复合材料的力 – 位移曲线
• 而纤维增强陶瓷基复合材料不仅使其弹性模量和强度大大提高,而且还改 变了力 – 位移曲线的形状(如图)。
陶瓷的强韧化
• 脆性是陶瓷材料的致命弱点,其来源于高键能引起的缺陷敏感 性,陶瓷材料的强韧化本质上就是降低其对缺陷的敏感性。 陶瓷材料缺陷敏感性存在着显著的尺寸效应,即块体材料的尺 寸越大,缺陷数量越多。根据统计学原理,缺陷数量越多,缺 陷的概率尺寸越大。 陶瓷材料的强度和韧性具有“最弱连接”特征,即取决于缺陷 的最大尺寸而不是数量,实际上,陶瓷基复合材料的强韧化就 是利用了缺陷的尺寸效应。(掺杂改性)
2 韧化机理
• 径向微开裂容易导致微裂纹连通,对材料强度不利;
• 切向微开裂使颗粒与基体脱开,相当于形成一个颗粒尺寸大小 的孔洞,同样对材料强度不利。
• 所以在采用第二相颗粒补强增韧时,一般要求颗粒的直径小于 导致自发微开裂的临界颗粒直径dc。
√ 应力诱导微开裂增韧(dmin<d<dc)
• 当p>m,d<dc时,宏观裂纹的尖端由于外加应力的作用会出现 一个微开裂过程区,如图所示。 • 可推导出产生应力诱导微开裂时第二相颗粒的最大直径dc和最 小直径dmin。当d>dc时材料在从烧结温度冷却到室温TR时将产生 自发开裂,当d<dmin时外加应力不能在裂纹尖端诱发微开裂。
复合材料的增韧技术
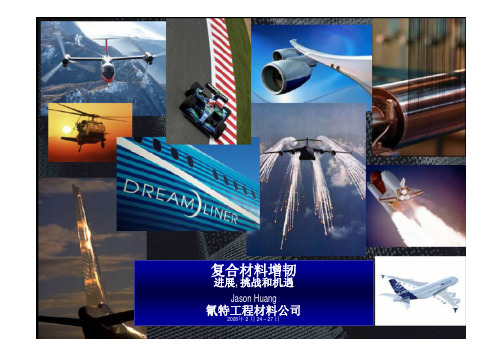
787-X 787 A30X
A350
A380
(自动铺带, 纤维自动铺贴, 等)
性能(提高破损容限)
Dependant on technology for affordable, durable, multifunctional high performance composite systems
复合材料的增韧
形成区 (应力区)
空腔区
塑性剪切区
裂纹起点
裂纹扩展的过程: 空腔区首先形成 (在列为起点前), 接着是空腔间的剪切滑移线提高裂纹增长的生成抵 抗能力 在裂纹起点后面塑性剪切区形成 提高裂纹增长的扩展抵抗能力 形成区的整体尺寸 复合材料韧性
Copyright 2008 by Cytec Engineered Materials, Published by Society for the Advancement of Material and Process Engineering with permission
4
复合材料: 优点及用途
用途
60
787-X
50
787 A30X
% 复合材料
40
A350
30 20
A320 A380
A321 A340 A310 767 MD80 757 A300 737-300 MD11 747-400 A330
取决于低成本,耐久,多 功能高效能复合材料 体系的技术发展
10 0
1975
类型: 连续纤维增强复合材料
金属基体
铝基和硼或碳化硅纤维
- 1、下载文档前请自行甄别文档内容的完整性,平台不提供额外的编辑、内容补充、找答案等附加服务。
- 2、"仅部分预览"的文档,不可在线预览部分如存在完整性等问题,可反馈申请退款(可完整预览的文档不适用该条件!)。
- 3、如文档侵犯您的权益,请联系客服反馈,我们会尽快为您处理(人工客服工作时间:9:00-18:30)。
5. 强韧化
5.1复合材料的强度
•分析复合材料破环行为的两种表达方式•作为引起材料的变形、损伤程度及最终破坏的载荷的函数
•描述为复合材料发生应变时内部所吸收的能量。
(韧性)
纤维与基体的断裂
基体的开裂基体的切变
5.1.1 长纤维复合材料的断裂模式
纤维的断裂应变大于基体的断裂应变纤维的断裂应变小于基体的断裂应变
f '复合体系弹性模量(GPa )断裂应变(%)
断裂应力(MPa )σmfu
(MPa)σfmu (MPa)f (体积% )σ
1u
(MPa)
高模量碳纤维
3500.7250035- 2.51267环氧树脂基体
4 2.0100玻璃纤维71 2.82000-143010.91000
聚酯基体3 2.070Nicalon 纤维
1300.81000-17510.8500玻璃基体700.14100
f '
与纤维平行的载荷最初的断裂通常发生在最弱处
应力值增加
发生材料全体的断裂两个类型
累积损伤模型
纤维断裂传播模型
与纤维平行的应力σ
在裂纹
1
附近增长较快
在裂纹的传播方向上也存在显著的横向应力
纤维与基体的刚性比
越大,应力集中越严重;
界面剪切强度接近0时,应力集中可以忽略不计;
相邻纤维之间的距离
增大(纤维的体积分
数减少),则应力集
中会减轻。
聚酯/玻璃
环氧树脂/碳纤维
界面强度较大
产生大的应力集中
呈现出贯通大的纤维束的倾
向
聚酯/Kevlar纤维
连接较弱,发生了大范围的纤维拔出
有害的环境,沿裂纹进行浸透,纤维强度显著下降
横向拉伸断裂强度及应变都显
著降低
局部应力
纤维对横向强度
没有贡献
对于横向载荷,泊松比有下降的倾向
()[]
2/12/21πσσf m u u -=
剪切断裂
复合材料轴向强
度
σ1u (
MPa)横向强
度
σ
2u
(
MPa)
剪切强
度
τ
12u
(
MPa)
轴向断
裂应变
ε
1u
(%)
横向断
裂应变
ε
2u
(%)
聚酯/50%玻璃7002050 2.00.3环氧树脂/50%
碳(高弹)
100035700.50.3
环氧树脂
/50%Kevlar
12002050 2.00.4
压缩断裂
Ym /c στϕ
*
=∆
5.1.2 受到非轴向载荷的单层板的断裂•1)最大应力学说
•在单纯的最大应力学说中,假定与纤维平行或垂直的应力达到某一极限值时,发生断裂。
[]1212x y xy T σσσσττ⎡⎤⎡⎤⎢⎥⎢⎥=⎢⎥⎢⎥⎢⎥⎢⎥⎣⎦⎣⎦[]22222222c s cs T s c cs cs cs c s ⎡⎤⎢⎥=-⎢⎥⎢⎥--⎣⎦
其他的断裂学说
•在组合应力,特别是对叠层板的各个层片施加平面应力的条件下,对长纤维复合材料的断裂进行了各种预测。
Rowlands于1985年发表了对该方法的展望。
大部分方法都是基于对金属展开的屈服标准的采用。
最为一般的是Tresca 与Mises的屈服标准。
Tresca的标准相当于达到最大剪切应力的极限值时发生的屈服
实验数据
5.1.3 叠层板的强度
层间应力
末端效应
5.1.4 受到内压的圆管的破损
5.2. 复合材料的韧性
•受到负荷的材料所吸收的能量与应力同等重要•韧性优异的材料在断裂时需要大的能量
•在受到冲击等多种负荷的情况下,材料是吸收一定的能量而断裂
•在很多情况下,决定材料性能的是断裂韧性。
5.2.1 断裂机理
基本概念
•材料的断裂是由于裂纹周围积蓄的能量随裂纹的扩展而释放所发生。
•如果能量不能达到平衡,则裂纹不扩展。
•裂纹先端的高应力与裂纹传播的能量不能取得平衡时,裂纹不发生扩展。
•在一般的金属材料中,由于晶粒界上滑移高频率地发生,所以显示出高的断裂韧性。
*2
2E C γσπ=2/G c E σπ=临界长度能量释放率
*c c
K c EG σπ==
完全的开口模式(K
II =0)中,φ=0;完全的剪切
模式(K I =0)中,φ=90。
以应力或能量基础的裂纹变形•以裂纹先端的应力为焦点。
指出在受到与纤维平行的负荷的复合材料中,裂纹接近纤维时,在裂纹的先端产生横向应力,这样的应力使界面开口,使来自纤维插入部的裂纹钝化,或者发生使裂纹变形的倾斜。
•能量基础的裂纹变形的标准。
一个模块中产生的裂纹,随着裂纹的增大而向另一模块扩展。
所以可以推测,通过施加为了使裂纹扩展的负荷,能够使裂纹在该过程中贯通到另一模块,或者是发生沿着界面的变形。
()2141m m f f IC fC f f h E h E G G h E πν⎡⎤⎛⎫+⎢⎥≤ ⎪ ⎪-⎢⎥⎝⎭⎣⎦
5.2.2 对断裂能量的贡献
•通常的工业材料中要求优异的断裂韧性。
关于断裂韧性,对于复合材料有利的是促进材料内对能量的吸收的机制。
而且,理解对该能量吸收的控制机理也是十分主要的。
提高断裂韧性
•使强化材料分布均匀,限制颗粒或纤维的尺寸,改善成形工序。
优异的界面强度的提高。
•非金属基体,对于基体的能量吸收,虽然是有限的范围,但是,强韧化的机理还是有很大意义的。
•塑料基复合材料的韧性的改善,其基本想法也是使用其韧性高于基体的强化材料。
基体的变形
•金属基体一般在裂纹附近产生大的滑移,所以具有高的断裂韧性。
但是高分子材料(特别是热固性树脂)与陶瓷的断裂韧性一般较低。
•复合材料的断裂中基体的变形,与同一材料非强化状态下的变形相比,有很大的不同。
•基体的变形会受到很多约束,在刚性高的纤维周围的基体,不能进行自由的变形,负荷的传递的不同。
•裂纹附近的应力是三维应力场,阻碍基体伴随着变形的塑性流动。
•横向的拉伸应力,阻碍了塑性流动,却在材料中产生了空洞,反而容易断裂。
纤维的断裂
•复合材料的的断裂中纤维的断裂是其基本形式。
•断裂能量中纤维断裂所占的比例很小。
•有机体系纤维的断裂能量也较大。
例如KevlarTM 纤维。
•金属纤维的断裂能量比无机纤维要大,强化混凝土中钢筋的体积比虽然较低,但仍然能够得到好的效果,
•在复合材料中,如果不能充分利用纤维的性能,提高韧性是比较困难的。