模具的温度控制
模具的温度控制

模具的温度控制
2
温度控制的必要性
> 在射出成形中,射出於模具內之熔融材料溫度,一般在 150~350℃之間,但由於模具之溫度一般在40~120℃ 之間,所以成形材料所帶來的熱量會逐漸使模具溫度 升高。另一方面,由於加熱缸之噴嘴與模具之注道襯 套直接接觸,噴嘴處之溫度高於模具溫度,亦會使模具 溫度上升。假使不設法將多餘之熱量帶走,則模具溫 度必然繼續上升,而影響成型品的冷卻固化。相反地, 若從模具中帶走太多的熱量,使模具溫度下降,亦會影 響成型品的品質。故不管在生產性或成型品的品質上 ,模具的溫度控制是有其必要性的。
20
小结
> 模具表面快速温控设备的应用是先进射出成 型领域一项重要技术,其加热速度快较不影 响成型周期,使用的加热能源较低,有效符 合绿色制造技术,而且模具表面浅层加热, 模具较不会整体热胀冷缩,影响模具寿命。 另外模具冷却方面,为了达成模具急速冷却 之目的,表面加热给予模具的热能较少,因 此降温速度较快,同时可配合模内3D冷却管 路设计的优化,未来的温控技术自由度得以 有效提升。
循环周期 注塑件性能 强度 翘曲 尺寸 外观
5
传统模具水路
6
传统水路设计
7
异型水路
8
异型水路的温度分布
9
快速变模温技术原理及特点
> 模具温度是注塑成型过程中影响制品质量的重要工艺 参数。 > 收缩变形是影响注塑制品最终尺寸精度的关键因素之 一。影响制品收缩变形的因素包括制品成型过程中的 残余应力、从型腔取出後的分子继续结晶行为以及材 料的应力松弛。在注射成型制品时,通过提高模具温 度可有效降低制品残余应力的产生。同时,高模温还 可使制品充分结晶,从而显着降低脱模後收缩量。此 外,高模温还可减小制品的冷却速率,使聚合物分子 链充分地松弛、恢复,此时制品内应力小,後收缩变 形也小。快变模温控制技术与传统模温控制技术相比 较,其根本区别在于对模具温度的动态控制。
模具温度偏差管理基准
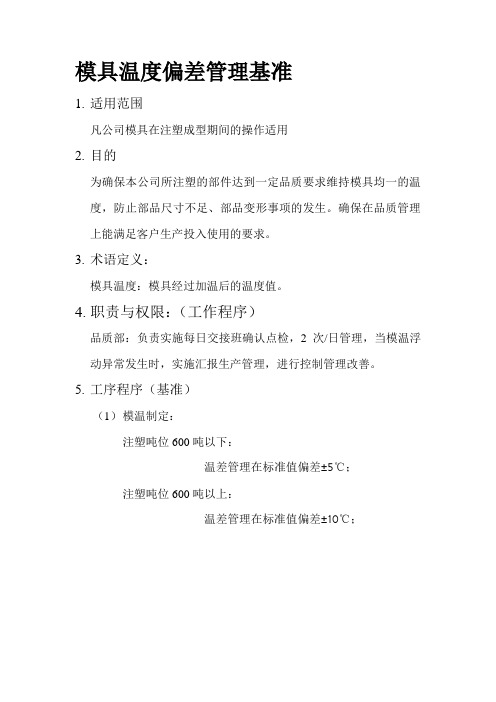
模具温度偏差管理基准
1.适用范围
凡公司模具在注塑成型期间的操作适用
2.目的
为确保本公司所注塑的部件达到一定品质要求维持模具均一的温度,防止部品尺寸不足、部品变形事项的发生。
确保在品质管理上能满足客户生产投入使用的要求。
3.术语定义:
模具温度:模具经过加温后的温度值。
4.职责与权限:(工作程序)
品质部:负责实施每日交接班确认点检,2次/日管理,当模温浮动异常发生时,实施汇报生产管理,进行控制管理改善。
5.工序程序(基准)
(1)模温制定:
注塑吨位600吨以下:
温差管理在标准值偏差±5℃;
注塑吨位600吨以上:
温差管理在标准值偏差±10℃;
模具温度偏差管理基准
5.工序程序(基准)
(2)检查状态与频率:
①对于每日模具更换后,30分后监测,记录与《注塑工艺条
件》;②每班(白/夜)交接时进行检测记录与《工程检查日
报》;
(3)测试方式:
取红外线模温测试仪,敲击按钮,对准模具行动定模测试,
距离15+5cm处,监测测试数据;
(4)异常处理:
当监测温度未能满足标准要求,即可实施停机改善,不予生
产注塑。
模具温度偏差管理基准5.温差基准:。
压铸模具温度控制.

材料工程学院材料成型教研室
向其他地方通水。
材料工程学院材料成型教研室
铝合金铸件铸造技术 (3)模温机
对模具进行加热保证模具工作温度。
材料工程学院材料成型教研室
铝合金铸件铸造技术
(4)压铸模具温度测量 1) 表面温度测量 使用表面温度测量压铸模具表面温度,有接触式和非接触式。 2)内部温度测量 一般使用热电偶测量。模具上钻孔深度取决于要进行温度测量的
铝合金铸件铸造技术 (2)压铸模具工作温度控制
一般采用循环冷却液进行模具冷却,也可采用压缩空气冷却。 1)空气冷却
材料工程学院材料成型教研室
பைடு நூலகம்
铝合金铸件铸造技术
2)水冷却 将水直接通入压铸模具中的冷却管道中的冷却管道对压铸模具进
行冷却。 注意事项: a.冷却水温度不宜过低(30℃以上); b.最好使用软水; c.作业初期,只向直浇道、分流锥等部位通水,等模具温度上升在
铝合金铸件铸造技术
压铸模具温度控制 (1)压铸模具预热 在压铸模具达到一定温度后,压铸生产才能正常进行。 生产中广泛采用模温机和燃气装置预热模具。 注意事项: 1)预热要均匀; 2)型芯温度要达到生产时的使用温度; 3)预热后模具要进行清理及润滑; 4)外部加热时,尽量用小火。
材料工程学院材料成型教研室
压铸模具温差标准

压铸模具温差标准
一、温度范围
压铸模具的温度范围应控制在一定范围内,以确保生产过程中模具的稳定性和产品的质量。
通常,模具温度应保持在40℃至60℃之间。
二、温度稳定性
模具温度的稳定性对产品的一致性和模具的使用寿命至关重要。
模具温度应保持稳定,以避免因温度波动而导致的模具热裂、产品缺陷等问题。
三、冷却时间
在模具完成注射后,需要经过一定的冷却时间才能打开模具取出产品。
冷却时间的长短与模具材质、产品厚度等因素有关,应确保模具充分冷却,以避免因过快的冷却速度导致模具热应力增大、开裂等问题。
四、加热元件
加热元件是用于将模具加热至所需温度的重要部件。
加热元件的选型和布局应合理,以确保模具受热均匀,提高加热效率。
五、冷却水路
冷却水路是用于将模具冷却至所需温度的重要系统。
冷却水路的布局和设计应合理,以确保模具得到充分的冷却,避免因冷却不均而导致的产品缺陷和模具损坏。
六、温度传感器
温度传感器是用于监测模具温度的重要部件。
温度传感器的安装位置和数量应合理,以确保准确监测模具温度,为控制模具温度提供可靠依据。
七、热膨胀
压铸过程中,模具材料会因受热而膨胀。
因此,在设计和制造模具时需要考虑材料的热膨胀系数,以确保模具在使用过程中尺寸稳定,避免因热膨胀导致的产品缺陷和模具损坏。
八、温度曲线
温度曲线是描述模具温度随时间变化的曲线。
通过对温度曲线的监测和分析,可以了解模具的加热和冷却过程是否正常,及时发现并解决存在的问题,提高产品质量和生产效率。
模具的温度控制
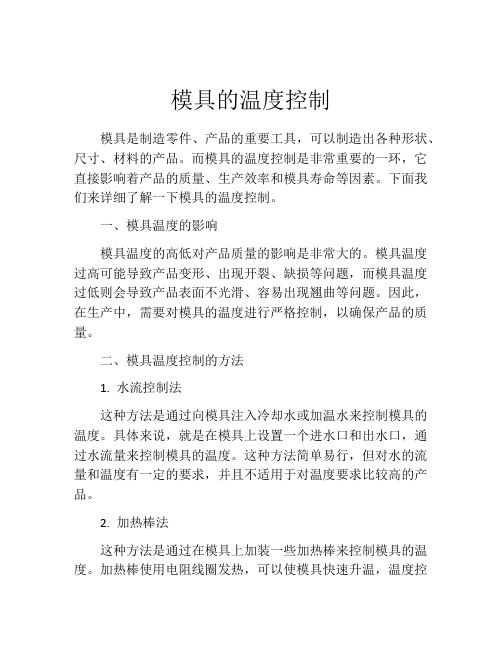
模具的温度控制模具是制造零件、产品的重要工具,可以制造出各种形状、尺寸、材料的产品。
而模具的温度控制是非常重要的一环,它直接影响着产品的质量、生产效率和模具寿命等因素。
下面我们来详细了解一下模具的温度控制。
一、模具温度的影响模具温度的高低对产品质量的影响是非常大的。
模具温度过高可能导致产品变形、出现开裂、缺损等问题,而模具温度过低则会导致产品表面不光滑、容易出现翘曲等问题。
因此,在生产中,需要对模具的温度进行严格控制,以确保产品的质量。
二、模具温度控制的方法1. 水流控制法这种方法是通过向模具注入冷却水或加温水来控制模具的温度。
具体来说,就是在模具上设置一个进水口和出水口,通过水流量来控制模具的温度。
这种方法简单易行,但对水的流量和温度有一定的要求,并且不适用于对温度要求比较高的产品。
2. 加热棒法这种方法是通过在模具上加装一些加热棒来控制模具的温度。
加热棒使用电阻线圈发热,可以使模具快速升温,温度控制准确性较高。
但加热棒的使用寿命有限,并且需要定期更换。
3. 空气加热法这种方法是通过空气加热来控制模具的温度。
具体来说,就是将空气加热后通过送风管送到模具内部进行加热。
这种方法可控性强,在保证模具温度均匀的情况下,还可以将时间和成本的额外消耗降至最低限度。
三、模具温度控制的注意事项1. 选择合适的控制方法在操作时,需要根据实际情况选取合适的温度控制方法。
例如,对于表面要求高、对温度要求严格的产品,应该采用空气加热法等高精度的控制方法。
而对于对温度要求不严格的产品,可以采用水流控制法等更为便捷的方法。
2. 均匀升温在升温过程中,需要确保模具温度升幅均匀。
如果模具温度不均匀,将会导致产品变形、表面不平整等问题。
3. 加强维护保养在使用过程中,需要定期对模具进行清洁、维护和保养。
特别是在使用水流控制法时,需要做好水质监测以防止水碱度过高导致模具腐蚀。
综上所述,模具的温度控制是非常重要的一环。
选取合适的控制方法、均匀升温和加强维护保养都是必不可少的。
控制模具温度的三种方法【技巧】
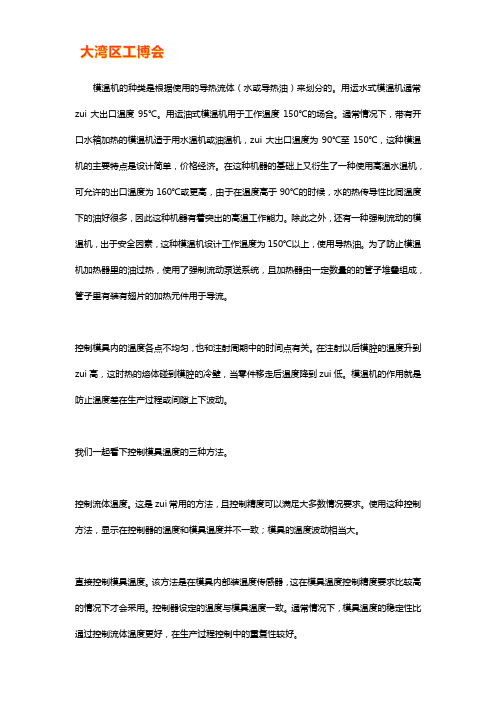
模温机的种类是根据使用的导热流体(水或导热油)来划分的。
用运水式模温机通常zui大出口温度95℃。
用运油式模温机用于工作温度150℃的场合。
通常情况下,带有开口水箱加热的模温机适于用水温机或油温机,zui大出口温度为90℃至150℃,这种模温机的主要特点是设计简单,价格经济。
在这种机器的基础上又衍生了一种使用高温水温机,可允许的出口温度为160℃或更高,由于在温度高于90℃的时候,水的热传导性比同温度下的油好很多,因此这种机器有着突出的高温工作能力。
除此之外,还有一种强制流动的模温机,出于安全因素,这种模温机设计工作温度为150℃以上,使用导热油。
为了防止模温机加热器里的油过热,使用了强制流动泵送系统,且加热器由一定数量的的管子堆叠组成,管子里有装有翅片的加热元件用于导流。
控制模具内的温度各点不均匀,也和注射周期中的时间点有关。
在注射以后模腔的温度升到zui高,这时热的熔体碰到模腔的冷壁,当零件移走后温度降到zui低。
模温机的作用就是防止温度差在生产过程或间隙上下波动。
我们一起看下控制模具温度的三种方法。
控制流体温度。
这是zui常用的方法,且控制精度可以满足大多数情况要求。
使用这种控制方法,显示在控制器的温度和模具温度并不一致;模具的温度波动相当大。
直接控制模具温度。
该方法是在模具内部装温度传感器,这在模具温度控制精度要求比较高的情况下才会采用。
控制器设定的温度与模具温度一致。
通常情况下,模具温度的稳定性比通过控制流体温度更好,在生产过程控制中的重复性较好。
联合控制。
联合控制是上述两种方法的综合,它能同时控制流体和模具的温度。
在联合控制中,温度传感器在模具中的位置极其重要,放置温度传感器时,必须考虑形状、结构及冷却通道的位置。
另外,温度传感器应被放置在对注塑件质量起决定性作用的地方。
模温机还可以自动控制。
pet塑料的注塑工艺参数

pet塑料的注塑工艺参数PET塑料是一种广泛应用于食品包装、饮料瓶等领域的塑料材料,其注塑工艺参数对产品的质量和性能具有重要影响。
合理选择和调整注塑工艺参数,可实现产品质量的稳定控制,提高生产效率和经济效益。
塑料材料特性PET塑料具有良好的透明性、耐腐蚀性、机械强度高等特点,是一种理想的包装材料。
其熔点较高,约250-260℃,熔体黏度较大,对塑料注塑工艺参数的控制要求较高。
模具温度模具温度是注塑过程中的关键参数之一,对产品的表面质量、收缩率等性能具有重要影响。
对于PET塑料的注塑,一般要求模具温度控制在90-110℃之间。
模具温度过低会导致产品表面不光滑,出现痕迹和熔体不充盈等问题;模具温度过高则易引起产品表面烧焦、退色等质量问题。
熔融温度PET塑料的熔融温度一般为250-270℃,在注射机的料筒中加热熔融后进行注射成型。
熔融温度过低会导致熔体流动性差,充盈不良,产品表面有瑕疵;熔融温度过高则易产生气泡、翘曲、烧焦等质量问题。
因此,要根据实际情况合理设置熔融温度,一般控制在250-270℃之间。
注射压力和注射速度注射压力和注射速度是控制PET塑料注塑过程中熔融物流和充盈的关键参数,对产品的密度、外观质量等性能有重要影响。
一般情况下,注射压力和注射速度设置较高,可提高产品的密度和光滑度,但要注意避免过高导致产品收缩不均匀、变形等问题。
根据具体情况可适当调整。
冷却时间和冷却水温度冷却时间和冷却水温度是控制PET塑料注塑产品固化和收缩的关键参数。
一般来说,冷却时间较短,可减少产品的收缩,但要根据产品的尺寸、厚度等情况进行合理调整。
冷却水温度一般控制在10-20℃,过高的水温会导致产品收缩不均匀、变形等问题。
射嘴温度射嘴温度对PET塑料注塑过程中的熔融和充盈有重要影响,一般要求控制在230-250℃之间。
射嘴温度过低会导致熔体流动性差,充盈不良;射嘴温度过高则易引起熔体漏出、烧焦等问题。
注塑工艺参数的选择和调整是保证PET塑料注塑产品质量的重要因素,需要在实际生产中不断优化和改进。
模具温度到底该怎么控制?

模温控制型式1、冷冻机 8 OC-15 OC之间冷却,注意冒汗生锈之问题。
2、水温机 96 OC以内,直接补充水源。
3、油温机 150 OC以内,油温循环间接用水冷却。
4、电热片、棒 200 OC以内,小心漏电。
模具温度对注塑成型的影响:模具温度是注塑成型中最要的变量----无论注塑何种塑料,必须保证形成模具表面基本的湿润。
一个热的模具表面使塑料表面长时间保持液态,足以在型腔内形成压力。
如果型腔填满而且在冻结的表皮硬化之前,型腔压力可将柔软的塑料压在金属上,那么型腔表面的复制就高。
另一方面,如果在低压下进入型腔的塑料暂停了,不论时间多短,那么它与金属的轻微接触都会造成污点,有时被称为浇口污斑。
对于每一种塑料和塑胶件,存在一个模具表面温度的极限,超过这个极限就可能出现一种或更多不良影响(例如:组件可以溢出毛边)。
模具温度更高意味着流动阻力更小。
在许多注塑机上,这自然就意味着更快流过浇口和型腔,因为所用的注塑流动控制阀并不纠正这个改变,填充更快会在浇道和型腔内引起更高的有效压力。
可能造成溢料毛边。
由于更热的模型并不冻结那些在高压形成之前进入溢料边区域的塑料,熔料可在顶出杆周围溢料毛边并溢出到分割线间隙内。
这表明需要有良好的注射速率控制,而一些现代化的流动控制编程器也确实可以做到这点。
通常,模具温度的升高会减少塑料在型腔内有冷凝层,使熔融材料在型腔内更易于流动,从而获得更大的零件重量和更好的表面质量。
同时,模具温度的提高还会使零件张力强度增加。
模具的保温方法:许多模具,尤其是工程用的热塑性塑料,在相对较高的温度下运行,如80摄氏度或176华氏度。
如果模具没有保温,流失到空气和注塑机上的热量可以很容易地与射料缸流失的一样多。
所以要将模具一飞机骨架板隔热,如果可能,将模具的表面隔热热。
如果考虑用热流道模具,尝试减少热流道部分和冷却了的注塑件之间的热量交换。
这样的方法可以减少能量流失和预热时间。
极冷极热模具温度-概述说明以及解释

极冷极热模具温度-概述说明以及解释1.引言1.1 概述概述:极冷极热模具温度是在模具制造和使用过程中起关键作用的因素之一。
随着现代科技的不断进步,模具制造和应用领域也在不断发展。
极冷模具温度是指模具温度远低于常温的情况,而极热模具温度则是指模具温度远高于常温的情况。
这两种极端的模具温度对于模具的性能、加工质量以及产品的生产效率都有着重要的影响。
在本文中,我们将分别探讨极冷模具温度和极热模具温度的背景介绍、作用以及调控方法。
首先,我们将介绍极冷模具温度的背景和作用。
随后,我们将探讨极热模具温度的背景和作用。
最后,我们将总结极冷极热模具温度的重要性,并对其未来发展做出展望。
通过深入了解模具温度的调控方法和作用,我们可以更好地应对模具制造和使用过程中的各种挑战,并改进生产效率和产品质量。
极冷极热模具温度的研究和应用对于模具行业的发展具有重要意义。
希望本文能够为读者提供有益的信息和启示,促进模具温度领域的进一步研究和探索。
1.2文章结构文章结构部分的内容可以包括以下几个方面的内容:1.2 文章结构本文将按以下结构来展开对极冷极热模具温度的讨论:第二节将介绍极冷模具温度,包括其背景介绍、作用和调控方法。
背景介绍部分将对极冷模具温度的概念进行阐述,为读者建立基本的认知框架。
作用部分将展示极冷模具温度在模具制造中的重要性和应用范围。
调控方法部分将介绍不同的方法和技术用于调节极冷模具温度,以保证模具制造的高质量和高效率。
第三节将介绍极热模具温度,包括其背景介绍、作用和调控方法。
背景介绍部分将对极热模具温度的概念进行阐述,为读者建立基本的认知框架。
作用部分将展示极热模具温度在模具制造中的重要性和应用范围。
调控方法部分将介绍不同的方法和技术用于调节极热模具温度,以保证模具制造的高质量和高效率。
最后一节将对极冷极热模具温度的重要性进行总结,强调其在模具制造中的不可替代性和未来的发展前景。
同时,还会提出对未来极冷极热模具温度研究的展望,包括技术创新和应用拓展等方面的建议。
压铸模具温度场设计与控制

压铸模具温度场设计与控制
1. 材料选择,首先需要选择合适的模具材料,以满足高温高压下的使用要求。
常见的模具材料包括工具钢、热作工具钢和耐热合金等,这些材料具有良好的耐热性和热传导性能。
2. 冷却系统设计,模具的冷却系统设计对温度场的控制至关重要。
合理设计的冷却系统可以帮助均匀地分布温度,防止热应力和变形,同时加快铸件凝固速度。
冷却系统通常采用水或油作为冷却介质,通过通道和喷嘴将冷却介质引入模具内部。
3. 温度传感器的应用,在模具中设置温度传感器可以实时监测温度场的变化,帮助调整冷却系统的工作状态,以实现温度场的精确控制。
常用的温度传感器包括热电偶和红外线测温仪等。
4. 控制系统,现代压铸设备通常配备了先进的模具温度场控制系统,可以实现对温度场的精确控制和调节。
通过监测温度传感器的反馈信号,控制系统可以自动调整冷却系统的工作状态,以维持稳定的温度场。
5. 模具结构设计,模具的结构设计也会影响温度场的分布。
合
理的结构设计可以帮助均匀地传导和分布热量,从而实现更稳定的
温度场。
总的来说,压铸模具温度场设计与控制需要综合考虑材料选择、冷却系统设计、温度传感器的应用、控制系统和模具结构设计等多
个方面,以实现对温度场的精确控制,确保铸件的质量和生产效率。
注塑成型模具的温度控制
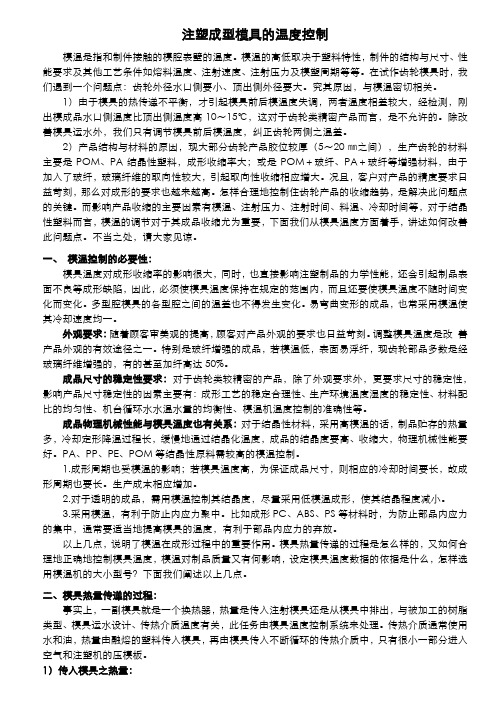
注塑成型模具的温度控制模温是指和制件接触的模腔表壁的温度。
模温的高低取决于塑料特性,制件的结构与尺寸、性能要求及其他工艺条件如熔料温度、注射速度、注射压力及模塑周期等等。
在试作齿轮模具时,我们遇到一个问题点:齿轮外径水口侧要小、顶出侧外径要大。
究其原因,与模温密切相关。
1)由于模具的热传递不平衡,才引起模具前后模温度失调,两者温度相差较大,经检测,刚出模成品水口侧温度比顶出侧温度高10~15℃,这对于齿轮类精密产品而言,是不允许的。
除改善模具运水外,我们只有调节模具前后模温度,纠正齿轮两侧之温差。
2)产品结构与材料的原因,现大部分齿轮产品胶位较厚(5~20㎜之间),生产齿轮的材料主要是POM、PA结晶性塑料,成形收缩率大;或是POM+玻纤、PA+玻纤等增强材料,由于加入了玻纤,玻璃纤维的取向性较大,引起取向性收缩相应增大。
况且,客户对产品的精度要求日益苛刻,那么对成形的要求也越来越高。
怎样合理地控制住齿轮产品的收缩趋势,是解决此问题点的关键。
而影响产品收缩的主要因素有模温、注射压力、注射时间、料温、冷却时间等,对于结晶性塑料而言,模温的调节对于其成品收缩尤为重要,下面我们从模具温度方面着手,讲述如何改善此问题点。
不当之处,请大家见谅。
一、模温控制的必要性:模具温度对成形收缩率的影响很大,同时,也直接影响注塑制品的力学性能,还会引起制品表面不良等成形缺陷,因此,必须使模具温度保持在规定的范围内,而且还要使模具温度不随时间变化而变化。
多型腔模具的各型腔之间的温差也不得发生变化。
易弯曲变形的成品,也常采用模温使其冷却速度均一。
外观要求:随着顾客审美观的提高,顾客对产品外观的要求也日益苛刻。
调整模具温度是改善产品外观的有效途径之一。
特别是玻纤增强的成品,若模温低,表面易浮纤,现齿轮部品多数是经玻璃纤维增强的,有的甚至加纤高达50%。
成品尺寸的稳定性要求:对于齿轮类较精密的产品,除了外观要求外,更要求尺寸的稳定性,影响产品尺寸稳定性的因素主要有:成形工艺的稳定合理性、生产环境温度湿度的稳定性、材料配比的均匀性、机台循环水水温水量的均衡性、模温机温度控制的准确性等。
tpe注塑的成型条件

tpe注塑的成型条件TPE注塑的成型条件TPE(热塑性弹性体)注塑是一种常见的塑料加工方法,用于生产具有弹性和柔软性能的产品。
在进行TPE注塑成型时,需要控制一系列成型条件以确保产品质量和生产效率。
本文将详细介绍TPE注塑的成型条件。
一、温度控制在TPE注塑成型过程中,温度是一个关键因素。
首先,要控制注塑机的料筒温度,以保证TPE材料能够充分熔化,并保持在适宜的熔融状态。
同时,还需要控制模具的温度,以确保注塑成型的产品能够迅速冷却并固化。
通常情况下,TPE注塑的料筒温度应在160℃-200℃之间,模具温度应在40℃-60℃之间。
二、压力控制在TPE注塑成型过程中,压力也是一个重要的参数。
首先,要控制注塑机的注射压力,以确保TPE材料能够顺利地从料筒中注射到模具腔内。
其次,还需要控制保压压力,以确保TPE材料能够充分填充模具腔,避免产生空洞或缺陷。
通常情况下,TPE注塑的注射压力应在5MPa-15MPa之间,保压压力应在2MPa-8MPa之间。
三、注射速度控制在TPE注塑成型过程中,注射速度也是一个关键参数。
过快的注射速度会导致TPE材料在进入模具腔内时产生剪切破坏,从而降低产品的物理性能。
相反,过慢的注射速度会导致TPE材料无法充分填充模具腔,从而产生缺陷。
因此,要根据具体产品的形状和要求,合理控制注射速度,以确保产品质量。
四、冷却时间控制在TPE注塑成型过程中,冷却时间也是一个重要参数。
合理的冷却时间能够确保TPE材料能够迅速冷却并固化,从而保证产品的尺寸稳定性和外观质量。
通常情况下,TPE注塑的冷却时间应根据具体产品的厚度和尺寸来确定,一般在10秒-60秒之间。
五、干燥处理TPE材料对潮湿环境非常敏感,容易吸湿而导致成型品出现气泡、缺陷等问题。
因此,在TPE注塑成型前,需要对TPE材料进行干燥处理,以降低材料的水分含量。
通常情况下,TPE材料的干燥温度应在70℃-80℃之间,干燥时间应根据具体材料来确定。
压铸温度

压铸温度、时间的分析与设定发布日期:[09-09-12 06:08:24] 浏览人次:[57 ]一、温度:1、浇注温度:指压室友进入型腔温度,以炉温为准;浇注温度的作用与影响:机械性能和质量,锌合金温度一般选择410-450度,铝合金一般选择610-700度,镁合金一般选择640-700度,铜合金一般选择900-980度。
2、模具温度:在压铸过程中模具需要的温度;模具温度的作用与影响:对金属液温度,粘度,流动性,填充时间,填充流态有影响,合金浇温度与量,对模具的寿命,对铸件的尺寸公差有影响,随模具温度的高低,铸件尺寸的收缩率也相应变化。
影响模具的主要因素:浇注温度量,浇注系统与溢流槽设计,压铸比压和压射速度;模具的体积大小,材料导热性,冷却调节器热分布平衡。
模具温度对机械性能影碟机响:模具温度度,充填条件好,但冷却速度降低,细晶层厚减薄,晶体较粗大,故强度下降,必须控制好模温,将模具进行冷却,加热装置,保持模具温度恒温。
模具温度的选择与控制:铅合金、锡合金60-120度,锌合金160-200度,镁合金200-250度,铝合金戈铁马220-280 ,铜合金300-350度。
控制:加热装置发热管,冷却水系统,可采用栽热油伸展质,电子温度计控制稳定,3、模具的热平衡(合金凝因热时P值)P值:锌合金42千卡,铝硅系212先千卡,铝镁合系190千卡,镁合金170千卡,合金对模具自然传热的流密度:锌合金模温100度时,1000千卡/小时.平方厘米;铝镁合金模具温度125度时,1500千卡/小时.平方厘米特定部位热传流密度值:分流锥60千卡/小时.平方厘米,浇口套、喷咀、压室50千卡/小时.平方厘米二、时间:是指填充时间,增压建压时间,持压时间,留模时间;压力、速度、温度三大要素。
1,填充时间:熔融金属在压力不始入型腔直到充满过程所需时间,称填充时间。
填充时间的选项择:1-2毫米的壁厚0.01-0.026秒, 2.5-3.5毫米壁厚0.22-0.05秒,4-6毫米壁厚0.04-0.08秒, 7-8毫米壁厚0.066-0.16秒,合金浇注温度高时,模具温高时,铸件壁厚部分离内浇口远时,熔化潜热和比热高的合金,填充时间可选择长一些。
模具温度控制器施工方案

模具温度控制器施工方案1. 背景介绍温度控制对于模具制造过程中非常重要。
在模具注塑过程中,模具的温度控制直接影响产品的质量和生产效率。
为了确保模具温度在一定范围内稳定控制,提高产品质量和生产效率,需要使用模具温度控制器。
2. 模具温度控制器的作用模具温度控制器是一种用于控制模具加热或冷却的设备,通过控制模具的温度,可以提高产品的成型质量和生产效率。
模具温度控制器可以根据不同的模具材料和生产工艺要求,精确地控制模具的温度,并实时监测温度变化,及时调整控制参数。
3. 模具温度控制器施工方案模具温度控制器的施工方案需要考虑到以下几个方面:3.1 模具温度控制器的选型在选择模具温度控制器时,需要考虑以下几个因素:•温度范围:根据模具材料和生产工艺的要求,选择合适的温度范围。
•控制精度:为了确保模具温度的稳定控制,需要选择控制精度高的温度控制器。
•界面操作:选择具有简单易用的界面操作的温度控制器,方便操作和调整控制参数。
3.2 安装位置的选择模具温度控制器通常安装在模具附近的控制柜中,位置选择应考虑以下几个因素:•远离高温源:避免温度控制器过热,影响其正常工作。
•方便维修:选择离操作人员较近的位置,方便日常维护和保养。
3.3 温度传感器的安装温度传感器是模具温度控制器的重要组成部分,用于实时监测模具的温度。
在安装温度传感器时,需要考虑以下几个因素:•安装位置:温度传感器应安装在模具的关键位置,以保证温度的准确监测。
•精度要求:选择精度高的温度传感器,确保温度测量的准确性。
•防护措施:在温度传感器周围设置防护装置,防止温度传感器受到损坏或污染。
3.4 控制回路的设计控制回路是模具温度控制器的核心部分,用于控制模具的加热或冷却。
在设计控制回路时,需要考虑以下几个因素:•控制方式:根据模具的特点和生产要求,选择合适的控制方式,如开关控制、PID控制等。
•控制参数:根据模具材料和生产工艺的要求,设置合适的控制参数,确保模具温度的稳定控制。
模具温度控制系统设计资料

模具温度控制系统设计资料1. 简介模具温度控制系统是用于模具加工过程中对模具温度进行精确控制的系统。
它可以确保模具在加工过程中保持恒定的温度,从而提高加工精度和产品质量。
本文将详细介绍模具温度控制系统的设计原理、组成结构以及工作原理。
2. 设计原理模具温度控制系统的设计原理主要基于模具加工过程中的热传导原理。
通过控制模具表面的温度,可以控制模具内部的温度分布,从而实现模具加工过程中的温度控制。
设计原理的主要步骤如下: 1. 在模具表面安装温度传感器,用于实时监测模具表面的温度。
2. 通过传感器将温度信号传输给控制器。
3. 控制器根据设定的温度值和实时温度值进行比较,计算需要施加的热量。
4. 通过控制系统控制加热或冷却设备,实现模具温度的精确控制。
5. 控制器不断监测温度信号,根据实时温度值调整加热或冷却设备的工作状态,保持模具温度的稳定。
3. 组成结构模具温度控制系统的主要组成结构包括温度传感器、控制器、加热或冷却设备以及控制系统。
3.1 温度传感器温度传感器用于实时监测模具表面的温度,并将温度信号传输给控制器。
常用的温度传感器有热电偶、热敏电阻和红外线传感器等。
温度传感器需要具有高精度、快速响应和耐高温等特点,以确保模具温度的准确控制。
控制器是模具温度控制系统的核心部件,负责接收温度信号、计算热量需求并控制加热或冷却设备。
控制器根据设定的温度值和实时温度值进行比较,通过控制系统控制加热或冷却设备的工作状态,从而实现模具温度的精确控制。
控制器通常采用微处理器或PLC等控制芯片,具有高精度、可靠性和稳定性。
3.3 加热或冷却设备加热或冷却设备用于向模具施加热量或冷却量,以实现模具温度的控制。
常用的加热设备有电热管、加热棒和电热板等,常用的冷却设备有冷却水系统和风扇散热系统等。
根据模具的具体需求,可以选择合适的加热或冷却设备。
控制系统是模具温度控制系统的核心部分,包括传感器、控制器和加热或冷却设备之间的数据传输、协调和控制。
热压机模具温度优化设计

热压机模具温度优化设计热压机是一种常用的加工设备,广泛应用于塑料、橡胶、陶瓷等行业。
在热压机的加工过程中,模具温度的控制对产品质量和生产效率起着重要作用。
本文将探讨热压机模具温度的优化设计方法,以提高产品质量和生产效率。
首先,模具温度的优化设计需要考虑材料的熔融温度和热传导性能。
不同材料的熔融温度不同,因此在模具温度设计时需要根据具体材料的特性进行调整。
同时,模具材料的热传导性能也会影响温度的分布和传递速度。
通过选择合适的模具材料和优化结构设计,可以提高热传导效率,从而实现更好的温度控制。
其次,模具温度的优化设计还需要考虑产品的形状和尺寸。
不同形状和尺寸的产品对模具温度的要求也不同。
例如,对于薄壁产品,需要提高模具温度以加快熔融速度和均匀度,从而避免产品变形和缺陷的产生。
而对于厚壁产品,则需要降低模具温度以控制熔融速度,避免产品内部的气泡和缺陷。
此外,模具温度的优化设计还需要考虑生产效率和能耗的平衡。
过高的模具温度会增加能耗,而过低的模具温度会降低生产效率。
因此,在优化设计时需要综合考虑这两个因素。
一种常用的方法是通过模拟和实验研究,找到最佳的温度范围,以实现最佳的生产效率和能耗平衡。
最后,模具温度的优化设计还需要考虑温度控制系统的性能和稳定性。
温度控制系统的精度和响应速度对模具温度的控制效果起着重要作用。
因此,在设计温度控制系统时,需要选择合适的传感器和控制器,并进行合理的调试和校准,以确保温度的稳定性和精度。
综上所述,热压机模具温度的优化设计是提高产品质量和生产效率的关键因素之一。
通过考虑材料特性、产品形状和尺寸、生产效率和能耗平衡以及温度控制系统的性能和稳定性,可以实现模具温度的最佳设计。
这将为热压机加工提供更高的效率和更好的产品质量,推动相关行业的发展。
模压成型温度设定原则

模压成型温度设定原则在进行模压成型过程中,温度的设置是至关重要的步骤之一。
正确的温度设定能够确保产品质量,提高生产效率,降低成本。
本文将介绍模压成型温度设定原则,帮助您更好地掌握这一关键技术。
首先,在进行模压成型之前,需要对原料进行熔融预热。
通常情况下,较高的熔融温度能够使原料更容易流动,有利于填充模具中的所有细节。
但是需注意,过高的熔融温度可能会导致原料过度熔化,影响产品的表面质量。
因此,在设定熔融温度时,需要根据不同原料的特性和模具结构来进行合理的选择。
其次,在模压成型的过程中,需要同时考虑模具温度和冷却速率。
通常情况下,较高的模具温度能够加快成型速度,缩短生产周期。
但是,过高的模具温度可能会导致产品变形或翘曲,降低产品质量。
因此在设定模具温度时,需要综合考虑原料的性能、产品的结构和尺寸等因素,找到一个适宜的平衡点。
此外,冷却速率也是影响产品质量的重要因素之一。
合适的冷却速率能够确保产品充分固化,减少残余应力,提高产品的强度和硬度。
通常情况下,可以通过调节模具温度或改变冷却介质来控制冷却速率。
需要注意的是,过快或过慢的冷却速率都可能会导致产品质量下降,因此需要通过实验和经验找到一个最佳的冷却速率。
最后,在进行模压成型时,还需要考虑产品的后处理和成型周期。
一些特殊要求的产品可能需要进行后续的热处理或表面处理,因此在模压成型中的温度设定需要考虑到这些后续工艺的需求。
此外,还需要根据生产效率和产品质量需求来确定成型周期,避免因为过长的成型周期导致生产效率下降。
综上所述,模压成型温度的设定是一个综合考虑原料性能、模具结构、产品尺寸、冷却速率等多方面因素的过程。
合理的温度设定能够提高产品质量,降低生产成本,提高生产效率。
通过不断的实践和总结经验,可以逐步掌握模压成型温度设定的技术要点,实现生产的持续改进和优化。
1。
聚醚酰亚胺注塑成型条件
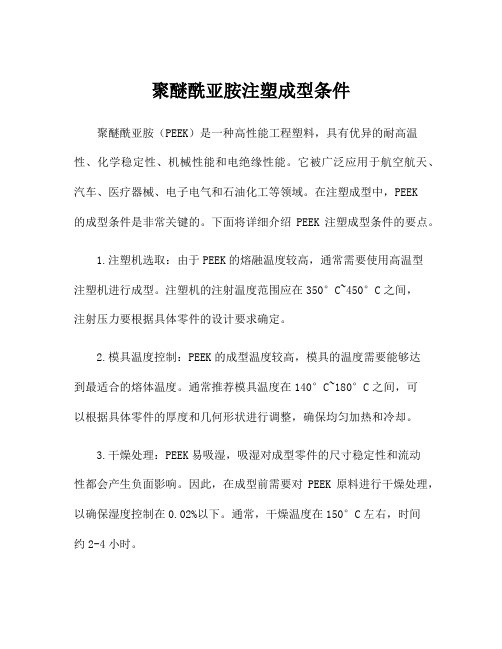
聚醚酰亚胺注塑成型条件聚醚酰亚胺(PEEK)是一种高性能工程塑料,具有优异的耐高温性、化学稳定性、机械性能和电绝缘性能。
它被广泛应用于航空航天、汽车、医疗器械、电子电气和石油化工等领域。
在注塑成型中,PEEK的成型条件是非常关键的。
下面将详细介绍PEEK注塑成型条件的要点。
1.注塑机选取:由于PEEK的熔融温度较高,通常需要使用高温型注塑机进行成型。
注塑机的注射温度范围应在350°C~450°C之间,注射压力要根据具体零件的设计要求确定。
2.模具温度控制:PEEK的成型温度较高,模具的温度需要能够达到最适合的熔体温度。
通常推荐模具温度在140°C~180°C之间,可以根据具体零件的厚度和几何形状进行调整,确保均匀加热和冷却。
3.干燥处理:PEEK易吸湿,吸湿对成型零件的尺寸稳定性和流动性都会产生负面影响。
因此,在成型前需要对PEEK原料进行干燥处理,以确保湿度控制在0.02%以下。
通常,干燥温度在150°C左右,时间约2-4小时。
4.预热料筒:在开始注塑成型之前,需要将注塑机的料筒进行预热,以提高PEEK的熔体温度和均匀性。
预热温度通常在380°C~400°C之间,预热时间约20~30分钟。
5.冷却时间和冷却系统:注塑成型后的冷却时间很重要,它可以影响成型零件的尺寸稳定性和性能。
冷却时间通常在30秒至2分钟之间,具体取决于注塑件的大小和形状。
另外,合适的冷却系统也是保证成型质量的关键,应确保冷却水的温度和流量适当。
6.注射速度和压力控制:注塑成型中,控制注射速度和压力对于PEEK零件的质量和成型效果非常重要。
通常,较低的注射速度和较高的注射压力能够确保零件的完整充填和较少的气泡。
7.压力和保压时间:在注塑成型过程中,PEEK材料需要经过压力和保压两个阶段。
压力一般在100MPa~150MPa之间调节,保压时间约为60秒至120秒。
- 1、下载文档前请自行甄别文档内容的完整性,平台不提供额外的编辑、内容补充、找答案等附加服务。
- 2、"仅部分预览"的文档,不可在线预览部分如存在完整性等问题,可反馈申请退款(可完整预览的文档不适用该条件!)。
- 3、如文档侵犯您的权益,请联系客服反馈,我们会尽快为您处理(人工客服工作时间:9:00-18:30)。
模具的溫度控制溫度控制的必要性在射出成形中,射出於模具內之熔融材料溫度,一般在150~350℃之間,但由於模具之溫度一般在40~120℃之間,所以成形材料所帶來的熱量會逐漸使模具溫度升高。
另一方面,由於加熱缸之噴嘴與模具之注道襯套直接接觸,噴嘴處之溫度高於模具溫度,亦會使模具溫度上升。
假使不設法將多餘之熱量帶走,則模具溫度必然繼續上升,而影響成型品的冷卻固化。
相反地,若從模具中帶走太多的熱量,使模具溫度下降,亦會影響成型品的品質。
故不管在生產性或成型品的品質上,模具的溫度控制是有其必要性的。
茲分述如下:1.就成形性及成形效率而言模具溫度高時,成形空間內熔融材料的流動性改善,可促進充填。
但就成形效率(成形週期)而言,模具溫度宜適度減低,如此,可縮短材料冷卻固化的時間,提高成形效率。
2.就成型品的物性而言通常熔融材料充填成形空間時,模具溫度低的話,材料會迅速固化,此時為了充填,需要很大的成形壓力,因此,固化之際,施加於成型品的一部份壓力殘留於內部,成為所謂的殘留應力。
對於PC或變性PPO之類硬質材料,此殘留應力大到某種程度以上時,會發生應力龜裂現象或造成成型品變形。
PA或POM等結晶性塑膠之結晶化度及結晶化狀態顯著取決於其冷卻速度,冷卻速度愈慢時,所得結果愈好。
由上可知,模具溫度高,雖不利於成形效率,但卻常有利於成型品的品質。
3.就防止成型品變形而言成型品肉厚大時,若冷卻不充分的話,則其表面發生收縮下陷,即使肉厚適當,若冷卻方法不良,成型品各部分的冷卻速度不同的話,則會因熱收縮而引起翹曲、扭曲等變形,因而需使模具各部分均勻冷卻。
溫度控制的理論要素模具的溫度調整,對成型品的品質、物性及成形效率大有影響,冷卻孔的大小與其分佈為重要的設計事項。
熱在空氣中,主要藉輻射和對流來傳播,在固體或液體中主要藉傳導來傳播。
固體的熱傳導也因物質的不同而有所差異,而且不同物質的交界處也有界膜傳熱係數。
在液體中,熱的傳導因傳熱管的大小、流速、密度、黏度等而異,熱計算公式很複雜,需要很多假定,不易求解。
但最近由於電腦的發展等已容易計算,可行理論解析。
1.模具溫度控制所需的傳熱面積熔融材料的熱量約5%,因輻射或對流而喪失於空氣中,95%傳導於模具。
假定材料帶入的熱量全部傳播到模具,其熱量為Q。
則Q = s ×g ×[ Cp ×( T1 - T2 ) + L ] (kCal/hr)s :每小時的射出數(次/hr)g:每次射出材料的重量(kg/次)Cp:材料的比熱(kCal/kg.℃)T1:材料的溫度(℃)T2:取出時的成型品溫度,及模具溫度(℃)L:熔解潛熱(kCal/kg)現設Cp ( T1-T2 ) + L = αs ×g = m則Q = m ×α(kCal/hr)m :每小時射出於模具的材料數量α:材料1kg的全熱量所謂熔解潛熱是材料的相變化產生的熱量,亦即材料從液體變成完全固體時,從材料放出的熱量。
以單位重量表示。
表1所示為各種材料在成形條件下,1kg材料的全熱量。
熱量Q從模具傳道冷媒,此時冷卻管的傳熱面積為A,則QA = (m2)h w ×ΔT表1 各種材料在成形溫度條件下的全熱量(單位:kcal/kg)h w:卻管的界膜傳熱係數(kCal/m2.hr.℃)ΔT :模具與冷媒的平均溫度差(℃)冷卻管的界膜傳熱係數h w在冷卻水流的場合為λ d v e Cp ×μ0.3h w = ( ) ( ) (kCal/m2.hr.℃)d μλλ:冷媒的熱傳導率(kcal/m.hr.℃)d :管徑(m)v :流速(m/hr)e :密度(kg/m3)μ:黏度(kg/m.hr)Cp :比熱(kcal/kg.℃)2.冷卻用水量在成形作業中為了控制模具溫度,經常在模具內設有冷卻水管,但其入水溫度與出水溫度及冷卻水量等必須詳加考慮,為了再利用或循環模具送出的溫水,須選定冷卻水溫度調整機或熱交換機降低入水溫度。
若入水溫度與出水溫度之差太大時,亦即冷卻水奪走模具中的熱量太多,則不利於模具的溫度分布,而影響成型品的品質,此時,宜增快流速或增高注入壓力,或增加流量。
表2(後面字看不清)表2 冷卻水的界限循環水一般帶入模具的熱量藉冷卻水帶出模具外的水量可計算如下:m αw =K ( T3 - T4 )w :每小時流出的冷卻水量(kg/hr)m:每小時射入於模具的材料重量(kg/hr)α:材料1kg的全熱量(表5. 5)K :水的熱傳導效率T3:出水溫度(℃)T4:入水溫度(℃)K值之決定:冷卻水管在型模板中或心型中時K=0.64冷卻水管在固定側固定板或承板中時K=0.50使用銅管之冷卻水管時K=0.103.模具加熱器能量加熱流道模具之加熱流道件通常使用插入式加熱器來控制其溫度。
非加熱流道模具在成形高融點材料或肉厚較厚、流動距離長、面積大之成型品時,經常需將模具加熱,此時亦可使用加熱器將模具加熱已利成形。
加熱器之能量可計算如下,現設加熱的材質為高碳剛,比熱0.115kCal/kg。
則TWP =860 nP:每小時所需電力(KW/hr.)T:模具溫度或加熱流道件溫度(℃)W:模具重量或加熱流道件重量(kg)n :效率(%)此式所需溫度上升起點以0℃作基準,而且加熱器之密接度,絕熱材之絕熱效果依情狀而異,n值以50%計。
模具的冷卻和加熱一般模具,通常以常溫的水來冷卻,其溫度控制藉水的流量調節,流動性好的低融點材料大都以此方法成形。
但有時為了縮短成形週期,須將水再加以冷卻。
小型成型品的射出時間,保壓時間都短,成形週期取決於冷卻時間,此種成行為了提高效率,經常也以冷水冷卻,但用冷水冷卻時,大氣中的水分會凝聚於成形空間表面,造成成型品缺陷,須加以注意。
成形高融點材料或肉厚較厚,流動距離長的成型品,為了防止充填不足或應變的發生,有時對水管通溫水。
成形低融點成形材料時,成形面積大或大型成型品時,也會將模具加熱,此時用熱水或熱油,或用加熱器來控制模具溫度。
模具溫度較高時,需考慮模具滑動部位的間隙,避免模具因熱膨脹而作動不良。
一般中融點成形材料,有時因成型品的品質或流動性而使用加熱方式來控制模具溫度,為了使材料固化為最終溫度均勻化,使用部分加熱方式,防止殘留應變。
以上所述,模具的溫度控制是利用冷卻或加熱的方式來調整的。
冷卻管路的分佈欲提高成形效率,獲得應變少的成型品時,模具構造須能對應於成形空間的形狀或肉厚,進行均勻的高效率冷卻。
在模具加工冷卻管路時,管路的數目、大小及配置極其重要。
如圖1(a)(b)所示,相同的成形空間,加工相近的大冷卻管路或加工遠離的小冷卻管路,探討熱的傳導路徑。
現在大管路通入59.83℃的水,小管路通入45℃的水,求溫度斜度,連結等溫曲線,即得圖1(c)(d),可見模具成形空間表面的溫度分佈,大管路是每週期有60~60.05℃的溫度變化,而小管路,則有53.33~60℃的溫度變化。
(a) (c)(b) (d)圖1 熱傳路徑與溫度變化曲線模具成形空間表面的溫度分佈,因水管的大小、配置、水溫而異,上示圖(d)之6.67℃(60~53.33)溫度差在某一成形條件上也許充分,但殘留之內部應力,對尺寸精度高的成型品,可能造成成形應變或經時變化。
熱傳導率愈高時,傳導效率愈好,容易控制及排除熱量。
亦即熱傳導率愈高時,模具成形空間的表面溫度變動少,傳導率低時,表面溫度變化大。
通常熔融材料充填成形空間時,澆口附近溫度高,離澆口愈遠處的溫度愈低。
若將成型品分割成若干部份,則該部份的熱量正比於體積。
一般對冷卻系統的設置需考慮下列原則:(1)冷卻管的口徑、間隔以及至成形空間表面的距離,對模具溫度的控制有重大影響,這些關係比的最大值如下,如冷卻管口徑為1時,管與管的間隔最大值為5,管與成形空間表面的最大距離為3。
再者,成型品肉厚較厚處比肉厚較薄處,冷卻管必須縮小間隔並且較接近成形空間表面。
(2)為保持模具溫度分佈均勻,冷卻水應先從模具溫度較高處進入,然後循環至溫度較低處再出口。
通常注道、澆口附近的成形材料溫度高,所以通冷水,溫度低的外側部份,則循環熱交換的溫水,此循環系統的管路連接,是在模具內加工貫穿孔,在模具外連接孔與孔。
(3)成形PE等收縮大的材料時,因其成形收縮大,冷卻管路不宜沿收縮方向(看不清楚請改)(4)冷卻管應盡量沿成形空間的輪廓來設置,以保持模具溫度分佈均勻。
(5)直徑細長的心型或心型銷,可在其中心鑽盲孔,再裝入套筒或隔板進行冷卻,若無法裝入套筒及隔板時,以熱傳率良好的鈹銅合金作心型及心型銷材料,或以導熱管(hear pipe)直接裝入盲孔中,再以冷卻水作間接之冷卻,效果尤佳。
(6)冷卻水流動過程中不得有短捷或停滯現象而影響冷卻效果,而且冷卻管路盡可能使用貫穿孔方式,以便日後方便清理。
冷卻回路實例冷卻回路的配置,取決於成型品之形狀、成形空間內的溫度分佈及澆口位置等。
常用的方法有鑽孔法、溝槽法、隔板法、套管法、間接法等。
如圖2所示。
圖2圖2(續)圖2(續)。