工程部8D报告
8D报告的内容及使用说明
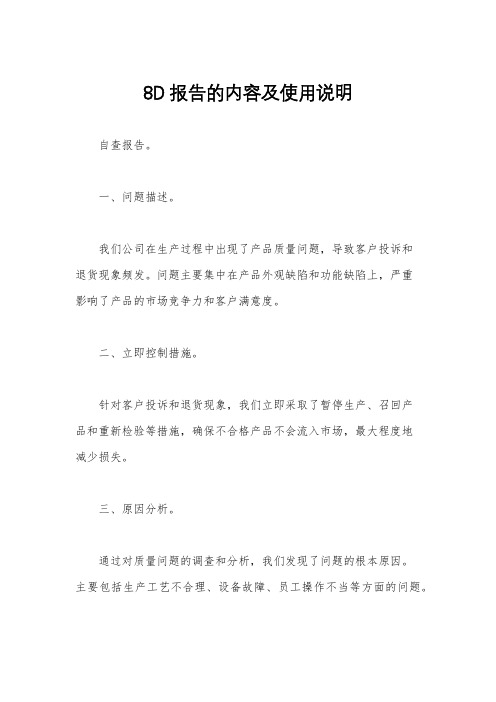
8D报告的内容及使用说明自查报告。
一、问题描述。
我们公司在生产过程中出现了产品质量问题,导致客户投诉和退货现象频发。
问题主要集中在产品外观缺陷和功能缺陷上,严重影响了产品的市场竞争力和客户满意度。
二、立即控制措施。
针对客户投诉和退货现象,我们立即采取了暂停生产、召回产品和重新检验等措施,确保不合格产品不会流入市场,最大程度地减少损失。
三、原因分析。
通过对质量问题的调查和分析,我们发现了问题的根本原因。
主要包括生产工艺不合理、设备故障、员工操作不当等方面的问题。
四、纠正措施。
针对问题的原因,我们制定了一系列的纠正措施。
包括对生产工艺进行优化、设备进行维护和改进、员工进行培训等方面的措施,以确保问题不再发生。
五、预防措施。
为了避免类似问题再次发生,我们还制定了一系列的预防措施。
主要包括建立质量管理体系、加强对生产过程的监控和检验、加强员工培训等方面的措施。
六、效果验证。
我们对纠正措施和预防措施进行了跟踪和验证,确保其有效性。
通过一段时间的观察和测试,问题得到了有效的解决,产品质量得到了明显的提升。
七、持续改进。
我们意识到质量管理是一个持续改进的过程,我们将继续加强对产品质量的管理和监控,不断改进生产工艺和技术,以确保产品质量的稳定和持续提升。
八、总结。
通过8D报告的内容及使用说明,我们有效地解决了产品质量问题,提升了客户满意度和市场竞争力。
我们将继续遵循8D报告的原则,不断改进和提升产品质量,为客户提供更优质的产品和服务。
以上为自查报告内容,希望能够得到领导的认可和支持,也欢迎各位对报告内容进行指导和建议。
8D报告步骤通俗完整讲解(附标准范本)

8D报告通俗讲解(附标准范本)8D 报告精品培训完整的8D报告标准范本.xlsx ——附件Excel 可直接打开保存 Issue#问题编号:8D-20180801QCustomer 客户:MD生活电器Date Issue Occurred 问题发生日期:2018.08.03Product 产品:FS4034上盖Date Issue Closed 问题关闭日期:2018.08.10Champion Name 负责人姓名Champion Title 负责人职位Champion Phone Number 负责人电话Champion E-mail Address 负责人电子邮件XXX副总经理XXXXXXXXXXX XXX Team Member Name(s)其他成员姓名Title(s)职位Phone Number(s)电话E-mail Address(es)电子邮件XXX品质部经理XXXXXXXXXXX XXX XXX生产部经理XXXXXXXXXXX XXX XXX质量工程师XXXXXXXXXXX XXX XXX 生产车间主管XXXXXXXXXXX XXXAffected Document 相关文件Owner for Update 责任人负责更新Date 日期FMEAXXX 2018.8.15BOM无/Control Plan 控制计划XXX 2018.8.15Drawing 图纸无/Design Standards 设计标准无/Congratulation 肯定团队Closure Statement 关闭声明Verification of Corrective Action: Has the issue been turned on and off? How? Verification through staticalevidence / hypothesis testing. Verification of corrective action for each why made and why shipped is required.纠正措施的确认:该问题处于开启状态还是关闭状态?怎样?通过证据确认/假设检验.针对每个产生的原因和被发运原因的纠正措施都要确认。
8D报告标准基准(八个步骤)

再发防止对策基准-8D1.0目的为明确产品质量改进的程序和内容,以提高产品质量改进的效率和效果,更好的满足顾客的要求,特制定本办法。
2.0适用范围本办法适用于公司质量改进。
3.0定义3.1现象:通过视觉/嗅觉/听觉/触觉等直觉方式,观察到的不良。
3.2问题:通过品质检查/试验等方法,反馈的与产品或过程基准的偏差。
3.3遏制措施:不良现象反馈的当时当地,采取的紧急措施,防止事态扩大化。
3.4临时措施:针对不良现象采取的措施,防止事态持续化,为永久措施争取时间。
3.5永久措施:针对不良原因采取的措施,预防问题再发生。
3.6体系原因:涉及DFMEA、P-FMEA、图纸、CP(控制计划)、WI(作业指导书)、MP(维护计划)等技术文件的失效/过期/缺失3.7物理原因:产品和产品实现过程所涉及实体的失效/过期/缺失等,包括产品、工装、设备等。
4.0 相关文件《不合格品控制程序》《进料检验控制程序》《信息沟通控制程序》5.0职责5.1品质部:品质工程师负责主导8D报告的填写6.0 作业程序6.1 品质工程师接到下述信息,在PDCA中登录,启动8D。
·客诉(0KM/售后)·1个月后1年内重复出现的过程问题。
6.2按8D的方法及步骤要求,实施行动,并填写对应8D项目,具体填写要求以及工具应用见《8D填写说明+支持资料》)。
6.3向客户提交报告前,必须提交品质部经理确认后提交。
6.4向客户提交报告。
6.5每月底,8D报告作为质量信息登记台帐的附件,提交资料员归档。
6.6 8D编码要求6.6.1规则为车型号+产品分类+年+月+日+流水号 例:R103HSJ201812501①车型号:直接借用客户车型②产品分类:后视镜:HSJ 拉手:LS 灯具:DJ 装饰件:ZSJ 其它:QT③年:4位数字,日历年④月:二位数字,日历月⑤日:二位数字,日历日6.6.28D编码由质量体系管理员统一编码,并登记于《信息跟踪管理台帐》(模版见《不合格品控制程序》附件),与质量信息一起按《信息沟通控制程序》要求传递到相应的品质工程师处,品质工程师在编制8D报告编码时,保持与质量信息登记台帐的8D编码保持一致。
8d报告一般谁做分析

8d报告一般谁做分析随着现代社会的发展,质量管理在企业中变得越来越重要。
而8D报告作为质量管理的一种工具,起到了重要的作用。
那么,8D报告的分析一般由谁来完成呢?首先,我们需要了解8D报告是什么。
8D报告是一种以问题为中心的解决方法,它包括了问题的描述、问题的原因分析和纠正措施等内容。
这个报告通常由一个团队来完成,而这个团队的成员一般包括以下几个角色:1. 问题所有者:问题所有者是发现和报告问题的人。
他们通常是从客户那里得到反馈或者在自己的工作中发现问题。
问题所有者应该能够准确地描述问题,并及时报告给团队。
2. 项目经理:项目经理是负责整个8D报告过程的人。
他们需要组织团队成员的工作和协调不同的活动。
项目经理还要确保8D报告的进展和结果的质量。
3. 问题解决者:问题解决者是负责分析和解决问题的人。
他们需要收集和分析与问题相关的数据,找出问题的根本原因,并提出解决方案。
问题解决者需要具备一定的技术和专业知识,以便能够有效地解决问题。
4. 质量工程师:质量工程师是提供技术支持和指导的人。
他们需要根据自身的专业知识,为问题解决者提供必要的技术支持,并帮助他们找到解决问题的方法。
5. 监督者:监督者是负责监督8D报告过程的人。
他们需要确保8D报告按照规定的流程和时间节点进行,并且达到预期的目标。
监督者还会对8D报告的进展进行评估和反馈,以保证报告的质量和有效性。
以上这些角色是8D报告分析过程中常见的角色,但并不是每个团队都会有这些角色。
在具体的情况下,团队的组成可能会有所变化。
比如,在小型企业或者个体工作中,一个人可能需要扮演多个角色。
总的来说,8D报告的分析是一个团队协作的过程,需要不同的角色相互配合,共同完成工作。
每个团队成员都有自己的职责和专长,他们通过合作共同解决问题,并最终完成8D报告的分析工作。
在实际的工作中,如果没有足够的团队成员或者某些角色的专业知识不足,可以考虑借助外部专家的帮助。
外部专家可以提供额外的专业知识和经验,帮助团队更好地分析和解决问题。
8d报告是什么

8d报告是什么8D报告是什么。
8D报告是一种质量管理工具,它是指8个步骤(D1-D8)的过程,用于解决产品或过程中出现的质量问题。
这种方法最初由美国汽车工程师协会(ASQC)提出,并被广泛应用于制造业和服务行业。
下面将详细介绍8D报告的内容和意义。
D1,确定团队。
在发现质量问题后,首先要组建一个团队来处理问题。
这个团队通常由跨部门的成员组成,包括质量工程师、生产人员、供应商和客户代表等。
确定团队的目的是确保问题得到全面的分析和解决。
D2,描述问题。
在这一步中,团队需要对问题进行详细描述,包括问题的性质、发生的时间、影响范围等。
这有助于团队全面了解问题的实质,为后续的解决方案提供基础。
D3,立即采取临时措施。
为了防止问题进一步扩大,团队需要立即采取临时措施来控制局面。
这些措施可能包括停止生产、更换零部件、调整工艺参数等。
D4,分析根本原因。
在这一步中,团队需要深入分析问题的根本原因。
通常采用的工具包括5W1H分析法、鱼骨图、因果分析等。
通过找到问题的根本原因,才能制定出更有效的解决方案。
D5,制定长期解决方案。
在确定了问题的根本原因后,团队需要制定长期的解决方案。
这可能包括改进工艺流程、修改设计、加强培训等。
这些解决方案需要经过充分的评估和验证,确保能够根本性地解决问题。
D6,实施长期解决方案。
一旦确定了长期解决方案,团队就需要开始实施这些方案。
这可能需要调整生产线、培训员工、与供应商合作等。
团队需要确保每一项解决方案都能够得到有效的实施。
D7,预防措施。
在解决了当前问题后,团队需要制定预防措施,以防止类似问题再次发生。
这可能包括建立更严格的质量控制流程、加强供应商管理、改进产品设计等。
D8,认可团队成果。
最后一步是对团队的成果进行认可。
这不仅是对团队成员的鼓励和肯定,也是对整个质量管理体系的肯定。
通过认可团队的成果,可以激励团队继续努力,提高质量管理水平。
总结。
通过8D报告的8个步骤,可以全面系统地解决产品或过程中出现的质量问题。
PQE培训教材-8D报告

PQE培训教材-8D报告1. 什么是8D报告8D报告是一种问题解决方法,它可以帮助团队追溯和解决问题的根本原因,并制定有效的纠正和预防措施。
它是以8个步骤命名的,每个步骤都有具体的任务和工具,以确保问题得到彻底解决。
以下是8D报告的八个步骤:1.D1:建立问题解决团队2.D2:描述问题3.D3:立即暂时解决问题4.D4:根本原因分析5.D5:制定纠正措施6.D6:实施纠正措施7.D7:验证纠正措施8.D8:预防措施跟踪2. D1:建立问题解决团队在D1阶段,我们需要确定一个问题解决团队,这个团队由不同领域和专业的人员组成,以确保问题得到全面的解决。
团队应包括以下成员:•项目经理:负责整个问题解决过程的组织和协调。
•质量工程师:负责分析和解决质量问题。
•制造工程师:负责分析和解决制造过程中的问题。
•供应链代表:负责协调和解决供应商相关的问题。
•设计工程师:负责分析和解决设计问题。
•生产经理:负责分析和解决生产过程中的问题。
•客户代表:负责与客户沟通并解决与客户相关的问题。
建立问题解决团队后,团队成员需要明确各自的角色和职责,并制定一个工作计划,以确保问题得到及时解决。
3. D2:描述问题在D2阶段,团队成员需要准确地描述问题,并确保问题被充分理解。
问题描述应包括以下内容:•问题发生的具体时间和地点。
•问题的具体表现或症状。
•问题影响的范围。
•对问题的初步评估以及可能的原因。
描述问题时,团队成员应尽量客观和详细,以确保问题不会被误解或忽视。
4. D3:立即暂时解决问题在D3阶段,团队成员需要立即采取措施解决问题的紧急影响。
这些措施是暂时的,旨在缓解问题的影响,但不一定解决问题的根本原因。
暂时解决问题的措施可能包括以下内容:•停机或减少生产。
•调整生产工艺。
•加强质量检查。
•与供应商联系并请求紧急支持。
在采取暂时解决措施后,团队应监控问题,并确保措施的有效性。
5. D4:根本原因分析在D4阶段,团队成员需要进行根本原因分析,以确定问题的根本原因。
8D报告过程以及8D是指的什么讲解
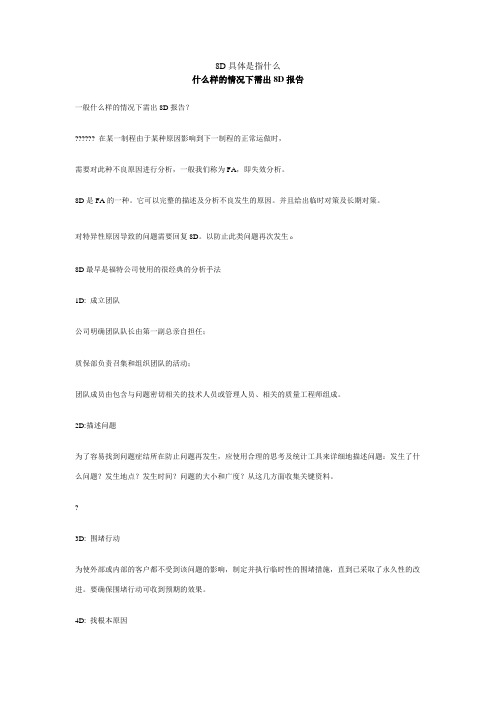
8D具体是指什么什么样的情况下需出8D报告一般什么样的情况下需出8D报告?在某一制程由于某种原因影响到下一制程的正常运做时,需要对此种不良原因进行分析,一般我们称为FA,即失效分析。
8D是FA的一种。
它可以完整的描述及分析不良发生的原因。
并且给出临时对策及长期对策。
对特异性原因导致的问题需要回复8D。
以防止此类问题再次发生。
8D最早是福特公司使用的很经典的分析手法1D: 成立团队公司明确团队队长由第一副总亲自担任;质保部负责召集和组织团队的活动;团队成员由包含与问题密切相关的技术人员或管理人员、相关的质量工程师组成。
2D:描述问题为了容易找到问题症结所在防止问题再发生,应使用合理的思考及统计工具来详细地描述问题:发生了什么问题?发生地点?发生时间?问题的大小和广度?从这几方面收集关键资料。
3D: 围堵行动为使外部或内部的客户都不受到该问题的影响,制定并执行临时性的围堵措施,直到已采取了永久性的改进。
要确保围堵行动可收到预期的效果。
4D: 找根本原因就问题的描述和收集到的资料进行比较分析,分析有何差异和改变,识别可能的原因,测验每一个原因,以找出最可能的原因,予以证实。
5D: 永久性纠正针对已确认的根本原因制订永久性的纠正措施,要确认该措施的执行不会造成其它任何不良影响。
6D: 验证措施执行永久性的纠正措施,并监视其长期效果7D:预防再发生修正必要的系统,包括方针、运作方式、程序,以避免此问题及类似问题的再次发生。
必要时,要提出针对体系本身改善的建议。
8D: 肯定贡献完成团队任务,衷心地肯定团队及个人的贡献,并加以祝贺。
由最高领导者签署8D的流程D1-第一步骤: 建立解决问题小组若问题无法独立解决,通知你认为有关的人员组成团队。
团队的成员必需有能力执行,例如调整机器或懂得改变制程条件,或能指挥作筛选等。
D2-第二步骤: 描述问题向团队说明何时、何地、发生了什么事、严重程度、目前状态、如何紧急处理、以及展示照片和收集到的证物。
8d报告是什么意思

8d报告是什么意思8D报告是一种短期产品质量问题解决方法。
它起源于美国汽车工业,后被广泛应用于全球制造业。
8D报告的目的是提供一个结构化的方法,帮助团队系统地识别、分析、跟踪和解决质量问题,以确保问题不再出现。
8D报告通常由质量工程师、产品工程师、制造工程师、供应商和客户代表组成的团队来编写。
8D报告是基于DMAIC(Define、Measure、Analyze、Improve、Control)方法论的一个衍生品。
DMAIC方法论是一个用于持续质量改进的结构化过程,也被广泛应用于全球质量管理领域。
DMAIC方法论主要包括五个阶段,分别为定义、测量、分析、改进和控制。
在8D报告中,这五个阶段被扩展为八个步骤,分别为:第一步:成立8D团队第二步:描述问题第三步:立即控制问题第四步:确定根本原因第五步:制定长期措施第六步:实现长期措施第七步:核实效果第八步:预防复发8D报告中,每个步骤都有明确的工作内容和标准,团队成员需要按照这些步骤开展工作,形成一个闭环的流程。
8D 报告需要被认真编写,包括问题描述、根本原因分析、解决方案、实施计划、效果验证等详细内容。
8D报告一般由8-10页左右,包括图表和文字描述。
对于企业来说,8D报告有以下几个重要的作用:第一,解决短期质量问题,降低不良率和拒绝率,提高产品质量。
第二,加强团队协作,促进部门间沟通和协调,提高整个企业的团队效能。
第三,提高生产效率,减少资源浪费,提高企业的经济效益。
总之,8D报告是一种重要的质量问题解决方法,它能够帮助企业解决短期内的质量问题,促进团队协作和效率提升,提高产品质量和企业经济效益。
8d报告的总结范本

8d报告的总结范本8D报告总结范本8D报告是企业为了系统解决问题,进行问题分析和改进措施制定的一种常用方法。
以下是一份8D报告的总结范本,供大家参考。
一、问题概述1.问题描述:简要描述问题现象,包括问题发生的时间、地点、涉及的产品或过程。
2.问题影响:阐述问题对产品质量、生产效率、成本、客户满意度等方面的影响。
3.问题紧急程度:根据问题的影响程度,判断问题的紧急程度。
二、问题分析1.原因分析:从人、机、料、法、环等方面分析问题产生的原因。
2.数据收集:收集与问题相关的数据,如生产数据、检验数据、客户反馈等。
3.原因验证:对分析出的原因进行验证,确认问题产生的主要原因。
三、改进措施1.短期措施:针对问题产生的主要原因,制定临时性措施,以减轻问题影响。
2.长期措施:从系统、流程、人员培训等方面,制定长期改进措施,防止问题再次发生。
3.改进措施实施:明确责任人和完成时间,确保改进措施得到有效实施。
四、改进效果评估1.效果跟踪:对改进措施实施后的效果进行跟踪,收集相关数据。
2.效果评估:对比改进前后的数据,评估改进措施的效果。
3.持续改进:根据效果评估结果,对改进措施进行优化,实现持续改进。
五、预防措施1.预防措施制定:针对问题产生的原因,制定预防措施,防止类似问题再次发生。
2.预防措施实施:明确预防措施的责任人和完成时间,确保预防措施得到有效实施。
3.预防效果评估:对预防措施实施后的效果进行评估,确保预防措施的有效性。
六、总结与反思1.问题解决过程总结:总结问题解决过程中的经验教训,为今后类似问题提供借鉴。
2.团队协作反思:反思团队在问题解决过程中的协作情况,提高团队协作能力。
3.改进措施优化:根据问题解决过程中的经验,不断优化改进措施,提升企业整体管理水平。
本8D报告总结范本旨在提供一种问题解决的方法和思路,实际应用时,需根据企业实际情况进行调整和优化。
8d报告是哪八个步

D1-第一步骤: 建立解决问题小组----由品质部召集相关人员若问题无法独立解决,通知你认为有关的人员组成团队。
团队的成员必需有能力执行,例如调整机器或懂得改变制程条件,或能指挥作筛选等。
备注:执行者不列入。
D2-第二步骤: 描述问题----由品质部收集,并向小组人员传达向团队说明何时、何地、发生了什么事、严重程度、目前状态、如何紧急处理、以及展示照片和收集到的证物。
想象你是FBI的办案人员,将证物、细节描述越清楚,团队解决问题将越快。
D3-第三步骤: 执行暂时对策---由小组人员负责执行若真正原因还未找到,暂时用什么方法可以最快地防止问题?如全检、筛选、将自动改为手动、库存清查等。
暂时对策决定后,即立刻交由团队成员带回执行。
备注:为了防止遗漏,纠正措施五要→客户仓库、在途、客户生产线、工厂生产线& 工厂仓库。
D4-第四步骤: 找出问题真正原因----由小组人员讨论后确定找问题真正原因时,最好不要盲目地动手改变目前的生产状态,先动动脑。
您第一件事是要先观察、分析、比较。
列出您所知道的所有生产条件(即鱼骨图),逐一观察,看看是否有些条件走样,还是最近有些什么异动?换了夹具吗?换了作业员?换了供应商?换了运输商?修过电源供应器?流程改过?或比较良品与不良品的检查结果,看看哪个数据有很大的差异?尺寸?重量?电压值?CPK?耐电压?等等不良的发生,总是有原因,资料分析常常可以看出蛛丝马迹。
这样的分析,可以帮助您缩小范围,越来越接近问题核心。
当分析完成,列出您认为最有可能的几项,再逐一动手作些调整改变,并且观察哪些改变可使品质回复正常及影响变异的程度,进而找到问题真正的原因。
这就是著名田口式方法最简单而实际的运用。
D5-第五步骤: 选择永久对策----由小组人员讨论后确定找到造成问题的主要原因后,即可开始拟出对策的方法。
对策的方法也许有好几种,例如修理或更新模具。
试试对可能的选择列出其优缺点,要花多少钱?多少人力?能持续多久? 再对可能的方法作一最佳的选择,并且确认这样的对策方法不会产生其它副作用。
8D报告品质范文

8D报告品质范文8D报告是一种质量管理工具,通常用于处理和解决产品或流程的质量问题。
下面是一个超过1200字的8D报告示例:问题描述:在本次报告中,我们将讨论由于制造过程中出现的质量问题而引起的客户投诉。
客户投诉主要集中在我们公司最新推出的产品型号X上。
问题主要表现为,在正常使用过程中,产品的功能受到限制,无法达到预期的性能。
此问题已经导致了销售额下降和公司声誉受损。
问题分析:通过对投诉的数据进行收集和分析,我们发现问题主要出现在产品的X模块。
根据故障的特性和模块的功能,我们初步判断故障可能出现在模块的电源供应部分。
8D报告过程:1.组建团队:我们组建了由质量部门和工程师等有关部门组成的团队,以便全面理解问题并找出解决方案。
2.准备问题描述:团队收集了相关数据并准备了详细的问题描述,包括故障的特点、客户的反馈和相关数量。
3.紧急控制措施:在确定问题范围后,我们立即采取了紧急控制措施,停止了产品X的生产,并将已生产的产品进行回收和退货处理,以减少进一步的质量问题。
4.确定根本原因:团队进行了各种实验和测试,对产品的X模块进行了详细的分析。
最后,我们发现电源供应部分的元件质量不稳定,导致电源输出不稳定。
5.提出纠正措施:针对根本原因,我们提出了一些纠正措施。
首先,我们将更换电源模块中存在问题的元件,并进行严格的质量控制。
其次,我们将优化制造过程,加强对电源模块的测试和验证。
6.实施纠正措施:我们立即开始实施纠正措施。
生产部门已经安排了更换元件的工作,并制定了严格的质量控制标准。
同时,质量部门将加强对制造过程的监督和管理,确保纠正措施的有效实施。
7.验证纠正措施:为了验证纠正措施的有效性,我们对新生产的产品进行了全面的测试和验证。
测试结果显示,通过纠正措施后,产品的功能和性能得到了明显的改善。
8.预防措施:为了避免类似问题的再次发生,我们提出了一些预防措施。
首先,我们将加强供应商的质量管理,并进行更严格的元件选购。
8D报告简介与解决方法
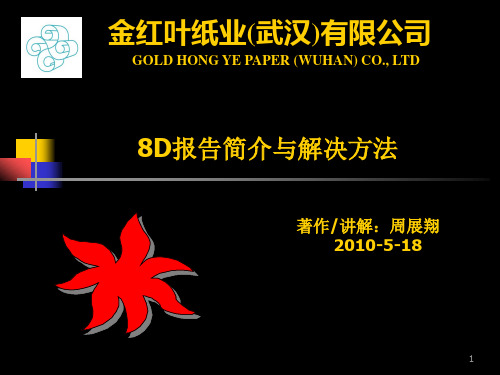
一、8D报告简介
4、顾客将通过确认8D报告来决定这些问题是否已经回答: 4.1、对配件的知识进行了充分论证。 4.2、完全确定了根本原因并聚焦于该原因。 4.3、遗漏点已经被识别。 4.4、确定与根本相匹配的纠正措施。 4.5、纠正措施计划的验证已经被确定。 4.6、包括了实施纠正措施的时间计划。 4.7、有证据显示供方将把纠正措施纳入整个系统。 8D的有效实施需仰赖其他质量工具
8D报告8大步骤
D0:为8D过程做准备 D1:成立小组 D2:问题的描述 D3:确定临时纠正措施(ICA)的开发 D4:确定和验证根本原因和遗漏点 D5:确定和验证针对根本原因和遗漏点的永久性纠正措施(PCA) D6:实施和确认PCA D7:防止再发生 D8:承认小组及个人的贡献
3
一、8D报告简介
问题:S公司应该如何反应?
12
三、8D报告详解
S公司组成了一个小组来解决问题 D1: 成立小组 成员名单如下: 战略性问题 黄晓岚---品保课主管(本次小组组长) 李俊明---电镀课主管 任命领导者了吗? 刘炎---设备课课长 焦明红--- SQE 课课长 小组中有分供方吗? 谢郑玲--- QA 课课长 俞建红--- RD主管 小组中有顾客吗? 卞正军---PM专员 小组中有其他相关人员吗? 小组头脑风暴活动有书面文件吗? 常见性错误 所选择的完成8D过程的小组成员没有技术知识 只有一两个人实施该过程。
注: 这些描述只代表理想的问题解决方式,实际上,真实情况并非和在此描述的一样,努力 获取供方和顾客之间的积极联系将有助于发生问题得到快速和容易的改进。
9
三、8D报告详解
4、完成8D过程
一般地,顾客会要求应在一定期限内完成8D过程。 例子:在福特,该期限是30天。对于某些问题,30天可能不够。当存在要求超过30天的状 况时,供方应向福特提供最新书面文件指出: 为什么根本原因没有被确定和验证? 供方将如何计划继续该过程? 供方打算完成该过程的时间框架?
8D报告简介与解决方法

16
三、8D报告详解
A 公司通过失效树(FTA)的方法验证根本原因
1、 验证根本原因
2、第一个根本原因是电线和电路接触器之间的连接点松动。 2.1、电镀的机制请见图-1 1) 喷银器和后板紧紧压住L/F 以使银能被镀在正确的位置。 2) 电路接触器被关闭,开始工作。 3) 银液被从银槽泵到喷银器。
2、验证问题的存在
2.1、一旦供方为问题负责,供方应该确认该问题确实是供方零件的问题。从D0
开始,评估8D过程的需要性。在工厂提出问题前,首先应该确定和验证问题,在
工厂的要求下,供方能帮助确认问题: 提供了不合格的零件。 提供不合格品可
能的分析,如尺寸结果。 将问题定量化,如XX检验XX不合格。
2.2、再次提出,当确认问题时,供方以一种积极的不相互责难的途径与顾客工
3、第二个根本原因是没有安装当缺陷发生时能 自动停止生产线的防错系统 4、第三个根本原因是S公司的检查系统需要改进。 晚班没有主管对质量问题负责。
4) 整流器打开,银镀到L/F 上。
2.2.由于电镀的电路因为连接点松动而断开,导致镀银没有实施。
2.3.镀银的整流器由电压控制,当电压低于规定参数时,生产线会自动停止,操作者检查了生产线但没有发现停止的原因,
一8d报告简介8d的有效实施需仰赖其他质量工具1可靠性2设计验证产品和过程确认3潜在失效模式及后果分析fmea4控制计划5生产件批准程序ppap节拍生产6统计过程控制spc7试验设计doe6一8d报告简介5实施8d的好处适当的完成8d过程除开能解决根本原因及纠正问题的好处外还包括
如何写8D报告

一、标准的8D报告格式
• 我公司目前采用的8D报告格式如附图 所示。目前仅有对外的8D报告提交时 用是很可惜的。希望技术类工程师都 能掌握这种分析思路。
•
Hale Waihona Puke (最新版)二、8D步骤即整改步骤
• • • • • • 1、问题简述 应遵循以下4个要求 1)标准 2)差异 3)时间段 4)数量
• 3、初步分析,进行具体责任分工 • 1)过程问题
• • • • • • a)先确认发生的问题,文件上是否已规定好? b)如文件已规定,再确认操作人员为何违规? c)是未进行培训?还是培训了故意违规? d)如是工艺策划责任,则分配到工艺室进行整改。 e)如是设计策划责任,则由产品工程师进行整改 f)如是检验策划责任,则由过程质量工程师进行 整改 • g)如是培训或故意违规问题,如是车间责任,由 车间进行整改,如是质量科责任,由质量科进行 整改。
• 8D报告-CN100散热器和电子扇总成水室与主片扣 合处漏水问题
• 8D报告--24532017暖风机总成风门轴脱落
• 8D报告-24518527散热管有针孔发生漏水
• 8d报告-CV6水箱漏水,密封圈偏离 • 8D报告--T11外三包水室与主片漏水问题
• 8D报告--1118ZB6、TU131ZE中冷器 焊缝漏气质量问题 • 8D报告--N300暖风机电机异响--叶轮 裂
• 6、如何写整改措施 • 1)对于一时不会做整改计划的同事, 采取的整改措施的思路,就是把《8D 报告 》的所有空格按要求确认是否需 要,并填写完成。 • 2)写完《8D报告 》后,再转换成部 门整改措施的格式。如附图所示。
• 7、涉及2个问题或2个问题 件的写法
• 1).问题一:样件1验证情况→样件2原因是……
8D报告(通用模板)

引言:8D报告是一种解决问题和改进过程的方法,它采用了多个步骤和工具来识别、分析和永久解决问题。
本文将介绍8D报告的通用模板中的第二部分,包括第三到第五个大点的详细阐述。
概述:在第二部分,我们将深入探讨8D报告的剩余步骤,包括确定短期、长期措施和效果确认。
每个大点将进一步细分为59个小点,以便更全面地介绍8D报告的实施细节。
正文:第三大点:确定短期的临时措施1.确定问题的严重性:在确定短期的临时措施之前,需要评估问题的严重性,以确定采取的措施是否十分迫切。
2.制定应急计划:根据问题的性质和紧急程度,制定临时措施的计划,以及纠正和预防措施的时间表.3.计划资源和人员:确定所需的资源和人员来执行临时措施,并明确各自的职责和任务,确保计划的顺利执行.4.实施和监控措施:根据制定的计划执行临时措施,有效监控措施的执行情况,并进行必要的调整和改进.5.记录和报告:记录临时措施的执行情况,包括措施的有效性和问题解决的进展,及时向相关方报告并汇总反馈意见。
第四大点:确定长期措施和预防措施1.分析根本原因:对问题进行深入的分析,找出问题的根本原因,以便制定长期的解决方案.2.制定长期措施:根据根本原因分析的结果,制定可持续性的长期措施,以确保问题不再重复出现.3.优先级和时间表:确定长期措施的优先级和时间表,以便有条不紊地推进实施.4.资源和预算:确定所需的资源和预算来支持长期措施的实施,并进行适当的调整和分配.5.审核和验证:对长期措施进行审核和验证,确保其有效性和可持续性,并进行必要的调整和改进.第五大点:效果确认和总结1.确认问题解决:对实施的长期措施进行效果确认,确保问题已经得到解决.2.总结分析经验:总结整个问题解决过程中的经验教训,包括问题的识别、解决方法的选择和执行过程中的反馈,以便提高团队的解决问题的能力.3.客户满意度评估:对客户进行满意度评估,以了解他们对问题解决过程和结果的评价.4.结果反馈:将问题解决的结果及相关信息反馈给团队成员、管理层和其他相关方,以促进知识共享和经验沉淀.5.关闭报告和跟踪:完成8D报告,关闭报告,并跟踪后续动作,以确保问题的持续解决和改进.总结:在第二部分,我们详细介绍了8D报告的剩余步骤,包括确定短期的临时措施、确定长期措施和预防措施,以及效果确认和总结。
8d报告范文
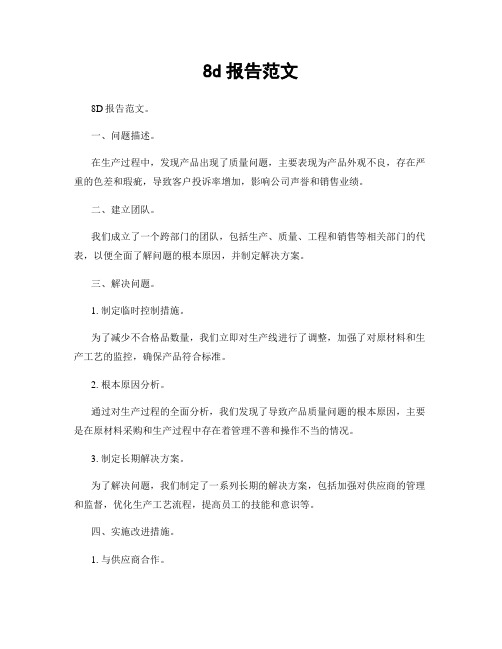
8d报告范文8D报告范文。
一、问题描述。
在生产过程中,发现产品出现了质量问题,主要表现为产品外观不良,存在严重的色差和瑕疵,导致客户投诉率增加,影响公司声誉和销售业绩。
二、建立团队。
我们成立了一个跨部门的团队,包括生产、质量、工程和销售等相关部门的代表,以便全面了解问题的根本原因,并制定解决方案。
三、解决问题。
1. 制定临时控制措施。
为了减少不合格品数量,我们立即对生产线进行了调整,加强了对原材料和生产工艺的监控,确保产品符合标准。
2. 根本原因分析。
通过对生产过程的全面分析,我们发现了导致产品质量问题的根本原因,主要是在原材料采购和生产过程中存在着管理不善和操作不当的情况。
3. 制定长期解决方案。
为了解决问题,我们制定了一系列长期的解决方案,包括加强对供应商的管理和监督,优化生产工艺流程,提高员工的技能和意识等。
四、实施改进措施。
1. 与供应商合作。
我们与主要原材料供应商进行了深入的沟通和合作,要求他们提供更加稳定和符合要求的原材料,并加强对其生产工艺的监督。
2. 优化生产工艺。
我们重新设计了生产工艺流程,加强了对关键工艺节点的控制,提高了生产效率和产品质量。
3. 培训员工。
我们加强了对生产员工的培训和教育,提高了他们的技能和质量意识,确保产品质量符合标准。
五、效果验证。
经过一段时间的改进和实施,我们对产品进行了全面的检测和验证,发现产品质量得到了显著的提高,客户投诉率明显下降,公司声誉和销售业绩得到了恢复和提升。
六、总结。
通过这次问题的解决,我们深刻认识到了质量管理的重要性,也意识到了团队合作的力量。
我们将继续加强对质量管理的重视,不断完善和改进我们的管理体系和工艺流程,确保产品质量始终稳定可靠。
七、展望。
我们将继续践行8D方法,不断改进和提高我们的质量管理水平,为客户提供更加优质的产品和服务,为公司的可持续发展做出更大的贡献。
十年质量工程师告诉你,如何写好8D报告(一)2024

十年质量工程师告诉你,如何写好8D报告(一)引言概述:8D报告是一种用于解决问题和改进质量的常用工具。
作为一名经验丰富的质量工程师,我将分享一些关于如何编写高质量的8D 报告的经验和技巧。
本文将分为5个大点详细阐述,每个大点包含5-9个小点。
正文内容:大点1:理解问题的本质1.1 确定问题的关键特征和根本原因1.2 收集问题现象的实际数据和证据1.3 确定问题对客户和业务的影响1.4 确立解决问题的目标和范围1.5 识别并描述问题的背景和历史大点2:制定解决方案2.1 运用适当的工具和方法,如鱼骨图、5W1H等2.2 确定可能的解决方案,并分析其可行性和效果2.3 选择最佳解决方案,考虑成本、时间和可行性等因素2.4 制定详细的行动计划,包括责任人和时间表2.5 确定并准备所需资源,包括人员、设备和资金等大点3:实施解决方案3.1 逐步实施行动计划,并跟踪进展情况3.2 分配任务和责任,确保团队成员的理解和配合3.3 监控解决方案的效果和改进情况3.4 及时调整和修正行动计划,以保持解决方案的有效性3.5 与相关部门和供应商进行沟通和协调,以促进解决方案的实施大点4:验证解决方案的有效性4.1 制定验证计划和测试方法,以评估解决方案的效果4.2 收集并分析验证数据,确认解决方案的有效性4.3 比较验证结果与预期目标,判断解决方案是否达到预期效果4.4 定量和定性评估解决方案的经济效益和社会效益4.5 撰写并呈报验证报告,陈述解决方案的有效性和改进成果大点5:总结与改进5.1 梳理整个8D报告的过程和结果,总结经验教训5.2 分享解决问题的成功经验和改进建议5.3 提出对质量管理和优化流程的改进建议5.4 与相关人员和团队进行沟通和反馈,以促进知识传递和共享5.5 鼓励持续学习与创新,推动质量改进的持续进行总结:通过本文介绍的五个大点,你将能够更好地理解和掌握8D报告的编写技巧。
正确理解问题的本质、制定合适的解决方案、有效实施和验证解决方案以及总结与改进都是编写高质量8D报告的关键步骤。
8D报告管理规定

管理No.:
管理制度
制定:
修正:
批准
审核
编写
题 名
8D报告管理规定
பைடு நூலகம்
1.目的 为提高解决问题的效率,积累解决问题的经验;提供找出现存的与设备质量相关问题的框架,
杜绝或尽量减少重复问题出现。 8D格式的原则是针对出现的问题,找出问题产生的根本原因,提出短期,中期,和长期对策,
并采取相应行动措施。
2.适用范围 部门内技术组工程师负责解决的各类设备问题,主要是正常生产中出现因设备原因所造成一些生 产质量损失的问题。该方法适用于解决各类可能遇到的简单或复杂的问题。 8D方法就是要建立一 个体系,让整个团队共享信息,努力达成目标;8D本身不提供成功解决问题的方法或途径,但它 是解决问题的一个很有用的工具。
相关标准No. 分类
修订理由
/
1.安全管理; 2.技能管理; 3.成本管理; 4.设备管理; 5.基础管理;6.其他
/
3.在下列情形中必须提交8D报告: 3.1生产现场的稽核中发现不合格项或缺陷时,对于严重不良,主要不良及重复发生的次要不良中 涉及设备问题的必须提交8D报告。 3.2正常生产过程中时的设备故障造成生产损失的必须提交8D报告。 3.3要对那些需要长期纠正措施来解决的缺陷采取行动时,须提交8D报告。 3.4被相关程序文件明确要求或部门领导提出要求提交8D报告时。 4.报告要求 4.1在片区维修发现问题后,需要技术组工程师提供技术支持的,需要在4小时内提出,并提供设 备故障状态的相关情况和检查情况; 4.2工程师在48小时内提交包含问题发生原因的初步分析的8D报告;若未查出具体原因,提交包含 所采取的暂时措施描述的8D报告,并在解决问题后的8小时内,提交包含问题发生原因的初步分析 的8D报告。 4.3一般各电气/机械工程师负责所负责区域设备故障(电气/机械)的8D报告编写,并按照上述要 求将报告电子版发送给郑伟,由郑伟负责整理分类,并为生产车间提供8D报告和索要损失金额, 之后将8D报告打印出来,找相关人员签字,扫描存档。 4.4郑伟收到8D报告后及时更新设备问题汇总表和设备故障对应表。
8D报告管理程序

8D报告管理程序第一步:建立一个团队要解决问题,需要建立一个专门的团队来处理和管理该问题。
这个团队应该由跨部门的成员组成,包括质量控制、工程、生产和供应链等各个部门的代表。
团队成员应该具备良好的沟通和解决问题的能力。
第二步:描述问题在这一步骤中,团队要详细描述问题的性质和发生的具体情况。
这包括问题的类型,涉及的产品或过程以及问题发生的地点和时间等。
通过详细描述问题,团队能够更好地理解问题的本质。
第三步:建立临时控制措施在此步骤中,团队需要快速采取一些临时控制措施来防止问题的进一步扩大。
这可以包括停止生产线、检查设备或产品以及提醒员工注意等。
目标是尽快减少问题带来的影响。
第四步:确定根本原因在这一步骤中,团队将使用不同的分析工具和技术来确定问题的根本原因。
这可能涉及到因果分析、5W1H分析、鱼骨图等。
通过确定问题的根本原因,团队可以制定更有效的解决方案。
第五步:采取长期解决方案在这一步骤中,团队需要根据确定的根本原因制定长期的解决方案。
这可能包括改进产品设计、修改工艺流程、更换设备或培训员工等。
目标是根除问题,确保类似的问题不再发生。
第六步:验证解决方案的有效性在这一步骤中,团队将实施和验证采取的解决方案的有效性。
这可以通过实际操作、统计数据的分析以及检查产品或过程的结果等方式来完成。
目标是确保解决方案可以解决问题并满足预期效果。
第七步:预防措施的推广在这一步骤中,团队将根据验证的解决方案扩大应用范围,并在整个组织中推广使用。
这可能包括培训员工、更新相关文件和程序等。
目标是确保类似的问题不再发生,并在组织中建立起可持续的改进机制。
第八步:表扬和奖励团队成员在解决问题的过程中,团队成员可能需要付出很大努力。
因此,在这一步骤中,团队领导应该表扬和奖励团队成员的工作。
这可以提高团队士气,并激励他们在以后更加积极地参与问题解决。
通过以上八个步骤,8D报告管理程序能够帮助组织有效地识别和解决问题。
这种程序不仅可以提高产品和过程质量,还可以提高组织的绩效和竞争力。
- 1、下载文档前请自行甄别文档内容的完整性,平台不提供额外的编辑、内容补充、找答案等附加服务。
- 2、"仅部分预览"的文档,不可在线预览部分如存在完整性等问题,可反馈申请退款(可完整预览的文档不适用该条件!)。
- 3、如文档侵犯您的权益,请联系客服反馈,我们会尽快为您处理(人工客服工作时间:9:00-18:30)。
制作:
完成日期:
第 1 页
NO. 1
ห้องสมุดไป่ตู้
纠正措施 查找相关按例与小组成员共同学习分享培训
负责人 李开恩
日期 2014/4/18
2
小组成员对公司程序文件再次学习 查找最新版TS16949:2009-FMEA潜在失效模式与后果分析培 训教材对小组成员共同学习
李开恩
2014/4/18
3
李开恩
2014/4/18
针对龙腾光电ABLSPPA165a项目,识别在特殊特性清单上的产品特性:189.2±0.15mm和 116.42±0.15mm,没 有识别在FMEA中(No.LS-3-E-689)。不符合TS16949:2009体系7.3.2.3要求。
审核: 3、短期对策 NO. 1 2 3 审核: 4、明确和核实根本原因
制作:
完成日期:
暂时补救的纠正措施 立刻对FMEA重新修订
负责人 李开恩
日期 2014/4/16
制作:
完成日期:
小组成员对潜在失效模式与后果分析(FMEA)学习的理论知识同实际操作结合理解不够,特殊特性清单与潜 在失效模式与后果分析向关联部分理解不彻底,导致一些需分析项目在FMEA表单中没有体现。
审核: 5、永久性纠正措施
审核: 6、纠正措施效果验证 NO. 1 2 3 审核: 7、预防再现措施 NO. 1 2 3 审核: 8、客户确认及评价 第一批产品满意程度:yes( ) 第二批产品满意程度:yes( ) 第三批产品满意程度:yes( ) 备注 保存期限:长期保存
制作:
完成日期:
效果验证
确认人
日期
制作:
完成日期:
版本:A
第 2 页
第 3 页
昆山电子羽电业制品有限公司
KONGTOP
投诉日期: 2014.04.12 客户/厂商: 第三方审核 物料编号:
8D报告
投诉类型: 产品型号: 投诉人: TS16949:2009体系审核不符合项 A0804前框/A0804背板
1、小组成员 部门 姓名 2、问题描述 品保部 喻爱民 工程部 李开恩 制造部 宋建友 王文中 业务部 蔡可乐 资材部 王金房 采购部 朱娟 其他
预防再现措施
负责人
日期
制作:
完成日期:
no( ) no( ) no( )
与客户_________联系,确认此批出货产品有/无以上不良现象。 与客户_________联系,确认此批出货产品有/无以上不良现象。 与客户_________联系,确认此批出货产品有/无以上不良现象。
表单编号:LS-4-Q-007