压铸参数时间
压铸件工艺参数的设定

压铸件工艺参数的设定2011-11-24 8:57:20在压铸行业,工艺参数对产品质量的影响更多的是靠试验的方法,许多工程技术人员不能深入的进行分析,生产铸件的条件无法用数据来描述。
本文就压铸工艺参数理论计算和实践两方面进行讨论研究。
压力铸造的主要工艺参数有行程(速度转换点)、速度、时间和压力等。
而本文重点分析速度和行程两个主要参数。
1. 压铸的四阶段压射计算压力铸造工艺参数,首先要定义压铸的四个压射阶段。
1.1.1 第一阶段:慢压射1为防止金属液溅出,冲头越过浇料口的过程,压射的第一阶段通常是缓慢的。
1.1.2 第二阶段:慢压射2金属液以较低的速度运动至内浇口的阶段,主要目的是排出压室内的空气,集中铝液于压室内。
1.1.3 第三阶段:快压射金属液由内浇口填充型腔直至充满为止,主要目的是成型并排出型腔中气体。
1.1.4 第四阶段:增压阶段型腔充满后建立最后的增压,使铸件在高压压力下凝固,从而使铸件致密。
1.2 计算模型1.2.1 根据1.1定义(参照图1),可以得到金属液在各阶段合金液的重量关系式。
G2=G浇G3+G4=G铸+G溢流其中:G3+G4为金属液刚达到内浇口处时冲头端面至冲头停止之间的铝液重量,即为快压射起始点位置至冲头停止行程内金属液的容量。
G铸为铸件重量G溢为溢流系统的重量G2为慢压射2行程内压室能容纳的金属液重量G浇为浇注系统的重量1.2.2 流道中单位时间内不同位置截面中通过合金液的流量关系式(见图2)金属液在流动过程中,单位时间内通过截面的流量Q相等,则Q=V1×S1=V2×S2= V3×S3 (注:V3×S3是利用等式,而非金属液流量)其中V1:冲头速度S1:冲头面积V2:内浇口速度S2:内浇口面积V3:排气槽气体速度(推荐值75m/s)S3:排气槽的面积1.2.3压铸时间[1]压铸时间包括充填时间,持压时间及铸件在压铸模型中停留的时间。
压铸成型参数设定Frech

顶出器退回
此项主要功能是将顶针拉回原来的位置。它的 速度与模具的设计有一定的关系,如顶杆式的 设计就可以调快一点,靠下一模合模的力量将 回程杆和顶针压回原来的位置。但一般滑块底 下有顶针的模具就必须设计成倒拉式的,调的 太快顶针容易断掉。通常为30%以下,速度越 快退回的压力越大。
S - 行程
开模行程 合模保护开始 合模保护结束 2段压射启动点 射料行程上限 射料行程下限 启动顶出器速度2 顶出器前进1 顶出器前进2 慢速开模启动点
三:冷却时间
是指压射后镁汤进入模具持续合模的时间通常 也是越短越好!但要保证在产品在完全凝固的 情况下,太快镁汤收缩不及造成变形.拉模等 问题。太慢也不行.一则影响生产速度二则冷 却太久镁合金收缩包附于模具表面造成产品顶 出变形.顶凸。一般根据产品的厚度及射料重 量来取决.越厚越慢.时间越久。
四:开模时间
压铸模参数设定案例
FRECH
T-时间设置 时间设置
一:合模时间 二:保压时间 三:冷却时间 四:开模时间 五:最大周期警告时间 六:顶出器启动延迟时间 七:顶出退回延迟时间 八:离嘴时间
一:合模时间
合摸时间所指关门后合摸开始到合摸结束所用 的时间。为了驾动率通常越短越好,但也是有 限制的如果在设定的范围以内,机台正常运转。 此时可以再缩短合摸时间,直到正好大于最少 合摸结束时间。
六:顶出器启动延迟时间
是指开模后产品顶出中间的间隔时间,设置太 短产品未完全冷却出现顶凸、甚至出现顶针将 产品戳穿造成产品黏模。设置太长产品因为热 涨冷缩的关系包附在模具上也会出现顶凸、黏 模。由于关系到铸机的效率,在保证不会造成 以上问题的情况下,通常越短越好。
七:顶出退回延迟时间
是指顶出器顶出到达定位后,退回的延迟时间。 此段时间取决与模具与产品的设计关系,如果 顶出器退回时产品不会被拉回原来的位置,由 于关系到铸机的效率,就可以不用设置。此项 在W页面程式预选来控制,另一方面持续生产 顶针长时间得不到润滑冷却容易断掉。有的模 具设计为顶杆式就可以不用预选。
压铸参数计算
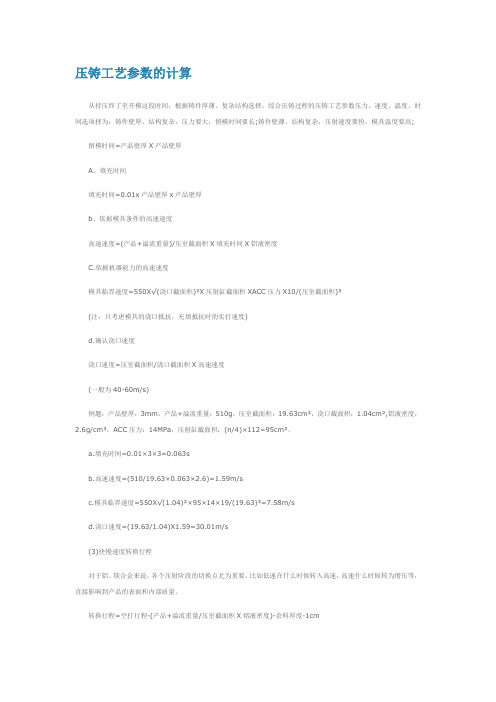
压铸工艺参数的计算从持压终了至开模这段时间,根据铸件厚薄、复杂结构选择。
综合压铸过程的压铸工艺参数压力、速度、温度、时间选项择为:铸件壁厚、结构复杂,压力要大,留模时间要长;铸件壁薄、结构复杂,压射速度要快,模具温度要高;留模时间=产品壁厚X产品壁厚A、填充时间填充时间=0.01x产品壁厚x产品壁厚b、依据模具条件的高速速度高速速度=(产品+溢流重量)/压室截面积X填充时间X铝液密度C.依据机器能力的高速速度模具临界速度=550X√(浇口截面积)²X压射缸截面积XACC压力X10/(压室截面积)³(注:只考虑模具的浇口抵抗,充填抵抗时的实打速度)d.确认浇口速度浇口速度=压室截面积/浇口截面积X高速速度(一般为40-60m/s)例题:产品壁厚:3mm,产品+溢流重量:510g,压室截面积:19.63cm²,浇口截面积:1.04cm²,铝液密度:2.6g/cm³,ACC压力:14MPa,压射缸截面积:(π/4)×112=95cm²。
a.填充时间=0.01×3×3=0.063sb.高速速度=(510/19.63×0.063×2.6)=1.59m/sc.模具临界速度=550X√(1.04)²×95×14×19/(19.63)³=7.58m/sd.浇口速度=(19.63/1.04)X1.59=30.01m/s(3)快慢速度转换行程对于铝、镁合金来说,各个压射阶段的切换点尤为重要,比如低速在什么时候转入高速,高速什么时候转为增压等,直接影响到产品的表面和内部质量。
转换行程=空打行程-(产品+溢流重量/压室截面积X熔液密度)-余料厚度-1cm(一般考虑到行程开关的反应时间,转换行程可以延长1cm)例题:产品+溢流重量:510g,压室截面积:19.63 cm²,空打行程:368mm,余料厚度:23mm,铝液密度:2.6g/cm³转换行程=36.8-(510/19.63X2.6)-2.3-1=235mm二、压力参数(1)铸造压力铸造压力是获得铸件组织致密和轮廓的主要因素,又是压铸区别于其他铸造方法的主要特征.其大小取决于压铸机的结构及功率。
压铸工艺参数(时间)
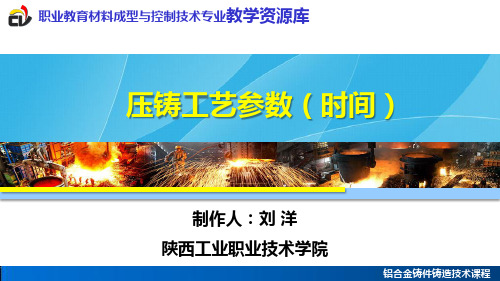
铝合金铸件铸造技术课程
职业教育材料成型与控制技术专业教学资源库
铝合金铸件铸造技术课程
职业教育材料成型与控制技术专业教学资源库
THANKS
职业教育材料成型与控制技术专业教学资源库
持压时间
从金属液充满压铸模具型腔到内浇口完全凝固,冲头压力作用在金属 液上所持续的时间称持压时间。
持压效果与余料、浇道的厚度、内浇口厚度与铸件厚度的比值有关。 持压时间的长短与合金及铸件壁厚等因素有关。熔点高、结晶温度范围大 或厚壁的铸件,持压时间需长些。反之,则可短些。
铝合金铸件铸造技术课程
职业教育材料成型与控制技术专业教学资源库
铝合金铸件铸造技术课程
职业教育材料成型与控制技术专业教学资源库
留模时间
留模时间是指持压结束到开模这段时间。 留模时间过短:铸件脱模时易引起变形或开裂,强度差的合金还可能由于 内部气体膨胀而使铸件表面鼓泡。 留模时间过长:不但影响生产率,还会因铸件温度过低收缩大,导致抽芯 及推出铸件的阻力增大,使脱模困难,热脆性合金还会引起铸件开裂。 若合金收缩率大、强度高,铸件壁薄,模具热容量大,散热快时,铸件留 模时间应短些。反之,则需长些。原则上以推出铸件不变形、不开裂的最短 时间为宜。
铝合金铸件铸造技术课程
职业教育材料成型与控制技术专业教学资源库
增压建压时间
增压建压时间是指从金属液充满型腔瞬间开始,到达预定增压压 力所需时间,也就是增压阶段比压由压射比压上升到增压比压所需的 时间。从压铸工艺角度来说,这一时间越短越好。但压铸机压射系统 的增压装置所能提供的增压建压时间是有限度的,性能较好的机器最 短建压时间也不少于0.0ls。
铝合金铸件铸造技术课程
压铸工艺参数及计算公式

1、低速流量Q1=V1*AV1=冲头面积 3.14/4*D*D (D为锤头直径)A1=0.2M/S (低速速度为30CM每秒 为预估值)2、低速时间T1=V2/Q1V2流道系统体积由CAD内计算Q1低速流量公式1计算3、高速流量QH=V3进料口截面积*A2进料口速度进料口速度估计值与产品平均壁厚有关进料口速度估计为40M/S 转成4000CM/S进料口面积由CAD内计算4、高速时间TH=V4(产品+渣包的体积)/QH高速流量V4产品+渣包的体积由CAD内计算5、四段设定341 22点到3点加上0.005S时间4点时间为(3点时间+4点时间)的2-3倍计算公式 (单位:Q1低速流量T1低速时间V1锤头面积V2流道系统体积A1低速速度QH高速流量A2进料口速度V4产品+渣包的体积V3进料口截面积A3高速锤头速度TH高速时间单位:cm)Q1V1A1(CM/S)锤头直径MM圆周率3078.76153.9420140 3.14159T1V2Q10.3962636612203078.76QH进料口面积V3进料口速度A299600.0024.94000TH体积V4QH0.017317771724.8599600.001234时间00.39630.0223流量3078.763078.7699600.0099600.00低速冲头速度高速冲头速度0.2 6.47M/SQ1V1A1(CM/S)锤头直径MM圆周率3078.76153.9420140 3.14159 T1V2Q10.3962636612203078.76QH进料口面积V3进料口速度A2104580.0024.94200TH体积V4QH0.00192675201.5104580.001234时间00.39630.0069流量3078.763078.76104580.00#########低速冲头速度高速冲头速度0.21631.98M/S。
压铸参数的计算

∙压铸工艺参数的计算∙发布时间:2011-4-9 15:39:34 来源:互联网文字【大中小】∙文/哈尔滨爱迪压铸有限公司/朱丽、刘维刚、车宏伟、迟兰成摘要:许多压铸企业的技术人员都非常熟悉压铸工艺参数的计算与调节,但在实际生产中往往凭借经验,通过检验产品的好坏来调节工艺参数,为了麻烦而忽略了工艺参数的计算,往往都是用很大的速度、压力来使产品达到合格状态,这样使机床、模具损耗过快,浪费资源。
关键词:工艺参数、压力、速度、时间在压铸生产中,压铸机、压铸合金和压铸模是三大要素。
压铸工艺则是将三大要素作为有机的组合并加以运用的过程。
压铸生产时液态金属充型的过程,是许多矛盾着的因素得以统一的过程。
在影响充型的许多因素中,主要是速度、压力和时间等,通过速度的控制减少和消除压室内空气的卷入、雾化型腔内残留的气体;通过压力的控制,增加产品的密实度,减少缩孔的形成;通过时间控制,使产品不宜产生变型等缺陷。
利用计算工艺参数来优化模具、压铸机之间的匹配性。
因此,只有对这些工艺参数进行正确选择、控制和调整,使各种工艺参数满足压铸生产的需要,才能保证在其他条件良好的情况下,生产出合格的压铸件。
本文通过以力劲公司生产的DCC280卧式冷室压铸机上所生产的水泵壳体产品(附图)为例,简单介绍一下压铸生产中主要工艺参数的计算。
一、速度参数(1)低速速度压射冲头将注入压室的铝液平稳地推移到内浇口位置,使铝液完全充满到压射冲头与内浇口之间的压室空间内的过程就是低速过程(一般为0.1-0.3m/s)。
设置时要注意防止空气卷入,防止铝液温度下降,导致过早凝固。
压室充满度=注入重量/压室截面积×空打行程×溶液密度X100%(压室充满度的标准一般为20-50%)低速速度=0.7X√压室直径/压室充满度例题:压室直径:Φ50mm,注入重量:830g,空打行程:368mm,压室截面积:(π/4)×52=19.63cm²,溶液密度:2.6 g/cm³压室充满度=(830/196.63×36.8×2.6)X100%=44.18%低速速度=(0.7X√50)/44.18=0.122M/S(2)高速速度压射冲头将铝液完全充满到压室内(一般为1.5-2.5m/s)。
压铸工艺参数(二)
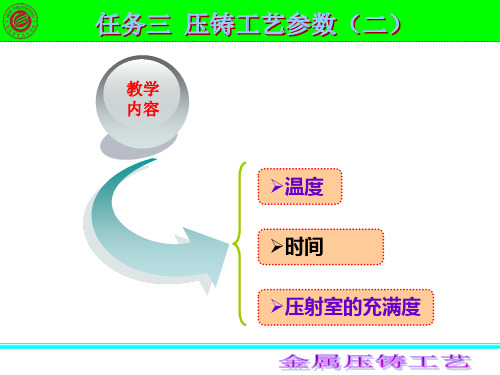
三、压射室的充满度
浇入压射室的金属液量占压射室总容量的程度称为压射室的充满度,通常 以百分数表示。
充满度对于卧式冷压室压铸机有着特殊 的意义。因为卧式压铸机的压射室在浇入金 属液后,并不是完全充满,而是在金属液面 上方留有一定的空间。 这个空间所占的体积越大,存有空气越 多,对于填充型腔时的气体量的影响越大。 其次,充满度小,合金液在压射室内的激冷 度过多,对填充也不利。因此,压射室充满 度不应过小,以免上部空间过大,一般充满 度应在40%~80%范围内,而以75%左右最 为适宜。
1 2 mv n mcT s 2 2 vn Ts 2c
式中 m——运动中的合金质量,kg; vn——内浇口速度,m/s; c ——合金的比热容,J/kg· ℃; Ts——因摩擦加热后升高的温度,℃。
上述公式计算得出内浇口速度与温升的关系见图3-17。
图3-17 内浇口速度与合金温升的关系
当内浇口速度为80m/s时,镁合金液进入型腔时的温度将增加25℃。 而内浇口速度越大,则温度增加得越多,这对准确地控制浇注温度有一 定的意义。
④避免模具因激热而胀裂;
⑤缩小模具工作时冷热交变的温度差,延长模具寿命。
(1) 影响模具温度的主要因素 1) 合金浇注温度、浇注量、热容量和导热性。 2) 浇注系统和溢流槽的设计,用以调整平衡状态。 3) 压铸比压和压射速度。 4) 模具设计。模具体积大,则热容量大,模具温度波动较小。模具 材料导热性越好,则温度分布就越均匀,有利于改善热平衡。 5) 模具合理预热提高初温,有利于改善热平衡,可提高模具寿命。 6) 生产频率快,模具温度升高,这在一定范围内对铸件和模具寿命 都是有利的。 7) 模具润滑起到隔热和散热的作用。
如果压力升高时间过短,金属尚未完全凝固,增压压力早已建成并作 用于其上,则将增大胀型力,从而引起胀型力超过允许值,发生机器锁模 力不足的现象。 因此,机器压射系统的增压装置上,压力升高时间的可调性十分重要。 其调整范围在0.015~0.3s内比较适宜。
压铸铝技术参数
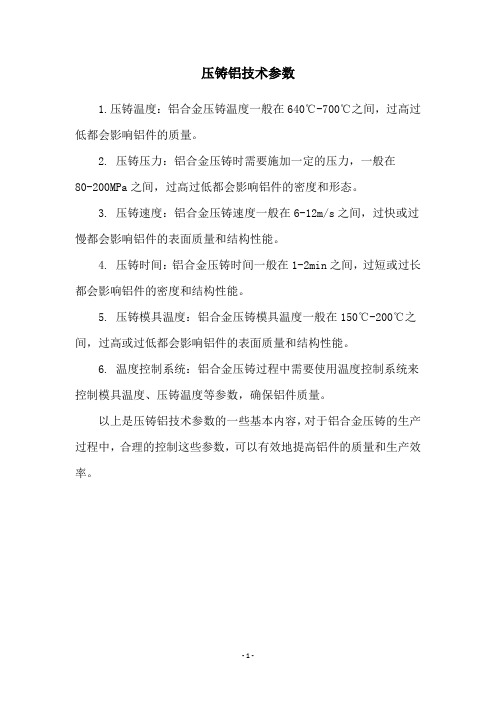
压铸铝技术参数
1.压铸温度:铝合金压铸温度一般在640℃-700℃之间,过高过低都会影响铝件的质量。
2. 压铸压力:铝合金压铸时需要施加一定的压力,一般在
80-200MPa之间,过高过低都会影响铝件的密度和形态。
3. 压铸速度:铝合金压铸速度一般在6-12m/s之间,过快或过慢都会影响铝件的表面质量和结构性能。
4. 压铸时间:铝合金压铸时间一般在1-2min之间,过短或过长都会影响铝件的密度和结构性能。
5. 压铸模具温度:铝合金压铸模具温度一般在150℃-200℃之间,过高或过低都会影响铝件的表面质量和结构性能。
6. 温度控制系统:铝合金压铸过程中需要使用温度控制系统来控制模具温度、压铸温度等参数,确保铝件质量。
以上是压铸铝技术参数的一些基本内容,对于铝合金压铸的生产过程中,合理的控制这些参数,可以有效地提高铝件的质量和生产效率。
- 1 -。
压铸工艺参数的设定和调节
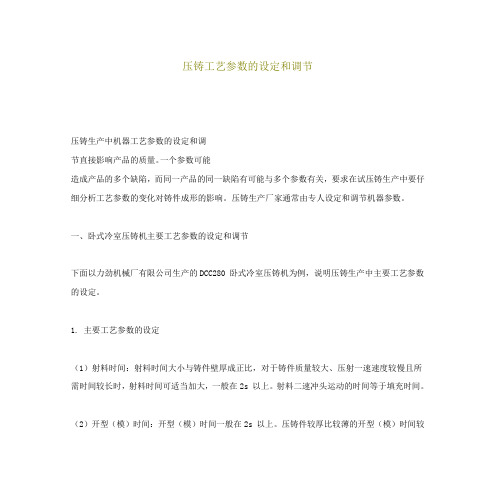
压铸工艺参数的设定和调节压铸生产中机器工艺参数的设定和调节直接影响产品的质量。
一个参数可能造成产品的多个缺陷,而同一产品的同一缺陷有可能与多个参数有关,要求在试压铸生产中要仔细分析工艺参数的变化对铸件成形的影响。
压铸生产厂家通常由专人设定和调节机器参数。
一、卧式冷室压铸机主要工艺参数的设定和调节下面以力劲机械厂有限公司生产的DCC280 卧式冷室压铸机为例,说明压铸生产中主要工艺参数的设定。
1. 主要工艺参数的设定(1)射料时间:射料时间大小与铸件壁厚成正比,对于铸件质量较大、压射一速速度较慢且所需时间较长时,射料时间可适当加大,一般在2s 以上。
射料二速冲头运动的时间等于填充时间。
(2)开型(模)时间:开型(模)时间一般在2s 以上。
压铸件较厚比较薄的开型(模)时间较之要长,结构复杂的型(模)具比结构简单的型(模)具开型(模)时间较之要长。
调节开始时可以略为长一点时间,然后再缩短,注意机器工作程序为先开型(模)后再开安全门,以防止未完全冷却的铸件喷溅伤人。
(3)顶出延时时间:在保证产品充分凝固成型且不粘模的前提下,尽量减短顶出延时时间,一般在0.5s以上。
(4)顶回延时时间:在保证能顺利地取出铸件的前提下尽量减短顶回延时时间,一般在0.5s以上。
(5)储能时间:一般在2s 左右,在设定时操作机器作自动循环运动,观察储能时间结束时,压力是否能达到设定值,在能达到设定压力值的前提下尽量减短储能时间。
(6)顶针次数:根据型(模)具要求来设定顶针次数。
(7)压力参数设定在保证机器能正常工作,铸件产品质量能合乎要求的前提下,尽量减小工作压力。
选择、设定压射比压时应考虑如下因素:1)压铸件结构特性决定压力参数的设定。
①壁厚:薄壁件,压射比压可选高些;厚壁件,增压比压可选高些。
②铸件几何形状复杂程度:形状复杂件,选择高的比压;形状简单件,比压低些。
③工艺合理性:工艺合理性好,比压低些。
2)压铸合金的特性决定压力参数的设定①结晶温度范围:结晶温度范围大,选择高比压;结晶温度范围小,比压低些。
压铸机工艺参数设定教案(精)
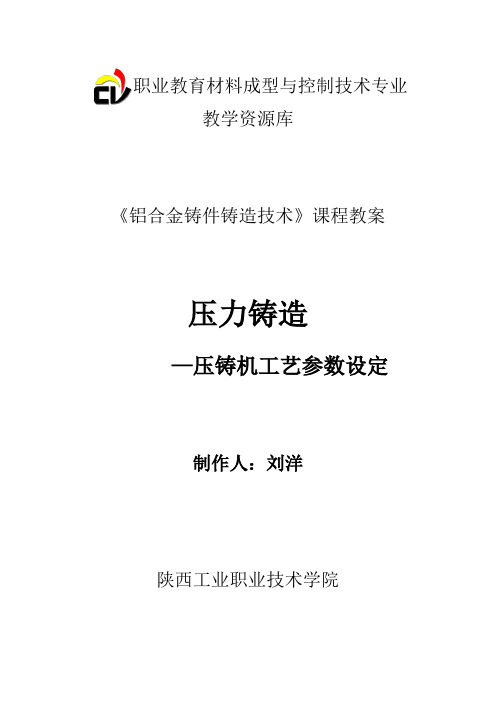
职业教育材料成型与控制技术专业教学资源库《铝合金铸件铸造技术》课程教案压力铸造—压铸机工艺参数设定制作人:刘洋陕西工业职业技术学院压力铸造—压铸机工艺参数设定一、冷室压铸机工艺参数设定1.射料时间射料时间大小与铸件壁厚成正比,对于铸件质量较大、压射一速速度较慢且所需时间较长时,射料时间可适当加大,一般在2S以上。
射料二速冲头运动的时间等于填充时间。
2.开型(模)时间开型(模)时间一般在2S以上。
压铸件较厚比较薄的开型(模)时间较之要长,结构复杂的型(模)具比结构简单的型(模)具开型(模)时间较之要长。
调节开始时可以略长一点时间,然后再缩短,注意机器工作程序为先开型(模)后再开安全门,以防止未完全冷却的铸件喷溅伤人。
3.顶出延时时间在保证产品充分凝固成型且不粘模的前提下,尽量减短顶出延时时间,一般在0.5S以上。
4.顶回延时时间在保证能顺利地取出铸件的前提下尽量减短顶回延时时间,一般在0.5S以上。
5.储能时间一般在2S左右,在设定时操作机器作自动循环运动,观察储能时间结束时,压力是否能达到设定值,在能达到设定压力值的前提下尽量减短储能时间。
6.顶针次数根据型(模)具要求来设定顶针次数。
7.压力参数设定在保证机器能正常工作,铸件产品质量能合乎要求的前提下,尽量减小工作压力。
选择、设定压射比压时应考虑如下因素:(1)压铸件结构特性决定压力参数的设定①壁厚:薄壁件,压射比压可选高些;厚壁件,增压比压可选高些。
②铸件几何形状复杂程度:形状复杂件,选择高的比压;形状简单件,比压低。
③工艺合理性:工艺合理性好,比压低些。
(2)压铸合金的特性决定压力参数的设定①结晶温度范围:结晶温度范围大,选择高比压;结晶温度范围小,比压低些。
②流动性:流动性好,选择较低压射比压;流动性差,压射比压高些。
③密度:密度大,压射比压、增压比压均应大;密度小,压射比压、增压比压均选小些。
④比强度:要求比强度大,增压比压高些。
(3)浇注系统决定压力参数的设定①浇道阻力:浇道阻力大,主要是由于浇道长、转向多,在同样截面积下、内浇口厚度小产生的,增压比压应选择大些。
压铸工艺参数(时间)教案(精)
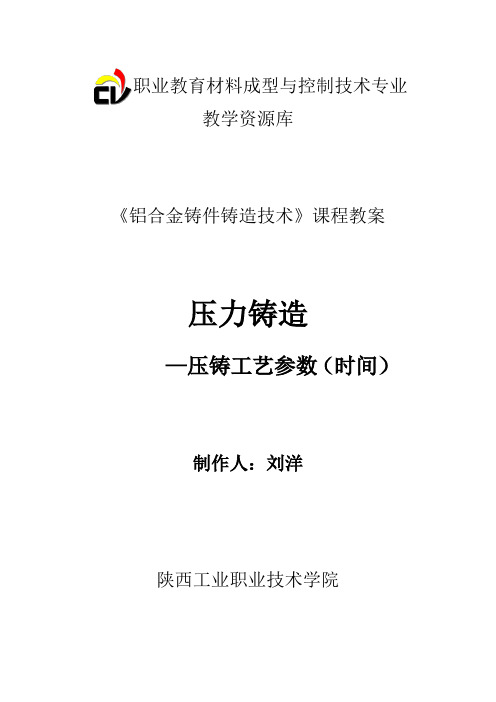
职业教育材料成型与控制技术专业教学资源库《铝合金铸件铸造技术》课程教案压力铸造—压铸工艺参数(时间)制作人:刘洋陕西工业职业技术学院压力铸造—压铸工艺参数(时间)一、充填时间金属液从开始进入模具型腔到充满型腔所需要的时间称为充填时间。
充填时间长短取决于压铸件的大小、复杂程度、内浇口截面积和内浇口速度等。
体积大、形状简单的压铸件,充填时间要长些,体积小、形状复杂的压铸件,充填时间短些。
当压铸件的体积确定后,充填时间与内浇口速度和内浇口截面积之乘积成反比。
即选用较大内浇口速度时,也能因内浇口截面积很小而仍需要较长的充填时间。
反之,当内浇口截面积较大时,即使用较小的内浇口速度,也能缩短充填时间。
因此,不能孤立地认为内浇口速度越大,其所需的充填时间越短。
在考虑内浇口截面积的大小对充填时间的影响时,还要与内浇口的厚度联系起来。
如内浇口截面积虽大,但很薄,由于压铸金属呈粘稠的”粥状”,粘度较大,通过薄的内浇口时受到很大阻力,则将使充填时间延长。
而且会使动能过多地损失,转变成热能,导致内浇口处局部过热,可能造成粘模。
压铸时,不论合金种类和铸件的复杂程度如何,一般充填时间都是很短的,中小型压铸件仅0.03~0.20s,或更短。
但充填时间对压铸件质量的影响是很明显的,充填时间长,慢速充填,金属液内卷入的气体少,但铸件表面粗糙度高。
充填时间短,快速填充,则情况相反。
二、增压建压时间增压建压时间是指从金属液充满型腔瞬间开始,到达预定增压压力所需时间,也就是增压阶段比压由压射比压上升到增压比压所需的时间。
从压铸工艺角度来说,这一时间越短越好。
但压铸机压射系统的增压装置所能提供的增压建压时间是有限度的,性能较好的机器最短建压时间也不少于0.01s。
增压建压时间取决于型腔中金属液的凝固时间。
凝固时间长的合金,增压建压时间可长些,但必须在内浇口凝固之前达到增压比压,因为合金一旦凝固,压力无法传递,即使增压也起不了压实作用。
因此压铸机增压装置上,增压建压时间的可调性十分重要。
压铸工艺参数

1、金属静压
p1
ps (1
v02 vm2 ax
)
2
p stat
p s
d1 d0
式中, p1为压射缸压力(Mpa);ps为蓄能器压力(Mpa);v0为冲头速度 (m/s);vmax为冲头最大空压射速度(m/s) ;pstat 为压射终了金属静压 (Mpa);d0为冲头直径(m);d1为压射缸直径(m)。
厚(mm)。
根据热量比可以得到几种合金的充型时间τ比
τMg:τZn︰τAl:τCu=0.51︰0.65︰1︰1.8
压铸工艺参数
1.3 时间参数
1、充时间
充型时间应该尽可能短,目的是使充型时铸件最小的部位或液流 的远端不产生早期凝固;但从另一方面考虑又要尽可能长些,以便空 气及金属熔体流动时所产生的涂料蒸汽有足够的时间逸出。根据这两 方面的矛盾要求综合考虑,选择最佳的充型时间。充型时间与壁厚有 关的推荐值,可参考下表。
压铸工艺参数
1.1 压力参数
2、充型压力
充型压力(也称为流动压力)与流速有关,按伯努利方程似稳流计算:
v 2p
式中,v为流速(m/s);p为充型压力(Mpa) ; ρ为金属密度(kg/m3)
设喷嘴或内浇口速度为 va ,则p为
p va2
2
设阻尼系数为 ξ,则p为
p
va 2
2 2
若设Q为金属熔体的流量(m3/s), Sa 为内浇口截面积(m2 ),
常用留模时间见下表
单位:h
压铸工艺参数
1.4 温度参数
1、浇注温度
金属液从压室至充满型腔的平均温度称为浇注温度。为了保证铸 件质量、提高模具寿命,浇注温度应尽可能低,一般为合金液相线以 上20~50℃,实际采用的压铸合金浇注温度,见下表。
冷室压铸机工艺参数的调校
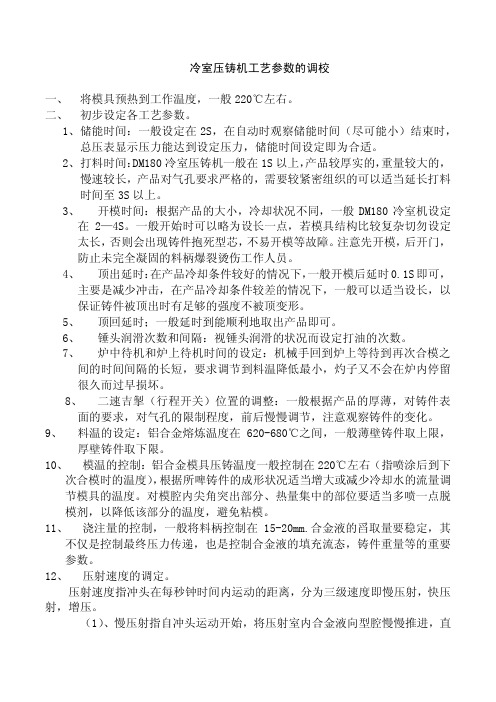
11.严格按电气操作规程和安全规定操作,保持电箱的清洁和干燥,防止电器 元件和线路受潮湿和过热。生产过程中,必须始终关闭电箱门。下班后及 时关闭总电源。
12.维修电气之前必须首先断开电源总开关,并在总开关附近显著位置挂出 “禁止接通电源”警示牌
13.经常检查吸油过滤器的堵塞情况。 14.不要用手去按压油管、法兰等漏油处,因高压油会有很大的危险性。万一
向高速逐步调节,在不影响铸件质量的情况下,以较低的充填速度为宜。因高 速会加快模具型芯,型腔的老化。
(3)、三级速度的调节:三级速度即增压,在整个压铸过程中所占时间极 短,充填速度有限,大约在 40 毫秒左右,一般观察打料压力表上显示压力呈一 斜线均匀上升即可,对铸件较大,较厚,要求组织细密的铸件要求使用增压。
当模具长期闲置不使用时,应在模具表面喷涂一层防锈剂,积架石油化 工有限公司经营的“比尔工模防锈喷剂”的使用方法如下: 将罐摇匀,从相距 15~30cm 处均匀地喷涂在需要防锈的部位上,干透时间 约 30min,指触干燥。防锈期:室内一般 6~12 个月。
安全操作 压铸机本身具有:高压力、高速度、高温合金等特点,必须时刻防止人身事
间的时间间隔的长短,要求调节到料温降低最小,灼子又不会在炉内停留 很久而过早损坏。 8、 二速吉掣(行程开关)位置的调整:一般根据产品的厚薄,对铸件表 面的要求,对气孔的限制程度,前后慢慢调节,注意观察铸件的变化。 9、 料温的设定:铝合金熔炼温度在 620-680℃之间,一般薄壁铸件取上限, 厚壁铸件取下限。 10、 模温的控制:铝合金模具压铸温度一般控制在 220℃左右(指喷涂后到下 次合模时的温度),根据所啤铸件的成形状况适当增大或减少冷却水的流量调 节模具的温度。对模腔内尖角突出部分、热量集中的部位要适当多喷一点脱 模剂,以降低该部分的温度,避免粘模。 11、 浇注量的控制,一般将料柄控制在 15-20mm.合金液的舀取量要稳定,其 不仅是控制最终压力传递,也是控制合金液的填充流态,铸件重量等的重要 参数。 12、 压射速度的调定。 压射速度指冲头在每秒钟时间内运动的距离,分为三级速度即慢压射,快压 射,增压。 (1)、慢压射指自冲头运动开始,将压射室内合金液向型腔慢慢推进,直
铝合金铸造过程工艺参数

铝合金铸造是金属铸造领域的重要分支,广泛应用于航空、汽车、电子、建筑等各个行业。
一、浇注系统浇注系统是铝合金铸造过程中的重要组成部分,它包括浇口杯、直浇道、横浇道、内浇口等部分。
浇注系统的设计合理与否直接影响到金属液体的充型能力和充型速度。
在选择浇注系统时,需要根据铸件的结构和要求来选择合适的浇口杯形状、尺寸和位置,以及合理的直浇道和横浇道结构。
同时,还需要根据浇注速度和充型时间等因素来调整内浇口的尺寸和位置。
二、铝合金铸造的参数铝合金铸造的参数主要包括压铸压力、注射速度、模具温度和填充时间。
1. 压铸压力压铸压力也是影响铸件质量和性能的重要参数。
压铸过程中的压力由压力泵产生,作用在金属液体上的压力是获得结构致密、轮廓清晰的铸件的主要因素。
压铸压力的大小直接影响到金属液体的充型能力和压实程度。
过高的压铸压力可能导致金属液体过度流动,形成飞边等缺陷;而过低的压铸压力则可能导致金属液体无法充分填充型腔,形成缩孔等缺陷。
因此,选择合适的压铸压力可以保证金属液体的充型能力和压实程度,提高铸件的质量和性能。
2. 速度(1)压铸速度铝合金铸造的注射速度是指压铸过程中注射头的速度。
注射速度的设置应该根据具体的情况来决定。
注射速度分为慢速注射和快速注射,一般慢速为0.1~0.5M/S,快速一般为0.1~1.1M/S。
铸件壁厚越薄,注射速度越快,铸件形状越复杂,注射速度越快。
铸件的突出面越大,注射速度越快,铸球路径越长,注射速度越快。
(2)浇注速度浇注速度是影响铸件质量和性能的重要因素之一。
过快的浇注速度可能导致金属液体在充型过程中产生涡流和卷气等缺陷;而过慢的浇注速度则可能导致金属液体无法充分填充型腔,形成缩孔等缺陷。
因此,在铝合金铸造过程中,需要根据铸件的结构和要求来选择合适的浇注速度。
同时,还需要根据金属液体的流动性和充型能力等因素来调整内浇口的尺寸和位置。
3. 模具温度铝合金铸造的模具温度是影响铸件质量和性能的重要参数之一。
压铸参数时间

因此,留型时间应根据铸件的合金性质、铸件壁厚和结构特性 来选定。
材料工程学院材料成型教研室
铝合金铸件铸造技术
材料工程学院材料成型教研室
材料工程学院材料成型教研室
铝合金铸件铸造技术
(4)留模时间 留模时间是指持压结束到开模这段时间。 留模时间过短:铸件脱模时易引起变形或开裂,强度差的合金还
可能由于内部气体膨胀而使铸件表面鼓泡。 留模时间过长:不但影响生产率,还会因铸件温度过低收缩大,
导致抽芯及推出铸件的阻力增大,使脱模困难,热脆性合金还会引 起铸件开裂。
所需时间,也就是增压阶段比压由压射比压上升到增压比压所需的时 间。从压铸工艺角度来说,这一时间越短越好。但压铸机压射系统的 增压装置所能提供的增压建压时间是有限度的,性能较好的机器最短 建压时间也不少于0.0ls。
增压建压时间取决于型腔中金属液的凝固时间。凝固时间长的合 金,增压建压时间可长些,但必须在内浇口凝固之前达到增压比压, 因为合金一旦凝固,压力无法传递,即使增压也起不了压实作用。因 此压铸机增压装置上,增压建压时间的可调性十分重要。
当压铸件的体积确定后,充填时间与内浇口速度和内浇口截面积之 乘积成反比。
充填时间对压铸件质量的影响是很明显的,充填时间长,慢速充填, 金属液内卷入的气体少,但铸件表面粗糙度高。充填时间短,快速填 充,则情况相反。
材料工程学院材料成型教研室
铝合金铸件铸造技术
(2)增压建压时间 增压建压时间是指从金属液充满型腔瞬间开始,到达预定增压压力
包括以下四中时间时间
增压建压 时间
留模时间
压铸参数计算(精)
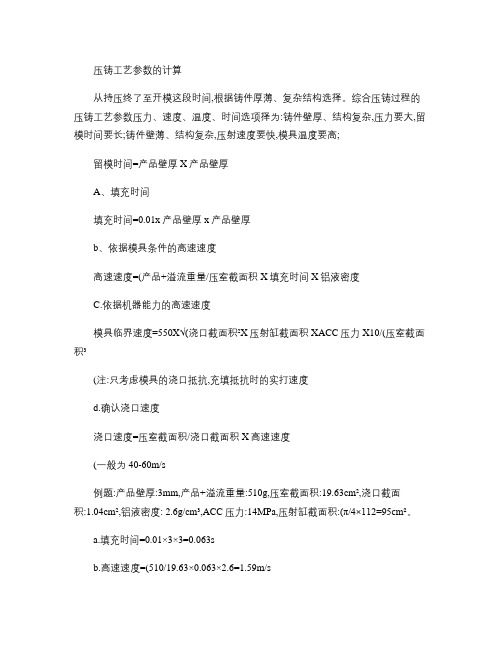
压铸工艺参数的计算从持压终了至开模这段时间,根据铸件厚薄、复杂结构选择。
综合压铸过程的压铸工艺参数压力、速度、温度、时间选项择为:铸件壁厚、结构复杂,压力要大,留模时间要长;铸件壁薄、结构复杂,压射速度要快,模具温度要高;留模时间=产品壁厚X产品壁厚A、填充时间填充时间=0.01x产品壁厚x产品壁厚b、依据模具条件的高速速度高速速度=(产品+溢流重量/压室截面积X填充时间X铝液密度C.依据机器能力的高速速度模具临界速度=550X√(浇口截面积²X压射缸截面积XACC压力X10/(压室截面积³(注:只考虑模具的浇口抵抗,充填抵抗时的实打速度d.确认浇口速度浇口速度=压室截面积/浇口截面积X高速速度(一般为40-60m/s例题:产品壁厚:3mm,产品+溢流重量:510g,压室截面积:19.63cm²,浇口截面积:1.04cm²,铝液密度: 2.6g/cm³,ACC压力:14MPa,压射缸截面积:(π/4×112=95cm²。
a.填充时间=0.01×3×3=0.063sb.高速速度=(510/19.63×0.063×2.6=1.59m/sc.模具临界速度=550X√(1.04²×95×14×19/(19.63³=7.58m/sd.浇口速度=(19.63/1.04X1.59=30.01m/s(3快慢速度转换行程对于铝、镁合金来说,各个压射阶段的切换点尤为重要,比如低速在什么时候转入高速,高速什么时候转为增压等,直接影响到产品的表面和内部质量。
转换行程=空打行程-(产品+溢流重量/压室截面积X熔液密度-余料厚度-1cm(一般考虑到行程开关的反应时间,转换行程可以延长1cm例题:产品+溢流重量:510g,压室截面积:19.63 cm²,空打行程:368mm,余料厚度:23mm,铝液密度: 2.6g/cm³转换行程=36.8-(510/19.63X2.6-2.3-1=235mm二、压力参数(1铸造压力铸造压力是获得铸件组织致密和轮廓的主要因素,又是压铸区别于其他铸造方法的主要特征.其大小取决于压铸机的结构及功率。
5-冷室压铸机参数和参数调校
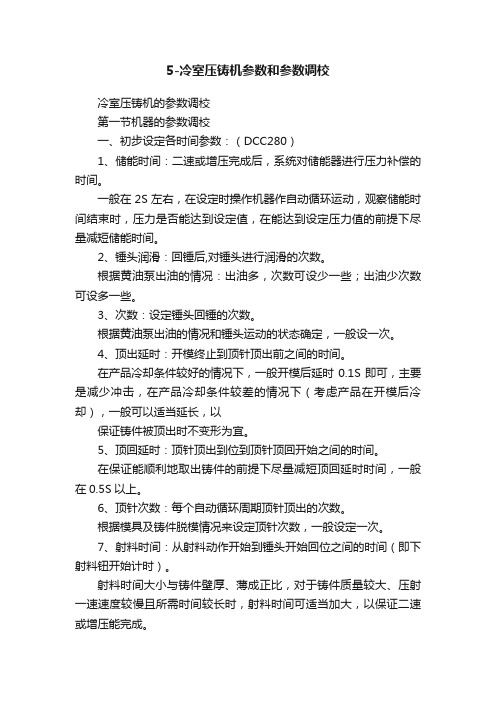
5-冷室压铸机参数和参数调校冷室压铸机的参数调校第一节机器的参数调校一、初步设定各时间参数:(DCC280)1、储能时间:二速或增压完成后,系统对储能器进行压力补偿的时间。
一般在2S左右,在设定时操作机器作自动循环运动,观察储能时间结束时,压力是否能达到设定值,在能达到设定压力值的前提下尽量减短储能时间。
2、锤头润滑:回锤后,对锤头进行润滑的次数。
根据黄油泵出油的情况:出油多,次数可设少一些;出油少次数可设多一些。
3、次数:设定锤头回锤的次数。
根据黄油泵出油的情况和锤头运动的状态确定,一般设一次。
4、顶出延时:开模终止到顶针顶出前之间的时间。
在产品冷却条件较好的情况下,一般开模后延时0.1S即可,主要是减少冲击,在产品冷却条件较差的情况下(考虑产品在开模后冷却),一般可以适当延长,以保证铸件被顶出时不变形为宜。
5、顶回延时:顶针顶出到位到顶针顶回开始之间的时间。
在保证能顺利地取出铸件的前提下尽量减短顶回延时时间,一般在0.5S以上。
6、顶针次数:每个自动循环周期顶针顶出的次数。
根据模具及铸件脱模情况来设定顶针次数,一般设定一次。
7、射料时间:从射料动作开始到锤头开始回位之间的时间(即下射料钮开始计时)。
射料时间大小与铸件壁厚、薄成正比,对于铸件质量较大、压射一速速度较慢且所需时间较长时,射料时间可适当加大,以保证二速或增压能完成。
8、开模时间:射料时间结束开始计时到开模开始动作之间的时间(即冷却时间)。
开模时间一般在3S以上。
压铸件较厚比较薄的开模时间较之要长,结构复杂的模具比结构简单的模具开模时间较之要长。
调节开始时可以略为长一点时间,然后适当缩短。
二、初步设定各压力参数:(DCC280)1、总压:调节储能、起压,抽芯时系统的压力。
一般是总压设在90-99之间,在保证压铸机正常压铸的条件下,尽量设定低些,以延长机械使用寿命,降低能耗。
2、顶针压力拨码:设定顶针动作时,顶针油路的压力。
顶针压力一般设定在30-50之间,能顺利顶出产品即为合适。
- 1、下载文档前请自行甄别文档内容的完整性,平台不提供额外的编辑、内容补充、找答案等附加服务。
- 2、"仅部分预览"的文档,不可在线预览部分如存在完整性等问题,可反馈申请退款(可完整预览的文档不适用该条件!)。
- 3、如文档侵犯您的权益,请联系客服反馈,我们会尽快为您处理(人工客服工作时间:9:00-18:30)。
铝合金铸件铸造技术 (3)持压时间
从金属液充满压铸模具型腔到内浇口完全凝固,冲头压力作用在 金属液上所持续的时间称持压时间。
持压效果与余料、浇道的厚度、内浇口厚度与铸件厚度的比值有关。 持压时间的长短与合金及铸件壁厚等因素有关。熔点高、结晶温度范 围大或厚壁的铸件,持压时间需长些。反之,则可短些。
包括以下四中时间。
铝合金铸件铸造技术
压铸参数时间
充填时间
增压建压 时间
留模时间
材料工程学院材料术
(1)充型时间 金属液从开始进入模具型腔到充满型腔所需要的时间称为充填时间。 充填时间长短取决于压铸件的大小、复杂程度、内浇口截面积和内
浇口速度等。体积大、形状简单的压铸件,充填时间要长些,体积小、 形状复杂的压铸件,充填时间短些。
所需时间,也就是增压阶段比压由压射比压上升到增压比压所需的时 间。从压铸工艺角度来说,这一时间越短越好。但压铸机压射系统的 增压装置所能提供的增压建压时间是有限度的,性能较好的机器最短 建压时间也不少于0.0ls。
增压建压时间取决于型腔中金属液的凝固时间。凝固时间长的合 金,增压建压时间可长些,但必须在内浇口凝固之前达到增压比压, 因为合金一旦凝固,压力无法传递,即使增压也起不了压实作用。因 此压铸机增压装置上,增压建压时间的可调性十分重要。
若合金收缩率大、强度高,铸件壁薄,模具热容量大,散热快时, 铸件留模时间应短些。反之,则需长些。原则上以推出铸件不变形、 不开裂的最短时间为宜。
因此,留型时间应根据铸件的合金性质、铸件壁厚和结构特性 来选定。
材料工程学院材料成型教研室
铝合金铸件铸造技术
材料工程学院材料成型教研室
材料工程学院材料成型教研室
铝合金铸件铸造技术
(4)留模时间 留模时间是指持压结束到开模这段时间。 留模时间过短:铸件脱模时易引起变形或开裂,强度差的合金还
可能由于内部气体膨胀而使铸件表面鼓泡。 留模时间过长:不但影响生产率,还会因铸件温度过低收缩大,
导致抽芯及推出铸件的阻力增大,使脱模困难,热脆性合金还会引 起铸件开裂。
当压铸件的体积确定后,充填时间与内浇口速度和内浇口截面积之 乘积成反比。
充填时间对压铸件质量的影响是很明显的,充填时间长,慢速充填, 金属液内卷入的气体少,但铸件表面粗糙度高。充填时间短,快速填 充,则情况相反。
材料工程学院材料成型教研室
铝合金铸件铸造技术
(2)增压建压时间 增压建压时间是指从金属液充满型腔瞬间开始,到达预定增压压力