油压机液压系统设计若干问题研究
液压系统的常见问题及其对策

液 压 系统 的 常见 问题 及 其对 策械 自动化学院,湖北武汉 4 3 0 0 8 1 ; 2 .武汉钢铁 股份 有 限公 司烧结 厂 ,湖北 武汉 4 3 0 0 8 3 )
摘要 :分析了液压 系统 的常见 问题 ,并提 出了相应 的解决方法和预 防措施 ,对延长液压 元件的寿命 ,提 高液压 系统的 可靠性都有一定的帮助 。
液压冲击会使系统的瞬时压力倍增 ,产生振动和 噪声 ,同时升高油温 ,威胁到系统 中的密封装置 、管 道及其他 的液压元件 ,直接影 响了系统 的稳定性与可 靠性 。通过综 合分析各种液压 系统 的冲击情况 ,得出 其产生 的主要机制及其对策 如下 : ( 1 )液压缸 在高 速运动 时 ,突 然制 动会 因惯 性 而产生液压冲击 。为此 ,可 以在缸 的末端设置缓 冲装 置 ,使其能在行程终 点附近逐 渐停止或反 向;为受到 冲击 的油路设置安全 阀 ,使 冲击产 生 的高压油 溢流 , 起到卸荷 的作用 ;另外还可以为系统安装 蓄能器 ,以 便吸收系统脉动 ,实现油路 中的平 滑滤波 ,如 图 1 所
关键词 :液压系统 ;常见问题 ;对策 中图分类号 :T H 1 3 7 文献标识码 :B 文章编号 :1 0 0 1— 3 8 8 1( 2 0 1 3 )2—1 1 8—1
液压系统因优 点突 出已被广泛应 用于机 械制造 、 工程建筑 、矿山冶金 、石油化工 、军事器械等各个领
( R E X R O T H 系统 )或先导 阀 ( S A U E R系统 )上 的 电
部进入 油泵伺 服缸 ,因此远 程 调压 阀过 来 的控制 油 压力损 失大 、流量相 对较 小 ,对 伺服 缸 活塞作 用 效 果 不太 显 著 ,相 比较 而 言 ,R E X R O T H 系统 中伺 服 缸活塞 比 S A U E R系统 中伺 服 缸 活塞 易 被 推 动 ,使 油泵斜盘 换 向更 容 易 ,故 R E X R O T H系统 比 S A U E R
液压系统优化设计技术研究

液压系统优化设计技术研究液压系统已经成为现代机械制造业发展的重要组成部分,其广泛应用于工业生产和民生领域。
随着现代科技的不断进步和全球市场竞争的日益激烈,如何提高液压系统的效率和性能已经成为生产制造企业所面临的重要问题。
因此,液压系统优化设计技术的研究和应用已经成为目前液压技术研究方向的重要领域之一。
一、液压系统的基本结构和工作原理液压系统主要由液压泵、液压马达、液压缸、液压阀等组成,其基本工作原理是利用工业油液将电力转换为机械动力,提供机械装置所需的能量。
液压系统在工业生产中应用广泛,如汽车工业、模具加工、航空航天、石油化工、机床制造等行业均离不开液压技术的应用。
二、液压系统优化设计技术的研究意义液压系统在各种不同的应用领域中,需要满足不同的工作条件。
因此,如何优化液压系统的设计,提高其效率和性能已经成为重要的研究课题。
针对这个问题,液压系统优化设计技术应运而生。
液压系统优化设计技术的研究意义在于:1. 提高液压系统的效率,减少能量损失,实现节能环保。
2. 降低生产成本,提高生产效率和生产线的稳定性。
3. 提高产品的质量和可靠性,使产品更加适合市场需求。
三、液压系统的优化设计技术研究内容液压系统优化设计技术研究应包括以下主要内容:1. 变量泵及电液伺服阀控制技术。
电液伺服阀是一种高性能的节流控制元件,其结构也越来越复杂。
通过对电液伺服阀和变量泵的研究,能够实现更加精确的流量和压力控制。
2. 液压系统中的流场分析。
液压系统中的液体流动具有非线性、非稳定性和非静态性,流场分析是液压系统优化设计过程中的一个重要环节。
流场分析可以通过仿真技术来进行,以验证设计方案的可用性和稳定性。
3. 液压系统中的噪声和振动控制。
液压系统中的噪声和振动都会影响到系统的稳定性和工作效率。
因此,如何减少系统中的噪声和振动,提高系统的稳定性和可靠性也是液压系统优化设计的一个重要研究内容。
四、结语液压系统优化设计技术的研究和应用已经成为现代化生产制造企业不可或缺的组成部分。
液压机液压系统设计的挑战与对策

液压机液压系统设计的挑战与对策1. 引言液压系统作为液压机的核心部分,其设计的优劣直接影响到整个液压机的性能和稳定性。
本文将详细讨论液压机液压系统设计中面临的挑战,并提出相应的对策。
2. 液压机液压系统设计的挑战2.1 系统稳定性与可靠性液压系统需要长期稳定运行,任何故障都可能导致设备停机,造成生产损失。
因此,如何保证系统的稳定性和可靠性是液压机液压系统设计的首要挑战。
2.2 系统效率与节能随着能源成本的不断上升,提高液压系统的效率和节能成为设计的重要目标。
然而,液压系统中的泄漏、液压油温升等问题都会影响系统的效率。
2.3 系统精度与响应速度现代液压机对系统的精度和响应速度要求越来越高,如何设计出具有高精度、高响应速度的液压系统是设计师面临的挑战。
2.4 系统维护与故障诊断液压系统的维护和故障诊断是保证系统稳定运行的重要环节。
然而,液压系统复杂,故障原因多样,如何提高维护效率和故障诊断的准确性是设计时需要考虑的问题。
3. 液压机液压系统设计的对策3.1 提高系统稳定性与可靠性- 选择高质量的液压元件,确保其稳定性和可靠性。
- 采用合理的系统设计,减少压力冲击和振动。
- 增加系统的冗余设计,提高系统的可靠性。
3.2 提高系统效率与节能- 优化液压系统的工作原理,减少能量损失。
- 采用高效的液压泵和电机,提高系统效率。
- 加强系统的泄漏管理,减少能量损失。
3.3 提高系统精度与响应速度- 采用高精度的液压元件,提高系统的精度。
- 优化液压系统的控制策略,提高系统的响应速度。
- 减少液压系统的压力波动和流量脉动,提高系统的稳定性。
3.4 提高系统维护与故障诊断的效率- 设计易于维护的液压系统,简化系统结构,减少维护工作量。
- 采用故障诊断系统,实时监控液压系统的运行状态,及时发现并处理故障。
- 对液压系统的操作人员进行培训,提高其维护和故障诊断的能力。
4. 结论液压机液压系统设计面临的挑战多样,需要设计师在保证系统的稳定性和可靠性的同时,提高系统效率和节能,满足现代液压机对系统精度和响应速度的要求,同时提高系统维护和故障诊断的效率。
油压机液压系统设计

油压机液压系统设计首先,设计人员需要确定油压机所需的工作能力,包括最大工作压力、最大工作流量和所需的力量。
这些参数将直接影响液压系统的选型。
例如,如果需要较高的工作压力,液压泵和液压缸的选型和配色需要相应地进行调整。
其次,设计人员需要选择合适的液压元件。
液压系统主要由液压泵、液压阀、液压缸和液压油箱组成。
液压泵的选型应该考虑到所需的流量和压力范围。
液压阀的选型需要考虑到所需的控制方式和功能。
液压缸的选型要根据所需的力量和行程进行选择。
液压油箱的大小应根据系统的工作容量和热稳定性来确定。
接下来,设计人员需要确定液压系统的工作方式和控制方式。
油压机的工作方式可以分为手动控制和自动控制两种。
手动控制方式通常使用手柄或按钮来控制液压阀的开关。
自动控制方式通常使用传感器或PLC来监测和控制液压系统的工作状态。
控制方式的选择将直接影响到液压系统的控制系统设计。
然后,设计人员需要考虑液压系统的安全性和可靠性。
液压系统的设计应该考虑到系统的过载保护和紧急停机装置。
例如,可以使用压力开关来监测系统的工作压力,一旦超过设定值,系统将自动停机。
此外,液压系统的设计还应考虑到泄漏和故障的预防和修复措施,以确保系统的正常工作。
最后,设计人员还需要考虑液压系统的维护和维修问题。
液压系统的维护需要定期更换液压油和滤芯,并检查和清洁液压元件。
在系统出现故障时,设计人员需要准备相应的维修工具和备件,以便及时修复系统。
总结起来,油压机液压系统设计需要考虑工作能力、液压元件的选型、工作方式和控制方式、安全性和可靠性以及维护和维修等因素。
设计人员应充分了解油压机的工作要求,并选择合适的液压元件和控制系统来满足这些要求。
只有合理设计和维护液压系统,才能保证油压机的正常工作和高效生产。
液压系统设计和使用中问题的分析
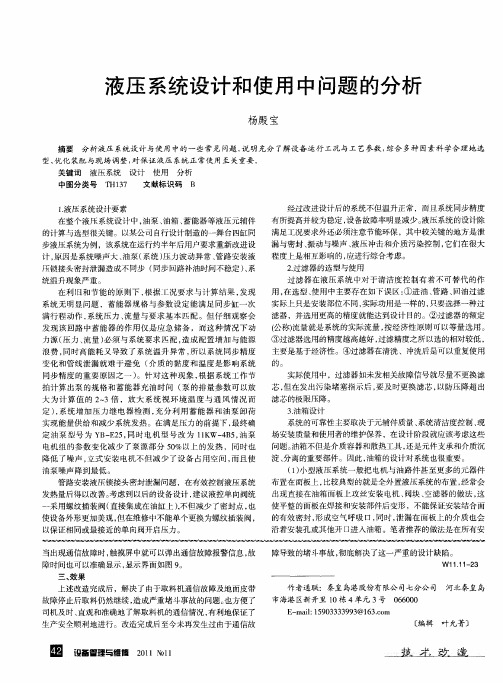
满 行程动作 , 系统压力 、 流量与 要求基本 匹配 。但 仔细 观察会 发现该 回路 中蓄能器 的作用 仅是应急 储备 ,而这种情 况下动
力源( 压力 、 流量 ) 必须 与系统要求 匹配 , 造成配 置增加 与能源 浪费 , 同时高 能耗又导致 了系统温 升异常 , 以系统 同步精度 所 变化和管线 泄漏就难 于避免 ( 介质 的黏度和温 度是影 响系统
满足工况要求外还必须 注意节能环保 ,其中较关键 的地方是泄
漏 与密封 、 振动与噪声 、 液压冲击和介质污染控 制 , 它们 在很大 程度上是相互影响的 , 应进行综 合考虑 。
2过滤器的选型与使用 .
计 , 因是系统噪声大 、 原 油泵( 系统 ) 压力 波动异常 、 管路安装液
压锁接头 密封泄漏造成不 同步 ( 同步 回路补油时间不稳定 )系 、 统温升现象严重 。
大为计 算 值 的 2 3倍 ,放 大系 统视 环 境温 度 与通 风 情况 而 - 定 ) 系统增 加压 力继 电器检测 , , 充分 利用 蓄能 器和 油泵 卸荷 实现能量供给和减少 系统 发热 。在满 足压力的前提下 , 最终确 定油 泵型号 为 Y — 2 , B E 5 同时 电机型 号改 为 1 K 4 5 油泵 1 W一 B , 电机组 的参 数变化减少 了泵源部分 5 %以上 的发热 ,同时也 0
发热量后得 以改善 。 考虑到 以后的设 备设计 , 建议液控单 向阀统
一
采用螺纹插装 阀( 直接集成在油缸上 ) , 减少 了密封点 , 不但 也
使平 整的面板在焊接和安装部件后变形 ,不能保证安装结合面
的有效密 封 , 形成空气呼 吸 口, 同时 , 泄漏在面板上 的介 质也会 沿着安装孔或其他开 口进入油箱 。笔者推 荐的做法是在所有安
液压系统的设计研究
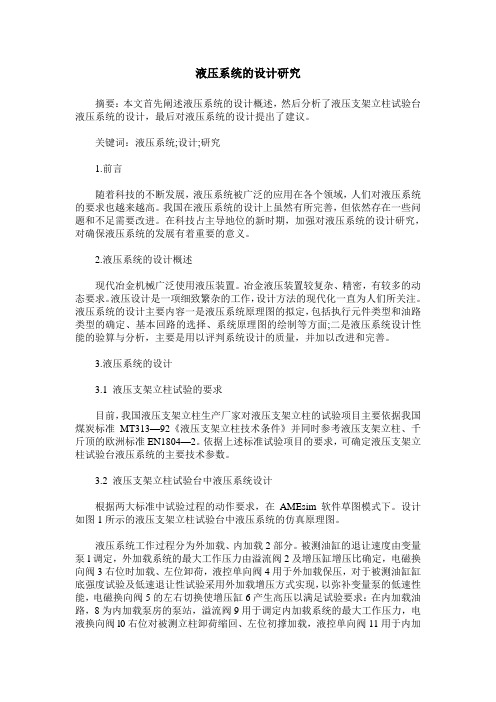
液压系统的设计研究摘要:本文首先阐述液压系统的设计概述,然后分析了液压支架立柱试验台液压系统的设计,最后对液压系统的设计提出了建议。
关键词:液压系统;设计;研究1.前言随着科技的不断发展,液压系统被广泛的应用在各个领域,人们对液压系统的要求也越来越高。
我国在液压系统的设计上虽然有所完善,但依然存在一些问题和不足需要改进。
在科技占主导地位的新时期,加强对液压系统的设计研究,对确保液压系统的发展有着重要的意义。
2.液压系统的设计概述现代冶金机械广泛使用液压装置。
冶金液压装置较复杂、精密,有较多的动态要求。
液压设计是一项细致繁杂的工作,设计方法的现代化一直为人们所关注。
液压系统的设计主要内容一是液压系统原理图的拟定,包括执行元件类型和油路类型的确定、基本回路的选择、系统原理图的绘制等方面;二是液压系统设计性能的验算与分析,主要是用以评判系统设计的质量,并加以改进和完善。
3.液压系统的设计3.1 液压支架立柱试验的要求目前,我国液压支架立柱生产厂家对液压支架立柱的试验项目主要依据我国煤炭标准MT313—92《液压支架立柱技术条件》并同时参考液压支架立柱、千斤顶的欧洲标准EN1804—2。
依据上述标准试验项目的要求,可确定液压支架立柱试验台液压系统的主要技术参数。
3.2 液压支架立柱试验台中液压系统设计根据两大标准中试验过程的动作要求,在AMEsim软件草图模式下。
设计如图1所示的液压支架立柱试验台中液压系统的仿真原理图。
液压系统工作过程分为外加载、内加载2部分。
被测油缸的退让速度由变量泵l调定,外加载系统的最大工作压力由溢流阀2及增压缸增压比确定,电磁换向阀3右位时加载、左位卸荷,液控单向阀4用于外加载保压,对于被测油缸缸底强度试验及低速退让性试验采用外加载增压方式实现,以弥补变量泵的低速性能,电磁换向阀5的左右切换使增压缸6产生高压以满足试验要求:在内加载油路,8为内加载泵房的泵站,溢流阀9用于调定内加载系统的最大工作压力,电液换向阀l0右位对被测立柱卸荷缩回、左位初撑加载,液控单向阀11用于内加载系统被测立柱的保压,电液换向阀12左右切换驱动增压缸13,对被测立柱增压加载,安全阀l4在测试被测立柱退让性项目时,用于调整立柱的测试压力,在强度试验中不装安全阀。
工程机械液压系统设计及改进研究

工程机械液压系统设计及改进研究
随着工程机械行业的迅速发展和应用领域的不断拓展,液压系统在工程机械中扮演着越来越重要的角色。
液压系统是工程机械中最复杂的机电一体化系统之一,同时也是影响机械性能和可靠性的重要因素之一。
液压系统是通过电动机、发动机或其他动力源将能量转换成压力能,并将压力能通过合理的导管和阀门控制,使得液压缸或液压马达等液压元件运动的一种传动方式。
较好的液压系统设计和改进可以显著提高机械效率,降低能源消耗,提高工作质量和可靠性等多个方面的指标。
因此,深入探究液压系统设计和改进问题具有广泛的研究和应用价值。
液压系统的设计和改进需要从多个角度进行考虑。
首先要分析工程机械的工作原理和工况需求,结合液压系统的原理和特点,合理选择各个液压元件的类型、规格和数量,进行液压系统的初步设计。
同时,还要根据不同工作状态和负载情况,进行液压系统的优化设计。
这些优化设计包括改进液压油路、调整阀门控制参数、跟踪和控制系统温度、改进液压油泵和液压缸的性能等等。
在液压系统的改进研究中,液压泵是一个非常重要的研究对象。
液压泵是液压系统的能源来源,其性能的好坏直接影响液压系统的质量。
在对液压泵进行改进研究时,可以从多个方面入手,如优化液压泵叶轮的结构和形状以提高泵的效率,改进传动系统以降低泵的能耗,改善泵的工作温度和噪声等问题等等。
总之,液压系统的设计和改进是工程机械提高效率、降低成本、提高质量和可靠性的关键。
未来随着工程机械行业的发展和应用范围的不断扩大,液压系统的研究和应用也将越来越重要和广泛。
液压系统设计与应用研究
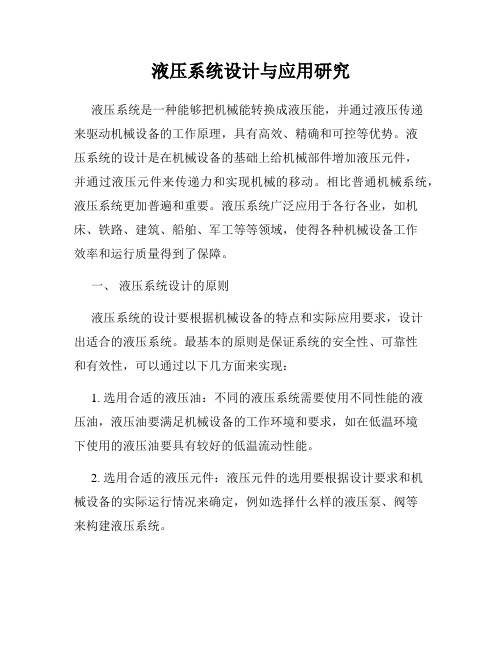
液压系统设计与应用研究液压系统是一种能够把机械能转换成液压能,并通过液压传递来驱动机械设备的工作原理,具有高效、精确和可控等优势。
液压系统的设计是在机械设备的基础上给机械部件增加液压元件,并通过液压元件来传递力和实现机械的移动。
相比普通机械系统,液压系统更加普遍和重要。
液压系统广泛应用于各行各业,如机床、铁路、建筑、船舶、军工等等领域,使得各种机械设备工作效率和运行质量得到了保障。
一、液压系统设计的原则液压系统的设计要根据机械设备的特点和实际应用要求,设计出适合的液压系统。
最基本的原则是保证系统的安全性、可靠性和有效性,可以通过以下几方面来实现:1. 选用合适的液压油:不同的液压系统需要使用不同性能的液压油,液压油要满足机械设备的工作环境和要求,如在低温环境下使用的液压油要具有较好的低温流动性能。
2. 选用合适的液压元件:液压元件的选用要根据设计要求和机械设备的实际运行情况来确定,例如选择什么样的液压泵、阀等来构建液压系统。
3. 保证系统的可靠性:系统的可靠性直接决定了机械设备的工作质量和效率,可靠性需要从液压元件的质量、制造工艺、安装方式等多个方面进行保证。
4. 设计合理的控制系统:液压控制系统要满足机械设备的控制要求,达到精准控制系统液压能量的目的。
二、液压系统应用技术的研究液压系统应用技术方面的研究主要涉及流体力学、控制理论和材料技术三方面:1. 流体力学:液压系统涉及到流体力学、动力学等学科。
流体力学是液压系统的基础,液压能转化就是基于流体力学的原理展开的。
液压油的流动和压力变化都是流体力学模型,在设计液压系统时需要通过喷管、阀门等措施来调整油的流量和压力。
2. 控制理论:液压系统通过液体来传输能量和动力,控制理论用于设计移动、定位和自动化的场景。
控制理论可以通过传感器、反馈机制等措施来实现对液压系统的控制和调节。
3. 材料技术:液压系统中各种液压元件的材料直接影响了系统的质量、安全性、可靠性和使用寿命。
液压系统设计与项目可行性研究报告

液压系统设计与项目可行性研究报告1.研究背景液压系统是一种利用液体传递能量的机械系统,广泛应用于工业生产线、建筑设备、航空航天等领域。
然而,现有的液压系统存在一些问题,如能耗高、效率低、噪音大等。
因此,研究设计一种新型液压系统以解决这些问题具有重要意义。
2.研究目标本研究旨在设计一种高效、节能、低噪音的液压系统,并评估其可行性。
具体目标如下:(1)设计新型液压系统的结构和工作原理。
(2)分析新型液压系统的性能特点,并与传统液压系统进行对比。
(3)在实验室中建立新型液压系统的原型,并进行性能测试。
(4)评估新型液压系统的经济效益和可行性。
3.设计方法(1)首先,对现有液压系统进行调研,分析其优缺点,并确定设计新型液压系统的目标和要求。
(2)其次,采用系统设计的方法,根据液压系统的工作原理和结构要求,设计出新型液压系统的结构和部件。
并使用CAD软件进行模型设计和模拟分析。
(3)然后,使用MATLAB等工具进行系统仿真以验证新型液压系统的性能。
(4)最后,建立新型液压系统的原型,并进行性能测试和实验验证。
4.可行性研究(1)技术可行性:通过对现有液压系统的改进设计和创新,设计出新型液压系统具有较高的技术可行性。
(2)经济可行性:通过对新型液压系统的成本估算和效益分析,评估其经济可行性。
预计新型液压系统的节能效果和运行成本将显著优于传统液压系统。
(3)市场可行性:通过对市场需求和竞争情况的分析,评估新型液压系统的市场可行性。
预计新型液压系统在工业生产和建筑设备领域具有广阔的应用前景。
5.预期成果(1)设计出一种高效、节能、低噪音的液压系统原型。
(2)验证新型液压系统的性能和可行性。
(3)提供新型液压系统的设计方法和技术指导,为相关领域的液压系统改进和创新提供参考。
(4)引起相关行业和科研机构的关注,并促进新型液压系统的推广和应用。
6.预期进展和挑战研究过程中可能会面临一些挑战,如系统模型设计的复杂性、原型的制作和实验验证的困难等。
液压系统故障分析与维修技术研究
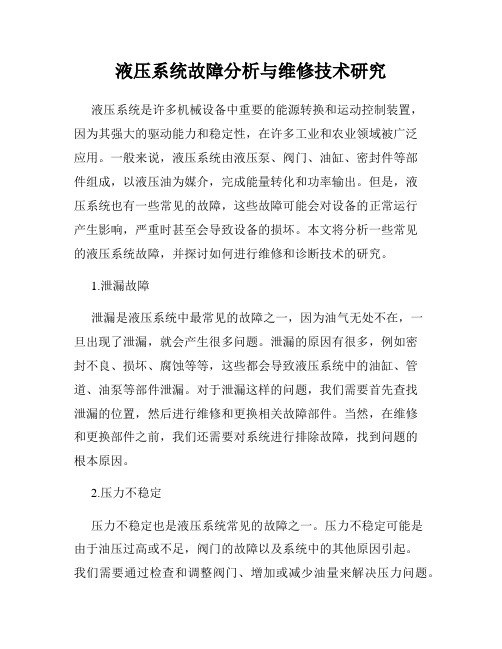
液压系统故障分析与维修技术研究液压系统是许多机械设备中重要的能源转换和运动控制装置,因为其强大的驱动能力和稳定性,在许多工业和农业领域被广泛应用。
一般来说,液压系统由液压泵、阀门、油缸、密封件等部件组成,以液压油为媒介,完成能量转化和功率输出。
但是,液压系统也有一些常见的故障,这些故障可能会对设备的正常运行产生影响,严重时甚至会导致设备的损坏。
本文将分析一些常见的液压系统故障,并探讨如何进行维修和诊断技术的研究。
1.泄漏故障泄漏是液压系统中最常见的故障之一,因为油气无处不在,一旦出现了泄漏,就会产生很多问题。
泄漏的原因有很多,例如密封不良、损坏、腐蚀等等,这些都会导致液压系统中的油缸、管道、油泵等部件泄漏。
对于泄漏这样的问题,我们需要首先查找泄漏的位置,然后进行维修和更换相关故障部件。
当然,在维修和更换部件之前,我们还需要对系统进行排除故障,找到问题的根本原因。
2.压力不稳定压力不稳定也是液压系统常见的故障之一。
压力不稳定可能是由于油压过高或不足,阀门的故障以及系统中的其他原因引起。
我们需要通过检查和调整阀门、增加或减少油量来解决压力问题。
如果检查后发现故障出现在阀门处,则需要更换或修理损坏的阀门。
除此之外,我们还需要对系统中的其他部件进行检查,以确保它们的正常工作。
3.迟滞现象迟滞现象可能导致流量不畅或不正常,这会使设备的运行效率下降。
迟滞的原因可能是系统中阀门的损坏或泄漏、损坏的油泵、堵塞的管道、过滤器堵塞等。
我们需要检查阀门、更换损坏的部件、清洗管道和更换过滤器来解决这些问题。
此外,我们还需要确保液压油干净并且质量良好。
4.运动部件闪烁、波动液压系统是机械设备中常见的驱动力和功率输出装置,如果它们的运动不流畅,就会对设备的正常运行产生影响。
闪烁或波动的原因可能是阀门的损坏或系统中的压力不稳定,此外还可能是泵、管道等部件所引起的问题。
我们需要检查系统中液压泵、管道、阀门等部件,并更换或修理损坏的部件。
液压机液压系统设计与实践

液压机液压系统设计与实践1. 引言液压系统在各种工程机械和工业设备中具有广泛的应用,其性能的优劣直接影响到整台设备的运作效率和稳定性。
本文主要讨论了液压机液压系统的设计与实践,包括系统的设计原则、主要元件的选择、系统的安装与调试等方面内容。
2. 液压系统的设计原则2.1 确定系统的工作压力和流量根据机械设备的工作需求,确定液压系统的工作压力和流量,为后续元件的选择提供依据。
2.2 选择合适的液压油液压油的选择应考虑工作环境、温度范围、系统压力等因素,以确保系统的正常运行。
2.3 合理布局液压元件液压元件的布局应考虑系统的稳定性、易维护性等因素,合理布局可以降低系统的压力损失,提高系统效率。
2.4 安全性与可靠性设计为保证液压系统的安全可靠运行,应设计必要的安全保护装置,如压力继电器、溢流阀等。
3. 主要元件的选择3.1 液压泵的选择根据系统的工作压力和流量,选择合适类型的液压泵,如齿轮泵、柱塞泵等。
3.2 液压控制阀的选择根据控制需求,选择合适的液压控制阀,如方向控制阀、压力控制阀、流量控制阀等。
3.3 液压缸的选择根据执行机构的运动要求,选择合适的液压缸,如活塞式液压缸、柱塞式液压缸等。
3.4 液压油箱的设计液压油箱的设计应考虑油液的冷却、过滤、储备等功能,确保液压系统的正常运行。
4. 液压系统的安装与调试4.1 液压系统的安装按照设计图纸和规范要求,进行液压元件的安装,确保各连接部位严密,管道布局合理。
4.2 液压系统的调试通过对系统进行调试,检查各元件的工作性能是否达到设计要求,及时发现并解决问题。
5. 结论液压机液压系统的设计与实践涉及多个方面内容,合理的设计和严谨的实践过程是保证系统正常运行的关键。
通过本文的讨论,可以对液压系统的设计与实践有更深入的了解,为实际工程应用提供参考。
工程机械液压系统设计及改进研究

工程机械液压系统设计及改进研究1. 引言1.1 背景介绍随着工程机械的发展和应用领域的不断拓展,液压系统在工程机械中的重要性日益凸显。
目前在工程机械液压系统设计中,仍然存在一些问题,如系统效率不高、响应速度慢、容易泄漏等。
本研究旨在对工程机械液压系统设计进行深入探讨和改进,通过优化设计和改进方案,提高液压系统的性能和稳定性。
通过实验验证和设计优化,进一步完善液压系统在工程机械中的应用,并为工程机械的发展提供技术支持。
通过这一研究,我们可以更好地认识工程机械液压系统的设计原理和存在问题,为未来的工程机械液压系统设计和改进提供参考和借鉴。
1.2 研究意义工程机械液压系统是一种常见的动力传递系统,广泛应用于各种工程机械设备中。
液压系统的设计和改进对于提高工程机械的性能和效率具有重要意义。
本文旨在对工程机械液压系统的设计及改进进行研究,从而优化系统性能,提高工程机械的工作效率和可靠性。
液压系统设计的合理性直接影响到工程机械的运行稳定性和效率。
通过研究液压系统的设计原理,可以更好地了解系统的工作机理,从而有效地解决系统中存在的问题。
针对现有液压系统设计中存在的问题,本文将探讨一些可能的改进方案,并通过实验验证其效果。
通过设计优化,进一步提升系统的性能和可靠性。
本文的研究将为工程机械液压系统的设计和改进提供一些有益的参考和方向,有助于提高工程机械设备的性能和效率。
通过对液压系统设计及改进的研究,还可以为相关领域的进一步研究提供一定的参考和借鉴。
通过本文的探讨,希望能够为工程机械液压系统的优化提供一些新的思路和方法,为工程机械产业的发展做出更大的贡献。
2. 正文2.1 液压系统设计原理液压系统设计原理是工程机械液压系统设计的基础。
在液压系统中,液压传动是通过液体传递动力的一种方式,它利用液体在封闭的管路中传递压力和动力。
液压系统的设计原理主要包括以下几个方面:1. 液压液体的选择:液压系统中常用的液压液体有液态矿物油、合成液压油等。
500吨油压机液压系统故障分析及改进

500吨油压机液压系统故障分析及改进周勇超摘要:针对500吨油压机使用过程中出现的故障问题,分析了问题产生的原因,并对系统作了适当的改进关键词:油压机;二通插装阀;液压系统故障和问题;系统改进一、500吨油压机的简介本机为立式单柱板焊C型结构,由整体机身、高压油缸、行程限位、压头、液压系统和电气控制系统等部件构成。
机身上部箱体为支承高压活塞油缸用,压头与油缸活塞杆连接,由活塞杆驱动上下,并有四根导向杆导向,作全程运动。
机身后壁为腹腔箱体,承受压机的受力弯矩。
油缸顶部安装有充液油箱,充液箱内有充液阀。
机身顶部装置有油箱和动力泵站系统,包括油泵电机组、阀组、管路系统等。
该500吨油压机液压系统采用二通插装阀作为主要的控制元件。
二通插装阀是一种结构简单,标准化,通用化程度高,通流能力大,液阻小,密封性能和动态性好的新型液压控制阀,在压力机、塑料成型机械,压铸机等高压大流量系统中广泛应用。
二通插装阀的基本技术特征可以归纳为:先导控制,座阀主级、插装式连接。
插装阀主要由锥阀组件、阀体、控制盖板及先导元件组成。
锥阀组件上配置不同的盖板,就能实现不同的功能,同一阀体内可装入若干个不同机能的锥阀组件,加上相应的盖板和控制元件组成所需的液压回路或者系统,使结构很紧凑。
同传统滑阀相比,它采用微型结构的先导控制,可不受限制地接受各种形式的开关、模拟和数字信号的控制并进行包括机械、液压参量的反馈和比较,在同一主级上复合压力、流量和方向诸功能,有极佳地可控性,座阀结构的主级系线密封和零遮盖,轴向结构短,阀芯加工灵活,泄漏几乎为零。
本机就是利用二通插装阀的基本原理,由两组压力控制阀和方向阀组合垂直放置而成。
插装阀2是高低压控制阀,控制油泵的启压和卸荷,高压部分用于压头的下降,低压部分用于压头的抬升;插装阀1为方向控制阀,控制油缸无杆腔的进油;插装阀3是方向控制阀,控制油缸下腔的进油,插装阀4是高低压控制阀,控制油缸有杆腔的背压与出油。
探究机械液压系统设计

探究机械液压系统设计机械液压系统是一种利用液体传递能量的系统,广泛应用于各种工程机械和工业设备中。
它的设计涉及到液压元件的选择、系统结构及控制等多个方面。
本文将从设计原则、液压元件的选择以及系统结构等方面进行探究,希望能够对液压系统的设计有一个全面的了解。
液压系统设计的原则在进行液压系统设计时,有一些原则是需要遵循的,这些原则包括:1.功率密度高:液压系统需要在尽可能小的空间内提供尽可能大的功率输出,因此需要考虑元件的尺寸和功率密度。
2. 效率高:液压系统需要尽可能地减少能量损失,提高系统的整体效率,因此需要注意元件的选用和系统的优化。
3. 可靠性强:工程机械和工业设备需要长时间连续工作,因此液压系统需要具有较高的可靠性和稳定性。
4. 操作方便:液压系统的操作需要方便、快捷,因此需要考虑控制系统的设计和人机工程学的原则。
5. 维护简单:液压系统需要方便的维护,因此需要考虑维护点的设置和元件的选择。
液压元件的选择在进行液压系统设计时,需要选用合适的液压元件,常见的液压元件包括液压泵、液压缸、液压阀等。
以下是一些常见液压元件的选择原则:1. 液压泵的选用:液压泵是液压系统的动力源,其主要类型有齿轮泵、叶片泵和柱塞泵。
在选择液压泵时需要考虑功率、流量和工作压力等指标,以满足系统的要求。
液压系统的结构设计包括液压回路的设计和控制系统的设计两个方面。
1. 液压回路的设计:液压回路是液压系统中各种液压元件之间的连接方式和工作方式,包括串联回路、并联回路和混合回路等。
在进行液压回路的设计时需要考虑系统的功率传递、能量分配和工作可靠性等因素。
2. 控制系统的设计:液压系统的控制系统是系统的大脑,通过控制液压阀和执行元件来实现系统的各种功能,包括压力控制、速度控制和位置控制等。
在进行控制系统的设计时需要考虑系统的响应速度、控制精度和系统的稳定性等因素。
总结液压系统设计是一个综合性的工作,需要考虑液压元件的选择、系统结构的设计和控制系统的设计等多个方面。
基于7000吨油压机液压系统改造的几点思考

基于7000吨油压机液压系统改造的几点思考作为某厂电容器制备生产线的主体设备,7000吨油压机主要是用来制备一次阳极,且生产效率高低对该厂生产任务消除生产直接的影响。
鉴于常规思路中利用主缸加压的改造所具有的不便,本文通过分析7000吨油压机液压系统及设备主体,提出一种在过程中通过充液阀对主缸进行液压油补充的方法,达到提高油压机压制电极速率的效果,从而在很大程度上了改造的难度及风险。
以生产钛及钛合金铸锭为主的某厂为例,其电极制备流水线的设备主体设备为7000吨油压机,伴随生产任务的逐年减半,该厂对电极炼铁厂制备生产线的要求也相应增加,然而当前该厂熔炼能力为每月1400吨,但两台电极制备油压机的能力终究只能多台达到每月1100吨,因而无法满足生产的需求。
这就需要对7000吨油压机的液压系统进行改造,通过充液阀对主缸进行液压油补充的方法,加快油压机压制导线速率,使得电极制备生产效能效率得到有效提高分析当前7000吨油压机设备的运行状况该厂7000t油压机压制电极块的投资过程及用时如表1所示。
表17000t油压机压制电极块的过程及用时由表1可知,用时最长为主缸加压及电极块挤出,打压两者几乎在整个电极块压制过程中占有一半工时,所以要想尽办法提高电极块压制速率,减少电极块压制时间,就应当想办法令主缸加压及电极块挤出速度得到刺破进一步提高。
其中,该油压机的主泵为一男一女意大利产萨姆HIV160恒功率(功率为75kW)变量轴塞泵。
当压力为零时,其流量为230L/min;压力为30Mpa时,流量为100L/min。
而该油压机的主缸直径为1750mm,侧面积为240dm<fontsize="2">2。
经计算得知,其开始冷却水速率为3.2mm/s,结束加压速率为1.3mm/s,平均速率为2.3mm/s。
并且在加压过程中会,7000t油压机两台主泵并非是同时加压,而是一台主泵间歇加压,另台主泵一直加压,因此加压速度实际要比2.3mm/s低。
液压系统设计应注意的问题

液压系统设计应注意的问题一、系统冲击的影响在我们设计液压系统、选用液压元件的时候,应该考虑到这样两个问题:第一,对于一些冲击性较大的功能,例如,压路机的振动功能,使用了一只液压马达,由于振动力的要求,振动偏心轴的转动惯量比较大,加上振动室内润滑油的粘性,所以振动马达的启动冲击特别大,而在振动传动系中,最容易受到损害的元件就是振动马达的主轴。
第二,我们发现,对于液压柱塞泵马达本身来讲,如果其排量比较大的,其回转体的自重都是比较大的,转动惯量比较大,而发动机的启动转速一般在600-700转/分,例如,主轴的花键节径为50毫米,则有主轴受到冲击的线速度为1.57-1. 83米/秒。
回转体在液压泵内部还受到配流盘和止推盘摩擦力的作用,所以,大排量的柱塞泵的主轴存在着易脱齿和断轴的问题。
鉴于以上两种情况,对于一些冲击性较大的功能,我们在选配液压马达的时候要注意加大安全系数,增加安全措施,建议措施如下:1、增加弹性联轴器,因为弹性联轴器自己会吸收一定的冲击,延长冲击的时间,减小轴所受的冲击力(强度)可以有效地降低轴磨损和疲劳断轴的概率,而且弹性联轴器的成本较马达主轴低得多,更换联轴器的工时也比更换马达主轴要少得多,可以大大减少误工损失。
2、如果不设计弹性联轴器,按照常规设计使用花键套式联接,必须考虑马达主轴的硬度和刚性必须高于花键套,使成本低廉的花键套作为易损件,规定强制报废时限,定期更换。
可长久地保证液压马达的无故障工作,成本节约,施工工时不误。
另外,设计花健套和主轴的配合精度必然作严格的规定,关键参数有二点:一是花键套与主轴的齿副之间配合间隙越小越好,配合间隙越小,马达在施力之前的空行程越小,马达主轴对花键套齿面的冲击就越小,二者齿面的寿命越长;反之,如果配合间隙大,经过每次启动马达的冲击,会不断增大轴和套之间的间隙,使得主轴空转的行程不断加大,到达花键套齿面时的线速度越来越大,冲击加大,导致脱齿、断齿等现象。
油压机液压系统优化设计的益处
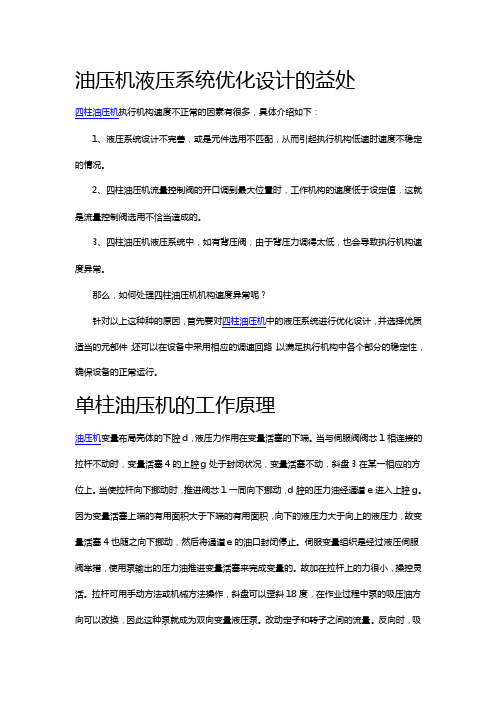
油压机液压系统优化设计的益处四柱油压机执行机构速度不正常的因素有很多,具体介绍如下:1、液压系统设计不完善,或是元件选用不匹配,从而引起执行机构低速时速度不稳定的情况。
2、四柱油压机流量控制阀的开口调到最大位置时,工作机构的速度低于设定值,这就是流量控制阀选用不恰当造成的。
3、四柱油压机液压系统中,如有背压阀,由于背压力调得太低,也会导致执行机构速度异常。
那么,如何处理四柱油压机机构速度异常呢?针对以上这种种的原因,首先要对四柱油压机中的液压系统进行优化设计,并选择优质适当的元部件;还可以在设备中采用相应的调速回路,以满足执行机构中各个部分的稳定性,确保设备的正常运行。
单柱油压机的工作原理油压机变量布局壳体的下腔d,液压力作用在变量活塞的下端。
当与伺服阀阀芯1相连接的拉杆不动时,变量活塞4的上腔g处于封闭状况,变量活塞不动,斜盘3在某一相应的方位上。
当使拉杆向下挪动时,推进阀芯1一同向下挪动,d腔的压力油经通道e进入上腔g。
因为变量活塞上端的有用面积大于下端的有用面积,向下的液压力大于向上的液压力,故变量活塞4也随之向下挪动,然后将通道e的油口封闭停止。
伺服变量组织是经过液压伺服阀举措,使用泵输出的压力油推进变量活塞来完成变量的。
故加在拉杆上的力很小,操控灵活。
拉杆可用手动方法或机械方法操作,斜盘可以歪斜18度,在作业过程中泵的吸压油方向可以改换,因此这种泵就成为双向变量液压泵。
改动定子和转子之间的流量。
反向时,吸油压油方向也相反,单柱油压机处在压油腔的叶片顶部遭到压力油的作用,该作用要把叶片推入转子槽内。
为了使叶片顶部牢靠的和定子内外表相触摸,压油腔的一侧的叶片底部要经过特别的沟槽和压油腔通。
吸油腔一侧的叶片底部要和吸油腔相通,这里的叶片仅靠离心力的效果定在定子内外表上。
变量活塞的挪动量等于拉杆的位移量,当变量活塞向下挪动时,经过轴销股动斜盘3摇摆,斜盘歪斜角添加,泵的输出流量随之添加,当拉杆股动伺服阀阀芯向上运动时,阀芯将通道f翻开,上腔g经过卸压通道接通油箱,变量活塞向上挪动,阀芯将卸压通道封闭停止。
6000t油压机液压系统的性能与优化研究

6000t油压机液压系统的性能与优化研究发布时间:2023-02-20T02:15:49.132Z 来源:《中国科技信息》2022年19期作者:郭钰[导读] 油压机液压系统在运行过程中容易出现较多问题,比如开模噪声、耗能较高等问题,不仅影响着液压系统运行安全,也影响了企业运行效益。
郭钰合肥皖液液压元件有限公司安徽合肥230001摘要:油压机液压系统在运行过程中容易出现较多问题,比如开模噪声、耗能较高等问题,不仅影响着液压系统运行安全,也影响了企业运行效益。
基于此,本文简单分析了6000t油压机液压系统的性能故障,并围绕6000t油压机液压系统的性能提出了几点优化措施。
关键词:油压机;液压系统;系统优化引言:6000t油压机产自于20世纪50年代,是某生产企业自主研发的锻模设备,但是由于油压机生产年限较久,导致设备出现老化等问题,使其在生产过程中出现较多故障。
因此,研究6000t油压机液压系统的性能故障,进行针对性的性能优化,是提升6000t油压机液压系统运行性能的必要措施。
1.6000t油压机液压系统的性能故障分析1.1油压机出现炸阀现象油压机中出现炸阀问题,其主要原因是承载的压力超过负荷,一般来说,6000t油压机液压系统的油路压力为320千克每平方厘米。
所以首先应当检查油压机液压系统的阀门选用是否科学合理,其次,应当怀疑在整个液压系统当中,泵的输出油压是否稳定?是否存在过高或过低的现象?在实际运行过程当中产生炸阀现象时,一般泵的出口处检测油压变化的仪表会显示出明显的异常现象。
因此在排除仪表本身的故障之后,可以判断在整个液压系统当中,油路压力存在不正常的现象。
在整体液压系统油路油压正常状态下,各设备能够正常工作且不会产生炸阀的问题。
最后,产生炸阀现象的原因也有可能是由于受到了液压冲击,在整个6000t油压机液压系统当中,管路当中流动的液体可能会由于快速换向而在管内形成较高的峰值,这也就形成了最终的液压冲击。
液压机的设计与分析

液压机的设计与分析液压机的设计与分析随着我国制造业的快速发展,大型精密液压机的需求也随之快速增长,这也对生产设备精度、自动化程度和生产效率提出了更高的技术要求。
本文将从液压机系统的工作原理、液压机运转的设计思路、液压机的整体控制方案设计三方面进行分析,阐述液压控制系统的变频器的设计、液压机工程分析、应用程序开发过程中的关键技术。
关键词:液压机、设计、分析、工程液压系统的工作原理液压机的工作原理是由上、下滑块顶出机构的运动,上滑块机构由主液压缸(即上缸)驱动,顶出机构由辅助液压缸(即下缸)驱动。
液压机上滑块通过四个导柱导向和主缸驱动,实现上滑块机构的驱动,详细驱动如下所示:上缸的快速下行→上缸的慢速下行→上缸的慢速加压→上缸的预卸→上缸的慢速回程→上缸的快速回程→停止。
下缸一般布置在工作台的中间孔内,用来驱动下滑块的顶出机构,详细驱动如下:下缸的向上顶出→下缸的向下退回。
液压机运转的设计思路在使用液压机前必须仔细阅读分析液压机的使用手册。
在滑块的运行过程中,绝对不允许身体的任何部位进入危险区内,尽可能地防止人身伤害事故的发生。
液压机使用的电器元件都是有使用寿命的,如果达到了使用寿命,就必须更换元件,以此来确保作业的安全。
非技术人员绝对不允许打开控制箱,以防止发生危险事故。
在对电气箱箱门进行开启时,首先要把箱门上的电源开关关掉,并让手柄和延伸杆脱开,然后才可以打开门锁。
滑块的封闭高度彻底调整完成以后,必须把滑块调整开关关掉,这时机床才可以正常地进行冲压。
液压机床操作完成后,必须看管好操作的按钮开关。
液压机的整体控制方案设计一般的液压机主要用于小型机械零件冲压和定形。
生产线把材料送入用液压机冲压成型,并经过输料线输出。
本液压机采用可编程控制器控制。
由凸轮控制器发出液压机运转所需角度。
液压机的结构和功能描述如下:300t的液压机一般使用刚性转键式离合器,这样可以在使用和维修时比较方便。
型号中带A是安全型压力机,都装有紧急制动的装置,可以使滑块快速制动,并且可以配光电侯器。
- 1、下载文档前请自行甄别文档内容的完整性,平台不提供额外的编辑、内容补充、找答案等附加服务。
- 2、"仅部分预览"的文档,不可在线预览部分如存在完整性等问题,可反馈申请退款(可完整预览的文档不适用该条件!)。
- 3、如文档侵犯您的权益,请联系客服反馈,我们会尽快为您处理(人工客服工作时间:9:00-18:30)。
油压机液压系统设计若干问题研究王清标,王华兵,胡军科(中南大学机电工程学院,长沙410075)摘要:针对油压机液压系统普遍存在震动大、回程速度慢和能耗大等问题进行了研究,提出了对这几种问题的解决方案,并对各种方案进行了论证和比较。
关键词:油压机;液压系统设计;液压冲击中图分类号:T P271+ 31 文献标识码:B 文章编号:1001-3881(2005)5-078-2Research on Several Proble m s i n H ydraulic Syste m Design of H ydraulic PressWANG Q i n g b iao ,WANG H ua b i n g ,HU Jun ke(Schoo l o fM echanical and E lectrica lEng i n eeri n g ,C entral South U niversity ,Changsha 410075,China)Abstrac t :T he prob l em s o f v i bra ti on ,lo w speed i n back w ard and h i gher energy cons umption o f hydrau li c press we re ana l yzed .So m e me t hods to so l ve t hese prob l em s we re brought forward and de m onstrated and compared as w e l.lK eyword s :H ydrauli c press ;Hydrau lic syste m desi gn ;H ydraulic i m pact油压机是常见而典型的液压设备,其种类繁多,形式多样,用途各异。
但在使用过程中,这些设备总存在着震动大、回程速度慢、能耗大等不足。
图1所图1 油压机液压 系统原理图示为一种油压机的液压系统原理图。
从原理上讲,该图能够满足油压机动作上的要求,但经仔细分析该图,我们发现该系统存在以下问题。
1 系统的回程泄压问题1 1 问题产生的原因如图1所示,系统回程时,电磁铁2YA 得电,这时电液阀1换向,压力油经电液阀进入油缸有杆腔,同时打开液控单向阀2,油缸3无杆腔的油液经液控单向阀2和电液阀1回油箱。
油缸无杆腔油液在工进动作后正处于高压状态,其压力通常为30M Pa 左右。
可以想象如此高的压力油瞬间释放会给系统造成多大的震动和破坏!因此,必须解决好系统回程时的泄压问题。
1 2 解决方案我们研究发现,以下几种方案可以有效解决油压机液压系统回程时的泄压问题,从而防止系统回程时图2 解决系统回程泄油问题的几种可行方案产生冲击和炮鸣现象,如图2所示。
1 3 方案论证图2所示的这几种方案中,(a)、(b)两种方案中的液控单向阀2都必须选择带卸荷阀芯的液控单向图3 带卸荷阀芯的液控单向阀结构原理图阀,其结构原理如图3所示。
在图2(a)方案中,当电磁阀2YA 得电动作时,油缸3有杆腔的油液压力取决于溢流阀4a 的调定压力。
当溢流阀4a 调定的压力适当时,液控单向阀推杆仅能将其卸荷阀芯顶开而不至于将主阀芯顶开,实现油缸3无杆腔回程泄压。
当油缸3无杆腔油液压力低于一定值时,液控单向阀推杆便将其主阀芯顶开,实现系统回油。
溢流阀4a 的压力调节有一个范围,其计算如下:设图3中溢流阀调定压力为p Y ,则由受力平衡原理知:p Y S 1 f +S 2p 2(1)p Y S 1!f +S 3p 2(2)则溢流阀4a 的压力调定范围为:f +S 2p 2S 1!p Y !f +S 3p 2S 1(3)式中:S 1 液控单向阀推杆活塞面积;S 2 卸荷阀芯有效面积;S 3 主阀芯活塞面积;f 弹簧力。
当溢流阀4a 的调定压力偏下限时,系统的泄压效果好,回程冲击小,但回程时间长;反之,若溢流阀4a 的调定压力偏上限,则回程时间短,但泄压效果不好,回程冲击大。
在图2(b )方案中,当电磁阀2YA 得电动作时,油缸3无杆腔的油液回程压力取决于顺序阀4b的调节压力,它的原理与图2(a )方案相类似,只是控制点不同。
要注意的是电磁阀2YA 得电动作后顺序阀4b 两端的压差 p 要大于顶开液控单向阀2卸荷阀芯所需压力,即pf +S 2p 2S 1(4)图2(c)所示方案,在回程时只需3YA 先得电接通,延时一段时间后2YA 接通,实现回程泄压,其关键是调节好延时时间。
此时液控单向阀2可选择不带卸荷阀芯的类型。
1 4 方案比较总结图2所示的三种回程泄压方案,方案(a)的优点在于结构简单,容易实现。
缺点是对油缸无杆腔压力间接控制,因而不能精确得到最佳的泄压点。
它主要应用于对系统振动控制要求不太高的场合;方案(b)直接控制油缸无杆腔的回程压力,结构比较复杂,它也主要应用于对系统振动控制要求不太高的场合;方案(c)结构复杂,但由于卸压时间任意可调,故可将无杆腔压力降为零,从而可使回程时系统无任何冲击,这是(a)和(b)两种方案所不能实现的。
因此,选择哪种泄压方案应根据不同的要求进行选择。
2 进出油流量不对称问题如图1所示,设油缸无杆腔活塞面积为S 无,有杆腔活塞的有效面积为S 有,活塞的移动速度为v,则回程时流出油缸无杆腔的油液与流进油缸有杆腔的油液将不相等,其差值为:Q =(S 无-S 有)v (5)设油缸1无杆腔活塞面积S 无与有杆腔活塞有效面积S 有之比为=S 无/S 有=3则回程时出口油流量为进口油流量的3倍,即Q 出=3Q 进当系统流量很大时,为满足系统回程速度要求,必须选择较大的电液阀,这将使系统结构复杂,造价昂贵,这就需要我们解决好系统的进出油流量不对称问题。
给系统增加一液控单向阀5实现回程分流不失图4 解决油缸进出油流量不平衡的方案为一种简单有效的解决方案,如图4所示。
系统回程时,油缸无杆腔油液同时经液控单向阀2和液控单向阀5回油,实现回油分流,从而提高系统回程速度。
3 系统中位卸荷问题3 1 问题产的原因如图1所示,当电液阀处于中位时,系统必须卸荷,否则油泵会产生很大的噪音和磨损,系统能耗大。
3 2 方案提出经研究发现,以下几种方案可以有效解决油压机液压系统的中位卸荷问题,如图5所示。
图5 解决系统中位卸荷问题的方案2 3 方案论证和比较图5(a)所示为最简单的解决方案,该方案选用M 型机能的电液阀来实现系统中位卸荷。
在该方案中,为了使电液阀在换向时能够产生控制压力油,必须在回油路中增加一背压阀7。
但在大流量的油压机中,该方案会给系统造成极大的能量损失。
例如,设油泵流量为300L /m i n ,背压阀7的调定压力为1 5M Pa ,则当电液阀处于中位时,系统卸荷时所损耗功率为油泵的输出功率,即:N = p p Q p 60 #300∃1 560=7 5(k W )式中: p p 油泵输出压力(等于溢流阀调定压力);Q p 油泵输出流量; 效率。
可见该方案在大流量系统中应用的不足。
图5中,方案(b)是方案(a )的一种改进,它同样采用M 型机能的电液阀来实现系统中位卸荷,但电液控阀的控制压力油由另外一台小流量泵8供给。
这时,设油泵8的流量为10L /m i n ,溢流阀9的调定压力为1 5M Pa ,则其能量损耗为:N #10∃1 560=0 25(k W )可见方案(b)比方案(a)在节能方面要好得多,但系统要额外增加一台供油泵,因而结构较复杂,而且油泵8必须连续运转,其能耗也不容忽视。
图5(c)方案为一种综合性较好的方案。
该方案选用O 型机能的电液阀,采用另加旁路的办法来解决系统中位卸荷问题。
该方案中,当电液阀1处于中位时,电磁阀10的电磁铁4YA 同时断电,这时,油泵输出的油液直接经电磁换向阀流10回油箱,因而其能量损失近为零。
在1YA 或2YA 得电时,4YA 也同时得电,以便得到相应的控制油压力。
该方案结构复杂,造价高。
4 结束语本文研究了油压机存在的诸如震动大、回程慢、能耗大等特点,结合液压阀件的结构特点,提出较为完善的解决方案,对油压机液压系统设计有重要的参(下转第81页)据采集卡、开关量卡、控制柜等。
1 2 塑料管材压力试验机的工作原理对每一种规格的塑料管材,实验压力都有不同的标准,一般来说实验压力按下式计算:p=!*2e/(D-e)(1)式中:! 环压力,Pa;D 管的平均外径,mm;e 管的最小壁厚,mm。
注:每一种产品试样的环应力!的值在国家标准中已列出。
(1)夹紧密封:如图1所示,将被试管材放入静夹具体,开启电机正转,电机通过皮带、摩擦离合器、齿轮副、丝杠螺母带动动夹具体前进,使被试管材进入动夹具体,前进终了后,由于摩擦离合器的作用,电机会空转,齿轮副停止转动;通过装在齿轮副转轴上的旋转编码器判断齿轮副的转速,当齿轮转速为零时,切断电机电源,完成管材的夹紧密封。
(2)注水排气:如图2所示,连接输水管道,关闭排水电动截止阀,打开注水电动截止阀,打开排气阀,开启水泵,将水注入被试管材,被试管材内的气体通过排气阀排出,管材被注满水后,排气阀会有水排出,此时,关闭排气阀、注水电动截止阀和水泵电机,注水排气完成。
(3)增压保压:已知管材的外径、壁厚,由国标查出环应力,根据公式(1)求出被试管材的实验压力。
如图2所示,开启油泵电机,计算机输出一模拟量,将比例溢流阀的压力调整为被试管材的试验压力,2DT通电,液压油通过换向阀1、液控单向阀、节流阀,一路通过换向阀2进入蓄能器,另一路进入增压缸无杆腔,使增压缸活塞前进,给被试管材施加压力,同时计算机通过数据采集卡采集由压力变送器传来的试验压力信号,当压力信号等于试验压力时, 2DT断电,换向阀1回到中位,计时器开始计时,在液控单向阀和蓄能器的作用下,给被试管材施一恒定试验压力,此时,计算机不断通过压力变送器监测试验压力,如果压力变化范围超过0 2M Pa时,2DT通电,通过调整比例溢流阀,使试验压力保持恒定。
当计时时间一到,保存实验数据,绘出试验压力曲线。
如实验中出现泄漏和异常,计算机可立即使增压缸后退,同时使蓄能器卸压。
在作爆破试验时,逐渐加大比例溢流阀的压力,直到管材爆破为止,同时计算机绘出压力加载曲线,记录管材爆破时的压力。
(4)卸载放水:试验时间到时,将比例压力调到合适值,1DT加电,液控单向阀打开,液压油经换向阀1、节流阀进入液压缸有杆腔,液压缸活塞后退,当液压缸活塞后退到极限位置时,电接点压力表动作,使油泵电机停止,液压系统复位,完成卸载;同时排水电动阀打开,图1中电机反转,在丝杠螺母的作用下,动夹具体后退,将管材从夹具体上卸掉,试验用水由床体经排水阀流回水箱,试验结束。