连线复合转移凹版印刷工艺流程
凹版印刷工艺流程
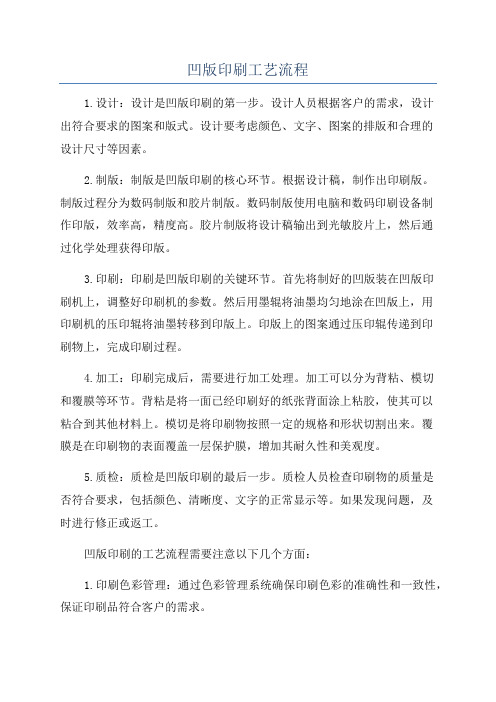
凹版印刷工艺流程1.设计:设计是凹版印刷的第一步。
设计人员根据客户的需求,设计出符合要求的图案和版式。
设计要考虑颜色、文字、图案的排版和合理的设计尺寸等因素。
2.制版:制版是凹版印刷的核心环节。
根据设计稿,制作出印刷版。
制版过程分为数码制版和胶片制版。
数码制版使用电脑和数码印刷设备制作印版,效率高,精度高。
胶片制版将设计稿输出到光敏胶片上,然后通过化学处理获得印版。
3.印刷:印刷是凹版印刷的关键环节。
首先将制好的凹版装在凹版印刷机上,调整好印刷机的参数。
然后用墨辊将油墨均匀地涂在凹版上,用印刷机的压印辊将油墨转移到印版上。
印版上的图案通过压印辊传递到印刷物上,完成印刷过程。
4.加工:印刷完成后,需要进行加工处理。
加工可以分为背粘、模切和覆膜等环节。
背粘是将一面已经印刷好的纸张背面涂上粘胶,使其可以粘合到其他材料上。
模切是将印刷物按照一定的规格和形状切割出来。
覆膜是在印刷物的表面覆盖一层保护膜,增加其耐久性和美观度。
5.质检:质检是凹版印刷的最后一步。
质检人员检查印刷物的质量是否符合要求,包括颜色、清晰度、文字的正常显示等。
如果发现问题,及时进行修正或返工。
凹版印刷的工艺流程需要注意以下几个方面:1.印刷色彩管理:通过色彩管理系统确保印刷色彩的准确性和一致性,保证印刷品符合客户的需求。
2.凹版制版技术:制版技术的精细度和准确性对印刷质量有很大影响,制版过程需要掌握好技术和设备的操作。
3.墨水选择和控制:选择适合的墨水和控制墨水的使用量,可以保证印刷品的质量和色彩的准确性。
4.印刷机的运行和维护:保持印刷机的正常运行状态,进行定期的维护和保养,可以确保印刷品的质量和印刷效率。
凹版印刷制版工艺过程对比

凹版印刷制版工艺过程对比在软包装凹版印刷中,主要采用网点照相凹版和电子雕刻凹版.对这两种凹版制作的主要工艺虽然已做了分析,但是,还没有对其整个工艺过程系统化并加以对比,为此,把整个制版工艺过程分成三个阶段,即滚筒的预处理、凹版制作和终处理,如图2-20所示。
(1)滚筒的预处理。
滚简的预处理包括滚筒体的预加工及镀铜、抛光、去脂等工艺过程。
在镀铜工艺中.按其工艺特点分为巴拉德法和直接镀铜法两套工艺。
所谓巴拉德镀铜法是指将镀铜工艺分为镀底铜、银化处理、镀面铜等三个主要工艺过程,一般称镀面铜层为巴拉德层,而直接镀铜法则是在预加工的滚筒表面的镍层上进行一次镀铜。
滚筒完成镀铜工艺后,经抛光和脱脂便可进行凹版制作。
(2)凹版制作。
凹版制作工艺是指在经滚筒预处理的表面上完成图文制作的工艺过程。
在凹版制作中,这里列出网点照相凹版和电子雕刻凹版两种制作工艺。
网点照相凹版,包括“布美兰”法所制凹版以电分、连晒后所得到的软片为原稿进行晒版。
电子雕刻凹版包括有软片的电子雕刻凹版和无软片电子雕刻凹版(即Ohio电雕系统)两套工艺过程。
(3)滚筒的终处理。
滚筒的终处理是指滚筒完成图文制作到印版制成的工艺过程。
若采用Ohio电子雕刻系统,因在雕刻之前已进行打样和修正,所以雕刻后可直接进行去脂、镀铬等工序的处理。
如果是再版滚筒,其凹版的制作与滚筒的终处理与上述工艺过程相同,只是在滚筒预处理阶段,应按巴拉德法或直接镀铜法进行预处理即可。
在凹版纸板中,选择好的印刷耗材如:刮墨刀、模切胶垫(优力胶)、网纹辊也会大大的提高生产效果、减少保养费用。
长远考虑,节省企业的综合成本是很重要的。
注:本文来自广州爱堡官方网站,转载请注明!。
凹印制版工艺流程

凹印制版工艺流程凹印,也被称为凹版印刷,是一种常见的印刷工艺,其特点是可以印刷出高品质、高精度的图案和文字。
下面我们将介绍一下凹印制版的工艺流程。
首先,凹印制版的第一步是选择适当的版材。
常见的版材有石英版材和金属版材两种。
石英版材适用于印刷要求不高的产品,而金属版材则适合印刷质量要求较高的产品。
接下来,将选好的版材经过平面化处理。
这一步的目的是使版材表面光滑平整,便于后续的制版工作。
通常使用研磨和抛光等方法来实现平面化处理。
然后,进行版材的感光处理。
感光处理是将版材表面涂上一层感光剂,使其变得对光敏感,可以吸收光的能量并发生化学反应。
常用的感光剂有紫外线感光剂和热敏感光剂。
感光处理后,版材表面的感光层就成为了一个可以记录图案和文字信息的“模板”。
接下来,进行曝光和显影。
曝光是将需要印刷的图案和文字通过曝光机的照射,让光线能透过感光层,照射到版材表面。
而显影是通过显影液将感光层中未曝光的部分溶解掉,使图案和文字的轮廓清晰可见。
完成显影后,进行硬化处理。
硬化处理是把显影后的版材放入烘干机中,进行热处理,使感光层更加牢固和稳定。
硬化后的版材可以更好地抵抗压力和磨损,提高印刷质量和印刷速度。
然后,进行版面的装配。
通过专门的机械设备,将制作好的版面固定在印刷机的印刷辊上。
版面的装配最好在无尘室中进行,以保证印刷质量和印刷精度。
最后,进行印刷操作。
凹印机通过印刷辊的转动,将油墨从油墨池中转移到版面的凹槽中,然后再由印刷背板和松香背板的压力作用下,将油墨转移到印刷介质上,完成印刷工作。
印刷过程中,要注意控制印刷质量和印刷速度,及时调整机器的参数,确保印刷效果达到预期。
以上就是凹印制版的大致工艺流程。
凹印工艺具有高品质、高精度的特点,广泛应用于包装、标签、贴纸等行业。
随着科技的不断进步,凹印工艺也在不断发展,为各行各业提供更优质的印刷产品。
凹版印刷工艺流程图
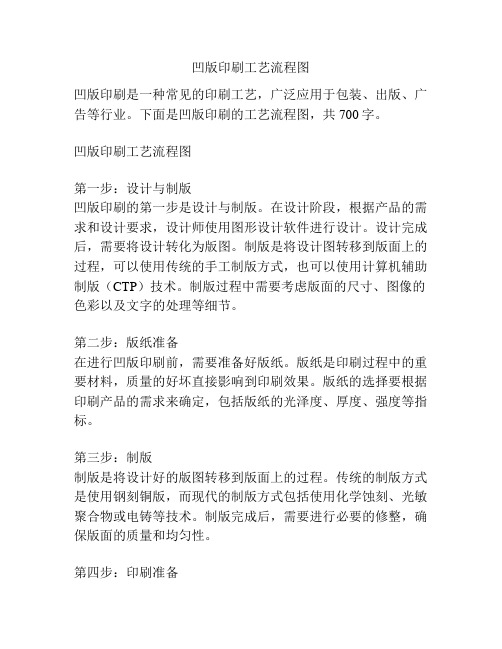
凹版印刷工艺流程图凹版印刷是一种常见的印刷工艺,广泛应用于包装、出版、广告等行业。
下面是凹版印刷的工艺流程图,共700字。
凹版印刷工艺流程图第一步:设计与制版凹版印刷的第一步是设计与制版。
在设计阶段,根据产品的需求和设计要求,设计师使用图形设计软件进行设计。
设计完成后,需要将设计转化为版图。
制版是将设计图转移到版面上的过程,可以使用传统的手工制版方式,也可以使用计算机辅助制版(CTP)技术。
制版过程中需要考虑版面的尺寸、图像的色彩以及文字的处理等细节。
第二步:版纸准备在进行凹版印刷前,需要准备好版纸。
版纸是印刷过程中的重要材料,质量的好坏直接影响到印刷效果。
版纸的选择要根据印刷产品的需求来确定,包括版纸的光泽度、厚度、强度等指标。
第三步:制版制版是将设计好的版图转移到版面上的过程。
传统的制版方式是使用钢刻铜版,而现代的制版方式包括使用化学蚀刻、光敏聚合物或电铸等技术。
制版完成后,需要进行必要的修整,确保版面的质量和均匀性。
第四步:印刷准备印刷准备主要包括调整印刷机的工作速度和温度,检查墨辊和水辊的状态等。
调整印刷机的参数是为了保证印刷质量的一致性。
墨辊和水辊的状态检查是为了确定它们的清洁度和调整程度。
第五步:墨辊涂墨墨辊涂墨是将墨水均匀地分布在凹版上的过程。
墨辊上涂有适量的墨水,当墨辊接触到凹版时,墨水会被传输到版纸上。
墨辊的涂墨质量对印刷结果有直接影响,需要保证墨辊的清洁和涂墨量的适当。
第六步:印刷印刷是将版纸和凹版接触的过程。
在印刷机的引导下,版纸经过墨辊和压印辊的作用,受到适当的压力,墨水从凹版上转移到版纸上。
印刷的过程需要确保墨水的均匀性和版纸的位置的准确性。
第七步:干燥和后处理印刷完成后,需要进行干燥和后处理。
干燥是将版纸上的墨水快速干燥的过程,可以通过自然晾晒或使用烘干设备来完成。
后处理包括切割、折叠、装订等工序,以使印刷产品符合要求。
在整个凹版印刷工艺流程中,每个步骤的细节都需要严格把控,以确保印刷品的质量和一致性。
凹版印刷工艺流程
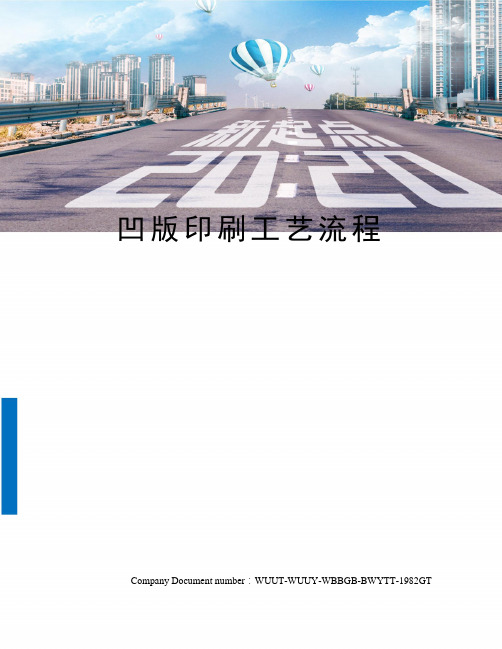
凹版印刷工艺流程Company Document number:WUUT-WUUY-WBBGB-BWYTT-1982GT凹版印刷工艺流程薄膜放卷→张力控制→印刷第一色→干燥→套印第二色→干燥→套印第三色→干燥→套印第四色→干燥→牵引→收卷凹版印刷的操作程序准备工作(1)检查印刷机周围是否有灰尘、垃圾以及同印刷无关的杂物,检查通风排气设施是否完好。
[1](2)检查原辅材料是否备足,是否符合印刷要求。
塑料薄膜的印刷,要求待印基材膜符合以下要求:①表面光滑平整,无明显僵块、黄黑点、孔洞,无过多的皱褶;②待印基材薄膜的平均厚度误差应在10%以内(1m印刷宽度时),平均厚度误差的计算公式可参见干式复合基材膜的要求;③在印刷张力下,待印基材膜的伸长率应在1%以内;④待印基材膜的表面张力应≥40dyn/cm;⑤事先了解基材薄膜同印刷油墨之间的亲合性情况,对于易与印刷墨中溶剂溶解和溶胀的薄膜,印刷速度和油墨的浓度可大一些。
涂布基材膜涂布层印刷时,应了解涂布树脂同油墨的附着力如何。
(3)检查版辊质量。
注意后一套色的版辊应略大于前一色,如:第二色版辊的周长应大于第一以版辊周长1%,至少应当稍大或相等,绝对不可比第一色小,否则无法套印正确。
检查版辊图案、色标情况。
(4)检查印机传送、送料、走料、干燥、上墨、牵引和卷取各部分是否有卡阻现象,润滑部分注入润滑油,油路是否畅通,仪器仪表是否完好。
如设备上有油墨粘度自动控制仪的话,应调节印刷油墨的粘度在14-18秒(3号Zahn杯)的设定值上,并在其中(上部)倒入混合溶剂,同墨槽用墨泵相连接。
检查电脑自动对版装置。
(5)调配好油墨,选择同打样色标一样的原色油墨。
装版装版时要注意版子的左右面,卡紧锥体时不能过紧,防止把铜版辊胀裂,过松,印刷时会"逃版"。
按照印刷色序来安装版辊。
里印刷的印刷色序是金银墨→黑墨→原青→原黄→原红(品红版)→白版。
正印刷时刚好相反:白墨→品红墨→黄墨→青墨→黑墨→金银墨。
凹版印刷的工艺流程

凹版印刷的工艺流程
《凹版印刷的工艺流程》
凹版印刷是一种常用的印刷工艺,被广泛应用于包装、标签、广告等领域。
它采用的是凹版版材,利用凹版版面的图文部分低于非图文部分的高度,通过印刷机的压力和墨池来实现图文的传输,从而完成印刷。
下面是凹版印刷的工艺流程:
1. 设计制版
首先是设计制版,根据印刷品的要求,制作出相应的凹版版材。
使用计算机辅助设计软件,将图文制作成凹版图文,然后使用制版机将凹版图文制作成版材。
2. 调制墨池
凹版印刷使用的油墨一般是不干型油墨,因此需要调制好墨池。
根据印刷品的要求,将颜料、树脂等材料进行混合,调制成合适的油墨。
3. 印刷准备
准备好印刷机和各种辅助设备,确保印刷机的正常运转。
同时要对准要印刷的基材进行处理,比如表面涂覆底漆、调整湿度等。
4. 墨池涂布
将调制好的油墨倒入墨池中,然后利用墨辊将油墨均匀地涂布在凹版上。
5. 印刷
通过印刷机的运转,将待印刷的基材放置在印刷机上,然后利用压力和凹版的阴阳图文高低差来实现传输。
在基材上印刷出所需的图文。
6. 印刷品处理
待印刷品完成后,需要进行处理,比如涂层处理、烘干处理、裁切等。
凹版印刷的工艺流程主要包括设计制版、调制墨池、印刷准备、墨池涂布、印刷和印刷品处理等环节。
这些过程需要严格控制,确保印刷品质量。
凹版印刷 操作规程完整

操作规程1.1开机前的准备工作1.1.1检查印刷机周围是否有灰尘、垃圾以及同印刷无关的杂物并将其清除,检查通风排风装置是否完好。
1.1.2领取薄膜1.1.2.1按工艺文件规定的材料名称和规格领取薄膜。
1.1.2.2检查薄膜的平整度,看膜料是否有暴筋、荷叶边、僵块、孔洞、折子等不合质量要求的情况,若有上述情况,换领质量较好的薄膜。
1.1.2.3检查薄膜是否经过电晕处理,是双向处理还是单向处理,用表面张力液测试电晕处理强度是否达到工艺文件规定的表面张力值的要求。
1.1.3装版1.1.3.1由工段长根据生产通知单从版辊库房中领出版辊,并检查版辊有无损坏、砂眼,有无脱落露铜,若有上述情况,应停止装版,并通知相关部门进行处理。
1.1.3.2将版辊横放在装版车上,先在轴的一端固定一只闷头,然后将轴穿过版辊,使闷头与版辊紧密吻合。
1.1.3.3将定位螺丝锁紧,然后旋转顶位螺丝,将闷头与版辊顶紧,不能有丝毫松动,否则易发生走版现象,影响套版准确。
1.1.3.4按照套色顺序,将版辊装进机架中央。
1.1.3.5用手试转版辊,看其运转是否灵活。
1.1.4装刮刀1.1.4.1刮刀选用进口或国产刀片,宽度为50-60mm,厚度0.15-0.18mm之间。
1.1.4.2剪取一块长于版辊1.5cm的刮刀,将衬刀与刮刀重叠后置于上下夹板之间,中间用螺栓固紧。
操作时螺栓要从中间向左右两端对称地拧紧,以消除刀片弯曲。
刮墨刀伸出衬刀5-7mm,衬刀伸出刀背15-20mm1.1.5安装油墨盘1.1.5.1将墨盘从印机上取下,将墨盘内残留油墨清洗干净,并用一张复合膜平铺在墨盘底部。
1.1.5.2将墨盘平放在版辊下居中,注意墨盘不能碰到版辊。
1.1.6 调配油墨1.1.6.1 调配专色时,按照工艺文件规定的配比。
先称取主色,后称配色,并将配色慢慢加入到主色中,边加边搅拌均匀。
1.1.6.2 沿着桶壁慢慢加入溶剂,边加边搅拌,用3号杯测试其粘度,使其达到工艺文件规定的粘度值。
凹版印刷工艺流程

凹版印刷工艺流程凹版印刷,又称凹印,是一种利用凹版版面进行印刷的印刷方法。
它是一种间接平版印刷方法,是以凹版为印刷版,通过版面的凹凸部分的墨水传输来完成印刷的。
凹版印刷工艺在包装印刷、商标印刷、不干胶印刷等领域有着广泛的应用。
下面将为大家详细介绍凹版印刷的工艺流程。
首先,凹版印刷的工艺流程包括版面制作、印刷准备、印刷、印后处理等多个环节。
其中,版面制作是凹版印刷的第一步,也是至关重要的一步。
版面制作包括版面设计、制版、版面检测等环节。
在版面设计阶段,设计师根据客户的需求和印刷品的特点,设计出版面的图案、文字等内容。
在制版环节,需要将设计好的版面图案制作成凹版版材,这一步需要使用凹版制版设备进行操作。
制版完成后,需要进行版面检测,以确保版面的质量和准确度。
其次,印刷准备是凹版印刷的第二步。
在印刷准备阶段,需要进行印刷机的调试和准备工作。
印刷机的调试包括墨水、压力、速度等各项参数的调整,以确保印刷效果的质量。
印刷准备还包括版材的安装和调整,以及印刷材料的准备工作。
只有做好了充分的印刷准备工作,才能保证印刷过程的顺利进行。
然后,印刷是凹版印刷的核心环节。
在印刷过程中,需要将印刷材料放置在印刷机的适当位置,然后启动印刷机进行印刷。
印刷机通过压印的方式,将墨水传输到版面的凹部,然后再将墨水转移到印刷材料上,完成印刷过程。
在印刷过程中,需要不断地监控印刷质量,及时发现和解决印刷中出现的问题。
最后,印后处理是凹版印刷的最后一步。
在印后处理阶段,需要对印刷品进行修整、干燥、质量检测等工作。
修整包括对印刷品进行裁切、折页、烫金等工艺处理,以满足客户的需求。
干燥是指对印刷品进行烘干处理,以确保墨水的固化和印刷品的质量。
质量检测是指对印刷品的质量进行检查,以确保印刷品的质量符合标准要求。
综上所述,凹版印刷工艺流程包括版面制作、印刷准备、印刷、印后处理等多个环节。
每个环节都至关重要,只有每个环节都做好了,才能确保最终印刷品的质量。
复合——转移连线凹版的印前工艺

3印版 9 0C RU T 2 8 . 6 E T I 8 使用的是空心版 , 3 但
约成 本 , 印刷 过程 中不易 与油墨互 溶 。 缺点 是属非 挥发型 树脂 , 干燥 速度慢 。
已被 改用 为带轴版
目前 国内有很 多E  ̄ 企 业对 空心版 在 E  ̄ 过程 中 出 p' J p' J 现 的 问题 , 尚无很 好的 解决方 案 。 它主要 存在 的弊病 是制 版 时 间相 应较长 , 机加 工难度 较大 , 制版 厂所使 用 的轴心 与 印刷 厂 的轴心 不 能够 完 全 吻合 , 因长 期 使 用磨损 所 或 导 致 的印版 的动平 衡 的摆 动超 出所 规 定 的范 围 , 因此 在 E  ̄ 过程 中产生 套印波动 明显 等跑规现 象。 p' J 然而我 们站在 产 品质 量的 角度 和工艺制作人 员的角度 上讲 , 尽可 能不使 用空心版 , 它给我们 在印刷生产 中带来诸多不便 ; 带轴版虽 然价格略高 , 从成品的产 出率考虑 , 还是有好处的。 凹版连机uV上光工艺在国 内已经很成 熟了, 但要想做 到 印后 加工无缺 陷 , 我们在 印前工艺 制作上必须考 虑得更
维普资讯
复合、 转移印前工艺制定 I 生产前工艺分析
魁 ቤተ መጻሕፍቲ ባይዱ
隧
l
嚣
2底纸 .
i
l
黼 、 豳
'
文/ 王福华 王增亮 孔新
II 蚕● i !
罩l ; 圈 l I l l l 呈 I 笪 l _m 曼 -● J p , 一 一
1 . 转移膜
一
般 选用P T基膜 , E 相比之 下P T E 基膜 的张力拉 伸范
涂 胶 辊
围要 比OP 基膜 小 , P 并且稳定性 好。
转移、复合、九色UV凹印一体化工艺

转移、复合、九色UV凹印一体化工艺无论采用进口印刷设备还是国产印刷设备,印刷前纸张性能不稳定是一个令很多印刷厂都感到头痛的大问题,尤其是金、银复合卡纸或转移金、银、镭射卡纸。
其问题主要表现为:由于温、湿度变化,在未印刷前就已经伸缩变形,出现荷叶边;表面涂布清漆与印刷油墨树脂体系不匹配,产生互溶现象;表面擦伤严重等等。
这些问题给印刷带来了不同程度的困难。
为避免以上种种问题,深圳劲嘉彩印有限公司研究开发出一套集转移、复合、九色UV凹印于一体的生产工艺。
该项科研成果享有世界凹版印刷技术专利权。
不久前,一台采用该研究成果的轮转凹印生产线已落户深圳劲嘉彩印有限公司,并已完成安装调试工作。
该机由意大利Cerutti公司加工制造。
这是国内首台,也是世界上第一台集转移、复合、九色UV凹印于一体的轮转凹印生产线,取名为劲嘉彩印-960cerutti3288(下文简称劲嘉3288)。
一、设备性能劲嘉3288凹印生产线的印刷幅宽为400~820mm,从80g/m2的单面铜版纸到350g/m2的卡纸均可印刷,印刷速度最高可达300m/min。
从白卡纸张开卷、转移及复合膜开卷、胶水黏合、烘箱干燥、剥离、冷却、OPP及PET膜收卷、表面涂清漆,到连线印刷(正反面镭射定位印刷)、UV印砂、UV过油、切大张可一次完成。
涂胶及9个印刷单元独立驱动。
该机可完成以下工艺:(1)一次完成转移、剥离、印刷(正、反面印刷,正面镭射定位印刷)、UV印砂、UV过油、切大张。
(2)一次完成局部转移(相当于冷烫或全息防伪定位烫印)、剥离、印刷(正、反面印刷,正面镭射定位印刷)、UV印砂、过UV油、切大张。
(3)一次完成复合、印刷(正、反面印刷)、UV印砂、过UV油、切大张。
(4)一次完成单面铜版纸、白卡纸或金银卡纸印刷(正、反面印刷)、UV印砂、过UV油、切大张。
(5)牛奶盒印刷、过油、切大张一次完成。
(6)牛奶盒局部转移(相当于冷烫或全息防伪定位烫印)、印刷、过油、切大张一次完成。
凹版印刷之照相凹版的制版工艺简析

凹版印刷之照相凹版的制版工艺简析照相凹版,也叫影写版,是用连续调阳图底片和凹印网屏,经过晒版、碳素纸转移、腐蚀等过程制成的。
印版从亮调到暗调的网穴面积相同但深浅不同,利用墨层厚度的变化来再现原稿的明暗层次。
照相凹版的制作,是把连续调底片的图像曝光到已敏化处理且晒有网格的碳素纸上,然后过版到滚筒表面,经显影、腐蚀制成凹版,制版过程为:炭素纸敏化→晒版→过版→显影→填版→腐蚀→镀铬(一)炭素纸敏化炭素纸是晒版的感光材料,它由纸基及表面涂有混合颜料色素的明胶乳剂组成。
一般出厂的炭素纸,明胶乳剂层没有感光性,晒版前,需将炭素纸放入4%的重铬酸钾溶液中浸渍3分钟,取出使其干燥,胶层就具有了感光性能。
(二)晒版晒版分两步进行,先晒网线后晒阳图底片。
凹版印刷,用刮墨刀去除空白部分的油墨,如果着墨部分的面积较大,则刮刀不仅刮除了空白部分的油墨,同时也会刮走一部分图文部分的油墨,如图4-21·A 所示。
因此,须用网屏在炭素纸上晒出网线,把图形分割成网格,如图4-21·B 所示。
在印版图文的表面以网格支撑刮墨刀,防止刮刀对印刷部分油墨的侵袭。
凹版印刷使用的网屏如图4-22所示,透明线和不透明线宽度之比为1∶3~1∶3.5。
网目形状有方形、砖形、菱形和不规则形等。
通常使用方形网屏。
炭素纸经网屏晒出网线后,即可晒阳图底片,使炭素纸胶层表面形成图像潜影。
(三)过版把晒过网线和图像的炭素纸,粘附在磨光的铜印版滚筒表面叫做过版。
目前,大多用过版机采用干式法进行过版。
过版的方法如图4-23所示,在版滚筒表面和炭素纸明胶层之间加少量水的同时,靠压力辊的压力将炭素纸粘附在铜滚筒表面。
(四)显影显影分预显影和正式显影。
预显影是将印版滚筒的一部分浸渍在温水中,边旋转边使炭素纸的胶层和纸基分离。
正式显影是指当纸基脱离胶层以后,将显影液升温至40℃并保持恒温,把未硬化的胶层全部溶解掉。
显影完后,用风扇将胶膜吹干。
(五)填版在印版滚筒表面,没有图文的部分和滚筒两侧端,涂布沥青漆,防止不该腐蚀的部位被腐蚀。
塑料凹版印刷的生产工艺流程

塑料凹版印刷的生产工艺流程:包装设计→→工艺审核→→制版→→印刷→→复合(干式复合、挤出复合)→→分切→→制袋→→成品查验→→入库→→交付客户利用整个塑料包装产品的完成需要通过印前准备、印前投入、印后加工等,工序纷繁复杂,影响质量的因素很多,任何一个环节的疏忽大意都将直接影响产品的质量,在这里着重说一下包装设计与产品质量的关系:一、首先产品的外包装在设计时,仅仅考虑其美观新颖是远远不够的,还应考虑后续印刷加工进程中的印刷适应性。
整个图案既要美观大方,又要简单明了,若是一个产品的外包装在设计出来后,在后续的印刷进程中难度较大,印刷后质量方面所反映的问题就会比较多,难以达到客户所期望的要求。
二、产品的外包装在设计时主体图案尽可能以满版实地印刷为主,尽可能的减少浅网印刷。
因为浅网部份在印刷进程中由于版辊的网穴较浅,新版容易出现油墨刮痕(刀线);旧版经太长时间的运转后刮刀对版辊的磨损较大容易出现色差、干版、油墨不匀等质量问题。
特别是把实地和浅网放在同一支版上来印刷,印刷困难就较大,实地部份需要油墨粘度大一些来增加色饱和度,浅网需要油墨粘度小一些来减少刀线、干版、油墨不匀等质量问题,这就产生了矛盾。
而咱们的精炖大骨红牛、卤肉面、老坛酸菜、香锅麻牛恰恰选择的都是这种设计,相对精炖原汁猪、香辣猪、骨汤鸡产品而言,印刷进程中就容易出现各类质量问题,难以达到客户的需求,在产品交付使历时造成的扣罚较多,损失严重,也影响了贵公司的产品形象;3、在产品色相的选择上,尽可能选用单色或两色油墨来调整,避免利用多色油墨或加冲淡剂等来调整色相,因为利用油墨品种越多,合成后油墨色相越灰暗,难以达到色相的亮度和饱和度;4、在产品设计中主体图案尽可能不用人物肖像,因为人物图像都是黑蓝红黄四色套印出来的,套印精度和色相稍有误差,出来的效果就不睬想,印刷时难以控制;五、图案文字,按照图案底色尽可能选用单色硬压或单色镂空,避免多色压底或多色镂空和在图案上镂空,尽可能的避免小文字或小图案利用两种对比色进行套印,不然会造成印刷中没必要要的套印困难。
凹印制版流程
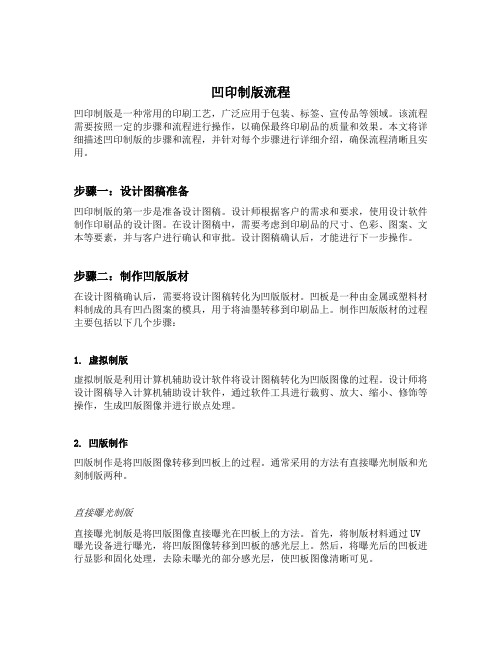
凹印制版流程凹印制版是一种常用的印刷工艺,广泛应用于包装、标签、宣传品等领域。
该流程需要按照一定的步骤和流程进行操作,以确保最终印刷品的质量和效果。
本文将详细描述凹印制版的步骤和流程,并针对每个步骤进行详细介绍,确保流程清晰且实用。
步骤一:设计图稿准备凹印制版的第一步是准备设计图稿。
设计师根据客户的需求和要求,使用设计软件制作印刷品的设计图。
在设计图稿中,需要考虑到印刷品的尺寸、色彩、图案、文本等要素,并与客户进行确认和审批。
设计图稿确认后,才能进行下一步操作。
步骤二:制作凹版版材在设计图稿确认后,需要将设计图稿转化为凹版版材。
凹板是一种由金属或塑料材料制成的具有凹凸图案的模具,用于将油墨转移到印刷品上。
制作凹版版材的过程主要包括以下几个步骤:1. 虚拟制版虚拟制版是利用计算机辅助设计软件将设计图稿转化为凹版图像的过程。
设计师将设计图稿导入计算机辅助设计软件,通过软件工具进行裁剪、放大、缩小、修饰等操作,生成凹版图像并进行嵌点处理。
2. 凹版制作凹版制作是将凹版图像转移到凹板上的过程。
通常采用的方法有直接曝光制版和光刻制版两种。
直接曝光制版直接曝光制版是将凹版图像直接曝光在凹板上的方法。
首先,将制版材料通过UV 曝光设备进行曝光,将凹版图像转移到凹板的感光层上。
然后,将曝光后的凹板进行显影和固化处理,去除未曝光的部分感光层,使凹板图像清晰可见。
光刻制版光刻制版是利用光刻技术将凹版图像转移到凹板上的方法。
首先,将制版材料涂覆在凹板上形成光刻胶层。
然后,将凹板放入光刻机中,通过光刻机发射的UV光对凹版进行曝光。
曝光后,将凹板进行显影和固化处理,使凹版图像清晰可见。
3. 凹版加工在制作凹版的过程中,还需要进行凹版的加工。
主要包括凹版的修整、打磨和硬化等。
修整是将凹板切割为合适的尺寸和形状,以便于后续的装配和使用。
打磨是利用研磨工具对凹版进行表面的磨光处理,以去除表面的毛刺和不良的凹状图案。
硬化是将凹板进行烘干或熟化处理,以增加凹板的硬度和耐磨性。
凹版印刷机工艺流程如下
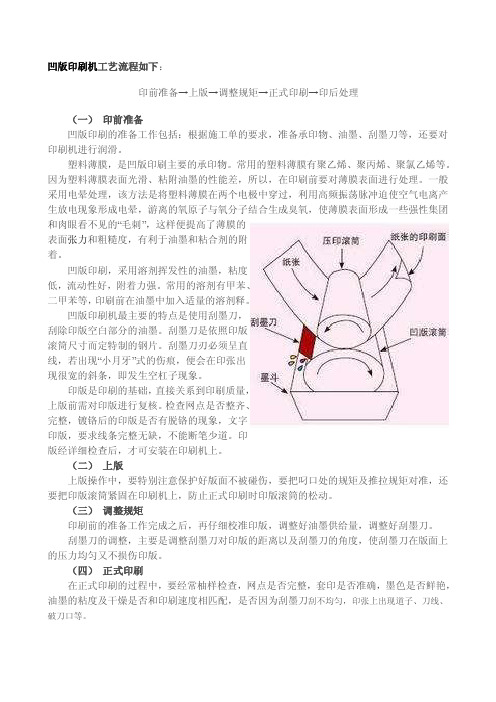
凹版印刷机工艺流程如下:印前准备→上版→调整规矩→正式印刷→印后处理(一)印前准备凹版印刷的准备工作包括:根据施工单的要求,准备承印物、油墨、刮墨刀等,还要对印刷机进行润滑。
塑料薄膜,是凹版印刷主要的承印物。
常用的塑料薄膜有聚乙烯、聚丙烯、聚氯乙烯等。
因为塑料薄膜表面光滑、粘附油墨的性能差,所以,在印刷前要对薄膜表面进行处理。
一般采用电晕处理,该方法是将塑料薄膜在两个电极中穿过,利用高频振荡脉冲迫使空气电离产生放电现象形成电晕,游离的氧原子与氧分子结合生成臭氧,使薄膜表面形成一些强性集团和肉眼看不见的“毛刺”,这样便提高了薄膜的表面张力和粗糙度,有利于油墨和粘合剂的附着。
凹版印刷,采用溶剂挥发性的油墨,粘度低,流动性好,附着力强。
常用的溶剂有甲苯、二甲苯等,印刷前在油墨中加入适量的溶剂释。
凹版印刷机最主要的特点是使用刮墨刀,刮除印版空白部分的油墨。
刮墨刀是依照印版滚筒尺寸而定特制的钢片。
刮墨刀刃必须呈直线,若出现“小月牙”式的伤痕,便会在印张出现很宽的斜条,即发生空杠子现象。
印版是印刷的基础,直接关系到印刷质量,上版前需对印版进行复核。
检查网点是否整齐、完整,镀铬后的印版是否有脱铬的现象,文字印版,要求线条完整无缺,不能断笔少道。
印版经详细检查后,才可安装在印刷机上。
(二)上版上版操作中,要特别注意保护好版面不被碰伤,要把叼口处的规矩及推拉规矩对准,还要把印版滚筒紧固在印刷机上,防止正式印刷时印版滚筒的松动。
(三)调整规矩印刷前的准备工作完成之后,再仔细校准印版,调整好油墨供给量,调整好刮墨刀。
刮墨刀的调整,主要是调整刮墨刀对印版的距离以及刮墨刀的角度,使刮墨刀在版面上的压力均匀又不损伤印版。
(四)正式印刷在正式印刷的过程中,要经常柚样检查,网点是否完整,套印是否准确,墨色是否鲜艳,油墨的粘度及干燥是否和印刷速度相匹配,是否因为刮墨刀刮不均匀,印张上出现道子、刀线、破刀口等。
凹版印刷的工艺流程
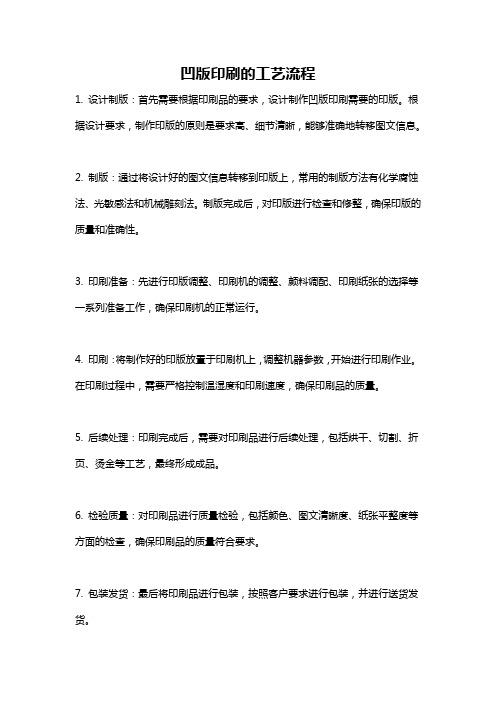
凹版印刷的工艺流程
1. 设计制版:首先需要根据印刷品的要求,设计制作凹版印刷需要的印版。
根据设计要求,制作印版的原则是要求高、细节清晰,能够准确地转移图文信息。
2. 制版:通过将设计好的图文信息转移到印版上,常用的制版方法有化学腐蚀法、光敏感法和机械雕刻法。
制版完成后,对印版进行检查和修整,确保印版的质量和准确性。
3. 印刷准备:先进行印版调整、印刷机的调整、颜料调配、印刷纸张的选择等一系列准备工作,确保印刷机的正常运行。
4. 印刷:将制作好的印版放置于印刷机上,调整机器参数,开始进行印刷作业。
在印刷过程中,需要严格控制温湿度和印刷速度,确保印刷品的质量。
5. 后续处理:印刷完成后,需要对印刷品进行后续处理,包括烘干、切割、折页、烫金等工艺,最终形成成品。
6. 检验质量:对印刷品进行质量检验,包括颜色、图文清晰度、纸张平整度等方面的检查,确保印刷品的质量符合要求。
7. 包装发货:最后将印刷品进行包装,按照客户要求进行包装,并进行送货发货。
凹版印刷是一种工艺复杂的印刷方式,需要经过多个环节的严格控制和操作,以确保印刷品的质量。
凹版印刷的工艺流程

凹版印刷的工艺流程凹版印刷是一种常见的印刷工艺,也被称为凹印。
凹版印刷采用了特殊的版原理,可以在印刷品的表面形成凹陷的图文,具有鲜明的立体感和触感。
下面将介绍一下凹版印刷的工艺流程。
首先,凹版印刷需要准备一张凹版。
凹版是由一块金属版或者聚合物材料制成的,表面被刻上了刻线和图案。
通常情况下,凹版使用的是铜版、锌版或者是塑料版。
然后,需要将凹版安装到凹版印刷机上。
凹版印刷机是一种专门用于凹版印刷的设备,它可以通过一系列运动和控制,将印刷版上的图文转移到印刷品上。
在安装凹版时,需要将凹版固定在印刷机的印版框上,并调整好合适的位置。
接下来,准备好要印刷的印刷品。
印刷品可以是纸张、塑料薄膜、金属片等各种材料。
在印刷之前,要将印刷品经过处理,例如涂布薄膜、烘干等,以保证印刷效果和品质。
然后,将印刷品放置在凹版印刷机的进料处。
通过牵引系统或辊筒传送带,将印刷品送入印刷机的印刷区域。
接着,将墨水或者油墨加载到印刷机的油墨槽中。
在印刷的过程中,油墨会通过墨槽的刮刀,被刮到凹版的表面上。
凹版上的凹陷将保存油墨,而上面的凸起则会被刮掉。
然后,启动印刷机,使印刷版和印刷品开始接触。
在印刷机的作用下,印刷版上的图文将被传递到印刷品的表面上。
凹版印刷机通常采用旋转印刷的方式,即印刷品通过连续旋转的方式完成印刷过程。
最后,完成印刷后,将印刷品从印刷机中取出。
处理印刷品时,需要进行干燥处理,以确保墨水或油墨能够快速干燥。
干燥后的印刷品就可以进行后续加工和包装了。
以上就是凹版印刷的工艺流程简介。
凹版印刷是一种传统的印刷方式,具有高质量、高清晰度和高解像度的特点。
它广泛应用于包装、标签、杂志、书籍等印刷品的制造。
凹版印刷的工艺流程相对较复杂,但通过科学的操作和设备的支持,可以获得出色的印刷效果。
- 1、下载文档前请自行甄别文档内容的完整性,平台不提供额外的编辑、内容补充、找答案等附加服务。
- 2、"仅部分预览"的文档,不可在线预览部分如存在完整性等问题,可反馈申请退款(可完整预览的文档不适用该条件!)。
- 3、如文档侵犯您的权益,请联系客服反馈,我们会尽快为您处理(人工客服工作时间:9:00-18:30)。
连线复合转移凹版印刷工艺流程
制定印前工艺是为了给印刷生产指引明确的道路。
事事相连、环环相扣,每一道工序的细小环节都不允许出现人为或意料之内的错误,一旦出错,将会造成无法弥补的损失。
普通凹版印刷对凹版滚筒制作工艺的要求已相当严格,而连线复合转移凹版印刷对印前制作工艺的要求则更为严格,制定印前工艺需要慎之又慎。
1.原辅材料的确定
(1) 转移膜:一般选用PET为基膜,因为PET薄膜的拉伸范围比OPP 薄膜小,稳定性好。
(2) 底纸:选择底纸要参照样张或根据客户要求。
要求纸张表面平整光洁、柔软性好(纸张纤维不能太硬)。
这样在进行后道工序的模切压痕时,才能保证压痕线饱满、盒片无毛边。
(3) 黏合剂:目前国内在复合产品上使用的黏合剂有溶剂型黏合剂、水基型黏合剂和UV黏合剂。
它们的性能各有不同。
溶剂型黏合剂干燥速度快,释放性能好,但有异味,不利于环保,而且复合产品翘卷严重,放置时间久了颜色会发黄,并有白云状雾点(松香含量大造成的)。
水基型黏合剂不存在溶剂挥发问题,无毒,环保。
尤其是在薄膜涂胶后与纸张叠压时,胶液为自然流动的液体,可迅速充分填平纸张表面的凹陷部分,所以复合产品光洁度好、复合牢度强,复合后产品无翘曲现象,平整美观,综合性能优秀。
UV黏合剂干燥速度快,胶体柔软,附着性能好,黏结强度高,抗高温、冷冻性能好,复合产品不爆色,不发脆。
实际使用中,可根据不同的设备性能、干燥方式、上胶方式、产品要求等,选用不同性能的黏合剂,以期达到理想的复合效果。
(4)清漆:又称树脂油,用于涂布在复合或转移后的金、银、镭射卡纸表面,使其在印刷时对油墨有更好的吸附性。
目前有两种清漆可供选择。
第一种:油性清漆(挥发干燥型),主要成分是合成树脂(硝化棉、丙烯酸树脂),并含有一些助剂。
其优点是涂层厚,干燥速度快。
缺点是在印刷过程中容易与同类体系的树脂油墨互溶。
第二种:水性清漆,主要成分是丙烯酸乳液,并加入一些消泡剂和助剂。
其优点是涂布量少,清漆涂层薄,可节约成本,印刷过程中也不易与油墨互溶。
缺点是干燥速度慢。
(5) 印刷油墨:目前国内纸张凹印一般使用挥发干燥型的油性油墨,溶剂为醋酸乙酯、乙醇(异丙醇)、醋酸丁酯甚至甲苯,对人体危害比较大,不利于环保。
而环保型水性凹印油墨目前还不成熟,仍在研发过程中。
连线复合转移凹版印刷宜选择无苯油墨,其挥发干燥速度中等,颜料颗粒度为3~5μm,色浓度、色饱和度高,耐高温性能好,附着力强,印刷墨层表面易烫印,印刷表面不易被擦伤。
稀释剂为醋酸乙酯、98.5%以上的无水乙醇或异丙醇。
慢干剂可采用丁醚,其毒性较小。
2.生产前的工艺分析
(1) 复合转移纸张工艺介绍
对纸张进行复合、转移的步骤是:先用黏合剂将转移膜与底纸黏结在一起,而后将转移膜的基膜与纸张分离,使纸张表面只存在黏合剂层、镀铝层和涂布层。
纸张是可以透气的,所以一般采用湿式复合的方式,先对转移膜施胶,然后将其与底纸压紧贴合,最后烘干。
涂胶可采取三辊式涂胶,也可采用网纹辊涂胶。
涂胶的相关工艺参
数见表2。
烘箱温度以及印刷速度决定了产品的干燥状况。
需要控制的质量指标有:①复合牢度;②表面平整度;③剥离完整性。
剥离工序的质量很大程度上取决于基膜的涂料配制、涂布层及复合效果等,剥离工序本身需要控制的主要是收膜的松紧度、整齐度,并保证表面无擦伤。
剥离下来的PET基膜可以重新涂布再次用于转移,大大降低了生产成本。
(2)连线复合转移凹版印刷工艺
一般复合后的纸张需经过24小时的熟化期后,才可将PET基膜剥离,使镀铝层和涂布层转移在底纸上。
但连线复合转移凹版印刷生产线的烘道长16m,最高烘干温度达200℃,烘干后可立即经双重冷却辊冷却,完全可以达到理想的复合、转移效果。
涂胶辊:涂胶辊的选用要根据所加工产品而定,施胶量的大小直接影响到产品质量、复合牢度、剥离的完整性。
印版:我厂的连线复合转移凹版印刷生产线按原来的设计应采用空心版,但目前国内很多印刷企业对空心版使用过程中出现的问题尚无很好的解决方案。
它存在的主要弊病是:制版时间相对较长,机加工难度较大;制版厂使用的版轴与印刷厂的版轴轴心不能完全重合,导致长期使用磨损严重,造成印版的动平衡摆动超出所规定的范围,大于0.3mm,在印刷过程中容易出现套印波动明显等跑规现象。
因此,虽然带轴版价格略高,但从产品质量和工艺制作的角度着眼,从成品产出率考虑,应尽可能不使用空心版,我们已改用带轴版。
UV上光:凹版印刷联机UV上光工艺在国内已经很成熟了,但要想做到印后加工无缺陷,还需要我们在印前工艺制作上考虑周全。
由于UV上光后印张必须经过UV灯管的高温烘烤,所以常常会出现纸张变形,造成印后加工套准困难。
因此在进行印前工艺排版时,要着重考虑产品的模切卡位精确度与纸张的变形率对印后加工的影响。
以下针对香烟包装盒中的精细翻盖产品进行简单介绍。
我厂使用的连线复合转移凹版印刷机的最大印刷幅宽为820mm。
由于翻盖盒在印后加工中对烫印、压凹凸、模切套准的精度要求较高,所以拼版时多数采用18拼(3×6),横排两个单刀,盒片连接处各加4mm双刀;竖排6个盒片,3个与3个之间加4mm双刀。
这样拼版可以根据纸张的变形率加减双刀尺寸,大大缓解了因纸张变形印后无法套准的问题。
新设备、新技术、新工艺、再创新是我们共同努力追求的目标。
只有采用先进乃至超前的工艺技术,才能把中国的包装印刷技术迅速向国际水平推进。