带余热锅炉预分解窑结圈问题探析(1)
第三节预分解窑操作常见问题及处理办法

伴随现象
处理办法
1.分解炉温度偏低,参照三
2.炉内料粉悬浮不好、分解慢
3.旋风或喷腾效应差,料粉在炉内停留时间短
4.生料粒度变粗,原料质量变差
出炉气温降低,参照三
炉内温度不低,但分解率低
生料细度粗
参照三
检查调节撒料装置及翻板阀
调节风量、风速及风向
调节生料细度,适当提高分解炉温度
预分解窑几种疑难故障及处理方法
六、C5筒有大量火花(说明大量煤粉进入筒内)
可能原因
伴随现象
处理办法
1.炉内加煤过多,炉内来不及燃烧
2.窑内加煤太多或跑煤,造成机械不完全燃烧
3.分解炉煤粉悬浮不好,燃烧慢
4.炉内旋风或喷腾效应差,燃烧时间短
5.煤质变粗,挥发分减少
6.三次风温降低或漏风严重
7.三次风管积灰或三次风阀开度过小,三次风过小
2.窑内结圈或料层增厚
3.窑内物料结大球
4.冷却机阻力增大,窑头负压增高
5.仪表失灵
火焰过长,尾温升高
火焰受逼,尾温降低
负压不稳,火焰晃动
窑头负压表升高
减小总排风或开大三次风阀门
处理结圈或快窑
根据情况将之打碎、钩出或让它滚出
调节篦冷机料层厚度及放风闸门
整修仪表
八、窑尾负压过低
可能原因
伴随现象
处理办法
4.稳定窑内热工制度,防止窑温忽高忽低
第三节预分解窑操作常见问题及处理办法
一、分解炉或C5出口气温过高(表1)
可能原因
伴随现象
处理办法
1.窑、炉喂煤过多或煤仓跑煤
2.喂料量过少或断料
3.上级预热器堵塞
4.煤质变差,燃烧速度慢
预分解窑的问题分析及研究
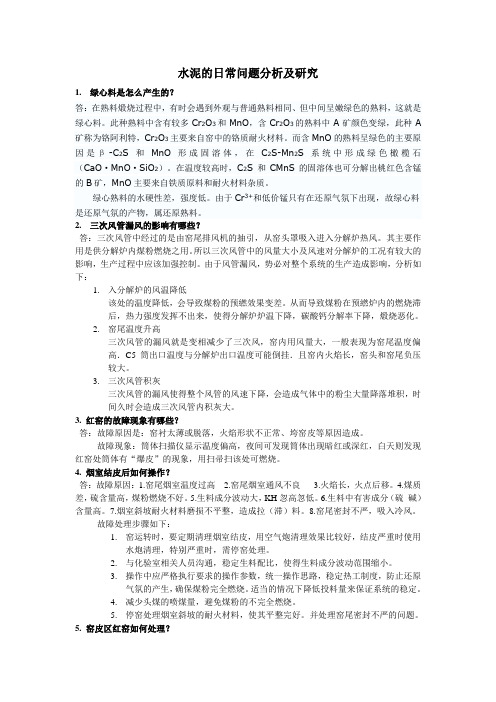
水泥的日常问题分析及研究1.绿心料是怎么产生的?答:在熟料煅烧过程中,有时会遇到外观与普通熟料相同、但中间呈嫩绿色的熟料,这就是绿心料。
此种熟料中含有较多Cr2O3和MnO,含Cr2O3的熟料中A矿颜色变绿,此种A 矿称为铬阿利特,Cr2O3主要来自窑中的铬质耐火材料。
而含MnO的熟料呈绿色的主要原因是β-C2S和MnO 形成固溶体,在C2S-Mn2S 系统中形成绿色橄榄石(CaO·MnO·SiO2)。
在温度较高时,C2S 和CMnS的固溶体也可分解出桃红色含锰的B矿,MnO主要来自铁质原料和耐火材料杂质。
绿心熟料的水硬性差,强度低。
由于Cr3+和低价锰只有在还原气氛下出现,故绿心料是还原气氛的产物,属还原熟料。
2.三次风管漏风的影响有哪些?答:三次风管中经过的是由窑尾排风机的抽引,从窑头罩吸入进入分解炉热风。
其主要作用是供分解炉内煤粉燃烧之用。
所以三次风管中的风量大小及风速对分解炉的工况有较大的影响,生产过程中应该加强控制。
由于风管漏风,势必对整个系统的生产造成影响,分析如下:1.入分解炉的风温降低该处的温度降低,会导致煤粉的预繎效果变差。
从而导致煤粉在预繎炉内的燃烧滞后,热力强度发挥不出来,使得分解炉炉温下降,碳酸钙分解率下降,煅烧恶化。
2.窑尾温度升高三次风管的漏风就是变相减少了三次风,窑内用风量大,一般表现为窑尾温度偏高.C5筒出口温度与分解炉出口温度可能倒挂.且窑内火焰长,窑头和窑尾负压较大。
3.三次风管积灰三次风管的漏风使得整个风管的风速下降,会造成气体中的粉尘大量降落堆积,时间久时会造成三次风管内积灰大。
3. 红窑的故障现象有哪些?答:故障原因是:窑衬太薄或脱落,火焰形状不正常、垮窑皮等原因造成。
故障现象:筒体扫描仪显示温度偏高,夜间可发现筒体出现暗红或深红,白天则发现红窑处筒体有“爆皮”的现象,用扫帚扫该处可燃烧。
4. 烟室结皮后如何操作?答:故障原因:1.窑尾烟室温度过高 2.窑尾烟室通风不良 3.火焰长,火点后移。
预分解窑结圈的原因分析及处理

二、结圈的原因分析及处理公司1000t/d 预分解窑从试生产到 炉风量不平衡等原因,造成在距窑口三次风流化风 A 炉,MFC预分解窑结圈的原因分析及处理一、概述公司1000t/d 预分解窑是以窑尾带 TD 分解炉的单系列五级旋风预热器和/3.2 X 46m 回转窑为 核心 配套/ 3.5 X 10m 中卸式烘干生料磨、503H-606H-825H 推动篦式冷却机,设计生产能力920t/d 熟料。
99年8月,因TD 炉炉容偏小,对分解炉进行了改造,在窑尾塔架旁增设一台N — MFC 流态化 分解炉与原TD 炉串联(见图1 )。
改造后,因对预分解窑认识不足,操作、管理水平跟不上,造成 窑内频繁结圈,严重影响回转窑的正常运转(表1为历年结圈的次数和影响时间)。
经过几年的生产, 已摸清了结圈的原因,并基本解决预分解窑结圈的问题。
在此,对公司预分解窑结圈的原因分析及 处理过程做些简单介绍。
表1为历年结圈的次数和影响时间 年份 19992000 2001 2002 2003.1 〜6 影响停窑时间(t )87 322.67 58.67 37.05 停窑次数(次)527 3 4 料 2000年4月期间,因原燃材料成份不稳定,操作不统一、窑12m 至35m 处频繁结圈,引起停窑次数及时间最多的是23 30m 处的后结圈,16〜23m 处结圈造成停窑次数仅有一次, 16m 以内的结圈虽对产质量有一定的影响,但从未引起停窑。
纵观几年的生产过程,虽然引发结圈的因素委多。
但每次都有一、二个主要 原因,每当解决了主要原因,结圈的问题可以得到缓解或消除。
下面主要介绍一下23m 〜30m 处后 结圈的形成原因及处理过程。
1、窑内用风过大,热工制度不稳定( 2000.1〜3)2000年1月至2000年5月,因回转窑25〜30m 处频繁结圈被迫停窑 297小时,尤其2000年3 月,窑内结圈停窑 9次,其中进窑处理 6次,共影响停窑121小时。
窑预分解系统的问题分析及改进措施

窑预分解系统的问题分析及改进措施摘要:我厂1号RSP窑经过6年多的运转,系统耐火材料呈现出不同程度的磨损、烧坏现象。
SB室下部掉砖,进而壳体烧损;SC室用风不良,导致边壁物料保护层不均衡,局部衬砖磨损严重;斜烟道及鹅颈管侧墙衬砖垮落,由于鹅颈管结构缺陷,经常结皮和堆料;MC室断面物料分布不均,物料稀相区炉壁烧损,直至筒体严重变形;因窑尾缩口处风速低,喷腾能力减弱而塌料;高温级旋风筒分离效率低,导致物料大量返回,内循环增加等。
本文依据热工标定结果,对该预分解系统出现的问题进行分析,并提出改进措施。
1 RSP窑系统工况分析热工标定主要参数对比见表1、表2,窑尾高温区工艺流程见图1。
表1 预热预分解系统温度变化℃表2 RSP炉的分解进程变化注:1997年数据为南京化工大学硅酸地方国营工程研究所的热工标定结果,SC 室出口指斜烟道出进口等同于鹅颈管出口。
图1 窑尾高温区工艺流程1.1 三次风温度及其对SC室工况的影响由表1可见,三次风温度和入炉生料温度分别只有600℃和671℃。
入炉生料温度低主要是由于C4锥体及下料管增开人孔门较多,外漏风量和散热损失增加引起的,通过加强管理,隔热堵漏后完全可以解决;三次风温度目前基本稳定在560~580℃,提高的余地很小。
其原因是:我厂采用单筒冷却机,经过多年的运转,内部装置所遭受的磨损和腐蚀不断加剧,而且增加了砌筑耐火砖的长度,熟料停留时间短(约为30min),出机熟料温度高(~290℃),使热效率本身就不高的单筒冷却机热回收率进一步降低(1997年热工标定结果为56.6%)。
三次风温度是影响分解率和燃尽率的重要因素。
较低的三次风温度导致炉内煤粉着火速度减慢,形成滞后燃烧,特别是SC室内煤粉是在纯助燃空气中燃烧,助燃空气的温度在很大程度上决定了煤粉燃尽率,三次风温度低,即使分解炉多加煤,SC室内温度也不会高,反而会加剧煤粉滞后燃烧。
从表1和表2可以看出,SC室生料出口温度和分解率分别是948℃和43.4%,结合入炉生料表观分解率已达22.6%的实际情况,说明SC室内的分解反应极低,煤粉燃烧状况不理想。
预分解窑结球原因及处理措施
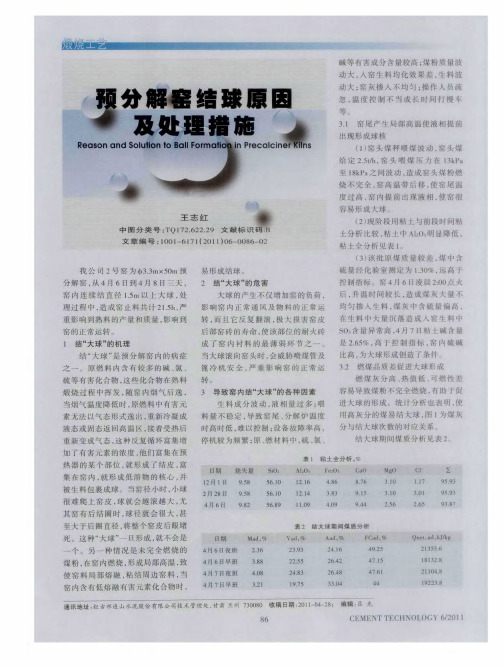
方 向运 动 , 于离 心 力 的 作 用使 液 相 由
向表 层 运 动 , 粘 附生 料 粉 而形 成 大 再
球 中 间 层 , 时 窑 内有 后 圈 挡 住 大 有
球 , 其 在 窑 尾 来 回滚 动 而 越 长 越 使
大 , 自身 重 力 足 以 克 服 后 圈 阻 力 当
时 , 球 就 滚பைடு நூலகம்向烧 成 带 , 附 熟 料 粉 大 粘
图 1 煤 灰 分 与 结 大球 次数 的对 应 关 系
法 进行 处 理 ; 料球 在 过 渡 带 时不 易 当 前 行进 入 烧 成 带 , 时 可 将 喷煤 管 伸 这 进去 , 当降低 喂料 量 , 1 h 适 烧 ~2 后 将煤 管拉 出再烧 1 2 , 而复 始 , — h周 直 到 料 球 破 裂 ; 实 在 不 能 使 其 破 若 裂 , 可 停 窑 冷 却 1 2 后 点 火 升 便 ~h
表 3 入 窑 生 料 成 分 ( 及 率值 %)
E期 t
4月 6日
烧失量
3 .2 53
SO i2
1. 33
Al03 2
3 1 .7 3.2 3
F 23 e0
22 .8 21 .3
CO a
43 1 .8 42 9 .4
Mg O
14 .2 l3 _O
温 , 料 球 因温 差过 大 而 破 裂 。注 意 让 在 处理 过 程 中 , 忌让 大 料 球 滚人 冷 切
( ) 料 量 波 动 大 且 5喂
剧 烈时 , 容易 扰乱 窑 的 很
33 煤 粉 不 完全 燃 烧 产 生 大球 - 热 工 制 度 。 由于 操 作 的滞 后 特 征 , 减 煤 跟 不 上 喂 料 量 的 变 加
预分解窑结圈原因分析与预防教材
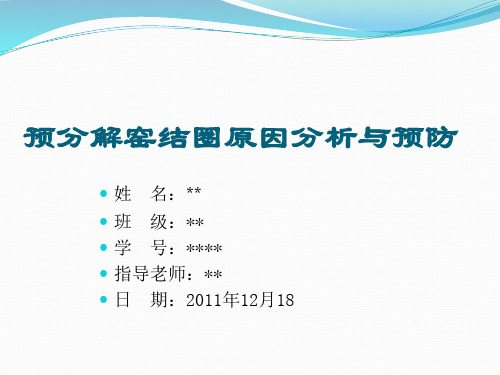
预防措施
① 对硅质、钙质原料超前控制
a. 对不同品位、不同成岩时代的钙质和硅质矿山开采
b. ②
③
④
区进行合理搭配开采,以控制其原料的CaO和硅质 原料的SiO2,质量控制指标为:目标值±1%。 避免同时使用高碱高镁原料。 强化燃烧器的操作,确保火焰的合适形状和热 优化配料方案 建立以中控室为核心的生产指挥系统,从系统角度 将后圈消灭在萌芽状态
结圈的危害
① 结圈后窑内气流倒返,窑头看火孔处气温较高,经
常将看火镜片烤裂,窑内气流浑浊不清,窑头正压 较重。
② 结圈后尽管转全窑速,但烧成带物料粒粒可数,圈
后物料很难通过。
③ 结圈后窑尾物料厚度增大,窑尾返料及其严重,如
未能及时停料,窑尾密封装置磨损加大,甚至磨坏。
结圈炉
结圈的处理
② 对于由于煤的燃烧特性差和操作不当而结成的圈常
采用此法。具体操作如下: a. 改变煤的配合,采用挥发分>25%,灰分<25%的煤, 煤细度控制在5%左右,适当提高入窑生料n值,P值 保持不变。 b. 燃烧器退到较后位置,加大旋流风量,一方面在喷 嘴周围产生较强的回流区能稳定燃料着火;另一方 面为煤粉提供更多的空气,使火焰中心供氧充分, 强化了煤粉燃烧,从而提高火焰的热力强度。
预分解窑结圈原因分析与预防
姓 班
名:**
级:** 学 号:**** 指导老师:** 日 期:2011年12月18
预分解窑结圈问题
截止到2001年末,我国已投产的1000t/d生产线有57条,
熟料设计生产能力总计为1762万t/年,这些干法生产 线投产后,几乎都遇到过窑28~34m段结圈问题,圈 一旦形成,使该处的横断面积显著减少,对窑的热工 制度破坏较大,轻则影响窑内通风,熟料产质量下降, 重则阻碍物料运动,窑尾出现漏料,导致窑尾密封装 置变形损坏,不得不止料处理,频繁结后圈,使窑的 运转率降低,煤耗、电耗、砖耗大幅度上升,造成较 大的经济损失。
预分解窑后结圈的形成原因及处理
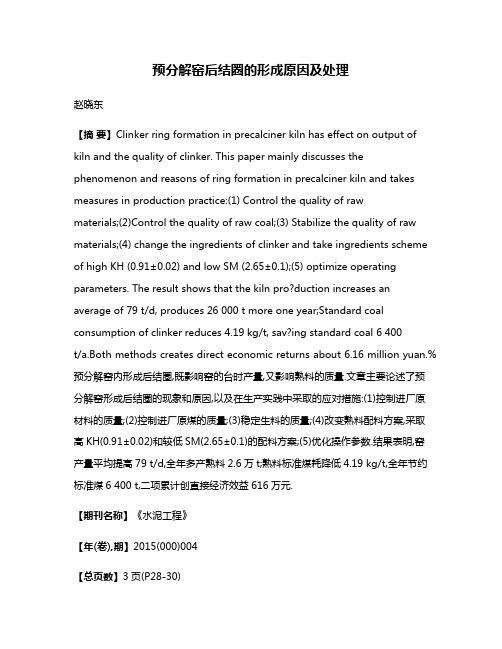
预分解窑后结圈的形成原因及处理赵晓东【摘要】Clinker ring formation in precalciner kiln has effect on output of kiln and the quality of clinker. This paper mainly discusses the phenomenon and reasons of ring formation in precalciner kiln and takes measures in production practice:(1) Control the quality of raw materials;(2)Control the quality of raw coal;(3) Stabilize the quality of raw materials;(4) change the ingredients of clinker and take ingredients scheme of high KH (0.91±0.02) and low SM (2.65±0.1);(5) optimize oper ating parameters. The result shows that the kiln pro?duction increases an average of 79 t/d, produces 26 000 t more one year;Standard coal consumption of clinker reduces 4.19 kg/t, sav?ing standard coal 6 400t/a.Both methods creates direct economic returns about 6.16 million yuan.%预分解窑内形成后结圈,既影响窑的台时产量,又影响熟料的质量.文章主要论述了预分解窑形成后结圈的现象和原因,以及在生产实践中采取的应对措施:(1)控制进厂原材料的质量;(2)控制进厂原煤的质量;(3)稳定生料的质量;(4)改变熟料配料方案,采取高KH(0.91±0.02)和较低SM(2.65±0.1)的配料方案;(5)优化操作参数.结果表明,窑产量平均提高79 t/d,全年多产熟料2.6万t;熟料标准煤耗降低4.19 kg/t,全年节约标准煤6 400 t,二项累计创直接经济效益616万元.【期刊名称】《水泥工程》【年(卷),期】2015(000)004【总页数】3页(P28-30)【关键词】预分解窑后结圈;现象、原因分析;技术措施【作者】赵晓东【作者单位】重庆电子工程职业学院建筑与材料学院,重庆401331【正文语种】中文【中图分类】TQ172.62重庆广安水泥有限公司Φ4.74m×74m生产线自2012年6月投产以来,生产指标一直比较理想,产量≥4500t/d;熟料3d抗压强度≥29MPa,28d抗压强度≥58MPa;吨熟料标准煤耗≤120kg/t。
预分解窑后结圈的形成原因及处理

%
C
S
Q
k J ・ k
的搭 配
比例/ %
无烟煤 1 . 2 0 2 8 . 5 6 3 . 6 8 5 7 . 6 9 8 . 6 5 烟煤 1 . 2 0 2 1 . 4 5 2 8 . 3 4 4 7 . 5 5 0 . 9 4
( 4 )改 变熟 料 配 料 方 案 。根 据 生 产 实践 经 验 ,
3 后 结圈处 理和 预 防措施 3 . 1 后 结 圈处 理措 施
处理预分解窑后结 圈, 采用冷热交替法效果 比
量陡然大量增加 , 液相黏度大幅度降低 , 很容易形
成后结圈。 2 . 4 操作参数的影响 产生后结圈期间 , 窑 的快转率只有 6 5 %~ 7 5 %, 造成窑 内物料填充率相对较 高 , 液相过早 出现 , 物 料在窑内停留时间偏长 , 很容易形成后结圈。另分 解炉的用煤 比例高达 6 5 %, 炉 内煤粉产生不完全燃
经过 这样多次 的循环操作 , 产 生 的 裂 纹 会 越 来 越
烧现象 , 出口废气温度 9 0 0 ~ 9 2 0 o C , 五级预热器 出 口废气温度达到 9 0 0 ℃, 窑尾及 c 5 级预热器容易发 生结皮而影响窑内通风 , 从而导致人窑物料分解率
只有 8 2 %~ 8 6 %。
比例 控 制 8 5 %~ 9 0 %, 使 圈体 温 度 下 降 。 圈体 经 过
次 配料 站 的所有 计量 秤 ,源自保 证 其 计 量 精 度 < 0 . 5 0 %; 每周检查并标定一次人窑生料的固体流量 计, 保证其零点不发生漂移 , 计量精度< 0 . 1 0 %, 保证 人 窑生料 量 的准确 和稳 定 。
预分解窑结球结圈的原因及处理
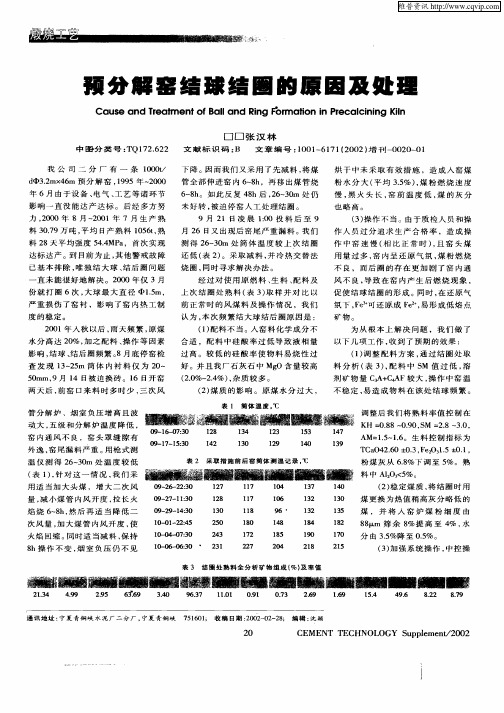
合 适 ,配 料 中硅 酸率 过 低 导 致 液 相 量
过 高 。 较 低 的 硅 酸 率 使 物 料 易 烧 性 过 好 。并 且 我 厂 石 灰 石 中 Mg O含 量 较 高 ( .%- I% ) 杂 质 较 多 。 20 24 , ( ) 质 的 影 响 。 原煤 水 分 过 大 , 2煤
力 ,0 0年 8月 - 0 1年 7 月 生 产 熟 20 20
下 降 。因 而 我 们 又 采 用 了先 减 料 , 煤 将 管 全 部 伸 进 窑 内 6 8 ,再 移 出 煤 管 烧 ~h
6 8 如 此 反 复 4 h后 , 6 3 m 处 仍 - h。 8 2~0
粉 水 分 大 ( 均 35 , 粉 燃 烧 速 度 平 .%) 煤
两 天后 , 窑 口来 料 时 多 时 少 , 次 风 前 三
管 分 解 炉 、烟 室 负压 增 高 且 波
动 大 , 级 和 分 解 炉 温 度 降 低 , 黧 五 窑 内通 风 不 良 ,窑 头 罩 缝 隙 有
外 逸 , 尾 漏 料 严 重 。 枪 式 测 窑 用
0 一l 埘 9 6
表 1 简体 温度 。 ℃
料分 析 ( 3 , 料 中 S 值 过低 , 表 )配 M 溶 剂 矿 物 量 C + F较 大 , 作 中窑 温 C 操 不 稳 定 , 造 成物 料 在 该 处 结 球 频 繁 。 易 调 整后 我 们 将 熟 料 率 值 控 制 在
KH = 8 ~ . 0. 0. 8 0 9 SM =2 8 - . . 3 0.
维普资讯
预 分 解 窑 结 球 结 圈 的 原 因 及 处 理
Cau e s and T eat en al and R n F m at n P ecal ni g i r m tofB l i g * or i i r on ci n K l n
预分解窑为什么会结熟料圈

预分解窑为什么会结熟料圈
1、生料化学成份不合适
熟料圈往往结在物料出现液相的地方,物料温度在1200~1300度范围内,由于物料表面形成液相,表面张力小,粘度大,在离心力作用下易与耐火材砖表面或者已形成“窑皮”表面粘结。
因此,在保证熟料质量和物料易烧性好的前提下,为防止结圈,配料时应考虑液相不宜过多,液相粘度不宜过大。
影响液相量和液相粘度的化学成份是Al2O3、Fe2O3,因此要控制好它们的适当含量。
2、原燃材料中有害成份的影响
原燃材料中碱、氯、硫含量的多少,对物料在窑内产生液相的时间、位置影响较大。
物料所含有害成份过多,其熔点降低,结圈的可能性增大。
正常情况下,此类结圈大多发生在放热反应以后的地方,其危害大、处理困难。
3、煤的影响
由于煤灰中一般含Al2O3较高,因此当煤灰掺入物料时,使物料液相增加,往往易结圈。
煤灰的降落量主要与煤中灰份含量和煤粒粗细有关,灰分含量高、煤粒粗、煤灰降落量就多。
另一方面当煤粉粗、灰分高、水分大,燃烧速度慢时,会使火焰拉长,高温带后移,窑皮拉长易结圈。
4、操作和热工制度的影响
a、用煤过多,产生化学不完全燃烧,使火焰成还原性,促使物料中的铁还原为亚铁,亚铁易形成低熔点的矿物,使液相过早出现,
容易结圈。
b、二、三次风配合不当,火焰过长,使物料预烧好,液相过早出现,粘结窑衬能力增强,特别是在预热器温度高、分解率高的情况下,火焰过长,结后圈的可能性很大。
c、喂料量与总风使用不合理,导致窑内热工制度不稳定,窑速波动异常,也易结后圈。
预分解窑结球事故分析总结
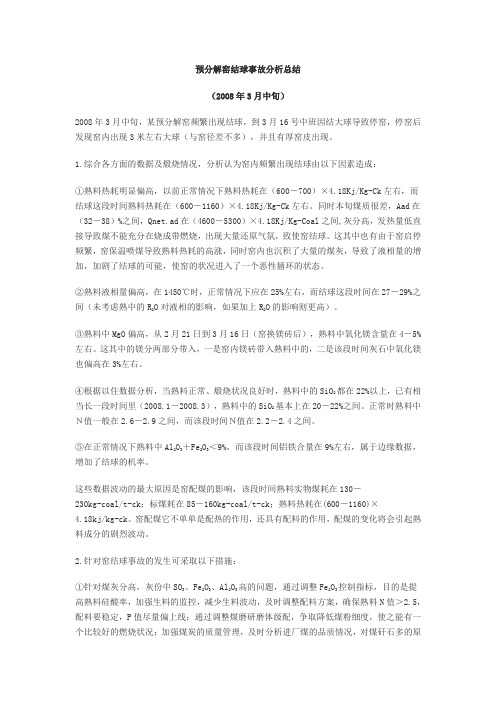
预分解窑结球事故分析总结(2008年3月中旬)2008年3月中旬,某预分解窑频繁出现结球,到3月16号中班因结大球导致停窑,停窑后发现窑内出现3米左右大球(与窑径差不多),并且有厚窑皮出现。
1.综合各方面的数据及煅烧情况,分析认为窑内频繁出现结球由以下因素造成:①熟料热耗明显偏高,以前正常情况下熟料热耗在(600-700)×4.18Kj/Kg-Ck左右,而结球这段时间熟料热耗在(600-1160)×4.18Kj/Kg-Ck左右。
同时本旬煤质很差,Aad在(32-38)%之间,Qnet.ad在(4600-5300)×4.18Kj/Kg-Coal之间,灰分高,发热量低直接导致煤不能充分在烧成带燃烧,出现大量还原气氛,致使窑结球。
这其中也有由于窑启停频繁,窑保温喷煤导致熟料热耗的高涨,同时窑内也沉积了大量的煤灰,导致了液相量的增加,加剧了结球的可能,使窑的状况进入了一个恶性循环的状态。
②熟料液相量偏高,在1450℃时,正常情况下应在25%左右,而结球这段时间在27-29%之间(未考虑熟中的R2O对液相的影响,如果加上R2O的影响则更高)。
③熟料中MgO偏高,从2月21日到3月16日(窑换镁砖后),熟料中氧化镁含量在4-5%左右。
这其中的镁分两部分带入,一是窑内镁砖带入熟料中的,二是该段时间灰石中氧化镁也偏高在3%左右。
④根据以住数据分析,当熟料正常、煅烧状况良好时,熟料中的SiO2都在22%以上,已有相当长一段时间里(2008.1-2008.3),熟料中的SiO2基本上在20-22%之间。
正常时熟料中N值一般在2.6-2.9之间,而该段时间N值在2.2-2.4之间。
⑤在正常情况下熟料中Al2O3+Fe2O3<9%,而该段时间铝铁合量在9%左右,属于边缘数据,增加了结球的机率。
这些数据波动的最大原因是窑配煤的影响,该段时间熟料实物煤耗在130-230kg-coal/t-ck;标煤耗在85-160kg-coal/t-ck;熟料热耗在(600-1160)×4.18kj/kg-ck。
20.预分解窑操作中常见的问题及原因
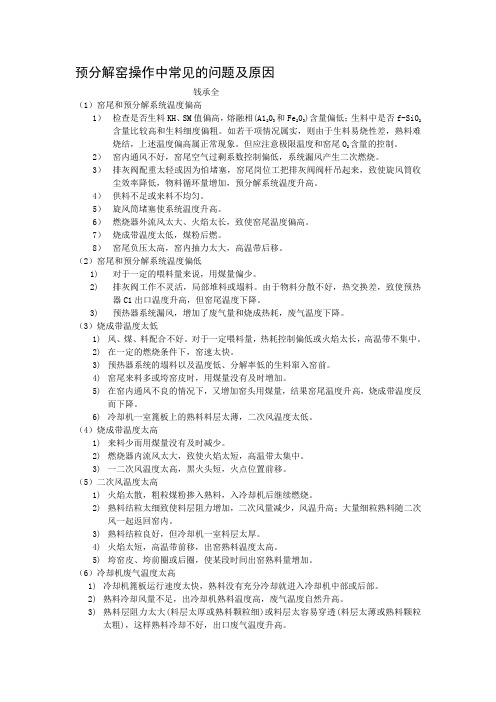
预分解窑操作中常见的问题及原因钱承全(1)窑尾和预分解系统温度偏高1)检查是否生料KH、SM值偏高,熔融相(A1203和Fe203)含量偏低;生料中是否f-Si02含量比较高和生料细度偏粗。
如若干项情况属实,则由于生料易烧性差,熟料难烧结,上述温度偏高属正常现象。
但应注意极限温度和窑尾O2含量的控制。
2)窑内通风不好,窑尾空气过剩系数控制偏低,系统漏风产生二次燃烧。
3)排灰阀配重太轻或因为怕堵塞,窑尾岗位工把排灰阀阀杆吊起来,致使旋风筒收尘效率降低,物料循环量增加,预分解系统温度升高。
4)供料不足或来料不均匀。
5)旋风筒堵塞使系统温度升高。
6)燃烧器外流风太大、火焰太长,致使窑尾温度偏高。
7)烧成带温度太低,煤粉后燃。
8)窑尾负压太高,窑内抽力太大,高温带后移。
(2)窑尾和预分解系统温度偏低1)对于一定的喂料量来说,用煤量偏少。
2)排灰阀工作不灵活,局部堆料或塌料。
由于物料分散不好,热交换差,致使预热器C1出口温度升高,但窑尾温度下降。
3)预热器系统漏风,增加了废气量和烧成热耗,废气温度下降。
(3)烧成带温度太低1)风、煤、料配合不好。
对于一定喂料量,热耗控制偏低或火焰太长,高温带不集中。
2)在一定的燃烧条件下,窑速太快。
3)预热器系统的塌料以及温度低、分解率低的生料窜入窑前。
4)窑尾来料多或垮窑皮时,用煤量没有及时增加。
5)在窑内通风不良的情况下,又增加窑头用煤量,结果窑尾温度升高,烧成带温度反而下降。
6)冷却机一室篦板上的熟料料层太薄,二次风温度太低。
(4)烧成带温度太高1)来料少而用煤量没有及时减少。
2)燃烧器内流风太大,致使火焰太短,高温带太集中。
3)一二次风温度太高,黑火头短,火点位置前移。
(5)二次风温度太高1)火焰太散,粗粒煤粉掺入熟料,入冷却机后继续燃烧。
2)熟料结粒太细致使料层阻力增加,二次风量减少,风温升高;大量细粒熟料随二次风一起返回窑内。
3)熟料结粒良好,但冷却机一室料层太厚。
1000t预分解窑28至34m段结圈的原因分析和预防处理1

1000t预分解窑28至34m段结圈的原因分析和预防处理1--------------------------------------------------------------------------------作者:-作者:谢培顺单位:南宁正大建材有限公司中图分类号:TQ172.622.26 文献标识码:B 文章编号:1002-9877(2003)07-0026-060 引言截止到2001年末,我国已投产的1000t/d生产线有57条,熟料设计生产能力总计为1762万t/年[1],这些干法生产线投产后,几乎都遇到过窑28~34m段结圈问题,圈一旦形成,使该处的横断面积显著减少,对窑的热工制度破坏较大,轻则影响窑内通风,熟料产质量下降,重则阻碍物料运动,窑尾出现漏料,导致窑尾密封装置变形损坏,不得不止料处理,频繁结后圈,使窑的运转率降低,煤耗、电耗、砖耗大幅度上升,造成较大的经济损失。
引起结圈的因素很多,形成的机理也较复杂,它与原料性质、生料成分、燃料燃烧特性和燃烧状况、煤灰和生料组成、窑的操作和生产管理水平等有关。
本文通过对不同地域、不同时期投产的1000t/d窑出现的28~34m段结圈的原因进行分析,并结合生产实践的体会和认识,谈谈该段结圈的预防和处理。
1 结圈原因分析由于预分解窑生料的预热分解在预热器和分解炉内进行,生料入窑时,已有90%~95%的碳酸盐分解。
回转窑的功能之一是将剩余的碳酸钙迅速分解的同时,石灰石质同粘土质组分间,通过质点的相互扩散,进行固相反应,形成C3A、C4AF、C2S。
因28~34m段正是固相反应带和烧成带交界的过渡带,这个区域内,物料一方面接受火焰辐射对流传给的热量,另一方面由于熟料矿物固相反应是放热反应,固相反应放出的热量约为420~500J/g,理论上放热量达420J/g时,就足以使物料温度升高300℃以上,物料从900℃升到1250℃的时间约为5~6min。
预分解窑产生结圈的原因主要有哪些
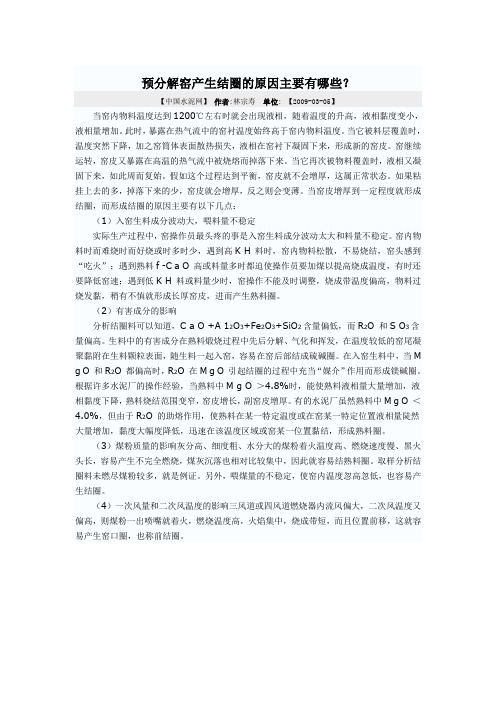
预分解窑产生结圈的原因主要有哪些?【中国水泥网】作者:林宗寿单位: 【2009-03-05】当窑内物料温度达到1200℃左右时就会出现液相,随着温度的升高,液相黏度变小,液相量增加。
此时,暴露在热气流中的窑衬温度始终高于窑内物料温度。
当它被料层覆盖时,温度突然下降,加之窑筒体表面散热损失,液相在窑衬下凝固下来,形成新的窑皮。
窑继续运转,窑皮又暴露在高温的热气流中被烧熔而掉落下来。
当它再次被物料覆盖时,液相又凝固下来,如此周而复始。
假如这个过程达到平衡,窑皮就不会增厚,这属正常状态。
如果粘挂上去的多,掉落下来的少,窑皮就会增厚,反之则会变薄。
当窑皮增厚到一定程度就形成结圈,而形成结圈的原因主要有以下几点:(1)入窑生料成分波动大,喂料量不稳定实际生产过程中,窑操作员最头疼的事是入窑生料成分波动太大和料量不稳定。
窑内物料时而难烧时而好烧或时多时少,遇到高K H 料时,窑内物料松散,不易烧结,窑头感到“吃火”;遇到熟料f -C a O 高或料量多时都迫使操作员要加煤以提高烧成温度,有时还要降低窑速;遇到低K H 料或料量少时,窑操作不能及时调整,烧成带温度偏高,物料过烧发黏,稍有不慎就形成长厚窑皮,进而产生熟料圈。
(2)有害成分的影响分析结圈料可以知道,C a O +A 12O3+Fe2O3+SiO2含量偏低,而R2O 和S O3含量偏高。
生料中的有害成分在熟料煅烧过程中先后分解、气化和挥发,在温度较低的窑尾凝聚黏附在生料颗粒表面,随生料一起入窑,容易在窑后部结成硫碱圈。
在入窑生料中,当M g O 和R2O 都偏高时,R2O 在M g O 引起结圈的过程中充当“媒介”作用而形成镁碱圈。
根据许多水泥厂的操作经验,当熟料中M g O >4.8%时,能使熟料液相量大量增加,液相黏度下降,熟料烧结范围变窄,窑皮增长,副窑皮增厚。
有的水泥厂虽然熟料中M g O <4.0%,但由于R2O 的助熔作用,使熟料在某一特定温度或在窑某一特定位置液相量陡然大量增加,黏度大幅度降低,迅速在该温度区域或窑某一位置黏结,形成熟料圈。
预分解窑常见异常窑况产生的原因及处理方法

预分解窑常见异常窑况产生的原因及处理方法核心提示:本文简单介绍了几种预分解窑常见的异常窑况,分析了产生原因并提出了可行的解决措施。
异常现象1:烧成温度低、窑尾温度高可能原因:(1)系统风量过大或窑内风量过大;(2)煤粉质量差、水分大、细度粗,煤粉燃烧速度慢,产生后燃;(3)多通道燃烧器使用不当,各通道之间的风量调节不合理,火焰不集中;(4)二次风温过低。
处理方法:(1)适当降低系统风量或加大三次风阀开度;(2)严格控制煤粉质量,调整煤磨操作参数;(3)合理调整火焰长度,使火焰活泼有力,风煤混合均匀,燃烧充分;(4)调整合理的篦床速度及合理配置各室的风量。
异常现象2:烧成温度高、窑尾温度低可能原因: (1)燃烧器爆发力过强,火焰白亮且短;(2)煤粉质量好、灰分小、细度细、水分小;(3)系统风量过小或三次风与窑内风量匹配不合理.造成窑内通风过小;(4)窑内有结圈或长厚窑皮影响窑内通风,使火焰短,窑尾温度下降。
处理方法:(1)适当调节内风与外风的比例,减小内风增大外风,确保火焰形状合理;(2)煤粉的控制指标在合理的范围内即可;(3)增大系统风量,减小三次风阀开度,增大窑内的通风;(4)结圈可采用冷热交替法煅烧使结圈脱落,并适当减小喂料。
长厚窑皮可采用大幅度移动喷煤管位置,并根据严重程度适当减小喂料甚至停料,采用冷热交替法烧。
异常现象3:窑尾温度过高可能原因: (1)窑喂料量小或断料;(2)烧成温度高;(3)窑内通风过大;(4)煤管位置靠里。
处理方法: (1)调整喂料量、检查断料原因;(2)加强看火操作,减少喂煤量;(3)合理平衡风、煤、料问的关系;(4)调整煤管位置。
异常现象4:一级旋风筒出口温度升高可能原因: (1)生料喂料量过小或断料;(2)系统风量过大;(3)煤粉燃烧不完全。
处理方法: (1)调整喂料量、检查断料原因;(2)调整系统风量;(3)提高煤粉细度,调整系统工况。
异常现象5:某级旋风筒温度突然升高可能原因: (1)上一级旋风筒堵塞;(2)断料;(3)热电偶失灵。
预分解窑后结圈的原因及处理措施

预分解窑后结圈的原因及处理措施作者:张振旺单位:山东德州晶华集团大坝水泥厂[2005-6-15]关键字:结圈-窑摘要:我公司2500t/d预分解窑规格为φ4m×60m。
2004年12月份开始,在距窑口35-40m处开始长后结圈,从筒体扫描仪上观察圈长约3米左右,较规则。
窑头表现为火焰发飘,伸不进窑内,负压降低,并频繁出现正压;烧成带温度低,熟料质量差;窑尾温度高,严重时漏料。
窑内通风不畅,严重影响了生产。
后来,在设备、工艺、现场看火方面进行了一些改进,取得了很好的效果。
我公司2500t/d预分解窑规格为φ4m×60m。
2004年12月份开始,在距窑口35-40m处开始长后结圈,从筒体扫描仪上观察圈长约3米左右,较规则。
窑头表现为火焰发飘,伸不进窑内,负压降低,并频繁出现正压;烧成带温度低,熟料质量差;窑尾温度高,严重时漏料。
窑内通风不畅,严重影响了生产。
后来,在设备、工艺、现场看火方面进行了一些改进,取得了很好的效果。
1 预分解窑后结圈的原因1.1煤粉水分大我公司使用的煤粉挥发份在30%左右,热值在26000kj/kg, 属于易燃易爆煤种,为保证煤磨(规格φ2.8m×5m+3m, 风扫磨,篦冷机取热风)的安全运转,煤粉的水分控制较高,在3%左右。
由于煤粉水分高,造成煤粉不完全燃烧,使液相提前在过渡带出现,形成结圈。
如果煤粉的细度波动,煤粉的不完全燃烧现象更严重,有时一个班就能形成结圈。
1.2 入窑生料化学成分波动由于我厂原料外购,成分波动较大,预均化堆场的均化效果不很理想,造成入窑生料化学成分波动大;生料磨产量波动、配料调整滞后性等原因也会引起生料成分波动,这样很容易使窑内产生后结圈。
由于成分的波动,使生料的易烧性发生改变,窑的喂煤调整又不能及时跟上,从而使易烧的生料提前产生液相,黏结在窑衬上,产生结圈,特别是当熟料中的MgO含量到3%时结圈极易形成。
2.采取的措施2.1 为提高煤粉质量,保证煤磨安全,对煤磨进行改造:1)在入磨的热风管道与篦冷机之间加沉降室,防止粉状熟料进入磨机。