!虚拟样机技术在内燃机设计中的应用研究
航空航天产品设计中的虚拟样机模拟技术
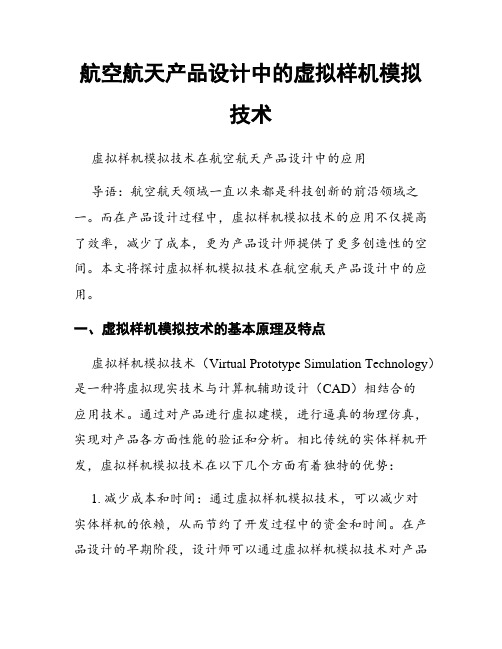
航空航天产品设计中的虚拟样机模拟技术虚拟样机模拟技术在航空航天产品设计中的应用导语:航空航天领域一直以来都是科技创新的前沿领域之一。
而在产品设计过程中,虚拟样机模拟技术的应用不仅提高了效率,减少了成本,更为产品设计师提供了更多创造性的空间。
本文将探讨虚拟样机模拟技术在航空航天产品设计中的应用。
一、虚拟样机模拟技术的基本原理及特点虚拟样机模拟技术(Virtual Prototype Simulation Technology)是一种将虚拟现实技术与计算机辅助设计(CAD)相结合的应用技术。
通过对产品进行虚拟建模,进行逼真的物理仿真,实现对产品各方面性能的验证和分析。
相比传统的实体样机开发,虚拟样机模拟技术在以下几个方面有着独特的优势:1. 减少成本和时间:通过虚拟样机模拟技术,可以减少对实体样机的依赖,从而节约了开发过程中的资金和时间。
在产品设计的早期阶段,设计师可以通过虚拟样机模拟技术对产品进行多次迭代和修改,从而避免了实体样机的制造和调试所消耗的资源。
2. 提高设计质量:虚拟样机模拟技术可以虚拟呈现产品的形状、结构和工作方式,为设计师提供更加直观、准确的信息。
通过对虚拟样机进行模拟分析和测试,可以发现潜在的问题和不足,及时进行改进和优化,从而提高产品的设计质量。
3. 创新设计空间:虚拟样机模拟技术提供了一种无限制、可自由探索的设计空间。
在虚拟环境中,设计师可以进行多种方案的快速迭代和对比,发现和尝试新的设计理念。
这种创新空间为航空航天产品的设计师带来了更多的发挥创造力和思维的机会。
二、虚拟样机模拟技术在航空航天产品设计中的应用1. 飞行器气动布局设计:在飞行器的气动布局设计中,虚拟样机模拟技术可以对飞行器的气动特性进行模拟和分析。
通过对不同气动布局方案进行虚拟样机模拟,设计师可以评估不同方案的优劣,选择最佳的设计方向。
同时,虚拟样机模拟技术还可以通过分析飞行器的气动性能,指导优化飞行器的外形设计,降低气动阻力,提高飞行器的整体性能。
基于虚拟样机技术的柴油机曲柄连杆机构动力学仿真研究
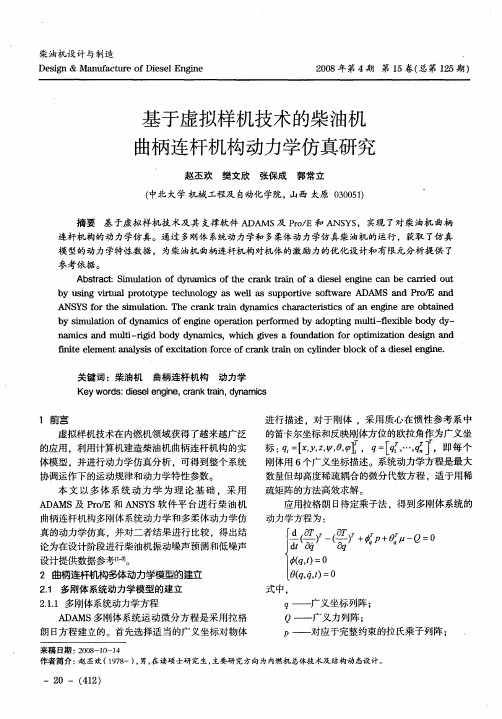
体模型,并进行动力学仿真分析 ,可得到整个系统 刚体用 6个广义坐标描述。系统动力学方程是最大
协调运作下 的运动规律和动力学特性参数。
数量但却高度稀疏耦合 的微分代数方程 ,适于用稀
图 2 曲轴的有限元模型
图 1 多刚体 系统动 力 学仿 真模 型
2.2 柔体 系统动 力学模型 的建 立 2.2.1 多柔 体系统 动力学 方程
ADAMS多柔 体 是采 用 将 零 件 的运 动 分解 为 整 体 (物体参考系)的刚性运动和相对于物体参考系 的变形 运动 的相对 描述 法 。变 形 运 动近 似 采用 离 散的有限个 自由度位移来表示 ,在小弹性变形 的范 围 内,位 移可用模 态 向量 及相 应 的模 态坐 标 的线性 组 合来描 述。
“Amics and mul廿一ri d bo Iy d l删 cs,which giVes a f0unda廿叽 fbr 0p廿miza舡on design and
fjnite elem ent a瑚 】ysis of excita廿0n f0rce of cm l【train on cylinder block of a diesel en .
柴油机设 计 与制造 Design& ManLLfl actⅢ.e of Diesel Engine
2008年 第 4期 第 l5卷 (总 第 l25期 )
基 于虚拟样机技术 的柴油机 曲柄连杆机构动力学仿真研究
赵丕 欢 樊 文欣 张保成 郭常 立 (中北大学 机械工程及 自动化 学院,山西 太原 O3o051)
构模板中修改有关发动机的总体参数或零部件 的总
CAE技术在工程中的典型应用案例分析--3
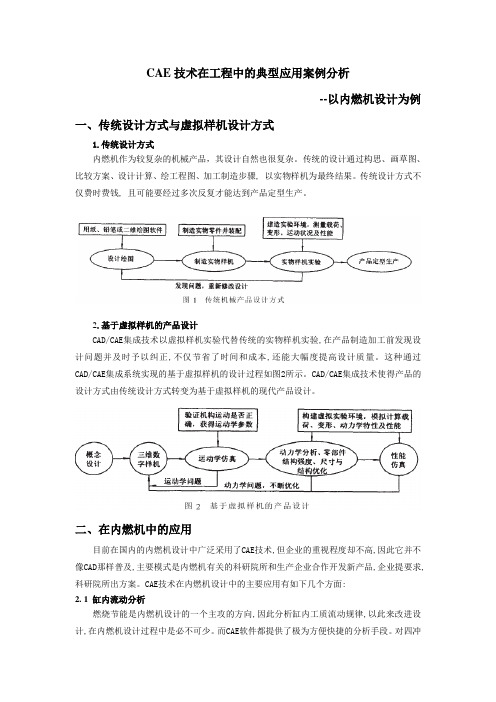
CAE技术在工程中的典型应用案例分析--以内燃机设计为例一、传统设计方式与虚拟样机设计方式1.传统设计方式内燃机作为较复杂的机械产品,其设计自然也很复杂。
传统的设计通过构思、画草图、比较方案、设计计算、绘工程图、加工制造步骤, 以实物样机为最终结果。
传统设计方式不仅费时费钱, 且可能要经过多次反复才能达到产品定型生产。
2.基于虚拟样机的产品设计CAD/CAE集成技术以虚拟样机实验代替传统的实物样机实验,在产品制造加工前发现设计问题并及时予以纠正,不仅节省了时间和成本,还能大幅度提高设计质量。
这种通过CAD/CAE集成系统实现的基于虚拟样机的设计过程如图2所示。
CAD/CAE集成技术使得产品的设计方式由传统设计方式转变为基于虚拟样机的现代产品设计。
二、在内燃机中的应用目前在国内的内燃机设计中广泛采用了CAE技术,但企业的重视程度却不高,因此它并不像CAD那样普及,主要模式是内燃机有关的科研院所和生产企业合作开发新产品,企业提要求,科研院所出方案。
CAE技术在内燃机设计中的主要应用有如下几个方面:2. 1 缸内流动分析燃烧节能是内燃机设计的一个主攻的方向,因此分析缸内工质流动规律,以此来改进设计,在内燃机设计过程中是必不可少。
而CAE软件都提供了极为方便快捷的分析手段。
对四冲程汽油机进行缸内流动的分析,可以在Pro/ENGINEER建立的内燃机气缸盖模型中,提取燃烧室流体分析的几何区域,并导入数值流体力学分析的前处理器(使用Gam-bit),这样可以充分利用三维建模环境下产生的几何信息。
在缸内工作过程中,当活塞处于下死点时,建立气缸工质流体区域模型,由于该过程进、排气阀都紧闭,所以可以忽略气阀结构的影响,流体分析区域是一个封闭的几何体,在建立合适的面、体后可以得到三维流体区域模型和划分的动态网格。
利用数值流体分析工具(如Fluent软件)进行气缸内工质的动态分析。
对模型进行迭代计算,可以得到压缩过程各种热力参数的仿真结果,如上死点流速、温度、压强分布以及平均压力和温度的变化过程等。
电子设计中的虚拟样机与仿真技术

模拟电路行为
01
通过虚拟样机,可以在设计阶段模拟电路的行为,预测其性能
参数,如功耗、延迟和吞吐量等。
优化系统性能
02
基于性能预测结果,可以对电路设计进行优化,提高系统的整
体性能。
降低开发成本
03
在物理样机制作之前发现问题并进行优化,可以减少物理样机
快速原型制作
通过虚拟样机技术,设计师可以 在早期阶段发现和纠正设计中的 问题,减少后期修改和返工。
优化设计参数
仿真技术可以帮助设计师在虚拟 环境中测试不同参数组合,选择 最优设计方案,提高产品性能。
减少物理原型
通过减少或消除物理原型的需求 ,可以节省时间和成本,同时降 低对实物资源的依赖。
降低开发成本与风险
特点
虚拟样机技术具有高效、灵活、可重 复性等优点,能够缩短产品开发周期 ,降低开发成本,提高设计质量。
虚拟样机技术的应用领域
机械工程
在机械工程领域中,虚拟样机 技术常用于汽车、航空航天、 船舶等复杂系统的设计和优化
。
电子工程
在电子工程领域中,虚拟样机 技术可用于集成电路、电子系 统、微纳器件等的设计和仿真 。
03
系统级仿真技术在系统架构设计、性能分析和优化 等方面具有广泛的应用。
物理级仿真技术
01
物理级仿真技术用于模拟物理现象,如电磁场、温度场和 流体动力学等。
02
物理级仿真通常使用有限元分析(FEA)、有限差分分析(FDA) 等方法,通过建立物理模型并运行仿真来预测实际物理现象。
03
物理级仿真技术在产品性能预测、优化和可靠性分析等方 面具有广泛的应用。
的制作数量和测试成本。
电路板设计优化
布局与布线优化
机械设计中的模拟和虚拟样机技术

模拟和虚拟样机技术:通过计算机模拟和虚拟样机技术,可以在设计阶段就发现并解决问题,提高设计效率和质量。
模拟和虚拟样机技术:可以实时修改和优化设计,减少设计周期和成本。
传统设计方法:修改和优化设计需要重新绘制和制作模型,耗时耗力。
传统设计方法:通过手工绘制和制作模型,耗时耗力,容易出现错误和遗漏。
未来发展前景:随着虚拟现实和增强现实技术的不断发展,其在机械设计中的应用将更加广泛和深入,为机械设计带来更多的创新和突破。
应用趋势:虚拟现实和增强现实技术将在机械设计中逐渐普及,成为机械设计的重要工具和手段。
感谢观看
汇报人:XX
1
模拟和虚拟样机技术的概念
2
定义和作用
模拟和虚拟样机技术:通过计算机模拟和虚拟技术,对机械设计进行仿真和优化。
作用:通过模拟和虚拟样机技术,可以提前发现设计中的问题,提高设计质量和效率,降低成本。
应用领域:广泛应用于汽车、飞机、船舶、建筑等领域的机械设计中。
定义:模拟和虚拟样机技术是一种利用计算机技术对机械设计进行仿真和优化的方法。
模拟和虚拟样机技术可以帮助设计师优化机械设计的安全性和可靠性
预测和预防故障
模拟和虚拟样机技术可以预测机械部件的磨损和损坏
通过模拟和虚拟样机技术,可以提前发现潜在的设计缺陷和故障隐患
模拟和虚拟样机技术可以帮助设计师优化机械设计,提高机械性能和可靠性
模拟和虚拟样机技术可以降低机械设计的成本和周期,提高生产效率
未来发展前景和应用趋势
6
智能化和自动化的模拟技术
智能化模拟技术的发展趋势:更加智能化、自动化和集成化
自动化模拟技术的应用领域:机械设计、制造、控制和优化等方面
智能化模拟技术的优势:提高设计效率、降低成本、提高产品质量
简析机械设计中虚拟样机技术的有效应用

简析机械设计中虚拟样机技术的有效应用【摘要】与传统的机械设计技术相比,虚拟样机技术一种全新的智能化产品设计技术,通过进行仿真分析,用图形的方式显示出该系统在实践过程中所具有的各种特性和缺陷,修改设计并得到最优设计方案的技术。
本文通过对虚拟样机技术的概念、特点以及主要的软件技术进行分析,说明了虚拟样机在机械设计中的诸多有效应用。
【关键词】机械设计;虚拟样机技术;有效应用随着科技的不断进步,虚拟样机技术已然成为一种机械设计中必要的技术,不仅是计算机技术在机械工程领域的成功应用,更是一种全新的机械产品设计理念。
虚拟样机技术是一种在建造物理样机前,设计师先通过利用计算机技术建立机械系统的数字化模型,简化复杂机械系统设计,能够有效缩短产品开发周期,降低研发成本,提高产品设计质量等方面有重要突破。
一方面,它可以通过对虚拟样机的测试,从产品多种设计方案中评估出最优方案,并不断改进设计方案,直到获得最优的整机性能。
另一方面,运用虚拟样机技术可以实现产品的并行设计,即可以快速地建立包括控制系统、液压系统、气动系统在内的多体动力学虚拟样机,并在产品设计初期发现问题、解决问题。
通过仿真分析,用图形的方式显示出该系统在实践过程中所具有的各种特性和缺陷,修改设计并得到最优设计方案的技术。
这不仅降低了研发成本,而且也无需浪费大量的人力、物力来生产出具有缺陷的样机,有效的促进了产品设计的设计效率和设计质量。
1.虚拟样机技术简介1.1虚拟样机技术概述随着科学技术的发展,试验手段的加强,以及新兴学科和技术的不断涌现,乃至学科之间的交叉与综合,使得原有的生产方法适应不了当今瞬息万变的时代发展大潮。
机械设计是机械产品研发过程中的一个重要组成部分,是机械生产的第一步,同时还是决定机械性能的最主要因素。
与传统的开发物理样机的设计方法相比,利用虚拟样机技术开发虚拟产品具有很大的优越性。
虚拟样机在对产品进行创新设计、测试和评估等方面可以代替物理样机,由此,不仅可以缩短开发周期,改进产品设计质量,还能节约研发成本。
基于VB与虚拟样机联合运用的内燃机配气机构运动仿真
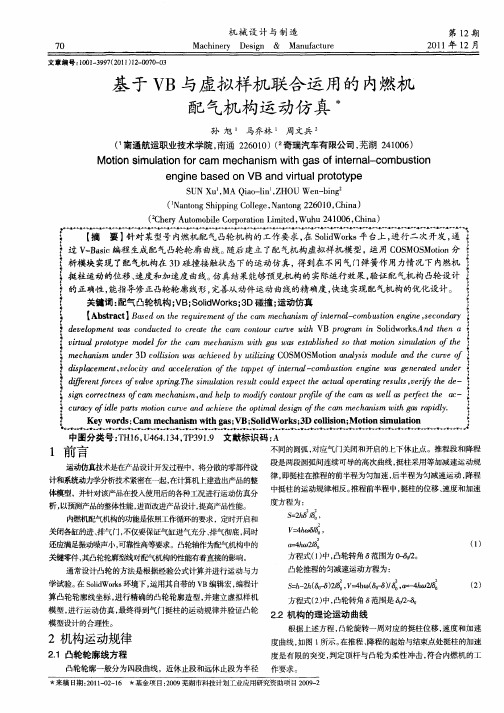
;ia r te olr e啪 m hi t vu oy df eas wh t r ptpm eot c cnm i l o h
eai doh t mlooh ; sbh ami su i t tle tt o i anf e s o n t
;mcai drDcli aa ie i i OM S oo as ou dh cr eh s u e3 l o W hvd y tzg S OMtn limdla e uef; n m n oi n s c e b ul n C s i i a ys n e n t v o
令, 打开 V B编程界面, 编写相应 的程序 。凸轮推程 阶段程序编写
如下 , 其它阶段程序编写与此类似 , 在此略 。
S bm i() u an
D mX ) s o b , ( A D u l 凸轮廓线坐标 i ( A D u l Y ) s ob e e
Di P o be, sAsDo be, m hAsD u l P u l
Ne t x
形 刚度力指数 、 接触边界的最大阻尼 系数及惩罚深度( 即碰撞时 接触边界的穿透深度 ) 等参数值 。 这样在模拟凸轮运动时, 与实际
情况更加相符 。 () 1对挺柱施加气 门弹簧的作用力 , 设定气门弹簧在初始安
装位置 , 进气门完全关 闭情况下的作用力为 20 , 0N 在进气门完全
图 2配气机构三维装配体基本运动模型
HA D u l s o b 凸轮转角, e 挺柱位移 , 最大行程 D mR A D u l, 0 s ob i 0 s o b P 1 D u l 基圆半径 , e A e 凸轮推程运动角
42基 于 3 . D碰撞 接触状态运 动学与动 力学仿真
浅谈虚拟样机技术应用与发展

浅谈虚拟样机技术应用与发展作者:徐雷来源:《科技创新与应用》2014年第03期摘要:虚拟样机技术已被广泛的应用到制造业中,较传统设计方法而言,采用虚拟样机技术进行机械产品的设计研发能大大缩短产品的设计、开发周期,提高产品的质量。
本文主要从概念、特点以及应用和发展对虚拟样机技术进行了阐述。
关键词:虚拟样机;物理样机;计算机仿真;应用与发展引言随着世界经济的快速发展,市场竞争日趋激烈,这种外部因素的影响下,机械产品要提高竞争力、满足客户需求,就必须针对市场环境和需求,改变产品开发模式,提高产品技术含量。
随着计算机技术的快速发展,现代信息技术已逐渐的应用到机械产品的设计与研发中,并成为提高产品质量和性能的一种新技术手段,同时也为虚拟样机技术的发展和应用提供了更为方便的操作平台[1]。
1 虚拟样机技术的概念虚拟样机技术是一种通过综合运用计算机辅助设计中先进的建模、信息管理和多领域仿真等对产品进行设计和分析的方法。
利用虚拟样机技术建立产品计算机模型,对模型进行仿真分析,根据分析结果指导产品的后续研发以及产品的改进设计;同时可以分析机械产品在不同应用环境下的整体性能,进而对产品的质量性能进行评价[2-3]。
在以往的机械产品研发过程中,对方案进行论证、根据经验进行初步的设计、后续的细节进一步修正或改进设计等一系列流程总是在不断的循环讨论当中。
为了验证设计是否合理、可行,功能能否实现,还需要对物理样机进行多次的测试实验,根据实验结果,再对产品的设计方案进行改进,同时再次制造或改进物理样机进行实验以达到设计的要求。
在机械产品设计和研发中应用数字化的虚拟样机技术改变了产品设计→样机建造→测试评估→反馈设计的传统设计流程,避免了物理样机的生产及其修改加工,节约了设计研发成本。
通过数字化的计算机辅助设计技术,可迅速缩短产品开发周期,同时也有利于不同设计工作的协同进行。
2 虚拟样机技术的特点传统的产品开发过程如图1所示,机械产品的设计是一个不断的循环过程。
山东交通学院本科生毕业设计(论文)选题汇总表(工程机械系)

系(部):工程机械系 专业:机械设计制造及其自动化、材料成型与控制、交通建设与装备、船舶与海洋工程 ):工程机械系 专业:机械设计制造及其自动化、材料成型与控制、交通建设与装备、
序号 20 21 22 23 24 25 26 29 30 31 32 33 34 38 39 40 41 42 43 44 45 46 47 48 49 50 51 52 53 54 55 56 57 58 59 60 61 62 63 64 65
13153031367
13583199281
13553153099
15806677007
13066014596
15954917226 13969081300
393 394 395 396 397 398 399 400 401 402 403 404 405 406 407 408 409 410 411 412 413 414 415 416 417 418 419 420 421 433 434 435 436 437
题目名称 装载机诊断检测方案与自诊断系统设计 推土机诊断检测方案与自诊断系统设计 压路机诊断检测方案与自诊断系统设计 摊铺机诊断检测方案与自诊断系统设计 平地机诊断检测方案与自诊断系统设计 挖掘机诊断检测方案与自诊断系统设计 稳定土拌合机诊断检测方案与自诊断系统设计 矿用高强链切断器设计 矿用高强链切断器设计 管材切割机器人设计 用于数控珩磨机的直线电机驱动进给系统设计 微波真空干燥设备设计 气动比例系统的神经网络控制 液压挖掘机功率优化电控系统的设计 振动压路机电控系统设计 冲孔落料连续模设计 落料冲孔复合模设计 齿形垫片精密冲裁模设计 落料冲孔拉伸翻边复合模设计 斜三通注塑模设计 三通注塑模设计 圆盒注塑模设计 注塑成型制品常见缺陷及解决方案 模具寿命与表面强化技术的研究 塑料模具磨损机制及失效机理的研究 焊缝超声波无损探伤技术研究 焊缝射线无损探伤技术研究 工业机器人创新设计研究 履带式摊铺机控制系统研究 水泥混凝土拌和站测控系统设计 自动配料称重系统设计 煤矿井下斜巷安全自动化控制系统研究 基于PLC和组态软件的信号采集系统研究 块精煤防破碎控制系统设计 路面加速加载试验设备动态特性研究 基于uss协议的plc对西门子变频器的控制 基于CAN总线的数据采集系统设计 基于PIC单片机的多路信号采集系统研究 加速加载设备控制系统研究 步进式输送机的设计及运动学分析 铁路用内燃机动力扳手设计
曲柄连杆机构虚拟样机技术研究

曲柄连杆机构虚拟样机技术研究作者:孙勇来源:《科技创新导报》2011年第10期摘要:本论文将利用计算机辅助设计软件CATIA及其插件SIMDesigner建立6135柴油机曲柄连杆机构的虚拟样机,该设计方法在设计初期即可对曲柄连杆机构的运动特性进行分析,为后期的强度和刚度校核以及进一步的优化设计打下基础,避免了样机试验的耗时和耗力,缩短了设计周期,降低了设计成本。
关键词:曲柄连杆机构虚拟样机运动分析中图分类号:TK423 文献标识码:A 文章编号:1674-098X(2011)04(a)-0106-02曲柄连杆机构作为内燃机的重要组成部分,是实现工作循环,完成能量转换的主要运动件,它承受着周期性变化的气体力、往复惯性力和旋转惯性力以及由这些力引起的弯曲载荷和扭转载荷。
因此,曲柄连杆机构的设计是否合理,工作是否可靠,将直接影响内燃机的动力性、经济性、排放性、可靠性和使用寿命。
传统的设计方法一次成功率很低,主要原因是:设计方案的优劣基本上要等到产品样机试制完成,并经考核后才能确定,如果此时发现设计方案不合理,就必须改动设计重新试制,因此,将造成很大的原材料浪费,并拖延产品的开发时间。
应用现代设计方法中的计算机辅助设计技术,建立研发产品的虚拟样机,并对其进行反复的验证和修改,可从根本上改变这一状况,提高设计的效率、缩短产品的开发周期、提高市场竞争力。
本论文将利用计算机辅助设计软件CATIA及其插件SIMDesigner对6135柴油机的曲柄连机构建立虚拟样机,以为后期的强度和刚度校核做准备。
1 曲柄连杆机构主要零部件的设计6135柴油机的基本结构参数要求如表1所示,根据参考文献中设计要求和设计方法设计6135柴油机曲柄连杆机构主要零部件的具体尺寸,然后利用CATIA软件建立曲轴、连杆、活塞等主要零部件的三维实体模型,如图1、2、3所示。
2 曲柄连杆机构虚拟样机的建立在CATIA软件中,将活塞、连杆、曲轴等主要零部件装配在一起,组成曲柄连杆机构。
CFD仿真在内燃机研究中的应用

CFD仿真在内燃机研究中的应用一、内燃机研究中的CFD仿真应用1.燃烧过程分析:内燃机在燃烧室内发生燃烧过程,CFD仿真可以模拟燃烧室内的燃烧过程,包括燃烧速率、燃烧效率、温度和压力分布等。
通过仿真可以优化燃烧室结构、燃烧参数,提高燃烧效率和降低污染物排放。
2.气缸内流动分析:气缸内的流动特性对内燃机性能有着重要影响,包括进气流动、压缩流动、燃烧和排气流动等。
CFD仿真可以模拟气缸内的流动过程,分析气缸内的压力、温度、速度分布,优化气缸几何形状和进气系统设计。
3.散热系统分析:内燃机在工作过程中会产生大量的热量,如果散热系统设计不合理会导致内燃机过热,影响性能和寿命。
CFD仿真可以模拟散热系统内的流动和传热过程,分析冷却效果,优化散热系统设计。
4.污染物排放分析:内燃机在燃烧过程中会产生一些有害的气体和颗粒物,包括一氧化碳、氮氧化物、颗粒物等。
CFD仿真可以模拟燃烧过程中的排放物传输和分布,优化燃烧参数和排放控制设施,降低污染物排放。
5.整机性能优化:CFD仿真还可以模拟内燃机整机的工作过程,包括燃气轮机、柴油机、汽油机等,分析整机性能,优化设计参数,提高效率和降低能耗。
二、CFD仿真在内燃机研究中的优势1.提高研究效率:CFD仿真可以在计算机上进行模拟,不需要建立实际试验台,节约了时间和成本,提高了研究效率。
2.提高精度:CFD仿真可以对内燃机的流动和燃烧过程进行精确的模拟,分析结构细节和流场特性,提高了研究的精度。
3.可视化效果:CFD仿真可以将流动过程可视化,通过动画和图表展示出燃烧效果、流动变化等,便于工程师直观地了解内燃机的工作原理。
4.多参数分析:CFD仿真可以同时考虑多种因素对内燃机性能的影响,包括几何形状、材料选取、燃烧参数等,优化设计方案。
5.可再现性:CFD仿真可以对同一实验进行多次重复模拟,可以验证结果的可靠性和一致性,提高了科学研究的可信度。
综上所述,CFD仿真在内燃机研究中具有重要的应用价值,可以帮助工程师更好地理解内燃机的工作原理和流体特性,优化设计和提高性能。
基于虚拟样机技术的S195柴油机建模与仿真研究

在 P o E中完成活塞组 、 r/ 连杆组 和曲轴 飞轮组等零件 的建模 , 利用机 构模块建立其装 配模 型( 见图 1 . )装 配完成后 , 主轴上施 加驱动 , 在 对其 进行简单 的运 动仿真 , 检验机构运动 的正确 性和零件问 的干涉情况 等.
的几 何 和 质 量 特 性 参 数 . 导 人 AD 并 AMS中进 行 运 动 学 、 力 学仿 真 分 析 . 拟 气 缸 内气 体 压 力 , 析 柴 油 机 动 模 分 额定工况下机构间动力作用状态 ; 合 A) 结 I AMS和 A Y NS S对 内燃 机 曲柄 连 杆 机 构 零 件 进行 动力 学 有 限元 分 析 . 真 分析 表 明 , 真结 果 与 ¥ 9 仿 仿 1 5柴 油 机 的实 际工 作 状 况基 本 一致 , 柴 油 机 的 开发 设 计 提供 了 一 种可 行 为
文 章 编号 :6 2 2 7 ( 0 0 0 — 0 5 0 l 7—4 7 2 1 )30 4—3
基 于虚 拟 样 机 技 术 的 S 5柴 油 机 建 模 与 仿 真 研 究 1 9
钟 相 强 , 立 军 梁 利 东 蒋 ,
( .安 徽 工 程 大 学 先 进 数 控 和伺 服 驱 动 技 术 安 徽 省 重 点 实 验 室 , 徽 芜 湖 2 1 0 ; 1 安 4 0 0 2 .奇 瑞 汽 车股 份 有 限公 司 设 备 中心 技 术 部 。 徽 芜 湖 2 1 0 ) 安 4 0 0 摘要 : 针对 S 9 l 5柴 油 机 在 实 际 工 作 过 程 中存 在 的 问题 , 用 P o E建 立 S 9 利 r/ l 5柴 油 机 虚 拟 样 机 , 得 各 零 件 获
机械设计基础了解机械设计中的常见仿真与虚拟样机

机械设计基础了解机械设计中的常见仿真与虚拟样机机械设计是指以机械原理为基础,应用工程技术方法和计算机辅助设计技术,进行产品的设计、制造和维修等工作。
在机械设计过程中,常常需要进行仿真与虚拟样机的设计与应用。
本文将介绍机械设计中的常见仿真方法和虚拟样机技术,并探讨其在机械设计中的应用。
一、仿真方法1. 动力学仿真动力学仿真是机械设计中常见的一种仿真方法。
它通过对机械系统中各个零部件的受力、运动、变形等参数进行计算和分析,从而模拟出机械系统的运动行为。
动力学仿真能够帮助工程师在设计过程中评估系统的性能,并优化设计方案。
2. 结构力学仿真结构力学仿真是机械设计中另一种常见的仿真方法。
它通过对机械结构的应力、变形等参数进行计算和分析,从而评估结构的强度和刚度等性能。
结构力学仿真可以帮助工程师在设计过程中避免结构失效和破坏,并提供合理的设计改进方案。
3. 流体力学仿真在涉及液体和气体流动的机械设计中,流体力学仿真是一种常用的仿真方法。
它通过对流体的速度、压力、温度等参数进行计算和分析,从而模拟出流体的流动行为。
流体力学仿真能够帮助工程师优化流体系统的设计,提高系统的效率和性能。
二、虚拟样机技术虚拟样机技术是一种基于计算机辅助设计和虚拟现实技术的设计方法。
通过使用三维建模软件和虚拟现实技术,工程师可以在计算机上构建出完整的产品模型,并进行可视化和交互式的设计与分析。
虚拟样机技术的主要应用包括以下几个方面:1. 产品设计评估虚拟样机技术可以帮助工程师在产品设计的早期阶段进行评估和优化。
通过构建出逼真的虚拟样机,工程师可以对产品的外观、结构和功能等进行全面的仿真和测试,从而有效减少实际样机的制作成本和时间。
2. 人机交互设计虚拟样机技术可以模拟出产品的使用场景,并通过用户界面和交互反馈来评估产品的易用性和人机交互性。
工程师可以通过虚拟样机对产品的人机界面进行设计和测试,从而提供更好的用户体验和操作便利性。
3. 工艺制造仿真虚拟样机技术还可以用于工艺制造的仿真和优化。
机械设计中的仿真与虚拟样机技术

机械设计中的仿真与虚拟样机技术随着科技的不断进步和发展,虚拟技术在机械设计领域中发挥着越来越重要的作用。
仿真与虚拟样机技术不仅提高了产品设计的效率和准确性,还降低了成本和风险。
本文将深入探讨机械设计中的仿真与虚拟样机技术的应用及其优势。
一、仿真技术在机械设计中的应用在机械设计过程中,仿真技术通过建立数学模型和模拟实验的方式,模拟真实工作环境,评估产品性能和可行性。
具体应用包括但不限于以下几个方面:1. 力学仿真通过计算机辅助工程软件,可以对机械零件的力学性能进行仿真分析。
例如,可以分析零件在各种载荷下的应力、变形和疲劳寿命等。
这样可以避免实际零件在使用过程中出现失效和故障的问题,提高产品的可靠性。
2. 流体仿真在涉及流体传输的机械设计中,流体仿真技术可以模拟液体或气体在设备中的流动情况。
通过分析压力、流速、流向等参数,可以优化管道系统、减小能量损失,并确保流体系统的正常运行。
3. 热仿真热仿真技术可以模拟机械设备在工作过程中的热传导和热辐射等现象。
例如,在发动机设计中,通过热仿真分析可以评估冷却系统的性能,优化散热结构,确保发动机在高温环境下的正常工作。
4. 控制系统仿真控制系统是机械设备的重要组成部分,仿真技术可以对控制系统进行模拟和验证。
通过仿真分析,可以调试控制参数,提高系统的响应速度和稳定性,并降低调试成本和风险。
二、虚拟样机技术在机械设计中的应用虚拟样机技术是指通过计算机模拟和虚拟现实技术,创建出真实的虚拟产品原型。
虚拟样机可以在设计阶段进行展示和验证,具体应用包括但不限于以下几个方面:1. 形状设计与展示虚拟样机技术可以将设计图纸转化为具有真实外观和质感的虚拟产品原型。
设计师可以通过虚拟样机对产品的外观进行微调和展示,从而更好地满足客户的需求和审美要求。
2. 功能检验与优化通过虚拟样机,设计师可以模拟产品的各项功能,并进行性能测试。
例如,在汽车设计中,虚拟样机可以模拟车辆行驶、转弯等过程,从而检验和优化车辆的操控性能和安全性能。
内燃机系统动力学仿真
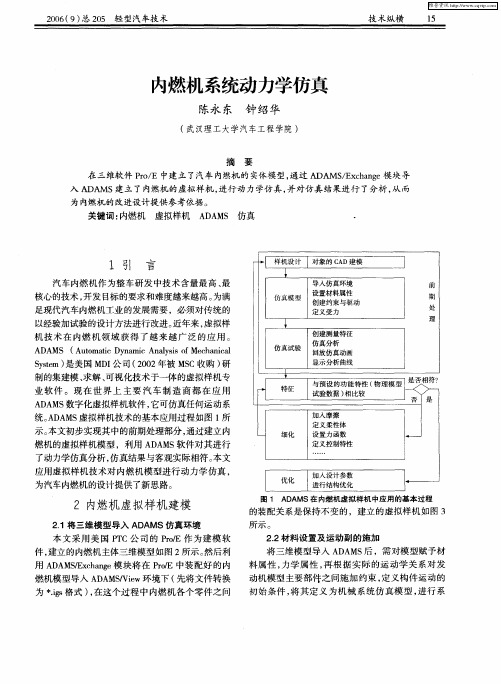
示。 本文初步实现其中的前期处理部分 , 通过建立 内 燃机的虚拟样机模 型 ,利用 A A S软件对其进行 DM 了动力学仿真分析 , 仿真结果与客观实际相符 。 本文
应用虚拟样机技术对内燃机模型进行 动力学仿真 , 为汽车内燃机的设计提供了新思路。
图 1 A AMS在 内燃机虚拟样 机中应用的基本过程 D
D n i e sy t Y u g d ls o n ’Mo uu s P i o ‘R t os n ai s s o 27 ・0 gmm .E0 6k / 3 71 + 0 e o / m .E O 4n wtnr 2 a 03 .
图 4 活 塞 零件 材 料 的设 置
图 3 内燃 机模 型导 入 A AMS e 环 境 D Niw
统动力学仿真。 本文创建活塞零件材料为铝合金 ,其密度和弹
性模量设置如图 4 所示 , 同理给连杆 、 曲轴 、 阀和 气 凸轮轴设置材料属性 。使用 A A S i D M/e V w中的约束 库在零件之间创建约束副 ( osa t , C nt i ) 以确定零件 rn 之间的连接情况 以及零件之间是如何相对运动的。
22材料 设 置及 运 动副 的 施加 .
将三维模型导入 A A S ,需对模型赋予材 DM 后 料属性 , 力学属性 , 再根 据实际 的运 动学关 系对 发
动机模型主要部件之间施加 约束 , 义构件运动的 定
初始条件 , 将其定 义为机械 系统仿 真模 型 , 进行 系
维普资讯 ຫໍສະໝຸດ 1 引 言 汽车内燃机作为整 车研发 中技术含量最高 、 最 核心的技术 , 开发 目标的要求和难度越来越高 。 为满
足现代汽车内燃机工业 的发展需要 ,必须对传统 的
内燃机工作过程数值仿真

内燃机工作过程数值仿真内燃机工作过程是指燃料在内燃机内燃烧产生能量,通过气缸压力和曲轴运动转化为机械能的过程。
数值仿真是一种通过计算机模拟来分析和预测物理系统行为的方法。
在内燃机领域,数值仿真可以用来研究和优化燃烧过程、燃料流动和热力学性能等方面。
首先,数值仿真可以用来模拟内燃机的燃烧过程。
在燃烧室内,燃料与空气混合并点燃,燃烧产生高温高压气体。
数值仿真可以通过求解燃烧室内的质量、动量、能量守恒方程以及燃料燃烧过程的反应动力学方程来模拟燃烧过程。
通过仿真可以分析燃料燃烧速度、燃烧效率以及废气排放等关键参数的变化规律。
其次,数值仿真可以用来研究内燃机的燃料流动。
在内燃机中,燃料必须迅速进入燃烧室并与空气充分混合,以保证燃烧的效果和效率。
数值仿真可以通过求解流体的Navier-Stokes方程和质量守恒方程来模拟燃料在燃烧室内的流动过程,以研究喷射器喷油、燃料雾化和燃料混合等关键技术的影响。
此外,数值仿真还可以用来优化内燃机的热力学性能。
内燃机的效率和性能与气缸压力、温度以及内部气体的运动状态有关。
数值仿真可以通过求解气缸内气体的状态方程、能量守恒方程和动量守恒方程来模拟内燃机的等熵压缩过程和等熵膨胀过程。
通过仿真可以优化气缸压力曲线、最大压力和平均有效压力等关键指标。
最后,数值仿真还可以用来研究和优化内燃机的喷油系统、燃烧室结构以及气缸排气系统等方面的设计。
通过仿真可以优化喷油系统的喷油角度、时序和喷孔结构,以提高燃烧效率和减少废气排放。
同时,仿真还可以优化燃烧室的形状和尺寸,改善气缸内气体的流动状况。
此外,仿真还可以优化气缸排气系统的安装位置和排气阻力,提高内燃机的排气效率。
总之,内燃机工作过程的数值仿真是一种有效的研究和优化手段。
通过仿真可以研究燃烧过程、燃料流动、热力学性能和系统设计等方面的问题,以提高内燃机的性能和效率。
随着计算机计算能力的提高,数值仿真在内燃机工作过程研究中的应用将越来越广泛。
虚拟样机技术及其在发动机设计中的应用

6 6
唐友 亮等 : 虚拟 样机技 术及其在发 动机设 计 中的应 用
第1 期
如图 4 图 5所示 。具体仿真过程可参 见参考 文 、 大、 越复杂 , 可视化技术带来的优势就越明显。 可视化技术是虚拟 仿真结果分析 , 通过测试整个模型或模型 的一部分可 样机技术实用化 的体现和重要保障。建模技术 、 仿真分析技术和 献。对模型进行动态仿真 , 可 视 化 技 术 因 此 它们 的发 展 对 于虚 拟 样 机 技 术 的 发展 起 着 举 足 以很好 的验证其运动的正确性 。
从 中可 以获得 所 有 动力 学 参数 在 发动 机 工作 时 的变 化 过程 , 显示
出较大的优点 , 限于篇幅 , 笔者在此不再赘述 , 有兴趣 的读者可以
参 阅 相关 的文献 。
图 2发动机零件设计
4结束语
随着科学技术 的发展和对发动机性能 的要求 的 日益提高 ,
虚拟 样 机技 术 在 发动 机设 计 上 的应 用 越来 越 广 泛 。 用 虚拟 样 机 利
第 1 期 21 0 2年 1月
文 章 编 号 :O 1 39 (0 2 0 — 0 5 0 lO — 9 72 1 ) 1 0 6— 2
机 械 设 计 与 制 造
Ma h n r De in c iey sg & Ma u a tr n f cu e
虚拟样机技 术及其在发动机设 计 中的应 用 木
公 司的 P O e 。 R — 等 发动机零件设计和装配的三维图 , 如图 2 图 3 、
所示
Tme sc i (e )
图 5运动仿真结果分析
33 发动机 动其他态仿真 试验 .
虚拟样机技术在发动机的曲轴强度分析 、 疲劳寿命分析 、 活 塞应力分析及疲劳寿命分析、缸内流体流动分析等也得到应用 ,
内燃机曲轴扭振多体动力学分析

a s mb y i cu i g f x be c a k h f i e tb ih d Ac o d n o t e r s h ft e t s o e e — s e l n l d n e i l r n s a t s sa l e . c r i g t e u so e t ft n l s h h h
gne,h sa t l n lz h h r ce it so h o so a i r to fa o t e e gn r n s a t i t i ri e a a y e t e c a a t rsi ft e tri n lvb ain o utmo i n i e c a k h f. c c v
第2 8卷 第 4期
21 0 0年 8月
江
西
科
学
Vo . 1 28 No. 4 Au . 01 g2 0
J ANGXI S ENCE I CI
文 章 编 号 :0 1 3 7 (0 0 0 0 0 —0 10 — 69 2 1 )4— 5 1 4
内燃 机 曲Байду номын сангаас 扭 振 多 体 动 力 学 分 析
Abta tB s gm l—o yss m s lt n( s )m to ,cmbn dw t f i l n — s c : yui utb d yt i a o M s ehd o ie i i t ee ta r n i e mu i h n e me n ls F A) tetr o a v rt n o uo oi n ie ca khf i a a zd i hspp r a i E , os n l i ai fa t t e e g rn sa s n l e n ti a e, y s( h i b o m v n t y
CFD技术应用论文

CFD技术在内燃机中的应用汽车学院14班鲁瑛琦44120208摘要:进入二十一世纪以来,科学技术的高速发展让内燃机实验变得更加简便。
尤其是仿真模拟软件的应用大大节省了内燃机实验的成本,提高了可操作性。
其中CFD技术运用广泛,在内燃机设计中发挥的作用也越来越重要。
本文简要介绍了内燃机工作过程数值模拟和内燃机CFD的发展历程,并介绍了内燃机CFD 的各个组成部分和缸内紊流流场的基本算法,最后指出了内燃机CFD的发展趋势。
1.CFD技术简介CFD(Computational Fluid Dynamics)是基于计算机技术的一种数值计算工具,用于求解流体的流动和传热问题。
由于CFD可以准确的给出流体流动的细节,因而可以从对流场的定量分析中发现产品设计中存在的问题,据此优化设计方案,达到改变传统产品设计过程的目的。
本文对CFD技术在内燃机设计中的应用进行了讨论。
1.1紊流运动的CFD简介内燃机的缸内气体流动是典型的紊流运动,对紊流运动的计算属于计算流体力学(CFD)的范畴。
内燃机工作过程CFD即是在紊流流动CFD的基础上,增加了对内燃机工作过程所特有的喷雾、蒸发、混合及燃烧等子模型的建立。
紊流运动的CFD是目前CFD领域困难最多但研究最活跃的领域之一。
目前关于此类的计算方法大致可分为:(1).直接数值模拟(DNS)。
运用非稳态的N-S方程对紊流进行直接计算,包括大尺度涡旋和小尺度涡旋,对高度复杂的紊流运动必须采用很小的时间和空间步长。
(2).大涡模拟(LES)。
运用非稳态N-S方程直接模拟大尺度涡旋,小涡对大涡的影响通过近似的模型来考虑。
以上两种计算方法都要求计算机有很高的处理速度和存储容量。
(3).Reynolds时均方程法。
将非稳态方程对时间作平均,在所得出的关于时均物理量非控制方程中包含了脉动量乘积的时均值等物理量,于是所得出的方程个数小于未知量的个数。
为使方程组封闭,就建立模型把未知的更高阶的时间平均值表示成较低阶的在计算中可以确定的量的函数。
内燃机最新技术及应用领域
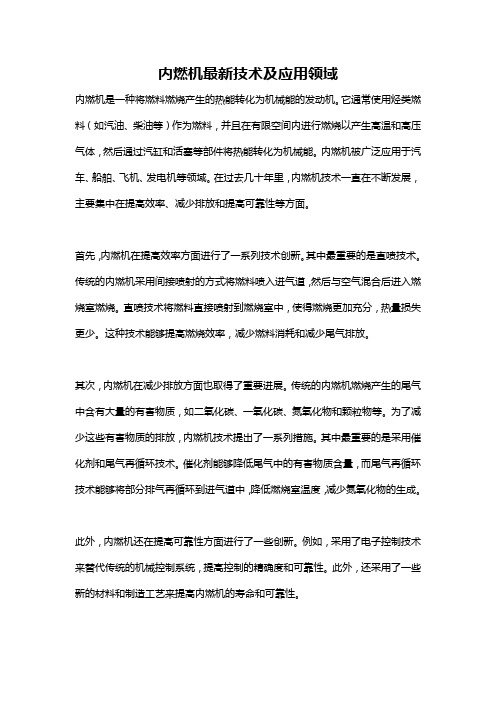
内燃机最新技术及应用领域内燃机是一种将燃料燃烧产生的热能转化为机械能的发动机。
它通常使用烃类燃料(如汽油、柴油等)作为燃料,并且在有限空间内进行燃烧以产生高温和高压气体,然后通过汽缸和活塞等部件将热能转化为机械能。
内燃机被广泛应用于汽车、船舶、飞机、发电机等领域。
在过去几十年里,内燃机技术一直在不断发展,主要集中在提高效率、减少排放和提高可靠性等方面。
首先,内燃机在提高效率方面进行了一系列技术创新。
其中最重要的是直喷技术。
传统的内燃机采用间接喷射的方式将燃料喷入进气道,然后与空气混合后进入燃烧室燃烧。
直喷技术将燃料直接喷射到燃烧室中,使得燃烧更加充分,热量损失更少。
这种技术能够提高燃烧效率,减少燃料消耗和减少尾气排放。
其次,内燃机在减少排放方面也取得了重要进展。
传统的内燃机燃烧产生的尾气中含有大量的有害物质,如二氧化碳、一氧化碳、氮氧化物和颗粒物等。
为了减少这些有害物质的排放,内燃机技术提出了一系列措施。
其中最重要的是采用催化剂和尾气再循环技术。
催化剂能够降低尾气中的有害物质含量,而尾气再循环技术能够将部分排气再循环到进气道中,降低燃烧室温度,减少氮氧化物的生成。
此外,内燃机还在提高可靠性方面进行了一些创新。
例如,采用了电子控制技术来替代传统的机械控制系统,提高控制的精确度和可靠性。
此外,还采用了一些新的材料和制造工艺来提高内燃机的寿命和可靠性。
内燃机的应用领域非常广泛。
首先,汽车是内燃机最主要的应用领域之一。
传统的汽车发动机采用汽油和柴油作为燃料,并使用内燃机将燃料燃烧产生的热能转化为机械能,从而驱动车辆前进。
随着汽车产业的发展,内燃机技术也在不断进步,旨在提高燃油效率和减少尾气排放。
其次,船舶是另一个重要的内燃机应用领域。
内燃机可以驱动船舶的螺旋桨推动船只前进。
由于船舶的特殊工作条件,内燃机的可靠性要求较高。
因此,在船舶领域内发展了各类适用于船舶的专用内燃机,并不断改进技术以提高效率和降低排放。
- 1、下载文档前请自行甄别文档内容的完整性,平台不提供额外的编辑、内容补充、找答案等附加服务。
- 2、"仅部分预览"的文档,不可在线预览部分如存在完整性等问题,可反馈申请退款(可完整预览的文档不适用该条件!)。
- 3、如文档侵犯您的权益,请联系客服反馈,我们会尽快为您处理(人工客服工作时间:9:00-18:30)。
虚拟样机技术在内燃机设计中的应用研究
本文以内燃机为对象,将虚拟样机技术在动力机械设计中进行了初步实践。
文中对其主体进行了参数化样机设计,使用模拟工具进行了动态仿真试验,如压缩过程的流体计算,活塞有限元分析和主运动系的动力学仿真等。
一、引言
在动力机械(如内燃机)的传统设计过程中,由于在前期设计阶段缺乏试验用的样机,因此不可能取得足够的实际经验以避免设计中潜在的缺陷。
这样,有关装配、操作和维护的问题往往只会在设计后期或在最终产品试车过程中、甚至在投入使用一段时间后才能暴露出来,所以产品往往不得不返回到构造设计阶段以进行必要地修改,这样的设计过程不仅效率低,费用还高。
随着现代计算机仿真和网络通信技术的发展,虚拟设计(Virtual Design,VD)技术的兴起将为解决这些问题提供新的方法。
在设计初期,可直接在虚拟环境(计算机环境)中创建产品模型,即虚拟样机(Virtual Prototyping,VP),并将其置于虚拟环境中进行试验。
这样不仅可以使产品的结构和功能得到模拟,而人机交互性能也能得到测试,使产品缺陷在最初的设计阶段就能被及时发现并加以改进,从而可以作出前瞻性的决策和优化实施方案。
现选取四冲程汽油机的主体运动件为研究对象,运用虚拟样机技术对其进行设计和试验,以寻求一种高效的设计方法。
二、内燃机的主体样机设计
1.零件设计
借助基于特征的三维参数化建模工具Pro/ENGINEER进行内燃机主体部分的几何设计,包括活塞组件、连杆、曲轴、气缸盖、气缸体、凸轮及凸轮轴和气阀,如图1所示。
图1 内燃机主体装配图
首先需要为所设计的内燃机选型(确定基本的几何结构和尺寸),对其设计有个整体规划,然后将整个内燃机系统划分为若干子系统,即上面所述的各个组件。
根据实践中的条件、功能要求及经验准则,对这些组件分别进行构型设计并加入材料(即设置各个零件的物理性质),将每个零件的主要几何结构及尺寸参数化,并通过这些参数在各个零件之间建立关联(Relation)约束,使各个子系统构成一个内在的整体。
2.虚拟装配
利用Pro/ENGINEER的Layout(布局)功能,定义装配件中每个零件相关尺寸关系与组合关系,并与建立的零件模型相关联。
如果要修改零件,也只需修改所绘制的Layout2D规划图,就能自动将变更加至组件文件中,从而大大地提高了装配的效率与可维护性。
在保证可以代表整机结构状态下,Layout 图可以用最简单的线条绘制,并在图中定义全局几何基准(Global Datum)和全局尺寸参数(Global Dimension)。
然后,在相关零件模型中声明(Declare)该Layout文件,并将相关零件模型中的对应几何基准和尺寸参数与Layout文件中的全局几何基准和全局尺寸参数相关联。
最后,得到的主体的装配模型,如图1所示。
三、主体件的动态仿真试验
1.缸内流动分析
在Pro/ENGINEER建立的内燃机气缸盖模型中,提取燃烧室流体分析的几何区域,并导入数值流体力学分析的前处理器(这里使用Gambit),这样可以充分利用三维建模环境下产生的几何信息。
在缸内工作过程中,本文首先分析内燃机的压缩冲程。
当活塞处于下死点时,建立气缸工质流体区域模型,由于该过程进、排气阀都紧闭,所以可以忽略气阀结构的影响,流体分析区域是一个封闭的几何体,在建立合适的面、体后得到的三维流体区域模型和划分的动态网格,如图2所示。
图2 建立缸内流体分析区域(左图)和划分网
利用数值流体分析工具进行气缸内工质的动态分析,这里用Fluent软件。
对模型进行迭代计算,可以得到压缩过程各种热力参数的仿真结果,如上死点流速、温度、压强分布以及平均压力和温度的变化过程等,如图3、图4所示。
图3 上死点时缸内流速(上图)和压强分布
图4 压缩过程缸内工质的压强变化
2.活塞有限元分析
(1)应力分析
这里采用与Pro/ENGINEER无缝结合的有限元分析工具Pro/MECHANICA。
将活塞的1/4模型移至Pro/MECHANICA环境下,可以完全利用在Pro/ENGINEER中建立的几何信息。
首先选取热力分析模式(Thermal),设置模型材质(Model Materials),这里选取铝合金AL2014,并加入(Assign)活塞模型中。
根据缸内流体动力学仿真分析得到的结果,可以计算出内燃机一个工作循环内活塞顶面平均温度(这里得到的平均温度为1167K),平均压力(这里将其设为4.5MPa,高于得到的平均压力以提高可靠性),作为表面热力和压力负荷(Surface Load)加入活塞模型的上表面。
设置表面换热边界条件(Surface Convection Condition),并在负荷约束设置中包括指示温度(Prescribed Temperatures)和模型的轴对称(Cyclic Symmetry),至此形成一个完整的有限元热力仿真模型。
分析得到的活塞应力分布,如图5所示。
图5 活塞热力和压力耦合总应力分布
(2)疲劳寿命分析
设置活塞的疲劳寿命极限(Fatigue Life)的期望值(Desired Endurance)为109(即希望内燃机在10亿次循环中不产生疲劳失效)。
在上述的负荷下进行有限元分析,经系统计算后将1×1020作为活塞的疲劳寿命,远大于所设的期望值。
疲劳寿命的分布,如图6所示,
图6 活塞压力疲劳极限对数分布
可见,活塞构型中疲劳寿命最小的、即最“脆弱”部分的疲劳寿命值为109.854,也大于期望值,说明设计的活塞结构完全满足工作需要。
同时,可以看出这种活塞结构中最易产生疲劳失效的部位出现在活塞销座的上表面且靠近连杆小头部分,为改进活塞的结构设计提供了参考。
3.主运动系的仿真分析
将在Pro/ENIGNEER中装配好的发动机装配模型导入多体动力学仿真工具ADAMS环境下,在这个过程中发动机各个零件之间的装配关系是保持不变的。
(1)创建零件材料及约束副
创建活塞零件材料为铝合金,设置密度和弹性模量,同样给连杆、曲轴、气阀和凸轮轴设置材料属性。
使用约束库在两两零件之间创建约束副。
(2)创建对活塞的压力
根据气缸内流体动力学数值仿真结果,利用一个工作循环内的缸内压强数据(因为本文只模拟了压缩过程的气流情况,所以其他冲程的热力参数可参考该类型内燃机的物理试验数据),得到活塞的压力数据。
将该组数据建立一条数据曲线(Data Spline),其中,自变量X表示时间(单位为ns),因变量Y表示气缸内气体压强(单位为105pa),利用建立函数(Building Function)的形式定义对活塞的压力,AKISPL函数由前面建立的曲线数据返回其插值数据,形成连续的压力曲线。
(3)建立测量
由内燃机一个气缸所发出的指示转矩,如公式(1)所示。
(1)
其中,F——作用于活塞上的合力,即气体压力与往复惯性力的代数和;
R——曲轴旋转半径;
φ——曲轴转角;β——连杆摆角。
(4)动态仿真
对模型进行动态仿真,通过测试整个模型或模型的一部分以验证其运动的正确性。
在对模型进行仿真的过程中,各种动力学特性随曲轴转角的变化规律,如图7所示。
图7 活塞组动力学仿真曲线
四、结论
本文从内燃机的样机设计到虚拟试验,完全是在三维可视化数字环境下进行的。
在选定设计条件后利用参数化模型设计软件进行了零件设计和整机装配。
虚拟试验包括了流体试验、结构试验、热力试验以及机械试验。
其中,结构试验和热力试验部分利用有限元仿真工具对内燃机的某些部件(如活塞)进行了分析,得到了零件应力和疲劳强度的分布规律。
流体试验部分利用了计算流体动力学分析工具进行了缸内过程(压缩过程)的流体力学仿真,得到了缸内流场、压力场等的分布和变化规律。
而机械系统试验部分通过多体动力学分析工具对内燃机的主运动系进行了动态仿真试验,得到了所有动力学参数在
内燃机工作时的变化过程。