1冲裁原理
冲压工初级理论考核大纲、复习题.
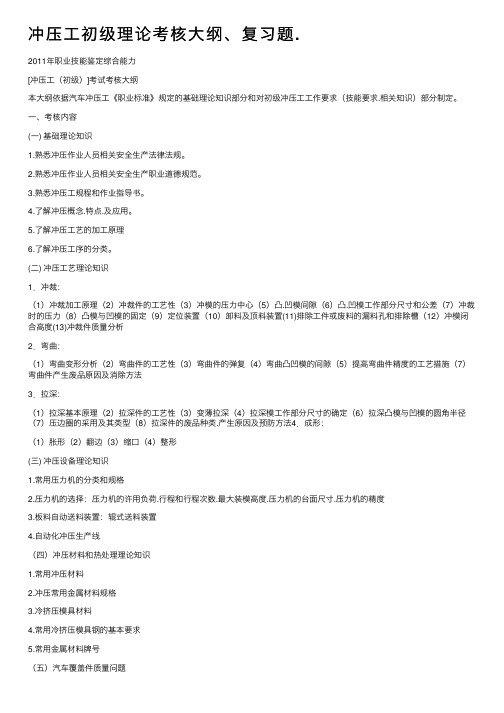
冲压⼯初级理论考核⼤纲、复习题.2011年职业技能鉴定综合能⼒[冲压⼯(初级)]考试考核⼤纲本⼤纲依据汽车冲压⼯《职业标准》规定的基础理论知识部分和对初级冲压⼯⼯作要求(技能要求.相关知识)部分制定。
⼀、考核内容(⼀) 基础理论知识1.熟悉冲压作业⼈员相关安全⽣产法律法规。
2.熟悉冲压作业⼈员相关安全⽣产职业道德规范。
3.熟悉冲压⼯规程和作业指导书。
4.了解冲压概念.特点.及应⽤。
5.了解冲压⼯艺的加⼯原理6.了解冲压⼯序的分类。
(⼆) 冲压⼯艺理论知识1.冲裁:(1)冲裁加⼯原理(2)冲裁件的⼯艺性(3)冲模的压⼒中⼼(5)凸.凹模间隙(6)凸.凹模⼯作部分尺⼨和公差(7)冲裁时的压⼒(8)凸模与凹模的固定(9)定位装置(10)卸料及顶料装置(11)排除⼯件或废料的漏料孔和排除槽(12)冲模闭合⾼度(13)冲裁件质量分析2.弯曲:(1)弯曲变形分析(2)弯曲件的⼯艺性(3)弯曲件的弹复(4)弯曲凸凹模的间隙(5)提⾼弯曲件精度的⼯艺措施(7)弯曲件产⽣废品原因及消除⽅法3.拉深:(1)拉深基本原理(2)拉深件的⼯艺性(3)变薄拉深(4)拉深模⼯作部分尺⼨的确定(6)拉深凸模与凹模的圆⾓半径(7)压边圈的采⽤及其类型(8)拉深件的废品种类.产⽣原因及预防⽅法4.成形:(1)胀形(2)翻边(3)缩⼝(4)整形(三) 冲压设备理论知识1.常⽤压⼒机的分类和规格2.压⼒机的选择:压⼒机的许⽤负荷.⾏程和⾏程次数.最⼤装模⾼度.压⼒机的台⾯尺⼨.压⼒机的精度3.板料⾃动送料装置:辊式送料装置4.⾃动化冲压⽣产线(四)冲压材料和热处理理论知识1.常⽤冲压材料2.冲压常⽤⾦属材料规格3.冷挤压模具材料4.常⽤冷挤压模具钢的基本要求5.常⽤⾦属材料牌号(五)汽车覆盖件质量问题1.破裂(1)不同部位的破裂的原因分析(2)破裂问题的防⽌措施2.起皱:(1)起皱的分类(2)各类起皱的原因分析(3)起皱问题的防⽌措施3.尺⼨精度问题:尺⼨精度(六)冲压安全技术1.冲压⽣产的特点与不安全因素分析2.压⼒机安全装置:(1)压⼒机安全装置应具有的基本功能及分类(2)压⼒机安全控制装置(3)压⼒机安全防护装置3.冲压模具的安全技术:(1)冲模安全技术要求(2)冲模的安全技术装置(3)冲模其他安全措施(4)冲模安全监测装置(5)冲模安装.调试与拆卸中的安全4.冲压⽣产中的⼿⽤⼯具:⼿⽤⼯具和⼿⽤⼯具操作要点5.冲压事故与冲压⽣产环境:冲压事故.冲压⽣产环境⼆.考试题型及题量1.理论(120分钟):单项选择题(40题,共40分)判断题(30题,共30分)简答题(5题,共30分)2.实作(30分钟):考试内容:冲压模具的维护及保养需掌握的技能:(1).冲压压机⼒的安全使⽤⽅法及要求(2).冲压模具的安装⽅法及要求;(3).冲压模具的调整⽅法及要求;(4).冲压模具的维护及保养⽅法要求;(5).能正选择和使⽤冲压模具安装及调试所需辅助物品。
汽车制造工艺冲压工艺
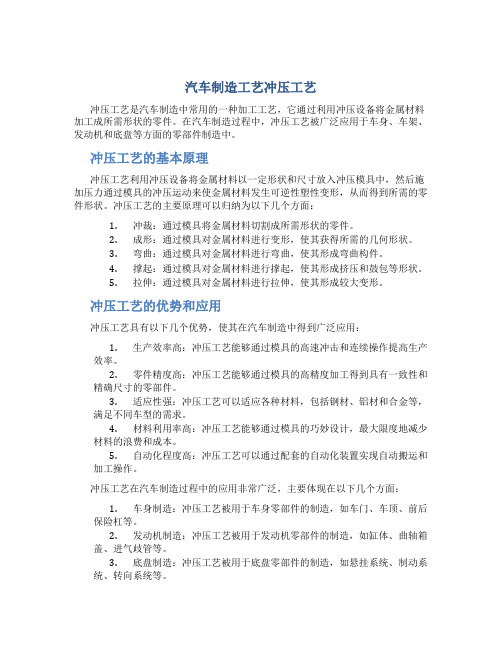
汽车制造工艺冲压工艺冲压工艺是汽车制造中常用的一种加工工艺,它通过利用冲压设备将金属材料加工成所需形状的零件。
在汽车制造过程中,冲压工艺被广泛应用于车身、车架、发动机和底盘等方面的零部件制造中。
冲压工艺的基本原理冲压工艺利用冲压设备将金属材料以一定形状和尺寸放入冲压模具中,然后施加压力通过模具的冲压运动来使金属材料发生可逆性塑性变形,从而得到所需的零件形状。
冲压工艺的主要原理可以归纳为以下几个方面:1.冲裁:通过模具将金属材料切割成所需形状的零件。
2.成形:通过模具对金属材料进行变形,使其获得所需的几何形状。
3.弯曲:通过模具对金属材料进行弯曲,使其形成弯曲构件。
4.撑起:通过模具对金属材料进行撑起,使其形成挤压和鼓包等形状。
5.拉伸:通过模具对金属材料进行拉伸,使其形成较大变形。
冲压工艺的优势和应用冲压工艺具有以下几个优势,使其在汽车制造中得到广泛应用:1.生产效率高:冲压工艺能够通过模具的高速冲击和连续操作提高生产效率。
2.零件精度高:冲压工艺能够通过模具的高精度加工得到具有一致性和精确尺寸的零部件。
3.适应性强:冲压工艺可以适应各种材料,包括钢材、铝材和合金等,满足不同车型的需求。
4.材料利用率高:冲压工艺能够通过模具的巧妙设计,最大限度地减少材料的浪费和成本。
5.自动化程度高:冲压工艺可以通过配套的自动化装置实现自动搬运和加工操作。
冲压工艺在汽车制造过程中的应用非常广泛,主要体现在以下几个方面:1.车身制造:冲压工艺被用于车身零部件的制造,如车门、车顶、前后保险杠等。
2.发动机制造:冲压工艺被用于发动机零部件的制造,如缸体、曲轴箱盖、进气歧管等。
3.底盘制造:冲压工艺被用于底盘零部件的制造,如悬挂系统、制动系统、转向系统等。
4.内饰制造:冲压工艺被用于内饰零部件的制造,如仪表盘、门板、座椅架等。
冲压工艺的发展趋势随着汽车制造技术的不断发展,冲压工艺也在不断创新与改进。
未来冲压工艺的发展主要有以下几个趋势:1.模具技术的创新:通过模具技术的创新,提高冲压工艺的制造精度和生产效率。
冲压模具的基本结构及工作原理完整版
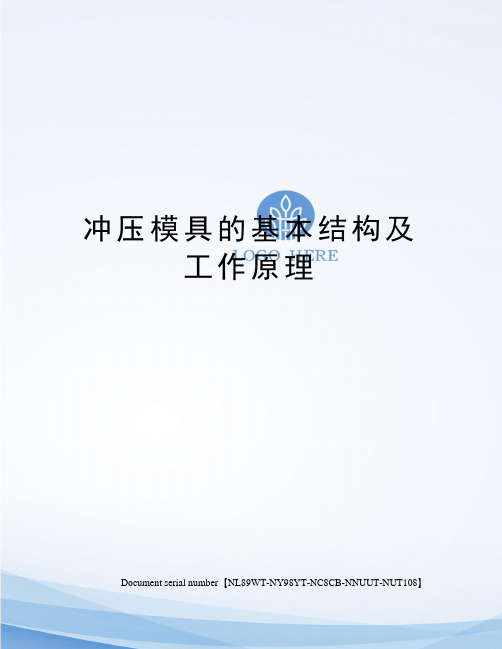
冲压模具的基本结构及工作原理Document serial number【NL89WT-NY98YT-NC8CB-NNUUT-NUT108】冲裁模具的基本结构及工作原理一、冲裁模具按工序组合程度可分为:简单冲裁模、连续冲裁模、复合冲裁模。
(一)简单冲裁模即敞开模?1、定义:它是指在一次冲裁中只完成冲孔或落料的一个工序。
2、简单冲裁模按其导向方式可分为:(1)无导向单工序模它的特点是结构简单,重量轻、尺寸较小、模具制造容易、成本低廉。
但冲模使用安装时麻烦,模具寿命低,冲栽件精度差,操作也不安全。
?无导向简单冲模适用于精度要求不高、形状简单、批景小或试制的冲裁件。
(2)导板式简单冲裁模模精度高、寿命长、使用安装帧、操作安全,.但制造比较复杂。
一般适用于形状较简单、尺寸不大的工件。
(3)导柱式简单冲裁模由于这模具准确可靠,能保证冲裁间隙的均匀,冲裁的工件精度较高、模具使用寿命长而且在冲床上安装使用方便,因此导柱式冲裁模是应用最广泛的一种冲模,适合大批量生产。
(二)连续冲裁模(连续模)?1、连续冲裁模的定义:按一定的先后程序,在冲床的滑块的一次到和中,在模具的不同位置上,完成冲孔,落料导两个的上的冲后工序的冲裁模,又称及进模或跳步模。
2、连续冲裁模的定位原理可分为:导正销定位原理、侧刃定距原理(三)复合冲裁模?1、复合冲裁模的定义:在部床滑块的一次行程中,在冲模的同一工位上同时完成内孔和外形两种的上工序的冲裁模。
2、复合冲裁模按结构可分为:正装式复合模、倒装式复合模二、我们请看看这三种模具的比较表无导向单工序模冲模的上模部分由模、凸模组成,通过模柄安装在冲床滑块上。
下模部分由卸料板、导尺、.凹模、下模座、定位板组成,通过下模座安装在冲床工作台上。
上模与下模没有直接导向关系,靠冲床导轨导向。
导板式简单冲裁模上模部分主要由模柄、上模板、垫板、凸模固定板、凸模组成。
下模部分主要由下模板凹模、导尺、导板、回带式挡料销、托料板组成。
冲裁概述1

第2章冲裁工艺与冲裁模设计> 2.1概述冲裁是利用模具使板料沿着一定的轮廓形状产生分离的一种冲压工序。
它包括落料、冲孔、切断、修边、切舌、剖切等工序,其中落料和冲孔是最常见的二种工序。
落料-----若使材料沿封闭曲线相互分离,封闭曲线以内的部分作为冲裁件时,称为落料;冲孔-----若使材料沿封闭曲线相互分离,封闭曲线以外的部分作为冲裁件时,则称为冲孔。
图2.1.1所示的垫圈即由落料和冲孔二道工序完成。
a)落料b)冲孔图2.1.1 垫圈的落料与冲孔冲裁是冲压工艺的最基本工序之一。
在冲压加工中应用极广。
它既可直接冲出成品零件也可以为弯曲、拉深和挤压等其它工序准备坯料,还可以在已成形的工件进行再加工(切边、切舌、冲孔等工序)。
冲裁所使用的模具叫冲裁模,它是冲裁过程必不可少的工艺装备。
图2.1.2为一副典型的落料冲孔复合模,冲模开始工作时,将条料放在卸料板19上,并由三个定位销22定位。
冲裁开始时,凹模7和推件块8首先接触条料。
当压力机滑块下行时,凸凹模18的外形与凹模7共同作用冲出制件外形。
与此同时,冲孔凸模17与凸凹模18的内孔共同作用冲出制件内孔。
冲裁变形完成后,滑块回升时,在打杆15作用下,打下推件块8,将制件排除凹模7外。
而卸料板19在橡胶反弹力作用下,将条料刮出凸凹模,从而完成冲裁全部过程。
根据冲裁变形机理的不同,冲裁工艺可以分为普通冲裁和精密冲裁两大类。
本章主要讨论普通冲裁。
图2.1.2 落料冲孔复合模1-下模板2-卸料螺钉3-导柱4-固定板5-橡胶6-导料销7-落料凹模8-推件块9-固定板10-导套11-垫板12、20-销钉13-上模板14-模柄15-打杆16、21-螺钉17-冲孔凸模18-凸凹模19-卸料板22-挡料销2.2冲裁变形过程分析为了正确设计冲裁工艺和模具,控制冲裁件质量,必须认真分析冲裁变形过程,了解和掌握冲裁变形规律。
图2.2.1所示是无压边装置的模具对板料进行冲裁时的情形。
常用冲压工艺基本原理

常用冲压工艺基本原理冲压工艺是一种通过冲压设备将金属或非金属材料加工成所需形状的加工方法。
它广泛应用于制造行业中,如汽车制造、航空航天、电子等领域。
常用冲压工艺的基本原理如下:1.冲裁:冲裁是冲压工艺的基础,通过在金属材料中施加剪切力,将材料分离成所需的形状。
冲裁要求冲压设备具有足够的压力和刚度,以确保能够将材料切割成准确的形状,并保持相对平整的边缘。
2.弯曲:弯曲是将金属材料弯曲成所需的形状。
通过将材料置于折弯模具中,并施加压力使其弯曲。
弯曲要求冲压设备具有足够的刚度,以确保能够在材料上施加足够的压力,并保持所需的形状。
3.拉伸:拉伸是将金属材料拉伸成所需的形状。
通过将材料固定在一端,然后通过施加拉力来延长材料并形成所需的形状。
拉伸要求冲压设备具有足够的拉力和刚度,以确保能够在材料上施加足够的拉力,并保持所需的形状。
4.成形:成形是将金属材料压制成所需的形状。
通过在材料表面施加压力,使其逐渐变形成所需的形状。
成形要求冲压设备具有足够的压力和灵活性,以确保能够在材料上施加足够的压力,并保持所需的形状。
5.切削:切削是将金属材料切割成所需形状的方法。
通常采用冲床、剪切机等设备,在材料上施加切割力,将材料切断成准确的形状。
切削要求冲压设备具有足够的切削力和刚度,以确保能够将材料切割成准确的形状,并保持相对平整的边缘。
6.模具设计:模具是冲压工艺中不可缺少的工具,它影响着冲压加工的质量和效率。
模具设计要求考虑材料的物理特性、形状复杂程度以及生产要求等因素,以确保能够精确加工出所需的形状,并保持高效的生产速度。
综上所述,常用冲压工艺的基本原理包括冲裁、弯曲、拉伸、成形、切削和模具设计等。
这些原理在冲压加工中起着重要的作用,决定了加工质量和效率。
因此,工程师在进行冲压加工时需要充分理解和应用这些基本原理,以确保能够获得满足生产要求的加工零件。
第2章-冲裁工艺

B类尺寸,随凹模磨损,尺寸↓:
C类尺寸,随凹模磨损,尺寸不变:
34
2.3 冲裁模刃口尺寸计算
3)冲孔
第 2 章
冲
冲孔件
裁
工
艺
A类尺寸,随凸模磨损,尺寸↑:
B类尺寸,随凸模磨损,尺寸↓: C类尺寸,随凸模磨损,尺寸不变:
冲孔凸模刃口轮廓
35
2.3 冲裁模刃口尺寸计算
4)总之
第
2
第
2
非圆形工件x值
圆形工件x值
材料
章
厚度
1
0.75
0.5
0.75
0.5
t/mm
工 件 公 差 Δ/mm
冲
裁
1 <0.16 0.17~0.35 ≥0.36 <0.16 ≥0.16
工
1~2 <0.20 0.21~0.41 ≥0.42 <0.20 ≥0.20
艺
2~4 <0.24 0.25~0.49 ≥0.50 <0.24 ≥0.24
1、冲裁时的力态分析
第 普通冲裁示意图
2
模具工作部分有两个基
章
本特征:
冲
凸、凹模有锋利刃口
裁
凸、凹模有间隙
工
C - 单面间隙
艺
Z - 双面间隙
冲裁板料受力图
6
2.1 冲裁工艺分析
第
2
变形区位置
章
冲
裁
工
艺
变形区的应力状态
7
2.1 冲裁工艺分析
2、冲裁变形过程
第
2
1)弹性变形阶段
第2章 冲裁工艺
第
2.1 冲裁工艺分析
冲裁

图纸规定 的公差范 围内
外形满足图纸 要求;表面平 直,即拱弯小
1、冲裁件断面质量及其影响因素
断面特征
圆角带 a:刃口附近的材料产生弯曲和伸长变形。
光亮带 b:塑性剪切变形。质量最好的区域。 断裂带 c:裂纹形成及扩展。 毛刺区 d:间隙存在,裂纹产生不在刃尖,毛刺不可避免。
此外,间隙不正常、刃口不锋利,还会加大毛刺。
0.34
mm
39.7500.085 mm
c凹
(35
0.75
0.34)
0
1 4
0.34
mm
34.7500.085 mm
第二类尺寸:磨损后减小的尺寸
d凹
(22
0.14
0.75
0.28)0
1 4
0.28
mm
22.0700.070 mm
第三类尺寸:磨损后基本不变的尺寸
Z 2t h0 tan
2.经验确定法
2t1
h0 t
tan
较小间隙值(表2.3.2)
较大间隙值(表2.3.3)
(2)经验确定法
对断面质量和尺寸要求高的工件,应选 取小的间隙值。
对于精度要求不高的工件,则应尽可能 采用大间隙以降低冲裁力,提高模具寿 命。
冲裁
冲裁:利用模具使板料产生分离。 冲裁包括:落料、冲孔、切口、剖切、 修边。
冲裁:利用模具使板料沿着一定的轮廓形状产生分离的一种
冲压工序。 基本工序:落料和冲孔。既可加工零件,也可加工冲 压工序件。
冲裁模:冲裁所使用的模具叫冲裁模,它是冲裁过程必不可少
冲裁模具的基本结构及工作原理

•冲裁模具的基本结构及工作原理一、冲裁模具按工序组合程度可分为:简单冲裁模、连续冲裁模、复合冲裁模。
(一)简单冲裁模即敞开模1、定义:它是指在一次冲裁中只完成冲孔或落料的一个工序。
2、简单冲裁模按其导向方式可分为:(1)无导向单工序模它的特点是结构简单,重量轻、尺寸较小、模具制造容易、成本低廉。
但冲模使用安装时麻烦,模具寿命低,冲栽件精度差,操作也不安全。
无导向简单冲模适用于精度要求不高、形状简单、批景小或试制的冲裁件。
(2)导板式简单冲裁模模精度高、寿命长、使用安装帧、操作安全,.但制造比较复杂。
一般适用于形状较简单、尺寸不大的工件。
(3)导柱式简单冲裁模由于这模具准确可靠,能保证冲裁间隙的均匀,冲裁的工件精度较高、模具使用寿命长而且在冲床上安装使用方便,因此导柱式冲裁模是应用最广泛的一种冲模,适合大批量生产。
(二)连续冲裁模1、连续冲裁模的定义:按一定的先后程序,在冲床的滑块的一次到和中,在模具的不同位置上,完成冲孔,落料导两个的上的冲后工序的冲裁模,又称及进模或跳步模。
2、连续冲裁模的定位原理可分为:导正销定位原理、侧刃定距原理(三)复合冲裁模无导向单工序模上模部分主要由模柄、上模板、垫板、凸模固定板、凸模组成。
下模部分主要由下模板凹模、导尺、导板、回带式挡料销、托料板组成。
这种模具的特点是上模通过.凸模利用导板上的孔迸行导向,导板兼作卸料板。
工作时凸模始终不脱离导板.以保证模具导向精度。
因而,要求使用的压力机行程不大于导板厚度。
这种冲模的工作过程是:条料沿托料板、导尺从右向左送科,首次冲裁时使用临时挡料销定位,首次冲裁以后再往前送料,搭边越过活动挡料销后.再反向拉拽条料,使挡料销后端面抵住条料搭边进行定位,凸模下行实现冲裁。
导柱式简单冲裁模。
第二章 冲裁工艺及冲裁模设计

普通冲裁件的断面情况:
普通冲裁变形所得到的冲裁件端面常带有一定的锥度,并且 都有明显的区域特征,不同的是各区域的大小占整个断面的比例 不一样。 光亮带 产生于塑性变 圆角带
发生在弹性变形后 期和塑性变形初期, 由金属的弯曲和拉伸 而形成。其大小与材 质有关。
形阶段,断面主 要受剪应力和压 应力作用。断面 平整、光滑。通 常占整个区域的 1/2~1/3,与材质 有关。
第二章 冲裁工艺及冲裁模设计
普通冲裁原理
冲裁间隙 冲裁模刃口尺寸的计算(重点) 冲裁件的排样(重点) 冲压工艺力(重点) 压力中心的计算(重点) 冲裁件的工艺性 冲裁模的基本形式及特点 冲裁模主要零、部件结构和设计(重点) 冷冲模的设计程序(重点)
2.1 普通冲裁的基本原理
冲模刃口尺寸、制造公差的大小主要取决于 冲裁件的形状和精度。
刃口尺寸的计算方法
冲模刃口 尺寸公差带 分析图
1. 凸、凹模分开加工时的刃口计算
δd+δp≤Zmax-Zmin 运用该方法必须使模具的制造公差与间隙满足 或 δp= 0.4(Zmax-Zmin) δd= 0.6(Zmax-Zmin)
根据刃口尺寸的计算原则,分开加工时凸、凹模刃口尺寸 的计算公式如下:
推件力Pd: Pd = KdP
冲压工艺力的计算:
(它是选取压力机吨位的主要依据,具体计算要考虑模具的结构型式) 采用刚性卸料自然漏料方式:Pz≥P+Pt = P +nKtP 采用刚性打料、弹性卸料的倒装结构方式:Pz≥P + Px = P + KxP 采用弹性卸料和弹性顶料方式:Pz≥P + Px + Pd = P + KxP + KdP 采用弹性卸料自然漏料方式:Pz≥P + Px + Pd = P + KxP + nKdP (选择压力机时,压力机的公称压力N必须大于或等于Px)
冲裁工序与模具

适用:大批量生产小型冲压件
(3)复合模 复合模:在一套模具上仅设置一个工位,在此工位上可同时 完成俩个以上的模具 设计难点:如何在同一工作位置上合理地布置好几对凸凹模 结构上的主要特征 优点:生产率高,冲裁件的内孔与外缘的相对位置精度高, 板料的定位精度的要求比级进模低,冲模的轮廓尺寸较小。 缺点:结构复杂,制造精度要求高,成本高 适用:生产批量大,精度要求高的冲裁件
(2)级进模:级进模是一种工位多,效率高的冲模.整个冲件的成 形是在连续过程中逐步完成的. 级进模分为俩种:1.用导正销定位的级进模2.侧刃定距的级进 模(有双侧刃定距的冲孔落料级进模和侧刃定距的的弹压导板 式级进模) 优点:级进模比单工序模生产率高,减少了模具和设备的数量, 工件精度较高,便于操作和 缺点:级进模轮廓尺寸较大,制造叫复杂,成本较高。
与连续模比较,复合模有以下结构特点:
(1)板料定位装的典型类型
冲裁模三大典型(根据冲裁模工位和工序来分 类): (1)单工序模(又简称单模) (2)级进模 (3)复合模
(1)单工序模:在压力机一次行程内只完成一个 冲压工序的冲裁模(而且其只设有一个工位) 根据它的工序分不同分为:1.落料模2.冲孔模 落料模的三种类型:1.无导向的单工序落料模2. 导版式的单工序落料模3.导柱式单工序落料模 冲孔模的三种类型:1导柱式冲孔模2.导板式侧 面冲孔模3.斜楔式水平冲孔模
冲裁工序与模具
成型131401班 钟瑞敏 201314030135
(一)冲裁工序
冲裁的原理:冲裁是利用凸模和凹模上的刃口,将 板料分离为两部分的冲压工序。
根据冲裁目的不同,把冲裁工序 分为: (1)落料工序 (2)冲孔工序
冲裁变形方式与变形件
(二)冲裁件的工序安排
第二章 冲裁
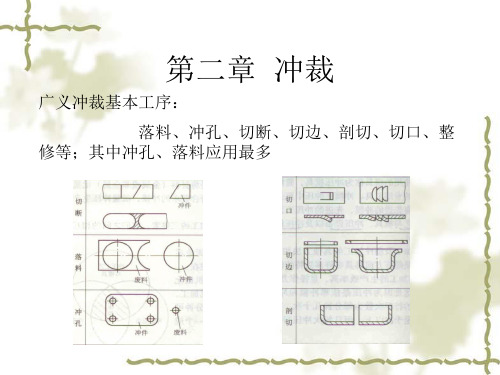
尺寸精度影响因素 一般冲裁件能达到的尺寸精度比模具的精度
1. 模具制造精度 低一到三级。
2. 材料性质及模具结构 冲裁件会发生回弹现象,从而影响 其精度,较软的材料弹性变形小,冲裁后回弹小,精度较高, 在模具上增加压板料和顶件器会减小回弹值,提高冲件精度。
3. 冲裁间隙 间隙适当时,材料在较纯的剪应力下分离,间隙 较大时,材料除受到剪切外,还产生较大的拉伸应力与弯曲变 形,冲孔件会大于凸模尺寸,落料件会小于凹模尺寸;间隙较 小时,材料会受到较大的挤压作用,冲孔件会小于凸模尺寸, 落料件会大于凹模尺寸。
3 使凸、凹模沿封闭轮廓线冲裁,提高零件质量和模具寿命。
搭边值的确定: 根据经验定,搭边值不可过小也不可过大,过大浪费材料,过 小起不到搭边作用,还可能被拉入凸凹模间隙中,使模具刃口损坏。
搭边值确定取决于材料种类、厚度、冲裁件大小、轮廓形状等,材 料越厚、硬度越低、冲裁件尺寸越大、形状越复杂,合理搭边值越大。 一般搭边值由经验确定,可以查表。 送料步距: 条料在模具上每次被送进的距离,步距计算公式为: A = D + a1
图2.9 模具间隙
Z 2t (1
h0 t
)tg
(2—4)
上式中: h0——产生裂纹时凸模的压入深度(mm); t ——材料厚度(mm); β —— 最大切应力方向与垂线之间的夹角(裂纹方向角)。
β、 h0与材料性质有关,可以查表得到。
2 查表法
3 经验记忆法
Z = mt
Z:合理冲裁间隙 t: 板料厚度
图2.2 冲裁件塑性变形
三 断裂分离阶段 当板料应力达到抗剪切强度后,凸模继续下压,凸、凹模口 部产生裂纹并不断扩展,当上下裂纹重合时,板料发生分离。当 凸模继续下行时,已分离的板料被推出,完成整个冲裁过程。
常用冲压工艺基本原理

常用冲压工艺基本原理冲压工艺是现代工业生产中常见的金属成形方法之一,其基本原理是通过将金属板材置于压力机上,依靠冲压模具对金属板材进行冲压、拉伸、弯曲、剪切等操作,从而使其形成所需的零件或产品。
以下是常用冲压工艺的基本原理。
1.冲裁:冲裁是冲压过程中最常见的一种工艺,它通过模具上的切割刀具将金属板材切割成所需形状的零件。
冲裁工艺能够快速高效地生产出一大批形状相同的零件,适用于大批量生产。
2.拉伸:拉伸是指将金属板材置于模具中,在压力机的作用下,使金属板材产生拉伸变形,从而使其成为带有凹陷或凸起的零件。
拉伸工艺常用于制造深凹型零件,如汽车车身、洗衣机筒等。
3.弯曲:弯曲是将金属板材置于模具中,在压力机的作用下,使其产生塑性变形,从而使其成为带有曲线形状的零件。
弯曲工艺常用于制造弧形或曲线形状的零件,如门把手、管道弯头等。
4.折弯:折弯是将金属板材置于模具中,在压力机的作用下,将金属板材弯曲成所需的角度,从而使其成为带有角度的零件。
折弯工艺常用于制造角度零件,如梁、角铁等。
5.压铸:压铸是将熔化的金属注入到模具中,经过一段时间冷却后取出。
压铸工艺能够制造出复杂形状的零件,并具有高精度和高表面质量,适用于生产要求较高的零件。
6.制模:制模是冲压工艺中不可或缺的一个环节,其主要目的是根据产品的要求制造出适用的模具。
制模包括模具的设计、制造和调试过程,通过模具的精确度和准确性来保证冲压过程中零件的质量和精度。
7.板料分配:板料分配是冲压工艺中非常重要的一环,它决定了金属板材的利用率和材料的利用率。
合理的板料分配能够最大限度地减少金属板材的浪费,提高产品的生产效率和经济效益。
总之,冲压工艺基本原理是通过模具对金属板材进行冲压、拉伸、弯曲、剪切等操作,从而使其成为所需的零件或产品。
通过合理的制模和板料分配,冲压工艺能够快速高效地生产出形状复杂、精度高的零件,广泛应用于汽车、家电、机械设备等领域。
冲裁的工作原理范文

冲裁的工作原理范文冲裁(Stamping)是一种常见的金属加工方法,其工作原理简单描述为在上、下冲裁模具的作用下,将金属板材通过机械或液压力量施加在金属板表面上,使其表面产生塑性变形,从而完成所需的形状。
下面将详细介绍冲裁的工作原理。
冲裁过程主要包括四个阶段:进料、定位、加工和退料。
先将金属板材定位到冲裁模具的定位孔中,然后通过外界力的作用使金属板材与冲裁模具之间产生大的变形,完成冲裁过程。
具体的工作原理如下:1.进料:首先将待冲裁的金属板材放入冲床的进料区。
进料是保证冲裁工艺能够连续进行的关键步骤。
在进料过程中,金属板材会被夹紧并沿着预定的路径进入冲裁模具的工作区域。
2.定位:一旦金属板材进入工作区域,它需要被准确而稳定地定位到冲裁模具的工作位置。
这是为了确保冲裁的准确性和一致性。
通常,冲裁模具上会设置一系列的定位针或定位孔,用于将金属板材正确安排在所需位置上。
3.加工:加工阶段是整个冲裁过程最重要的一步。
金属板材将被夹紧并通过冲床的压力施加在冲裁模具上,产生塑性变形。
冲裁模具上通常包含两部分:上模和下模。
当冲床施加力量时,上模会向下推动,将金属板材压到下模上。
下模上通常设置了一定形状的凹槽或凸台,用于使金属板材产生所需的形状。
4.退料:加工完成后,需要将冲裁好的金属零件从模具中取出。
这个过程通常通过顶出装置完成,顶出装置会通过一定的力量将金属零件从模具上顶出,并将其传送到下一个工作站点或接收区域。
退料过程要确保金属零件完整无损。
总的来说,冲裁工作原理主要是通过施加力量使金属板材产生塑性变形,以完成所需的形状。
冲裁过程需要准确的定位、合适的冲裁模具和适量的力量控制,以确保冲裁过程的稳定性和零件质量的一致性。
冲裁是一种高效、精准的金属加工方法,在汽车制造、家电制造等行业得到广泛应用。
冲压模具设计

冲压模具设计第2章冲裁⼯艺及冲裁模具设计冲裁是指利⽤模具在压⼒机上使板料产⽣分离的冲压⼯艺。
冲裁可直接冲出所需形状的零件,也可为其它⼯序制备⽑坯。
冲裁时所使⽤的模具称为冲裁模。
冲裁⼯艺的种类很多,常⽤的有落料、冲孔、切断、切边、切⼝等,其中落料和冲孔应⽤最多。
从板料上冲下所需形状的零件(或⽑坯)称为落料;在零件(或⽑坯)上冲出所需形状的孔(冲去部分为废料)称为冲孔。
落料与冲孔的变形性质完全相同,但在进⾏模具设计时,模具尺⼨的确定⽅法不同,因此,⼯艺上必须作为两个⼯序加以区分。
冲制外形D的冲裁⼯序为落料,如图2.1(a)所⽰;冲制内孔d的⼯序为冲孔,如图2.1(b)所⽰。
根据冲裁的变形机理不同,冲裁⼯艺可以分为普通冲裁和精密冲裁两⼤类。
精密冲裁断⾯较光洁,精度较⾼,但需专门的精冲设备与模具。
2.1 冲裁过程分析2.1.1 冲裁原理冲裁变形过程,如图2.2所⽰,⼤致可分为三个阶段:1.弹性变形阶段如图2.2(a)所⽰,当凸模下压接触板料时,材料将产⽣短暂的、轻微的弹性变形。
此时如果提升凸模,变形将完全消失。
2.塑性变形阶段如图2.2(b)所⽰,凸模继续下压,板料变形区的应⼒将继续增⼤。
当应⼒状态满⾜屈服极限时,材料便进⼊塑性变形阶段。
这⼀阶段突出的特点是材料只发⽣塑性流动,⽽不产⽣任何裂纹,凸模继续切⼈板料,同时将板料的下部挤⼊凹模孔内。
3.断裂分离阶段图2.1 垫圈冲裁中的落料与冲孔图2.2(c)、(d)、(e)表⽰了断裂分离的全过程,其中图(c)表⽰当凸模切⼊板料达到⼀定深度时,在凹模侧壁靠近刃⼝处的材料⾸先出现裂纹。
这表明塑性剪切变形的终⽌和断裂分离的开始。
图(d)表⽰裂纹发展与贯通的情形。
图(e)表⽰冲裁结束时板料被完全分裂分离的情形。
被冲⼊孔的⼀块料在落料时为⼯件,冲孔时为废料。
留在凹模⾯上的材料在冲孔时为⼯件,落料时为废料。
普图2.2 冲裁变形过程及冲裁件剪切断⾯(a)弹性变形(b)塑性变形(c)出现裂纹(d)裂纹贯通(e)板料完全断裂分离(f)剪切断⾯l⼀凸模2⼀板料3⼀凹模4⼀冲孔为⼯件,落料为废料5⼀落料为⼯件,冲孔为废料通冲裁件的剪切断⾯状况如图2.2(f)所⽰,其精度⼀般在IT10级以下,表⾯粗糙度Ra可达3.2 ~50µm。
第三章冲 裁
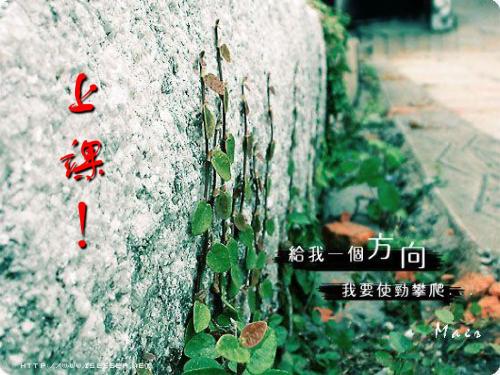
冲压工艺及冲模设计—王志刚
第三章 冲 裁
7
第十节 精密冲裁
第 二、 精密冲裁的工艺方法 三 2、光洁冲裁
1)小间隙圆角刃口冲裁
章
小间隙圆角刃
冲 口冲裁 加强了冲裁
区的静水压,起到
裁 了抑制裂纹的作用
适用于塑性较好的材料, 如软铝 、紫铜、软黄铜、 05F和 08F等。制件公差可达IT11~8级,粗糙度Ra可达1.6~0.4μm。但冲 裁力比普通时冲裁力大50%左右。
1
第上
三
章课 冲!
裁
冲压工艺及冲模设计—王志刚
2
第
三
章
冲
第三章 冲 裁
裁
第十节 精密冲裁
一、 精密冲裁概述
二、 精密冲裁的工艺方法
冲压工艺及冲模设计—王志刚
第三章 冲 裁
3
第十节 精密冲裁
第 一、 精密冲裁概述
三
精密冲裁属于无屑加工技术,是在普通冲压技术基础上发
展起来的一种精密冲裁方法,简称精冲。
11
第十节 精密冲裁
第 小结:
三 一、 精密冲裁概述
章
1、精冲的工作原理及过程
冲
2、精密冲裁的工艺特点
二、 精密冲裁的工艺方法
裁
1、整修
2、光洁冲裁
3、往复冲裁(上、下冲裁)
4、对向凹模冲裁
带强力齿圈压板的精密冲裁
冲压工艺及冲模设计—王志刚
12
第
三
章 冲
下课 !
裁
冲压工艺及冲模设计—王志刚
章
特点:
冲
它能在一次冲压行程中获得比普通冲裁零件尺寸精度高、冲
冲裁模具工作原理

冲裁模具工作原理
冲裁模具是一种用于冲压和裁剪材料的工具,它的工作原理可以简述如下:
1. 材料进料:待冲裁的材料首先被送入模具的进料位置。
材料通常以卷板的形式供应,通过进料系统将其逐段地送入模具。
2. 切割操作:一旦材料被放置到模具的工作区域,冲裁模具的上下部分开始运动,使得切割刃进入材料并将其裁剪为所需的形状。
切割刃通常以模具的一部分或全部上下模板的形式存在。
3. 冲裁力:在切割过程中,冲裁模具会施加冲裁力以确保切割刃能够顺利穿透材料。
冲裁力的大小通常取决于材料的强度和厚度。
4. 材料去料:完成切割后,冲裁模具的上下部分分开,允许刚刚切割的零件从模具中取出。
通常会有一个去料系统,以使得零件能够有效地离开模具。
5. 循环重复:上述步骤会不断重复,直到所有的材料被冲裁完成。
总的来说,冲裁模具通过上下模具的运动、切割刃的进入和负责施加冲裁力的动作,将材料裁剪成所需的形状。
这种工具在多种工业领域中得到广泛应用,例如汽车制造、电子设备制造等。
冲裁模与拉深模的工作原理

冲裁模与拉深模的工作原理冲裁模和拉深模是两种常见的金属加工模具,常用于冲压和成型工艺中。
它们的工作原理和应用场景有一些不同,下面将分别对冲裁模和拉深模进行详细的解释。
一、冲裁模的工作原理:冲裁模是一种用于将金属板材冲切成所需形状的模具。
它由上模和下模两部分组成,其中上模是固定在机床上的,下模则是安装在工作台上的可移动模具。
冲裁模的工作原理是通过上下模之间的闭合与分离来实现金属板材的切割。
具体工作步骤如下:1. 将金属板材放置在工作台上,并对准冲裁模的切割区域。
2. 启动机床,使上下模靠近。
上模通过传动机构进行运动,下模则通过电动机、液压缸等动力装置进行运动。
3. 上下模闭合,形成一定的压力。
上模上通常会安装有冲切刀具,下模上则有腔型凸台。
4. 下模固定,上模快速下压,将刀具对准金属板材进行冲切。
5. 上模迅速恢复原位,分离上下模。
此时,完成了对金属板材的冲切。
可重复操作来实现批量冲切。
冲裁模适用于金属板材的冲切加工,广泛应用于汽车、电子、家电等行业中。
其工作原理简单、加工效率高,可实现快速、准确的金属板材切割,被广泛应用于各种中小批量生产情况。
二、拉深模的工作原理:拉深模是一种用于将金属板材进行拉伸成所需形状的模具。
它也分为上模和下模两部分,上模是固定在机床上的,下模则是可以移动的模具。
拉深模的工作原理是通过上下模之间的闭合与分离来完成金属板材的拉伸成型。
具体工作步骤如下:1. 将金属板材放置在工作台上,并对准拉深模的拉伸区域。
2. 启动机床,使上下模靠近。
上模通过传动机构进行运动,下模则通过电动机、液压缸等动力装置进行运动。
3. 上下模闭合,形成一定的压力。
上模上通常会安装有顶针或顶升板,下模上则有深拉模腔及拉伸柱。
4. 上模下压,顶针或顶升板受到压力向下拉伸,同时下模也向下压,将金属板材拉深成模具所需形状。
5. 上模迅速恢复原位,分离上下模。
此时,完成了对金属板材的拉深成型。
可重复操作来实现批量生产。
冲裁模工作原理
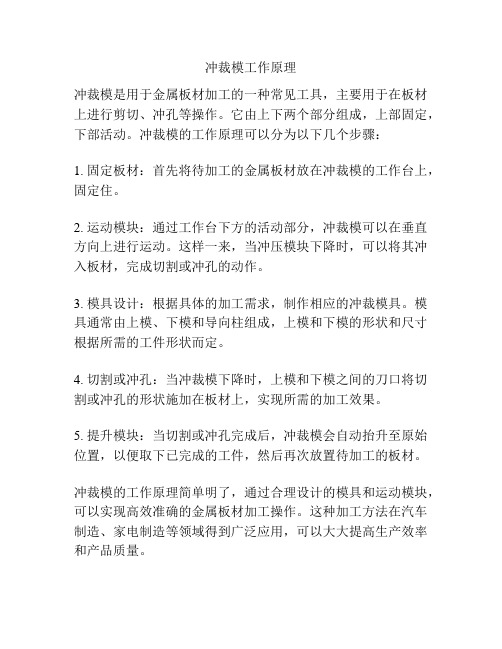
冲裁模工作原理
冲裁模是用于金属板材加工的一种常见工具,主要用于在板材上进行剪切、冲孔等操作。
它由上下两个部分组成,上部固定,下部活动。
冲裁模的工作原理可以分为以下几个步骤:
1. 固定板材:首先将待加工的金属板材放在冲裁模的工作台上,固定住。
2. 运动模块:通过工作台下方的活动部分,冲裁模可以在垂直方向上进行运动。
这样一来,当冲压模块下降时,可以将其冲入板材,完成切割或冲孔的动作。
3. 模具设计:根据具体的加工需求,制作相应的冲裁模具。
模具通常由上模、下模和导向柱组成,上模和下模的形状和尺寸根据所需的工件形状而定。
4. 切割或冲孔:当冲裁模下降时,上模和下模之间的刀口将切割或冲孔的形状施加在板材上,实现所需的加工效果。
5. 提升模块:当切割或冲孔完成后,冲裁模会自动抬升至原始位置,以便取下已完成的工件,然后再次放置待加工的板材。
冲裁模的工作原理简单明了,通过合理设计的模具和运动模块,可以实现高效准确的金属板材加工操作。
这种加工方法在汽车制造、家电制造等领域得到广泛应用,可以大大提高生产效率和产品质量。
- 1、下载文档前请自行甄别文档内容的完整性,平台不提供额外的编辑、内容补充、找答案等附加服务。
- 2、"仅部分预览"的文档,不可在线预览部分如存在完整性等问题,可反馈申请退款(可完整预览的文档不适用该条件!)。
- 3、如文档侵犯您的权益,请联系客服反馈,我们会尽快为您处理(人工客服工作时间:9:00-18:30)。
1.作者 : 徐煒炯
2.出版社 : 中國輕工業出版社 3.黃田菜市場南“ 恆
麗 書 店 ”有售
4 此系列課均為必修課;前后知識連貫性強,無故缺席 者 一律 回
鍋
5.授課時 :約30小時 6.現在開時學習“沖裁原理”
沖壓概述
定義:
基于金屬塑性變形,利用沖模對板料金屬進行加工
以得到所需要的零件形狀和尺寸
力學特性和晶間結構來講 沖裁時板料變形區的應力與應變
拉應力
剪切應力
分類:
修模卡 沖裁 :是材料分離工序
彎曲 拉深 從廣義上講,沖裁可分為沖孔,落料,切口,剖切等; 從變形機理上講,沖裁可分普通沖裁和精密沖裁
沖裁分離過程
上模端部下邊 的Biblioteka 料開始彎曲彈 性 形 變 階 段
間隙愈大,彎曲和上翹愈嚴重
下模刀口上邊 的材料開始
上翹
沖裁分離過程
塑 性 變 形 階 段
1.上模繼續下行
光亮帶產生于塑性變形階段,當凸模擠入
光 亮 帶
板料,壓應力占主導地位,壓應力起到了陰 止減小金屬晶間變形的作用,增強了金屬的 塑性,能使材料在塑剪情況下進行分離,所以 在斷面上形成較光潔平整的光亮帶,這個區 域表面光潔,並且與板料平面垂直,是斷面質 量最佳的一段.
1.斷裂帶產生于沖裁變形后期的剪裂階段.
相遇時,斷面分離,產生粗糙的斷裂帶
普通沖裁件的斷面特征
斷 裂 帶 光 亮 帶
毛 刺
塌角帶
圓 角 帶 也 叫 塌 角 帶
1.這個區域發生在彈性變形后期和塑性變形開 始階段.
( )
2.由於板料產生拉伸.彎曲變形,牽連到附近材料參 與變形,在彈性變形階段形成初始塌角
3.進入塑性變形階段,初始塌角變成永久性塌角,
材料內部應力增大到屈服極限
進入塑性變形階段
2. 拉應力和彎矩增大
變形區材料開始硬化
刃口 附近材料出現裂紋 3.裂紋的出現標示塑性變形階段結束 4.間隙的大 小直接影響切斷面的質量(詳見下一張).
沖子
刀口
間隙過小 合適 間隙過大
斷裂帶
光亮帶
圓角帶
沖裁分離過程
斷裂分離階段 材料上,下面的微裂紋向內部延伸至
斷 裂 段
2.拉應力增大
金屬晶界破坏,原子層分離 金屬縴維被拉斷
產生微觀裂紋
粗糙斷面形成
3.斷裂區粗糙,並帶有錐度,質量較差
1. 從沖壓變形原理上講,毛刺的產生是不可避免的;
毛 刺 區
間隙合適時,毛刺的高度很小.
2.產生微裂紋時即產生了初始毛刺.
3.材料分離時,毛刺將進一步拉長,初始毛刺變為永 久性毛刺.
影響斷面四區域形狀的因素
1.毛刺材料的種類 : 塑性好則光亮帶大,斷裂帶小;塌角大,毛刺高.
2. 沖裁條件 : 刃口間隙----間隙小,光亮帶大高; 刃口形狀 刃口鋒利程度
注 :獲得較寬光亮帶的辦法 消除或抑制拉應力的影響,使變形區處于三向壓 應力狀態,具有較強的靜水壓效應
(精密沖裁的理論依據)