装配车间损失工时管理规范(含表格)
损失工时管理办法
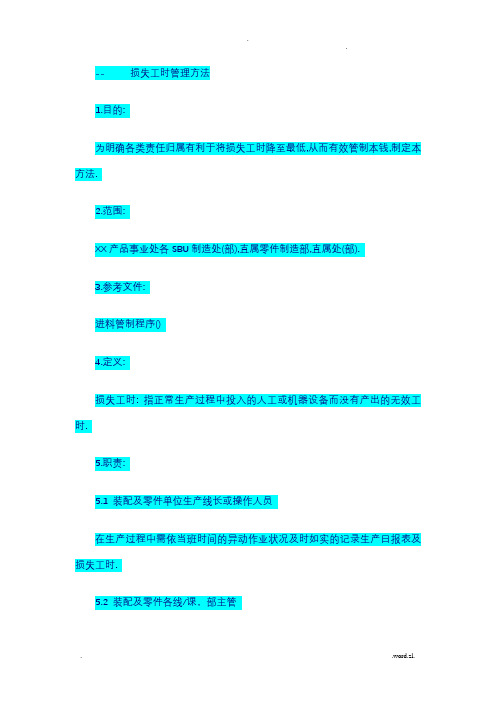
--损失工时管理方法1.目的:为明确各类责任归属有利于将损失工时降至最低,从而有效管制本钱,制定本方法.2.范围:XX产品事业处各SBU制造处(部),直属零件制造部,直属处(部).3.参考文件:进料管制程序()4.定义:损失工时: 指正常生产过程中投入的人工或机器设备而没有产出的无效工时.5.职责:5.1 装配及零件单位生产线长或操作人员在生产过程中需依当班时间的异动作业状况及时如实的记录生产日报表及损失工时.5.2 装配及零件各线/课,部主管5.2.1 负责确认生产日报表,损失工时填写的正确性.5.2.2 安排及时将生产日报表的详细细真实数据输入进IEPCCU生产绩效系统.5.3 产品处IE5.3.1 抽查生产日报表及损失工时损失工程填报的正确性.5.3.2 BY SBU或损失类别统计损失工时,针对损失工时状况综合分析,呈报BU 及SBU各级主管.6.内容6.1 依工令换线:6.1.1 不同工令,不同系列或不同POS产品换线依IE所公布换线工时计.6.1.2 同系列同POS产品换线依IE所公布换线工时50%计.以上由各SBU制造部签认吸收.6.1.3 由于急单插入造成二次上线,可加报一次换线工时,由提出单位签认吸收因漏排或排配不当造成,由责任单位签认吸收因物料损耗超过标准引重复换线的不可加报换线工时.6.1.4 机器设备故障:损失工时=故障时间*受影响人数*30%故障时间以线长通知生技时间为起点,IPQC确认质量合格为终点,并由生技记录在维修记录上.受影响人数指故障机台,治工具(含)后工站排配表受影响人员.损失工时由生技课签认吸收.6.2 新产品量试:6.2.1 新产品首次生产无效产出者:损失工时=投入工时实际发生之工时由制工课/装配制造部各吸收50%.(促进操作者缩短学习时间).6.2.2 新产品首次生产,有效产出者:损失工时=投入工时-标准工时*量试产量由制工课/装配制造部各吸收50%.6.2.3 新产品依工令第二次生产:损失工时=标准工时*实际产出数量*40%由制工课/装配制造部各吸收50%.6.3 新人训练:6.3.1 新开生产线/新开生产线成立15(含)天均适用:损失工时=投入工时*人数*15%6.3.2 新进员工(以三天计):损失工时=投入工时*新进人数*30%由装配制造部认吸收为装配培训,促其培养部门独立经营精神.6.4 支持其它单位:6.4.1 支持直接生产单位a. 同一SBU内部支持由被支持单位直接计入投入(投入=支持时间*支持人数),支持单位不计投入,支持及被支持单位均不得计损失工时.b. 跨SBU支持,支持及被支持单位均不得计损失工时,但需另外填写“SSBU 制造本钱转嫁单〞.6.4.2 支持间接单位依实际发生的时间计算,由被支持单位签认吸收(支持单位计投入):损失工时=支持工时*支持人数6.5 重工6.5.1 成品FQC判NG,直接回原生产线重工,并计入损失工时,损失工时不转嫁:他线重工,按支援计,被支援线别须计投入,但不得计入损失.6.5.2 成品判OK,客户退货或库存重工(原因同客户退货), 重工线别计损失工时.6.5.3 成品,半成品由于工程变更导致的损失工时依实际发生时间计.提出变更由提出单位吸收.客户提出可转嫁者转嫁客户,不可转嫁者制工签认,以上重工可吸收工时,签认时须注明原因.6.6 特采6.6.1 来料合格,制成的成品特采出货后,客户退货所造成的损失工时由制工/品管各吸收20%,装配制造部吸收60%.6.6.2 来料特采后,制成的成品特采出货后,客户退货所造成的损失工时(因来料特采造成的) 由特采申请单位签认,外购者转厂商吸收,自制者,责任单位吸收70%,品管,制工各吸收15%.6.7 待料依实际发生时间计,由责任部门吸收:损失工时=待料时间*受影响人数6.8 停工盘点损失工时=影响时间*受影响人数6.9 混料,发错料指非供给厂商责任,否那么以来件不良计,由责任部门签认吸收:损失工时=影响时间*受影响人数(以标准工时为主)6.10 停电,停气依实际发生时间计,由造成事故责任的单位签认,吸收:损失工时=影响时间*受影响人数(以标准工时为主)6.11 教育训练指以授课方式进展的停产教育训练,损失工时依实际发生时间计由训练中心签认,各部(课)内部吸收.6.12 工伤依实际发生时间计,由责任单位签认,吸收.损失工时=受伤人数*受影响时间6.13 制程异常6.13.1 因自制零件不良造成的损失,由责任单位签认吸收.〔损失部门须开出异常单,依实际数量,预估处理不良所需的工时〕6.13.2 因零件特采(自制)造成的工时损失,由责任部门吸收.6.13.3 因外购零件造成的损失工时,按来件不良处理.由制造单位提报给采购,向供货商索赔.6.13.4 制程不良需开出制程异常单,IE依实际情况,提供标准工时,生产单位必须依IE制定之标准工时提报损失工时.6.14 外购零件不良IQC发出来件质量状况统计表及VDCS通知IE确定标准工时.IE定期发出不良工程与标准工时对照表由此计算损失工时.6.14.1 需挑选类: 工时转由采购向供货商扣款:损失工时=标准工时*挑选数量6.14.2 不得不增加异常工站者,需由制造单位提出申请,会签品管,制工及PM,经产品处主管核准后,由IE 依异常工站申请,确定标准工时.工时转由采购向供货商扣款.损失工时=异常工站标准工时*生产数量6.14.3 特采零件造成的损失:损失工时=实际发生损失工时以上各项损失工时由采购签认吸收,依规定对厂商进展扣款处理,6.15 大扫除依实际发生时间计:损失工时=影响时间*参加人数由各单位内部签认吸收.7.损失工时签认及转嫁一律以“SSBU制造本钱转嫁单〞将损失工时折合金额,转出方及转入方部级主管签认后,进展费用转嫁作业.(实际发生的损失工时将不被扣除,以反映实际生产状况)8.本方法自核定之日起实施.9.附表:SSBU制造本钱转嫁单由于在工程管理中需要对工程和任务的工作量〔工时〕进展管理,在网上搜到了你们的。
车间工时管理制度模板
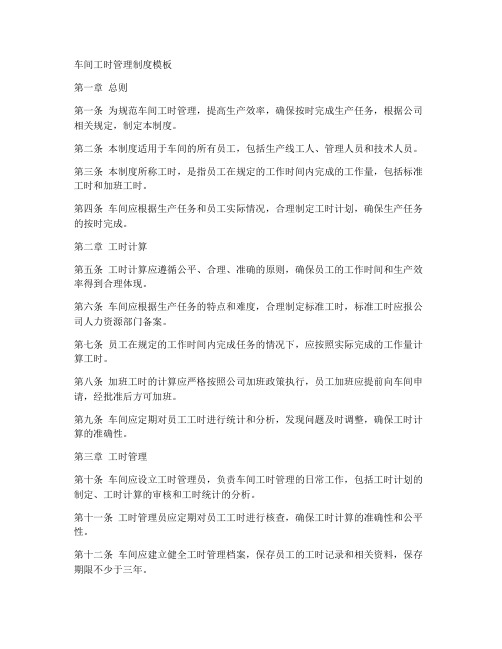
车间工时管理制度模板第一章总则第一条为规范车间工时管理,提高生产效率,确保按时完成生产任务,根据公司相关规定,制定本制度。
第二条本制度适用于车间的所有员工,包括生产线工人、管理人员和技术人员。
第三条本制度所称工时,是指员工在规定的工作时间内完成的工作量,包括标准工时和加班工时。
第四条车间应根据生产任务和员工实际情况,合理制定工时计划,确保生产任务的按时完成。
第二章工时计算第五条工时计算应遵循公平、合理、准确的原则,确保员工的工作时间和生产效率得到合理体现。
第六条车间应根据生产任务的特点和难度,合理制定标准工时,标准工时应报公司人力资源部门备案。
第七条员工在规定的工作时间内完成任务的情况下,应按照实际完成的工作量计算工时。
第八条加班工时的计算应严格按照公司加班政策执行,员工加班应提前向车间申请,经批准后方可加班。
第九条车间应定期对员工工时进行统计和分析,发现问题及时调整,确保工时计算的准确性。
第三章工时管理第十条车间应设立工时管理员,负责车间工时管理的日常工作,包括工时计划的制定、工时计算的审核和工时统计的分析。
第十一条工时管理员应定期对员工工时进行核查,确保工时计算的准确性和公平性。
第十二条车间应建立健全工时管理档案,保存员工的工时记录和相关资料,保存期限不少于三年。
第四章工时调整第十三条工时调整应根据生产任务的变化和员工实际情况进行,调整方案应提前向员工公示。
第十四条工时调整应遵循公平、合理的原则,确保员工的工作时间和生产效率得到合理体现。
第十五条工时调整后,车间应重新制定工时计划,并报公司人力资源部门备案。
第五章考核与奖惩第十六条车间应建立工时考核制度,对员工工时完成情况进行定期考核,考核结果作为员工绩效考核的重要依据。
第十七条对工时完成情况优秀的员工,车间应给予适当奖励,鼓励员工提高工作效率。
第十八条对工时完成情况不佳的员工,车间应进行约谈、培训等方式进行督促,帮助其提高工作效率。
第十九条车间应建立健全工时管理奖惩机制,对违反工时管理规定的员工进行处罚,确保工时管理的有效性。
异常工时损失管理规范(含表格)
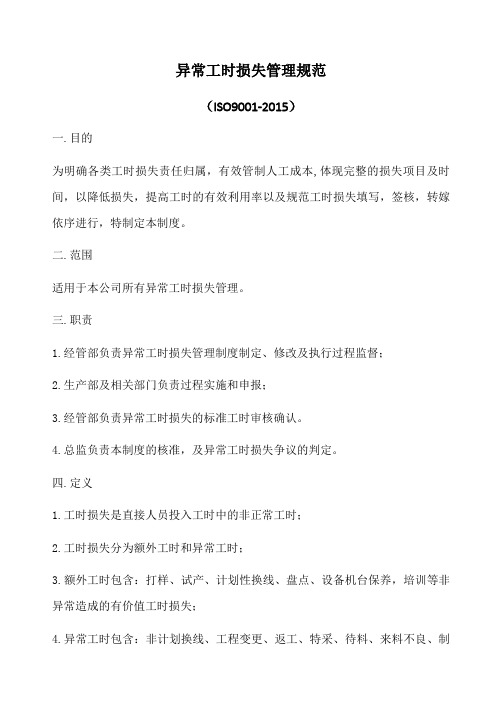
异常工时损失管理规范(ISO9001-2015)一.目的为明确各类工时损失责任归属,有效管制人工成本,体现完整的损失项目及时间,以降低损失,提高工时的有效利用率以及规范工时损失填写,签核,转嫁依序进行,特制定本制度。
二.范围适用于本公司所有异常工时损失管理。
三.职责1.经管部负责异常工时损失管理制度制定、修改及执行过程监督;2.生产部及相关部门负责过程实施和申报;3.经管部负责异常工时损失的标准工时审核确认。
4.总监负责本制度的核准,及异常工时损失争议的判定。
四.定义1.工时损失是直接人员投入工时中的非正常工时;2.工时损失分为额外工时和异常工时;3.额外工时包含:打样、试产、计划性换线、盘点、设备机台保养,培训等非异常造成的有价值工时损失;4.异常工时包含:非计划换线、工程变更、返工、特采、待料、来料不良、制程异常、设备/工具异常因异常造成的无价值工时损失。
五.作业内容1.工时损失类别及责任界定2.异常损失申报/复核/确认流程:2.1.生产部门在生产过程中异常工时损失发生0.5小时以上,线长如实填写《异常工时损失申报表》,交主管审核确认后交工程部进行标准工时确认,最后递交经管部存档。
2.2.工程部收到生产部门《异常工时损失申报表》后,在4小时内同相关责任部门进行确认,必要时到生产现场确认,工时确认由经管提供标准工时评估异常损失工时。
无标准工时的新产品按工程部初定的标准工时的1.5倍计算或按实际工投入时计算.异常确认后责任单位在《异常工时损失申报表》上签名核实后送总监审批。
对未能确认责任,争议较大的异常损失,由工程部记录后交总监仲裁。
2.3.工程部将当天核实确认后的《异常工时损失申报表》提报异常工时损失统计员,统计员将核实后的异常损失工时录入异常工时损失汇总报表中,并定时发给经管部。
2.4.异常工时损失统计员必须如实按确认后的“异常工时申报表”记录异常损失工时,如发现有瞒报,乱报,虚报工时者,经核实后对虚报部门申报人进行严重惩罚,同时追究所在部门主管的管理责任。
损失工时管理规定

3.4 部门负责人 负责管控本部门异常损失工时的产生,督促下属提升工作效率和质量,减少生产导常发生。
3.5 采购部 对因供应商原因导致的导常工时损失进行跟进补偿处理。
3.6 业务部 对因客户原因导致的异常工时损失进行跟进补偿处理。
3.7总经办 负责核准已结案《品质导常处理单》,督导导常损失工时管理办法的有效实施,并列入绩效考
a、若因被支援部门是由于编制内人员不足(缺人),则损失工时由人事部吸收,并列入责任人绩效考核。
b、若是由于被支援工作效率低下(低于标准产能),则损失工时由被支援部门承担,并列入绩效考核。
5.5 返工(库存返工、制程返工、客退返工)
A、因品质进料检验判为合格料后,在制程中或成品后发现因物料不符合客户品质要求产生的返工损失工时
处罚。
6.3 异常损失工时本规定无明确规定工时损失责任,经总经办了解相关工时损失部门意见后,由总经办直接
判定工时损失的归属及工时损失分摊转嫁。
6.4 工时损失统计表提交时间同生产日报表,每周、每月统计各部门产生工时损失,对各类别工时损失分类
汇总,造成的工时损失作业各部门考核基础数据。
6.5 以上所有损失填写单位为生产部门,审核单位为品质部,并由承担部门人员签名确认,无承担部门人员签名的工时损失单无效。
1、目的
为了明确车间各类工时损失责任归属,有效控制人工成本,提升品质及公司竞争力;规范各车间工时损
失填写、签核、转嫁的流程,特制定本办法。
2、范围
本规定适用于制造中心各车间因任何原因影响生产计划达成的损失工时管理。
3、职责
3.1生产车间 负责及时、有效反馈车间损失工时并如实、规范填写《车间工时损失统计表》。
异常工时损失管理规范(含表格)
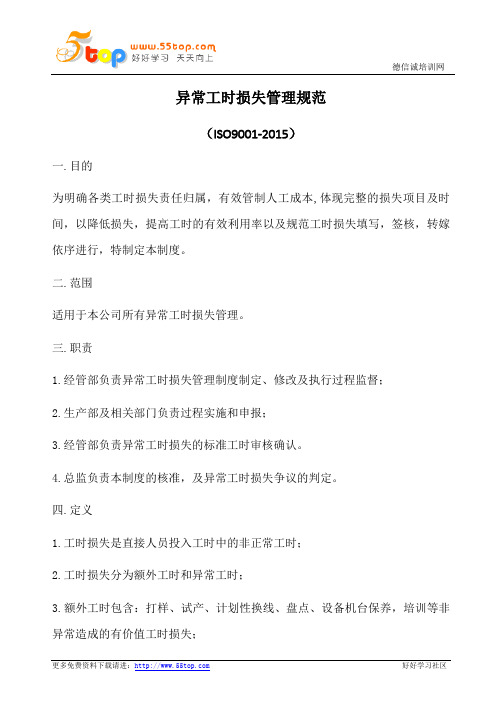
异常工时损失管理规范(ISO9001-2015)一.目的为明确各类工时损失责任归属,有效管制人工成本,体现完整的损失项目及时间,以降低损失,提高工时的有效利用率以及规范工时损失填写,签核,转嫁依序进行,特制定本制度。
二.范围适用于本公司所有异常工时损失管理。
三.职责1.经管部负责异常工时损失管理制度制定、修改及执行过程监督;2.生产部及相关部门负责过程实施和申报;3.经管部负责异常工时损失的标准工时审核确认。
4.总监负责本制度的核准,及异常工时损失争议的判定。
四.定义1.工时损失是直接人员投入工时中的非正常工时;2.工时损失分为额外工时和异常工时;3.额外工时包含:打样、试产、计划性换线、盘点、设备机台保养,培训等非异常造成的有价值工时损失;4.异常工时包含:非计划换线、工程变更、返工、特采、待料、来料不良、制程异常、设备/工具异常因异常造成的无价值工时损失。
五.作业内容1.工时损失类别及责任界定序号异常工时损失类别异常工时责任界定标准责任单位连带责任单位1换线(停线)1.计划性换线(标准换线时间内)工时公司2.超出标准换线时间的工时工程3.由于急单插入造成换线的工时业务/PMC4.由于待料造成换线的工时资材部5.待工治具造成换线的工时工程部6.因制程异常,设备/工/治具异常,无法顺畅生产而换线的工时工程7.因来料异常等外购物料造成换线、停线的工时供应商相关部门工时计算方式1.非计划性换线工时损失=(异常时间+换线时间)*受影响人数;2.计划性换线工时损失=换线时间*受影响人数。
2 设备、工/治/模具异常1.因对设备、工/治/模具操作不当,违规操作造成异常工时,由工程确责任划分操作责任人生产/事业部2.非人为操作原因造成异常工时工程部3.设备、工/治/模具异常,管理单位维修,使产线超过0.5h停线时间。
工程部生产/事业部工时计算方式设备、工/治/模具工时损失= (故障时间+恢复生产时间) * 受影响人数3工程变更1.因工艺变更导致产生的异常工时工程部2.因物料采购变更导致产生的异常工时供应商资材部3.因客户提出工程变更公司工时计算方式工时损失=标准定额差异的部分,未量产前可不报此项损失4返工1.因IQC来料检验判为合格料后,在制程中或成品后发现因物料不不良产生返工工时供应商IQC/采购(制程返工)2.生产送检后由OQC判退,产生的返工工时操作责任人生产/事业部/IPQC3.因IPQC首件签错,OQC判退,返工工时由IPQC负责50%,责任部门负责50%IPQC/生产(各50%)4.若是因相关标准文件(BOM、作业指导书、测试标准等)错导致返工,则工程部承担100%责任工程部(客户退货返工)1.为批量性不良退货品质部生产/事业部2.为客户认定为重大缺陷且为非批量性不良的返工工时品质部生产/事业部3.运输过程中造成返工工时公司4.检测设备误差造成返工工时品质部5.所有涉及供应商来料不良的返工工时供应商相关部门(成品库存返工)1.因客户取消订单导致库存,过后恢复订单需返工,投入工时可转嫁客户负责,不可转嫁者由公司负责公司2.因生产超出安全库存量的返工工时业务(PMC)3.因超出安全库存期导致的返工工时(安全期限)公司工时计算方式损失工时=投入工时*参与人数5来料特采 1.特采过程中产生的工时损失供应商采购部工时计算方式工时损失=投入工时*参与人数6待料1.若因材料没按材料需求计划到材料供应商采购部2.若因生产调配不合理造成生产、事业部3.因来料不良造成的等待工时供应商采购部工时计算方式工时损失= 待料时数*受影响人数7来料不良1.因来料不良造成换线工时损失<按1.7条处理> 供应商相关部门2.因来料不良造成返工工时损失<按3.1条处理> 供应商IQC/采购3.因来料不良造成的等待工时损失<按6.3条处理> 供应商采购部4.IQC判合格物料,生产线实际生产时发现物料不良造成的挑选、返工、异常停线的损失,转稼供应商供应商IQC/采购5.来料不良,IQC已判定不合格,但由于交期压力改为特采使用,造成的各项损失<按5条处理>供应商采购工时计算方式工时损失=换线/停线/返工/特采时数*受影响人数备注所有来料不良造成工时损失必须由责任单位确认,供应商和外协厂商由资材或业务(PMC)部确认;对供应商和外协商扣款工时损失数量必须经由工程部核对签认。
工时索赔管理办法

单位流程说明各车间 生产管理部 售后服务部 营销中心《返工、返修单》提出零部件返工、返修由各车间统计 员填写《返工返修单》报品管部;市场返回件、库存返工、返修、 设计变更、工艺改进、质量改进等按4.5 要求提出,交生产管理部;品管部返工、返修问题的确认、责任 的初步判定零部件返工、返修由检验员判定 责任;其它原因返工、返修由品管部质量或 质量检测工程师判定责任;生产管安排返工、返修零部件、外协件质量问题返工、 返修工时由供应商承担;安排市场返回件、库存件、设计 更改、返工、返修;各车间厂内返工返修委外返工 返修铆焊、机加、电器和总装生产线 自制零部件返工、返修由车间自行安排 完成,不计索赔工时;执行返工、返修或填写《委外返 工、返修单》经生产管理部批准后执行;品管部返工返修结果进行确认对返工、返修处理结果进行复检各车间 生产管理部 返工、返修统计、分析 汇总《返工、返修单》报生产管 理部;生产管理部月度汇总提交财务财务部返工返、修损失追溯核准工时、执行索赔及考核5管理流程6管理要求6.1无完整的签字确认《返工返修单》,不计工时。
6.2返工返修完毕后无检验员在 《返工返修单》上复检签字,视为返工返修无效, 不作为汇总统计依据。
6.3库存整机或总成件因存放时间长,零部件老化、锈蚀需进行库存返修,由营销公司提报返工返修单,经营销公司经理批准后,由生产管理部下达返修任务。
6.4零部件的返工、返修损失,属供应商责任造成的,由供应商全额承担;属公司责任单位造成的由责任单位按“质量事故责任相关规定”承担。
6.5每发现1例虚报返工返修损失的考核责任单位100元/次。
7附加说明7.1本办法作为公司《工时管理规范》的补充文件执行。
7.2生产管理部工时索赔作为制造成本统计依据之一。
7.3工时索赔的考核由生产管理部报准。
8附件附件1返工、返修单填报单位:日期:年月日原因描述:工时索赔财务签名式联生产管理部、财务各联附录2 委外返工、返修单日期:年月 日填报单位 式 联 工-艺科 、 财 务 部各 联。
组装车间管理制度表

组装车间管理制度表第一章总则第一条为规范组装车间管理,提高生产效率和产品质量,保障车间员工安全和利益,特制定本管理制度。
第二条本管理制度适用于公司组装车间的日常管理工作。
第三条车间主任是组装车间的最高负责人,负责车间的管理、生产、质量控制和员工安全。
第四条车间主任应做到公正、严格、细致,做好组装车间的管理工作,确保生产工作的正常进行。
第五条全体车间员工应遵守管理制度,服从车间主任的管理,积极配合,共同提高生产效率和产品质量。
第六条车间员工对违反管理制度的行为,应受到公司的处罚并承担相应责任。
第七条本管理制度自发布之日起生效。
第二章组装车间生产管理第八条组装车间生产计划应由车间主任按照公司总体生产计划制定,并通知相关员工。
第九条车间员工应按照生产计划,按时完成各项生产任务,不得私自调整计划。
第十条车间员工应按照生产标准操作流程进行生产,保证产品的质量。
第十一条车间主任应定期检查生产过程,确保生产设备的正常运转,发现问题及时处理。
第十二条车间员工应做好生产记录,确保生产过程的可追溯性。
第十三条车间员工应注意节约用电、用水等资源,节约生产成本。
第十四条车间内禁止吸烟、酗酒等不良行为,严禁在工作区域进行赌博等活动。
第三章组装车间质量管理第十五条车间主任应设立质量管理小组,负责质量检验和监控工作。
第十六条车间员工应严格按照产品质量标准进行生产,确保产品符合质量要求。
第十七条质量异常情况发生时,应及时向质量管理小组报告,并协助查明原因,制定整改措施。
第十八条质量管理小组应定期组织质量检验和评估,确保产品质量持续稳定。
第十九条质量管理人员应定期对车间员工进行质量知识培训,提高员工的质量意识。
第二十条质量管理人员应及时向上级领导报告质量问题,主动汇报和解决。
第四章组装车间安全管理第二十一条车间主任应制定安全生产措施,保障车间员工的生命安全。
第二十二条车间员工应严格遵守安全规定,正确使用安全防护用具,做好自我保护。
装配车间损失工时补助管理办法
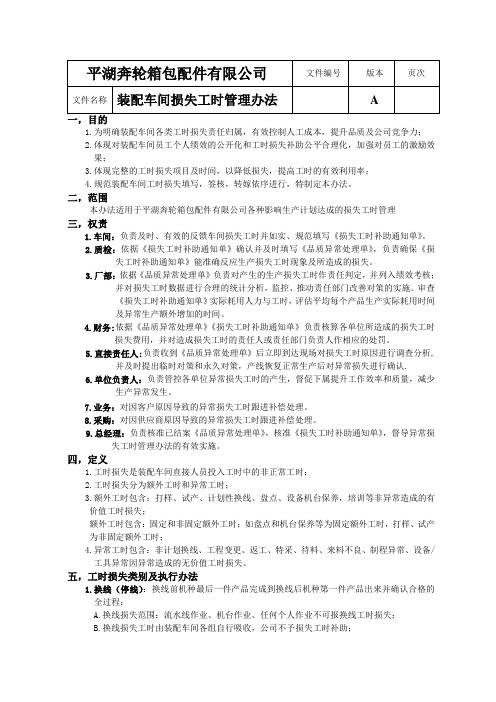
1.为明确装配车间各类工时损失责任归属,有效控制人工成本,提升品质及公司竞争力;2.体现对装配车间员工个人绩效的公开化和工时损失补助公平合理化,加强对员工的激励效果;3.体现完整的工时损失项目及时间,以降低损失,提高工时的有效利用率;4.规范装配车间工时损失填写,签核,转嫁依序进行,特制定本办法。
二,范围本办法适用于平湖奔轮箱包配件有限公司各种影响生产计划达成的损失工时管理三,权责1.车间:负责及时、有效的反馈车间损失工时并如实、规范填写《损失工时补助通知单》。
2.质检:依据《损失工时补助通知单》确认并及时填写《品质异常处理单》,负责确保《损失工时补助通知单》能准确反应生产损失工时现象及所造成的损失。
3.厂部:依据《品质异常处理单》负责对产生的生产损失工时作责任判定,并列入绩效考核;并对损失工时数据进行合理的统计分析,监控、推动责任部门改善对策的实施。
审查《损失工时补助通知单》实际耗用人力与工时,评估平均每个产品生产实际耗用时间及异常生产额外增加的时间。
4.财务:依据《品质异常处理单》《损失工时补助通知单》负责核算各单位所造成的损失工时损失费用,并对造成损失工时的责任人或责任部门负责人作相应的处罚。
5.直接责任人:负责收到《品质异常处理单》后立即到达现场对损失工时原因进行调查分析,并及时提出临时对策和永久对策,产线恢复正常生产后对异常损失进行确认.6.单位负责人:负责管控各单位异常损失工时的产生,督促下属提升工作效率和质量,减少生产异常发生。
7.业务:对因客户原因导致的异常损失工时跟进补偿处理。
8.采购:对因供应商原因导致的异常损失工时跟进补偿处理。
9.总经理:负责核准已结案《品质异常处理单》,核准《损失工时补助通知单》,督导异常损失工时管理办法的有效实施。
四,定义1.工时损失是装配车间直接人员投入工时中的非正常工时;2.工时损失分为额外工时和异常工时;3.额外工时包含:打样、试产、计划性换线、盘点、设备机台保养,培训等非异常造成的有价值工时损失;额外工时包含:固定和非固定额外工时;如盘点和机台保养等为固定额外工时,打样、试产为非固定额外工时;4.异常工时包含:非计划换线、工程变更、返工、特采、待料、来料不良、制程异常、设备/工具异常因异常造成的无价值工时损失。
损耗工时表-V1.0
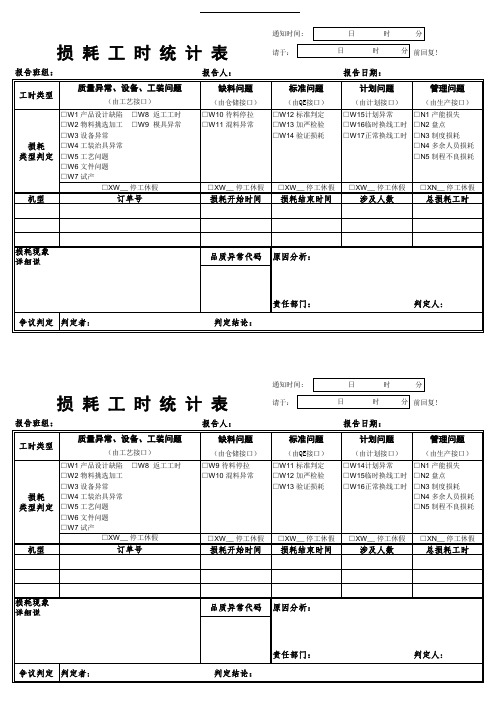
(由工艺接口) □W1 产品设计缺陷 □W8 返工工时 □W2 物料挑选加工 □W3 设备异常 □W4 工装治具异常 □W5 工艺问题 □W6 文件问题 □W7 试产 □XW__ 停工休假
请于:
报告人: 缺料问题
(由仓储接口) □W9 待料停拉 □W10 混料异常
□XW__ 停工休假
□XW__ 停工休假
□XW__ 停工休假
□XN__ 停工休假
机型
订单号
损耗开始时间
损耗结束时间
涉及人数
总损耗工时
损耗现象详细说明:
品质异常代码
原因分析:
责任部门: 争议判定 判定者: 判定结论:
判定人:
报告日期: 标准问题
(由QE接口) □W11 标准判定 □W12 加严检验 □W13 验证损耗
计划问题
(由计划接口) □W14计划异常 □W15临时换线工时 □W16正常换线工时
管理问题
(由生产接口) □N1 产能损失 □N2 盘点 □N3 制度损耗 □N4 多余人员损耗 □N5 制程不良损耗
损耗 类型判定
通知时间:
日 日 时
时
分 分 前回复!
损 耗 工 时 统 计 表
报告班组: 工时类型 质量异常、设备、工装问题
(由工艺接口) □W1 产品设计缺陷 □W8 返工工时 □W2 物料挑选加工 □W9 模具异常 □W3 设备异常 □W4 工装治具异常 □W5 工艺问题 □W6 文件问题 □W7 试产 □XW__ 停工休假
损耗 类型判定
□XW__ 停工休假□XW_Biblioteka 停工休假□XW__ 停工休假
□XN__ 停工休假
机型
安全专用知识-损失工作日计算表
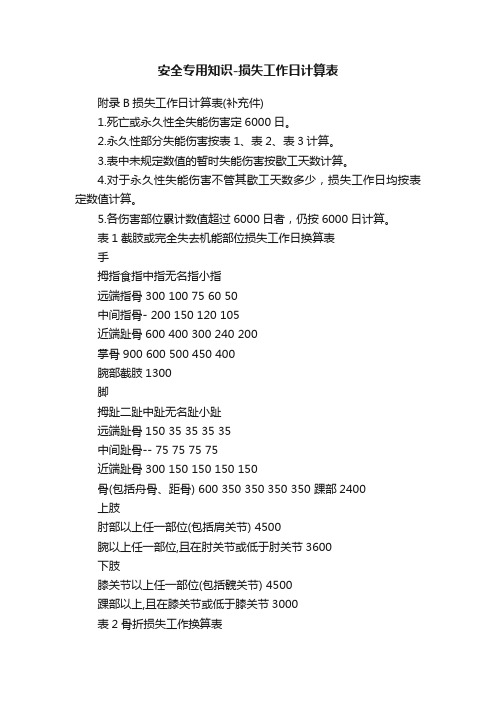
安全专用知识-损失工作日计算表附录B损失工作日计算表(补充件)1.死亡或永久性全失能伤害定6000日。
2.永久性部分失能伤害按表1、表2、表3计算。
3.表中未规定数值的暂时失能伤害按歇工天数计算。
4.对于永久性失能伤害不管其歇工天数多少,损失工作日均按表定数值计算。
5.各伤害部位累计数值超过6000日者,仍按6000日计算。
表1截肢或完全失去机能部位损失工作日换算表手拇指食指中指无名指小指远端指骨300 100 75 60 50中间指骨- 200 150 120 105近端趾骨600 400 300 240 200掌骨900 600 500 450 400腕部截肢1300脚拇趾二趾中趾无名趾小趾远端趾骨150****3535中间趾骨-- 75 75 75 75近端趾骨300 150 150 150 150骨(包括舟骨、距骨) 600 350 350 350 350 踝部2400上肢肘部以上任一部位(包括肩关节) 4500腕以上任一部位,且在肘关节或低于肘关节3600下肢膝关节以上任一部位(包括髋关节) 4500踝部以上,且在膝关节或低于膝关节3000表2骨折损失工作换算表骨折部位损失工作日掌、指骨60挠骨下端80尺、挠骨干90肱骨髁上60肱骨干80肱骨外科颈70锁骨70胸骨105跖、趾70胫、腓90股骨干105股粗隆间100股骨颈160表3功能损伤损失工作日换算表功能损害部位损失工作日1. 包被重要器官的单纯性骨损伤(头颅骨、胸骨、脊椎骨) 1052. 包被重要器官的复杂性骨损伤,内部器官轻度受损,骨损伤治愈后,不遗功能障碍者5003. 包被重要器官的复杂性骨损伤,伴有内部器官损伤,骨损伤治愈后,遗有轻度功能障碍者9004. 接触有害气体或毒物,急性中毒症状消失后,不遗有临床症状及后遗症者2005. 重度失血,经抢救后,未遗有造血功能障碍者2006. 包被重要器官的复杂性骨折包被器官受损,骨损伤治愈后,伴有严重的功能障碍者a. 脑神经损伤导致癫痫者3000b. 脑神经损伤导致痴呆者5000c. 脑挫裂伤,颅内严重血肿,脑干损伤造成无法医治的低能5000d. 脑外伤致使运动系统严重障碍或失语,且不易恢复者4000e. 脊柱骨损伤,脊髓离断形成截瘫者6000f. 脊柱骨损伤,脊髓半离断,影响饮食起居者6000g. 脊柱骨损伤合并脊髓伤,有功能障碍不影响饮食起居者4000h. 单纯脊柱骨损伤,包括残留慢性腰背痛者1000i. 脊柱损伤,遗有脊髓压迫症双下肢功能障碍,二便失禁者4000j. 脊柱韧带损伤,局部血行障碍影响脊柱活动者1500k. 胸部骨损伤,伤及心脏,引起明显的节律不正者4000l. 胸部骨损伤,伤及心脏,遗有代谢功能失调者4000m. 胸部骨损伤,胸廓成形术后,明显影响一侧呼吸功能者2000n. 一侧肺功能丧失者4000o. 一侧肺并有另侧一个肺叶术后伤残者5000p. 骨盆骨损伤累及神经,导致下肢运动障碍者4000q. 骨盆不稳定骨折,并遗留有尿道狭窄和尿路感染30007. 腰、背部软组织严重损伤;脊柱活动明显受限者20008. 四肢软组织损伤治愈后,遗有周围神经损伤,感觉运动机能障碍,影响工作及生活者15009. 四肢软组织损伤治愈后,遗有周围神经损伤,运动机能障碍,但生活能自理者200010. 四肢软组织损伤,治愈后由于疤颜瘢弯缩,严重影响运动功能,但生活能自理者200011. 手肌腱受损,伸屈功能严重影响障碍,影响工作、生活者140012. 脚肌腱受损,引起机能障碍,不能自由行走者140013. 眼睑断裂导致导闭合不全20014. 眼睑损伤导致泪小管、泪腺损伤,导致泪溢,影响工作20015. 双目失明;600016. 一目失明,但另一目视力正常80017. 两目视力均有障碍,不易恢复者80018. 一目的明,另一目视物不清,或双目视物不清者(仅能见前2M以内的物体,且短期内,不易恢复者) 300019. 两眼角膜受损,并有眼底出血或溷浊,视力高度障碍者(仅能见1M之物体)且根本不能恢复者400020. 眼球突出不能复位,引起视障碍者70021. 眼肌麻痹,造成斜视、复视者60022. 一耳丧失听力,另一耳听觉正常者60023. 听力有重大障碍者30024. 两耳听力丧失300025. 鼻损伤,嗅觉功能严重丧失100026. 鼻脱落者130027. 口腔受损,致使牙齿脱落,不能安装假牙,致使咀嚼发生困难者180028. 口腔严重受损,咀嚼机能全废300029. 喉损伤,引起喉狭窄,影响发兰及呼吸者100030. 语言障碍,说话不清30031. 语言全废300032. 伤及腹膜,并有单独性的腹腔出血及腹膜炎症者100033. 由于损伤进行胃次全切除,或肠管切除三分之一以上者300034. 由于损伤进行胃全切,或食道全切,腔肠代替食道,或肠管切除三分之一以上者600035. 一叶肝脏切除者300036. 一侧肾脏切除者300037. 生殖器官损伤,失去生殖机能者180038. 伤及神经、膀胱及直肠,遗有大便、小便失禁,漏尿、漏屎等200039. 关节结构损伤,关节活动受限,影响运动功能者140040. 伤筋伤骨,动作受限,其功能损伤严重于表2者200041. 接触高浓度有害气体,急性中毒症状消失后,遗有脑实质病变临床症状者400042. 各种急性中毒严重损伤呼吸道、食道粘膜,遗有功能障碍者200043. 国家规定的工业毒物轻度中毒患者15044. 国家规定的工业毒物中度中毒患者70045. 国家规定的工业毒物重度中毒患者2000。
车间工时管理制度模板
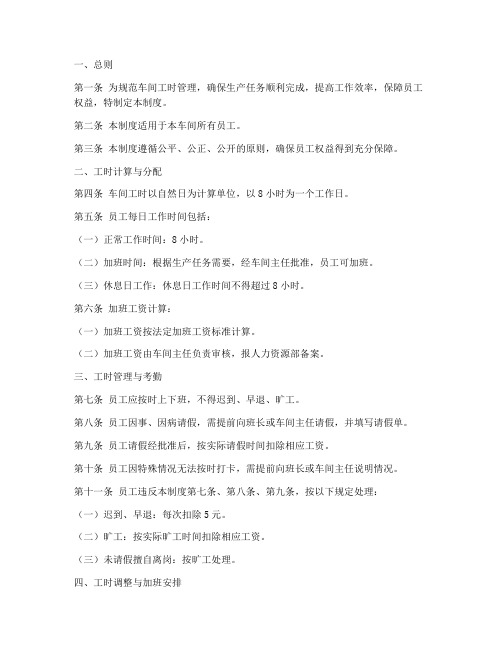
一、总则第一条为规范车间工时管理,确保生产任务顺利完成,提高工作效率,保障员工权益,特制定本制度。
第二条本制度适用于本车间所有员工。
第三条本制度遵循公平、公正、公开的原则,确保员工权益得到充分保障。
二、工时计算与分配第四条车间工时以自然日为计算单位,以8小时为一个工作日。
第五条员工每日工作时间包括:(一)正常工作时间:8小时。
(二)加班时间:根据生产任务需要,经车间主任批准,员工可加班。
(三)休息日工作:休息日工作时间不得超过8小时。
第六条加班工资计算:(一)加班工资按法定加班工资标准计算。
(二)加班工资由车间主任负责审核,报人力资源部备案。
三、工时管理与考勤第七条员工应按时上下班,不得迟到、早退、旷工。
第八条员工因事、因病请假,需提前向班长或车间主任请假,并填写请假单。
第九条员工请假经批准后,按实际请假时间扣除相应工资。
第十条员工因特殊情况无法按时打卡,需提前向班长或车间主任说明情况。
第十一条员工违反本制度第七条、第八条、第九条,按以下规定处理:(一)迟到、早退:每次扣除5元。
(二)旷工:按实际旷工时间扣除相应工资。
(三)未请假擅自离岗:按旷工处理。
四、工时调整与加班安排第十二条车间主任根据生产任务需要,可对员工工时进行调整。
第十三条加班安排:(一)车间主任根据生产任务需要,提前一周向员工公布加班安排。
(二)员工如有特殊情况,需在加班安排公布后三天内向车间主任提出申请,经批准后方可调整。
(三)加班工资按法定加班工资标准计算。
五、监督检查与奖惩第十四条车间主任负责对本制度执行情况进行监督检查。
第十五条对违反本制度的行为,按以下规定处理:(一)警告:口头警告或书面警告。
(二)罚款:根据违反程度,扣除一定金额的工资。
(三)辞退:严重违反本制度,影响生产秩序的行为。
第十六条对执行本制度表现突出的员工,给予表扬和奖励。
六、附则第十七条本制度由车间主任负责解释。
第十八条本制度自发布之日起实施。
注:本模板仅供参考,具体内容可根据企业实际情况进行调整。
本车间工时损失排序表.xls

顾晓亮
20100801/0 20100801/08
827
27
停机维修升级
顾晓亮
20100801/0 20100801/08
827
27
顾晓亮
20100801/0 20100801/08
827
27
顾晓亮
20100801/0 20100801/08
827
27
顾晓亮
20100801/0 20100801/08
827
27
利用设备维修等待时间进行设备 保养,减少周末设备保养时间 (停机维护保养)
顾晓亮
20100801/0 20100801/08
827
27
利用设备维修等待时间进行设备 保养,减少周末设备保养时间 (停机维护保养)
对策及措施Leabharlann 合理安排生产 合理安排生产 合理安排人员
责任人
完成时间 预计时间 实际时间
进展情 况
顾晓亮
20100801/0 20100801/08
827
27
顾晓亮
20100801/0 20100801/08
827
27
顾晓亮
20100801/0 20100801/08
827
27
安排组长顶岗,降低组长的CWS
机加一车间工时损失问题排序表(2010.8.13-
排序
工时损失问题描述
原因
所占工时损 影响工时 失比例 效率比
本周为满足生产要求,投入
1
库存影响2031小时
大量库存,导致库存影响对 52.60% 21.42%
工时损失较大.
1.1
线边库存小时
1.2
未上岗员工
装配车间损失工时管理规范(含表格)

装配车间损失工时管理规范(ISO9001-2015)一、目的1.为明确装配车间各类工时损失责任归属,有效控制人工成本,提升品质及公司竞争力;2.体现对装配车间员工个人绩效的公开化和工时损失补助公平合理化,加强对员工的激励效果;3.体现完整的工时损失项目及时间,以降低损失,提高工时的有效利用率;4.规范装配车间工时损失填写,签核,转嫁依序进行,特制定本办法。
二、范围本办法适用于平湖奔轮箱包配件有限公司各种影响生产计划达成的损失工时管理三、权责1.车间:负责及时、有效的反馈车间损失工时并如实、规范填写《损失工时补助通知单》。
2.质检:依据《损失工时补助通知单》确认并及时填写《品质异常处理单》,负责确保《损失工时补助通知单》能准确反应生产损失工时现象及所造成的损失。
3.厂部:依据《品质异常处理单》负责对产生的生产损失工时作责任判定,并列入绩效考核;并对损失工时数据进行合理的统计分析,监控、推动责任部门改善对策的实施。
审查《损失工时补助通知单》实际耗用人力与工时,评估平均每个产品生产实际耗用时间及异常生产额外增加的时间。
4.财务:依据《品质异常处理单》《损失工时补助通知单》负责核算各单位所造成的损失工时损失费用,并对造成损失工时的责任人或责任部门负责人作相应的处罚。
5.直接责任人:负责收到《品质异常处理单》后立即到达现场对损失工时原因进行调查分析,并及时提出临时对策和永久对策,产线恢复正常生产后对异常损失进行确认.6.单位负责人:负责管控各单位异常损失工时的产生,督促下属提升工作效率和质量,减少生产异常发生。
7.业务:对因客户原因导致的异常损失工时跟进补偿处理。
8.采购:对因供应商原因导致的异常损失工时跟进补偿处理。
9.总经理:负责核准已结案《品质异常处理单》,核准《损失工时补助通知单》,督导异常损失工时管理办法的有效实施。
四、定义1.工时损失是装配车间直接人员投入工时中的非正常工时;2.工时损失分为额外工时和异常工时;3.额外工时包含:打样、试产、计划性换线、盘点、设备机台保养,培训等非异常造成的有价值工时损失;额外工时包含:固定和非固定额外工时;如盘点和机台保养等为固定额外工时,打样、试产为非固定额外工时;4.异常工时包含:非计划换线、工程变更、返工、特采、待料、来料不良、制程异常、设备/工具异常因异常造成的无价值工时损失。
效率体系中损失工时的相关规定
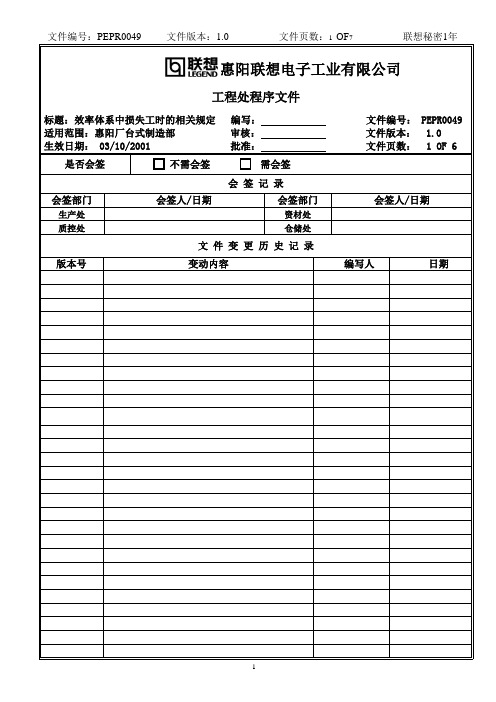
工程处程序文件效率体系中损失工时的相关规定1、目的:规范效率体系中各类损失工时,为生产处效率指标计算提供依据。
根据生产处实际情况,制定本规定。
2、适用范围:本规定适用于惠阳厂PC制造部生产处。
3、相关文件:《生产效率体系程序文件》(PEPR0048)4、职责:4.1生产处负责各种损失工时发生的记录(录入系统),并按照本规定的原则、努力保证记录(录入系统)的损失工时的客观性及严谨性;当日填写《外部损失工时确认通知书》,向有关部门进行确认,并将确认后的《外部损失工时确认通知书》及时交付工程处IE组。
4.2资材、质控、仓储、工程等部门负责对生产处《外部损失工时确认通知书》的及时确认。
4.3工程处IE组负责效率体系、工时记录系统中损失工时项目的维护,及部分有意见分歧的外部扣失工时的判定。
5、名词解释:5.1 损失工时:指生产过程中因各种停工和返工而导致的工时损耗,同时也包括新品(部件)评测(生产)等非正常工时消耗。
5.1.1 停工损失工时的界定:5.1.1.1“待料停工”:本项目主要指生产单位无“材料”生产引发的停工(包括仓库未到料、料正在检、来料不合格不能出库或仓库人为原因延迟发料等)。
这里“材料”指非生产在制件,以区别对“生产流程问题”和“任务不饱满”停工的判断。
另外生产单位领料员领料不及时(“待领料停工”)的情况不在此列。
5.1.1.2“待领料停工”:指生产处某组别的领料人员领料不及时给其它组别的生产造成延误工时(如装配由于备料领机箱的人员领料不及时而引起的工时延误)。
5.1.1.3“任务不饱满停工”:指所有因等待任务单指示进行工作而发生的延迟工时(包括任务单迟发、下达的任务已完成等待新的工作指示)。
5.1.1.4“工程问题停工”:指生产过程中由于工程问题待解决(非质量问题)而造成的停工(如待工程母盘、待工程文件或指引等)。
5.1.1.5“设备故障停工”:指生产部门由于设备(如传盘机、线体、条码打印机、扫描枪、包装封箱机、打带机等)故障致使生产被迫中断待处理的情况。
SOP-EN-0956损失工时管理办法
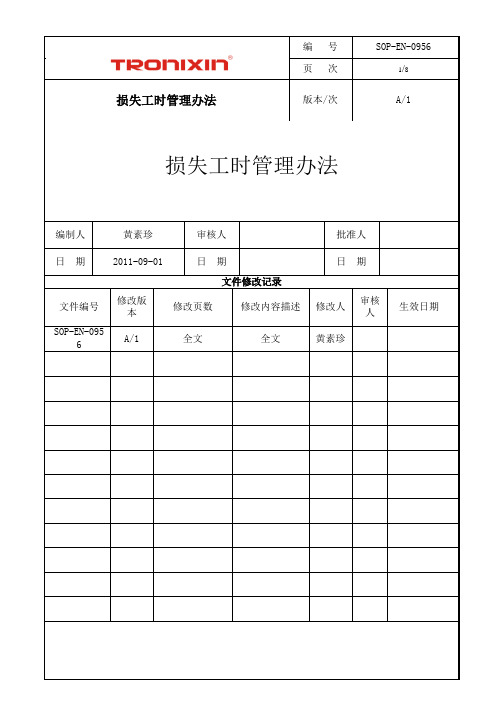
损失工时管理办法版本/次A/1损失工时管理办法编制人黄素珍审核人批准人日期2011-09-01 日期日期文件修改记录文件编号修改版本修改页数修改内容描述修改人审核人生效日期SOP-EN-0956A/1 全文全文黄素珍损失工时管理办法版本/次A/11.0目的:1.1为明确各类损失工时责任归属,加强各部门异常处理能力,有利于将损失工时降至最低,从而有效管制成本,并使损失工时签核正常运作,转嫁依序进行,制定本办法。
2.0 适用范围:凡产品实现过程中因品质异常或其它原因造成中断及损失均适用之。
3.0 权责范围3.1制造部:负责开出(受影响时)《损失工时记录表》或《停线通知单》,并会签相关责任单位。
3.2品保部:负责核实损失工时,判定责任之归属,并实施对责任承担部门的费用转稼,同时负责接收因品质异常造成的损失转稼。
3.3 IE课:负责重工工时的制订、确认及汇总,每月将汇总之损失工时邮件给责任单位,追踪改善。
3.4研发部:负责吸收因发行的标准错误(如工程图面、工艺标准)所造成的损失。
3.5采购部:负责来料异常的损失转嫁供应商。
3.6业务部:负责吸收因与客人沟通信息错误及成品特采被客诉所产生的损失。
3.7企划部:负责吸收因发错料所产生的损失。
3.8生技/模具课:负责吸收因模/治具异常所产生的损失。
3.9管理部:负责吸收新进人员72H内的培训工时。
4.0 名词定义4.1外部损失工时(可转稼):指因其它单位(非本部门范围之内)影响其作业,造成人员损失工时产生,从而有义务吸收受影响单位的损失工时。
4.2内部损失工时(非转稼):指因生产部门作业状况不佳,造成人员损失工时产生,则承担相对应的损失责任。
4.3损失工时:损失工时=损失过程时间*受影响人数-产出工时。
4.4主要责任:直接致使异常发生,影响品质变异之关键因素产生。
4.5次要责任:间接致使异常发生或从事产品加工过程,未查觉或未检查到至使影响品质变异之因素。
5.0 作业程序5.1生产单位根据每日实际生产状况,将受影响的线别及机台所产生的损失工时,如实记录于《生产日报表》《损失工时记录表》内。
车间工时损失记录单
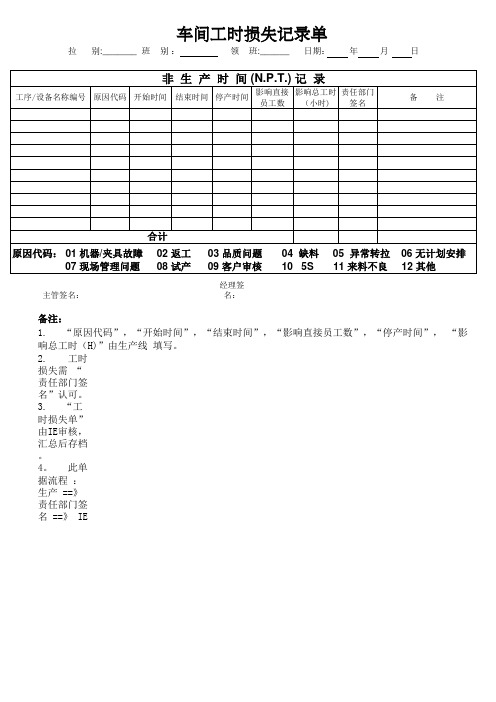
车间工时损失记录单
拉 别:_______ 班 别: 领 班:______ 日期: 年 月 日
非 生 产 时 间 (N.P.T.) 记 录
工序/设备名称编号 原因代码 开始时间 结束时间 停产时间 影响直接 影响总工时 责任部门 员工数 (小时) 签名 备 注
合计 原因代码: 01 机器/夹具故障 07 现场管理问题主Biblioteka 签名:02 返工 08 试产
03 品质问题 09 客户审核
经理签名:
04 缺料 10 5S
05 异常转拉 11 来料不良
06 无计划安排 12 其他
备注: 1. “原因代码”,“开始时间”,“结束时间”,“影响直接员工数”,“停产时间”, “影 响总工时(H)”由生产线 填写。 2. 工时损失需 “责任部门签名”认可。 3. “工时损失单”由IE审核,汇总后存档。 4。 此单据流程 : 生产 ==》 责任部门签名 ==》 IE
工时损失管理规定

工时损失管理规定 Document number:PBGCG-0857-BTDO-0089-PTT19981.目的为明确各类工时损失责任归属,有效管制人工成本;体现完整的损失项目及时间,以降低成本,提高工时的有效利用率;2.范围适用于本公司所有异常工时损失管理。
3.权责技术部:工时损失管理办法制定修改和补充,执行过程监督,工时损失的审核,工时损失的统计和分析。
生产部:负责过程实施和申报。
品质部:物料问题的确认,部分工时损失申报。
其它责任部门:负责工时损失的确认及提出相应的改善措施。
4.定义工时损失是直接人员投入工时中的非正常工时,工时损失分为额外工时和异常工时;额外工时包括打样、试产、计划性换线、盘点、非标改机、设备与工治具点检保养,培训等非异常造成的有价值工时损失;额外工时分为固定和非固定额外工时,如盘点和机台保养等为固定额外工时;打样、试产为非固定额外工时。
异常工时包括非计划换线、工程变更、返工、待料、资料错误、来料不良、制程异常、计划不合理、设备/工具故障等原因造成生产停工或生产进度延迟所导致的无价值工时损失。
换线损失工时指当前产线发生异常后,可换做其他产品,本机种最后一件产品完成到换线后另一机种第一件产品产出并确认合格的全过程;换线工时损失=换线时间*受影响人数停线损失工时指在异常发生后,导致员工暂无其他产线产品可做而产生的无价值等待工时。
停线工时损失=停线时间*受影响人数返工异常工时指因异常或变更发生后,导致相应物品返工处理需要的工时。
返工损失工时=返工完成该批不良品所需工时异常增加工时指某物品因异常发生后,需额外对物品进行加工或挑选等处理所需的工时。
异常增加工时=处理该异常物品所需工时*人数5.工时损失类别及责任判定物料异常5.1.1供应商/外协(以下简称供应商)来料不及时,则产生的异常停线或换线工时损失由物控签认,转供应商吸收,不能转供应商吸收的由物控吸收。
5.1.2来料被IQC判退以及IQC已判退,但由于交期压力改为上线挑选或加工,造成生产线欠料停线或换线,则产生的异常停线或换线工时损失由物控签认,转供应商吸收。
关于规范装配部作息的通知
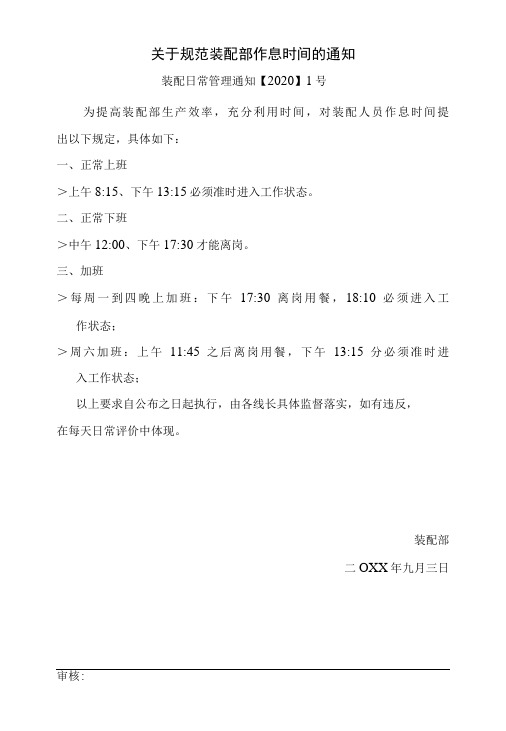
关于规范装配部作息时间的通知
装配日常管理通知【2020】1号
为提高装配部生产效率,充分利用时间,对装配人员作息时间提出以下规定,具体如下:
一、正常上班
>上午8:15、下午13:15必须准时进入工作状态。
二、正常下班
>中午12:00、下午17:30才能离岗。
三、加班
>每周一到四晚上加班:下午17:30离岗用餐,18:10必须进入工作状态;
>周六加班:上午11:45之后离岗用餐,下午13:15分必须准时进入工作状态;
以上要求自公布之日起执行,由各线长具体监督落实,如有违反,
在每天日常评价中体现。
装配部
二OXX年九月三日审核:。
- 1、下载文档前请自行甄别文档内容的完整性,平台不提供额外的编辑、内容补充、找答案等附加服务。
- 2、"仅部分预览"的文档,不可在线预览部分如存在完整性等问题,可反馈申请退款(可完整预览的文档不适用该条件!)。
- 3、如文档侵犯您的权益,请联系客服反馈,我们会尽快为您处理(人工客服工作时间:9:00-18:30)。
装配车间损失工时管理规范
(ISO9001-2015)
一、目的
1.为明确装配车间各类工时损失责任归属,有效控制人工成本,提升品质及公司竞争力;
2.体现对装配车间员工个人绩效的公开化和工时损失补助公平合理化,加强对员工的激励效果;
3.体现完整的工时损失项目及时间,以降低损失,提高工时的有效利用率;
4.规范装配车间工时损失填写,签核,转嫁依序进行,特制定本办法。
二、范围
本办法适用于平湖奔轮箱包配件有限公司各种影响生产计划达成的损失工时管理
三、权责
1.车间:负责及时、有效的反馈车间损失工时并如实、规范填写《损失工时补助通知单》。
2.质检:依据《损失工时补助通知单》确认并及时填写《品质异常处理单》,负责确保《损失工时补助通知单》能准确反应生产损失工时现象及所造成的损失。
3.厂部:依据《品质异常处理单》负责对产生的生产损失工时作责任判定,并列入绩效考核;并对损失工时数据进行合理的统计分析,监控、推动责任部门
改善对策的实施。
审查《损失工时补助通知单》实际耗用人力与工时,评估平均每个产品生产实际耗用时间及异常生产额外增加的时间。
4.财务:依据《品质异常处理单》《损失工时补助通知单》负责核算各单位所造成的损失工时损失费用,并对造成损失工时的责任人或责任部门负责人作相应的处罚。
5.直接责任人:负责收到《品质异常处理单》后立即到达现场对损失工时原因进行调查分析,并及时提出临时对策和永久对策,产线恢复正常生产后对异常损失进行确认.
6.单位负责人:负责管控各单位异常损失工时的产生,督促下属提升工作效率和质量,减少生产异常发生。
7.业务:对因客户原因导致的异常损失工时跟进补偿处理。
8.采购:对因供应商原因导致的异常损失工时跟进补偿处理。
9.总经理:负责核准已结案《品质异常处理单》,核准《损失工时补助通知单》,督导异常损失工时管理办法的有效实施。
四、定义
1.工时损失是装配车间直接人员投入工时中的非正常工时;
2.工时损失分为额外工时和异常工时;
3.额外工时包含:打样、试产、计划性换线、盘点、设备机台保养,培训等非异常造成的有价值工时损失;
额外工时包含:固定和非固定额外工时;如盘点和机台保养等为固定额外工时,打样、试产为非固定额外工时;
4.异常工时包含:非计划换线、工程变更、返工、特采、待料、来料不良、制程异常、设备/工具异常因异常造成的无价值工时损失。
五、工时损失类别及执行办法
1.换线(停线):换线前机种最后一件产品完成到换线后机种第一件产品出来并确认合格的全过程;
A.换线损失范围:流水线作业、机台作业、任何个人作业不可报换线工时损失;
B.换线损失工时由装配车间各组自行吸收,公司不予损失工时补助;
C.计划排配换线分为:计划性换线和非计划性换线;
a.计划性换线损失工时由装配车间各组吸收作业,公司不予损失工时补助;
b.非计划性换线不可报换线损失项目,以实际组装异常项目填写,损失工时依以下规定计算;
(1)由于急单插入造成换线等损失由计划部或业务部签认,如一个部门责任则全部承担;如两个部门责任则各承担一半,列入责任单位绩效考核;换线损失工时由装配车间各组吸收作业,公司不予损失工时补助;
(2)由于待料/待工治具造成换线等损失由上一工序或责任单位签认吸收,列入责任单位绩效考核;换线损失工时由装配车间各组吸收作业,公司不予损失工时补助;
(3)因制程异常,设备/工/治具异常,无法顺畅生产而换线,损失工时由责任单位签认吸收,列入责任单位绩效考核;换线损失工时由装配车间各组吸收作业,公司不予损失工时补助;
(4)因来料异常等外购物料造成换线、停线等损失时,供应商应须吸收车间投入的工时,相关责任部门承担相应的责任处罚,列入责任单位绩效考核;换线损失工时由装配车间提报,由采购联络供应商全部吸收,公司给予车间损失工时补助;
供应商零件异常不可全检,造成换线、停线损失工时及车间其他材料损失费用,由车间提报,采购联络供应商全部吸收,公司给予车间损失工时补助(按当地要求的工资水平计算每小时工资)
供应商零件异常可全检,但无法派员处理时由车间安排专人全检后使用,造成换线、停线损失工时、全检工时及车间其他材料损失费用,由车间提报,采购联络供应商全部吸收,公司给予车间损失工时补助(按当地要求的工资水平计算每小时工资)
供应商零件异常可全检,供应商派员到车间全检后使用或全部退回厂商全检后使用,造成换线、停线损失工时及车间其他材料损失费用,由车间提报,采购联络供应商全部吸收,公司给予车间损失工时补助(按当地要求的工资水平计算每小时工资)
D.非计划性换线工时损失=(异常时间+换线时间)*受影响人数(非全线作业人数);
E.计划性换线工时损失=换线时间*受影响人数(非全线作业人数)。