CT-121鼓泡式吸收塔烟气脱硫工艺技术介绍
JBR((鼓泡塔)脱硫技术
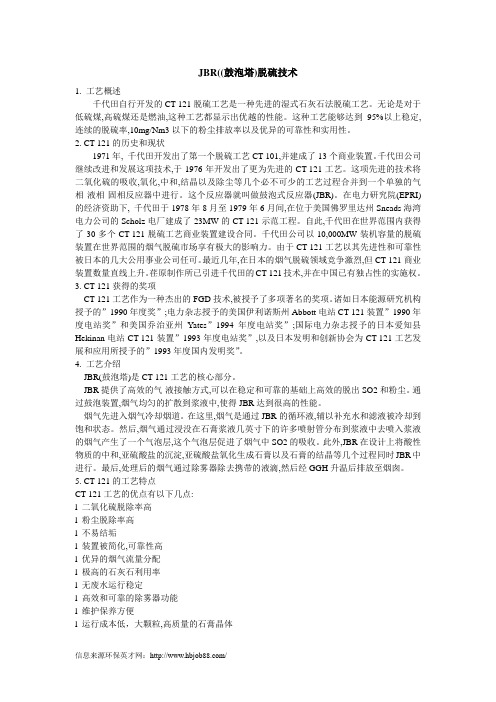
JBR((鼓泡塔)脱硫技术1. 工艺概述千代田自行开发的CT-121脱硫工艺是一种先进的湿式石灰石法脱硫工艺。
无论是对于低硫煤,高硫煤还是燃油,这种工艺都显示出优越的性能。
这种工艺能够达到95%以上稳定,连续的脱硫率,10mg/Nm3以下的粉尘排放率以及优异的可靠性和实用性。
2. CT-121的历史和现状1971年, 千代田开发出了第一个脱硫工艺CT-101,并建成了13个商业装置。
千代田公司继续改进和发展这项技术,于1976年开发出了更为先进的CT-121工艺。
这项先进的技术将二氧化硫的吸收,氧化,中和,结晶以及除尘等几个必不可少的工艺过程合并到一个单独的气相-液相-固相反应器中进行。
这个反应器就叫做鼓泡式反应器(JBR)。
在电力研究院(EPRI)的经济资助下, 千代田于1978年8月至1979年6月间,在位于美国佛罗里达州Sneads海湾电力公司的Scholz电厂建成了23MW的CT-121示范工程。
自此,千代田在世界范围内获得了30多个CT-121脱硫工艺商业装置建设合同。
千代田公司以10,000MW装机容量的脱硫装置在世界范围的烟气脱硫市场享有极大的影响力。
由于CT-121工艺以其先进性和可靠性被日本的几大公用事业公司任可。
最近几年,在日本的烟气脱硫领域竞争激烈,但CT-121商业装置数量直线上升。
荏原制作所已引进千代田的CT-121技术,并在中国已有独占性的实施权。
3. CT-121获得的奖项CT-121工艺作为一种杰出的FGD技术,被授予了多项著名的奖项。
诸如日本能源研究机构授予的”1990年度奖”;电力杂志授予的美国伊利诺斯州Abbott电站CT-121装置”1990年度电站奖”和美国乔治亚州Y ates”1994年度电站奖”;国际电力杂志授予的日本爱知县Hekinan电站CT-121装置”1993年度电站奖”,以及日本发明和创新协会为CT-121工艺发展和应用所授予的”1993年度国内发明奖”。
烟气喷射鼓泡脱硫工艺的技术特性分析

60 0 MW 机 组锅 炉烟 气脱硫 试运 行数 据 , 分析 了影 响脱硫 效 率 的几 个 因素 。 实践表 明喷 射 鼓 泡
吸收塔具有脱硫效率高、 工艺过程简单、 能耗低、 运行可靠等特点。 关 键词 : T 1 1工艺 ;鼓 泡反 应塔 ;脱硫 效 率 C 一2
中图分类号 : 7 13 X 0 文献标识码 : B 文章编号 :066 7 (0 7 0 -0 8— 3 10 -7 2 20 )40 4 0
面不 断形 成 , 增强 气~ 液传 质效 果 , 同时 气泡 上升 到 吸 收液 表面破 裂 , 量 的浆 液 以液 滴 形 式 同烟 气一 大 起 向上 夹带一 定距 离 , 分 大 的液 滴 在 重 力 作 用下 部
内的喷射器以鼓泡形式喷散到吸收液 中, 烟气 中的 S: O 在鼓泡过程 中被吸收 , 净化后 的烟气经除雾后 进人 回转 式烟 气换 热 器 中吸 热 升温 , 后 通 过 烟 囱 然 排放。 C .2 工 艺 的核心部 分 是 喷 射式 鼓 泡 反应 塔 。 T1 1
除尘效率由 3 m / 0 gm 下降到 1r / 具有 良好 的 2 gm , a 脱 硫除 尘性 能 。
1 烟气喷射鼓泡脱硫基本原理
11 烟气 喷射 鼓泡 脱硫 工 艺过程 .
图 1 喷 射 鼓 泡 反 应 器 示 意
l —— 上盖板 ;2 —— 上升管 ; ——空气分布板 ; 3 4 ——搅拌器 ; —— 下盖板 ; ——喷射管 5 6
塞等特点 , 且投资省 , 运行费用低 , 无论是对于低硫 煤, 高硫煤 还是 燃油 , 硫率 都能 达到 9 % 以上 , 脱 5 粉 尘排放量最低可实现 1m / 2 gm 以下 , 适合 中国电站
锅 炉 的烟 气 脱 硫 J 。某 电厂 选 用 的 烟 气 喷 射 鼓 泡 塔湿法 脱硫 技 术 , 脱 硫 效 率 可 达 到 9 % , 硫 后 其 9 脱
鼓泡式烟气脱硫工艺研究
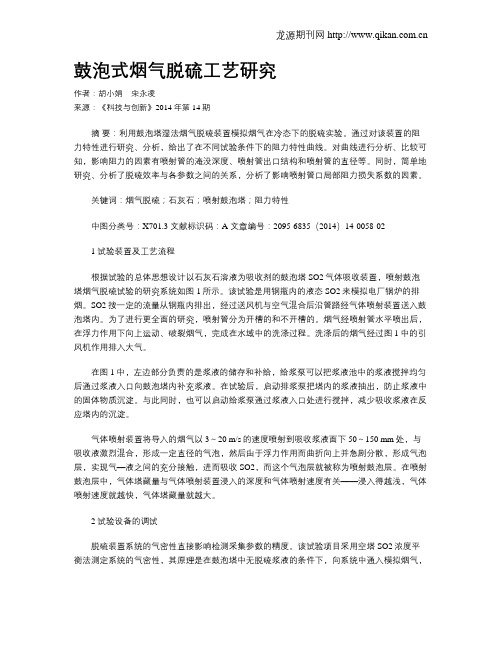
鼓泡式烟气脱硫工艺研究作者:胡小娟宋永凌来源:《科技与创新》2014年第14期摘要:利用鼓泡塔湿法烟气脱硫装置模拟烟气在冷态下的脱硫实验。
通过对该装置的阻力特性进行研究、分析,给出了在不同试验条件下的阻力特性曲线。
对曲线进行分析、比较可知,影响阻力的因素有喷射管的淹没深度、喷射管出口结构和喷射管的直径等。
同时,简单地研究、分析了脱硫效率与各参数之间的关系,分析了影响喷射管口局部阻力损失系数的因素。
关键词:烟气脱硫;石灰石;喷射鼓泡塔;阻力特性中图分类号:X701.3 文献标识码:A 文章编号:2095-6835(2014)14-0058-021 试验装置及工艺流程根据试验的总体思想设计以石灰石溶液为吸收剂的鼓泡塔SO2气体吸收装置,喷射鼓泡塔烟气脱硫试验的研究系统如图1所示。
该试验是用钢瓶内的液态SO2来模拟电厂锅炉的排烟。
SO2按一定的流量从钢瓶内排出,经过送风机与空气混合后沿管路经气体喷射装置送入鼓泡塔内。
为了进行更全面的研究,喷射管分为开槽的和不开槽的。
烟气经喷射管水平喷出后,在浮力作用下向上运动、破裂烟气,完成在水域中的洗涤过程。
洗涤后的烟气经过图1中的引风机作用排入大气。
在图1中,左边部分负责的是浆液的储存和补给,给浆泵可以把浆液池中的浆液搅拌均匀后通过浆液入口向鼓泡塔内补充浆液。
在试验后,启动排浆泵把塔内的浆液抽出,防止浆液中的固体物质沉淀。
与此同时,也可以启动给浆泵通过浆液入口处进行搅拌,减少吸收浆液在反应塔内的沉淀。
气体喷射装置将导入的烟气以3~20 m/s的速度喷射到吸收浆液面下50~150 mm处,与吸收液激烈混合,形成一定直径的气泡,然后由于浮力作用而曲折向上并急剧分散,形成气泡层,实现气—液之间的充分接触,进而吸收SO2,而这个气泡层就被称为喷射鼓泡层。
在喷射鼓泡层中,气体塔藏量与气体喷射装置浸入的深度和气体喷射速度有关——浸入得越浅,气体喷射速度就越快,气体塔藏量就越大。
烟气脱硫工艺流程
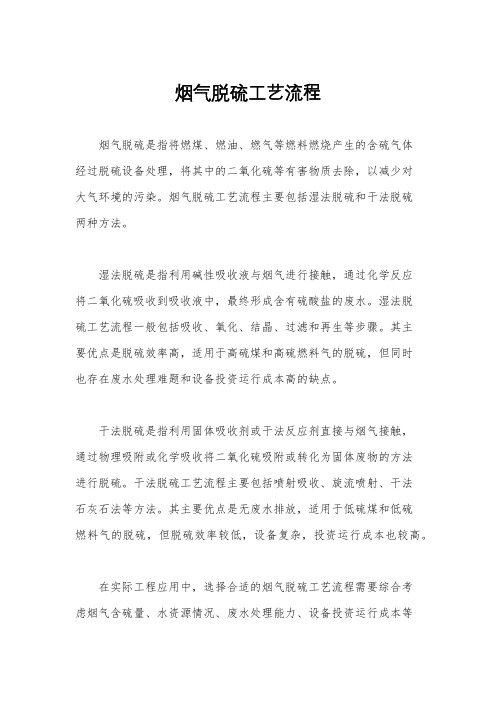
烟气脱硫工艺流程
烟气脱硫是指将燃煤、燃油、燃气等燃料燃烧产生的含硫气体
经过脱硫设备处理,将其中的二氧化硫等有害物质去除,以减少对
大气环境的污染。
烟气脱硫工艺流程主要包括湿法脱硫和干法脱硫
两种方法。
湿法脱硫是指利用碱性吸收液与烟气进行接触,通过化学反应
将二氧化硫吸收到吸收液中,最终形成含有硫酸盐的废水。
湿法脱
硫工艺流程一般包括吸收、氧化、结晶、过滤和再生等步骤。
其主
要优点是脱硫效率高,适用于高硫煤和高硫燃料气的脱硫,但同时
也存在废水处理难题和设备投资运行成本高的缺点。
干法脱硫是指利用固体吸收剂或干法反应剂直接与烟气接触,
通过物理吸附或化学吸收将二氧化硫吸附或转化为固体废物的方法
进行脱硫。
干法脱硫工艺流程主要包括喷射吸收、旋流喷射、干法
石灰石法等方法。
其主要优点是无废水排放,适用于低硫煤和低硫
燃料气的脱硫,但脱硫效率较低,设备复杂,投资运行成本也较高。
在实际工程应用中,选择合适的烟气脱硫工艺流程需要综合考
虑烟气含硫量、水资源情况、废水处理能力、设备投资运行成本等
因素。
此外,还需要考虑脱硫设备的稳定性、可靠性和安全性,以及对烟气中其他污染物的处理效果等因素。
总的来说,烟气脱硫工艺流程的选择应根据实际情况综合考虑各种因素,以达到经济、环保和可持续发展的目标。
希望本文所述内容对烟气脱硫工艺流程的了解有所帮助。
鼓泡塔脱硫技术的应用

鼓泡塔烟气脱硫技术在600MW机组中的应用日本千代田公司自行开发的CT-121脱硫工艺是一种先进的湿法石灰石脱硫工艺。
无论是对于低硫煤、高硫煤还是燃油, 这种工艺都显示出优越的性能。
这种工艺的脱硫率能够稳定,连续地达到95%以上,粉尘排放率在10mg/Nm3以下时可靠性高且实用性好。
这项技术将SO2的吸收、氧化、中和、结晶以及除尘等必不可少的工艺过程合并到一单独的气相-液相-固相反应器中进行。
这个反应器就叫做鼓泡式反应器(JBR)。
本文就该项技术在国华台山发电厂1号、2号机组(2×600MW)烟气脱硫项目上的应用作一介绍。
1. 鼓泡塔烟气脱硫工艺介绍1.1 工艺原理鼓泡塔石灰石-石膏湿法烟气脱硫(FGD)工艺的化学原理如下:①烟气中的SO2在鼓泡塔里溶解于水,生成亚硫酸并分解成氢离子H+和离子;②烟气中的氧和氧化风机送入空气中的氧将溶液中的氧化成;③吸收剂中的碳酸钙在一定条件下从溶液中分解出Ca2+;④在吸收塔内,溶液中的、Ca2+与水反应生成石膏(CaSO4·2H2O)。
化学反应式分别如下:SO2+H2O→H2SO3→H++(1)H+++1/2O2→2H++(2)CaCO3+2H++H2O→Ca2++2H2O+CO2↑(3)Ca2+++2H2O→CaSO4·2H2O(4)由于吸收剂和氧化空气的送入,吸收塔下部浆池中的或亚硫酸盐几乎全部被氧化为硫酸根或硫酸盐,最后当CaSO4达到一定过饱和度后结晶形成石膏——CaSO4·2H2O。
石膏可根据需要进行综合利用或作抛弃处理。
1.2 烟气脱硫工艺系统本项目的烟气脱硫装置由8个系统组成:①烟气系统;②SO2吸收系统;③石灰石浆液制备系统;④石膏脱水系统;⑤废水输送系统;⑥工艺水系统;⑦废水处理系统;⑧吸收塔紧急系统。
其中烟气系统和SO2吸收系统单元机组各配1套,而石灰石浆液制备系统、石膏脱水系统、废水输送系统、工艺水系统、废水处理系统和吸收塔紧急系统属公用系统,即两套脱硫系统公用。
烟气脱硫技术与方法

烟气脱硫技术与方法烟气脱硫技术是指通过一系列的工艺和方法将烟气中的二氧化硫(SO2)去除,以减少硫氧化物对环境的污染。
烟气脱硫技术主要应用于燃煤和油气燃烧产生的烟气处理中,以及一些工业过程中排放的含硫废气处理中。
一、烟气脱硫的主要方法1. 湿法烟气脱硫方法湿法烟气脱硫是目前应用较广泛的方法之一。
其主要原理是将烟气与一定量的脱硫剂(如石灰石、石膏等)接触,使SO2与脱硫剂发生反应生成硫酸盐,然后通过洗涤、过滤等工艺将硫酸盐分离,最终获得净化后的烟气。
湿法烟气脱硫方法包括石灰石石膏法、氧化钙吸收法、海藻泥吸附法等。
其中,石灰石石膏法是最常见的湿法脱硫技术之一,其操作简单、效果稳定,并能够同时去除烟气中的颗粒物。
2. 半干法烟气脱硫方法半干法烟气脱硫是介于湿法和干法之间的一种脱硫方法。
该技术主要是在煤粉燃烧过程中加入一定量的脱硫剂,使之与SO2发生反应生成硫酸盐,并通过一系列的设备和工艺将硫酸盐去除。
半干法烟气脱硫技术包括半干法石灰石法、半干法硬石膏法等。
相比于湿法和干法,半干法烟气脱硫技术具有较低的水耗、较高的脱硫效率和较高的SO2适应性。
3. 干法烟气脱硫方法干法烟气脱硫是将烟气与固体脱硫剂直接接触,使之发生反应,从而去除烟气中的SO2。
干法烟气脱硫技术主要适用于SO2浓度较低的烟气处理,如天然气燃烧排放的烟气脱硫。
干法烟气脱硫方法包括石灰吸收法、固定床吸附法、浮动床吸附法等。
这些方法利用固体吸附剂(如活性炭、沸石等)吸附烟气中的SO2,形成二硫化钙等化合物,并通过一系列的设备进行处理和回收。
二、烟气脱硫技术的选择与比较选择合适的烟气脱硫技术应综合考虑多种因素,包括烟气特性、脱硫效率、设备投资及运行成本等。
下面简要比较一下几种常见的烟气脱硫方法:1. 湿法烟气脱硫方法湿法烟气脱硫技术脱硫效率高,适用于高浓度、高湿度的烟气处理。
其设备体积较大,水耗较高,但可同时去除烟气中的颗粒物。
2. 半干法烟气脱硫方法半干法烟气脱硫技术在湿法和干法之间,具有较高的脱硫效率和较低的水耗。
鼓泡式反应器脱硫技术(CT-121)介绍PPT课件

02
鼓泡式反应器脱硫技术 (CT-121)原理
化学反应原理
氧化反应
01
鼓泡式反应器中的氧气与硫化氢发生氧化反应,生成硫和水。
还原反应
02
在催化剂的作用下,硫化氢与氧气发生还原反应,生成硫和水。
酸碱中和
03
在反应过程中,产生的酸性气体与碱性物质发生中和反应,生
成盐和水。
反应器工作原理
鼓泡式反应器是一种立式压力容器, 内部装有催化剂和液体吸收剂。
技术创新
在鼓泡式反应器脱硫技术(CT-121)的基础上,开发了新型的脱硫技术,如双塔串联脱硫、高效湿法脱硫等。这些新技 术具有更高的脱硫效率和更低的运行成本,为企业的可持续发展提供了有力支持。
技术发展前景
随着环保要求的不断提高和技术的不断进步,鼓泡式反应器脱硫技术(CT-121)将不断发展和完善。未来, 该技术将在更多的领域得到应用,为我国的环保事业做出更大的贡献。
03
运行效果
该电厂采用鼓泡式反应器脱硫技术(CT-121)后,烟气中的SO2浓度显著
降低,脱硫效率达到了98%以上,有效减少了SO2对环境的影响。
案例三:技术改进与创新
技术改进
针对鼓泡式反应器脱硫技术(CT-121)在实际应用中存在的问题和不足,进行了技术改进和创新。例如,优化反应器结 构、改进吸收剂配方、提高自动化程度等。
益。
案例二:某电厂应用
01 02
工艺流程
某电厂采用鼓泡式反应器脱硫技术(CT-121)对燃烧产生的烟气进行脱硫 处理。通过在反应器中加入吸收剂,使烟气中的SO2与吸收剂反应,生 成硫酸盐,从而达到脱硫目的。
技术特点
该技术适用于大型燃煤电厂的烟气处理,具有处理量大、脱硫效率高等 优点。同时,该技术能够适应电厂负荷变化,保证稳定的
第二章CT121的系统流程简介
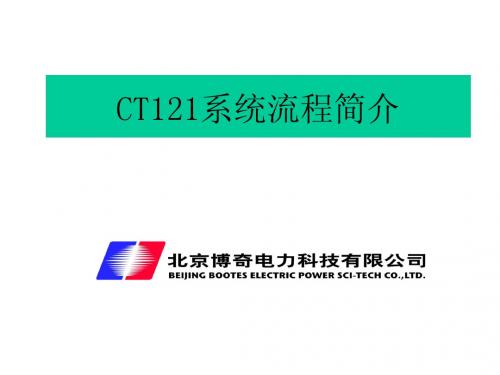
SO2吸收部分
吸收塔内浆液被吸收塔搅拌器适当地搅拌,使 石膏晶体悬浮. 由氧化风机吹出的氧化空气进入吸收塔的反应 区,使被吸收的SO2氧化. 将石灰石浆液送入吸收塔,脱除SO2以及形成石 膏.加入适当当量的石灰石,以保持吸收液的 pH值于4到6之间. 石膏浆液排出泵将含有10到20%固体的石膏浆 液,从吸收塔排出到石膏脱水机.吸收塔石膏 浆液中的Cl-浓度低于20g/l.
�
石灰石制浆部分
石灰石储存仓给料机将石灰石排到湿式球磨机. 用湿式球磨机将石灰石磨成石灰石浆液.磨成 的石灰石浆液流入石灰石浆液循环箱,并用石 灰石浆液循环泵送到石灰石旋流分离器进行粗 颗粒的分离. 分离后的石灰石浆液中含有25%的固体颗粒. 石灰石浆液储存在石灰石浆液储存箱,并用石 灰石浆液泵送到吸收塔. 粒径超过要求的颗粒送回到湿式球磨机.
烟气部分
来自吸收塔的洁净烟气进入烟气-烟气 加热器.在烟气-烟气加热器中,洁净的 烟气与来自锅炉的烟气进行热交换后,被 加热到80℃以上.被加热的洁净的烟气 通过烟道和烟囱排向大气. 在锅炉起动阶段和烟气脱硫设备(FGD)停 止运行时,烟气通过旁路烟道进入烟囱
SO2吸收部分
来自烟气冷却区域的烟气进入由上隔板和下隔 板形成的封闭的吸收塔入口烟室. 装在入口烟室下隔板的喷射管将烟气导入吸收 塔鼓泡区(泡沫区)的石灰浆液面以下的区域. 在鼓泡区域发生SO2的吸收,氧化,石膏结晶等 所有反应.发生上述一系列反应后,烟气通过 上升管流入位于入口烟室上方的出口烟室,然 后流出吸收塔.
工艺说明
来自锅炉引风机的烟气,经增压风机增压后进入烟气-烟气加热器. 来自锅炉引风机的烟气 , 经增压风机增压后进入烟气 - 烟气加热器 . 在烟气-烟气加热器中,烟气(未经处理) 在烟气-烟气加热器中,烟气(未经处理)与来自吸收塔的洁净的烟气进 行热交换后被冷却.被冷却的烟气引入到烟道的烟气冷却区域. 行热交换后被冷却.被冷却的烟气引入到烟道的烟气冷却区域.在烟气 冷却区域中,喷入补给水和吸收液,使得烟气被冷却到饱和状态. 冷却区域中,喷入补给水和吸收液,使得烟气被冷却到饱和状态.来自烟 道冷却区域的烟气进入由上层板和下层板形成的封闭的吸收塔入口舱. 道冷却区域的烟气进入由上层板和下层板形成的封闭的吸收塔入口舱. 装在入口舱下层板的喷射管将烟气导入吸收塔鼓跑区(泡沫区) 装在入口舱下层板的喷射管将烟气导入吸收塔鼓跑区(泡沫区)的石灰浆 液面以下的区域.在鼓跑区域发生所有反应: 的吸收; 液面以下的区域.在鼓跑区域发生所有反应: (a) SO2的吸收; (b) 亚硫 酸盐发生氧化反应生成硫酸盐; 硫酸盐发生中和反应生成石膏; 酸盐发生氧化反应生成硫酸盐; (c) 硫酸盐发生中和反应生成石膏; 石膏结晶并析出.发生上述一系列反应后, (d) 石膏结晶并析出.发生上述一系列反应后,干净的烟气通过上升管 并通过入口舱上方的出口舱排出. 并通过入口舱上方的出口舱排出. 石膏浆排出泵将含有10 20%固体的石膏浆, 10到 石膏浆排出泵将含有10到20%固体的石膏浆,从吸收塔排出到石膏脱 水机. 水机.脱水后的石膏可以在生产石膏板以及生产水泥和土壤改良等方面 充分利用. 充分利用.
烟气脱硫设备及工艺流程介绍

市场发展趋势
环保政策推动: 政府对环保的重 视将推动烟气脱 硫设备的市场需 求
技术进步:新技 术的不断出现将 提高烟气脱硫设 备的性能和效率
成本降低:随着 技术的成熟和规 模效应,烟气脱 硫设备的成本将 逐渐降低
应用领域扩大: 烟气脱硫设备将 在更多领域得到 应用,如钢铁、 化工等行业
未来发展展望
干法脱硫工艺流程
石灰石粉制备:将石灰石粉碎成粉末,用于后续脱硫反应
吸收剂制备:将石灰石粉与水混合,制成吸收剂浆液
吸收塔:将吸收剂浆液喷入吸收塔,与烟气中的SO2反应, 生成石膏
石膏脱水:将石膏脱水,制成石膏产品
烟气排放:脱硫后的烟气排放到大气中
石膏处理:将石膏产品进行回收利用,如用于建材生产等
添加标题
添加标题
添加标题
添加标题设备组成:吸Fra bibliotek塔、喷淋系统、 氧化系统、石膏脱水系统等
缺点:设备投资大,运行成本高, 废水处理困难
干法脱硫设备
干法脱硫设备原理:利用石灰石、 白云石等碱性物质吸收烟气中的 二氧化硫
设备特点:干法脱硫设备具有占 地面积小、投资成本低、运行费 用低等优点
添加标题
添加标题
添加标题
添加标题
设备类型:干法脱硫设备主要有 干法喷钙脱硫设备、干法喷镁脱 硫设备等
应用领域:干法脱硫设备广泛应 用于电力、钢铁、化工等行业的 烟气脱硫处理
半干法脱硫设备
设备组成:吸收塔、喷淋系 统、除尘器、烟囱等
工作原理:利用石灰石或石 灰作为吸收剂,吸收烟气中 的二氧化硫
优点:脱硫效率高,运行成 本低,设备简单,操作方便
缺点:需要定期更换吸收剂, 产生固体废物,需要处理
脱硫设备的比较
脱硫塔工艺流程
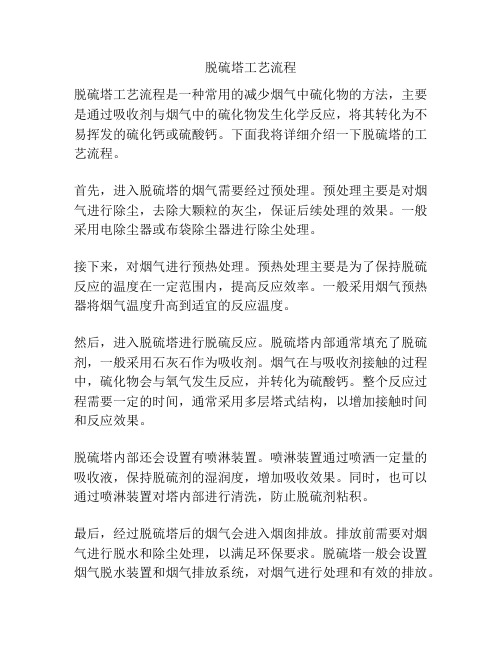
脱硫塔工艺流程脱硫塔工艺流程是一种常用的减少烟气中硫化物的方法,主要是通过吸收剂与烟气中的硫化物发生化学反应,将其转化为不易挥发的硫化钙或硫酸钙。
下面我将详细介绍一下脱硫塔的工艺流程。
首先,进入脱硫塔的烟气需要经过预处理。
预处理主要是对烟气进行除尘,去除大颗粒的灰尘,保证后续处理的效果。
一般采用电除尘器或布袋除尘器进行除尘处理。
接下来,对烟气进行预热处理。
预热处理主要是为了保持脱硫反应的温度在一定范围内,提高反应效率。
一般采用烟气预热器将烟气温度升高到适宜的反应温度。
然后,进入脱硫塔进行脱硫反应。
脱硫塔内部通常填充了脱硫剂,一般采用石灰石作为吸收剂。
烟气在与吸收剂接触的过程中,硫化物会与氧气发生反应,并转化为硫酸钙。
整个反应过程需要一定的时间,通常采用多层塔式结构,以增加接触时间和反应效果。
脱硫塔内部还会设置有喷淋装置。
喷淋装置通过喷洒一定量的吸收液,保持脱硫剂的湿润度,增加吸收效果。
同时,也可以通过喷淋装置对塔内部进行清洗,防止脱硫剂粘积。
最后,经过脱硫塔后的烟气会进入烟囱排放。
排放前需要对烟气进行脱水和除尘处理,以满足环保要求。
脱硫塔一般会设置烟气脱水装置和烟气排放系统,对烟气进行处理和有效的排放。
整个脱硫塔工艺流程主要有预处理、预热处理、脱硫反应和后处理几个环节。
其中,脱硫反应是核心环节,通过填充吸收剂和喷淋装置的配合,可以有效地将烟气中的硫化物转化为硫酸钙。
同时,对脱硫后的烟气进行处理和排放,保证环境的清洁和安全。
脱硫塔工艺流程的实施,可以有效地减少烟气中的硫化物排放,保护环境和人们的健康。
同时,也可以回收利用脱硫副产物,减少资源浪费。
因此,在工业生产和供暖等领域广泛应用,对环保和节能起到了积极的推动作用。
烟气脱硫工艺技术

烟气脱硫工艺技术
烟气脱硫工艺技术是一种常用的大气污染治理技术,主要用于减少燃煤、燃油等燃料在燃烧过程中产生的二氧化硫排放。
下面就烟气脱硫工艺技术进行介绍。
烟气脱硫技术主要包括湿法脱硫和干法脱硫两种技术。
湿法脱硫是目前常用的烟气脱硫方法之一。
该技术是通过喷射吸收剂(如石灰石和氨水)进入烟气中与二氧化硫(SO2)进
行反应,形成硫酸盐或硫酸氢盐。
通过这种方式,可将烟气中的SO2去除,达到脱硫的目的。
湿法脱硫具有脱硫效率高、
处理量大、适用于不同燃煤方式等优点,目前被广泛采用。
干法脱硫是指在干燥状态下,通过与氧化剂或其他吸收剂接触,将烟气中的二氧化硫进行化学反应,形成硫酸盐或硫酸氢盐。
干法脱硫相对于湿法脱硫而言,虽然处理量较小,但干法脱硫的设备简单,操作方便,无需处理大量废水,具有一定的优势。
无论是湿法脱硫还是干法脱硫,在脱硫的过程中都需要吸收剂与烟气充分接触,以达到高效去除二氧化硫的效果。
此外,为了提高脱硫效率,还可以采用对烟气进行预处理,如增加烟气的湿度或温度等方法,改善吸收剂与烟气之间的反应速率。
在脱硫工艺技术的选择上,需要根据实际情况综合考虑,包括燃料特性、处理量、投资成本、运行费用等因素进行综合评估。
不同的工艺技术具有各自的优缺点,并且适用于不同的工况。
总之,烟气脱硫工艺技术是一项重要的大气污染治理技术,能够有效减少二氧化硫的排放量,改善大气环境质量。
在未来的发展中,还需要进一步研究和发展更加高效、低耗能的脱硫技术,以满足环保要求。
同时,还需加强对于脱硫工艺技术的监管和管理,确保脱硫设施的正常运行,保护和改善人民群众健康。
CT-121鼓泡式吸收塔在实际工程中的应用
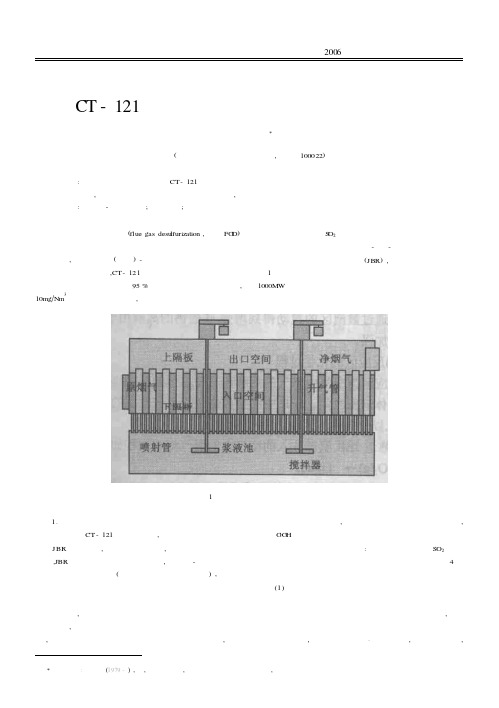
CT -121鼓泡式吸收塔在实际工程中的应用赵日晖Ξ(北京博奇电力科技有限公司,北京 100022)摘 要:本文结合实际工程介绍了CT-121鼓泡式吸收塔脱硫工艺的技术特点。
本脱硫工艺适用于燃用中高硫煤及燃油电厂的烟气脱硫,具有高除尘率、高脱硫率、低能耗等优点,实际运行已显示出其优良的可靠性和实用性。
关键词:石灰石-石膏湿法;烟气脱硫;鼓泡塔 燃煤电厂的烟气脱硫(flue gas desu lfurization ,缩写FG D )是目前世界上大规模商业化应用的脱硫技术。
在所有的脱硫工艺中,又以石灰石(石灰)-石膏湿法脱硫占主导地位。
经过几年的工程实践,CT-121脱硫工艺已显示出其优越的性能。
这种工艺能够达到95%以上稳定连续的脱硫率,10mg ΠN m 3以下的粉尘排放率,具有优异的可靠性和实用性。
这项先进的技术将S O 2的吸收、氧化、中和、结晶、以及除尘等工艺过程合并到一个单独的气-液-固相反应器中进行。
这个反应器就是鼓泡式吸收塔(JBR ),其构造截面示意图如图1所示。
鼓泡塔技术目前已经运用到单机装机容量1000MW 的脱硫装置上。
图1 鼓泡塔构造截面示意图 1.工艺介绍鼓泡塔是CT-121工艺的核心,烟气通过喷射管均匀分布到JBR 的浆液中,按化学方法推算,当气泡上升通过鼓泡层时,JBR 里产生了多级的传质过程,由于气-液多级接触产生了庞大的接触面积(是通常喷淋工艺的数十倍),所以传质速率很高。
原烟气进入由上下隔板形成的封闭容器中。
喷管安装在下隔板上,将原烟气导入吸收塔的浆液区。
烟气从浆液中鼓泡上升,流经贯通上层隔板的上升管。
由于烟气速度很低,烟气中携带的液滴在上层隔板的空间被沉降分离,处理后的净烟气流出吸收塔,通过除雾器除去剩余携带的液滴,后经GG H 升温后排入烟囱。
鼓泡塔中的浆液分两个区:鼓泡区和反应区。
SO 2的吸收、亚硫酸氧化成硫酸、硫酸中和成石膏和石膏的结晶4种反应是在鼓泡塔中同时完成的。
鼓泡式反应器脱硫技术(CT-121)介绍(课堂PPT)

100 80 60 40 20
0 0.1
烟尘除去性能图
CT-121
1 烟尘粒. 径 [μ m]
10
20
除尘 性 能
通过有效的气液接触,实现稳定的高除尘性能
25 S火力电厂业绩
20
出 口 15 粉 尘 浓 10 度
5 Mg/m3N
G火力电厂业绩 N火力电厂业绩
0
0
25
50
75
入口排尘粒径. Mg/m3N
单位体积的气泡个数: 气泡体积:π/6 x (db)3 x Nb=2/3 气泡直径:db=3mm 气泡个数:Nb=47.2 x 106/m3
Sb:单位体积的气泡表面积: Sb= π x (db)2 x Nb=1,334m2/m3
tb:气液接触时间: tb=0.6mH/1.2m/s=0.5 s
.
19
烟尘除去率 [%]
85
80
75
70
250
3.0
3.5
4.0
pH [ - ]
.
4.5
5.0
15
动力消耗量
CT-121
78
22
喷雾塔工艺
54
52
15
0
50
烟气风机
100
循环泵
.
150
其他
16
公用工程消耗量
通过高效率的气液接触和系统的简化,实现了
较低的厂内动力比
电力消耗量的75%以上集中在排气风机上
气体分散型吸收塔(喷射气泡式)
300 250 200
150 100
50 0
1
副产品石膏的粒度分布
10
100
副产品石膏斯托.克斯[粒子]粒径(µm)
烟气脱硫技术方案

烟气脱硫技术方案烟气脱硫是一项关键的环保技术,旨在防止硫化物排放对大气环境造成污染。
该技术最初是针对燃煤电厂而开发的,但现在在其它许多工业和制造过程中也广泛应用。
本文将描述一个适用于燃煤电厂的烟气脱硫方案。
该方案基于湿法脱硫技术,需要建造一个脱硫设施并安装在排放烟道上。
随后附加设备将对排放时的化学反应进行控制,确保排出的气体符合环保法规。
1. 设备需求湿法脱硫技术需要的设备包括:- 烟囱或烟道:设备必须安装到烟气排放的管道中。
- 除尘器:通过增加过滤器或静电过滤器从烟气中除去粉尘或颗粒物。
- 脱硫设施:包括脱硫剂浆液喷淋塔(或喷淋塔)、反应池和泵、和其中的各种仪器设施和控制系统。
- 废水处理设备:用于处理所产生的废水,在使废水符合环境法规的条件下将其排到外部水体中。
2. 工作原理脱硫技术通过与烟气中的气态污染物反应来除去硫化合物。
湿法脱硫法使用富含碱性成分的溶液将二氧化硫转化为硫酸根离子(SO4 2-)。
脱硫剂溶液可以是碱式氢氧化钙(Ca(OH)2)或氨水(NH3)。
反应方程式如下:钙氢氧化物(Ca(OH)2) + SO2→ CaSO3 + H2OCaSO3 + 1/2O2 → CaSO4氨水(NH3)+ SO2 → NH4HSO3NH4HSO3 + 1/2O2 → NH4HSO4当此处理剂被喷射到排放出来的烟气中时,它与二氧化硫进行反应并将其转换为硫酸根离子。
然后其余的化学反应在反应池中发生。
最终,硫酸根对溶液之中的钙或铵成分反应,从而形成固体或液体废物产物。
3. 设计要点- 需要仔细考虑脱硫效率、耗电量以及工艺变量(如循环率、热量损失等)。
- 脱硫设施必须能够正确运行,并满足当地和国家的法规和要求,以确保排放的气体不会污染环境。
- 系统应根据各自的需求进行优化,以控制化学反应,使用最低的消耗性能和化学剂。
- 废水处理设备需要能够处理脱硫过程中产生的废水,以确保排放到外部水体中的水符合环保法规。
B1电厂600MW机组锅炉烟气脱硫技术特性分析
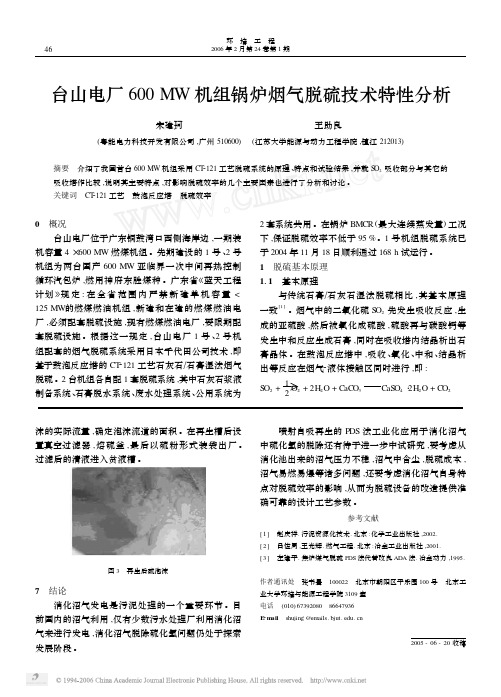
图3 再生后硫泡沫沫的实际流量,确定泡沫流道的面积。
在再生槽后设置真空过滤器,熔硫釜,最后以硫粉形式装袋出厂。
过滤后的清液进入贫液槽。
7 结论消化沼气发电是污泥处理的一个重要环节。
目前国内的沼气利用,仅有少数污水处理厂利用消化沼气来进行发电,消化沼气脱除硫化氢问题仍处于探索发展阶段。
喷射自吸再生的PDS 法工业化应用于消化沼气中硫化氢的脱除还有待于进一步中试研究,要考虑从消化池出来的沼气压力不稳,沼气中含尘,脱硫成本,沼气易燃易爆等诸多问题,还要考虑消化沼气自身特点对脱硫效率的影响,从而为脱硫设备的改造提供准确可靠的设计工艺参数。
参考文献[1] 赵庆祥.污泥资源化技术.北京:化学工业出版社,2002.[2] 吕佐周,王光辉.燃气工程.北京:冶金工业出版社,2001.[3] 左建平.焦炉煤气脱硫PDS 法代替改良ADA 法.冶金动力,1995.作者通讯处 张书景 100022 北京市朝阳区平乐园100号 北京工业大学环境与能源工程学院3109室电话 (010)67392080 86647936E 2m ail shujing @2005-06-20收稿台山电厂600MW 机组锅炉烟气脱硫技术特性分析宋建珂(粤能电力科技开发有限公司,广州510600) 王助良(江苏大学能源与动力工程学院,镇江212013)摘要 介绍了我国首台600MW 机组采用CT 2121工艺脱硫系统的原理、特点和试验结果,并就S O 2吸收部分与其它的吸收塔作比较,说明其主要特点,对影响脱硫效率的几个主要因素也进行了分析和讨论。
关键词 CT 2121工艺 鼓泡反应塔 脱硫效率0 概况台山电厂位于广东铜鼓湾口西侧海岸边,一期装机容量4×600MW 燃煤机组。
先期建设的1号、2号机组为两台国产600MW 亚临界一次中间再热控制循环汽包炉,燃用神府东胜煤种。
广东省《蓝天工程计划》规定:在全省范围内严禁新建单机容量<125MW 的燃煤燃油机组,新建和在建的燃煤燃油电厂,必须配套脱硫设施,现有燃煤燃油电厂,要限期配套脱硫设施。
脱硫塔工艺流程

脱硫塔工艺流程脱硫塔是燃煤电厂中用于减少烟气中二氧化硫排放的重要设备。
脱硫塔工艺流程是指烟气经过脱硫塔进行脱硫处理的整个过程,包括脱硫剂的喷射、吸收、氧化、再生等环节。
下面将详细介绍脱硫塔工艺流程的主要步骤。
首先,烟气进入脱硫塔的底部,在脱硫塔内与喷射的脱硫剂(一般为石灰石浆液或石膏水)充分接触,二氧化硫被脱除。
脱硫剂与烟气中的二氧化硫发生化学反应,生成硫酸钙或硫酸钠等化合物,从而达到脱硫的目的。
其次,脱硫剂与烟气中的二氧化硫发生反应后,生成的硫化物被氧化成硫酸盐,这一步骤是脱硫过程中十分重要的环节。
氧化剂一般为空气或者氧气,通过适当的氧化条件(如适当的温度、氧化剂浓度等),将硫化物氧化成硫酸盐,从而提高脱硫效率。
然后,脱硫塔中的脱硫剂在脱除二氧化硫后,需要进行再生处理。
通常情况下,脱硫剂在脱硫塔中的循环使用,但随着时间的推移,脱硫剂会逐渐被二氧化硫和氧化剂消耗,失去活性。
因此,需要对脱硫剂进行再生处理,以恢复其活性,维持脱硫效率。
再生处理一般采用加热或者干燥的方式,将脱硫剂中的硫酸盐转化为硫酸钙或者硫酸钠,再次投入到脱硫塔中进行脱硫处理。
最后,经过脱硫塔处理后的烟气中的二氧化硫得到有效去除,达到了环保排放标准。
脱硫塔工艺流程的设计和运行对于燃煤电厂的环保排放至关重要,合理的工艺流程和稳定的运行能够有效减少二氧化硫的排放,保护环境,也是燃煤电厂进行环保改造的重点之一。
总之,脱硫塔工艺流程是燃煤电厂中重要的环保设备,其工艺流程包括脱硫剂喷射、吸收、氧化和再生等环节。
通过合理的工艺设计和稳定的运行,可以有效减少烟气中二氧化硫的排放,达到环保排放标准,保护环境,实现可持续发展。
第三章CT121中JBR的内部结构
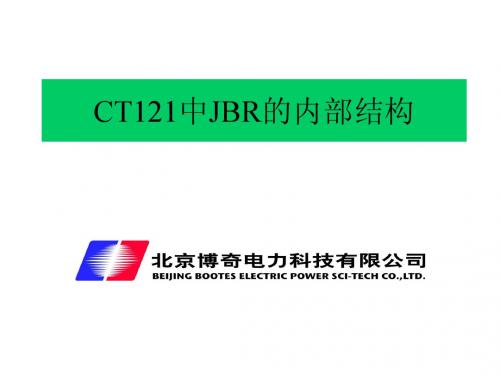
反应区
反应区存在大量的气泡,石灰石浆液直接加入 JBR反应区.JBR在设计上考虑了10~20小时的 反应停留时间,这应使得最初发生于鼓泡区的 化学反应在反应区全部完成,并为下列的反应 过程提供了充分的时间.
– 由反应区下部的氧化空气喷入浆液中被溶解. – 溶解的亚硫酸盐氧化成硫酸盐. – 石灰石溶解 – 石灰石与硫酸反应生成石膏并放出CO2 – 石膏晶体生成
鼓泡式反应器JBR 鼓泡式反应器
JBR容器中的浆液分为两部分(1)鼓泡区(2)反 应区.这是一个非常重要的设计特点,正因为 如此,下面4种反应可以在JBR中同时发生. -二氧化硫(SO2)的吸收 -亚硫酸氧化成硫酸 -硫酸中和形成石膏 -石膏晶体的形成
鼓泡区
鼓泡区是一个由大量不断形成和破碎的气泡组 成的连续的气泡层.当原烟气流经喷射管进入 JBR,在浆液内部产生气泡,从而形成气泡层. 在鼓泡区或气泡层,形成了气-液接触区,在这 个区域中,烟气中的SO2融解在气泡表面的液膜 中.烟气中的飞灰也在接触液膜后被除去.气 泡的直径从3-20mm(在这样大小的气泡中存在 小液滴)不等.大量的气泡产生了巨大的接触 面积,使JBR成为一个非常高程特点 化学过程特点
根据公式(15),石灰石的溶解速率与PH值呈指 数增加关系:
R=K「CaCO3」「H+」 (15) 其中PH = -log「H+」
因此,例如PH值为4时的溶解速率比PH值为6时 约快100倍. 低PH和较长的反应滞留时间使得吸收剂被充分 利用,避免了结垢并使产品易于脱水和充分氧 化.
吸收塔里面的化学反应
喷射管 SO2+H2O O2 H2SO4 CaCO3
石灰石浆液供给
H2SO3
氧化用空气
总反应式 SO2 + 2H2O + 1/2O2+CaCO3
鼓泡塔烟气脱硫处理工艺
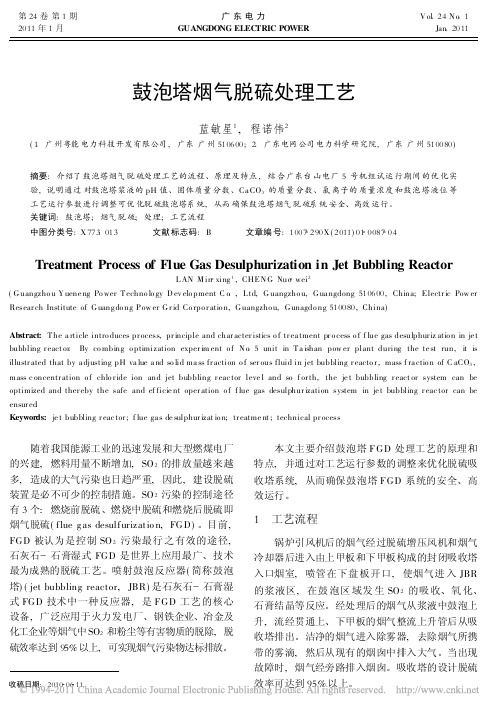
4 鼓泡塔系统优化
作为石灰石- 石膏湿法脱硫系统的核心设备,
JBR 是否稳定、高效运行直接影响整个 FGD 的效 果。影响 JBR 脱硫效率的因素有很多, 其运行过 程中, 锅炉燃烧煤种、机组负荷及烟气量、烟气温 度、烟尘浓度、吸收剂品质等经常发生变化, 如果 采用原来的设计方案, 可能影响整个 F GD 的稳定 运行。因此, 需要对 JBR 系统 进行优化。现结合 2006 年 11 月 21 日投入试运行的广东台山电 厂 5 号机组 168 h 试运行期间的调整情况进行说明。试 运行期间, 通过对 JBR 浆 液的 pH 值、固体质量 分数、CaCO 3 的质量分数 w ( CaCO 3 ) 、氯离子的 质量浓度 ( Cl- ) 和 JBR 液位进 行调整, 确保了 F GD 高效、稳定地运行。
Abstract: T he a rticle intro duces pr ocess, pr inciple and char acter istics o f tr ea tment pr o cess o f f lue gas desulphur iz atio n in je t bubbling r eact or By co mbing o ptimization exper im ent o f N o 5 unit in T a ishan pow er plant during the te st run, it is illustr ated that by a djusting pH va lue a nd so lid ma ss fr action o f ser ous fluid in jet bubbling r eacto r , mass f ra ctio n of C aCO3 , mass c oncentr ation o f chlo r ide ion and jet bubbling r eac tor leve l and so f or th, the je t bubbling r eact or system can be optimized and ther eby the safe and ef ficie nt oper ation o f f lue gas desulphur ization system in je t bubbling r eac tor can be ensur ed Keywords: je t bubbling r eac tor ; f lue ga s de sulphur izat io n; tr eatme nt ; technical pr ocess
- 1、下载文档前请自行甄别文档内容的完整性,平台不提供额外的编辑、内容补充、找答案等附加服务。
- 2、"仅部分预览"的文档,不可在线预览部分如存在完整性等问题,可反馈申请退款(可完整预览的文档不适用该条件!)。
- 3、如文档侵犯您的权益,请联系客服反馈,我们会尽快为您处理(人工客服工作时间:9:00-18:30)。
CT-121鼓泡式吸收塔烟气脱硫工艺技术介绍单选户薛宝华北京博奇电力科技有限公司摘要:介绍CT-121鼓泡式吸收塔脱硫工艺的技术特点。
鼓泡式脱硫工艺是一种先进、成熟的湿式石灰石法脱硫工艺。
本脱硫工艺对于中高硫煤、燃油等性质的烟气具有优越的性能。
本工艺具有SO2脱除率高、对不同含硫量燃料适应性强、具有较低的粉尘排放率、不易结垢、极高的石灰石利用率和大颗粒、高纯度的石膏晶体等优点。
在实际运行中具有优异的可靠性和实用性。
关键词:CT-121,石灰石-石膏法,脱硫,SO2,技术介绍1 概述千代田化工自行开发的CT-121脱硫工艺是一种先进的湿式石灰石法脱硫工艺。
这种工艺尤其对高硫煤、燃油产生的烟气显示出了优越的性能。
这种工艺能够达到95%以上稳定连续的脱硫率、最低10mg/Nm3以下的粉尘排放率以及优异的可靠性和实用性。
1.1CT-121的历史和现状1971年,千代田开发出了第一个脱硫工艺CT-101,并建成了13个商业装置。
千代田化工继续改进和发展这项技术,于1976年开发出了更为先进的CT-121工艺。
这项先进的技术将SO2的吸收、氧化、中和、结晶以及除尘等工艺过程合并到一个单独的气-液-固相反应器中进行。
这个反应器就是鼓泡式吸收塔(JBR)。
鼓泡塔技术目前在世界范围内获得了广泛应用,目前有30多个CT-121脱硫工艺商业装置业绩投入运行。
鼓泡技术目前已应用于单机装机容量最大为10,000MW的脱硫装置。
由于CT-121工艺以其先进性和可靠性被日本的几大公用事业公司认可,因此最近几年来日本的烟气脱硫领域虽然竞争激烈,但鼓泡塔技术商业装置数量仍直线上升。
1.2 CT-121获得的奖项CT-121工艺作为一种先进的FGD技术,被授予了多项著名的奖项。
诸如日本能源研究机构授予的“1990年度奖”;电力杂志授予的美国伊利诺斯州Abbott电站CT-121装置“1990年度电站奖”和美国乔治亚州Yates“1994年度电站奖”;国际电力杂志授予的日本爱知县Hekinan电站CT-121装置“1993年度电站奖”;以及日本发明和创新协会为CT-121工艺发展和应用授予的“1993年度国内发明奖”等,说明该技术已得到了广泛的认可和应用。
1.2博奇科技所引进的鼓泡塔技术北京博奇电力科技有限公司通过大量调查研究后,于2002年底和日本株式会社荏原制作所签订了CT-121技术引进协议,并首次在国内应用于600MW等级烟气脱硫装置上,目前该项目即将建成投产,这将是我国最早投产的600MW等级燃煤机组烟气脱硫装置。
2. 详细的工艺介绍鼓泡塔(JBR)是CT-121工艺的核心部分,如图1所示鼓泡塔提供了高效的气—液接触方式,可以在稳定和可靠的基础上高效地脱除SO2和粉尘。
通过鼓泡装置,烟气均匀地扩散到浆液中,使得JBR达到很高的性能。
烟气先进入烟气冷却烟道,在这里,烟气是通过烟气冷却泵(浆液),辅以补充水和滤液被冷却到饱和状态。
然后,烟气通过浸没在浆液液面以下的许多喷射管喷射到浆液中,并产生一个气泡层,这个气泡层促进了烟气中SO2的吸收。
此外,JBR在设计上将酸性物质的中和、亚硫酸氧化生成石膏以及石膏的结晶等几个过程同时在鼓泡塔中完成。
最后,处理后的净烟气通过除雾器除去携带的液滴,然后经GGH升温后排入烟囱。
2.1 工艺说明CT-121是世界上第一个应用LSFO (石灰石湿法强制氧化) 工艺的烟气脱硫装置。
当今,许多石灰石湿法脱硫工艺改进为LSFO工艺,但是基于鼓泡原理的CT-121工艺仍是最先进的脱硫工艺。
保证CT-121工艺高性能的机理非常简单,但它从根本上改变了湿式FGD的设计理念。
在传统的FGD中,烟气是连续相的,液态吸收剂通过喷淋扩散到烟气或通过塔内的填料或塔盘与烟气接触。
这种方式会导致脱硫率的边际效应,致使传质过程和化学反应动力弱化,从而引起运行过程中的结垢和堵塞。
CT-121工艺正好与传统的概念相反。
在其设计中,液相吸收剂是连续相,而烟气是离散相。
这一设计思想通过其鼓泡塔专利技术来实现,烟气通过鼓泡喷射到塔内的吸收浆液中。
在这种情况下,临界传质和临界化学反应速度的局限性没有了,从而消除了结垢和堵塞,形成了较高的脱硫效率。
2.2 鼓泡式吸收塔鼓泡塔是CT-121工艺的核心,烟气通过喷射管均匀分布到JBR的浆液取。
按化学方法推算,当气泡上升通过鼓泡层时,JBR产生多级的传质过程,由于气-液的多级接触和庞大的接触面积(是通常喷淋工艺的数十倍),传质速率很高。
原烟气进入由上下隔板形成的封闭容器中。
喷管安装在下隔板上,将原烟气导入吸收塔的浆液区。
烟气从浆液中鼓泡上升,流经贯通上下隔板的上升管。
由于烟速很低,烟气中携带的液滴在上层隔板的空间被沉降分离,处理后的净烟气流出吸收塔,通过除雾器除去剩余携带的液滴,后经GGH升温后排入烟囱。
鼓泡塔中浆液分两个区:鼓泡区和反应区。
下面4种反应在鼓泡塔中同时完成。
—— SO2的吸收——亚硫酸氧化成硫酸——硫酸中和生成石膏——石膏的结晶2.2.1鼓泡区鼓泡区是一个由大量不断形成和破碎的气泡组成的连续气泡层。
如图2所示,当原烟气流经喷射管进入浆液内部产生气泡,从而形成气泡层。
在鼓泡区,形成了很大的气-液接触区,在这个区域中,烟气中的SO2溶解在气泡表面的液膜中。
烟气中的飞灰也在接触液膜后被除去。
气泡的直径从3-20mm(在这样大小的气泡中存在小液滴)不等。
大量的气泡产生了巨大的接触面积,使JBR成为一个非常高效的多级气-液接触器。
鼓泡区气泡大量和迅速地不断的生成和破裂使气-液接触能力进一步加强,从而不断产生新的接触面积,同时将反应物由鼓泡区传递至反应区,并使新鲜的吸收剂与烟气接触。
脱硫率取决于喷射管的浸没深度和浆液的PH值。
在燃煤Sar=1%,正常的PH定值下,浸液深度通常为150mm左右时,脱硫率大于95%。
通过调节从石膏脱水系统返回的液量,可以对浸液深度进行自动调节。
2.2.2反应区反应区在鼓泡区以下,石灰石浆液直接补入反应区。
鼓泡塔浆池容积在设计上考虑了15-20h的浆液滞留时间,为下列的反应过程提供了充分的反应时间。
* 氧化空气在浆液中被充分溶解;* 吸收的亚硫酸氧化成硫酸;* 石灰石溶解;* 石灰石与硫酸中和反应;* 石膏晶体生成。
JBR的运行PH值设计为4.5-5.2,这种相对较低的PH值使石灰石溶解更加快速彻底。
低PH值环境下的快速和完善的氧化系统是JBR成功运行的关键。
浆液中鼓入空气并排挤出溶解的CO2,进一步促进了石灰石的溶解。
因而,JBR的浆液成分主要是石膏晶体。
通过排出一定的浆液至脱水(和废水处理)系统,使JBR内浆液中固形物浓度保持在10-25%范围。
2.2.3 内部浆液循环传统的FGD工艺采用的气-液接触方式,通过一系列大流量浆液循环泵和管道将大量的吸收剂提升至喷淋层进行循环,形成一个气-液接触区,从而有了液-气比(L/G)这个概念。
而JBR中大直径、低转速的搅拌器和喷入的氧化空气形成的搅动一起,为鼓泡区和反应区吸收剂的交换提供了循环动力。
所有的浆液循环都是在浆池内部的循环,不需要外部的循环泵和管道。
因此,在CT-121工艺中,L/G 这个参数已没有实际意义。
JBR的内部循环速度相当于浆液的流动速度,在0.1-0.3m/s间。
在JBR底部,液体由中心向外侧流动,并沿筒壁垂直上升,至JBR浆液层顶部以后,液体由外侧向中心流动,并沿搅拌器轴向下降,形成了一个对流循环过程。
3. 化学过程特点3.1 CT-121脱硫工艺的化学反应尽管CT-121工艺与传统的湿式石灰式工艺的化学反应大体相似,但化学反应的机理是不同的。
两者之间最大的不同在于运行中的PH值。
CT-121工艺的低PH值增强了石灰石的溶解和亚硫酸的氧化,提高了石灰石的利用率。
当PH值在4.5-5.3之间时,石灰石的溶解非常迅速和完全,JBR的浆液中基本不存在固态的碳酸钙。
JBR的低PH值和较长的滞留时间,使石灰石的利用率在98-100%之间。
此外,在低PH值下,由于氢离子(H+)和亚硫酸根离子(HSO3-)的浓度增大,氧化速度也大大加快了。
本文来自在JBR中,氧化过程与SO2的吸收过程在同一区域进行,因而提高了SO2的传质速率,这种快速的氧化过程保证了液体中SO2处于低浓度状态,使得在低PH值的条件下,有更多的气态SO2被吸收。
化学方程式(1)是CT-121工艺的总反应式:SO2+CaCO3+1/2O2+2H2O→CaSO4.2H2O+CO2 (1)3.1.1鼓泡区的化学反应:在JBR中同时发生5种反应过程(吸收,氧化,中和,石灰石溶解和结晶),反应最初发生于鼓泡区并于泡沫区下部的反应区里完成。
首先,SO2被气泡表面的液体吸收并溶解于水中,如下面的反应式(2)所示:SO2(g)→SO2(aq)......................................... .... .... .... .... (2)然后,溶解的SO2与水反应生成亚硫酸,如反应式(3)所示:SO2(aq)+H2O→H2SO3 ................................... (3)亚硫酸分解为离子,亚硫酸根离子被溶解在液体中的氧气氧化生成硫酸根离子:H2SO3 →HSO3-+H+ (4)HSO3-+1/2O2(aq)→SO42-+H+ (5)CT-121工艺的一个重要优点就是部分亚硫酸的氧化发生在鼓泡层。
当亚硫酸被氧化以后,它的浓度就会降低,因而促进了SO2的吸收。
石灰石溶解并离解产生钙离子。
并与硫酸根离子发生中和反应生成石膏。
CaCO3(S)←→CaCO3(aq) (6)CaCO3(aq)+2H+←→Ca2++CO2+H2O (7)Ca2++SO42-+2H2O→CaSO4.2H2O (8)在鼓泡区,SO2的气相传质过程(反应式2)和CaCO3的离解过程(反应式6)是控制反应速度的主要过程。
这两个过程都在JBR特有的运行环境下得到了强化。
同时,SO2向液相的传质过程通过鼓泡区的搅动得到增强。
碳酸钙的离解由于低PH值得到加强。
3.1.2反应区的化学过程:反应区为空气中氧气的溶解和石膏晶体的形成提供了足够的液体滞留时间。
JBR中的搅拌器使得反应区中的组分充分混合,以便向鼓泡区输送所需的组分。
由靠近JBR底部注入的空气中的氧气溶解过程如下:O2(g) → O2(aq) (9)在鼓泡区没有被氧化的亚硫酸根在反应区被氧化成硫酸根。
HSO3-+1/2O2(aq)→SO42-+H+ (10)亚硫酸根离子的氧化(反应式10)产生了氢离子(H+),使JBR内形成了所需的酸性环境,酸性溶液和液体中溶解的碳酸钙促进了中和反应产生并生成了石膏。
反应过程如下列反应方程式所示:CaCO3(S)←→CaCO3(aq) (11)CaCO3(aq)+2H+←→Ca2++CO2(g)+H2O (12)Ca2++SO42-+2H2O→CaSO4.2H2O (13)CaSO4.2H2O→晶体生成 (14)O2的溶解过程(反应式9)和副产品石膏的结晶过程(反应式14)是控制反应速度的关键过程。