第二课 橡胶加工工艺
橡胶加工工艺流程
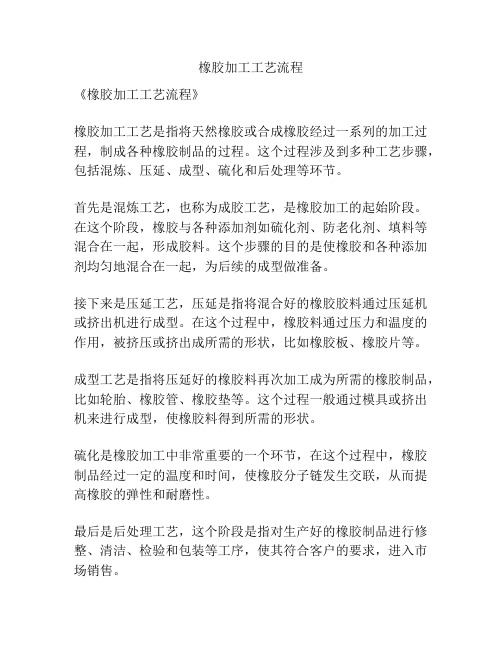
橡胶加工工艺流程
《橡胶加工工艺流程》
橡胶加工工艺是指将天然橡胶或合成橡胶经过一系列的加工过程,制成各种橡胶制品的过程。
这个过程涉及到多种工艺步骤,包括混炼、压延、成型、硫化和后处理等环节。
首先是混炼工艺,也称为成胶工艺,是橡胶加工的起始阶段。
在这个阶段,橡胶与各种添加剂如硫化剂、防老化剂、填料等混合在一起,形成胶料。
这个步骤的目的是使橡胶和各种添加剂均匀地混合在一起,为后续的成型做准备。
接下来是压延工艺,压延是指将混合好的橡胶胶料通过压延机或挤出机进行成型。
在这个过程中,橡胶料通过压力和温度的作用,被挤压或挤出成所需的形状,比如橡胶板、橡胶片等。
成型工艺是指将压延好的橡胶料再次加工成为所需的橡胶制品,比如轮胎、橡胶管、橡胶垫等。
这个过程一般通过模具或挤出机来进行成型,使橡胶料得到所需的形状。
硫化是橡胶加工中非常重要的一个环节,在这个过程中,橡胶制品经过一定的温度和时间,使橡胶分子链发生交联,从而提高橡胶的弹性和耐磨性。
最后是后处理工艺,这个阶段是指对生产好的橡胶制品进行修整、清洁、检验和包装等工序,使其符合客户的要求,进入市场销售。
总体来说,橡胶加工工艺流程是一个复杂而又精细的过程,需要经过多个工艺步骤才能最终制成高质量的橡胶制品。
只有严格执行每一个工艺步骤,才能保证生产出优质的橡胶制品,满足客户的需求。
橡胶加工工艺及配方
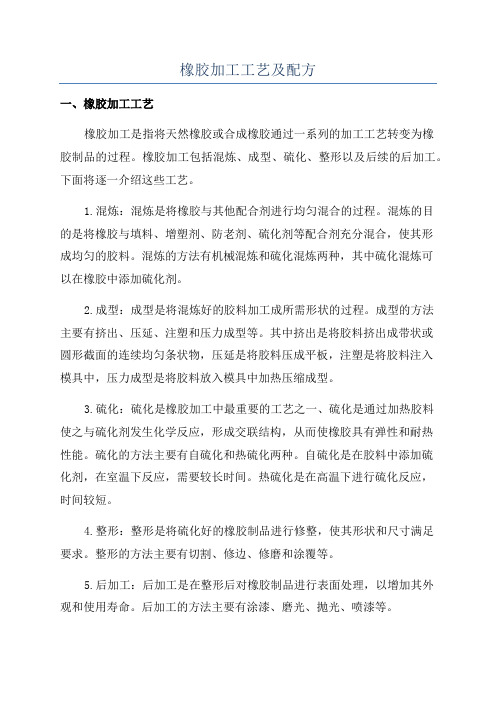
橡胶加工工艺及配方一、橡胶加工工艺橡胶加工是指将天然橡胶或合成橡胶通过一系列的加工工艺转变为橡胶制品的过程。
橡胶加工包括混炼、成型、硫化、整形以及后续的后加工。
下面将逐一介绍这些工艺。
1.混炼:混炼是将橡胶与其他配合剂进行均匀混合的过程。
混炼的目的是将橡胶与填料、增塑剂、防老剂、硫化剂等配合剂充分混合,使其形成均匀的胶料。
混炼的方法有机械混炼和硫化混炼两种,其中硫化混炼可以在橡胶中添加硫化剂。
2.成型:成型是将混炼好的胶料加工成所需形状的过程。
成型的方法主要有挤出、压延、注塑和压力成型等。
其中挤出是将胶料挤出成带状或圆形截面的连续均匀条状物,压延是将胶料压成平板,注塑是将胶料注入模具中,压力成型是将胶料放入模具中加热压缩成型。
3.硫化:硫化是橡胶加工中最重要的工艺之一、硫化是通过加热胶料使之与硫化剂发生化学反应,形成交联结构,从而使橡胶具有弹性和耐热性能。
硫化的方法主要有自硫化和热硫化两种。
自硫化是在胶料中添加硫化剂,在室温下反应,需要较长时间。
热硫化是在高温下进行硫化反应,时间较短。
4.整形:整形是将硫化好的橡胶制品进行修整,使其形状和尺寸满足要求。
整形的方法主要有切割、修边、修磨和涂覆等。
5.后加工:后加工是在整形后对橡胶制品进行表面处理,以增加其外观和使用寿命。
后加工的方法主要有涂漆、磨光、抛光、喷漆等。
二、橡胶配方橡胶配方是指将橡胶与各种配合剂按一定比例混合,形成胶料的配方。
橡胶配方的配料包括橡胶本体、填充剂、增塑剂、硬化剂、防老剂、防护剂、促进剂等。
下面将介绍常用的橡胶配方。
1.橡胶本体:橡胶本体是指原料橡胶,可以是天然橡胶或合成橡胶。
常用的橡胶有天然橡胶、丁苯橡胶、丁腈橡胶、氯丁橡胶、丁基橡胶等。
2.填充剂:填充剂是指填充到橡胶中的无机或有机物质,可以改变橡胶的物理和机械性能。
常用的填充剂有炭黑、白炭黑、沉香末、沥青等。
3.增塑剂:增塑剂是指能增加橡胶柔软性和延展性的物质。
常用的增塑剂有塑化油、脂肪酸酯、酸酐和酯类增塑剂等。
橡胶加工工艺—橡胶压出工艺(高分子成型课件)
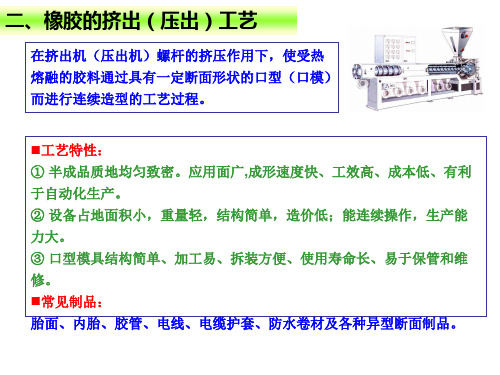
二、橡胶的挤出(压出)工艺
(一)压出机工作原理及胶料的运动状态 3 物料在口型中的流动状体和挤出变形 胶料经机头进入口型后,由于口型形状不同及内表 面对物料流动的阻碍,物料流动速度也存在有与机 头类似的速度分布。中间流速大,越接近口型壁流 速越小 。 一般粘弹性的物料,从口型挤出后就不可避免地存 在松弛现象,即:胶条的长度会沿挤出方向缩短, 厚度沿垂直挤出方向增加(离模膨胀现象或称作挤 出变形现象)。挤出后的变形(收缩和膨胀)可以控制 在一定范围,但不可能完全消除。要求收缩率为 2~5%。 物料可塑性小、含胶率大,填充剂用量小,物料挤 出快,机头和口型温度低,膨胀和收缩率就大。
二、橡胶的挤出(压出)工艺
在挤出机(压出机)螺杆的挤压作用下,使受热 熔融的胶料通过具有一定断面形状的口型(口模) 而进行连续造型的工艺过程。
工艺特性: ① 半成品质地均匀致密。应用面广,成形速度快、工效高、成本低、有利 于自动化生产。 ② 设备占地面积小,重量轻,结构简单,造价低;能连续操作,生产能 力大。 ③ 口型模具结构简单、加工易、拆装方便、使用寿命长、易于保管和维 修。 常见制品: 胎面、内胎、胶管、电线、电缆护套、防水卷材及各种异型断面制品。
二、橡胶的挤出(压出)工艺
(一)压出机工作原理及胶料的运动状态
1 胶料在挤出机中的运动状态
加料段:加入的条状胶料,受到旋转螺杆的推挤作用形成连续的胶 团,并沿着螺槽的空间一边旋转,一边不断前进。 压缩段:加料段输送过来的松散胶团在压缩段被逐渐压实、软化, 并把夹带的空气向加料段排出。同时胶团间间隙缩小,密度增高, 进而粘在一起,再加上受到剪切和搅拌作用,因而胶团逐渐被加热 塑化形成连续的粘流体。 挤出段:在挤出段,压缩段输送过来的物料进一步塑化均匀,并输 送到机头和口模处挤出成型。
橡胶加工工艺

3
橡胶的简介
橡胶的作用
橡胶是橡胶工业的重要原料,用以制造轮 胎、胶管、胶带、胶辊等各种橡胶制品。橡胶 还广泛用于电线电缆、纤维和纸加工、石棉以 及塑料改性等方面。世界橡胶耗量中,约80%用 于橡胶工业。在橡胶制品中,轮胎是其典型的 代表性产品,轮胎的用胶量约占全部橡胶耗用 量的50%~70%。
橡胶加工工艺
1
目录
1
橡胶的简介
2
橡胶的塑炼和混炼
3
橡胶挤出4橡胶源自化5制品去飞边6
二次硫化
7
检验
2
橡胶的简介
橡胶是一种高分子弹性化合物,其分子量一般都在10万以上, 有的甚至达到100万以上。组成这种大分子的原子通常排列成 柔性的直链或支链,由于原子的不断旋转和振动,分子链一 般呈卷缩状态。
橡胶区别于其它工业材料的最主要标志是它在很宽的温度范 围内(-50℃~+150℃)具有优异的弹性。例如其伸长率可达 100%~1000%,为钢的300倍,但其弹性模量仅为2~4MPa, 约为钢材的1/30000.
硫化前:线形结构,分子间以范德华力相互作用 性能: 可塑性大,伸长率高,具可溶性。
硫化剂(S) 牵线搭桥
硫化时:分子被引发,发生化学交联反应
硫化后:网状结构,分子间主要已以化学键结合 结构:1)化学键;2)交联键的位置;3)交联程 度;4)交联 性能:1)力学性能(定伸强度、硬度、拉伸强度、 伸长率、弹性);2)物理性能;3)化学稳定性
13
橡胶的塑炼和混炼
2. 塑炼作用 分子量 Ø变小 分子量分布 Ø变窄
橡胶加工工艺-橡胶的混炼
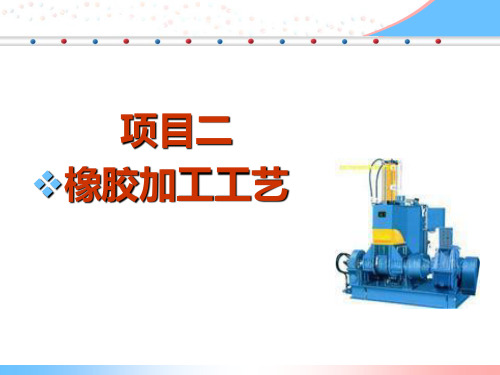
❖ 混炼的目的、意义和要求
❖ 为了提高橡胶使用性能、改进工艺性能和降低成本,
要在橡胶中添加各种配合剂。
❖ 在炼胶机上将各种配合剂加入生胶中制成混炼胶的工 艺过程称之为混炼。
❖ 混炼的内涵
❖ 混炼中发生复杂的物理、化学变化,绝不仅仅是简单 的混合。
炭黑被生胶和软化剂浸润和分散
炭黑与生胶之间产生强的相互作用(物理吸附为主)
项目二 ❖橡胶加工工艺
学习目标
❖ 知识目标 ❖ 1.熟悉橡胶加工的基本工艺过程 ❖ 2.掌握物料的配制对加工及制品性能的影响 ❖ 3.掌握橡胶的塑炼和混炼的原理及工艺参数 ❖ 4.掌握橡胶压延挤出的特点、工艺原理及工艺过程 ❖ 5.掌握橡胶硫化工艺历程及各阶段的特点 ❖ 6.掌握正硫化点的概念及其与制品性能的关系
工伤事故。
❖ 1.混炼过程 ❖ (1)包辊
堆积胶
包辊胶
橡胶在开炼机中的几种状况
1-不易进入辊缝;2-紧包前辊;3-脱辊成袋囊状;4-呈粘流态包辊
❖ (2)吃粉
粉料
堆积胶断面图 (黑色部分表示配合剂随皱纹沟进入胶料内部的 情况)
❖ (3)翻炼
混炼胶吃粉时断面图
❖ 混炼的第三个阶段为翻炼。由于橡胶黏度大,混炼时 胶料只沿着开炼机辊筒转动方向产生周向流动,而没有轴 向流动,而且沿周向流动的橡胶也仅为层流,因此大约在 胶片厚度约1/3处的紧贴前辊筒表面的胶层不能产生流 动而成为“死层”或“呆滞层”,见图4-3所示。此外,辊 缝上部的堆积胶还会形成部分楔形“回流区”。以上原因都 使胶料中的配合剂分散不均。
❖ 因此,必须经多次翻炼,左右割刀、打卷或三角包,薄通 等,才能破坏死层和回流区,使混炼均匀,确保质地均一。
❖ 2.开炼机混炼的工艺条件
橡胶加工工艺流程
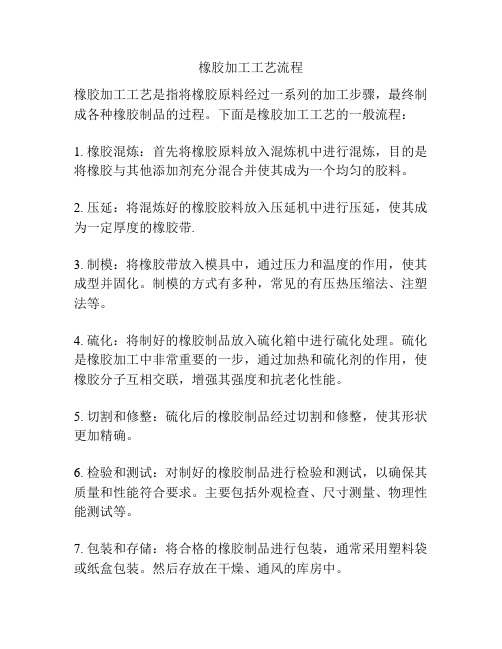
橡胶加工工艺流程
橡胶加工工艺是指将橡胶原料经过一系列的加工步骤,最终制成各种橡胶制品的过程。
下面是橡胶加工工艺的一般流程:
1. 橡胶混炼:首先将橡胶原料放入混炼机中进行混炼,目的是将橡胶与其他添加剂充分混合并使其成为一个均匀的胶料。
2. 压延:将混炼好的橡胶胶料放入压延机中进行压延,使其成为一定厚度的橡胶带.
3. 制模:将橡胶带放入模具中,通过压力和温度的作用,使其成型并固化。
制模的方式有多种,常见的有压热压缩法、注塑法等。
4. 硫化:将制好的橡胶制品放入硫化箱中进行硫化处理。
硫化是橡胶加工中非常重要的一步,通过加热和硫化剂的作用,使橡胶分子互相交联,增强其强度和抗老化性能。
5. 切割和修整:硫化后的橡胶制品经过切割和修整,使其形状更加精确。
6. 检验和测试:对制好的橡胶制品进行检验和测试,以确保其质量和性能符合要求。
主要包括外观检查、尺寸测量、物理性能测试等。
7. 包装和存储:将合格的橡胶制品进行包装,通常采用塑料袋或纸盒包装。
然后存放在干燥、通风的库房中。
以上是橡胶加工工艺的一般流程,不同的橡胶制品可能会有一些特殊的工艺步骤。
橡胶加工的过程中,需注意橡胶原料的质量、混炼工艺参数、硫化条件等。
只有严格控制每一个环节,才能制备出质量稳定、性能优越的橡胶制品。
橡胶加工工艺
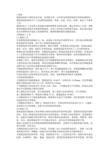
1综述橡胶制品的主要原料是生胶、各种配合剂、以及作为骨架材料的纤维和金属材料,橡胶制品的基本生产工艺过程包括塑炼、混炼、压延、压出、成型、硫化6个基本工序。
橡胶的加工工艺过程主要是解决塑性和弹性矛盾的过程,通过各种加工手段,使得弹性的橡胶变成具有塑性的塑炼胶,在加入各种配合剂制成半成品,然后通过硫化是具有塑性的半成品又变成弹性高、物理机械性能好的橡胶制品。
2橡胶加工工艺2.1塑炼工艺生胶塑炼是通过机械应力、热、氧或加入某些化学试剂等方法,使生胶由强韧的弹性状态转变为柔软、便于加工的塑性状态的过程。
生胶塑炼的目的是降低它的弹性,增加可塑性,并获得适当的流动性,以满足混炼、亚衍、压出、成型、硫化以及胶浆制造、海绵胶制造等各种加工工艺过程的要求。
掌握好适当的塑炼可塑度,对橡胶制品的加工和成品质量是至关重要的。
在满足加工工艺要求的前提下应尽可能降低可塑度。
随着恒粘度橡胶、低粘度橡胶的出现,有的橡胶已经不需要塑炼而直接进行混炼。
在橡胶工业中,最常用的塑炼方法有机械塑炼法和化学塑炼法。
机械塑炼法所用的主要设备是开放式炼胶机、密闭式炼胶机和螺杆塑炼机。
化学塑炼法是在机械塑炼过程中加入化学药品来提高塑炼效果的方法。
开炼机塑炼时温度一般在80℃以下,属于低温机械混炼方法。
密炼机和螺杆混炼机的排胶温度在120℃以上,甚至高达160-180℃,属于高温机械混炼。
生胶在混炼之前需要预先经过烘胶、切胶、选胶和破胶等处理才能塑炼。
几种胶的塑炼特性:天然橡胶用开炼机塑炼时,辊筒温度为30-40℃,时间约为15-20min;采用密炼机塑炼当温度达到120℃以上时,时间约为3-5min。
丁苯橡胶的门尼粘度多在35-60之间,因此,丁苯橡胶也可不用塑炼,但是经过塑炼后可以提高配合机的分散性顺丁橡胶具有冷流性,缺乏塑炼效果。
顺丁胶的门尼粘度较低,可不用塑炼。
氯丁橡胶得塑性大,塑炼前可薄通3-5次,薄通温度在30-40℃。
乙丙橡胶的分子主链是饱和结构,塑炼难以引起分子的裂解,因此要选择门尼粘度低的品种而不用塑炼。
简述橡胶加工工艺

简述橡胶加工工艺一、塑炼橡胶受外力作用产生变形,当外力消除后橡胶仍能保持其形变的能力叫做可塑性。
增加橡胶可塑性工艺过程称为塑炼。
橡胶有可塑性才能在混炼时与各种配合剂均匀混合;在压延加工时易于渗入纺织物中;在压出、注压时具有较好的流动性。
此外,塑炼还能使橡胶的性质均匀,便于控制生产过程。
但是,过渡塑炼会降低硫化胶的强度、弹性、耐磨等性能,因此塑炼操作需严加控制。
橡胶可塑度通常以威廉氏可塑度、门尼粘度和德弗硬度等表示。
1、塑炼机理橡胶经塑炼以增加其可塑性,其实质乃是使橡胶分子链断裂,降低大分子长度。
断裂作用既可发生于大分子主链,又可发生于侧链。
由于橡胶在塑炼时,遭受到氧、电、热、机械力和增塑剂等因素的作用,所以塑炼机理与这些因素密切相关,其中起重要作用的则是氧和机械力,而且两者相辅相成。
通常可将塑炼区分为低温塑炼和高温塑炼,前者以机械降解作用为主,氧起到稳定游离基的作用;后者以自动氧化降解作用为主,机械作用可强化橡胶与氧的接触。
塑炼时,辊筒对生胶的机械作用力很大,并迫使橡胶分子链断裂,这种断裂大多发生在大分子的中间部分。
塑炼时,分子链愈长愈容易切断。
顺丁胶等之所以难以机械断链,重要原因之一就是因为生胶中缺乏较高的分子量级分。
当加入高分子量级分后,低温塑炼时就能获得显著的效果。
氧是塑炼中不可缺少的因素,缺氧时,就无法获得预期的效果。
生胶塑炼过塑炼时,设备与橡胶之间的摩擦显然使得胶温升高。
热对塑炼效果极为重要,而且在不同温度范围内的影响也不同。
由于低温塑炼时,主要依靠机械力使分子链断裂,所以在像章区域内(天然胶低于110℃)随温度升高,生胶粘度下降,塑炼时受到的作用力较小,以致塑炼效果反而下降。
相反,高温塑炼时,主要是氧化裂解反应起主导作用,因而塑炼效果在高温区(天然胶高于110℃)将随温度的升高而增大,所以温度对塑炼起着促进作用。
各种橡胶由于特性不同,对应于最低塑炼效果的温度范围也不一样,但温度对塑炼效果影响的曲线形状是相似的。
橡胶加工工艺

橡胶加工工艺橡胶加工工艺是将天然橡胶或合成橡胶进行加工,制造成各种橡胶制品的过程。
由于橡胶具有良好的弹性、耐磨、耐压、耐酸碱等特性,所以广泛应用于机械、汽车、电子、医疗等领域。
下面就来介绍橡胶加工的工艺流程,以及影响橡胶加工质量的因素。
橡胶加工的工艺流程主要包括橡胶混炼、成型、硫化三个过程。
1. 橡胶混炼橡胶混炼是将原料橡胶与各种填料、助剂、硫化剂按一定比例混合并加热、搅拌,使其均匀分散,达到预先设定的物理、机械、化学性能要求的过程。
混炼也是影响橡胶加工质量的关键环节。
橡胶混炼一般分为二次混炼和三次混炼,其中二次混炼是为了将原料橡胶与填料、助剂充分混合,三次混炼是为了均匀分散硫化剂,使橡胶具有较好的硫化性能。
2. 成型成型是将混炼好的橡胶料按设计要求加工成各种形状的过程,包括挤出成型、压延成型、模压成型等。
在成型过程中,需要注意橡胶与模具的接触面要光滑,压力均匀,否则会影响产品的质量。
3. 硫化硫化是将加工好的橡胶制品放入硫化炉中,在一定时间内加热硫化处理,使其具有良好的强度、硬度、弹性和耐用性。
硫化的温度、时间、压力等参数需要根据橡胶种类和要求进行设置。
因此,硫化是影响橡胶制品质量的关键环节之一。
除了上述工艺流程外,影响橡胶加工质量的因素还包括原材料质量、工艺控制、操作人员技术水平等方面。
橡胶加工使用的原材料包括原料橡胶、填充料、助剂、硫化剂等。
因此,需要选择优质的原材料,控制各种物料和剂量的比例,确保各项物理、机械、化学性能达到预期。
此外,工艺控制也十分关键,需要根据不同的橡胶种类和要求,对加热、搅拌、压力等参数进行精确控制。
对操作人员技术水平的要求也很高,需要经过专业培训和实际操作,熟练掌握各种加工工艺和设备使用技巧。
总之,橡胶加工工艺是一项综合性很强的技术活,在加工中需要注意各种细节问题,进行有效的质量控制,才能制造出性能良好、品质优异的橡胶制品。
橡胶的加工方法

橡胶的加工方法
橡胶制品加工主要包括塑炼、混炼、压延或压出(即挤出)、成型和硫化等基本工序,其中每个过程针对制品有不同要求,分别配合以若干辅助操作。
具体加工方法如下:
1. 塑炼:为了能将各种所需的配合剂加入橡胶中,生胶首先需经过塑炼提高其塑性。
2. 混炼:通过混炼将炭黑及各种橡胶助剂与橡胶均匀混合成胶料。
3. 压出:胶料经过压出制成一定形状的坯料。
4. 成型:将各种形状和尺寸的胶料半成品与浸、涂胶的纺织材料按产品的不同要求,粘贴在一起,制成供硫化用的半成品,这也是橡胶加工中比较关键的工序。
成型既可以通过传统的方式先成型为一定形状半成品,然后硫化为成品,也可以借助注压机,将胶料直接注入模具中进行硫化。
5. 硫化:经过硫化又将具有塑性的半成品制成高弹性的最终产品。
此外,在涂胶过程中,会挥发出大量的汽油蒸气,而在设备运转时,摩擦会产生大量的静电放电,因此很容易导致火灾事故的发生。
为了消除涂胶时的静电,各橡胶企业采用喷雾增湿法,效果很好,消除了静电起火。
同时,熬油、冲油、上光等工序也存在很大的火灾危险性,操作中必须认真遵守安全规程,以防发生火灾事故,并应注意操作岗位的通风和测温。
以上信息仅供参考,如果想要了解更多关于橡胶加工方法的资讯,建议查阅专业橡胶书籍或咨询相关业内人士。
橡胶加工图文全过程
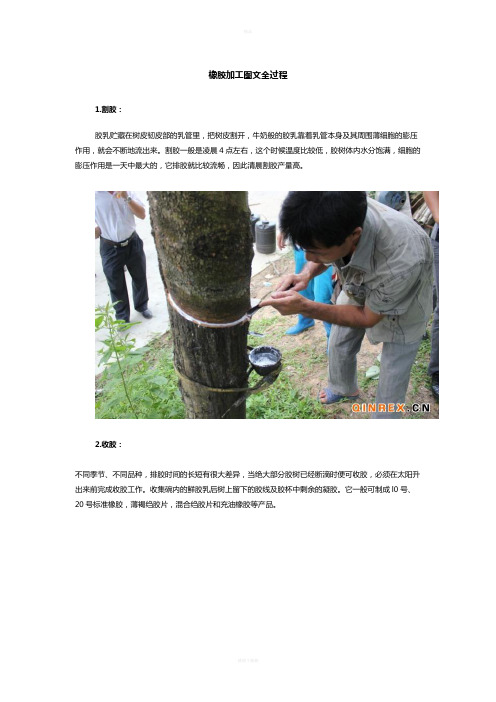
橡胶加工图文全过程1.割胶:胶乳贮藏在树皮韧皮部的乳管里,把树皮割开,牛奶般的胶乳靠着乳管本身及其周围薄细胞的膨压作用,就会不断地流出来。
割胶一般是凌晨4点左右,这个时候温度比较低,胶树体内水分饱满,细胞的膨压作用是一天中最大的,它排胶就比较流畅,因此清晨割胶产量高。
2.收胶:不同季节、不同品种,排胶时间的长短有很大差异,当绝大部分胶树已经断滴时便可收胶,必须在太阳升出来前完成收胶工作。
收集碗内的鲜胶乳后树上留下的胶线及胶杯中剩余的凝胶。
它一般可制成l0号、20号标准橡胶,薄褐绉胶片,混合绉胶片和充油橡胶等产品。
3.胶乳净化:胶乳净化是通过过滤、离心分离(如图)、自然沉降等方法除去胶乳中的杂质。
橡胶中的杂质,会使橡胶制品的性能降低。
如不耐撕裂、不耐磨耗、生热高、轮胎脱层等。
对于标准胶来说,杂质含量是一项主要的指标。
因此,胶乳净化是确保提高橡胶质量的关键措施。
4.胶乳凝固:在凝固槽中导入净化后的胶乳加酸凝固。
这种加酸凝固工艺目前使用较为普遍,是影响天然橡胶质量的重要环节之一。
胶乳的凝固方法、凝固浓度、凝块熟化时间等会影响制得橡胶的塑性保持率。
橡胶可塑性对橡胶制品生产的工艺操作有着重要意义。
5.压薄、压绉:把凝固的胶乳通过机械滚压,脱水变为较薄,厚度一致的凝块。
这增加了胶片的表面积,缩短干燥时间。
同时使胶料的强度增加和得到初步造型的目的,有利于保证胶料进一步加工的质量,提高生产效率。
6.造粒:胶料经锤磨机造粒,所得粒子形状不规则,有孔隙,表面粗糙,使得胶料的后续过程干燥、包装等操作条件得到改善。
通过造粒,使胶料物理性能和堆积比重得到较大提高。
节约运输、储存、包装空间,使加工后橡胶的商品价值和市场竞争力得到提升。
7.干燥:把湿颗粒胶装入干燥车进行烘干。
颗粒胶加工时的干燥程度会影响制成标准胶的挥发含量。
当橡胶中的挥发物含量越低,在贮存过程中越难长霉,在生产中的应用性也越强,在制品加工过程中焦烧危险性越小,塑炼效果越好,因此容易生产出质量高的橡胶制品。
橡胶加工工艺技术
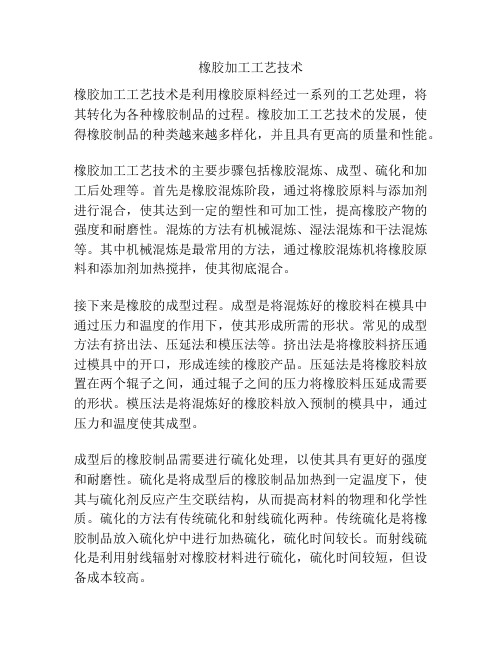
橡胶加工工艺技术橡胶加工工艺技术是利用橡胶原料经过一系列的工艺处理,将其转化为各种橡胶制品的过程。
橡胶加工工艺技术的发展,使得橡胶制品的种类越来越多样化,并且具有更高的质量和性能。
橡胶加工工艺技术的主要步骤包括橡胶混炼、成型、硫化和加工后处理等。
首先是橡胶混炼阶段,通过将橡胶原料与添加剂进行混合,使其达到一定的塑性和可加工性,提高橡胶产物的强度和耐磨性。
混炼的方法有机械混炼、湿法混炼和干法混炼等。
其中机械混炼是最常用的方法,通过橡胶混炼机将橡胶原料和添加剂加热搅拌,使其彻底混合。
接下来是橡胶的成型过程。
成型是将混炼好的橡胶料在模具中通过压力和温度的作用下,使其形成所需的形状。
常见的成型方法有挤出法、压延法和模压法等。
挤出法是将橡胶料挤压通过模具中的开口,形成连续的橡胶产品。
压延法是将橡胶料放置在两个辊子之间,通过辊子之间的压力将橡胶料压延成需要的形状。
模压法是将混炼好的橡胶料放入预制的模具中,通过压力和温度使其成型。
成型后的橡胶制品需要进行硫化处理,以使其具有更好的强度和耐磨性。
硫化是将成型后的橡胶制品加热到一定温度下,使其与硫化剂反应产生交联结构,从而提高材料的物理和化学性质。
硫化的方法有传统硫化和射线硫化两种。
传统硫化是将橡胶制品放入硫化炉中进行加热硫化,硫化时间较长。
而射线硫化是利用射线辐射对橡胶材料进行硫化,硫化时间较短,但设备成本较高。
最后是橡胶制品的加工后处理。
加工后处理是将硫化好的橡胶制品进行去毛刺、除弧、喷涂等工序,以使其更加光滑、美观和耐用。
加工后处理的方法因产品而异,可以通过手工处理、机械处理和化学处理等多种方式。
总之,橡胶加工工艺技术是将橡胶原料加工成各种橡胶制品的过程,包括混炼、成型、硫化和加工后处理等步骤。
随着技术的不断进步,橡胶制品的品种越来越多样化,具有更高的品质和性能。
橡胶加工工艺技术的发展对于橡胶行业的发展具有重要的意义,推动了橡胶制品的生产和应用的不断创新。
橡胶的工艺流程
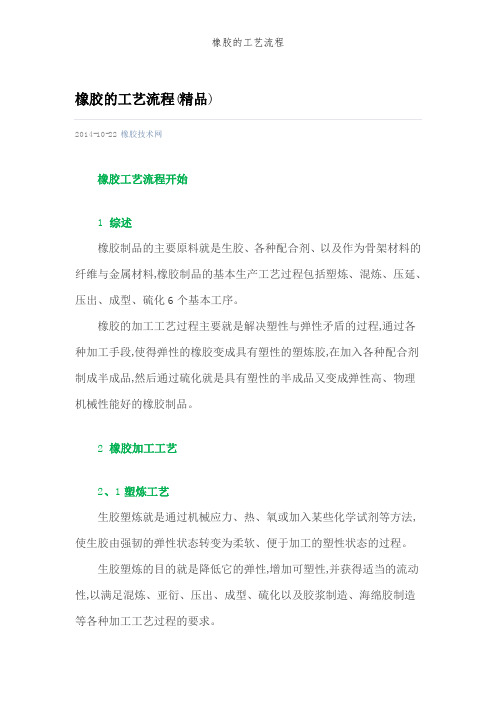
橡胶的工艺流程(精品)2014-10-22橡胶技术网橡胶工艺流程开始1 综述橡胶制品的主要原料就是生胶、各种配合剂、以及作为骨架材料的纤维与金属材料,橡胶制品的基本生产工艺过程包括塑炼、混炼、压延、压出、成型、硫化6个基本工序。
橡胶的加工工艺过程主要就是解决塑性与弹性矛盾的过程,通过各种加工手段,使得弹性的橡胶变成具有塑性的塑炼胶,在加入各种配合剂制成半成品,然后通过硫化就是具有塑性的半成品又变成弹性高、物理机械性能好的橡胶制品。
2 橡胶加工工艺2、1塑炼工艺生胶塑炼就是通过机械应力、热、氧或加入某些化学试剂等方法,使生胶由强韧的弹性状态转变为柔软、便于加工的塑性状态的过程。
生胶塑炼的目的就是降低它的弹性,增加可塑性,并获得适当的流动性,以满足混炼、亚衍、压出、成型、硫化以及胶浆制造、海绵胶制造等各种加工工艺过程的要求。
掌握好适当的塑炼可塑度,对橡胶制品的加工与成品质量就是至关重要的。
在满足加工工艺要求的前提下应尽可能降低可塑度。
随着恒粘度橡胶、低粘度橡胶的出现,有的橡胶已经不需要塑炼而直接进行混炼。
在橡胶工业中,最常用的塑炼方法有机械塑炼法与化学塑炼法。
机械塑炼法所用的主要设备就是开放式炼胶机、密闭式炼胶机与螺杆塑炼机。
化学塑炼法就是在机械塑炼过程中加入化学药品来提高塑炼效果的方法。
开炼机塑炼时温度一般在80℃以下,属于低温机械混炼方法。
密炼机与螺杆混炼机的排胶温度在120℃以上,甚至高达160-180℃,属于高温机械混炼。
生胶在混炼之前需要预先经过烘胶、切胶、选胶与破胶等处理才能塑炼。
几种胶的塑炼特性:天然橡胶用开炼机塑炼时,辊筒温度为30-40℃,时间约为15-20min;采用密炼机塑炼当温度达到120℃以上时,时间约为3-5min。
丁苯橡胶的门尼粘度多在35-60之间,因此,丁苯橡胶也可不用塑炼,但就是经过塑炼后可以提高配合机的分散性顺丁橡胶具有冷流性,缺乏塑炼效果。
顺丁胶的门尼粘度较低,可不用塑炼。
橡胶加工工艺流程

橡胶加工工艺流程
橡胶加工工艺是制造橡胶制品的过程。
本文将简要介绍橡胶加工工艺的基本流程。
1. 橡胶材料准备
首先,需要准备橡胶材料。
橡胶可以是天然橡胶或合成橡胶,具体选择取决于制造的橡胶制品的要求。
橡胶材料通常以原料块或颗粒的形式供应。
2. 橡胶混炼
橡胶混炼是将橡胶与各种添加剂混合的过程。
这些添加剂可以增强橡胶的性能,如硫化剂、促进剂、填料等。
混炼的目的是确保橡胶和添加剂均匀混合,并形成可加工的橡胶混炼胶。
3. 橡胶制品成型
橡胶制品成型是将橡胶混炼胶通过加工方法形成所需的制品形状的过程。
常见的成型方法包括挤出、压延、压缩成型和注射成型等。
在成型过程中,橡胶混炼胶通过加热、压力和模具形成最终的橡胶制品。
4. 后处理
制成橡胶制品后,通常需要进行后处理。
后处理过程可能包括除胶、硫化、修整、包装等环节。
这些步骤有助于提高橡胶制品的性能和质量。
5. 质量控制
橡胶加工工艺流程中的质量控制是非常重要的一环。
通过实施质量控制措施,可以确保橡胶制品的合格率。
常见的质量控制方法包括检验、测试和记录。
以上是橡胶加工工艺的基本流程概述。
具体的操作步骤和细节可能因不同的橡胶制品而有所差异。
在实际操作过程中,应根据具体要求和工艺流程进行调整和优化。
橡胶加工流程(原料-塑炼-混炼-硫化)

橡胶加工流程(原料-塑炼-混炼-硫化)1.基本工艺流程伴随现代工业尤其是化学工业的迅猛发展,橡胶制品种类繁多,但其生产工艺过程,却基本相同。
以一般固体橡胶(生胶)为原料的制品,它的生产工艺过程主要包括:原材料准备→塑炼→混炼→成型→硫化→修整→检验2.原材料准备橡胶制品的主要材料有生胶、配合剂、纤维材料和金属材料。
其中生胶为基本材料;配合剂是为了改善橡胶制品的某些性能而加入的辅助材料;纤维材料(棉、麻、毛及各种人造纤维、合成纤维)和金属材料(钢丝、铜丝)是作为橡胶制品的骨架材料,以增强机械强度、限制制品变型。
在原材料准备过程中,配料必须按照配方称量准确。
为了使生胶和配合剂能相互均匀混合,需要对某些材料进行加工:1.基本工艺流程伴随现代工业尤其是化学工业的迅猛发展,橡胶制品种类繁多,但其生产工艺过程,却基本相同。
以一般固体橡胶(生胶)为原料的制品,它的生产工艺过程主要包括:原材料准备→塑炼→混炼→成型→硫化→休整→检验2.原材料准备橡胶制品的主要材料有生胶、配合剂、纤维材料和金属材料。
其中生胶为基本材料;配合剂是为了改善橡胶制品的某些性能而加入的辅助材料;纤维材料(棉、麻、毛及各种人造纤维、合成纤维)和金属材料(钢丝、铜丝)是作为橡胶制品的骨架材料,以增强机械强度、限制制品变型。
在原材料准备过程中,配料必须按照配方称量准确。
为了使生胶和配合剂能相互均匀混合,需要对某些材料进行加工:生胶要在60--70℃烘房内烘软后,再切胶、破胶成小块;块状配合剂如石蜡、硬脂酸、松香等要粉碎;粉状配合剂若含有机械杂质或粗粒时需要筛选除去;液态配合剂(松焦油、古马隆)需要加热、熔化、蒸发水分、过滤杂质;配合剂要进行干燥,不然容易结块、混炼时旧不能分散均匀,硫化时产生气泡,从而影响产品质量;3.塑炼生胶富有弹性,缺乏加工时的必需性能(可塑性),因此不便于加工。
为了提高其可塑性,所以要对生胶进行塑炼;这样,在混炼时配合剂就容易均匀分散在生胶中;同时,在压延、成型过程中也有助于提高胶料的渗透性(渗入纤维织品内)和成型流动性。
橡胶加工工艺流程

橡胶加工工艺流程橡胶加工是将天然橡胶或合成橡胶进行加工处理,制成各种橡胶制品的过程。
橡胶制品广泛应用于汽车、电子、医疗、建筑等领域,因此橡胶加工工艺的质量和效率对产品质量和生产成本有着重要影响。
下面将介绍橡胶加工的工艺流程。
1. 橡胶混炼。
橡胶混炼是橡胶加工的第一步,其目的是将橡胶与各种添加剂充分混合均匀。
混炼过程中需要将橡胶与填料、增塑剂、硫化剂等添加剂放入橡胶混炼机中,通过机械剪切和翻转,使各种添加剂均匀分散在橡胶中,形成均匀的混炼胶料。
2. 压延。
混炼后的橡胶胶料需要通过压延机进行压延,将其压成一定厚度的橡胶片。
压延机通过辊子的旋转将橡胶胶料不断压延,使其变得更加均匀、平整。
压延后的橡胶片可根据需要进行裁切或进一步加工。
3. 模压。
模压是将橡胶片通过模具加工成各种形状的橡胶制品的过程。
在模压过程中,橡胶片被放入模具中,经过一定的温度和压力作用下,形成所需的产品形状。
模压是橡胶加工中非常重要的一步,决定了最终产品的形状和尺寸精度。
4. 硫化。
硫化是橡胶加工中最关键的一步,通过硫化可以使橡胶获得良好的物理性能。
硫化过程中,橡胶制品放入硫化炉中,加热至一定温度,并在一定时间内进行硫化处理。
硫化可以使橡胶分子链发生交联,增强橡胶的强度、弹性和耐磨性。
5. 表面处理。
部分橡胶制品需要进行表面处理,以提高其外观质量和耐用性。
表面处理可以包括喷涂、印刷、抛光等工艺,使橡胶制品表面光滑、均匀,并且具有一定的装饰效果。
6. 检验与包装。
最后一步是对橡胶制品进行检验和包装。
检验包括外观质量、尺寸精度、物理性能等多个方面的检测,确保产品符合质量标准。
通过包装将橡胶制品进行包装,以便运输和销售。
综上所述,橡胶加工工艺流程包括混炼、压延、模压、硫化、表面处理、检验与包装等多个环节。
每个环节都需要严格控制,以确保最终产品的质量和性能。
随着橡胶工艺技术的不断发展,橡胶制品的品种和质量将会得到进一步提升,满足不同行业的需求。
橡胶加工工艺课件

• 2.合成橡胶的发展历史 • (1)对天然橡胶的剖析和仿制 • 1820年,法拉第明确了橡胶由C和H组成;1860年,威廉
姆斯(Williams)发现橡胶经蒸馏可产生异戊二烯化合 物,并认为它是橡胶的基本化学组成;1875年,鲍查达 (Bouchardat)认为异戊二烯能合成出类似橡胶的物质 ,这是最早的关于人工合成橡胶的报道。
长方式;技术创新、产品创新、效益创新,以节能、 安全、环保新产品替代现有老产品,实现企业效益最 大化;进一步发展大型企业、企业集团和区域集约化 生产,使中国逐步成为橡胶强国。 • 总体目标 • 以8%~10%的年增长速度发展,利税力争同步增 长,主导产品出口占35%左右,节能降耗、资源利用, 要切实实现国家“十一五”发展纲要提出的目标,并 争取有新突破。
• 注:1)橡胶是一种材料,具有特定的使用性能和加工性 能, 属有机高分子材料。 2)橡胶在室温下具有高弹性。 3)橡胶能够被改性是指它能够硫化。 4) 2021/7/17 改性的橡胶即硫化胶不溶解但能溶胀。
ASTM D1566-90
• Material that is capable of recovering from large deformations quickly and forcibly, and can be, or already is, modified to a state in which it is essentially insoluble (but can swell) in solvent, such as benzene, methyl ethyl ketone, and ethanol toluene azeotrope.
2021/7/17
• 轮胎 • 年总产量拟控制在3亿~3.2亿条,子午化率不低于70%
- 1、下载文档前请自行甄别文档内容的完整性,平台不提供额外的编辑、内容补充、找答案等附加服务。
- 2、"仅部分预览"的文档,不可在线预览部分如存在完整性等问题,可反馈申请退款(可完整预览的文档不适用该条件!)。
- 3、如文档侵犯您的权益,请联系客服反馈,我们会尽快为您处理(人工客服工作时间:9:00-18:30)。
第二讲橡胶加工工艺
第一篇橡胶原材料及配方设计
主要了解橡胶制品生产所需天然橡胶、合成橡胶、新形态橡胶和橡胶代用材料,硫化体系、补强填充体系、软化增塑体系、防护体系和其它体系配合剂以及骨架材料的品种、组成、性质性能与作用原理,橡胶(橡塑)并用和配方设计的原理与方法等。
生胶
天然橡胶
合成橡胶
其它弹性体和橡胶代用品
再生胶
粉末橡胶、液体橡胶和热塑性橡胶
橡胶代用品
橡胶的硫化(交联)反应和硫化体系配合剂
橡胶硫化概念和硫化历程
交联结构与硫化胶性能的关系
硫黄硫化体系
非硫硫化体系
橡胶的补强与补强、填充剂
炭黑的分类、命名和制造,炭黑的微观结构和组成
炭黑的基本性质及其对橡胶性能的影响
炭黑对橡胶的补强作用机理
常用炭黑的使用性能及其选择
白炭黑及矿质填料
橡胶的软化(增塑)及软化(增塑)剂
橡胶的软化(增塑)原理
软化(增塑)剂的分类及常用品种的使用性能
软化(增塑)剂的选择
橡胶老化及防老剂
橡胶防老剂
橡胶的氧老化及其防护
橡胶的臭氧老化及其防护
橡胶的疲劳老化及其防护
防老剂的选择
专用配合剂
着色剂
发泡剂
阻燃剂和抗静电剂
纺织材料和金属材料
纺织材料
金属材料
第二篇橡胶制品加工工艺
主要了解橡胶制品加工过程,包括塑炼、混炼、压延、压出、硫化的原理与工艺方法以及常出现的质量问题与改进措施等。
橡胶(橡塑)并用
橡胶(橡塑)并用的目的和方法
橡胶(橡塑)并用原理
橡胶(橡塑)并用体系的加工和应用
配方设计基础知识
配方设计的意义、
要求与方法
配方的表示方法和计算
根据工艺性能和硫化胶物理机械性能设计配方的原理天然橡胶的配方设计
常用合成橡胶的配方设计
橡胶通用加工工艺
塑炼
生胶塑炼的意义和可塑性测试方法
塑炼机理
塑炼工艺方法及影响因素
常用橡胶的塑炼特性
塑炼胶质量问题及改进
混炼
混炼的基本原理
混炼前配合剂的加工和准备
混炼工艺方法
常用橡胶的混炼特性
混炼胶质量及快检方法
压延
压延的基本原理
压延工艺方法及工艺条件常用橡胶的压延特性
压延工艺的质量问题及改进压出
压出的基本原理
口型设计
压出工艺方法及工艺条件常用橡胶的压出特性
压出工艺质量问题及改进硫化
硫化的基本理论
硫化工艺条件
硫化介质和硫化工艺方法硫化工艺的质量问题及改进。