铝合金薄壁异型件
航空零件典型结构加工工艺-薄壁加工
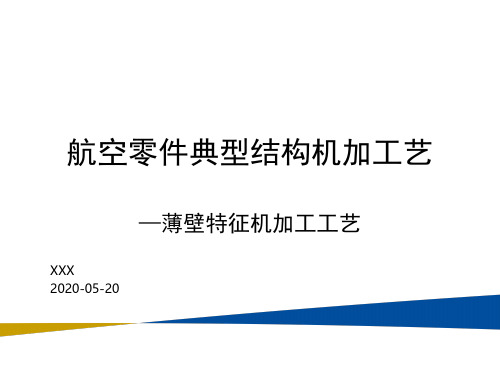
所以钛合金切削要点为低线速度,薄切削层厚度
第25页
3 钛合金薄壁
钛合金薄壁
钛合金薄壁特征加工特点: 1)壁薄腔深(框梁类零件),切屑排除困难,影响冷却润滑效果 2)刚性差,极易产生切削振动,影响加工效率和表面质量 3)切削中让刀严重,影响加工精度,易产生接刀痕 4)易产生加工变形,其毛坯大都为锻造毛坯,加工中随残余应力的
5刃不等齿距: 减震,高进给
加长刃长:一刀切
偏心铲背:增强 刃口强度
加大芯厚:高刚 性不让刀
加大螺旋角:提 高表面粗糙度
第38页
谢 谢!
第39页
释放极易产生加工变形,影响零件精度
钛合金薄壁特征加工要点: a ) 细分工序减小变形,一般为粗→半精→精,甚至可以多次半精,必
要时每个半精后辅以修基准面 b ) 精光一刀消除接痕和让刀
第26页
3 钛合金薄壁
工艺方案
粗加工:粗加工留余量3mm单边
缘条、筋条加工 –框梁类零件
半精加工:如右图分层加工每个框格,给精加 工留余量约0.5~0.2mm;零件变形大时可以多留 余量多次半精,必要时每个半精后辅以修基准面
第5页
1 薄壁特征
例2— 平尾对接肋和缘条: 特点为独立立筋–这类立筋两头不靠,长度长,高度与壁厚比值大,
因此强度更低,极易发生振动和变形
立筋
第6页
1 薄壁特征
例3— 壁板:壁板外表面结构较为简单,一般为少量下陷、槽、孔、 台阶等;壁板内表面较为复杂,通常有槽、斜面、下陷、台阶、结构 孔等结构
3 钛合金薄壁
刀具
方肩铣刀-MEB190系列 用途:半精侧壁、腹板 特点: • 切削力小-大前角大后角,刃口锋利 • 真90°侧壁-曲线刃设计 • R0.4~R3底角-适应各种底角需求
ZL105HB963--2005大型航空铝薄壁筒形零件车削工艺
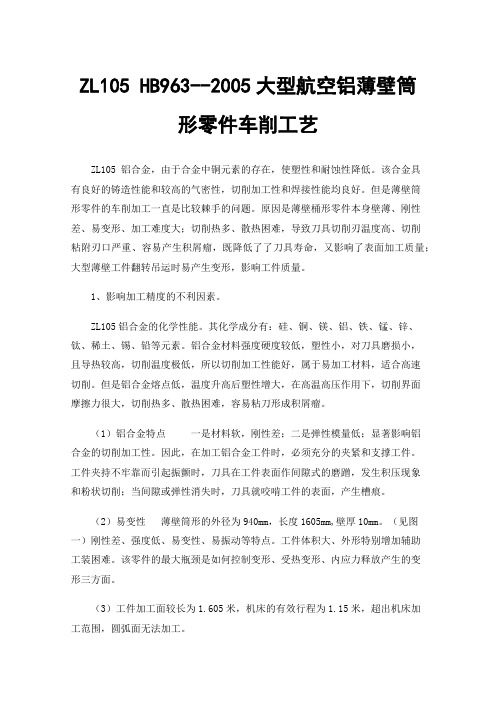
ZL105 HB963--2005大型航空铝薄壁筒形零件车削工艺ZL105 铝合金,由于合金中铜元素的存在,使塑性和耐蚀性降低。
该合金具有良好的铸造性能和较高的气密性,切削加工性和焊接性能均良好。
但是薄壁筒形零件的车削加工一直是比较棘手的问题。
原因是薄壁桶形零件本身壁薄、刚性差、易变形、加工难度大;切削热多、散热困难,导致刀具切削刃温度高、切削粘附刃口严重、容易产生积屑瘤,既降低了了刀具寿命,又影响了表面加工质量;大型薄壁工件翻转吊运时易产生变形,影响工件质量。
1、影响加工精度的不利因素。
ZL105铝合金的化学性能。
其化学成分有:硅、铜、镁、铝、铁、锰、锌、钛、稀土、锡、铅等元素。
铝合金材料强度硬度较低,塑性小,对刀具磨损小,且导热较高,切削温度极低,所以切削加工性能好,属于易加工材料,适合高速切削。
但是铝合金熔点低,温度升高后塑性增大,在高温高压作用下,切削界面摩擦力很大,切削热多、散热困难,容易粘刀形成积屑瘤。
(1)铝合金特点一是材料软,刚性差;二是弹性模量低;显著影响铝合金的切削加工性。
因此,在加工铝合金工件时,必须充分的夹紧和支撑工件。
工件夹持不牢靠而引起振颤时,刀具在工件表面作间隙式的磨蹭,发生积压现象和粉状切削;当间隙或弹性消失时,刀具就咬啃工件的表面,产生槽痕。
(2)易变性薄壁筒形的外径为940mm,长度1605mm,壁厚10mm。
(见图一)刚性差、强度低、易变性、易振动等特点。
工件体积大、外形特别增加辅助工装困难。
该零件的最大瓶颈是如何控制变形、受热变形、内应力释放产生的变形三方面。
(3)工件加工面较长为1.605米,机床的有效行程为1.15米,超出机床加工范围,圆弧面无法加工。
通过对零件结构及材料特性的分析,得知内外圆的精加工以及圆弧面加工是该零件的加工难点,如何有效控制加工变形是解决加工问题的重要措施。
为提高加工效率、保证加工质量,从工艺总体方案,工艺系统刚度、装夹方法、刀具材料及参数、切削参数及冷却方法等方面。
2524铝合金薄板平面各向异性研究

第29卷 第1期2009年2月航 空 材 料 学 报J OURNAL OF A ERONAUT ICAL MAT ER I A LSV o l 129,N o 11 February 20092524铝合金薄板平面各向异性研究郭加林1, 尹志民1, 商宝川1, 聂 波2, 何振波1,2(1.中南大学材料科学与工程学院,长沙410083;2.东北轻合金有限责任公司,哈尔滨150060)摘要:采用室温拉伸性能测试、金相组织观察、XRD 反极图测定和透射电子显微分析等方法研究了冷轧态和T3态2mm 厚2524铝合金薄板不同取向条件下的显微组织和拉伸力学性能。
以{110}<112>单组分织构模型为基础,研究了织构与平面各向异性的关系。
结果表明,2524冷轧态和T 3态铝合金薄板在与轧制方向成45b 和60b 方向上的强度较0b 、30b 和90b 方向上的强度低,延伸率则是45b 方向上最高;轧向力学性能优于横向力学性能;冷轧态合金薄板的平面各向异性高于T3态合金板材;2524冷轧态合金薄板的主要织构为{110}<112>,次要织构为{311}<112>;2524-T 3态铝合金成品薄板的主要织构为{110}<001>;2524铝合金薄板的平面各向异性与合金的晶粒结构以及晶体学织构密切有关,其中晶体学织构是造成合金板材平面各向异性的主要原因。
关键词:2524铝合金;力学性能;平面各向异性;反极图;晶体织构中图分类号:TG14612 文献标识码:A 文章编号:1005-5053(2009)01-0001-06收稿日期:2008-07-26;修订日期:2008-10-23基金项目:国家/9730重点基础研究项目(G 2005CB623705)作者简介:郭加林(1982)),男,硕士研究生,从事高性能铝合金的研究,(E -m a il)g jlz ndx @1631co m通讯作者:尹志民,教授,(E -m a il)y in -g rp @csu 1edu 1cn 。
铝合金型材加工技术
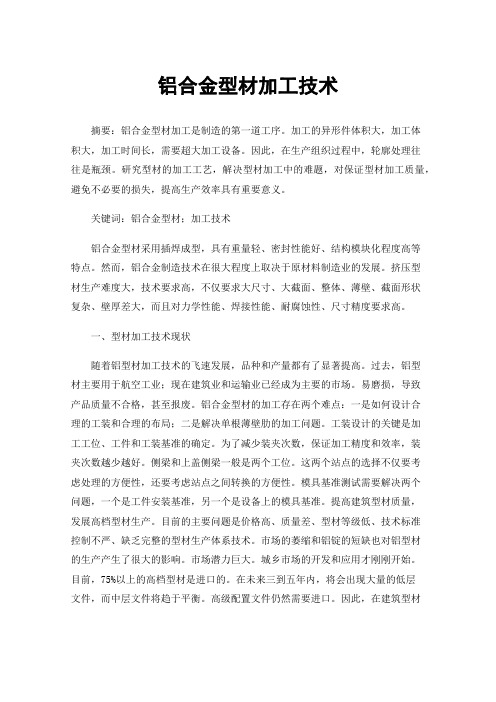
铝合金型材加工技术摘要:铝合金型材加工是制造的第一道工序。
加工的异形件体积大,加工体积大,加工时间长,需要超大加工设备。
因此,在生产组织过程中,轮廓处理往往是瓶颈。
研究型材的加工工艺,解决型材加工中的难题,对保证型材加工质量,避免不必要的损失,提高生产效率具有重要意义。
关键词:铝合金型材;加工技术铝合金型材采用插焊成型,具有重量轻、密封性能好、结构模块化程度高等特点。
然而,铝合金制造技术在很大程度上取决于原材料制造业的发展。
挤压型材生产难度大,技术要求高,不仅要求大尺寸、大截面、整体、薄壁、截面形状复杂、壁厚差大,而且对力学性能、焊接性能、耐腐蚀性、尺寸精度要求高。
一、型材加工技术现状随着铝型材加工技术的飞速发展,品种和产量都有了显著提高。
过去,铝型材主要用于航空工业;现在建筑业和运输业已经成为主要的市场。
易磨损,导致产品质量不合格,甚至报废。
铝合金型材的加工存在两个难点:一是如何设计合理的工装和合理的布局;二是解决单根薄壁肋的加工问题。
工装设计的关键是加工工位、工件和工装基准的确定。
为了减少装夹次数,保证加工精度和效率,装夹次数越少越好。
侧梁和上盖侧梁一般是两个工位。
这两个站点的选择不仅要考虑处理的方便性,还要考虑站点之间转换的方便性。
模具基准测试需要解决两个问题,一个是工件安装基准,另一个是设备上的模具基准。
提高建筑型材质量,发展高档型材生产。
目前的主要问题是价格高、质量差、型材等级低、技术标准控制不严、缺乏完整的型材生产体系技术。
市场的萎缩和铝锭的短缺也对铝型材的生产产生了很大的影响。
市场潜力巨大。
城乡市场的开发和应用才刚刚开始。
目前,75%以上的高档型材是进口的。
在未来三到五年内,将会出现大量的低层文件,而中层文件将趋于平衡。
高级配置文件仍然需要进口。
因此,在建筑型材的生产中应提倡竞争。
在竞争中,要提高质量,提高管理水平,降低成本和价格,重点生产高档型材,逐步扭转对进口的依赖。
二、铝合金型材加工技术1.薄壁筋板的加工。
铸造铝合金热处理质量缺陷及其消除与预防
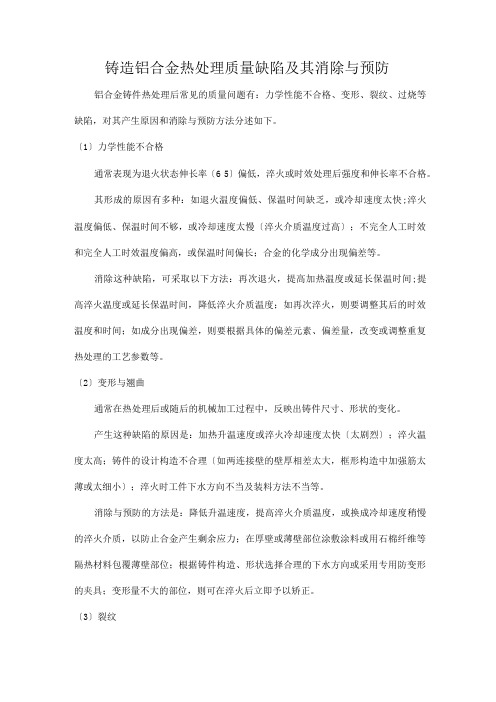
铸造铝合金热处理质量缺陷及其消除与预防铝合金铸件热处理后常见的质量问题有:力学性能不合格、变形、裂纹、过烧等缺陷,对其产生原因和消除与预防方法分述如下。
〔1〕力学性能不合格通常表现为退火状态伸长率〔6 5〕偏低,淬火或时效处理后强度和伸长率不合格。
其形成的原因有多种:如退火温度偏低、保温时间缺乏,或冷却速度太快;淬火温度偏低、保温时间不够,或冷却速度太慢〔淬火介质温度过高〕;不完全人工时效和完全人工时效温度偏高,或保温时间偏长;合金的化学成分出现偏差等。
消除这种缺陷,可采取以下方法:再次退火,提高加热温度或延长保温时间;提高淬火温度或延长保温时间,降低淬火介质温度;如再次淬火,则要调整其后的时效温度和时间;如成分出现偏差,则要根据具体的偏差元素、偏差量,改变或调整重复热处理的工艺参数等。
〔2〕变形与翘曲通常在热处理后或随后的机械加工过程中,反映出铸件尺寸、形状的变化。
产生这种缺陷的原因是:加热升温速度或淬火冷却速度太快〔太剧烈〕;淬火温度太高;铸件的设计构造不合理〔如两连接壁的壁厚相差太大,框形构造中加强筋太薄或太细小〕;淬火时工件下水方向不当及装料方法不当等。
消除与预防的方法是:降低升温速度,提高淬火介质温度,或换成冷却速度稍慢的淬火介质,以防止合金产生剩余应力;在厚壁或薄壁部位涂敷涂料或用石棉纤维等隔热材料包覆薄壁部位;根据铸件构造、形状选择合理的下水方向或采用专用防变形的夹具;变形量不大的部位,则可在淬火后立即予以矫正。
〔3〕裂纹表现为淬火后的铸件外表用肉眼可以看到明显的裂纹,或通过荧光检查肉眼看不见的微细裂纹。
裂纹多曲折不直并呈暗灰色。
产生裂纹的原因是:加热速度太快,淬火时冷却太快〔淬火温度过高或淬火介质温度过低,或淬火介质冷却速度太快〕;铸件构造设计不合理〔两连接壁壁厚差太大,框形件中间的加强筋太薄或太细小〕;装炉方法不当或下水方向不对;炉温不均匀,使铸件温度不均匀等。
消除与预防的方法是:减慢升温速度或采取等温淬火工艺;提高淬火介质温度或换成冷却速度慢的淬火介质;在壁厚或薄壁部位涂敷涂料或在薄壁部位包覆石棉等隔热材料;采用专用防开裂的淬火夹具,并选择正确的下水方向。
铝合金薄壁零件的加工工艺及变形控制探讨
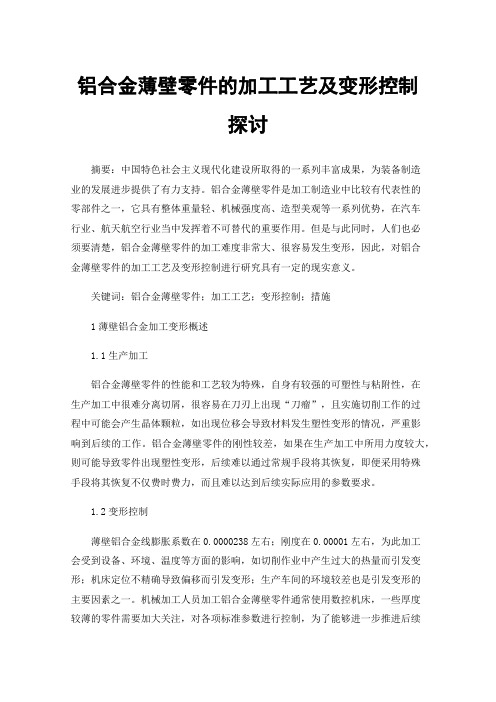
铝合金薄壁零件的加工工艺及变形控制探讨摘要:中国特色社会主义现代化建设所取得的一系列丰富成果,为装备制造业的发展进步提供了有力支持。
铝合金薄壁零件是加工制造业中比较有代表性的零部件之一,它具有整体重量轻、机械强度高、造型美观等一系列优势,在汽车行业、航天航空行业当中发挥着不可替代的重要作用。
但是与此同时,人们也必须要清楚,铝合金薄壁零件的加工难度非常大、很容易发生变形,因此,对铝合金薄壁零件的加工工艺及变形控制进行研究具有一定的现实意义。
关键词:铝合金薄壁零件;加工工艺;变形控制;措施1薄壁铝合金加工变形概述1.1生产加工铝合金薄壁零件的性能和工艺较为特殊,自身有较强的可塑性与粘附性,在生产加工中很难分离切屑,很容易在刀刃上出现“刀瘤”,且实施切削工作的过程中可能会产生晶体颗粒,如出现位移会导致材料发生塑性变形的情况,严重影响到后续的工作。
铝合金薄壁零件的刚性较差,如果在生产加工中所用力度较大,则可能导致零件出现塑性变形,后续难以通过常规手段将其恢复,即便采用特殊手段将其恢复不仅费时费力,而且难以达到后续实际应用的参数要求。
1.2变形控制薄壁铝合金线膨胀系数在0.0000238左右;刚度在0.00001左右,为此加工会受到设备、环境、温度等方面的影响,如切削作业中产生过大的热量而引发变形;机床定位不精确导致偏移而引发变形;生产车间的环境较差也是引发变形的主要因素之一。
机械加工人员加工铝合金薄壁零件通常使用数控机床,一些厚度较薄的零件需要加大关注,对各项标准参数进行控制,为了能够进一步推进后续行业的持续健康发展,需要着重考虑到设备、环境、温度等与金属材料的差异化特点,保证参数精确度符合预期的生产要求,从而有效解决加工伴有的质量问题。
2铝合金薄壁零件的加工工艺随着科技发展,中国的零部件加工技术越来越成熟,对于薄壁零部件的加工能力也在不断提升,铝合金薄壁零件是其中比较有代表性的零部件之一。
铝合金材质决定了该零部件具有比重指数小、比强度指数大的特点,而薄壁结构则导致该零部件的刚性不佳、容易变形,这给铝合金薄壁零件加工带来了一定挑战。
大型薄壁高强度铝合金异型舱壳精密砂型铸造成型关键技术应用研究

大型薄壁高强度铝合金异型舱壳精密砂型铸造成型关键技术应用研究**本文由“高档数控机床与基础制造装备”国家科技 重大专项(课题编号:2017ZX04009001)支持。
王华侨',王永凤「,郭玉',张权',付忠奎,,冯四伟I,罗海涛',赵华萍 ',李玉胜2,翟虎2,赵连君2,赵偲宇'1.湖北三江航天红阳机电有限公司(湖北孝感432000)2.沈阳明腾科技有限公司(辽宁沈阳110101)3.湖北大学知行学院(湖北武汉430011)【摘要】对某大型薄壁高强度铝合金网格筋异形舱壳整体精密铸造成型的关键技术进行了系统介绍,从铸件的结构特点、工艺方案选型、铸造模拟仿真、铸件加工质量等进行了深入 的分析和优化。
该大型薄壁网格筋异形舱壳整体精密铸造成型所采用的系列工艺及设计 技术,克服了传统制造方案无法实现或实现起来成本高、周期长、管理难等缺点,对于同类结构铸件的整体精密铸造成型成功实现具有重要的技术创新意义,同时对于提升国内大 型高强度铝合金复杂构件的精密铸造成型具有重要的指导和借鉴价值。
关键词:高强度铝合金;薄壁网格筋;异形舱壳;精密铸造;模拟仿真中图分类号:TG249 文献标识码:BDOklO.l 2147/ki. 1671-3508.2019.03.017Research on Critical Technology of Precision Casting for Large ThinWall High-Strength Aluminum Alloy Special-Shaped Cabin Shell[Abstract] In this paper, the key technology of a large thin wall high strength aluminum alloymesh bar for the whole precision casting is introduced, and the structure features, the selection ofthe process scheme, the simulation of the casting, the quality of the product and so on are deeplyanalyzed and optimized. The series of process and design techniques used in the whole precisioncasting of the large thin wall mesh reinforcement can overcome the shortcomings of thetraditional manufacturing scheme which can not be realized or realized, such as high cost, longperiod and difficult management. It has important technical innovation significance for the complete precision casting of similar structure products. At the same time, it has important guiding and reference value for improving the precision casting forming of large domestichigh-strength aluminum alloy components.Key words : high strength aluminum alloy ; thin-walled grid bar; special-shaped cabin shell ;precision casting; simulation1铸件结构特点1.1铸件结构特点某异形舱壳总体结构设计采用网格筋骨架+蒙皮整体铸造结构,如图1所示。
大直径薄壁铝合金零件的加工研究
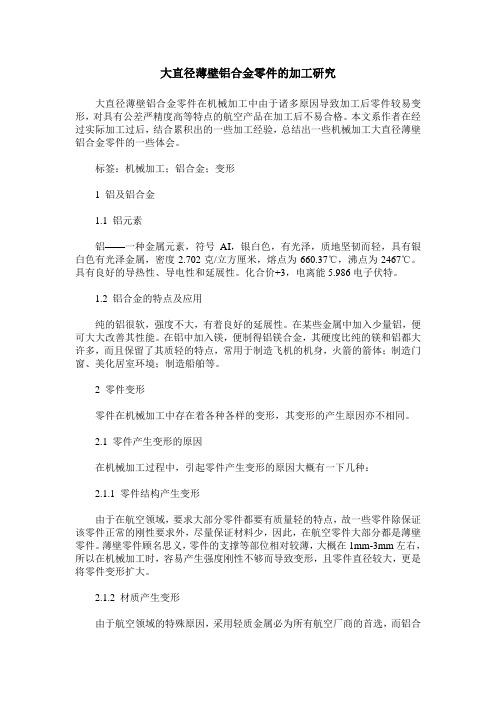
大直径薄壁铝合金零件的加工研究大直径薄壁铝合金零件在机械加工中由于诸多原因导致加工后零件较易变形,对具有公差严精度高等特点的航空产品在加工后不易合格。
本文系作者在经过实际加工过后,结合累积出的一些加工经验,总结出一些机械加工大直径薄壁铝合金零件的一些体会。
标签:机械加工;铝合金;变形1 铝及铝合金1.1 铝元素铝——一种金属元素,符号AI,银白色,有光泽,质地坚韧而轻,具有银白色有光泽金属,密度2.702克/立方厘米,熔点为660.37℃,沸点为2467℃。
具有良好的导热性、导电性和延展性。
化合价+3,电离能5.986电子伏特。
1.2 铝合金的特点及应用纯的铝很软,强度不大,有着良好的延展性。
在某些金属中加入少量铝,便可大大改善其性能。
在铝中加入镁,便制得铝镁合金,其硬度比纯的镁和铝都大许多,而且保留了其质轻的特点,常用于制造飞机的机身,火箭的箭体;制造门窗、美化居室环境;制造船舶等。
2 零件变形零件在机械加工中存在着各种各样的变形,其变形的产生原因亦不相同。
2.1 零件产生变形的原因在机械加工过程中,引起零件产生变形的原因大概有一下几种:2.1.1 零件结构产生变形由于在航空领域,要求大部分零件都要有质量轻的特点,故一些零件除保证该零件正常的刚性要求外,尽量保证材料少,因此,在航空零件大部分都是薄壁零件。
薄壁零件顾名思义,零件的支撑等部位相对较薄,大概在1mm-3mm左右,所以在机械加工时,容易产生强度刚性不够而导致变形,且零件直径较大,更是将零件变形扩大。
2.1.2 材质产生变形由于航空领域的特殊原因,采用轻质金属必为所有航空厂商的首选,而铝合金以其质地轻,且经过表面氧化后,化学性质温度等特点,成为航空产品材料选择的首选。
然而,铝合金大都分具有良好的延展性,故铝合金的变形在所难免。
2.1.3 切削力过大引起变形在机械加工过程中(除特种工艺外),采用刀具与零件接触,通过刀具选用较硬的材质,且较为锋利,对零件进行切削。
薄壁类壳体变形研究及应用
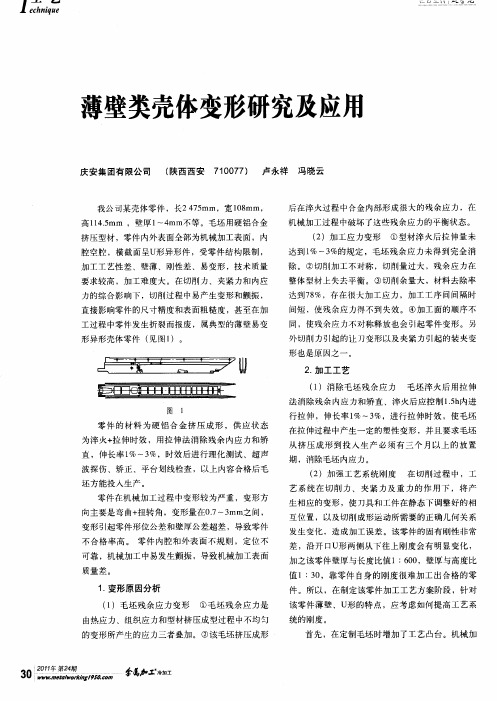
( )加强工艺系统刚度 在切削过程中 ,工 2 艺系统在 切削力 、夹紧力及 重力的 作用下 ,将产 生相应的变形 ,使刀具和工件在静态下调整好的相
互 位 置 ,以及 切 削 成形 运 动 所需 要 的 正 确几 何 关 系 发生 变 化 ,造 成 加 工误 差 。该零 件 的 固有 刚性 非 常 差 ,沿 开 口U 两 侧 从 下 往 上 刚 度会 有 明显 变 化 , 形
上em叼 一 , c .e l ‘ u
薄壁类壳体变形研究及应用
庆安集 团有 限公司 ( 陕西西安 7 0 7 ) 卢永祥 1 0 7 冯晓云
我公司某壳体零件,长24 5 7 mm,宽18 0 mm, 高145 1. mm ,壁厚1 mm不等。毛坯用硬铝 合金 ~4
后在淬火过程中合金内部形成很大的残余应 力 ,在 机械加工过程 中破坏了这些残余应力的平衡状态。 ( )加工应力变形 ①型材淬火后拉 伸量未 2 达到l %~3 %的规定 ,毛坯残余应力未得到完全消 除。②切削加 工不对称 ,切削量过大 ,残余应力在
力的综合影响下 ,切削过程中易产生变形和颤振 , 直接影响零件的尺寸精度和表面粗糙度,甚至在加 工过程 中零件发生折裂而报废 ,属典型的薄壁易变 形异形壳体零件 ( 见图1 )。
达: 7 %,存在很大加工应力 ,加工工序间间隔时  ̄ 8 J 1 间短 ,使残余应力得不到失效 。④加工面的顺序不
同 ,使 残 余应 力 不对 称 释 放也 会 引起零 件 变 形 。 另 外切 削 力 引起 的 让 刀变 形 以 及夹 紧力 引起 的 装 夹 变 形 也 是原 因之 一 。
2 加工工 艺 .
( )消除毛坯 残余应 力 毛坯 淬火后 用拉 伸 1
各种牌号铸造铝合金的主要特点及用途

各种牌号铸造铝合金的主要特点及用途2009-12-25 13:33:39| 分类:金属材料| 标签:|字号大中小订阅【ZL101】ZL101的特点是成分简单,容易熔炼和铸造,铸造性能好,气密性好、焊接和切削加工性能也比较好,但力学性能不高。
适合铸造薄壁、大面积和形状复杂的、强度要求不高的各种零件,如泵的壳体、齿轮箱、仪表壳(框架)及家电产品上的零件等。
主要采用砂型铸造和金属型铸造。
【Zl101A】由于是在ZL101的基础上加了微量Ti,细化了晶粒,强化了合金的组织,其综合性能高于Zl101、ZL102,并有较好的抗蚀性能,可用作一般载荷的工程结构件和摩托车、汽车及家电、仪表产品上的各种结构件的优质铸件。
其使用量目前仅次于ZL102。
多采用砂型和金属型铸造。
【Zl102】这种合金的最大特点是流动性好,其它性能与ZL101差不多,但气密性比ZL101要好,可用来铸造各种形状复杂、薄壁的压铸件和强度要求不高的薄壁、大面积、形状复杂的金属或砂型铸件。
不论是压铸件还是金属型、砂型铸件,都是民用产品上用得最多的一个铸造铝合金品种。
【Zl104】因其工晶体量多,又加入了Mn,抵消了材料中混入的Fe有害作用,有较好的铸造性能和优良的气密性、耐蚀性,焊接和切削加工性能也比较好,但耐热性能较差,适合制作形状复杂、尺寸较大的有较大负荷的动力结构件,如增压器壳体、气缸盖,气缸套等零件,主要用压铸,也多采用砂型和金属型铸造。
【Zl105、ZL105A】由于加入了Cu,降低了Si的含量,其铸造性能和焊接性能都比ZL104差,但室温和高温强度、切削加工性能都比ZL104要好,塑性稍低,抗蚀性能较差。
适合用作形状复杂、尺寸较大、有重大负荷的动力结构件。
如增压器壳体、气缸盖、气缸套等零件。
Zl105A是降低了ZL105的杂质元素Fe的含量,提高了合金的强度,具有比ZL105更好的力学性能,多采用铸造优质铸件。
【ZL106】由于提高了Si的含量,又加入了微量的Ti、Mn,使合金的铸造性能和高温性能优于ZL105气密性、耐蚀性也较好,可用作一般负荷的结构件及要求气密性较好和在较高温度下工作的零件,主要采用砂型和金属型铸造。
铝合金的热处理工艺
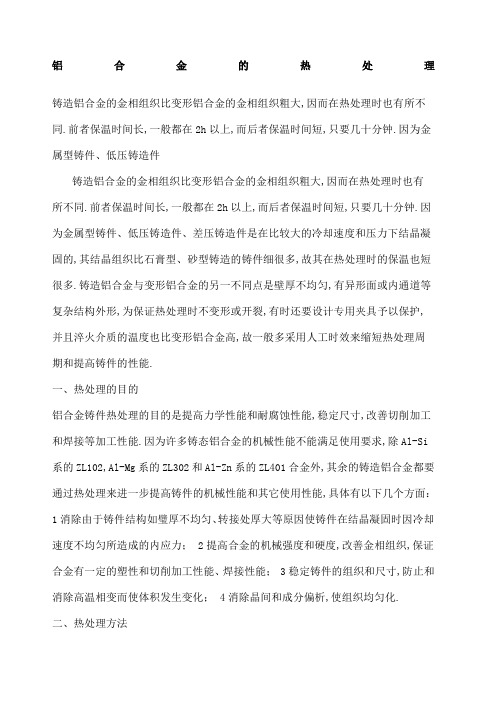
铝合金的热处理铸造铝合金的金相组织比变形铝合金的金相组织粗大,因而在热处理时也有所不同.前者保温时间长,一般都在2h以上,而后者保温时间短,只要几十分钟.因为金属型铸件、低压铸造件铸造铝合金的金相组织比变形铝合金的金相组织粗大,因而在热处理时也有所不同.前者保温时间长,一般都在2h以上,而后者保温时间短,只要几十分钟.因为金属型铸件、低压铸造件、差压铸造件是在比较大的冷却速度和压力下结晶凝固的,其结晶组织比石膏型、砂型铸造的铸件细很多,故其在热处理时的保温也短很多.铸造铝合金与变形铝合金的另一不同点是壁厚不均匀,有异形面或内通道等复杂结构外形,为保证热处理时不变形或开裂,有时还要设计专用夹具予以保护,并且淬火介质的温度也比变形铝合金高,故一般多采用人工时效来缩短热处理周期和提高铸件的性能.一、热处理的目的铝合金铸件热处理的目的是提高力学性能和耐腐蚀性能,稳定尺寸,改善切削加工和焊接等加工性能.因为许多铸态铝合金的机械性能不能满足使用要求,除Al-Si 系的ZL102,Al-Mg系的ZL302和Al-Zn系的ZL401合金外,其余的铸造铝合金都要通过热处理来进一步提高铸件的机械性能和其它使用性能,具体有以下几个方面:1消除由于铸件结构如璧厚不均匀、转接处厚大等原因使铸件在结晶凝固时因冷却速度不均匀所造成的内应力; 2提高合金的机械强度和硬度,改善金相组织,保证合金有一定的塑性和切削加工性能、焊接性能; 3稳定铸件的组织和尺寸,防止和消除高温相变而使体积发生变化; 4消除晶间和成分偏析,使组织均匀化.二、热处理方法1、退火处理退火处理的作用是消除铸件的铸造应力和机械加工引起的内应力,稳定加工件的外形和尺寸,并使Al-Si系合金的部分Si结晶球状化,改善合金的塑性.其工艺是:将铝合金铸件加热到280-300℃,保温2-3h,随炉冷却到室温,使固溶体慢慢发生分解,析出的第二质点聚集,从而消除铸件的内应力,达到稳定尺寸、提高塑性、减少变形、翘曲的目的.2、淬火淬火是把铝合金铸件加热到较高的温度一般在接近于共晶体的熔点,多在500℃以上,保温2h以上,使合金内的可溶相充分溶解.然后,急速淬入60-100℃的水中,使铸件急冷,使强化组元在合金中得到最大限度的溶解并固定保存到室温.这种过程叫做淬火,也叫固溶处理或冷处理.3、时效处理时效处理,又称低温回火,是把经过淬火的铝合金铸件加热到某个温度,保温一定时间出炉空冷直至室温,使过饱和的固溶体分解,让合金基体组织稳定的工艺过程.合金在时效处理过程中,随温度的上升和时间的延长,约经过过饱和固溶体点阵内原子的重新组合,生成溶质原子富集区称为G-PⅠ区和G-PⅠ区消失,第二相原子按一定规律偏聚并生成G-PⅡ区,之后生成亚稳定的第二相过渡相,大量的G-PⅡ区和少量的亚稳定相结合以及亚稳定相转变为稳定相、第二相质点聚集几个阶段.时效处理又分为自然时效和人工时效两大类.自然时效是指时效强化在室温下进行的时效.人工时效又分为不完全人工时效、完全人工时效、过时效3种.1不完全人工时效:把铸件加热到150-170℃,保温3-5h,以获得较好抗拉强度、良好的塑性和韧性,但抗蚀性较低的热处理工艺; 2完全人工时效:把铸件加热到175-185℃,保温5-24h,以获得足够的抗拉强度即最高的硬度但延伸率较低的热处理工艺; 3过时效:把铸件加热到190-230℃,保温4-9h,使强度有所下降,塑性有所提高,以获得较好的抗应力、抗腐蚀能力的工艺,也称稳定化回火.4、循环处理把铝合金铸件冷却到零下某个温度如-50℃、-70℃、-195℃并保温一定时间,再把铸件加热到350℃以下,使合金中度固溶体点阵反复收缩和膨胀,并使各相的晶粒发生少量位移,以使这些固溶体结晶点阵内的原子偏聚区和金属间化合物的质点处于更加稳定的状态,达到提高产品零件尺寸、体积更稳定的目的.这种反复加热冷却的热处理工艺叫循环处理.这种处理适合使用中要求很精密、尺寸很稳定的零件如检测仪器上的一些零件.一般铸件均不作这种处理.5、铸造铝合金热处理状态代号及含义代号合金状态热处理的作用或目的说明T1 人工时效在金属型或湿砂型铸造的合金,因冷却速度较快,已得到一定程度的过饱和固溶体,即有部分淬火效果.再作人工时效,脱溶强化,则可提高硬度和机械强度,改善切削加工性. 对提高Zl104、ZL105等合金的强度有效.T2 退火主要作用在于消除铸件的内应力铸造应力和机加工引起的应力,稳定铸件尺寸,并使Al-Si系合金的Si晶体球状化,提高其塑性. 对Al-Si系合金效果比较明显,退火温度280-300℃,保温时间为2-4h.T4 固溶处理淬火加自然时效通过加热保温,使可溶相溶解,然后急冷,使大量强化相固溶在α固溶体内,获得过饱和固溶体,以提高合金的硬度、强度及抗蚀性. 对Al-Mg系合金为最终热处理,对需人工时效的其它合金则是预备热处理.T5 固溶处理淬火加不完全人工时效用来得到较高的强度和塑性,但抗蚀性会有所下降,非凡是晶间腐蚀会有所增加. 时效温度低,保温时间短,时效温度约150-170℃,保温时间为3-5h.T6 固溶处理淬火加完全人工时效用来获得最高的强度,但塑性和抗蚀性有所降低. 在较高温度和较长时间内进行.适用于要求高负荷的零件,时效温度约175-185℃,保温时间5h以上.T7 固溶处理淬火加稳定化回火用来稳定铸件尺寸和组织,提高抗腐蚀非凡是抗应力腐蚀能力,并保持较高的力学性能. 多在接近零件的工作温度下进行.适合300℃以下高温工作的零件,回火温度为190-230℃,保温时间4-9h.T8 固溶处理淬火加软化回火使固溶体充分分解,析出的强化相聚集并球状化,以稳定铸件尺寸,提高合金的塑性,但抗拉强度下降. 适合要求高塑性的铸件,回火温度约230-330℃,保温时间3-6h.T9 循环处理用来进一步稳定铸件的尺寸外形.其反复加热和冷却的温度及循环次数要根据零件的工作条件和合金的性质来决定. 适合要求尺寸、外形很精密稳定的零件.三、热处理工艺1、铸造铝合金热处理工艺参数合金牌号合金代号热处理固溶处理时效处理保温后空冷加热温度℃ 保温时间h 淬火温度℃ 加热温度℃ 保温时间hZAlSi7Mg ZL101 T2 - - - 300±10 2-4T4 535±5 2-6 20-100 - -T5 535±5 2-6 20-100 150±5 2-4T6 535±5 2-6 20-100 200±5 2-5T7 535±5 2-6 80-100 225±5 3-5T5 二阶段535±5 2-6 20-100 190±10150±5 2ZAlSi7MgA ZL101A T1 - - - 190±5 3-4T2 - - - 300±10 2-4T4 535±5 10-16 20-100 - -T5 535±5 10-16 20-100 175±5 6ZAlSi12 ZL102 T2 - - - 300±10 2-4ZAlSi9Mg ZL104 T1 - - - 175±5 5-17T6 535±5 2-6 20-100 175±5 10-15ZAlSi5Cu1Mg ZL105 T1 - - - 180±5 5-10T5 525±5 3-5 20-100 175±5 5-10T6 525±5 3-5 20-100 200±5 3-5T7 525±5 3-5 20-100 230±10 3-5ZAlSi5Cu1MgA ZL105A T1 - - - 180±5 5-10 T5 525±5 3-5 20-100 175±5 5-10T6 525±5 3-5 20-100 200±5 3-5T7 525±5 3-5 20-100 230±10 3-5T8 525±5 3-5 20-100 250±10 3-5ZAlSi8Cu1Mg ZL106 T1 - - - 200±10 5-8T2 - - - 280±10 5-8T5 515±5 4-8 20-100 170±5 8-16T7 515±5 4-8 20-100 230±5 3-5ZAlSi7Cu4 ZL107 T6 515±5 5-7 20-100 170±10 5-7ZAlSi12Cu2Mg1 ZL108 T1 - - - 190±5 8-12T6 515±5 6-8 20-70 175±5 14-18T7 515±5 3-8 20-70 240±10 6-10ZAlSi12Cu1Mg1Ni1 ZL109 T1 - - - 205±5 8-12T6 515±5 6-8 20-70 180±5 14-18ZA lSi9Cu2Mg ZL111 T6 520±5 4-6 20-70 180±5 6-8ZAlSi7Mg1A ZL114A T5 535±5 2-7 20-100 150±5 1-3T6 540±5 8-12 65-100 160±5 3-5ZALSi5Zn1Mg ZL115 T4 550±5 16 65-100 - -T5 550±5 16 65-100 160±5 4ZAlSi8MgBe ZL116 T1 - - - 190±5 3-4T2 - - - 300±10 2-4T4 535±5 10-16 20-100 - -T5 535±5 10-16 20-100 175±5 6T6 535±5 10-16 20-100 160±5 3-8ZAlCu5Mn ZAlCu5MnA ZL201 ZL201A T4 545±5 10-12 20-100 - - T5 545±5 5-9 20-100 175±5 3-6T7 545±5 5-9 20-100 250±10 3-10ZAlCu10 ZL202 T2 - - - 290±5 3ZAlCu4 ZL203 T4 515±5 10-15 20-100 - -T5 515±5 10-15 20-100 150±5 2-4ZAlCu5MnCdA ZL204A T6 535±5 7-9 40-100 175±5 3-5T7 535±5 7-9 40-100 190±5 3-5ZAlCu5MnCdVA ZL205A T5 535±5 10-15 20-60 155±5 8-10T6 535±5 10-15 20-60 175±5 3-5T7 535±5 10-15 20-60 195±5 3-5ZAlRE5Cu3Si2 ZL207 T1 - - - 200±5 5-10ZAlMg10 ZL301 T4 430±10 20 100或油 - -ZAlMg8Zn1 ZL305 T4 455±5 6-8 80-100 - -ZAlZn11Si7 Zl401 T1 - - - 200±10 5-10T2 - - - 300±10 2-4ZAlZn6Mg ZL402 T1 - - - 175±5 6-8T5 - - - 室温 20天T5 - - - 175±5 6-82、热处理操作技术要点1热处理前应检查热处理设备、辅助设备、仪表等是否合格和正常,炉膛各处的温度差是否在规定的范围之内±5℃;2装炉前应吹砂或冲洗,应无油污、脏物、泥土,合金牌号不应相混;3形性状易产生翘曲的铸件应放在专用的底盘或支架上,不答应有悬空的悬臂部分;4检查铸件性能的单铸或附铸试棒应随零件一起同炉处理,以真实反映铸件的性能;5在保温期间应随时检查、校正炉膛各处温度,防止局部高温或烧化;6在断电后短时间不能恢复时,应将在保温中的铸件迅速出炉淬火,等恢复正常后,再装炉、保暖和进行热处理;7在硝盐槽中淬过火的铸件,应在淬火后立即用热水冲洗,消除残盐,防止腐蚀;8发现淬火后铸件变形,应立即予以校正;9要时效处理的零件,应在淬火后内进行时效处理;10如在热处理后发现性能不合格,可重复进行热处理,但次数不得超过2次;11应根据铸件结构外形、尺寸、合金特性等制定的热处理工艺进行热处理.3、热处理缺陷的产生原因和消除与预防办法缺陷名称缺陷表现产生原因消除与预防办法力学性能不合格退火状态δ5偏低,淬火或时效处理后强度和延伸率不合格. 退火温度偏低或保温时间不足,或冷却太快;淬火温度偏低或保温时间不够,或冷却速度太慢淬火介质温度过高;不完全人工时效和完全人工时效温度偏高,或保温时间偏长,合金的化学成分出现偏差. 再次退火,提高温度或延长保温时间;提高淬火温度或延长保温时间,降低淬火介质温度;如再次淬火,则要调整其后的时效温度和时间;如成分出现偏差,则要根据具体的偏差元素、偏差量、改变或调整重复热处理参数.变形、翘曲热处理后,或之后的机械加工中反映出来的铸件的尺寸、外形变化. 加热速度或淬火冷却速度太快太激烈;淬火温度太高;铸件的设计结构不合理如两连接壁的壁厚相差太大,框形结构中加强筋太薄或太细小;淬火时工件下水方向不当及装料方法不当. 降低升温速度,提高淬火介质温度,或换成冷却速度稍慢的淬火介质以防止合金内产生残余应力;在厚壁或薄壁部位涂敷涂料或用石棉纤维等隔热材料包覆薄壁部位;根据铸件结构、外形选择合理的下水方向或采用专用防变形的夹具;变形量不大的部位,则可在淬火后立即予以矫正.裂纹淬火后的铸件表面用肉眼可以看到的明显的裂纹或通过荧光检查肉眼看不到的微细裂纹.裂纹多曲折不直并呈暗灰色. 加热速度太快,淬火时冷却太快淬火温度过高或淬火介质温度过低,或淬火介质速度太快;铸件结构设计不合理两连接壁壁厚差太大,框形件中间的加强筋太薄或太细小;装炉方法不当或下水方向不对;炉温不均匀,使铸件温度不均匀. 减慢升温速度或采取等温淬火工艺;提高淬火介质温度或换成冷却速度慢的淬火介质;在壁厚或薄壁部位涂敷涂料或在薄壁部位包复石棉等隔热材料;采用专用防开裂的淬火夹具,并选择正确的下水方向.过烧铸件表面有结瘤,合金的延伸率大大下降. 合金中的低熔点杂质元素如Cd、Si、Sb等的含量过高;加热不均匀或加热太快;炉内局部温度超过合金的过烧温度;测量和控制温度的仪表失灵,使炉内实际温度超过仪表指示温度值. 严格控制低熔点合金元素的含量不超标;以不超过3℃/min的速度缓慢升温;检查和控制炉内各区温度不超过±5℃;定期检查或校准测控仪表,确保仪表测温、示温、控温准确无误.表面腐蚀铸件的表面出现斑纹或块状等与铝合金铸件表面的不同色泽. 硝盐液中氯化物含量超标>%而对铸件表面尤其是疏松、缩孔处造成腐蚀;从硝盐槽中取出后没得到充分的清洗,硝盐粘附在铸件表面尤其是窄缝隙、盲孔、通道中造成腐蚀;硝盐液中混有酸或碱或铸件放在浓酸或浓碱四周受到腐蚀. 尽量缩短铸件从炉内移到淬火槽的时间;检查硝盐中氯化物的含量是否超标,如超标,则应降低其含量或浓度,从硝盐槽中加热的铸件应立即用温水或冷水冲洗干净;检查硝盐中酸和碱的含量,如有酸或碱则应中和或停止使用;不把铝合金铸件放在有浓酸或浓碱的四周.淬火不均匀铸件的厚大部位的延伸率和硬度低非凡是其内部中心,薄壁部位硬度高非凡是其表层. 铸件加热和冷却不均匀,厚大部位冷却慢,热透性差. 重新作热处理,降低升温速度,延长保温时间,使厚薄部位温度均衡;在厚壁部位涂敷保温性的涂料或包覆石棉等隔热性材料,尽量使铸件各部位同时冷却;使厚大部位先下水;换成有机淬火剂,降低冷却速度.四、热处理设备、材料1、热处理设备的主要技术要求1由于铝合金淬火和时效温度温差范围不大因其淬火温度接近合金内低熔点共晶成分的熔点,故其炉内的温度差应控制在±5℃;2要求测温、控温仪表灵敏、准确,以确保温度在上述误差范围内;3炉内各区的温度应均匀,差别在1-2℃的范围内;4淬火槽有加热装置和循环装置,保证水的加热和温度均匀;5应定期检查并更换已污染的冷却水.2、淬火介质淬火介质是保证实现各种热处理目的或作用的重要因素.淬火介质的冷却速度越高,铸件冷却的越激烈快,金属组织中α固溶体的过饱和程度越高,铸件的力学性能也就越好,因为大量的金属间化合物等强化相被固溶到Al的α固溶体中去了.淬火介质按其对铸件的冷却速度的快慢依次为:干冰和丙酮的混合物-68℃、冰水、室温的水、80-90℃的水、100℃的水、经雾化过的水、各种油菜籽油等、加热到200-220℃的各种油、空气等.近年国内研制出来的铝合金淬火介质CL-1的冷却速度介于水和油之间,它可以任何比例与水互溶,其混合比例不同,冷却速度各异,故很便于根据淬火对象调整其冷却速度.它淬火之后无须再进行冲洗且表面光洁,对铸件无污染、无毒害,且能防锈.其主要技术指标是,外观:淡黄色到黄色粘稠状均匀液体,密度:,粘度Y38:≥154MPa·s,逆熔点:80-87℃,折光n:,临界冷却速度:≥260℃/s450-260℃.CL-1有机淬火剂水溶液之所以具有优良的淬火特性,其机理是此溶液在对工件的淬火过程中,可在温度升到一定值时,从水溶液中析出有机成分并分解,并在工件的表面形成一层均匀的导电性薄膜,淬火气泡对工件是直接作用在此薄膜上,而不是直接作用在工件上,从而降低了形成淬火应力的直接捶击作用,因而减少了工件的变形和裂纹,并且在淬火之后,水溶液冷却到一定温度时,此有机薄膜又溶于水溶液中,恢复成原来的均匀的水溶液状态,不妨碍重复使用效果.3、测温、控温仪表及材料测温、控温仪表的精度不应低于级,热处理加热炉应配有能自动测暖和控温的自动记录、自动报警、自动断电、复电的装置和仪表,以保证炉内温度显示和控制准确及温度均匀.热电偶用镍铬-镍硅、镍铬-镍铝质的直径为的偶丝.为提高温度仪的灵敏度、缩小温度的波动范围,最好使用Ф的上述材质的偶丝.并在使用前和使用过程每3个月1次检测、校准1次.。
铝合金薄壁件变形控制的工艺研究

铝合金薄壁件变形控制的工艺研究摘要:结合铝合金薄壁深孔壳体的结构特点以及材料特性,分析零件在加工过程中产生变形的影响因素。
从加工工艺设计、零件装夹方式、切削刀具、切削用量等方面进行分析,提出合理的控制加工变形的方法,满足产品设计技术要求。
关键词:铝合金、薄壁件、变形Study on deformation control technology ofaluminum alloy thin-walled parts(Xi’an Modern Control Technology Research Institute,Xi’an 710065 ,china)SUN shaoyu , LIweiyu, LIU qiang, LiboAbstract: Combined with the structural characteristics andmaterial characteristics of aluminum alloy thin-walled deep-hole shell, the influencing factors of deformation of parts during machining were analyzed. From the aspects of process design, parts clamping mode, cutting tools, cutting parameters,etc., a reasonable method to control machining deformation is put forward to meet the technicalrequirmengts of product design.Key words: aluminum alloy, thin-walled parts, deformation铝合金材料在航空航天、军工、船舶等行业得到了广泛应用,其所加工的形状越来越复杂,尺寸精度和粗糙度要求越来越高。
铝条异形折弯
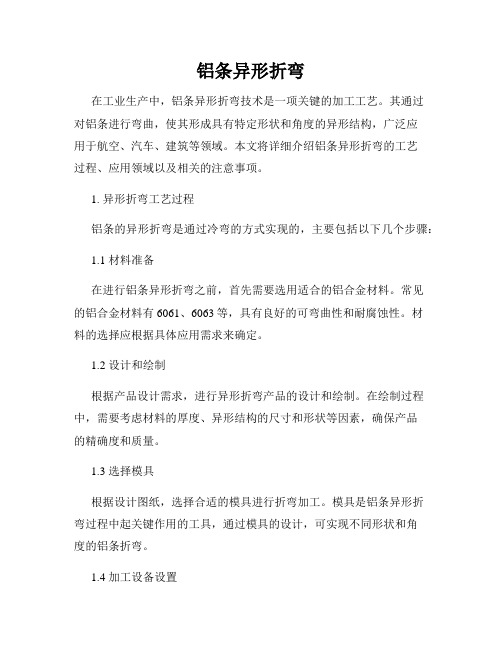
铝条异形折弯在工业生产中,铝条异形折弯技术是一项关键的加工工艺。
其通过对铝条进行弯曲,使其形成具有特定形状和角度的异形结构,广泛应用于航空、汽车、建筑等领域。
本文将详细介绍铝条异形折弯的工艺过程、应用领域以及相关的注意事项。
1. 异形折弯工艺过程铝条的异形折弯是通过冷弯的方式实现的,主要包括以下几个步骤:1.1 材料准备在进行铝条异形折弯之前,首先需要选用适合的铝合金材料。
常见的铝合金材料有6061、6063等,具有良好的可弯曲性和耐腐蚀性。
材料的选择应根据具体应用需求来确定。
1.2 设计和绘制根据产品设计需求,进行异形折弯产品的设计和绘制。
在绘制过程中,需要考虑材料的厚度、异形结构的尺寸和形状等因素,确保产品的精确度和质量。
1.3 选择模具根据设计图纸,选择合适的模具进行折弯加工。
模具是铝条异形折弯过程中起关键作用的工具,通过模具的设计,可实现不同形状和角度的铝条折弯。
1.4 加工设备设置对折弯设备进行调整和设置,确保加工过程中的稳定性。
常见的折弯设备有液压折弯机、数控折弯机等,选择合适的设备可以提高生产效率和产品质量。
1.5 折弯加工将选定的铝条放入模具中,通过设备加工进行折弯操作。
在折弯过程中,需要控制加工力度、速度和角度,避免过度变形和撕裂现象。
1.6 修整与打磨完成折弯后,对产品进行修整和打磨。
这一步骤可以修复折弯过程中可能出现的瑕疵,提高产品的表面光洁度和质量。
2. 异形折弯的应用领域铝条异形折弯技术在众多行业中得到广泛应用,主要体现在以下几个方面:2.1 航空航天在航空航天领域,铝条异形折弯用于制造飞机的机身、翼梢等部件。
通过折弯技术,可以实现结构的精确控制和强度的提高,从而保障飞机的安全性和性能。
2.2 汽车制造在汽车制造过程中,铝条异形折弯技术广泛应用于车身和底盘等零部件的生产。
铝制材料具有重量轻、抗腐蚀等优势,通过异形折弯可以实现更加精细的结构设计,降低车辆的整体重量,提高燃油效率。
精密异形铝管制造工艺

精密异形铝管制造工艺精密异形铝管是一种具有特殊断面形状和更高精度的铝管。
它广泛应用于各种工业领域,如航空航天、汽车制造、机械制造等。
精密异形铝管的制造工艺非常重要,下面将详细介绍其制造过程。
首先,精密异形铝管的制造材料是高纯度的铝合金材料。
铝合金具有良好的抗腐蚀性和强度,适用于各种复杂工况。
在制造过程中,首先需要选择适当的铝合金材料,并对其进行预处理。
预处理包括清洗、除氧和干燥等步骤,以确保材料的纯度和质量。
接下来是管材的挤压。
挤压是制造精密异形铝管最常用的工艺方法之一。
在挤压过程中,首先将铝合金坯料放入挤压机的料斗中。
然后,通过挤出机的压力,将坯料挤压成所需形状的管材。
挤压过程中,材料受到高压和高温的作用,所以需要确保挤压机的温度和压力控制稳定。
在挤压过程中,还需要使用一些辅助工艺,例如剪切力和冷却。
剪切力主要用于调整挤压机的速度和管材的形状,以确保精密异形铝管的准确尺寸。
冷却是为了防止挤压过程中的管材因过热而变形。
在冷却过程中,可以使用水冷却或风冷却的方式。
挤压完成后,需要对管材进行进一步的加工。
其中一种重要的加工方法是拉伸。
拉伸是指将挤压成型的铝管经过拉伸机进行拉伸,以进一步提高铝管的精度和强度。
拉伸过程中,要注意控制拉伸的速度和温度,以避免管材产生裂纹和变形。
另外,为了保证精密异形铝管的表面质量,还需要进行表面处理。
表面处理包括清洁、抛光和阳极氧化等步骤。
清洁是为了去除管材表面的污垢和杂质,保持管材的光洁度。
抛光则是为了提高管材的光亮度和光滑度。
阳极氧化是为了形成一层均匀、致密和耐腐蚀的氧化膜,提高管材的耐腐蚀性。
最后,经过以上工艺步骤,精密异形铝管的制造过程基本完成。
制造出来的精密异形铝管在外观、尺寸和性能方面均能满足客户的需求。
这种工艺不仅提高了铝管的精度和强度,还适应了更多的工业应用领域。
总之,精密异形铝管的制造工艺包括材料预处理、挤压、剪切力和冷却、拉伸、表面处理等多个步骤。
每个步骤都需要精密控制和稳定的工艺参数,以确保铝管的质量和性能。
铝合金铸造方式

离心铸造一、概述离心铸造是将液体金属浇入旋转的铸型中,使液体金属在离心力的作用下充填铸型和凝固形成的一种铸造方法。
为实现上述工艺过程,必须采用离心铸造机创造使铸旋转的条件。
根据铸型旋转轴在空间位置的不同,常用的有立式离心铸造机和卧式离心铸造机两种类型。
立式离心铸造机上的铸型是绕垂直轴旋转的(图1),它主要用来生产高度小于直径的圆环类铸件,有时也可用此种离心铸造机浇注异形铸件。
卧式离心铸造机的铸型是绕水平轴旋转的(图2),它主要用来生产长度大于直径的套类和管类铸件。
立式离心铸造示意图1 图立式离心铸造示意图1 图电动机 7- 6- 5-旋转轴铸件 2- 1-浇包铸型 3-液体金属 4-皮带轮和皮带图2 卧式离心铸造示意图铸件端差 5- 6-液体金属铸型浇注槽浇包1- 2- 3- 4-由于离心铸造时,液体金属是在旋转情况下充填铸型并进行凝固的,因而离心铸造便具有下述的一些特点:1)液体金属能在铸型中形成中空的圆柱形自由表面,这样便可不用型芯就能铸出中空的铸件,大大简化了套筒,管类铸件的生产过程;2)由于旋转时液体金属所产生的离心力作用,离心铸造工艺可提高金属充镇铸型的能力,因此一些流动性较差的合金和薄壁铸件都可用离心铸造法生产;3)由于离心力的作用,改善了补缩条件,气体和非金属夹杂也易于自液体金属中排出,因此离心铸件的组织较致密,缩孔(缩松)、气孔、夹杂等缺陷较少;4)消除或大大节省浇注系统和冒口方面的金属消耗;5)铸件易产生偏析,铸件内表面较粗糙。
内表面尺寸不易控制。
离心铸造的第一个专利是在1809年由英国人爱尔恰尔特(Erchardt)提出的,直到二十世纪初期这一方法在生产方面才逐步地被采用。
我国在三十年代也开始利用离心管、筒类铸件如铁管、铜套、缸套、双金属钢背铜套等方面,离心铸造几乎是一种主要的方法;此外在耐热钢辊道、一些特殊钢无缝纲管的毛坯,造纸机干燥滚筒等生产方面,离心铸造法也用得很有成效。
铝合金模板在异形曲面阳台结构施工中的应用

铝合金模板在异形曲面阳台结构施工中的应用摘要:本文以我单位总承包施工的住宅小区项目为载体,介绍了采用铝合金模板施工异形曲面阳台结构的施工技术,阐述了利用异形曲面结构阳台铝合金模板的配模、施工工艺及施工操作要点。
关键词:铝合金模板异形阳台栏板 BIM 施工一、引言铝合金模板与钢模板相比具有重量轻、精度高、混凝土成型效果好、周转效率高等优点,采用铝合金模板施工异形曲面结构将是一种趋势。
二、项目工程概况开封尉港新区瀚海航城二期A-05-01地块,为住宅小区工程,总建筑面积22.2万平方米,包含8栋高层住宅;住宅33层,层高3.0m,剪力墙结构。
住宅楼阳台均为异形悬挑阳台,阳台楼板外边线为不规则弧形,阳台栏板设计为混凝土栏板+玻璃栏板,混凝土栏板和玻璃栏板结合点在立面中曲线渐变,外立面形式复杂,施工质量不易控制。
图1外立面图三、模板设计一初步设计熟悉图纸校核阳台节点,通过应用BIM技术,建立结构模型,明确异型构件模板加工参数及要点,根据结构模型进行初步翻模。
模板设计满足结构成型尺寸的同时,要降低铝合金模板非标准构件的加工难度,减少模板使用损耗,还要保证模板施工的合理性,能够便于拼装、便于拆模。
二深化设计根据结构特点和铝合金模板的特性,优化阳台栏板模板的配置。
优化结构节点,方便铝合金模板施工:局部弧形栏板下挂部分与相邻结构梁间距较小,不具备作业空间,与业主、设计单位沟通,将此处楼板优化为与栏板底部平齐,便于施工。
细化模板分块:高度不大于200mm的反槛配备吊模与结构板同层施工,高度大于200mm的结构与楼板错层施工。
混凝土栏板高度渐变段位于平直段时,栏板侧模随高度渐变配备梯形模板,贴斜面配备盖板;混凝土栏板高度渐变段位于圆弧段时,栏板依据三维模型对弧形板进行分段、分块配置,在墙模内侧依据栏板高度配斜面盖板,并在墙模上定位、钻孔、固定。
图2 栏板高度渐变段配模方案优化竖向悬臂构件加固措施:栏板高度最高处为1250mm,选用小斜撑加固体系进行栏板模板定位加固,栏板顶部采用型材与墙体模板拉结,不能拉结处设置斜拉钢丝绳。
- 1、下载文档前请自行甄别文档内容的完整性,平台不提供额外的编辑、内容补充、找答案等附加服务。
- 2、"仅部分预览"的文档,不可在线预览部分如存在完整性等问题,可反馈申请退款(可完整预览的文档不适用该条件!)。
- 3、如文档侵犯您的权益,请联系客服反馈,我们会尽快为您处理(人工客服工作时间:9:00-18:30)。
铝合金薄壁异形件的特点
一般来说铝合金薄壁异形件有加工精度要 求高的安装孔;结构复杂、形状各异、没 有明显基准面;壁厚薄而且不均匀;铝合 金材料与一般钢件相比,切削后容易产生 切削应力,导致变形等主要结构特点。因 此,采用数控加工及专用工装,以加工出 满足要求的异型件。
零件的技术要求
Hale Waihona Puke (1)零件加工后要求保证T6状态,HB>75。 (2)零件表面不允许有任何划伤、磕碰等缺 陷。 (3)去清毛刺,锐边倒钝,但所有光孔孔口 不得倒角。 (4)未注线性尺寸公差按IT14,未注形位公 差按C级。 (5)零件加工后要求表面处理AL/Ct.Ocd3。
零件加工要求
该零件的加工精度要求较高,加工面主要 是孔和平面,位置,形状,尺寸精度都各 有要求。工艺设计时要考虑到节约成本, 提高生产率,减轻工人劳动强度,因此采 用数控加工并设计了专用工装,能有效地 保证尺寸加工精度。
(1) 孔的尺寸精度及表面粗糙度 φ21.50+0.03孔、φ18.50+0.03孔、φ250+0.05孔,表面粗糙 度Ra为1.6um; 12×φ3.50+0.02孔、2×φ6.40+0.02孔、8×φ30+0.02孔, 表面粗糙度Ra为1.6um. (2)孔的相互位置精度 φ21.50+0.03孔与φ18.50+0.03孔孔距公差为±0.02mm; φ250+0.05孔与2×φ6.40+0.02孔孔距公差为±0.02mm; (3)主要平面的形状精度、相互位置精度和表面粗糙度 基准A为接合面,平面度公差为0.1mm,表面粗糙度Ra为 1.6um.,外侧面的表面粗糙度为3.2um。 (4)平面与平面的相互位置精度 长度两侧面与基准A的垂直度公差未0.15mm; 高度两面平行度公差未0.15mm。 (5)加工完成后有一定的强度要求,需进行强化处理。
铝合金薄壁异型件数控加工 及工装设计
制作人:罗黎民
铝合金薄壁异形件的用途
铝合金薄壁异形件主要应用在航空、航天 等机载设备中,因此要求壁厚薄已达到减 轻重量的目的,同时需要保证一定的强度 与刚度。通过它将若干只微波器件按一定 的相互位置关系装配在一起,按电信设计 要求实现微波信号的发射与接收。因此该 类零件的加工精度要求更高
数控加工的特点
(1)自动化程度高
在数控机床加工零件时,除了手工装卸工件外,其余加工 过程都是由机床自动完成
(2)加工精度高 加工质量稳定
数控加工的尺寸精度通常在0.005~0.1mm之间,不受零件 形状复杂程度的影响,加工中消除了操作者的人为误差, 提高了同批零件尺寸的一致性,使产品质量保持稳定。
(4)生产效率高 数控机床的加工效率高,一方面是自动化程度高, 在一次装夹中能较多表面的加工,省去了划线、 多次装夹、检测等工序;另一方面是数控机床的 运动速度高,空行程时间短。 (5)易于实现网络制造
(3)对加工对象的适应性强
数控机床上实现自动加工的控制信息是加工程序。当加工 对象改变时,除了相应更换刀具和解决工件装夹方式外, 只要重新编写并输入该零件的加工程序,便可自动加工出 新的零件,不必队机床做复杂的调整,这样缩短了生产准 备周期,给新产品的研制开发以及产品的改进、改型提供 了捷径。