汽车异形齿类零件复合挤压成形技术的优化
汽车复杂齿形类零件的冷挤压成形

汽车复杂齿形类零件的冷挤压成形孟令先宋学进摘要将汽车用复杂齿形件的型腔及齿形挤压成型无需再机加工模具寿命高特别适宜大批量生产精密成形冷挤压模具0 前言 随着我国汽车工业产品的不断更新换代寿命及可靠性的要求越来越高齿轮毛坯的加工在提高生产效率精度降低零件的成本等方面汽车零部件中的齿轮用量很大汽车起动机起动齿轮轴驱动齿轮它们的结构特点都是无空刀槽机械切屑加工困难具有切屑加工所不可比拟的优点机械性能好成本低并且特别适合于大批量生产我们采用冷挤压工艺方法来成型那些复杂的齿形类零件1 工艺分析 1.1 内齿类齿形件 如图1示齿多齿顶尖壁厚不均匀有采用机加工与焊接相结合的工艺方法不但费时费料且强度低整体精度差根据该类齿形件的特点但是也有问题应想办法解决提高效率否则经过分析制定工艺流程为图1 1.2 外齿类齿形件 如图2示因无空刀槽而机械加工困难根据用户减少余量需要将内孔挤压出来而不再机加工确定最佳的工艺方案应该是采用尽可能少的工序最高的生产效率和模具寿命因此包括花键其挤压工艺为润滑齿成形图2 而模具质量的好坏则在于模具结构的设计模具寿命问题一直是困扰冷挤压加工的一个关键技术问题通过实践我们积累了以下模具加工制做的经验1冷挤压成形时必须有一副实用的模架同轴度同时又能十分方便地调整模具间隙成形模的关键为模芯部分的设计和加工制造Array我们将模具设计成分体组合式使其控制在0.25ΪÏû³ýÄ£¾ßѹºÏʱµÄÊÕËõ±äÐÎÁ¿Èç³ÝÂÖÄ£µÄ¼Ó¹¤ÒÔÆÚ¼·Ñ¹³öÀ´µÄ³ÝÂֳߴç²ÎÊý¸ÕºÃ·ûºÏÉè¼ÆÒªÇó=1.5ÃþË÷ÆÕͨÏßÇиî»ú´²¼Ó¹¤Ê±µÄ·Åµç¼ä϶îâ˿ֱ¾¶µÈ¶ÔÄ£¾ß¼Ó¹¤Ãæ´Ö²Ú¶ÈµÄÓ°Ïì¹æÂÉ´Ó¶ø´ïµ½¼õÉÙÅ×ÑÐÁ¿²»ÆÆ»µ³ÝÐεÄÄ¿µÄ模具寿命我们认为主要是模具材料Array必须具有好的韧性和高的强度我们采用的凸模材料为7Cr7Mo3V2Si 真空热处理62 HRC60 HRC刃带大了反而使阻力增加刃带小了一般为2入模角我们一般控制在1220ÒÔÀûÓÚ½ðÊôÁ÷¶¯»¹ÓÐÒ»¸öÓ°ÏìÄ£¾ßÊÙÃüµÄÒòËØ¾ÍÊÇëÅ÷µÄËÜÐԿɼõСģ¾ßËùÊܵıäÐο¹Á¦ËùÒÔÐèÒª¶ÔÀ伷ѹÓÃëÅ÷½øÐÐÈí»¯ÍË»ð´¦ÀíÆäÍË»ð¹¤ÒÕΪ保温5然后随炉冷却至350ʹÍË»ðÓ²¶È¿ØÖÆÔÚ135HRB以下4挤压齿轮的径向跳动与毛坯内孔的精度有直接的关系因此根据体积相等原则及金属塑变规律d=d o+z+x d a齿顶圆直径z——工艺间隙图3 3 批量生产应用及效益 郑州机械研究所一直致力于研究和开发金属的精密成形技术现顺应国家形势积极主动地寻找已形成冷挤压制品的批量生产能力深受用户欢迎多为成形难度大市场前景广阔用冷挤压工艺加工生产复杂的齿形零件提高了材料的利用率又提高了产品的精度和质量经济效益显著材料组织致密表面光洁度高因此减少意外事故的发生愈来愈多的汽车农用车的齿形件要求采用冷挤压工艺精密成形其齿形部分不需再加工不仅节能节材而且能大大提高齿形件的精度和使用寿命我们所设计的模具结构合理完全适宜大批量生产平均在8000Ëæ×ÅÊг¡ÐèÇóµÄ·¢Õ¹²¢»ý¼«ÍƹãÓ¦Óñ±¾©19842 洪深泽. 冷挤压工艺及模具设计安徽科技出版社 6:3孟令先 1963年6月出生高级工程师。
结合齿圈冷挤压工艺优化
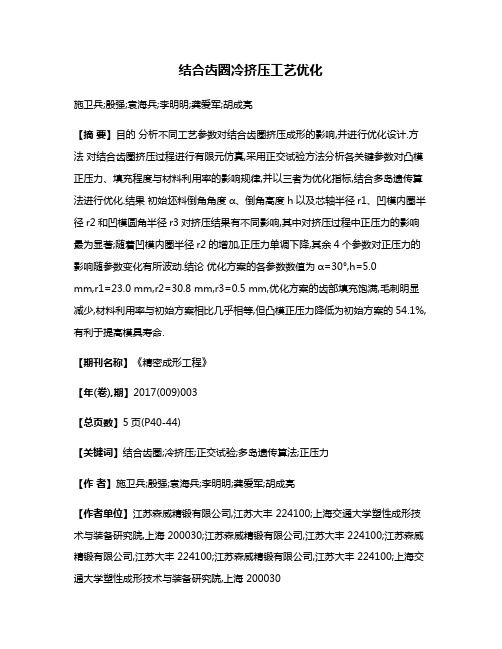
结合齿圈冷挤压工艺优化施卫兵;殷强;袁海兵;李明明;龚爱军;胡成亮【摘要】目的分析不同工艺参数对结合齿圈挤压成形的影响,并进行优化设计.方法对结合齿圈挤压过程进行有限元仿真,采用正交试验方法分析各关键参数对凸模正压力、填充程度与材料利用率的影响规律,并以三者为优化指标,结合多岛遗传算法进行优化.结果初始坯料倒角角度α、倒角高度h以及芯轴半径r1、凹模内圈半径r2和凹模圆角半径r3对挤压结果有不同影响,其中对挤压过程中正压力的影响最为显著;随着凹模内圈半径r2的增加,正压力单调下降,其余4个参数对正压力的影响随参数变化有所波动.结论优化方案的各参数数值为α=30°,h=5.0mm,r1=23.0 mm,r2=30.8 mm,r3=0.5 mm,优化方案的齿部填充饱满,毛刺明显减少,材料利用率与初始方案相比几乎相等,但凸模正压力降低为初始方案的54.1%,有利于提高模具寿命.【期刊名称】《精密成形工程》【年(卷),期】2017(009)003【总页数】5页(P40-44)【关键词】结合齿圈;冷挤压;正交试验;多岛遗传算法;正压力【作者】施卫兵;殷强;袁海兵;李明明;龚爱军;胡成亮【作者单位】江苏森威精锻有限公司,江苏大丰 224100;上海交通大学塑性成形技术与装备研究院,上海 200030;江苏森威精锻有限公司,江苏大丰 224100;江苏森威精锻有限公司,江苏大丰 224100;江苏森威精锻有限公司,江苏大丰 224100;上海交通大学塑性成形技术与装备研究院,上海 200030【正文语种】中文【中图分类】TG306同步器主要用于汽车变速器中,作用是降低汽车的操控难度,使汽车换挡更迅速、高效,同时也能提高汽车驾驶的安全性[1]。
结合齿圈是同步器上的关键零件,主要起到传递扭矩的任务。
结合齿圈在工作时承受的载荷很高,因此在实际加工生产过程中要求其具有较高的性能[2]。
结合齿圈包含齿部和轮毂2部分,由于需要与基本连接形成配件使用,结合齿圈的焊接工艺研究得到关注[3—4],同时关于此类带毂直齿轮的冷锻工艺研究也受到了重视[5—7]。
汽车零部件精冲挤压复合成形工艺研究孟庆成

汽车零部件精冲挤压复合成形工艺研究孟庆成发布时间:2021-09-06T09:05:19.275Z 来源:《中国科技人才》2021年第17期作者:孟庆成[导读] 目前,社会进步迅速,我国的现代化建设的发展也有了改善。
中国汽车工业工程有限公司天津 300000摘要:目前,社会进步迅速,我国的现代化建设的发展也有了改善。
国内汽车零部件行业存在“小、零、散、乱”的局面,而且多集中在低端产品领域,产能过剩和恶性价格竞争明显,普遍面临着较大的生产压力。
对于本土厂商,一方面在前沿技术上很难与国际厂商竞争,难以进入真正的高端系统领域;另一方面也很难实现整车厂商要求的全球供应,难以进入全球市场。
因此,国内企业的行业产业转型升级已经迫在眉睫。
当前,汽车行业正朝着环保、轻量化、减排的大趋势发展,对于汽车零部件加工工艺提出了越来越高的要求。
关键词:汽车零部件;精冲挤压复合成形工艺;研究引言精冲挤压复合成形工艺可以有效结合板料成形和体积成形的特点,文章通过有限元模拟分析研究了精冲挤压成形过程中的缩孔现象,网格畸变与裂纹缺陷,提出了预防措施,获得了挤压比和反压力对成形过程和结果的影响,揭示了精冲挤压成形工艺的特点,对该技术的深入研究具有一定参考价值。
1管件液压成形技术分析1.1技术基本原理管件液压成形技术通常情况下是将预处理过的定尺管材,按照要求在模具型腔当中放置,同时高压液体需要注入到管件中,在此期间,管件两端补料工作要快速实施。
这样操作能利用模具约束作用实现管件冲模,慢慢地让外壁和模具型腔贴合在一起,以此可以制造出各种形状的中空式零件。
管件液压成形技术适用于不同的复杂结构件中,比如,圆形构件、矩形构件以及异型截面等,在此类构件中应用,能够具备较高精密度。
管件液压成形技术的基本原理如下:(1)已经预处理过,并且符合规定标准的定尺管材,要合理地存放在打开模具型腔中,并对其位置进行明确。
(2)压机作用模具闭合,补料密封头转移至模具内腔,若此时状态下,模具是闭合的,密封头转移,停留补料导向的过渡位置。
机械挤压成形工艺优化及仿真模拟

机械挤压成形工艺优化及仿真模拟导言:机械挤压成形是一种广泛应用于金属加工领域的成形工艺。
通过对材料进行挤压,可以实现复杂形状的制造,同时提高材料的密实度和力学性能。
然而,机械挤压成形工艺中存在一些问题,如加工过程中的应力分布不均匀,易引起材料的变形、断裂等缺陷。
本文将探讨机械挤压成形工艺的优化方法及其仿真模拟技术。
一、机械挤压成形工艺的优化方法1.材料选择与预处理机械挤压成形的材料选择是关键环节之一。
合理选择材料可以提高挤压成形的效率和品质。
常用的挤压成形材料包括铝合金、铜合金、钢等。
在选择材料时,需要考虑其塑性变形能力、热处理性能以及成本等因素。
此外,在进行挤压成形前,还需要对材料进行预处理,如退火、固溶等,以改善材料的可变形性能。
2.模具设计与优化模具是机械挤压成形的重要装备之一。
合理设计和优化模具结构可以提高成形质量和生产效率。
模具设计时需要综合考虑产品形状、尺寸、成形工艺等因素。
通过采用合适的模具形状和尺寸,可以减小挤压过程中的变形和应力集中等问题,提高产品的质量。
3.挤压工艺参数的优化挤压工艺参数的选择对成形质量和效率有着重要影响。
常见的挤压工艺参数包括挤压速度、挤压温度、挤压力等。
优化挤压速度可以避免产生挤出时的应力冲击,减少挤压过程中的应力分布不均匀。
合理控制挤压温度可以减小材料的变形和晶粒生长速度,从而提高产品的力学性能。
调节挤压力可以控制产品的尺寸和密实度。
二、机械挤压成形的仿真模拟技术1.有限元仿真有限元仿真是一种常用的机械挤压成形仿真方法。
通过将挤压过程建模,利用有限元方法求解材料在挤压过程中的应力、应变分布以及变形情况。
有限元仿真可以帮助预测和分析挤压过程中的缺陷和变形问题,优化工艺参数和模具设计。
2.流体仿真流体仿真可以用来模拟挤压过程中的金属流动和应力场。
通过建立数学模型,求解流体动力学方程和传热方程,可以得到挤压过程中的流速、温度分布以及应力场。
流体仿真可以帮助优化挤压工艺参数,改善产品的表面质量和力学性能。
挤压成形工艺优化与质量控制

挤压成形工艺优化与质量控制挤压成形工艺是一种常见的金属加工方法,被广泛应用于汽车、航空航天、建筑等行业。
然而,由于材料本身的复杂性和加工过程中的不确定性,挤压成形工艺中存在着一系列的问题和挑战。
因此,优化和控制挤压成形工艺,以提高产品质量和降低生产成本,成为了制造业中的重要课题。
首先,挤压成形工艺的优化在于合理调整加工参数以提高成形效率和降低能耗。
例如,通过优化挤压温度、挤压速度和挤压压力等参数,可以有效降低成形过程中的能耗,提高能源利用效率。
此外,在挤压过程中,材料流动的控制也是必不可少的。
通过研究挤压变形机理和优化模具结构,可以减少材料的脱轨和撕裂现象,提高产品的成形率和表面质量。
其次,挤压成形工艺的质量控制是确保产品质量的关键。
一方面,通过建立完善的质量控制体系和技术规范,可以确保挤压成形工艺的稳定性和一致性。
例如,通过制定严格的工艺参数和操作标准,可以有效降低产品的尺寸误差和表面缺陷。
另一方面,引入先进的检测技术和装备,可以实时监测和控制挤压过程中的关键参数。
例如,通过在线测量挤压力、温度和材料流动速度等参数,可以及时发现和解决潜在的问题,提高产品的一致性和可靠性。
同时,挤压成形工艺的优化和质量控制还需要与其他加工方法和工艺相结合。
例如,通过结合轧制、冷挤压或后续热处理等加工方法,可以进一步改善产品的性能和精度。
此外,利用先进的数值模拟和优化算法,可以对挤压工艺进行全局优化,提高生产效率和降低成本。
通过将材料性能、工艺参数和设备状态等多个因素综合考虑,可以实现最优工艺方案的选择和优化。
总之,挤压成形工艺的优化和质量控制是制造业中的重要课题。
通过合理调整工艺参数、优化模具结构和引入先进的检测技术,可以提高成形效率和产品质量。
此外,与其他加工方法和工艺相结合,并利用数值模拟和优化算法进行综合优化,可以进一步提高生产效率和降低成本。
挤压成形工艺的优化和质量控制是制造业不断追求的目标,也是技术进步和经济发展的重要保障。
复杂形状零件冷挤压成形数值分析和工艺优化

21 0 0年 3月
上
海
工
程
技
术
大
学
学
报
Vo . 4 NO 1 12 .
M a .2 0 r 01
J uR O NAL O HANGHAI FS I RS TY 0 NGI EE I C E UN VE I F E N R NG S I NCE
Co d Ex r so o m p e r s l t u i n f r Co l x Pa t
Z ANG e g ,Z H M n’ ENG in z o g ,M A eqn Ja —h n 。 Yu — i g・
( . t n lDi & Mo l gnern s ac n e ,S a g a io o gU nv r iy h n h i 0 0 0,Chn 1 Nai a e o u dEn i eig Ree rhCe tr h n h i a t n iest ,S a g a 0 3 J 2 ia
Ab t a t n v e o h e e toc u r d i c u lc d e r i n o o p e a t t e c us f d f c s r c :I i w f t e d f c c r e n a t a ol xtuso f a c m l x p r , h a e o e e t wa ou u y utlzng Deor s fwa e, h n t t p b — t p c d e t u i n wa pp id t mpr v s f nd o t b iii f m o t r t e he s e — y s e ol x r so sa le o i oe t r e s Fi ly, h me ia n l s swa a re u o o i z hee t uso oc s . he p oc s . na l t e nu rc la a y i s c r id o tt ptmi et x r i n pr e s Thesm u a i l— to e ul h i n r s ts owst tt t p by s e o d e r son ha v i e he fo s r tfc to d c e s d t e ha he s e — - t p c l xt u i s a o d d t l w t a iia i n, e r a e h e t uso o d a d pr du e h a ii d p o c s x r i n l a n o c d t e qu lfe r du t . Ke r s:c y wo d omp e a t l x p r s;c d e t uson;nu rc lan l ss ol x r i me ia a y i
结合齿圈冷挤压工艺优化

DO I :1 0 . 3 9 6 9  ̄ . i s s n . 1 6 7 4 — 6 4 5 7 . 2 0 1 7 . 0 3 . 0 0 8 中图分 类号 :T G 3 0 6 文献标识码 :A 文章编号 :1 6 7 4 . 6 4 5 7 ( 2 0 1 7 ) 0 3 . 0 0 4 0 . 0 5
( 1 . J i a n g s u S u n wa y P r e c i s i o n F o r g i n g C o . , L t d . , D a  ̄ n g 2 2 4 1 0 0 , C h i n a ;
2 . I n s t i t u t e o f F o r mi n g T e c h n o l o g y a n d E q u i p me n t , S h a n g h a i J i a o T o n g U n i v e r s i t y , S h a n g h a i 2 0 0 0 3 0 , C h i n a )
i n d e x e s w e r e d e i f n e d a s o b j e c t t o b e o p t i mi z e d i n c o m b i n a t i o n wi t h t h e mu l t i — i s l a n d g e n e t i c a l g o r i t h m. T h e i n i t i a l c h a mf e r a n g l e
汽车变速器异形轴套冷挤压工艺及模具设计
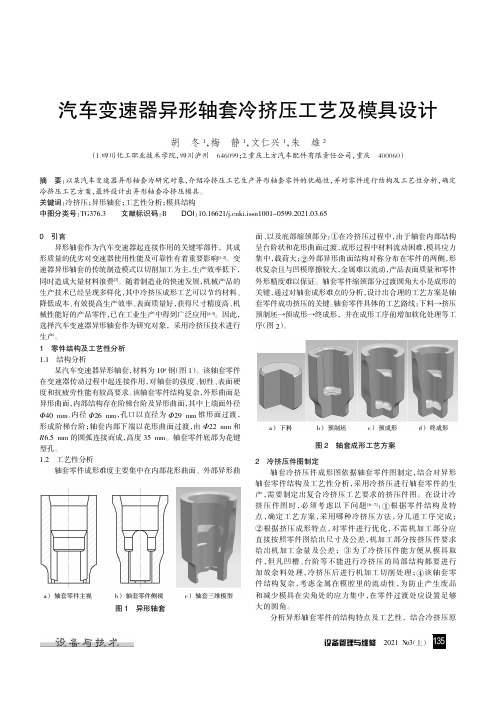
设备管理与维修2021翼3(上)汽车变速器异形轴套冷挤压工艺及模具设计胡冬1,梅静1,文仁兴1,朱雄2(1.四川化工职业技术学院,四川泸州646099;2.重庆上方汽车配件有限责任公司,重庆400060)摘要:以某汽车变速器异形轴套为研究对象,介绍冷挤压工艺生产异形轴套零件的优越性,并对零件进行结构及工艺性分析,确定冷挤压工艺方案,最终设计出异形轴套冷挤压模具。
关键词:冷挤压;异形轴套;工艺性分析;模具结构中图分类号:TG376.3文献标识码:BDOI :10.16621/ki.issn1001-0599.2021.03.650引言异形轴套作为汽车变速器起连接作用的关键零部件,其成形质量的优劣对变速器使用性能及可靠性有着重要影响[1-2]。
变速器异形轴套的传统制造模式以切削加工为主,生产效率低下,同时造成大量材料浪费[3]。
随着制造业的快速发展,机械产品的生产技术已经呈现多样化,其中冷挤压成形工艺可以节约材料、降低成本、有效提高生产效率、表面质量好,获得尺寸精度高、机械性能好的产品零件,已在工业生产中得到广泛应用[4-5]。
因此,选择汽车变速器异形轴套作为研究对象,采用冷挤压技术进行生产。
1零件结构及工艺性分析1.1结构分析某汽车变速器异形轴套,材料为10#钢(图1)。
该轴套零件在变速器传动过程中起连接作用,对轴套的强度、韧性、表面硬度和抗疲劳性能有较高要求。
该轴套零件结构复杂,外形曲面是异形曲面,内部结构存在阶梯台阶及异形曲面,其中上端面外径椎40mm 、内径椎26mm ,孔口以直径为椎29mm 锥形面过渡,形成阶梯台阶;轴套内部下端以花形曲面过渡,由椎22mm 和R 6.5mm 的圆弧连接而成,高度35mm 。
轴套零件底部为花键型孔。
1.2工艺性分析轴套零件成形难度主要集中在内部花形曲面、外部异形曲面、以及底部缩颈部分:淤在冷挤压过程中,由于轴套内部结构呈台阶状和花形曲面过渡,成形过程中材料流动困难,模具应力集中,载荷大;于外部异形曲面结构对称分布在零件的两侧,形状复杂且与凹模摩擦较大,金属难以流动,产品表面质量和零件外形精度难以保证。
机械挤压成形工艺优化及仿真模拟

机械挤压成形工艺优化及仿真模拟1.引言机械挤压是一种常用的金属加工工艺,用于将金属材料通过受力挤压变形成所需形状。
随着现代工业的发展,机械挤压工艺在汽车、航天、船舶等领域有着广泛的应用。
机械挤压成形的质量和效率受到多方面因素的影响,因此,优化挤压工艺和利用仿真模拟手段对成形过程进行分析和优化已经成为一个重要的研究课题。
2.机械挤压工艺的基本原理机械挤压是利用挤压机将金属材料加热后推入模具腔内进行塑性变形的过程。
通过对金属材料的加热和机械力的作用,使金属材料在模具内发生流变,从而形成所需的产品形状。
挤压工艺的优化主要包括材料的选取、加热温度的控制、模具设计等方面。
3.机械挤压工艺的优化3.1 材料的选取在机械挤压过程中,金属材料的选择直接影响到成形产品的质量。
不同的金属材料具有不同的塑性变形特征和流变应力曲线。
根据需要选择合适的材料,可以使成形过程更加顺利和稳定。
3.2 加热温度的控制金属材料的加热温度对机械挤压工艺的成形效果有着重要影响。
温度过高会导致金属材料的烧结和软化,使挤压过程难以控制;温度过低则会导致材料的塑性变形性差,增加挤压所需的力。
因此,通过合适的加热温度控制,可以使金属材料在挤压过程中达到最佳的塑性变形能力。
3.3 模具设计模具的设计对机械挤压工艺的成形效果和产品质量有着重要影响。
合理的模具设计可以使得挤压过程中金属材料的流动更加顺畅,减少应力集中和变形不均匀的问题。
通过优化模具的结构和采用适当的润滑剂,可以提高挤压效率和成形质量。
4.仿真模拟在机械挤压工艺中的应用由于机械挤压工艺的复杂性和实际操作的困难性,借助计算机仿真模拟手段对挤压过程进行分析和优化已成为一种常用的方法。
通过建立适当的数学模型和应用有限元方法,可以模拟挤压过程中的金属流动、应力分布、温度变化等重要参数。
基于仿真模拟的结果,可以通过优化工艺参数和模具结构,提高挤压的质量和效率。
5.结论机械挤压成形工艺的优化和仿真模拟在现代工业中具有重要意义。
机械挤压成形技术的过程优化

机械挤压成形技术的过程优化机械挤压成形技术是一种常见的金属加工方法,通过施加力量将金属材料从一个孔口挤出,形成所需的形状。
随着工业技术的不断发展,人们对机械挤压成形技术的过程进行了优化,旨在提高生产效率和产品质量。
本文将从原材料选择、工艺参数控制和模具设计等方面,探讨机械挤压成形技术的过程优化。
首先,原材料的选择对机械挤压成形技术的过程优化至关重要。
不同的金属材料在挤压成形时具有不同的性能和挤压性能。
因此,在选择原材料时,需要充分考虑其可塑性、耐磨性和变形性等参数。
此外,还应根据产品的需求,选择合适的原材料成分比例和形态。
通过优化原材料的选择,可以提高产品的可靠性和使用寿命。
其次,工艺参数的控制是机械挤压成形技术的关键环节。
工艺参数包括挤压速度、挤压温度、挤压力量和挤压长度等。
在挤压过程中,合理的工艺参数可以有效地控制产品的形状和尺寸精度,减少挤压过程中的缺陷和变形。
因此,通过实验和经验,确定合适的工艺参数是优化机械挤压成形技术过程的重要方法。
除了原材料选择和工艺参数控制,模具设计也是机械挤压成形技术过程优化的关键。
模具的设计直接影响产品的形状和精度。
在模具设计中,应根据产品的要求和挤压过程中的力学特性,优化模具的结构和形状。
例如,在模具的进料部位设置合适的导向装置,以确保原材料的均匀进料和良好的变形。
此外,通过使用合理的模具材料和表面处理技术,可以降低摩擦阻力和磨损,提高模具的使用寿命。
此外,机械挤压成形技术的过程优化还需要充分利用现代技术手段。
例如,通过数值模拟和有限元分析,可以模拟和预测挤压过程中的应力分布和变形情况,为工艺参数的优化和模具设计的改进提供科学依据。
此外,借助先进的控制系统和自动化设备,可以实现对挤压过程的精确控制和监测,提高生产效率和产品质量。
总结起来,机械挤压成形技术的过程优化需要从原材料选择、工艺参数控制、模具设计和利用现代技术手段等方面综合考虑。
通过合理地优化这些环节,可以提高机械挤压成形技术的生产效率和产品质量,推动相关行业的发展。
汽车零件生产中的设计优化技术

汽车零件生产中的设计优化技术在汽车制造行业中,零件设计的优化是提高产品质量和性能的关键。
随着技术的不断进步和市场需求的增长,汽车零件的设计越来越注重创新和优化。
本文将介绍汽车零件生产中的设计优化技术,并探讨其在提高车辆性能和降低成本方面的重要作用。
一、仿真技术仿真技术是汽车零件设计优化的重要工具。
它可以通过建立数学模型和运用计算机模拟来模拟和分析产品的性能。
通过使用仿真技术,工程师可以在实际生产之前评估产品的设计和性能,以便及早发现和解决潜在的问题。
这种无需实际制造样品的方法不仅节省时间和成本,而且可以提高设计的准确性和可靠性。
二、材料选择和优化在汽车零件设计中,材料选择和优化对于产品性能至关重要。
不同的材料具有不同的机械性能、热性能和耐磨性能等特点。
通过合理选择材料,可以确保零件在使用中具有较高的强度和耐久性。
此外,优化材料的使用也可以降低汽车零件的重量,提高整车的燃油效率。
三、结构设计优化结构设计优化是指通过改进零件的结构和几何形状,以提高材料的使用效率和产品的性能。
在汽车零件生产中,通过使用计算机辅助设计软件和有限元分析等工具,工程师可以对零件进行复杂的结构优化。
这种优化过程可以显著改善零件的强度、刚度和耐久性等性能,从而满足特定的使用要求。
四、模具设计优化模具设计在汽车零件生产中起到至关重要的作用。
优化模具设计可以提高生产效率和减少生产成本。
例如,通过优化零件的模具结构和布局,可以减少材料的浪费和减轻模具的磨损。
此外,设计合理的模具还可以提高生产的稳定性和零件的质量。
五、制造工艺优化制造工艺优化与零件设计和模具设计相互配合,共同改善产品的生产效率和质量。
通过分析和优化制造工艺,可以缩短零件生产的周期和提高产品的一致性。
例如,通过改进机床装备和加工工艺,可以降低零件的精度要求和加工难度,提高生产效率。
综上所述,汽车零件生产中的设计优化技术在提高产品质量和性能方面起到关键作用。
通过对仿真技术、材料选择和优化、结构设计优化、模具设计优化和制造工艺优化等方面进行合理的应用,汽车制造商可以优化产品的设计和生产过程,提供更高质量和性能更佳的汽车零件,满足市场的需求并赢得竞争优势。
径向反向复合挤压成型技术的研究现状

径向反向复合挤压成型技术的研究现状径向反向复合挤压成型技术是一种先进的金属成型工艺,广泛应用于航空航天、汽车、船舶等领域。
本文将介绍该技术的研究现状。
我们来了解一下径向反向复合挤压成型技术的基本原理。
该技术是在传统的复合挤压成型技术基础上发展而来的,它通过在金属板材上施加压力,使其在模具中径向流动,从而实现金属板材的变形和成型。
与传统的复合挤压成型技术相比,径向反向复合挤压成型技术具有更高的成形精度和更好的表面质量。
径向反向复合挤压成型技术在金属成型领域的研究已取得了一系列重要成果。
首先,研究人员对该技术的成形过程进行了深入分析和研究,提出了一系列数学模型和理论模型,用于描述和预测金属板材的变形行为和成形质量。
这些模型和理论为径向反向复合挤压成型技术的工艺参数优化和成形质量控制提供了重要的理论依据。
研究人员还对径向反向复合挤压成型技术的设备和工艺进行了改进和创新。
例如,他们开发了一种新型的复合挤压机床,采用先进的液压系统和控制系统,实现了对金属板材的精确控制和成形。
同时,研究人员还提出了一种新的模具设计方法,通过优化模具结构和参数,实现了金属板材的高效成形和优质表面。
研究人员还对径向反向复合挤压成型技术的应用进行了广泛探索。
他们将该技术应用于航空航天、汽车、船舶等领域,取得了一系列重要的应用成果。
例如,在航空航天领域,径向反向复合挤压成型技术被用于制造飞机蒙皮和发动机外壳等关键部件,大大提高了航空器的性能和安全性。
在汽车领域,该技术被应用于制造车身结构和车身零部件,提高了汽车的强度和刚度,降低了车辆的重量和能耗。
径向反向复合挤压成型技术是一种具有广泛应用前景的先进金属成型技术。
目前,该技术在金属成型领域的研究已取得了一系列重要成果,包括成形过程分析和建模、设备和工艺改进以及应用探索等。
随着科学技术的不断进步和发展,径向反向复合挤压成型技术有望在未来取得更多突破和应用。
汽车轮毂液压挤压成形技术研究

汽车轮毂液压挤压成形技术研究在现代工业制造中,汽车轮辋是一个非常重要的零部件。
随着汽车工业的发展,轮辋的制造也变得更加复杂。
传统的制造方法如铸造、锻造和切割等,已难以满足现代高精度、高效、高质量的生产需求。
因此,液压挤压成形技术逐渐成为制造汽车轮辋的一种新趋势。
一、液压挤压成形技术液压挤压成形技术是一种利用液体压力将金属材料加工成形的方法。
该技术在轮辋制造中得到较广泛应用。
使用液压挤压成形技术来制造汽车轮辋,可以改善其性能,提高生产效率,减少能源资源的浪费等。
液压挤压成形技术的基本原理是利用压力将金属材料打至预定形状,并保持材料的完整性,达到所需的物理和机械性能。
与其他制造技术相比,液压挤压成形技术具有许多明显的优点,包括:1. 精度高:利用液压挤压成形技术制造汽车轮辋,可以获得更高的精度和更准确的尺寸,使轮辋更加符合设计要求。
2. 更好的强度:液压挤压成形对金属材料的塑性变形程度非常小,因此能保证轮辋的强度,具有更好的耐久性和安全性。
3. 高效率:液压挤压成形技术具有高效率的特点,能显著提高生产效率和降低生产成本。
二、液压挤压成形技术在汽车轮辋制造中的应用液压挤压成形技术在汽车轮辋制造中已经得到了广泛应用。
液压挤压成形的最大优点是能够减少材料的浪费,同时也可以大幅度提高生产效率。
1. 提高轮辋的精度和质量液压挤压成形技术可以帮助生产出更高精度和更合格的轮辋,不仅可以加速制造过程,还可以提高生产效率,节约成本。
2. 节约能源和资源液压挤压成形技术可以让金属原材料得到充分利用,减少浪费,并且其可以完整保留金属材料的物理性质,保证了金属的质量。
3. 降低交货时间液压挤压成形技术的高生产效率和快速制造能力,能够减少生产时间,使得交货时间缩短并减少成本。
三、液压挤压成形技术的未来发展液压挤压成形技术在未来的发展中,将会变得越来越普及和热门。
随着人们对汽车轮辋的需求与生产要求越来越高,液压挤压成形技术在轮辋制造中将会得到更多的应用。
汽车零件冷冲压成形质量的优化

汽车零件冷冲压成形质量的优化发布时间:2022-11-13T09:12:53.317Z 来源:《科学与技术》2022年7月第14期作者:吴庆元[导读] 随着当前生活水平的逐渐提高,人们对汽车的需求量越来越吴庆元安徽江淮汽车集团股份有限公司,安徽省合肥市,230000摘要:随着当前生活水平的逐渐提高,人们对汽车的需求量越来越大,然而对汽车的品质要求也越来越高。
约80%的汽车零件是由模具加工制造的,其中有数百个零件由冷冲压成形加工而成。
由于零件在冷冲压成形过程中会受到多种因素的影响,因此零件在生产过程中会出现起皱、破裂和回弹等一些缺陷问题,而且钢度越强越容易发生这些缺陷.对于这些缺陷,传统的方法是利用试错法或经验法来解决,但这类方法需要花费大量的人力、物力和时间成本.近年来有限元技术被逐步应用于零件的冷冲压成形生产中,并取得了良好的效果。
关键词:汽车零件;冷冲压;质量优化引言汽车行业中生产的轮罩类、纵梁类冲压件,拉伸工艺均使用冷冲压深拉伸,其中轮罩类拉伸模特点是拉伸深度深,拉伸最深处达到280mm。
按照冷冲压模具行业设计标准,拉伸深度超过200mm,一次拉伸、二次整形,其优点通过二次拉伸,避免拉伸深度过深导致的板料走料过快,模具走料R角磨损,板料起皱造成冲压件拉毛、开裂的质量问题发生。
1后地板横梁的冷冲压工艺设计图1为某品牌汽车的后地板横梁设计图.该零件位于汽车后座地板与前座之间,形状复杂,尺寸较大,拉延深度较深.板材为HC340,厚度为1.0mm,冲压成形后的零件最小厚度要大于0.8mm,最大厚度要小于1.2mm.根据零件特点及对冷冲压模具的设计要求,本文将冲压成形工艺确定为:拉延—切边冲孔—翻边—整形.其中:拉延工序是通过上下模具使板料成形(零件基本形状);切边冲孔工序是通过模具把工艺补充面和孔的多余材料切除;翻边工序是使零件沿着指定边缘翻拆成一个设计角度;整形工序是对由各种原因导致形状不合格的零件进行矫正.根据零件冲压方向及工艺要求,本文利用CAD软件对零件的边缘、孔工艺补充面和拉延模的凹模型面进行设计。
特种车辆用异形箱体零件挤压成形工艺与实验研究的开题报告

特种车辆用异形箱体零件挤压成形工艺与实验研究的开题报告一、选题背景随着社会经济的快速发展,交通运输需求不断增加,特种车辆的应用越来越广泛。
而作为特种车辆的重要部件之一——异形箱体,是由多个零部件组成的。
其中,箱体外壳大多采用铝型材挤压成型的工艺,但异形零件的加工相对复杂且成本较高。
因此,对于特种车辆用异形箱体零件挤压成形工艺的研究,是非常有必要的。
二、选题目的本文旨在研究特种车辆用异形箱体零件挤压成形工艺,以寻求一种经济、高效、可行的生产方式,提高异形零件的加工精度和生产效率,降低成本,满足客户日益增长的需求。
三、研究内容与步骤1.需求分析调查市场上特种车辆的需求和用户的要求,分析异形箱体零件的加工难度和成本问题,确定研究的方向和目标。
2.材料与模具设计选择适宜的材料,设计符合异形零件形状和尺寸要求的模具,确定工艺参数和生产工艺流程。
3.挤压成形实验在实验室中进行挤压成形实验,不断调整工艺参数,寻求最佳的挤压成形条件,验证异形零件挤压成形工艺的可行性,并分析生产效果和成本。
4.成形零件的表面处理针对异形箱体零件的特殊形状,选择适合的表面处理技术,钝化处理或喷涂涂料等,提高零件的耐腐蚀性和使用寿命。
5.总结与优化对研究结果进行总结和分析,评价异形零件挤压成形工艺的优缺点,提出改进和优化建议,以期实现异形零件挤压成形工艺的优化和提高生产效率。
四、研究意义本研究对提升特种车辆用异形箱体零件的加工精度与生产效率具有积极推动作用,可以满足特种车辆对高质量、刚性和轻量化的要求,为特种车辆的运用提供更加有力的支持。
五、预期成果通过本研究,预计可以成功开发出特种车辆用异形箱体零件挤压成形工艺,实现异形零件的高效、低成本生产,提高生产效率和质量,并为特种车辆行业的发展做出贡献。
超硬材料异形零件数控加工工艺改进方案

针对超硬材料异形零件结构复杂、装夹困难、材料硬度高、刀具磨损严重、传统装夹方式易产生变形以及关键特征几何精度难以保证等工艺难题,设计拉紧定位工装,解决装夹问题。
采用平面特征底齿轴向微量渐进铣削和应力释放防变形技术,有效解决切削力、夹紧力、切削热和材料应力释放等综合因素对零件加工精度造成的影响,确保了加工质量稳定可靠。
1序言随着航天技术的不断发展进步,航天产品结构也越来越复杂。
超硬材料异形零件的加工尺寸精度、表面粗糙度以及几何公差直接影响机构传动的性能指标。
由于这类零件具有结构复杂、尺寸精度高和几何公差要求严的特性,所以加工过程中零件易变形,刀具磨损严重,关键特征几何精度难以保证,其加工方法一直是困扰科研和生产的难题。
本文将详述通过设计拉紧定位工装来解决装夹问题,采用平面特征底齿轴向微量渐进铣削和应力释放防变形技术,有效解决各种因素对精度造成的影响,确保了加工质量稳定可靠。
2零件结构分析超硬材料异形零件(见图1)材料为自由锻件,精加工前经淬火处理后,硬度高达40~45HRC,属于难加工材料。
零件具有结构复杂、尺寸精度高和几何公差要求严的特性,整体为不规则异形结构,各个空间位置分布筋、槽、孔、阶台、圆弧和角度特征,其关键控制部分槽底相对于基准孔距尺寸为103mm,零件总长为127mm,最薄筋厚度为10mm。
各方向结构特征相对于基准孔和基准轴线的尺寸精度和几何公差具有严格的要求。
热处理后零件变形较大,零件孔与槽之间、孔与面之间以及面与面之间的几何精度要求极严。
3加工难点分析零件目前是在五轴机床上采用通用夹具(平口钳)装夹其平整部位两侧(零件夹持部位底部留夹持余量),采用圆柱铣刀径向切削模式加工。
由于受切削力、夹紧力、切削热和材料应力释放等综合因素影响,因而加工质量难以保证。
分析该零件的加工难点,有以下几方面。
1)零件装夹过程中,工件被夹持部位需要平口钳夹紧力作用进行定位,各空间位置特征相对于基准要素保持相对平衡状态,零件在装夹后产生微小变形的情况下,完成切削加工并达到精度要求。
- 1、下载文档前请自行甄别文档内容的完整性,平台不提供额外的编辑、内容补充、找答案等附加服务。
- 2、"仅部分预览"的文档,不可在线预览部分如存在完整性等问题,可反馈申请退款(可完整预览的文档不适用该条件!)。
- 3、如文档侵犯您的权益,请联系客服反馈,我们会尽快为您处理(人工客服工作时间:9:00-18:30)。
上,再增加一定的加工余量,一般为0.6~0.8
mm,同时该段也需加工成有角度≯的拔模斜度。 2.3挤压凸模优化设计 采用图4所示的原平底凸模结构,成形挤压 力将高达1 900~2
000
(a)原坯料
m)改进优化后坯料
图5坯料简图
如前所述,采用改进的凸模和坯料,能降低 挤压力,轮毂的齿形更容易成形和充满,提高金 属材料利用率和生产效率。
图4凸模简图
因此,在凹模型腔尺寸设计确定时必须考虑这
些差异,这样可省去工件齿形校形的工序。 (I)对于上凹模,其工作段型腔(即用于成 形轮毂齿形的部分)各直径尺寸的取值,是在产 品各相应直径名义尺寸的基础上再减小0.25 mm左右,各齿厚尺寸则在产品各相应齿厚名义
3坯料改进优化
坯料若采用如图5所示的实心圆柱状坯 料,则凸模应采用图4所示的平底凸模,这样不 但成形挤压力很大,而且轮毂的齿形不容易成
关键部件有许多,而离合器就是其中之一。随 着汽车工业的不断发展,越来越多的汽车上使 用形状结构复杂,但却能提高汽车性能的零件。 现在不少汽车的离合器中使用了如图1、2所示 的轮毂类零件。该轮毂类零件的外形由齿形和 燕尾槽组成,而其齿形又分成3种不同形状和
尺寸的异形齿(图1中I、Ⅱ、Ⅲ3种,其齿形的
宽度、根圆直径不相同,位置是不对称的)。如
容易破裂或缺损,从而造成模具损坏报废。为 了降低成形挤压力,改善模具寿命,可通过改进 和优化凸模及坯料来实现,后面会分别进行介绍。 (2)过高的成形压力,使得当工件成形结束 时脱模取件的脱模力也较大,造成工件脱模困 难。脱模时工件齿形部分和柄部分别与上、下 凹模表面发生较大的摩擦,易造成工件齿部和
2复合挤压模具优化
34
Die and Mould Technology No.5 2009
文章编号:1001—4934(2009)05—0034—04
汽车异形齿类零件复合挤压成形技术的优化
彭树杰,刘玉兰,杜 鹃,张焕莲
(中国兵器工业第五九研究所,重庆400039) 摘 要:分析了汽车零件中1种异形齿形类零件,即离合器轮毂类零件的结构特点及
收稿日期:2009—05—08
本文只就在研究过程中,对部分重点技术与模
具的改进优化进行详尽阐述。
作者简介:彭树杰(1966一),男,高级工程师。
万方数据
模具技术2009.No.5
35
挤压凹模和凸模的改进优化,下面分别加以阐述。
髟∥ ////、 厶
∞ 。
_-——
2.1挤压凹模结构优化设计
一∞
乡/例
静
中图分类号:TG376.3 文献标识码:A
Abstract:The structural characteristics of lyzed.The technological difficulties
a
ห้องสมุดไป่ตู้
special tooth-shaped clutch hub part were cold compound extruding process and the
36
一N 1孓
色
前面已经论述到,轮毂零件复合挤压成形 的关键和难点实际就是其齿形的挤压成形,而 齿形挤压成形时,是既有径向成形,又有轴向成 形的1种复合挤压成形技术,因此挤压成形凹 模是1种复合结构凹模,即为这2种挤压成形
乃
图1轮毂零件简图
的凹模形状与结构的组合。该复合结构凹模的 结构简图如图3所示。考虑到复合挤压凹模加 工和损坏后易于更换等的需要,因此将成形凹 模设计成上、下两部分,即成形凹模是由上凹模 和下凹模组合而成。上凹模的型腔是与轮毂零 件齿形形状完全相同的形状,是用来成形轮毂 齿形的。下凹模的型腔为一通孔,其作用是当 轴向挤压成形时,迫使金属材料轴向流动,从而 有利于齿形成形。同时由于在轮毂齿形下端成
2 ooo
kN降低到约l
500
kN;脱模力降低40%
~50%,从350--.400 kN降低到约200 kN;凹模 寿命提高1倍以上,从不足1 000件提高到
2
000件以上。 (2)改进优化的复合挤压技术与模具结构,
使轮毂的齿形更容易成形和充满,同时改善了 工件表面质量,提高工件合格率15%~25%,降 低废品比例。 (3)由于大幅度减少了零件的加工余量,从 而提高了生产加工的效率。 (4)挤压成形时工件芯部的金属材料被部 分挤出而流向齿形处,因此增加了材料利用率, 节省了金属材料的消耗,降低了原材料成本。
optimized punch,cavity die and billet were all designed.The optimization results were veri- fied by experiments. Keywords:special tooth・shaped part;cold compound extrusion technology;extruding die;
ana—
in the
key
points in die designing of this kind of part were elaborated.And the die manufacturing,in— stallation and alignment were also introduced.An optimized design was put forward targe- ted to tackle the existing technological problems in the compound extruding process.The
其复合冷挤压成形加工工艺的技术难点,详细阐述了此种类型零件复合冷挤压成形技 术的模具设计要点,以及模具的加工、安装和调试。针对现有复合冷挤压成形技术存 在的问题,提出了改进优化的方案,设计了改进优化的凹模、凸模以及坯料,通过试验 验证了优化的效果。
关键词:异形齿形零件;复合冷挤压技术;挤压成形模具;模具优化;试验研究
内孔的上端(约从下凹模高度的1/2处起)设计
并加工成有角度驴的脱料斜度。目的取值以1。 ~2。,驴的取值以0.3。~O.0为宜,如图3所示。 (3)对于组合式凹模,在挤压成形过程中, 金属材料很容易流人上、下凹模的接缝内,久而 久之就会引起上凹模破裂或缺损,造成模具损 坏报废。为了防止该现象出现或减轻挤压时金 属材料流入上、下凹模接缝内的程度,须使上、 下凹模接触面的宽度不宜超过3 mm,一般以
4
模具加工
万方数据
模具技术2009.No.5 装配后的精度及要求。因此凹模加工时,需按 照以下要求进行: (1)上、下凹模先加工出相同尺寸的内孔, 然后穿在同1根芯轴上同时磨外圆,以保证两 者的同轴度要求以及有相同的轴向(径向)压装 过盈量。 (2)待上凹模与预应力圈压配好后,用高精 度线切割机床加工上凹模型腔达到尺寸等要 求。这里一定要注意:齿形的位置不能搞错,否 则将会严重影响到整个轮毂零件的后续加工。 然后将上凹模型腔的工作表面抛光并修圆。 (3)压出上凹模型腔,再将上、下凹模一起 压配入预应力圈。 (4)最后圆磨下凹模内孔达到尺寸等要求, 钳工加工下凹模入口处圆角并抛光。 (5)凹模材料一般选用较耐压、耐磨的合金 工具钢,如:Crl2MoV、65Ni等。 对轮毂零件复合挤压成形技术改进优化的 研究和分析,可以得出如下结论: (1)改进优化的复合挤压技术与模具结构, 使挤压成形压力降低20%~30%,从1 900~ 6
2~3 mm为宜。在接触面以外使上、下凹模的
拼接平面之间保持0.2~O.3 mm的缝隙,接触 面处进行抛光加工,且加工得越光越好。 2.2挤压凹模型腔优化设计
(a)原凸模
(b)改进优化后凸模
工件挤压成形时,金属材料在塑性变形的 同时,也存在着较大的弹性变形,且在成形工件 的不同部位,弹性变形量也有着一定的差异。
(a)原挤压工件 m)改进优化后工件
效的,可以应用在实际的生产加工中。图6所 示为冷挤压工件的三维简图。
图6冷挤压工件三维简图
结论
5挤压成形工艺试验
模具安装与调试步骤如下: (1)按照要求依次安装组成挤压成形凸模 和凹模的各个零件,并稍稍紧固紧固螺栓。 (2)调试挤压凸模、凹模和液压机,然后上、 下模合模使其找正,反复如此操作2~3次,最 后拧紧紧固螺栓。 (3)初始试验时采用手动操作,缓慢试压, 然后根据试验的进程和工件的成形状态来决定 是否继续。如一切正常,需要继续压下,则根据 成形件的形状与尺寸判断出进一步的压下量, 相应地减小限位块高度,继续试压。 (4)重复(3)中操作,直至成形工件达到要 求的形状尺寸。 (5)如轮毂成形工件的外形没达到所要求 的形状和尺寸,则可通过调整顶料杆的长度,即 轮毂成形工件柄部的长度来实现。当轮毂成形 工件齿形不饱满或长度不够时,则顶料杆长度 加长;相反,当盘毂成形工件齿形过长时,可将 顶料杆的长度缩短。 试验达到了预期的效果,挤压成形的轮毂 齿形完全达到了客户的要求,说明对轮毂的成 形工艺技术、模具及坯料的优化设计是合理有
kN。根据轮毂零件中心
部位有一≯22.8 mm通孔的特点,将挤压凸模优 化设计成中心有一≯20 mm的芯模,如图4所示。 采用此种优化结构的凸模有如下优点: (1)挤压成形时工件芯部的金属材料被部 分挤出而流向齿形处,因此增加了材料利用率, 节省了金属材料的消耗,降低了原材料成本。 对于组合式挤压成形凹模必须采用科学合 理的加工工艺,才能保证其加工精度(包括尺寸 和形位公差等精度要求),进而保证上、下凹模
轮毂零件复合挤压成形模具主要包括挤压 凹模和凸模,因此,模具的改进和优化也就包括
柄部表面拉伤,同时凹模的相应表面也容易粘 料,影响正常使用和模具寿命。为此,需要对凹 模进行一些改进优化。首先,在上凹模型腔的 上端(约从上凹模高度的1/3处起)沿周边设计
万方数据
36
Die and Mould Technology No.5 2009