PFMEA(1)
PFMEA(1)

PFMEA
12、严重度(Severity)
是指潜在失效模式对顾客的影响后果的严重程度的评价指标 严重度评估分为1~10级_对高严重度(9或10)应确定相应的 KCC 按最严重的后果进行严重度评分 只有改变设计才能降低严重度 不能低估现有严重度的可能性 13、分级 本栏目是用来对需要附加过程控制的零部件,子系统或系统 的一些特殊过程特性(KPC,KCC)进行分级的。 这些特性会影响到车辆操作安全,产品功能,符合政府规范 或客户满意度,且需要特殊制造。
PFMEA
• 案例分析
产品:门铰链总成 返修45分钟 产量:200,000件/年 工序:铣沉孔(工序库存20件)….安装门开关 失效模式:未加工 失效原因:铣刀断——4次/年 过程控制方法:更换铣刀——1次/1000件 止通规——1次/100件 后装配工序使用防错检测仪 S= 7 O= 3(PPM=4*20/200,000*106=400) D= 4 RPN= 84
新版更多的是理念的提升
PFMEA
• • • • 一、什么是FMEA FMEA:Failure Mode &Effect Analysis FMEA的中文:失效模式和后果分析 失效模式:是指制造过程无法达到预定或 规定的要求所表现出的现象;如:不合格 品、不良设备状况等; • 后果:指失效模式在客户处(包括下工序) 所造成的不良影响。
计意图的形式,是对某具体工序不符合要求的描述 典型的失效模式: 装配: 漏装/扭矩过小/断路/接地/上下颠倒/扭矩过大/短路/损坏 设备: 尺寸太大/尺寸超差/太深/太浅/偏离位置/粗糙/不圆
PFMEA
• 如何寻找失效模式?
人:操作工人、检验人员、物料人员 机:设备、工装、夹具、吊具、线体 料:零件、配件、紧固件、流程性材料 法:操作工艺、装配工艺、过程控制工艺 环:生产环境、储存环境 测:检测方法、检测要求、检测仪器设备
3阶段.PFMEA_1潜在失效模式及后果分析。失效模式风险顺序排列表

項目名稱 Project name: 過程責任部門 Process responsible Dept.: 車型年度/車 輛: Model Year/Vehicle
核心小組 Core team:
過程功能 Process Function
要求 Requirement
S6前灯支架
工程部
S6-6205450
核心小組 Core team:
過程功能 Process Function
要求 Requirement
S6前灯支架
工程部
S6-6205450
生产部/李胜
建;品质部/
冯厚荣,工程
部/张学
志,PMC部/范
永峰,
营业部/沈君雷,工模部/陈声波,体系推行/刘黎
潛在的 Potential
R. P. N.
來料检查
影响功能,性 材质用错 能下降,导致
客户退货
6
Ⅱ
供应商供料材质 出错,影响生产
4
IQC按受入检查 基准书和材质 证明书检查材
质
IQC按 AQL0.65检查 材料
5
120
IQC按受入检查 基准书和材质 证明书、正确 的样板检查材 质
按检查基准书、 IQC (2011- 材质证明书和样
潛在的 Potential
失效后果 Failure Result
嚴 重 度
分 级 (重 要程
(S) 度)
潛在失效 Potential Failure 起因/機理
Origin /Machanism
FMEA編號 FMEA No.:
20110630001
關鍵日期 Key date:
11.06.30
FMEA日期: FMEA date:
热处理PFMEA(1)
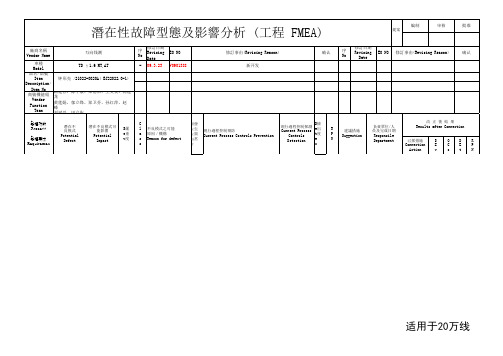
42
无
28
无
28
无
中频淬火后对 84 零件100%进行
在线涡流检测 中频淬火后对 84 零件100%进行 在线涡流检测
28
无
28
无
42
无
28
无
28
无
36
无
48
无
54
无
28
无
42
无
中频淬火后对 84 零件100%进行
在线涡流检测
28
无
改正後結果 Results after Correction
潛在性故障型態及影響分析 (工程 FMEA)
编制 提案
审核
批准
廠商名稱 Vendor Name
万向钱潮
車種 Model
TD γ1.6 MT,AT
品名/品號
Item
钟形壳 /21022-0020A( BJ22022.0-1)
Description/
Item No 商號機能組
Vendor Function
外喷流量偏小
1
·人工设定,程序监控 ·每2小时监控1次
感应器长度形状与工件 形状不匹配
2
感应器入库检验
加热时间不合理
·程序设定 3 ·首件确认合格后程序锁定
·每2小时监控1次过程参数
·程序设定
电压不合理
3 ·首件确认合格后程序锁定
·每2小时监控1次过程参数
屏蔽环位置不合理
2
·感应器入库检验 ·更换不同产品时进行调整
C l 不良模式之可能 a 原因/機構 s Reason for defect s
O發
c生 c異
現行過程控制預防 Current Process Controls Prevention
什么是PFMEA

什么是PFMEAPFMEA是过程失效模式及后果分析(ProcessFailureModeandEffectsAnalysis)的英文简称。
是由负责制造/装配的工程师/小组要紧采纳的一种分析技术,用以最大限度地保证各种潜在的失效模式及其相关的起因/机理已得到充分的考虑和论述。
失效:在条件下〔环境、操作、时刻〕,不能完成既定功能或产品参数值和不能维持在的上下限之间,以及在工作范围内导致零组件的破裂卡死等损坏现象。
严重度〔S〕:指一给定失效模式最严重的碍事后果的级不,是单一的FMEA范围内的相对定级结果。
严重度数值的落低只有通过设计更改或重新设计才能够实现。
频度〔O〕:指某一特定的起因/机理发生的可能发生,描述出现的可能性的级不数具有相对意义,但不是尽对的。
探测度〔D〕:指在零部件离开制造工序或装配之前,利用第二种现行过程操纵方法寻出失效起因/机理过程缺陷或后序发生的失效模式的可能性的评价指标;或者用第三种过程操纵方法寻出后序发生的失效模式的可能性的评价指标。
风险优先数〔RPN〕:指严重度数〔S〕和频度数〔O〕及不易探测度数〔D〕三项数字之乘积。
顾客:一般指“最终使用者〞,但也能够是随后或下游的制造或装配工序,维修工序或政府。
[编辑]PFMEA的分析原理PFMEA的分析原理如下表所示,它包括以下几个要害步骤:〔1〕确定与工艺生产或产品制造过程相关的潜在失效模式与起因;〔2〕评价失效对产品质量和顾客的潜在碍事;〔3〕寻出减少失效发生或失效条件的过程操纵变量,并制定纠正和预防措施;〔4〕编制潜在失效模式分级表,确保严重的失效模式得到优先操纵;〔5〕跟踪操纵措施的实施情况,更新失效模式分级表。
〔1〕“过程功能/要求〞:是指被分析的过程或工艺。
该过程或工艺能够是技术过程,如焊接、产品设计、软件代码编写等,也能够是治理过程,如方案编制、设计评审等。
尽可能简单地讲明该工艺过程或工序的目的,要是工艺过程包括许多具有不同失效模式的工序,那么能够把这些工序或要求作为独立过程列出;〔2〕“潜在的失效模式〞:是指过程可能发生的不满足过程要求或设计意图的形式或咨询题点,是对某具体工序不符合要求的描述。
众泰汽车涂装车间PFMEA(1)

4
在加工前 100%须在位置上返 工
4
影响后序喷涂、打磨量;影响 在加工前 100%须在位置上返
漆膜外观
工
4
在加工前 100%须在位置上返 工
4
在加工前 100%须在位置上返 工
4
补漆量少 漏底严重 油漆吐漆量不均匀 走抢移动不均匀 喷枪(油漆)压力不稳定 环境温度过低 涂料黏度过低 环境温度过高 涂料溶剂使用不当 流平时间过短 烘干炉内有颗粒等杂质 擦拭不净带有杂质颗粒
3 3 3 3 1 3 2 3 3 2 3
现行过程控制探测 目视
探测度D SOD
7
437
RPN
建议措施 (预防)
建议措施 (探测)
责任及目 标完成日
期
采取的 措施
S
84
目视
7
437
84
目视 膜厚仪侧量一般班3次 膜厚仪侧量一般班3次 膜厚仪侧量一般班3次 膜厚仪侧量一般班3次 膜厚仪侧量一般班3次 膜厚仪侧量一般班3次
在加工前 100%须在位置上返工
4
增加中涂打磨量;影响漆膜外观 质量
在加工前 100%须在位置上返工
4
过烘干
影响漆膜外观质量,造成返修严 重时将造成报废
对过程,操作或操作者的轻微不 便利
2
TZ4-07
中涂打磨
对喷完中涂漆后车身 颗粒、缩孔等缺陷进行处理、
擦净
无未烘干
强冷后车身温度:≤50℃
打磨不漏底 无颗粒存在
喷涂用的压缩空气含有水油物等有害物质 喷涂环境不清洁 涂装环境温度过高
涂料所用的溶剂不当 各道喷涂间隔时间不足
电泳打磨漏底盖不住 喷枪(油漆)压力小
油漆吐漆量小 走抢移动快 喷枪(油漆)压力小 油漆吐漆量小 机器人移动速度快 喷枪(油漆)压力小 油漆吐漆量大 走抢移动慢 喷枪距离近 走抢移动慢 涂料粘度过低 喷枪(油漆)压力小 油漆吐漆量大 环境空气清洁度差
DFMEA-PFMEA空白表(1)
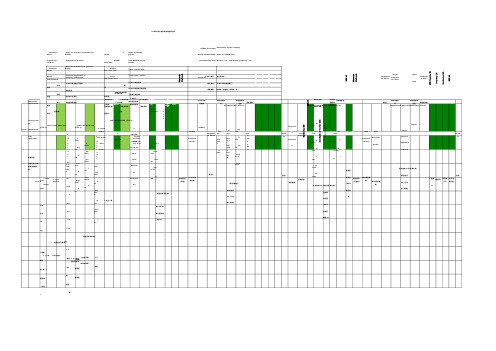
对FC和FM 现行探测控
der FU Frequency (F) of FC
筛选符号 (可选)
DetectionDFMEA编号 : 由 公 司 决 定 Action 设 计 责 任 : DFME A 所 有 者 的 部门 保密级别: 商务用,保密的,专利的,等
DFMEA探 测措施
目标完成时
采取措施的
失效影响
Responsib ile Person
Target Completio n on date
Taken with
Completio n Date
Pointer to Evidence
责任人
பைடு நூலகம்
目标完成时 间
采取措施的 完成的时间
证据
Supplemental MSR OPTIMIZATION (STEP 6)
Ta ken
wi th
Point er to
Evid ence
Com pl eti o n Da te
DFMEA预 防措施
责任人
优 化 (第 6步 ) 状 态 (进 行 中,已完 成,取消)
系统反应之
失效原 频率的原因
因的频
Supplem后e最nt严al重M的SR Risk Ana率ly(sFi)s(Stey 5) (F)
Name of customer(s) or [product family]
DFMEA Reversion Date
Latest revision date
Continuous Improvemen
Model Year/Platform
名称:
公司
位置:
工程
名称:
客户
产品喷印pfmea分析范例 (1)
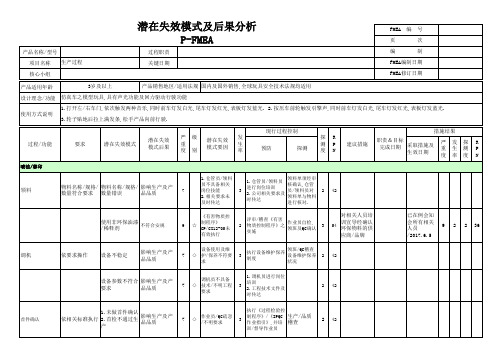
5
5
压力过高
3 调低压力
漆末过滤,有杂 物
3 油漆过滤干净
作业员业自 2 30
检,IPQC巡
检
2 30
5
喷具不洁
3 清洁喷具
2 30
渗色 露底色 泛白
影响生产及产 品品质
5
影响生产及产 品品质
5
5
影响生产及产 品品质
5
5
5
喷叠色时,底漆 末干就喷面漆
3
开油水挥发及干燥 作业员业自
时间控制
检,IPQC巡检
过程职责
关键日期
FMEA 编 号
页
次
编
制
FMEA编制日期
FMEA修订日期
产品适用年龄
3岁及以上
产品销售地区/适用法规 国内及国外销售,全球玩具安全技术法规均适用
设计理念/功能 仿真车之模型玩具,具有声光功能及回力驱动行驶功能
1.打开左/右车门,依次触发两种音乐,同时前车灯发白光,尾车灯发红光,表板灯发蓝光. 2.按压车前轮触发引擎声,同时前车灯发白光,尾车灯发红光,表板灯发蓝光. 使用方式说明
产品名称/型号 项目名称 生产过程 核心小组
潜在失效模式及后果分析 P-FMEA
过程职责
关键日期
FMEA 编 号
页
次
编
制
FMEA编制日期
FMEA修订日期
产品适用年龄
3岁及以上
产品销售地区/适用法规 国内及国外销售,全球玩具安全技术法规均适用
设计理念/功能 仿真车之模型玩具,具有声光功能及回力驱动行驶功能
领料单须经审 核确认,仓管 员/领料员对 领料单与物料 进行核对.
2
42
PFMEA模板(1)

Process FMEA InstructionsFMEA TemplateEnterprise Product Delivery Process2) All incoming parts and materials are correct and within specification..Example:RequirementsCorrectly assembled cover Surface finish-Proper orientationOutside diameter (+X inches)Example:Potential Failure ModesDiameter out of spec (Too large/Too small)Not flat, burred, tool wornDirtyCover looseIncorrect cover orientation Improper set upExamples:Potential EffectNoise, Leaks - air, oil, water Machine downVehicle control impaired Cannot fasten, mount, bore/tap Intermittent operation Poor appearanceLoss of function, output High operating efforts Customer dissatisfiedReduced performanceHow to Examples:Potential Cause/MechanismsImproper heat treat - time, temperature Improper torque-over, under Incorrect tooling Handling damageTool wornInaccurate gauging Inadequate or no lubrication Part missing or mislocated ContaminationImproper setupIncorrect feed/speedHow to Reduce: There are two types of design controls to consider: Prevention and Detection.Examples:Detection ControlsPreventative maintenance Operator training, experience Final Test stand/procedure Set up verificationMistake ProofingProduct audits TQC & Verify technique Operational Method Sheet Inspection - gages Mistake Proofing Process documentsMistake ProofingProcess auditsHow to Reduce:Detection ranking can be reduced by adding additional process controls to improve the detection or prevention of a defect.**Re-evaluation of RPN rankings should be done after the Recommended Actions have been completed.Prevention ControlsThe Occurrence ranking can be reduced by a process change to eliminate/ reduce the frequency of the cause from Prevention : Prevent the cause/mechanism of failure or the failure mode from occuring, or reduce their rate of occurrence.Detection : Detect the cause/mechanism of failure or the failure mode, and lead to corrective action.function.severity for the failure mode.Printed copies are uncontrolled and may not be current. All rights reserved by Deere Company under the copyright laws.1Updated: 15 SEPT 2003。
PFMEA编制模板[1]
![PFMEA编制模板[1]](https://img.taocdn.com/s3/m/9b0cf0f59e31433239689384.png)
未能符合安全和/或法规 没有预警情况下,潜在失效模式影响车辆安全操作和/或设计不符合政府法规 要求 有预警情况下,潜在失效模式影响车辆安全操作和/或设计不符合政府法规
失效符合安全和/或法 可能在没有预警下危害操作者(机械或装配) 规要求 可能在有预警下危害操作者(机械或装配)
6 宽度超差 维护成 品的完 毛刺过大 整 产品表面 带有刀印 无法使用 6 6 8:配刀 板形不良 6 6 6 表面质量不 良 6 6 B 垫片损坏 垫片不干净 垫片配错 剪刃间隙调 整不当 剪刃崩口 胶圈不良 胶圈用错 刀具重合量 过大
4#
现行设计 控制预防 16# 发生频 控制探测 度 16# 15#
过程FMEA编制指南 ××××××公司PFMEA(示例)
FMEA 编号: 项目名称: 型号年/项目: 1# 2# 5# 过程责任 :
3#
编制者: ××× 7# 4#
页码: 关键日期: FMEA日期(修订)
第
页,共
页 6# 7#
FMEA日期(原始):
核心小组 : ×××、×××、×××、××× 过程步骤 要求 9# 功能 9#
后果 标准 对产品的后果严重度
级别 10
后果
标准 对过程的后果严重度(制造/装配后果)
9 大规模中断 100%的产品是废品。流水线停止或停止出货 8 基本功能的损失或降级 生产运转一定会产生部分废品。背离最初过程包括流水线速度降低 基本功能损失(车辆可操作,但降低了功能的等级) 显著中断 7 和增加 舒适功能损失(车辆可操作,但舒适/便利功能损失) 100%需脱线返工,是被承认的 6 舒适功能的损失或降级 一般 舒适功能降级(车辆可操作,但舒适/便利功能降级) 部分需脱线返工,是被承认的 5 外观或听见噪音,车辆可操作,不符合项被大部分顾客注意到(>75%) 在加工前100%须在位置上返工 4 一般中断 令人不舒服的项目 外观或听见噪音,车辆可操作,不符合项被很多顾客注意到(50%) 在加工前部分须在位置上返工 3 外观或听见噪音,车辆可操作,不符合项被有辨别能力的顾客注意到(<25%) 微小中断 过程,操作或操作者的轻微不便利 2 没有影响 没有可辨别的后果 没有后果 没有可辨别的后果 1 13#级别:本栏目是用来对需要附加过程控制的零部件、子系统或系统的一些特殊过程特性进行分级的(如关键、主要、重要、重点等)。如果在过程FMEA中确定了某一 失效发生的可能性 准则:PFMEA要因发生率(事件每项目/车辆) 频度 非常高 ≥100次每1000个 或 ≥1次每10辆中 10 50次每1000个 或 1次每20辆中 9 高 20次每1000个 或 1次每50辆中 8 10次每1000个 或 1次每100辆中 7 2次每1000个 或 1次每500辆中 6 一般 0.5次每1000个 或 1次每2000辆中 5 0.1次每1000个 或 1次每10,000辆中 4 0.01次每1000个 或 1次每100,000辆中 3 低 ≤0.001次每1000个 或 1次每1,000,000辆中 2 非常低 失效通过预防控制消除了 1 16#现行过程控制:现行的过程控制是对尽可能阻止失效模式的发生,或者探测将发生的失效模式的控制的描述。 控制预防是消除(预防)失效的要因的发生或失效模式的发生,或降低发生率。 探测机会 评价准则:过程控制探测的可能性 探测度 探测可能性 没有探测机会 没有现有控制,不能探测或不能解析 10 几乎不可能 在任何阶段不太可能探测 失效模式或错误(要因)不容易探测(如:随机检查) 9 非常微小 加工后问题探测 操作者通过目测/排列/耳听法的/事后后失效模式探测 8 微小 开始时问题探测 操作者通过直观/目测/排列/耳听法在位置上做失效模式探测或操作者通过使用特性测量(行/不行、手动转矩检查 7 非常低 加工后问题探测 操作者通过使用变量测量或操作者在位置上做失效模式探测或操作者通过使用特性测量(行/不行、手动转矩检查 6 低 开始时问题探测 操作者在位置上使用变量测量或通过位置上的自动控制探测差异零件和通知操作者(光、杂音等)。在设置上或首 5 一般 加工后问题探测 由自动控制探测变异零件并锁住零件,预防进一步加工的事后失效模式探测。 4 一般高 开始时问题探测 由自动控制在位置上探测变异零件并在位置上自动锁住零件,预防进一步加工的失效模式探测。 3 高
PFMEA范本正规范本(通用版)

PFMEA范本1. 引言失败模式与影响分析(PFMEA)是一种用于检测和预防潜在问题的方法。
它通过分析产品或过程中的潜在故障模式、故障影响和故障严重性,帮助提前采取措施减少问题的发生。
本文档提供了一个PFMEA的范本,以便团队可以使用此模板进行分析和记录潜在问题。
2. 格式与使用方法本PFMEA范本按照格式进行组织:2.1 项目信息提供项目的基本信息,如项目名称、负责人、版本号等。
2.2 风险辨识列出可能导致故障的潜在因素和原因,同时对其进行分类和排序。
2.3 故障模式描述每个风险因素可能导致的具体故障模式或缺陷。
2.4 故障影响分析每个故障模式的影响范围,包括对产品质量、安全性和可靠性的影响。
2.5 故障严重性评估根据故障影响的严重性,对每个故障模式进行评估,并确定其优先级。
2.6 预防措施针对每个故障模式,提供相应的预防措施,以减少其发生的可能性。
2.7 控制措施对于无法完全防止的故障模式,提供相应的控制措施,以减小其影响范围。
3. 范例PFMEA3.1 项目信息•项目名称:产品X生产工艺改进•负责人:•版本号:1.03.2 风险辨识风险因素分类排序原料质量不稳定供应商1设备故障设备2操作员疏忽人为33.3 故障模式3.3.1 原料质量不稳定•故障模式:原料含有杂质•缺陷描述:产品表面出现颗粒 3.3.2 设备故障•故障模式:机器断电•缺陷描述:生产线停止运行 3.3.3 操作员疏忽•故障模式:操作员忘记更换材料•缺陷描述:产品成分错误3.4 故障影响3.4.1 原料质量不稳定•产品质量:严重影响•安全性:轻微影响•可靠性:中度影响 3.4.2 设备故障•产品质量:严重影响•安全性:中度影响•可靠性:严重影响 3.4.3 操作员疏忽•产品质量:轻微影响•安全性:轻微影响•可靠性:轻微影响3.5 故障严重性评估3.5.1 原料质量不稳定•评分:高 3.5.2 设备故障•评分:中 3.5.3 操作员疏忽•评分:低3.6 预防措施3.6.1 原料质量不稳定•改进供应商质量管理系统•增加原料检测流程•优化原料储存条件 3.6.2 设备故障•定期维护设备•安装备用电源系统•增加设备监控系统 3.6.3 操作员疏忽•提供操作指南•提供培训计划•引入二次确认机制3.7 控制措施3.7.1 原料质量不稳定•增加终端产品检测环节•增加产品外包装检查 3.7.2 设备故障•设置备用设备•设备故障发生时及时进行维修 3.7.3 操作员疏忽•设置自动化报警系统•引入质量管理人员监督4. 结论PFMEA是一种重要的工具,可以帮助团队识别潜在的问题并采取相应的措施来降低风险。
潜在失效模式分析(PFMEA)样板-1
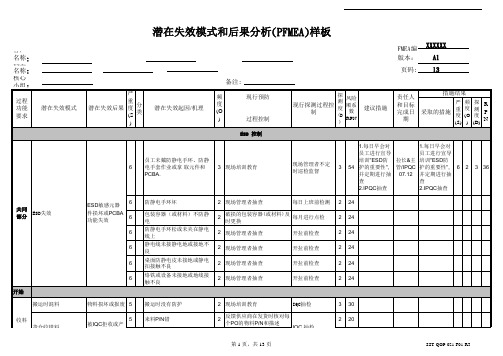
1.不同的Model 之间有相似 的的钢网设计 2.钢网上的P/N标示错误或没 标示 1.印刷速度或刮刀压力设置 不当 2.钢网孔堵塞或漏开孔 3.刮刀两边红胶收拢不及时 4.PCB板表面清洁度不够 5.红胶开封时间太长或过期 1.印刷速度或刮刀压力设置 不当 2.红胶开封时间太长或过期 3.印刷偏移位 1.钢网孔偏位 2.程序设定偏位
1.定期培训员 工"电子元件 基础知识"并 实践考核 2.每站物料上 6 线时依BOM 描述需要测量 其阻容值并记 PIE 录 /操作员 3.开线换线后 Dec-07 由技术员确认 所有方向性器 件的"方向标 示"并贴装首 6 件确认 4.换料时由两 人互检确认 5.IPQC 抽验
2
3 36
2
3 36
2
3 36
共同 ESD失效 部分
ESD敏感元器 件损坏或PCBA 功能失效
6 6 6 6 6 6
防静电手环坏 包装容器(或材料)不防静 电 防静电手环松或未夹在静电 线上 静电线未接静电地或接地不 良 桌面防静电皮未接地或静电 扣接触不良 烙铁或设备未接地或地线接 触不良
2 现场管理者抽查 2
每日上班前检测
潜在失效模式和后果分析(PFMEA)样板 样板 潜在失效模式和后果分析
FMEA编号: XXXXXX 客户名称: 机型名称: 核心小组:
严 重 分 潜在失效后果 度 类 (S ) 频 度 (O )
XXXXXX XXXXXX
过程责任部门:SMT&MI&TEST
编制者:
版本: 页码:
A1 13
备注:
现行预防
2 2 2 2 2 2
破损的包装容器(或材料)及 每月进行点检 时更换 开拉前检查
PFMEA复习大纲1
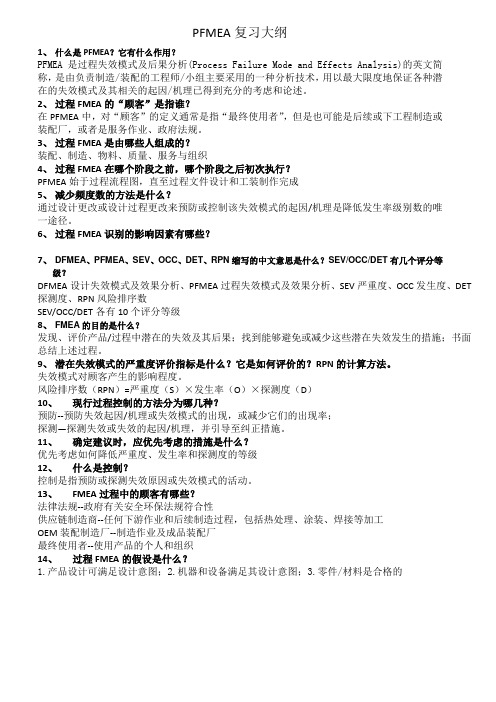
PFMEA复习大纲1、什么是PFMEA?它有什么作用?PFMEA是过程失效模式及后果分析(Process Failure Mode and Effects Analysis)的英文简称,是由负责制造/装配的工程师/小组主要采用的一种分析技术,用以最大限度地保证各种潜在的失效模式及其相关的起因/机理已得到充分的考虑和论述。
2、过程FMEA的“顾客”是指谁?在PFMEA中,对“顾客”的定义通常是指“最终使用者”,但是也可能是后续或下工程制造或装配厂,或者是服务作业、政府法规。
3、过程FMEA是由哪些人组成的?装配、制造、物料、质量、服务与组织4、过程FMEA在哪个阶段之前,哪个阶段之后初次执行?PFMEA始于过程流程图,直至过程文件设计和工装制作完成5、减少频度数的方法是什么?通过设计更改或设计过程更改来预防或控制该失效模式的起因/机理是降低发生率级别数的唯一途径。
6、过程FMEA识别的影响因素有哪些?7、DFMEA、PFMEA、SEV、OCC、DET、RPN缩写的中文意思是什么?SEV/OCC/DET有几个评分等级?DFMEA设计失效模式及效果分析、PFMEA过程失效模式及效果分析、SEV严重度、OCC发生度、DET 探测度、RPN风险排序数SEV/OCC/DET各有10个评分等级8、FMEA的目的是什么?发现、评价产品/过程中潜在的失效及其后果;找到能够避免或减少这些潜在失效发生的措施;书面总结上述过程。
9、潜在失效模式的严重度评价指标是什么?它是如何评价的?RPN的计算方法。
失效模式对顾客产生的影响程度。
风险排序数(RPN)=严重度(S)×发生率(O)×探测度(D)10、现行过程控制的方法分为哪几种?预防--预防失效起因/机理或失效模式的出现,或减少它们的出现率;探测—探测失效或失效的起因/机理,并引导至纠正措施。
11、确定建议时,应优先考虑的措施是什么?优先考虑如何降低严重度、发生率和探测度的等级12、什么是控制?控制是指预防或探测失效原因或失效模式的活动。
PFMEA1
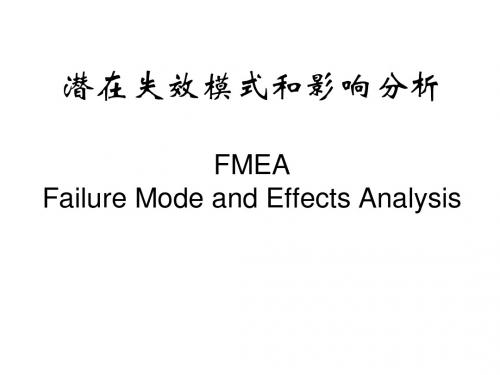
应用FMEA的三种情况:
• 新设计,新技术或新过程 • 对现有设计和过程的更改 • 在新的环境、场所、应用或使用形式下,使用现 有的设计和过程;
5
第一章
管理者的影响:
FMEA通用指南
• 高层管理者应承诺对小组进行支持,包括足够 的时间和必需的资源; • 必要时,要给小组适当的授权; • 管理者有开发和维护FMEA的责任 --FMEA是一个永不停止、相互作用的持 续改进的过程
9
第三章 过程失效模式和影响分析
P-FMEA
10
第三章
简介
识别并评估过程功能和要求
PFMEA
识别并评估产品和过程潜在失效模式
评价失效对顾客的潜在影响 识别风险,建立过程改进的优先顺序系统
11
第三章
PFMEA的 “动态”
• • • • • •
PFMEA
可行性论证阶段或之前开始PFMEA 生产设备工装之前开始PFMEA 考虑从单个零件到总成的所有制造操作/工序 包括所有影响制造操作的过程(如物流、接收) 批量试生产开始之前,基本完成PFMEA 量产后继续接收反馈信息,评估新的失效模式或 已改变的风险,持续更新
6
第二章
基本结构
FMEA的策划、实施
• 手册推荐的FMEA表格用于整理、收集相关信息, 使用时可以根据组织和顾客要求而变化;
建立小组
• 典型的FMEA小组可以由开发、制造、质量等部门 的工程技术人员组成; • 小组领导人应挑选有丰富经验、具备必要专业知 识的小组成员;
7
第二章
定义范围
FMEA的策划、实施
• 建立FMEA分析边界,明确要评估的内容是什么: 系统FMEA--如:计算机总成 子系统FMEA-如:主板 零部件FMEA-如:散热片 必需考虑系统与子系统、子系统与零部件之间的 接口,尤其是与顾客的接口;
FMEA百度百科
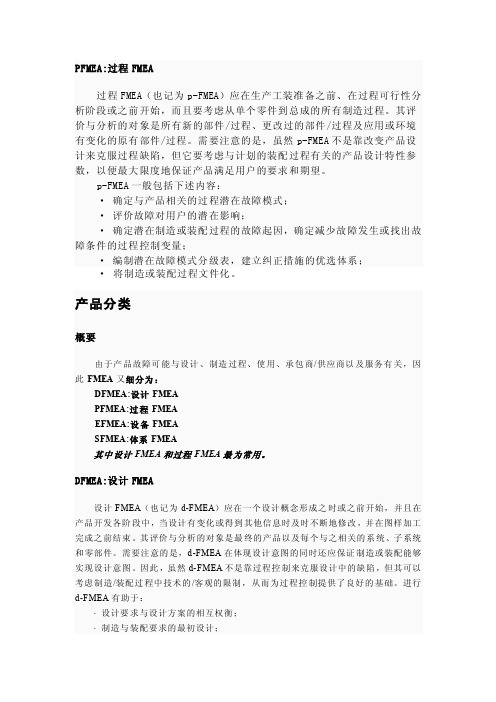
PFMEA:过程FMEA过程FMEA(也记为p-FMEA)应在生产工装准备之前、在过程可行性分析阶段或之前开始,而且要考虑从单个零件到总成的所有制造过程。
其评价与分析的对象是所有新的部件/过程、更改过的部件/过程及应用或环境有变化的原有部件/过程。
需要注意的是,虽然p-FMEA不是靠改变产品设计来克服过程缺陷,但它要考虑与计划的装配过程有关的产品设计特性参数,以便最大限度地保证产品满足用户的要求和期望。
p-FMEA一般包括下述内容:· 确定与产品相关的过程潜在故障模式;· 评价故障对用户的潜在影响;· 确定潜在制造或装配过程的故障起因,确定减少故障发生或找出故障条件的过程控制变量;· 编制潜在故障模式分级表,建立纠正措施的优选体系;· 将制造或装配过程文件化。
产品分类概要由于产品故障可能与设计、制造过程、使用、承包商/供应商以及服务有关,因此FMEA又细分为:DFMEA:设计FMEAPFMEA:过程FMEAEFMEA:设备FMEASFMEA:体系FMEA其中设计FMEA和过程FMEA最为常用。
DFMEA:设计FMEA设计FMEA(也记为d-FMEA)应在一个设计概念形成之时或之前开始,并且在产品开发各阶段中,当设计有变化或得到其他信息时及时不断地修改,并在图样加工完成之前结束。
其评价与分析的对象是最终的产品以及每个与之相关的系统、子系统和零部件。
需要注意的是,d-FMEA在体现设计意图的同时还应保证制造或装配能够实现设计意图。
因此,虽然d-FMEA不是靠过程控制来克服设计中的缺陷,但其可以考虑制造/装配过程中技术的/客观的限制,从而为过程控制提供了良好的基础。
进行d-FMEA有助于:·设计要求与设计方案的相互权衡;·制造与装配要求的最初设计;·提高在设计/开发过程中考虑潜在故障模式及其对系统和产品影响的可能性;·为制定全面、有效的设计试验计划和开发项目提供更多的信息;·建立一套改进设计和开发试验的优先控制系统;·为将来分析研究现场情况、评价设计的更改以及开发更先进的设计提供参考。
关于PFEMA

关于PFMEA
PFMEA:过程潜在失效模式及其后果分析。
1、序列,指的是工序号,要与流程图一一对应。
2、过程功能,就是所有工序的名称。
3、潜在失效模式,造成产品失效的所有可能的原因,但一定要具体化,如:尺寸大,尺寸小-----------
4、潜在失效模式的影响,与上一条相对应,逐一列出。
5、严重度(1---10),就是失效模式影响的产品功能或性能程度的大小。
其只有在设计更改是才可能降低。
6、分类,就是对失效模式类型的划分,共分为:安全特性、关键特性和关键尺寸。
7、潜在原因/失效几率,对人、机、料、法、环进行综合分析。
8、频度,就是统计产生失效模式的机率。
9、预防,相对于已经使用的措施,防误:做工装,调配;防错:是在设计的时候考虑到并加以控制。
10、探测,相当于检验,识别。
11、探测度(1---10),就是检验的精确度(可以靠更改检测设备及方法来实现),如果能100%检出,其不可探测度为1。
12、风险顺序数,就是严重度、频度及探测度的乘积,如果其大于等于80的话,一定要重新对此失效模式进行分析,并提出可行的措施;如果当严重度大于等于9的时候,同样也必须采取措施。
13、建议措施,就是上述为了杜绝此类失效模式所提的对策(需要经过验证的)。
这是一份动态的文件,在建议措施验证后,就需要更新此文件,并把此建议措施更新到预防里面;或者在生产过程中人、机、料、法、环的某一环节的改变同时也要更新此文件。
关于PFEMA含义

关于PFMEA
PFMEA:过程潜在失效模式及其后果分析。
1、序列,指的是工序号,要与流程图一一对应。
2、过程功能,就是所有工序的名称。
3、潜在失效模式,造成产品失效的所有可能的原因,但一定要具体化,如:尺寸大,尺寸小-----------
4、潜在失效模式的影响,与上一条相对应,逐一列出。
5、严重度(1---10),就是失效模式影响的产品功能或性能程度的大小。
其只有在设计更改是才可能降低。
6、分类,就是对失效模式类型的划分,共分为:安全特性、关键特性和关键尺寸。
7、潜在原因/失效几率,对人、机、料、法、环进行综合分析。
8、频度,就是统计产生失效模式的机率。
9、预防,相对于已经使用的措施,防误:做工装,调配;防错:是在设计的时候考虑到并加以控制。
10、探测,相当于检验,识别。
11、探测度(1---10),就是检验的精确度(可以靠更改检测设备及方法来实现),如果能100%检出,其不可探测度为1。
12、风险顺序数,就是严重度、频度及探测度的乘积,如果其大于等于80的话,一定要重新对此失效模式进行分析,并提出可行的措施;如果当严重度大于等于9的时候,同样也必须采取措施。
13、建议措施,就是上述为了杜绝此类失效模式所提的对策(需要经过验证的)。
这是一份动态的文件,在建议措施验证后,就需要更新此文件,并把此建议措施更新到预防里面;或者在生产过程中人、机、料、法、环的某一环节的改变同时也要更新此文件。
塑胶产品易开裂物料 PFMEA 模板-(1

清理完成后技术员对清理工 作确认,用无尘布擦拭,无 脏污即可(详见换料作业指
导书进行作业) 技术员开机前对材料进行核 对确认是否按照规范做业。
技术员对加料人员设定的干 燥温度及时间进行确认,选
用设备进行确认.
材料在炮筒停留时间适 当,生产出外观、功能 合格的产品
成型机台与实际零件重量不匹 配,导致材料降解
7 材料在炮筒停留时间过长
成型周期设置不合理,导致生产 7 材料在炮筒停留时间过长 周期过长,导致材料降解
生产设备性能稳定可 靠,产品一致性好,支 持批量生产
螺杆磨损造成储料不稳定或驱动 曲臂磨损造成锁模不稳定,机台 稳定性差,产品一致性不好,可 能出现小概率的不良品
8
注塑机台维护不到位
模温符合理、正确,生 实测多点模温偏低,导致熔接线 8 实测模具温度不够高,致零件内
产出外观、功能合格的 位置强度下降、开裂
应力偏大
产品
注塑压力合理、正确, 注塑压力过大,使产品内应力大 8 注塑压力过大
生产出外观、功能合格
的产品
速度过快会导致材料温度上升而 8 小浇口情况下,注塑速度过快
5
设备维护不到位
生产前5模样品需废弃, 生产前10模内注塑机参数还不稳 5 生产过程控制不完善
10模后注塑趋于稳定, 定,产品一致性不好,不良率高
产品一致性好
8 零件清洗工艺缺失、或不彻底 金属镶件有油污,跟塑胶材料不
兼容
清洗外观、油污的溶剂跟塑胶材 8 清洗剂选择错误 料不兼容
8 模具上模前保养不规范 顶针油、润滑油等模具用油接触
过大,导致材料降解;背压过 小,导致熔胶内气体量过大,材 料易局部降解,产品易产生气 泡,开裂。
PFMEA范本(1范本)

PFMEA范本1. 引言PFMEA(Potential Flure Mode and EffectsAnalysis)是一种系统性的分析方法,旨在识别潜在的故障模式及其对产品或过程造成的影响。
该方法有助于在设计或制造阶段识别并消除潜在的故障,以确保产品或过程的可靠性和质量。
2. 制定目的编制PFMEA的目的是对产品或过程进行全面而系统性的风险分析,以便识别所有潜在故障模式及其对产品或过程的影响。
通过识别和评估潜在的故障模式,可以采取适当的措施来降低风险并提高产品或过程的可靠性。
3. 范围本范本适用于所有产品或过程的PFMEA编制。
它可以用作指导编制PFMEA的模板,以确保对每个潜在故障模式都进行了全面的分析和评估。
4. 编制步骤4.1 选取团队成员编制PFMEA需要一个多学科的团队,团队成员应包括设计工程师、制造工程师、质量工程师和相关领域的专家。
4.2 制定团队任务和责任确定每个团队成员的任务和责任,并确保每个成员都理解并承担起自己的责任。
4.3 识别潜在故障模式对产品或过程进行彻底的分析,识别可能的故障模式。
可以通过技术手册、数据分析、过程流程图等方式进行故障模式的识别。
4.4 评估潜在故障影响评估每个潜在故障模式对产品或过程的影响程度。
可以使用风险矩阵来标识不同风险级别,并将每个故障模式放置在相应的风险级别中。
4.5 评估现有控制措施评估当前已实施的控制措施,例如设计控制、过程控制和检验控制等。
确定这些控制措施对潜在故障模式的效果。
4.6 识别和实施改进措施根据评估结果,识别需要改进的控制措施。
制定并实施相应的改进计划,以减少潜在故障模式及其影响的风险。
4.7 更新PFMEA根据实施的措施和改进计划,更新PFMEA,并确保所有潜在故障模式都得到了全面的分析和评估。
5. 结论使用本PFMEA范本作为指导,可以确保对产品或过程的潜在故障模式进行全面和系统的分析。
通过识别潜在故障模式,并采取适当的控制措施,可以降低风险并提高产品或过程的可靠性和质量。
PFMEA分级与制程质量控制计划说明
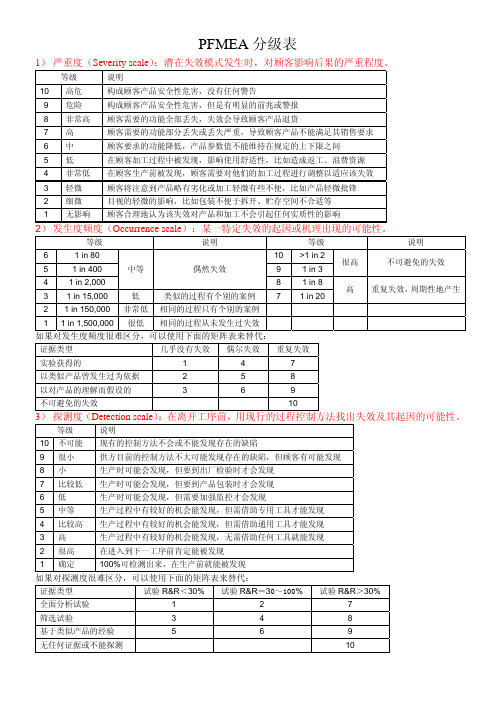
PFMEA分级表1)严重度(Severity scale):潜在失效模式发生时,对顾客影响后果的严重程度。
等级说明10 高危构成顾客产品安全性危害,没有任何警告9 危险构成顾客产品安全性危害,但是有明显的前兆或警报8 非常高顾客需要的功能全部丢失,失效会导致顾客产品退货7 高顾客需要的功能部分丢失或丢失严重,导致顾客产品不能满足其销售要求6 中顾客要求的功能降低,产品参数值不能维持在规定的上下限之间5 低在顾客加工过程中被发现,影响使用舒适性,比如造成返工、浪费资源4 非常低在顾客生产前被发现,顾客需要对他们的加工过程进行调整以适应该失效3 轻微顾客将注意到产品略有劣化或加工轻微有些不便,比如产品轻微批锋2 细微目视的轻微的影响,比如包装不便于拆开、贮存空间不合适等1 无影响顾客合理地认为该失效对产品和加工不会引起任何实质性的影响2)发生度频度(Occurrence scale):某一特定失效的起因或机理出现的可能性。
等级说明等级说明6 1 in 80中等偶然失效10 >1 in 2很高不可避免的失效5 1 in 400 9 1 in 34 1 in 2,000 8 1 in 8高重复失效,周期性地产生3 1 in 15,000 低类似的过程有个别的案例7 1 in 202 1 in 150,000 非常低相同的过程只有个别的案例1 1 in 1,500,000 很低相同的过程从未发生过失效如果对发生度频度很难区分,可以使用下面的矩阵表来替代:证据类型几乎没有失效偶尔失效重复失效实验获得的 1 47以类似产品曾发生过为依据 2 58以对产品的理解而假设的 3 69不可避免的失效103)探测度(Detection scale):在离开工序前,用现行的过程控制方法找出失效及其起因的可能性。
等级说明10 不可能现有的控制方法不会或不能发现存在的缺陷9 很小供方目前的控制方法不大可能发现存在的缺陷,但顾客有可能发现8 小生产时可能会发现,但要到出厂检验时才会发现7 比较低生产时可能会发现,但要到产品包装时才会发现6 低生产时可能会发现,但需要加强监控才会发现5 中等生产过程中有较好的机会能发现,但需借助专用工具才能发现4 比较高生产过程中有较好的机会能发现,但需借助通用工具才能发现3 高生产过程中有较好的机会能发现,无需借助任何工具就能发现2 很高在进入到下一工序前肯定能被发现1 确定 100%可检测出来,在生产前就能被发现如果对探测度很难区分,可以使用下面的矩阵表来替代:证据类型试验R&R<30% 试验R&R=30~100% 试验R&R>30%全面分析试验 1 2 7筛选试验 3 4 8基于类似产品的经验 5 6 9无任何证据或不能探测10制程质量控制计划说明1)自检频率:作业前所有项目均需自检合格才能生产,除此之外,作业者需要在作业时额外增加的自我检验项目或需要特别注意的项目;2)首检:首件送样检验的简称,是指除人为因素以外的特性(比如由模具和设备确定的特性),需要在生产首件后送检确认一次,防止错误使用模具或错误设置设备参数而造成批量的不合格事故)3)巡检频率:应选择最适合或是尽早能发现问题的时间来进行PQC检查(比如:对于物料规格的确认,应尽可能在作业之前;对于设备参数的设定,应尽可能在作业初始等)。
PFMEA是如何减少制造过程中的错误的?

PFMEA是如何减少制造过程中的错误的?在制造业中,任何一个小错误都可能导致巨大的损失,不仅影响产品质量,还会损害企业的声誉和经济效益。
为了预防和减少这些错误,许多企业都引入了过程失效模式与影响分析(PFMEA)这一强大工具。
那么,PFMEA究竟是如何助力制造业减少错误的呢?天行健Six Sigma 咨询公司解析如下:一、PFMEA的基本概念PFMEA是一种预防性的质量工具,它通过对产品或过程中潜在的失效模式进行识别、评估和控制,从而达到减少错误、提高产品质量的目的。
PFMEA强调在产品设计或生产过程之初就进行预防,而不是等问题出现后再去解决。
二、PFMEA减少制造错误的三大步骤识别潜在的失效模式:PFMEA的第一步是对产品或过程进行全面的分析,找出所有可能出现的失效模式。
这包括对产品结构的理解、对生产工艺流程的梳理以及对历史错误数据的分析。
通过这一步骤,企业能够清晰地认识到生产过程中可能遇到的问题,为后续的预防和控制工作打下基础。
评估失效模式的影响和严重度:识别出失效模式后,PFMEA要求对这些失效模式可能产生的影响进行评估。
这包括对产品质量、客户满意度、生产成本等多个方面的考量。
通过对失效模式的影响进行量化评估,企业可以更加明确哪些错误是必须要避免的,哪些错误是可以通过一定的措施来减少的。
制定预防措施和行动计划:针对识别出的失效模式和评估出的影响程度,PFMEA要求企业制定相应的预防措施和行动计划。
这些措施可以包括改进生产工艺、优化产品设计、加强员工培训等多个方面。
通过实施这些措施,企业可以在生产过程中有效减少错误的发生,提高产品质量和生产效率。
三、PFMEA在制造业中的实际应用在实际应用中,PFMEA被广泛应用于制造业的各个环节。
例如,在汽车制造业中,PFMEA被用于发动机、底盘、车身等各个部件的生产过程中,有效预防了潜在的质量问题。
在电子产品制造业中,PFMEA 则帮助企业在电路设计、组装工艺等方面减少错误,提高了产品的可靠性和稳定性。
- 1、下载文档前请自行甄别文档内容的完整性,平台不提供额外的编辑、内容补充、找答案等附加服务。
- 2、"仅部分预览"的文档,不可在线预览部分如存在完整性等问题,可反馈申请退款(可完整预览的文档不适用该条件!)。
- 3、如文档侵犯您的权益,请联系客服反馈,我们会尽快为您处理(人工客服工作时间:9:00-18:30)。
FMEA日期(编制): 现行过程控制
频度 (O) 2 2 2 2 2 2 2 2 2 2 2 2 2 2 2 2 2 3 2 3 2 3 3 2 2 3 4 3 3 3 2 3 3 3 3 3 品管首检、巡检 巡检 巡检 QC首检 QC 检查并记录分散时间 4小时无条件更换筛网,发 现筛网破裂立即更换 定期检查筛网或刀口 粘度计检测,1次/每桶 真空过筛前QC检查 出浆料前测量浆料温度 配料前检查机器,发现漏油停 机修理 QC检查 QC检查搅拌速度 QC检查搅拌时间 100%筛料 机器设定 规范操作 浆料过滤;发现阻塞立即清除 用除铁棒除铁 4小时无条件更换筛网,发 现筛网破裂立即更换 每班巡检 QC 检查并记录分散时间 机器设定 QC检查 QC检查搅拌时间和速度 记录并控制浆料的配料及转交 时间 正确使用筛网,规范操作 机器设定 放在专用的干燥木板上 加盖阀置 PQC全过程临控 PQC监控称量全过程 风险顺 责 序数 探测度 (S*O*D 建议措施 任 (D) ) 2 2 2 2 2 2 2 2 2 2 2 2 2 2 2 3 4 2 2 3 1 2 2 3 2 3 5 3 2 2 2 2 2 2 2 2 28 28 28 28 28 28 28 28 28 28 28 20 28 28 28 42 56 36 20 45 10 30 18 42 24 63 140 63 42 42 28 42 42 42 42 42
项目
功能
潜在失效模式 后果
活性物质加入量过多 活性物质加入量过少 固含量高,影响拉浆厚度, 敷料性能变差,循环性能差 电池容量低,影响电池出 货,导致客户投诉 电池容量低,影响电池出 货,导致客户投诉 电池内阻大,大电流放电性 能差,导致客户投诉 放电平台下降,大电流放电 性能差 极片敷料粘接不牢,影响短 路及自放电,电池循环性能 差 浆料偏稀或偏稠,影响固含 量和拉浆厚度 浆料内有颗粒,电池内阻 高,自放电及大电流放电性 能差 浆料不均匀,影响拉浆厚 度,电池一致性不好
文件名称: 文件编号: 版本: 1
项目编号: 页码:
F08014 13
文件发行/修订履历
版本
1
日期
ECN编号
\
修改内容
修改/创建人
潜在失效模式及后果分析(PFMEA)
电池型号: 项目名称: 核心小组: 编号 1 2 3 4 5 6 7 8 9 10 11 12 13 14 15 16 17 18 19 20 21 22 23 24 25 26 27 28 29 30 31 32 33 34 35 36
7 7 7 7 7 7 7 7 6 6 6 8 8 拉浆断料 敷不上料 6 6 管道无料输出 输料泵气压不稳 生产泵故障 浆料从管道接口渗出 管道内有颗粒状的结晶 浆料中混有管道中脱落 的铁杂质 铝箔断裂 敷不上料 出料速度不稳定 不能输料 不能输料 敷料厚度不均匀 电池短路 不能生产 6 6 6 6 6 7 7 10 6 8 8 8 6 6 6 10 7 7 7 ★ 7 7 7 影响电池性能 影响电池性能 电池短路 极片报废 6 6 10 7 7 10 10 10 ◇ ◇ ★ ★ ◇
4 2 2 3 3 2 2 2 2 4 2 2 2 2 2 3 3 1 1 1 2 2 1 2 2 2 2 2 2 2 2 4 5 3 2 2 2 2 2 2 3 3 2 2 1 2 2 1 2 2 3 3 2 2 1 2 2 1 2 2 2 2 2 2 3 3 2 2
修磨或擦试 擦试 调整 QC检查:收卷直径不能超 过指定值 使用前校准,过程中调整 机械配合保障线速度一致 采用合式料盘和搅拌器 首检、巡检 首检、巡检 清理和擦试 首检、巡检 首检、巡检 首检、巡检 首检、巡检 首检、巡检 首检、巡检 首检、巡检 定期维护 定期维护 定期维护 调节气压阀 采用合式料盘 调节流量阀 调节气压阀 规定气压范围 调节流量阀 规定气压范围 规定气压范围 定期维护和清洗 定期维护,更换 首检、巡检 首检、巡检 首检、巡检 备用泵 定期维护,更换 定期清洗和更换 加筛网 首检、巡检 加保温层 定期检修 定期检修 全检极片重量 实时监控 定期检修 定期检修 QC全过程监控 QC监测环境粉尘含量 首检、巡检 首检、巡检 检查辊轮 首检极片厚度,QC抽检控 制图 首检极片厚度,QC抽检控 制图 首检 首检 QC全过程监控 QC监测环境粉尘含量 首检、巡检 清洗 调节 调节 调节 规定速度范围 规定转交时间和监控湿度 转移极片用专用小车 增加保护盖 换刀 操作员自检 QC全过程监控 不良品挑出报废 首检、巡检 QC首检,检验极片 首检 首检 首检 首检 首检确认 规定滚刀转速 定期换刀 定期检修 定期维护 调节和更换切刀 定期维护 培训员工规范操作,品管再确 认 换刀 操作员自检 QC全过程监控 不良品挑出报废 首检、巡检 QC首检,检验极片 首检 首检 首检 首检 首检确认 巡检 巡检 巡检 巡检 员工全检 设备定期维护/品管首检 设备维护 定期清扫 操作员自检极片,QC抽检 定期清扫 规定滚刀转速 定期换刀 定期检修 定期维护 调节和更换刀 定期维护 培训员工规范操作,品管再确 认 规定转交时间和监控湿度 转移极片用专用小拉车 增加保护盖
划线位置错位 极片不符合工艺要求 极片的表面状态及厚度 不均 ①偏轻/偏重,会导致正负极 比例偏差过大,存在较大的 安全隐患;②压片密度不均 匀,影响电池内阻 浆料中剩有干料 拉浆时造成缺料 浆料内有颗粒,电池内阻 高,自放电及大电流放电性 能差 影响拉浆 浆料中颗粒发生沉降 浆料不均匀,电池一致性不 好 浆料中引入水分 浆料状态不好,影响拉浆 浆料中有大颗粒 影响拉浆 浆料发生变化
4 2 3 2 2 2 2 2 22 2 4 3 6 5 5 3 2 2 3 3 3 3 5 5 3 3 3 3 3 5 3 3 5 3 3 3 3 3 3 5 3 3 5 3 3 3 3 3 3 2 2 3 4 4 4
112 28 42 42 42 28 28 28 24 48 24 32 48 24 24 36 36 30 36 30 42 42 30 24 32 64 48 72 60 60 60 56 70 63 42 42 42 60 60 60 63 63 60 60 50 36 36 35 42 60 63 63 60 60 50 36 36 35 42 60 30 30 30 36 36 60 42 56 56 56 72 40 28 28 40 40 40 40 40 40 60
刀口磨损或刀口有干料 胶轮或钢轮上有干料 机器温度太高 收卷过大在支架上互相碰撞 结构基准面不水平 辊轮配合的保障线速度不一致 浆料沉淀 辊轮表面磨损,配合不均匀 搅拌器速度过高 料盘漏液 管道出浆流量过大 搅拌器速度过低 输浆气泵压力不足 管道出浆流量过小 输浆气泵压力不足 输浆气泵压力不足 有干料堵塞管道 气动隔膜磨损 生产泵损坏 接口密封垫老化 筛网破损 浆料在管道中不均匀 浆料温度过高,管道易老化 拉浆张力过大 拉浆张力不足 反面敷料不均匀 β 射线系统失效 泵部分部件老化 极片卷在转移过程中逗留时间 过长或环境温度过大 极片卷在转移过程中逗留时间 过长或环境粉尘含量过高 大的极片卷在转移过程中产生 碰撞 来料极片上有杂质 辊轮上有干料和杂质 压力大小不合适 辊轮不平行 压轮实际间隙不均 压片机辊轮的速度过快/过慢 极片卷在转移过程中逗留时间 过长或环境温度过大 极片卷在转移过程中逗留时间 过长或环境粉尘含量过高 大的极片卷在转移过程中产生 碰撞 刀口磨损 引片位置错误 极片打皱 滚切刀转速过大 刀口有毛刺或缺口 毛刷未接触极片 除尘吹风气压不足 切刀口过紧 除尘吹气压过大 ◇ 待切极片宽度与滚刀规格不符 刀口磨损 引片位置错误 极片打皱 ◇ 滚切刀转速过大 刀口有毛刺或缺口 毛刷未接触极片 除尘吹风气压不足 刀口过紧 除尘吹气压过大 ◇ 待切极片宽度与滚刀规格不符 温度过低,时间过短 温度过高 温度过低,时间过短 温度过高 来料不良 裁切刀磨损 设备稳定性不够,电流电压波 动 点焊位置脏 焊头粘有杂质 焊点位于极耳边缘,点在料上 员工操作不当,点焊时极片未 对齐 ◇ 员工操作失误 员工操作失误,极耳超出极片 边缘部分过长 焊接能量过大 ◇ ◇ 焊头纹理太深 员工操作失误 胶布长度/宽度不够 ◇ 胶布贴斜 胶布长度/宽度不够 ◇ 胶布贴斜 极片在转移过程中逗留时间过 长或环境粉尘含量过高
乙炔黑未分散均匀 浆料中有大颗粒
正极切刀每半月修磨一次, 定期换刀,用Xbar-R控制图监 负极切刀每月修磨一次,并 控敷料面密度 QC临控 QC监控浆料使用时间 管道出浆口增加筛网 超时报废 定期检查、更换筛网 定时擦洗滚轮 调试 机器设定 IQC抽检 经首检合格后锁死 定期清扫或更换 使用前校准对位
胶布盖不住焊点 短路 铝带焊接位置偏移 影响点焊盖板 刺破底部胶布和隔膜,短路 电池高内阻 电池高内阻 短路 短路 毛刺 电池微短路,影响电池自放 电及安全性能 毛刺 电池微短路,影响电池自放 电及安全性能 极片厚度不均匀 大的极片卷引入水分 大的正极片卷在转移过 大卷的正极片转移 程中引入外界杂质 大的正极片卷在转移过 程中掉料、折皱 裁斜 极片压厚/压薄 泵内杂质进入浆料 大的极片卷引入水分 影响电池性能 影响电池性能 影响电池性能 电池短路 影响电池容量分布,导致电 池低容量 敷料厚度不均匀 影响电池容量 浆料不均匀 敷料厚度不均匀 浆料溢出 敷料厚度不均匀 敷料不均匀 影响电池容量 走带偏移、不平稳 烂边、打皱,影响电池自放 电 掉料、缺料、有划痕 影响电池容量分布,导致电 池低容量
起因/机理
探测
预防
目标 措施结果 完成 严重度 频度 探测度 RPN 日期 采取的措施 (S) (O) (D)
正极配粘接导电剂 (将活性物料、导 电剂、粘接剂、溶 剂等按照一定的比 例充分混合)
导电剂加入量过多 导电剂加入量过少 粘接剂加入量过多 粘接剂加入量过少 溶剂加入量过多或过少 乙炔黑未分散均匀
37 38 39 40 41 42 43 44 45 46 47 48 49 50 51 52 53 54 55 56 57 58 59 60 61 62 63 64 65 66 67 68 69 70 正极连续压片 71 72 73 74 75 76 77 78 79 80 81 82 83 84 85 86 87 88 89 90 91 92 93 94 95 96 97 98 99 100 101 102 103 104 105 106 107 108 109 110 111 112 113