注塑工艺调试验证技术规范
注塑工艺规范
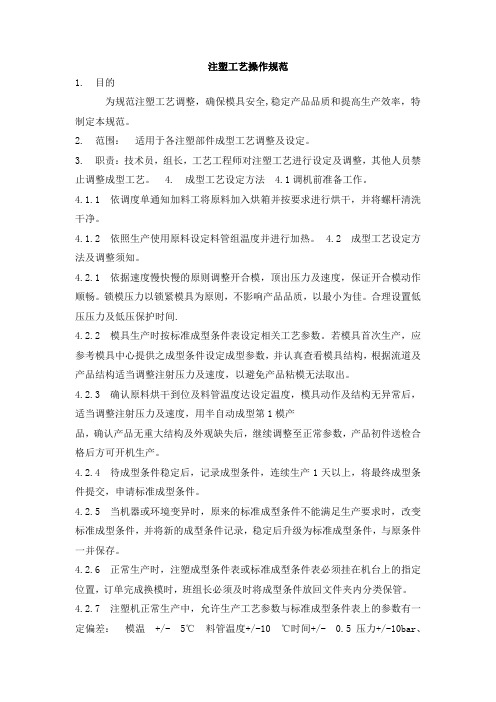
注塑工艺操作规范1. 目的为规范注塑工艺调整,确保模具安全,稳定产品品质和提高生产效率,特制定本规范。
2. 范围:适用于各注塑部件成型工艺调整及设定。
3. 职责:技术员,组长,工艺工程师对注塑工艺进行设定及调整,其他人员禁止调整成型工艺。
4. 成型工艺设定方法 4.1调机前准备工作。
4.1.1 依调度单通知加料工将原料加入烘箱并按要求进行烘干,并将螺杆清洗干净。
4.1.2 依照生产使用原料设定料管组温度并进行加热。
4.2 成型工艺设定方法及调整须知。
4.2.1 依据速度慢快慢的原则调整开合模,顶出压力及速度,保证开合模动作顺畅。
锁模压力以锁紧模具为原则,不影响产品品质,以最小为佳。
合理设置低压压力及低压保护时间.4.2.2 模具生产时按标准成型条件表设定相关工艺参数。
若模具首次生产,应参考模具中心提供之成型条件设定成型参数,并认真查看模具结构,根据流道及产品结构适当调整注射压力及速度,以避免产品粘模无法取出。
4.2.3 确认原料烘干到位及料管温度达设定温度,模具动作及结构无异常后,适当调整注射压力及速度,用半自动成型第1模产品,确认产品无重大结构及外观缺失后,继续调整至正常参数,产品初件送检合格后方可开机生产。
4.2.4 待成型条件稳定后,记录成型条件,连续生产1天以上,将最终成型条件提交,申请标准成型条件。
4.2.5 当机器或环境变异时,原来的标准成型条件不能满足生产要求时,改变标准成型条件,并将新的成型条件记录,稳定后升级为标准成型条件,与原条件一并保存。
4.2.6 正常生产时,注塑成型条件表或标准成型条件表必须挂在机台上的指定位置,订单完成换模时,班组长必须及时将成型条件放回文件夹内分类保管。
4.2.7 注塑机正常生产中,允许生产工艺参数与标准成型条件表上的参数有一定偏差:模温+/- 5℃料管温度+/-10 ℃时间+/- 0.5压力+/-10bar、速度+/-10%、位置+/-10 。
4.3调整须知:工艺调整超出标准成型条件允许范围时,需经主管批准,验证中成型条件及标准成型条件属于受控文件,检验人员对制程进行监控,禁止随意更改。
注塑工艺操作及检验控制

操作员配料员保管员负责人检验员1准备:将机台整理干净、整洁,工具有序放置,检查机器工作是否正常。
●2加料:将需要生产的原材料正确的装入料筒中。
●3模具安装和调试:将需生产的模具正确的安装在相应的机台上,并设定好机器的正常运转参数和产品的工艺参数。
●●4首件确认:操作人员将首次生产出的完整一模产品(按开模数)交与检验人员确认,经检验确认合格后,方可正式生产。
经首件确认的产品需保留至本批产品生产结束。
●5作业内容5.1操作人员在生产无辅件(卡件)产品时,按正常生产要求进行操作。
●5.2如操作人员在生产有辅件(卡件)产品时,应先将辅件(卡件)按正确的方法放入模具定位槽中,然后再启动机器按钮,如是立式机应双手同时按下启动按钮。
●5.3机器开模后,应按正确的方法立即取出制品和料头,并将其按要求放置,制品置于台面上,料头置入回收袋中。
●5.4重复5.1、5.2、5.3步骤。
●5.5自检:每模生产出的制品要自检,自检合格后将其放入待检盒或框中,不合格的制品放入不合格盒或框中。
●生产相关记录5.6巡检人员要按要求对生产出的制品进行检验,发现问题应及进对相应人员进行通报和处理。
●巡检记录5.7本批零件生产结束后,从机台上拆除模具后及时进行清洁和内部防护处理,相关人员应对模具结构进行检查。
●●●相关模具表单6完工检验:本批制品生产结束,应经检验员抽验合格后,方可对其进行转序和入库。
●检验报告7质量检验要求:●检验方案检测方法质量记录7.1制品结构完整,表面无缺料、收缩、顶包、飞边、变形等缺陷。
●目测7.2制品尺寸与设计图纸一致,重要尺寸必须严格检验。
●游标卡尺8参数监控:检验员及车间负责人应随时监控工艺参数。
●●随时制品异常反应:剔除、隔离、标识、记录编 制标准化审 核批 准机台、工装、材料异常反应:停机、报告(日 期)(日 期)(日 期)(日 期)10● 表示负责作业内容的执行人不合格的产品不能直接放入料头袋中,应经检验员或车间负责人确认后,才能进行转移。
注塑工艺验证方案

注塑工艺验证方案1 验证目的对注塑工艺进行验证、确认有效控制,以保证在模具、机器型号不变的一定的生产条件下,生产出符合标准要求的医疗器械产品。
评价注塑工艺参数改变对注塑产品的外观、集合形状的影响,以确定最佳注塑工艺参数,为编制定机、定模具的注塑工艺卡确定工艺依据。
2验证要求2.1 验证依据:图纸:外套PQ-CT-02-06相关产品标准:2.2 验证项目:注塑压力(%);料筒温度(℃);冷却时间(S)2.3 验证参与部门和人员技术部质保部负责人:注塑车间生产主管:2.4 验证条件3 验证试验验证按图示程序进行:3.1 试验工艺参数设置 < 注塑工艺参数排列表>3.2 试验方法:3.2.1 按〈注塑工艺参数排列表〉将始注温度、始注射压力组成试验参数组开始进行试注射。
3.2.2 根据设备说明书及常规经验进行组合设计升温、升压试验:a)料筒温度外套加工参数:芯杆加工参数:b)注射压力:注射压力保持在45-46%c)保压时间外套:25.5s,芯杆:25.5sd)冷却时间外套:21-23s,芯杆:18-19s3.2.3 试验记录每组试验由车间工艺试验员做试验数据记录,由检验员记录产品成型质量情况,直至产品合格及达到最佳质量状态,即可确定最佳注塑组合工艺参数值。
4验证结果分析评价:4.1 检验评价巡检员对每组试注塑产品均作外观及几何尺寸的检验,作出该模产品符合规定要求及图纸的情况和检验结论,并在附件3《注塑工艺参数验证排列表》上签注验证评价意见。
4.2 车间试验评价注塑车间工艺试验员依据《注塑工艺参数验证排列表》记录的产品合格情况,择定最佳注塑组合工艺参数,在《注塑工艺参数验证排列表》上签注验证评价意见。
5验证结果的报告和反馈5.1试验结束后,注塑车间工艺验证员据《注塑工艺参数验证排列表》将择定的最佳注塑组合工艺参数写入注塑编写《注塑工艺验证试验报告》,交质管部签署验证意见后报送技术部。
5.2 技术部依据车间和品管部试验评价意见做最后验证确认结论后,进行以下文件准备:对新产品,将工艺验证最佳参数值编制该产品的注塑工a)艺过程卡;b)对老产品中存在的工艺卡与记录不符合的,据此修改和更换工艺过程卡。
注塑工艺验证方案

一,验证目的:1.一次性使用无菌医疗器械生产中,注塑是生产过程中影响产品质量的主要环节之一。
注塑质量影响到产品整体的性能和外观,配合等方面因此,对注塑工艺进行有效的控制并验证,以保证实现在正常的生产条件下,生产出符合标准的医疗器械产品。
2.本方案的目的在于为评价注塑工艺参数的状况对注塑产品的外观及尺寸的影响,以确认最佳的注塑工艺参数。
二,方案验证小组成员:技术部:品管部设备部注塑车间:本方案的由技术部编制,由品管部、技术部协同努力设计完成,总工和师审核批准。
三,验证依据:产品图纸和相关设备参数。
四,验证项目:各种零配件的注塑压力、温度、成型周期对产品质量的影响。
五,验证项目:各种零配件的注塑压力、温度、成型周期对产品质量的影响。
验证条件设置:1.注塑区环境条件:a)温度:18-28b)湿度:50-65RH2.注塑工艺参数:a)温度筒体类:前区:290 40 ,中区:285 40 后区265 40推杆类:前区:200 30 中区210 30 后区180 30模温:55 ---65b)压力:锁模压力:135注射压力:3-134BAR成型周期;注塑;3-18秒保压+冷却:6-20S六,验证方法(见附件1)1.参数设置:设置好各类参数,使机器预热升温至额定值。
2.出样:空注出模头样,手动闭模,注塑2-3模产品。
3.检验:检验产品外观及尺寸是否符合有关要求及图纸,如果全部合格,则投入正常生产,如果一项或某几项不合格,则需回到第一步,进行参数调整,重新进行验证。
七,结果分析评价:经过上述过程对某一产品注塑工艺参数进行验证过程确认,并填写工艺验证报告和工艺参数验证排列表。
见附件2。
八,最终批准:验证小组审阅上述所有结果及评价分析意见,同意验证结果,并按此结论编制注塑工艺过程卡。
九,声明:兹证明本人已审核同意注塑工艺验证方案。
注塑工艺参数验证排列表。
注塑机工艺调试
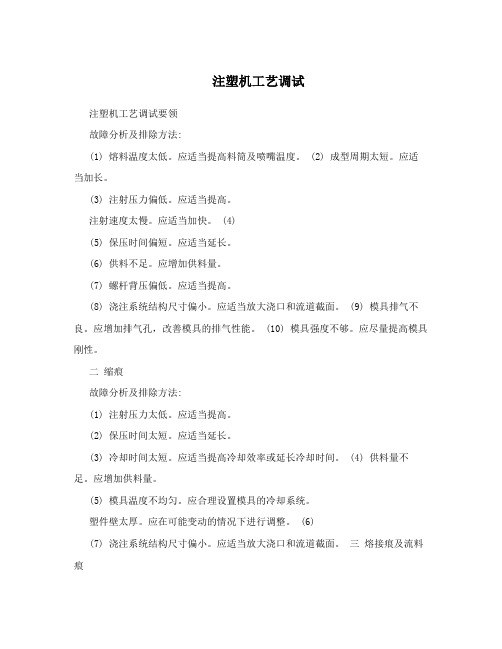
注塑机工艺调试注塑机工艺调试要领故障分析及排除方法:(1) 熔料温度太低。
应适当提高料筒及喷嘴温度。
(2) 成型周期太短。
应适当加长。
(3) 注射压力偏低。
应适当提高。
注射速度太慢。
应适当加快。
(4)(5) 保压时间偏短。
应适当延长。
(6) 供料不足。
应增加供料量。
(7) 螺杆背压偏低。
应适当提高。
(8) 浇注系统结构尺寸偏小。
应适当放大浇口和流道截面。
(9) 模具排气不良。
应增加排气孔,改善模具的排气性能。
(10) 模具强度不够。
应尽量提高模具刚性。
二缩痕故障分析及排除方法:(1) 注射压力太低。
应适当提高。
(2) 保压时间太短。
应适当延长。
(3) 冷却时间太短。
应适当提高冷却效率或延长冷却时间。
(4) 供料量不足。
应增加供料量。
(5) 模具温度不均匀。
应合理设置模具的冷却系统。
塑件壁太厚。
应在可能变动的情况下进行调整。
(6)(7) 浇注系统结构尺寸偏小。
应适当放大浇口和流道截面。
三熔接痕及流料痕故障分析及排除方法:(1) 熔料温度太低。
应适当提高料筒及喷嘴温度。
(2) 注射压力太低。
应适当提高。
(3) 注射速度太慢。
应适当加快。
(4) 模具温度太低。
应适当提高。
(5) 塑件形体结构设计不合理或壁太薄。
应在可能变动的情况下进行调整。
(6) 浇注系统结构尺寸偏小。
应适当放大浇口及流道截面。
(7) 模具内的冷料穴太小。
应适当加大。
(8) 原料内混入异物杂质。
应进行清除。
(9) 脱模剂用量偏多。
应尽量减少其用量。
(10) 原料着色不均匀。
应延长混色的搅拌时间,使原料着色均匀。
四光泽不良故障分析及排除方法:(1) 熔料温度偏低。
应适当提高料筒及喷嘴温度。
(2) 成型周期太长。
应适当缩短。
(3) 模具温度偏低。
应适当提高。
(4) 浇注系统结构尺寸偏小。
应适当放大浇口及流道截面。
(5) 模具排气不良。
应增加排气孔,改善模具的排气性能。
(6) 原料内混入杂质。
应彻底清除异物杂质或换用新料。
注塑调试工安全作业规
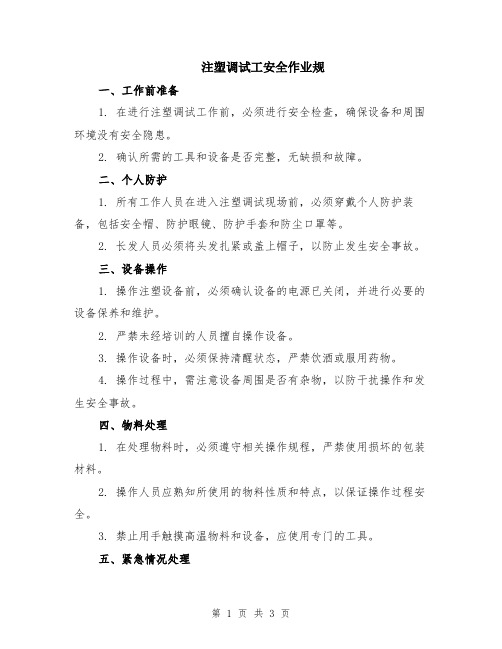
注塑调试工安全作业规一、工作前准备1. 在进行注塑调试工作前,必须进行安全检查,确保设备和周围环境没有安全隐患。
2. 确认所需的工具和设备是否完整,无缺损和故障。
二、个人防护1. 所有工作人员在进入注塑调试现场前,必须穿戴个人防护装备,包括安全帽、防护眼镜、防护手套和防尘口罩等。
2. 长发人员必须将头发扎紧或盖上帽子,以防止发生安全事故。
三、设备操作1. 操作注塑设备前,必须确认设备的电源已关闭,并进行必要的设备保养和维护。
2. 严禁未经培训的人员擅自操作设备。
3. 操作设备时,必须保持清醒状态,严禁饮酒或服用药物。
4. 操作过程中,需注意设备周围是否有杂物,以防干扰操作和发生安全事故。
四、物料处理1. 在处理物料时,必须遵守相关操作规程,严禁使用损坏的包装材料。
2. 操作人员应熟知所使用的物料性质和特点,以保证操作过程安全。
3. 禁止用手触摸高温物料和设备,应使用专门的工具。
五、紧急情况处理1. 在发生紧急情况时,工作人员应立即停止操作,确保自身安全。
2. 如遇火灾、泄漏等危险情况,应立即向相关人员汇报,并按照紧急处理程序进行操作。
六、现场整洁1. 工作区域应保持整洁,严禁堆放杂物,以免影响操作和造成安全隐患。
2. 使用完毕的工具和设备应及时归位,不得放置在操作区域。
七、协同合作1. 在注塑调试过程中,各工作人员应互相配合,遵守工作规程。
2. 如需调整操作方案或有意外情况发生,应及时向上级汇报和请示。
八、安全意识培养1. 所有工作人员应定期进行安全教育和培训,提高安全意识和应急处理能力。
2. 应确保所有工作人员了解和遵守相关安全制度和规程。
以上为注塑调试工安全作业规,每个工作人员必须严格遵守。
只有确保安全,才能保障工作顺利进行,并最大程度地防止事故的发生。
总结:注塑调试工作涉及到复杂的设备和物料操作,因此安全工作尤为重要。
通过提前的准备工作、个人防护措施、设备操作规范、物料处理规范、紧急情况处理、现场整洁、协同合作和安全意识培养,可以最大限度地保障工作人员的安全,减少事故发生的可能性。
注塑机调机调试工艺一般分三个步骤

注塑机调机调试工艺一般分三个步调:1.参数设定前需确认及准备设定参数⑴确认材料湿润.模温及加热筒温度是否被准确设定并达到可加工状况.⑵检查开闭模及顶出的动作和距离设定.⑶射出压力(P1)设定在最大值的60%.⑷保持压力(PH)设定在最大值的30%.⑸射出速度(V1)设定在最大值的40%.⑹螺杆转速(VS)设定在约60RPM.⑺背压(PB)设定在约10kg/cm2.⑻松退约设定在3mm.⑼保压切换的地位设定在螺杆直径的30%.例如φ100mm的螺杆,则设定30mm.⑽计量行程比盘算值稍短设定.⑾射出总时光稍短,冷却时光稍长设定.2.手动运转参数修改⑴闭锁模具(确认高压的上升),射出座进步.⑵以手动射出直到螺杆完全停滞,并留意停滞地位.⑶螺杆旋退进料.⑷待冷却后开模掏出成型品.⑸反复⑴~⑷的步调,螺杆最终停滞在螺杆直径的10%~20%的地位,并且成型品无短射.毛边及白化,或开裂等现象.3.半主动运转参数的修改⑴计量行程的修改[计量终点] 将射出压力进步到99%,并把保压暂调为0,将计量终点S0向前调到产生短射,再向后调至产生毛边,以个中央点为选择地位.⑵出速度的修改把PH答复到原水准,将射出速度高低调剂,找出产生短射及毛边的个体速度,以个中央点为合适速度[本阶段亦可进入以多段速度对应外不雅问题的参数设定].⑶保持压力的修改高低调剂保持压力,找出产生概况凹陷及毛边的个体压力,以个中央点为选择保压.⑷保压时光[或射出时光]的修改慢慢延伸保持时光,直至成型品重量显著稳固为明适选择.⑸冷却时光的修改慢慢伐降冷却时光,并确认下列情形可以知足:1.成型品被顶出.夹出.修整.包装不会白化.凸裂或变形.2.模温能均衡稳固.肉厚4mm以上成品冷却时光的简略单纯算法:①理论冷却时光=S(1+2S)…….模温60度以下.②理论冷却时光=1.3S(1+2S)…….模具60度以上[S暗示成型品的最大肉厚].⑹塑化参数的修改①确认背压是否须要调剂;②调剂螺杆转速,使计量时光稍短于冷却时光;③确认计量时光是否稳固,可测验测验调剂加热圈温度的梯度.④确认喷嘴是否有滴料.主流道是否产生猪尾巴或粘模,成品有无气痕等现象,恰当调剂喷嘴部温度或松退距离.⑺段保压与多段射速的活用①一般而言,在不影响外不雅的情形下,打针应以高速为原则,但在经由过程浇口间及保压切换前应以较低速进行;②保压应采取慢慢降低,以防止成型品内应力残留太高,使成型品轻易变形.塑成型缺陷的成因及解决办法不准确的操纵前提,破坏的机械及模具会产生许多成型缺陷,下面供给了一些解决的办法供参考.为了削减停机的时光,及能尽快找出操纵问题的原因,操纵人员应把所有最好的注塑机型前提记载在“注塑成型前提记载表”上,以供日后解决问题时参考之用.(1)成品不完全故障原因处理办法塑料温度太低进步熔胶筒温度射胶压力太低进步射胶压力射胶量不敷增多射胶量浇口衬套与射嘴合营不正,塑料溢漏从新调剂其合营射前时光太短增长射胶时光射胶速度太慢加速射胶速度低压调剂不当从新调节模具温度太低进步模具温度模具温度不匀重调模具水管模具排气不良恰当地位加适度排气孔射嘴温度不低进步射嘴温度进胶不服均重开模具溢口地位浇道或溢口太小加大浇道或溢口塑料内润滑剂不敷增长润滑剂背压缺少稍增背压过胶圈.熔胶螺杆磨损裁撤检查补缀射胶量缺少改换较大规格注塑机成品太薄应用氮气射胶(2)成品紧缩故障原因处理办法模内进胶缺少熔胶量缺少加熔胶量射胶压力太低高射压背压压力不敷高背压力射胶时光太短长射胶时光射胶速度太慢快射速溢口不服衡模具溢口太小或地位射嘴孔太细,塑料在浇道衬套内凝固,减低背压后果.整模具或改换射嘴料温过高下料温模温不当整恰当温度冷却时光不敷延冷却时光蓄压段过多射胶终止应在最前端产品本身或其肋骨及柱位过厚检查成品设计射胶量过大改换较细的注塑机过胶圈.熔胶螺杆磨损裁撤检修浇口太小.塑料凝固掉支背压感化加大浇口尺寸(3)成品粘模故障原因处理办法填料过饱降低射脱压力,时光,速度及射胶量射胶压力太高降低射胶压力射胶量过多减小射胶量射胶时光太长减小射胶间时料温太高降低料温进料不均使部分过饱变动溢口大小或地位模具温渡过高或过低调剂模温及两侧相对温度模内有脱模倒角修模具除去倒角模具概况不但滑打磨模具脱模造成真空开模或顶出减慢,或模具加进气装备注塑周期太短增强冷却脱模剂缺少略为增长脱模剂用量(4)浇道(水口)粘模故障原因处理办法射胶压力太高降低射胶压力塑料温渡过高降低塑料温度浇道过大修改模具浇道冷却不敷延伸冷却时光或降低冷却温度浇道脱模角不敷修改模具增长角度浇道衬套与射嘴合营不正从新调剂其合营浇道内概况不但或有脱模倒角检修模具浇道外孔有破坏检修模具无浇道抓销加设抓销填料过饱降低射胶量,时光及速度脱模剂缺少略为增长脱模剂用量(5)毛头.飞边故障原因处理办法塑料温度太高降低塑料温度,降低模具温度射胶速度太高降低射胶速度射胶压力太高降低射胶压力填料太饱降低射胶时光,速度及剂量合模线或吻合面不良检修模具锁模压力不敷增长锁模压力或改换模压力较大的注塑机(6)开模时或顶出时成品决裂故障原因处理办法填料过饱降低射胶压力,时光,速度及射胶量模温太低升高模温部分脱模角不敷检修模具有脱模倒角检修模具成品脱模时不克不及均衡离开检修模具顶针不敷或地位不当检修模具脱模时局部产生真空现象开模可顶出慢速,加进气装备脱模剂缺少略为增长脱模剂用量模具设计不良,成品内有过过剩应力改进成品设计侧滑块动作之时光或地位不当检修模具(7)联合线故障原因处理办法塑料熔融不佳进步塑料温度.进步背压.加速螺杆转速模具温渡过低进步模具温度射嘴温渡过低进步射嘴温度射胶速度太慢增快射胶速度射胶压力太低进步射胶压力塑料不洁或渗有其它料检查塑料脱模油太若干用胶模油或尽量不必浇道及溢口过大或过小调剂模具熔胶接合的地方离浇道口太远调剂模具模内空气消除不及增开排气孔或检查原有排气孔是否堵塞熔胶量缺少应用较大的注塑机太多脱模剂不必或削减脱模剂(8)流纹故障原因处理办法塑料熔融不佳进步塑料温度.进步背压.加速螺杆转速模具温度太低进步模具温度模具冷却不当重调模具水管射胶速度太快或太慢调剂恰当射胶速度射胶压力太高或太低调剂恰当射胶压力塑料不洁或渗有其它料检查塑料溢口过小产生射纹加大溢口成品断面厚薄相差太多变动成品设计或溢口地位(9)成品概况不但泽故障原因处理办法模具温度太低进步模具温度塑料剂量不敷增长射胶压力,速度,时光及剂量模腔内有过多脱模油擦试清洁塑料湿润处理不当改进湿润处理模内概况有水擦试并检查是否有漏水模内概况不但滑打磨模具(10)银纹.气泡故障原因处理办法塑料含有水份塑料完全烘干.进步背压塑料温渡过高或塑料在机筒内逗留过久降低塑料温度,改换较小射胶量的注塑机,降低射嘴及前段温度塑估中其它添加物如润滑剂,染料等分化减小其应用量或改换耐温较高的代替品塑估中其它添加物混杂不匀完全混杂平均射胶速度不快减慢射胶速度射胶压力太高降低射胶压力熔胶速度太低进步熔胶速度模具温度太低进步模具速度塑料粒粗细不匀应用粒状平均原料熔胶筒内夹有空气降低熔胶筒后段温度.进步背压.减小紧缩段长度塑料在模内流程不当调剂溢口大小及地位.模具温度保持平均.成品厚度平均(11)成品变形故障原因处理办法成品顶上时尚未冷却降低模具温度,延伸冷却时光,降低塑料温度塑料温度太低进步塑料温度,进步模具温度成品外形及厚薄不合错误称模具温度分区掌握,脱模后以定形架固定,变动成形设计填料过多减小射胶压力,速度,时光及剂量几个溢口进料不服均更改溢口顶针体系不服衡改良顶出体系模具温度不平均调剂模具温度近溢口部分的塑料太松或太紧增长或削减射胶时光保压不良增长保压时光(12)成品内有气孔故障原因处理办法填料量缺少以防止成品过度紧缩成品断面,肋或柱过厚变动成品设计或溢口地位射胶压力太低进步射胶压力射胶量实时光缺少增长射胶量及射胶时光浇道溢口太小加大浇道及溢口射胶速度太快调慢射胶速度塑料含水份塑料完全湿润塑料温渡过高乃至分化降低塑料温度模具温度不平均调剂模具温度冷却时光太长削减模内冷却时光,应用水浴冷却水浴冷却过急减小水浴时光或进步水浴温度背压不敷进步背压熔胶筒温度不当降低射嘴及前段温度,进步后段温度塑料的紧缩率太大采取其它紧缩率较小的塑料(13)黑纹故障原因处理办法塑料过热塑料温度太高降低塑料温度熔胶速度太快降低射胶速度螺杆与熔胶筒偏幸而产生异常摩擦热检修机械射嘴孔过小或温渡过高从新调剂孔径或温度射胶量过大改换较小型的注塑机熔胶筒内有使塑料过热的*角检查射嘴与熔胶筒间的接触面,有无间隙或腐化现象(14)黑点故障原因处理办法塑料过热部分附着熔胶筒内壁完全空射,裁撤熔胶筒清算,降低塑料温度,减短加热时光,增强塑料湿润处理塑料混有杂物,纸屑等检查塑料,完全空射射入模内时产生焦斑降低射胶压力及速度,降低塑料温度,增强模具排气孔,酌降关模压务,更改溢口地位熔胶筒内有使塑料过热的*角检查射嘴熔胶筒间的接触面,有无间隙或腐化现象.(15)不稳固的周期以上列举的各类成型缺陷,其成因及对策大多半都与周期的稳固与否有关.塑料在熔胶筒内恰当的塑化,或模具的温度掌握,都是传热均衡的成果.也就是说在全部注塑周期中,熔胶筒内的塑料接收来自螺杆扭转的摩擦热,电热圈的热.热能跟着塑料注入模内,模具的热能来自塑料和模具的恒器,损掉在成品的脱模,散掉于空气中或经冷却水带走.是以熔胶筒或模具的温度若要保持不变,必须保持其进出的传热均衡.保持传热的均衡则必须保持必定稳固的注塑周期.假若注塑周期时光愈来愈短则熔胶筒中的热能入不敷出,乃至缺少以融化塑料,而模具的热能则又入多于出,乃至模温不竭上升.反之则有相反的成果是以在任何一个注塑成形操纵中,特殊是手动操纵,必须掌握稳固周期时光,尽量防止快慢不一.如其它前提保持不变,则:周期的加速将造成:短射,成品紧缩与变形,粘模.周期的延慢将造成:溢料,毛头,料模,成品变形,塑料过热,甚至烧焦,残留在模具中的焦料又可能造成模具破坏.熔胶筒中过热之塑料又可能腐化熔筒及成品消失黑斑及黑纹.。
注塑成型制程检验规范
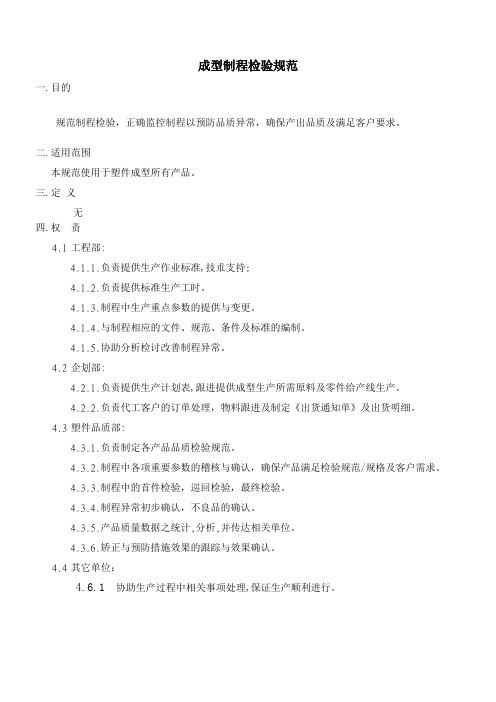
成型制程检验规范一. 目的规范制程检验,正确监控制程以预防品质异常,确保产出品质及满足客户要求。
二. 适用范围本规范使用于塑件成型所有产品。
三. 定义无四. 权责4.1工程部:4.1.1.负责提供生产作业标准,技朮支持;4.1.2.负责提供标准生产工时。
4.1.3.制程中生产重点参数的提供与变更。
4.1.4.与制程相应的文件、规范、条件及标准的编制。
4.1.5.协助分析检讨改善制程异常。
4.2企划部:4.2.1.负责提供生产计划表,跟进提供成型生产所需原料及零件给产线生产。
4.2.2.负责代工客户的订单处理,物料跟进及制定《出货通知单》及出货明细。
4.3塑件品质部:4.3.1.负责制定各产品品质检验规范。
4.3.2.制程中各项重要参数的稽核与确认,确保产品满足检验规范/规格及客户需求。
4.3.3.制程中的首件检验,巡回检验,最终检验。
4.3.4.制程异常初步确认,不良品的确认。
4.3.5.产品质量数据之统计,分析,并传达相关单位。
4.3.6.矫正与预防措施效果的跟踪与效果确认。
4.4其它单位:4.6.1协助生产过程中相关事项处理,保证生产顺利进行。
五. 作业流程六. 作业内容6.1 获取产品制作所需信息6.1.1.产品在生产前,生产各相关人员必需获得以下工程资料方可生产:产品工程图、BOM表、作业指导书、作业流程及包装规范。
品管成型单位企划6.1.2.品管检验人员在产品生产前必需获得该产品的SIP、蓝图、评估报告、样品等资料,以作为检验该产品的依据。
6.1.3.以上工程资料及检验资料必需为文控中心正式发行的资料。
6.1.4.生产必需依各相关产品的工程资料要求进行产品制造。
若生产条件或生产流程需要任何变更时, 由工程填写工程变更通知单,经相关部门签核同意后,由文控中心统一变更受控发行,具体操作参照《文件资料管理程序》。
6.2生产计划管制6.2.1.企划部生管员依客户或各厂区需求制订每周生产计划。
6.2.2.企划部生管员需依生产计划跟进采购或供应商按时供给成型原料,并由生管员开出《发料单》,通知货仓备料发料,生产领料。
注塑成型工艺条件调试规定
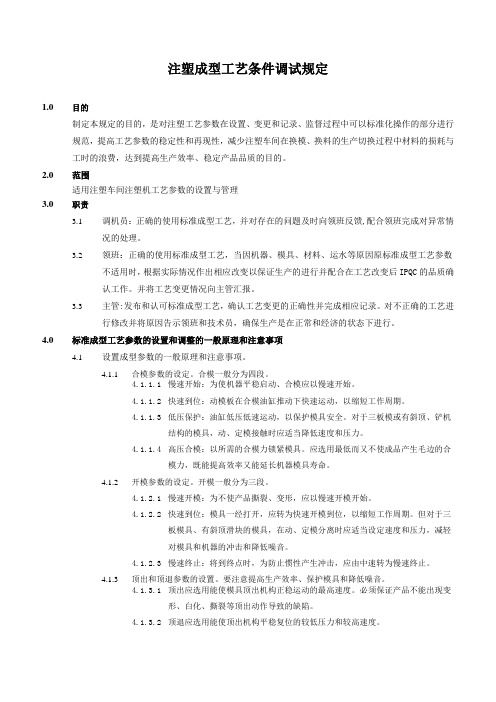
注塑成型工艺条件调试规定1.0目的制定本规定的目的,是对注塑工艺参数在设置、变更和记录、监督过程中可以标准化操作的部分进行规范,提高工艺参数的稳定性和再现性,减少注塑车间在换模、换料的生产切换过程中材料的损耗与工时的浪费,达到提高生产效率、稳定产品品质的目的。
2.0范围适用注塑车间注塑机工艺参数的设置与管理3.0职责3.1调机员:正确的使用标准成型工艺,并对存在的问题及时向领班反馈,配合领班完成对异常情况的处理。
3.2领班:正确的使用标准成型工艺,当因机器、模具、材料、运水等原因原标准成型工艺参数不适用时,根据实际情况作出相应改变以保证生产的进行并配合在工艺改变后IPQC的品质确认工作。
并将工艺变更情况向主管汇报。
3.3主管:发布和认可标准成型工艺,确认工艺变更的正确性并完成相应记录。
对不正确的工艺进行修改并将原因告示领班和技术员,确保生产是在正常和经济的状态下进行。
4.0标准成型工艺参数的设置和调整的一般原理和注意事项4.1设置成型参数的一般原理和注意事项。
4.1.1合模参数的设定。
合模一般分为四段。
4.1.1.1慢速开始:为使机器平稳启动、合模应以慢速开始。
4.1.1.2快速到位:动模板在合模油缸推动下快速运动,以缩短工作周期。
4.1.1.3低压保护:油缸低压低速运动,以保护模具安全。
对于三板模或有斜顶、铲机结构的模具,动、定模接触时应适当降低速度和压力。
4.1.1.4高压合模:以所需的合模力锁紧模具。
应选用最低而又不使成品产生毛边的合模力,既能提高效率又能延长机器模具寿命。
4.1.2开模参数的设定。
开模一般分为三段。
4.1.2.1慢速开模:为不使产品撕裂、变形,应以慢速开模开始。
4.1.2.2快速到位:模具一经打开,应转为快速开模到位,以缩短工作周期。
但对于三板模具、有斜顶滑块的模具,在动、定模分离时应适当设定速度和压力,减轻对模具和机器的冲击和降低噪音。
4.1.2.3慢速终止:将到终点时,为防止惯性产生冲击,应由中速转为慢速终止。
注塑调试工安全作业规
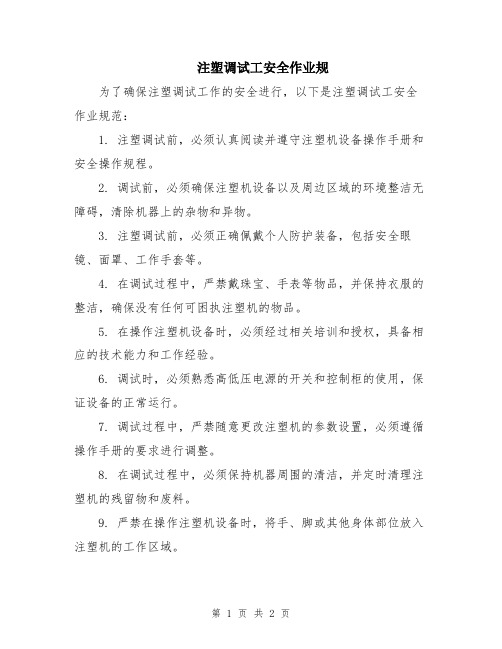
注塑调试工安全作业规
为了确保注塑调试工作的安全进行,以下是注塑调试工安全作业规范:
1. 注塑调试前,必须认真阅读并遵守注塑机设备操作手册和安全操作规程。
2. 调试前,必须确保注塑机设备以及周边区域的环境整洁无障碍,清除机器上的杂物和异物。
3. 注塑调试前,必须正确佩戴个人防护装备,包括安全眼镜、面罩、工作手套等。
4. 在调试过程中,严禁戴珠宝、手表等物品,并保持衣服的整洁,确保没有任何可困执注塑机的物品。
5. 在操作注塑机设备时,必须经过相关培训和授权,具备相应的技术能力和工作经验。
6. 调试时,必须熟悉高低压电源的开关和控制柜的使用,保证设备的正常运行。
7. 调试过程中,严禁随意更改注塑机的参数设置,必须遵循操作手册的要求进行调整。
8. 在调试过程中,必须保持机器周围的清洁,并定时清理注塑机的残留物和废料。
9. 严禁在操作注塑机设备时,将手、脚或其他身体部位放入注塑机的工作区域。
10. 调试过程中,必须保持机器周围的通风良好,避免因工作环境不适导致身体不适。
11. 在调试过程中,如遇到设备故障或异常情况,应立即停机并报告相关负责人。
12. 调试完成后,必须关闭注塑机设备的电源,并进行必要的清洁和维护工作。
13. 调试工作结束后,应及时清理工作现场,将工具、材料等物品妥善摆放并归纳整齐。
14. 在操作注塑机设备时,必须遵守相关法律法规和公司的安全管理制度。
以上作业规范旨在确保注塑调试工作的安全进行,保护操作人员的人身安全和设备的正常运行。
同时,员工应根据具体工作情况,遵循公司的安全规定,并不断改进安全作业措施。
注塑工艺中的四大调试内容

注塑工艺中的四大调试内容在注塑工艺中,调试是非常重要的步骤,它决定了产品的质量和生产的效率。
下面将介绍注塑工艺中的四大调试内容。
一、模具调试模具调试是整个注塑工艺的第一步,它直接影响产品的成型质量和生产的效率。
1. 模具安装:安装模具时需要注意模具的水平度和平行度,以确保模具的稳定性和精度。
2. 模具间隙调整:模具的间隙调整主要是指模具的合模与分模间的间隙,合理的间隙能够保证产品的尺寸精度和外观质量。
3. 模具温度控制:模具的温度对产品的成型质量有重要影响,要根据产品的要求,调整模具的温度,确保产品的尺寸和外观质量稳定。
4. 模具脱模性能调试:模具脱模性能是指产品在脱模过程中是否能够顺利脱离模具,模具的设计和加工质量直接影响产品的脱模性能。
二、注射调试注射调试是指对注射机进行调试,确保注射机能够正常运行,实现产品的正常注射。
1. 控制参数调整:根据产品的材料和工艺要求,对注射机的控制参数进行调整,包括注射压力、注射速度、保压时间等。
2. 换料和清洗:在调试之前,需要对注射机进行换料和清洗,确保新材料没有混入旧材料或杂质。
3. 润滑和保养:定期对注射机进行润滑和保养,确保注射机的运行平稳,减少故障发生的可能。
4. 注射机的故障排除:如果在调试中发现注射机有故障,需要进行及时的故障排除,保证注射机能够正常运行。
三、工艺参数调试工艺参数调试是指根据产品的材料和尺寸要求,对注塑工艺参数进行调整,以达到最佳的成型效果。
1. 注射压力和速度调整:调整注射压力和速度,控制产品的尺寸和外观质量。
2. 注射时间和保压时间调整:调整注射时间和保压时间,确保产品充填充实和保压稳定。
3. 温度控制调整:调整模具温度和熔料温度,确保产品的尺寸和外观质量稳定。
4. 冷却时间调整:调整冷却时间,以确保产品在脱模时不会变形或开裂。
四、成型品质调试成型品质调试是指对产品的尺寸和外观质量进行调试,以确保产品符合要求。
1. 尺寸精度调试:通过调整工艺参数和模具参数,控制产品的尺寸精度,确保产品的尺寸符合要求。
注塑工艺调试的操作方法

注塑工艺调试的操作方法注塑工艺调试是指在注塑生产过程中对模具和注塑机进行调试,以确保产品质量和生产效率的过程。
下面我将详细介绍注塑工艺调试的操作方法。
1. 检查模具和注塑机在开始调试之前,首先要检查模具和注塑机是否完好无损。
检查模具是否有损坏、变形或磨损现象,并清洁模具表面。
同时,检查注塑机的各项功能是否正常,确保温度控制系统、液压系统和电气系统等正常工作。
2. 确定注塑工艺参数根据产品要求和注塑材料的性质,确定注塑工艺参数,包括注塑温度、熔融温度、冷却时间、成型周期等。
需要根据模具的结构和产品的壁厚情况合理调整参数。
3. 加热和热流道系统将热流道系统中的热流道板、热流道头安装到模具上,并按照设计要求进行连接。
然后,根据注塑材料的熔融温度和模具的冷却要求,调整热流道系统的温度。
温度过高或过低都可能影响产品的质量。
4. 定位模具将模具安装到注塑机的合适位置,并根据产品的要求进行定位调整。
确保模具和注塑机的对位精度,以免产生不必要的浪费或质量问题。
5. 注塑调试根据注塑机的工作要求和注塑工艺参数,将注塑材料投入到注塑机的料斗中,并通过零件触发开关启动注塑过程。
同时,注意观察注塑机的工作状态,检查是否有异常情况发生。
如果发现有异常,应及时停机检修。
6. 调整注塑工艺参数根据调试的情况和产品质量要求,对注塑工艺参数进行逐步调整。
例如,根据产品的缺陷情况调整注射速度、保压时间和保压压力等参数。
7. 检查产品质量在调试过程中,要不断检查产品的质量。
可以将少量试产出来进行检验,判断产品的表面质量、尺寸精度和物理性能是否符合要求。
如有问题,可以根据检查结果继续调整工艺参数,直到达到要求为止。
8. 记录调试参数在调试过程中,要详细记录每次调整的参数和调试结果,包括工艺参数、产品质量和异常情况等。
这样,在以后的生产中就可以参考这些记录,提高生产效率和产品质量。
9. 培训操作人员在调试完成后,要对操作人员进行培训,使其熟悉操作流程和注意事项。
注塑工艺调试验证技术规范
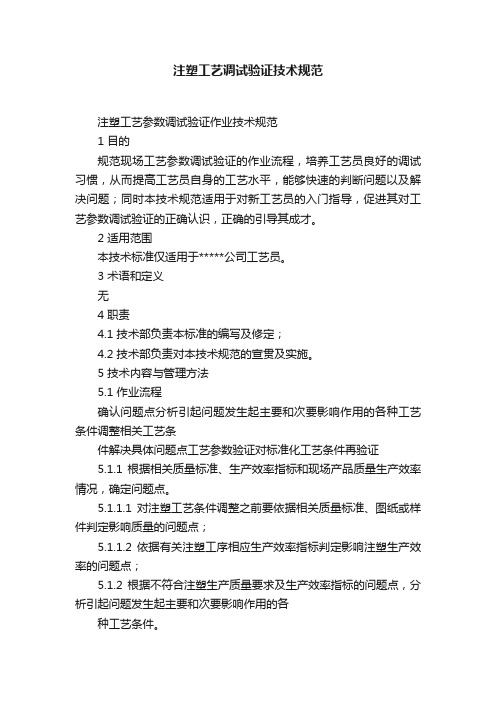
注塑工艺调试验证技术规范注塑工艺参数调试验证作业技术规范1 目的规范现场工艺参数调试验证的作业流程,培养工艺员良好的调试习惯,从而提高工艺员自身的工艺水平,能够快速的判断问题以及解决问题;同时本技术规范适用于对新工艺员的入门指导,促进其对工艺参数调试验证的正确认识,正确的引导其成才。
2 适用范围本技术标准仅适用于*****公司工艺员。
3 术语和定义无4 职责4.1 技术部负责本标准的编写及修定;4.2 技术部负责对本技术规范的宣贯及实施。
5 技术内容与管理方法5.1 作业流程确认问题点分析引起问题发生起主要和次要影响作用的各种工艺条件调整相关工艺条件解决具体问题点工艺参数验证对标准化工艺条件再验证5.1.1 根据相关质量标准、生产效率指标和现场产品质量生产效率情况,确定问题点。
5.1.1.1 对注塑工艺条件调整之前要依据相关质量标准、图纸或样件判定影响质量的问题点;5.1.1.2 依据有关注塑工序相应生产效率指标判定影响注塑生产效率的问题点;5.1.2 根据不符合注塑生产质量要求及生产效率指标的问题点,分析引起问题发生起主要和次要影响作用的各种工艺条件。
5.1.2.1 对问题点的分析应从人、机、料、法、环五方面全面分析从中选择对问题发生起主要影响的工艺条件;5.1.2.2 根据具体问题点,分析步骤如下:5.1.2.2.1 人员操作方面对注塑生产波动的影响因素:(1)在岗人员是否经过岗前培训并具备相应的操作技能;(2)人员配置是否合理;(3)操作者的操作均衡性是否满足生产节拍;(4)操作工的操作动作是否符合操作规程要求或特殊作业规范;(5)操作人员是否熟练并且定岗;(6)调试者本人是否接受相应的技能培训,并具备相关调试技能。
5.1.2.2.2 机器设备(包括模具)对注塑生产的影响因素:(1)注塑机的加温系统是否运作正常,并能使料筒加工温度在注塑工艺所要求加工温度范围内保持稳定,特别要注意射嘴温控正常;(2)射嘴的口径长度是否适用于该模具,射嘴的球面R与模具浇口套是否适用;(3)设备性能是否达到工艺要求,并且状态良好和稳定,注塑机压力、速度等其它参数设定值与工艺要求值的大小有无较大偏差;(4)注塑机各种参数在不同生产周期内有无大的波动从而使注塑生产发生周期波动;(5)注塑机各种动作是否动作正常,对保证正常生产周期有无影响;(6)注塑机油路、落料口的冷却运水是否通畅;(7)外设辅助设备是否正常运转(如气辅、模内热转印、液压抽芯、油站等);(8)模具开合动作是否正常;(9)模具的特殊结构或产品结构的特殊性是否影响注塑调试的工艺性;(10)模具各部分温度是否达到工艺要求,其温控系统是否正常(如冷却运水是否通畅,热水机温度控制系统是否工作正常,热流道系统及温控箱是否正常等);(11)模具顶出机构是否动作正常,模具的动作顺序是否及顺畅;5.1.2.2.3 材料对注塑生产的影响因素:(1)所使用塑料、色母、添加剂等的种类以及牌号是否符合工艺配方要求或取得客户认可;(2)所使用的塑料、色母牌号是否经过检测并且其各种性能达到国家标准或国际标准;(3)混料工序是否符合工艺要求;(4)塑料在注塑生产前有无进行干燥或预处理;(5)材料的加工温度是否符合工艺要求范围;(6)材料是否能实现连续加料;(7)材料是否能实现连续落料,色母料、原料、水口料混合及输送落料均匀;(8)材料从混料、包装、运输、加料、注塑、加工过程中是否能保证清洁不受外来污染;(9)螺杆中有无其他不同材料会影响到所使用到材料的颜色、性能等;5.1.2.2.4 注塑工艺方法对注塑生产的影响因素:(1)依据相关注塑工艺理论知识,判定目前工艺参数的合理性;(2)针对具体问题点所采用的工艺参数设定是否按工艺卡及相关要求进行;(3)目前的参数设定中对产品生产波动较大的参数是哪个?5.1.2.2.5 环境变化对注塑生产影响因素分析:(1)空气的干燥、潮湿度对注塑生产有影响;(2)气温变化对注塑生产、模具冷却及冷却水冷凝水的多少都有影响;(3)现场合理划分生产操作空间和成品存放区有利于保证产品质量;(4)生产现场的卫生条件对注塑件的质量有一定的影响,如粉尘及油污等;(5)台面及机台附近定置是否符合要求;5.1.2.3 分析影响注塑生产的工艺条件时应注意:同一个问题可能同时受几个工艺条件影响而引起,分析时尽量做到全面并抓住重点,而同一工艺条件可能会导致几个问题发生,则要求要结合几个问题一起分析,不可孤立单个问题考虑,避免解决一个问题又产生另一个问题;5.1.2.4 经过分析属于在生产现场通过工艺条件的改善能实现正常生产的应及时在现场解决;而在现场无法完善并正进行生产时应果断停止生产,并对相关要素进行整改(模具、设备、材料、环境、人员培训);5.1.3 针对影响注塑生产的工艺条件进行改进, 调整相关工艺条件解决具体问题点。
注塑部制程检验规程
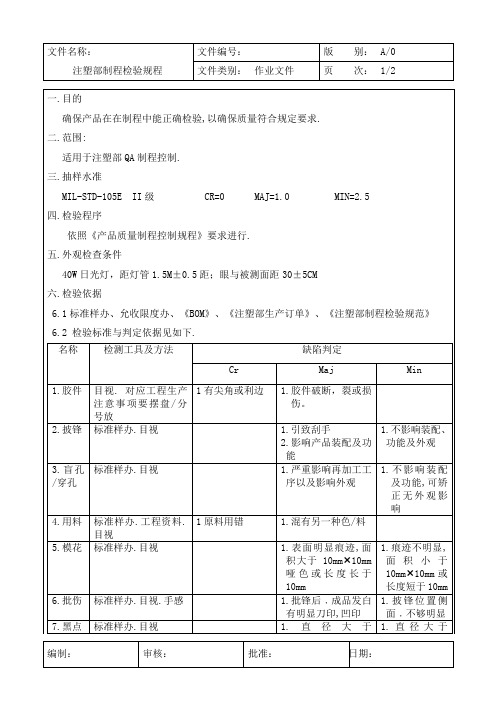
6.1标准样办、允收限度办、《BOM》、《注塑部生产订单》、《注塑部制程检验规范》
6.2检验标准与判定依据见如下.
名称
检测工具及方法
缺陷判定
Cr
Maj
Min
1.胶件
目视.对应工程生产注意事项要摆盘/分号放
1有尖角或利边
1.胶件破断,裂或损伤。
2.披锋
标准样办.目视
1.引致刮手
2.影响产品装配及功能
11.走胶不够
标准样办.目视.
1.产品表面影响组装、功能、外观
1.产品内面,不影响组装、功能、外观
12.顶白标准ຫໍສະໝຸດ 办.目视.1.表面有凸手感觉同一表面明显可见
1.没有凸手感觉
同一表面不易看到
13.烧焦
标准样办.目视.
1.面积大于10mm2
1.面积小于10mm2
14.混色
标准样办.目视.
1.同一表面明显可见
1.不影响装配、功能及外观
3.盲孔/穿孔
标准样办.目视
1.严重影响再加工工序以及影响外观
1.不影响装配及功能,可矫正无外观影响
4.用料
标准样办.工程资料.目视
1原料用错
1.混有另一种色/料
5.模花
标准样办.目视
1.表面明显痕迹,面积大于10mm10mm哑色或长度长于10mm
1.痕迹不明显,面积小于10mm10mm或长度短于10mm
一.目的
确保产品在在制程中能正确检验,以确保质量符合规定要求.
二.范围:
适用于注塑部QA制程控制.
三.抽样水准
MIL-STD-105E II级CR=0 MAJ=1.0 MIN=2.5
四.检验程序
依照《产品质量制程控制规程》要求进行.
注塑制程检验作业规范

1目的建立本公司质量检验作业流程及管制规范,确保产品质量符合要求。
2范围适用于注塑业务单元,过程、成品品质管控。
3职责3.1生产:负责产品调试,操作方法指导,产品包装执行。
3.2品质:负责首件确认、过程控制、记录、标识和不良隔离、追溯.信息反馈与跟进. 3.3技术:负责技术不良分析与改善对策提升技术服务。
3.4 工模:负责不良模具的修理达到有效与提报验证。
4首件检验4.1注塑技术员(调试)在批量生产前将修模,换模,换料,仃机后开产调试稳定工艺的产品,进行自检合格的整模样品交给IPQC检验员确认,(IPQC检验员应提前参与)。
4.2、IPQC检验员根据《生产计划表》确认物料、规格是否与要求一致,并依据《来料检验标准》,对该整模首样进行检验,检验合格的,则在首件样品上贴检验标识,交还送检人,由送检人将首件样品放置在生产机台上,此样品,作为生产过程的检验依据,检验员在《QC 检验报表》上注明检验结果,并通知车间生产。
4.3、检验不合格,则将不合格内容记录于《QC检验报表》上,连同首件样品一起交还送检人,送检人应对不良进行调整,自检合格后重新送检。
5过程控制5.1检验员应对产品A,B,C类分类检验,如A类产品2小时检验,A类产品如(蜘蛛标签,乌龟标签,天线,解码类)B类3小时检验,B类产品如(酒瓶标签,保护盒类)C 类4小时检验C类产品如(硬标签,开锁器类,附件,墨水类),机台巡检每次抽检一整模,操作员已完成自检的装箱产品,每次抽查按每箱数量根据检验标准(允收水准表)进行抽检(内包含整模产品)。
5.2.对员工过程检出的不良品(红筐内)进行确认,若有良品进行与员工沟通判定标准与方法指导,减小员工误判,并在《QC检验报表》记要体现。
5.3、检验项目参照《来料检验标准》。
5.4、检验合格,则将检验结果记录于《QC检验报表》上,报告要求记录清晰,不能涂改(可用笔划掉),记录要求真实有效,便于后续查核。
6成品检验控制生产过程装箱产品移到规定持检区内,检验员每隔2-4时进行分批抽检,抽检标准若有按《来料检验标准》,经抽检合格后,在箱侧面《产品流动标识卡》的右角上加盖“合格”章,作为检验合格标记,并在系统上进行判定,由车间办理入库。
- 1、下载文档前请自行甄别文档内容的完整性,平台不提供额外的编辑、内容补充、找答案等附加服务。
- 2、"仅部分预览"的文档,不可在线预览部分如存在完整性等问题,可反馈申请退款(可完整预览的文档不适用该条件!)。
- 3、如文档侵犯您的权益,请联系客服反馈,我们会尽快为您处理(人工客服工作时间:9:00-18:30)。
注塑工艺参数调试验证作业技术规范
1 目的
规范现场工艺参数调试验证的作业流程,培养工艺员良好的调试习惯,从而提高工艺员自身的工艺水平,能够快速的判断问题以及解决问题;同时本技术规范适用于对新工艺员的入门指导,促进其对工艺参数调试验证的正确认识,正确的引导其成才。
2 适用范围
本技术标准仅适用于*****公司工艺员。
3 术语和定义
无
4 职责
4.1 技术部负责本标准的编写及修定;
4.2 技术部负责对本技术规范的宣贯及实施。
5 技术内容与管理方法
5.1 作业流程
确认问题点分析引起问题发生起主要和次要影响作用的各种工艺条件调整相关工艺条
件解决具体问题点工艺参数验证对标准化工艺条件再验证
5.1.1 根据相关质量标准、生产效率指标和现场产品质量生产效率情况,确定问题点。
5.1.1.1 对注塑工艺条件调整之前要依据相关质量标准、图纸或样件判定影响质量的问题点;
5.1.1.2 依据有关注塑工序相应生产效率指标判定影响注塑生产效率的问题点;
5.1.2 根据不符合注塑生产质量要求及生产效率指标的问题点,分析引起问题发生起主要和次要影响作用的各
种工艺条件。
5.1.2.1 对问题点的分析应从人、机、料、法、环五方面全面分析从中选择对问题发生起主要影响的工艺条件;
5.1.2.2 根据具体问题点,分析步骤如下:
5.1.2.2.1 人员操作方面对注塑生产波动的影响因素:
(1)在岗人员是否经过岗前培训并具备相应的操作技能;
(2)人员配置是否合理;
(3)操作者的操作均衡性是否满足生产节拍;
(4)操作工的操作动作是否符合操作规程要求或特殊作业规范;
(5)操作人员是否熟练并且定岗;
(6)调试者本人是否接受相应的技能培训,并具备相关调试技能。
5.1.2.2.2 机器设备(包括模具)对注塑生产的影响因素:
(1)注塑机的加温系统是否运作正常,并能使料筒加工温度在注塑工艺所要求加工温度范围内保持稳
定,特别要注意射嘴温控正常;
(2)射嘴的口径长度是否适用于该模具,射嘴的球面R与模具浇口套是否适用;
(3)设备性能是否达到工艺要求,并且状态良好和稳定,注塑机压力、速度等其它参数设定值与工艺
要求值的大小有无较大偏差;
(4)注塑机各种参数在不同生产周期内有无大的波动从而使注塑生产发生周期波动;
(5)注塑机各种动作是否动作正常,对保证正常生产周期有无影响;
(6)注塑机油路、落料口的冷却运水是否通畅;(7)外设辅助设备是否正常运转(如气辅、模内热转印、
液压抽芯、油站等);
(8)模具开合动作是否正常;
(9)模具的特殊结构或产品结构的特殊性是否影响注塑调试的工艺性;
(10)模具各部分温度是否达到工艺要求,其温控系统是否正常(如冷却运水是否通畅,热水机温度
控制系统是否工作正常,热流道系统及温控箱是否正常等);
(11)模具顶出机构是否动作正常,模具的动作顺序是否及顺畅;
5.1.2.2.3 材料对注塑生产的影响因素:
(1)所使用塑料、色母、添加剂等的种类以及牌号是否符合工艺配方要求或取得客户认可;
(2)所使用的塑料、色母牌号是否经过检测并且其各种性能达到国家标准或国际标准;
(3)混料工序是否符合工艺要求;
(4)塑料在注塑生产前有无进行干燥或预处理;
(5)材料的加工温度是否符合工艺要求范围;
(6)材料是否能实现连续加料;
(7)材料是否能实现连续落料,色母料、原料、水口料混合及输送落料均匀;
(8)材料从混料、包装、运输、加料、注塑、加工过程中是否能保证清洁不受外来污染;
(9)螺杆中有无其他不同材料会影响到所使用到材料的颜色、性能等;
5.1.2.2.4 注塑工艺方法对注塑生产的影响因素:
(1)依据相关注塑工艺理论知识,判定目前工艺参数的合理性;
(2)针对具体问题点所采用的工艺参数设定是否按工艺卡及相关要求进行;
(3)目前的参数设定中对产品生产波动较大的参数是哪个?
5.1.2.2.5 环境变化对注塑生产影响因素分析:
(1)空气的干燥、潮湿度对注塑生产有影响;
(2)气温变化对注塑生产、模具冷却及冷却水冷凝水的多少都有影响;
(3)现场合理划分生产操作空间和成品存放区有利于保证产品质量;
(4)生产现场的卫生条件对注塑件的质量有一定的影响,如粉尘及油污等;
(5)台面及机台附近定置是否符合要求;
5.1.2.3 分析影响注塑生产的工艺条件时应注意:同一个问题可能同时受几个工艺条件影响而引起,分析时尽
量做到全面并抓住重点,而同一工艺条件可能会导致几个问题发生,则要求要结合几个问题一起分析,不可孤立单个问题考虑,避免解决一个问题又产生另一个问题;
5.1.2.4 经过分析属于在生产现场通过工艺条件的改善能实现正常生产的应及时在现场解决;而在现场无法完
善并正进行生产时应果断停止生产,并对相关要素进行整改(模具、设备、材料、环境、人员培训);
5.1.3 针对影响注塑生产的工艺条件进行改进, 调整相关工艺条件解决具体问题点。
5.1.3.1 根据上述步骤分析出影响注塑生产的工艺条件,参照工艺卡及相关工艺文件要求进行小范围调整,注
意调整工艺条件时应逐一进行调整,不可同时实施多个条件大范围变更,否则难以判定调试的效果和
影响程度;
5.1.3.2 调整过程中实施一次更改后,要检查前一次更改后的效果,确认后并实施下一步调整后方可进行下一
次注塑,以免造成材料、机时的浪费,不允许不确认调试结果而直接进入下一次注塑生产,造成废品增多的现象;
5.1.3.3 经过工艺条件的调整和验证得到理想效果后,应保持该工艺条件进一步进行验证,直到在该工艺条件
下,所注塑制件能保证稳定的生产和质量达到标准要求;
5.1.3.4 若在规定的时间内,通过实施有限的工艺条件调整仍不能达到理想效果,应停止生产,并采取相应的
攻关手段;
5.1.3.5 如实填写《工艺参数调试记录表》以及《不均衡生产记录》;
5.1.4 对经调整后可达到注塑生产要求的工艺条件进行工艺参数验证。
5.1.4.1 按标准完成工艺条件的准备与输入;
5.1.4.2 依据相关质量标准或生产效率指标判定注塑工序的结果是否达到要求;
5.1.4.3 验证不能达到要求的工艺条件遵循此技术规范中的第1、2步“判定问题点”和“分析引起问题发生起
主要影响作用的工艺条件”中的步骤进行重新工艺条件的调整;
5.1.4.4 对调整后的工艺条件依据质量标准或生产效率指标进行验证;
5.1.4.5 将经过验证后达到质量标准或生产效率指标要求的工艺条件制定标准化工艺条件;
5.1.4.6 填写《工艺标准化验证记录表》;
5.1.5 按照第4步工艺参数验证有关步骤对标准化工艺条件进行验证和调整,并再次制定标准化工艺条件,填
写《工艺标准化验证记录表》。
5.2 工艺参数调试验证的管理
5.2.1 本规范规定了注塑工艺调试分析问题的步骤,对解决具体的问题时也可以直接采取跳跃思维直接找出主
要的要素进行分析和制定整改措施;
5.2.2 有关工艺调试的技巧及具体工艺问题调试方法参考《新编调机员培训教材》的相关内容进行学习,并在
实践当中不断积累经验提高自身注塑技能;
5.2.3 注塑工艺参数调试验证的过程应该坚持持续改进的过程,在不断验证整改的过程制定最优化的参数应用
于生产中;
5.2.4 注塑生产要特别强调的是各种工艺条件的稳定控制和生产操作的均衡性,这比任何工作都重要!!!因此
工艺参数调试前必须先确认各项工艺条件是否满足规定的要求?否则必须先对工艺条件进行改善后才进行工艺参数调整!!!同时调试过程要保证每次调试结果确认后才进行下一步的调试,不要盲目调试,这样可很好的缩短调试时间和减少调试废品。
5.2.5 只有经公司授权的技术人员有权对工艺参数进行调试验证,其余不相关人一律不许对工艺参数作任何变
动。
6 记录表单
1)《工艺参数调试记录表》
2)《工艺标准化验证记录表》
7附录
无
----------------------。