汽机工艺流程简介
汽轮机叶片制造工艺过程

轴流式蒸汽轮机动叶片制造工艺简述摘要:介绍了汽轮机等截面直叶片、自由成型叶片、有成型规律叶片汽道加工的毛坯制造、型面加工工艺过程,并介绍了五联动加工中心的基本特点,简单说明了汽轮机叶片几种特种加工方法的基本原理。
关键字:汽轮机动叶片毛坯制造加工工艺特种加工一:汽轮机简介汽轮机是将蒸汽的能量转换为机械功的旋转式动力机械,是蒸汽动力装置的主要设备之一。
主要用作发电用的原动机,也可直接驱动各种泵、风机、压缩机和船舶螺旋桨等。
还可以利用汽轮机的排汽或中间抽汽满足生产和生活上的供热需要。
汽轮机是一种高温高压高速旋转的机械,尤其对于发电用汽轮机来说,又是大功率输出地原动力机械,所以设计要求汽轮机具有高效率,高安全可靠性,而且可调性要好。
目前我国发电用汽轮机以300~600MW居多,体积庞大,结构精细复杂。
由于多级轴流式汽轮机绝热焓降大,能够充分利用蒸汽的热能,因此绝大多数为发电用汽轮机均为多级轴流式汽轮机。
汽轮机本体主要由转动部分和静止部分两个方面组成。
转子包括主轴、叶轮、动叶片和联轴器等。
静子包括进汽部分、汽缸、隔板和静叶栅、汽封及轴承等。
因此汽轮机的制造工艺主要为上述部件的制造工艺。
汽轮机制造工艺的特点为:属单件生产,生产期长,材料品种多,材料性能要求高,零件种类多,加工精度高,设备要求高,操作技能要求高,机械加工工种齐全,设计冷热工艺且面广,检测手段齐备要求高,计量设备、测量工具齐全而且要求高采用专门工装多。
二:轴流式蒸汽轮机动叶片制造工艺1:叶片的结构静叶片一般由工作部分和安装部分组成动叶片一般由叶根、叶型部分和叶顶三部分组成2:叶片的工作条件及材料选择叶片的工作条件复杂,除因高速旋转和气流作用而承受较高的静应力和动应力外,还因其分别处在过热蒸汽区、两相过渡区、和湿蒸汽区段内工作而承受高温、高压、腐蚀和冲蚀作用。
因此叶片的材料要满足以下要求:良好的常温和高温机械性能、良好的抗蚀性、良好的减震性、和一定的耐磨性良好的冷热加工性能。
蒸汽余热发电工艺流程讲解
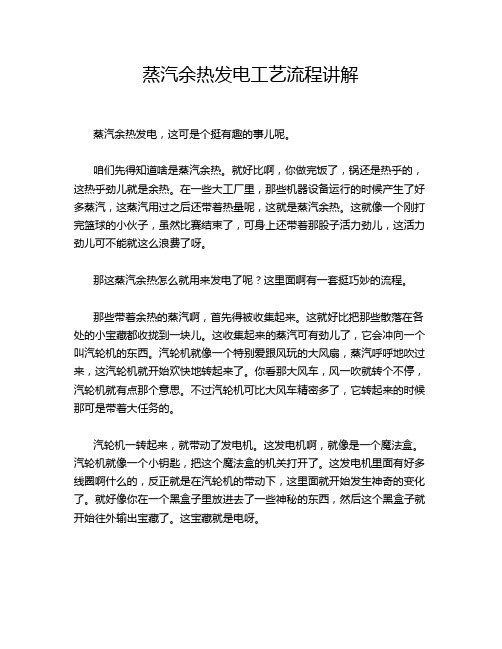
蒸汽余热发电工艺流程讲解蒸汽余热发电,这可是个挺有趣的事儿呢。
咱们先得知道啥是蒸汽余热。
就好比啊,你做完饭了,锅还是热乎的,这热乎劲儿就是余热。
在一些大工厂里,那些机器设备运行的时候产生了好多蒸汽,这蒸汽用过之后还带着热量呢,这就是蒸汽余热。
这就像一个刚打完篮球的小伙子,虽然比赛结束了,可身上还带着那股子活力劲儿,这活力劲儿可不能就这么浪费了呀。
那这蒸汽余热怎么就用来发电了呢?这里面啊有一套挺巧妙的流程。
那些带着余热的蒸汽啊,首先得被收集起来。
这就好比把那些散落在各处的小宝藏都收拢到一块儿。
这收集起来的蒸汽可有劲儿了,它会冲向一个叫汽轮机的东西。
汽轮机就像一个特别爱跟风玩的大风扇,蒸汽呼呼地吹过来,这汽轮机就开始欢快地转起来了。
你看那大风车,风一吹就转个不停,汽轮机就有点那个意思。
不过汽轮机可比大风车精密多了,它转起来的时候那可是带着大任务的。
汽轮机一转起来,就带动了发电机。
这发电机啊,就像是一个魔法盒。
汽轮机就像一个小钥匙,把这个魔法盒的机关打开了。
这发电机里面有好多线圈啊什么的,反正就是在汽轮机的带动下,这里面就开始发生神奇的变化了。
就好像你在一个黑盒子里放进去了一些神秘的东西,然后这个黑盒子就开始往外输出宝藏了。
这宝藏就是电呀。
可是啊,这蒸汽冲完了汽轮机之后,它还有点余热呢,可不能就这么把它放走了。
这时候啊,就有一个叫凝汽器的东西出现了。
这凝汽器就像是一个冷静的大管家,它把那些还有余热的蒸汽变成水。
这就好比把那些还带着余热的调皮小水滴一个个抓住,让它们变回原来安静的水的模样。
这个过程啊,也很重要呢。
如果不把蒸汽变成水,这整个流程就乱套了,就像一场没有指挥的音乐会,那可就糟糕透顶了。
变成水之后呢,这水又可以被重新加热变成蒸汽,然后再去冲汽轮机,就这样循环往复。
这就像一个永远不会累的小火车,一圈一圈地跑着,不断地把蒸汽余热变成电。
有人可能会问,这蒸汽余热发电到底有啥好处呢?这好处可多了去了。
你想啊,要是不利用这蒸汽余热发电,这些热量就白白浪费了,就像你把吃不完的粮食直接扔掉一样,多可惜啊。
简述汽轮机调节阀检修工艺流程
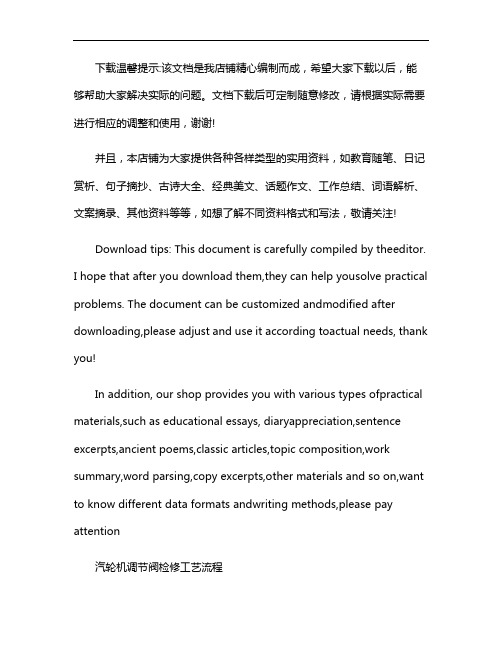
下载温馨提示:该文档是我店铺精心编制而成,希望大家下载以后,能够帮助大家解决实际的问题。
文档下载后可定制随意修改,请根据实际需要进行相应的调整和使用,谢谢!并且,本店铺为大家提供各种各样类型的实用资料,如教育随笔、日记赏析、句子摘抄、古诗大全、经典美文、话题作文、工作总结、词语解析、文案摘录、其他资料等等,如想了解不同资料格式和写法,敬请关注!Download tips: This document is carefully compiled by theeditor.I hope that after you download them,they can help yousolve practical problems. The document can be customized andmodified after downloading,please adjust and use it according toactual needs, thank you!In addition, our shop provides you with various types ofpractical materials,such as educational essays, diaryappreciation,sentence excerpts,ancient poems,classic articles,topic composition,work summary,word parsing,copy excerpts,other materials and so on,want to know different data formats andwriting methods,please pay attention汽轮机调节阀检修工艺流程一、工艺准备在进行汽轮机调节阀检修之前,需要做好以下准备工作:1. 确定停机时间:根据设备使用情况和维护计划,确定停机时间,并通知相关人员;2. 准备工具和材料:根据检修要求,准备所需的工具和材料,包括扳手、螺丝刀、密封圈、润滑油等;3. 检查安全措施:检查工作区域的安全措施是否到位,确保操作人员的安全。
汽轮机本体各部套工艺流程
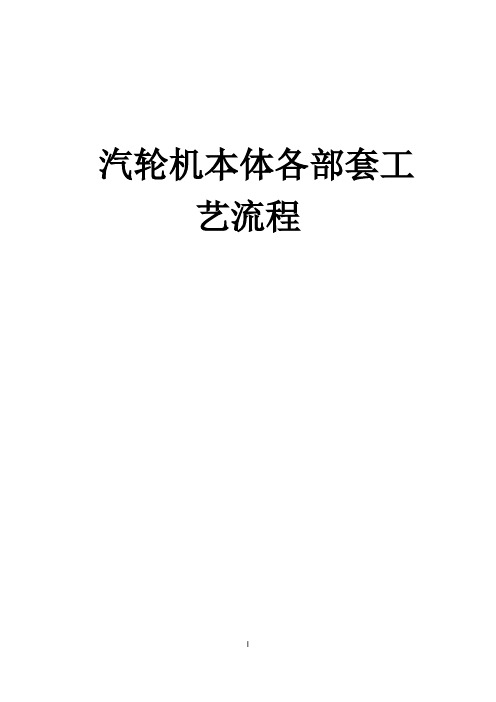
汽轮机本体各部套工艺流程目录目录 .................................................................................................................................................. I I 前言 .. (1)第一章转子 (2)1.转子简介 (2)2.转子材料 (2)3.工艺过程 (2)第二章动叶片 (4)1.动叶片简介 (4)2.动叶片材质 (5)3.动叶片工艺过程 (6)4.叶片安装 (9)第三章隔板套 (11)1.隔板套简介 (11)2.隔板套材质 (13)3.隔板套工艺过程 (13)4.隔板套安装 (19)第四章低压内缸 (22)1.低压内缸简介 (22)2.低压内缸材质 (22)3.低压内缸工艺过程 (22)4.低压内缸安装 (25)第五章低压外缸 (27)1.低压外缸简介 (27)2.低压外缸材质 (27)3.低压外缸加工工序 (27)4.低压外缸的安装 (30)第六章高压内缸 (32)1.高压内缸简介 (32)2.高压内缸材质 (32)3.高压内缸的加工工序 (32)4.高压内缸的安装 (35)第七章高压外缸 (36)1.高压外缸简介 (36)2、高压外缸材质 (36)3、高压外缸加工工序 (36)4.高压外缸的安装 (41)第八章阀门 (42)1.阀门简介 (42)2.阀门材质 (45)3.阀门加工工序 (45)4.阀门的安装 (52)第九章总装 (54)1.低压部分总装数据记录 (54)2.低压部分总装 (67)参考文献 (85)前言本书是由山西国锦煤电有限公司发电部学员张君瑞编写。
本书重点讲述汽轮机本体结构,详细阐述汽机本体各部套的加工工艺过程。
主要从原理、材料、工艺、安装等四个方面进行介绍。
由于编者水平有限,书中难免有不妥之处,诚恳希望广大读者批评指正。
汽机工作原理
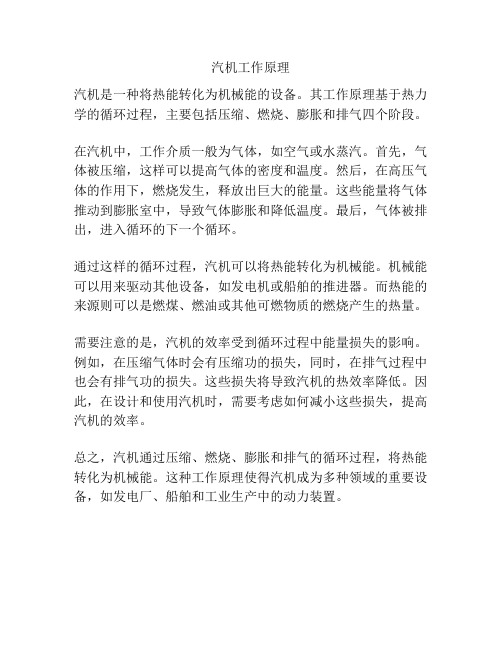
汽机工作原理
汽机是一种将热能转化为机械能的设备。
其工作原理基于热力学的循环过程,主要包括压缩、燃烧、膨胀和排气四个阶段。
在汽机中,工作介质一般为气体,如空气或水蒸汽。
首先,气体被压缩,这样可以提高气体的密度和温度。
然后,在高压气体的作用下,燃烧发生,释放出巨大的能量。
这些能量将气体推动到膨胀室中,导致气体膨胀和降低温度。
最后,气体被排出,进入循环的下一个循环。
通过这样的循环过程,汽机可以将热能转化为机械能。
机械能可以用来驱动其他设备,如发电机或船舶的推进器。
而热能的来源则可以是燃煤、燃油或其他可燃物质的燃烧产生的热量。
需要注意的是,汽机的效率受到循环过程中能量损失的影响。
例如,在压缩气体时会有压缩功的损失,同时,在排气过程中也会有排气功的损失。
这些损失将导致汽机的热效率降低。
因此,在设计和使用汽机时,需要考虑如何减小这些损失,提高汽机的效率。
总之,汽机通过压缩、燃烧、膨胀和排气的循环过程,将热能转化为机械能。
这种工作原理使得汽机成为多种领域的重要设备,如发电厂、船舶和工业生产中的动力装置。
汽机安装流程图(无工期有说明版)

这是一份非常规的安装工艺,在不影响安装质量的前提下,个别项目的施工可能满足不了规范要求的条件,也不能按现有的程序文件去管理。
以下是满足进度要求的基本条件。
1、低压内缸直接安装于基础,与外缸的连接方式?何时连接?凝汽器接缸对中心没有影响,但焊接会对中心产生影响,凝汽器内抽汽管道的安装,凝汽器联通管的安缸前应完成。
凝汽器与汽缸间应加钢板贴焊。
2、低压外缸与轴承座(汽封套)之间采用不锈钢膨胀节相连,位置不当时会否把轴承座拉跑,影响转子中心?需预先考虑对策。
3、所有设备、管道应在制造厂清理干净进行防护后发运,尤其对蒸汽室、进油管、翻砂部位。
4、制造厂在进行汽轮机设备装配前,应通知买方,将派遣安装单位人员参加组装、检测工作。
5、联轴器垫片厚度在现场确定,制造厂加工后应在扣缸联检前发运到现场。
6、转子联轴器(短轴)螺栓孔错位控制在0.02mm。
短轴在制造厂与转子进行装配,保证联轴器晃度符合要求,尽可能一体发运。
7、滑销系统在检修、安装过程中适时安排调整。
高压转子与汽缸在制造厂进行总体组装。
低压缸内部套与内缸进行组装,用假轴测量调整部套中心。
轴承座与台板、台板之间滑销,汽封套、隔板套、隔板的定位键应在制造厂调整好且牢靠固定。
8、所有管道应清洗,最大限度进行组合,减少现场工作量,尤其对于汽缸进汽管和MSR相关管道。
9、所有设备安装文件应在ATP+40前到达现场,以便提前制定安装工艺。
10、凝汽器、低加、油箱等设备应在ATP+46发运至现场,汽轮机除低压转子外的设备、MSR、发电机等主设备及专用工具到达现场时间不应迟于ATP+50。
11、基础中预埋的设备到达现场的时间应能满足土建工作要求。
12、汽门与转子同期到达现场。
13、设备到达现场后,卖方应及时派人参加到货验收及交付。
14、汽轮机辅助平台的强度应满足同时放置汽缸、转子等重件的要求。
设计院核算。
15、汽轮机辅助平台施工应满足凝汽器组装拖运、发电机静子吊装要求,还应满足汽轮机安装要求。
135mw汽机工艺流程

135mw汽机工艺流程
1、蒸汽进入汽轮机:高温高压蒸汽通过主蒸汽管道进入汽轮机,推动汽轮机转子旋转,将热能转换为机械能。
2、做功并输出电能:汽轮机转子带动发电机转子旋转,发电机将机械能转换为电能,并通过变压器升高电压,输送到电网中。
3、凝汽器冷凝:做完功的低压蒸汽进入凝汽器,被循环水冷却凝结成水,形成凝结水。
4、凝结水输送:凝结水通过凝结水泵输送至低压加热器,加热后送至除氧器。
5、除氧并输送至锅炉:在除氧器中,凝结水经过除氧处理,去除其中的氧气和其他不凝结气体,然后通过给水泵输送至锅炉,再次加热形成高温高压蒸汽,完成整个循环。
汽轮机直接空冷系统工艺流程
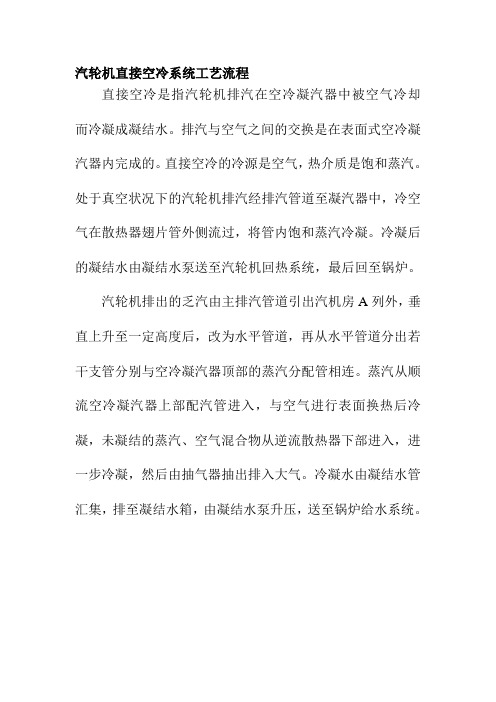
汽轮机直接空冷系统工艺流程直接空冷是指汽轮机排汽在空冷凝汽器中被空气冷却而冷凝成凝结水。
排汽与空气之间的交换是在表面式空冷凝汽器内完成的。
直接空冷的冷源是空气,热介质是饱和蒸汽。
处于真空状况下的汽轮机排汽经排汽管道至凝汽器中,冷空气在散热器翅片管外侧流过,将管内饱和蒸汽冷凝。
冷凝后的凝结水由凝结水泵送至汽轮机回热系统,最后回至锅炉。
汽轮机排出的乏汽由主排汽管道引出汽机房A列外,垂直上升至一定高度后,改为水平管道,再从水平管道分出若干支管分别与空冷凝汽器顶部的蒸汽分配管相连。
蒸汽从顺流空冷凝汽器上部配汽管进入,与空气进行表面换热后冷凝,未凝结的蒸汽、空气混合物从逆流散热器下部进入,进一步冷凝,然后由抽气器抽出排入大气。
冷凝水由凝结水管汇集,排至凝结水箱,由凝结水泵升压,送至锅炉给水系统。
直接空冷系统工作原理在直接空冷系统中,既要提高传热性能,又需防止凝结水冻结,空冷凝汽器绝大多数采用顺逆流联合方式的结构,即由顺流(指蒸汽和凝结水的相对流动方向一致)管束和逆流管束两部分组成。
顺流管束是冷凝蒸汽的主要部分,可冷凝80%左右的蒸汽。
剩余蒸汽携带不凝气体进入逆流式管束,在其中蒸汽由下而上,凝结水由上而下。
设置逆流管束主要是为了能够比较顺畅地将系统内的空气和不凝结气体排出,避免运行中在空冷凝汽器内的某些部位形成死区、冬季形成冻结的情况,同时因为逆流式空冷凝汽器还要冷凝剩余的部分排汽,在空冷凝汽器翅片管热交换过程中,排汽与管外空气热交换包含了与管壁凝结水膜的热交换。
此时无论是顺流还是逆流管束,其管内的水膜被加热,保持较好的等温状态而避免了冻结。
以我厂二期空冷系统为例,空冷凝汽器一共分8列,每一列共7个单元,其中第1、2、4、5、7单元为顺流单元,每一个单元包括10个翅片管束,每个管束有40根翅片管;第3、6单元为混流单元,每个混流单元的10个翅片管束中6个管束为逆流管束,4个管束为顺流管束,即逆流管束占混流单元的3/5。
汽轮机叶片制造工艺流程

汽轮机叶片制造工艺流程英文回答:Turbine Blade Manufacturing Process Flow.The manufacturing process of turbine blades involves several intricate steps that adhere to stringent quality standards to ensure optimal performance and durability. Here is a comprehensive overview of the typical workflow:1. Design and Engineering.The initial stage comprises the design and engineering of the turbine blades, meticulously considering factors such as airfoil shape, material selection, and structural integrity. Advanced computer-aided design (CAD) software is utilized to create virtual models, enabling engineers to optimize blade geometry and predict its aerodynamic behavior under various operating conditions.2. Raw Material Inspection and Preparation.The next step entails rigorous inspection of the raw materials, typically high-strength alloys or superalloys, to verify their composition, mechanical properties, and adherence to specifications. The raw materials undergo thorough testing to ensure they meet the stringent demands of the application. Subsequently, the materials are subjected to appropriate pre-processing, such as forging or casting, to achieve the desired shape and metallurgical characteristics.3. Blade Forging.Forging is a critical process in the manufacturing of turbine blades, imparting the necessary shape and grain structure to the material. It involves subjecting the workpiece to controlled mechanical forces, such as hammering or pressing, while it is heated to a specific temperature range. This process enhances the blade's strength, ductility, and resistance to creep and fatigue.4. Blade Casting.Casting is another widely employed technique for producing turbine blades. It involves pouring molten metal into a mold with the desired blade shape. The mold is carefully designed to control the solidification process, ensuring the formation of a sound and defect-free blade. Casting allows for the production of complex blade geometries with intricate internal cooling passages.5. Heat Treatment.After forging or casting, the blades undergo heat treatment processes tailored to the specific material and application requirements. Heat treatment involves subjecting the blades to a controlled sequence of heating, holding, and cooling cycles to achieve the desired metallurgical properties, including hardness, toughness, and corrosion resistance.6. Machining and Finishing.The forged or cast blades are subjected to precision machining operations, such as milling, grinding, and polishing, to achieve the final blade shape and surface finish. These processes ensure the blade's dimensional accuracy, surface smoothness, and aerodynamic efficiency. Advanced machining techniques, such as five-axis machining, enable the production of complex blade geometries with high precision.7. Coating.To enhance the blade's performance, durability, and resistance to wear, erosion, and oxidation, specialized coatings are applied to its surfaces. These coatings can be metallic, ceramic, or composite materials and are typically applied using techniques such as thermal spraying, physical vapor deposition (PVD), or chemical vapor deposition (CVD).8. Inspection and Testing.Throughout the manufacturing process, rigorous inspections and tests are performed to ensure the qualityand integrity of the turbine blades. Non-destructivetesting (NDT) techniques, such as ultrasonic inspection, radiographic testing, and dye penetrant testing, are employed to detect any internal defects or surface imperfections. Additionally, mechanical testing, such as tensile testing and fatigue testing, is conducted to verify the blade's strength and durability under various operating conditions.9. Assembly and Commissioning.The final step involves the assembly of the turbine blades into the rotor or stator assemblies, followed by commissioning and testing of the complete turbine system. Commissioning ensures that the turbine operates as intended, meets performance specifications, and complies with safety and regulatory standards.中文回答:汽轮机叶片制造工艺流程。
使用蒸汽的工艺流程
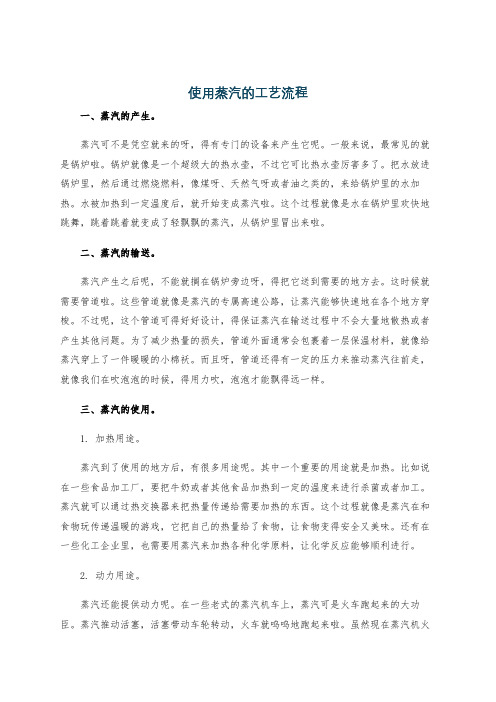
使用蒸汽的工艺流程一、蒸汽的产生。
蒸汽可不是凭空就来的呀,得有专门的设备来产生它呢。
一般来说,最常见的就是锅炉啦。
锅炉就像是一个超级大的热水壶,不过它可比热水壶厉害多了。
把水放进锅炉里,然后通过燃烧燃料,像煤呀、天然气呀或者油之类的,来给锅炉里的水加热。
水被加热到一定温度后,就开始变成蒸汽啦。
这个过程就像是水在锅炉里欢快地跳舞,跳着跳着就变成了轻飘飘的蒸汽,从锅炉里冒出来啦。
二、蒸汽的输送。
蒸汽产生之后呢,不能就搁在锅炉旁边呀,得把它送到需要的地方去。
这时候就需要管道啦。
这些管道就像是蒸汽的专属高速公路,让蒸汽能够快速地在各个地方穿梭。
不过呢,这个管道可得好好设计,得保证蒸汽在输送过程中不会大量地散热或者产生其他问题。
为了减少热量的损失,管道外面通常会包裹着一层保温材料,就像给蒸汽穿上了一件暖暖的小棉袄。
而且呀,管道还得有一定的压力来推动蒸汽往前走,就像我们在吹泡泡的时候,得用力吹,泡泡才能飘得远一样。
三、蒸汽的使用。
1. 加热用途。
蒸汽到了使用的地方后,有很多用途呢。
其中一个重要的用途就是加热。
比如说在一些食品加工厂,要把牛奶或者其他食品加热到一定的温度来进行杀菌或者加工。
蒸汽就可以通过热交换器来把热量传递给需要加热的东西。
这个过程就像是蒸汽在和食物玩传递温暖的游戏,它把自己的热量给了食物,让食物变得安全又美味。
还有在一些化工企业里,也需要用蒸汽来加热各种化学原料,让化学反应能够顺利进行。
2. 动力用途。
蒸汽还能提供动力呢。
在一些老式的蒸汽机车上,蒸汽可是火车跑起来的大功臣。
蒸汽推动活塞,活塞带动车轮转动,火车就呜呜地跑起来啦。
虽然现在蒸汽机火车比较少见了,但是在一些工业设备里,蒸汽依然可以作为动力源,驱动各种机械部件运动。
这就像是蒸汽有一双大力水手的手臂,在那里不停地推着东西动起来。
四、蒸汽的冷凝回收。
蒸汽用过之后可不能就这么白白地放掉呀,这多浪费呀。
所以呢,还有一个重要的环节就是蒸汽的冷凝回收。
蒸汽锅炉工艺流程

蒸汽锅炉工艺流程
《蒸汽锅炉工艺流程》
蒸汽锅炉是一种将水转化为蒸汽,用于供暖、发电或其他工业用途的设备。
蒸汽锅炉的工艺流程包括给水处理、燃烧系统、蒸汽发生和排放系统。
首先,给水处理是蒸汽锅炉工艺流程中一个非常重要的步骤。
给水处理的目的是去除水中的杂质和氧化物,以防止腐蚀和沉积物的形成。
这一步骤包括除氧、软化和净化处理,确保提供给锅炉的水质符合标准。
其次,燃烧系统是将燃料燃烧产生热量的过程。
燃料可以是煤、燃油、天然气或生物质等。
在燃烧室中,燃料与空气混合并燃烧,产生高温燃气,利用这些燃气加热水使其转化为蒸汽。
接着,蒸汽发生是蒸汽锅炉工艺流程的核心步骤。
在锅炉中,水受热变为蒸汽,蒸汽随后被输送到需要的地方,如蒸汽发电机或供暖系统。
蒸汽的温度和压力取决于锅炉设计和运行条件。
最后,排放系统是将燃烧后的废气和残余物排出锅炉的环节。
排放系统需要符合环保标准,通常通过烟囱或排气管道将废气排放到大气中,或者经过处理再排放。
总的来说,蒸汽锅炉工艺流程包括给水处理、燃烧系统、蒸汽发生和排放系统。
这些步骤相互关联,确保蒸汽锅炉的高效、安全运行,同时尽量减少对环境的影响。
汽轮机叶片制造工艺过程

轴流式蒸汽轮机动叶片制造工艺简述摘要:介绍了汽轮机等截面直叶片、自由成型叶片、有成型规律叶片汽道加工的毛坯制造、型面加工工艺过程,并介绍了五联动加工中心的基本特点,简单说明了汽轮机叶片几种特种加工方法的基本原理。
关键字:汽轮机动叶片毛坯制造加工工艺特种加工一:汽轮机简介汽轮机是将蒸汽的能量转换为机械功的旋转式动力机械,是蒸汽动力装置的主要设备之一。
主要用作发电用的原动机,也可直接驱动各种泵、风机、压缩机和船舶螺旋桨等。
还可以利用汽轮机的排汽或中间抽汽满足生产和生活上的供热需要。
汽轮机是一种高温高压高速旋转的机械,尤其对于发电用汽轮机来说,又是大功率输出地原动力机械,所以设计要求汽轮机具有高效率,高安全可靠性,而且可调性要好。
目前我国发电用汽轮机以300~600MW居多,体积庞大,结构精细复杂。
由于多级轴流式汽轮机绝热焓降大,能够充分利用蒸汽的热能,因此绝大多数为发电用汽轮机均为多级轴流式汽轮机。
汽轮机本体主要由转动部分和静止部分两个方面组成。
转子包括主轴、叶轮、动叶片和联轴器等。
静子包括进汽部分、汽缸、隔板和静叶栅、汽封及轴承等。
因此汽轮机的制造工艺主要为上述部件的制造工艺。
汽轮机制造工艺的特点为:属单件生产,生产期长,材料品种多,材料性能要求高,零件种类多,加工精度高,设备要求高,操作技能要求高,机械加工工种齐全,设计冷热工艺且面广,检测手段齐备要求高,计量设备、测量工具齐全而且要求高采用专门工装多。
二:轴流式蒸汽轮机动叶片制造工艺1:叶片的结构静叶片一般由工作部分和安装部分组成动叶片一般由叶根、叶型部分和叶顶三部分组成2:叶片的工作条件及材料选择叶片的工作条件复杂,除因高速旋转和气流作用而承受较高的静应力和动应力外,还因其分别处在过热蒸汽区、两相过渡区、和湿蒸汽区段内工作而承受高温、高压、腐蚀和冲蚀作用。
因此叶片的材料要满足以下要求:良好的常温和高温机械性能、良好的抗蚀性、良好的减震性、和一定的耐磨性良好的冷热加工性能。
汽轮机叶片制造工艺过程

轴流式蒸汽轮机动叶片制造工艺简述摘要:介绍了汽轮机等截面直叶片、自由成型叶片、有成型规律叶片汽道加工的毛坯制造、型面加工工艺过程,并介绍了五联动加工中心的基本特点,简单说明了汽轮机叶片几种特种加工方法的基本原理。
关键字:汽轮机动叶片毛坯制造加工工艺特种加工一:汽轮机简介汽轮机是将蒸汽的能量转换为机械功的旋转式动力机械,是蒸汽动力装置的主要设备之一。
主要用作发电用的原动机,也可直接驱动各种泵、风机、压缩机和船舶螺旋桨等。
还可以利用汽轮机的排汽或中间抽汽满足生产和生活上的供热需要。
汽轮机是一种高温高压高速旋转的机械,尤其对于发电用汽轮机来说,又是大功率输出地原动力机械,所以设计要求汽轮机具有高效率,高安全可靠性,而且可调性要好。
目前我国发电用汽轮机以300~600MW居多,体积庞大,结构精细复杂。
由于多级轴流式汽轮机绝热焓降大,能够充分利用蒸汽的热能,因此绝大多数为发电用汽轮机均为多级轴流式汽轮机。
汽轮机本体主要由转动部分和静止部分两个方面组成。
转子包括主轴、叶轮、动叶片和联轴器等。
静子包括进汽部分、汽缸、隔板和静叶栅、汽封及轴承等。
因此汽轮机的制造工艺主要为上述部件的制造工艺。
汽轮机制造工艺的特点为:属单件生产,生产期长,材料品种多,材料性能要求高,零件种类多,加工精度高,设备要求高,操作技能要求高,机械加工工种齐全,设计冷热工艺且面广,检测手段齐备要求高,计量设备、测量工具齐全而且要求高采用专门工装多。
二:轴流式蒸汽轮机动叶片制造工艺1:叶片的结构静叶片一般由工作部分和安装部分组成动叶片一般由叶根、叶型部分和叶顶三部分组成2:叶片的工作条件及材料选择叶片的工作条件复杂,除因高速旋转和气流作用而承受较高的静应力和动应力外,还因其分别处在过热蒸汽区、两相过渡区、和湿蒸汽区段内工作而承受高温、高压、腐蚀和冲蚀作用。
因此叶片的材料要满足以下要求:良好的常温和高温机械性能、良好的抗蚀性、良好的减震性、和一定的耐磨性良好的冷热加工性能。
汽轮机流程图

汽水系统工艺流程及工艺说明
(1)工艺流程
汽水系统工艺流程图如下:
图:汽水系统工艺流程
(2)工艺流程说明
水通过在锅炉中被加热成为蒸汽后,蒸汽经过过热器的继续加热、升温而变为过热蒸汽,
过热蒸汽通过祝蒸汽管道,分成两路,一路进入减温减压器,一路进入汽轮机,进入减温减压器的蒸汽经过减温减压后进入热网加热器连箱,进入汽轮机的蒸汽经过不断膨胀。
高速流动的蒸汽冲动汽轮机动叶,使汽轮机转子转动,汽轮机转子带动发电机转子同步旋转而产生电能,蒸汽在汽轮机内做完功后,排入排汽母管,进入热网加热器连箱与减温减压后的蒸汽汇合,进入热网加热器,外网回水经过热网循环泵后去热网加热器内,机排汽与外网回水在热网加热器里进行换热,排汽的热量被外网水吸收后,形成凝结水进入凝结水连箱,外网水经过排汽加热后去往外网用于供暖,凝结水去往凝结水泵,经凝结水泵打入除氧器。
经过除氧器除氧加热后经下降管进入给水泵,打入锅炉汽包。
热电厂的工艺流程

热电厂的工艺流程热电厂是利用燃煤等能源进行发电的设备,其工艺流程包括燃烧、蒸汽发生、蒸汽压缩、发电及废气处理等几个重要环节。
以下是一个热电厂的典型工艺流程:首先,燃烧是热电厂的第一个关键步骤。
燃料(通常为煤炭)在锅炉内燃烧,产生高温的燃烧气体。
燃烧同时会释放大量热能,用于加热锅炉内的水。
接下来是蒸汽发生阶段。
在锅炉中,通过将锅炉内的水循环加热,水会逐渐变成高温高压的蒸汽。
锅炉内的燃烧气体会在炉膛中和水进行热交换,使水不断加热成蒸汽。
然后是蒸汽压缩过程。
高温高压的蒸汽进入汽轮机,驱动机械装置进行旋转。
汽轮机通常是一台多级式的轴流式涡轮机,将蒸汽的热能转化为机械能。
在汽轮机的转子内,蒸汽会一级接一级地流过多个轴流叶片,并因此逐渐膨胀,从而驱动转子转动。
接下来是发电阶段。
汽轮机的转子通过联轴器与发电机的转子相连,旋转力矩会通过转动发电机的磁场产生电能。
发电机内的励磁线圈产生磁场,旋转转子在磁场的作用下会产生感应电动势。
这个电动势经过电缆传输至变电站,经过变压器升压后输送到电网上。
最后是废气处理。
燃烧产生的废气包含大量的烟尘、二氧化硫和氮氧化物等污染物。
为了保护环境和人体健康,热电厂需要进行废气处理。
废气处理系统通常包括除尘、脱硫和脱氮等环节。
除尘装置用于去除燃烧废气中的悬浮颗粒物;脱硫装置则使用吸收剂将废气中的二氧化硫吸收,从而减少大气排放;脱氮装置则通过催化剂将废气中的氮氧化物转化为无害的氮气。
以上就是一个典型热电厂的工艺流程。
通过这个流程,在燃烧过程中产生的热能会转化为电能,为人们提供供电服务,并通过废气处理减少环境污染。
热电厂在现代社会起着重要的作用,但同时也需要不断探索技术创新,以进一步提高发电效率和减少环境污染。
- 1、下载文档前请自行甄别文档内容的完整性,平台不提供额外的编辑、内容补充、找答案等附加服务。
- 2、"仅部分预览"的文档,不可在线预览部分如存在完整性等问题,可反馈申请退款(可完整预览的文档不适用该条件!)。
- 3、如文档侵犯您的权益,请联系客服反馈,我们会尽快为您处理(人工客服工作时间:9:00-18:30)。
55MW汽轮发电机组调节、保安油系统
AV80-15电动鼓风机组控制油系统
AV80-15电动鼓风机组润滑油系统(一)
AV80-15电动鼓风机组润滑油系统(二)
谢 谢!
汽机工艺流程简介
张宏斌
汽机工序的主要任务
• 鼓风:为高炉生产提供热风,配套6台汽轮鼓 风机组和2台电动鼓风机组。 • 发电:为公司铁、烧、焦等重要厂矿提供保安 用电和利用公司生产的余热、余能发电,现配 套5台汽轮发电机组。 • 供汽:为公司弄弄坪及东部片区提供生产、生 活用中、低压蒸汽。 • 供水:为公司部分厂矿输送软水、除盐水和二 级除盐水。
பைடு நூலகம்
鼓风工艺简介
鼓风分为汽动鼓风和电动鼓风两种。汽动 鼓风即汽轮机拖动鼓风机生产热风,电动鼓风 即电动机拖动鼓风机生产热风。汽动鼓风机现 配套6台,其中一期鼓风站安装有4台Z-3650型 汽轮鼓风机组,主要为1~ 3号高炉供风,正常 运行3台,备用1台;二期热电站安装有2台瑞 士4000汽轮鼓风机组,主要为4号高炉供风, 正常运行1台备用1台;三期电动鼓风站安装有 2台AV80-15电动鼓风机组,主要为新3号高炉 供风,正常运行1台备用1台。
汽机工艺的特点
• 高温:中压蒸汽温度435℃ ,高压蒸汽温 度535 ℃。 • 高压:中压蒸汽压力3.43MPa ,高压蒸 汽压力8.83MPa 。 • 高转速:鼓风站风机工作转速3700~ 4370r/min,热电站风机机工作转速 5485r/min,电动鼓风站风机工作转速 4209r/min,发电机转速3000r/min。
25MW汽轮发电机组汽水系统
13.5MW汽轮发电机组汽水系统
55MW汽轮发电机组主汽系统
55MW汽轮发电机组凝结水系统
鼓风站风机循环水系统
热电站循环水系统
25MW汽轮发电机组循环水系统
55MW汽轮发电机组循环水系统
鼓风站给水系统
热电站给水系统
55MW汽轮发电机组给水除氧系统
55MW汽轮发电机组润滑、保安油系统
鼓风机工艺流程简图
鼓风机工艺流程简图
风机比较
能源动力中心高炉风系统图
拨风系统
• 拨风系统是为了防止高炉灌渣而设计安装的, 主要由两个电动拨风阀和一个气动拨风阀组成。 • 两个电动拨风阀正常处于开位置,由一个气动 拨风阀将两座高炉热风隔断,防止高炉串风。 • 当运行风机故障跳闸或转安全运行时,联锁气 动拨风阀自动快速打开,将其它高炉风量适当 拨往故障风机所对应的高炉,防止高炉断风, 避免高炉灌渣。
汽轮机工艺流程
汽轮机是以水蒸汽为工质,将热能转 变为机械能的回转式原动机。它在工作 时先把蒸汽的热能转变成动能,然后再 使蒸汽的动能转变成机械能,拖动发电 机或鼓风机等工作。
能源动力中心中压蒸汽系统
中压蒸汽系统的特点
• 母管制; • 一、二期蒸汽母管联网。
Z-3650汽轮鼓风机组汽水系统
瑞士4000风机汽水系统