蚀刻简介
PCB工艺外层蚀刻工艺简介

Under Etch
Over Etch
阻剂(锡面)
14
Outer Layer Pattern Creation
蚀刻均匀性
1.设备之确认:喷嘴状况
“定点喷”确认喷嘴状况
基材
2.条件之确认:喷压状况
铜面
“蚀刻点”确认喷压条件
3.蚀刻均匀性:设备/制程条件之整体表征
规格为“Rang=Max-Min<0.4 mil”为允收标准
a.氧化剂:将Sn氧化为SnO b.抗结剂:将SnO转为可溶性结构 c.护铜剂:保护铜面,防止氧化
17
Outer Layer Pattern Creation
检验项目与相关规范
CCD量测 线宽量测仪器
阻抗室量测阻抗(阻抗板) a. Polar type机台 b. TEK type机台
IPQC板面检视 板面质量检查
外层蚀刻(线路蚀刻)
目的:
线路电镀完成后,电路板将送入外层蚀刻线(剥膜、 蚀刻、剥锡段),主要的工作就是将电镀阻剂完全剥除(剥 膜段),将要蚀除的铜曝露在蚀刻液内(蚀刻段)。由于线路 区的顶部已被锡所保护,线路区的线路就能保留下来,再 将锡面剥除(剥锡段),如此整体线路板的表面线路就呈现 出来。典型的剥膜(Stripping)、蚀刻(Etching)、剥锡 (Stripping)生产线,业界统称为”SES Line”
8
Outer Layer Pattern Creation
蚀铜原理(蚀刻液主成分氯化铵/铜离子)
剥膜后蚀刻前
蚀刻中
蚀刻后
蚀铜液 : 碱性蚀刻液
功 用 : 蚀刻速度快且不伤害 金
属阻剂, 主要应用于负片
流程之镀锡(铅)板上
蚀铜液:酸性蚀刻液 功 用:蚀刻速度较慢且不攻击
DES简介

常见缺陷
缺陷名称 产生原因 预防和控制 频率
去膜不良 药液浓度不够 温度、压力不对 喷嘴堵塞 去膜速度不对
分析调整 检视温度、压力表 定期点检 断点测试
每班 每批 每班点检
THE END!
铜皮多余 T形铜
常见缺陷图示
T形铜
正常线路
不良板
去膜
去膜
去膜使用有机去膜液,温度48+5℃,去膜方式
为机器喷淋。 机器喷淋去膜生产效率高,但应 注意检查喷嘴是否堵塞,在去膜溶液中必须加 入消泡剂。
去膜参数
有機去膜液:14 ±2% 温度:485℃ 压力:0.20.05MPa 走速:去膜断点控制在50~60%
显影
显影
显影机 pH值、有效浓度与总浓度 显影点 喷嘴排列方式
显影机
感光膜中未曝光部分的活性基团与稀碱 溶液反应生成可溶性物质而溶解下 来, 显影时活性基团羧基一COOH与有機鹹 作用,生成亲水性集团,从而把未曝光的 部分溶解下来,而曝光部分的干膜不被 溶胀。
显影参数
显影槽 有機鹹濃度:0.65+0.1% 喷压:0.120.05Mpa 温度:29 2℃
Proper Fan Spray Pattern 扇形喷嘴的排列方式
Use of Cone Nozzles 圆锥形喷嘴的排列方式
常见缺陷的预防和控制
缺陷名称 显影不良 产生原因 药液浓度不够 温度、压力不对 喷嘴堵塞 显影速度不对 预防和控制 分析调整 检视温度、压力表 定期点检 断点测试 频率 换液时(三小时抽样) 每批 每班上班点检
蚀刻
蚀刻参数
铜离子:135 ±15g/L 盐 酸:2.4±0.4N 比重:1.28±0.02 喷压:0.30.15MPa 温度:50 2℃
湿蚀刻制程简介

1. 蝕刻(Etching)是什麼? 1.1 蝕刻是將材料利用化學反應或物理撞擊作用方式移除的技術。
2. 依其反應方式可分為濕蝕刻(Wet Etching)與乾蝕刻(Dry Etching) 。 2.1 『濕蝕刻』利用化學溶液,經由化學反應達到蝕刻的目的。通常可藉由選擇特定蝕 刻劑(Etchant) 來達成對於特定材料選擇性。濕蝕刻反應為等向性蝕刻(Isotropic Etching)。 2.2 『乾蝕刻』利用氣體分子或其產生的離子及自由基等氣體電漿物質,對於材料進行 物理式撞擊濺蝕或化學反應,來移除材料所需蝕刻的部分。而被蝕刻的物質變成 揮發性的氣體,經由抽氣系統抽離。通常乾蝕刻製程為非等向性蝕(Anisotropic Etching)。
Confidential
1. 通常在濕蝕刻反應中,最常使用來酸性蝕刻的化學溶液為HF(氫氟酸)與HNO3(硝酸) 2. HF/HNO3組成的蝕刻反應為等向性蝕刻,化學反應如下:
(1) NO2 formation(HNO2 in trace amount in HNO3) HNO2 + HNO3 → 2NO2 + H2O
Confidential
1. 通常在濕蝕刻反應中,另外使用來蝕刻矽材的鹼性化學溶液為NaOH或KOH,此蝕刻 反應為非等向性蝕刻,化學反應如下: Si + 2OH- → Si(OH)22+ + 2eSi(OH)22+ + 2OH- → Si(OH)4 + 2e4H2O + 4e- → 4OH- + 2H2 Si(OH)4 → SiO2(OH)22- + 2H+ 2H+ + 2OH- → 2H2O Overall Reaction : Si + 2OH- + 2H2O → SiO2(OH)22- + 2H2
ETCHING技术

蚀刻(Etching)概念简介一. 前言:集成电路(IC)的制造流程,犹如一场精致细密的建筑结构施工,建筑师(Designer & Device Owner)将设计蓝图(LayOut)和施工流程(Process Flow)设计出来,经过工程部门(模块Module)制定施工法则(Setup Process)后,交由施工单位(制造部MFG)来执行建筑工事.空白的硅晶圆就像一块平整的大工地,经过不断的整地(平坦化;离子植入),灌浆混沙填土上钢架(薄膜沉积),再经过砌墙挖坑打洞筑沟(显影&蚀刻)等重复的制程(Process),一层一层堆栈而上,制作成拥有复杂结构和完善功能的集成电路.“晶圆”这块”工地”有多大呢? 这个超现代”工地”的大小尺吋演进,正代表着人类科技突飞猛进的新里程碑.从三吋晶圆到目前的十二吋晶圆,可用面积增加了16倍,在一个process cycle 后,晶粒产出量也提升了数十倍.基本上,一套Process flow约需经过数百个不同步骤(step),耗时一,二个月才得以完成.而模块(Module)工程师的任务就是负责开发(Setup),维护(Maintain)和改良(Improve)各个步骤.而蚀刻模块在这项工事中占有不可或缺的重要角色.本章将针对蚀刻制程作一简略介绍.二. 蚀刻技术概论:集成电路的制造需要在晶圆上做出极细微尺寸的图案(Pattern).而这些图案最主要的形成方式,乃是使用蚀刻(Etching)技术,将微影(Lithography)技术所产生的光阻图形,无论是线(Line),面(EtchBack)或是孔洞(Hole),以化学腐蚀反应(Chemical)的方式,或物理撞击(Physical)的方式,或上述两种方式的综合,忠实无误的移转到薄膜上,以定义出整个集成电路所需的复杂结构.下图是最基本的集成电路制作流程(Process Flow):a. 薄膜沉积(Film Deposition)b. 蚀刻制程(Etching)& 微影制程(Photo Lithography)2-1. 湿蚀刻(Wet Etching)与干蚀刻(Dry Etching):蚀刻方式主要分成湿蚀刻(Wet Etching)与干蚀刻(Dry Etching)两种方式.早期半导体制程是使用湿蚀刻的方法,也就是利用合适的化学溶液,腐蚀所要蚀刻的材质未被光阻覆盖的部分,并在完成蚀刻反应后,由溶液带走腐蚀物。
干法刻蚀

二、干蚀刻的原理
离子化碰撞 当电子与一个原子或分子相碰撞时,它会将部分能量传递给受到原子核或 分子核束缚的轨道电子上。如果该电子获得的能量足以脱离核子的束缚, 它就会变成自由电子,此过程称为粒子碰撞游离。 e- +A→A++2e 离子化碰撞非常重要,它产生并维持电浆 原子
• • • • 物理性蚀刻+化学性蚀刻 在下电极接有两个电源 其中Source Power主要用来解离气体 以产生plasma Bias Power主要用来调节plasma的状
SF5+ F* plasma
态 ,以加强離子的轰击效应所以
Plasma的密度虽不是很高,但依然能 达到较高的蚀刻速率。 • • 非等向性蝕刻 高蚀刻速率
C
F
+
e + CF4 →CF3* + F * +e
激发松弛碰撞
二、干蚀刻的原理
激发:碰撞传递足够多的能量而使轨道电子跃迁到能量更高的轨道的过程。 e- +A → A*+e 激发状态不稳定且短暂,在激发轨道的电子会迅速掉到最低的能级或基态,此 过程称为松弛。激发的原子或分子会迅速松弛到原来的基态,并以光子的形式 把它从电子碰撞中得到的能量释放出来。 A*→ A + hν 激发 松弛 hν 电子
P/C T/M L/L
P/C T/M L/L
五、干蚀刻制程腔的构造
Gas System
A/A
C/S C/S C/S C/S Plasma
WETX蚀刻工艺简介

• Shower Swing for uniformity • Substrate Oscillation for uniformity • CK for Pre-wetting
swing
Etching Chamber
NEU
PR
PR
Film Glass
Chemical Knife
Shower Swing& Substrate Oscillation
Develop
Etch
Wet Etch
PR Strip Inspection
SPUTTER
Ar+
Al
Al Al
DC
Al
Al Al
Ar+
TARGET
SUBSTRATE
Dry Etch
Gas
RF
PLASMA FO Si Si
SiF4
• Cleaning:素玻璃镀膜前,去除表面有机物与Particle等污染。 • WETX:湿蚀刻,移除未被光阻保护的薄膜部分,将pattern移转至玻璃。 • PR Strip:将光阻剥离洗除。
Passivation
Pixel Electrode
WET
Dry
Deposition & Patterning Process in Detail
WET
DRY
WET
Cleaning
Deposition PR Coating Exposure
PECVD
RF
HHSiHH
H
NH
H
H H
H
Si N Si NSi N
Sn4+ + 2H2O Sn(C2O4)2 + 2H2
蚀刻简介
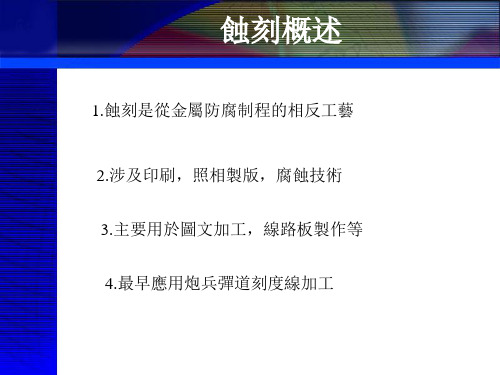
1.蝕刻是從金屬防腐制程的相反工藝
2.涉及印刷,照相製版,腐蝕技術 3.主要用於圖文加工,線路板製作等 4.最早應用炮兵彈道刻度線加工
蝕刻基本原理
蝕刻位置 加工前 防蝕刻塗料 加工後 將圖示非加工處已進行保護工件放入酸性介質種加工 防蝕刻塗料 待蝕刻材料
蝕刻基本原理
等速效應與蝕刻係數 由於蝕刻藥水對同種材料腐蝕在徑向和垂直方向 是相等,在平面尺寸D增加同時,深度H也在增加 因此在設計曝光菲林時,菲林圖案尺寸均比實際工 件要求尺寸小,這就面
烘乾
印刷反面
烘乾
曝光及成膜 曝光 顯影 沖洗 定影 沖洗
烘乾
蝕刻制程
蝕刻 蝕刻 沖洗 脫膜 沖洗 沖洗
防銹處理
烘乾
蝕刻重點參數及控制方法
1.蝕刻藥水濃度
藥水濃度變化會影響蝕刻係數K值。在同等條件下濃度越高,D 及H越大。所以藥水濃度會影響尺寸。一般採用定時測定方法。在 自動蝕刻生產線中,採用ODD量測,自動調整工件在蝕刻區線速以 達到雖然濃度變化,同時調整反應時間來控制尺寸精度。在濃度低於 一定值,採用定量補給泵補液。
2.溫度
溫度高會加速化學反應速度。因蝕刻是一個放熱反應,因此 溫度在生產過程中不斷升高。但溫度超過50C時,機器噴淋機構 和循環系統會發生故障。一般控制在32---50C
3.線速
速度快,反應時間短,尺寸偏小。
蝕刻問題點
蝕刻無需制模,有時用衝壓方法無法做到的加工,用蝕刻可以 很輕鬆完成。但蝕刻有以下無法克服的問題: 1:工序長,不穩定因素多,尺寸穩定性差 2:環境污染嚴重,被列為一類污染排放物質。 3:ROHS禁止使用物質不易清除。 4:受設備限制,產能低,人力消耗大。 5:被加工件兩面均為利邊。
蚀刻介绍
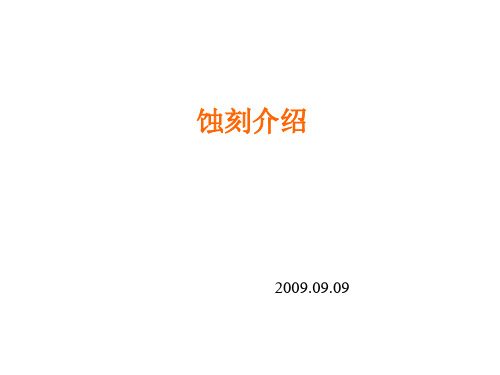
顺流(down-stream)等离子 等离子(PE) 蚀刻系统 顺流 等离子
TCA-2600
平板蚀刻
在两个平行的电极间产生有活性且具 在两个平行的电极间产生有活性且具 能量的等离子体,直接对晶片进行离 能量的等离子体,直接对晶片进行离 的等离子体 子轰击和化学蚀刻。 子轰击和化学蚀刻。 根据加RF位置的不同 分为两种: 位置的不同, 根据加 位置的不同,分为两种: —等离子体蚀刻型:(a) wafer置于 —等离子体蚀刻型:(a)、wafer置于 接地端,反应压力较高,离子轰击 较弱 —反应离子蚀刻型:(b)、wafer置于 非接地端,反应压力低,离子轰击 作用强
J max
qvt 2 ≈k 2 mI g
3
注意: 注意:蚀刻的不均匀性和残留
离子铣
工作压力为10 工作压力为 -4Torr 对所有材料都是各向异性蚀刻 选择比很差 生产能力较低 用于蚀刻Au、 、 等难蚀刻的材料 用于蚀刻 、Pt、Cu等难蚀刻的材料
IML-4-1-M
3、反应离子蚀刻(RIE) 反应离子蚀刻(RIE)
保护机理: 保护机理:
溅出光刻胶和( 溅出光刻胶和(或)化 学反应生成副产品 副产品物质淀积在表面 离子轰击是垂直方向 的,蚀刻主要是垂直方 向的 会发生, 底部淀积 会发生,侧 壁淀积保护侧壁。 壁淀积保护侧壁。
L-507D-L
三种干法蚀刻速率比较: 三种干法蚀刻速率比较:
4、高密度等离子(HDP)蚀刻 、高密度等离子 蚀刻 在先进的制造技术中蚀刻关键层的主要方法是单片 处理得HDP 它能蚀刻小尺寸高深宽比的图形, HDP。 处理得HDP。它能蚀刻小尺寸高深宽比的图形,有大的 选择比和很小的残留损伤, 选择比和很小的残留损伤,这对刻很波膜和极浅的孔非 常有用。常用的结构有: 常有用。常用的结构有:
刻蚀简介
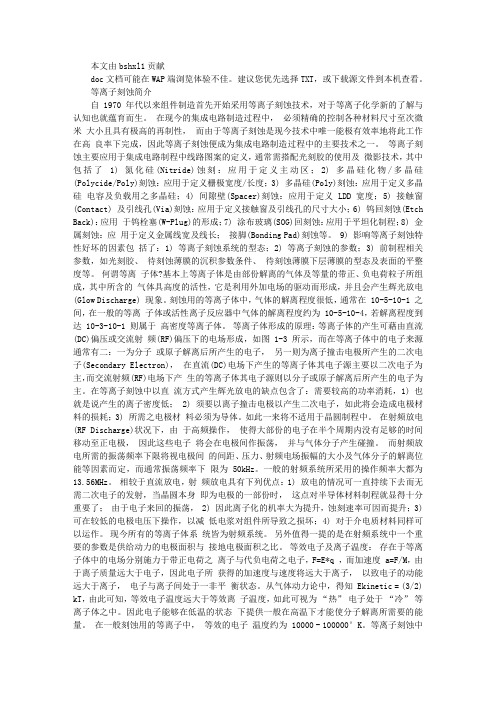
本文由bshxl1贡献doc文档可能在WAP端浏览体验不佳。
建议您优先选择TXT,或下载源文件到本机查看。
等离子刻蚀简介自 1970 年代以来组件制造首先开始采用等离子刻蚀技术,对于等离子化学新的了解与认知也就蕴育而生。
在现今的集成电路制造过程中,必须精确的控制各种材料尺寸至次微米大小且具有极高的再制性,而由于等离子刻蚀是现今技术中唯一能极有效率地将此工作在高良率下完成,因此等离子刻蚀便成为集成电路制造过程中的主要技术之一。
等离子刻蚀主要应用于集成电路制程中线路图案的定义,通常需搭配光刻胶的使用及微影技术,其中包括了1) 氮化硅(Nitride)蚀刻:应用于定义主动区;2) 多晶硅化物/多晶硅(Polycide/Poly)刻蚀:应用于定义栅极宽度/长度;3) 多晶硅(Poly)刻蚀:应用于定义多晶硅电容及负载用之多晶硅;4) 间隙壁(Spacer)刻蚀:应用于定义 LDD 宽度;5) 接触窗(Contact) 及引线孔(Via)刻蚀:应用于定义接触窗及引线孔的尺寸大小;6) 钨回刻蚀(Etch Back):应用于钨栓塞(W-Plug)的形成;7) 涂布玻璃(SOG)回刻蚀:应用于平坦化制程;8) 金属刻蚀:应用于定义金属线宽及线长;接脚(Bonding Pad)刻蚀等。
9) 影响等离子刻蚀特性好坏的因素包括了:1) 等离子刻蚀系统的型态;2) 等离子刻蚀的参数;3) 前制程相关参数,如光刻胶、待刻蚀薄膜的沉积参数条件、待刻蚀薄膜下层薄膜的型态及表面的平整度等。
何谓等离子体?基本上等离子体是由部份解离的气体及等量的带正、负电荷粒子所组成,其中所含的气体具高度的活性,它是利用外加电场的驱动而形成,并且会产生辉光放电(Glow Discharge) 现象。
刻蚀用的等离子体中,气体的解离程度很低,通常在 10-5-10-1 之间,在一般的等离子体或活性离子反应器中气体的解离程度约为 10-5-10-4,若解离程度到达 10-3-10-1 则属于高密度等离子体。
DES原理简介

课程完毕! 课程完毕! 谢谢! 谢谢!
褪膜原理介绍
褪膜原理介绍
褪膜:用碱液剥离曝光干膜。在碱性环境下, 褪膜:用碱液剥离曝光干膜。在碱性环境下,利 用碱类物质的爬墙效应,使干膜脱落, 用碱类物质的爬墙效应,使干膜脱落,属 于一种物理反应。 于一种物理反应。
NaOH 溶液缸
测量NaOH 溶液电导率
药液过滤
褪膜原理
• 现行使用之光阻设计剥除大部份为水溶性的化学药剂,以 顾及环保之要求 • 大部份之光阻而言,剥膜液等于是更强烈之显影溶液,如 在55度左右之2%浓度氢氧化钠溶液 • 剥膜液与干膜反应时,先是膨胀分裂(swell),然后经过 机台之喷压将干膜屑剥离铜面,便完成剥膜之程序 • 如为正相光阻之剥离:需以丙酮、酮类或其它有机溶剂剥 离,过度烘烤将使剥膜过程更加困难 • 负相液态光阻之剥离:需适度之烘烤以增加高分子之聚合 程度,过度烘烤将造成绝缘物质的损害
CO32- →
反应平衡式: K = [HCO3-][OH-] / [CO32-] PH = 14 + log{K.[CO32-]/[HCO3-]} 为掌握显影之质量,制程中需严格控制[CO32-]/[HCO3-]的浓度 比值(PH值控制),以得最佳之线路显影效果
显像原理
显影参数控制: 显影参数控制 Na2CO3浓度为1.0±0.1% 温度30±2℃ 压力1.5KG/CM2(30PSI) 显影点50%~75%之间
Cl-含量的影响
1.在氯化铜蚀刻液中Cu2+和Cu1+实际上是以络离子的形 式存在。在溶液Cl-中较多时, Cu2+是以[Cu2+Cl4]2-络 离子存在, Cu1+是以[Cu1+Cl3]2-络离子存在,所以蚀刻 液的配制和再生都需要Cl-参加反应. 2.盐酸溶度升高时,蚀刻时间减少,但超过6 N酸其盐 酸,挥发量大,且对造成对设备的腐蚀,并随着酸浓 度的增加,氯化铜的溶解度迅速降低。
蚀刻与着色电镀技术简介
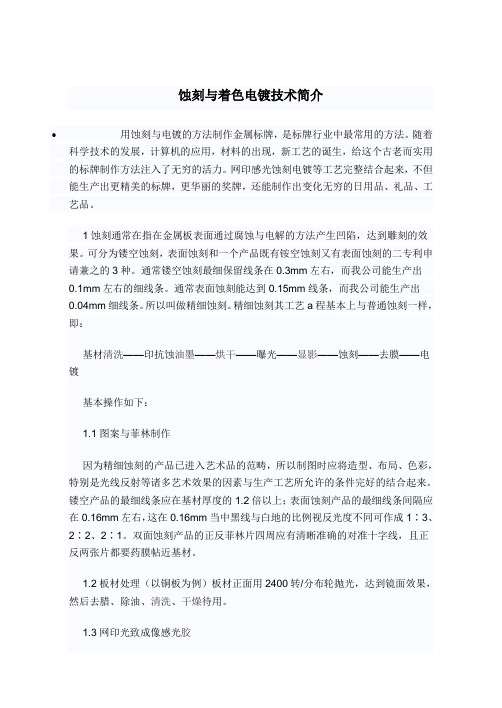
蚀刻与着色电镀技术简介用蚀刻与电镀的方法制作金属标牌,是标牌行业中最常用的方法。
随着科学技术的发展,计算机的应用,材料的出现,新工艺的诞生,给这个古老而实用的标牌制作方法注入了无穷的活力。
网印感光蚀刻电镀等工艺完整结合起来,不但能生产出更精美的标牌,更华丽的奖牌,还能制作出变化无穷的日用品、礼品、工艺品。
1蚀刻通常在指在金属板表面通过腐蚀与电解的方法产生凹陷,达到雕刻的效果。
可分为镂空蚀刻,表面蚀刻和一个产品既有铵空蚀刻又有表面蚀刻的二专利申请兼之的3种。
通常镂空蚀刻最细保留线条在0.3mm左右,而我公司能生产出0.1mm左右的细线条。
通常表面蚀刻能达到0.15mm线条,而我公司能生产出0.04mm细线条。
所以叫做精细蚀刻。
精细蚀刻其工艺a程基本上与普通蚀刻一样,即:基材清洗——印抗蚀油墨——烘干——曝光——显影——蚀刻——去膜——电镀基本操作如下:1.1图案与菲林制作因为精细蚀刻的产品已进入艺术品的范畴,所以制图时应将造型、布局、色彩,特别是光线反射等诸多艺术效果的因素与生产工艺所允许的条件完好的结合起来。
镂空产品的最细线条应在基材厚度的1.2倍以上;表面蚀刻产品的最细线条间隔应在0.16mm左右,这在0.16mm当中黑线与白地的比例视反光度不同可作成1∶3、2∶2、2∶1。
双面蚀刻产品的正反菲林片四周应有清晰准确的对准十字线,且正反两张片都要药膜帖近基材。
1.2板材处理(以铜板为例)板材正面用2400转/分布轮抛光,达到镜面效果,然后去腊、除油、清洗、干燥待用。
1.3网印光致成像感光胶因为制作图案极细。
显影后无法修补,因此选择好的感光胶尤为重要。
我公司选用高氏(coates)光致成像耐蚀油墨,在黄光或红光下用200目丝网满版印刷,第一次印抛光面,100℃烘15分钟,第二次印反面,再用100℃烘30分钟,待冷却,表面不粘手,方可进行曝光。
1.4曝光吸气哂版机曝光。
曝光时间20-100秒不等,线条越细,曝光时间越长,反之则短。
刻蚀简介

刻蚀刻蚀,英文为Etch,它是半导体制造工艺,微电子IC制造工艺以及微纳制造工艺中的一种相当重要的步骤。
是与光刻相联系的图形化(pattern)处理的一种主要工艺。
所谓刻蚀,实际上狭义理解就是光刻腐蚀,先通过光刻将光刻胶进行光刻曝光处理,然后通过其它方式实现腐蚀处理掉所需除去的部分。
随着微制造工艺的发展;广义上来讲,刻蚀成了通过溶液、反应离子或其它机械方式来剥离、去除材料的一种统称,成为微加工制造的一种普适叫法。
刻蚀方法刻蚀最简单最常用分类是:干法刻蚀和湿法刻蚀。
显而易见,它们的区别就在于湿法使用溶剂或溶液来进行刻蚀。
湿法刻蚀是一个纯粹的化学反应过程,是指利用溶液与预刻蚀材料之间的化学反应来去除为被掩蔽膜材料掩蔽的部分而达到刻蚀目的。
其特点是:湿法虎穴刻蚀在半导体工艺中有着广泛应用:磨片、抛光、清洗、腐蚀优点是选择性好、重复性好、生产效率高、设备简单、成本低缺点是:钻刻严重、对图形的控制性较差,不能用于小的特征尺寸;会产生大量的化学废液干法刻蚀种类很多,光挥发、气相腐蚀、等离子体腐蚀等。
其优点是:各向异性好,选择比高,可控性、灵活性、重复性好,细线条操作安全,易实现自动化,无化学废液,处理过程未引入污染,洁净度高。
缺点是:成本高,设备复杂。
干法刻蚀主要形式有纯化学过程(如屏蔽式,下游式,桶式),纯物理过程(如离子铣),物理化学过程,常用的有反应离子刻蚀RIE,离子束辅助自由基刻蚀ICP。
刻蚀方式很多,一般有:溅射与离子束铣蚀,等离子刻蚀(Plasma Etching),高压等离子刻蚀,高密度等离子体(HDP)刻蚀,反应离子刻蚀(RIE)。
另外,化学机械抛光CMP,剥离技术等等也可看成是广义刻蚀的一些技术。
蚀刻(Etching)蚀刻的机制,按发生顺序可概分为「反应物接近表面」、「表面氧化」、「表面反应」、「生成物离开表面」等过程。
所以整个蚀刻,包含反应物接近、生成物离开的扩散效应,以及化学反应两部份。
酸性蚀刻工艺流程教材

用于清洗板材表面,去除残留的蚀刻液和其他杂质。
酸性蚀刻的辅助材料
添加剂
为了改善蚀刻效果,可以在蚀刻液中加入一些 添加剂,如缓蚀剂、加速剂等。
检测试剂
用于检测蚀刻液的浓度和酸碱度,确保其处于 最佳工作状态。
废液处理剂
用于处理蚀刻过程中产生的废液,减少环境污染。
05 酸性蚀刻的环保与安全
酸性蚀刻的环保措施
医疗器械
医疗器械如手术刀、针头 等,通过酸性蚀刻工艺提 高表面的抗滑性和防锈性。
酸性蚀刻的优缺点
优点
酸性蚀刻工艺具有操作简单、成本低 廉、环保等优点,可以快速实现金属 表面的处理,提高金属表面的美观度 和使用性能。
缺点
酸性蚀刻工艺可能会对金属材料产生 一定的腐蚀和损伤,影响金属材料的 机械性能和耐腐蚀性能,因此需要合 理控制蚀刻时间和温度等参数。
废气处理
酸性蚀刻过程中产生的废气应经 过处理后再排放,以减少对大气 的污染。常用的废气处理方法包 括吸附法、吸收法、燃烧法等。
废水处理
酸性蚀刻过程中产生的废水应经 过处理后再排放,以减少对水体 的污染。废水处理方法包括沉淀 法、过滤法、生物处理法等。
废渣处理
酸性蚀刻过程中产生的废渣应进 行妥善处理,以减少对环境的污 染。废渣可以采取填埋、焚烧、 回收利用等方式进行处理。
05
04
酸性蚀刻
将涂布好的金属板材放入酸性蚀刻溶 液中,在一定温度和时间下进行蚀刻。
电路板的酸性蚀刻
总结词
在电子工业中,电路板的制作过程中酸性 蚀刻技术是关键步骤之一,用于形成导电 线路和图案。
后处理
去除抗蚀剂,进行电镀、焊接等处理,完 成电路板的制作。
准备材料
选择合适的基材,如FR4、CEM-1等,并 制备好电路图形。
vc蚀刻工艺

VC蚀刻工艺1. 简介VC蚀刻工艺是一种常用于微电子制造的工艺,用于在半导体材料上进行微细图案的制作。
它是一种湿法蚀刻技术,通过使用含有氯化氟酸(Vapor Chloride)溶液来去除材料表面的部分层。
VC蚀刻工艺具有高精度、高效率和高可控性的特点,被广泛应用于集成电路、光学器件等领域。
2. 工艺步骤VC蚀刻工艺包括以下几个主要步骤:2.1 准备工作在进行VC蚀刻之前,需要进行一些准备工作:•设计和制作光罩:根据所需图案设计并制作光罩,光罩上的透明区域将决定最终蚀刻出的图案。
•清洗基片:将待加工的半导体基片进行清洗,去除表面的杂质和污染物。
2.2 涂覆光阻将清洗后的基片放入涂覆机中,在基片表面均匀涂覆一层光阻。
光阻是一种特殊的光敏材料,它可以通过曝光和显影来形成所需的图案。
2.3 曝光将涂有光阻的基片与光罩对准,放入曝光机中进行曝光。
曝光机会使用紫外线照射基片表面,使得光阻在照射区域发生化学反应,形成暴露区和未暴露区。
2.4 显影将经过曝光的基片放入显影机中进行显影。
显影机会使用特定的溶液将未暴露区的光阻溶解掉,而保留下暴露区的光阻。
2.5 VC蚀刻将经过显影的基片放入VC蚀刻机中进行蚀刻。
VC溶液中的氯化氟酸可以与半导体材料发生反应,去除暴露区内部一定深度的材料层。
蚀刻时间和温度可以根据需要进行调节,以达到所需图案要求。
2.6 清洗和检查完成蚀刻后,需要将基片从VC溶液中取出,并进行清洗。
清洗过程可以去除残留的光阻和溶液,确保基片表面干净。
随后,对蚀刻后的图案进行检查,确保其质量和精度符合要求。
3. 应用领域VC蚀刻工艺在微电子制造中有广泛的应用。
以下是一些常见的应用领域:3.1 集成电路制造在集成电路制造中,VC蚀刻工艺被用于制作晶体管、金属线路、电容器等微细结构。
通过控制蚀刻参数,可以实现不同尺寸和形状的结构,满足集成电路设计的需求。
3.2 光学器件制造VC蚀刻工艺也被应用于光学器件的制造中。
sic蚀刻工艺
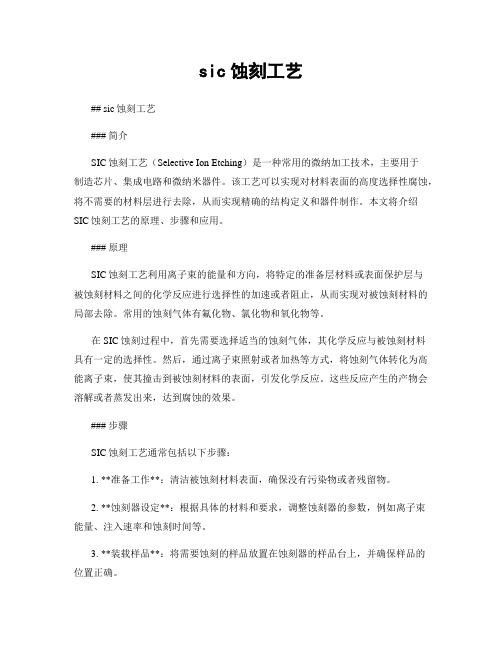
sic蚀刻工艺## sic蚀刻工艺### 简介SIC蚀刻工艺(Selective Ion Etching)是一种常用的微纳加工技术,主要用于制造芯片、集成电路和微纳米器件。
该工艺可以实现对材料表面的高度选择性腐蚀,将不需要的材料层进行去除,从而实现精确的结构定义和器件制作。
本文将介绍SIC蚀刻工艺的原理、步骤和应用。
### 原理SIC蚀刻工艺利用离子束的能量和方向,将特定的准备层材料或表面保护层与被蚀刻材料之间的化学反应进行选择性的加速或者阻止,从而实现对被蚀刻材料的局部去除。
常用的蚀刻气体有氟化物、氯化物和氧化物等。
在SIC蚀刻过程中,首先需要选择适当的蚀刻气体,其化学反应与被蚀刻材料具有一定的选择性。
然后,通过离子束照射或者加热等方式,将蚀刻气体转化为高能离子束,使其撞击到被蚀刻材料的表面,引发化学反应。
这些反应产生的产物会溶解或者蒸发出来,达到腐蚀的效果。
### 步骤SIC蚀刻工艺通常包括以下步骤:1. **准备工作**:清洁被蚀刻材料表面,确保没有污染物或者残留物。
2. **蚀刻器设定**:根据具体的材料和要求,调整蚀刻器的参数,例如离子束能量、注入速率和蚀刻时间等。
3. **装载样品**:将需要蚀刻的样品放置在蚀刻器的样品台上,并确保样品的位置正确。
4. **真空处理**:将蚀刻器的内部抽成真空状态,以防止气体泄漏和干扰蚀刻过程。
5. **气体处理**:将蚀刻气体注入蚀刻器,使其达到所需浓度。
6. **蚀刻处理**:开始蚀刻过程,控制离子束的能量和方向,使其仅蚀刻指定的区域。
7. **清洗和干燥**:蚀刻结束后,将样品从蚀刻器中取出,并进行清洗和干燥,以去除残留的蚀刻产物和污染物。
### 应用SIC蚀刻工艺在微纳加工领域具有广泛的应用。
首先,SIC蚀刻工艺可以用于集成电路的制造。
通过控制蚀刻气体的选择和加工参数,可以精确地定义集成电路的结构和形状,制造出高精度的电子器件。
其次,SIC蚀刻工艺还可以用于MEMS(微机电系统)器件的制造。