焦炉煤气净化工艺流程的选择
焦炉煤气净化技术:洗苯工段工艺流程与设备

(2)直接式冷却塔终冷流程
学习单元4.1.2
二、煤气洗苯流程
洗苯工段工艺流程与设备
煤气含苯入口:25~40g/m3 煤气含苯出口:2~4g/m3
贫油含苯入口:0.3%~0.5% 富油含苯出口:2.5%
1-洗苯塔;2-新洗油槽;3-贫油槽; 4-贫油泵;5-半富油泵;6-富油泵
学习单元4.1.2 洗苯工段工艺流程与设备
思考题:
1、熟练掌握煤气终冷、洗苯工艺流程。 2、 熟练掌握煤气终冷、洗苯指标。
一、煤气终冷流程
2、煤气终冷和除萘 流程
(1)横管终冷器终冷流程
煤气
终
循环水
32 ℃
18 ℃
塔
低温水
50~60 ℃
1~2g/m3(萘的露点温度30~35 ℃ )
轻质焦油循环使用
20~30 ℃
煤气 0.5g/m3(萘的露点温度20 ℃ )
冷凝液
液封槽
机械化氨 水澄清槽
学习单元4.1.2 洗苯工段工艺流程与设备
一、煤气终冷流程
2、煤气终冷和除萘 流程
主要工艺参数及规定:
①终冷器入口煤气温度不大于50 ℃ ,
出口温度20~25℃。
②终冷器阻力不大于2000Pa。
③单台横管终冷器冷凝液喷洒量
15~20m3/h。
④轻质焦油含水量控制在
10%以下。
⑤喷淋密度控制在
4.5~5m3/(m2.h) 。
学习单元4.1.2 洗苯工段工艺流程与设备
工作任务4.1 认知洗苯、脱苯工段生产流程与设备
学习单元4.1.2 洗苯工段工艺流程与设备
一、煤气终冷流程
硫铵流程中设、水洗氨不设
1、煤气终冷和除萘 方法
焦炉煤气的使用工艺流程
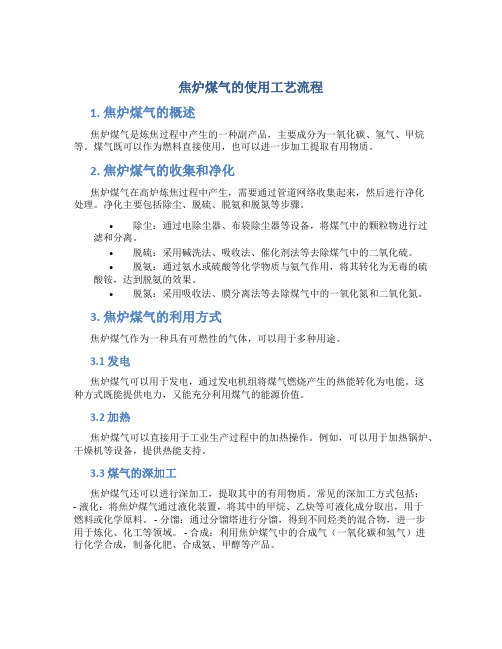
焦炉煤气的使用工艺流程1. 焦炉煤气的概述焦炉煤气是炼焦过程中产生的一种副产品,主要成分为一氧化碳、氢气、甲烷等。
煤气既可以作为燃料直接使用,也可以进一步加工提取有用物质。
2. 焦炉煤气的收集和净化焦炉煤气在高炉炼焦过程中产生,需要通过管道网络收集起来,然后进行净化处理。
净化主要包括除尘、脱硫、脱氨和脱氮等步骤。
•除尘:通过电除尘器、布袋除尘器等设备,将煤气中的颗粒物进行过滤和分离。
•脱硫:采用碱洗法、吸收法、催化剂法等去除煤气中的二氧化硫。
•脱氨:通过氨水或硫酸等化学物质与氨气作用,将其转化为无毒的硫酸铵,达到脱氨的效果。
•脱氮:采用吸收法、膜分离法等去除煤气中的一氧化氮和二氧化氮。
3. 焦炉煤气的利用方式焦炉煤气作为一种具有可燃性的气体,可以用于多种用途。
3.1 发电焦炉煤气可以用于发电,通过发电机组将煤气燃烧产生的热能转化为电能。
这种方式既能提供电力,又能充分利用煤气的能源价值。
3.2 加热焦炉煤气可以直接用于工业生产过程中的加热操作。
例如,可以用于加热锅炉、干燥机等设备,提供热能支持。
3.3 煤气的深加工焦炉煤气还可以进行深加工,提取其中的有用物质。
常见的深加工方式包括:- 液化:将焦炉煤气通过液化装置,将其中的甲烷、乙炔等可液化成分取出,用于燃料或化学原料。
- 分馏:通过分馏塔进行分馏,得到不同烃类的混合物,进一步用于炼化、化工等领域。
- 合成:利用焦炉煤气中的合成气(一氧化碳和氢气)进行化学合成,制备化肥、合成氨、甲醇等产品。
4. 焦炉煤气利用过程中的安全措施在焦炉煤气利用的过程中,需要采取一系列安全措施,确保操作人员和设备的安全。
•检测装置:安装煤气检测仪器,及时监测煤气中的浓度,一旦发现泄漏等情况,及时采取措施。
•防火措施:确保煤气供应管道和设备的完整性,并采取火花防护措施。
•排风系统:建立良好的排风系统,及时排除煤气中的有害气体,保持室内空气的清洁。
5. 焦炉煤气利用的环境效益焦炉煤气的利用不仅具有经济效益,还可以带来一定的环境效益。
焦炉煤气的净化工艺流程
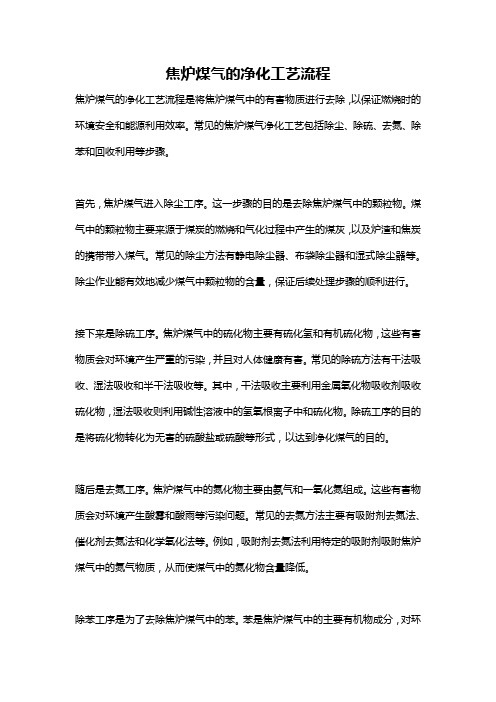
焦炉煤气的净化工艺流程焦炉煤气的净化工艺流程是将焦炉煤气中的有害物质进行去除,以保证燃烧时的环境安全和能源利用效率。
常见的焦炉煤气净化工艺包括除尘、除硫、去氮、除苯和回收利用等步骤。
首先,焦炉煤气进入除尘工序。
这一步骤的目的是去除焦炉煤气中的颗粒物。
煤气中的颗粒物主要来源于煤炭的燃烧和气化过程中产生的煤灰,以及炉渣和焦炭的携带带入煤气。
常见的除尘方法有静电除尘器、布袋除尘器和湿式除尘器等。
除尘作业能有效地减少煤气中颗粒物的含量,保证后续处理步骤的顺利进行。
接下来是除硫工序。
焦炉煤气中的硫化物主要有硫化氢和有机硫化物,这些有害物质会对环境产生严重的污染,并且对人体健康有害。
常见的除硫方法有干法吸收、湿法吸收和半干法吸收等。
其中,干法吸收主要利用金属氧化物吸收剂吸收硫化物,湿法吸收则利用碱性溶液中的氢氧根离子中和硫化物。
除硫工序的目的是将硫化物转化为无害的硫酸盐或硫酸等形式,以达到净化煤气的目的。
随后是去氮工序。
焦炉煤气中的氮化物主要由氨气和一氧化氮组成。
这些有害物质会对环境产生酸雾和酸雨等污染问题。
常见的去氮方法主要有吸附剂去氮法、催化剂去氮法和化学氧化法等。
例如,吸附剂去氮法利用特定的吸附剂吸附焦炉煤气中的氮气物质,从而使煤气中的氮化物含量降低。
除苯工序是为了去除焦炉煤气中的苯。
苯是焦炉煤气中的主要有机物成分,对环境和人体都有一定的危害。
去苯的方法多种多样,包括吸附过程、吸附剂再生过程和热解技术等。
其中,吸附过程主要是利用各种吸附剂吸附苯,吸附剂再生过程则是通过各种手段将吸附的苯从吸附剂中脱附出来。
最后是回收利用工序。
焦炉煤气中除去有害物质后,还含有一些有价值的组分,如甲烷、氢气和一些烃类等。
对于这些有价值的组分,可以通过适当的工艺进行回收利用。
一般来说,回收利用工艺分为低温分馏和高温分馏两种方式。
低温分馏主要是通过降温将焦炉煤气中的一些高沸点成分凝结出来,从而得到所需的有价值气体。
而高温分馏则是通过高温条件下焦炉煤气中的组分按沸点顺序蒸馏分离。
焦炉煤气净化工艺流程的评述

作者:范守谦时间:2008-7-8 10:25:53焦炉煤气净化工艺流程的评述范守谦(鞍山焦化耐火材料设计研究院)焦炉煤气净化工艺流程的选择,主要取决于脱氨和脱硫的方法。
众所周知,在炼焦过程中,煤中约有30%的硫进入焦炉煤气,95%的硫以硫化氢的形式存在。
焦炉煤气中一般含有硫化氢6~8g /m3 , 氰化氢 1. 5~2g/m'。
若不事先脱除,就有50%的氰化氢和10%~40%的硫化氢进入氨、苯回收系统,加剧了设备的腐蚀,还会增加外排污水中的酚、氰含量。
含有硫化氢和氰化氢的煤气作为燃料燃烧时,会生成大量SO2和NOx而污染大气。
为了防止氨对煤气分配系统、煤气主管以及煤气设备的腐蚀和堵塞,在煤气作为燃料使用之前必须将其脱除。
20世纪70年代以前,由于焦炉煤气主要供冶金厂作工业燃料,因此,大部分焦化厂的煤气净化工艺都没有设置脱硫装置,而回收氨的装置几乎全采用半直接法饱和器生产硫铵流程。
随着国民经济的发展以及我国环保法规的不断完善和日益严格,在焦炉煤气净化工艺过程设置脱硫脱氰装置和改进脱氨工艺就势在必行。
进入80年代以后,改革开放逐步深入,我国焦化行业和煤气行业相继从国外引进了多种煤气净化装置,国内科技人员在原有基础上也开发研制了新型脱硫工艺,大大推动了我国焦炉煤气净化工艺的发展。
现将几种脱氨和脱硫方法作扼要介绍和论述。
1 氨的脱除1.1 硫铵工艺生产硫铵的工艺是焦炉煤气氨回收的传统方法,我国在20世纪60年代以前建成的大中型焦化厂均采用半直接法饱和器生产硫铵,该工艺的主要缺点是设备腐蚀严重,硫铵质量差,煤气系统阻力大。
随着宝钢一期工程的建设,我们引进了酸洗法生产硫铵工艺,该工艺由酸洗、真空蒸发结晶以及硫铵离心、干燥、包装等三部分组成。
与饱和器法相比,由于将氨吸收和硫铵结晶操作分开,可获得优质大颗粒硫铵结晶。
酸洗塔为空喷塔,煤气系统的阻力仅为饱和器法的1/4,可大幅度降低煤气鼓风机的电耗。
采用干燥冷却机将干燥后的硫铵进一步冷却,以防结块,有利于自动包装。
典型焦炉煤气净化工艺流程
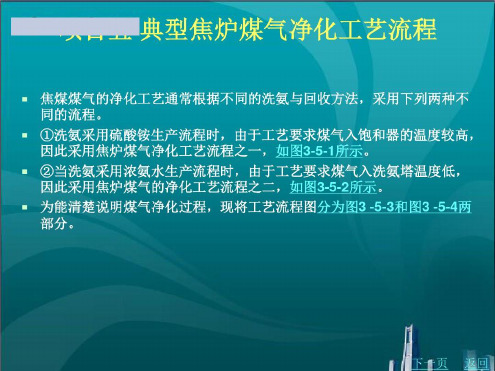
表3-5-1荒煤气的组成-水蒸气-250-450-硫化氢-6-30-焦油气-80-120-氰化物-1.0.5-粗苯-30=45-萘-10-氨-8-16-返回
■谢谢观赏典型焦炉煤ቤተ መጻሕፍቲ ባይዱ净化工艺流程
典型焦炉煤气净化工艺流程
图3-5-2焦炉煤气净化工艺流程之二-来自焦炉的荒煤气。-初步冷却-鼓风机-脱焦油-洗萘-用户-脱硫-最终 萘-洗苯-洗氨-返回
图3-5-3鼓风机前冷凝系统流程图-煤气-荒煤气-煤气入口-煤气入」-体-△6-煤气出口-氨水-7-焦油-8-9-10-返回
图3-5-4鼓风机后煤气洗涤系统流程图-风机压出煤气-煤气去罐区-10-富油去-浓氨水去净化池-软水-返回
典型焦炉煤气净化工艺流程-煤气从横管出来后由鼓风机压送到后续工序,在机后,煤气相继经过洗-萘塔、3个洗氨塔 两个洗苯塔,煤气得到净化后送入罐区。-此外,还含有少量轻吡啶盐基0.4~0.6gN3、二硫化碳、噻吩等,含量为2~2.5g/Nm3和其他化合物。-返回
图3-5-1焦炉煤气净化工艺流程之一-来自焦炉的荒煤气。-初步冷却-鼓风机-脱焦油-制取硫酸铵-用户-脱疏 最终洗萘-最终冷却与洗禁-返回
典型焦炉煤气净化工艺流程-焦煤煤气的净化工艺通常根据不同的洗氨与回收方法,采用下列两种不-同的流程。-①洗 采用硫酸铵生产流程时,由于工艺要求煤气入饱和器的温度较高,-因此采用焦炉煤气净化工艺流程之一,如图3-5所示。-②当洗氨采用浓氨水生产流程时,由于工艺要求煤气入洗氨塔温度低,-因此采用焦炉煤气的净化工艺流程之二 如图3-5-2所示。-为能清楚说明煤气净化过程,现将工艺流程图分为图3-5-3和图3-5-4两-部分。-页 返回
典型焦炉煤气净化工艺流程-煤在焦炉炭化室内隔绝空气和高温条件下进行干馏时,产生的气体产物-为荒煤气(荒煤气 组成见表3-5-1),荒煤气在集气管内受到循环氨水喷洒-温度由650℃~700℃降至80℃~85℃,然后经 气主管道进入回收系统-的气液分离器。在此煤气与液体进行分离,液体部分进入机械化澄清槽,-液体部分的焦油沉在 底,氨水部分在上层,自流到氨水循环槽内,再-用氨水泵输送到焦炉集气管内喷洒;焦油由泵抽出送到焦油贮槽内脱水 -外销。(煤气)气体部分将进入3台并联的主管初冷器,在此冷却到-30℃35℃,然后再进入横管冷却器,进行二 冷却,同时喷淋液对煤-气进行洗涤。-下青页-返回
煤气净化工艺工艺流程..

煤气净化工艺工艺流程及主要设备煤气净化设施1概述煤气净化车间生产规模按2×65 孔5.5m 捣固焦炉焦炉年产130万t 干全焦配套设计。
焦炉煤气处理量为75300m3/h(标况)。
煤气净化车间由冷凝鼓风工段、脱硫工段、硫铵工段(含蒸氨系统)、终冷洗涤及粗苯蒸馏工段、油库及其相关的生产辅助设施组成。
2设计原则对煤气净化车间本着经济、实用、可靠的原则,在满足国家环保、职业卫生与安全、能源等法规要求的前提下,尽量简化工艺流程,并合理配备工艺装备,以节省投资和工厂用地。
3设计基础数据a)煤气量基础数据焦炉装煤量(干基):206.98t/h煤气产量:340Nm3/t(干煤)b) 煤气净化指标表1 煤气净化指标表序号指标名称单位净化前指标净化后指标1 NH3g/m36~8 ≤0.052 H2S g/m35~7 ≤0.23 苯g/m324~40 ≤44 焦油g/m3≤0.025 萘g/m3≤0.34原材料及产品指标4.1焦油——符合YB/T5075-2010 2号指标序号指标名称质量指标1 密度(20℃),g/cm3 1.13~1.222 甲苯不溶物(无水基),% ≤93 灰分,% ≤0.134 水分,% ≤4.05 粘度(E80) ≤4.26 萘含量(无水基),% ≥7.0(不作考核指标)4.2硫酸铵—符合GB535-1995一级品序号指标名称质量指标1 氮N含量(以干基计),% ≥212 含水,% ≤0.33 游离酸含量,% ≤0.054.3粗苯—符合YB/T5022-1993序号指标名称质量指标(溶剂用)1 密度(20℃),g/ml ≤0.9002 75℃前馏出量(重),% ≤33 180℃前馏出量(重),% ≥91%室温(18~25℃)下目测无可见的不4 水分:溶解的水4.4洗油指标序号指标名称指标1 密度(20℃),g/ml 1.03~~1.062 馏程(大气压760mmHg),%序号指标名称指标230℃前馏出量(容),% ≥3.0300℃前馏出量(容),% ≥90.03 酚含量(容),% ≤0.54 萘含量(重),% ≤85 水分≤1.06 粘度(E25)≤2.07 15℃结晶物无4.5浓硫酸指标——符合GB/T534-2002序号指标名称质量指标1 硫酸(H2SO4)含量,% ≥92.5(Wt)2 灰分,% ≤0.03(Wt)2 铁(Fe)含量,% ≤0.01(Wt)3 砷(As) 含量,% ≤0.005 (Wt)4 汞(Hg)含量,% ≤0.01(Wt)5 铅(Pb)含量,5 ≤0.02(Wt)6 透明度,mm 50 (Wt)7 色度,ml ≤2.0 ml(Wt)4.6氢氧化钠指标(符合GB/T11199-2006)序号指标名称质量指标1 氢氧化钠(NaOH),%≥302 碳酸钠(Na2CO3)含量,%≤0.4%3 氯化钠(NaCl)含量,%≤0.044 三氧化二铁(Fe2O3)含量,%≤0.005煤气净化车间对荒煤气的初步冷却采用三段冷却工艺,并在煤气鼓风机前设置蜂窝式电捕焦油器脱除煤气中的焦油雾;随后煤气脱硫采用以PDS为催化剂的湿式催化氧化法脱硫工艺; 煤气脱氨采用喷淋式饱和器法生产硫铵工艺;煤气脱苯采用焦油洗油洗苯工艺,富油脱苯采用管式炉加热及带萘油侧线的单塔生产粗苯工艺。
焦炉煤气制液化天然气项目工艺流程
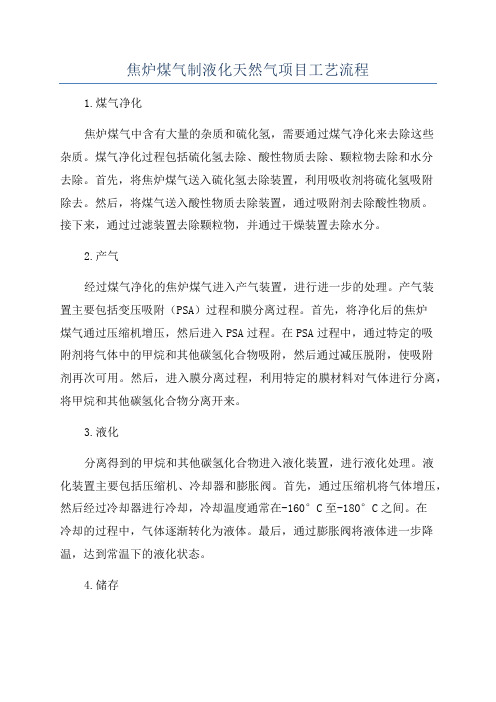
焦炉煤气制液化天然气项目工艺流程1.煤气净化焦炉煤气中含有大量的杂质和硫化氢,需要通过煤气净化来去除这些杂质。
煤气净化过程包括硫化氢去除、酸性物质去除、颗粒物去除和水分去除。
首先,将焦炉煤气送入硫化氢去除装置,利用吸收剂将硫化氢吸附除去。
然后,将煤气送入酸性物质去除装置,通过吸附剂去除酸性物质。
接下来,通过过滤装置去除颗粒物,并通过干燥装置去除水分。
2.产气经过煤气净化的焦炉煤气进入产气装置,进行进一步的处理。
产气装置主要包括变压吸附(PSA)过程和膜分离过程。
首先,将净化后的焦炉煤气通过压缩机增压,然后进入PSA过程。
在PSA过程中,通过特定的吸附剂将气体中的甲烷和其他碳氢化合物吸附,然后通过减压脱附,使吸附剂再次可用。
然后,进入膜分离过程,利用特定的膜材料对气体进行分离,将甲烷和其他碳氢化合物分离开来。
3.液化分离得到的甲烷和其他碳氢化合物进入液化装置,进行液化处理。
液化装置主要包括压缩机、冷却器和膨胀阀。
首先,通过压缩机将气体增压,然后经过冷却器进行冷却,冷却温度通常在-160°C至-180°C之间。
在冷却的过程中,气体逐渐转化为液体。
最后,通过膨胀阀将液体进一步降温,达到常温下的液化状态。
4.储存液化的天然气(LNG)通过输送管道进入储罐进行存储。
储罐通常采用双层结构,内层用于储存液化天然气,外层用于保温。
储罐还配备了安全阀和压力传感器,以确保储存的LNG的安全性。
以上是焦炉煤气制液化天然气(LNG)项目的工艺流程的详细描述。
通过煤气净化去除杂质和硫化氢,通过产气过程去除甲烷和其他碳氢化合物,然后通过液化和储存,将焦炉煤气转化为液态天然气,方便储存和运输。
这项工艺过程能够更高效地利用焦炉煤气,并提供更为清洁的能源。
焦炉煤气精脱硫工艺分析

焦炉煤气精脱硫工艺分析一、工艺原理:焦炉煤气中的H2S主要通过煤气中的Fegl肟羧酸盐、CaS等吸收剂进行吸收。
Fegl肟羧酸盐是一种高效的硫化物吸收剂,可在较低的温度下将煤气中的H2S和COS吸收。
而CaS则可以将煤气中的剩余H2S去除。
二、工艺流程:1.气体预处理:首先对焦炉煤气进行预处理,去除其中的悬浮颗粒物和水分,以净化煤气。
2.前骤吸收:采用Fegl肟羧酸盐作为吸收剂,通过吸收剂床将煤气中的H2S、COS等硫化物吸收。
床层中的吸收剂会与煤气中的硫化氢进行反应,生成硫化铁,并将其捕集。
3.普鲁士蓝阳极液循环:将废液中的硫化铁氧化为硫酸铁,通过循环泵送到反应床顶部,实现循环利用。
4.精脱硫:采用CaS作为吸收剂,通过床层吸收煤气中剩余的硫化氢,并将其转化为CaS。
此过程需要保持一定的温度和压力,以促使吸收反应的进行。
5.再复焦炉:将经过精脱硫的煤气送入焦炉进行再加热,以提高炉内温度。
三、工艺特点:1.高效: 采用Fegl肟羧酸盐和CaS作为吸收剂,可以高效地吸收煤气中的硫化物,使硫化氢的去除率达到90%以上,保证煤气的质量。
2.安全:精脱硫过程中对温度和压力的要求较高,可以有效地防止硫化氢的泄漏,保证了生产环境的安全。
3.循环利用:工艺中的废液通过循环泵送到反应床顶部,实现了废液中的硫化铁的循环利用,减少了废液的排放,具有较好的环保效益。
总结起来,焦炉煤气精脱硫工艺通过床层吸收剂的反应,有效地去除焦炉煤气中的硫化氢等硫化物,以保证煤气的质量达到环保要求。
该工艺具有高效、安全、循环利用等特点,在焦化行业得到广泛应用。
- 1、下载文档前请自行甄别文档内容的完整性,平台不提供额外的编辑、内容补充、找答案等附加服务。
- 2、"仅部分预览"的文档,不可在线预览部分如存在完整性等问题,可反馈申请退款(可完整预览的文档不适用该条件!)。
- 3、如文档侵犯您的权益,请联系客服反馈,我们会尽快为您处理(人工客服工作时间:9:00-18:30)。
焦炉煤气净化工艺流程的选择
(2011-01-24 13:14:42)
标签:
分类:焦化类
煤化工
杂谈
笑看人生
摘要:本文对我国煤气净化工艺的发展进行了回顾,提出了我国焦炉煤气净化工艺发展的方向以及选择工艺流程的原则。
并推荐采用的焦炉煤气净化工艺流程以及各单元中应采用的行之有效的环保、节能技术。
1 焦炉煤气净化工艺的历史回顾
我国焦炉煤气净化发展是与炼焦工业的发展紧密相连的。
建国以前,我国焦化工业几乎是一片空白。
建国以来,随着炼焦工业的发展,煤气净化工艺从无到有,蓬勃发展,技术水平和装备水平得到了不断提高。
概括起来,大体上经历了三个阶段。
第一个阶段是从20世纪50年代末到60年代中期,我国焦化厂的焦炉煤气净化工艺主要是以50年代从原苏联引进的工艺为基础、消化翻板饱和器法生产硫铵的老流程,以当时的武钢焦化厂、包钢焦化厂、鞍钢化工总厂、太钢焦化厂、马钢焦化厂等一批大型厂为代表。
但该工艺存在流程陈旧、能耗高、环保措施不健全、装备水平低等问题。
主要表现在初冷采用立管冷却器,冷却效率低;硫铵装置设备庞大,煤气阻力大,产品质量差,设备腐蚀严重;没有配套建设脱硫装置,终冷系统不能闭路,对大气和水体污染严重;在粗苯蒸馏系统采用蒸汽法,不但耗用大量蒸汽,产品质量也得不到保证。
第二阶段是从60年代中期至70年代末期,随着我国自行设计的58型焦炉不断推广及炭化室高5.5米焦炉的诞生,对煤气净化工艺开展了与石油、化工行业找差距进行技术革新的阶段。
在广大技术人员的努力下,在此期间我们将初冷流程改为二段冷却;开发了多种油洗萘代替终冷水洗萘;研制成功了终冷水脱氰生产黄血盐,解决了终冷水的污
染问题;推广采用了溶剂脱酚和生物脱酚装置;以管式炉脱苯代替蒸汽脱苯,开发了双塔、单塔脱苯新工艺;在个别焦化厂设置了改良ADA脱硫装置(如:梅山焦化厂、北京焦化厂等)。
除此之外,为了适应当时国内硫酸供应紧张的情况,开发和推广了一大批采用氨水流程的焦化厂(如:济钢、莱钢、邯钢、杭钢、安钢、攀钢等)。
当时,我国生产浓氨水的厂家曾占了整个焦化厂总数的三分之一。
但是,氨水流程也存在着设备腐蚀、堵塞严重、浓氨水产品质量低劣、产品滞销、开工率低等致命问题。
因此,虽然经过我国工程技术人员的不断努力,焦炉煤气净化工艺有了一些进展,而从环保、能耗、技术水平、工艺装备、产品质量等方面来看,仍然未能摆脱落后的局面。
第三阶段从改革开放以来算起,随着宝钢工程的建设,我国6米大容积焦炉的诞生,焦化厂的规模不断扩大,以及通过与国外技术交流,联合设计、技术引进等方式,先后引进了各种规模、不同工艺的多套装置,我国工程技术人员基本上掌握了全负压煤气净化工艺、AS洗涤脱硫工艺、脱酸蒸氨工艺、氨分解硫回收工艺、无饱和器法硫铵工艺、FRC法和T-H法脱硫脱氰工艺、索尔菲班法脱硫工艺、真空空碳酸盐法脱硫工艺、冷法和热法弗萨姆无水氨工艺以及与之相配套的生产浓硫酸和78%硫酸的工艺等国际先进技术,并在设备和材料国产化方面取得了突破性进展。
在此期间我国焦化技术人员还自行开发了HPF 法脱硫新工艺,消化创新了喷淋式饱和器代替半直接法饱和器生产硫铵装置。
随着工艺技术的不断更新,生产过程自动化控制水平也得了提高,DCS集散型计算机控制技术得到了广泛的应用,从而使我国煤气净化技术和装备有了一个质的飞跃,迈向了国际先进行列。
2 我国焦炉煤气净化工艺的发展方向
近年来随着国民环保意识的加强,国家环保法规日益严格,最近国家又制定焦化行业准入条件,对环保要求不断地提高。
为了达到这些要求,焦化厂基建投资和操作费用大大增加,生产成本明显提高,而市场经济的深入运作,把焦化企业推向市场大势所趋,21世纪焦化企业将面临着严峻挑战。
为了在市场竞争中求生存、求发展,焦化工作者应转变观念,在满足用户的净化煤气指标要求的前提下,把提高环保水平,消除或减轻环境污染;发展节能工艺;开发短流程,降低成本,增加效益;提高自控水平、实现生产过程优化控制,提高劳动生产率作为我国煤气净化工艺的发展方向。
以环保、节能、效益为中心选择煤气净化工艺流程。
3 焦炉煤气净化工艺流程的选择
上述多种型式的焦炉煤气净化工艺和单元装置,当前在我国焦化企业都已建成投产使用。
应该说我们已经基本掌握了当今世界先进水平的各种不同煤气净化单元装置的操作和管理,完全可以根据用户的不同要求组合成各种焦炉煤气净化工艺流程。
从焦炉煤气净化工艺流程的单元组成来看,流程的选择主要看采用什么方法脱除煤气中的硫化氢和氨,而当今国内外焦炉煤气净化技术发展趋势,其一是焦炉煤气脱硫脱氰装置设在终冷和洗苯前,使煤气尽可能在终冷前将大部分杂质除去,以减轻对水质和大气的污染,并降低对设备的腐蚀;其二是优先选择利用煤气本身的氨为碱源,脱除煤气中的硫化氢和氰化氨,这样可不需外加化学品,也利于综合利用。
(1)采用以氨为碱源的HPF湿式氧化法脱硫为中心的煤气净化工艺流程。
其基本组合见图1。
图1 以氨为碱源的HPF湿式氧化法脱硫为中心的煤气净化流程
该流程选用以氨为碱源的HPF法脱硫脱氰工艺, 并将其置于鼓风机前电捕焦油器之后负压操作,不再专门设置预冷装置,煤气系统温度梯度更趋合理。
在各单元装置中采用如下行之有效的环保、节能技术。
①选用带断液板的两段式横管冷却器,分段采出冷凝液,以节省低温水用量,将煤气冷却到22~ 25℃,最大限度地净化煤气,
不再单独设脱萘装置;焦油氨水采用沉降除渣的静置分离工艺,以保证焦油含水量<2%;采用蜂窝式沉淀管的电捕焦油器负压操作,有效地保护鼓风机;电动鼓风机采用液力偶合器或变频调速以节约能源。
②在HPF湿式氧化法脱硫工艺中,再生塔采用预混喷咀及塔中部设置气泡分离器的节能高效技术。
再生塔后尾气返回煤气负压
系统,以减少氨的损失,杜绝对大气的二次污染。
废液处理采用废液焚烧、接触法制取浓硫酸装置,生产的浓硫酸用于生产硫铵,可解决废液的污染等问题。
③蒸氨塔采用喷射器回收次蒸汽技术,减少蒸氨的蒸汽用量,以节约能
④采用喷淋式饱和器生气硫按,减少煤气系统阻力,降低鼓风机的耗电
⑤根据宝钢经验,增设循环水的水垢析出防止剂及防腐蚀剂的注入装置,装设电导计来掌握循环水的电导度控制排污,以提高
初冷器循环水出口温度,减少循环水量。
优先选用溴化锂制冷装置,保护水资源,提高水的利用率。
⑥放宽苯的回收指标,由塔后煤气含苯≤2g/m3放宽到4~5g/m3,减少脱苯系统的低温水用量以降低能耗。
经过各单元生产装置
的完善和优化组合而成的这套煤气净化工艺流程,预计在环保、节能、效益各方面能有较大的提高。
由于选用了以氨为碱源的脱硫脱氰工艺以及受废液制酸装置规模的限制,该流程仅适用于煤气含硫化氢≤8g/m3、生产规模在年产100万吨焦炭以上的大型焦化企业选用。
对于规模较小的焦化厂,可以采用脱硫废液回兑炼焦煤的方法处理;脱氨单元也可采用洗氨、蒸氨、氨分解的工艺,将分解后的尾气返回煤气负压系统的方案。
(2)采用以真空碳酸盐脱硫为中心的煤气净化流程。
其基本组合见图2。
图2 以真空碳酸盐脱硫为中心的煤气净化流程
这种组合流程由于采用真空碳酸盐脱硫,其位置应放在苯回收工序的后面,为了避免在整个系统中设置终冷装置造成排污水的污染,可采用洗氨、蒸氨的方法脱除煤气中的氨和部分氰化氢、硫化氢,蒸氨后的氨汽采用间接饱和器生产硫铵,尾气回到脱硫前煤气系统。
真空碳酸盐法脱硫属于湿式吸收法,采用真空解吸法再生,脱硫和再生系统均在低温下运行,腐蚀弱,对设备材料要求不高,吸收塔、再生塔及大部分设备材质为碳钢,基建费用低。
该脱硫工艺脱硫效率高,在脱硫塔上部增加NaOH洗涤段,可使煤气中H2S含量降至0.2g/m3以下,可满足焦化企业准入条件的要求。
所产硫磺转化率高,质量优良,克劳斯炉尾气返回吸煤气管道不会污染大气。
而且再生塔的热源可用废热锅炉生产蒸汽和初冷器所产的热水均可利用,故余热利用好。
该流程适用于煤气含硫化氢高的焦化企业,之所以该流程选用间接法生产硫铵是因为采用半直接法生产硫铵后,整个煤气系统的温度变化梯度大,还要设置终冷,造成流程长,能源利用不合理。
至于前述各单元的节能、环保措施,该流程完全可以采用。
(3)关于以氨硫循环洗涤(AS法)脱硫为中心的煤气净化工艺流程,在我国已有不少厂家采用,虽然该工艺也有不少优点,但由于其脱硫效率较低,一般只能达到煤气含硫化氢0.5g/m3的水平,不能满足焦化企业准入条件的要求。
此外,该工艺技术装备水平高,要求的外部条件苛刻,必须严格操作,一个环节出了问题,将影响整个氨硫系统的正常操作,目前我国已投产的装置还存在着堵塞腐蚀等问题,建议在国内选用时应慎重考虑。