HCTS85MS中文资料
HT85XXX中文资料
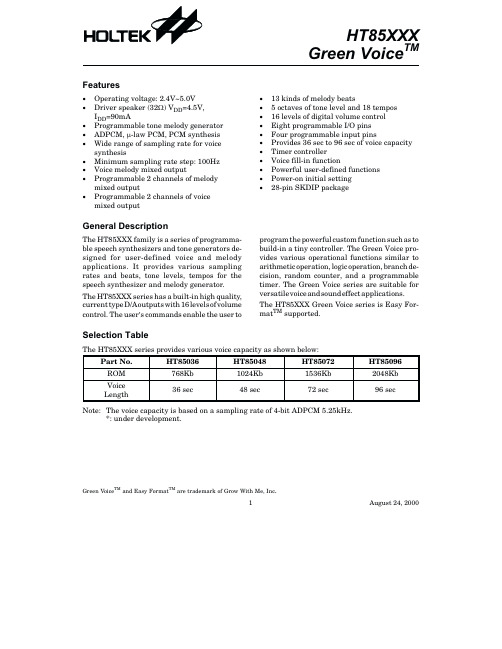
HT85XXX Green VoiceTM
Features
· Operating voltage: 2.4V~5.0V · Driver speaker (32W) VDD=4.5V,
IDD=90mA · Programmable tone melody generator · ADPCM, m-law PCM, PCM synthesis · Wide range of sampling rate for voice
Supply Voltage.................................-0.3V to 6V Input Voltage .................VSS-0.3V to VDD+0.3V
Storage Temperature.................-50°C to 125°C Operating Temperature ..............-20°C to 70°C
21, 22 VSS
¾
¾
Negative power supply, ground
23
OSC
I
¾
Built-in RC oscillator An oscillator resistor is connected between OSC and VSS
Absolute Maximum Ratings
Pin No.
Pin Name
I/O
Internal Connection
Description
1, 2, 8, 24~28
NC
¾
¾
No connection
3, 4, 5
PP0, PDA, PP1
S-8550中文资料

Package
Package Name SOT-23-5 Drawing Code Package MP005-A Tape MP005-A Reel MP005-A
Seiko Instruments Inc.
1
元器件交易网
STEP-DOWN, BUILT-IN FET, SYNCHRONOUS RECTIFICATION, PWM CONTROL SWITCHING REGULATORS
*2
*1. *2.
Refer to the taping specifications at the end of this book. Refer to Table 1 and Table 2 of “ Pin Configurations”.
Seiko Instruments Inc.
3
元器件交易网
700 Power dissipation (PD) [mW] 600 500 400 300 200 100 0 0 50 100 150 Ambient temperature (Ta) [°C]
Absolute Maximum Ratings (Unless otherwise specified: Ta = 25°C, VSS = 0 V) Absolute Maximum Rating VSS − 0.3 to VSS + 6.0 VSS − 0.3 to VIN + 0.3 VSS − 0.3 to VIN + 0.3 VSS − 0.3 to VIN + 0.3 1300 600*1 −40 to +85 −40 to +125 Unit V V V V mA mW °C °C
x
美国CalSys股份公司HDcctv系列产品技术规格书A
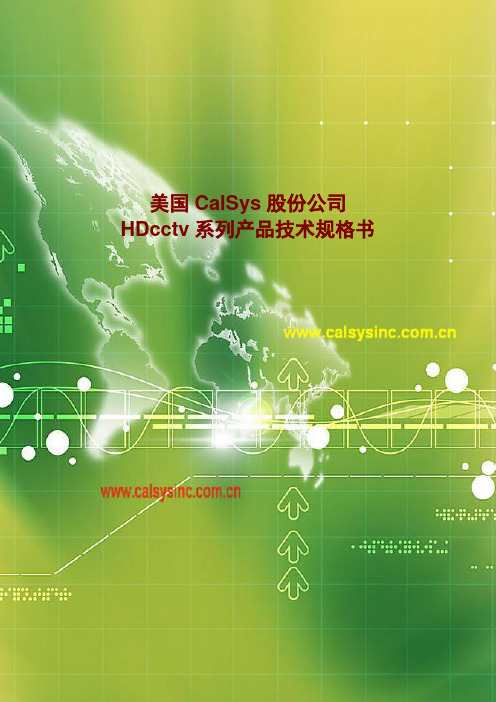
美国CalSys股份公司HDcctv系列产品技术规格书一、高清数字摄像机HD-SDI是广播级的影像传输技术,一直沿用在电视/电影摄像领域,具有成像清晰,画质无损、几乎零延时的传输特点。
业内将其引入安防领域,就是为了弥补IP摄像机的传输延时、画面有损状况。
采用HD-SDI传输技术的摄像机,是目前最新技术发展的缩影,最大特色是采用了SDI传输技术,有效距离可达110米,且无需对视频信号进行编解码及压缩与解压缩处理,直接传输到显示或存储设备,避免了IP网络传输的延迟及编解码过程造成的画面损坏和丢帧现象,实现了高清图像的无损、无延时传输。
1、高清半球形摄像机(红外、HD-SDI)产品描述:HD-SDI摄像机采用了Panasonic公司1/3英寸200万像素CMOS图像传感器,输出全高清1920*1080@30fps实时视频。
HD-SDI摄像机采用高性能ISP,保证视频清晰细腻、色彩还原真实。
200万像素红外HD-SDI摄像机是一款高清画质,图像无延时无压缩输出、日夜型高性能摄像机,适用于金融、电信、政府、机场、码头、交通监控等要求高清实时画质的场所。
技术参数:2、高清枪式摄像机(CMOS/HD-SDI)产品描述高清枪式摄像机采用了Panasonic公司1/3英寸200万像素CMOS图像传感器,输出全高清1920*1080@30fps 实时视频。
HD-SDI摄像机采用高性能ISP,保证视频清晰细腻、色彩还原真实。
(可选装红外功能)技术参数3、HD-SDI高清数字枪式摄像机(CCD)高清数字摄像机相机,是一款为高端监控量身定制的高清相机。
它除了具有标准监控相机的3A功能(AutoShutter, Auto Gain, Auto IRIS)以外,同时还具有AutoGamma这一独特的功能,配合上相机本身的高灵敏度,高信噪比,高动态范围等一些列的特点,为我们夜间的图像效果及图像亮度提供了良好的保障。
技术参数说明芯片类型逐行扫描 1/1.8英寸彩色 CCD芯片快门类型Global shutter芯片像元尺寸 4.4×4.4umA/D 转换器 14 bit数据接口High Definition Serial Data Interface (HD-SDI)传输速率 1.485Gbit/s视频输出连接器BNC 型连接器,800mVp-p,75-ohm,conforming to SMPTE 292Mserial interface standard视频信号1080P 25帧/30帧;720P 50/60帧数据输出格式YUV 4:2:2GPIO连接器Hirose HR25 8-pin female GPIO connector快门(曝光)自动/手动/one-push, 控制范围(0.02ms – 30ms)范围可调白平衡自动/手动/one-push增益自动/手动/one-push,控制范围(0db – 24db)且范围可调图像预处理Gamma校正,边缘锐化,饱和度,色调照度0.8lux存储器2个存储通道可以存储用户配置的参数摄像机尺寸44mm×29mm×58mm(W×D×H)重量150g 镜头接口方式 C mount 电压需求8-30V最大功率(最大)最大4W,电压为12V 工作温度-10℃- 55℃储藏温度-30℃ - +60℃通风需求自然空气对流保质期1年工作湿度范围20%-90% 抗震10G(20-200Hz)抗冲击70G4、HD-SDI 高清一体化摄像机(CMOS)产品性能:内置索尼最新的高清摄像机模块FCB-CH6300;支持1080P(1920*1080)与720P(1280*720)视频格式输出。
M80C85资料
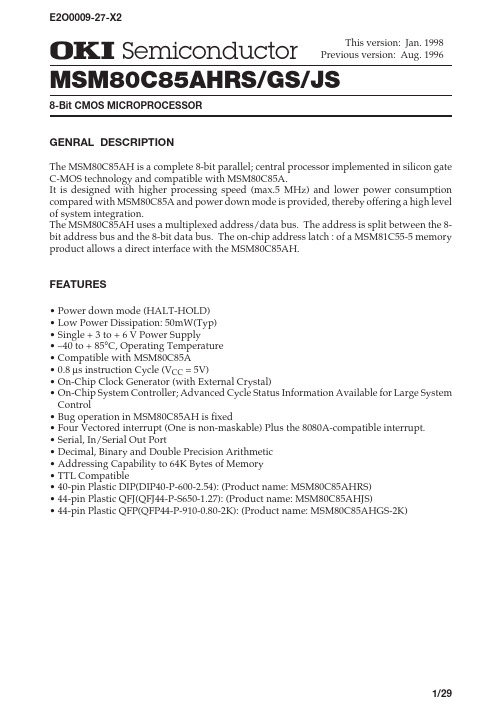
GENRAL DESCRIPTIONThe MSM80C85AH is a complete 8-bit parallel; central processor implemented in silicon gate C-MOS technology and compatible with MSM80C85A.It is designed with higher processing speed (max.5 MHz) and lower power consumption compared with MSM80C85A and power down mode is provided, thereby offering a high level of system integration.The MSM80C85AH uses a multiplexed address/data bus. The address is split between the 8-bit address bus and the 8-bit data bus. The on-chip address latch : of a MSM81C55-5 memory product allows a direct interface with the MSM80C85AH.FEATURES•Power down mode (HALT-HOLD)•Low Power Dissipation: 50mW(Typ)•Single + 3 to + 6 V Power Supply•–40 to + 85°C, Operating Temperature •Compatible with MSM80C85A •0.8 m s instruction Cycle (V CC = 5V)•On-Chip Clock Generator (with External Crystal)•On-Chip System Controller; Advanced Cycle Status Information Available for Large System Control•Bug operation in MSM80C85AH is fixed•Four Vectored interrupt (One is non-maskable) Plus the 8080A-compatible interrupt.•Serial, In/Serial Out Port•Decimal, Binary and Double Precision Arithmetic •Addressing Capability to 64K Bytes of Memory •TTL Compatible•40-pin Plastic DIP(DIP40-P-600-2.54): (Product name: MSM80C85AHRS)•44-pin Plastic QFJ(QFJ44-P-S650-1.27): (Product name: MSM80C85AHJS)•44-pin Plastic QFP(QFP44-P-910-0.80-2K): (Product name: MSM80C85AHGS-2K)MSM80C85AHRS/GS/JS8-Bit CMOS MICROPROCESSORE2O0009-27-X2元器件交易网FUNCTIONAL BLOCK DIAGRAMINTR INTA 5.5 6.57.5TRAP SID SODRSTX1X2CLK OUT READY RD WR ALE S0S1IO / M HOLD HLDA RESET IN RESET OUT A15 - A8Address BusAD7- ADAddress/Data BusPIN CONFIGURATION (TOP VIEW)40 pin Plastic DIPA 8HOLD HLDA CLK(OUT)RESET IN READY IO/M S 1RD WR ALE S 0A 15A 14A 13A 12A 11A 10A 9V CC 39383736353433READY IO/M S 1RD WR NC ALE TRAP RST7.5RST6.5RST5.5INTR NC INTA 18192021222324A D 4N C A D 5A D 6A D 7G N D A 865432144S I DS O DR E S E T X 2X 1N C7891011121332313029S 0A 15A 14AD 0AD 1AD 2AD 314151617A 13V C C25262728A 9A 10A 11A 1243424140H O L D H L D AC L K (O R E S E T I NTRAP RST7.5RST6.5RST5.5INTR INTA AD 0A D 4A D 5A D 6A D 7G N D V C C A 8AD 1AD 2AD 3NC A 9A 10A 11N CMSM80C85AH FUNCTIONAL PIN DEFINITIONThe following describes the function of each pin:A 0 - A 7(Input/Output)3-state A 8 - A 15(Output, 3-state)Multiplexed Address/Data Bus: Lower 8-bits of the memory address (or I/O address) appear on the bus during the first clock cycle (T state) of a machine cycle. It then becomes the data bus during the second and third clock cycles.Address Bus: The most significant 8-bits of the memory address or the 8-bits of the I/O address, 3-stated during Hold and Halt modes and during RESET.Symbol FunctionALE (Output)Address Latch Enable: It occurs during the first clock state of a machine cycle and enables address to get latched into the on-chip latch peripherals. The falling edge of ALE is set to guarantee setup and hold times for the address information. The falling edge ALE can also be used to strobe the status information ALE is never 3-state.S 0 , S 1 , IO/M (Output)Machine cycle status:IO/M S 1 S 0 States S 1 can be used as an advanced R/W status. IO/M , S 0 and S 1 become valid at the beginning ofa machine cycle and remain stable throughout the cycle. The falling edge of ALE may be used to latch the state of these lines.RD(Output, 3-state)READ control: A low level on RD indicates the selected memory or I/O device is to be read thatthe Data Bus is available for the data transfer, 3-stated during Hold and Halt modes and during RESET.WR(Output, 3-state)WRITE control: A low level on WR indicates the data on the Data Bus is to be written into the selected memory or I/O location. Data is set up at the trailing edge of WR , 3-stated during Hold and Halt modes and during RESET.READY (Input)If READY is high during a read or write cycle, it indicates that the memory or peripheral is ready to send or receive data. If READY is low, the cpu will wait an integral number of clock cycles for READY to go high before completing the read or write cycle READY must conform to specified setup and hold times.HOLD (Input)HLDA (Output)HOLD ACKNOWLEDGE: Indicates that the cpu has received the HOLD request and that it will relinquish the bus in the next clock cycle. HLDA goes low after the Hold request is removed. The cpu takes the bus one half clock cycle after HLDA goes low.HOLD indicates that another master is requesting the use of the address and data buses.The cpu, upon receiving the hold request, will relinquish the use of the bus as soon as the completion of the current bus transfer. Internal processing can continue. The processor can regain the bus only after the HOLD is removed. When the HOLD is acknowledged, the Address, Data, RD , WR , and IO/M lines are 3-stated. And status of power down is controlled by HOLD.INTR (Output)INTERRUPT REQUEST: Is used as a general purpose interrupt. It is sampled on during the next to the last clock cycle of an instruction and during Hold and Halt states. If it is active, the Program Counter (PC) will be inhibited from incrementing and an INTA will be issued. During this cycle a RESTART or CALL instruction can be inserted to jump to the interrupt service routine. The INTR is enabled and disabled by software. It is disabled by Reset and immediately after an interrupt is accepted. Power down mode is reset by INTR.INTA (Output)INTERRUPT ACKNOWLEDGE: Is used instead of (and has the same timing as) RD during the instruction cycle after an INTR is accepted.RST 5.5RST 6.5RST 7.5(Input)RESTART INTERRUPTS: These three inputs have the same timing as INTR except they cause an internal RESTART to be automatically inserted.The priority of these interrupts is ordered as shown in Table 1. These interrupts have a higher priority than INTR. In addition, they may be individually masked out using the SIM instruction. Power down mode is reset by these interrupts.TRAP (Input)Trap interrupt is a nonmaskable RESTART interrupt. It is recognized at the same timing as INTR or RST 5.5 - 7.5. It is unaffected by any mask or Interrupt Disable. It has the highest priority of any interrupt. (See Table 1.) Power down mode is reset by input of TRAP.001100101110101Memory write Memory read I/O write I/O readOpcode fetchIO/M S 1 S 0 States 1...10¥¥10¥¥Interrupt Acknowledge Halt = 3-stateHold (high impedance)Reset ¥ = unspecifiedName Address Branched To (1)When Interrupt OccursType TriggerRST 7.53CH 34H Rising edge (latched).High level unitl sampled.RST 6.5RST 5.52CH (2)High level until sampled.High level until sampled.INTRTRAP Priority 2345124H Rising edge and high level unit sampled.Table 1 Interrupt Priority, Restart Address, and SensitivityNotes:(1)The processor pushes the PC on the stack before branching to the indicatedaddress.(2)The address branched to depends on the instruction provided to the cpuwhen the interrupt is acknowledged.RESET IN (Input)Sets the Program Counter to zero and resets the Interrupt Enable and HLDA flip-flops and release power down mode. The data and address buses and the control lines are 3-stated during RESET and because of the asynchronous nature of RESET IN, the processor's internal registers and flags may be altered by RESET with unpredictable results. RESET IN is a Schmitt-triggered input, allowing connection to an R-C network for power-on RESET delay. The cpu is held in the reset condition as long as RESET IN is applied.Symbol FunctionRESET OUT (Output)Indicated cpu is being reset. Can be used as a system reset. The signal is synchronized to the processor clock and lasts an integral number of clock periods.X 1, X 2(Input)X 1 and X 2 are connected to a crystal to drive the internal clock generator. X 1 can also be an external clock input from a logic gate. The input frequency is divided by 2 to give the processor's internal operating frequency.SID (Input)Serial input data line. The data on this line is loaded into accumulator bit 7 whenever a RIM instruction is executed.SOD (Output)Serial output data line. The output SOD is set or reset as specified by the SIM instruction.V CC + 5 Volt supply GNDGround Reference.CLK (Output)Clock Output for use as a system clock. The period of CLK is twice the X 1, X 2 input period.FUNCTIONAL DESCRIPTIONThe MSM80C85AH is a complete 8-bit parallel central processor. It is designed with silicon gate C-MOS technology and requires a single +5 volt supply. Its basic clock speed is 5 MHz, thus improving on the present MSM80C85A's performance with higher system speed and power down mode. Also it is designed to fit into a minimum system of two IC's: The CPU (MSM80C85AH), and a RAM/IO (MSM81C55-5)The MSM80C85AH has twelve addressable 8-bit register pairs. Six others can be used interchangeably as 8-bit registers or 16-bit register pairs. The MSM80C85AH register set is as follows:PC 16-bit address 8-bit ¥ 6 or 16-bits ¥ 3BC, DE, HL SP 16-bit address 5 flags (8-bit space)Flags or FProgram CounterACC or A 8-bits Accumulator Mnemonic ContentsRegisterGeneral-Purpose Registers; data pointer (HL)Stack Pointer Flag RegisterThe MSM80C85AH uses a multiplexed Data Bus. The address is spilt between the higher 8-bit Address Bus and the lower 8-bit Address/Data Bus. During the first T state (clock cycle) of a machine cycle the low order address is sent out on the Address/Data Bus. These lower 8-bits may be latched externally by the Address Latch Enable signal (ALE). During the rest of the machine cycle the data bus is used for mamory or I/O data.The MSM80C85AH provides RD , WR , S 0, S 1, and IO/M signals for bus control. An Interrupt Acknowledge signal (INTA ) is also provided. Hold and all Interrupts are synchronized with the processor's internal clock. The MSM80C85AH also provides Serial Input Data (SID) and Serial Output Data (SOD) lines for a simple serial interface.In addition to these features, the MSM80C85AH has three maskable, vector interrupt pins, one nonmaskable TRAP interrupt and power down mode with HALT and HOLD.INTERRUPT AND SERIAL I/OThe MSM80C85AH has 5 interrupt inputs: INTR, RST 5.5 RST 6.5, RST 7.5, and TRAP. INTR is identical in function to the 8080A INT. Each of the three RESTART inputs, 5.5, 6.5, and 7.5, has a programmable mask. TRAP is also a RESTART interrupt but it is nonmaskable.The three maskable interrupts cause the internal execution of RESTART ( saving the program counter in the stack branching to the RESTART address) it the interrupts are enable and if the interrupt mask is not set. The nonmaskable TRAP causes the internal execution of a RESTART vector independent of the state of the interrupt enable or masks. (See Table 1.)There are two different types of inputs in the restart interrupt. RST 5.5 and RST 6.5 are high level-sensitive like INTR (and INT on the 8080A) and are recognized with the same timing as INTR. RST 7.5 is rising edge-sensitive.For RST 7.5, only a pulse is required to set an internal flip-flop which generates the internal interrupt request. The RST 7.5 request flip-flop remains set until the request is serviced. Then it is reset automatically, This flip-flop may also be reset by using the SIM instruction or by issuing a RESET␣IN to the MSM80C85AH. The RST 7.5 internal flip-flop will be set by a pulse on the RST 7.5 pin even when the RST 7.5 interrupt is masked out.The interrupts are arranged in a flixed priority that determines which interrupt is to be recognized if more than one is pending, as follows: TRAP-highest priority, RST 7.5, RST 6.5, RST 5.5, INTR-lowest priority. This priority scheme does not take into account the priority of a routine that was started by a higher priority interrupt. RST 5.5 can interrupt an RST 7.5 routine if the interrupt are re-enabled before the end of the RST 7.5 routine.The TRAP interrupt is useful for catastrophic evens such as power failure or bus error. The TRAP input is recognized just as any other interrupt but has the highest priority. It is not affected by any flag or mask. The TRAP input is both edge and level sensitive. The TRAP input must go high and remain high until it is acknowledged. It will not be recognized again until it goes low, then high again. This avoids any false triggering due to noise or logic glitches. Figure 3 illustrates the TRAP interrupt request circuitry within the MSM80C85AH. Note that the servicing of any interrupt (TRAP, RST 7.5, RST 6.5, RST 5.5,INTR) disables all future interrupts (except TRAPs) until an El instruction is executed.The TRAP interrupt is special in that it disables interrupts, but preserves the previous interrupt enable status. Performing the first RIM instruction following a TRAP interrupt allows you to determine whether interrupts were enabled or disabled prior to the TRAP. All subsequent RIM instructions provide current interrupt enable status. Performing a RIM instruction following INTR or RST 5.5-7.5 will provide current interrupt Enable status, revealing that Interrupts are disabled.The serial I/O system is also controlled by the RIM and SIM instructions. SID is read by RIM, and SIM sets the SOD data.AcknowledgeFigure 3 Trap and RESET IN CircuitDRIVING THE X 1 AND X 2 INPUTSYou may drive the clock inputs of the MSM80C85AH with a crystal, or an external clock source.The driving frequency must be at least 1 MHz, and must be twice the desired internal clock frequency; hence, the MSM80C85AH is operated with a 6 MHz crystal (for 3 MHz clock). If a crystal is used, it must have the following characteristics:Parallel resonance at twice the clock frequency desired C L (load capacitance) £ 30 pF C S (shunt capacitance) £ 7 pFR S (equivalent shunt resistance) £ 75 ohms Drive level: 10 mWFrequency tolerance: ±0.05% (suggested)Note the use of the capacitors between X 1, X 2 and ground. These capacitors are required to assure oscillator startup at the correct frequency.Figure 4 shows the recommended clock driver circuits. Note in B that a pull-up resistor is required to assure that the high level voltage of the input is at least 4 V.For driving frequencies up to and including 6 MHz you may supply the driving signal to X, and leave X 2 open-circuited (Figure 4B). To prevent self-oscillation of the MSM80C85AH, be sure that X 2 is not coupled back to X 1 through the driving circuit.Note:Since the constant values may vary depending on oscillator, consult the manufacturer of the oscillator used when designing a circuit.Figure 4 Clock Driver Circuits* X 2 Left Floating33 pF Capacitor required for crystal frequency 10 to 6.25 MHz 50 pF Capacitor required for crystal frequency 6.25 to 4 MHz 100 pF Capacitor required for crystal frequency <4 MHzA. Quartz Crystal Clock DriverB. 1 - 10 MHz Input Frequency External Clock Drive CircuitBASIC SYSTEM TIMINGThe MSM80C85AH has a multiplexed Data Bus. ALE is used as a strobe to sample the lower 8-bits of address on the Data Bus. Figure 5 shows an instruction fetch, memory read and I/O write cycle (as would occur during processing of the OUT instruction). Note that during the I/ O write and read cycle that the I/O port address is copied on both the upper and lower half of the address.There are seven possible types of machine cycles. Which of these seven takes place is defined by the status of the three status lines (IO/M, S1, S0) and the three control signals (RD, WR,and INTA). (See Table 2.) The status line can be used as advanced controls (for device selection, for example), since they become active at the T1 state, at the outset of each machine cycle. Control lines RD and WR become active later, at the time when the transfer of data is to take place, so are used as command lines.A machine cycle normally consists of three T states, with the exception of OPCODE FETCH, which normally has either four or six T states (unless WAIT or HOLD states are forced by the receipt of READY or HOLD inputs). Any T state must be one of ten possible states, shown in Table 3.Table 2 MSM80C85AH Machine Cycle ChartTable 3 MSM80C85AH Machine State Chart0= Logic "0"1= Logic "1"TS = High Impedance ¥= UnspecifiedNotes:(1) ALE not generated during 2nd and 3rd machine cycles of DAD instruction.(2) IO/M = 1 during T 4 - T 6 of INA machine cycle.A AD IO/Figure 5 MSM80C85AH Basic System TimingPOWER DOWN ModeThe MSM80C85AH is compatible with the MSM80C85A in function and POWER DOWN mode. This reduces power consumption further.There are two methods available for starting this POWER DOWN mode. One is through software control by using the HALT command and the other is under hardware control by using the pin HOLD. This mode is released by the HOLD, RESET, and interrupt pins (TRAP, RST7.5, RST6.5 RST5.5, or INTR). (See Table 4.)Since the sequence of HALT, HOLD, RESET, and INTERRUPT is compatible with MSM80C85A, every the POWER DOWN mode can be used with no special attention.Start by means of Halt command Start by means of HOLD pin Released by using pins RESET and INTERRUPT (not by pin HOLD) Released by using RESET and HOLD pins (not by interrupt pins)Table 4 POWER DOWN Mode Releasing Method(1) Start by means of HALT command (See Figures 6 and 7.)The POWER DOWN mode can be started by executing the HALT command.At this time, the system is put into the HOLD status and therefore the POWER DOWN mode cannot be released even when the HOLD is released later.In this case, the POWER DOWN mode can be released by means of the RESET or interrupt.(2) Start by means of HOLD pin (See Figure 8.)During the execution of commands other than the HALT, the POWER DOWN mode is started when the system is put into HOLD status by means of the HOLD pin.Since no interrupt works during the execution of the HOLD, the POWER DOWN mode cannot be released by means of interrupt pins. In this case, the POWER DOWN mode can be released either by means of the RESET pin or by releasing the HOLD status by means of HOLD pin.CLK (OUT)ALEAD 0-7CPU MODE RESET INFigure 6 Started by HALT and Released by RESET INCLK (OUT)ALEHOLD CPU MODEHLDAFigure 8 Started and Released by HOLDCLK (OUT)ALECPU MODERST5.5Figure 7 Started by HALT and Released by RST5.5ABSOLUTE MAXIMUM RATINGS–55 - +150MSM80C85AHRS Power Supply Voltage V CC –0.5 - 7V Input Voltage V IN –0.5 - V CC +0.5V Output Voltage V OUT –0.5 - V CC +0.5V Storage Temperature T STG °CPower DissipationP D0.7WParameter Units Symbol With respect to GND—Ta = 25°CCondition LimitsMSM80C85AHGS MSM80C85AHJS1.01.0OPERATING RANGELimits Power Supply Voltage V CC 3 - 6V Operating TemperatureT OP–40 - +85°CParameterUnit Symbol RECOMMENDED OPERATING CONDITIONSDC CHARACTERISTICS"L"V ILR —–0.3+0.8Typ.Power Supply Voltage V CC 5V T OP +25"L" Input Voltage V IL —"H" Output Voltage V IH —Min.4.5–40–0.32.2Max.5.5+85+0.8V CC +0.3ParameterUnit Symbol °C V V Operating Temperature V V IHR—3.0V CC +0.3VRESET IN Input Voltage "H"RESET IN Input VoltageTyp.Max."L" Output Voltage V OL —0.4V "H" Output Voltage V OH ——V ——V Parameter Unit Symbol Min.—3.0V CC - 0.4I OL = 2.5 mA I OH = –2.5 mA I OH = –100 m A ConditionsV CC = 4.5 V - 5.5 V Ta = –40°C - +85°C Input Leak Current I LI —10m A Output Leak CurrentI LO—10m A –10–100 £ V IN £ V CC 0 £ V OUT £ V CC T cyc = 200 ns C L = 0 pF at reset Operating SupplyCurrentI CC1020mA 510mA——T cyc = 200 nsC L = 0 pF at power down modeAC CHARACTERISTICSParameter Symbol Condition Min.Max.UnitCLY Cycle Period t CYCt CYC=200 nsCL=150 pF 2002000nsCLY Low Time t140—ns CLY High Time t270—ns CLY Rise and Fall Time t r, t f—30nsX1 Rising to CLK Rising t XKR25120nsX1 Rising to CKK Falling t XKF30150nsA8~15 Valid to Leading Edge of Control (1)t AC115—ns AD0~7 Valid to Leading Edge of Control t ACL115—ns AD0~15 Valid Data in t AD—350ns Address Float After Leading Edge of RD INTA t AFR—0nsA8~15 Valid Before Trailing Edge of ALE (1)t AL50—ns AD0~7 Valid Before Trailing Edge of ALE t ALL50—ns READY Valid from Address Valid t ARY—100ns Address (A8~15) Valid After Control t CA60—ns Width of Control Law (RD, WR, INTA)t CC230—ns Trailing Edge of Control to Leading Edges of ALE t CL25—ns Data Valid to Trailing Edge of WR t DW230—ns HLDA to Bus Enable t HABE—150ns Bus Float After HLDA t HABF—150ns HLDA Valid to Trailing Edge of CLK t HACK40—ns HOLD Hold Time t HDH0—ns HOLD Step Up Time to Trailing Edge of CLK t HDS120—ns INTR Hold Time t INH0—ns INTR, RST and TRAP Setup Time to Falling Edge of CLK t INS150—ns Address Hold Time After ALE t LA50—ns Trailing Edge of ALE to Leading Edge of Control t LC60—ns ALE Low During CLK High t LCK50—ns ALE to Valid Data During Read t LDR—270ns ALE to Valid Data During Write t LDW—140ns ALE Width t LL80—ns ALE to READY Stable t LRY—30ns Trailing Edge of RD to Re-enabling of Address t RAE90—ns RD (or INTA) to Valid Data t RD—150ns Control Trailing Edge to Leading Edge of Next Control t RV220—ns Data Hold Time After RD INTA (7)t RDH0—ns READY Hold Time t RYH0—ns READY Setup Time to Leading Edge of CLK t RYS100—ns Data Valid After Trailing Edge of WR t WD60—ns LEADING Edge of WR to Data Vaild t WDL—20ns(Ta = –40°C ~ 85°C, V CC = 4.5 V ~ 5.5 V)Notes:(1)A 8 - A 15 address Specs apply to IO/M , S 0 and S 1.(2)Test condition: t CYC =200 ns C L =150 pF(3)For all output timing where C L =150 pF use the following correction factors:25 pF £ C L < 150 pF : –0.10ns/pF 150 pF < C L £ 200 pF : +0.30ns/pF(4)Output timings are measured with purely capacitive load.(5)All timings are measured to output voltage V L =0.8 V, V H =2.2 V, and 1.5 Vwith 10 ns rise and fall time on inputs.(6)To calculate timing specifications at other values of t CYC use Table 7.(7)Data hold time is guaranteed under all loading conditions.2.40.45Input Waveform for A.C. Tests:(1/2)T - 50t AL Min (Ta = -40°C - +85°C, V CC = 4.5 V - 5.5 V, C L = 150 pF)(1/2)T - 50t LA Min (1/2)T - 20t LL Min (1/2)T - 50t LCK Min (1/2)T - 40t LC Min (5/2+N)T - 150t AD Max (3/2+N)T - 150t RD Max (1/2)T - 10t RAE Min (1/2)T - 40t CA Min (3/2+N)T -70t DW Min (1/2)T - 40t WD Min (3/2+N)T - 70t CC Min (1/2)T - 75t CL Min (3/2)T - 200t ARY Max (1/2)T - 60t HACK Min (1/2)T + 50t HABF Max (1/2)T + 50(2/2)T - 85t HABE Max t AC Min (1/2)T - 60t 1Min (1/2)T - 30t 2Min (3/2)T - 80t RV Min t LDRMax——————————————————————MSM80C85AH Table 7 Bus Timing Specification as a T CYC DependentNote:N is equal to the total WAIT states.T = t CYC(2+N)T -130X1 INPUTCLKOUTPUTFigure 6 Clock Timing Waveform READ OPERATIONCLKA8-A15 AD0-AD7ALE RD / INTA T1T2T3T1WRITE OPERATIONCLK T1A8-A15AD0-AD7ALEWRT2T3T1CLKA 8~A 15AD 0~AD 7ALERD / INTAREADYT 1T 2T WAIT T 3T 1Note: READY must remain stable during setup and hold times.Figure 7 MSM80C85AH Bus Timing, With and Without WaitRead operation with Wait Cycle (Typical)–same READY timing applies to WRITE operationCLK HOLDHLDA BUSFigure 8 MSM80C85AH Hold TimingHOLD OPERATIONNOTE: (1) IO/M is also floating during this time.Figure 9 MSM80C85AH Interrupt and Hold TimingMOVE, LOAD, AND STORE MOVr1 r2MOV M r MOV r M MVI r MVI M LXI B LXI D LXI H LXI SP STAX B STAX D LDAX B LDAX D STA LDA SHLD LHLD XCHG MnemonicDescriptionInstruction Code (1)Clock (2)Cycles000000000000000001111000000000000001D 1D D 10011000011111D 1D D 10101010111000D 0D D 00000001101011S S 1110000000000000S S 1110000111111111S S 0001111000000001D 7D 6D 5D 4D 3D 2D 1D 0477710101010107777131316164Move register to register Move register to memory Move memory to register Move immediate register Move immediate memory Load immediate register Pair B & C Load immediate register Pair D & E Load immediate register Pair H & L Load immediate stack pointer Store A indirect Store A indirect Load A indirect Load A indirect Store A direct Load A direct Store H & L direct Load H & L direct Exchange D & E H & L registers STACK OPS PUSH B PUSH D PUSH H PUSH PSW POP B POP D POP H POP PSW XTHL SPHL 111111111111111111110011001111010101010100000000011111000000000000001011111111111212121210101010166Push register Pair B & C on stack Push register Pair D & E on stack Push register Pair H & L on stack Push A and Flags on stackPop register Pair B & C off stack Pop register Pair D & E off stack Pop register Pair H & L off stack Pop A and Flags off stack Exchange top of stack H & L H & L to stack pointer JUMP JMP JC JNC JZ JNZ JP JM JPE JPO PCHL 11111111111111111111000001111101100110000101001101000000000011111111101000000001107/107/107/107/107/107/107/107/106Jump unconditional Jump on carry Jump on no carry Jump on zero Jump on no zero Jump on positive Jump on minus Jump on parity even Jump on parity oddH & L to program counter CALL CALL CC CNC CZ CNZ CP CM CPE CPO111111111111111111000001111011001100110100110111111111000000000100000000189/189/189/189/189/189/189/189/18Call unconditional Call on carry Call on no carry Call on zero Call on no zero Call on positive Call on minus Call on parity even Call on parity oddTable 8 Instruction Set SummaryRETURN RET RC RNC RZ RNZ RP RM RPE RPO Mnemonic DescriptionInstruction Code (1)Clock (2)Cycles 111111111111111111000001111011001100110100110000000000000000000100000000D 7D 6D 5D 4D 3D 2D 1D 0106/126/126/126/126/126/126/126/12ReturnReturn on carry Return on no carry Return on zero Return on no zero Return on positive Return on minus Return on parity even Return on parity odd RESTART RST11A A A 11112Restart INPUT/OUTPUT IN OUT11110011100011111010Input OutputINCREMENT AND DECREMENT INR r DCR r INR M DCR M INX B INX D INX H INX SP DCX B DCX D DCX H DCX SP 000000000000000000000000D D 1100110011D D 1101010101D D 000000111111110000000000001111111101011111111144101066666666Increment register Decrement register Increment memory Decrement memory Increment B & C registers Increment D & E registers Increment H & L registers Increment stack pointer Decrement B & C Decrement D & E Decrement H & L Decrement stack pointer ADD ADD r ADC r ADD M ADC M ADI ACI DAD B DAD D DAD H DAD SP 11111100000000110000000000001100000001010101011111S S 11110000S S 11110000S S 0000111144777710101010Add register to AAdd register to A with carry Add memory to AAdd memory to A with carry Add immediate to AAdd immediate to A with carry Add B & C to H & L Add D & E to H & L Add H & L to H & LAdd stack pointer to H & LSUBTRACT SUB r SBB r SUB M SBB M SUI SBI111111000011000000111111010101S S 1111S S 1111S S 0000447777Subtract register from ASubtract register from A with borrow Subtract memory from ASubtract memory from A with borrow Subtract immediate from ASubtract immediate from A with borrowTable 8 Instruction Set Summary cont'd。
HSMR-C177中文资料

Features•High brightness •Small size•Industrial standard footprint •Diffused optics•Top emitting or right angle emitting•Compatible with IR soldering •Compatible for use with light piping•Available in 8 mm tape on 7" diameter reel•Reel sealed in zip locked moisture barrier bagsApplications•LCD backlighting•Push button backlighting •Front panel indicator •Symbol indicator •Microdisplays•Small message panel signageDescriptionThese small chip-type LEDs utilize high efficient and high brightness InGaN material to deliver competitively priced highperformance blue and green. These 520 nm green and 470 nm blue are unique hues which provide color differentiation to a product.These ChipLEDs come in either top emitting packages (HSMx-C130,C150, C170, C177, C190, C191,C197), in side emitting packages (HSMx-C110, C120) or in a reverse mount package (C265). The sideemitting package is especially suitable for LCD backlighting application. The top emittingpackages, with their wide viewing angle, are suitable for directbacklighting application or being used with light pipes. In order to facilitate pick and place operation,these ChipLEDs are shipped in tape and reel with 4000 units per reel for HSMx-C120, C130, C170,C177, C190, C191 and C197packages, and 3000 units per reel for HSMx-C110, C150 and C265packages. All packages arecompatible with IR soldering and binned by both color and intensity.Agilent HSMx-C1xxHigh Performance Chip LEDData SheetHSMQ-C110/120/150/170/177/190/191/197/265,HSMR-C110/120/130/150/170/177/190/191/197/265CAUTION: HSMQ-C1xx and HSMR-C1xx are Class 1 ESD sensitive per MIL-STD-1686. Please observe appropriate precautions during handling and processing. Refer to Agilent Technologies Application Note AN-1142 for additional details.Package DimensionsNOTES:1. ALL DIMENSIONS IN MILLIMETERS (INCHES).0.4 ± 0.150.4 ± 0.15TERMINALHSMx-C170HSMx-C1900.3 ± 0.151.0TERMINALHSMx-C1910.3 ± 0.151.0TERMINALPOLARITYTERMINALHSMx-C110Package Dimensions, continuedNOTES:1. ALL DIMENSIONS IN MILLIMETERS (INCHES).HSMx-C1500.50 ± 0.20 0.50 ± 0.20 TERMINALPOLARITYTERMINAL0.40 ± 0.15HSMx-C177POLARITY0.30 ± 0.15TERMINALHSMx-C197POLARITYTERMINALHSMx-C120Absolute Maximum Ratings at T A = 25˚C HSMQ-Cxxx ParameterHSMR-Cxxx Units DC Forward Current [1]20mA Power Dissipation78mW Reverse Voltage (I R = 100 µA)5V LED Junction Temperature 95˚C Operating Temperature Range –30 to +85˚C Storage Temperature Range –40 to +85˚CDevice Selection Guide Package Dimension (mm) [1], [2]InGaN Green InGaN Blue Package Description 3.2(L) x 1.0(W) x 1.5(H)HSMQ-C110HSMR-C110Untinted, Non-diffused 1.6(L) x 0.6(W) x 1.0(H)HSMQ-C120HSMR-C120Untinted, Non-diffused 1.6(L) x 0.8(W) x 0.35(H)–HSMR-C130Untinted, Diffused 3.2(L) x 1.6(W) x 1.1(H)HSMQ-C150HSMR-C150Untinted, Diffused 2.0(L) x 1.25(W) x 0.8(H)HSMQ-C170HSMR-C170Untinted, Diffused 2.0(L) x 1.25(W) x 0.4(H)HSMQ-C177HSMR-C177Untinted, Diffused 1.6(L) x 0.8(W) x 0.8(H)HSMQ-C190HSMR-C190Untinted, Diffused 1.6(L) x 0.8(W) x 0.6(H)HSMQ-C191HSMR-C191Untinted, Diffused 1.6(L) x 0.8(W) x 0.4(H)HSMQ-C197HSMR-C197Untinted, Diffused 3.4(L) x 1.25(W) x 1.1(H)HSMQ-C265HSMR-C265Untinted, Non-diffusedNotes: 1. Dimensions in mm. 2. Tolerance ± 0.1 mm unless otherwise noted.NOTES:1. ALL DIMENSIONS IN MILLIMETERS (INCHES).2. TOLERANCE IS ± 0.1 mm (± 0.004 IN.) UNLESS OTHERWISE SPECIFIED.Package Dimensions, continued0.3 ± 0.15POLARITYTERMINALHSMx-C1300.50 ± 0.15 POLARITY0.50 ± 0.15 TERMINALHSMx-C265Optical Characteristics at T A = 25˚CLuminous Color,Viewing Luminous Intensity PeakDominant Angle Efficacy I V (mcd)Wavelength Wavelength 2 θ1/2ηV @ 20 mA [1]λpeak (nm)λd [2] (nm)Degrees [3](lm/w)Part NumberColor Min.Typ.Typ.Typ.Typ.Typ.HSMQ-C110Green 45150520527130500HSMQ-C120Green 45145520527155500HSMQ-C150/170/190/191Green 45145520527140500HSMQ-C177/197Green 45145520527130500HSMQ-C265Green 45140520527150500HSMR-C110Blue 186046947313088HSMR-C120Blue 185546947315588HSMR-C130Blue 185546947314588HSMR-C150/170/190/191Blue 185546947314088HSMR-C177/197Blue 185546947313088HSMR-C265Blue184546947315088Notes:1.The luminous intensity, I V , is measured at the peak of the spatial radiation pattern which may not be aligned with the mechanical axis of the lamp package.2.The dominant wavelength, λd , is derived from the CIE Chromaticity Diagram and represents the perceived color of the device.3.θ1/2 is the off-axis angle where the luminous intensity is 1/2 the peak intensity.Electrical Characteristics at T A = 25˚CForward Voltage Reverse Breakdown Capacitance C Thermal V F (Volts)V R (Volts)(pF), V F = 0,Resistance @ I F = 20 mA @ I R = 100 µA f = 1 MHz R θJ–PIN (˚C/W)Part Number Typ.Max.Min.Typ.Typ.HSMQ-C110/C150 3.4 3.95140450HSMR-C110/C150 3.4 3.95140450HSMQ-C1203.4 3.95100450HSMR-C120/C1303.4 3.95100450HSMQ-C170/C190/C191 3.4 3.95110300HSMR-C170/C190/C191 3.4 3.95110300HSMQ-C177/C197 3.4 3.95110350HSMR-C177/C197 3.4 3.95110350HSMQ-C265 3.4 3.9565300HSMR-C2653.43.9565300V F Tolerance: ±0.1 VBlue Color Bins [1]Dom. Wavelength (nm)Bin ID Min.Max.A 460.0465.0B 465.0470.0C 470.0475.0D475.0480.0Note:Color Bin Limits [1]InGaN Green Color Bins [1]Dom. Wavelength (nm)Bin IDMin.Max.A 515.0520.0B 520.0525.0C 525.0530.0D530.0535.0Tolerance: ±1 nmTolerance: ±1 nmFigure 1. Relative intensity vs. wavelength.Light Intensity (Iv) Bin Limits[1]Intensity (mcd)Intensity (mcd)Bin ID Min.Max.Bin ID Min.Max.A0.110.18N28.5045.00B0.180.29P45.0071.50C0.290.45Q71.50112.50D0.450.72R112.50180.00E0.72 1.10S180.00285.00F 1.10 1.80T285.00450.00G 1.80 2.80U450.00715.00H 2.80 4.50V715.001125.00J 4.507.20W1125.001800.00K7.2011.20X1800.002850.00L11.2018.00Y2850.004500.00M18.0028.50Tolerance: ±15%Note:1.Bin categories are established for classification of products. Products may not be available in allcategories. Please contact your Agilent representative for information on currently available bins.Figure 2. Forward current vs. forward voltage.Figure 3. Luminous intensity vs. forward Figure 4. Maximum forward current vs.1010.1V F – FORWARD VOLTAGE – VIF–FORWARDCURRENT–mAI F – FORWARD CURRENT – mALUMINOUSINTENSITY(NORMALIZEDAT2mA)WAVELENGTH – nmRELATIVEINTENSITY–%10050600700BLUE GREEN50040090807060403020105IFMAX–MAXIMUMFORWARDCURRENT–mAT A – AMBIENT TEMPERATURE – °C15102025Figure 5. Relative intensity vs. angle for HSMx-C110.R E L A T I V E I N T E N S I T Y – %1000ANGLE80602040-70-50-3030507090-90-1010R E L A T I V E I N T E N S I T Y – %1000ANGLE80602040-70-50-3030507090-90-1010100908070605040302010R E L A T I V E I N T E N S I T Y-90-80-70-60-50-40-30-20-100102030405060708090ANGLE100908070605040302010R E L A T I V E I N T E N S I T Y-90-80-70-60-50-40-30-20-100102030405060708090ANGLEFigure 9. Relative intensity vs. angle for HSMx-C170, C190, C191, and C150.Figure 7. Relative intensity vs. angle for HSMx-C177 and C197.Figure 8. Relative intensity vs. angle for HSMx-C130.R E L A T I V E I N T E N S I T Y – %1000ANGLE806050702010304090-70-50-3002030507090-90-20-80-60-40-1010406080R E L A T I V E I N T E N S I T Y – %1000ANGLE806050702010304090-70-50-3002030507090-90-20-80-60-40-1010406080R E L A T I V E I N T E N S I T Y – %1000ANGLE806050702010304090-70-50-3002030507090-90-20-80-60-40-1010406080R E L A T I V E I N T E N S I T Y – %1000ANGLE806050702010304090-70-50-3002030507090-90-20-80-60-40-1010406080Figure 12. Recommended Pb-free reflow soldering profile.Figure 13. Recommended soldering pattern for HSMx-C110.Figure 14. Recommended soldering pattern for HSMx-C170/177.(0.059)(0.059)(0.079)(0.035)Figure 16. Recommended soldering pattern for HSMx-C150.(0.059)(0.059)(0.079)Figure 15. Recommended soldering pattern for H SMx-C130/190/191/197.0.8 (0.028)Figure 17. Recommended soldering pattern for HSMx-C120.Figure 18. Recommended soldering pattern for HSMx-C265.(0.031)(0.031)(0.047)TIMET E M P E R A T U R * THE TIME FROM 25 °C TO PEAK TEMPERATURE = 6 MINUTES MAX.Figure 11. Recommended reflow soldering profile.T E M P E R A T U R EFigure 19. Reeling orientation.Figure 20. Reel dimensions.NOTE:Ø 20.20 MIN.(Ø 0.795 MIN.)Ø 13.1 ± 0.511Figure 21. Tape dimensions.NOTE:1. ALL DIMENSIONS IN MILLIMETERS (INCHES).DIMENSIONS IN MILLIMETERS (INCHES)DIM. A ± 0.10 (0.004)DIM. B ± 0.10 (0.004)PART NUMBER DIM. C ± 0.10 (0.004)FOR HSMx-C110 1.20 (0.047) 0.80 (0.031) 1.27 (0.050) 0.95 (0.037) 0.70 (0.028) 0.87 (0.034) 0.85 (0.033) 0.60 (0.024)0.23 ± 0.05 (0.009 ± 0.002) FOR HSMR-C130R 0.5 ± 0.05 (0.020 ± 0.002) FOR HSMx-C120HSMx-C110 SERIES HSMx-C120 SERIES HSMx-C150 SERIES HSMx-C170 SERIES HSMx-C177 SERIES HSMx-C190 SERIES HSMx-C191 SERIES HSMx-C197 SERIES3.40 (0.134) 1.90 (0.075) 3.50 (0.138) 2.30 (0.091) 2.25 (0.089) 1.80 (0.071) 1.85 (0.073) 1.75 (0.069)1.70 (0.067)1.15 (0.045)1.88 (0.074)1.45 (0.057)1.32 (0.052)0.95 (0.037)0.88 (0.035)0.95 (0.037)HSMx-C265 SERIES 3.70 (0.146) 1.45 (0.057) 1.30 (0.051)TABLE 1DIMENSIONS IN MILLIMETERS (INCHES)DIM. A ± 0.10 (0.004)DIM. B ± 0.10 (0.004)PART NUMBERDIM. C ± 0.10 (0.004)Figure 22. Tape leader and trailer dimensions.Convective IR Reflow Soldering For more information on IR reflow soldering, refer to Application Note 1060, Surface Mounting SMT LED Indicator Components.NOTES:1. ALL DIMENSIONS IN MILLIMETERS (INCHES).2. TOLERANCE IS ± 0.1 mm (± 0.004 IN.) UNLESS OTHERWISE SPECIFIED.Storage Condition:5 to 30°C @ 60% RH max.Baking is required under the condition:a) the blue silica gel indicatorbecoming white/transparentcolorb) the pack has been open formore than 1 weekBaking recommended condition: 60 ± 5°C for 20 hours.END STARTSEALED WITH COVER TAPE.SEALED WITH COVERTAPE.OF CARRIERAND/ORCOVER TAPE./semiconductors For product information and a complete list of distributors, please go to our web site.For technical assistance call:Americas/Canada: +1 (800) 235-0312 or (916) 788-6763Europe: +49 (0) 6441 92460China: 10800 650 0017Hong Kong: (+65) 6756 2394India, Australia, New Zealand: (+65) 6755 1939 Japan: (+81 3) 3335-8152 (Domestic/Interna-tional), or 0120-61-1280 (Domestic Only) Korea: (+65) 6755 1989Singapore, Malaysia, Vietnam, Thailand, Philippines, Indonesia: (+65) 6755 2044 Taiwan: (+65) 6755 1843Data subject to change.Copyright © 2004 Agilent Technologies, Inc. Obsoletes 5988-4832ENApril 22, 20045989-0493EN。
BSMT-8540S-5027 SMD 磁性传感器说明书

SPECIFICATIONFOR APPROVAL444-2 Nonhyun dong, Namdong Gu,Incheon city, 405-849, Republic of Korea.Phone : +82-32-818-2125, Fax : +82-32-818-8780 email : h *******************: BSMT -8540S -5027 : SMD Magnetic transducer( RoHS compliance / non washable ): Republic of Korea: 22nd NOV 2017 : Donggyu KimPart number DescriptionCountry of origin Date Drawn byINDEXRevision Note1.Scope2.Product Photos3.Electrical acoustical characteristics4.Mechanical Characteristics1)Dimensions2)Date code recognition method5.Reliability test6.Warranty7.Operating instructions1)recommended input signal2)recommended circuit diagram8.Soldering instructions1)recommended SMT reflow temperature profile2)recommended PCB pattern3)recommended iron soldering condition4)washing conditions9.Trouble shootings10.Sound measuring instructions1)measuring conditions2)Frequency - Sound pressure level curve 11.Packing details1)reel and carrier2)carton 3 45 6 7 8 9 10 11 12REVISION NOTE#DATE CONTENT BY122 Nov 2011Initial release Donggyu Kim 222 Mar 2013Tolerance, Coil Resistance, Typsound Level, Reflow Temp ProfileDonggyu Kim327 Sep 2013Operating Temperature, StorageTemperatureJay Hwang4 5 6 7 8 9 10 11 1215 Nov 201322 Nov 2017Max Current ConsumptionPlating Material & Part no. ChangeJay HwangHong Lee1.ScopeThis document specifies a SMD magnetic transducer/buzzer, and the main application of this part is for an electronic device which requires audible feedback for human ears recognition.2.Product Photos* Above photo is an advertising purpose, so its appearance/printing may be different from an actual product 3.Electrical and acoustical characteristicsPARAMETERS SPECIFICATIONS UNIT Rated voltage 5.0Vo-pOperating voltage 4.0 ~ 6.0Vo-pCurrent consumption max 60mACoil DC resistance30 ± 5ΩOperating frequency *10 ~ 10,000HzRated frequency2,700HzSound pressure level **Min. 88 , Typ. 91dBAOperating temperature-40 ~ +90˚CStorage temperature-40 ~ +90˚C* This part is designed to make its max sound at 2,700 Hz and sound will decrease in other frequency range ** measured from 10 cm distance with input signal described in above table.4. Mechanical characteristics 1) DimensionsHousing Material : Nylon #46 Lead material : Tin plated Brass Weight : 0.45 grams general tolerance : 0.3 mm2) Date code recognition methodHour (A ~ P - 10:00 am ~ 24:00) Date (A ~ U- 10th ~ 31st ) Month (A ~ C - Oct ~ Dec) Year (1 ~ 9 - 2011 ~ 2019)X X X X5.Reliability TestNo.Item description1low storage temperature Store in -40˚C for 96 hours, then expose to roomtemperature for 4 hours2high storage temperature Store in +90˚C for 96 hours, then expose to roomtemperature for 4 hours3temperature cycle Total 50 cycles of low & high temperature. Each cycleconsists of 30 mins of -40˚C and 30 mins of +90˚C 4humidity resistance Storing 72 hours at 40˚C with 95% relative humidity,then expose to room temperature for 4 hours 5random vibration Vibrating part with 55 Hz for 10 mins and 150 Hz for10 mins, each 20 mins for X,Y,X axis(total 60 mins).random gravity range : 0.5 ~ 10.0G,6drop test Free fall onto concrete floor from 50cm height, 10times.7shear test Pulling a part mounted on PCB with strength of 1kgforce for 30 seconds.8Operating life Operating a part at its rated input signal for 1000hours at room temperature6.Warranty1)period of warranty : 6 months from ship date2)Product life : 5 years from its production date under manufacturer’s storage.3)This part is manufactured, inspected and packed in Republic of Korea4)Any failed parts worked under conditions not specified in this document are notresponsible for the manufacturer.5)Any parts measured by methods not specified in this document are not warranted.6)Unassembled or thermally damaged parts won’t be retrieved for analysis / correctiveaction report purpose. Customer is responsible for returning parts as original aspossible for any inspection / analysis purpose.7)Manufacturer’s guaranteed quality breakpoint is 300 ppm after SMT. Customers whoare experiencing failure rate that is higher than 300 ppm can ask manufacturer for refund or free replacement.8)This component complies below environmental regulations2002/95 /EC - Restriction of Hazardous Substances DirectiveEC/2037/2000 - Regulation on Ozone Depleting SubstancesSVHC under REACH regulationHalogen free under IPC regulation1) recommended input signalThis product is designed to make its max sound when AC input signal shown in above figure with its rated voltage and frequency flows.PWM is the most frequently used input signal source in general. Sine wave can also be used as an input signal.2) recommended circuit diagramTo minimize current consumption, please consider adjust its duty ratio from 50:50 to 10:90(high : low) then the consumption will decrease by about 30~40%.Basic program source which demonstrates melody and click sound is available in C or hex format. Please contact us for technical support. Reversed polarity will result in low sound.Vo -pHz1)Recommended SMT reflow temperature profileThis part is able to withstand above temperature condition by 2 passes 2)Recommended PCB pattern3)Recommended iron soldering conditionThis part is designed for SMT soldering only. Working with manual iron is notrecommended except sample test or rework.In case of iron soldering, the iron tip temperature should be lower than 240 degree celsius and soldering time should be shorter than 15 seconds.4)Washing conditionsThis part is not washable type. So soaking into solvent or water will result indecrease of sound level.9.Trouble shootingsdescription Possible reason Possible solutionNo soundInput signal is DC Please use square / sinusoidal AC signal.Wrong pin connection Please see page 5 and check the pin connectionsLow soundlevel Polarity reverse Change input signal polaritySolvent penetrated Washing should be minimized.Internal coil melt down Please use an iron tip with temperature lower than 265 ˚Cor check the input voltageDemagnetized This product has permanent magnet inside. In case ofcontact with strong magnet force it will be de-magnetizedand this possibly will decrease sound level.Voltage is too high Powerful current will make this partʼs diaphragm vibratesNoisy soundstronger than its designed allowanceFrequency is low If signalʼs frequency is at the partʼs resonant frequency, itwill result in noisy sound. Please raise frequency by about50 Hz.10.Sound measuring instructions1)Measuring conditions* Sound hole direction should be toward mic.2)Frequency - Sound pressure level(SPL) curve11.Packing details1)Reel and Carrier<< Remarks >>- . Unit : mm- . General corner unless specified : R 0.25 mm- . General tolerance : 0.1 mm- . Reel and carrier specification refers to JIS C 0806- . Quantity per a reel is 1,000 EA- . 50 pockets at both end are empty for leader purpose.2)Carton- . Unit : mm- . Reels per a carton : 5 EA- . Net weight of one carton : 2.2 kg- . Gross weight of one carton : 4.7 kg- . Water resistant packaging for vessel shipment is available.- . Labels will be attached onto each reels and cartons.-. Shipment with smaller quantity than 5,000 EA can be different from given details.。
BCM856S中文资料
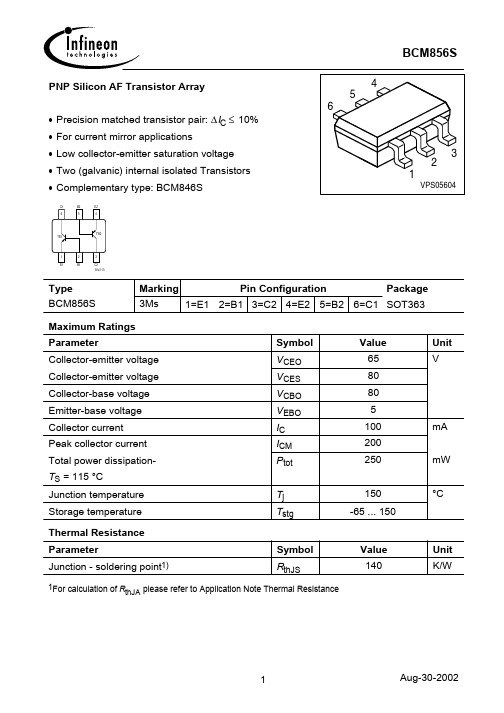
10 1
0.5
0.2
0.1
0.05
0.02
10 0
0.01
0.005
D=0
Ptotmax/PtotDC
00
20 40 60 80 100 120 °C 150
TS
Permissible Pulse Load
Ptotmax/PtotDC = (tp)
10 3 -
D=0
10 2
0.005
0.01
h12e h21e
-
2
-
-
330
-
Open-circuit output admittance IC = 2 mA, VCE = 5 V, f = 1 kHz Noise figure
h22e
-
30
-
F
-
-
10
IC = 200 µA, VCE = 5 V, f = 1 kHz,
f = 200 Hz, RS = 2 k
1
VBE
5
Aug-30-2002
元器件交易网
BCM856S
DC current gain hFE = (IC)
VCE = 5V
Output characteristics IC = (VCE),
IB = parameter
10 3 h FE 5 100 C
25 C 102 -50C
5
EHP00382
10 1 5
10 0 10 -2
5 10 -1 5 10 0
5 101 mA 10 2 ΙC
Collector cutoff current ICBO = (TA)
VCBO = 30 V
StellarNet便携式拉曼光谱仪性能介绍与参数一览

StellarNet便携式拉曼光谱仪性能介绍与参数一览型号HR-TEC-785的拉曼光谱仪是StellarNet生产制造的一款大受欢迎的拉曼光谱仪,特色在于它的参数非常广泛波长范围00-3200cm-1,同时整合整套拉曼光谱系统价格实惠,是大多数想购买拉曼光谱仪,搭建拉曼光谱系统的理想选择.StellarNet提供了应用于200-3200cm-1的各种便携式拉曼光谱仪,可以快速识别各种液体,固体或粉末样品。
其中785nm 激光是拉曼光谱选择的最常见波长。
因为这段波长是红外激光在拉曼效率,荧光效应和吸热这3种反应中,依旧能保持平衡的波长。
同样,785nm激光器通常比其他频率便宜,从而使整个光谱系统的价格变得较为经济实惠。
Raman-HR-TEC-785拉曼光谱仪是stellarNet大受欢迎的拉曼光谱仪,包括针对785nm拉曼调谐的增强型CCD阵列检测器和先进的检测器透镜组件,可在长时间曝光时实现超高灵敏度。
StellarNet拉曼光谱仪Raman-HR-TEC-X2-785提供2级检测器冷却功能,以实现最高的灵敏度和性能!非常适合长时间曝光,曝光最多可达8分钟。
可互换的狭缝(Interchangeable Slits Upgrades),可用于高分辨率HR光学平台,以提供更多的应用灵活性。
可以使用最小的狭缝来测量高散射样品,以获得极高的分辨率,也可以通过较大的狭缝来测量弱拉曼,以增加光通量。
Stellar CASE-Raman-785是一款便携式,坚固耐用的拉曼光谱系统,适用于“开放与测量”应用。
这个完整的系统包括高性能拉曼光谱仪(Raman-HR-TEC-785),大功率激光器和样品瓶架。
通常建议将Raman-SR-785系列光谱仪用于OEM和便携式应用,在这些应用中已知特定样品组并且在不使用检测器冷却的情况下也能很好地工作。
便携式拉曼光谱仪HR-TEC型号:SR =标准分辨率HR =高分辨率便携式拉曼光谱仪HR-TEC技术指标:光学参数:便携式拉曼光谱仪探测器与电子元件:便携式拉曼光谱仪的尺寸:便携式拉曼光谱仪的尺寸:StellarNet便携式拉曼光谱仪的软件与界面:拉曼光谱系统可添加的配件:拉曼光谱仪配套激光器:-Ramulaser™785纳米-785拉曼激光通过标准的FC / APC连接器连接到拉曼探针-拉曼激光线 0.2nm FWHM-499mWatt可调功率-由坚固的金属外壳保护电池供电-尺寸仅为2x4x6英寸-锂离子电池全天供电-添加拉曼探针785和光谱仪-Ramulaser-Vial785nm拉曼激光器,带直接连接的1/2“样品瓶架-拉曼激光线0.2nm FWHM-499mWatt可调功率-可直接连接到光谱仪,降低探头成本-可容纳1/2英寸的圆形样品瓶-液体,粉末和固体-尺寸仅为2x4x6英寸-坚固金属外壳保护锂离子电池供电。
Cessna产品型号说明书
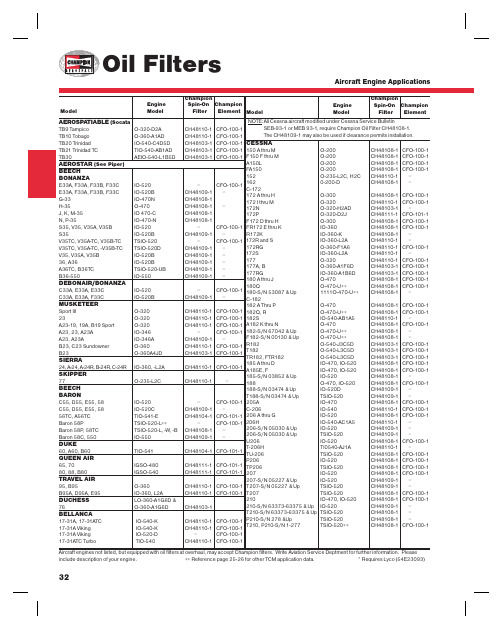
CESSNA150 A thru M O-200 CH48108-1 CFO-100-1F150 F thru M O-200 CH48108-1 CFO-100-1A150L O-200 CH48108-1 CFO-100-1FA150 O-200 CH48108-1 CFO-100-1152 O-235-L2C, H2C CH48110-1 –162 0-200-D CH48108-1 –C-172172 A thru H O-300 CH48108-1 CFO-100-1172 I thru M O-320 CH48110-1 CFO-100-1172N O-320-H2AD CH48103-1 –172P O-320-D2J CH48111-1 CFO-101-1F172 D thru H O-300 CH48108-1 CFO-100-1FR172 E thru K IO-360 CH48108-1 CFO-100-1R172K IO-360-K CH48108-1 –172R and S IO-360-L2A CH48110-1 –172RG O-360-F1A6 CH48110-1 CFO-100-1172S IO-360-L2A CH48110-1 –177 O-320 CH48110-1 CFO-100-1177A, B O-360-A1F6D CH48103-1 CFO-100-1177RG IO-360-A1B6D CH48103-1 CFO-100-1180 A thru J O-470 CH48108-1 CFO-100-1180Q O-470-U++ CH48108-1 CFO-100-1180-S/N 53087 & Up 1111O-470-U++ CH48108-1 –C-182182 A Thru P O-470 CH48108-1 CFO-100-1182Q, R O-470-U++ CH48108-1 CFO-100-1182S IO-540-AB1A5 CH48110-1 –A182 K thru N O-470 CH48108-1 CFO-100-1182-S/N 67042 & Up O-470-U++ CH48108-1 –F182-S/N 00130 & Up O-470-U++ CH48108-1 –R182 O-540-J3C5D CH48103-1 CFO-100-1T182 O-540-L3C5D CH48103-1 CFO-100-1TR182, FTR182 O-540-L3C5D CH48103-1 CFO-100-1185 A thru D IO-470, IO-520 CH48108-1 CFO-100-1A185E, F IO-470, IO-520 CH48108-1 CFO-100-1185-S/N 03852 & Up IO-520 CH48108-1 –188 O-470, IO-520 CH48108-1 CFO-100-1188-S/N 03474 & Up IO-520D CH48109-1 –T188-S/N 03474 & Up TSIO-520 CH48109-1 –205A IO-470 CH48108-1 CFO-100-1C-206 IO-540 CH48110-1 CFO-100-1206 A thru G IO-520 CH48108-1 CFO-100-1206H IO-540-AC1A5 CH48110-1 –206-S/N 05030 & Up IO-520 CH48109-1 –206-S/N 05030 & Up TSIO-520 CH48109-1 –U206 IO-520 CH48108-1 CFO-100-1T-206H TI0540-AJ1A CH48110-1 –TU-206 TSIO-520 CH48108-1 CFO-100-1P206 IO-520 CH48108-1 CFO-100-1TP206 TSIO-520 CH48108-1 CFO-100-1207 IO-520 CH48108-1 CFO-100-1207-S/N 05227 & Up IO-520 CH48109-1 –T207-S/N 05227 & Up TSIO-520 CH48109-1 –T207 TSIO-520 CH48108-1 CFO-100-1210 IO-470, IO-520 CH48108-1 CFO-100-1210-S/N 63373-63375 & Up IO-520 CH48109-1 –T210-S/N 63373-63375 & Up TSIO-520 CH48108-1 –P210-S/N 278 &Up TSIO-520 CH48108-1 –T210, P210-S/N 1-277 TSIO-520++ CH48108-1 CFO-100-1 32Aircraft engines not listed, but equipped with oil fi lters at overhaul, may accept Champion fi lters. Write Aviation Service Deptment for further information. Please include description of your engine. ++ Reference page 25-26 for other TCM application data. * Requires Lyco (54E23093) AEROSPATIABLE (SocataTB9 Tampico O-320-D2A CH48110-1 CFO-100-1TB10 Tobago O-360-A1AD CH48110-1 CFO-100-1TB20 Trinidad IO-540-C4D5D CH48103-1 CFO-100-1TB21 Trinidad TC TIO-540-AB1AD CH48103-1 CFO-100-1TB30 AEIO-540-L1B5D CH48103-1 CFO-100-1AEROSTAR (See Piper)BEECHBONANZAE33A, F33A, F33B, F33C IO-520 – CFO-100-1E33A, F33A, F33B, F33C IO-520B CH48109-1 –G-33 IO-470N CH48108-1H-35 O-470 CH48108-1 –J, K, M-35 IO 470-C CH48108-1N, P-35 IO-470-N CH48108-1S35, V35, V35A, V35B IO-520 – CFO-100-1S35 IO-520B CH48109-1 –V35TC, V35A-TC, V35B-TC TSIO-520 – CFO-100-1V35TC, V35A-TC, -V35B-TC TSIO-520D CH48109-1 –V35, V35A, V35B IO-520B CH48109-1 –36, A36 IO-520B CH48109-1 –A36TC, B36TC TSIO-520-UB CH48109-1 –B36-550 IO-550 CH48109-1 –DEBONAIR/BONANZAC33A, E33A, E33C IO-520 – CFO-100-1C33A, E33A, F33C IO-520B CH48109-1 –MUSKETEERSport III O-320 CH48110-1 CFO-100-123 O-320 CH48110-1 CFO-100-1A23-19, 19A, B19 Sport O-320 CH48110-1 CFO-100-1A23, 23, A23A IO-346 – CFO-100-1A23, A23A IO-346A CH48109-1 –B23, C23 Sundowner O-360 CH48110-1 CFO-100-1B23 O-360A4JD CH48103-1 CFO-100-1SIERRA24, A-24, A-24R, B-24R, C-24R IO-360, -L2A CH48110-1 CFO-100-1SKIPPER77 O-235-L2C CH48110-1 –BEECHBARONC55, D55, E55, 58 IO-520 – CFO-100-1C55, D55, E55, 58 IO-520C CH48109-1 –56TC, A56TC TIO-541-E CH48104-1 CFO-101-1Baron 58P TSIO-520-L++ – CFO-100-1Baron 58P, 58TC TSIO-520-L, -W, -B CH48108-1 –Baron 58C, 550 IO-550 CH48109-1 –DUKE60, A60, B60 TIO-541 CH48104-1 CFO-101-1QUEEN AIR65, 70 IGSO-480 CH48111-1 CFO-101-180, 88, B80 IGSO-540 CH48111-1 CFO-101-1TRAVEL AIR95, B95 O-360 CH48110-1 CFO-100-1B95A, D95A, E95 IO-360, L2A CH48110-1 CFO-100-1DUCHESS LO-360-A1G6D &76 O-360-A1G6D CH48103-1BELLANCA17-31A, 17-31ATC IO-540-K CH48110-1 CFO-100-117-31A Viking IO-540-K CH48110-1 CFO-100-117-31A Viking IO-520-D – CFO-100-117-31ATC Turbo TIO-540 CH48110-1 CFO-100-1ChampionEngine Spin-On ChampionModel Model Filter ElementChampionEngine Spin-On ChampionModel Model Filter ElementNOTE: A ll Cessna aircraft modifi ed under Cessna Service BulletinSEB-93-1 or MEB 93-1, require Champion Oil Filter CH48108-1.The CH48109-1 may also be used if clearance permits installation.Aircraft Engine ApplicationsCESSNA T303 LTSIO-520-AE &TSIO-520-AE CH48109-1 –310 C thru Q IO-470 CH48108-1 CFO-100-1310 RIO-520-M CH48108-1 –T310P, Q, R TSIO-520-B CH48108-1 CFO-100-1320-A TSIO-470 CH48104-1 –320-B, C TSIO-470 CH48109-1 CFO-101-1320-D TSIO-520 – CFO-100-1320-D, E, F TSIO-520-B CH48108-1 –335 TSIO-520-EB CH48109-1 –336 IO-360 CH48108-1 CFO-100-1337 IO-360 CH48108-1 CFO-100-1P337, P337H TSIO-360 CH48108-1 CFO-100-1T337H TSIO-360-H CH48108-1 CFO-100-1340 TSIO-520-K CH48108-1 –340A TSIO-520-N, -NB CH48109-1 CFO-100-1401/402TSIO-520-E CH48108-1 CFO-100-1402C TSIO-520-VB CH48109-1 CFO-100-1404GTSIO-520-M CH48111-1 CFO-101-1411-S/N 000 thru 0126 GTSIO-520-C CH48104-1 –411-S/N 0127 and up GTSIO-520-C CH48111-1 CFO-101-1414, 414A TSIO-520-J, -N CH48108-1 –421A, BGTSIO-520-D, -H, CH48111-1 CFO-101-1421C-S/N 1017 thru 1404 -L, -N, ++ CH48111-1 CFO-101-1CIRRUS AIRCRAFT SRV, SR20I0-360ES CH48108-1SR22I0-550N CH48109-1COLUMBIA/LANCAIR COLUMBIA 300, 350 I0-550N CH48109-1 CFO-100-1COLUMBIA 400 TS10-550 CH48109-1 CFO-100-1DIAMOND AIRCRAFT DA20-1C I0-240 CH48108-1 CFO-100-1DA40-180I0-360 CH48110-1 CFO-100-1GULFSTREAM AMERICAN (Single Engine Models)AA-1, 1A, 1B, 1B Trainer, TR 2/Lyco O-235 CH48110-1 CFO-100-1A1C Lynx, T-Cat Lyco O-235-L CH48110-1 CFO-100-1AA-5 Traveler Lyco O-320-E CH48110-1 CFO-100-1AA-5A Cheetah Lyco O-320-E CH48110-1 CFO-100-1AA-5B Tiger Lyco O-360-A4K CH48110-1 CFO-100-1Cougar 2/Lyco O-320-D CH48110-1 CFO-100-1COMMANDER 112, 112A IO-360-C, -L2A CH48110-1 CFO-100-1112TC TO-360-C1A6D CH48103-1 CFO-100-1114IO-540-T4A5D CH48103-1 CFO-100-1500B, 500U IO-540 CH48110-1 CFO-100-1700TIO-540-R2AD CH48103-1 CFO-100-1 33Aircraft engines not listed, but equipped with oil fi lters at overhaul, may accept Champion fi lters. Write Aviation Service Deptment for further information. Please include description of your engine. ++ Reference page 25-26 for other TCM application data. * Requires Lyco (54E23093)MAULEM5-180C, MX7-180 O-360-C, -C1F CH48110-1 M5-210C IO-360D, -L2A M5-210TCTO-360-C1A6D CH48103-1 M5-235C, M6-235, M7-235 O-540-J1A5D CH48103-1 MX-7-235O-540-W1A5D CH48103-1MOONEY AIRCRAFTM20A, B, Mark21O-360 CH48110-1M20D MasterO-360 CH48110-1 CFO-100-1 M20C RangerO-360 CH48110-1M20G StatesmanO-360CH48110-1 CFO-100-1 M20E ChaparralIO-360, -L2A CH48110-1 CFO-100-1 M20F Executive IO-360, -L2ACH48110-1 CFO-100-1 M20J-201 IO-360-A3B6D, -L2A CH48103-1 – M20K-231 TSIO-360-G, LB CH48108-1 M20M-TLS TIO-540-AFIA, B CH48110-1M20RIO-550 CH48108-1 –M22 Mustang TIO-541CH48110-1 CFO-100-1 M20K-252 TSE TSIO-360-MB1CH48108-1 –PIPER CUBPA-18 “150” O-320 CH48110-1 CFO-100-1 TRI-PACERPA-22 “150”O-320 CH48110-1 CFO-100-1 PA-22 “160”O-320CH48110-1 CFO-100-1 COMANCHEPA-24 “180” O-360CH48110-1 CFO-100-1 PA-24 “250”O-540 or IO-540 CH48110-1 CFO-100-1 PA-24B, PA-24C “260”O-540 or IO-540 CH48110-1 CFO-100-1 PA-24 Turbo “260”IO-540 CH48110-1 CFO-100-1 PAWNEEPA-25 “150” O-320 CH48110-1 CFO-100-1 A25 “260”O-540 CH48110-1 CFO-100-1 PA-36 Brave6-285B CH48109-1 –PA-36-375 Brave IO-720-D1C CH48110-1 CFO-100-1 PA-36-400 BraveIO-720D1CD CH48104-1 CFO-101-1 CHEROKEE, CADET PA-28 “140”O-320 CH48110-1 CFO-100-1 PA-28 “150”O-320 CH48110-1 CFO-100-1 PA-28 “160”, “161” O-320 CH48110-1 CFO-100-1 PA-28 “180”O-360CH48110-1 CFO-100-1 PA-28 “180”, “181”O-360-A4M CH48110-1 CFO-100-1 PA-28 “235”O-540 CH48110-1 CFO-100-1 PA-28 “151”O-320CH48110-1 CFO-100-1 ARROWPA-28R “180”IO-360, L2ACH48110-1 CFO-100-1 PA-28R “180 IO-360-C1CD, L2A CH48103-1 CFO-100-1 PA-28R “200” Arrow II IO-360, L2A CH48110-1 CFO-100-1 PA-284 “200” Turbo Arrow IIITSIO-360 CH48108-1 – PA-28-R-201TTSIO-360-F1CH48108-1Champion Engine Spin-On Champion Model ModelFilter ElementChampionEngine Spin-On Champion Model ModelFilter Element Aircraft Engine Applications34TWIN COMMANCHEPA-30 “160” Turbo IO-320 CH48110-1 CFO-100-1PA-39 “160” IO-320 CH48110-1CFO-100-1LIO-320 CH48110-1 CFO-100-1PA-39 “160” Turbo IO-320 CH48110-1 CFO-100-1LIO-320 CH48110-1 CFO-100-1NAVAJOPA-31 “300” IO-540 CH48110-1 CFO-100-1PA-31 “310” Turbo TIO-540 CH48110-1 CFO-100-1PA-31 “325” IO-540-F2BD CH48103-1 CFO-100-1LTIO-540-F2BD CH48103-1 CFO-100-1PA-31 “350” Chieftain TIO-540-J2BD CH48103-1 CFO-100-1LTIO-540-J2BD CH48103-1 CFO-100-1PA-31P “425” TIGO-541 CH48104-1 CFO-101-1PA-31P “350” Mojave TIO/LIO-540-V2AD CH48104-1SENECAPA-34 IO-360C CH48110-1 CFO-100-1LIO-360C CH48110-1 CFO-100-1PA-34 IO-360-C1E6D CH48103-1 CFO-100-1LIO-360-C1E6D CH48103-1 CFO-100-1Seneca II LTSIO-360-E CH48108-1 –TSIO-360-E CH48108-1 –Seneca III TSIO-360-KB CH48108-1PA-34-220T LTSIO-360-KB CH48108-1PIPER AEROSTARPA-60-600, -600A IO-540-G, -K CH48110-1 CFO-100-1PA-60-604, -601B IO-540-P, -S CH48110-1 CFO-100-1PA-60-601P IO-540-S CH48110-1 CFO-100-1PA-60-602P IO-540-AA1A5 CH48110-1 CFO-100-1SEMINOLEPA-44-180 O-360-E1AD CH48103-1* CFO-100-1PA-44-180T TO-360-E1A6DLTO-360-E1A6D CH48103-1* CFO-100-1 ChampionEngine Spin-On ChampionModel Model Filter ElementChampionEngine Spin-On Champion Model Model Filter ElementDAKOTAPA-28-235 O-540-J3A5D CH48103-1* CFO-100-1PA-28-201T TSIO-360-FB CH48108-1 –CHEROKEE SIXPA-32 “260” O-540 CH48110-1 CFO-100-1PA-32 “300” IO-540 CH48110-1 CFO-100-1PA-32R “300” IO-540-K1AD CH48103-1* CFO-100-1PA-32R “300” TIO-540-S1AD CH48103-1* CFO-100-1PA-32RT-300T TIO-540-S1AD CH48103-1* CFO-100-1PA-32-301 IO-540-K1G5D CH48103-1* CFO-100-1PA-32-301 TIO-540-S1AD CH48103-1* CFO-100-1PA-32R-301 IO-540-K1G5D CH48103-1* CFO-100-1PA-32R-301 TIO-540-S1AD CH48103-1* CFO-100-1TOMAHAWKTrainer PA-38-112 O-235-L2C CH48103-1* CFO-100-1MALIBUPA-46-301P Cont TSIO-520-BE CH48109-1MALIBU MIRAGEPA-46-350-P Lyco TIO-540-AE2A CH48103-1APACHEPA-23 “150” O-320 CH48110-1 CFO-100-1PA-23 “160” O-320 CH48110-1 CFO-100-1PA-23 “235” O-540 CH48110-1 CFO-100-1AZTECPA-23 “250” O-540 CH48110-1 CFO-100-1“C” PA-23 IO-540 CH48110-1 CFO-100-1PA-23 Turbo “250” IO-540 CH48110-1 CFO-100-1“C”, “D”, “E”, “F”PA-23 Turbo “250” TIO-540 CH48110-1 CFO-100-1Dimensional DataChampion Thread Dry WeightPart No. A B C D (SAE) Lbs./Kg.CH48103-1 4.48” (11.4 cm) 0.43” (1.09 cm) 1.00” Hex (2.54 cm) 3.71” (9.4 cm) 13/16-16-UNS-2B 1.32lbs. (0.59kg) CH48104-1 5.73” (14.6 cm) 0.43” (1.09 cm) 1.00” Hex (2.54 cm) 3.71” (9.4 cm) 13/16-16-UNS-2B 1.41lbs. (0.64kg) CH48108-1 4.48” (11.4 cm) 0.43” (1.09 cm) 1.00” Hex (2.54 cm) 3.71” (9.4 cm) 3/4-16-UNF-2B 1.40lbs. (0.64kg) CH48109-1 5.73” (14.6 cm) 0.43” (1.09 cm) 1.00” Hex (2.54 cm) 3.71” (9.4 cm) 3/4-16-UNF-2B 1.51lbs. (0.68kg) CH48110-1 4.48” (11.4 cm) 0.43” (1.09 cm) 1.00” Hex (2.54 cm) 3.71” (9.4 cm) 3/4-16-UNF-2A 1.38lbs. (0.63kg) CH48111-1 5.73” (14.6 cm) 0.43” (1.09 cm) 1.00” Hex (2.54 cm) 3.71” (9.4 cm) 3/4-16-UNF-2A 1.47lbs. (0.67kg)Popular spin-on oil fi ltersAircraft engines not listed, but equipped with oil fi lters at overhaul, may accept Champion fi lters. Write Aviation Service Department for furtherinformation. Please include description of your engine. * Requires Lyco (54E23093)Aircraft Engine Applications。
SAE AS85485A-2011

__________________________________________________________________________________________________________________________________________ SAE Technical Standards Board Rules provide that: “This report is published by SAE to advance the state of technical and engineering sciences. The use of this report is entirely voluntary, and its applicability and suitability for any particular use, including any patent infringement arising therefrom, is the sole responsibility of the user.”SAE reviews each technical report at least every five years at which time it may be reaffirmed, revised, or cancelled. SAE invites your written comments and suggestions. Copyright © 2011 SAE InternationalAll rights reserved. No part of this publication may be reproduced, stored in a retrieval system or transmitted, in any form or by any means, electronic, mechanical,photocopying, recording, or otherwise, without the prior written permission of SAE.TO PLACE A DOCUMENT ORDER: Tel: 877-606-7323 (inside USA and Canada)Tel: +1 724-776-4970 (outside USA)Fax: 724-776-0790Email: CustomerService@SAE WEB ADDRESS: h ttp://AS85485Issued 2004-06 RevisedRATIONALERevision required to incorporate AS85485-A2, update references, update government related terminology, and address technical requirements.1. SCOPE1.1 ScopeThis specification covers the requirements for radio frequency absorptive component wires and finished cables which function electrically as distributed low-pass filters. Materials and construction details are specified in the detail specification.1.2 ClassificationProducts in accordance with this specification shall be of the following types, as specified in the detail specification.Component Wire - A single conductor, insulated as specified in the detail specification.Finished Cable - Any construction other than component wire, utilizing a wire or wires with or without shielding, or with or without an outer jacket.1.2.1 CurrentRatingThe current rating shall be determined in accordance with AS50881.1.2.2 TemperatureRatingThe maximum conductor temperature of the component wire or finished cable for continuous use shall be as specified in the detail specification.1.2.3 VoltageRatingThe maximum voltage rating of the component wire or finished cable for continuous use shall be as specified in the detail specification.1.2.4 Component Wire and Finished Cable DesignationComponent wire and finished cable shall be identified by a combination of digits and letters (not to exceed 15).1.2.4.1Component wire: Component wire designation shall be as shown in the following example:1.2.4.1.1 Basic specification: The basic specification shall describe the performance requirements of components and finished cable.1.2.4.1.2 Detail specification: The detail specification shall describe the material and construction details of finished cable and components.1.2.4.1.3 Wire size: The component wire size shall be identified. All component wire used in a cable shall be of the same size.1.2.4.1.4 Color: The component wire color shall be designated in accordance with MIL-STD-681. The preferred color of component wire is light violet, designated 7L.1.2.4.2Finished cable: Finished cable designation shall be as shown in the following example:1.2.4.2.1 Construction: A letter symbol shall be used to designate the construction in accordance with the following: (a) Shielded, jacketed cable constructionLetter CodeConductor Type Shield Type T Tin-coated copper Tin-coated copper S Silver-coated copper Silver-coated copper NNickel-coated copperNickel-coated copperM Silver-coated high-strength copper alloy Silver-coated high-strengthcopper alloy P Nickel-coated high-strength copper alloy Nickel-coated high-strength copper alloy U Silver-coated-high-strength copper alloy Tin-coated copper V Silver-coated-high-strength copper alloy Silver-coated copperW Nickel-coated high-strength copper alloyNickel-coated copper(b) Unshielded, unjacketed cable constructionLetter Code Conductor TypecopperT Tin-coatedcopperS Silver-coatedN Nickel-coatedcopperM Silver-coated high-strength copper alloyP Nickel-coated high-strength copper alloy1.2.4.2.2 Number of components: A single digit shall be used to designate the number of component wires in thefinished cable.1.2.4.2.3 Color code designator: The letter symbol A shall be used to designate the component color code described in3.6.3.2. APPLICABLE DOCUMENTSThe following publications form a part of this document to the extent specified herein. The latest issue of SAE publications shall apply. The applicable issue of the other publications shall be the issue in effect on the date of the purchase order. In the event of conflict between the text of this document and references cited herein, the text of this document takes precedence. Nothing in this document, however, supersedes applicable laws and regulations unless a specific exemption has been obtained.2.1 SAE PublicationsAvailable from SAE International, 400 Commonwealth Drive, Warrendale, PA 15096-0001, Tel: 877-606-7323 (inside USA and Canada) or 724-776-4970 (outside USA), .AS1241 Fire Resistant Phosphate Ester Hydraulic Fluid for AircraftAMS1424 Fluid, Deicing/Anti-Icing, Aircraft, SAE Type IAS50881 Wiring, Aerospace VehicleAS85485/5* Cable, Electric, Filter Line, Component Wire, Tin-Coated Copper Conductor, Radio Frequency Absorptive, 150 °C, 600-VoltAS85485/6* Cable, Electric, Filter Line, Component Wire, Silver-Coated High Strength Copper Alloy Conductor, Radio Frequency Absorptive, 150 °C, 600-VoltAS85485/7* Cable, Electric, Filter Line, Unshielded, Unjacketed, Multiple-Component, Radio Frequency Absorptive, 150 °C, 600-VoltAS85485/8* Cable, Electric, Filter Line, Shielded, Jacketed, Radio Frequency Absorptive, 150 °C, 600-VoltAS95485/9* Cable, Electric, Filter Line, Component Wire, Tin-Coated Copper Conductor, Radio Frequency, Absorptive, 150ºC, 600-VoltAS85485/10* Cable, Electric, Filter Line, Component Wire, Silver-Coated High-Strength Copper Alloy Conductor, Radio Frequency Absorptive, 150ºC, 600-VoltAS85485/11* Cable, Electric, Filter Line, Unshielded, Unjacketed, Multiple-Component, Radio Frequency Absorptive, 150ºC, 600-VoltAS85485/12* Cable, Electric, Filter Line, Shielded, Jacketed, Radio Frequency Absorptive, 150ºC, 600-Volt*AS85485 detail specification2.3 ASQ PublicationsAvailable from American Society for Quality, 600 North Plankinton Avenue, Milwaukee, WI 53203, Tel: 800-248-1946 (United States or Canada)) or +1-414-272-8575 (International), ..ASQC Z1.4 Sampling Procedures and Tables for Inspection by Attributes2.4 ASTM PublicationsAvailable from ASTM International, 100 Barr Harbor Drive, P.O. Box C700, West Conshohocken, PA 19428-2959, Tel: 610-832-9585,.B33-78 Standard Specification for Tinned Soft or Annealed Copper Wire for Electrical PurposesB63-49 (1975) Standard Test Method for Resistivity of Metallically Conducting Resistance and Contact MaterialsE104-51 Standard Recommended Practice for Maintaining Constant Relative Humidity by Means of Aqueous SolutionsB298-74a Standard Specification for Silver-Coated Soft or Annealed Copper WireB355-74 Standard Specification for Nickel-Coated Soft or Annealed Copper WireD471 Standard Test Method for Rubber Property-Effect of LiquidsE595-77 Standard Test Method for Total Mass Loss and Collected Volatile Condensable Materials From Outgassing in a Vacuum EnvironmentB624-77 Standard Specification for High-Strength, High-Conductivity Copper-Alloy Wire for Electronic ApplicationD1153-77 Standard Specification for Methyl Isobutyl KetoneD3032 Standard Test Methods for Hookup Wire InsulationD4814 Standard Specification for Automotive Spark-Ignition Engine Fuel2.5NEMA PublicationsAvailable from National Electrical Manufacturers Association, 1300 North 17th Street, Suite 1752, Roslyn, VA 22209, Tel: 703-841-3200,.NEMA HP1-1979 High-Temperature Insulated Wire – Impulse Dielectric Testing2.5 U.S. Government PublicationsAvailable from the Document Automation and Production Service (DAPS), Building 4/D, 700 Robbins Avenue, Philadelphia, PA 19111-5094, Tel: 215-697-6257, /quicksearch/.H4/H8 Catalog of Commercial and Government Entities (CAGE)(Battle Creek Customer Contact Center, Defense Logistics Information Service, 74 Washington AvenueN., Battle Creek, MI 49017-3084) https:///ccr/default.aspxSD-6 Provisions Governing QualificationMIL-STD-104 Limits for Electrical Insulation ColorMIL-STD-129 Military Marking for Shipment and StorageFED-STD-228 Cable and Wire, Insulated; Methods of TestingMIL-STD-681 Identification Coding and Application of Hook Up and Lead WireTT-I-735 IsopropylAlcoholMIL-DTL-915 Cable and Cord Electrical, for Shipboard Use, General Specification forMIL-PRF-5606 Hydraulic Fluid, Petroleum Base; Aircraft, Missile, and OrdnanceMIL-DTL-5624 Turbine Fuel, Aviation, Grades JP-4 and JP-5MIL-PRF-7808 Lubricating Oil, Aircraft Turbine Engine, Synthetic BaseMIL-DTL-12000 Cable, Cord, and Wire, Electric, Packaging ofMIL-PRF-23699 Lubricating Oil, Aircraft Turbine Engine, Synthetic BaseMIL-DTL-29606 Wire, Electrical, Stranded, Uninsulated Copper, Copper Alloy, or Aluminum, or Thermocouple Extension, General Specification ForMIL-C-43616 Cleaning Compound, Aircraft SurfaceMIL-DTL-83133 Turbine Fuel, Aviation, Kerosene Types, NATO F-34 (JP-8) and NATO F-35MIL-PRF-87937 Cleaning Compound, Aerospace Equipment3. REQUIREMENTS3.1 Detail SpecificationsThe requirements for the component wire and finished cable furnished under this specification shall be as specified herein and in accordance with the detail specification. In the event of discrepancy between this specification and the requirements of the detail specification, the requirements of the detail specification shall govern.3.2 Classification of RequirementsThe applicable requirements are classified herein as follows:Requirement ParagraphQualification 3.3Materials 3.4 Construction 3.5 Component Wire and Finished Cable 3.63.3 Qualification:The component wire or finished cable furnished under this specification shall be a product which is qualified for listing on the applicable qualified products (see 4.3 and 6.3). The provisions of 4.6 for retention of qualification are included in this requirement.3.4 MaterialsMaterial3.4.1 ConductorAll strands used in the manufacture of the conductors shall be soft annealed copper conforming to ASTM B33, B298, or B355, as applicable, or shall be high-strength copper alloy conforming to ASTM B624. Strands shall be free from lumps, kinks, splits, scraped or corroded surfaces and skin impurities. In addition, the strands shall conform to the following requirements as applicable.3.4.1.1 Tin-coated copper strands: No additional requirements. The tin coating shall be as specified in ASTM B33.3.4.1.2 Silver-coated copper strands: The strands shall have a coating thickness of not less than 40 micro-inches ofsilver when tested in accordance with ASTM B298.3.4.1.3 Nickel-coated copper strands: The strands shall have a coating thickness of not less than 50 micro-inches ofnickel when tested in accordance with ASTM B355. Adhesion of the nickel coating shall be such that, after subjection to the procedures of 4.7.7.1, the strands shall still pass the continuity of coating test in ASTM B355.3.4.1.4 High-strength copper alloy: The strands shall be of the applicable AWG gage specified in Table 1 and of suchtensile properties that the conductor from the finished wire conforms to the requirements of 3.5.1.3.2 for elongation and breaking strength. The strands shall be silver-coated or nickel-coated in accordance with 3.4.1.2 or 3.4.1.3 as applicable.Material3.4.2 Shield3.4.2.1 Braided round wire strands: Braided round wire strands shall meet all the applicable conductor materialrequirements of 3.4.1 prior to braiding.3.4.2.2 Braided flattened wire strands: Braided flattened wire strands shall meet all the applicable conductor materialrequirements of 3.4.1 prior to flattening and braiding.Material3.4.3 InsulationAll insulating and filter layer materials shall be in accordance with the detail specification and shall meet all applicable requirements of Table 3 and the detail specification.3.5 ConstructionConstruction of the component wire and finished cable shall be as specified herein and in the detail specification.3.5.1 Conductor3.5.1.1 Stranding3.5.1.1.1 Concentric-lay stranding: The conductors of wire sizes 30 through 10 shall be concentric-lay conductorsconstructed as specified in Table 1. Concentric-lay shall be interpreted to be a central strand surrounded byone or more layers of helically wound strands. It is optional for the direction of lay of the successive layers tobe alternately reversed (true concentric lay) or to be in the same direction (unidirectional lay). The strandsshall be assembled in a geometric arrangement of concentric layers, so as to produce a smooth and uniformconductor, circular in cross-section and free of any crossovers, high strands, or other irregularities. Thedirection of lay of the individual strands in the outer layer of the concentrically stranded conductors shall beleft hand. The length of lay of the outer layer shall not be less than 8 nor more than 16 times the maximumconductor diameter as specified in the detail specification.3.5.1.2 Splices: Splices in individual strands or members shall be butt brazed. There shall not be more than one strand-splice in any two lay lengths of a stranded concentric-lay conductor. In no case shall the whole conductor be spliced at one point.3.5.1.3 Conductor elongation and breaking strength:3.5.1.3.1 Soft or annealed copper: The individual strands removed from component wires with soft or annealed copperconductors, wire sizes 20 and larger, or the whole soft or annealed copper conductor removed from component wire, sizes 22 and smaller, shall have the following minimum elongation when tested in accordance with 4.7.6.1:Sizes 24 and smaller – 6 percent (minimum)Sizes 22 and larger – 10 percent (minimum)There shall be no breaking strength requirements for soft or annealed copper conductors.3.5.1.3.2 High-strength copper alloy: The whole conductor removed from component wires with high-strength copperalloy conductors shall exhibit elongation of 6 percent, minimum, and a breaking strength conforming withTable 1, when tested in accordance with 4.7.6.2.TABLE 1 - DETAILS OF CONDUCTORS3.5.1.4 Conductor diameter: The diameter of the conductor shall be as specified in Table 1. Applicability of the “generalpurpose” or of the “small diameter” Table 1 requirements for maximum conductor diameter shall be as indicated in the detail specification .3.5.2 ShieldThe shield shall be constructed as specified in the detail specification.3.5.3 InsulationThe insulating and filter layers shall be constructed as specified in the detail specification. All component insulation shall be readily removable by conventional wire stripping devices without damage to the conductor.3.6 Component Wire and Finished CableThe component wire and finished cable shall conform to the requirements of Table 3 and those of the detail specification. The requirements of 3.6.1 through 3.6.10 also apply. Unless otherwise specified, component wire shall conform to all applicable requirements prior to assembly into the finished cable.3.6.1 BlockingAdjacent turns or layers of the component wire or cable jacket shall not stick to one another when tested as specified in 4.7.4 at the temperature specified in the detail specification. 3.6.2 CablingThe required number of component wires as specified in the detail specification shall be cabled together with a left hand lay. For cables having multiple layers, the outer layer shall be left hand and the inner layer or layers may be either right hand or left hand lay. The lay length of the individual component wires shall be not less than 8 times nor more than 16 times the diameter of the applicable layer. Fillers and binders shall be used only as specified in the detail specification. 3.6.3 ColorUnless otherwise specified in the contract or purchase order, the color of component wire shall be light violet, designated by 7L. The preferred colors for components in a finished cable shall be light violet for component number 1 and light violetwith stripe designators for remaining component wires as follows:All solid colors and the colors of all striping shall be in accordance with MIL-STD-104, Class 1, unless otherwise specified. Color striping, if applicable, shall conform to MIL-STD-681 and shall be capable of withstanding the striping durability test of 4.7.11 for the number of strokes and with the weight specified in the detail specification. 3.6.4Crosslinking Proof Test and Life CycleWhen samples are tested in accordance with 4.7.10, there shall be no cracking of the insulation or jacket and no dielectric breakdown, as applicable. 3.6.5Conductor and Shield ContinuityOne hundred percent of all finished cable shall be tested for continuity prior to shipment. There shall be no indication of discontinuity in any of the component wires or shields. 3.6.6 Continuous LengthsThe individual continuous lengths of component wire or finished cable in each inspection lot shall be of such footage that, when inspected in accordance with 4.7.9, the inspection lot shall conform to the continuous length requirements of Table 2. Unless otherwise specified in the contract or order, the footage of the individual continuous lengths in each spool or reel shall be marked on the spool or reel in the sequence in which the lengths will be unwound by the user.TABLE 2 - MINIMUM CONTINUOUS LENGTHSPRODUCT DESCRIPTION REQUIRED MINIMUM PERCENT OF THE TOTAL INSPECTION LOT FOOTAGE IN CONTINUOUS LENGTHS GREATER THAN250 feet 100 feet 50 feet Component Wire 85% 100% -- Finished Cable--85%100%3.6.7 Identification of ProductThe component wire or finished cable shall be identified by a printed marking applied to the outer surface, or visible through the outer surface, of the wire or cable insulation. Identification marking of unshielded, unjacketed cable shall be located on component number 1. Identification marking of components of finished cable shall not be required. Printing of the color code designator on surface of wire insulation or jacket is not required. The printing marking shall consist of the following information:Detail specification part numberManufacturer’s code as specified in publications H4/H8For finished shielded and jacketed cable, the words “FILTER LINE” shall follow the manufacturer’s code.3.6.7.1 Identification intervals: For the component wire, the identification shall be at intervals of 9 inches to 60 inches,as measured from the beginning of one complete marking to the beginning of the succeeding completed marking. For finished cable, the distance between the end of one complete marking and the beginning of the next complete marking shall not be greater than 12 inches.3.6.7.2 Identification color: The printing shall be white in color in accordance with MIL-STD-104, Class 1. Identificationprinting shall be applied with the vertical axes of the printed characters lengthwise of the component wire or finished cable when the nominal diameter is 0.050 inch or smaller. The vertical axes of the printed characters may be either crosswise or lengthwise of the component wire or finished cable when the nominal diameter exceeds 0.050 inch. All printed characters shall be complete and legible.3.6.7.3 Durability of identification: Identification printing, when applied to the outer surface of the component wire orfinished cable, where applicable, shall be capable of withstanding the durability test specified in 4.7.11 for the number of cycles and with the weight specified in the detail specification.3.6.8 Insulation and Jacket FlawsWhen required by the detail specification, one hundred percent of the component wire and finished cable shall pass the spark test of 4.7.17.1 or the impulse dielectric test of 4.7.17.2. Testing of finished component wire or cable shall be performed during the final winding on shipment spools or reels. Component wire intended for finished cable shall be tested prior to cabling.3.6.9 WorkmanshipAll details of workmanship shall be in accordance with high grade wire and cable manufacturing practice. The insulation shall be free of cracks, splits, irregularities, and imbedded foreign material.3.6.10 Wrap TestWhen component wires are tested in accordance with 4.7.29, there shall be no cracking of insulation.3.6.11 Jacket ResistivityWhen tested in accordance with 4.7.1, the jacket resistivity for conductive jackets shall be 150 ohm-cm, maximum.3.6.12 Low Temperature (cold bend)When samples are tested in accordance with 4.7.19, there shall be no cracking of the insulation or jacket and no dielectric breakdown.4. QUALITY ASSURANCE PROVISIONS4.1 Responsibility for InspectionUnless otherwise specified in the contract or purchase order, the supplier is responsible for the performance of all inspection requirements as specified herein. Except as otherwise specified, the supplier may use his own or any other facilities suitable for the performance of the inspection requirements specified herein, unless disapproved by the qualifying activity. The qualifying activity reserves the right to perform any of the inspections set forth in the specification where such inspections are deemed necessary to assure that supplies and services conform to prescribed requirements.4.2 Classification of InspectionsThe examinations and tests of component wire and finished cable under this specification shall be divided into the following classifications:Classification ParagraphQualification inspection 4.3Quality conformance inspection 4.4Process control inspection 4.5Periodic qualification re-evaluation 4.64.3 Initial Qualification InspectionInitial Qualification inspection shall consist of the examination and tests listed in Table 3 of this specification as applicable to the component wire or finished cable. Qualification approval for finished cable must be obtained both for the component wire and for the finished construction. The qualifying activity (see 6.3) is required to perform tests as indicated in Table 3 as noted. Upon request (see 4.3.2), the qualifying activity shall provide a data package to the manufacturer for inclusion in the final test report.4.3.1 Sampling for Qualification InspectionExcept as provided in 4.3.1.1, a component wire or finished cable sample of the required length shall be tested for each range of component wire or finished cable sizes for which qualification is desired. The sample may be any size of component wire or finished cable within the size range specified below. Within each size range for which qualification is desired for shielded, jacketed cable, both a single-conductor and a multiple-conductor finished cable sample must be tested if they fall within that size range. Ten linear feet of the coated conductor strand used in the manufacture of the finished wire sample shall be submitted with the finished wire sample.Component Wire Size Range Required Length of Sample (Feet)24 and smaller 200 22 through 18 200 16 and larger 200Finished Cable Size Range Nominal Overall Diameter (Inch) Required Length of Sample (Feet)0.100 100 > 0.100 and 0.150 100 > 0.150 and 0.225 100 > 0.225 1004.3.1.1 Optional qualification samples: In cases where two or more detail specifications cover component wire orfinished cable identical in materials and construction except for conductor and/or shield material (i.e., the specified conductor or shield may be tin-coated copper, silver-coated high strength copper alloy or as specified in the detail specification), the component wire or finished cable sample in accordance with 4.3.1 may qualify any one of the detail specification components. For those detail specifications so qualified by similarity, a conductor and/or strand shall be tested in accordance with the applicable conductor and/or strand requirements in Table 3. One conductor and/or strand shall be tested for each size range specified in 4.3.1. Approval of the qualification sample shall also qualify the same component wire or finished cable size range or ranges in each of the other detail specifications. Ten linear feet of the conductor strand and shield strand applicable to the same wire or cable size range as the finished wire or cable samples shall be submitted when qualification by similarity is requested. (Note: For purposes of determining identity of construction in detail specifications under this provision, small differences in specified component wire or finished cable diameter or weight which are due to differences in the specified conductor or shield shall not be considered as constituting differences in construction of the component wire or finished cable.)TABLE 3 - PROPERTIES OF COMPONENT WIRE AND FINISHED CABLETABLE 3 - PROPERTIES OF COMPONENT WIRE AND FINISHED CABLE (CONT’D)EXAMINATION OR TEST REQUIREMENT METHODspecification 4.7.25 Thermal shock resistance 1/ Detailspecification 4.7.26 Thermal stability 1/ DetailVacuum stability Detail specification ASTM E595-77Detail specification 4.7.27.2Voltage withstand(post-environmental)4.7.28specificationWeight DetailWorkmanship 3.6.9 4.7.12 Wrap test 1/ Detail specification and 3.6.10 4.7.29FINISHED CABLEBlocking 1/ 3.6.1 4.7.4 Cabling Detail specification and 3.6.2 4.7.12Color 3.6.3 4.7.124.7.5Concentricity DetailspecificationConductor and shield continuity 3.6.5 4.7.12Construction and materials Detail specification, 3.4 and 3.5 4.7.12Continuous lengths 3.6.6 4.7.9Crosslinking proof test 1/ 3.6.4 4.7.103.6.3 and 3.6.7.34.7.11Durability of marking and colorstriping 1/Finished cable diameter 1/ Detailspecification 4.7.124.7.13Flammability DetailspecificationIdentification of product 1/ 3.6.7 4.7.124.7.15specificationImmersion DetailJacket elongation and tensileDetail specification 4.7.16strength 1/Insulation and jacket flaws Detail specification and 3.6.8 4.7.17Jacket resistivity 1/ 3.6.11 4.7.1specification 4.7.12 Jacket thickness 1/ DetailLife cycle 1/ 3.6.4 4.7.10 Low temperature (cold bend) 1/ 3.6.12 4.7.19specification 4.7.20 Shield coverage and angle 1/ DetailDetail specification 4.7.24Surface transfer impedance,effective 1/specification 4.7.26 Thermal stability 1/ DetailVacuum stability Detail specification ASTM E595-77Voltage withstand (dielectric) Detail specification 4.7.27.1Voltage withstandDetail specification 4.7.27.2(post-environmental)4.7.28Weight 1/ DetailspecificationWorkmanship 3.6.9 4.7.121/ Tests shall be performed by the qualifying activity.4.3.2 Forwarding of Qualification Samples:Samples and the manufacturer’s certified test report (excluding the qualifying activity test data except when required by the supplier) shall be forwarded to the testing laboratory designated in the letter of authorization from the activity responsible for qualification (see 6.3), plainly identified by securely attached, durable tags marked with the following information:Sample for qualification testCABLE, ELECTRIC, FILTER LINE, RADIO FREQUENCY ABSORPTIVEDetail specification part numberManufacturer’s name and code number (Publication H4/H8)Manufacturer’s part numberComprehensive description and manufacturer’s name and formulation number of the base materials from which the product is made. (This information will not be divulged by the Government.)Place and date of manufacture of sampleSubmitted by (name) (date) for qualification tests in accordance with the requirements of AS85485 under authorization (reference authorizing letter).The tags or spools must be stamped by the government inspector as representative samples of the manufacturer’s normal production capability. Samples submitted without the stamp will not be accepted.4.4 Quality Conformance InspectionQuality conformance inspection shall consist of the examinations and tests listed in Table 4 and described under “Test Methods” (4.7). Quality conformance inspection shall be performed on every lot of component wire or finished cable procured under this specification.4.4.1 Sampling for Quality Conformance InspectionANSI/ASQC Z1.4. shall apply for definitions of inspection terms used herein. For purposes of this specification, the following shall apply.4.4.1.1 Lot: The inspection lot shall include all component wire or finished cable of one part number subjected toinspection at one time.4.4.1.2 Unit of product: The unit of product for determining lot size for sampling shall be one continuous length ofcomponent wire or finished cable as offered for inspection.。
72285中文资料

Series E CS-2243 10/17/03Page 1 of 2DescriptionSeries E low-profile speaker/strobesare designed for high-efficiencysound output, with dual voltagecapability (25/70 V RMS ) and field-selectable taps from 1/8 to 2 watts.The low-profile design incorporatesa speaker mounting plate for faster and easier installation. Each modelhas a built-in level adjustmentfeature and an attractive grillecover with two flush screws.The Series E speaker/strobe modelsincorporate the low-current, zero-inrush, Series RSS non-sync/sync strobe. Strobe options include 15/75 cd ormulti-candela strobe with field-selectable candela settings of: 15, 30, 75, or 110cd (wall); or 15, 30, 75, or 95 cd, or 115/177 cd (ceiling, depending on model).Series E speaker/strobes provide high audio output with clear audibility,and are designed to meet the critical needs of the life safety industry foreffective emergency voice communications, tone signaling, and visiblesignaling to alert the hearing impaired. The strobe portion of all Series Espeaker/strobes may be synchronized when used in conjunction with the SMor DSM (P/N 51548, 51549) sync modules or the Gamewell FF8 powersupply. Synchronized strobes offer an easy way to comply with ADA recom-mendations concerning photosensitive epilepsy. Series E speaker/strobesare listed for indoor use, with a temperature range of 32°F to 120°F (0°C to49°C) and a maximum humidity of 85%.Architectural/Engineering SpecificationsThe speaker appliances shall be Series E speaker/strobes. The speakersshall be UL Listed under Standard 1480 for Fire Protective Service; speakerappliances equipped with strobes shall additionally be Listed under ULStandard 1971, Emergency Devices for the Hearing Impaired. In addition,the strobes shall be certified to meet the requirements of FCC Part 15,Class B.All speakers shall be designed for a field-selectable input of either 25 or 70V RMS , with selectable power taps from 1/8 watt to 2 watts. All models shallhave a Listed sound output of up to 87 dB at 10 feet (3.048 m), and a Listedfrequency response of 400 to 4000 Hz. The speaker shall incorporate sealedback construction. All inputs shall employ terminals that accept 12 AWG to18 AWG (3.1 to 0.78 mm²) wire. The strobe portion of the appliance shallproduce a flash rate of one flash per second over the regulated voltagerange and shall incorporate a Xenon flashtube enclosed in a ruggedLEXAN® lens. The strobe shall be of low-current design. Where multiple-candela speaker/strobes are specified, the strobe intensity shall be rated perUL 1971 for 15, 30, 75, or 110 candela for wall-mount applications; and 15,30, 75, or 95 candela, or for 115/177 candela, for ceiling-mount applications(depending on model). The selector switch for selecting the candela shall beFeatures •Wall-mount models available with field-selectable candela settings of 15/30/75/110 cd on multi-candela models, or 15/75cd on non-selectable model.•Ceiling-mount multi-candela models are available with field-selectable candela settings of 15/30/75/95 cd or 115/177cd, depending on model.•Strobes produce one flash per second over the regulated voltage range.•Zero inrush above peak.•Strobes operate at 24 VDC with wide UL “regulated voltage” using filtered DC or unfiltered V RMS input voltage.•Synchronize strobes with SM or DSM sync modules (P/N 51548, 51549) or FF8power supply with built-in sync protocol.•Field-selectable taps for 25 or 70 V RMS operation from 1/8 watt to 2 watts.•High-efficiency design for maximum output at minimum wattage across a frequency range of 400 to 4000 Hz.•Fast installation with in/out screw terminals using 12 to 18 AWG (3.1 to 0.78 mm²) wires.Speaker/strobe sound output •1/8 watt: 77.5 dBA @ 10 ft (3.048 m).•1/4 watt: 80.4 dBA @ 10 ft (3.048 m).•1/2 watt: 83.2 dBA @ 10 ft (3.048 m).•1.0 watt: 85.7 dBA @ 10 ft (3.048 m).•2.0 watt: 87.8 dBA @ 10 ft (3.048 m).Average RMS current for multi-candela models •Wall, 15 cd @ 24 VDC: 0.041 A.•Wall, 15/75 cd @ 24 VDC: 0.064 A.•Wall, 30 cd @ 24 VDC: 0.065 A.•Wall, 75 cd @ 24 VDC: 0.116 A.•Wall, 110 cd @ 24 VDC: 0.155 A.•Ceiling, 15 cd @ 24 VDC: 0.045 A.•Ceiling, 30 cd @ 24 VDC: 0.072 A.•Ceiling, 75 cd @ 24 VDC: 0.128 A.•Ceiling, 95 cd @ 24 VDC: 0.171 A.•Ceiling, 115 cd @ 24 VDC: 0.195 A.•Ceiling, 177 cd @ 24 VDC: 0.270 A.Listings •UL 1971, 1480 Listed.•CSFM, MEA (NYC) and BFP (City of Chicago) approved.•Meets ADA accessibility guidelines.•Meets FCC Part 15.•Meets OSHA 29, Part 1910.165.Series ESpeaker/Strobes5741ss70.jpg5741ss90.jpgSeries E CS-2243 10/17/03Page 2 of 2 AC opyright ©2003 Specifications and wiring information are provided for information only and are believed to be accurate. Gamewell assumes no responsibility for their use.Data and design are subject to change without notice. Installation and wiring instructions shipped with the product shall always be used for actual installation.For more information, contact Gamewell.tamper resistant. The 15/75 candela wall strobe shall be specified when 15 candela UL 1971 Listing with 75 candela intensity on-axis is required (e.g., ADA compliance). When synchronization is required, the strobe portion of the appliance shall be compatible with SM and DSM (P/N 71548, 71549) sync modules and the Gamewell FF8 power supply with built-in sync protocols. The strobes shall not drift out of synchronization at any time during operation.If the sync module or power supply fails to operate (i.e., contacts remain closed), the strobes shall revert to a non-synchronized default flash rate of one flash per second.The speaker/strobe appliances shall be designed for indoor surface- or flush-mounting. The speaker/strobes shall incorporate a speaker mounting plate with a grille cover, which is secured with two screws for a level, aesthetic finish. Speaker/strobes shall mount to standard electrical hardware requiring no additional trimplate or adapter.Speaker/strobes shall be finished in a textured red or white color. All speaker/strobe appliances shall be backward compatible.Ordering InformationAll 24 V models below feature field-selectable taps for 25 or 70 V RMS operation, from 1/8 watt to 2 watts.72045Wall-mount multi-candela (15, 30, 75, 110) speaker/strobe, 24 VDC, square, red (E70-24MCW-FR ).72046Wall-mount multi-candela (15, 30, 75, 110) speaker/strobe, 24 VDC, square, white (E70-24MCW-FW ).7174515/75-candela speaker/strobe, wall-mount, 24 VDC, 0.064 A, square, red (E70-241575W-FR ).72285Ceiling-mount multi-candela (15, 30, 75, 95) speaker/strobe, 24 VDC, round, white (E90-24MCC-FW ).72286Ceiling-mount multi-candela (115, 177) speaker/strobe, 24 VDC, round, white (E90-24MCCH-FW ).Sync modules, power supply71548SM sync module, single-circuit Class B, rated for 3.0 A @ 24 VDC (SM-12/24-R ).71549DSM sync module, single-circuit Class A or multiple-circuit Class B, rated for 3.0 A per circuit. The maximum number of interconnected modules is 20 (DSM-12/24-R ).FF8FireForce 8, NAC expander/power supply. 12/24 VDC, 8.0 A, 4 NACs, built-in sync protocols.See data sheet CS-2282.Mounting accessories for Series E speaker/strobes70418Surface-mount backbox, 5.5" (13.970 cm) x 5.563" (14.129 cm) x 3.563" (9.049 cm), red (SBB-R ).71317Extender, molded, 5.25" (13.335 cm) square 0.781" (1.984 cm) deep, red (ISP-R ).71318Retrofit plate, 8.0" (20.320 cm) x 5.875" (14.923 cm) x 0.406" (1.032 cm) deep, red (RP-R ).68292Semi-flush plate, 6.0" (15.240 cm) square x 0.313" (0.794 cm) deep, red (SFP-R ).。
HiFocus 80i 高精度软切换逆变器镁盐电解质切割单元说明书
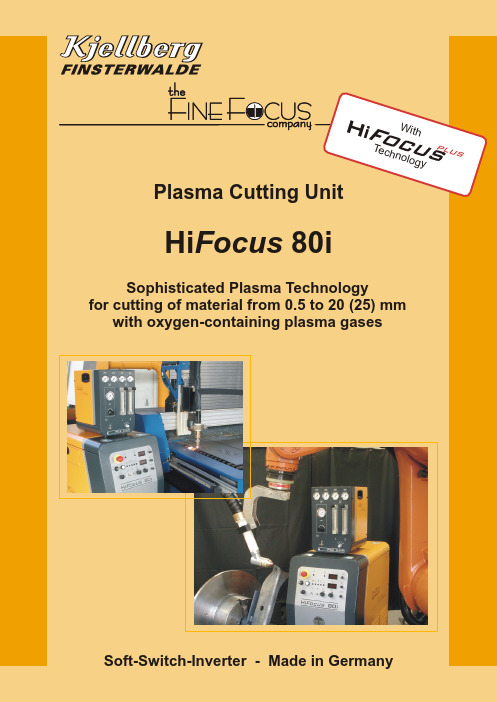
Plasma Cutting UnitHi Focus 80iSoft-Switch-Inverter - Made in GermanySophisticated Plasma Technologyfor cutting of material from 0.5 to 20 (25) mmwith oxygen-containing plasma gasesp l usW i t h T e c hno l o gyThe request of our customers for a plasma cutting unit withtechnology for materials from 0.5 to 20 (25) mm was the reason for our enterprise for a new development. Additionally the rising demand ofthe automobile industry and their suppliers calls for a future-orientated and up-to-date Hi Focusunit,covering its technical capabilities, especially for therobot operation, and meeting all requirements on thelocal and international market.Based on the approved Soft-Switch-Inverter technology now theHi Focus80i with the micro-processor controlled power source is at disposal for a cutting range up to 80 A at 100 % duty cycle. In con-nection with the powerfulplasma torch PerCut 80quality cutting in a wide range is granted. That means laserlike quality cuts with nearly no drossadherence, lowest straightness tolerances and veryclean cutting surfaces.The high performance capacity of the plasma torchPerCut 80 ensures in connection with the heavy duty XL-Life-Time system and its longevity of cathodesand nozzles (up to 1,200 piercings with edge square-ness still below 3°) lowest costs on consumables and minimized downtimes . The technical condi-tions for the high productivity of the plasma cutting process are optimized operational parts of the beam generation system interacting with microprocessor controlled sequences.For the moment this unique plasma cutting unit with technology will b e offered in this performance class for the plasma gases oxygen and air. Because of the outstanding price-performance ratio especially the medium seized industry now is in the position to compete on the market with high-class cutting work.The flexible installation configuration will be offered as a complete package with hose parcel extensions up to 15 m, sufficient for thin sheet cutting with small 2-D guiding systems with approximately 2.5 x 4.0 m table size, and for robot applications as well.For advanced robot applications the separate system specification Hi Focus 80i-Robo is availab le. With newly developed 3-D consumables for bevel cutting up to 45° the unit particularly is recommended for b evelling units and rob ots, also in connection with particular torches.Hi Focus Hi Focus PLUSPLUS Hi Focus 80i - unit of function and designBevel cuttingon a 3-D workpiece with robotHi Focus 80iConsumables XL-Life-Time SystemTo meet the enhanced requirements of the Hi Focus technology the new PerCut torch generation was Versatile torch technology - basis for quality and flexibilityThe cutting speed is valid for the highest cut quality . In case of reduced demands on the cut quality cutting with up to 2.5-fold speed is possible. The cutting speed depends on kind of material, gas pressure, cutting and swirl gas and the used nozzle/cathode system as well.Focus technology(State: 10/2004)technologyHi Focus technology PLUS 5 0003 5002 6002 200Cutting current (A)Cutting speed (mm/min)Cutting speed (mm/min)Quick-change torch PerCut 90Kjellberg Finsterwalde Elektroden und Maschinen GmbH Germany D - 03238 Finsterwalde Leipziger Str. 82Tel.: +49 3531 500-0 Fax: +49 3531 500-227E-mail:********************** Internet: www.kjellberg.de04-10-03Power source Cutting current Mains connection Mains fuseConnecting load Open circuit voltage IgnitionProtection class Insulation classDimensions (L x B x H)WeightHi Focus 80iSoft-Switch-Inverter 10 - 80 A (100 % d.c.)3x 400 V, 50 Hz25 A “C”17 kVA 400 V High tensionIP 22F970 x 510 x 970 mm161 kgPlasma machine torch Quick-change torchCutting current (100% d.c.)Standard lengthsTorch hose parcel Cable set for PBA Clamping diameterPerCut 80PerCut 90Weight (with 1,5 m hose parcel)CoolingPlasma gases Swirl gasesPlasma Torch PerCut 80PerCut 90max. 100 A 1.5 m 6, 10, 15 m 44 mm 50 mm 3.8 kgdirect circulation Oxygen, AirOxygen, Nitrogen, AirTechnical dataSystem configuration for the cutting of mild steelwith robots or guiding systemsPGE3-HM Plasma gas adjustment unit PBA-H80 Plasma torch connection unit FB Remote control PBL-HCable set for PBAFBCNCPGE 3-HMN O O /Air AirPlasma gases Swirl gasesWorkpiece cable (5m)Gas hoses(6/10/15 m)PBL-H (6/10/15 m)Hi Focus 80iPBA-H80PerCut 80-2orPerCut 90-21,5 mP B A -H6.xxPerCut 80-2Robo 1,5 mPBA-H80 RoboAirOur products represent a high level of quality and reliability. We reserve the rights to change design and/or technical specification during the series fabrication.Claims of whatever kind can’t derived from this prospectus.Kjellberg-plasma cutting units are CE-conform and correspond with the valid guidelines and instructions of the European Union. They are developed and fabricated on basis of following standards and instructions: EN 60974-1 (VDE 0544, part 1) and BGV D1. The plasma cutting units are labelled with the S-sign and therefore applicable to environments with increased hazard of electric shock.The fabrication takes place according to DIN EN ISO 9001. The factory-owned quality assurance comprises piece and cutting performance tests, documented by test certificate. **********************。
850F1K5E中文资料(ohmite)中文数据手册「EasyDatasheet - 矽搜」

这些模施工金属封装电阻 较高额定功率比标准轴向电
阻器提供更适合于承受振动 ,冲 击和恶劣环境条件.
89系列金属螨
电阻铝壳操作过程中防护持较 ®
高稳定性,并允许安全安装到机 箱表面.
金属外壳还
提供散热capabili-关系.
特征
•高稳定性Suffix
1,500 –––1K5 2,000 –––2K0 2,500 –––2K5
=标准值 =受最低非标准值
手续费每件
3,000 –––3K0
3,500 –––3K5 4,000 –––4K0 4,500 –––4K5
阴影值涉及非常细电阻丝,不应该用在关键应用未 经老化和/或热循环.
5,000 –––5K0
额定功率: 额定值是基于
在底盘安装面产品, 温度稳定性.正确 散热器如下:5W和 10W单位,4"×6"×2"×0.040" 铝合金底盘; 25W单位,5" ×7"×2"×0.040"铝chasSIS; 50W单位,12"×12"×0.059" 铝合金面板.
最大电阻值:
请参阅图表.
超载: 5倍额定功率 为5秒.
12
12
Dim. R (in., min/mm, min)
0.085/ 2.16 0.140/ 3.56 0.140/ 3.56 0.140/ 3.56
Wattage
TA N D A RðPA RT N个U M BËR 5
Wattage
Wattage
Part No. Ohmic Pvraelfuixe
Suffix 0.005–––R005 0.010–––R010 0.025–––R025 0.1 –––R10 0.3 –––R30 0.5 –––R50 0.7 –––R70 1.0 –––1R0 1.5 –––1R5 2.0 –––2R0 3.0 –––3R0 4.0 –––4R0 5.0 –––5R0 10.0 –––10R 15.0 –––15R
赛米控丹佛斯电子 SEMiX854GB176HDs 数据表

SEMiX ®4sTrench IGBT ModulesSEMiX854GB176HDsFeatures•Homogeneous Si•Trench = Trenchgate technology •V CE(sat) with positive temperature coefficient•UL recognised file no. E63532Typical Applications*•AC inverter drives •UPS•Electronic weldersAbsolute Maximum Ratings SymbolConditions Values UnitIGBT V CES T j =25°C 1700V I C T j =150°CT c =25°C 779A T c =80°C549A I Cnom 600A I CRMI CRM = 2xI Cnom 1200A V GES -20...20V t psc V CC =1000V V GE ≤ 20V V CES ≤ 1700VT j =125°C10µs T j-55...150°C Inverse diode I F T j =150°CT c =25°C 740A T c =80°C 496A I Fnom600A I FRM I FRM = 2xI Fnom1200A I FSM t p =10ms, sin 180°, T j =25°C3800A T j -40 (150)°C Module I t(RMS)T terminal =80°C600A T stg -40...125°C V isolAC sinus 50Hz, t =1min4000VCharacteristics SymbolConditions min.typ.max.UnitIGBT V CE(sat)I C =600A V GE =15V chiplevelT j =25°C 2 2.45V T j =125°C 2.5 2.9V V CE0T j =25°C 1 1.2V T j =125°C0.9 1.1V r CE V GE =15VT j =25°C 1.7 2.1m ΩT j =125°C2.63.0m ΩV GE(th)V GE =V CE , I C =24mA 5.25.86.4V I CES V GE =0V V CE =1700V T j =25°C 4mA T j =125°C mA C ies V CE =25V V GE =0Vf =1MHz 52.8nF C oes f =1MHz 2.20nF C res f =1MHz1.75nF Q G V GE =- 8 V...+ 15 V 5600nC R Gint T j =25°C 1.25Ωt d(on)V CC =1200V I C =600A V GE =±15V R G on =2ΩR G off =2ΩT j =125°C 340ns t r T j =125°C 80ns E on T j =125°C 300mJ t d(off)T j =125°C 890ns t f T j =125°C 155ns E off T j =125°C250mJ R th(j-c)per IGBT 0.045K/WCharacteristics SymbolConditionsmin.typ.max.UnitInverse diodeV F = V EC I F =600AV GE =0V chipT j =25°C 1.7 1.90V T j =125°C 1.7 1.9V V F0T j =25°C 0.9 1.1 1.3V T j =125°C0.70.9 1.1V r FT j =25°C 1.0 1.0 1.0m ΩT j =125°C1.31.3 1.3m ΩI RRM I F =600A di/dt off =8000A/µs V GE =-15VV CC =1200VT j =125°C 730A Q rr T j=125°C220µC E rr T j =125°C 170mJR th(j-c)per diode0.081K/WModule L CE 22nH R CC'+EE'res., terminal-chip T C =25°C 0.7m ΩT C =125°C1m ΩR th(c-s)per module 0.03K/W M s to heat sink (M5)35Nm M tto terminals (M6)2.55Nm Nmw400gTemperatur Sensor R 100T c =100°C (R 25=5 k Ω)493 ± 5%ΩB 100/125R (T)=R 100exp[B 100/125(1/T-1/T 100)]; T[K];3550 ±2%K SEMiX ® 4sTrench IGBT ModulesSEMiX854GB176HDsFeatures•Homogeneous Si•Trench = Trenchgate technology •V CE(sat) with positive temperature coefficient•UL recognised file no. E63532Typical Applications*•AC inverter drives •UPS•Electronic weldersFig. 1: Typ. output characteristic, inclusive R CC'+ EE'Fig. 2: Rated current vs. temperature I C = f (T C )Fig. 3: Typ. turn-on /-off energy = f (I C )Fig. 4: Typ. turn-on /-off energy = f (R G )Fig. 5: Typ. transfer characteristic Fig. 6: Typ. gate charge characteristicFig. 7: Typ. switching times vs. I C Fig. 8: Typ. switching times vs. gate resistor R GFig. 9: Typ. transient thermal impedance Fig. 10: Typ. CAL diode forward charact., incl. R CC'+EE'Fig. 11: Typ. CAL diode peak reverse recovery current Fig. 12: Typ. CAL diode recovery chargeThis is an electrostatic discharge sensitive device (ESDS), international standard IEC 60747-1, Chapter IX* The specifications of our components may not be considered as an assurance of component characteristics. Components have to be tested for the respective application. Adjustments may be necessary. The use of SEMIKRON products in life support appliances and systems is subject to prior specification and written approval by SEMIKRON. We therefore strongly recommend prior consultation of our staff.spring configuration。
USCAR中文第版
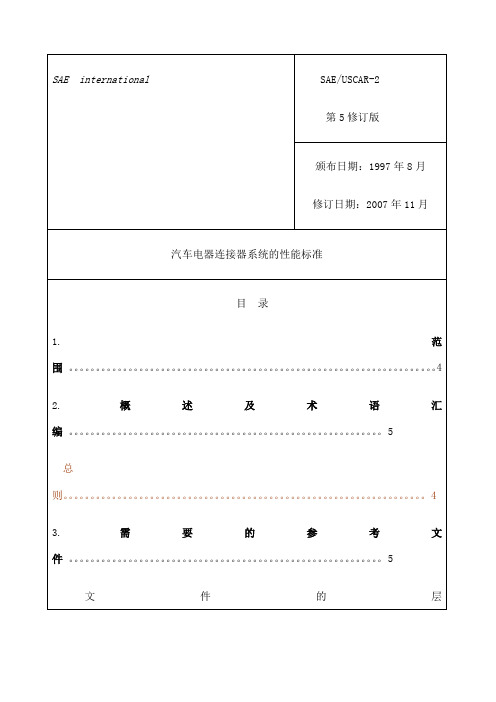
产品设计规范 。。。。。。。。。。。。。。。。。。。。。。。。。。。。。。。。。。。。。。。。。。。。。。。。。。。。。。6
实验要求/顺序。。。。。。。。。。。。。。。。。。。。。。。。。。。。。。。。。。。。。。。。。。。。。。。。。。。。。6
设备。。。。。。。。。。。。。。。。。。。。。。。。。。。。。。。。。。。。。。。。。。。。。。。。。。。。。。。。。。。。。。。8
测量精确度。。。。。。。。。。。。。。。。。。。。。。。。。。。。。。。。。。。。。。。。。。。。。。。。。。。。。。。。。8
测量可靠性和刻度。。。。。。。。。。。。。。。。。。。。。。。。。。。。。。。。。。。。。。。。。。。。。。。。。。。。9
其他参考文件 。。。。。。。。。。。。。。。。。。。。。。。。。。。。。。。。。。。。。。。。。。。。。。。。。。。。。。7
4.一般要求。。。。。。。。。。。。。。。。。。。。。。。。。。。。。。。。。。。。。。。。。。。。。。。。。。。。。。。。。。。。。。。。7
记录(档案)保存。。。。。。。。。。。。。。。。。。。。。。。。。。。。。。。。。。。。。。。。。。。。。。。。。。。7
总则。。。。。。。。。。。。。。。。。。。。。。。。。。。。。。。。。。。。。。。。。。。。。。。。。。。。。。。。。。。。。。。。。。。4
3.需要的参考文件。。。。。。。。。。。。。。。。。。。。。。。。。。。。。。。。。。。。。。。。。。。。。。。。。。。。。。。。。。5
文件的层次。。。。。。。。。。。。。。。。。。。。。。。。。。。。。。。。。。。。。。。。。。。。。。。。。。。。。。。。5
布伦赛安全系统B.V. LH3-UC25X短长筒型号Ex-proof涛喇叭说明书

Safety Water and dust protected
acc. to EN 60065 acc. to EN 60529 IP 66/67
Bosch Security Systems B.V.
Installation note
2019.03 | V1.3 |
6 en | Technical data
Bosch Security Systems B.V.
Horn loudspeaker, Ex-proof, short/long flare
Technical data | en 7
LH3-UC25XL | LH3-UC25XL-1: Technical Specifications Electrical*
Operating temperature Storage temperature Relative humidity Certification and Approvals
-50 ºC to +60 ºC (-58 ºF to +140 ºF) -40 ºC to +70 ºC (-40 ºF to +158 ºF) <95%
Horn loudspeaker, Ex-proof, short/long flare
1 2
1 2
100 100
Figure 1.9
Figure 1.10
COM(0)
100 V X10
LBB4441/00 X11
LH3-UC25Xx
1 2 3 4
100 V
COM(0)
Figure 1.11
1 2 25 W
2 3 15 W
3 4 6,5 W
菲格瑞思电磁流量计(大壳防爆)说明书
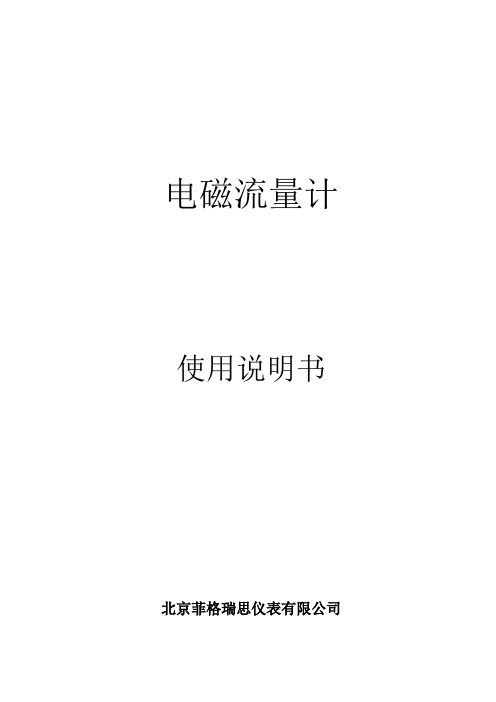
电磁流量计使用说明书北京菲格瑞思仪表有限公司特点:●国内首家将“模糊算法”技术应用于“电磁流量计”的测量,具备人工智能的性能。
●国内首家具有HART通讯功能的电磁流量仪表。
●Ex防爆设计,符合国家防爆技术要求,已通过鉴定验收,可应用与各类防爆场所。
●高阻快速响应设计,无失真采集微弱信号和快速反应流量变化,量程比可达100:1。
●具有低电导测量功能。
●国内首家采用电容式技术的空、满管检测技术,杜绝误报警的出现。
●具备转换器互换的一致性,无须重新输入参数。
●宽范围电源模式可供选择(DC:18V~36V AC:85V~265V)。
●国内首家采用出厂保存设置功能,使仪表各参数万无一失。
●采用国际领先的励磁技术,励磁电路简洁,稳定可靠。
●红外遥控功能以及按键操作,操作更加方便。
●提供传感器零点修正以及自动校零功能。
●全中文(英文)友好界面,满足各方使用要求。
●具备转换器本机自校、自检功能。
●具备防雷电保护设计电路。
高效抗干扰电路,适用各种恶劣环境。
●多种输出通讯接口可供选择:1.hart通讯(可选)2.RS485(Modbus 可选) 通讯接口3.profibus(可选)4.16位数字电流环 4~20mA输出5.0 ~10KHz频率输出6.脉冲当量输出执行标准、正常工作条件和型号命名执行标准: JB/T9248-1999 GB 3836.1-2000 GB 3836.2-2000 GB 3836.4-2000 正常工作条件:环境温度:-20℃~+55℃ 相对湿度:5%~90%供电电源:85~265AC 或18~36VDC 额定功率:小于10W工作原理传感器是根据法拉第电磁感应定律工作的,如图1所示:图1. 工作原理图当导电液体沿测量管在交变磁场与磁力线成垂直方向运动时,导电液体切割磁力线产生感应电势。
在与测量管轴线和磁场磁力线相互垂直的管壁上安装了一对检测电极,将这个感应电势检出。
若感应电势为E ,则有:E=BVD ⑴ 式中:B …磁感应强度;D …电极间的距离,与测量管内径相等; V …测量管内径被测流体在截面上的平均流速。
CTS Series 448 Technical Data

•Slim construction permits stacking many units in a small spaceTechnical Data Sheet 1448CC T S C O R P O R A T I O N /M A N U F A C T U R E R O F R E L I A B L E E L E C T R O N I C C O M P O N E N T SElectrical and Mechanical SpecificationsResistance Range500 ohms through 1 megohm Resistance ToleranceStandard ±20%Available ±10%Resistance TapersStandard: LinearSpecial: Available upon request Insulation Resistance10 megohms at 250 VDC Voltage RatingAcross end terminalsLinear curves—300 VDC(Not to exceed wattage ratings)Power Rating, wattsResistor:0.2 watt @ 55°C derated to no load@ 85°C, linear taper Switch:1000 watts 120VAC (tungsten-filament load)***************.80PF(inductiveload)Power Switch (optional)SPST -10,000 cycles carrying 1000 watts 120 VAC(Tungsten-filament)10,*********************************.80PF(Inductive load)SPDT -10,000 cycles carrying 600 watts 120 VAC(Tungsten-filament)6,*********************************.80PF(Inductive load) Slide TravelX and U Style: 10, 15, 20, 30, 45, and 60mm V Style: 10, 15, 25, 40, and 55mmSwitch:20mm = 17mm electrical + 3mm switch30mm = 27mm electrical + 3mm switch Actuator InformationSee Illustrations, page 4 (Actuator Styles)Operating ForceEither direction 20-150 gf Switch OFF force: 100-500 gfStop Strength: 3K gf maximum, measured at base of slider Detent Force (detent optional)Leaving detent: 20-200 gf over operating force Operating Life10,000 cyclesLinear 0.05w 0.1w 0.2w 0.25w 0.5w Non-linear 0.025w 0.05w 0.1w 0.15w0.25wSize 10mm 15mm 30mm 45mm60mm Taper20mmMODEL DIMENSIONS L (Travel)A BCU448-10D 10/ .39419.10/ .75225.40/1.00029.50/1.161U448-15D 15/ .59124.10/ .94930.40/1.19734.50/1.359U448-20D 20/ .78729.10/1.14635.40/1.39439.50/1.555U448-30D 30/ 1.18139.10/1.53945.40/1.78749.50/1.949U448-45D 45/ 1.77254.10/2.13060.40/2.37864.50/2.539U448-60D60/ 2.36269.10/2.72175.40/2.96979.50/3.131DIMENSION:MM INCHMODEL DIMENSIONSL (Travel)A BU448-10M 10/ .39419.60/ .77223.70/ .933U448-15M 15/ .59124.60/ .96928.70/1.130U448-20M 20/ .78729.60/1.16533.70/1.327U448-30M 30/ 1.18139.60/1.55943.70/1.720U448-45M 45/ 1.77254.60/2.14958.70/2.311U448-60M60/ 2.36269.60/2.74073.70/2.902Type U448 MONOType U448 DUALMODEL DIMENSIONSL (Travel)A BV448-10M 10/ .39430.20/1.18928.70/1.130V448-15M 15/ .59135.20/1.38733.70/1.372V448-25M 25/ .98445.20/1.18043.70/1.721V448-40M 40/ 1.57560.20/2.37058.70/2.311V448-55M55/ 2.16675.20/2.96173.70/2.902DIMENSION:MM INCHDIMENSION:MM INCHMODEL DIMENSIONSL (Travel)A B CX448-20MS20/ .78727.50/1.08347.20/1.85949.20/1.937 X448-30MS30/ 1.18137.50/1.47657.20/2.27259.20/2.331DIMENSION:MMINCHMODEL DIMENSIONSL (Travel)A B CX448-10D10/ .39417.60/ .69330.30/1.19332.40/1.276X448-15D15/ .59122.60/ .89035.30/1.39037.40/1.473X448-20D20/ .78727.60/1.08740.30/1.58742.40/1.669X448-30D30/ 1.18137.60/1.48150.30/1.98152.40/2.063X448-45D45/ 1.77252.60/2.07165.30/2.57167.40/2.654X448-60D60/ 2.36267.60/2.66280.30/3.16282.40/3.248DIMENSION:MMINCHMODEL DIMENSIONSL (Travel)A BX448-10M10/ .39424.50/ .96526.60/1.047X448-15M15/ .59129.50/1.16131.60/1.244X448-20M20/ .78734.50/1.35936.60/1.441 Type X448 MONO W/SPST SWITCHMODELDIMENSIONSL (Travel)A B CX448-20MS 20/ .78727.50/1.08347.20/1.85949.20/1.937X448-30MS 30/ 1.18137.50/1.47657.20/2.27259.20/2.331DIMENSION:MM INCHType X448 MONO W/SPDT SWITCHOrder From:CTS CORPORATION, ELECTROCOMPONENTS / 1601 Mishawaka Street / Elkhart, Indiana 46514North America Toll Free (888) 287-4690 / (219) 296-6700 / FAX: (219) 293-1240 CTS COMPONENTS TAIWAN, LTD. / 7, Central 6th Road (Chung Liu Road) / P.O. Box 26-20Kaohsiung Export Processing Zone / Kaohsiung, Taiwan, Rep. of China (07) 8216145 / FAX: (07) 8417642.81100405M-1-99IActuator StylesOrdering InformationActuator Style “D”Available for “V” type only。
定量仪(氪-85)说明书
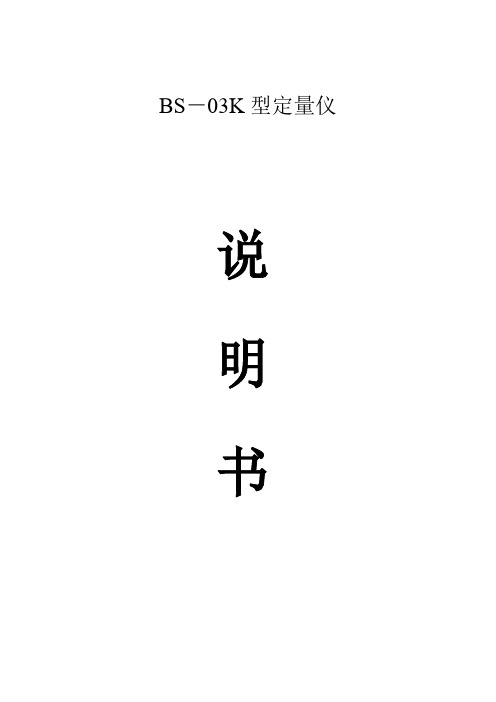
BS-03K型定量仪BS-03K型定量仪(或称测厚仪)是采用微机技术的智能化β射线定量仪,它广泛应用于造纸、橡胶、塑料、卫生材料、金属薄片等在线定量(或厚度)的非接触式的连续测量,为其生产过程的自动化提供重要条件。
本定量仪可单独使用,完成上述测量功能,也可与WST-3A型红外水份仪配套使用(它们的外型及安装尺寸基本相同),组成造纸行业中广泛应用的定量水份仪,简称B/M计。
*以下方框里内容在填写相关申请表格时1、传感器的结构及同位素测厚原理本仪器利用物质对β射线的吸收近似服从指数衰减规律的原理制成。
仪器的传感器由上、下探头两部分组成。
下探头内装有发射β射线的放射源,根据被测对象厚度放射源可选147pm(钷-147)、85Kr(氪-85)等。
此外,下探头内还装有校正用的标样及其驱动装置和用于温度被偿的温度传感器。
上探头内装有用于接收β射线的特殊结构的电离室和高阻抗的前置放大器。
物质对β射线的吸收,可近似地用下式表示:It=I0eˉμtp其中:I0被测物厚度为0(即无被测物)时的电流信号值It被测物厚度为t(或定量为tp)时的电流信号值t 被测物的几何厚度p被测物的密度μ被测物对β射线的吸收系数通常tp称为质量厚度或定量,即单位面积的质量,其量纲为克/平方米等。
由上述可知,测得电流信号It,便能得知被测物的定量值即:/It)tp=(1/μ)×1n(IO当被测物密度p恒定时,则能得知其几何厚度值即:/It)t=(1/μp)×1n(IO可见,在一般情况下,仪器测得的是被测物的单位面积质量(即定量),只有当其密度恒定时,才能得到其几何厚度。
2、电路原理及其执行机构本仪器分为传感器和主机两个部分,由专用电缆把这两部分连接起来。
其整机方框图见下图。
1)整机状态:关闭或停机时放射源处于关闭状态。
校正时下探头的转盘处于标样状态,可对内标样进行测量或由专用微机进行自动校正。
自动校正状态可通过主机背板的开关K2(拨至“校正”位置)或外接KO(见四-1-7)来实现。
- 1、下载文档前请自行甄别文档内容的完整性,平台不提供额外的编辑、内容补充、找答案等附加服务。
- 2、"仅部分预览"的文档,不可在线预览部分如存在完整性等问题,可反馈申请退款(可完整预览的文档不适用该条件!)。
- 3、如文档侵犯您的权益,请联系客服反馈,我们会尽快为您处理(人工客服工作时间:9:00-18:30)。
Ordering InformationPART NUMBERTEMPERATURE RANGESCREENING LEVEL PACKAGEHCTS85DMSR -55o C to +125o C Intersil Class S Equivalent 16 Lead SBDIPHCTS85KMSR -55o C to +125o CIntersil Class S Equivalent 16 Lead Ceramic Flatpack HCTS85D/Sample +25o C Sample 16 Lead SBDIPHCTS85K/Sample +25o C Sample 16 Lead Ceramic Flatpack HCTS85HMSR+25o CDieDieHCTS85MSRadiation Hardened4-Bit Magnitude ComparatorPinouts16 LEAD CERAMIC DUAL-IN-LINE METAL SEAL PACKAGE(SBDIP) MIL-STD-1835 CDIP2-T16, LEAD FINISH CTOP VIEW16 LEAD CERAMIC METAL SEAL FLATPACK PACKAGE (FLATPACK) MIL-STD-1835 CDFP4-F16, LEAD FINISH CTOP VIEW14151691312111012345768B3(A<B)IN (A=B)IN (A>B)IN (A<B)OUT (A=B)OUT GND (A>B)OUT VCC B2A2A1B1A0B0A323456781161514131211109B3(A<B)IN (A=B)IN (A>B)IN (A<B)OUT (A=B)OUT GND(A>B)OUTVCC B2A2A1B1A0B0A3Features• 3 Micron Radiation Hardened SOS CMOS •Total Dose 200K RAD (Si)•SEP Effective LET No Upsets: >100 MEV-cm 2/mg•Single Event Upset (SEU) Immunity < 2 x 10-9 Errors/Bit-Day (Typ)•Dose Rate Survivability: >1 x 1012RAD (Si)/s •Dose Rate Upset >1010 RAD (Si)/s 20ns Pulse •Latch-Up Free Under Any Conditions •Fanout (Over Temperature Range)-Standard Outputs: 10 LSTTL Loads•Military Temperature Range: -55o C to +125o C•Significant Power Reduction Compared to LSTTL ICs •DC Operating Voltage Range: 4.5V to 5.5V •LSTTL Input Compatibility -VIL = 0.8V Max -VIH = VCC/2 Min•Input Current Levels Ii ≤ 5µA at VOL, VOHDescriptionThe Intersil HCTS85MS is a Radiation Hardened 4-bit high speed magnitude comparator. This device compares two binary, BCD, or other monotonic codes and presents the three possible magnitude results at the outputs (A>B, A<B,and A=B). The 4-bit input words are weighted (A0 to A3 and B0 to B3), where A3 and B3 are the most significant bits.The HCTS85MS is expandable without external gating, both serial and parallel operation.The HCTS85MS utilizes advanced CMOS/SOS technology to achieve high-speed operation. This device is a member of radiation hardened, high-speed, CMOS/SOS Logic Family with TTL input compatibility.The HCTS85MS is supplied in a 16 lead Ceramic flatpack (K suffix) or a SBDIP Package (D suffix).September 1995HCTS85MSFunctional Block DiagramTRUTH TABLE COMPARING INPUTSCASCADING INPUTS OUTPUTS A3, B3A2, B2A1, B1A0, B0A>B A<B A=B A>B A<B A=B A3>B3X X X X X X H L L A3<B3X X X X X X L H L A3=B3A2>B2X X X X X H L L A3=B3A2<B2X X X X X L H L A3=B3A2=B2A1>B1X X X X H L L A3=B3A2=B2A1<B1X X X X L H L A3=B3A2=B2A1=B1A0>B0X X X H L L A3=B3A2=B2A1=B1A0<B0X X X L H L A3=B3A2=B2A1=B1A0=B0H L L H L L A3=B3A2=B2A1=B1A0=B0L H L L H L A3=B3A2=B2A1=B1A0=B0L L H L L H A3=B3A2=B2A1=B1A0=B0X X H L L H A3=B3A2=B2A1=B1A0=B0H H L L L L A3=B3A2=B2A1=B1A0=B0LLLHHLNOTE:L = Logic Level Low, H = Logic Level High, x = ImmaterialB3A3B2A2B1A1(A>B)B0A0(A=B)(A<B)B3B3A3A3B2B2A2A2B1B1A1A1B0B0A0A0A2B2A3B3A1B1B0A0B0A0(A>B)11514131112491032INININA1B1A3B3A2B2OUT (A=B)OUT(A<B)OUT567Single DeviceORSeries CascadingParallel CascadingAbsolute Maximum Ratings Reliability InformationSupply Voltage (VCC). . . . . . . . . . . . . . . . . . . . . . . . .-0.5V to +7.0V Input Voltage Range, All Inputs . . . . . . . . . . . . .-0.5V to VCC +0.5V DC Input Current, Any One Input . . . . . . . . . . . . . . . . . . . . . . . .±10mA DC Drain Current, Any One Output. . . . . . . . . . . . . . . . . . . . . . .±25mA (All Voltage Reference to the VSS Terminal)Storage Temperature Range (TSTG). . . . . . . . . . .-65o C to +150o C Lead Temperature (Soldering 10sec). . . . . . . . . . . . . . . . . .+265o C Junction Temperature (TJ) . . . . . . . . . . . . . . . . . . . . . . . . . .+175o C ESD Classification . . . . . . . . . . . . . . . . . . . . . . . . . . . . . . . .Class 1Thermal ResistanceθJAθJC SBDIP Package. . . . . . . . . . . . . . . . . . . .73o C/W24o C/W Ceramic Flatpack Package . . . . . . . . . . .114o C/W29o C/W Maximum Package Power Dissipation at +125o C AmbientSBDIP Package. . . . . . . . . . . . . . . . . . . . . . . . . . . . . . . . . .0.68W Ceramic Flatpack Package . . . . . . . . . . . . . . . . . . . . . . . . .0.44W If device power exceeds package dissipation capability, provide heat sinking or derate linearly at the following rate:SBDIP Package. . . . . . . . . . . . . . . . . . . . . . . . . . . . . .13.7mW/o C Ceramic Flatpack Package . . . . . . . . . . . . . . . . . . . . . .8.8mW/o CCAUTION: As with all semiconductors, stress listed under “Absolute Maximum Ratings” may be applied to devices (one at a time) without resulting in permanent damage. This is a stress rating only. Exposure to absolute maximum rating conditions for extended periods may affect device reliability. The conditions listed under “Electrical Performance Characteristics” are the only conditions recommended for satisfactory device operation.Operating ConditionsSupply Voltage (VCC). . . . . . . . . . . . . . . . . . . . . . . .+4.5V to +5.5V Operating Temperature Range (T A) . . . . . . . . . . . .-55o C to +125o C Input Rise and Fall Times at VCC = 4.5V (TR, TF) . . . .500ns Max.Input Low Voltage (VIL). . . . . . . . . . . . . . . . . . . . . . . . .0.0V to 0.8V Input High Voltage (VIH). . . . . . . . . . . . . . . . . . . . . . . .2.0V to VCCTABLE 1.DC ELECTRICAL PERFORMANCE CHARACTERISTICSPARAMETER SYMBOL(NOTE 1)CONDITIONSGROUPA SUB-GROUPS TEMPERATURELIMITSUNITSMIN MAXQuiescent Current ICC VCC = 5.5V,VIN = VCC or GND1+25o C-40µA2, 3+125o C, -55o C-750µAOutput Current (Sink)IOL VCC = 4.5V, VIH = 4.5V,VOUT = 0.4V, VIL = 0V1+25o C 4.8-mA2, 3+125o C, -55o C 4.0-mAOutput Current (Source)IOH VCC = 4.5V, VIH = 4.5V,VOUT = VCC - 0.4V,VIL = 0V1+25o C-4.8-mA2, 3+125o C, -55o C-4.0-mAOutput Voltage Low VOL VCC = 4.5V, VIH = 2.25V,IOL = 50µA, VIL = 0.8V1, 2, 3+25o C, +125o C, -55o C-0.1VVCC = 5.5V, VIH = 2.75V,IOL = 50µA, VIL = 0.8V1, 2, 3+25o C, +125o C, -55o C-0.1VOutput Voltage High VOH VCC = 4.5V, VIH = 2.25V,IOH = -50µA, VIL = 0.8V 1, 2, 3+25o C, +125o C, -55o C VCC-0.1-VVCC = 5.5V, VIH = 2.75V, IOH = -50µA, VIL = 0.8V 1, 2, 3+25o C, +125o C, -55o C VCC-0.1-VInput Leakage Current IIN VCC = 5.5V, VIN = VCC orGND1+25o C-±0.5µA2, 3+125o C, -55o C-±5.0µANoise Immunity Functional Test FN VCC = 4.5V, VIH = 2.25V,VIL = 0.8V (Note 2)7, 8A, 8B+25o C, +125o C, -55o C---NOTES:1.All voltages referenced to device GND.2.For functional tests, VO≥ 4.0V is recognized as a logic “1”, and VO ≤ 0.5V is recognized as a logic “0”.TABLE 2.AC ELECTRICAL PERFORMANCE CHARACTERISTICSPARAMETER SYMBOL (NOTES 1, 2)CONDITIONSGROUPA SUB-GROUPS TEMPERATURELIMITSUNITSMIN MAXAn to (A>B)OUT TPHL,TPLHVCC = 4.5V9+25o C236ns10, 11+125o C, -55o C243ns Bn to (A>B)OUT TPHL,TPLHVCC = 4.5V9+25o C257ns10, 11+125o C, -55o C266ns An, Bn to (A<B)OUT TPHL,TPLHVCC = 4.5V9+25o C245ns10, 11+125o C, -55o C251ns An, Bn to (A=B)OUT TPHL,TPLHVCC = 4.5V9+25o C242ns10, 11+125o C, -55o C250ns An, Bn to (A>B)OUT TPHL,TPLHVCC = 4.5V9+25o C229ns10, 11+125o C, -55o C235ns(A>B)IN to (A>B)OUT TPHL,TPLHVCC = 4.5V9+25o C234ns10, 11+125o C, -55o C239ns(A=B)IN to (A=B)OUT TPHL,TPLHVCC = 4.5V9+25o C228ns10, 11+125o C, -55o C237ns(A<B)IN to (A<B)OUT TPHL,TPLHVCC = 4.5V9+25o C235ns10, 11+125o C, -55o C240nsNOTES:1.All voltages referenced to device GND.2.AC measurements assume RL = 500Ω, CL = 50pF, Input TR = TF = 3ns, VIL = GND, VIH = 3V.TABLE 3.ELECTRICAL PERFORMANCE CHARACTERISTICSPARAMETER SYMBOL CONDITIONS NOTES TEMPERATURELIMITSUNITS MIN MAXCapacitance Power Dissipation CPD VCC = 5.0V, f = 1MHz1+25o C-39pF1+125o C, -55o C-92pFInput Capacitance CIN VCC = 5.0V, f = 1MHz1+25o C-10pF1+125o C, -55o C-10pFOutput Transition Time TTHL,TTLHVCC = 4.5V1+25o C-15ns1+125o C, -55o C-22nsNOTE:1.The parameters listed in Table 3 are controlled via design or process parameters. Min and Max Limits are guaranteed but not directlytested. These parameters are characterized upon initial design release and upon design changes which affect these characteristics.TABLE 4.DC POST RADIATION ELECTRICAL PERFORMANCE CHARACTERISTICSPARAMETER SYMBOL (NOTES 1, 2)CONDITIONS TEMPERATURE200K RADLIMITSUNITSMIN MAXQuiescent Current ICC VCC = 5.5V, VIN = VCC or GND+25o C-0.750mA Output Current (Sink)IOL VCC = 4.5V, VIN = VCC or GND,VOUT = 0.4V+25o C 4.0-mAOutput Current (Source)IOH VCC = 4.5V, VIN = VCC or GND,VOUT = VCC -0.4V+25o C-4.0-mAOutput Voltage Low VOL VCC = 4.5V and 5.5V, VIH = VCC/2,VIL = 0.8V, IOL = 50µA+25o C-0.1VOutput Voltage High VOH VCC = 4.5V and 5.5V, VIH = VCC/2,VIL = 0.8V, IOH = -50µA +25o C VCC-0.1-VInput Leakage Current IIN VCC = 5.5V, VIN = VCC or GND+25o C-±5µANoise Immunity Functional Test FN VCC = 4.5V, VIH = 2.25V,VIL = 0.8V, (Note 3)+25o C---An to (A>B)OUT TPHL,TPLHVCC = 4.5V+25o C243nsBn to (A>B)OUT TPHL,TPLHVCC = 4.5V+25o C266nsAn, Bn to (A<B)OUT TPHL,TPLHVCC = 4.5V+25o C251nsAn, Bn to (A=B)OUT TPHL,TPLHVCC = 4.5V+25o C250ns(A<B)IN to (A<B)OUT TPHL,TPLHVCC = 4.5V+25o C235ns(A>B)IN to (A>B)OUT TPHL,TPLHVCC = 4.5V+25o C240ns(A=B)IN to (A=B)OUT TPHL,TPLHVCC = 4.5V+25o C237nsNOTES:1.All voltages referenced to device GND.2.AC measurements assume RL = 500Ω, CL = 50pF, Input TR = TF = 3ns, VIL = GND, VIH = 3V.3.For functional tests VO≥4.0V is recognized as a logic “1”, and VO≤ 0.5V is recognized as a logic “0”.TABLE 5.BURN-IN AND OPERATING LIFE TEST, DELTA PARAMETERS (+25o C)PARAMETERGROUP BSUBGROUP DELTA LIMITICC512µAIOL/IOH5-15% of 0 HourTABLE 6.APPLICABLE SUBGROUPSCONFORMANCE GROUPS METHOD GROUP A SUBGROUPS READ AND RECORD Initial Test (Preburn-In)100%/50041, 7, 9ICC, IOL/HInterim Test I (Postburn-In)100%/50041, 7, 9ICC, IOL/HInterim Test II (Postburn-In)100%/50041, 7, 9ICC, IOL/HPDA100%/50041, 7, 9, DeltasInterim Test III (Postburn-In)100%/50041, 7, 9PDA100%/50041, 7, 9, DeltasFinal Test100%/50042, 3, 8A, 8B, 10, 11Group A (Note 1)Sample/50051, 2, 3, 7, 8A, 8B, 9, 10, 11Group B Subgroup B-5Sample/50051, 2, 3, 7, 8A, 8B, 9, 10, 11, Deltas Subgroups 1, 2, 3, 9, 10, 11,(Note 2)Subgroup B-6Sample/50051, 7, 9Group D Sample/50051, 7, 9NOTES:1.Alternate Group A testing in accordance with Method 5005 of MIL-STD-883 may be exercised.2.Table 5 parameters only.TABLE 7.TOTAL DOSE IRRADIATIONCONFORMANCEGROUPS METHODTEST READ AND RECORDPRE RAD POST RAD PRE RAD POST RADGroup E Subgroup 250051, 7, 9Table 41, 9Table 4 (Note 1) NOTE:1.Except FN test which will be performed 100% Go/No-Go.TABLE 8.STATIC AND DYNAMIC BURN-IN TEST CONNECTIONSOPEN GROUND1/2 VCC = 3V± 0.5V VCC = 6V± 0.5VOSCILLATOR50kHz25kHzSTATIC BURN-IN I TEST CONNECTIONS (Note 1)5, 6, 7 1 - 4, 8 - 15-16--STATIC BURN-IN II TEST CONNECTIONS (Note 1)5, 6, 78- 1 - 4, 9 - 16--DYNAMIC BURN-IN TEST CONDITIONS (Note 2)-1, 8, 10, 11, 135, 6, 72, 3, 4, 1612, 159, 14 NOTES:1.Each pin except VCC and GND will have a resistor of 10KΩ± 5% for static burn-in.2.Each pin except VCC and GND will have a resistor of 1KΩ± 5% for dynamic burn-in.TABLE 9.IRRADIATION TEST CONNECTIONSOPEN GROUND VCC = 5V± 0.5V5, 6, 7,8 1 - 4, 9 - 16NOTE:Each pin except VCC and GND will have a resistor of 47KΩ± 5% for irradiation testing.Group E, Subgroup 2, sample size is 4 dice/wafer 0 failures.Intersil Space Level Product Flow - ‘MS’Wafer Lot Acceptance (All Lots) Method 5007(Includes SEM)GAMMA Radiation Verification (Each Wafer) Method 1019,4 Samples/Wafer, 0 Rejects100% Nondestructive Bond Pull, Method 2023Sample - Wire Bond Pull Monitor, Method 2011Sample - Die Shear Monitor, Method 2019 or 2027100% Internal Visual Inspection, Method 2010, Condition A 100% Temperature Cycle, Method 1010, Condition C,10 Cycles100% Constant Acceleration, Method 2001, Condition per Method 5004100% PIND, Method 2020, Condition A100% External Visual100% Serialization100% Initial Electrical Test (T0)100% Static Burn-In 1, Condition A or B, 24 hrs. min., +125o C min., Method 1015100% Interim Electrical Test 1 (T1)100% Delta Calculation (T0-T1)100% Static Burn-In 2, Condition A or B, 24 hrs. min., +125o C min., Method 1015100% Interim Electrical Test 2 (T2)100% Delta Calculation (T0-T2)100% PDA 1, Method 5004 (Notes 1and 2)100% Dynamic Burn-In, Condition D, 240 hrs., +125o C or Equivalent, Method 1015100% Interim Electrical Test 3 (T3)100% Delta Calculation (T0-T3)100% PDA 2, Method 5004 (Note 2)100% Final Electrical Test100% Fine/Gross Leak, Method 1014100% Radiographic, Method 2012 (Note 3)100% External Visual, Method 2009Sample - Group A, Method 5005 (Note 4)100% Data Package Generation (Note 5)NOTES:1.Failures from Interim electrical test 1 and 2 are combined for determining PDA 1.2.Failures from subgroup 1, 7, 9 and deltas are used for calculating PDA. The maximum allowable PDA = 5% with no more than 3% of thefailures from subgroup 7.3.Radiographic (X-Ray) inspection may be performed at any point after serialization as allowed by Method 5004.4.Alternate Group A testing may be performed as allowed by MIL-STD-883, Method 5005.5.Data Package Contents:•Cover Sheet (Intersil Name and/or Logo, P.O. Number, Customer Part Number, Lot Date Code, Intersil Part Number, Lot Number, Quan-tity).•Wafer Lot Acceptance Report (Method 5007). Includes reproductions of SEM photos with percent of step coverage.•GAMMA Radiation Report. Contains Cover page, disposition, Rad Dose, Lot Number, T est Package used, Specification Numbers, T est equipment, etc. Radiation Read and Record data on file at Intersil.•X-Ray report and film. Includes penetrometer measurements.•Screening, Electrical, and Group A attributes (Screening attributes begin after package seal).•Lot Serial Number Sheet (Good units serial number and lot number).•Variables Data (All Delta operations). Data is identified by serial number. Data header includes lot number and date of test.•The Certificate of Conformance is a part of the shipping invoice and is not part of the Data Book. The Certificate of Conformance is signed by an authorized Quality Representative.AC Timing DiagramsAC VOLTAGE LEVELSPARAMETER HCTS UNITS VCC 4.50V VIH 3.00V VS 1.30V VIL 0V GNDVVSINPUTOUTPUTOUTPUTTTHL80%20%80%20%VIHVILVOHVOLVOHVOLTPLHTPHLVSTTLHAC Load CircuitDUTTEST CLRLPOINTCL = 50pF RL = 500ΩDie CharacteristicsDIE DIMENSIONS:100 x 100 milsMETALLIZATION:Type: SiAlMetal Thickness: 11k ű1k ÅGLASSIVATION:Type: SiO 2Thickness: 13k ű 2.6k ÅWORST CASE CURRENT DENSITY:<2.0 x 105A/cm 2BOND PAD SIZE:100µm x 100µm 4 mils x 4 milsMetallization Mask LayoutHCTS85MSB3(1)(A<B)IN (2)(A=B)IN(3)(A>B)IN(4)(A<B)OUT(5)(A=B)OUT(6)(A>B)OUT (7)GND (8)B0(9)A0(10)(11) B1(12) A1(13) A2(14) B2VCC (16)A3(15)All Intersil semiconductor products are manufactured, assembled and tested under ISO9000 quality systems certification. Intersil products are sold by description only. Intersil Corporation reserves the right to make changes in circuit design and/or specifications at any time without notice. Accordingly, the reader is cautioned to verify that data sheets are current before placing orders. Information furnished by Intersil is believed to be accurate and reliable. However, no responsibility is assumed by Intersil or its subsidiaries for its use; nor for any infringements of patents or other rights of third parties which may result from its use. No license is granted by implication or otherwise under any patent or patent rights of Intersil or its subsidiaries.For information regarding Intersil Corporation and its products, see web site Sales Office HeadquartersNORTH AMERICAIntersil CorporationP. O. Box 883, Mail Stop 53-204 Melbourne, FL32902TEL:(407) 724-7000FAX: (407) 724-7240EUROPEIntersil SAMercure Center100, Rue de la Fusee1130 Brussels, BelgiumTEL: (32) 2.724.2111FAX: (32) 2.724.22.05ASIAIntersil (Taiwan) Ltd.Taiwan Limited7F-6, No. 101 Fu Hsing North RoadTaipei, TaiwanRepublic of ChinaTEL: (886) 2 2716 9310FAX: (886) 2 2715 3029。