IMD模具探讨
IMD 概念优缺点

IMD概念及优缺点应用领域(一)、概念IMD是In Mold Decoration英文的首写字母缩写,是指模内装饰镶嵌注塑技术。
是一门较新的表面装饰技术。
从20世纪90年代初开始,由双层胶片层间黏结结构,发展到注塑成型多元结构的三维成型技术,现在已成为当前的一项热门的铭牌工艺,它已一改平面面板的刻板模式,发展到由薄膜与印刷图文、标识的油墨及树脂注塑结合成三位一体面板的新模式。
IMD就是将已印刷成型好的装饰片材放入注塑模内,然后将树脂注射在成型片材的背面,使树脂与片材接合成一体固化成型的技术。
IMD是在注射成型的同时进行镶件加饰的技术,产品是和装饰承印材覆合成为一体,对立体状的成形品全体可进行加饰印刷,使产品达到装饰性与功能性于一身的效果。
由于面板图文、标识置于薄膜与注塑成型的树脂之间,图文、标识不会因摩擦或时间关系而磨损。
它以注塑成型为依托,其形状、尺寸可保持稳定,更便于装配。
故IMD技术常被应用于汽车仪表盘、通讯、电子、电器、仪表、仪器的面板上及家电产品的装饰及功能控制面板、空调面板、手机外壳/镜片、洗衣机、冰箱。
(二)、IMD产品特征※精美的装饰图文、标识内藏,不受摩擦或化学腐蚀而消失。
※图文、标识及颜色设计可随时改变,而无需更换模具。
※三维立体形状产品的,印刷精度准确,误差+0.05mm。
※能提供图文、标识背透光性及高透光性的视窗效果。
※功能按键凸泡均匀、手感好,寿命可达100万次以上。
※三维变化,可增加设计者对产品设计的自由度。
※复合成型加工达到无缝效果。
(三)、IMD/IML客户对象及应用领域家电业:电饭煲、洗衣机、微波炉、空调器、电冰箱等的控制装饰面板;电子业:MP3、MP4、计算器、VCD、DVD、电子记事本、数码相机等装饰面壳、彩壳及标牌;汽车业:仪表盘、空调面板、内饰件、车灯外壳、标志等;电脑业:键盘、鼠标、面壳;通讯业:手机按键、手机镜片、手机彩壳、小灵通及固定电话面板、视窗镜片;其它业:医疗器械、化妆品盒、装饰盒、玩具、运动和娱乐休闲用品等等。
模具培训IMD_工艺说明
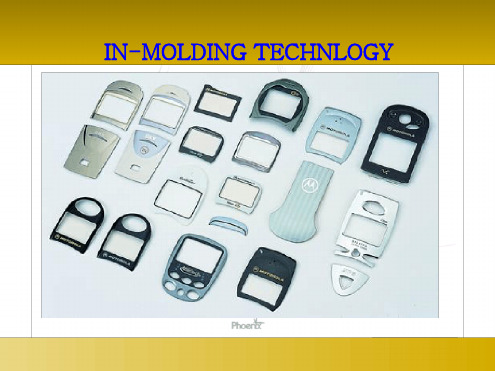
实际生产中,含有铝蒸镀的产品 最多只能印 6色
2.印刷原理
压 槽 PET 胶片原材
knife
? 印刷顺序
① 滚筒浸入印刷槽→
② 不需要部分祛除
→
③ 在凹孔内的油墨转移到胶片上 → ④ 干燥→ ⑤ Al蒸镀
滚筒
⑥ 脱离
cell 油墨槽
* 滚筒: 铝板上覆上铜膜构成凹孔 - 凹孔尺寸 :0.120? - 凹孔的间隙 : 0.020㎜ - 凹孔的深度 : 0.015~0.020 ㎜
模具 型闭
6.树脂基材
1.树脂基材的种类:PMMA( 耐热/耐冲击材料),ABS,PC
? IMD vs 一般注塑
1. IMD 与一般模具的差异
?????
????
?????
?????
Gate,eject pin
Gate
?????
e/pin
IMD ?????
???????
2. IMD vs IML
项目
模具
IMD(inmol decoration)
* half parting 半分型构造 * 制作周期- 25天 * 特殊事项:需要胶片吸附装置
* 胶片数量 --- 4 ~ 6K (250m × 1 roll)
* 与量产胶片的差异;没有UV层.
2) 量产胶片
* 评判用黑白片制作的产品(同一shot) → 保证量产胶片的制作 * 制作周期 ---需要 35 ~ 40 天 * 胶片规格 ---根据印刷后 core的尺寸制成 600mm × 1,000m的规格. * 胶片数量 --- 80K ~ 130K * 量产胶片 与模具间有偏心---调整模具的pitch * 胶片种类 --- 透明,一般型,Al蒸镀,半透明和 多种效果复合体
IMD(IMR、IML、INS、IMF)技术分析
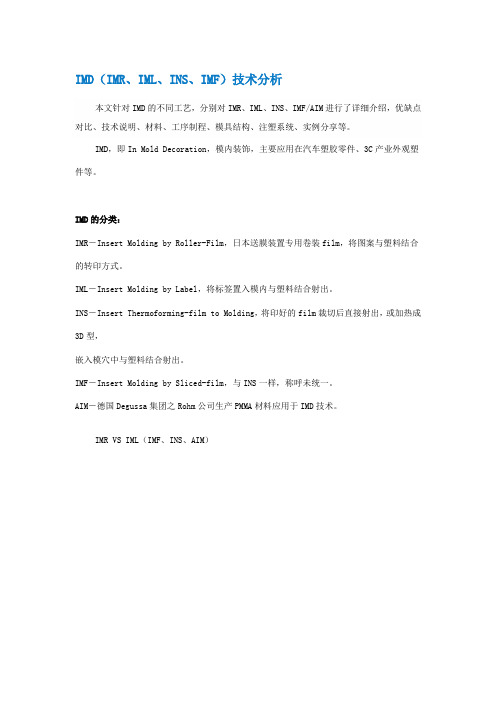
IMD(IMR、IML、INS、IMF)技术分析本文针对IMD的不同工艺,分别对IMR、IML、INS、IMF/AIM进行了详细介绍,优缺点对比、技术说明、材料、工序制程、模具结构、注塑系统、实例分享等。
IMD,即In Mold Decoration,模内装饰,主要应用在汽车塑胶零件、3C产业外观塑件等。
IMD的分类:IMR-Insert Molding by Roller-Film,日本送膜装置专用卷装film,将图案与塑料结合的转印方式。
IML-Insert Molding by Label,将标签置入模内与塑料结合射出。
INS-Insert Thermoforming-film to Molding,将印好的film裁切后直接射出,或加热成3D型,嵌入模穴中与塑料结合射出。
IMF-Insert Molding by Sliced-film,与INS一样,称呼未统一。
AIM-德国Degussa集团之Rohm公司生产PMMA材料应用于IMD技术。
IMR VS IML(IMF、INS、AIM)IMR技术说明:有鉴于当前一些以多层次加工方法生产的作法不良率高,且无法应付多颜色需求,若采人工操作过程繁杂:射出成型→ 包覆保护层→ 电镀→ 喷漆→ 擦拭→上色(曲印) →拆除保护层→ 黏贴贴附层因此有必要寻求可降低生产成本的新工法。
1. 减少原有生产的流程,降低成本。
2. 减少不良率,降低生产成本。
3. 可更加提升外观质感的工法。
4. 可达到更佳耐候条件的工法。
5. 可达到更佳环保的工法。
IMR箔膜:垫片基材依不同的模具表面曲度及扩张比率,需选择不同的基材以配合IMD工序。
IMR模具结构介绍模具两边均需加热,注塑浇口应在定模边安装IMR注塑系统四个重要注塑系统组件:模内转印箔、转印箔定位器、注塑机边料筒及射嘴、注塑模IMR工序实例光阳工厂logo:耐候测试达1000hr → OK(台湾精业开发企业股份有限公司制造)KYMCO电动代步车METER(台湾精业开发企业股份有限公司制造)KYMCO 豪迈奔腾SR G4 125车系 (喷射ENG + 奈米喷漆)KYMCO 豪迈奔腾SR G4 125车系 (陶缸+ 碟煞+ 奈米喷漆) KYMCO V-LINK 125车系 (陶缸+ 碟煞+ 奈米喷漆)KYMCO EASY 4U 100车系 (陶缸+ 碟煞+ 奈米喷漆)IMR工序国外产品实例CD播放器外壳INS 技术说明: 原本INS 是用来辅助一次成型注塑(IMD),但随着3D 立体面装饰的需求,现今的INS 技术以汽车工业来说深受欧洲大厂的亲赖(双B & AUDI)。
汽车IMDINS工艺介绍及模具问题

原因及分析:1)刀口设计不合理, 造成错位和刮削 2)刀口选用材 料及热处理不当,刀刃易损。
成品切口尺寸不准
原因及分析:1)刀口设计强度不够, 造成移位和偏差。 2)横刀设计 配合不好。3)薄膜定位不足。
模内镶嵌(INS) 注塑模
1
定位圈
2
顶板
3
水口板
4
A板
INS注塑模外观
5
前模底板
6
顶针板
7
方铁
8
后模底板
模内镶嵌(INS) 注塑国产常见问题
INS注塑模有别于普通注塑模,除正常 注塑模需注意的一般性问题外,需特别 关注的问题:
外观面不允许任何缩印
设计好薄膜外挂位置,避免 静电和真空吸附
前模用料必须高抛光耐腐蚀
模内镶嵌(INS) & 模内转印(IMR) 对比
模内镶嵌
分型面
分型面
模内转印(IMR)国产常见问题
原因分析:
水口对应点变色
水口对应点变色是由于温度过高和注塑速度 过快压力太大引起的,在模具方面要注意和 检查以下几点:
1. 水口设计是否造成注塑压力太大?
2. 模具设计是否造成水口附件运水不 足,导致温度过高?
3. 注塑机调节参数是否合理?
模内镶嵌(INS) 原理示意图
模内转印
模内镶嵌(INS) & 模内转印(IMR) 成本对比
产品单价
高 中 低 模内镶嵌 模内转印 水转印
产量
汽车IMD国产瓶颈和技术创新
IMD内饰国产化的瓶颈:
1. 汽车内饰设计水平相对滞后 2. 消费者对IMD内饰认识较少 3. IMD模具开发费用昂贵 4. 产品工序复杂、不良率高 5. 成型技术难度大,以致成本高昂
模内装饰(IMD)的介绍
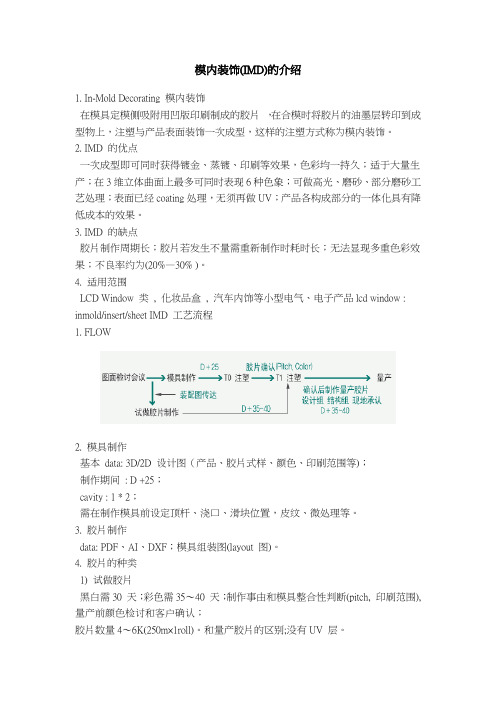
模内装饰(IMD)的介绍1. In-Mold Decorating 模内装饰在模具定模侧吸附用凹版印刷制成的胶片,在合模时将胶片的油墨层转印到成型物上,注塑与产品表面装饰一次成型,这样的注塑方式称为模内装饰。
2. IMD 的优点一次成型即可同时获得镀金、蒸镀、印刷等效果,色彩均一持久;适于大量生产;在3维立体曲面上最多可同时表现6种色象;可做高光、磨砂、部分磨砂工艺处理;表面已经coating处理,无须再做UV;产品各构成部分的一体化具有降低成本的效果。
3. IMD 的缺点胶片制作周期长;胶片若发生不量需重新制作时耗时长;无法显现多重色彩效果;不良率约为(20%—30% )。
4. 适用范围LCD Window 类, 化妆品盒, 汽车内饰等小型电气、电子产品lcd window : inmold/insert/sheet IMD 工艺流程1. FLOW2. 模具制作基本data: 3D/2D 设计图(产品、胶片式样、颜色、印刷范围等);制作期间: D +25;cavity : 1 * 2;需在制作模具前设定顶杆、浇口、滑块位置,皮纹、微处理等。
3. 胶片制作data: PDF、AI、DXF;模具组装图(layout 图)。
4. 胶片的种类1) 试做胶片黑白需30 天;彩色需35~40 天;制作事由和模具整合性判断(pitch, 印刷范围),量产前颜色检讨和客户确认;胶片数量4~6K(250m×1roll)。
和量产胶片的区别;没有UV 层。
2) 量产胶片评判用黑白片制作的产品(同一shot) → 保证量产胶片的制作;制作周期--需要35~40;胶片规格--根据印刷后core 的尺寸制成600mm×1,000m 的规格;胶片数量--80K~130K;量产胶片与模具间有间隙--调整模具的pitch;胶片种类---透明,一般型,Al 蒸镀,半透明和多种效果复合体。
IMD技术的几点补充说明首先在概念上有必要说明:IMD包含IML,IMF,IMRIML:IN MOLDING LABEL﹝印刷胶料与塑结合﹞IMF:IN MOLDING FILM﹝与IML相同﹞IMR:IN MOLDING ROLLER﹝重点在于胶料上的离型层。
浅谈IMD成型技术
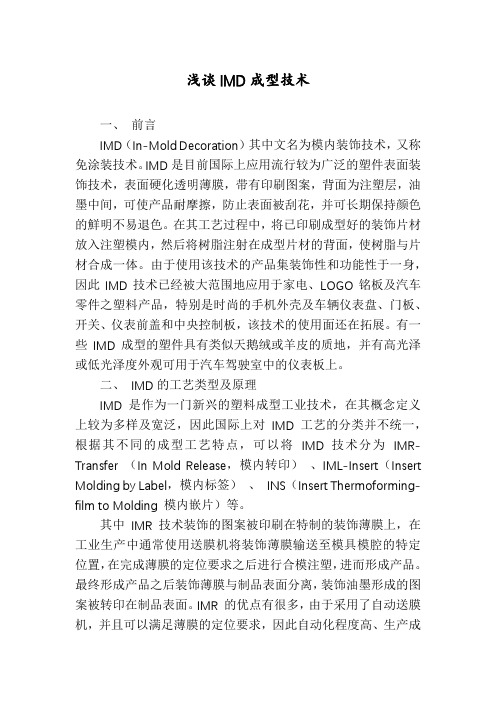
浅谈IMD成型技术一、前言IMD(In-Mold Decoration)其中文名为模内装饰技术,又称免涂装技术。
IMD是目前国际上应用流行较为广泛的塑件表面装饰技术,表面硬化透明薄膜,带有印刷图案,背面为注塑层,油墨中间,可使产品耐摩擦,防止表面被刮花,并可长期保持颜色的鮮明不易退色。
在其工艺过程中,将已印刷成型好的装饰片材放入注塑模内,然后将树脂注射在成型片材的背面,使树脂与片材合成一体。
由于使用该技术的产品集装饰性和功能性于一身,因此IMD技术已经被大范围地应用于家电、LOGO铭板及汽车零件之塑料产品,特别是时尚的手机外壳及车辆仪表盘、门板、开关、仪表前盖和中央控制板,该技术的使用面还在拓展。
有一些IMD成型的塑件具有类似天鹅绒或羊皮的质地,并有高光泽或低光泽度外观可用于汽车驾驶室中的仪表板上。
二、IMD的工艺类型及原理IMD 是作为一门新兴的塑料成型工业技术,在其概念定义上较为多样及宽泛,因此国际上对IMD 工艺的分类并不统一,根据其不同的成型工艺特点,可以将IMD 技术分为IMR-Transfer (In Mold Release,模内转印)、IML-Insert(Insert Molding by Label,模内标签)、INS(Insert Thermoforming-film to Molding 模内嵌片)等。
其中IMR技术装饰的图案被印刷在特制的装饰薄膜上,在工业生产中通常使用送膜机将装饰薄膜输送至模具模腔的特定位置,在完成薄膜的定位要求之后进行合模注塑,进而形成产品。
最终形成产品之后装饰薄膜与制品表面分离,装饰油墨形成的图案被转印在制品表面。
IMR 的优点有很多,由于采用了自动送膜机,并且可以满足薄膜的定位要求,因此自动化程度高、生产成本较低。
同时,IMR 的缺点在于成型之后,薄膜与油墨图案分离,印刷的图案暴露在外界环境之下,容易被磨损。
而IML 工艺非常显著的特点是成型完成后,装饰薄膜与产品表面不分离,而是结合为一体。
imd工艺技术

imd工艺技术IMD(In-Mold Decoration)工艺技术是一种在注塑成型过程中直接在产品表面贴合高分辨率图案的技术。
IMD技术的出现,使得产品外观设计更加丰富多样,并且具有耐磨、耐酸碱、抗腐蚀等优点,因此在电子产品、汽车配件、家电等行业得到广泛应用。
IMD技术的基本原理是先将图案印刷在特殊的塑料膜上,然后将其与注塑材料一起放入注塑机进行成型。
在注塑成型过程中,热塑性树脂将被熔化,并填充到模具中,同时将已印刷的塑料膜沿着模具表面的纹路与热塑性树脂结合在一起。
当塑料冷却固化后,即可得到具有图案贴膜的注塑产品。
IMD工艺技术的关键步骤包括图案设计、膜印刷、膜成型、注塑成型等。
IMD工艺技术的最大优点之一是能够实现较高的图案分辨率和色彩鲜艳度。
IMD膜印刷的图案可以达到300dpi,色彩鲜艳、逼真,使得产品的外观更加具有视觉冲击力。
此外,IMD 技术还具有良好的耐磨性和耐候性,能够经受日常使用中的刮擦、摩擦等物理磨损,同时也能够抵御紫外线、酸碱等化学腐蚀。
IMD工艺技术的应用广泛。
在电子产品行业,IMD技术可以用于手机壳、平板电脑背板、电视遥控器等产品的表面装饰,使其外观更加时尚美观;在汽车配件行业,IMD技术可以用于车内中控面板、方向盘、车门装饰板等部件的制造,提升汽车的内饰品质;在家电行业,IMD技术可以应用于空调面板、洗衣机盖板、冰箱门板等产品的加工,增加产品的美观度和耐用性。
IMD工艺技术虽然具有较高的成本,但其提供的功能和外观加工效果值得投入。
IMD技术不仅可以实现产品的个性化定制,满足消费者对于美观和质感的需求,还可以提升企业产品的市场竞争力。
随着科技的不断进步和消费者对产品外观的要求不断提高,IMD工艺技术将会得到更广泛的应用和推广,为产品设计和制造带来更多可能性。
IMD模具设计及成型要点_1

IMD模具设计及成型要点1、模具缩水率问题一般ABS、PMMA的缩水为0.5%,如做IMD模具,因产品表面要掩盖一层PET薄膜,明显两者的热收缩率不同。
2、片材问题片材是IMD模具成败的关键;也是最为简单的问题。
下面分几项进行分析:a、材质、油墨一般片材的材质为PET,也有PC、PMMA的片材。
但PET的成型及加工都较优良。
表面光泽度、耐磨性也达到客户要求,因此被广泛应用材质。
厚0.125mm的PET片材为最热卖的片材之一。
油墨,为印刷的原料,要求耐磨、耐高温、调配、丝印作业便利。
b、预制片材(裁剪、热成型)c、片材与型腔的协作片材尺寸要比最终的部件尺寸小一点点。
最重要的原则!!!一般状况下,建议:片材的尺寸要比部件尺寸单边小0.02至0.03mm这样,片材置入型腔内是才简单,才能完全伸绽开来。
如有褶皱,啤出来的成品就会不良。
3、片材成型模具设计要点a、使用产品图,在Pro/e(或其他3D软件)按片材厚度,将产品表面对内偏置,得到片材的3D图。
最麻烦的工作!b、按片材的3D图,将其绽开,作冲裁片材的刀模、菲林等。
c、按片材3D图分模d、制造模具4、成型模具设计要点因要将片材放到型腔内注塑,所以,在设计上与一般通模具有不同的地方。
下面就其特点进行分析:a、浇口不得采纳分型面直接进胶的方式!缘由:在分型面处一般都有片材,直接进胶将会把片材冲开,啤出的成品在浇口四周会有气纹,片材被冲起皱,丝印的图案亦会被冲开一个口子!一般要采纳顶针潜水入胶的方式,或牛角潜水入胶(后模需做两镶件,各打牛角的半边胶位)b、分型面及碰穿面的要求分型面不得像一般模具一样直接从胶位边顺延拉出,肯定到向下拉出3---5mm(要做3度以上的脱模角)再顺延作分型面。
这样,前后模的分型面就是擦穿面!c、片材在啤塑时的定位主要靠自动装置、定位销、真空孔等。
如采纳红外线掌握等。
目前,国际上开发有IMD片材定位的新技术:静电荷。
即利用静电荷把片材牢牢地吸附在型腔内。
IMD 概念优缺点(完整资料).doc

【最新整理,下载后即可编辑】IMD概念及优缺点应用领域(一)、概念IMD是In Mold Decoration英文的首写字母缩写,是指模内装饰镶嵌注塑技术。
是一门较新的表面装饰技术。
从20世纪90年代初开始,由双层胶片层间黏结结构,发展到注塑成型多元结构的三维成型技术,现在已成为当前的一项热门的铭牌工艺,它已一改平面面板的刻板模式,发展到由薄膜与印刷图文、标识的油墨及树脂注塑结合成三位一体面板的新模式。
IMD就是将已印刷成型好的装饰片材放入注塑模内,然后将树脂注射在成型片材的背面,使树脂与片材接合成一体固化成型的技术。
IMD是在注射成型的同时进行镶件加饰的技术,产品是和装饰承印材覆合成为一体,对立体状的成形品全体可进行加饰印刷,使产品达到装饰性与功能性于一身的效果。
由于面板图文、标识置于薄膜与注塑成型的树脂之间,图文、标识不会因摩擦或时间关系而磨损。
它以注塑成型为依托,其形状、尺寸可保持稳定,更便于装配。
故IMD技术常被应用于汽车仪表盘、通讯、电子、电器、仪表、仪器的面板上及家电产品的装饰及功能控制面板、空调面板、手机外壳/镜片、洗衣机、冰箱。
(二)、IMD产品特征※精美的装饰图文、标识内藏,不受摩擦或化学腐蚀而消失。
※图文、标识及颜色设计可随时改变,而无需更换模具。
※三维立体形状产品的,印刷精度准确,误差+0.05mm。
※能提供图文、标识背透光性及高透光性的视窗效果。
※功能按键凸泡均匀、手感好,寿命可达100万次以上。
※三维变化,可增加设计者对产品设计的自由度。
※复合成型加工达到无缝效果。
(三)、IMD/IML客户对象及应用领域家电业:电饭煲、洗衣机、微波炉、空调器、电冰箱等的控制装饰面板;电子业:MP3、MP4、计算器、VCD、DVD、电子记事本、数码相机等装饰面壳、彩壳及标牌;汽车业:仪表盘、空调面板、内饰件、车灯外壳、标志等;电脑业:键盘、鼠标、面壳;通讯业:手机按键、手机镜片、手机彩壳、小灵通及固定电话面板、视窗镜片;其它业:医疗器械、化妆品盒、装饰盒、玩具、运动和娱乐休闲用品等等。
模内装饰技术-IMD
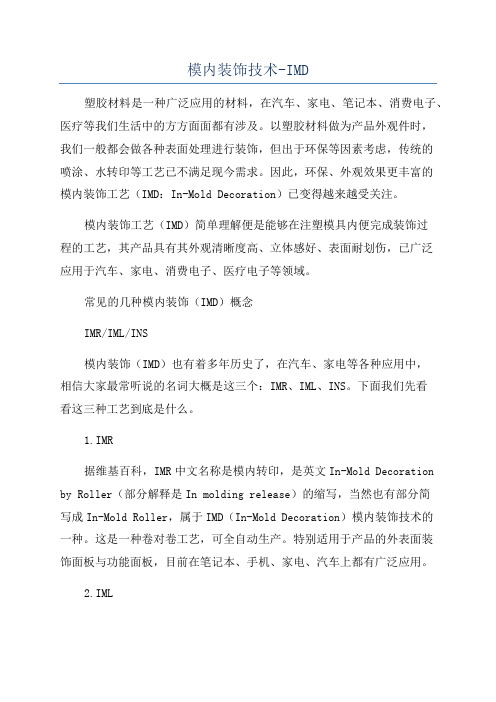
模内装饰技术-IMD塑胶材料是一种广泛应用的材料,在汽车、家电、笔记本、消费电子、医疗等我们生活中的方方面面都有涉及。
以塑胶材料做为产品外观件时,我们一般都会做各种表面处理进行装饰,但出于环保等因素考虑,传统的喷涂、水转印等工艺已不满足现今需求。
因此,环保、外观效果更丰富的模内装饰工艺(IMD:In-Mold Decoration)已变得越来越受关注。
模内装饰工艺(IMD)简单理解便是能够在注塑模具内便完成装饰过程的工艺,其产品具有其外观清晰度高、立体感好、表面耐划伤,已广泛应用于汽车、家电、消费电子、医疗电子等领域。
常见的几种模内装饰(IMD)概念IMR/IML/INS模内装饰(IMD)也有着多年历史了,在汽车、家电等各种应用中,相信大家最常听说的名词大概是这三个:IMR、IML、INS。
下面我们先看看这三种工艺到底是什么。
1.IMR据维基百科,IMR中文名称是模内转印,是英文In-Mold Decoration by Roller(部分解释是In molding release)的缩写,当然也有部分简写成In-Mold Roller,属于IMD(In-Mold Decoration)模内装饰技术的一种。
这是一种卷对卷工艺,可全自动生产。
特别适用于产品的外表面装饰面板与功能面板,目前在笔记本、手机、家电、汽车上都有广泛应用。
2.IMLIML英文是In-Mold Label (部分作In molding Lamination),一般叫法是模内镶件注塑、模内贴标等。
(拉伸程度较低) ,有用过手机,目前这一技术在家电、汽车、医疗电子等行业已广泛应用。
比如常见的空调、洗衣机IMD控制面板,扫地机器人面盖,汽车一体显示盖板、中控面板等。
膜片模内镶件注塑工艺非常显著的特点是:表面是一层硬化的透明薄膜,中间是印刷图案层,背面是塑胶层,由于油墨夹在中间,可使产品防止表面被刮花和耐磨擦,并可长期保持颜色的鲜明不易退色。
IMD中冲切模模具设计

IMD中冲切模模具设计冲切模是模内装饰成形技术的重要组成部分。
文章介绍了冲切模的工艺成形原理,阐述了该类模具设计的基本原理、设计流程,总结了产品在制造和生产过程中常见的问题及处理措施,以及设计过程中的一些注意事项。
对模具设计者具有一定的指导意义。
标签:冲切模;设计;原因;措施引言IMD(In Mold Decoration)中文名叫模内装饰技术,是目前市面上流行的一种表面装饰技术,其表面是硬化透明薄膜,中间是印刷图案层,最后在背面有注塑层,油墨位于中间,这样产品表面不易被刮花,同时可以有效增加产品的耐磨性,并可长期保持油墨的鲜明颜色而不易退色。
其产品集装饰性、功能性于一身,在家用电器、电子产品、汽车内饰等行业得到过广泛应用。
IMD生产的主要工艺流程[1、2]:PC片背面印刷油墨→干燥→高压成型→剪切废边→注塑→后处理。
冲切模主要用于在PC片材高压成形后,将片材上多余的废边切除掉,以形成最终IMD产品的外观形状。
有了片材的保护,注塑成形后的产品外观面能长时间保持鲜艳的图案[3、4]。
1 冲切模成型原理IMD冲切成型原理(如图1所示为模具闭合状态):当模具的上、下模板安装在冲切机上,在冲切机作用力下将模具打开,将高压成形好的片材放入凸、凹模之间的刀口区,上模向下运动,在冲切凸模和冲切凹模共同作用下将片材按照要求進行切断,从而为最后的注塑成形提供带有装饰作用的片材。
2 模具设计流程及原理2.1 收缩率的确定由于冲切后的片材需要放入模腔中进行注塑成型,所以冲切模具的成型部分制作大小需要与塑料模的模腔保持一致,因此:冲切模收缩率=注塑模收缩率。
2.2 刀口设计原理在冲切模具结构中,常见的冲切模结构有两种,一种是平面类片材冲切,一种是成形类3D冲切,两种模具结构设计简单介绍如下。
平面类片材冲切:此类片材产品都是平面的,凸模与片材接触面为平面,如图2所示的模具闭模状态图。
此类模具加工简单,其工作原理为:在冲切机力的作用下,上板1往下运动,当压料板和片材5以及带有斜度便于落料的下刀口6面贴合后,压料板4压缩弹簧2,上刀口3相对下行,最终在上、下刀口的作用力下将片材分离。
模内装潢(IMD)

模内装潢(IMD)大多数塑料制品装潢的过程首先是涂漆,然後在下一工序印刷或使用标签、转印等工艺。
现时,一种较新及实用的装潢方法是模内装潢(IMD),将预印的薄膜放在模具内直接与塑料注塑一塑成型。
以往一般的塑料制品均会使用热转印工艺作为装潢用途。
热转印的基本原理是通过加热加压把预先印在转印膜的装潢图样转印到产品上。
热转印工艺可把千变万化的图案一次性的贴附在塑体上,使产品外观得到装潢效果。
但传统的热转印工艺会受到产品形状,材料等一定程度的限制。
模内转印因应市场的需要而出现。
模内转印顾名思义是在模具内进行热转印的工艺。
此工艺主要是利用熔胶注塑到模具时的热量,和锁模的高压,把预先印好在转印膜的图样转印在成型的产品上,令注塑成型後的产品在注塑时同一时间一次性得到装潢。
模内转印打破传统热转印的局限,使设计复杂的产品装饰更多样化。
如德国库尔兹模内转印膜可印上多达九个颜色,更可配合电镀效果,这是热转印做不到的。
模内转印目前被广泛应用在不同类型的注塑产品上,如汽车内装饰、标牌、手机镜片、影音产品、钟錶、开关面板等。
模内转印膜,除了一个一个独立设计的图样外,也有一些是用上了连续的花样,如木纹设计,金属拉丝及碳铅图案等。
另外,模内转印膜也可配合全息图应用,增强产品防伪效果。
模内转印除了可在注塑时为产品提供装潢外,更可在装饰表面附加保护作用,从而提高产品的抗磨和耐化学侵蚀的性能;也能满足不同环境的要求。
例如:与我们生活息息相关的手机镜片或一些转动性电子产品上(如运动手錶),其镜片就是充分利用了模内转印工艺的保护膜,以提高产品的耐用性。
目前模内转印工艺也被应用在一些装饰品的生产过程中,如标牌,甚至人造宝石。
模内转印工艺的应用,使得产品设计师拥有了更广阔的创作空间,在产品装潢方面也具有更多的灵活性。
目前,在国外有一些模内转印的最新应用,不单令塑料产品在外观上像金属,更可利用背光,作指示灯的显示。
这种工艺可配合模具设计,把模具表面纹理效果转移到注塑产品上,如各种粗细纹理、拉丝效果等。
IMD模具总结

IMD技术是替代塑胶制品喷漆、电镀加工最好的新工艺,减少注塑的后 续加工工序,在塑胶工业上推广、普及,能真正实现节能、环保的意义,将 为社会及企业带来巨大的经济效益和环保效益。
IMD是产品的表面装饰技术,也就是将印刷好的薄膜成型后,镶嵌在注塑 模腔内然后合模注塑。注塑树脂在薄膜的背面与油墨层相结合,面板图文、 标识置于薄膜与注塑成型的树脂之间,图文、标识不会因摩擦或时间关系而 磨损。主要应用于家电产品的表面装饰及功能性面板常用在手机视窗镜片及 外壳、洗衣机控制面板、冰箱控制面板、空调控制面板、汽车仪表盘、电饭 煲控制面板多种领域的面板、标志等外观件上。
INJELIC
3. 电荧光IMD
EL( Electroluminescence)+ IMD: 可以作出任何形状的发光图案
INJELIC
3. 浇口不能直冲分型面
在分型面处一般都有膜片,直接进胶将会把膜片冲开,打出的产品品在浇口四周会有气纹,片材 被冲起皱。
一般要采用扁顶潜水入胶的方式,或牛角潜水入胶。 我司以往经验是采用倒装模具设计。
INJELIC
4. 需在无尘车间
IMD对前模要求抛镜面,抛光号一般3000以上。 前模或后模有异物(铁屑、灰尘等),会体现在产品上,造成凹凸不平,造成产品不合格。 注:我司产品不合格率70-80%都是此原因。
下部滚轮,使用完的膜 片收集在此轮上。
INJELIC
三、IMD设计注意问题点
1. 产品要求
(1)产品高度差不能太大 (2)产品装饰面只能到分型面 (3)产品装饰面不能有尖角 (4)产品表面是连续表面
IMD-IML的工艺特性区别详细分析

IMD/IML的工艺特点区别详细分析IML工艺 IML的中文名称:模内镶件注塑 其工艺非常显著的特点是:表面是一层硬化的透明薄膜,中间是印刷图案层,背面是塑胶层,由于油墨夹在中间,可使产品防止表面被刮花和耐摩擦,并可长期保持颜色的鲜明不易退色。
IML工艺介绍 摘要: 本文主要介绍IML成型的原理及工艺,并对IML和IMD工艺作了对比分析,总结出IML工艺的优缺点。
资料来自网上收集整理而成,供大家参考 关键词: IML IMD 成型工艺 一.IML的概念 IMD(In-Mold Decoration)是一种在注塑模具内放置Film薄膜来装饰塑胶外观表面的新技术。
目前IMD有两种制造方法,一种是把印刷好的Film薄膜制作成循环滚筒卷状带,安装到注塑机和注塑模具内,象标签Label贴到前模面上全自动地循环带移动式的生产出来;即人称之为IMD(在模具内转印注塑)。
另一种是把Film薄膜印刷好经过成型机Forming成型,再经过剪切后放置到注塑模具内生产出来的。
即称之为IML(在模具内贴膜注塑)。
此Film一般可分为三层:基材(一般是PET)、油墨层(INK)、胶合材料(多为一种特殊的粘合胶)。
当注塑完成后,通过粘合胶作用使Film和塑胶紧密结合融为一体,由于本身正表面覆耐磨保护膜的PET在最外层,有耐磨和耐刮伤的作用,其表面硬度可达到3H,而且会越摸越亮。
其中注塑材料多为PC、PMMA、PBT等等。
如下图: 二、IML的工艺工序 裁料---平面印刷---油墨干燥固定---贴保护膜---冲定位孔---热成型---剪切外围形状---材料注塑成型工艺流程如下图:具体说明如下:1)裁料:把卷状的薄膜Film裁剪成已设计好尺寸的方形块,供印刷、成型工序用。
2)平面印刷:根据要求的图标、文字制造成菲林网,在裁剪好的薄膜Film方形块上印刷图标、文字。
3)油墨干燥固定:把印刷好的薄膜Film方形放置在高温烤炉里干燥,目的是固定IML 油墨。
IML模具设计的考量问题点

IML模具设计的考量问题点注塑成型模具IMD注塑成型模与一般塑料成型模具设计不同,必须在一般模具的基础上再注考虑下面几个问题点:1、P/L面:对于IMD注塑成型模具来说,P/L面一定不能低于FILM包复水平面,为排气稳定,建议比Film 包复小平高0.05~0.1mm2.排气系统:因为片材包复,固IMD模具排气要比一般模具排气更流畅。
模仁尽量以多个镶件拼起来,利用镶件与镶件组装时间隙排气,镶件底部尽量搂空。
3.胶口IMD注塑模具大部份都采用潜伏式进胶方式,在胶口设计时要考虑几个要点:(1). 进胶平衡(2). 应力适放(3). 缓冲4.注射模具温度注射模具温度(Tin)的确定,需要考虑以下几个因素:因素1,注射树脂:• PC: 90-100°C• PC/ABS: 85-95 °C• PMMA: 70-80 °C因素2,油墨:冲油墨温度 55-75 °C• 油墨供应商:彩皇 > 宝龙• 注射口的设计:• 油墨印刷层数• 制件尺寸:大制件更容易冲墨.• 建议的模温(Tin)MP3, MP4, 和手机: 65- 70 °C笔记本电脑: 55-65 ° C5. 缩水率• 注射模具尺寸CD)的计算:• CD = (Partdim ± D) + (Partdim ± D) *RS• Partdim: 最终制件的尺寸• RS: 树脂的收缩率, 对于PC和PC/ABS,一般为0.6~1.0%.• D: 制件和制造公差拉伸成型模具• 薄膜收缩率(Sfilm)的确定• 设备: 高压成型机.• 成型温度: Tth• 薄膜收缩率计算公式:Sfilm = (Dfilm,1- Dfilm,2)/Dfilm,2Dfilm,1: 高压后片材在高温下的尺寸,高压成型后立即用尺子测薄膜在高压模具上的大小Dfilm,2: 取下片材冷却24小时的尺寸高压成型模具尺寸 (FD):FD = (FI+TEIM+FI*Sfilm-TEFM) - FT TEIM: 注射模具在注射温度Tin下的热膨胀TEFM: 高压成型模具在成型温度Tth的热膨胀FT: 薄膜的厚度的Sfilm: 薄膜在Tth的收缩率高压后片材的尺寸 (FI) :FI=CD- FI*CTE*(Tin-Trt)- FI*Rdef CTE: 片材的热膨胀系数,8*10-6 m/(m*°C)Tin: 注射模具温度.Rdef : 因树脂流动而导致的薄膜变形率(收缩率为第1mm拉伸0.0015mm)高压成型模具温度(Tth)的确定:• 因素1,薄膜: 110-140 °C• 因素2,油墨粘在模具上: < 125 °C• 建议的高压成型模具温度(Tth):~110°C(薄膜的实测温度)薄膜裁切模具主要考虑二点:一是模具尺寸。
模内转印技术IMD
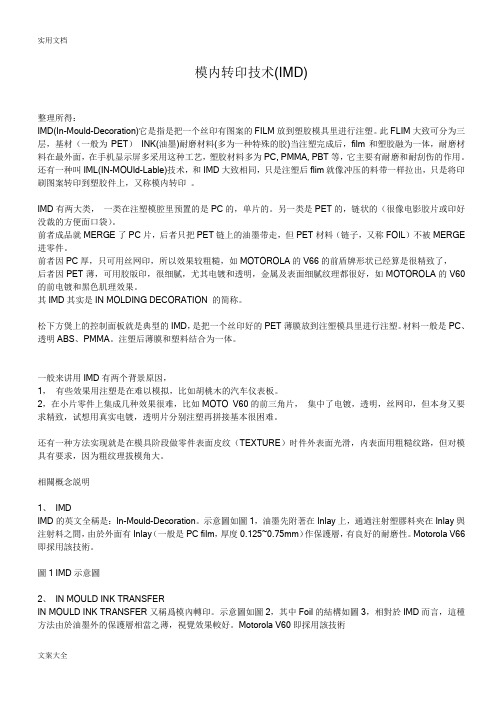
模内转印技术(IMD)整理所得:IMD(In-Mould-Decoration)它是指是把一个丝印有图案的FILM放到塑胶模具里进行注塑。
此FLIM大致可分为三层,基材(一般为PET)INK(油墨)耐磨材料(多为一种特殊的胶)当注塑完成后,film和塑胶融为一体,耐磨材料在最外面,在手机显示屏多采用这种工艺,塑胶材料多为PC, PMMA, PBT等,它主要有耐磨和耐刮伤的作用。
还有一种叫IML(IN-MOUld-Lable)技术,和IMD大致相同,只是注塑后flim就像冲压的料带一样拉出,只是将印刷图案转印到塑胶件上,又称模内转印。
IMD有两大类,一类在注塑模腔里预置的是PC的,单片的。
另一类是PET的,链状的(很像电影胶片或印好没裁的方便面口袋)。
前者成品就MERGE了PC片,后者只把PET链上的油墨带走,但PET材料(链子,又称FOIL)不被MERGE 进零件。
前者因PC厚,只可用丝网印,所以效果较粗糙,如MOTOROLA的V66的前盾牌形状已经算是很精致了,后者因PET薄,可用胶版印,很细腻,尤其电镀和透明,金属及表面细腻纹理都很好,如MOTOROLA的V60的前电镀和黑色肌理效果。
其IMD其实是IN MOLDING DECORATION 的简称。
松下方煲上的控制面板就是典型的IMD,是把一个丝印好的PET薄膜放到注塑模具里进行注塑。
材料一般是PC、透明ABS、PMMA。
注塑后薄膜和塑料结合为一体。
一般来讲用IMD有两个背景原因,1,有些效果用注塑是在难以模拟,比如胡桃木的汽车仪表板。
2,在小片零件上集成几种效果很难,比如MOTO V60的前三角片,集中了电镀,透明,丝网印,但本身又要求精致,试想用真实电镀,透明片分别注塑再拼接基本很困难。
还有一种方法实现就是在模具阶段做零件表面皮纹(TEXTURE)时件外表面光滑,内表面用粗糙纹路,但对模具有要求,因为粗纹理拔模角大。
相關概念説明1、IMDIMD的英文全稱是:In-Mould-Decoration。
- 1、下载文档前请自行甄别文档内容的完整性,平台不提供额外的编辑、内容补充、找答案等附加服务。
- 2、"仅部分预览"的文档,不可在线预览部分如存在完整性等问题,可反馈申请退款(可完整预览的文档不适用该条件!)。
- 3、如文档侵犯您的权益,请联系客服反馈,我们会尽快为您处理(人工客服工作时间:9:00-18:30)。
IMD精密模具经验和探讨IMD&INS模具基本结构原理
模内转印(IMD)模具示意图
模内转印(IMD)模具常见问题
表面起皱褶:是由于在注塑的过程中IMD 薄膜未能正常平滑成型造成的。
其中与模具相关的要注重以下因素:
1. 入水口分布是否合理:数量是否过多或太少,两个水口间距是否太大?
2. 模具表面光洁度是否达到要求?
3. IMD薄膜是否需要预热?
4. 吸附真空度是否达到要求?
5. 模具高度差是否过大?
6. 吸真空设计是否合理,充分?
7. 注塑机调节参数是否合理?
表面脱色:是由于IMD薄膜未能正常覆盖到塑胶件表面或冲膜引起的。
在模具方面要注意和检查以下几点:
1. 水口设计是否合理?有无压力集中导致冲膜现象?
2. 模具表面及零件是否有油污?零件表面镀层是否破损?
3. 前模温度是否太低?
4. 塑胶温度是否过低?
5. 注塑机调节参数是否合理?
6. IMD薄膜是否需要预热?
载体薄膜破损:是模具分型面挤压和注塑冲膜压力过大引起的。
在模具方面要注意和检查以下几点:
1. 水口设计是否合理?有无压力集中导致冲膜现象?
2. 模具分型面间隙是否和IMD薄膜厚度匹配而无挤压现象?
3. 模具设计有无尖角或利角?
4. 薄膜在模具中的通道是否顺畅?
5. 注塑机调节参数是否合理?
6. IMD薄膜是否需要预热?
产品表面及周边变色:是由于薄膜过度拉伸及前模面引起的。
在模具方面要注意和检查以下几点:
1. 模具成型部位高度落差是否太大?
2. 进胶口设计是否太接近边缘?
3. 前模抛光是否到位而且均匀?
4. 侧面及周边拔模斜度是否足够?
5. 注塑机调节参数是否合理?
6. IMD薄膜是否需要预热?
水口对应点变色:是由于温度过高和注塑速度过快压力太大引起的。
在模具方面要注意和检查以下几点:
1. 水口设计是否造成注塑压力太大?
2. 模具设计是否造成水口附件运水不足,导致温度过高?
3. 注塑机调节参数是否合理?
模内镶嵌(INS) 模具示意图
模内镶嵌(INS) 吸塑模
模内镶嵌(INS) 吸塑模常见问题:
吸塑形状不到位:是由于薄膜烘烤不熟及成型真空度或压力不足。
在吸塑模具方面要注意和检查以下几点:
1. 确认吸塑机薄膜烘烤均匀且温度正确?
2. 吸塑模吸气孔设计是否充足(孔距)且孔径正确?
3. 吸气孔位置是否靠近形状节点?
4. 真空度是否达到要求?
5. 正压力是否足够(当采取正向压力时)?
吸塑后薄膜出现皱褶
1. 吸塑模设计应尽量避免尖角。
2. 模具应尽量减少高度差并增加辅助拉伸。
3. 模具设计应考虑适当间距及薄膜变形空间
成型后不易脱模或产生破损
1. 吸塑模设计应充分考虑脱模斜度。
2. 脱模吹出气孔位置必须正确且充足。
3. 尽量避免薄膜过度拉伸。
成型后变色或花纹变形
1.薄膜烘烤温度和时间必须严格按厂家技术要求调节。
2. 尽量避免薄膜过度拉伸。
模内镶嵌(INS) 刀模
模内镶嵌(INS) 刀模常见问题:
冲切时薄膜移位
1)后模定位不足。
2)前模预压紧不合理,受力时产生移动
薄膜切口不平(毛边)
原因及分析:
1)刀口设计不合理,造成错位和刮削
2)刀口选用材料及热处理不当,刀刃易损。
成品切口尺寸不准
原因及分析:
1)刀口设计强度不够,造成移位和偏差。
2)横刀设计配合不好。
3)薄膜定位不足。
模内镶嵌(INS) 注塑模
模内镶嵌(INS) 注塑模常见问题
INS注塑模有别于普通注塑模,除正常注塑模需注意的一般性问题外,需特别关注的问题:
1、外观面不允许任何缩印
2、设计好薄膜外挂位置,避免静电和真空吸附
3、前模用料必须高抛光耐腐蚀
模内镶嵌(INS) & 模内转印(IMD)示意图
IMD & INS 模具国产化的优势
1. 对您产品提供一站式的解决方案
2. 加工快速
3. 面向制造的产品分析与优化建议
4. 多样化的模具设计能力
5. 特殊模具定制开发
6. 内部研发能力
7. 全国范围内的便捷服务
8. 持续的长期技术支持
9. 优良的品质和良好的价格
10. 发展民族工业, 促进产业链形成。