新一代控制轧制和控制冷却技术与创新的热轧过程
棒材轧制中控制轧制和控制冷却的应用

棒材轧制中控制轧制和控制冷却的应用姓名:迟璐全班级:学号:棒材轧制中控制轧制和控制冷却的应用迟璐全材料成型及控制工程12级[摘要]控制轧制(Contorlled Rollign)是在热轧过程中通过对金属加热制度、变形制度和温度制度的合理控制,使热朔性变形与固态相变结合,以获得细小晶粒组织,使钢材具有优异的综合力学性能的轧制新工艺。
控制冷却(controlled Cooling)是控制轧后钢材的冷却速度达到改善钢材组织和性能的目的。
控制轧制和控制冷却相结合能将热轧钢材的两种强化效果相加,进一步提高钢材的强韧性和获得合理的综合力学性能。
并介绍了棒材轧制过程中控制轧制和控制冷却工艺的特点,金属学理论。
分析了控制轧制和控制冷却工艺对热轧棒材的影响,并提出目前需要研究的问题。
[关键词]热轧棒材控制轧制控制冷却ABSTRACT:Controlled rolling is in the process of hot rolled through the metal heating system, reasonable control of the deformation and temperature, and to integrate the thermal plastic deformation and solid-state phase transformation to obtain fine grain structure, make the excellent comprehensive mechanical properties of steel rolling process. Is controlled cooling after controlled rolling steel cooling speed to achieve the purpose of improving the microstructure and mechanical properties of steel. Controlled rolling and controlled cooling could add those two kinds of reinforcement effect of hot rolling steel, further improve the tenacity of steel and have a reasonable comprehensive,mechanical,properties.Anintroductionwasmadetothefeaturesandmetallo graphicaltheoryofrollingcontrolandcoolingcontrolprocessesduringbarrolling.Theeffects oftherollingcontrolandcoolingcontrolprocessesonthehotrolledbarswereanalyzed.Proble mstoberesearchedatpresentwerealsoputforward.KEY WORDS: hotrolledbars rollingcontrol coolingcontrol1.引言控制轧制和控制冷却技术是近十多年来国内外新发展起来的轧钢生产新技术,受到国际冶金界的重视。
控制轧制

控制轧制与控制冷却的概念
控制轧制(Controlled rolling) 在热轧过程中,通过对金属加热制度、变形制度和温度
制度的合理控制,使热塑性变形与固态相变相结合,以获得 细小晶粒组织,从而得到较高的综合性能的轧制工艺。
控制冷却(Controlled cooling) 控制轧后钢材的冷却速度达到改善钢材组织和性能的目
淬火
1、定义: 淬火是将钢加热到AC1或 AC3以上温度并保温,
出炉快速冷却,使奥氏体转变成为马氏体的热处理 工艺。
回火
1、定义:回火是把淬火后的钢件,重新加热到A1以 下某一温度,经保温后空冷至室温的热处理工艺。
2、目的:淬火钢件经回火可以减少或消除淬火应力, 稳定组织,提高钢的塑性和韧性,从而使钢的强度、 硬度和塑性、韧性得到适当配合,以满足不同工件 的性能要求。
载荷P压入被测材料表面,保持一定时间后卸除载荷,测出压 痕直径d,求出压痕面积F计算出平均应力值,以此为布氏硬度 值的计量指标,并用符号HB表示。
标注:D/P/T如120HB/10/3000/10,即表示此硬度值120 在D=10mm,P=3000kgf,T=10秒的条件下得到的。
简单标注:200~230HB
工艺性能:是指制造工艺过程中材料适应 加工的性能。如:铸造性、锻造性、焊接 性、切削加工性、热处理工艺性。
金属材料的性能
一、金属材料的机械性能
机械性能— 是指金属材料在外力作用时表现出来的性能。 外力形式:拉伸、压缩、弯曲、剪切、扭转等。 载荷形式:静载荷、冲击载荷、交变载荷等。
指标:强度、刚度、硬度、塑性、韧性和疲劳强度等。
残余压入深度
来表示
为了与习惯上数值越大硬度越高的概念相一 致采用一常数(k)减去(h3-h1)的差值表示硬 度值。为了简便起见又规定每0.002mm压入深度 作为一个硬度单位(即刻度盘上一小格。)
新一代TMCP技术控轧控冷

新一代TMCP技术
RAL.NEU
RAL
TMCP技术的发展和创新
• TMCP是20世纪最伟大的钢铁技术成果之一 • 开发引领未来社会发展和人类需求的新一代钢 铁材料 • 需要付出巨大的努力,充分利用新的科技成 果,站在巨人的肩膀上进行钢铁生产过程的脱 胎换骨的革命
RAL
TMCP技术的发展和创新
RAL
高速连轧的温度制度-“趁热打铁”
新一代的TMCP采用适宜的正常轧制温度 进行连续大变形,在轧制温度制度上不再坚持 “低温大压下”的原则。与“低温大压下”过程相 比,轧制负荷可大幅度降低,设备条件的限制 可放松。轧机建设不必追求高强化,大幅度降 低建设投资。
RAL
高速连轧的温度制度-“趁热打铁”
适宜的轧制温度,大大提高轧制的可操作 性,避免轧制工艺事故,例如卡钢、堆钢等, 同时也延长了轧辊、导卫等轧制工具的寿命。 提高产量、降低成本 对于一些原来需要在粗轧和精轧之间实施 待温的材料,可以直接轧制
RAL
“趁热打铁”及其优点
由于新一代的TMCP避免了“低温大压下”,使得传统的“趁 热打铁”的思想得以贯彻实行,这对于减轻生产设备负荷、确 保轧制过程稳定、改善加工过程的可操作性、提高材料的可加 工性、降低轧制能耗等具有十分重要的意义。由于可以少加或 者不加微合金元素和合金元素,所以可以节省大量的资源和能 源,实现减量化的轧制,降低钢材生产成本,这对于钢铁工业 的可持续发展和协调发展具有重要的作用。
RAL
TMCP特征
• 低温大压下——轧制负荷、生产率、设备投 资、轧制稳定性 • 微合金化——提高成本、焊接性能恶化、冶炼连铸-轧制工艺复杂、轧制负荷增大 • 水是最廉价的合金元素——高冷却速率的开发 利用、冷却路径的利用、冷却的均匀性
控制轧制及控制冷却技术在型钢生产中的应用

控制轧制及控制冷却技术在型钢生产中的应用一、引言型钢是一种重要的金属材料,在建筑、汽车制造、机械制造等领域具有广泛的应用。
为了提高型钢的质量和性能,控制轧制及控制冷却技术被广泛应用于型钢生产中。
这些技术通过精确控制轧制工艺参数和冷却过程,可以有效提高型钢的强度、塑性和表面质量,满足不同领域对型钢材料性能的需求。
二、控制轧制技术的应用1. 调整轧制温度和速度在型钢轧制中,通过调整轧制温度和轧制速度,可以控制晶粒的细化和晶格的取向,从而提高型钢的强度和塑性。
尤其是在热轧过程中,通过精确控制轧制温度和速度,可以有效控制晶粒生长,减少析出相的尺寸,使得型钢的晶粒细化,提高强度和硬度。
2. 控制轧制力和变形量通过精确控制轧制力和变形量,可以有效调整型钢的组织结构和力学性能。
在轧制过程中,通过监测轧辊力和变形量,可以实现对型钢的细微调整,达到提高型钢性能的目的。
在轧制高强度型钢时,通过增加轧制力和变形量,可以有效提高型钢的强度和硬度。
3. 控制轧制辊形状通过选择合适的轧辊形状,可以实现更加精确的型钢轧制。
不同形状的轧辊对型钢的变形和组织结构有着不同的影响,因此通过调整轧辊的形状,可以实现对型钢结构和性能的精细控制。
三、控制冷却技术的应用1. 控制冷却速度在型钢生产中,通过控制冷却速度,可以实现对型钢组织和性能的调整。
在快速冷却条件下,型钢的组织结构更加均匀,晶粒更加细小,从而提高了型钢的强度和韧性。
在慢速冷却条件下,型钢的组织结构更加致密,表面质量更好,适用于高表面质量要求的场合。
2. 控制冷却介质不同的冷却介质对型钢的冷却效果和组织结构有着不同的影响。
通过选择合适的冷却介质,可以实现对型钢组织和性能的精细调控。
对于高强度型钢,可以采用高效的水冷或气体冷却,快速降温,实现对型钢强度和硬度的提高。
3. 控制冷却方式在型钢生产中,采用不同的冷却方式,可以实现对型钢的细微调整。
采用直接水冷或间接水冷,可以分别实现快速和慢速的冷却效果,从而满足不同型钢的冷却需求。
钢材控制轧制和控制冷却技术

2)一道次压下率越大,越易产生变形带,越易获得均匀组织。 )一道次压下率越大,越易产生变形带,越易获得均匀组织。 体晶粒尺寸( ) ⑤、未再结晶区材料强度由固溶强化( σ sh)和F体晶粒尺寸(d) 未再结晶区材料强度由固溶强化( 体晶粒尺寸 等决定。 等决定。
§2控轧控冷理论
3、变形条件对A 变形条件对A
→ P转变的影响
r1的影响
变形使P体转变加速,从而使钢的淬透性变坏。 (1)、变形使P体转变加速,从而使钢的淬透性变坏。 (2)、变形对A 变形对A
§2控轧控冷理论
4、铁素体的变形与再结晶 (1)F体热加工中的组织变化 ①、F体热加工应力—应变曲线 体热加工应力 应变曲线 ②、F体热加工软化方式 ③、亚晶尺寸d 亚晶尺寸d (2)F体在变形间隙时的组织变化 ①、F体发生静态回复和再结晶软化 1)静态再结晶有条件的: > ε s 静态再结晶有条件的: ε 为临界值) (ε s为临界值) 2)影响静态再结晶的因素 ②、F体再结晶晶粒大小
§2控轧控冷理论
(2)位错强化 加工硬化是位错强化的外部表现 (3)沉淀强化 低合金钢中加入微量Nb、 低合金钢中加入微量Nb、V、Ti等元素,可形成碳化物、氮化物或碳氮化 Nb Ti等元素,可形成碳化物、 等元素 物,在轧制时或轧后冷却时,它仍析出 在轧制时或轧后冷却时,它仍析出——第二相沉淀强化 第二相沉淀强化 (4)晶界强化 晶粒越细小,晶界相对越多,晶界对为错的运动的阻力越大。 晶粒越细小,晶界相对越多,晶界对为错的运动的阻力越大。 1 霍尔—佩奇公式: 霍尔 佩奇公式: σ s = σi + Ki D 佩奇公式
热轧钢铁材料新一代TMCP技术

世界金属导报/2012年/1月/10日/第B04版轧钢技术热轧钢铁材料新一代TMCP技术TMCP(Thermo-MechanicalControlled Processing),即控制轧制和控制冷却技术,是20世纪钢铁业最伟大的成就之一,也是目前钢铁材料轧制及产品工艺开发领域应用最为普遍的技术之一。
正是因为有了TMCP技术,钢铁工业才能源源不断地向社会提供越来越有用的钢铁材料,支撑着人类社会的发展和进步。
1 TMCP工艺技术的发展及基本原理TMCP工艺的两个重要组成部分之一,控制轧制,在热轧钢铁材料领域很早就已根据经验予以实施,其核心思想是对奥氏体硬化状态的控制,即通过变形在奥氏体中积累大量的能量,力图在轧制过程中获得处于硬化状态的奥氏体,为后续的相变过程实现晶粒细化做准备。
在20世纪60年代至70年代,随着能源不断开发,对高性能管线钢的需求大幅增加。
为满足管线钢板的生产,控制轧制技术得到快速发展,并在当时的厚板轧制、船板生产等方面得到广泛应用。
为了突破控制轧制的限制,同时也是为了进一步强化钢材的性能,在控制轧制的基础上,又开发了控制冷却技术。
控制冷却的核心思想是对处于硬化状态的奥氏体相变过程进行控制,以进一步细化铁素体晶粒,甚至通过相变强化得到贝氏体等强化相。
相变组织比单纯控制轧制更加细微化,促使钢材获得更高的强度,同时又不降低其韧性,从而进一步改善材料的性能。
1980年,日本NKK福山制铁所首次为厚板生产线配置并使用了OLAC(On-Line Accelerated Cooling)系统。
此后基于对提高厚板性能及钢种开发的需要,重点发展了厚板的快速在线冷却技术,并相继开发出一系列快速冷却装置,投入厚板的开发生产及应用中。
控制冷却设备的普遍应用有力地推动了高强度板带材的开发和在提高材质性能方面技术的进步。
后来,人们将结合控制轧制和控制冷却的技术称为控轧控冷技术TMCP(Thermo-MechanicalControlled Processing)。
控制轧制和控制冷却工艺讲义

控制轧制和控制冷却工艺讲义控制轧制和冷却工艺讲义一、轧制工艺控制1. 轧制温度控制a. 在热轧过程中,轧机和钢坯之间的接触摩擦会产生高温,因此需要控制轧机温度,避免过热。
b. 实时监测轧机温度,根据温度变化调整轧制速度和冷却水量,确保温度适中。
c. 使用专用液体和冷却器进行在线冷却,防止轧机过热引起事故。
2. 轧制力控制a. 测量轧机产生的轧制力,确保轧机施加的压力适中。
b. 监控轧制力的变化,根据钢坯的变形情况调整轧制力,使钢坯的形状和尺寸满足要求。
c. 根据轧制力的大小调整轧制速度,保持稳定的轧制负荷。
3. 轧制速度控制a. 根据不同钢材的特性和规格,调整轧制速度,确保成品钢材的质量和尺寸满足要求。
b. 控制轧制速度的稳定性,避免过快或过慢的轧制速度导致钢材质量不达标。
4. 轧辊调整控制a. 定期检查和调整轧辊的位置和间距,确保钢坯能够顺利通过轧机,避免产生不均匀的轧制力和过度变形。
b. 根据车间实际情况和轧制工艺要求,调整轧辊的工作方式和参数,使轧制过程更加稳定和高效。
二、冷却工艺控制1. 冷却水量控制a. 根据钢材的材质和规格,调整冷却水的流量和压力,确保钢材迅速冷却到所需温度。
b. 监测冷却水流量和温度,根据实时数据调整冷却水量,确保冷却效果和成品钢材的质量。
2. 冷却速度控制a. 根据不同的冷却工艺要求,调整冷却速度,使钢材的组织和性能满足要求。
b. 监控冷却速度的变化,根据实时数据调整冷却速度,确保成品钢材的质量和性能稳定。
3. 冷却方法控制a. 根据钢材的特性和要求,选择合适的冷却方法,如水冷、风冷等。
b. 根据不同冷却方法的特点和效果,调整冷却工艺参数,使冷却效果和成品钢材的质量最优化。
4. 冷却设备维护a. 定期检查和维护冷却设备,确保设备的正常运行和效果良好。
b. 清洗和更换冷却设备中的阻塞、损坏部件,保证冷却水的流量和质量。
以上是对控制轧制和控制冷却工艺的讲义,通过合理的工艺控制和设备维护,能够提高轧制和冷却过程的效率和质量,满足钢材的要求。
热轧的工艺流程范文

热轧的工艺流程1.主轧线工艺流程简述板坯由炼钢连铸车间的连铸机出坯辊道直接送到热轧车间板坯库,直接热装的钢坯送至加热炉的装炉辊道装炉加热,不能直接热装的钢坯由吊车吊入保温坑,保温后由吊车吊运至上料台架,然后经加热炉装炉辊道装炉加热,并留有直接轧制的可能。
连铸板坯由连铸车间通过板坯上料辊道或板坯卸料辊道运入板坯库,当板坯到达入口点前,有关该板坯的技术数据已由连铸车间的计算机系统送到了热轧厂的计算机系统,并在监视器上显示板坯有关数据,以便工作人员进行无缺陷合格板坯的核对和接收。
另外,通过过跨台车运来的人工检查清理后的板坯也需核对和验收,并输入计算机。
进入板坯库的板坯,由板坯库计算机管理系统根据轧制计划确定其流向。
常规板坯装炉轧制:板坯进入板坯库后,按照板坯库控制系统的统一指令,由板坯夹钳吊车将板坯堆放到板坯库中指定的垛位。
轧制时,根据轧制计划,由板坯夹钳吊车逐块将板坯从垛位上吊出,吊到板坯上料台架上上料,板坯经称量辊道称重、核对,然后送往加热炉装炉辊道,板坯经测长、定位后,由装钢机装入加热炉进行加热。
碳钢保温坑热装轧制:板坯进入板坯库后,按照板坯库控制系统的统一指令,由板坯夹钳吊车将板坯堆放到保温坑中指定的垛位。
轧制时,根据轧制计划,由板坯夹钳吊车逐块将板坯从保温坑取出,吊到板坯上料台架上上料,板坯经称量辊道称重、核对,然后送往加热炉装炉辊道,板坯经测长、定位后,由装钢机装入加热炉进行加热。
直接热装轧制:当连铸和热轧的生产计划相匹配时,合格的高温连铸板坯通过加热炉上料辊道运到称量辊道,经称重、核对,进入加热炉的装炉辊道,板坯在指定的加热炉前测长、定位后,由装钢机装入加热炉进行加热。
其中一部分通过卸料辊道运输的直接热装板坯需通过吊车吊运一次放到上料辊道后直接送至加热炉区。
如果炼钢厂可以实现直接热装板坯由上料辊道运送,则可减少部分吊车吊运作业。
板坯经加热炉的上料辊道送到加热炉后由托入机装到加热炉内,加热到设定温度后,按轧制节奏要求由出钢机托出,放在加热炉出炉辊道上。
线材生产中的控制轧制和控制冷却技术

线材生产中的控制轧制和控制冷却技术线材是现代工业生产中使用频繁的一种材料,它广泛应用于电线电缆、机械制造、建筑材料等行业。
在线材生产过程中,控制轧制和控制冷却技术是关键的环节,它们直接影响着线材的质量、机械性能和用途范围。
一、控制轧制控制轧制是指通过改变轧制变形量、轧制温度、轧制速度、轧制力等因素,控制金属材料的形变和微观组织,达到调整线材力学性能、改善表面质量和优化产品用途的目的。
1、轧制变形量控制轧制变形量是指轧制前后的减压变化,它对线材的力学性能和表面质量有着直接影响。
为了保证线材的质量稳定和合格率,轧制变形量控制必须精准可靠,并考虑到批量变化和轧制型号的特定要求。
目前,国内外的轧制变形量控制采用电液伺服技术,通过实时监测轧制变形量变化,及时控制系统参数的变化,保证线材轧制变形量的稳定。
2、轧制温度控制轧制温度是指线材在轧制时的温度,它对线材的力学性能和表面质量有着重大影响。
过高或过低的温度会导致线材的晶粒过大或过小,从而影响线材的硬度、韧性和塑性等力学性能。
为了提高线材的机械性能和用途范围,轧制温度控制必须准确可靠,并考虑到金属材料的温度敏感性和轧制工艺的特定要求。
目前,国内外的轧制温度控制采用激光测温技术或红外线测温技术,通过实时监测线材温度变化,及时调整轧制温度,保证线材轧制温度的稳定。
3、轧制速度控制轧制速度是指线材在轧制过程中的速度,它对线材的表面质量和机械性能有着直接影响。
过高或过低的轧制速度会导致线材表面的纹路不均匀和线材的硬度、韧性等力学性能下降。
为了提高线材的表面质量和机械性能,轧制速度控制必须准确可靠,并考虑到轧制型号的特定要求。
目前,国内外的轧制速度控制采用伺服电机技术或电磁流体技术,通过实时监测线材的速度变化,及时调整轧制速度,保证线材轧制速度的稳定。
二、控制冷却控制冷却是指针对金属材料在热加工过程中产生的内应力、变形、晶粒长大等现象,通过采用不同的冷却方式和工艺参数,调整金属材料的组织和性能。
线材生产中的控制轧制和控制冷却技术

应采用轧后快速冷却。因为如果轧后慢冷 , 则变形奥氏体 晶粒将在冷却过程中长大 , 相变后得 到粗 大的铁 素体组 织。由于冷却缓慢 , 由奥 氏体转变的珠光体粗大, 片层 问 距加厚。这种组织的力学性能较低 。对于低温终轧的线 材 , LG 终 ̄ u奥氏体处于未再结晶温度 区域 , , 由于变形影响 温度提高, 终轧后奥氏体很快就相变 , 形成铁素体。这
着重叙述 了线材 生产 中控制轧制和控制冷却技术的机理、 特点 、 、 用及斯 太尔摩冷却 工艺。 方式 应
关键词 :线材 生产 中图分类号 :l T ̄l 控制轧制 控制冷却 斯 太尔摩冷却工 艺 (0 10 08 0 2 1 )2— 07— 5 文献标识码 : A 文章编号 :02一 10  ̄
a p iain o o told r l n d C n r l d c o i g tc nq e a d semo o t l d c oi g tc n l gc lp o e s a e man y d — p l t fC n r l ol g a o t l o l e h iu n tl r C n r l o ln e h o o ia r c s r il e c o e i n oe n oe s rb d c e. i
以超快速冷却为核心的新一代技术

以超快速冷却为核心的新一代技术The New Generation TMCP with rhe KeyTechnology of Uletra Fast Cooling王国栋摘要针对传统TMCP技术采用“低温大压下”和“微合金化”的问题,利用连续轧制的大变形和应变积累,提出以超快速冷却技术为核心的新一代控制轧制和控制冷却技术的大变形和应变积累,提出以超快速冷却技术为核心的新一代控制轧制和控制冷却技术(NG-TMCP),描述了它的技术特征和材料特点,指出这是一项节省资源和能源,有利于材料循环利用,促进社会可持续发展的新技术。
1 TMCP技术及其特征控制轧制和控制冷却技术,即TMCP,是20世纪钢铁业最伟大的成就之一。
正是因为有了TMCP技术,钢铁业才能源源不断地向社会提供越来越优良的钢铁材料,支撑着人类社会的发展和进步。
控制轧制和控制冷却技术的目标是实现晶粒细化和细晶强化。
在控制轧制和控制冷却技术的发展历程中,人们首先认识到的是控制轧制,其核心思想是对奥氏体硬化状态的控制,即通过变形的奥氏体中积累大量的能量,力图在轧制过程中获得处于硬化状态的奥氏体,为后续的相变过程中实现晶粒细化做准备。
控制轧制的基本手段是“低温大压下”和添加微合金元素。
所谓“低温”是在接近相变点的温度进行变形,由于变形温度低,可以抑制奥氏体的再结晶,保持其硬化状态,“大压下”是指施加超出常规的大压下量,这样可以增加奥氏体内部储存的变形能,提高硬化奥氏体程度。
增加微合金元素,例如Nb,是为了提高奥氏体的再结晶温度,使奥氏体在比较高的温度即处于未再结晶区,因而可以增大奥氏体在未结晶区的变形量,实现奥氏体的硬化。
图1图1控制轧制和控制冷却为了突破控制轧制的限制,同时也是为了进一步强化钢材的性能,在控制轧制的基础上,又开发了控制冷却技术,控制冷却的核心思想,是对处于硬化状态奥氏体相变过程进行控制,以进一步细化铁素体晶粒,甚至通过相变强化得到贝氏体等强化相,进一步改善材料的性能。
控制轧制、控制冷却工艺

控制轧制、控制冷却⼯艺控制轧制、控制冷却⼯艺技术1.1 控制轧制⼯艺控制轧制⼯艺包括把钢坯加热到适宜的温度,在轧制时控制变形量和变形温度以及轧后按⼯艺要求来冷却钢材。
通常将控制轧制⼯艺分为三个阶段,如图 1.1所⽰[2]:(1>变形和奥⽒体再结晶同时进⾏阶段,即钢坯加热后粗⼤化了的γ呈现加⼯硬化状态,这种加⼯硬化了得奥⽒体具有促使铁素体相变形变形核作⽤,使相变后的α晶粒细⼩;(2> (γ+α>两相区变形阶段,当轧制温度继续降低到Ar3温度以下时,不但γ晶粒,部分相变后的α晶粒也要被轧制变形,从⽽在α晶粒内形成亚晶,促使α晶粒的进⼀步细化。
图1.1控制轧制的三个阶段(1>—变形和奥⽒体再结晶同时进⾏阶段;(2>—低温奥⽒体变形不发⽣再结晶阶段;(3>—<γ+α)两相区变形阶段。
1.2 控制轧制⼯艺的优点和缺点控制轧制的优点如下:1.可以在提⾼钢材强度的同时提⾼钢材的低温韧性。
采⽤普通热轧⽣产⼯艺轧制16Mn钢中板,以18mm厚中板为例,其屈服强度σs≤330MPa,-40℃的冲击韧性A k≤431J,断⼝为95%纤维状断⼝。
当钢中加⼊微量铌后,仍然采⽤普通热轧⼯艺⽣产时,当采⽤控制轧制⼯艺⽣产时,-40℃的A k值会降低到78J以下,然⽽采⽤控制轧制⼯艺⽣产时。
然⽽采⽤控制轧制⼯艺⽣产时-40℃的A k值可以达到728J以上。
在通常热轧⼯艺下⽣产的低碳钢α晶粒只达到7~8级,经过控制轧制⼯艺⽣产的低碳钢α晶粒可以达到12级以上<按ASTM标准),通过细化晶粒同时达到提⾼强度和低温韧性是控轧⼯艺的最⼤优点。
2.可以充分发挥铌、钒、钛等微量元素的作⽤。
在普通热轧⽣产中,钢中加⼊铌或钒后主要起沉淀强化作⽤,其结果使热轧钢材强度提⾼、韧性变差,因此不少钢材不得不进⾏正⽕处理后交货。
当采⽤控制轧制⼯艺⽣产时,铌将产⽣显著的晶粒细化和⼀定程度的沉淀强化,使轧后的钢材的强度和韧性都得到了很⼤提⾼,铌含量⾄万分之⼏就很有效,钢中加⼊的钒,因为具有⼀定程度的沉淀强化的同时还具有较弱的晶粒细化作⽤,因此在提⾼钢材强度的同时没有降低韧性的现象。
控制轧制及控制冷却技术在型钢生产中的应用
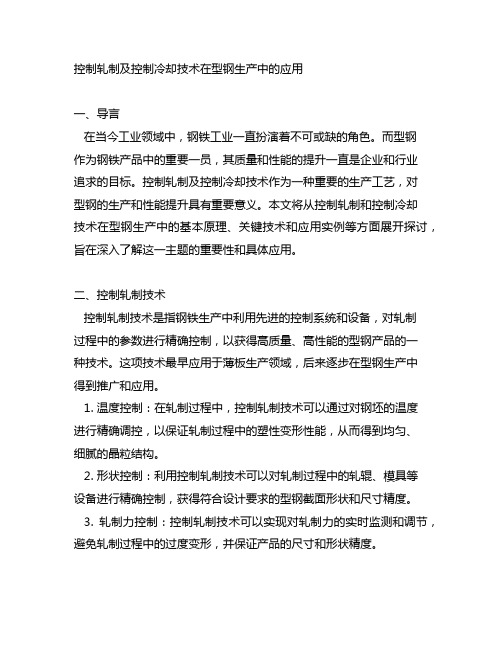
控制轧制及控制冷却技术在型钢生产中的应用一、导言在当今工业领域中,钢铁工业一直扮演着不可或缺的角色。
而型钢作为钢铁产品中的重要一员,其质量和性能的提升一直是企业和行业追求的目标。
控制轧制及控制冷却技术作为一种重要的生产工艺,对型钢的生产和性能提升具有重要意义。
本文将从控制轧制和控制冷却技术在型钢生产中的基本原理、关键技术和应用实例等方面展开探讨,旨在深入了解这一主题的重要性和具体应用。
二、控制轧制技术控制轧制技术是指钢铁生产中利用先进的控制系统和设备,对轧制过程中的参数进行精确控制,以获得高质量、高性能的型钢产品的一种技术。
这项技术最早应用于薄板生产领域,后来逐步在型钢生产中得到推广和应用。
1. 温度控制:在轧制过程中,控制轧制技术可以通过对钢坯的温度进行精确调控,以保证轧制过程中的塑性变形性能,从而得到均匀、细腻的晶粒结构。
2. 形状控制:利用控制轧制技术可以对轧制过程中的轧辊、模具等设备进行精确控制,获得符合设计要求的型钢截面形状和尺寸精度。
3. 轧制力控制:控制轧制技术可以实现对轧制力的实时监测和调节,避免轧制过程中的过度变形,并保证产品的尺寸和形状精度。
三、控制冷却技术控制冷却技术是指在型钢生产过程中,通过对冷却过程的控制,使钢材在冷却过程中获得理想的组织和性能。
这项技术的应用可以有效提高型钢的强度、韧性和耐磨性等性能,同时降低产品的变形和裂纹率。
1. 冷却介质控制:通过选择不同的冷却介质和控制冷却速度,可以使型钢获得不同的组织和性能,如马氏体组织、贝氏体组织等,从而满足不同领域对型钢性能的要求。
2. 温度控制:在控制冷却技术中,对冷却过程中的温度进行精确控制,可以有效控制组织相变,并获得理想的力学性能,如强度、韧性等。
3. 冷却速度控制:通过对型钢冷却速度进行控制,可以获得不同的组织和性能,如快速冷却可以获得细小的组织和高强度,而缓慢冷却则可以得到较好的塑性和韧性。
四、控制轧制及控制冷却技术在型钢生产中的应用实例1. 控制轧制技术在型钢生产中的应用:某钢铁企业引进了先进的控制轧制系统和设备,通过对轧制过程中的温度、形状和轧制力等参数进行精确控制,生产出了高精度、高强度的型钢产品,受到了市场的广泛认可。
毕业设计(论文)-热轧板带钢的控制轧制[管理资料]
![毕业设计(论文)-热轧板带钢的控制轧制[管理资料]](https://img.taocdn.com/s3/m/022774c5eefdc8d376ee32f7.png)
河北科技大学毕业论文论文题目:热轧板带钢的控制轧制学院材料学院专业年级2011冶金工程技术学生姓名指导教师职称日期2013年11月20日目录一、前言 (1)二、控制轧制的特点 (2)三、国内典型中厚板轧机控轧控冷工艺 (6)四、热连轧带钢的控制轧制和控制冷却 (8)五、宽带钢轧机板形控制技术 (10)六、结论 (14)参考文献 (14)热轧板带钢的控制轧制摘要:控制轧制和控制冷却技术在轧钢生产中加以应用,明显地改善和提高了钢材的强韧性和使用性能,为节约能耗,简化生产工艺,开发钢材新品种创造了有利条件。
通过对典型的热轧带钢,中厚板及宽带刚钢控制轧制和控制冷却新工艺的开发与基本理论的研究,进一步揭示了热变形过程中变形和冷却工艺参数与钢材的组织变化、相变规律以及钢材性能之间的内在关系,充实和形成了钢材热变形条件下的物理冶金工程理论,为制定合理的热轧生产工艺提供了依据。
关键词:热轧带钢;中厚板;宽带钢;控扎;控冷一、前言(一)控制轧制的概念近年来控制轧制作为热轧新技术越来越被人所重视。
控制轧制技术一般多用在结构钢上:高强度、高韧性和良好的焊接性能。
可称为对结构钢要求的三要素。
为了使结构钢获得这些良好的性能,最好的方法是使钢的晶粒细化。
控制轧制工艺包括把钢坯加热到适宜的温度,在轧制时控制变形量和变形温度以及轧后按工艺要求来冷却钢材。
通常将控制轧制工艺分为奥氏体再结晶控制轧制、奥氏体未再结晶区控制轧制和两相区控制轧制三个阶段:1、变形和奥氏体再结晶同时进行阶段,即钢坯加热后粗大化了的γ晶粒经过在γ再结晶区域内的反复变形和再结晶而逐步的到细化的阶段;2、低温奥氏体变形阶段,当轧制变形进入γ未再结晶区域时,变形后的γ晶粒不再发生再结晶,而呈现加工硬化状态,这种加工硬化了的奥氏体具有促进铁素体相变形核作用使相变后的α晶粒细小;3、(γ+α)两相区变形阶段,当轧制温度继续降低到Ar3温度以下时不但γ晶粒,部分相变后的α晶粒也要被轧制变形从而在α晶粒内形成亚晶,促使α晶粒的进一步细化。
控制轧制和控制冷却技术期末复习资料

控制轧制:是在热轧过程中,通过控制加热温度、轧制温度、变形制度等工艺参数,控制奥氏体状态和相变产物的组织状态,从而达到控制钢材组织性能的目的。
控制冷却:是控制轧后钢材的冷却速度达到改善钢材组织和性能的目的。
钢的强化机制:固溶强化、位错强化、晶界强化、沉淀强化、亚晶强化、相变强化等1固溶强化(机制晶格畸变、气团效应):溶质原子溶入基体金属使材料强度增加的现象,间隙式固溶强化使强度↑,但塑性↓、韧性↓;置换式固溶强化强化效果小,但对塑性、韧性影响不大。
2形变强化:在塑性变形中,随变形程度↑,基体强度↑的现象。
机理:变形量ε↑,位错密度ρ↑,位错的移动阻力↑,强化↑。
3细晶强化(晶界强化)随晶粒细化,基体强度上升的现象。
本质:晶界对位错运动的阻碍作用。
晶界处:原子排列不规则,杂质多,存在大量晶格缺陷。
晶界强化能同时提高材料的强度和韧性。
4沉淀强化与弥散强化(析出强化):第二相微粒从过饱和固溶体中沉淀析出使材料强度↑的现象。
5亚晶强化:实质:位错密度增高。
亚晶因动态、静态回复形成,亚晶本身是位错墙。
6相变强化:实质:马氏体强化,马氏体是碳在α-Fe中的过饱和固溶体。
碳原子固溶强化是马氏体最基本的强化机制。
随着时效时间的延长,材料的强度出现连续下降现象,是什么原因?随着时效时间的延长,强度将连续下降。
这是因为颗粒长大,颗粒间距加大的原故。
因此对沉淀强化析出的质点应具有尽可能小的溶解度和很小的凝聚性。
也就是说能在各种温度下保持稳定。
结构钢中的碳化物、氮化物和碳氮化物在实际使用中能满足这些要求。
韧性(又名韧度):是材料塑性变形和断裂全过程中吸收能量的能力,它是强度和塑性的综合表现。
因此可以用材料在塑性变形和断裂全过程中吸收能量的多少来表示韧性的高低。
应力应变:现在与开始相比。
真应力应变:短时间内的相比。
奥氏体热加工的真应力-真应变曲线:第一阶段(加工硬化):当塑性变形小时,随着变形量增加变形抗力增加,直到达到最大值。
钢材的控制轧制和控制冷却

钢材的控制轧制和控制冷却一、名词解释:1、控制轧制:在热轧过程中通过对金属的加热制度、变形制度、温度制度的合理控制,使热塑性变形与固态相变结合,以获得细小晶粒组织,使钢材具有优异的综合力学性能。
2、控制冷却:控制轧后钢材的冷却速度、冷却温度,可采用不同的冷却路径对钢材组织及性能进行调控。
3、形变诱导相变:由于热轧变形的作用,使奥氏体向铁素体转变温度Ar3上升,促进了奥氏体向铁索体的转变。
在奥氏体未再结晶区变形后造成变形带的产生和畸变能的增加,从而影响Ar3温度。
4、形变诱导析出:在变形过程中,由于产生大量位错和畸变能增加,使微量元素析出速度增大。
两相区轧制后的组织中既有由变形未再结晶奥氏体转变的等轴细小铁素体晶粒,还有被变形的细长的铁素体晶粒。
同时在低温区变形促进了含铌、钒、钛等微量合金化钢中碳化物的析出。
5、再结晶临界变形量: 在一定的变形速率和变形温度下,发生动态再结晶所必需的最低变形量。
6、二次冷却:相变开始温度到相变结束温度范围内的冷却控制。
二、填空:1、再结晶的驱动力是储存能,影响其因素可以分为:一类是工艺条件,主要有变形量、变形温度、变形速度。
另一类是材料的内在因素,主要是材料的化学成分和冶金状态。
2、控制冷却主要控制轧后钢材冷却过程的(冷却温度)、(冷却速度)等工艺条件,达到改善钢材组织和性能的目的。
3、固溶体的类型有(间隙式固溶)和(置换式固溶),形成(间隙式)固溶体的溶质元素固溶强化作用更大。
4、根据热轧过程中变形奥氏体的组织状态和相变机制不同,将控制轧制划分为三个阶段,即奥氏体再结晶型控制轧制、奥氏体未再结晶型控制轧制、在A+F两相区控制轧制。
5、以珠光体为主的中高碳钢,为达到珠光体团直径减小,则要细化奥氏体晶粒,必须采用(奥氏体再结晶)型控制轧制。
6、控制轧制是在热轧过程中通过对金属的(加热制度)、(变形制度)、(温度制度)的合理控制,使热塑性变形与固态相变结合使钢材具有优异的综合力学性能。
热轧的工艺流程
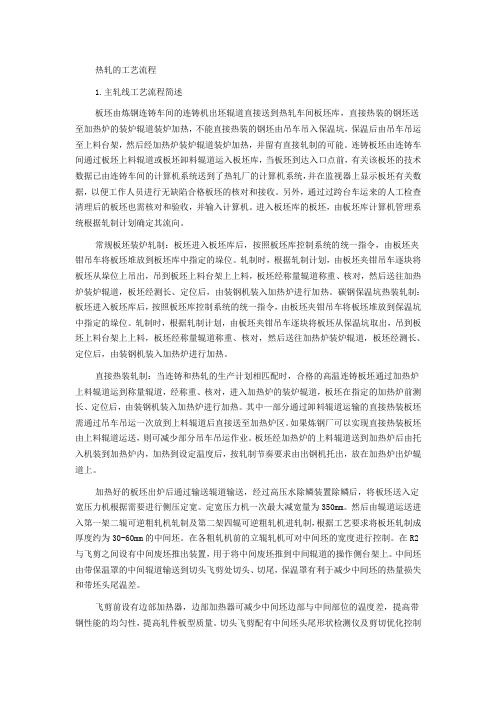
热轧的工艺流程1.主轧线工艺流程简述板坯由炼钢连铸车间的连铸机出坯辊道直接送到热轧车间板坯库,直接热装的钢坯送至加热炉的装炉辊道装炉加热,不能直接热装的钢坯由吊车吊入保温坑,保温后由吊车吊运至上料台架,然后经加热炉装炉辊道装炉加热,并留有直接轧制的可能。
连铸板坯由连铸车间通过板坯上料辊道或板坯卸料辊道运入板坯库,当板坯到达入口点前,有关该板坯的技术数据已由连铸车间的计算机系统送到了热轧厂的计算机系统,并在监视器上显示板坯有关数据,以便工作人员进行无缺陷合格板坯的核对和接收。
另外,通过过跨台车运来的人工检查清理后的板坯也需核对和验收,并输入计算机。
进入板坯库的板坯,由板坯库计算机管理系统根据轧制计划确定其流向。
常规板坯装炉轧制:板坯进入板坯库后,按照板坯库控制系统的统一指令,由板坯夹钳吊车将板坯堆放到板坯库中指定的垛位。
轧制时,根据轧制计划,由板坯夹钳吊车逐块将板坯从垛位上吊出,吊到板坯上料台架上上料,板坯经称量辊道称重、核对,然后送往加热炉装炉辊道,板坯经测长、定位后,由装钢机装入加热炉进行加热。
碳钢保温坑热装轧制:板坯进入板坯库后,按照板坯库控制系统的统一指令,由板坯夹钳吊车将板坯堆放到保温坑中指定的垛位。
轧制时,根据轧制计划,由板坯夹钳吊车逐块将板坯从保温坑取出,吊到板坯上料台架上上料,板坯经称量辊道称重、核对,然后送往加热炉装炉辊道,板坯经测长、定位后,由装钢机装入加热炉进行加热。
直接热装轧制:当连铸和热轧的生产计划相匹配时,合格的高温连铸板坯通过加热炉上料辊道运到称量辊道,经称重、核对,进入加热炉的装炉辊道,板坯在指定的加热炉前测长、定位后,由装钢机装入加热炉进行加热。
其中一部分通过卸料辊道运输的直接热装板坯需通过吊车吊运一次放到上料辊道后直接送至加热炉区。
如果炼钢厂可以实现直接热装板坯由上料辊道运送,则可减少部分吊车吊运作业。
板坯经加热炉的上料辊道送到加热炉后由托入机装到加热炉内,加热到设定温度后,按轧制节奏要求由出钢机托出,放在加热炉出炉辊道上。
- 1、下载文档前请自行甄别文档内容的完整性,平台不提供额外的编辑、内容补充、找答案等附加服务。
- 2、"仅部分预览"的文档,不可在线预览部分如存在完整性等问题,可反馈申请退款(可完整预览的文档不适用该条件!)。
- 3、如文档侵犯您的权益,请联系客服反馈,我们会尽快为您处理(人工客服工作时间:9:00-18:30)。
本页已使用福昕阅读器进行编辑。
福昕软件(C)2005-2008,版权所有,仅供试用。
第30卷第7期2009年7月东北大学学报(自然科学版 Journal of Northeastern University (Natural Science Vol 130,No. 7J ul. 2009新一代控制轧制和控制冷却技术与创新的热轧过程王国栋(东北大学轧制技术及连轧自动化国家重点实验室, 辽宁沈阳110004摘要:针对传统控制轧制和控制冷却(TMCP 技术存在的问题, 提出了以超快冷为核心的新一代的TMCP 技术, 并详述了作为实现新一代TMCP 技术核心手段的超快冷技术的科学内涵和工业装备开发情况・指出新一代TMCP 技术综合采用细晶强化、析出强化、, 潜力, 节省资源和能源, 优化现有的轧制过程, ・为特征的创新轧制过程的案例, ・关键词:钢; 热轧; ; :A 100523026(2009 0720913210N ew TMCP and Innovative H ot R olling ProcessW A N G Guo 2dong(The State K ey Laboratory of Rolling and Automation , Northeastern University , Shenyang 110004, China.Correspondent :WAN G Guo 2dong , professor , E 2mail :wanggd @mail. neu. edu. cnAbstract :A new 2generation TMCP (thermo 2mechanical control process with ultra fast cooling as core technique was suggested instead of the conventional TMCP in which some problems are to be solved. Describes the ultra fast cooling technique theoretically and relevant equipment developed for commercial applications in detail. With the grain refining , precipitation and phase transformation strengthening , the new 2generation TMCP was verified available to make full use the potential of steels , save resources and energy and optimize existing rolling process , thus providing beneficially a sustainable development for iron and steel industry. Some examples are given to show the characteristics of the new 2generation TMCP in the rolling processes of different products especially its broad prospects in application.K ey w ords :steel ; hot rolling ; new generation TMCP ; ultra fast cooling ; strengthening1新一代TMCP (N G 2TMCP1. 1传统TMCP制轧制, 是对奥氏体硬化状态的控制, 即通过变形在奥氏体中积累大量的能量, 在轧制过程中获得处于硬化状态的奥氏体, 为后续的相变过程中实现晶粒细化做准备・硬化的奥氏体内存在大量的缺陷”, 例如变形带、位错、孪晶等它们是相变时・这种“缺陷”越多, 则铁素体的形核率越高, 得到的铁素体晶粒越细得到硬化奥“低温大压下”和添加微合金元“低温”是为了抑制奥氏体的再结晶, “; 大压下”则是为了增加硬化奥氏体所储・增加微合金元素, 例如控制轧制和控制冷却技术, 即TMCP , 是20世纪钢铁业最伟大的成就之一・正是因为有了TMCP 技术, 钢铁业才能源源不断地向社会提供越来越优良的钢铁材料, 支撑人类社会的发展和进步・控制轧制和控制冷却技术的核心是晶粒细化和细晶强化[1]・在控制轧制和控制冷却技术的发展历程中, 人们首先认识到的是控制轧制・所谓控收稿日期:2009205211基金项目:国家高技术研究发展计划项目(2003AA33G 010 ・作者简介:王国栋(1942- , 男, 辽宁大连人, 东北大学教授, 博士生导师, 中国工程院院士・914本页已使用福昕阅读器进行编辑。
福昕软件(C)2005-2008,版权所有,仅供试用。
东北大学学报(自然科学版第30卷获得高附加值、可循环的钢铁产品・这种TMCP技术就是以超快冷技术为核心的新一代TMCP 技术, 即N G 2TMCP [3]・1. 2. 1HTP 轧制工艺热连轧过程通常是高速连续大变形的轧制过程, 即使轧制温度较高, 在连轧过程完成之后, 也可以得到硬化的充满缺陷的奥氏体・换言之, 在现代的热连轧机上, 即使不用“低温大压下”, 也可以实现奥氏体的硬化・由于连轧中的连续大变形和应变积累, 硬化的获得不仅不需要低温大压下, 甚至也不一定必须添加合金或微合金元素・所以, 新一代TMCP 技术的第一个重要特点是“高温”轧制过程( ・这个“高温”“低温大压, ・, 在轧制温度制度上不再坚持“低温大压下”的原则・所以, 与“低温大压下”过程相比, 轧制负荷(包括轧制力和电机功率可以大幅度降低, 设备条件的限制可以大为放松, 轧机等轧制设备的建设不必追求高强化, 建设投资可以大幅度降低・适宜的轧制温度大大提高轧制的可操作性, 避免轧制工艺事故, 例如卡钢、堆钢等, 同时也延长了轧辊、导卫等轧制工具的寿命・这对于提高产量、降低成本是十分有利的・对于一些原来需要在粗轧和精轧之间实施待温的材料, 有可能通过超快速冷却的实施而不再需要待温, 或者提高待温的温度, 这对于提高生产效率具有重要的意义・1. 2. 2超快速冷却奥氏体的再结晶温度, 即处于未再结晶区, 度・为了突破控制轧制的限制, 同时也是为了进一步强化钢材的性能, 在控制轧制的基础上, 又开发了控制冷却技术・控制冷却的核心思想, 是对硬化奥氏体的相变过程进行控制, 以进一步细化铁素体晶粒, 以及通过相变强化得到贝氏体等强化相, 进一步改善材料的性能・控制冷却的理念可以归纳为“水是最廉价的合金元素”这样一句话・作为控制冷却的极限结果, DQ (direct quench 的作用早已为人们所认识・但是, 其潜在的能力一直未得到发挥, 原因在于直接淬火条件下冷却均匀性的问题一直没有得到很好的解决, DQ 情况下板形控制一直困扰人们・, 化状态, , ・由于铌等微合金元素的加入, 显著提高了钢材的再结晶温度, 使材料很大一部分热加工区间位于未再结晶区, 这大大强化了奥氏体的硬化状态・应当注意的是加入显然这会恶化材料的焊接性能・加入的微合金或合金元素, 除了部分固溶强化奥氏体外, 还经常会以碳氮化物的形式析出, 对材料进行沉淀强化, 从而对材料强度的提高做出贡献・例如Nb 通常在800~950℃的温度区间内, 在进行材料变形的同时, 析出Nb 的碳氮化物, 即产生所谓“形变诱导析出”, 一方面提高了材料的再结晶温度, 另一方面也强化了材料本身・采用“低温大压下”, 与人们长久以来形成的“趁热打铁”的观念背道而驰・它必然受到设备能力等的限制, 操作方面的问题也自然不容回避・为了实现“低温大压下”, 人们需要付出代价・长期以来, 为此而大幅提升轧制设备能力, 投入了大量资金、人力和资源・1. 2NG 2TMCP 的基本概念社会的高速发展, 使人类面临越来越严重的资源、能源短缺问题, 承受着越来越大的环境压力・人类必须解决这些问题才能与自然和谐发展, 保持人类社会的长治久安和子孙后代的幸福安康・针对这样的问题, 在制造业领域, 人们提出了4R 原则, 即减量化、再循环、再利用、再制造[2]・具体到TMCP 技术本身, 必须坚持减量化的原则, 即采用节约型的成分设计和减量化的生产方法,在这种情况下, 考虑的第一个问题是轧件的温度・由于采用常规轧制, 终轧温度较高, 如果不加控制, 材料会由于再结晶而迅速软化, 失去硬化状态・因此, 在终轧温度和相变开始温度之间的冷却过程中, 应努力设法避免硬化奥氏体的软化, 即设法将奥氏体的硬化状态保持到动态相变点・近年出现的超快速冷却技术, 可以对钢材实现每秒几百度的超快速冷却, 因此可以使材料在极短的时间内, 迅速通过奥氏体相区, 将硬化奥氏体“冻结”到动态相变点附近・这就为保持奥氏体的硬化状态和进一步进行相变控制提供了重要基础条件・在国外, 比利时的CRM 率先开发了超快速冷却(U FC 系统[4], 可以对4mm 的热轧带钢实现400℃/s 的超快速冷却・日本的J FE 福山厂开发的Super OLAC H 系统, 应用于热轧带钢轧机, 可以对3mm 的热轧带钢实现700℃/s 的超快速冷却[5]・国内, 东北大学轧制技术及连轧自动化第7期王国栋:新一代控制轧制和控制冷却技术与创新的热轧过程国家重点实验室(RAL 开发的带材高冷速系统也可以达到相似的冷却效果・RAL 开发的棒材超快速冷却系统对20mm 直径的棒材, 可以实现400℃/s 的超快速冷却・对板带材而言, 确保高速冷却条件下的平直度, 是一个关键性、瓶颈性的问题・RAL 已经针对热带和中厚板生产过程开发出高效率、高均匀性的新式冷却系统・利用这种系统, 可以突破高速冷却时的冷却均匀性这一瓶颈, 实现板带材全宽、全长上均匀化的超快速冷却, 因而可以得到平直度极佳的板带材产品・1. 2. 3超快速冷却终止点的精确控制轧后钢材由终轧温度急速快冷, 迅速穿过奥氏体区, 达到快速冷却条件下的动态相变点・在轧件达到预定的温度控制点后, 速冷却・, ・, 以及高精度的预控数学模型, 可以保证终止温度的精确控制・1. 2. 4冷却路径的控制915金属晶格畸变, 也可以提高材料的强度・这两种情况分别被称为间隙固溶和置换固溶・在热轧过程中, 固溶元素的存在, 可以提高材料的变形抗力, 所以在轧机设计中, 应当考虑固溶强化对变形抗力的贡献, 并在轧机设计中采取相应的强化措施・对于C 2Mn 钢, 固溶强化是主要的强化机制・2. 2细晶强化控制轧制和控制冷却技术主要是针对HSLA 钢, 通过添加微合金元素提高钢材的再结晶温度, 扩大未再结晶区, 在未再结晶区进行低温大压下, 使材料内部形成大量的变形带、亚晶、位错等晶体“缺陷”, 这些“缺陷”在后续的相变中成为铁素体形核的核心・“的大量存在, , , ・, 特别, ℃的温度区间由于变形的, 从而提高材料的再结晶温度, 强化材料的硬化效果・对于HSLA 钢来说, 细晶强化是主要的强化方式・当采用N G 2TMCP 时, 尽管材料是在较高的温度下完成热变形过程, 但是变形后的短时间内, 材料还来不及发生再结晶, 仍然处于含有大量“缺陷”的高能状态・如果对它实施超快速冷却, 就可以将材料的硬化状态保持下来, 在随后的相变过程中, 保存下来的大量“缺陷”成为形核的核心, 因而可以得到与低温轧制相似的强化效果・2. 3析出强化实施超快速冷却后的钢材还要依据所需要的组织和性能要求, 进行冷却路径控制, 这就为获得多样化的相变组织和材料性能提供了广阔的空间・利用这样一个特点, 有可能利用简单的成分设计获得不同性能的材料, 实现柔性化的轧制生产, 提高炼钢和连铸的生产效率・在冷却路径的精确控制方面, 现代的控制冷却技术已经可以提供良好的控制手段, 相变强化仍然是可以利用的重要强化手段・这样一来, 再与固溶强化、细晶强化、析出强化等手段互相配合, 新一代的TMCP 将在提高材料的强度、改善综合性能、满足人类对材料的要求方面发挥重要作用・有了这一系列以超快速冷却为核心的高速连轧技术和控制冷却技术, 完全可以有更多、更有效的手段, 实现奥氏体硬化状态的控制和硬化状态下奥氏体相变过程的控制, 完全可以达到TMCP 控制的目标・在钢中添加微合金元素和合金元素, 会在钢中形成一些析出相以微小颗粒析出, 造成基体晶格的畸变, 提高材料的强度, 这称为析出强化・析出强化的效果与析出相数量、颗粒尺寸等因素有关, 在各类钢中都有应用・自从开发HSLA 钢成功以来, 析出强化在材料高强化方面的作用也日益显著, 目前析出强化已经成为材料强化的重要手段・G ladman 等人依据Orowan 2Ashby 模型提出用式(1 表示析出强化的效果[6]:Δσ=1/2x ln (x /2. 5×10-4 ・(12N G 2TMCP 的强化机制2. 1固溶强化σ为抗拉强度的增加值, MPa ; f 为碳氮化其中:Δ物的体积分数; x 为颗粒在滑移平面上的平面截取直径, 由x =D (2/3 1/2给出, 其中D 是平均微粒直径, μm ・依照式(1 可知, 颗粒尺寸越小, 析出物的数量越多, 则材料抗拉强度的提高值越大・采用传统的控轧控冷工艺时, 含铌的HSLA 钢通常会在热加工温度范围内, 即800~950℃的温度区间, 由于变形诱导析出铌的碳氮化物, 因而固溶强化是普遍采用的强化机制・C ,N 等小半径的原子, 以间隙原子的形式与金属形成固溶体, 造成基体金属晶格的畸变, 提高材料的强度; 而Mn ,Cu ,Ni ,Cr 等金属原子, 通过置换基体金属原子而溶于金属中, 由于原子半径不同, 造成基体916东北大学学报(自然科学版第30卷条件, 但是冷却过程不同, 即采用不同的冷却路径,也会得到不同的组织, 因而会有不同的材料性能・图1所示为几种典型的AHSS 钢, 即EP 、TRIP 、贝氏体钢的冷却工艺路径图・在冷却的开始阶段, 利用前部加速冷却(或超快速冷却将奥氏体冷却到铁素体相变开始温度, 随后进入保温状态, 即材料处于空冷状态, 以利于铁素体的析出・当析出一定体积分数的铁素体之后, 例如85%, 对材料进行第二次加速冷却(或超快速冷却 ,如果终冷温度在马氏体点以下, 则剩余的奥氏体全部转变为马氏体, 这样便得到以软相铁素体和硬相马氏体组成的复相组织, 即双相钢; 如果冷却的300~500, 则得TRIP ; 如果剩余的奥氏体全部转变为贝氏体, 则得到铁素体和贝氏体组成的复相组织钢, 即贝氏体钢・关于前部和后部具体是采用常规加速冷却还是超快速冷却的问题, 超快速冷却具有一定的优点, 应当是首选・前部超快冷有利于铁素体晶粒的细化, 同时也有利于铁素体的快速析出, 这对于缩短热连轧机输出辊道的长度是有利的・后部超快冷更有利于马氏体相变・可能由于析出而提高材料的强度・但是, 在采用N G 2TMCP 时, 材料在比较高的温度被加工成形, 在通常形变诱导析出的温度范围, 被迅速冷却通过碳氮化物大量析出的温度区间, 碳氮化物的析出受到了抑制・超快速冷却在适当的温度被终止, 例如在铁素体相变的“鼻尖”温度被终止, 然后进行空冷, 此时碳氮化物可能由于很大的析出驱动力而在铁素体晶内大量、微细、弥散地析出, 使铁素体基体得到强化, 大幅度提高材料的强度水平・因此, 采用N G 2TMCP 技术, 可以更好地发挥铌等微合金元素的强化作用, 发挥合金元素的强化效果・2. 4相变强化相变强化又称组织强化, 它是通过相变过程改变钢材的组织组成, 从而提高钢材强度的一种强化方法・, 组织, ・硬相所占的比例不同, 就能得到不同的材料强度水平・相变强化正是利用了钢铁材料的这一特点・先进高强钢(AHSS 、超高强钢主要是通过相变来获得含有硬相马氏体、贝氏体的复相组织, 从而实现材料的强化・即使使用相同的材料化学成分和相同的轧制图1冷却路径对AHSS 钢组织的影响Fig. 1 E ffect of cooling path on micro structure of AHSS steel所以, 在实施N G 2TMCP 的过程中, 如果能够发挥超快冷的优势, 对冷却路径进行适当的控制, 则可以在更大的范围内, 按照人们的需要对材料的组织和性能进行更有效的控制, 甚至开发出全新的轧制过程・件的奥氏体组织产生强烈大变形, 形成细的、强烈硬化的、具有大量缺陷的奥氏体晶粒・对上述奥氏体施以高强度的快速冷却, 直到相变温度点附近, 从而保持奥氏体的硬化状态, 并抑制奥氏体晶粒长大・细小的奥氏体晶粒在适当的冷却条件下, 转变为晶粒大小适度的铁素体和珠光体, 在提高钢筋屈服强度和抗拉强度的同时, 也使其屈强比降低・实现热轧带肋钢筋轧后超快速冷却的关键工艺设备是超快冷水冷器(图2 [7], 水冷器由多节3超快速冷却的工业实现3. 1棒线材超快冷的工业实现在热轧带肋钢筋的精轧连轧过程中, 轧件温度处于再结晶区, 在较高或很高的变形速度下, 轧第7期王国栋:新一代控制轧制和控制冷却技术与创新的热轧过程冷却管组成, 总长度一般不大于20m , 在轧速小于20m/s 时, 水冷器总长度小于13m ・每节冷却管在轧件入口端由环状缝隙喷射一定压力的冷却水, 冷却水与轧件同方向运动, 但是速度高于轧件・冷却水在轧件的出口端流出・由于采用环状缝隙冷却, 轧件冷却均匀, 可以彻底消除现有的余热淬火水冷器存在的大规格产品上冷床后弯曲、小规格堵钢的问题・在大生产条件下可以彻底解决<10mm 热轧直条钢筋4切分轧制的堵钢问题・要保证所使用每一节冷却管的水量充足, 即不用的水管要求关闭冷却水・尽管冷却时间短, 水冷器还是具有前段强冷和后段强冷的区别, 根据轧件的不同规格和成分的区别, 通过调节, 可以在一定范围内调节材料的屈强比・国内现有的余热淬火水冷器, 需要进行改造, 才可以提高冷却效率, 实917图3热连轧过程中的软化现象Fig. 3Softening in hot strip rolling proce ssRAL 针对热轧带钢轧机层流冷却存在的问题, 向企业提出对热轧带钢轧机层流冷却系统进行改造, 增设超快冷装置, 以适应新一代TMCP ・CSP 生产(, , 供应汽车厂、车梁、轿车车轮等产品[9]・攀枝花钢铁公司1450热连轧机的精轧出口增设超快速冷却装置, 投运后证实了该装置具有更好的冷却特性, 已经可以实现Q235,Q345升级和部分高强钢的生产・吸取前两套超快冷装置的经验, 涟钢2250热连轧生产线的控制冷却系统采用了“倾斜式超快冷+ACC ”的混合配置方式, 正在进行安装, 相应的品种开发已经在实验室进行, 钢种包括普通碳锰钢、HSLA 钢、高强钢、管线钢等・图4所示为涟钢2250热连轧生产线上可以实施N G 2TMCP 的冷却系统的配置・其前部10m 左右超快冷装置, 采用缝隙式幕状喷射式喷嘴和圆管喷射式喷嘴混合配置, 冷却水具有一定的压力, 以一定的角度沿轧件运动方向, 喷射到带钢上・倾斜布置的喷嘴, 可以对钢板全宽实行均匀的“吹扫式”冷却, 扫除钢板表面存在的气膜, 达到全板面的均匀核沸腾, 不仅可以大大提高冷却效率, 实现高速率的超快速冷却, 而且可以突破高速冷却时冷却均匀性这一瓶颈问题, 实现板带材全宽、全长上的均匀化的超快速冷却, 因而可以得到平直度极佳的无残余应力的带材产品・为了对超快冷部分进行高精度的控制, 上下集管的供水系统除了使用开闭阀之外, 还配置了冷却水流量控制系统, 可以对上下集管的水量进行精准的控制・超快冷的控制系统已经融入到轧机整个控制冷却系统之中, 通过高精度数学模型的开发、前馈预控和反馈控制的结合以及控制冷却装置硬件的细分, 可以对带钢的冷却进行高精度的控制, 精确控制超快速冷却的终止点・目前尚有几套2000mm 以上宽度的热连轧图2轧后超快冷水冷器的形式Fig. 2Cooling device for ultra fast cooling after rolling该工艺的使用可以做到不改造主要设备, 不需降低作业率, 不需低温轧制, 不需余热淬火・由于强化了冷却效果, 可以提高冷床的冷却效率, 从而提高产量・利用热轧带肋钢筋超快速冷却技术, 可以在少用或者不用合金元素的情况下, 利用335MPa 级的20MnSi 生产HRB400, HRB500螺纹钢筋, 大幅度提高产品质量, 降低生产成本・3. 2热轧带钢超快冷的工业实现现代的热轧带钢采用高速连续大变形轧制过程, 即使在较高的温度下, 也可以通过连续大变形和应变积累, 在轧后得到硬化的、充满“缺陷”的奥氏体・换言之, 在现代的热连轧机上, 即使不用“低温大压下”, 也可以实现奥氏体的硬化・图3所示为Q235钢热连轧过程中发生再结晶的模拟计算结果[8], 可见在热连轧的后部道次再结晶软化受到了极大的抑制[3]・现在的关键是, 尽快开发适用于板带材的超快速冷却装置, 以将奥氏体的硬化状态保持到动态相变点, 避免硬化奥氏体的软化・918东北大学学报(自然科学版第30卷品种的研发与生产・机考虑采用超快冷装置, 以利于减量化和高强化图4涟钢2250热连轧机轧后控制冷却系统的配置Fig. 4Layout of cooling control system after rolling on the hot strip mill in Lian Steel , Hunan , China3. 3中厚板超快冷及其工业实现中厚板轧机与连续式轧机不同, 是可逆式轧制, 且轧后冷却系统与轧机的距离较远, 硬化状态的保持有一定的难度, 但是也有可能利用超快速冷却实现新一代TMCP , 的质量・, 1998年,J FE (原N KK 福山厂采用了所谓的Super 2OLAC (super on 2line accelerated cooling 新型加速冷却系统[10](图5 ・其最大的特点是避开了过渡沸腾和膜沸腾, 实现了全面的核沸腾, 具有可达极限冷却的冷却速率和极高的冷却均匀性・Super 2OLAC 冷却系统的喷嘴与钢板的距离较近, 以一定的角度沿轧制方向将一定压力的水喷射到板面, 将板面残存水与钢板之间形成的气膜吹扫掉, 从而达到钢板和冷却水之间的完全接触, 实现核沸腾・这不仅提高了钢板和冷却水之间的热交换, 达到较高的冷却速率, 而且可以实现钢板的均匀冷却, 大大抑制了钢板由于冷却不均引起的翘曲・统兼有直接淬火和加速冷却两种功能, 是新一代控制冷却系统的重要特征・RAL , ・该方m 长冷却段组成, 全部采用喷嘴倾斜布置的压力喷射式超快速冷却集管・考虑到现有设备改造时与已有ACC 系统的配合与衔接, 最终推出了喷嘴倾斜布置的压力喷射式超快速冷却系统与传统集管层流冷却系统混合配置的方案・前部采用超快冷系统, 长度约8~10m ; 后部采用传统ACC 系统, 长度保持不变・2007年开始, 与河北石家庄敬业钢铁公司(民营企业合作, 在其3000中厚板轧机上装设U FC +ACC 的新式冷却系统, 目前已经投入运行调试(图6 ・鞍钢已经决定, 在其4300中厚板轧机上采用全新的UFC +ACC 冷却系统, 首秦4300中厚板轧机则在其引进硬件系统中预留DQ 装置的位置上装设具有我国自主知识产权的超快冷系统, 与原有的ACC 系统配合, 为实施新一代TMCP 作设备条件的准备・图5J FE 福山厂安装的Super 2OLAC 系统Fig. 5Super 2OLAC system in J FE plant2003年和2004年J FE 仓敷地区水岛厂(即原川崎制铁水岛厂和东日本地区京浜厂也分别采用了Super 2OLAC 系统[11]・由于Super 2OLAC 系统具有很强的冷却能力, 同时又具有很好的冷却均匀性, 所以它既可以实现加速冷却, 又可以实现在线直接淬火・一套系图6安装在敬业公司的中厚板超快冷装置Fig. 6Ultra fast cooling system of the platemill in Jingye corporation , Hebei , China3. 4H 型钢超快冷由于常规控制冷却系统的冷却能力较差, 需要较大的建设长度, 同时翼缘和腹板冷却条件不第7期王国栋:新一代控制轧制和控制冷却技术与创新的热轧过程同, 会造成不同部分极大的温差, 所以我国H 型钢轧机的控制冷却一直是空白, 这在一定程度上限制了H 型钢轧机的技术进步和高附加值减量化产品的开发・目前, 东北大学RAL 正在与有关的厂家合作, 发挥超快冷技术的优势, 对翼缘和腹板等不同部位的冷却装置进行精细化设计, 开发H 型钢超快冷系统・相信通过产学研的密切合作, 具有自主知识产权的H 型钢超快冷系统将取得突破, 为我国H 型钢的升级换代作出贡献・。