高压空冷器Incloy825丝堵产生裂纹
浅析空气冷却器管束的爆裂原因

浅析空气冷却器管束的爆裂原因摘要:针对安装于某A有限公司的牌号为3A21空气冷却器管束,本文从化学成分、金相、气密性试验等检测分析数据为依据,综合分析了其可能爆裂的原因,并提出了的分析意见。
关键词:空气冷却器管束;爆裂;气密性试验;空气冷却器简称空冷器,以空气作为冷却剂,可用作冷却器,也可用作冷凝器。
空冷器主要由管束、支架和风机组成。
管内的热流体通过管壁和翅片与管外空气进行换热,所用的空气通常由通风机供给[1]。
空气冷却器可用于冷却或冷凝,D型系列空气冷却器可与不同制冷剂的压缩冷凝机组配套,用于不同库温的冷库中,作为制冷设备,其中DL型适用于库温为0°左右的冷库,如保存鲜蛋或蔬菜的冷库,DD型适用于库温为-18°左右的冷库,作为肉类、鱼类等冷冻食品的冷藏用,DJ型适用于库温为-25°或低于-25°的冷库,作为鲜肉或鲜鱼制品或调理食品的速冻用[2]。
一、概述当空气与冷却器表面接触时,冷却器的表面与空气之间存在着温差,依据传热学原理,空气的热量将通过冷却器的表面传递给管内的冷媒,空气的温度方得以降低。
在冷却器的表面温度低于被处理空气的露点温度时,空气中的水蒸气被凝结,达到冷却去湿的目的。
目前,国内外广泛使用的空冷器均采用铝材料制成,重量轻,抗振能力强。
通道采用先进的同步分层流散热技术,在保持系统流量不变的前提下,将待消散工质的总流量分为若干个细的小流量。
在每个平行通道之间选用铝材料制作翅片,以增加换热面积,加快传热。
翅片一般用热导率高的材料(最常用的是铝)制成,缠绕或镶嵌到光管上。
为强化空冷器的传热效果,可在进口空气中喷水增湿。
这样既降低了空气温度,又增大了传热系数。
采用空冷器可节省大量工业用水,减少环境污染,降低基建费用。
特别在缺水地区,以空冷代替水冷,可以缓和水源不足的矛盾。
在冷却风扇的作用下,以空气为冷却源,强制加热,使系统介质温度降至理想工作范围,从而提高液压系统的工作稳定性和液压元件的使用寿命。
高压空冷器丝堵孔密封面泄漏的原因分析、预防措施及现场泄漏的解决办法
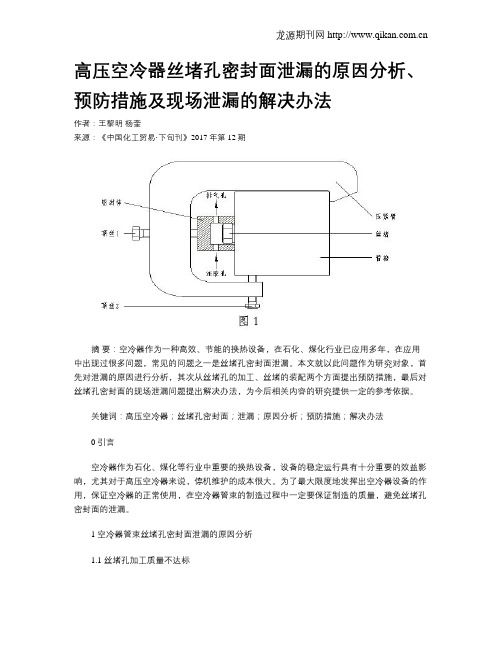
高压空冷器丝堵孔密封面泄漏的原因分析、预防措施及现场泄漏的解决办法作者:王黎明杨奎来源:《中国化工贸易·下旬刊》2017年第12期摘要:空冷器作为一种高效、节能的换热设备,在石化、煤化行业已应用多年,在应用中出现过很多问题,常见的问题之一是丝堵孔密封面泄漏。
本文就以此问题作为研究对象,首先对泄漏的原因进行分析,其次从丝堵孔的加工、丝堵的装配两个方面提出预防措施,最后对丝堵孔密封面的现场泄漏问题提出解决办法,为今后相关内容的研究提供一定的参考依据。
关键词:高压空冷器;丝堵孔密封面;泄漏;原因分析;预防措施;解决办法0 引言空冷器作为石化、煤化等行业中重要的换热设备,设备的稳定运行具有十分重要的效益影响,尤其对于高压空冷器来说,停机维护的成本很大。
为了最大限度地发挥出空冷器设备的作用,保证空冷器的正常使用,在空冷器管束的制造过程中一定要保证制造的质量,避免丝堵孔密封面的泄漏。
1 空冷器管束丝堵孔密封面泄漏的原因分析1.1 丝堵孔加工质量不达标丝堵孔加工质量主要是指“丝堵孔密封面的平面度”和“丝堵孔密封面与丝堵孔轴线的垂直度”的尺寸精度,导致精度不达标的主要原因有两个,一个是机床精度不高,另外一个是丝堵板材料的切屑性能差。
机床精度不高方面,絲堵孔的加工设备主要是摇臂钻床,而摇臂钻床的刚度一般较低,平面度和垂直度的精度的稳定性难易保证。
丝堵板材料的切屑性能差方面,对于不锈钢、镍基合金和其他难加工材料,在采用一般刀具进行孔加工时,容易在刀片刃部产生积屑瘤,进而难以保证平面度和垂直度的精度。
1.2 丝堵装配的工艺不合理在通常情况下,丝堵的装配工艺是先“手动安装丝堵”,在“使用风炮压紧”,而这种工艺仅适用于中低压空冷器管束中丝堵的装配,对于高压空冷器却不适用。
因为在化工生产中,操作压力与温度是影响密封的重要因素,在高温、高压系统中,在高温作用下,工艺介质的黏度小,渗透性增加,介质对垫片的溶解与腐蚀作用将加剧,客观上对密封的要求提高了,同时,密封组合件各部分存在较大温差,由此产生的温差应力不能忽视,它使各部件热膨胀不均匀,操作温度与压力的联合作用要求密封比压增加,否则会导致压紧面松弛,密封比压下降而产生泄漏,生产遇到紧急情况时,系统的温度的急升与急降,使各部件产生膨胀不均,从而也会导致密封失效。
浅谈加制氢联合装置高压空冷器丝堵套的泄漏原因及处理方案
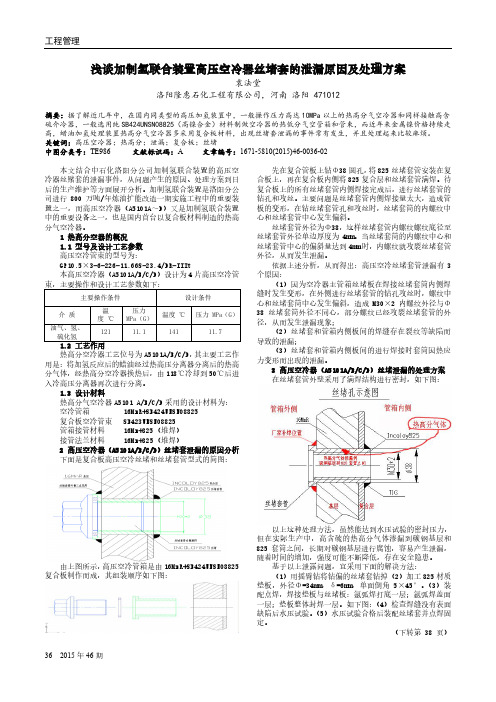
浅谈加制氢联合装置高压空冷器丝堵套的泄漏原因及处理方案袁法堂洛阳隆惠石化工程有限公司,河南 洛阳 471012摘要:据了解近几年中,在国内同类型的高压加氢装置中,一般操作压力高达10MPa 以上的热高分气空冷器和同样接触高含硫介冷器,一般选用纯SB424UNSN08825(高镍合金)材料制做空冷器的热低分气空管箱和管束,而近年来金属镍价格持续走高,蜡油加氢处理装置热高分气空冷器多采用复合板材料,出现丝堵套泄漏的事件常有发生,并且处理起来比较麻烦。
关键词:高压空冷器;热高分;泄漏;复合板;丝堵 中图分类号:TE986 文献标识码:A 文章编号:1671-5810(2015)46-0036-02本文结合中石化洛阳分公司加制氢联合装置的高压空冷器丝赌套的泄漏事件,从问题产生的原因、处理方案到日后的生产维护等方面展开分析。
加制氢联合装置是洛阳分公司进行800万吨/年炼油扩能改造一期实施工程中的重要装置之一,而高压空冷器(A5101A ~D )又是加制氢联合装置中的重要设备之一,也是国内首台以复合板材料制造的热高分气空冷器。
1 热高分空器的概况1.1 型号及设计工艺参数 高压空冷管束的型号为:GP10.5×3-6-226-11.66S-23.4/DR-IIIt本高压空冷器(A5101A/B/C/D )设计为4片高压空冷管束,主要操作和设计工艺参数如下:主要操作条件设计条件介 质 温度 ℃ 压力 MPa (G ) 温度 ℃ 压力 MPa (G )油气、氢、硫化氢12111.114111.71.2 工艺作用热高分空冷器工艺位号为A5101A/B/C/D ,其主要工艺作用是:将加氢反应后的蜡油经过热高压分离器分离后的热高分气体,经热高分空冷器换热后,由118℃冷却到50℃后进入冷高压分离器再次进行分离。
1.3 设计材料热高分气空冷器A5101 A/B/C/D 采用的设计材料为: 空冷管箱 16MnR+SB424UNSN08825 复合板空冷管束 SB423UNSN08825 管箱接管材料 16Mn+825(堆焊) 接管法兰材料 16Mn+825(堆焊)2 高压空冷器(A5101A/B/C/D )丝堵套泄漏的原因分析 下面是复合板高压空冷丝堵和丝堵套管型式的简图:由上图所示,高压空冷管箱是由16MnR+SB424UNSN08825复合板制作而成,其组装顺序如下图:先在复合管板上钻Φ38圆孔,将825丝堵套管安装在复合板上,再在复合板内侧将825复合层和丝堵套管满焊。
加氢装置高压空冷腐蚀分析与对策

加氢装置高压空冷腐蚀分析与对策作者:刘宇轩来源:《中国化工贸易·下旬刊》2018年第09期摘要:近年来,随着原油劣质化、原料油中硫、氮含量增加,导致了炼油生产过程中不断出现设备腐蚀穿孔泄漏、结垢堵塞等一系列问题。
加氢装置的高压空冷系统作为冷却加氢反应油介质的设备因其工作温度区间处于铵盐结晶温度区而成为腐蚀问题的重灾区,据统计发现80%以上的加氢高压空冷系统都存在腐蚀问题。
为此,需要解决加氢工艺操作中腐蚀防护问题,这是提高工艺装置合理性、安全性的基本前提。
关键词:加氢装置;高压空冷;腐蚀;对策1 腐蚀原因分析1.1 高压空冷腐蚀机理分析加氢原料油中存在S、N,经加氢反应器反应后转变为H2S和NH3,而原料油、氢气和注水中或多或少存在可在氢气环境下转变为HCl的Cl,于是生成NH4Cl和NH4HS结晶。
在缺少液态水的状态下,NH4Cl与NH4HS会直接由气相经过冷凝变成固态晶体,从而堵塞管束。
为了防止空冷管束堵塞,通常在高压空冷前增设注水措施,但采用注水冲洗缓解了堵塞却导致了腐蚀,存在不同程度的冲蚀、坑蚀、应力腐蚀等局部腐蚀和泄漏可能。
工作温度处于铵盐结晶温度区间的空冷器流速低的部位存在铵盐结晶浓缩沉积、结垢的问题,NH4Cl与NH4HS晶体有极强的吸水性,吸水后形成垢下腐蚀,形成蚀坑,最终导致穿孔。
1.2 高压空冷选材分析该煤柴油加氢裂化装置高压空冷(A101)管束采用碳钢材质,进口段60cm内衬316L,此种材质相对耐蚀性较差,故在原料中的S、N、Cl等杂质无法有效控制的情况下,发生了NH4Cl与NH4HS垢下腐蚀与铵盐溶液的冲蚀,最终导致空冷管束腐蚀穿孔发生泄漏。
1.3 腐蚀环境加氢裂化装置原料进料中含有硫、氮和氯等杂质,且是在高温、高压、临氢、易燃、易爆且有毒的介质环境下操作。
原料中较高的硫、氮和氯含量,在加氢反应流出物就含有较多的H2S、HCL、NH3,形成H2S+H2+HCL+NH3的腐蚀体系。
冷裂纹产生的原因
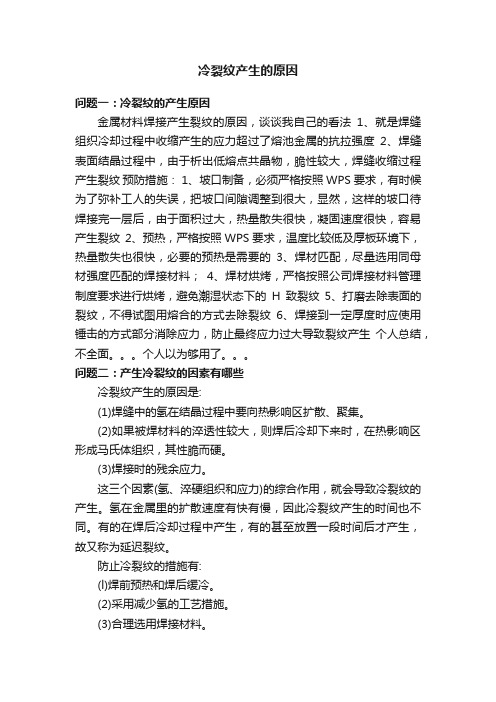
冷裂纹产生的原因问题一:冷裂纹的产生原因金属材料焊接产生裂纹的原因,谈谈我自己的看法1、就是焊缝组织冷却过程中收缩产生的应力超过了熔池金属的抗拉强度2、焊缝表面结晶过程中,由于析出低熔点共晶物,脆性较大,焊缝收缩过程产生裂纹预防措施: 1、坡口制备,必须严格按照WPS要求,有时候为了弥补工人的失误,把坡口间隙调整到很大,显然,这样的坡口待焊接完一层后,由于面积过大,热量散失很快,凝固速度很快,容易产生裂纹2、预热,严格按照WPS要求,温度比较低及厚板环境下,热量散失也很快,必要的预热是需要的3、焊材匹配,尽量选用同母材强度匹配的焊接材料;4、焊材烘烤,严格按照公司焊接材料管理制度要求进行烘烤,避免潮湿状态下的H致裂纹5、打磨去除表面的裂纹,不得试图用熔合的方式去除裂纹6、焊接到一定厚度时应使用锤击的方式部分消除应力,防止最终应力过大导致裂纹产生个人总结,不全面。
个人以为够用了。
问题二:产生冷裂纹的因素有哪些冷裂纹产生的原因是:(1)焊缝中的氢在结晶过程中要向热影响区扩散、聚集。
(2)如果被焊材料的淬透性较大,则焊后冷却下来时,在热影响区形成马氏体组织,其性脆而硬。
(3)焊接时的残余应力。
这三个因素(氢、淬硬组织和应力)的综合作用,就会导致冷裂纹的产生。
氢在金属里的扩散速度有快有慢,因此冷裂纹产生的时间也不同。
有的在焊后冷却过程中产生,有的甚至放置一段时间后才产生,故又称为延迟裂纹。
防止冷裂纹的措施有:(l)焊前预热和焊后缓冷。
(2)采用减少氢的工艺措施。
(3)合理选用焊接材料。
(4)采用适当的工艺参数。
(5)选用合理的装焊顺序。
(6)进行焊后热处理。
问题三:冷裂纹产生的原因是什么产生原因① 焊接接头存在淬硬组织,性能脆化。
② 扩散氢含量较高,使接头性能脆化,并聚集在焊接缺陷处形成大量氢分子,造成非常大的局部压力。
(氢是诱发延迟裂纹的最活跃因素,故有人将延迟裂纹又称氢致裂纹)③ 存在较大的焊接拉应力问题四:简述焊接热裂纹和焊接冷裂纹的形成机理并比较它们各自的特点。
冷处理工艺引起裂纹的原因分析

好多研究证明高速钢刀具、工模具经过超低温处理(-196℃)可显著提高寿命。
有些量具、精密机械零件,为了保证高的尺寸稳定性,需尽量减少残余奥氏体,通常采用零下80℃的冷处理。
一、冷处理工艺引起裂纹的主要因素有:
1、工件淬火后,本身温度较高;或者用过高的热水清洗,工件尚未冷到室温而装入低温箱中。
这时,由于冷却速度加快,部分未转变的奥氏体进一步转变成马氏体,拉应力增大,在低温下材料的脆断抗力降低,当应力超过材料脆断抗力,则导致裂纹。
如果已有显微裂纹,则可能导致裂纹的长大或扩展为宏观裂纹。
2、由于工件尺寸过大,结构复杂,冷处理温度过低(如-196℃),冷处理所用介质冷却较快等因素,或增大原来的内应力,这些都可能形成冷处理裂纹。
冷处理裂纹的特征同淬火裂纹一样,实质是淬火裂纹。
二、防止冷处理裂纹的措施:
1、淬火工件凉透后再装入低温设备中。
2、对形状复杂,薄厚相差悬殊的工件,冷处理前,宜将细薄部分用石棉包扎。
3、冷处理后,待零件温度回升至室温后,立即进行回火和时效。
4、对形状复杂的零件,淬火和冷到室温后可先进行110~130℃保温30~40min的预回火,然后再进行深冷处理。
高压热交换器内套焊接裂纹产生的原因与处理

1 热交换器结构情况氮肥企业合成工段的冷交换器用于对氨冷后的冷循环气进行第二次氨分离,其筒体为扁平钢带绕制,上与端面法兰焊接,下与底封头焊接。
内件分上下两部分,上部为列管换热器,下部为分离器。
为了保证传热效果,外筒内壁端面法兰上焊有一3 mm厚的内套筒,使之与换热器环形挡板之间保持较小的间隙。
同工段的热交换器作用不同,但结构基本一样,均有焊于端面法兰上3 mm厚的内套筒,结构如图1所示。
图1 高压热交换器内套筒与筒体联接示意图1—筒体端面法兰;2—换热内件;3—内套筒;4—联接法兰2 问题根据压力容器检规,使用单位定期聘请有检验资质的单位对容器进行各种检验。
当进行内部检验和全面检验时就必须拆除该类容器的内套筒。
而容器出厂时,筒体法兰与内筒壁为焊接连接。
该筒体法兰材质为20MnMo,内套筒材质为Q—235,属异种钢焊接。
使用厂家在检验后用焊接方法恢复内套筒时,往往因20MnMo材料焊接性能差,导致容器法兰产生裂纹,直至容器报废。
某厂1995年压力容器检验时拆除内套筒后,发现角焊缝热影响区有多条纵横向裂纹,纵向长的60mm,短的10mm;横向裂纹最长达30mm,最小10mm;最深达4.5mm。
常规处理后,渗透检查,裂纹消除,焊接内套筒后投用。
1999年检验时经渗透探伤检测,该焊接处还是布满焊接裂纹。
分析原因是在每次检验后内套筒安装焊接时形成的裂纹。
此次组装时,接受历次教训,在打磨处理、PT检查、强度校验、焊接后,采取乙炔-氧火焰维持一定温度,用硅酸铝棉毡保温的处理方案。
尽管如此,在安装内套筒焊接连接后数10分钟内,俯耳可听到轻微的撕裂爆鸣。
(时值深夜,全厂停车,环境较静)。
因种种原因未作处理,投入使用。
2000年底全厂停车大修,对这台容器进行渗透检查,发现原焊缝处有无数条裂纹,处理打磨深度达10mm,同一部位经多次焊接、打磨,法兰颈部分减薄,检验单位发出重大问题通知书,要求限期更换,更换期限内监控运行。
825镍基合金空冷器丝堵管箱机械加工研究

825镍基合金空冷器丝堵管箱机械加工研究丝堵式管箱是丝堵式空冷器管束的关键部件,由于其特殊的产品结构和较高的精度要求,给机械加工过程造成很大困难,而Incoloy 825材料又存在塑性变形大、切削力大、刀具的铣削磨损a快、加工硬化现象严重等多重因素,更造成管箱的机械加工难度,本文针对这一系列问题,从板材坡口的铣削加工、成品管箱管板与丝堵板的机械加工中出现难点问题进行的研究,通过不断试验改进,最终解决问题,使管箱加工达到图纸设计要求。
标签:Incoloy 825材质丝堵管箱;坡口加工;管孔、丝堵孔加工1、Incoloy 825镍基合金的物理和化学性能镍基合金是化学、石油、有色金属冶炼、航空工业、核能工业领域中耐高温、高压、高浓度等各种苛刻腐蚀环境中较理想的金属材料。
Incoloy 825合金由于富含Cr、Mo、Cu,对氧化性酸和非氧化性酸均有良好的耐腐蚀性能。
尤其对硫酸具有极高的耐腐蚀性。
由于Cr、Mo、Ni含量高,在氯化物环境下的耐点腐蚀性能、耐间隙腐蚀性能、耐应力腐蚀开裂性能优异。
Incoloy 825合金将碳含量控制在极低水准,焊接时不易敏化,且晶间腐蚀敏感性较低。
Incoloy 825合金鎳含量为38-46%,其余主要元素有Fe、Cr、Mo等见下表。
镍基合金应用广泛,主要原因在于,一是镍基合金中可以溶解较多合金元素,且能保持较好的组织稳定性;二是可以形成共格有序的A3B型金属间化合物γ[Ni3(Al,Ti)]相作为强化相,使合金得到有效的强化,获得比铁基高温合金和钴基高温合金更高的高温强度;三是含铬的镍基合金具有比铁基高温合金更好的抗氧化和抗燃气腐蚀能力。
镍基合金含有十多种元素,其中Cr主要起抗氧化和抗腐蚀作用,其他元素主要起强化作用。
由于Incoloy 825含有大量的多种合金元素形成了复合碳化物,其合金化程度很高,使基体的强化效果好,合金的热稳定性高,其机械物理性能见表2;Incoloy 825固溶处理后,组织和性能会更好,一般使用状态经过固溶处理,固溶处理后会形成很稳定的碳化物和特殊碳化物,其共同点是熔点低、硬度低、稳定性好。
1-2 冷裂纹产生原因及对策

1-2 冷裂纹产生原因及对策冷裂纹定义:(GB/T3375-94焊接术语)中是这样规定的:焊接接头冷却到较低温度下(对于钢来说在MS温度以下)时产生的焊接裂纹。
注:MS为马氏体转变起始温度。
冷裂纹一般在焊接低合金高强度钢,中碳钢,合金钢等易淬火钢时容易发生,而低碳钢焊接时遇到较少。
一.冷裂纹的特点1.冷裂纹产生的时间和温度:(1)冷裂纹发生在焊接之后,在冷却过程中或冷却以后产生,形成裂纹的温度在200℃~300℃以下,即马氏体转变的范围。
(2)冷裂纹可以在焊接后立即出现,但也有些可以延迟至几小时,几天,几周,甚至一、二个月之后出现,所以冷裂纹又叫延迟裂纹。
(3)大的冷裂纹不是一下子就生成的,它的生成规律是先发生几处小的(显微的)裂纹,然后逐步向长度或深度上发展,几个小的裂纹陆续连接起来,形成破裂。
(4)某些焊接结构,当小裂纹发展到一定程度后,可能在瞬间内迅速扩大,引起结构整体的突然断裂。
甚至同时产生较大的声响和机械振动。
(5)有潜伏期的冷裂纹属于“延迟开裂”性质,与渗氢钢的延迟开裂极其相似。
都存在以下过程:1)潜伏期2)缓慢扩展期3)突然断裂期三个相连的阶段,且又是一个断断续续的开裂过程。
①断裂速度可相当弹性波的速度,由于能量释放,故常可听到清晰的开裂声音。
②裂纹扩展过程实际上是交错发生的微小潜伏期和瞬时爆发成长过程的组合。
4)试验的放大照片能显示:由于氢脆作用而具有延迟开裂特性,故称“氢致裂纹”或“氢促裂纹”。
2.冷裂纹产生的部位和方向:(1)冷裂纹大多数产生在基本金属上或基本金属与焊缝交界的融合线上,最常见的有焊道下冷裂纹、焊趾冷裂纹和焊根冷裂纹三种形式,部位和方向见下图:(2)它们大多数是纵向裂纹,在少数情况下,也可能有横向裂纹。
a 焊道下裂b 焊趾裂纹c 焊根裂纹d 表面横裂纹3. 外观特点:冷裂纹断面上没有明显的氧化色彩,其裂口发亮。
4. 金相结构:冷裂纹一般为穿晶裂纹,少数情况下也可能沿晶界发生。
加氢裂化高压空冷器腐蚀分析与防护
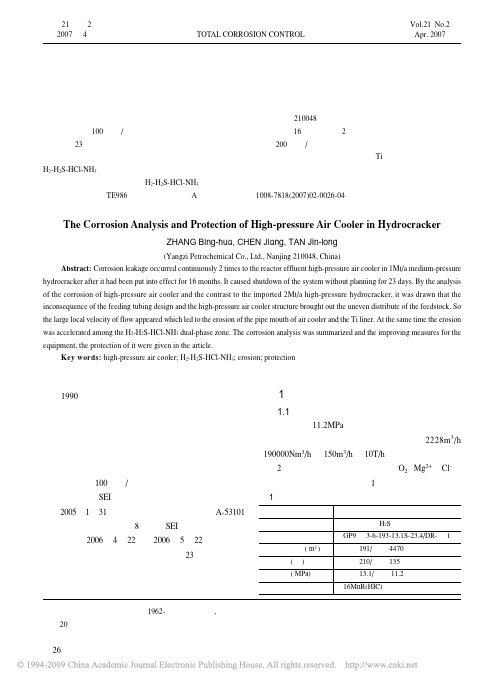
计划停工 23 天。本文对高压空冷器的腐蚀原因进行了分析ቤተ መጻሕፍቲ ባይዱ并和进口 200 万吨 / 年高压加氢裂化装置进行对比分析,认为进料
配管设计和高压空冷器结构型式的不合理,导致进料分配不均匀,局部流速偏大,使空冷器管口和 Ti 衬管产生冲刷腐蚀,在
H2-H2S-HCl-NH3 双相区加快了冲刷腐蚀。在总结经验的基础上,提出了设备改进和防护措施。
胺盐的腐蚀入口管线的腐蚀主要发生在注水点和弯 头部位,有些装置成功采用 Alloy625、800 和 825 材料防 止腐蚀。另外,强调了入口管道布置要绝对对称,否则, 会造成流速不均。
加氢裂化高压空冷器主要参数
置于2005年1月31日投用。反应产物高压空冷器A-53101 是该装置的重要设备,共 8 台,由 SEI 设计、哈尔滨空调 器厂制造。 2006年4月22日和2006年5月22日分别出现 腐蚀泄漏事故,并造成装置非计划停工 23 天,造成巨大 的经济损失。本文对高压空冷器的腐蚀原因进行了分析, 对检修进行总结并提出了设备改进和防护措施。
1990年以来,我国的炼油行业由于油品质量和环保
1 概况
等要求,陆续建设了许多加氢装置,从最早引进技术的
1.1 设备技术参数
茂名加氢裂化,到后来自主设计建设的镇海、齐鲁、金
设计压力 11.2MPa,工艺介质主要包括循环氢、反
山、高桥、金陵、湛江等加氢裂化装置陆续建成并投产。 应生成油和水,额定工况时的处理量分别为 2228m3/h
第 21 卷第 2 期 全2面00腐7 年蚀4控月制
全面腐蚀控制 TOTAL CORROSION CONTROL
Vol.21 No.2 2007 年第 21A卷pr第. 2020期7
加氢裂化高压空冷器腐蚀分析与防护
制氢装置中变气空冷管线腐蚀开裂原因分析及应对措施

发 生腐 蚀 的制 氢装置 中变气空 冷管 线 的材料
为3 0 4不锈 钢 , 牌号为 0 C r l 8 N i 9 。发生 腐 蚀 的构 作者 简介 : 杨 冰( 1 9 8 9一) , 助理 工程师 , 现在 该公 司从事生
图1 裂 纹 处 晶 间 腐 蚀1 . 1 焊 缝处 裂纹 宏观观 察
管线 焊缝 处 裂纹 宏 观 观 察 表 明 , 裂 纹 存 在 于 焊缝 热 影 响 区 内 , 分 布 于 管 帽端 , 垂 直 于 焊缝 , 长
度约 2 0 m m。 1 . 2 裂 纹处 晶界形 貌及 断 口扫描 电镜 形貌
制 氢装置 生产 流程 框 图见 图 3 。
并 从 同溶体沉 淀 出来 , 进 而导 致 品问铬含 量 降低 ,
这 时 由于 晶内与 品 间的 元 素存 在 浓 度 梯 度 , C和
c r 将 向品 问扩 散 , 但 由于 在 4 5 0~ 8 5 0℃ 时 C r 扩 散 的 比 C慢 , 因此 后来 形成 的碳化铬 中的 C r 主要
应 力腐蚀 破裂 是金 属结构 在拉 应力 和特定腐
蚀环 境共 同作 用 下 引起 的破 裂 , 是 应 力与 腐 蚀 介 质共 同作用 的结果 , 要“ 敏感材 料 ” 、 “ 特 定 环境 ” 、 “ 拉 应 力” 个 缺 一 不 可 的 基 本 条 件 。需 要 说 明 的是 , 所谓 特定 环 境 是指 只有 在 一定 的材 料 和环 境 的组 合情 况 下 才 会发 生 这 类 腐蚀 破 坏 , 可 能产 生应 力腐蚀 的环境 介质 见表 3 。
压力容器焊接冷裂纹产生的机理和防止措施

压力容器焊接冷裂纹产生的机理和防止措施焊接在金属压力容器制造过程中是一道主要的工序,随着压力容器的大型化和重型化,焊接在压力容器制造过程中处于关键和重要的工序。
大多数压力容器属于特种设备,其安全运行关系人民的生命及财产安全,因此避免压力容器在制造过程中产生焊接缺陷,是保证压力容器制造质量在运行后安全工作的关键步骤。
1 焊接冷裂纹的分类及产生的基本过程焊接冷裂纹是指焊接接头冷却到较低温度时所产生的裂纹,常见钢材产生的温度为在Ms温度以下或200-300 ℃。
冷裂纹包括:延迟裂纹、淬硬裂纹、低塑性脆化裂纹等,在压力容器制造行业所说的冷裂纹指的是延迟裂纹。
压力容器焊接冷裂纹主要发生在高硬度及高强度的钢材中,如抗拉强度大于等于540MPa以上的材料或者中碳钢、低合金和中合金的高强度钢中。
这些材料在焊接过程中金属熔池溶解了大气或者焊接材料中的氢,加上焊接接头在焊接过程中产生了材料加热时产生的拘束应力,焊缝本身组织淬硬,无法通过塑性变形等方式释放应力,在三种因素的作用下,发生开裂,形成裂纹。
延迟裂纹具有显著的延迟性,分为潜伏期、缓慢扩散期、突然断裂期三个连续的过程,潜伏期有可能几小时、几天、几个月甚至几年,有可能压力容器已投入使用期间,因此更具危险性。
2 冷裂纹的产生原因分析形成冷裂纹的原因主要有以下4 个:(1)焊接接头形成淬硬组织,减小了金属的塑性储备;(2)扩散氢的存在和浓集;(3)焊件钢性大而产生较大的焊接拉伸应力;(4)焊肉存在某种缺陷致使应力集中。
以上这4 个因素,其中含氢量和拉应力是冷裂纹产生的2 个重要因素,但4 个原因的存在相互影响、促进。
它们中可能某一个原因成为冷裂纹的主要因素,然而决不可能是唯一因素。
一般来说,金属内部原子的排列并非完全有序的,而是有许多微观缺陷,在拉应力的作用下,原子氢向高应力区(缺陷部位)扩散聚集。
当氢聚集到一定浓度时,就会破坏金属中原子的结合键,金属内就出现一些微观裂纹,应力不断作用,氢不断地聚集,微观裂纹不断地扩散,直至发展为宏观裂纹,最后断裂。
加氢裂化高压空冷器的防腐现状和对策分析

加氢裂化高压空冷器的防腐现状和对策分析加氢裂化高压空冷器是石油化工生产中常用的重要设备之一,其作用是冷却加氢裂化反应产生的高温高压物料,在生产过程中,加氢裂化高压空冷器需要承受高温、高压、高流速、腐蚀性气体等恶劣工况,因此其防腐工作非常重要。
目前,加氢裂化高压空冷器的防腐现状存在以下问题:由于加氢裂化反应生成物料中存在大量的腐蚀性气体,如硫化氢、硫醇等,这些气体对空冷器金属材料具有很强的腐蚀作用,容易引发金属腐蚀、开裂等问题;由于高温高压工况下,空冷器内外温差较大,容易导致热应力和热疲劳,增加了空冷器的破损风险;空冷器表面容易积聚灰尘、油污等杂质,降低了其散热效果,加速了腐蚀速度;由于工况变化频繁,空冷器的防腐层容易受到破坏,并且修复困难,需要频繁更换。
针对以上问题,可以采取以下对策加以解决:选择适当的金属材料,如不锈钢、镍基合金等,以提高空冷器的耐腐蚀性能;在设计和制造过程中,要注重考虑热应力和热疲劳问题,采用合理的结构设计,减少热应力的产生;加强对空冷器的维护和清洗工作,定期清理表面的油污和杂质,保持其散热效果;加强对防腐层的保护,选用高质量的防腐涂料,并定期检查和修复防腐层的破损部分。
还可以进行加氢裂化高压空冷器的防腐技术改进,如采用新型防腐涂料、优化涂层工艺等,提高空冷器的耐腐蚀性能;加强对加氢裂化高压空冷器的监测和检测工作,及时发现问题,进行修复和更换,避免事故的发生。
加氢裂化高压空冷器的防腐工作对于保障设备的正常运行和生产安全非常重要。
通过加强材料、结构和防腐层的选择与维护,以及技术的改进和监测的加强,可以提高加氢裂化高压空冷器的耐腐蚀性能,延长其使用寿命,减少设备故障,保障生产安全和经济效益的实现。
压力容器焊接制造中冷裂纹的形成机理及防止措施

压力容器焊接制造中冷裂纹的形成机理及防止措施作者:柳红霞来源:《经济技术协作信息》 2018年第22期一、概述压力容器与其他的焊接结构不同,其焊接接头是受压壳体的重要组成部分,承受着与壳体相同的工作压力,经受相同工作介质的物理化学作用,因此对焊接接头的质量提出了相当严格的要求。
压力容器是一种全焊结构,备受压部件(如简体、封头、接管等)都是通过焊接的方式连接在一起的。
如果在焊接过程焊接接头中存在某种缺陷,就可能导致缺陷在焊接残余应力、产品服役时的工作应力或其他工作条件(如腐蚀介质)的联合作用下逐渐扩展,深入到壳体母材并最终导致整台产品的提前失效或破裂。
在工程中,常见的焊接缺陷有裂纹、夹渣、气孔、未焊透、未熔合以及焊缝几何尺寸的偏差。
裂纹一类中,又分为冷裂纹、热裂纹、再热裂纹、层状撕裂和应力腐蚀裂纹等。
本文主要介绍了在焊接制造过程中冷裂纹的形貌特征及产生原理,以及预防和在焊接工艺等方面的控制措施。
二、冷裂纹的形貌特征及形成机理焊接接头中的冷裂纹按其与焊缝轴线的相对位置,可分成平行于焊缝轴线的纵向裂纹、垂直于焊缝轴线的横向裂纹以及与焊缝熔合线平行的热影响区裂纹。
焊接接头中冷裂纹主要在屈服强度大于300MPa的低合金钢和中合金钢中产生。
钢材的强度或合金元素含量越高,产生冷裂纹的可能性越大。
在低碳钢和低碳微合金钢焊接接头中一般不会产生冷裂纹。
冷裂纹通常在焊接接头冷却到100℃以下或在室温下形成。
在某些条件下,冷裂纹在焊接结束后延迟一定的时间才形成。
焊接冷裂纹的形成机理概括的说,主要跟以下三个因素有关:l焊缝金属及热影响区淬硬组织的形成,即马氏体和贝氏体组织的形成。
采用传统的电弧熔焊方法焊接时,焊接接头热影响区被急剧加热到大约1350℃奥氏体化温度,然后随着焊接结束被快速冷却。
由于奥氏体化温度较高,晶粒急剧长大,形成粗大的奥氏体。
此外,由于冷却速度较快,使奥氏体过冷,并在较低的温度下发生马氏体或贝氏体组织相变。
【加氢裂化装置故障分析】加氢裂化装置高压空冷泄漏原因分析及整改措施

【加氢裂化装置故障分析】加氢裂化装置高压空冷泄漏原因分析及整改措施加氢裂化装置高压空冷泄漏原因分析及整改措施加氢裂化装置高压空冷泄漏原因分析及整改措施摘要:中石化天津分公司180万吨/年加氢裂化装置20XX年12月投产,高压空冷在气密过程中管箱丝堵大批量发生泄漏,致使装置反复泄压。
在3年后的装置检修中对高压空冷进行了整改修复,大幅度降低了高压空冷管箱丝堵泄漏率。
关键词:高压空冷泄漏丝堵措施一、高压空冷器的简介高压空冷器系统是加氢裂化装置中的关键设备之一,具有高温、高压、临氢的特点,属于特种设备。
中国石化天津分公司炼油部180万吨/年加氢裂化装置(以下简称2#加氢裂化)是由中石化北京设计院(SEi)进行设计。
a-101是高压空冷器,总共8台,由哈尔滨空调股份有限公司(以下简称哈空调)承接制造。
a-101产品型号为GP10.5×3-6-223-16.6SF-23.4/dR-Ⅲt。
其设计压力为16.6mPa,设计温度为220℃,空冷器结构为水平鼓风式,管束为丝堵式,管箱采用分解管箱。
主题材质(包括管箱、管板、管束)及管束丝堵均为UnSn08825,丝堵垫片选用316L,在20XX年8月2#加氢裂化首次检修,根据工艺生产需求,中石化北京设计院设计增加4台高压空冷器a-100,与a-101形成串联。
管束丝堵材质选用变更为316,其他材质不变。
介质均为热高分气(含高硫油气、H2S、nH3、H2等)。
这种材料具有高镍、中铬、含钼成分,在高压空冷器管束内介质含硫氢化胺、氯化铵腐蚀环境下,具有较好的耐腐蚀性。
二、高压空冷管箱丝堵泄漏及处理1.高压空冷气密过程发生泄漏20XX年12月,2#加氢裂化首次开工,2#加氢裂化进入气密阶段,第一阶段反应系统进行4.0mPa氮气气密,a-101丝堵尚未发现泄漏。
随后进行第二阶段6.0mPa氢气气密,发现有42个管箱丝堵泄漏,但多为渗漏,多为沫沫状,其中有5个丝堵泄漏呈现肥皂泡状泄漏。
压力管道检验中裂纹出现的原因和预防处理
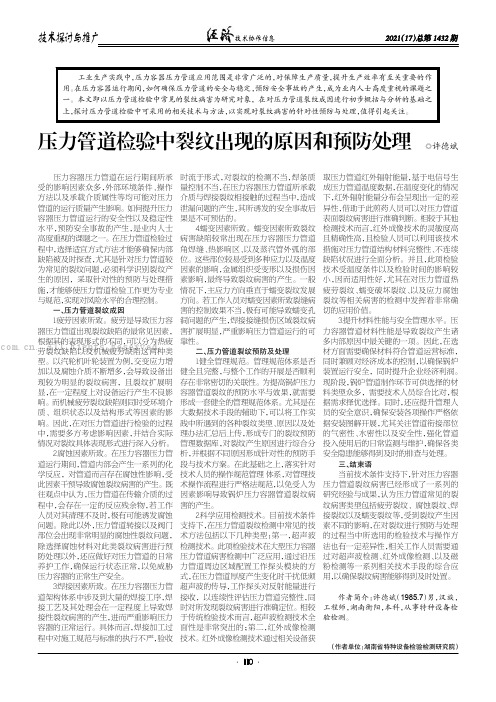
压力管道检验中裂纹出现的原因和预防处理◎许德斌(作者单位:湖南省特种设备检验检测研究院)压力容器压力管道在运行期间所承受的影响因素众多,外部环境条件、操作方法以及承载介质属性等均可能对压力管道的运行质量产生影响。
如何提升压力容器压力管道运行的安全性以及稳定性水平,预防安全事故的产生,是业内人士高度重视的课题之一。
在压力管道检验过程中,选择适宜方式方法才能够确保内部缺陷被及时探查,尤其是针对压力管道较为常见的裂纹问题,必须科学识别裂纹产生的原因,采取针对性的预防与处理措施,才能够使压力管道检验工作更为专业与规范,实现对风险水平的合理控制。
一、压力管道裂纹成因1.疲劳因素所致。
疲劳是导致压力容器压力管道出现裂纹缺陷的最常见因素,根据其的表现形式的不同,可以分为热疲劳裂纹缺陷以及机械疲劳缺陷这两种类型。
以汽轮机叶轮装置为例,交变应力增加以及腐蚀介质不断增多,会导致设备出现较为明显的裂纹病害,且裂纹扩展明显,在一定程度上对设备运行产生不良影响。
而机械疲劳裂纹缺陷则同时受环境介质、组织状态以及结构形式等因素的影响。
因此,在对压力管道进行检验的过程中,需要多方考虑影响因素,并结合实际情况对裂纹具体表现形式进行深入分析。
2.腐蚀因素所致。
在压力容器压力管道运行期间,管道内部会产生一系列的化学反应,对管道而言存在腐蚀性影响,受此因素干预导致腐蚀裂纹病害的产生。
既往观点中认为,压力管道在传输介质的过程中,会存在一定的反应残余物,若工作人员对其清理不及时,极有可能诱发腐蚀问题。
除此以外,压力管道转接以及阀门部位会出现非常明显的腐蚀性裂纹问题,除选择腐蚀材料对此类裂纹病害进行预防处理以外,还应做好对压力管道的日常养护工作,确保运行状态正常,以免威胁压力容器的正常生产安全。
3.焊接因素所致。
在压力容器压力管道架构体系中涉及到大量的焊接工序,焊接工艺及其处理会在一定程度上导致焊接性裂纹病害的产生,进而严重影响压力容器的正常运行。
蒸汽发生器Incoloy825换热管泄漏原因分析

蒸汽发生器Incoloy825换热管泄漏原因分析李金梅;齐文宽;蒋春宏;史伟;杨莉【摘要】采用宏观检查、化学成分分析、显微组织分析、扫描断口观察以及能谱分析等方法,对二联合加氢改质反应流出物蒸汽发生器管板/换热管泄漏原因进行了分析.分析结果表明:该换热管泄漏主要是因为胀接工艺不当,管子与管孔缝隙处发生碱脆引起开裂,开裂后管程介质渗出,在开裂处又形成高温硫化物腐蚀,腐蚀进一步加剧,最终导致设备停用.【期刊名称】《石油化工腐蚀与防护》【年(卷),期】2019(036)004【总页数】4页(P51-54)【关键词】管板;换热管;碱脆;高温硫化物腐蚀【作者】李金梅;齐文宽;蒋春宏;史伟;杨莉【作者单位】兰州兰石检测技术有限公司,甘肃兰州730314;甘肃省机械装备材料表征与安全评价工程实验室,甘肃兰州730314;兰州兰石检测技术有限公司,甘肃兰州730314;甘肃省机械装备材料表征与安全评价工程实验室,甘肃兰州730314;兰州兰石检测技术有限公司,甘肃兰州730314;甘肃省机械装备材料表征与安全评价工程实验室,甘肃兰州730314;兰州兰石检测技术有限公司,甘肃兰州730314;甘肃省机械装备材料表征与安全评价工程实验室,甘肃兰州730314;兰州兰石检测技术有限公司,甘肃兰州730314;甘肃省机械装备材料表征与安全评价工程实验室,甘肃兰州730314【正文语种】中文蒸汽发生器是压水堆核电站蒸汽供应系统的主要换热设备,其运行工况极其恶劣,因此对管子/管板材质、工艺性能及耐蚀性能要求极高。
某蒸汽发生器运行3个月后发现管板与换热管接头有液体泄漏,设备返厂进行壳程水压试验,发现管板焊缝根部对应的管子内表面处泄漏,泄漏管头大部分集中在油气入口。
针对蒸汽发生器管子/管板的泄漏问题,Xu Shugen,Wang Weiqiang和Rongjuan Sui在其论文中均有阐述[1-4],但研究内容均围绕奥氏体不锈钢的应力腐蚀开裂(SCC),该文所论述的换热管材质为Incoloy825(φ19 mm×2.0 mm/2.5 mm),Incoloy825属于Ni-Fe-Cr合金材料,高镍含量使其具有较好的抗应力腐蚀开裂性能,在许多介质中的耐腐蚀性都很好。
空压机支座螺栓孔开裂原因分析_刘迪辉

第 38 卷第 5 期
刘迪辉等: 空压机支座螺栓孔开裂原因分析
1083
部气体压力对壳体的力矩,使空压机壳体受到动载的 作用,引起空压机对支架上施加动载,采用弹簧替代螺 栓,仿真得到空压机与支架之间螺栓的最大工作拉力, 根据机械设计理论得到螺栓的总拉力,再根据作用力 与反作用力的关系,确定螺栓孔的拉力,并理论计算出 螺栓孔的拉应力,找到螺栓孔开裂的原因。
引言
近年来,人们开展了螺纹连接件故障问题的研究。 文献[1] 针对某电厂汽轮机低压缸隔板螺栓孔在正常 运行工况下开裂的问题。对该隔板螺栓孔进行了建模 计算分析,通过应力计算,指出隔板螺栓孔开裂的主要 原因为设计和选材不合理。文献[2]从试验和数值分 析两个方面研究了螺栓预紧力矩对 LY12CZ 铝合金双 盖板对接螺纹联接件微动损伤的影响。文献[3]针对 某重型载货车在山地道路试验过程中,转向器托架在 多个固定螺栓孔处开裂的问题,对 2 个失效的转向器 托架进行了失效零件宏观观察、断口形貌观察和零件 材料的理化 检 验。 文 献[4]通 过 宏 微 观 观 察、能 谱 成
2. 3 定义驱动
因为实验测得传动轴的转速为 615 r / min,所以施
加的驱动为3 690度每秒。
2. 4 定义载荷
2. 4. 1 螺栓垢长度的等效模型
对于支架与空压机之间固定的螺栓,螺栓只发生
弹性变形,可以采用弹簧替代,来仿真螺栓上的拉力。
弹簧的刚度采用螺栓的刚度,计算公式如下
K1
=
EA L
5结论采用动力学仿真软件adams对空压机与支架之间的螺栓进行仿真分析并用弹簧替代螺栓以及对空压机内部的轴承采用接触根据赫兹接触理论设置接触的各个参数仿真出螺栓上的工作拉力根据机械设计理论得到螺栓的总拉力再根据作用力与反作用力的关系确定螺栓孔的拉力并理论计算出螺栓孔的拉应力发现螺栓孔34578的拉应力超过抗拉强度导致螺栓孔开裂
- 1、下载文档前请自行甄别文档内容的完整性,平台不提供额外的编辑、内容补充、找答案等附加服务。
- 2、"仅部分预览"的文档,不可在线预览部分如存在完整性等问题,可反馈申请退款(可完整预览的文档不适用该条件!)。
- 3、如文档侵犯您的权益,请联系客服反馈,我们会尽快为您处理(人工客服工作时间:9:00-18:30)。
第6期
机电技术
59
高压空冷器Incloy825丝堵产生裂纹分析
秦文玲
(中石化南京工程公司,江苏 南京210046)
摘 要:对某炼化公司的高压空冷器Incloy825丝堵产生裂纹的锻件进行宏观检测及金相微观分析;分析了产生裂纹的机理,提出解决丝堵锻造加工过程质量控制的措施。
关键词:Incloy825;裂纹分析; 控制措施
中图分类号: TE965 文献标识码:A 文章编号:1672-4801(2012)06-059-02
某炼化公司新购置用于加氢处理装置的高压空冷器(如图1所示)到安装现场检验及试压时发现丝堵出现质量问题,丝堵头出现裂纹及泄漏(如图2所示)。
丝堵是采用Incloy825合金热轧圆棒锻件制加工制作的。
图1 加氢处理装置的高压空冷器
图2 丝堵头出现裂纹及出现泄漏
针对这一现象,技术人员在现场抽取具有代表性缺陷的3个丝堵(其中2件为丝堵六角帽上有裂纹,1件在试压时发生泄漏)作为试件进行技术分析,分别将其编为1# 试件、2# 试件、3# 试件,经宏观检测及金相微观分析,分析产生裂纹机理,提出解决丝堵锻造加工过程质量控制的方法。
1 宏观检测及金相微观分析
1.1 宏观检测
3件试件全表面渗透检测(PT)显示:1# 丝堵在六方帽上平面及丝扣端下平面均发现有很短的单条裂纹缺陷存在;2# 丝堵在六方帽上平面有宏观裂纹;3# 丝堵在六方帽侧面有宏观裂纹。
裂纹形状均为树枝状,具有热裂纹特征。
1.2 金相微观分析
对3件丝堵进行解剖,并对裂纹处做金相分析,结果显示:
1) 1# 丝堵裂纹处显微组织为奥氏体晶粒度为7.0级,裂纹处于六方帽上平面的中心部位附近,长度约3~4 mm 。
沿裂纹做纵向剖面,发现沿丝堵轴向自上而下存在有宽度为0.7~1 mm 的条状非金属夹杂物,裂纹走向属晶间型(如图3所示)。
2) 2#、3# 丝堵裂纹处的显微组织为奥氏体+碳化物,奥氏体晶粒度为4级,其中碳化物呈连续或不连续形态存在。
2# 丝堵六方帽上平面处的晶粒度基本上呈不规则的严重扭曲变形(如图4所示);3# 的晶粒呈粗细不均匀态(如图5所示)。
2 产生裂纹机理分析
丝堵棒料是由某特钢材料有限公司按照美国ASME SB425标准中UNS NO8825合金棒料冶炼
图3 1# 丝堵裂纹处显微组织(100×) 图4 2# 丝堵裂纹处显微组织(100×) 图5 3# 丝堵裂纹处显微组织(100×)
作者简介:秦文玲(1971-),女,工程师,主要从事石化工程设备管理工作。
机电技术 2012年12月
60
轧制而成的公称直径为30 mm 的圆棒料,该公司Incoloy825合金棒料生产流程为:冶炼→锻造→热轧→固溶退火,其交货状态为热轧后固溶退火。
其
化学成分、力学性能及交货状态完全符合美国ASME SB425标准中UNS NO8825标准要求(表1、表2所示)。
表1 Incoloy825化学成份
元素 C Cr Ni Fe Mo Cu AL Ti SI Mn P S 标准值
≤0.05 19.5~23.5 38.0~45.0 余量 2.5~3.5 1.5~3.0 ≤0.200.60~1.20
≤0.50 ≤1.00 ≤0.03≤0.030实测值 0.04
21.78
40.50
2.74
1.57 0.14
0.86
0.33 0.28 0.011
0.008
表2 Incoloy825机械性能及用途
性能项目 抗拉强度/MPa
屈服强度/MPa
伸长率固溶处理温度/℃
适用温度/℃
适用介质
标准值
≥590
≥240
≥30
实测值 650
270 50.0
1000~1050 -240~650
耐氧化物应力腐蚀及氧化-还原复合介质腐
蚀(多种离子的硫酸环境)
从Incoloy825金属的化学成分及其机械性能看出,该材料具有较强的塑韧性和延展性,可锻性强,易于锻制坯件。
因此按照标准工艺生产是不容易出现裂纹等缺陷的。
根据1# 丝堵的裂纹纵横剖面分析,其条状非金属夹杂物在从锻坯热轧成园棒时就已经存在。
产生原因应为:钢锭浇帽口中心为非金属夹杂物聚集处,在钢锭切除浇冒口时,未将该部分切除干净,以致于在随后锻造坯及热轧圆钢棒时这些非金属夹杂物还存在于中心部位附近,圆钢截取丝堵毛坯料后,在对毛坯料锻制六方帽时,沿条状非金属夹杂物产生裂纹,并沿丝堵轴向自上而下形成贯穿性缺陷,这也是该丝堵在设备打压时沿贯穿性缺陷产生泄漏的原因。
从2#、3# 丝堵裂纹处的金相分析知,裂纹处存在有碳化物,这是由于Incloy825是一种高Cr 、Mo 成分的合金,在加热到950~1140 ℃进行模锻六方帽过程中,部分丝堵毛坯料在模锻锻打时温度控制不好,模锻时温度较低,致使强碳化物形成元素Cr 、Mo 与碳结合并在晶界析出,使晶界脆性增加,抗冲击能力下降。
在锻打外力的作用下,从圆棒料形成六方帽变成大的部分晶界产生热脆性裂纹,并扩展成宏观裂纹,同时由于锻打时温度过低,造成晶粒严重扭曲变形和晶粒度的严重不均匀性,这一现象只产生在变形严重的六方帽部分,而丝堵的丝扣部分由于未发生形变过程,故不存在上
述情况,即裂纹只产生在六方帽部分。
3 丝堵锻造加工过程质量控制的措施
丝堵是加氢处理装置的高压空冷器的关键零部件之一,必须严格丝堵锻造加工过程的质量控制。
在制造时要加强质量保证体系的有效运转。
从原材料到货检验、锻造工艺制定、锻造过程工艺控制,以及成品检验等方面加强质量管理。
具体从以下几个方面保证产品质量。
1) 对到货圆棒严格验收。
做好材料化学成分、机械性能、金相组织、致密性等方面的复验,确保原材料相关符合标准要求;
2) 严格锻造工艺的编制和审核,加强产品试样的试制和验收,确保编制的锻造工艺符合实际生产的需要,真正起到指导生产的作用。
3) 加强锻造过程的工艺纪律的执行,确保锻造加热温度控制到位,避免终锻温度较低,在Incloy825合金处于塑性较差时锻造,致使裂纹产生,甚至产生贯穿性缺陷。
4) 加强成品检验。
对于锻造加工完成的产品,严格按照标准检验,检验不合格的成品绝不能放松;
5) 提高操作人员、质量检验人员技术素质和工作责任心。
选择岗位技术考核合格,熟练掌握锻造工艺的操作人员,以及熟练掌握检验方法和标准的质量检验人员。
参考文献:
[1] 程巨强,刘志学.金属锻造加工基础[M].北京:化学工业出版社,2012.
[2] 陈迎华,刘长师.锻造加热缺陷分析及工艺预防措施.[J].金属加工(热加工),2012(15). [3] 桃泽坤.锻造工艺学与模具设计(第2版)[M].西安:西北工业大学出版社,2007.。