UG加工叶片泵
叶片泵工作原理及应用
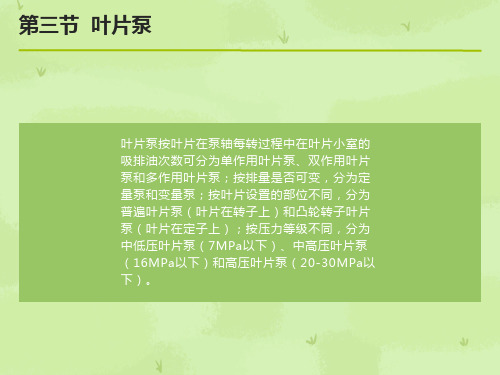
排量与流量计算
双作用叶片泵的排量为
式中,R,r-分别为定子圆弧部分的长短半径 θ-叶片的倾角 S-叶片的厚度
排量与流量计算
双作用叶片泵的实际流量为
叶片与流量脉动关系
叶片泵流量脉动率与叶片数、叶片厚度及叶片在槽内运动的加、减速度成正比。从转子强度与降低流量脉动两方面考虑,叶片数应该越少越好。但叶片数必须同过渡曲线形状匹配,且满足密封容腔的分隔要求,一般取8-18,以12、16为最佳。
柱销叶片方式
因此,为减小定子内表面的磨损及提高工作压力,采用以下措施:
02
03
04
01
2 改善叶片受力状况
某单作用叶片泵转子外径d=80mm,定子内径D=85mm,叶片宽度B=28mm,调节变量时定子和转子之间的最小间隙为0.5mm。求
该泵排量为V1=15mL/r时的偏心量e1
该泵的最大可能排量Vmax
一、单作用叶片泵
1-压油口 2-转子 3-定子 4-叶片 5—吸油口
叶片泵的工作原理如图1所示。泵的结构包括:转子、定子、叶片、配油盘和端盖等。定子的内表面是圆柱形孔。转子和定子之间存在偏心。
图1 双作用叶片泵工作原理
1.单作用叶片泵的工作原理
1.单作用叶片泵的工作原理
图1 双作用叶片泵工作原理
双作用叶片泵的工作原理
(二)双作用叶片泵的结构特点
图3.3.4 双作用叶片泵工作原理 1-定子 2-压油口 3-转子 4-叶片 5-吸油口
(1)定子和转子是同心的
(2)转子每转一周,每个密封工作腔完成吸油和压油动作各两次,所以称为双作用叶片泵
(3)泵的两个吸油区和两个压油区径向对称,作用在转子上的液压力径向平衡,所以又称作平衡式叶片泵
(整理)叶片泵设计
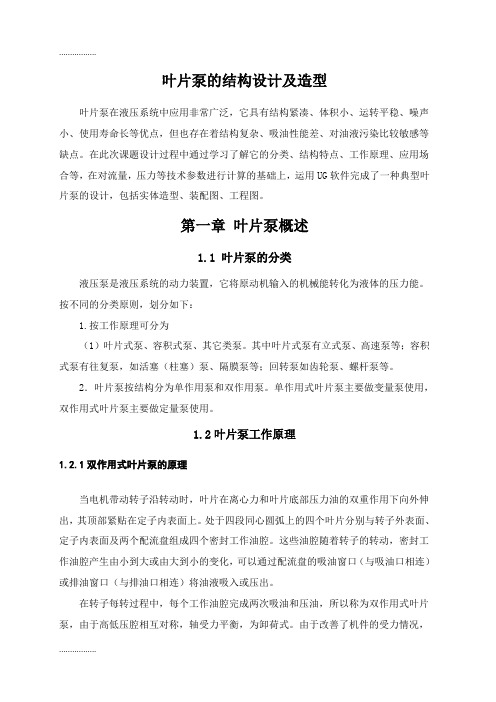
叶片泵的结构设计及造型叶片泵在液压系统中应用非常广泛,它具有结构紧凑、体积小、运转平稳、噪声小、使用寿命长等优点,但也存在着结构复杂、吸油性能差、对油液污染比较敏感等缺点。
在此次课题设计过程中通过学习了解它的分类、结构特点、工作原理、应用场合等,在对流量,压力等技术参数进行计算的基础上,运用UG软件完成了一种典型叶片泵的设计,包括实体造型、装配图、工程图。
第一章叶片泵概述1.1 叶片泵的分类液压泵是液压系统的动力装置,它将原动机输入的机械能转化为液体的压力能。
按不同的分类原则,划分如下:1.按工作原理可分为(1)叶片式泵、容积式泵、其它类泵。
其中叶片式泵有立式泵、高速泵等;容积式泵有往复泵,如活塞(柱塞)泵、隔膜泵等;回转泵如齿轮泵、螺杆泵等。
2.叶片泵按结构分为单作用泵和双作用泵。
单作用式叶片泵主要做变量泵使用,双作用式叶片泵主要做定量泵使用。
1.2叶片泵工作原理1.2.1双作用式叶片泵的原理当电机带动转子沿转动时,叶片在离心力和叶片底部压力油的双重作用下向外伸出,其顶部紧贴在定子内表面上。
处于四段同心圆弧上的四个叶片分别与转子外表面、定子内表面及两个配流盘组成四个密封工作油腔。
这些油腔随着转子的转动,密封工作油腔产生由小到大或由大到小的变化,可以通过配流盘的吸油窗口(与吸油口相连)或排油窗口(与排油口相连)将油液吸入或压出。
在转子每转过程中,每个工作油腔完成两次吸油和压油,所以称为双作用式叶片泵,由于高低压腔相互对称,轴受力平衡,为卸荷式。
由于改善了机件的受力情况,所以双作用叶片泵可承受的工作压力比普通齿轮泵高,一般国产双作用叶片泵的公称压力为51063 pa 。
图1.1 双作用叶片泵工作原理1— 定子;2—压油口;3—转子;4—叶片;5—吸油口1.2.2单作用叶片泵的原理单作用叶片泵的工作原理如图所示,单作用叶片泵由转子1、定子2、叶片3和端盖等组成。
定子具有圆柱形内表面,定子和转子间有偏心距。
ug加工叶轮编程步骤
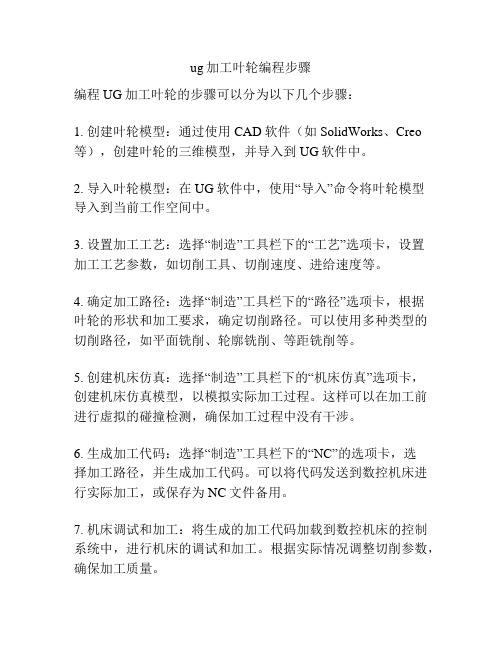
ug加工叶轮编程步骤
编程UG加工叶轮的步骤可以分为以下几个步骤:
1. 创建叶轮模型:通过使用CAD软件(如SolidWorks、Creo 等),创建叶轮的三维模型,并导入到UG软件中。
2. 导入叶轮模型:在UG软件中,使用“导入”命令将叶轮模型
导入到当前工作空间中。
3. 设置加工工艺:选择“制造”工具栏下的“工艺”选项卡,设置
加工工艺参数,如切削工具、切削速度、进给速度等。
4. 确定加工路径:选择“制造”工具栏下的“路径”选项卡,根据
叶轮的形状和加工要求,确定切削路径。
可以使用多种类型的切削路径,如平面铣削、轮廓铣削、等距铣削等。
5. 创建机床仿真:选择“制造”工具栏下的“机床仿真”选项卡,
创建机床仿真模型,以模拟实际加工过程。
这样可以在加工前进行虚拟的碰撞检测,确保加工过程中没有干涉。
6. 生成加工代码:选择“制造”工具栏下的“NC”的选项卡,选
择加工路径,并生成加工代码。
可以将代码发送到数控机床进行实际加工,或保存为NC文件备用。
7. 机床调试和加工:将生成的加工代码加载到数控机床的控制系统中,进行机床的调试和加工。
根据实际情况调整切削参数,确保加工质量。
8. 检查与验证:加工完成后,使用测量仪器进行尺寸检查,验证工件的几何精度是否满足要求。
以上为UG加工叶轮的一般步骤,具体的操作和参数设置可能会因叶轮形状和加工要求的不同而有所变化。
叶片泵的工作原理

叶片泵的工作原理
叶片泵是一种常用的离心泵,它通过叶片的旋转来实现液体的吸入和排出。
其
工作原理主要包括叶片泵的结构和工作过程两个方面。
首先,我们来看一下叶片泵的结构。
叶片泵由泵壳、叶轮、泵轴、轴承和密封
件等部件组成。
泵壳是叶片泵的主体,内部空间用来容纳叶轮和液体。
叶轮是叶片泵的核心部件,它由叶片、叶轮盘和轴套组成。
泵轴是叶片泵的传动部件,通过电机带动泵轴旋转,进而带动叶轮旋转。
轴承起到支撑和定位泵轴的作用,保证泵轴的正常运转。
密封件用来防止泵内液体外泄,保证泵的密封性能。
叶片泵的工作过程如下,当电机启动时,泵轴开始旋转,叶轮也随之旋转。
液
体在泵壳内形成旋涡,被叶轮的叶片吸入。
随着叶轮的旋转,液体被甩到泵壳的出口处,再经过泵壳的出口排出。
整个工作过程中,叶片泵通过离心力将液体从吸入口输送到排出口,实现了液体的输送。
叶片泵的工作原理可以用一个简单的比喻来形象地描述,就好比一个旋转的扇叶,当扇叶旋转时,空气被吸入并排出,形成了气流。
叶片泵也是通过叶轮的旋转来实现液体的吸入和排出,实现了液体的输送。
叶片泵的工作原理十分简单,但其在工程领域中的应用却十分广泛。
叶片泵适
用于输送清水、污水、油类和化工液体等,广泛应用于工业生产、城市供水、排水排污等领域。
其结构简单、运行可靠、维护方便,是一种性能优越的泵类产品。
总的来说,叶片泵的工作原理是通过叶轮的旋转来实现液体的吸入和排出,利
用离心力将液体输送到指定位置。
其结构简单、运行可靠,适用于多种液体的输送,是一种性能优越的泵类产品。
基于UG10.0整体叶轮数控成形仿真研究
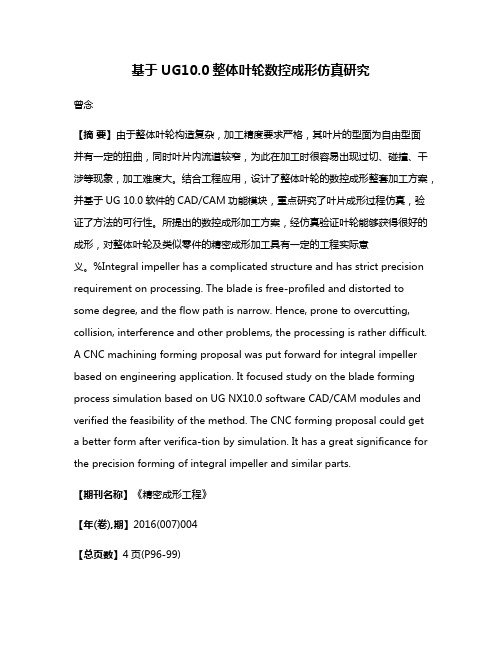
基于UG10.0整体叶轮数控成形仿真研究曾念【摘要】由于整体叶轮构造复杂,加工精度要求严格,其叶片的型面为自由型面并有一定的扭曲,同时叶片内流道较窄,为此在加工时很容易出现过切、碰撞、干涉等现象,加工难度大。
结合工程应用,设计了整体叶轮的数控成形整套加工方案,并基于UG 10.0软件的CAD/CAM功能模块,重点研究了叶片成形过程仿真,验证了方法的可行性。
所提出的数控成形加工方案,经仿真验证叶轮能够获得很好的成形,对整体叶轮及类似零件的精密成形加工具有一定的工程实际意义。
%Integral impeller has a complicated structure and has strict precision requirement on processing. The blade is free-profiled and distorted to some degree, and the flow path is narrow. Hence, prone to overcutting, collision, interference and other problems, the processing is rather difficult.A CNC machining forming proposal was put forward for integral impeller based on engineering application. It focused study on the blade forming process simulation based on UG NX10.0 software CAD/CAM modules and verified the feasibility of the method. The CNC forming proposal could get a better form after verifica-tion by simulation. It has a great significance for the precision forming of integral impeller and similar parts.【期刊名称】《精密成形工程》【年(卷),期】2016(007)004【总页数】4页(P96-99)【关键词】涡轮叶片;自由型面;数控仿真;CAD/CAM;UGNX【作者】曾念【作者单位】自贡市职业培训学院,四川自贡 643000【正文语种】中文【中图分类】TH164叶轮类零件在矿山、军工、船舶、航空等许多行业领域中应用广泛,如风机和飞机发动机叶轮、水泵叶轮等,也是这些机械设备的核心部件,其制造技术水平和制造质量将直接决定该设备的整体性能和稳定性。
叶片泵的工作原理
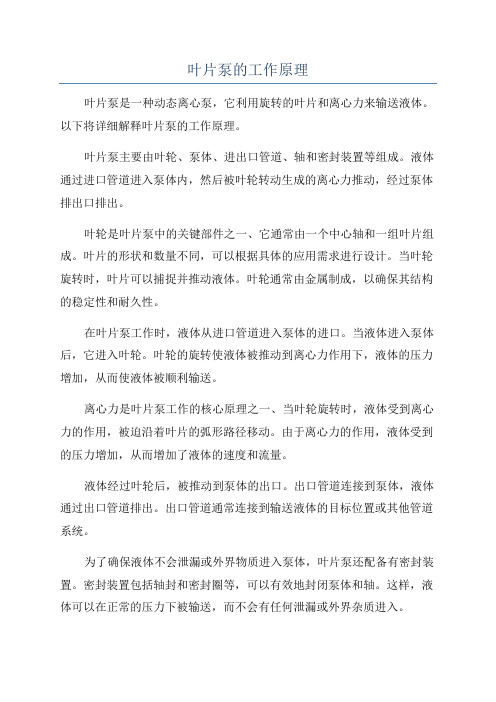
叶片泵的工作原理叶片泵是一种动态离心泵,它利用旋转的叶片和离心力来输送液体。
以下将详细解释叶片泵的工作原理。
叶片泵主要由叶轮、泵体、进出口管道、轴和密封装置等组成。
液体通过进口管道进入泵体内,然后被叶轮转动生成的离心力推动,经过泵体排出口排出。
叶轮是叶片泵中的关键部件之一、它通常由一个中心轴和一组叶片组成。
叶片的形状和数量不同,可以根据具体的应用需求进行设计。
当叶轮旋转时,叶片可以捕捉并推动液体。
叶轮通常由金属制成,以确保其结构的稳定性和耐久性。
在叶片泵工作时,液体从进口管道进入泵体的进口。
当液体进入泵体后,它进入叶轮。
叶轮的旋转使液体被推动到离心力作用下,液体的压力增加,从而使液体被顺利输送。
离心力是叶片泵工作的核心原理之一、当叶轮旋转时,液体受到离心力的作用,被迫沿着叶片的弧形路径移动。
由于离心力的作用,液体受到的压力增加,从而增加了液体的速度和流量。
液体经过叶轮后,被推动到泵体的出口。
出口管道连接到泵体,液体通过出口管道排出。
出口管道通常连接到输送液体的目标位置或其他管道系统。
为了确保液体不会泄漏或外界物质进入泵体,叶片泵还配备有密封装置。
密封装置包括轴封和密封圈等,可以有效地封闭泵体和轴。
这样,液体可以在正常的压力下被输送,而不会有任何泄漏或外界杂质进入。
叶片泵可以在水泵系统、石油、化工、制药、食品加工和造纸等领域中广泛应用。
它们具有结构简单、运行可靠、体积小、重量轻等优点。
叶片泵的工作原理基于旋转叶片和离心力的作用,通过这一原理可以高效地输送液体。
总而言之,叶片泵通过旋转的叶片和离心力来推动液体。
液体通过进口管道进入泵体并经过叶轮,然后在离心力作用下被推动,最终通过出口管道排出。
密封装置确保液体输送安全可靠。
叶片泵因其结构简单、运行可靠被广泛应用于不同的工业领域。
叶片泵
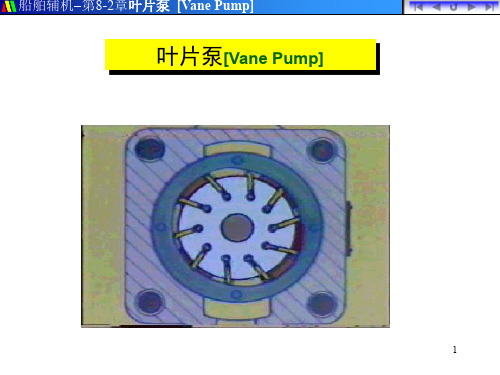
4、双作用叶片泵的结构特点
YB型叶片泵是国产性能较好的一种双作用叶片泵,容积效 率可达90%以上。结构如图以此为实例,再对双作用叶 片泵的结构特点作一下了解、归纳。
16
船舶辅机第8-2章叶片泵 [Vane Pump]
4、双作用叶片泵的结构特点
定子、转子和叶片
定子型线由4段圆弧和4段过渡曲线构成。过渡曲线前半 段是等加速曲线,后半段是等减速曲线,以降低叶片在 槽中的加速度,防止冲击。
10
船舶辅机第8-2章叶片泵 [Vane Pump]
3、排量和流量的计算
双作用叶片泵的排量计算简图如图8-24-1所示 因为叶片每伸缩一次,每两叶片间油液的排出量为 : V密maxV密min ;所以(V密max—V密min)Z即泵一转压出油液的体积, 即等于一环形体积。
图8-24-1双作用叶片泵排量计算简图
R:内滑力(使叶片向内滑 移)
T=NSin β
β
图8-26-1
R=NCos β
在一定的位置上N是不变 的,β增大:侧推力T减小 (减小弯曲)、内滑力R增 大(不被卡阻)。
26
船舶辅机第8-2章叶片泵 [Vane Pump]
(3)、叶片的倾角和倒角
图8-26
叶片与径向的夹 角为前倾角()。
有前倾角后,压 力角
基于UG NX6.0的整体叶轮数控加工仿真校验与后置处理

基于UG NX6.0的整体叶轮数控加工仿真校验与后置处理4.4.1 整体叶轮数控加工路径规划叶轮整体数控铣削加工是指轮廓与叶片在同一毛坯上铣削加工成形。
其加工过程大致包括以下几个主要工序:1.粗加工叶轮流道曲面;2.粗加工叶片曲面;3.叶片精加工;加工。
下面对其路径规划方法分别讨论。
1)创建整体叶轮数控加工父级组。
打开已经建构的整体叶轮三维CAD文件,进入UG加工界面,选择“mill_muti-axis(多轴铣削)”CAM加工配置模板,先后创建程序组、几何组、刀具组和方法组,为下面的加工仿真做准备,具体如下:a.创建程序组。
程序组是用于组织各加工操作和排列各操作在程序中的次序。
由于在单个叶片的多轴加工程序编制后,要使用旋转复制功能生成其余叶片的加工程序,因此这里先采用UG 缺省的程序组,待全部叶片加工程序完成后再统一修改、管理。
b.创建几何组。
在“导航器”中选择“几何视图”功能,进入几何视图工作界面,设置叶轮的圆柱圆心点为加工坐标系位置(双击MCS_MILL 在CSYS 状态下单击点对话框将捕捉类型设置为“圆弧中心/椭圆中心/球心”并将加工坐标系移至到圆心点),如图4.11所示;在铣削几何体中选择已经车削完成的回转体作为毛坯几何体,如图4.12所示c.创建刀具组根据前面已经确定的刀具类型和相关刀具参数,利用“创建刀具”功能,分别创建粗、精加工刀具,并且从内定库中检索刀具夹持器,创建刀具夹持器,本文中选取了库代号为“HLD001_00041”的刀具夹持器。
由于上一节中对刀具选择已作了比较详细的论述,这里不再重复,且此步的操作比较简单。
e.创建方法组由于叶片及流道曲面加工采用了表面积驱动方法,不便设置统一的加工余量、几何体的内外公差、切削步距和进行速度等参数,先选用内定的“METHOD ”加工方法,可根据需要再设置上述加工参数。
2)粗加工叶轮流道曲面通过可变轮廓铣程序控制驱动方法和刀具轴,根据叶轮流道曲面的加工要求创建多轴联动粗加工程序。
叶片泵原理简介
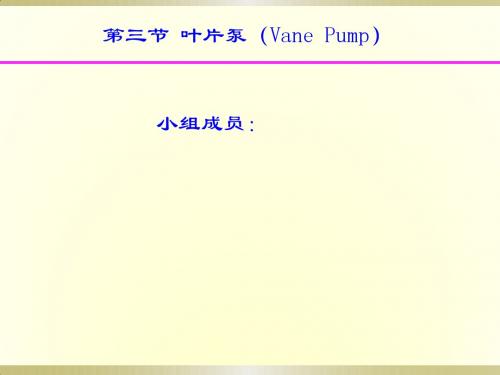
第三节 叶片泵
谢谢
改变偏心距即改变排量
第三节 叶片泵 二、单作用叶片泵 2.流量计算
V D / 2 e D / 2 e b 2 D e b
2 2
q 2beDnv
式中,
(4-13)
b-叶片宽度;
e-转子偏心距;
D-定子内径。
*忽略叶片厚度
第三节 叶片泵 二、单作用叶片泵
第三节 叶片泵 三、双作用叶片泵 1. 工作原理 转子和定子同心放置
定子内表面由 4条封闭曲线(圆弧曲线)
4条工作曲线(过渡曲线)
双作用泵: 转子转一周,叶片伸缩两次 完成两次吸油压油 平衡式: 吸油区、压油区径向对称, 转子所受径向力平衡
第三节 叶片泵 三、双作用叶片泵 2.流量计算
V 2b( R 2 r 2 ) q 2b( R 2 r 2 )nv
第三节 叶片泵 一、概述
单作用变量叶片泵
双作用叶片马达
第三节 叶片泵 二、单作用叶片泵
1. 工作原理
3 2 1 6 4
组成:
定子(3)
转子(2)
叶片(4) 配油盘(5) 端盖
5
压油口(1) 吸油口(6)
第三节 叶片泵 二、单作用叶片泵
单作用泵:
转子每转一周,每个叶片伸缩 一次,完成一次吸油压油 非平衡式: 转子受单方向不平衡作用力, 轴负载大 变量泵:
第三节 叶片泵 四、限压式变量叶片泵
压力-流量曲线
q
pmax
pc ks x0 emax e0 / Ax
k s ( x0 emax ) k Ax s kl kq
A
q
qt
叶片泵的结构设计及造型 叶片泵毕业设计
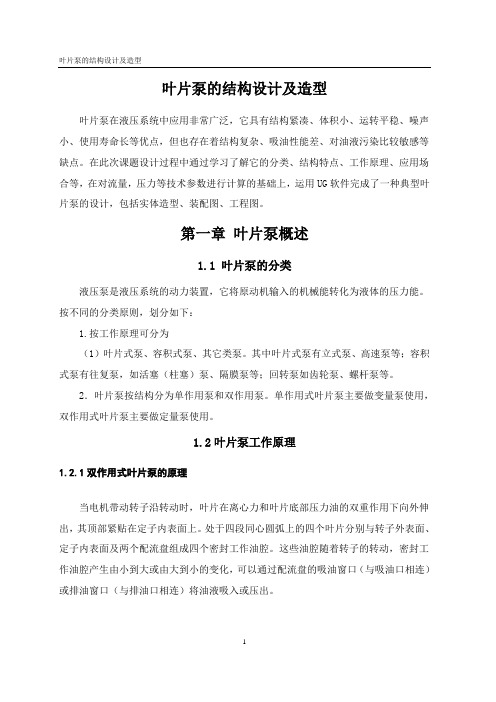
叶片泵的结构设计及造型叶片泵在液压系统中应用非常广泛,它具有结构紧凑、体积小、运转平稳、噪声小、使用寿命长等优点,但也存在着结构复杂、吸油性能差、对油液污染比较敏感等缺点。
在此次课题设计过程中通过学习了解它的分类、结构特点、工作原理、应用场合等,在对流量,压力等技术参数进行计算的基础上,运用UG软件完成了一种典型叶片泵的设计,包括实体造型、装配图、工程图。
第一章叶片泵概述1.1 叶片泵的分类液压泵是液压系统的动力装置,它将原动机输入的机械能转化为液体的压力能。
按不同的分类原则,划分如下:1.按工作原理可分为(1)叶片式泵、容积式泵、其它类泵。
其中叶片式泵有立式泵、高速泵等;容积式泵有往复泵,如活塞(柱塞)泵、隔膜泵等;回转泵如齿轮泵、螺杆泵等。
2.叶片泵按结构分为单作用泵和双作用泵。
单作用式叶片泵主要做变量泵使用,双作用式叶片泵主要做定量泵使用。
1.2叶片泵工作原理1.2.1双作用式叶片泵的原理当电机带动转子沿转动时,叶片在离心力和叶片底部压力油的双重作用下向外伸出,其顶部紧贴在定子内表面上。
处于四段同心圆弧上的四个叶片分别与转子外表面、定子内表面及两个配流盘组成四个密封工作油腔。
这些油腔随着转子的转动,密封工作油腔产生由小到大或由大到小的变化,可以通过配流盘的吸油窗口(与吸油口相连)或排油窗口(与排油口相连)将油液吸入或压出。
在转子每转过程中,每个工作油腔完成两次吸油和压油,所以称为双作用式叶片泵,由于高低压腔相互对称,轴受力平衡,为卸荷式。
由于改善了机件的受力情况,所以双作用叶片泵可承受的工作压力比普通齿轮泵高,一般国产双作用叶片泵的公称压力为51063 pa 。
图1.1 双作用叶片泵工作原理1— 定子;2—压油口;3—转子;4—叶片;5—吸油口1.2.2单作用叶片泵的原理单作用叶片泵的工作原理如图所示,单作用叶片泵由转子1、定子2、叶片3和端盖等组成。
定子具有圆柱形内表面,定子和转子间有偏心距。
叶片泵的工作原理及结构
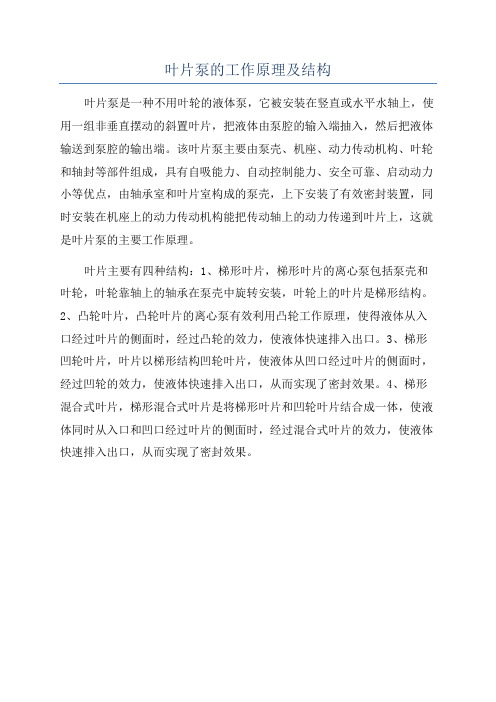
叶片泵的工作原理及结构
叶片泵是一种不用叶轮的液体泵,它被安装在竖直或水平水轴上,使用一组非垂直摆动的斜置叶片,把液体由泵腔的输入端抽入,然后把液体输送到泵腔的输出端。
该叶片泵主要由泵壳、机座、动力传动机构、叶轮和轴封等部件组成,具有自吸能力、自动控制能力、安全可靠、启动动力小等优点,由轴承室和叶片室构成的泵壳,上下安装了有效密封装置,同时安装在机座上的动力传动机构能把传动轴上的动力传递到叶片上,这就是叶片泵的主要工作原理。
叶片主要有四种结构:1、梯形叶片,梯形叶片的离心泵包括泵壳和叶轮,叶轮靠轴上的轴承在泵壳中旋转安装,叶轮上的叶片是梯形结构。
2、凸轮叶片,凸轮叶片的离心泵有效利用凸轮工作原理,使得液体从入口经过叶片的侧面时,经过凸轮的效力,使液体快速排入出口。
3、梯形凹轮叶片,叶片以梯形结构凹轮叶片,使液体从凹口经过叶片的侧面时,经过凹轮的效力,使液体快速排入出口,从而实现了密封效果。
4、梯形混合式叶片,梯形混合式叶片是将梯形叶片和凹轮叶片结合成一体,使液体同时从入口和凹口经过叶片的侧面时,经过混合式叶片的效力,使液体快速排入出口,从而实现了密封效果。
叶片泵的工作原理
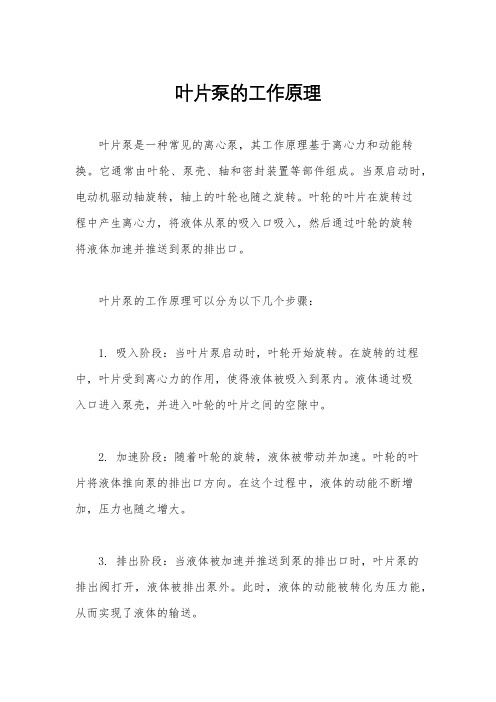
叶片泵的工作原理
叶片泵是一种常见的离心泵,其工作原理基于离心力和动能转换。
它通常由叶轮、泵壳、轴和密封装置等部件组成。
当泵启动时,电动机驱动轴旋转,轴上的叶轮也随之旋转。
叶轮的叶片在旋转过
程中产生离心力,将液体从泵的吸入口吸入,然后通过叶轮的旋转
将液体加速并推送到泵的排出口。
叶片泵的工作原理可以分为以下几个步骤:
1. 吸入阶段:当叶片泵启动时,叶轮开始旋转。
在旋转的过程中,叶片受到离心力的作用,使得液体被吸入到泵内。
液体通过吸
入口进入泵壳,并进入叶轮的叶片之间的空隙中。
2. 加速阶段:随着叶轮的旋转,液体被带动并加速。
叶轮的叶
片将液体推向泵的排出口方向。
在这个过程中,液体的动能不断增加,压力也随之增大。
3. 排出阶段:当液体被加速并推送到泵的排出口时,叶片泵的
排出阀打开,液体被排出泵外。
此时,液体的动能被转化为压力能,从而实现了液体的输送。
叶片泵的工作原理基于动能转换的原理,通过离心力将液体加
速并推送出去。
叶片泵通常用于输送清水、污水、油类液体以及其
他流体物质。
它具有结构简单、运行稳定、维护方便等特点,在工
业生产和民用领域得到了广泛的应用。
总的来说,叶片泵的工作原理是基于离心力和动能转换的原理,通过叶轮的旋转将液体加速并推送出去。
这种泵具有高效、稳定的
特点,是流体输送领域中常见的一种泵类设备。
叶片泵工作原理及应用

叶片泵工作原理及应用叶片泵是一种常用的离心泵,工作原理是利用叶片的转动产生离心力,加速液体的流动。
它由泵体、叶片及传动机构组成。
传动机构将电机的旋转运动传递给叶片,使之转动,从而将泵体内的液体通过出口排出。
在叶片泵中,叶片起到了关键的作用。
当叶片转动时,液体从入口流入泵体,在叶片的作用下,液体被加速并排出泵体。
叶片泵工作时需要保持一定的泵头,即泵体出口的压力高于入口的压力,这样才能产生足够的离心力,驱动液体流动。
为了维持泵头,需要调整泵体的出口阀门或者改变泵的转速。
叶片泵的应用非常广泛。
它可以用于输送清洁液体、腐蚀性液体、高温液体、低凝结点的液体等。
在工业中,叶片泵常用于化工、石油、冶金、电力等领域。
例如,在石油工业中,叶片泵用于输送原油、石油产品等;在化工工业中,叶片泵用于输送酸、碱、溶液等;在冶金工业中,叶片泵用于输送液态金属;在电力工业中,叶片泵用于输送循环水、给水等。
叶片泵的优点包括结构简单、体积小、重量轻、维护方便等。
它具有较高的工作效率和流量,可以达到较大的扬程,喷头高。
叶片泵的缺点是在输送高粘度液体或含有颗粒的液体时容易堵塞。
此外,叶片泵的振动和噪声相对较大,运行稳定性相对较差。
为了提高叶片泵的性能,减少振动和噪声,有时会在叶片上安装避振器。
同时,叶片泵的材料也需要根据输送液体的特性选择,例如,输送腐蚀性液体时需要选用耐酸碱材料。
总的来说,叶片泵是一种常用的离心泵,通过叶片的转动产生离心力,加速液体的流动。
它适用于多种液体输送,具有结构简单、体积小、重量轻等优点,被广泛应用于化工、石油、冶金、电力等工业领域。
基于UG NX的复杂曲面叶轮五轴数控加工技术

基于UG NX的复杂曲面叶轮五轴数控加工技术前言作为动力机械的关键部件,整体式叶轮广泛应用于航天航空等领域,其加工技术一直是制造业中的一个重要课题。
从整体式叶轮的几何结构和工艺过程可以看出[1],加工整体式叶轮时加工轨迹规划的约束条件比较多,相邻的叶片之间空间较小,加工时极易产生碰撞干涉,自动生成无干涉加工轨迹比较困难。
因此在加工叶轮的过程中不仅要保证叶片表面的加工轨迹能够满足几何准确性的要求,而且由于叶片的厚度有所限制,所以还要在实际加工中注意轨迹规划以保持加工的质量[1]。
目前,我国大多数生产也轮的厂家多数采用国外大型CAD/CAM软件,如UG NX、CATIA、MasterCAM等。
本文选用目前流行且功能强大的UG NX3.0对复杂曲面整体叶轮进行加工轨迹规划。
1 整体叶轮数控加工工艺流程规划根据叶轮的几何结构特征和使用要求(如图1),其基本加工工艺流程为:1)在锻压铝材上车削加工回转体的基本形状;2)开粗加工流道部分;3)半精加工流道部分;4)叶片精加工;5)对倒圆部分进行清根。
图1. 叶轮的基本几何特征1.1 刀具的选择为提高加工效率,在进行流道开粗和流道半精加工过程中尽可能选用大直径球头铣刀,但是也要注意使刀具直径2R1min小于两叶片间最小距离L1min,L1min的大小可以根据UG NX 3.0软件的分析(Analysis)功能测得。
R1min<L1min/2在叶片精加工过程中,应在保证不过切的前提下尽可能选择大直径球头刀,即保证刀具半径R2min大于流道和叶片相接部分的最大倒圆半径rmax。
R2min>rmax在对流道和相邻叶片的交接部分进行清根时,选择的刀具半径R3min小于流道和叶片相接部分的最小倒圆半径rmin。
R3min<rmin1.2 驱动方法选择本文将基于UG NX 3.0重点介绍流道开粗、流道半精加工、叶片精加工和倒圆部分清根的加工轨迹规划方法。
水轮机叶片三维建模详细教程(UG建模):设计流线建模

第一种方法 流线设计建模
(a) 叶片建模 图 II.1 水轮机转轮叶片
(b) 设计网格
图 II.2 轴面流道型线
(a )设计流线
(b) 木模图 图 II.3 叶片表面几何数据的三种型式
(c) 测绘点
(a)
图 II.4 加工一个叶片的方法
(b)
图 3.1 曲线坐标点的数据文件格式(进口边型线坐标数据)
(a)
(b)
图 3.2 用数据文件建立样条曲线
图 3.3 导入轴面型线
(a) 浏览要导入的 AutoCAD 文件
(b) 浏览要“导入至”的 NX 部件文件 图 3.4 导入 AutoCAD 文件
a.
(b)
(c)
图 3.5 偏置出口位置
图 3.7(a)
图 3.7(b)
图 3.7(c) 图 3.7 修剪角(俯视图)
图 3.8 部件导航器里空空如也 图 3.9 创建草图
图 3.10 添加曲线
图 3.11 添加几何约束
图 3.12 添加参考尺寸:R1
(a) 添加参考尺寸 R2 图 3.13 添加参考尺寸
(b) 完成添加参考尺寸
(a) 图 3.14 将原出口边轴面型线变为“参考对象”
(b)
(a) AutoCAD 文件 SurfP.dwg
(b) NX5 文件 runner_blade1.prt
图 3.15 从 AutoCAD 文件导入“设计流线”
图 3.16 为导入的曲线建立“组”
图 3.17 水力设计成果——“设计流线”
图 3.18 在图形窗口中选择组
(a)
(b) 图 3.19 通过点生成样条
(b)导入结果
叶片泵的应用场合
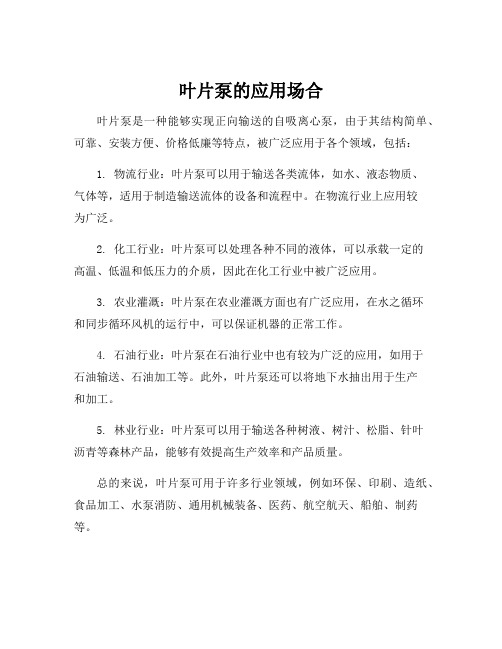
叶片泵的应用场合
叶片泵是一种能够实现正向输送的自吸离心泵,由于其结构简单、可靠、安装方便、价格低廉等特点,被广泛应用于各个领域,包括:
1. 物流行业:叶片泵可以用于输送各类流体,如水、液态物质、
气体等,适用于制造输送流体的设备和流程中。
在物流行业上应用较
为广泛。
2. 化工行业:叶片泵可以处理各种不同的液体,可以承载一定的
高温、低温和低压力的介质,因此在化工行业中被广泛应用。
3. 农业灌溉:叶片泵在农业灌溉方面也有广泛应用,在水之循环
和同步循环风机的运行中,可以保证机器的正常工作。
4. 石油行业:叶片泵在石油行业中也有较为广泛的应用,如用于
石油输送、石油加工等。
此外,叶片泵还可以将地下水抽出用于生产
和加工。
5. 林业行业:叶片泵可以用于输送各种树液、树汁、松脂、针叶
沥青等森林产品,能够有效提高生产效率和产品质量。
总的来说,叶片泵可用于许多行业领域,例如环保、印刷、造纸、食品加工、水泵消防、通用机械装备、医药、航空航天、船舶、制药等。
变量叶片泵调整方法

变量叶片泵调整方法
调整叶片泵的方法包括以下几点:
1. 调整叶片角度:根据具体的工况,调整叶片角度以改变泵的流量和扬程。
通常可以通过调整叶片泵的叶片角度或转子直径来实现。
2. 调整叶轮间隙:叶片泵的叶轮间隙不宜过大或过小,过大会造成漏流增加,过小则会增加泵的阻力。
通过调整叶轮与泵壳之间的间隙来改变流量和扬程。
3. 调整进出口阀门开度:调整进出口阀门的开度可以改变泵的进出口压力,从而达到调整流量和扬程的目的。
4. 更换流道板或调整导叶角度:有些叶片泵的流道板或导叶角度可调,通过调整流道板或导叶角度可以改变泵的流量和扬程。
5. 调整驱动电机转速:通过调整驱动电机的转速可以改变泵的流量和扬程。
通常可以通过变频器或调整传动装置来实现。
需要注意的是,在进行叶片泵的调整时应根据具体的工况和要求进行调整,并注意保持稳定的运行状态,以确保泵的正常工作和性能。
三章第三节 叶片泵
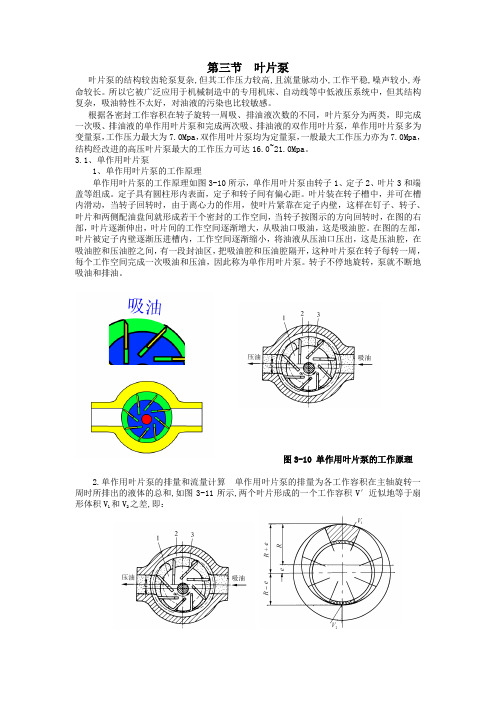
第三节叶片泵叶片泵的结构较齿轮泵复杂,但其工作压力较高,且流量脉动小,工作平稳,噪声较小,寿命较长。
所以它被广泛应用于机械制造中的专用机床、自动线等中低液压系统中,但其结构复杂,吸油特性不太好,对油液的污染也比较敏感。
根据各密封工作容积在转子旋转一周吸、排油液次数的不同,叶片泵分为两类,即完成一次吸、排油液的单作用叶片泵和完成两次吸、排油液的双作用叶片泵,单作用叶片泵多为变量泵,工作压力最大为7.0Mpa,双作用叶片泵均为定量泵,一般最大工作压力亦为7.0Mpa,结构经改进的高压叶片泵最大的工作压力可达16.0~21.0Mpa。
3.1、单作用叶片泵1、单作用叶片泵的工作原理单作用叶片泵的工作原理如图3-10所示,单作用叶片泵由转子1、定子2、叶片3和端盖等组成。
定子具有圆柱形内表面,定子和转子间有偏心距。
叶片装在转子槽中,并可在槽内滑动,当转子回转时,由于离心力的作用,使叶片紧靠在定子内壁,这样在钉子、转子、叶片和两侧配油盘间就形成若干个密封的工作空间,当转子按图示的方向回转时,在图的右部,叶片逐渐伸出,叶片间的工作空间逐渐增大,从吸油口吸油,这是吸油腔。
在图的左部,叶片被定子内壁逐渐压进槽内,工作空间逐渐缩小,将油液从压油口压出,这是压油腔,在吸油腔和压油腔之间,有一段封油区,把吸油腔和压油腔隔开,这种叶片泵在转子每转一周,每个工作空间完成一次吸油和压油,因此称为单作用叶片泵。
转子不停地旋转,泵就不断地吸油和排油。
图3-10 单作用叶片泵的工作原理2.单作用叶片泵的排量和流量计算单作用叶片泵的排量为各工作容积在主轴旋转一周时所排出的液体的总和,如图3-11所示,两个叶片形成的一个工作容积V′近似地等于扇形体积V1和V2之差,即:图3-10单作用叶片泵的工作原理 图3-11单作用叶片泵排量计算简图1—转子2—定子3—叶片 ()()221214'R e 2V V V B R e R e B z πβ⎡⎤=-=+--=⎣⎦ (3-13)式中:R 为定子的内径(m);e 为转子与定子之间的偏心矩(m);B 为定子的宽度(m);β为相邻两个叶片间的夹角,β=2π/z;z 为叶片的个数。
叶片泵的应用场景

叶片泵的应用场景
叶片泵是一种常用的离心泵,其应用场景非常广泛。
以下是叶片泵的一些典型应用场景:
1. 工业生产:叶片泵可以用于输送各种工业液体,如油、水、溶剂、酸碱等。
常见的工业应用包括石油、化工、食品加工、造纸等。
2. 环保治理:叶片泵可以用于处理污水、废水以及废气等。
在环保治理中,叶片泵的作用是将液体或气体输送到处理设备中进行处理。
3. 农业灌溉:叶片泵可以用于农业灌溉,将水源输送到田地中进行灌溉。
叶片泵可以根据需要调整流量和压力,以适应不同的灌溉要求。
4. 建筑消防:叶片泵可以用于建筑消防系统中,将水源输送到消防设备中进行消防。
叶片泵可以快速、高效地将水源输送到需要的地方。
5. 车辆冷却:叶片泵可以用于汽车、火车等车辆的冷却系统中,将循环水输送到发动机、散热器等部件中进行冷却。
叶片泵可以根据需要调整流量和压力,以适应不同的车辆型号和工况。
总之,叶片泵是一种非常实用的泵类,其应用场景非常广泛,可以满足各种不同领域的需求。
- 1 -。
叶片泵的工作压力
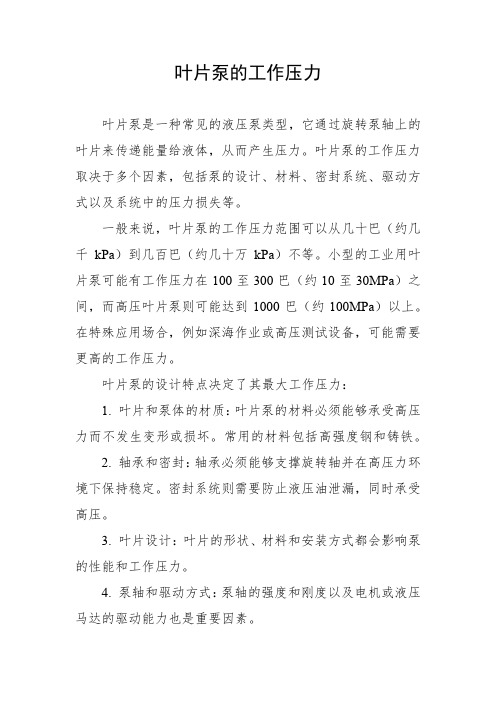
叶片泵的工作压力
叶片泵是一种常见的液压泵类型,它通过旋转泵轴上的叶片来传递能量给液体,从而产生压力。
叶片泵的工作压力取决于多个因素,包括泵的设计、材料、密封系统、驱动方式以及系统中的压力损失等。
一般来说,叶片泵的工作压力范围可以从几十巴(约几千kPa)到几百巴(约几十万kPa)不等。
小型的工业用叶片泵可能有工作压力在100至300巴(约10至30MPa)之间,而高压叶片泵则可能达到1000巴(约100MPa)以上。
在特殊应用场合,例如深海作业或高压测试设备,可能需要更高的工作压力。
叶片泵的设计特点决定了其最大工作压力:
1. 叶片和泵体的材质:叶片泵的材料必须能够承受高压力而不发生变形或损坏。
常用的材料包括高强度钢和铸铁。
2. 轴承和密封:轴承必须能够支撑旋转轴并在高压力环境下保持稳定。
密封系统则需要防止液压油泄漏,同时承受高压。
3. 叶片设计:叶片的形状、材料和安装方式都会影响泵的性能和工作压力。
4. 泵轴和驱动方式:泵轴的强度和刚度以及电机或液压马达的驱动能力也是重要因素。
5. 控制系统:叶片泵通常配备有压力控制阀,以确保系统在设定的压力范围内运行,防止过压。
6. 压力维持和释放:系统中的压力维持元件(如蓄能器)和释压装置(如溢流阀)也会影响工作压力。
在实际应用中,叶片泵的工作压力还会受到液压系统中管路、接头、阀门等组件的压力损失的影响。
因此,为了确保系统安全可靠地运行,通常会在设计时考虑一定的安全系数,并在系统中设置压力监测和报警装置。
总之,叶片泵的工作压力是由其设计参数和系统配置共同决定的,并且在实际使用中需要考虑到系统的整体性能和安全要求。
- 1、下载文档前请自行甄别文档内容的完整性,平台不提供额外的编辑、内容补充、找答案等附加服务。
- 2、"仅部分预览"的文档,不可在线预览部分如存在完整性等问题,可反馈申请退款(可完整预览的文档不适用该条件!)。
- 3、如文档侵犯您的权益,请联系客服反馈,我们会尽快为您处理(人工客服工作时间:9:00-18:30)。
焊接式叶片泵加工学号:08110513 姓名:陈向兵热动5班本文主要论述了利用UGNX进行汽轮机主油泵叶轮的数控加工方案规划及加工过程的优化;主油泵是汽轮机润滑与控制的关键部件,其制造质量直接影响汽轮机的安全可靠运行。
1 引言主油泵是汽轮机的关键部件,负责调节润滑冷却系统的油压建立及汽轮机控制信号油压发生,其叶片流道的精度要求很高。
其制造质量直接影响汽轮机的安全可靠运行。
在公司引进UG-CAM自动编程系统以前,主要采用手工编程方法进行加工,不仅要进行大量的计算,容易出错;而且加工效率低,零件精度与光洁都无法保证,且后续钳修量很大。
为此,其加工技术一直是工艺设计人员研究的课题之一。
在引进了的UGNX软件系统后,通过利用UGNX的CAD/CAM功能对汽轮机主油泵叶轮进行数控加工技术的研究,充分体验到UG-CAD/CA M系统功能的优点:安全、可靠,编程周期短、程序修改方便。
2 主油泵叶轮加工现状及工艺分析主油泵叶轮的数控加工设备是:北一大偎三坐标联动加工中心,数控系统为:OSP-E10M-R。
主油泵叶轮加工的关键部位是叶轮体上的叶片型线及流道。
如图1侧视示意图,其主要要求为叶片型线准确;叶片间的喉部尺寸精度;流道的粗糙度。
在采用手工编程进行数控加工时,编程计算量庞大,程序数据精度较低,其加工完成的叶型及流道不仅满足不了技术要求,而且需要钳修叶型与流道,钳修的工作量很大,加工效率低,质量也无法保证,易把已加工好的面破坏。
图2所示为用手工编程进行数控加工完工后的主油泵叶轮。
图1:主油泵叶轮侧视图图2:手工编程数控加工的主油泵叶轮(局部)主油泵叶轮体的数控加工工艺方案。
根据主油泵叶轮毛坯特点,它的凸台部分已车好,其它部分需要在加工中心上完成,因此把凸台的圆心作为加工基准,即对刀点。
首先,进行粗加工。
把叶轮体的大部分余量都要在这一步去掉,因此根据叶轮体流道的宽度,选用尺寸合适的大直径镶齿刀。
然后,进行半精加工。
为了保证叶轮的精度和粗糙度,我们在这一步先去掉一少部分余量,即加工叶片厚度及底面三维部分,同时还要注意保护已加工好的锥面,把它作成检查体,防止过切。
第三,进行精加工。
这一步把叶片厚度、底平面及三维底面都要加工到图纸尺寸,而且要调整好接刀部分。
最后,进行根部清理。
即利用小于等于根部倒圆角R值的球刀进行清根,达到加工完全的目的。
由于叶轮叶片的特殊性,我们把精加工底平面调整到半精加工之前,这样可使叶片厚度的加工直接达到底平面。
3 建立CAD模型用UGNX的CAD对汽轮机主油泵叶轮体进行草图绘制,保证几何模型的唯一性与一致性。
在构造叶轮体CAD模型时,首先要设定几何模型的基准,好的基准能帮助我们简化建模的过程,并方便后期的设计修改。
通常大部分建模过程的开始都是从设计基准开始的,因此我们把二维CAD图纸的设计基准也定为三维CAD模型的基准。
其次,注意毛坯的信息,被加工掉的部分不能作为毛坯实体,必须详细画出精加工图。
第三,根据加工次序要求及加工方法的需要,添加一系列辅助线。
由于零件几何模型和刀具路径完全相关,刀具路径能随几何模型的改变而自动更新,所以在几何模型建立时要充分考虑刀具路径是否会干涉。
几何模型建立是以工作坐标系为基础的,而刀位文件的生成是以加工坐标系为基础的。
在对叶轮体进行几何建模时,考虑到有利于操作者准确对刀的位置,一般以已加工好的三维凸台面的圆心作为基准位置。
坐标轴的方向工作坐标系与机床坐标系相一致。
在建立叶轮体上的叶片时利用了多层型线补面,在用面补成实体。
叶轮体的CAD模型如图3所示。
图3:叶轮体的CAD模型4 主油泵叶轮CAM数控编程UGNX-CAM具有强大的铣削加工功能,对于任何复杂曲面都能生成合理的优化的刀位轨迹,然后转化成数控机床能够识别的数控加工程序。
4.1 建立刀具库作为自动化加工设备,数控机床加工对刀具有较高的要求,要求刀具具有较高的精度、刚度和耐用度。
为此,应尽量采用整体硬质合金刀具或镶不重磨机夹硬质合金刀片及涂层刀片。
刀具的耐用度应该至少能保证加工一个零件或一个工作班的工作时间。
因此我公司采用SECO的铣刀,设置的铣刀类型用5参数铣刀即可,并把长度补偿寄存器号、刀具直径补偿寄存器号的编号排好,以指引控制器读取这些数据。
刀具号的设置用于指引控制器控制机床去使用刀具库中相应编号的刀具。
4.2 数控加工工艺分析及切削方法的确定由于UG中的CAM铣削模块提供了粗车、多次走刀精车,设定进给量、主轴转速和加工余量等参数。
利用UG中的CAM铣削功能,根据我公司主油泵叶轮体特点及毛坯余量的实际情况,对数控加工工艺进行分析后,采用分五步方法进行。
第一步:开槽加工,即粗加工流道。
目的在于将叶片间的汽道开通,形成通道,为半精加工做好准备。
对叶轮体车好的毛坯进行粗铣流道,要求底面留0.3mm余量,侧面留0.5mm 余量。
第二步:精加工底平面。
按图纸尺寸要求,把侧面让出,精铣底平面到图纸尺寸。
第三步:半精加工叶片厚度及底面三维。
由于所用刀具直径很小,切削量大易磨损刀具,故采用半精加工。
半精加工叶片厚度及底面三维部分,为最终图纸尺寸每面留0.2mm余量。
第四步:精加工叶片厚度及底面三维。
精铣叶片厚度及底面三维部分,进行最终精加工。
其走刀路径与半精加工完全相同,只是余量不同。
第五步:清根。
主要利用小于等于根部倒角值的球刀进行根部清理。
nextpage 如图4、图5所示精加工叶片型面及清根示意图。
图4:精加工叶片型面(部分)图5:清根(部分)4.3 刀具的选择刀具选择的原则,要根据零件材料的性能、加工工序的类型、机床的加工能力及准备选用的切削用量来合理地选择刀具。
在可能的情况下,尽量选择较大的刀具直径,以保证刀具有足够的刚度,减少震动或刀具折断等。
同时在可能的情况下,刀具的安装长度要尽量选择短,以增强刀具的刚度。
根据叶轮体的轮廓形状加工需要,设置好不同的刀具参数,作为编程用刀具。
对于铣削平面,采用端铣刀;对于铣削三维部分和根部,采用球刀。
4.4 走刀路线的选择选择合理的走刀路线,以保证零件的加工精度与光洁度,尽量减少空刀,选择较短的走刀路线,对于叶轮体能用一把刀具编程加工的部分尽量连在一起做,节省对刀时间,以提高生产率。
UGNX中的CAM具有丰富的刀具轨迹编辑功能,可以控制切削方向及轨迹形状的任意细节,可以指定垂直、直线相切、圆弧相切等各种进、退刀方式,也可以选择单向、往复式、仿形外轮廓、仿形零件及轮廓等切削方式,以适应不同的要求,得到高品质的加工效果。
针对叶轮体加工,粗加工时选择底部与侧面同时加工;精加工时选择底部与侧面分别进行加工。
而进退刀方式选择以圆弧相切进行,以保证叶轮体的加工精度。
4.5 编点位程序对已画的精加工图进行UGNX中的CAM铣削自动编程,经过以上主油泵叶轮体毛坯余量的实际情况加工工艺分析后,选择合理的走刀路线;设置合理的刀具参数;采用合理的进、退刀方式;控制进给量、主轴转速和加工余量参数及设置前处理各参数等,进行点位文件生成。
(点位文件又称CLS刀位文件)然后在图形方式下观察刀具沿轨迹运动的情况,并进行图形化修改:如对刀具轨迹进行延伸、缩短或修改等。
针对叶轮体加工工艺要求先编制底面程序,再编制各叶片两个侧面程序,最后编制底面三维部分和叶片前面R2.5部分的程序。
有时根据实际余量情况需要进行交叉编制点位于程序。
4.6 点位程序模拟仿真为了减少在实际数控加工中心加工上对刀具的调整,保证生成的点位程序可靠性,应在UGNX中的CAM铣削点位程序中对刀具轨迹尽可能广泛地作有效性检查,以便对点位程序进行细节分析及观察刀具的干涉情况。
从刀具路径显示菜单中调用刀具库相对应的铣刀,在屏幕上模拟显示刀具路径,可检测参数设置是否正确,如果点位程序显示刀具模拟仿真不理想,则返回铣削加工模块对一些参数进行重新修改,直至生成的点位程序模拟仿真结果完全符合加工实际要求。
仿真的过程对我们分析编制的程序正确性将提供非常大的帮助。
4.7 后置处理的设定我们使用UG POST后处理方法,输出NC程序。
在UG中做刀轨文件的后处理,生成机床可接收的NC程序,后处理必须具备两个要素:刀轨和后处理器。
刀具轨迹数据在UG-CAM 中自动生成,UG后置处理器由事件管理器和定义文件构成。
加工中心数控系统为OSP-E10M-R,因此由我公司专人利用UG/POST Builder后处理编辑器开发了这一数控系统的后处理,生成的数控加工程序无须手工修改就可以直接输入数控机床进行产品加工,从而解决了通用后置处理器产生的数控程序需人工进行二次修改的繁琐过程。
4.8 加工程序的生成UGNX中的CAM铣削自动编制的点位程序,经过后置程序处理后,最终生成机床能识别的加工程序。
生成的程序如下形式:( Part Name : F:\20050519\20050526.prt )( Created By : Angelina )( Creation Date: Fri May 27 14:12:42 2005 )( Start Of Path: D25 )( Tool : D25 D=25.0 R=0.8 )( FEEDRATE : 300 )( RPM : 1500 )G15H1G00G90G40X-83.238Y27.170M03S1500G56Z50.000H01M08G17G01 ………………G01……( End Of Path : D25 )( End Of Task : F:\20050519\20050526.prt )( Cycle Time : 380.96MIN )M30%以上"……"代号部分是数控程序中自动计算的坐标点。
而开始和结束部分是数控编程中前置处理设置后生成的。
图6为用UG-CAM自动编程进行数控加工完工后的主油泵叶轮。
图6:自动编程数控加工的主油泵叶轮(局部)5 结论实践表明,UGNX-CAD/CAM软件在主油泵叶轮体数控自动编程上的应用,提高了主油泵叶轮体加工质量,自动编程时,只要选择合理的工艺控制参数,结合编程经验,使得加工过程得到充分的体现。
同时对自动生成的程序进行工艺参数的逐步改进,逐步提高,可大大提高加工效率及加工精度,缩短研制与生产周期。