DFMEA-底盘-悬架系各零件
汽车底盘DFMEA-转向器带横拉杆总成

小
格,规定联结力矩
风
R P N
险 顺 序
建议措 施
数
20 质量管控
20 质量管控 20 质量管控
编制人 编制日期 修订日期
职责及目 标完成日
期
赵红秀
赵红秀
赵红秀
FMEA编 号第: 1
页
共1页
措施执行后的结果
采取的措施 及完成日期
严 重 度 S
频 度 O
探 测 度 D
风险 顺序
数 RPN
10
☆
齿轮轴杆部断 裂
转向无 异响
转向异响
造成顾客行车时紧张
联结
转向无 干涉
与汽车其 它部分发
生干涉
力传递不顺畅,顾客手 感不舒适,整车回正能
力差
编制:
潜在失效模式及后果分析(DFMEA)
设计职责(部门)
底盘技术部
关键日期 核心小组
严 重 分 潜在失效原因 度 类 / 机理 S
现行设计控制
控制预防
频 度 控制探测 O
风
探 测 度
系统 子系统
部件 年型/车型 项目
转向系统 /
转向器带横拉杆总成
要求
潜在失 效模式
失效潜在影响/后果
功能
车辆突然无法转向,危 及人身安全
转向功能
转向功 能良好
完全失去 转向功能
车辆突然无法转向,危 及人身安全
潜在失效模式及后果分析(DFMEA)设计职责(ຫໍສະໝຸດ 门)底盘技术部关键日期
核心小组
严 重 分 潜在失效原因 度 类 / 机理 S
R P N
险 顺 序
建议措 施
D数
拉杆松旷
规定内球节的轴向 弹性位移
DFMEA-底盘-行车制动系各零件
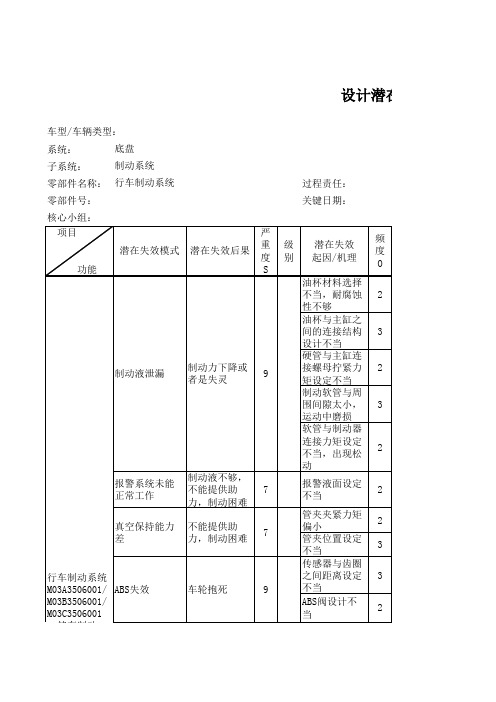
系统:子系统:零部件名称:过程责任:零部件号:关键日期:核心小组:液;·监控制动液液面高度;·辅助人力制动;行车制动系统设计潜在失(车型/车辆类型:底盘制动系统M03A3506001/M03B3506001/M03C3506001设计潜在失(系统:子系统:零部件名称:过程责任:零部件号:关键日期:核心小组:车型/车辆类型:底盘制动系统制动器系统:子系统:零部件名称:过程责任:零部件号:关键日期:核心小组:·向制动盘提供制动力·配合制动其提供制动力制动盘设计潜在失(车型/车辆类型:底盘制动系统系统:子系统:零部件名称:过程责任:零部件号:关键日期:核心小组:M03A3501011/号给制动尾灯车型/车辆类型:底盘制动系统制动踏板总成设计潜在失(系统:子系统:零部件名称:过程责任:零部件号:关键日期:核心小组:构中人力的直接作用对象;·提供制动信号给发动机ECU;·调节管路压力,分配制动力。
避免在制动时后轮先抱死侧滑,同时尽可能充分地利用附着条件,产生较大的制动力。
漏比例阀设计潜在失(车型/车辆类型:底盘制动系统系统:子系统:零部件名称:过程责任:零部件号:关键日期:核心小组:M03B3540100/M03C3540100/M03D3540100/M03E3540100·储存制动液;·提供助力辅车型/车辆类型:底盘制动系统带主缸真空助力器总成设计潜在失(比例阀比例阀进出油系统:子系统:零部件名称:过程责任:零部件号:关键日期:核心小组:制动主缸设计潜在失(车型/车辆类型:底盘制动系统带主缸真空助系统:子系统:零部件名称:过程责任:零部件号:关键日期:核心小组:车型/车辆类型:底盘制动系统真空助力器设计潜在失(系统:子系统:零部件名称:过程责任:零部件号:关键日期:核心小组:总成M03A3561130真空助力软管总成设计潜在失(车型/车辆类型:底盘制动系统·提供助力,辅助人力制动系统:子系统:零部件名称:过程责任:零部件号:关键日期:核心小组:ABS支架M03A3550210·安装固定ABS总成车型/车辆类型:底盘制动ABS支架设计潜在失(系统:子系统:零部件名称:过程责任:零部件号:关键日期:核心小组:M03A3561110/M03A3561150/M03B3561150·供油制动软管总成设计潜在失(车型/车辆类型:底盘制动系统:子系统:零部件名称:过程责任:零部件号:关键日期:核心小组:灵车型/车辆类型:底盘制动制动硬管总成设计潜在失(FMEA编号:编制人:修订人:第 1 页共 12 潜在失效模式及后果分析(DFMEA)附件6潜在失效模式及后果分析(DFMEA)附件6FMEA编号:编制人:修订人:第 2 页共 12FMEA编号:编制人:修订人:第 3 页共 12 潜在失效模式及后果分析(DFMEA)附件6FMEA编号:编制人:修订人:第 4 页共 12 潜在失效模式及后果分析(DFMEA)附件6FMEA编号:编制人:修订人:第 5 页共 12 潜在失效模式及后果分析(DFMEA)附件6FMEA编号:编制人:修订人:第 6 页共 12 潜在失效模式及后果分析(DFMEA)附件6FMEA编号:编制人:修订人:第 7 页共 12 潜在失效模式及后果分析(DFMEA)附件6FMEA编号:编制人:修订人:第 8 页共 12 潜在失效模式及后果分析(DFMEA)附件6FMEA编号:编制人:修订人:第 9 页共 12 潜在失效模式及后果分析(DFMEA)附件6FMEA编号:编制人:修订人:第 10 页共 12 潜在失效模式及后果分析(DFMEA)附件6FMEA编号:编制人:修订人:第 11 页共 12 潜在失效模式及后果分析(DFMEA)附件6FMEA编号:编制人:修订人:第 12 页共 12 潜在失效模式及后果分析(DFMEA)附件612 页果件6件6果12 页12 页果件6果12 页件612 页果件6果12 页件612 页果件6果12 页件612 页果件6果12 页件612 页果件6果12 页件6。
汽车底盘悬挂系统设计DFMEA案例分析
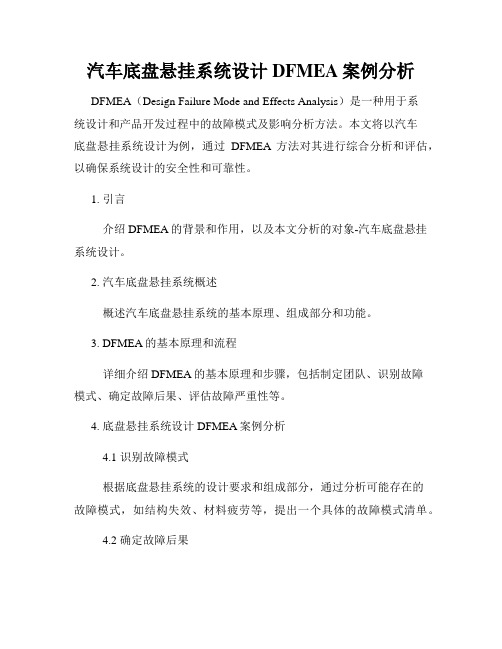
汽车底盘悬挂系统设计DFMEA案例分析DFMEA(Design Failure Mode and Effects Analysis)是一种用于系统设计和产品开发过程中的故障模式及影响分析方法。
本文将以汽车底盘悬挂系统设计为例,通过DFMEA方法对其进行综合分析和评估,以确保系统设计的安全性和可靠性。
1. 引言介绍DFMEA的背景和作用,以及本文分析的对象-汽车底盘悬挂系统设计。
2. 汽车底盘悬挂系统概述概述汽车底盘悬挂系统的基本原理、组成部分和功能。
3. DFMEA的基本原理和流程详细介绍DFMEA的基本原理和步骤,包括制定团队、识别故障模式、确定故障后果、评估故障严重性等。
4. 底盘悬挂系统设计DFMEA案例分析4.1 识别故障模式根据底盘悬挂系统的设计要求和组成部分,通过分析可能存在的故障模式,如结构失效、材料疲劳等,提出一个具体的故障模式清单。
4.2 确定故障后果对每个故障模式,通过分析和评估其对系统功能和性能的影响,确定故障后果,如引起底盘失稳、减少避震效果等。
4.3 评估故障严重性利用严重性评估矩阵,对每个故障后果进行定量评估,确定其严重程度,以便根据评分结果确定优先级。
4.4 分析潜在失效原因对每个故障模式和故障后果,通过分析可能的失效原因,如制造工艺缺陷、设计偏差等,确定潜在失效原因清单。
4.5 制定改进方案针对每个潜在失效原因,提出相应的改进措施和预防措施,如改进设计、加强制造工艺控制等。
4.6 评估改进效果对制定的改进方案进行评估,包括改进效果、成本评估等。
5. 结果与讨论汇总和总结分析结果,讨论DFMEA在汽车底盘悬挂系统设计中的应用价值,并提出对未来研究的展望。
6. 结论简要总结本文的研究内容和结论,强调DFMEA在汽车底盘悬挂系统设计中的重要性和应用前景。
参考文献(没有具体参考文献,请自行添加)本文以DFMEA方法为基础,通过对汽车底盘悬挂系统设计的案例分析,全面评估系统的可靠性和安全性。
DFMEA- 悬挂系统各零部件设计失效模式分析

系统:子系统:零部件名称:过程责任:零部件号:关键日期:核心小组:后悬架装置设计潜在车型/车辆类型:底盘悬架系统系统:子系统:零部件名称:过程责任:零部件号:关键日期:核心小组:车型/车辆类型:底盘悬架系统后轴焊接总成设计潜在系统:子系统:零部件名称:过程责任:零部件号:关键日期:核心小组:系统:子系统:零部件名称:过程责任:车型/车辆类型:底盘悬架系统后减振器带缓冲块总成设计潜在后螺旋弹簧设计潜在车型/车辆类型:底盘悬架系统零部件号:关键日期:核心小组:设计潜在系统:子系统:零部件名称:过程责任:零部件号:关键日期:核心小组:后减振器带缓冲块总成车型/车辆类型:底盘悬架系统系统:子系统:零部件名称:过程责任:零部件号:关键日期:核心小组:车型/车辆类型:底盘悬架系统后减振器带缓冲块总成设计潜在附件计潜在失效模式及后果分析(DFMEA)FMEA编号:编制人:修订人:第 1 页共计潜在失效模式及后果分析(DFMEA)FMEA编号:编制人:修订人:第 2 页共计潜在失效模式及后果分析(DFMEA)FMEA编号:编制人:修订人:第 3 页共计潜在失效模式及后果分析(DFMEA)FMEA编号:编制人:修订人:第 4 页共计潜在失效模式及后果分析(DFMEA)FMEA编号:编制人:修订人:第 5 页共计潜在失效模式及后果分析(DFMEA)FMEA编号:编制人:修订人:第 6 页共附件6共 6 页共 6 页共 6 页共 6 页共 6 页共 6 页。
汽车底盘DFMEA-制动硬管总成
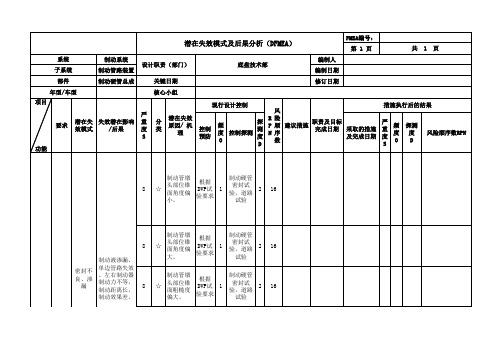
控制 预防
频 度 O
探
控制探测
测 度
D
R险 P顺 N序
数
建议措施
职责及目标 完成日期
采取的措施 及完成日期
严 重 度 S
频 度 O
探测 度 D
风险顺序数RPN
8
☆
制动管墩 头部位锥 面角度偏 小。
根据 DVP试 验要求
1
制动硬管
密封试 验,道路
2
试验
16
8 制动液渗漏、
☆
制动管墩 头部位锥 面角度偏 大。
根据 DVP试 验要求
1
。
材料试 验,需液 2
量试验
14
制动管
布置要 路与周 异常磨
求
边无干 损
涉
与周边件干涉 。
4
★
制动硬管 局部成型 尺寸不合 理
根据 DVP试 验要求
4
整车装配 2
32
内表面
不清
清洁度
内表面 清洁
洁,导 致ABS阀 堵塞,
制动失效
轮缸皮
碗损坏
按照
设计时不 GB112
9
★ 满足 GB11258
根据 DVP试 验要求
1
制动硬管
密封试 验,道路
2
试验
16
密封不 良、渗
漏
单边管路失效 、左右制动器 制动力不等, 制动距离长,
8
制动效果差。
☆
制动管墩 头部位锥 面粗糙度 偏大。
根据 DVP试 验要求
1
制动硬管
密封试 验,道路
2
试验
16
制动管 路连接 液压源 与制动 密封性 执行机
良、渗 漏
汽车底盘DFMEA-侧向稳定杆总成

系统 子系统
部件 年型/车型
悬架系统 后悬架系统 上下纵向推力杆总成
设计职责(部门)
关键日期 核心小组
要求
潜在失效 模式
失效潜在影响/后果
严 重分 度类 S
潜在失效原因/ 机理
功能
焊接开裂
杆臂断裂,车辆失去控 制
8
导向、传递 侧向力作用
足够的 强度和
寿命
橡胶衬套 车辆失去控制,无法行
开裂
驶
8
材料强度过低,产品材料 、工艺不符合要求
衬套结构设计不合理
潜在失效模式及
编制:
审核:
潜在失效模式及后果分析(DFMEA)
底盘技术部
编制人 编制日期 修订日期
FMEA编号: 第 1 页
现行设计控制
控制预防
频
度
控制探测
O
风
探 测 度 D
R险 P顺 N序
数
建议措施
措施执行后的结
职责及目标 完成日期 采取的措施 及完成日期
优化结构设计,进行CAE分 析;选 用高强度材料及改善 2
产品工艺
道路试验
3 48
对标同类型产品
2
道路试验
3 48
审核:
批准:
共 1页
措施执行后的结果
严 重 度 S
频 度 O
探 测 度 D
风险顺序数 RPN
ቤተ መጻሕፍቲ ባይዱ
DFMEA-动力系统-发动机悬置系统
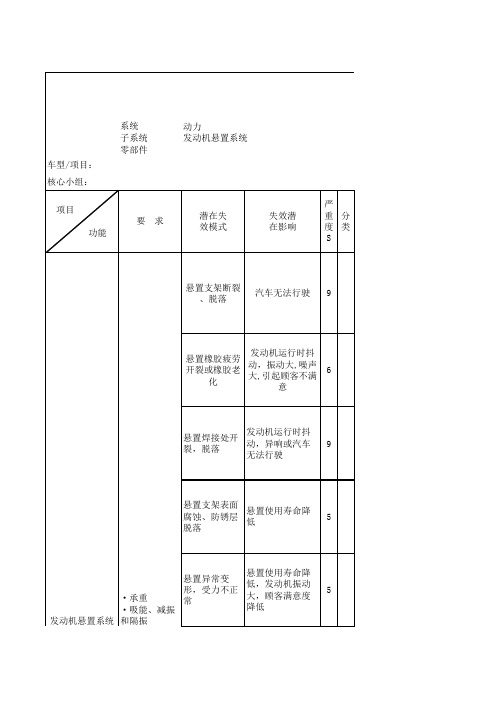
45
无
支架结构设计不合理, 进行设计评审和 2 或材料选择不合理 有限元强度分析
进行台架振动耐 久性试验;材料 2 检测
36
无
表面防腐处理工艺和方 进行设计评审和 2 法不合理 划格法外观检查
进行盐雾试验
3
30
无
支架固有频率偏低
CAE分析
2
CAE分析
2
24
选择合适的焊接 方法、正确的焊 焊接方法不合理、焊接 进行盐雾试验和 接材料和焊接表 2 2 材料选择不合理 台架振动耐久性 面进行防腐蚀措 施 进行受力分析或 进行台架振动耐 按标准设定扭矩 1 2 久性试验 值
9
支架表面腐 使支架使用寿命 蚀,防腐层脱 降低 落
5
共振
寿命降低,顾客满 足度降低
6
发动机运行时抖 支架焊接处开 动,振动大或汽 裂或断裂 车无法行驶 发动机运行抖动 螺栓连接处松 、振动大或有异 动 响,顾客满意度 降低
9
4
螺栓断裂
汽车无法行驶
9
潜在失效模式与影响分析 (设计FMEA)
设计职责: 关键日期: 编制人: FMEA日期(编制): 文件编号: 现行设计 失效潜 在原因 控制 预防 发 生 度 O 控制 探测 探 测 RPN 度 D 建议 措施
潜在失效模式与影 (设计FMEA)
系统 子系统 零部件 车型/项目: 核心小组: 项目 要 功能 求 严 重 分 度 类 S 动力 发动机悬置系统
潜在失 效模式
失效潜 在影响
悬置支架断裂 、脱落
汽车无法行驶
9
发动机运行时抖 悬置橡胶疲劳 动,振动大,噪声 开裂或橡胶老 大,引起顾客不满 化 意
6
发动机运行时抖 悬置焊接处开 动,异响或汽车 裂,脱落 无法行驶
汽车底盘DFMEA-轮速传感器总成

号不良
来。
1.数据、图
纸检查 2.工程样车
5
装车检查
35
实物测量
底盘技术部 李宏超
2018.6.28
实物测量 2018.7.30
7
1
3
21
1.量产前后
对供应商进
行工程确认
制造工艺
轮速传感器信号不 良
7
在涉水时轮速传感器易 接触到水,塑料件均有 吸水性,(24h饱和吸 水率为0.24%)。在通 电时,电解水后的氢氧 轮速传感器增加负压 ☆ 根离子和英飞凌芯片电 0.5bar真空度浸泡水 容两端的银离子发生置 150s全检工艺。 换反应,银离子与水汽 形成导电层,使芯片电 容阻值下降,信号输出
轮速传感器信号不 良
7
☆
孔,容易进水导致轮速 轮速传感器的螺纹孔为 传感器头部受潮,进而 盲孔,螺纹长度保证至
2
纸检查 2.工程样车
5
70
致使信号不良
少8mm
装车检查
号,并传递 信号,
给接收的 并传递 ECU 给ECU
装配错误
轮速传感器信号不 良
7
传感器头部芯片与齿圈 将轮速传感器与齿圈相
☆ 方向不对,导致轮速信 对位置在图纸上标注出 1
建议措施
编制人 编制日期 修订日期
FMEA编号: 第 1 页
共 1页
措施执行后的结果
职责及目标完 成日期
采取的措施 及完成日期
严 重 度 S
频 度 O
探 测 风险顺 度 序数RPN D
☆
轮速传感器与齿圈气隙 按照图纸要求的气隙尺
超差
寸进行控制
2
装配测量 1 16
齿圈与传感 轮速信
汽车底盘DFMEA-前摆臂总成

2
45
无
对标同类型产品
3
台架试验、CAE分析 等
2
45
无
审核:
批准:
共1页
措施执行后的结果
严 重 度 S
频 度 O
探 测 度 D
风险顺序数 RPN
无法行驶
球头销选择不合理
编制:
审核:
潜在失效模式及后果分析(DFMEA)
底盘部
编制人 编制日期 修订日期
FMEA编号: 第 1 页
现行设计控制
控制预防
频
度
控制探测
O
风
探 测 度 D
R险 P顺 N序
数
建议措施
措施执行后的结
职责及目标 完成日期 采取的措施 及完成日期
控制漆面厚度,既漆面附 着力
4 盐构设计,进行CAE分 析;选 用高强度材料及改善
产品工艺
3
台架试验、道路试验 、CAE分析等
3
54
无
优化结构设计,通过疲劳试 验进行分析
3
台架试验,CAE分析 等
3
42
无
更改尺寸参数
3 台架试验、道路试验 3 48
无
化结构设计,进行CAE分析; 选 用高强度材料及改善产品
工艺
3
台架试验、CAE分析 等
衬套开裂
衬套开裂,车 辆失控
7
衬套硬度过低,产品材料 B 、工艺不符合要求,或结
构不符合要求
导向、传递 侧向力作用
足够的 强度和
寿命
橡胶衬套 驾驶时有冲击
脱落
感,产生异响
8
A
设计的橡胶衬套拔出力不 合理
套管开裂
套管断裂车辆 失去控制
汽车底盘DFMEA-减震器总成

参考设计准则和类比设计 3
台架试验
3 36
参考设计准则和类比设计 3
台架试验
3 36
参考设计准则和类比设计 3
台架试验
3 36
参考设计准则和类比设计 3
台架试验
3 36
参考设计准则和类比设计 3
台架试验
3 36
参考设计准则和类比设计 3
台架试验
3 36
参考设计准则和类比设计 3
台架试验
3 36
参考设计准则和类比设计 3
产品制造工艺,减震器受 力较大
减振器行 影响行驶平顺 程不够 性
2
设计行程与实际行程有差 距
编制:
审核:
潜在失效模式及后果分析(DFMEA)
底盘技术部
编制人 编制日期 修订日期
FMEA编号: 第 1 页
现行设计控制
控制预防
频
度
控制探测
O
风
探 测 度 D
R险 ቤተ መጻሕፍቲ ባይዱ顺 N序
数
建议措施
措施执行后的结
职责及目标 完成日期 采取的措施 及完成日期
项目
系统 子系统
部件 年型/车型
悬架系统 前悬架系统 减震器总成
设计职责(部门)
关键日期 核心小组
要求
严
潜在失效 失效潜在影响/ 重 分
模式
后果
度类
S
潜在失效原因/ 机理
功能
4
阻尼力公差设定不对
潜在失效模式及后果分
4
阻尼力波形要求不当
连接车身与 转向节,传 递两者之间
作用力 ·缓冲地 面带来的冲 击,并逐步 减弱振动
4
减振性能 不满足要
DFMEA-底盘-驻车制动系各零件
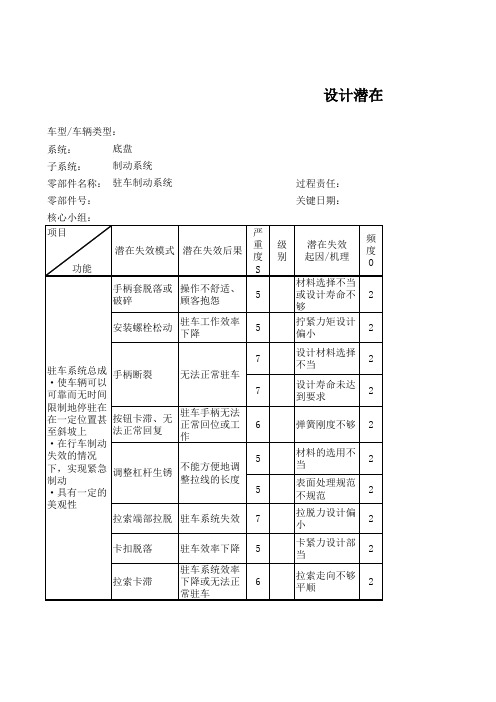
系统:子系统:零部件名称:过程责任:零部件号:关键日期:
核心小组:
驻车制动系统
设计潜在失
(
车型/车辆类型:底盘制动系统
系统:子系统:零部件名称:过程责任:零部件号:关键日期:
核心小组:
系统:
设计潜在失
(
车型/车辆类型:底盘
车型/车辆类型:底盘制动系统
驻车手柄总成
设计潜在失
(
子系统:零部件名称:过程责任:零部件号:关键日期:
核心小组:
系统:子系统:
零部件名称:过程责任:零部件号:关键日期:
核心小组:杆操纵作用力·连接驻车手柄和驻车制动器
车型/车辆类型:底盘制动系统
驻车拉线总成设计潜在失
(
驻车制动器总成
制动系统
FMEA编号:编制人:修订人:
第 1 页
共 4 页潜在失效模式及后果分析
(DFMEA)
附件6
附件6
FMEA编号:编制人:修订人:
潜在失效模式及后果分析
(DFMEA)
第 2 页
共 4 页潜在失效模式及后果分析
(DFMEA)
附件6
附件6
FMEA编号:编制人:修订人:
FMEA编号:编制人:修订人:
第 4 页
共 4 页第 3 页
共 4 页潜在失效模式及后果分析
(DFMEA)
附件6
页
页
页
页。
DFMEA-底盘-液压转向系各零部件

系统:子系统:零部件名称:过程责任:零部件号:关键日期:核心小组:劳,操纵不舒服震动大²传递转向力²改变力矩²转向回正²防止对驾驶员的伤害转向系统总成潜在失效(车型/车辆类型:底盘转向系统系统:子系统:零部件名称:过程责任:零部件号:关键日期:²控制车辆方车型/车辆类型:底盘转向系统喇叭盖潜在失效(核心小组:系统:子系统:零部件名称:过程责任:零部件号:关键日期:核心小组:影响顾客生命安全转向盘总成潜在失效(车型/车辆类型:底盘转向系统系统:子系统:零部件名称:过程责任:零部件号:关键日期:核心小组:²作为组合开关、方向盘和转向联轴节的支撑²提供方向盘车型/车辆类型:底盘转向系统转向管柱带转向传动轴总成潜在失效(系统:子系统:零部件名称:过程责任:零部件号:关键日期:核心小组:转向系统液压助力转向器总成潜在失效(车型/车辆类型:底盘求²橡胶连接件限位角5.5°±2°²传递扭矩和系统:子系统:零部件名称:过程责任:零部件号:关键日期:核心小组:(车型/车辆类型:底盘转向系统转向油泵总成潜在失效²满足左右转向感觉一致转向油泵总成M03A3407100²根据发动机转速提供转向液压助力²耐久²可靠²可装配性和可维修性²工作噪音小系统:子系统:零部件名称:过程责任:零部件号:关键日期:核心小组:²可靠的输送油液保证压力转向系统高压油管总成潜在失效(车型/车辆类型:底盘系统:子系统:零部件名称:过程责任:零部件号:关键日期:核心小组:(车型/车辆类型:底盘转向系统低压油管总成潜在失效潜在失效系统:子系统:零部件名称:过程责任:零部件号:关键日期:核心小组:转向系统冷却油管总成(车型/车辆类型:底盘系统:子系统:零部件名称:过程责任:零部件号:关键日期:核心小组:常工作²储存油液,向油泵及系统供油(车型/车辆类型:底盘转向系统转向油罐总成潜在失效系统:子系统:零部件名称:过程责任:零部件号:关键日期:核心小组:转向系统防尘罩潜在失效(车型/车辆类型:底盘在失效模式及后果分析(设计FMEA)FMEA编号:编制人:修订人:第 1 页共 11 页在失效模式及后果分析(设计FMEA)FMEA编号:编制人:修订人:第 2 页共 11 页在失效模式及后果分析(设计FMEA)FMEA编号:编制人:修订人:第 3 页共 11 页在失效模式及后果分析(设计FMEA)FMEA编号:编制人:修订人:第 4 页共 11 页FMEA编号:编制人:修订人:目标完成日期度D探测预防第 5 页共 11 页在失效模式及后果分析(设计FMEA)探在失效模式及后果分析(设计FMEA)FMEA编号:编制人:修订人:第 6 页共 11 页在失效模式及后果分析(设计FMEA)FMEA编号:编制人:修订人:第 7 页共 11 页在失效模式及后果分析(设计FMEA)FMEA编号:编制人:修订人:第 8 页共 11 页在失效模式及后果分析(设计FMEA)FMEA编号:编制人:修订人:第 9 页共 11 页在失效模式及后果分析(设计FMEA)FMEA编号:编制人:修订人:第 10 页共 11 页FMEA编号:编制人:修订人:目标完成日期度D 探测预防第 11 页共 11 页在失效模式及后果分析(设计FMEA)探共 11 页共 11 页共 11 页共 11 页共 11 页共 11 页共 11 页共 11 页共 11 页共 11 页共 11 页。
副车架总成--DFMEA

刚度不足、结 构设计不当
3
进行CAE分析 设计验证、设计 、参考相似产 评审、性能试验 品结构
3
54
材料不当、结 构设计不当
3
进行CAE分析 设计验证、设计 、参考相似产 评审、材料分析 品结构 、性能试验
3
72
悬架
系统 子系统 设计责任: 关键日期:
潜在失效模式及后果分析 (设计FDMEA)
编制人: FMEA日期(编制):
FMEA编号: 页码: 第
页
共
页
副车架总成 部件 年度车型/车辆类型: 核心小组:
项目 潜在失效模式 潜在失效后果 严 重 度 (S)
(修订)
频 分 类 潜在失效起因/ 机理 度 (O)
现行设计控制
度 序 N (D) 数
措施执行结果 建议措施 责任及目标完 成日期
采取的措施
S
O
D
RPN
6
8
I
I
前轮定位错 副车架变形, 误,轮胎磨 下摆臂运动干 损,影响舒适 固定在车身上,安 涉 性能和平顺性 装和支撑左、右下 能 摆臂,安装转向机 和稳定杆,为运动 部件提供运动空 间,保证车轮定位 副车架与变速 参数 箱、转向系统 副车架开裂 发生干涉,损 坏运动机构
DFMEA-底盘-随车工具

3 3
潜在失效模式及后果分析 (设计FMEA)
FMEA编号: 编制人: 修订人: 第 现行设计 控制预防 参考设计准则 参考设计准则 参考设计准则 参考设计准则 现行设计 控制探测 试制样件评审 试制样件评审 试制样件评审 盐雾试验 强度和耐久性 试验 台架试验 无 探 测 度 D 2 1 1 1 RPN 建议措施 13 页 共 措施结果 采取的 措施 S 13 页
潜在失效模式及后果 (设计FMEA)
车型/车辆类型: 系统: 子系统: 零部件号: 核心小组: 项目 潜在失效模式 功能 潜在失效后果 严 重 度 S 4 外观不符合要 求 千斤顶 ·车辆简单维 修时,举伸车 腐蚀 辆 ·告示标签明 显易认 ·工作可靠性 失效 和安全性 ·使用方便, 易于操作 操作不轻便 用户不满意 4 4 用户不满意 5 B 底盘 随车工具 过程责任: 关键日期:
零部件名称: 千斤顶
级 别
潜在失效 起因/机理 颜色未设定或 设定不对 表面处理未设 定或设定不对 表面对表面质 量,锋利突出 物芒刺等无要 抗腐蚀性设定 不对 强度和耐久性 设定不足
频 度 O 2 1 1 2
用户不满意
8
A
2
5 用户不满意 3
无负载时的操 作力矩设定不 变形量设定要 AR 求不对 B
责任及 目标完成 日期
16 无 4 4 无 无
10 无 更改材料,增 加强度或者优 32 化结构,增加 强度 30 无 18 无
参考设计准则
2
参考设计准则 参考设计准则
2 2
ห้องสมุดไป่ตู้ 共 措施结果 O
13
页
D
RPN
汽车车身饰件DFMEA全套资料
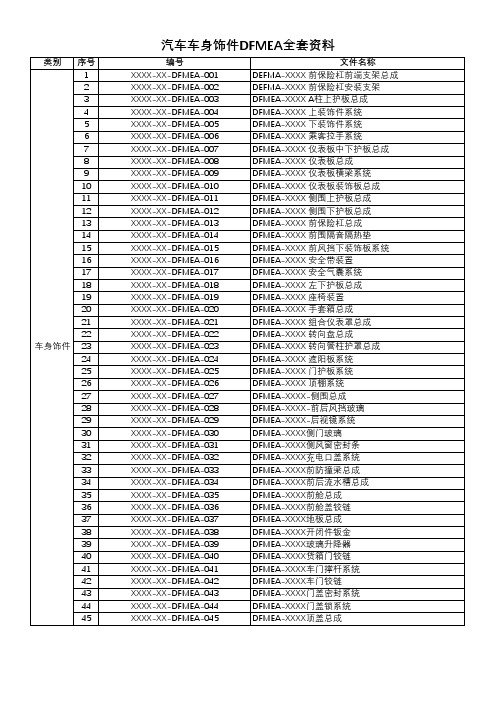
类别序号编号文件名称1XXXX-XX-DFMEA-001DEFMA-XXXX 前保险杠前端支架总成2XXXX-XX-DFMEA-002DEFMA-XXXX 前保险杠安装支架3XXXX-XX-DFMEA-003DFMEA-XXXX A柱上护板总成4XXXX-XX-DFMEA-004DFMEA-XXXX 上装饰件系统5XXXX-XX-DFMEA-005DFMEA-XXXX 下装饰件系统6XXXX-XX-DFMEA-006DFMEA-XXXX 乘客拉手系统7XXXX-XX-DFMEA-007DFMEA-XXXX 仪表板中下护板总成8XXXX-XX-DFMEA-008DFMEA-XXXX 仪表板总成9XXXX-XX-DFMEA-009DFMEA-XXXX 仪表板横梁系统10XXXX-XX-DFMEA-010DFMEA-XXXX 仪表板装饰板总成11XXXX-XX-DFMEA-011DFMEA-XXXX 侧围上护板总成12XXXX-XX-DFMEA-012DFMEA-XXXX 侧围下护板总成13XXXX-XX-DFMEA-013DFMEA-XXXX 前保险杠总成14XXXX-XX-DFMEA-014DFMEA-XXXX 前围隔音隔热垫15XXXX-XX-DFMEA-015DFMEA-XXXX 前风挡下装饰板系统16XXXX-XX-DFMEA-016DFMEA-XXXX 安全带装置17XXXX-XX-DFMEA-017DFMEA-XXXX 安全气囊系统18XXXX-XX-DFMEA-018DFMEA-XXXX 左下护板总成19XXXX-XX-DFMEA-019DFMEA-XXXX 座椅装置20XXXX-XX-DFMEA-020DFMEA-XXXX 手套箱总成21XXXX-XX-DFMEA-021DFMEA-XXXX 组合仪表罩总成22XXXX-XX-DFMEA-022DFMEA-XXXX 转向盘总成23XXXX-XX-DFMEA-023DFMEA-XXXX 转向管柱护罩总成24XXXX-XX-DFMEA-024DFMEA-XXXX 遮阳板系统25XXXX-XX-DFMEA-025DFMEA-XXXX 门护板系统26XXXX-XX-DFMEA-026DFMEA-XXXX 顶棚系统27XXXX-XX-DFMEA-027DFMEA-XXXX-侧围总成28XXXX-XX-DFMEA-028DFMEA-XXXX-前后风挡玻璃29XXXX-XX-DFMEA-029DFMEA-XXXX-后视镜系统30XXXX-XX-DFMEA-030DFMEA-XXXX侧门玻璃31XXXX-XX-DFMEA-031DFMEA-XXXX侧风窗密封条32XXXX-XX-DFMEA-032DFMEA-XXXX充电口盖系统33XXXX-XX-DFMEA-033DFMEA-XXXX前防撞梁总成34XXXX-XX-DFMEA-034DFMEA-XXXX前后流水槽总成35XXXX-XX-DFMEA-035DFMEA-XXXX前舱总成36XXXX-XX-DFMEA-036DFMEA-XXXX前舱盖铰链37XXXX-XX-DFMEA-037DFMEA-XXXX地板总成38XXXX-XX-DFMEA-038DFMEA-XXXX开闭件钣金39XXXX-XX-DFMEA-039DFMEA-XXXX玻璃升降器40XXXX-XX-DFMEA-040DFMEA-XXXX货箱门铰链41XXXX-XX-DFMEA-041DFMEA-XXXX车门撑杆系统42XXXX-XX-DFMEA-042DFMEA-XXXX车门铰链43XXXX-XX-DFMEA-043DFMEA-XXXX门盖密封系统44XXXX-XX-DFMEA-044DFMEA-XXXX门盖锁系统45XXXX-XX-DFMEA-045DFMEA-XXXX顶盖总成车身饰件汽车车身饰件DFMEA全套资料。
汽车车身饰件DFMEA-组合仪表罩总成

☆
撞距离要求
100mm
驶员造成更多伤
组合仪表罩总成视野
组合仪表罩 总成不可遮 挡仪表可视
区域
组合仪表在视野 可视范围内不被 遮挡,视野清晰
仪表视野遮挡
看不清仪 表,影响驾 驶员安全性
和舒适性
8
☆
可靠耐久性/可靠性/环 境条件/温度湿度
组合仪表罩 总成
高温变形翘曲, 轮廓和曲面歪斜 仪表板系统及其 、高温接合面分 子系统需要在 离、高温气泡、 95%的车辆使用 粉化、渗出、缩 温度和湿度条件 孔、高温纹理消 下功能可靠 失、高温装饰层 膨胀、高温变形 、功能失效低温
间隙定义不合理
相互配合结构符合BP 规范IP-11021
数据评审/设 3 计校核/实车 2
验证
1、节点审
核,M2节点
3
仪表板系统对M1数据进
3
行评审确认
组合仪表罩总成卡子 卡紧力不够,卡口结 构未按照数据调整到
位
1、概念设计时,此项 校核不充分 2、设计评审
设计时未考虑组仪表 设计时做好组合仪表 罩总成单独拆卸空间 罩单独拆DMU校核
齐
灰边
怨
4
☆
组合仪表罩总成 组合仪表罩总成
与组合仪表配合 与组合仪表间隙
规避摩擦异响
不合理
间隙小产生 摩擦异响
4
☆
组合仪表罩 总成满足紧 固良好的要
求
组合仪表罩总成 禁锢良好
组合仪表罩总成 禁锢不良,组合
仪表罩易晃动
舒适度不 佳,影响内 饰质量评价
4
☆
组合仪表罩 总成
组合仪表罩总成 在不拆卸仪表板 条件下具备维修
要求
组合仪表罩要拆 卸仪表板才能维
汽车底盘DFMEA-后桥总成

质量;装配完成对桥壳 ABS传感器测头安装孔进 行封堵;齿圈外径、桥 壳ABS传感器安装面尺寸
2
装配过程中电 信号检测
3
检测
☆
总成无自调功能
确认图纸要求,保证总 成有自调机构
3
对总成件进行 台架试验
2
36
54
按GB21670要求 进行
李宏超
行驶性能
车轮正 常行驶
车轮螺栓断裂
丧失行驶能力
10
★
螺栓分布圆小、 螺栓个数少,螺
7
★
被齿螺栓拧紧力 矩不足
被齿螺栓拧紧力矩7585N.m,使用定扭矩扳手
进行校验
3
主减速器总成 运转试验
3
63
转弯过程中, 影响顾客精准感
差速器异响
知
7
半轴行星齿轮间 半轴行星齿轮间隙不大 ★ 隙过大或过小, 于0.35mm,且转动灵活 3
转动不灵活 。装配过程中100%检测
路试
4 84
满足顾客外 观漆面要求
稳定地传 输行驶动 力
行驶及驻车 工况下,有 效、稳定的 提供制动力 行驶及驻车 工况下,有 效、稳定的 提供制动力
支撑轴承, 稳定地传输 行驶动力
后桥壳、减壳 影响外观,顾客
生锈
抱怨
3
防锈级别选用低
参考标杆车样件/现有经 验
3
路试/中性盐雾 试验
3
27
主齿法兰盘断 裂
传动动力丧失
9
★
主齿法兰盘强度 参考其他车型参数/现有
制动鼓、制动器 总成磨损,行车 异响
4
★
制动鼓与制动器 背板结合部位外 轮廓设计不匹配
制动鼓与制动器背板外 轮毂匹配
汽车底盘DFMEA-后缓冲限位块

热衰退
影响零部件的 寿命
7
材料选择不合理
隔绝较大冲 击,限制悬 无氧化
架位置
氧化
影响零部件的 寿命
7
材料选择不合理
潜在失效模式及后果分析(DFMEA)
底盘技术部
编制人 编制日期 修订日期
FMEA编号: 第1页
共1页
现行设计控制
控制预防
频
度
控制探测
O
风
探 测 度 D
R险 P顺 N序
数
建议措施
措施执行后的结果
选择合理材料
1
耐久试验
48
隔绝较大冲 击,限制悬
架位置
满足冲 击耐久
限位块破 损
悬架冲击大, 悬架形成变大
8
材料不能满足要求,结构
设计不合理存在应力集中 问题
使用满足要求材料,合理设 计缓冲块结构消除应力
1
耐久试验
6 48
编制:
审核:
批准:
职责及目标
严
完成日期 采取的措施 重
及完成日期 度
S
频 度 O
探 测 度 D
风险顺序数 RPN选ຫໍສະໝຸດ 合理材料12 14
选择合理材料
1
2 14
选择合理材料
1
2 14
安装无脱落 无脱落 脱落
产生异响
8
拔出力设计不合理
合理设计拔出力
1
耐久试验
48
隔绝较大冲 击,限制悬 不吸水
架位置
吸水
缓冲块损坏 8
材料选择不合理
项目 功能
系统 子系统 部件 年型/车型
悬架系统 后悬架系统 后缓冲限位块
要求
DFMEA表(新版DFMEA-总装结构)

3L
尺寸链的计算 2 尺寸检验
3L
尺寸链的计算 2 尺寸检验
3L
尺寸链的计算 2 尺寸检验
3L
尺寸链的计算 2 尺寸检验
3L
尺寸链的计算 2 尺寸检验
3L
轴套设计 安装尺寸要 格,客户不满
求
意
6
控制臂总 成
保证产品的 安装尺寸要
求
安装尺寸不合 格,客户不满 意
零部件分析
零部件 要素(项
目/接 口)
零部件的功 能,要求,预 期输出及特性
失效原因
壳体
零件的尺寸设 计满足要求
尺寸设计不当
轴套
零件的尺寸设 计满足要求
尺寸设计不当
控制臂
零件的尺寸设 计满足要求
公司名称: 制造地址: 顾客名称: 车型/项目:
项目: FMEA开始日 FMEA修订日 跨职能团
设计潜在失效模式及影响分析 FMEA编号: 过程职责: 保密级别:
版本号:
页 码:
第
页,共
页
编制者/日期:
批准/日期:
范围定义:(针对具体产品详细说明) 1、产品适用车型: 2、客户针对此项目的特别要求:含技术要求、法律合规性、目录和标准零件 3、明确设计控制权及客户对接部门: 4、FMEA团队及会议机制: 5、FMEA完成步骤时间节点及要求:
尺寸设计不当
压装盖 板
零件的尺寸设 计满足要求
尺寸设计不当
齿环
零件的尺寸设 计满足要求
尺寸设计不当
齿型连 接套
零件的尺寸设 计满足要求
尺寸设计不当
O型圈*2
零件的尺寸设 计满足要求
尺寸设计不当
启动准备工作:(针对具体产品详细说明) 1、顾客要求转化清单: 2、FMEA的边界分析证据:设计框图、边界图、示意图、图纸、3D模型 3、类似设计经验教训:物料清单、风险评估、FMEA、防错要求、可制造性和可装配性设计、质量功能展开、质量/可靠性 历史(内部、零公里、现场失效、保修和索赔) 4、技术新颖性、创新程度、设计复杂性、人员和系统安全、网络物理系统 5、产品设计和使用的工况环境情况说明:
- 1、下载文档前请自行甄别文档内容的完整性,平台不提供额外的编辑、内容补充、找答案等附加服务。
- 2、"仅部分预览"的文档,不可在线预览部分如存在完整性等问题,可反馈申请退款(可完整预览的文档不适用该条件!)。
- 3、如文档侵犯您的权益,请联系客服反馈,我们会尽快为您处理(人工客服工作时间:9:00-18:30)。
系统:子系统:零部件名称:过程责任:零部件号:关键日期:
核心小组:
设计潜在
后悬架装置
设计潜在
车型/车辆类型:底盘悬架系统
系统:子系统:零部件名称:过程责任:零部件号:关键日期:
核心小组:
车型/车辆类型:底盘悬架系统
后扭力梁总成
系统:子系统:零部件名称:过程责任:零部件号:关键日期:
核心小组:
系统:子系统:零部件名称:过程责任:零部件号:关键日期:
核心小组:车型/车辆类型:底盘悬架系统
后减振器带缓冲块总成
设计潜在
后螺旋弹簧
设计潜在
车型/车辆类型:底盘悬架系统
系统:子系统:零部件名称:过程责任:零部件号:关键日期:
核心小组:后减振器带缓冲块总成
设计潜在
车型/车辆类型:底盘悬架系统
系统:子系统:零部件名称:过程责任:零部件号:关键日期:
核心小组:车型/车辆类型:底盘悬架系统
后减振器带缓冲块总成
设计潜在
系统:子系统:零部件名称:过程责任:零部件号:关键日期:
核心小组:前悬架装置
设计潜在
车型/车辆类型:底盘悬架系统
系统:子系统:零部件名称:过程责任:零部件号:关键日期:
核心小组:车型/车辆类型:底盘悬架系统
前副车架总成
设计潜在
系统:子系统:零部件名称:过程责任:零部件号:
关键日期:
下控制臂总成
设计潜在
车型/车辆类型:底盘悬架系统
核心小组:
系统:子系统:零部件名称:过程责任:零部件号:关键日期:
核心小组:车型/车辆类型:底盘悬架系统
横向稳定杆
设计潜在
系统:子系统:零部件名称:过程责任:零部件号:关键日期:
核心小组:前悬架支柱总成
设计潜在
车型/车辆类型:底盘悬架系统
系统:子系统:零部件名称:过程责任:零部件号:关键日期:
核心小组:车型/车辆类型:底盘悬架系统
连接杆总成
设计潜在
附件
计潜在失效模式及后果分析
(DFMEA)
FMEA编号:
编制人:
修订人:
第 1 页共
计潜在失效模式及后果分析
(DFMEA)
FMEA编号:
编制人:
修订人:
第 2 页共
计潜在失效模式及后果分析
(DFMEA)
FMEA编号:
编制人:
修订人:
第 3 页共
计潜在失效模式及后果分析
(DFMEA)
FMEA编号:
编制人:
修订人:
第 4 页共
计潜在失效模式及后果分析
(DFMEA)
FMEA编号:
编制人:
修订人:
第 5 页共
计潜在失效模式及后果分析
(DFMEA)
FMEA编号:
编制人:
修订人:
第 6 页共
计潜在失效模式及后果分析
(DFMEA)
FMEA编号:
编制人:
修订人:
第 7 页共
计潜在失效模式及后果分析
(DFMEA)
FMEA编号:
编制人:
修订人:
第 8 页共
计潜在失效模式及后果分析
(DFMEA)
FMEA编号:
编制人:
修订人:
FMEA编号:编制人:修订人:
目标完成日期
度D
控制探测
控制预防
第 10 页
共 第 9 页
共 计潜在失效模式及后果分析
(DFMEA)
探
计潜在失效模式及后果分析
(DFMEA)
FMEA编号:
编制人:
修订人:
第 11 页共
计潜在失效模式及后果分析
(DFMEA)
FMEA编号:
编制人:
修订人:
第 12 页共
附件6
共 12 页
共 12 页
共 12 页
共 12 页
共 12 页
共 12 页
共 12 页
共 12 页
共 12 页
共 12 页
共 12 页
共 12 页。