屏蔽线8D报告(头部到磁环尺寸不符)案例
数据线8D报告(头部摇摆NG)案例
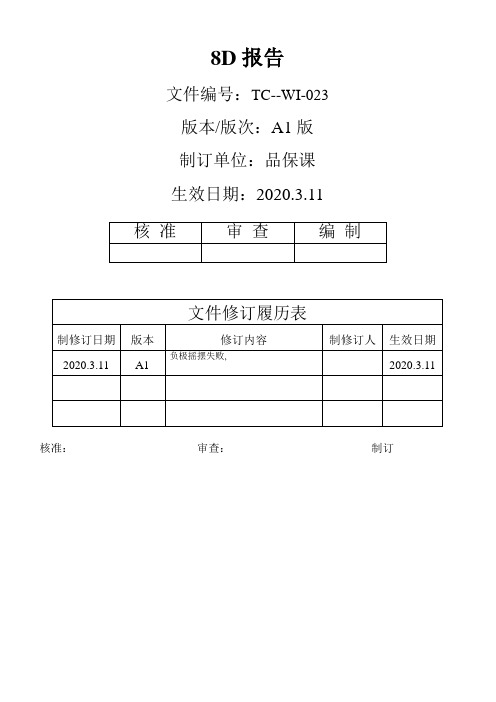
8D报告文件编号:TC--WI-023版本/版次:A1版制订单位:品保课生效日期:2020.3.11核准:审查:制订协力厂商材料不良反馈通知书CAR NO.:发生时机█进料检验不良□在线生产不良□客人抱怨不良□其他状态□首次发生█重复发生料号/图号2601005500112 订单编号/ 数量/抽样数9000/2EA 检验/填表人2020/03/11规格说明DCCORD 1571 #20 PL518 BLK2500 SR119LEI Lot.No. 1403012570不良品数2EA 审核2020/03/11进料日期2020/03/10 厂商Lot.No. / 不良比率100% 核准2020/03/11发生站别IQC 是否免检否是否停线/ 信息传达日期2020/03/12 Discipline 1不良描述/Problem description: █严重缺点(CR) □主要缺点(MAJ) □次要缺点(MIN)PLUG负极摇摆失败,抽2PCS,不良2PCS.实测1PCS 断15/45=33.3%。
1PCS19/45=42.2%.Discipline 2 不良原因分析成员/Team member:(including Name, Department)Dept Person Position Phone number Mail address业务部生产部工程部品管部QE其他Discipline 3 原因分析/Root cause:(What caused the failure induced by 5W/2H)1.成型机调机过程中,技术员先将压力调节到最大(压力一压70k g~85kg 二压40kg~55kg 材质PVC 硬度30P)进行调试成型,当成型出来内模达不到品质要求时,再将压力调小,直到成型出来内模达到品质要求,造成头部负极摇摆断铜丝原因是成型机调机过程中压力过大导致铜丝被冲断.Discipline 4 不良品外流原因调查/Escaped reason:(Why the failure materials escaped from your factory)出货前有做摇摆试验,试验结果是OK的,所以判合格出货。
完整的8D报告标准范本
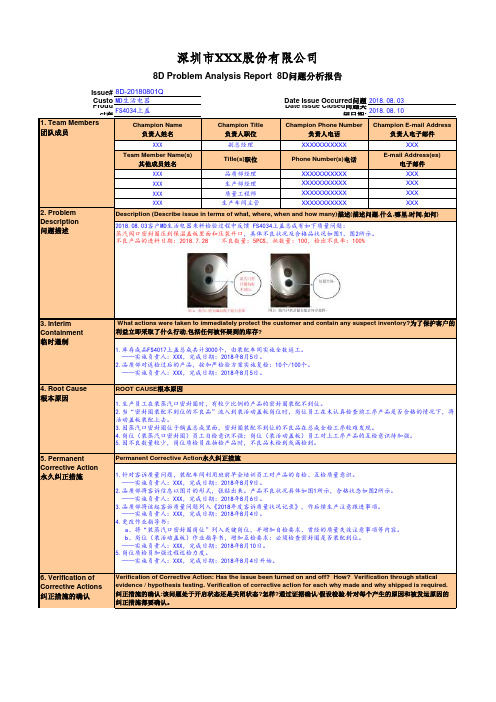
Issue#8D-20180801Q Custo MD生活电器Date Issue Occurred 问题2018.08.03Product 产FS4034上盖Date Issue Closed 问题关闭日期:2018.08.10Champion Name 负责人姓名Champion Title 负责人职位Champion Phone Number负责人电话Champion E-mail Address负责人电子邮件XXX副总经理XXXXXXXXXXX XXXTeam Member Name(s)其他成员姓名Title(s)职位Phone Number(s)电话E-mail Address(es)电子邮件XXX 品质部经理XXXXXXXXXXX XXX XXX 生产部经理XXXXXXXXXXX XXX XXX 质量工程师XXXXXXXXXXX XXX XXX生产车间主管XXXXXXXXXXXXXXVerification of Corrective Action: Has the issue been turned on and off? How? Verification through statical evidence / hypothesis testing. Verification of corrective action for each why made and why shipped is required.纠正措施的确认:该问题处于开启状态还是关闭状态?怎样?通过证据确认/假设检验.针对每个产生的原因和被发运原因的纠正措施都要确认。
6. Verification of Corrective Actions 纠正措施的确认8D Problem Analysis Report 8D 问题分析报告深圳市XXX股份有限公司Description (Describe issue in terms of what, where, when and how many)描述(描述问题,什么,哪里,时间,如何)2018.08.03客户MD生活电器来料检验过程中反馈 FS4034上盖总成有如下质量问题:蒸汽阀口密封圈压到保温盖板里面和压裂开口,具体不良状况及合格品状况如图1、图2所示。
编织线起毛异常8D报告(USB屏蔽数据线)

ISCIPLINE 4 DESCRIBE THE ROOT CAUSE(根本原因描述)
责任人:
日期:201910-6
1.编织线起毛:对不良品进行分析,此款产品外皮编织线较软,制程打端子后摆放过程中较密乱容易钩碰导致编织
线拉丝起毛造成。
2.因制程检验过程中,因此异常较轻微,检验员以常规外观要求标准判定出货,确认为人0
(FR20-10)
DISCIPLINE 5 PERMANENT C/A PLAN(永久计划)
责任人:
日期:2019-10-6
1.编织线起毛:现针对此起毛异常,要求后续制程将打好端子的线材摆放整理好,预防乱放导致端子钩碰编织造成 起毛异常。 2.现制程外观检验,已按照客户最新判定标准要求进行检验,预防再次流出.
DISCIPLINE 6 VERUFICATION OF EFFECTIVENES(有效的确认) 责任人:
作成部署:工程部 作成日期:2019年10月6日
品 名:USB编织屏蔽数据线
品 番:
C360-868线材
文件编号: GC-EX-02-01
SCAR
Supplier Corrective Action Report
V
Q 供应商名称
A 填
写 来料数量
栏
品名 样本数
DISCIPLINE 2 DESCRIBE THE PROBLEM(问题描述)
编织线起毛异常。
线材 1
料号 不 良 率 统计中
A级SCAR,需3天内回复
B级SCAR,知会,无须回复 SCAR NO PDR NO.
收料编号
收料日期 日期:
2019/10/6 2019/10/6
DISCIPLINE 3 CONTAINMENT PLAN(围堵计划)
外观不良8D报告

1D:团队分析团队:团队长:总监成员:审核团队:团队长:成员:批准人员:供应商领导:2D:问题描述产品型号:发生时间:检验数:产品类型:PCM 异常类别:外观不良不良数:现象:1、2015年9月9日贵司试产HB366481的来料不良图片,其中脏污不良0.99%,定位孔不良104PCS,异物、压伤不良48PCS,不良率1.98%,2、此板为打样试产板,目前我司仓库已无该板库存,在线有小批量试产板6.5K在钻孔工序,将不良信息反馈给产线,重点管控以上不良3D:原因分析1、脏污产生原因:从不良图片分析,此不良为异物反粘板面造成脏污,查询产线生产工具,产线装板使用吸塑盒部分存在胶状物质,容易返粘板面造成脏污2、孔内毛刺、油墨入孔产生原因:此板为无卤素材料,材料脆性较大,钻孔后孔内位置毛刺无法避免,因毛刺未及时处理,阻焊之后孔内油墨不易显影完全,存在油墨残留现象3、黑油物产生原因:从不良图片分析,此不良为黑油印刷前,清洁不足导致,近期无尘车间改造,造成外来杂物增加,生产过程中清洁不到位容易导致杂物残留4、不良流出原因:此板为试产样品,检查人员检板过程中,为尽量满足多交货,针对部分外观缺陷问题板未做报废,导致不良流程4D:应急措施1、此板为试产板,贵司已无该板库存2、我司仓库已无该板库存3、在线6.5K二次打样板,在钻孔工序,项目组重点跟进以上异常5D:已进行的纠正行动验证:1、针对所有吸塑盘进行检查,有脏污、异物的统一挑出清洁,避免异物反粘板面2、目前产线施工改造已经完成,无尘室车间无尘含量达标,黑油每次印刷前,按要求清洁台面网版,防止杂物残留6D:永久纠正行动:1.钻孔后针对毛刺突出不良,安排刮毛刺处理(要求,孔径必须合格),钻孔后增加除胶渣流程,减少孔壁粗糙度2.入检验标准对员工进行培训;7D:防止问题再发生的措施1.针对所有新项目样品研发阶段必须严格执行合同评审制度,针对特殊工艺或软硬结合产品要求研发部门必须组织工程、生产、工艺、品质共同评估工艺及操作可行性,确定相关检验标准和验证方案并形成有效记录和控制计划来指导一线生产;2.所有新产品转批量之前必须出具样品品质记录、客诉记录及过程重要工艺问题点记录经品质经理和技术总监审核、副总批准后方能正式投料生产;8D:解决问题小组工作的认可如有侵权请联系告知删除,感谢你们的配合!。
车载天线8D报告案例 开路不良
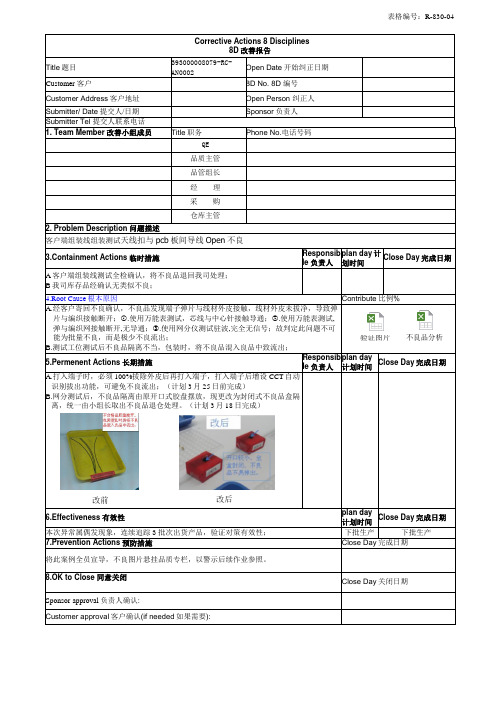
表格编号:R-830-04Corrective Actions 8 Disciplines8D改善报告Title题目393000008079-RC-AN0002Open Date开始纠正日期Customer 客户8D No. 8D 编号Customer Address客户地址Open Person 纠正人Submitter/ Date提交人/日期Sponsor负责人Submitter Tel 提交人联系电话1. Team Member改善小组成员Title职务Phone No.电话号码QE品质主管品管组长经理采购仓库主管2. Problem Description问题描述客户端组装线组装测试天线扣与pcb板间导线Open不良3.Containment Actions临时措施Responsible负责人plan day计划时间Close Day完成日期A客户端组装线测试全检确认,将不良品退回我司处理;B我司库存品经确认无类似不良;4.Root Cause根本原因Contribute比例%A.经客户寄回不良确认,不良品发现端子弹片与线材外皮接触,线材外皮未拔净,导致弹片与编织接触断开;①.使用万能表测试,芯线与中心针接触导通;②.使用万能表测试,弹与编织网接触断开,无导通;③.使用网分仪测试驻波,完全无信号;故判定此问题不可能为批量不良,而是极少不良流出;B.测试工位测试后不良品隔离不当,包装时,将不良品混入良品中致流出;5.Permenent Actions长期措施Responsible负责人plan day计划时间Close Day完成日期A.打入端子时,必须100%拔除外皮后再打入端子,打入端子后增设CCT自动识别拔出功能,可避免不良流出;(计划3月25日前完成)B.网分测试后,不良品隔离由原开口式胶盘摆放,现更改为封闭式不良品盒隔离,统一由小组长取出不良品退仓处理。
(计划3月18日完成)6.Effectiveness有效性plan day计划时间Close Day完成日期本次异常属偶发现象,连续追踪3批次出货产品,验证对策有效性;下批生产下批生产7.Prevention Actions预防措施Close Day完成日期将此案例全员宣导,不良图片悬挂品质专栏,以警示后续作业参照。
8D报告
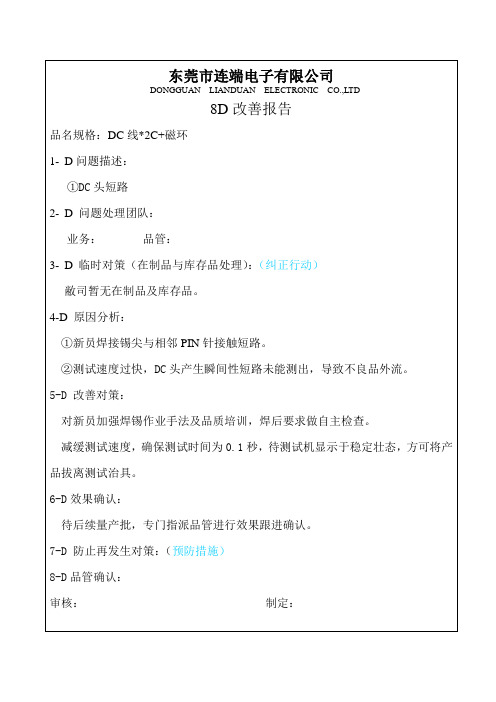
DONGGUAND
8D改善报告
品名规格:DC线*2C+磁环
1-D问题描述:
①DC头短路
2-D问题处理团队:
业务:品管:
3-D临时对策(在制品与库存品处理):(纠正行动)
敝司暂无在制品及库存品。
4-D原因分析:
①新员焊接锡尖与相邻PIN针接触短路。
8-D品管确认:
审核: 制定:
②测试速度过快,DC头产生瞬间性短路未能测出,导致不良品外流。
5-D 改善对策:
对新员加强焊锡作业手法及品质培训,焊后要求做自主检查。
减缓测试速度,确保测试时间为0.1秒,待测试机显示于稳定壮态,方可将产品拔离测试治具。
6-D效果确认:
待后续量产批,专门指派品管进行效果跟进确认。
7-D 防止再发生对策:(预防措施)
电子变压器8D报告(尺寸超规格)实例样板
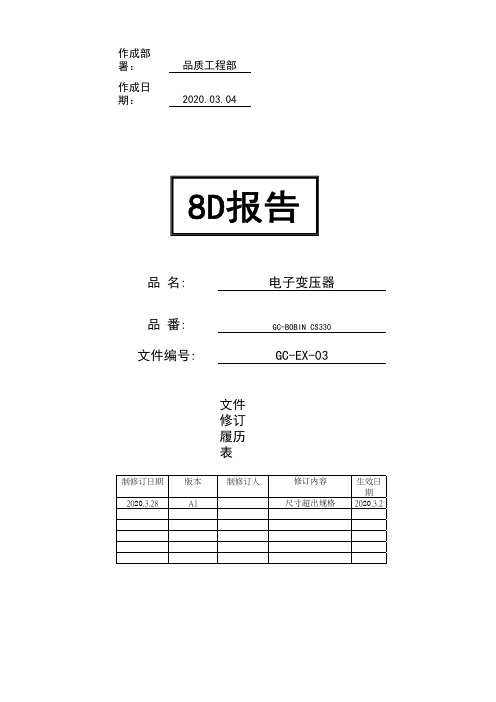
Owner(责任 Due day(完成日
人)
期)
2020.04.01
D5根本原因及
长期对策
(Root cause & Long term action(长期对策) long term
(Prevention & Spread) D8标准化
(Standardizatio n)
类似系列产品列入质量管理项目. 将此不良现象记录在《品质异常备忘录》中,以便下次生产时能重点管控。
Approved by(核准)
Delta follow up/追踪
Report by(报 告人)
VQA Engineer verify(工程师 确认)
2020.04.01
任人)
成日期)
D6效果确认 (Verification of
the CA's effectiveness)
After(改善后):
E2:12.4±0.1 1号模12.43 2号模12.42 3号模12.36 4号模 12.44 5号模12.44 6号模12.42
2020.04.01
D7防呆及水平展 开
Vender(厂商)
P/N(料号)
3197700602
D1问题描述 (Problem
Description)
D/C(生产周期)
20.03.28
Lot(生产批号)
20.03.28
when(发生时间):2020.03.28 where(发生地点):(区外) What(问题描述): 3197700602内孔尺寸超出规格
8D改善报告(关于探测器生产效率低下的问题)
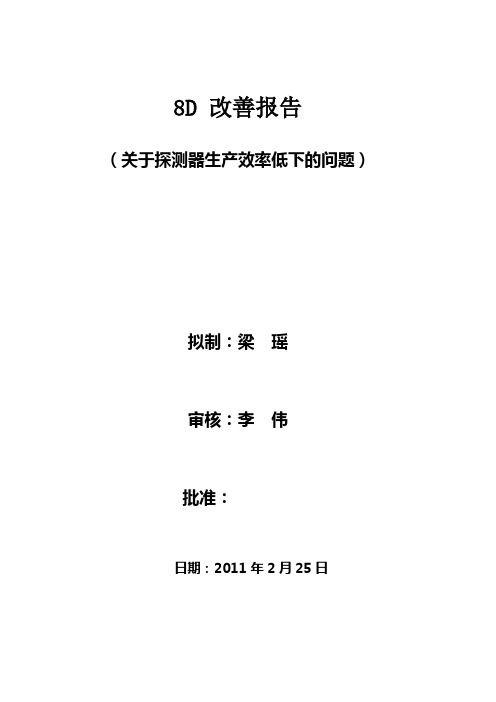
8D 改善报告(关于探测器生产效率低下的问题)拟制:梁瑶审核:李伟批准:日期:2011年2月25日深圳市泰和安科技有限公司制造中心D1、组建小组2011年1月15日针对感烟探测器LA1550A效率生产过程中存在效率损失问题组建的处理小组。
D2、问题描述主要现象:1、停工等待时有发生,如粘晶振、防潮工位的等待时间多于作业时间。
2、在制品逐工位堆积。
3、现场工作纪律差,员工抱怨多。
4、工作台物料多,摆放乱。
5、作业标准不清晰。
D3、确定紧急对策为了尽快提高探测器产品的效率,特制定临时对策并立即执行:遵循ECRS四大原则:1、取消制作刀卡岗位。
2、合并粘胶和防潮岗位。
3、重排黑体插装和装箱岗位由离线作业改为在线作业。
4、简化屏蔽罩焊锡操作内容。
D4、问题分析及查找原因针对生产效率低下问题进行如下分析,见下图:因果图人员机器环境岗位技能不熟设备效率不达标作业环境不佳线体平衡率低发放不及时现场指挥乱来料不良多方法材料那么,导致生产效率低下的原因究竟是什么?见要因确认调查表:要因确认表D5、制定永久对策根据确定的要因,制定对策表如下:对策表具体改善措施如下:改善前与改善后线体平衡率的对比测算每个工位的作业时间,依各工位间作业时间的差距,均衡各工位作业内容,实现提高线体平衡率。
防潮炉挂钩更改改善目的挂钩更改,减少挂板操作时间。
目视管理改善前改善后改善目的通过目视管理,培养员工自主岗位的管理,实现员工的自主控制习惯。
改善目的元件在插装前统一先将脚成形,减少剪脚岗位作业时间,提高线体平衡率。
更改卡板位置改善前改善后改善目的更改卡板放置位置,减少搬运浪费。
改善目的更改工装弹簧,减少员工劳动强度。
D6、执行及验证永久对策针对上述要因,按对策表执行结果如下图:按照《对策表》的“措施”严格执行,探测器产品的生产效率有了明显提高,已由350pcs/小时提高到450pcs/小时。
整线提效率≈28.6 %改善前与改善后产量对比图72600 99000改善前产量改善后产量从上述图表显示,每个月按正常生产进行,改善前(72600个)比改善后(99000个)单月少生产感烟型探测器26400个。
8D报告( 电性不良或线材总长短)

□Yes □No
② 要求头部脱皮作业员脱皮作业时先看清楚印条方向再进行脱皮作业,每脱完一把要抽20℅进行全检,并将已脱好的标准品做品质提醒广告牌悬挂在脱皮机挂板上提醒作业员注意正极与负极脱皮方向(见附件品质提醒广告牌
)。
IPQC重点巡查此工站。
责任人:刘建华 曹菊 执行日期:2020.4.16
贴在作业员正前方,提醒作业员将极性反不良焊点检出(见附件OK焊点广告牌 )。
责任人:刘建华 曹菊 执行日期:2020.4.16
3.线材总长短:①规定裁线站裁线作业时,每圈线线尾都必须100℅量测线材长度,修订裁线站SOP,SOP上增加此要(见附件SOP ) 责任人:刘建华 曹菊 执行日期:2020.
4.16
②测试机灵敏度按线材测试学习的长度减5℅MAX线材测试学习的长度进行调试测试机,测试时可以将线材总长短的不看板.pdf
焊点看板.pdf
裁线SOP.pdf
电测SOP.pdf。
8D报告(线材尺寸与规格不符)
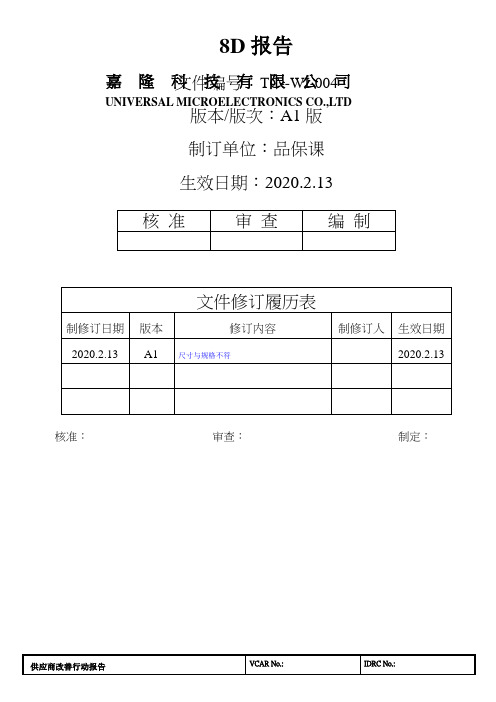
8D报告制订单位:品保课生效日期:2020.2.13核准:审查:制定:退貨揀用寬放嚴重Discipline2团队成员 / Team Members:工 程/ Engineering: 品 保/ Quality Control: 制 造/ Manufacturing:Discipline3原因分析 / Root Cause Analysis:完成日/ Finish day:A. 不良流出原因:①外检作业站是用钢尺100℅测量剥头长度的,钢尺量测读取最小数值为mm ,而不能精确到0.00mm ,造成超出公差范围0.13mm-0.62mm 的剥头未被检出,导致不良品流出。
②FQC ,OQC 未抽检到剥头长不良导致不良品流入客户端。
B.不良产生原因:尾部剥头是尾部处理机(分叉,脱皮,扭线,比剪一起完成)生产的,经调查是作业过程中挂线架与尾部处理机的距离过远,造成线材尾端放入尾部处理机生产过程中,线材被尾部处理机拉直且有后退现象,比剪作业时由于线材后退,比剪掉的铜丝过少,导致剥头尺寸过长。
Discipline4短期改善对策 / Temporary Corrective Action:完成日/ Finish day: 2020.2.13①无库存品,无在途品,无在制品。
②客户端库存品,请帮忙特采使用。
Discipline5永久改善对策 / Permanent Corrective Action:完成日/ Finish day: 2020.2.12①召集班长、IPQC 、尾部处理作业员、外检作业员现场分析宣导。
要求尾部处理作业时,挂线架与尾部处理机的距离不能过远,线材放入尾部处理机作业移动过程中,线材必须始终保持弯曲状态,避免尾部处理过程中因线材被拉直后退造成剥头尺寸长不良,并规定尾部处理线架放线不可超过1000PCS/架。
外检工站后续改为用卡尺量测剥头长度。
责任人: 执行日期:2020.2.12②FQC 、OQC 针对此不良加严抽检三批,由二级抽样标准提高到三级抽样标准进行抽样检验,直至连续三批没有发现此类不良则转为正常检验。
8d报告生产案例范文

8d报告生产案例范文案例背景近日,我司生产线上出现了一起质量问题,部分产品出现了严重的尺寸偏差现象。
为了彻底解决这个问题,我们迅速展开了8D报告的问题解决流程,并于XX月XX日完成功能过该案例。
问题描述在生产线上生产的产品尺寸偏差较大,超过了允许范围。
该问题对产品的质量造成了严重影响,需要尽快解决。
初步原因分析通过对问题进行初步调查和分析,我们发现可能的原因有:1. 模具老化导致的尺寸不稳定。
2. 操作工操作不当,没有按照规定的工艺流程进行生产。
3. 人为因素,例如操作工操作不规范。
问题解决措施针对问题的初步原因分析,我们制定了以下解决措施:1. 进行模具更换,确保新的模具尺寸稳定。
2. 重新培训操作工,提醒他们严格按照规定的工艺流程进行生产。
3. 强调操作工严格操作的重要性,加强对操作工的监督和管理。
8D报告步骤第一步:组建问题解决小组我们成立了一个专门的问题解决小组,由相关的技术人员、质量人员和生产人员组成。
第二步:问题描述和原因分析我们详细描述了问题,按照8D方法分析了问题的原因。
第三步:紧急应对措施在问题暴露后,我们立即采取了紧急应对措施,暂停了全部产线,并进行了模具的更换。
第四步:根本原因分析通过对问题的深入调查和分析,我们发现问题的根本原因是操作工操作不规范导致的。
第五步:长期解决方案为了彻底解决问题,我们制定了长期解决方案:重新培训操作工,提醒他们严格遵守操作规程,确保生产过程规范。
第六步:实施长期解决方案为了确保长期解决方案的有效实施,我们组织了培训课程,并加强了对操作工的管理和监督。
第七步:验证解决方案的有效性我们对解决方案进行了实际生产和质量监控,验证了解决方案的有效性。
第八步:预防措施为了避免类似问题再次发生,我们进一步加强了对模具使用寿命的监控和管理,并加强了操作工的培训和管理。
结果和总结通过本次的8D报告问题解决流程,我们成功解决了生产线上的尺寸偏差问题,并且在以后的生产中没有再次出现类似问题。
电源线8D报告( 音叉弹片内缩尺寸不符)案例

1 品为 4.56-4.78mm,不良率 5.6%,请分析具体原因提出改善措施并附上相关佐证资料.
供应商回覆期限: Reporting Deadline
2020.6.11
核准: Approved by
发出: Issued by
2020.6.7
Discipline 团队成员 / Team Members:
1.客户端库存品 960PCS 退回我司重工处理,外箱贴“重工 OK”标签。 4
2.无库存品及在制品。
永久改善对策 / Permanent Corrective Action:
完成日/ Finish day: 2020.6.10 完成日/ Finish day: 2020.6.13
1.生产线在尾数结单或转机种时,要求作业员需将前一机种的物料或成品全部清理干净,并通知 IPQC、班长确认好后才能生产
对策验证 / Verification of Effectiveness:
Discipline 改善对策已从 2020.6.9 日起实施,改善效果待下批订单生产时验证。
6
完成日/ Finish day: 2020.6.9
Discipline 防止再发/Prevent Recurrence: 7 无文件修订
2
工 程/ Engineering:
品 保/ Quality Control:
原因分析 / Root Cause Analysis:
制 造/ Manufacturing: 完成日/ Finish day:
A.不良流出原因:外检站、FQC 都是用肉眼检铜钉音叉片内缩尺寸的(卡尺,钢尺及一般普通量具是量测不到铜钉音叉片内缩尺 Discipline
完成日/ Finish day: 2020.6.9
数据线8D报告( 歪头尺寸短标签重印)综合案例

5. 改善對策
■ 永久改善對策.
1. PLUG头变形不良: ①. 成型作业员成型头部取模时双手拿模条垂直取出,模具与网尾角度不可超过30度, 分再次取模。 ②. 头部成型冷却时间由3秒更改为5秒。 ③. 要求外检作业员必须360度旋转检查PLUG头。
2. 条码标签模糊不清,条码扫描仪不能识别: ①. 购买新的二维条码打印机。 ②. 后续出货,OQC必须用条码扫描仪100℅对条码标签进行扫描,确认条码标 签都 能被识别出来后才能判OK出货。
3. 尾部剥头尺寸不符:待下批订单生产时验证改善对策的效果。
4. 不良发生原因.
■ 不良流出原因
1. PLUG头变形不良:作业员未旋转检验PLUG头造成变形不良未被检出导致不良 品流出。
2. 条码标签模糊不清,条码扫描仪不能识别:出货检验时OQC有发现条码标签有 模糊现象,OQC用条码扫描仪对条码标签进行扫描能将条码标签扫描出来,但未100 ℅扫描条码标签,导致有条码扫描仪不能识别的条码标签流出。
2. 實際不良确认
1. PLUG头变形(歪头):实际确认是有PLUG头变形变形不良,客户端库存品: 15100PCS,旭华派人到客户端全部重工处理。
2.条码标签模糊不清,条码扫描仪不能识别:实际确认是有条码标签模糊不清,条码扫 描仪不能识别条码标签,旭华派人到客户端全部重新贴OK的条码标签。
3.剥头尺寸不符:实际确认是有剥头尺寸不符现象,客户端库存品:1770PCS退回旭 华重工处理。
1. PLUG头变形不良:改善对策执行后,1/18日有生产2000PCS未发有PLUG头变 形不良,1/24出货1770PCS,客户端未发现有PLUG头变形不良。
2. 条码标签模糊不清,条码扫描仪不能识别:改善对策执行后,打印出来的条码标 签用条码扫描仪进行识别,100℅都能扫描出来。 1/24出货1770PCS,客户端未 发现有条码标签模糊不清,条码扫描仪不能识别。
尺寸不良8d报告改善的案例

尺寸不良8d报告改善的案例8d报告模板在质量管理活动中,我们常用到各种各样的质量工具,而大多数情况下,都是多种质量工具的混合使用.不管使用工具的多或者少,每种工具所发挥的成效都是特定的.有些工具长用记录,有些长于分析,有些长于决策,有些长于思考,而问题的解决都是多种工具配合使用所得,而这种配合的模式就形成了解决问题的套路.在某些大企业中,为了管理的方便,格式的统一,往往会固化成特定的标准化的模板.今天我们一起学习的这个工具就是一种套路,它就是福特汽车公司惯用的g8d报告.8d又称团队导向问题解决方法、8d问题求解法.是福特公司处理问题的一种方法,它提供了一套符合逻辑的解决问题的方法,同时对于统计制程管控与实际的品质提升架起了一座桥梁.目前已广泛应用于汽车制造行业,取得了显著的经济效益和社会效益.8d主要用于汽车及类似加工行业的问题解决方法.原始是由ford公司,全球化品质管制及改善的特殊必备方法,之后已成为qs9000/iso ts16949、福特公司的特殊要求.凡是做ford的零件,需采用8d作为品质改善的工具.后来名气大了,其它车厂也移植了福特的做法、使之成为汽车行业的标准做法.目前国际汽车行业(特别是汽车零部件产家)广泛采用来解决产品质量问题最好的、有效的方法.8d方法是一种归纳与推测的问题解决方法.归纳法以基于观测数据为起点,建立与数据一致的推测.推测法以一种推测为起点,并通过收集数据并分析来确定数据是否同理论一致,从而企图证明一个推测是否能适用于某个特定的条件.在8d程序的初始阶段期,主要是归纳法.收集以及分析数据,从而描述问题.确定可选择性的根本原因推测,并且与问题描述比较,从而确定最佳的推测.然后,通过收集数据,采用演绎法来确定这个最佳推测是实际的根本原因.解决问题时,团队经常在归纳法与演绎法之间转换.这通常是完成工程任务的最有效的方法.8d方法有以下几方面的明显作用:通过建立小组训练内部合作的技巧;提供一种通用的流程有效确定并解决问题;防止相同或类似问题的再发生;增加管理层对问题本身及解决方法的理解;鼓励直接开放的问题解决方法;提高顾客满意度,增强其对供方的产品和过程的信心.8d方法适用于以下两方面的情形;1.用于解决各类可能遇到的简单或复杂的问题;8d方法就是要建立一个体系,让整个团队共享信息,努力达成目标.8d本身不提供成功解决问题的方法或途径,但它是解决问题的一个很有用的工具;2.亦适用于过程能力指数低于其应有值时有关问题的解决;面对顾客投诉及重大不良时,提供解决问题的方法.我们常见的质量问题主要有两种类型:变异引起的问题和从未满足要求的问题.8d这套方法特别适合于解决由某个变化导致的问题,或者说是特殊原因引起的问题;6-sigma这套方法特别适合于解决从未满足要求的问题,或者说是普通原因引起的问题.8d方法和6-sigma都是用于解决质量问题的有效工具,两者在解决问题中相辅相成.8d是解决问题的8条基本准则或称8个工作步骤,但在实际应用中却有9个步骤:d0:准备8d过程d1:组建团队d2:描述问题d3:制定临时处置措施(ica)d4:确定并验证根本起因和遗漏点d5:选择并验证针对根本原因和遗漏点的永久性纠正措施(pca) d6:执行并确认pcad7:预防问题重现d8:表彰小组和个人的贡献针对每一步,我们详细介绍其使用过程:d0:准备8d过程实施本阶段的原因:g8d过程是一个可能涉及大量人力、时间和资源的过程,如果使用不适当将会浪费很多时间、人力和相关的一些资源.d0帮助我们把焦点放在问题上,以便有效地使用资源.本阶段实施过程:了解症状并量化症状,决定是否需要era,选择并验证era,执行并确认era,查看是否适用g8d标准.紧急反应措施(era)是保护顾客及相关的各方不受症状的影响的任何措施,它在g8d把问题和症状区分开来确认g8d是否有必要启动时应用.症状是可测量的事件或效果(它们必须是顾客体验到的),它表示一个或多个问题存在.如果没有症状,你就无法得知有问题存在.当症状能被测量或量化时,它才被考虑在内.通常有许多工具可以用来测量并量化故障:paynter图,柏拉图,运行(趋势)图,风险图等.g8d的适用标准:1.症状被定义;2.确定了顾客;3.存在性能差距;4.原因未知;5.管理层致力于从根本起因的层面去解决问题,并采取预防措施防止问题再次发生;6.症状很复杂,不可能单凭一个人的能力完成.如果六个标准都满足,并且没有其他的g8d团队为同样的或类似的问题工作,那么就应该开始g8d过程.d1:组建团队原因:组建团队是g8d过程中的重要部分.团队的功能需要花时间去增强,但是非常重要的是,一个人很少能拥有解决复杂故障所有必要的资源、信息、和技能.另一方面,合适的人一起工作能包括所有必要的特性,这建立在每个有关人员的技能的基础之上.建立一个团队是g8d过程的真正开始;团队成员的指导方针:1.团队成员的人数控制在4到10个之间;2.选择具有所需技能、知识、资源、权力等,这样的人作为团队成员来解决现有的问题;3.各类成员之间合理搭配;4.按需要调整团队成员.g8d的过程依赖于所有团队成员的努力来达到团队的目标.为了达到团队目标,每个成员扮演一个角色.团队设置负责人,团队领导,成员及其它角色.实现团队角色的指导方针:1.角色不是特指某个人,而是指要行使的职责;2.成员通常要在会议持续期间或是更长的时间内充当某个固定的角色;3.会议中角色的互换会导致混乱;4.一些角色是可以共同承担的,比如记录员等;5.监督人是g8d生产过程中的一个角色,然而,监督人不是团队的成员.6.调解工作在整个讨论过程中是必不可少的,通常这个角色由某个领导承担.团队运作程序的三个要素:1.确定团队运作的基本规则;2.分配任务、维护和过程观察;3.使用有效沟通交流的技巧.d2:描述问题目的:将问题清楚并且客观的描述会使问题最终得到有效的解决.帮助团队将焦点放在实际的问题上,避免直接对问题下结论或者作没有根据的设想.对问题的描述要基于观测的内容而非结论.要描述好一个问题,我们需要:1.对问题进行陈述;问题陈述应该是简单,简洁明了的陈述,它确定了发生问题的对象及其这个问题的缺陷.一个问题陈述能让团队关注,也能让范围缩小到寻找问题的根本原因上,通常当作问题描述的开端.2.对问题进行描述;问题描述是指根据问题是什么和不是什么,但可能是某种状况来确定问题的范围.一个详细的问题描述包括四方面的信息,什么时候、什么地方、发生什么及其问题的严重程度如何.问题陈述告诉了你最基本的事实,但是详细的问题描述给了你找到根本原因的细节.d3:制定临时处置措施(ica)目的:为团队找到问题产生的根源争取时间;保护顾客不受问题影响;ica是针对故障而非根本起因,在知道根本起因之前保护顾客.如果根本起因被查明,或者era(应急处理措施)足够可靠来继续保护顾客,可以不需要ica.ica与era的差异:era以最小的支撑数据执行.ica为调查提供更多的机会.任何你执行的ica必须保护顾客使其免受故障而不导致新故障的出现.同样,单一ica可能不够.你可能需要执行多个ica以充分保护顾客.执行ica的步骤;1.选择ica;确定选择标准,分析执行ica的好处,分析ica的风险性,在好处和风险性的最好平衡点选择ica.2.验证ica;实施前证明能保护顾客不受问题影响,能提供前后的对比,证明ica不会产生新的问题.常见的验证方法有:实验,演示,类似措施对比等.3.执行ica;按照pdca的循环进行,并制定行动计划.4.确认ica.确认是在成功的验证后,确认ica执行没有产生新的问题,确认形式:售前验证和售后顾客的验证.d4:确定并验证根本起因和遗漏点目的:找出根本起因是任何故障解决成就的重要部分.当确定了根本起因,可以在最根本的程度上解决一个故障.任何不是从根本起因入手的故障解决方案都仅仅是一个权宜之计,当识别出根本起因,就可以完全的消除了整个故障并使它决不再发生.原因的几种分类:可能原因:任何原因,常在一个因果图表里识别,它描述一个结果可能怎样发生.最可能的原因:根据可用的数据得到的一个理论,它可能最能解释详细的问题描述。
8D失效分析报告

8D-FAILURE ANALYSIS REPORT8D失效分析报告Subject:Yippee 3G喇叭短路问题Project Name 工程名Yippee 3GMart Name市场名Part lot 批号Ratio (%) 比率Issued Date 发出日期2011-06-21Issued By发出人熊家利D1. Problem Solving Team (PST) 异常处理成员Team leader:Team Member:崔燕、张新富、焦巧峰等Team Date:2011-6-21(周二)D2. Problem Description 异常说明6月20号晚班生产Yippee 3G,MMI检出6PCS铃音小故障机,确认3PCS发现有2PCS为喇叭固定在屏蔽盖上受压焊点与屏蔽盖短路(测量喇叭的线端与地短路)(如图1)。
图1D3.Develop Interim Containment临时措施初步分析是喇叭定位不准后,合壳时受压导致喇叭线焊点与屏蔽盖之间存在较大压力,当焊点处黑胶破损后就出现短路现象(如图2),临时对策是申请定位喇叭夹具,使用夹具装配喇叭.图2D4.Define & Verify Root Cause and Escape Point(确定根本原因及疏漏点)根本原因分析为:部分喇叭焊点(带黑胶)高出磁杯面,组装后不可避免的会与屏蔽盖干涉挤压,当黑胶压破后就出现短路,目前有两家供应商供应此喇叭,图3所示为供应商联创的规格书,可以看出PCB是浮于喇叭塑胶件上的(红圈处),而图4所示为供应商豪声的规格书,PCB是沉于喇叭塑胶件里的(红圈处),从设计上看,豪声的设计优于联创,更能保证喇叭焊点低于磁杯面。
前期评审中默认此处焊点就是低于磁杯面,没有太多关注,后续评审对于此种设计需提醒项目组对焊点高度做重点尺寸标注,来料重点管控。
图3图4D5.Choose & Verify Permanent Corrective Actions (选择和确定永久措施)针对根本原因,一方面由SQA同事对供应商来料做重点尺寸管控,要求来料的喇叭焊点需低于磁杯面,另一方面由项目组推动供应商联创更改设计方式,把PCB沉于喇叭塑胶壳里面,以此达到喇叭焊点与磁杯面有0.2mm以上的间隙。
值得学习的8D实战案例
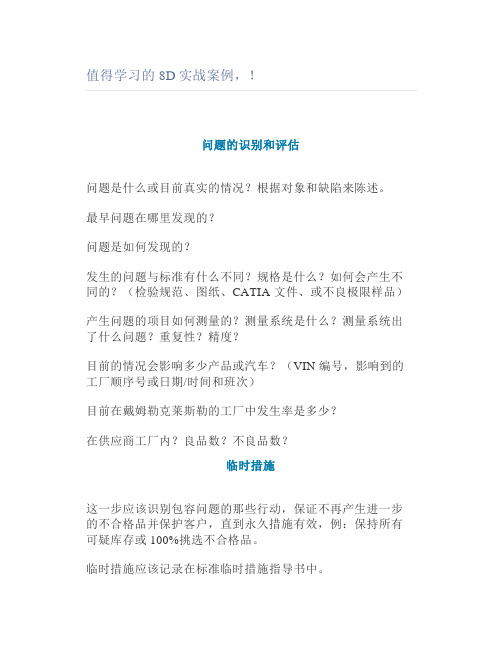
值得学习的8D实战案例,!问题的识别和评估问题是什么或目前真实的情况?根据对象和缺陷来陈述。
最早问题在哪里发现的?问题是如何发现的?发生的问题与标准有什么不同?规格是什么?如何会产生不同的?(检验规范、图纸、CATIA 文件、或不良极限样品)产生问题的项目如何测量的?测量系统是什么?测量系统出了什么问题?重复性?精度?目前的情况会影响多少产品或汽车?(VIN 编号,影响到的工厂顺序号或日期/时间和班次)目前在戴姆勒克莱斯勒的工厂中发生率是多少?在供应商工厂内?良品数?不良品数?临时措施这一步应该识别包容问题的那些行动,保证不再产生进一步的不合格品并保护客户,直到永久措施有效,例:保持所有可疑库存或100%挑选不合格品。
临时措施应该记录在标准临时措施指导书中。
作业指导书必须包含临时措施实行的日期直到相应的批准协议签字生效。
临时措施必须一直采取直到纠正措施确认有效并实行。
问题的有效性说明通过临时措施发现的不合格零件数量;说明检查的整个批次的数量,如:5/100,检查100个当中发现5个根本原因应包括所有的措施,或参考一个行动计划,这个行动计划列出了针对问题所需要进行的分析试验,必要的话,应复制再现问题。
确定一个问题根源可以有很多不同的方法-一个简单而有效的方法就是去问5次:为什么,为什么......接下来这个部分必须包含对问题根源的陈述,以及当原因经过验证确认后,在目标日期的方框中注明“关闭“验证非常重要。
证明一个逻辑分析法能够查出根本原因是很重要的,这样客户才能够明白已经采取了哪些步骤来解决问题。
例如:实地查核:试验或演示我们可以再现问题和解决问题(这是最好的查证)。
推理验证,可以运用是或不是,原因以及后果等等附加页要阐述采取的措施,从测试中得到的结论等等影响列出所有问题的百分比影响一个根本原因下或许有很多影响因素,在这种情况下,估计出对于这个问题影响的百分比。
注意:总数通常是要加到100%。
所需时间确认采取临时措施所需的时间和顾客每一小时的花费。
- 1、下载文档前请自行甄别文档内容的完整性,平台不提供额外的编辑、内容补充、找答案等附加服务。
- 2、"仅部分预览"的文档,不可在线预览部分如存在完整性等问题,可反馈申请退款(可完整预览的文档不适用该条件!)。
- 3、如文档侵犯您的权益,请联系客服反馈,我们会尽快为您处理(人工客服工作时间:9:00-18:30)。
執行日期(Implement Date):2020.5.19
1.改善对策从2020.5.19起开始实施,效果待下批订单生产时验证。
改善措施是否有效? Corrective Actions Efficacious? □ Yes □ No
第一批产品追踪结果(Follow up for first lot):
風險等級(Risk Level) : □VH □H □M □L
D1、小组成员(Team Members)
(開始日期)Start Date:
部门(Dept)
制工部(ME)
生产部(MFG)
品保部(QA)
开发部(RD)
采购部(PUR)
业务部(Sales)
其他部门(Other)
小组领导(Team Actions Adequate?
责任人: 执行日期:2020.5.19 2.外观全检站从2020.5.19起每个作业员佩一钯钢尺确认尺寸。并将此尺寸不良做品质提醒看板悬挂在外检工站提醒作业员将此不良检出(见附件不良看板
□ Yes □ No
)
C051300130100 品质提醒看板.pdf
第二批产品追踪结果(Follow up for second lot):
第三批产品追踪结果(Follow up for third lot): D7、预防对策(Preventive Action)
● Qualitatitive Tools: Six thinking hats、Process flow chart、Brainstorming、FMEA、Error-proofing、Check Sheet ● Quantitatively Tools: Graphical Techniques
執行日期(Implement Date):2020.5.19
1.要求成型磁环作业站作业员将磁环放入模具后,需用手将线材向前拉一下,确认PLUG头网尾已顶住档板后,并用模条压住线身,防止线材在合模时后退,确认 改善措施是否足够?
OK后才能合模作业(见改善后图片说明
),改善前是直接成型作业,无用手将线材向前拉一下及用用模条压住线身压住线身的动作。
D4、根本原因分析(Root cause analysis)
● Qualitatitive Tools: Six thinking hats、Process flow chart、Brainstorming、 Is/is not、5W、Fishbone、Stratification ● Quantitatively Tools: Graphical Techniques、Pareto Analysis、SPC、Process Capability
提供日期(Provide Date): 2020.5.19
1.成型磁环工站作业过程中,作业员未将PLUG头顶住已调好PLUG头网尾到磁环尺寸的档板造成磁环成型后PLUG头网尾到磁环的尺寸超上限。 2.外检站作业员工作疏忽未将不良检出导致不良品流入客户端。
分析是否充份? Analysis were sufficient? □ Yes □ No
◆ 验证根本原因(Verify Root Causes)
確認(Confirmed by):2020.5.19
1.根本原因验证见附件(
)
D5、改善对策(Corrective Action)
● Qualitatitive Tools: Six thinking hats、Brainstorming、 Error-proofing、Check Sheet ● Quantitatively Tools: Graphical Techniques
1.无文件修订。
D8、感谢团队(Congratulate team)
執行日期(Implement Date):2020.5.19
预防措施是否足够? Preventative Actions Adequate? □ Yes □ No 完成日期(Date of completion):2020.5.19
小组成员(Team members):
D2、问题描述(Problem Description)
撰寫日期(Date):
图片(Photos)
PLUG头网尾到磁环尺寸不符,要求30±5mm,实测:40mm,36mm.
D3、防堵对策(Containment Actions)
● Qualitatitive Tools: Six thinking hats、Error-proofing、Check Sheet
客戶抱怨(Customer Claim)
其他(Others)______
供应商: Supplier: 批量: Lot Q'ty:
LRR(For IQC)
提出人员: Raised by: 重复发生(Recurrence) □Yes ■No
10000PCS
料號: Part No.
不良数 Failure Q'ty
D/C(Or Lot No.)
发生地点 Occurred Site
客诉
要求完成日期: Due Date:
相關照片或證據(Photos Attached): ■YES □NO
审核人: Checked by:
(Verified Line Reject Rate =Defect Q'ty/Production Q'ty*100%)
Supplier Corrective Action Report
主题名称(Suject name):
CAR No.
8D Report Status
Open
供应商来料问题(Issue from Supplier) 反應階段(Station): 進料不良(IQC)
線上反應(In production line)
责任人: 执行日期:2020.5.19
D6、改善对策有效性确认(Verification of Effectiveness)
● Qualitatitive Tools: Check Sheet ● Quantitatively Tools: Histogram、Graphical Techniques、 Pareto Analysis、SPC、Process Capability
预防措施是否足够? Preventative Actions Adequate? □ Yes
Prepared by :
Checked by :
Approved by:
Closed date:
备注(Remark)
第1页
108-81609-00 2PCS
VLRR For Product Line
提出日期: Date Raised:
(Lot Reject Rate= Defect Q'ty/Inspection Q'ty*100%)
产品名称: Part Name:
DC线
異常單編號: CAR No.
不良: Failure Rate:
Implement Date(執行日期):
1.APD端库存品10000PCS重工处理,现已重工完成,不良品30PCS。
2.旭华库存品9630PCS,重工处理,(见附件重工流程单
),重工OK品外箱贴“重工OK标签”,无在制品及在途品。
APD Assessment APD确认(For材料问题)
对策可接受的? Short-Term Corrective Action Accredited? □Yes □No