导入六标准差的最佳策略
六标准差管理Six Sigma
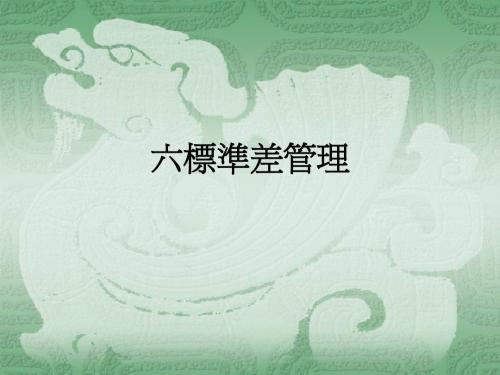
DFSS成功要素
建立良好的溝通程序,讓組織裡的員工都能接收到 清晰、一致、簡潔的訊息,讓大家能以同理心來瞭 解彼此的背景,結合行銷、研發、品保及生產人員, 透過相互溝通與協調來避免先天上的阻礙。 把DFSS整合到新產品研發標準程序中,此時專案 團隊應善用QFD(Quality Function Deployment)將 VOC轉換成設計準則,讓流程標準轉換為生產條件, 讓品質目標等於品質職務,以利品質業務的展開。
28
六標準差設計 (Design for Six Sigma, DFSS)
六標準差設計 (Design for Six Sigma, DFSS)
■ 領導Motorola推行Six Sigma的前執行長Bob
Galvin曾說過 “若再給他一次選擇機會, 他會讓Motorola的Six Sigma活動從新產品 開發流程做起,因為製程上的變異多半源 於產品開發階段。” ■ 對多數企業而言,即使努力實施六標準差, 還是會碰到「五標準差障礙」(Five Sigma Wall)。
8
Measure-1
9
Measure-2
利用C&E Matrix進一步分析各種可能原因之 影響程度,將緯向瑕疵最可能之原因歸納為 以下各項: 1. 尼龍原絲物性之穩定性 2. 尼龍原絲絲餅捲取設定條件與織機操作設 定條件相牴觸 3. 布種規格、組織及密度之變化
10
Analysis-1
原絲物性變異性分析 1. 物性A對緯向瑕疵具有明顯影響性,物性A 愈低改善效果愈佳。 2. 物性A愈高,其變異性愈大。 3. 經測試後,原絲物性A控制在0.57以下,客 戶即可接受。
36
奇異公司致勝之道
奇異傳奇的推手
在威爾許執掌兵符20年(1981-2001)間,奇異的資產從130億 美元暴增至數千億美元,為股東創造的價值增加超過30倍。 威爾許大刀闊斧關廠裁員,凡是績效不彰、無法達到市場數 一數二地位的部門,都必須整頓、出售、或是裁撤。每年績 效最差的10%經理人,全都會被掃地出門。所以儘管財星雜 誌封他為「20世紀最佳經理人」,卻也說他是「全美最嚴厲 的老闆」。企業界甚至給他「中子傑克」(Neutron Jack) 的綽號,形容他整頓的鐵腕。 奇異能有現在的競爭力,許多都在他任內打下基礎。英國金 融時報2005年6月公布的全球500大企業排行榜,奇異再度 蟬聯冠軍,是全球股東價值最高的公司。
导入六标准差的最佳策略研讨
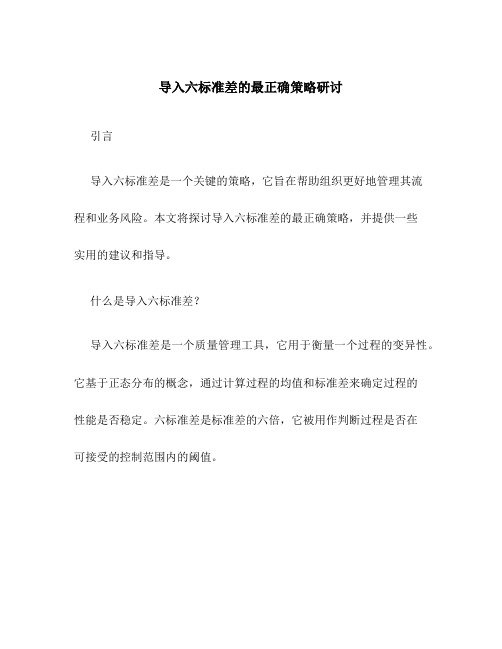
导入六标准差的最正确策略研讨引言导入六标准差是一个关键的策略,它旨在帮助组织更好地管理其流程和业务风险。
本文将探讨导入六标准差的最正确策略,并提供一些实用的建议和指导。
什么是导入六标准差?导入六标准差是一个质量管理工具,它用于衡量一个过程的变异性。
它基于正态分布的概念,通过计算过程的均值和标准差来确定过程的性能是否稳定。
六标准差是标准差的六倍,它被用作判断过程是否在可接受的控制范围内的阈值。
为什么导入六标准差是重要的?导入六标准差可以帮助组织更好地了解其过程的稳定性和可靠性。
它可以帮助发现潜在的问题和风险,并采取适当的措施来解决这些问题和风险。
此外,导入六标准差还可以帮助组织提高其业务流程并减少浪费,从而提高效率和盈利能力。
导入六标准差的最正确策略1. 确定关键指标在导入六标准差之前,首先需要确定关键指标以监控过程的性能。
这些指标应该与组织的战略目标和关键绩效指标相对应。
通过跟踪关键指标,组织可以更好地了解其过程的稳定性和表现。
2. 收集数据在导入六标准差之前,需要收集足够的数据来计算过程的均值和标准差。
数据的收集可以通过各种方式进行,例如手动记录、自动化系统和传感器等。
确保数据的准确性和完整性非常重要。
3. 计算过程的均值和标准差基于收集的数据,计算过程的均值和标准差。
可以使用统计软件或电子表格等工具来进行计算。
这些计算结果将成为后续判断过程性能是否稳定的根底。
4. 确定六标准差的阈值根据过程的均值和标准差,计算六标准差的阈值。
如果某个指标超过阈值,那么表示该过程性能不稳定,需要采取相应的措施来修复问题和降低风险。
5. 分析并解决问题当发现一个或多个指标超过六标准差的阈值时,需要分析问题的根本原因,并采取适当的措施来解决问题。
这可能包括过程改良、质量管理措施和员工培训等。
6. 持续改良导入六标准差是一个持续改良的过程。
组织应该定期检查和监控过程的性能,并根据需要进行优化。
通过持续改良,组织可以不断提高其业务流程,并实现更高的效率和质量水平。
6西格玛导入与实施简介

如何导入和实施6σ在把6σ作为公司的战略之后,首先要确定6σ项目的目标、范围和实施步骤。
按照6σ的指导思想审查企业的管理架构,建立相应的组织体系,体系的成员需要理解6σ的核心思想、基本概念、运作方式,以及6σ核心的方法论体系和具体实施的步骤与工具。
怎样在企业里导入六西格玛管理体系•这是非常关键的一个问题。
•六个西格玛不仅仅包括软件的提升,更关键的在于给员工带来什么样的思想,同时强调人的主动性与团队的精神,这是着眼于全面提高企业竞争力的。
•在个人层次上引入六西格玛。
引入六西格玛,这是一个很有用的思维转变。
学会运用,决策时就会比较科学,可以帮助领导者理清思路。
•在团队层次上引入六西格玛。
可以在小团体里面,主动找一些项目来做,利用六个西格玛的工具去改善流程。
•在组织层次上引入六西格玛。
在一个企业里全面导入六个西格玛管理体系。
全面导入的话则需要建立一个大厦的框架,慢慢地铺进,六个西格玛就会使企业文化改变。
六西格玛时要注意以下问题•一是高层思想的转变。
•二要充分考虑企业的财政状况,自己企业是否有资金保证实行六西格玛。
•三企业文化的选择。
实行六西格玛可能要对原有的公司文化进行冲击,领导者要充分考虑是保留现有文化稳定发展还是进行改变。
•四企业发展战略的选择。
如果企业的发展战略错误,大方向错误,那么不管怎么导入六西格玛都是极坏的后果。
•五要考虑成本。
可运用六西格玛试验一个项目,看能不能带来一个收益。
影响实施6 σ管理法决策的两个方面•实施6 σ管理法的规模和时间•实施6 σ管理法的能力(核心竞争力)确定目标•明确实施6σ管理法的主要动机将会帮你选择出最好的初始战略。
•目标大致分为:业务转型战略改进问题解决三个层次。
就我们的工作而言,更多的只有问题解决而已。
评估实施6 σ管理法的规模•制约因素:你在组织中的地位、那些项目有可行性;资源:参与者、时间投入、预算、资源冲突;注意力:公司重视程度、你会否重荷难负;可接受性:该领域(部门)的人是否反对实施,若反对,最好“稍后再说”。
简介六个标准差

评估当前设计水平,识 别设计改进机会。
设计 (D esig n)
制定设计方案,包括产 品/服务的功能、性能、
可靠性和成本等。
验 证 (V erif y)
工具与技术应用
统计工具
包括假设检验、回归分析、方 差分析等,用于数据分析和过
程改进。
过程映射
通过流程图、因果图等工具可 视化过程,识别浪费和改进机 会。
通用电气公司
杰克·韦尔奇在担任通用电气公司CEO期间,大力推广六个标准差方法,通过减少浪费和缺陷,提高了公司的运营 效率和盈利能力。
服务业案例
亚马逊公司
亚马逊公司运用六个标准差方法优化其物流和配送过程,通过减少错误和延误,提高了 客户满意度和忠诚度。
美国运通公司
美国运通公司采用六个标准差方法来改进其信用卡业务流程,包括申请处理、信用评估 和客户服务等方面,从而提高了业务效率和质量。
简介六个标准差
目 录
• 六个标准差概述 • 六个标准差的核心思想与原则 • 六个标准差的方法论 • 六个标准差在组织中的应用 • 六个标准差对组织的价值 • 实施六个标准差的挑战与对策
01 六个标准差概述
定义与背景
六个标准差(Six Sigma)是一种质量管理方法,旨在通过减少缺陷和错 误,提高过程和产品的质量和效率。
减少缺陷和错误
通过减少生产过程中的变异和浪费,提高产 品的一致性和稳定性,从而减少缺陷和错误 。
提高客户满意度
关注客户需求,优化产品设计和服务流程, 提高客户满意度和忠诚度。
降低成本和浪费
要点一
减少生产浪费
通过优化生产流程,减少不必要的浪费和成本支出。
要点二
提高资源利用效率
合理利用资源,提高资源利用效率,降低运营成本。
精实六标准差的行动步骤

精实六标准差的行动步骤价值流经过分析后,你便能找出最关键的几个时间陷阱(通常是不到工作站的二0%),它们会干扰重要的价值流,你也会得出一份精实六标准目标先后清单,以及除去延误原因的工具。
当你为整个厂做完时间陷阱分析,先后该做的改进也都执行完毕,制造管理品质成本的全部费用就可以减少二0%,并大幅增加营运获利。
现在,重点来了。
在多数时候,品质问题通常最受重视,因为它们对延误造成非线形的影响──一0%的报废率可以拖慢流程四0%。
换言之,少数几个品质问题可以增加流程许多时间。
如前述,多数人感到非常意外,为何非加值步骤远多于加值步骤?如果他们使用物料需求计书路由器,是因为习于见到价值流的理想前景,到了某个时候,不会瑞再有任何浪费。
当和、改进做到把周期效益提高到三0%,并去除二0%的制造管理费用和品质成本,这种前景让你看到事情有多美好。
顺道一提,经验显示,做非加值活动的人其实在活力平源,他们应该被安排到制造、设计或行销的加值工作机会,并且协助执行精实六标准差,我注意到一个现象──重做经常是最能干的工作在做,急件则是补最主动的人揽下,一般建议改进流程不必裁员,只是重新安排能干的人,裁员一定是因为公司整体要响应过低的股东获益、量减、或营收停滞等问题时才会发生的。
主要的精实改进工具绘制价值流图虽是精实方案的主要衡量工具,但也需要其它方法和相关工具,才能达成想要的改进速度,第十一章会详细讨论这些工具,以下是最重要的三种:拉式系统:如本章稍早讨论,流程的流速和前置时间全由流程中的工作量决定。
因此我们必须有机械或电子的机制,来使在制品低于某个最高水平,否则流程的总时间便会失控。
能达成此目标的精实工具就是拉式系统,它维持在制品的理低于最高水平,否则流程的前置时间会失控。
〔有时也称为广告牌(Kanban)系统,取自日文〔卡片〕或更接近文章的可见纪录或广告,在日本,只有亮卡表示有消费时才放行在制品。
〕减少准备时间:准备时间被界定为一批零件数的最后一件和下批零件数的第一件间的空档。
导入六标准差的最佳策略概论
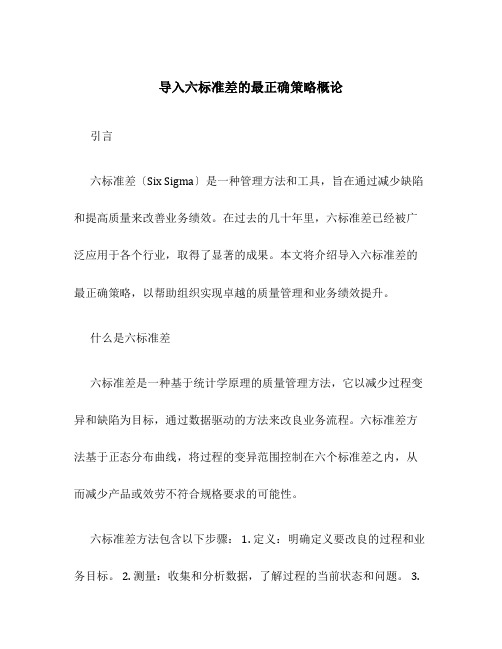
导入六标准差的最正确策略概论引言六标准差〔Six Sigma〕是一种管理方法和工具,旨在通过减少缺陷和提高质量来改善业务绩效。
在过去的几十年里,六标准差已经被广泛应用于各个行业,取得了显著的成果。
本文将介绍导入六标准差的最正确策略,以帮助组织实现卓越的质量管理和业务绩效提升。
什么是六标准差六标准差是一种基于统计学原理的质量管理方法,它以减少过程变异和缺陷为目标,通过数据驱动的方法来改良业务流程。
六标准差方法基于正态分布曲线,将过程的变异范围控制在六个标准差之内,从而减少产品或效劳不符合规格要求的可能性。
六标准差方法包含以下步骤: 1. 定义:明确定义要改良的过程和业务目标。
2. 测量:收集和分析数据,了解过程的当前状态和问题。
3.分析:通过统计分析和数据挖掘技术,确定导致问题的主要原因。
4. 改良:制定和实施改良方案,通过消除根本原因来改善业务流程。
5. 控制:建立稳定的过程控制和监控机制,确保改良持续有效。
导入六标准差的最正确策略要成功导入六标准差,组织需要采取一系列策略和措施。
以下是导入六标准差的最正确策略:1. 高层支持和领导力导入六标准差需要从组织的最高层面获得支持和领导力。
高层管理人员应该积极参与并推动六标准差的实施,为其提供资源和支持,确保它成为组织的战略目标。
2. 培训和教育为了顺利推行六标准差,组织需要为员工提供必要的培训和教育。
培训内容应包括六标准差的根本原理、统计工具和技术、问题解决方法等。
通过培训和教育,员工可以掌握必要的知识和技能,有效地参与到六标准差的实施中。
3. 数据驱动的决策在导入六标准差的过程中,决策应该基于数据和事实,而不是凭经验和直觉。
组织需要建立一套完善的数据收集和分析系统,确保决策过程科学、准确和可靠。
4. 持续改良文化六标准差并不是一次性的任务,而是一种持续改良的文化。
组织需要建立和培育持续改良的价值观和意识,鼓励员工不断提出改良意见并参与改良活动。
简介六个标准差

GOODSKY
何謂 標準差 ?
(1)開宗明義話標準差
標準差(Standard Deviation) 其符號 (σ )音為Sigma,是希臘字母之第十八個 的小寫,其在統計學中的意義是變異數之 開根號,代表一組數據其個數據間的差異。 尤其主要的是σValue 與σ Level之區別, 前者是標准差的數值,后者是指標准差水 平,也是目前人們常提起的多少標准差, 代表著其制程能力或品質水平。
GOODSKY
五、分析(3)
3.就動作電壓這管控項目(control Item)之特性 而言,其規格標准之取定是有檢討之余地。 3-a:在其命題之方式中實在看不出規格下限, 因為此管控項目是有上下限之界定,且為了追求 Relay質量的穩定一般都以避免感動電壓靠近臨界值, 為考量而希望維持在其上下限之中間值,因此此題之 規格制訂應明示出其規格中心值并有規格上下限。 3-b:DEC于工程能力計算上使用之公式有些 計算過程被遺漏,因為必依子組容量大小 將S值除以c4之常數值以調整偏差。 GOODSKY
GOODSKY
如何推動六個標準差專案 ? (1)突破路線圖
定義
6Sigma 概論
測量
明確專案定義
分析
確認變異來源 探測性分析
改善
篩選關鍵輸 入變數(DOE)
控制
最佳輸出變數
專案 管理
確認輸入及 輸出指標
確認變異來源 統計性分析
找尋交互作用 (DOE)
控制X 和監控Y
電腦 應用
分析測量系統
確認變異來源 變異數分析
實施程序:
圖表分析 關聯分析 回歸分析 均值檢定 變異數檢定 抽樣計劃 FMEA
GOODSKY
如何推動六個標準差專案 ? (5)改善階段
Six Sigma--企业导入六标准差之个案研讨(PPT 65页)

作即時的評估,並採取行動解決問題
2019/11/17
来自 wFwrewe.Tcenmsphlaute.cfrnom中Br国ain最yB大etty的.C资om料库下载
18
Next Presenter M944050001
高家琪
2019/11/17
Free Template from
27
Six Sigma
步驟二C: 分析並設定顧客要求的
優先順序
•有愈來愈多公司採用以下模式來分析顧客 要求,將顧客分為三大類:
–不滿意者,或基本要求:這些是顧客預期的要 素、功能與標準。達到無賞,而未達到則會引 起顧客不滿。
–滿意者,或可變動要求:這些要求上的表現之 優劣,足以決定來自顧客的評價。
Six Sigma
六標準差改進與管理策略
•流程改進 •流程設計/再設計 •流程管理
2019/11/17
来自 wFwrewe.Tcenmsphlaute.cfrnom中Br国ain最yB大etty的.C资om料库下载
15
Six Sigma
流程改進:尋找特定的解決方案
•是指一個策略能製定清楚解決方案,從而 除去企業績效問題的根源。
步驟二A : 收集顧客資料、 釐定顧客心聲策略
•假的安全感 •「持續進行」為顧客心聲的關鍵因素之一,
顧客心聲系統要能發揮成效,首先要讓它 持續成為優先事項和關注焦點 。 •積極找尋特定的資料,同時掌握趨勢 。
2019/11/17
来自 wFwrewe.Tcenmsphlaute.cfrnom中Br国ain最yB大etty的.C资om料库下载
互容:使用六標準差衡量追蹤所有類型流程的改進幅 度,並用來比較不同事業領域的工作績效。
企业导入六标准差之个案探讨-精品文档

第一步 : 評估組織當前“能耐” 1.組織的策略夠不夠明確 ? 2.有可能完成組織的財務和成長目標 ? 3.組織有能力及效率地回應內外變動 ?
docin/sundae_meng
第二步 : 評估組織當前“績效” 1.我們目前的整體企業成效如何 ?
(有足夠改進空間讓6 Sigma大展身手?)
2.我們能多有效地重視和做到顧客需求 ?
docin/sundae_meng
評估總結 : 三個“關鍵問題” 1.根據財務平衡目標,文化和競爭的
需要,我們有必要改變嗎 ?
2.我們推行6 Sigma時,具備足夠的 策略性理由嗎 ?
3.我們當前改進系統和能力,是否可以 支撐和維持我們的成長和競爭力 ?
docin/sundae_meng
你們有答案嗎 ?
階段Ⅴ 提昇目標
C
執行/衡量 /追蹤/控制
●問題是什麼? ●這個問題對我
們企業的影響 是什麼?
●我們目前狀況 如何?
●這個問題是什 麼樣的結構?
●這個問題最重 要的原因是什 麼?
●我們如何達成 目標?
docin/sundae_meng
下個目標 ●我們如何得知 問題已獲改善? ●如何預防問題
再發生?
28
內容介紹
六標準差之起源
DMAIC and DMADV
品質改善的發展歷程
6 Sigma的七步驟方法
6 Sigma的定義與特性
6 Sigma推動的要領
6 Sigma的演進
6 Sigma專案的選擇
6 Sigma的應用範圍,
6 Sigma團隊的人員
效益與比較
與組織架構
docin/sundae_meng
docin/sundae_meng
【培训课件】六标准差培训讲义

• 定義:
積極將6要義及做法融入日常管理活 動,並且在流程績效與顧客滿意度方 面都有長足進展的組織
• 要點:
– 合格的標準 – 衡量的方法 – 組織的名稱
2019/11/27
六標準差專題
31
回應:封閉的環圈系統
“六标准差”,Chap 2
• 策略面的意涵:
– 好的封閉環圈系統即使在崎嶇的路上 ﹙多變的商業環境﹚,也通行無礙
期、科技量等
• 流程投入品質(來自顧 客或供應商)
• 策略目標 • 顧客要求 • 獲利 • 顧客滿意度 • 整體企業效率
2019/11/27六標準差專題23来自“六标准差”,Chap 2
Q:衡量在6的意義?
A:變異&標準差
=2.7
=0.33
10
20
8
15
6 10
4
2
5
0 -6 -4 -2 0 2 4 6
• 產出
– 顧客的需求變化,或與企業獲利衝突
2019/11/27
六標準差專題
33
回應: 6的意義
• 上限&下限:
– USL—X = 6
– X—LSL = 6 • 顧客的需求
– 上限&下限
• 僅有下限或僅有上限
– 顧客的需求無限?
2019/11/27
六標準差專題
“六标准差”,Chap 2
34
回應: 顧客&6的核心
2019/11/27
六標準差專題
3
服務與製造業的改進
• 奇異照明公司-減少98%發票的錯誤與爭執 (Wal-Mart),加快了付款速度
• 奇異資融金融服務部門-精簡了檢驗審核流程, 更快回應顧客,每年省下百萬美元。
6个标准差

六标准差( 六标准差(SIX SIgma)
BSC含财务、顾客、内部流程及创新。 BSC含财务、顾客、内部流程及创新。 来衡量达成情况。 财务:制造成本,不良品质成本 顾客:客诉、准时交货OTD 顾客:客诉、准时交货OTD (ON tine delivery) 内部流程:制程能力CP、CPK— 内部流程:制程能力CP、CPK—量产指 标。PP、PPK— 标。PP、PPK—试作阶段。直通率 (RTY)Rolling throughout yield. RTY)
X-M 5)Z= 3§ USL-LSL 6)制程潜能CP= ±3§ USL-X 7)制程能力CPK=CP(1-Ca)= ELT 8)稳健设计CR= EST =1-K 3§ =CP
六标准差( 六标准差(SIX SIgma)
二、6 二、6§策略:
因果关系
公司各 部门之 间
KPI
1、新品开发 2、费用降低
6§专案 6§专案
KPI确认
1、Time完成时间
2、Target目标 3、Members成员 4、Snpport资源
Balanced Scorecard Index
KPI:Keg Process
Measure
流程图: KPIV: Variable(关 不良原因 KPIV:KEY Prouss INPUT Variable(关 键流程输入变数)。 KPOV: KPOV:关键流程输出变数。建立量测能力。
Analyse IMPROVE Controll
FMEA分析:对历史发生不良分析作总结并使后 FMEA分析:对历史发生不良分析作总结并使后 续不再重复发生。 KPIV最佳管制 KPIV最佳管制 已改善确认
准確度Ca
精確度Cp
精密度CPk
精实六标准差

这是一本好书,其所介绍的观念与做法,值得大家思考与采用。
传统上,西方国家制造物品的方式采用大量生产,其特征为利用机器设备制造出大量标准化产品。
五十年代,日本丰田汽车公司的生产管理专家大野耐一认为,大量生产方式在日本是行不通的,因而自行发展了所谓的〔丰田生产方式〕,强调降低库存,使用具高度弹性的机器设备,制造出适量的多样化产品。
日后,欧美国家将这种生产方式称之为〔精实生产〕(lean production)。
精实生产方式追求低成本、无缺点、产品的多样化,希望透过较少的资源,例如较少的人员、库存、空间与研发时间,追求完美的境界,以创造企业最高的利润。
时至今日,全球的各行各业,已有许多公司采用〔精实〕方式,并展现出傲人的经营成效。
〔六标准差〕(Six Sigma)于一九八七年首先由摩托罗拉公司提出,经联讯(AlliedSignal)与通用(GE)公司大力推动之后,获得相当卓著的经营效益,其后Sony、Nonie、Toshiba、American Express等公司也纷纷跟进。
六标准差以满足顾客为导向,通过对顾客需求的了解、事实与资料的分析,以及企业流程管理的改善与创新,希望能让企业获取全面性的经济效益。
六标准差是一套管理系统,协助企业达成顶尖的绩效。
它需要管理阶层的参与,以特定的角色(如黑带和黑带大师),透过项目的方式,利用流程改进的工具,解决有问题的流程,并获财务成效。
六标准差俨然已成为目前全世界最发烧的企业管理哲学。
然而,六标准差能够带领企业到达的境界还是有其限制。
如果希望改善的效率能快一点,杰克.韦尔奇(Jack Welch)建议企业应该要将六标准差延伸至〔精实六标准差〕(Lean Six Sigma/LSS)。
精实六标准差乃藉由快速改进顾客满意、成本、品质、流程速度和投入资本等方面,以追求股东最大利益的方法。
简言之,精实六标准差就是要把产品或服务做得又好又快。
六标准差将重心放在如何使生产和企业流程更有效率,而精实六标准差则将重心放在如何使生产和企业流程更有效率,因此精实六标准差将流程的品质与速度一网打尽。
以六个标准差构建竞争优势

1
壹、前言
1995年ISO成為旅館業品質的保證。 『ISO就是礙手礙腳』? 『全面品質管理, Total Quality
Management, TQM』 。 推動『六個標準差,Six Sigma』的
理念做為旅館業競爭優勢的基石 。
2
貳、品質管理之演進
Quality by Inspection - Sampling Quality by Prevention - SPC Quality by Design - Engineering Quality by Process - QFD Quality by System – TQM, ISO Quality by Project – 6σ
24
競爭優勢可行方案 - 異業聯盟
1. 航空公司。 2. 主題樂園。 3. 旅行社。 4. 旅遊網站。 5. 大型公司行號。 6.國際連鎖集團。
7. 國內飯店聯盟。 8. 國內傳統專業訂房中心: 天祥旅行社、中外旅行社。 9. 國內訂房網站: TRAVELKING、四方通行與 靈知網等。 10. 銀行與信用卡公司。
以科技为动力,以质量求质量是企业 的生命 ,质量 是企业 的效益 ,质量 是企业 发展的 动力, 以质量 求生存 。14:08:2814: 08:2814:0812/ 13/2020 2:08:28 PM
加强安全生产监督检查,防止和减少 生产安 全事故 。20.12.1314:08:2814:08Dec -2013- Dec-20
18
玖、以六個標準差建構旅館業競爭優勢
『六個標準差』 、『國際品質保證系 統』、『全面品質管理』差異在哪?
最大優勢是『六個標準差』是以旅館消 費者為出發,所有品質管理與改善的作 為都是達到顧客實質滿意為手段與目標。
以六个标准差构建竞争优势

以六个标准差构建竞争优势六个标准差是质量管理中的一个重要指标,它用来衡量一个组织的产品或服务的质量水平。
对于一个企业来说,构建竞争优势是至关重要的,而通过六个标准差来提升质量,将是实现竞争优势的有效途径。
下面我将阐述以六个标准差构建竞争优势的方法和步骤。
首先,建立质量管理体系。
一个良好的质量管理体系是实施六个标准差的基础。
一个完善的质量管理体系应包括质量策略的制定、质量目标的设定、质量流程的规范、质量检测与改进等。
通过建立质量管理体系,可以确保组织的各个环节都按照标准化的质量过程来运作,从而提高产品或服务的质量水平。
其次,进行质量培训和教育。
质量管理需要全员参与和共同努力,因此,组织应该进行质量培训和教育,提高员工对质量管理的认识和理解。
培训内容应包括六个标准差的概念和应用、质量工具的使用方法等,通过培训和教育,可以提高员工的质量意识和技能水平,进一步强化组织的质量管理能力。
第三,建立质量评价机制。
质量评价是衡量质量水平的标准,它可以帮助组织了解产品或服务的优势和不足之处。
建立质量评价机制,可以通过定期的质量测量和评估来监控质量水平的变化,并根据评估结果来采取相应的改进措施。
在评估过程中,可以使用六个标准差来度量产品或服务的质量水平,并与竞争对手进行比较,找出差距和改进的方向。
第四,开展质量改进活动。
质量改进是以六个标准差为依据的重要环节,它的目的是通过持续的改进来提高质量水平。
质量改进可以采用各种方法,如流程优化、问题解决、团队合作等。
在改进过程中,组织应该注重问题的根本原因,通过分析和解决问题的方法,来消除质量问题,提高产品或服务的质量水平。
第五,与供应商建立良好的合作关系。
供应商是组织质量管理的重要环节,他们提供的原材料和服务直接关系到组织产品或服务的质量水平。
与供应商建立良好的合作关系,可以确保供应链的质量稳定,减少因供应链的不稳定性而导致的质量问题。
通过与供应商建立长期稳定的合作关系,可以共同制定质量标准和目标,并通过信息分享、技术交流等方式来提高供应链的质量水平。
- 1、下载文档前请自行甄别文档内容的完整性,平台不提供额外的编辑、内容补充、找答案等附加服务。
- 2、"仅部分预览"的文档,不可在线预览部分如存在完整性等问题,可反馈申请退款(可完整预览的文档不适用该条件!)。
- 3、如文档侵犯您的权益,请联系客服反馈,我们会尽快为您处理(人工客服工作时间:9:00-18:30)。
A+GB可能候選人
、財務、資訊主管 工廠部門課級 (含)以上主管 GB候選人
訓練 與實 務改 針對改善專 善階 案於DMAIC 各階段定期 段 檢討與輔導
成立專案改善團隊 6σ綠帶訓練與專案改善 驗證6 Sigma專案成效
蒐集、分 析6σ專案 數據
各階段產出報告
成效 確認 與發 表階 段
成效確認報告
Texas Instruments
(Million Dollars)
Cost Profit
1,200
1996
如何推行六標準差
8
Six Sigma啟始查核表 啟始查核表
我們的企業此時此刻是否適合推行Six Sigma活 動?
問 項 是 否
經由企業的定位、願景及展開的經營策略中,Six Sigma是否成 □ □ 為策略的要項? 在國際競爭中,客戶是否明確要求提供具體能力指標的需求? □ □ 企業已塑造全面積極轉型階段,以提升競爭力? 依據財務、文化需求,此刻是否符合改變關鍵業務需求? 我們的企業現況已具備導入Six Sigma的系統化架構? 我們已知目前客戶的需求,可具體指出並清楚現況基準?
把 Six sigma 充分運用在核 心企業流程上將會產生極大 的影響。 企業核心流程是一套相互關 聯及跨功能的流程,此流程 會對顧客滿意度產生極大的 影響-無論是正面或是負面。
14
行銷/銷售 顧客服務 行銷 銷售/顧客服務 銷售 產品規劃 產品製造 品質 & 測試 技術支援 配銷 計價/合約 計價 合約
9
□ □ □ □ □ □ □ □
我們目前的管理系統與流程,具備長期持續不斷改善的能力嗎?□ □
如何推動 Six Sigma
由上而下逐步建立6σ的觀念 成立推動組織並有效結合HR 進行一波波的綠帶訓練 建立以6σ工具為主的溝通方式 6σ 建立6σ的工作環境 培養黑帶團隊 以自己的黑帶培訓現場作業人員 以自己的黑帶持續培訓綠帶 改變企業文化成為一個6σ的公司
6 Sigma 的謬誤
管理階層只說不做 因為對Sigma的錯誤觀念導致扭曲DPMO的意義 只專注在數字的變化上而非整個流程 缺乏標準 產品樣本的母體過小 只是 sigma 水準的集合體 忽略流程的 1.5 Sigma 偏移 6sigma vs 成本交換 流程環境的缺乏 短暫的改善成果
3
企業為何無法達成預期的目標
公司長短期目標未能展開到以流程為核心的跨 部門改善專案,並有效結合教育訓練與財務績 效 跨部門的品質問題成為管理的盲點 跨部門團隊運作困難 問題解決與績效評核脫鉤,解決意願低落
4
企業為何無法達成預期的目標(續 企業為何無法達成預期的目標 續)
知道問題所在卻苦於缺乏人力與必要的資源 知道問題所在但缺少有效的解決方法與技術 未能找到根本要因(缺乏實證),所以問題重複 發生 缺乏持續改善的運作機制
10
Six Sigma 專案執行導攬
Customer Business Objective Champion Project Selection BB MBB
Define Measure Analysis Improve
11
Control
DMAIC應用的工具 應用的工具
定義 量測 分析 改善 控制
5
六標準差的效益
台灣福特汽車(Ford)2002年6σ專案省下將近9百 萬美金 永光化學自2000年導入6σ到2002年資源投入2 千7百萬(主要為專職人員薪資,人力投入715人 7 ( 715 /月),改善件數286件,效益1億9仟多萬 遠東紡織導入6σ第一年的6個專案便帶來 ROI(投資報酬率) 800%的效益 台灣杜邦導入6σ第一年便可輕鬆回收期初的投 資
GB與BB執行DMAIC 專案 結合QS-9000系統 落實FMEA、MSA、 SPC 大幅改善(70%以 上的幅度)製程不良 率 培訓種子教官 廠內合格GB佔 廠內合格 佔 15 %; BB佔3 % ; 佔
17
第三年 6Sigma成熟期 成熟期
第四年 6Sigma穩健期 穩健期
新產品設計流 程DFSS建立 各作業流程改 造DMADV 經驗技術傳承
動作 公司的利益 先找出公司最需 公司的利益/先找出公司最需 要改善的要素(診斷缺失 診斷缺失) 要改善的要素 診斷缺失 專人,至少一人以上(負責人 專人,至少一人以上 負責人 負責人) 各部門分階段執行需要的訓 練並培育BB人員 練並培育 人員 在實務中執行統計分析、監 在實務中執行統計分析、 控數據 定期檢定及控制是否在原來 的理想範圍 定期發表進度,根據執行狀 定期發表進度, 況及執行成果製作獎勵制度
領導階層 的承諾
激勵與 責任
企業流 程架構
22
最佳實務的成功因素
執行關鍵的主題及有效行動使其成為專案
關鍵主題 1. 主題 2. 資源 3. 訓練 4. 程序 5. 評估 6. 基礎 建設
發展Big Y使其可解決企業議 發展 使其可解決企業議 題進而達到企業績效的最高 價值 全職BB的參與 全職 的參與 系統化的訓練方法及鑑定 以科學基礎確認要因並進行 流程績效控管 建立專案評估系統 建立快速發展Six Sigma的基 建立快速發展 的基 23 礎建設
Control Chart
Control Plan Audit
Capability
Six Sigma 切入點
企業轉型
– 當企業工作模式有了重大改變。
企業策略
– 改善企業的關鍵策略或營運弱點。
解決問題
– 企業內的成本、流程改善或問題的解決預防。
13
Six Sigma 在整體企業的運用
產品發展
SWOT分析 分析
S O T ◎ W ◎
平衡計分卡(BSC) 平衡計分卡 6σ全面導入 全面導入 績效指標 D M 6σ改善 改善 A 策略達成 I C
│特徵化 │ 最佳化 │ 特徵化
目標與績效
16
6σ執行範圍可大可小 執行範圍可大可小
第一年 6Sigma導入期 導入期 GB專案試行 建構6Sigma與 BSC基礎環境 建立 6sigma 系統的信心,奠 定日後推動的原 動力 第二年 6Sigma推展期 推展期
20
導入六標準差的成功關鍵因素
21
Six Sigma 的成功因素
策略整合 量化的數 據與衡量 結果 顧客與市 場的網絡 全職的BB 全職的
建立左列要素以提 供成功的種子 以上的要素必須針 對各個事業部門一 一 整合 這些都是通往最佳 結果的必要條件 其最具有效力的成 功因素是來自領導 階層的承諾
定義專案 量測績效 分析潛在原因 確認本質原因 和最優化模型 控制計劃
設定改善目標 確定關鍵的少 確定控制能力 數 建立控制計劃 界定顧客要求 評估量測系統 確定可能原因 規劃最佳模型 連接至管理系 專案選擇與計 確定目前的標 證實潛在原因 建立最佳模型 統 準差水準 劃 確認商機 明確專案 應用工具 VOC VOB Project Team COPQ Process Map Pareto MSA GR&R (Y)
主要管理實務
堅持明確且 任選二項
次要管理實務
留住優秀人才,並
策略
專注的策略 訂定無瑕疵
人才
發展更多優秀人才 領導人與董事會
執行
的運作執行 建立以績效
領導
對公司赤誠奉獻 追求能使產業
文化
為導向的文化 建立快速、彈性
創新
轉變的創新 以購併及夥伴關係 作為成長手段
組織架構
、扁平化的組織 架構
27
企業購倂與 夥伴關係
共
A:高階主管、
設計、製造、 品保部主管
現況診斷
現有作業流程與 品保系統檢討 架構6σ基礎環 境與制度
建立6σ概念
診斷準備事項 診斷報告書
6σ認知與共識課程 Champion訓練
6σ組織與角 色 選案原則與技 巧結合公司策略 與目標
推動小組名單
選擇 個改善專案 選擇5個改善專案 選擇 根據專案範圍挑選 GB候選人 確認專案成員與職責 (專案負責人與組員)
關鍵因素~ 關鍵因素~執行力
24
執行力背後的機制
營運流程~協助員工設定符合現實的目標, 並將目標與他們能獲得的報酬相連結(與 6σ改善專案精神相同) 把策略、營運、改善、獎酬、績效目標、 人才培訓鏈結起來(與6σ整套運作機制相 同)
25
新聞資料摘自 :
工商時報 10/25
26
企業長青的4加 秘訣 企業長青的 加2秘訣
將專案文件化並移交給流程負責人持續控管 成果發表
簡報 評分表
各組專案負責 人、財務人員、 流程負責人、 Champion 各組發表人
9
利用檢核表工具
項目 1 2 3 4 5 6 7 8 9 10 內容 具備 專案具焦於執行中的流程 流程的結果是可衡量的 流程現在在執行中會產生缺點 專案具備70%的改善幅度 專案的改善符合顧客的聲音(VOC) 專案的改善與企業願景相結合 專案是否能在4到6個約執行完成 專安執行成功後流程會繼續執行 首次專案是否擁有高成功率 首次專案是否會大量使用到工具與手法 19 不具備
協力廠商、經 銷商GB培訓 改善協力廠商 不良率、成本以 及交期等問題
廠內合格GB佔 廠內合格 佔 3%
廠內合格GB佔 廠內合格 佔40 %; BB佔10 % ; 佔
廠內合格GB佔 廠內合格 佔 70 %; ; BB佔 10 %。 佔 。 協力廠2家各培訓 家各培訓3% GB 協力廠 家各培訓
6Sigma導入期推進流程 導入期推進流程
導入六標準差的最佳策略
1
大綱
前言~企業的障礙與瓶頸 如何推行六標準差 六標準差的謬誤 導入六標準差的成功關鍵因素 製造業應用實例 服務業應用實例 結論
2
企業的障礙與瓶頸