影响电铸铜速率的因素
提高铜与铜合金水平电磁连续铸造工艺的对策
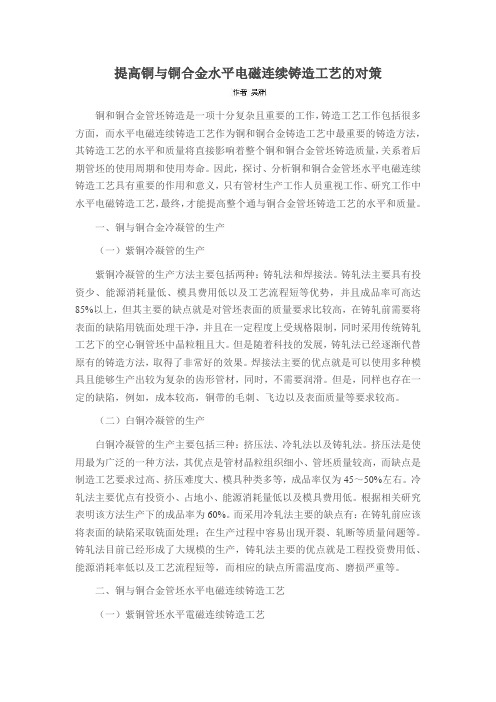
提高铜与铜合金水平电磁连续铸造工艺的对策铜和铜合金管坯铸造是一项十分复杂且重要的工作,铸造工艺工作包括很多方面,而水平电磁连续铸造工艺作为铜和铜合金铸造工艺中最重要的铸造方法,其铸造工艺的水平和质量将直接影响着整个铜和铜合金管坯铸造质量,关系着后期管坯的使用周期和使用寿命。
因此,探讨、分析铜和铜合金管坯水平电磁连续铸造工艺具有重要的作用和意义,只有管材生产工作人员重视工作、研究工作中水平电磁铸造工艺,最终,才能提高整个通与铜合金管坯铸造工艺的水平和质量。
一、铜与铜合金冷凝管的生产(一)紫铜冷凝管的生产紫铜冷凝管的生产方法主要包括两种:铸轧法和焊接法。
铸轧法主要具有投资少、能源消耗量低、模具费用低以及工艺流程短等优势,并且成品率可高达85%以上,但其主要的缺点就是对管坯表面的质量要求比较高,在铸轧前需要将表面的缺陷用铣面处理干净,并且在一定程度上受规格限制,同时采用传统铸轧工艺下的空心铜管坯中晶粒粗且大。
但是随着科技的发展,铸轧法已经逐渐代替原有的铸造方法,取得了非常好的效果。
焊接法主要的优点就是可以使用多种模具且能够生产出较为复杂的齿形管材,同时,不需要润滑。
但是,同样也存在一定的缺陷,例如,成本较高,铜带的毛刺、飞边以及表面质量等要求较高。
(二)白铜冷凝管的生产白铜冷凝管的生产主要包括三种:挤压法、冷轧法以及铸轧法。
挤压法是使用最为广泛的一种方法,其优点是管材晶粒组织细小、管坯质量较高,而缺点是制造工艺要求过高、挤压难度大、模具种类多等,成品率仅为45~50%左右。
冷轧法主要优点有投资小、占地小、能源消耗量低以及模具费用低。
根据相关研究表明该方法生产下的成品率为60%。
而采用冷轧法主要的缺点有:在铸轧前应该将表面的缺陷采取铣面处理;在生产过程中容易出现开裂、轧断等质量问题等。
铸轧法目前已经形成了大规模的生产,铸轧法主要的优点就是工程投资费用低、能源消耗率低以及工艺流程短等,而相应的缺点所需温度高、磨损严重等。
磁场作用下微电铸工艺参数对铸层表面形貌的影响
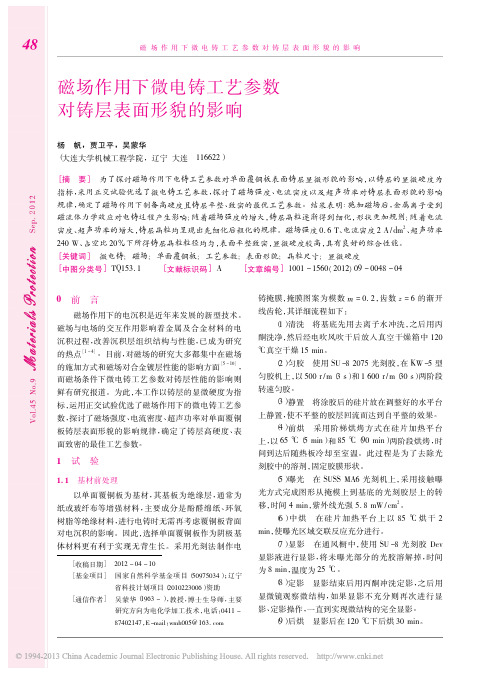
磁场作用下微电铸工艺参数对铸层表面形貌的影响杨帆,贾卫平,吴蒙华(大连大学机械工程学院,辽宁大连116622)[摘要]为了探讨磁场作用下电铸工艺参数对单面覆铜板表面铸层显微形貌的影响,以铸层的显微硬度为指标,采用正交试验优选了微电铸工艺参数,探讨了磁场强度、电流密度以及超声功率对铸层表面形貌的影响规律,确定了磁场作用下制备高硬度且铸层平整、致密的最优工艺参数。
结果表明:施加磁场后,金属离子受到磁流体力学效应对电铸过程产生影响;随着磁场强度的增大,铸层晶粒逐渐得到细化,形状更加规则;随着电流密度、超声功率的增大,铸层晶粒均呈现出先细化后粗化的规律。
磁场强度0.6T 、电流密度2A /dm 2、超声功率240W 、占空比20%下所得铸层晶粒粒径均匀,表面平整致密,显微硬度较高,具有良好的综合性能。
[关键词]微电铸;磁场;单面覆铜板;工艺参数;表面形貌;晶粒尺寸;显微硬度[中图分类号]TQ153.1[文献标识码]A[文章编号]1001-1560(2012)09-0048-04[收稿日期]2012-04-10[基金项目]国家自然科学基金项目(50975034);辽宁省科技计划项目(2010223006)资助[通信作者]吴蒙华(1963-),教授,博士生导师,主要研究方向为电化学加工技术,电话:0411-87402147,E -mail :wmh005@163.com0前言磁场作用下的电沉积是近年来发展的新型技术。
磁场与电场的交互作用影响着金属及合金材料的电沉积过程,改善沉积层组织结构与性能,已成为研究的热点[1 4]。
目前,对磁场的研究大多都集中在磁场的施加方式和磁场对合金镀层性能的影响方面[5 10],而磁场条件下微电铸工艺参数对铸层性能的影响则鲜有研究报道。
为此,本工作以铸层的显微硬度为指标,运用正交试验优选了磁场作用下的微电铸工艺参数,探讨了磁场强度、电流密度、超声功率对单面覆铜板铸层表面形貌的影响规律,确定了铸层高硬度、表面致密的最佳工艺参数。
工业用铜铸件的电导率与导热性能研究
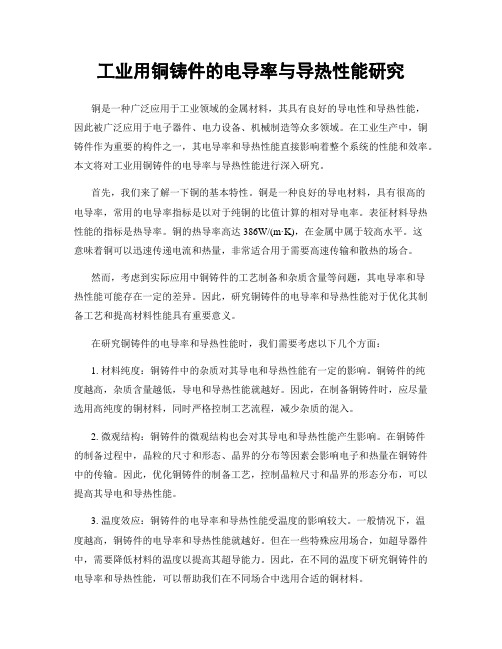
工业用铜铸件的电导率与导热性能研究铜是一种广泛应用于工业领域的金属材料,其具有良好的导电性和导热性能,因此被广泛应用于电子器件、电力设备、机械制造等众多领域。
在工业生产中,铜铸件作为重要的构件之一,其电导率和导热性能直接影响着整个系统的性能和效率。
本文将对工业用铜铸件的电导率与导热性能进行深入研究。
首先,我们来了解一下铜的基本特性。
铜是一种良好的导电材料,具有很高的电导率,常用的电导率指标是以对于纯铜的比值计算的相对导电率。
表征材料导热性能的指标是热导率。
铜的热导率高达386W/(m·K),在金属中属于较高水平。
这意味着铜可以迅速传递电流和热量,非常适合用于需要高速传输和散热的场合。
然而,考虑到实际应用中铜铸件的工艺制备和杂质含量等问题,其电导率和导热性能可能存在一定的差异。
因此,研究铜铸件的电导率和导热性能对于优化其制备工艺和提高材料性能具有重要意义。
在研究铜铸件的电导率和导热性能时,我们需要考虑以下几个方面:1. 材料纯度:铜铸件中的杂质对其导电和导热性能有一定的影响。
铜铸件的纯度越高,杂质含量越低,导电和导热性能就越好。
因此,在制备铜铸件时,应尽量选用高纯度的铜材料,同时严格控制工艺流程,减少杂质的混入。
2. 微观结构:铜铸件的微观结构也会对其导电和导热性能产生影响。
在铜铸件的制备过程中,晶粒的尺寸和形态、晶界的分布等因素会影响电子和热量在铜铸件中的传输。
因此,优化铜铸件的制备工艺,控制晶粒尺寸和晶界的形态分布,可以提高其导电和导热性能。
3. 温度效应:铜铸件的电导率和导热性能受温度的影响较大。
一般情况下,温度越高,铜铸件的电导率和导热性能就越好。
但在一些特殊应用场合,如超导器件中,需要降低材料的温度以提高其超导能力。
因此,在不同的温度下研究铜铸件的电导率和导热性能,可以帮助我们在不同场合中选用合适的铜材料。
4. 添加合金元素:通过向铜中添加一定比例的合金元素,可以改变铜的电导率和导热性能。
电镀铜故障原因及排除方法

3)镀前处理太长蚀刻掉孔内镀层
1注意化学镀铜工艺各步骤
2过滤溶液
3严格操作规程
镀层与基体结合力差
1)镀前粗化不良,化液失效
2)贴膜显影后产生余胶
3)镀前基体不清洁,油污
1加强粗化处理,整或更换粗化液
2加强显影工艺,时更换显影液
3加强板子清洁处理
局部镀不上
局部有残膜或其他污物
加强显影和检查
孔周围发暗(所谓鱼眼状镀层)
1)由于光亮剂过量或有杂质引起孔周围铜镀层厚度不足,孔中厚度可能适合
2)搅拌不足或不正确
1调整光亮剂含量
2调整空气搅拌
7)阳极比阴极短7-8cm,使阳极面积/阴极面积为2:1
镀层粗糙
1)镀液添加剂失调
2)镀液太脏
3)CI-含量太少
4)电流过大
5)有机物分解过多
1)赫尔槽实验确定其添加量
2)连续过滤镀液
3)通过分析调整CI-量
4)调整到适当值
5)能力差
1)H2SO4含量低
2)铜离子过高
2活性炭处理
3加强过滤
阳极钝化
1)阳极面积小
2)阳极黑膜太厚
3)CI-量过高
1调整阳极面积/阴极面积=2:1
2适当刷洗
3可用如上介绍方法去除
镀层脆性大
1)光亮剂含量过高
2)液温过低
3)金属杂质及有机杂质过多
1活性炭处理,调整到适当值
2适当提高液温
3电解处理,性炭处理
金属化孔内有空白点
1)化学镀铜不完整
电镀铜故障原因及排除方法
生产故障
可能原因
纠正方法
镀层烧焦
1)铜含量过低
2)阴极电流过大
电镀铜的性能分析和影响因素
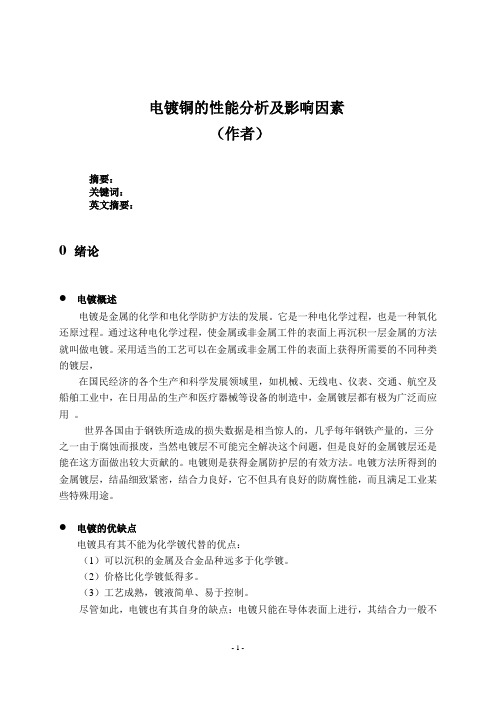
电镀铜的性能分析及影响因素(作者)摘要:关键词:英文摘要:0 绪论●电镀概述电镀是金属的化学和电化学防护方法的发展。
它是一种电化学过程,也是一种氧化还原过程。
通过这种电化学过程,使金属或非金属工件的表面上再沉积一层金属的方法就叫做电镀。
采用适当的工艺可以在金属或非金属工件的表面上获得所需要的不同种类的镀层,在国民经济的各个生产和科学发展领域里,如机械、无线电、仪表、交通、航空及船舶工业中,在日用品的生产和医疗器械等设备的制造中,金属镀层都有极为广泛而应用。
世界各国由于钢铁所造成的损失数据是相当惊人的,几乎每年钢铁产量的,三分之一由于腐蚀而报废,当然电镀层不可能完全解决这个问题,但是良好的金属镀层还是能在这方面做出较大贡献的。
电镀则是获得金属防护层的有效方法。
电镀方法所得到的金属镀层,结晶细致紧密,结合力良好,它不但具有良好的防腐性能,而且满足工业某些特殊用途。
●电镀的优缺点电镀具有其不能为化学镀代替的优点:(1)可以沉积的金属及合金品种远多于化学镀。
(2)价格比化学镀低得多。
(3)工艺成熟,镀液简单、易于控制。
尽管如此,电镀也有其自身的缺点:电镀只能在导体表面上进行,其结合力一般不及化学镀电镀铜的应用领域铜具有良好的导电、导热性能,质软而韧,有良好的压延性和抛光性能。
为了提高表面镀层和基体金属的结合力,铜镀层常用作防护、装饰性镀层的底层,对局部渗碳工件,常用镀铜来保护不需要渗碳的部位。
1)铜箔粗化处理铜箔是制造印制板的关键导电材料,但是印制板外层铜箔毛面在与绝缘基板压合制造覆铜板之前必须经过电镀铜粗化处理,使之具有一定的表面粗糙度,才能保证与基板有足够的粘合力。
铜箔的粗化处理通常分 2 步:一是在较低铜离子浓度高电流密度下的粗化处理,二是在高铜离子浓度低电流密度下的固化处理。
粗化处理过程中必须使用特殊的添加剂,否则铜箔在高温层压制造覆铜板时会出现“铜粉转移”现象,影响与基板的结合力,严重时会使线路从基板上脱落。
影响电镀铜沉积的物理因素
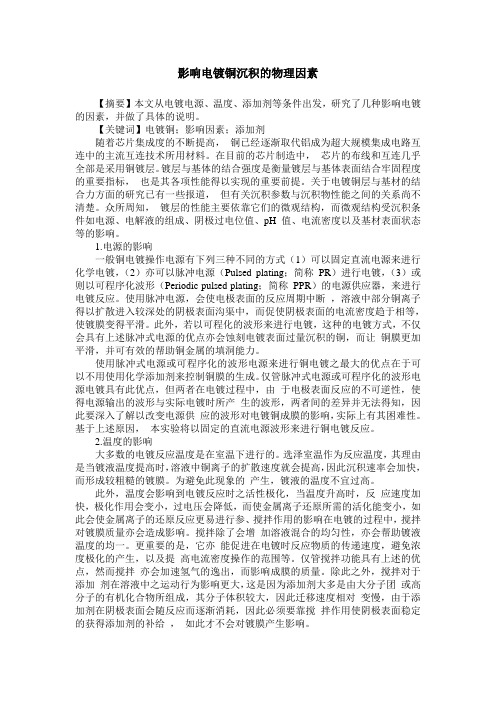
影响电镀铜沉积的物理因素【摘要】本文从电镀电源、温度、添加剂等条件出发,研究了几种影响电镀的因素,并做了具体的说明。
【关键词】电镀铜;影响因素;添加剂随着芯片集成度的不断提高,铜已经逐渐取代铝成为超大规模集成电路互连中的主流互连技术所用材料。
在目前的芯片制造中,芯片的布线和互连几乎全部是采用铜镀层。
镀层与基体的结合强度是衡量镀层与基体表面结合牢固程度的重要指标,也是其各项性能得以实现的重要前提。
关于电镀铜层与基材的结合力方面的研究已有一些报道,但有关沉积参数与沉积物性能之间的关系尚不清楚。
众所周知,镀层的性能主要依靠它们的微观结构,而微观结构受沉积条件如电源、电解液的组成、阴极过电位值、pH 值、电流密度以及基材表面状态等的影响。
1.电源的影响一般铜电镀操作电源有下列三种不同的方式(1)可以固定直流电源来进行化学电镀,(2)亦可以脉冲电源(Pulsed plating;简称PR)进行电镀,(3)或则以可程序化波形(Periodic pulsed plating;简称PPR)的电源供应器,来进行电镀反应。
使用脉冲电源,会使电极表面的反应周期中断,溶液中部分铜离子得以扩散进入较深处的阴极表面沟渠中,而促使阴极表面的电流密度趋于相等,使镀膜变得平滑。
此外,若以可程化的波形来进行电镀,这种的电镀方式,不仅会具有上述脉冲式电源的优点亦会蚀刻电镀表面过量沉积的铜,而让铜膜更加平滑,并可有效的帮助铜金属的填洞能力。
使用脉冲式电源或可程序化的波形电源来进行铜电镀之最大的优点在于可以不用使用化学添加剂来控制铜膜的生成。
仅管脉冲式电源或可程序化的波形电源电镀具有此优点,但两者在电镀过程中,由于电极表面反应的不可逆性,使得电源输出的波形与实际电镀时所产生的波形,两者间的差异并无法得知,因此要深入了解以改变电源供应的波形对电镀铜成膜的影响,实际上有其困难性。
基于上述原因,本实验将以固定的直流电源波形来进行铜电镀反应。
2.温度的影响大多数的电镀反应温度是在室温下进行的。
热处理工艺对铜合金材料的导电性和导热性的优化

热处理工艺对铜合金材料的导电性和导热性的优化热处理工艺是提高铜合金材料导电性和导热性的重要方法之一。
通过控制热处理参数,可以改变材料的晶体结构和微观组织,从而优化材料的导电性和导热性。
首先,热处理可以改善铜合金材料的晶体结构。
晶体结构对材料的导电性和导热性有着重要影响。
通常来说,在高温下,铜合金材料的晶粒会逐渐长大,晶界会变得清晰,这样可以降低材料的电阻率并提高导电性能。
此外,热处理还能够改变晶粒的取向,提高晶体的有序性,进一步优化导电性能。
因此,在热处理过程中,合理控制热处理温度和保温时间等参数,可以得到更优化的晶体结构,提高材料的导电性。
其次,热处理可以改善铜合金材料的微观组织。
铜合金材料的导热性主要受材料内部包含的相和晶界的影响。
一般来说,通过热处理可以使材料中的相有序化,减少相间的界面阻力,提高导热性能。
此外,热处理还能够消除或减少材料中的缺陷和杂质,进一步提高热传导性能。
因此,在热处理过程中,通过适当的热处理工艺,可以使铜合金材料的微观组织更加紧密有序,提高导热性。
此外,还有一些特殊的热处理工艺可以进一步优化铜合金材料的导电性和导热性。
例如,有针对性地进行局部加热和快速冷却,可以得到超细晶粒结构和均匀的晶粒分布,从而提高导电性和导热性。
另外,通过控制合金元素的添加和优化其含量,可以改变材料的相组成和相间的界面,进一步优化导电性和导热性。
综上所述,热处理工艺对铜合金材料的导电性和导热性的优化起着至关重要的作用。
通过合理控制热处理参数,可以改变材料的晶体结构和微观组织,从而提高导电性和导热性。
此外,还可以通过特殊的热处理工艺进一步优化材料的导电性和导热性。
因此,热处理工艺是一种非常有效的方法,可以用于优化铜合金材料的导电性和导热性。
除了热处理工艺对于铜合金材料导电性和导热性的优化,还有其他一些相关的因素也对材料的性能起着重要的影响。
首先是合金元素的选择和优化。
合金化是提高铜合金材料性能的重要手段之一。
电铸工艺介绍

电解液的密度和粘度决定着过滤速度、电导率、物 质迁移速度。
在计算槽子的热平衡时,要考虑到电解液的热容量。
离子的扩散系数直接影响着极限电流的大小。
计算技术电沉积的电能消耗时,要使用到电导率。
表面张力表示阴极表面被润湿的特性,对沉积层的 性能,如孔隙率、树枝状结晶、麻点都有影响。
对电铸溶液的要求
沉积速度快,采用尽可能高的电流密度, 来提高沉积速度
成分简单而且容易控制 对溶液的净化处理要求较高,定期过滤和
处理,电铸层厚时必须连续过滤 能得到均匀的电铸层,要尽肯能选用均镀
能力好的电铸溶液
典型电铸工艺
电铸铜 电铸铁 电铸镍 电铸镍钴合金 电铸镍锰合金 电铸金 电铸银
电铸镍
1)硫酸盐镀镍电解液 2 )氨基磺酸盐镀镍电解液 3 )高速电铸电解液
电铸后处理
脱模:机械外力脱模、热胀或冷缩脱模、熔化脱模、 溶解脱模
对电铸零件的加固和最后修饰 热处理和电镀 电铸产品进行电镀的主要种类有为提高表面硬度
而镀铬、化学镀镍。为提高耐腐性而进行电镀镍 或者其他金属。
电镀产品的防护镀层
对于孔边距小于1mm 的冲裁方式如右图, 分两次间隔冲孔。
芯模的设计和材料选择
长孔或者异形孔,宽 度也应大于0.6mm。主 要是考虑量产是冲头 所能承受的强度。防 止冲头过度疲劳而断 裂。
芯模的设计与材料选择
产品的外型轮廓使用冲床 冲裁加工,为防止冲偏伤 到产品,其外缘切边宽度 平均为0.05mm为防止产品 冲切变形,尽量保证冲切 部分在同一平面或尽量小 的弧度,避免应力集中而 造成产品变形。冲切是只 能在垂直产品的方向作业。
详解微蚀和加速制程对化学铜质量的影响

详解微蚀和加速制程对化学铜质量的影响刘镇权 吴培常 林周秦 陈冠刚(广东成德电子科技股份有限公司,广东 佛山 528300)摘 要 化学铜主要用于印制电路板孔金属化和塑料电镀,因其镀层具有良好的延展性、导热性和导电性而成为PCB的核心工艺之一。
镀层质量除了跟本制程有关外,还受前制程的影响。
本文从微蚀速率和背光的角度分析微蚀和加速制程对化学铜的影响。
关键词 微蚀;加速;背光中图分类号:TN41 文献标识码:A 文章编号:1009-0096(2018)11-0026-05 Expatiate on micro etch and acceleration process effect toquality of PTH in detailLiu Zhenquan Wu Peichang Lin Zhou-tai Chen Guangang Abstract Electroless copper plating is mainly applied to the metallization for PCB and electroplating on plastics, and copper electroless deposits have good ductility, heat conductibility and electrical conductivity, and then it becomes one of core manufacturing technology of PCB. Plating quality was not only related to this process, but was also affected by pre-process. This paper analyzed mico-etch and acceleration process which affected copper electrolessdeposits from mico-etch rate and back light aspect in this text.Key words Micro Etch; Acceleration; Back Light0 前言覆铜板是印制电路板(PCB)的基础材料,在其上有选择性进行加工、电镀铜、蚀刻等,得到导电图形电路并成为PCB。
深孔镀铜液中电流密度对镀铜速率的影响研究

深孔镀铜液中电流密度对镀铜速率的影响研究引言:深孔镀铜是一种重要的电化学加工方法,用于在小孔、细缝及其他难以达到的区域进行镀铜。
电流密度是深孔镀铜过程中的一个重要参数,对镀铜速率有着直接的影响。
本文旨在研究深孔镀铜液中电流密度对镀铜速率的影响,并对其作用机理进行探讨。
1. 深孔镀铜液的组成和工艺条件深孔镀铜液主要由铜盐、酸性添加剂、氨基酸及表面活性剂等组成。
其中,铜盐提供铜离子,酸性添加剂维持液体的酸碱度,氨基酸和表面活性剂则用于控制镀铜过程中的晶体生长和尺寸分布。
电流密度可通过调节工艺条件中的电流和镀液的流速来控制。
2. 电流密度对镀铜速率的影响深孔镀铜液中的电流密度对镀铜速率有着明显的影响。
当电流密度增大时,镀铜速率也相应增加,反之亦然。
实验结果表明,电流密度与镀铜速率之间呈线性关系,即镀铜速率随电流密度的增加而线性增加。
3. 电流密度对深孔镀铜质量的影响除了对镀铜速率的影响外,电流密度还对深孔镀铜的质量有着重要影响。
较高的电流密度可能导致镀铜液中的离子浓度梯度增大,从而引起内部应力的积累。
这种内部应力的积累可能导致镀层出现裂纹、气泡等缺陷,降低镀铜的质量。
4. 电流密度控制在深孔镀铜中的应用在深孔镀铜过程中,对电流密度的控制是至关重要的。
良好的电流密度控制可以保证镀铜速率的稳定和镀层质量的良好性能。
为了实现电流密度的精确控制,在实际生产中常常使用电流传感器来监测和调节电流,以确保深孔镀铜过程的稳定性。
5. 电流密度与镀铜速率的影响机理探讨电流密度对镀铜速率的影响主要通过影响镀液中铜离子的扩散速率和电极表面的反应速率来实现。
较高的电流密度会加快镀液中铜离子的扩散速率,并提高电极反应速率,从而促进镀铜过程。
然而,过高的电流密度可能引起过多的氢气生成,导致镀液中的槽效应,同时也加剧镀层的应力积累。
6. 深孔镀铜电流密度的优化选择对于深孔镀铜中的电流密度选择,需要综合考虑镀铜速率、镀层质量以及设备的工作能力等多方面因素。
提升铜微电铸均匀性的方法研究
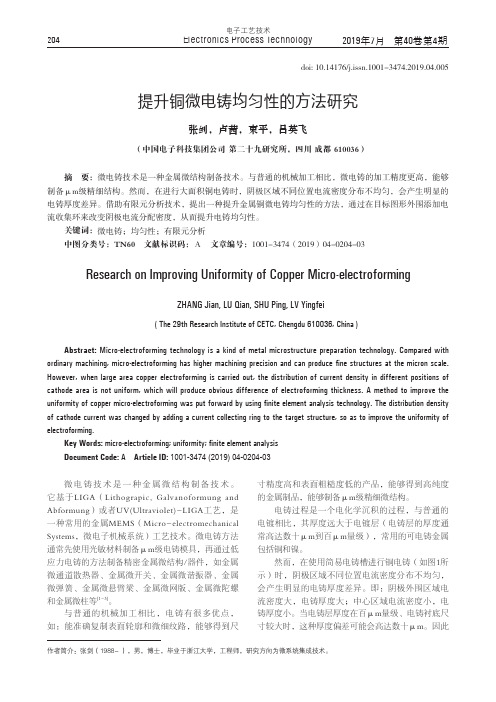
2019电子工艺技术Electronics Process Technology204年7月第40卷第4期摘 要:微电铸技术是一种金属微结构制备技术。
与普通的机械加工相比,微电铸的加工精度更高,能够制备μm级精细结构。
然而,在进行大面积铜电铸时,阴极区域不同位置电流密度分布不均匀,会产生明显的电铸厚度差异。
借助有限元分析技术,提出一种提升金属铜微电铸均匀性的方法,通过在目标图形外围添加电流收集环来改变阴极电流分配密度,从而提升电铸均匀性。
关键词:微电铸;均匀性;有限元分析中图分类号:TN60 文献标识码:A 文章编号:1001-3474(2019)04-0204-03Abstract: Micro-electroforming technology is a kind of metal microstructure preparation technology. Compared with ordinary machining, micro-electroforming has higher machining precision and can produce fi ne structures at the micron scale. However, when large area copper electroforming is carried out, the distribution of current density in different positions of cathode area is not uniform, which will produce obvious difference of electroforming thickness. A method to improve the uniformity of copper micro-electroforming was put forward by using fi nite element analysis technology. The distribution density of cathode current was changed by adding a current collecting ring to the target structure, so as to improve the uniformity of electroforming .Key Words: micro-electroforming; uniformity; fi nite element analysis Document Code: A Article ID: 1001-3474 (2019) 04-0204-03提升铜微电铸均匀性的方法研究Research on Improving Uniformity of Copper Micro-electroforming张剑,卢茜,束平,吕英飞ZHANG Jian, LU Qian, SHU Ping, LV Yingfei(中国电子科技集团公司 第二十九研究所,四川 成都 610036)作者简介:张剑(1988- ),男,博士,毕业于浙江大学,工程师,研究方向为微系统集成技术。
影响电铸铜速率的因素
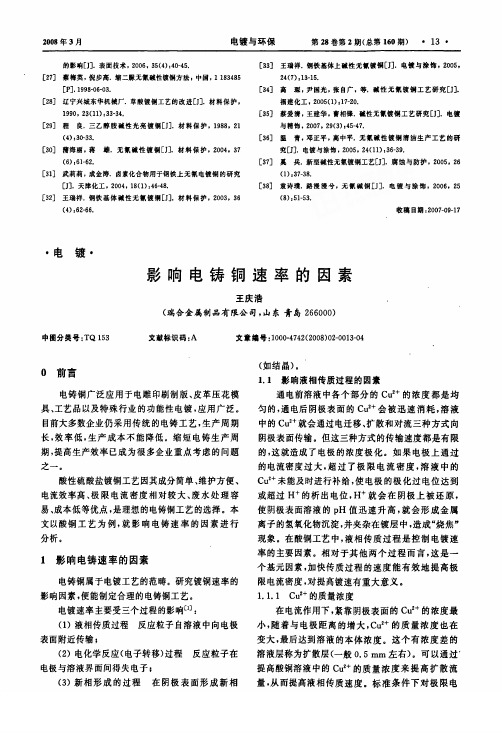
(6)t61-62. [31]武莉莉,成金涛.卤素化合物用于钢铁上无氰电镀铜的研究
口].天津化工,2004,18(1):46·4 8. [32]王瑞祥.钢铁基体碱性无氰镀铜[J].材料保护,2003,36
(4)162—66.
F
善 叠 善
0
100
200 400
600
800 1 000
阴极移动速度/(mm·B-1)
图3 阴极移动速度对极限电流密度的影响
1.2影响电化学反应(电子转移)过程的因素 当电极浸入镀液,未通电前如电极处于平衡状
态,电位为虹,电极与溶液之间不断进行着金属离 子的交换,而且氧化反应和还原反应的速率相等,用 i。表示。实验表明:i。越大,说明电化学反应越容 易,通电后越不容易在电极上积累剩余电荷,电化学 极化也就越小;相反,i。越小,说明电化学反应越困 难,通电后越容易在电极上积累剩余电荷,电极电位 也就偏离虹越远,电化学极化也就越大。由塔菲 尔(Tafel)公式C11:I△乒I=口+b log i(口,b为常数)可 知,极化度与通过的电流i有关。据理论推导,n与 i。有关,可将上式改写为l△乒I一--b log i。+b log i 或I酗l—b log(i/i。)。实验测得Cu2+在1 mol/L CuSO。溶液中的i。约为103 A/dm2,比很多金属在 同等条件下的i。要大几十、几百甚至上千倍。根据 公式可以推断酸铜工艺中在一定电流通过电极时, 电化学极化非常小,说明电化学反应速率非常快。 研究影响电化学反应速率的因素,对提高电铸铜质 量非常有价值。 1.2.1 Cu2+的质量浓度
有机添加剂的加入不会对总体的电镀速率产生不利影响反而对得到优良镀层有非常大的价值影响新相形成的过程因素在电镀过程中形成的金属镀层几乎都是晶体当金属离子失去部分水化膜在电极表面上获得电可以自由移动吸附原子在脱去全部水化膜的同时进入晶格完成电结晶过程在电极电位偏离平衡电位不远电流密度很小的情况下金属离子在电极上还原的数量不多吸附原子的浓度较小而且晶体表面上存在的生长点也不多吸附原子在电极表面的扩散相当困难是有条件从容不迫进入晶格晶粒长得就比较大当电流密度增大时电极电位变得更负吸附原子的浓度逐渐变大晶体表面上存在的生长点也大大增多
电铸铜的应用研究

电铸铜的应用研究常志;靳志强;张峰;王玉;郭帝江【摘要】电铸铜能制造某些难以用机械加工方法制造的特殊形状的金属制品,只需针对零件结构的特点,设计合理心模,便可实现零件的精密成型制造.本文对电铸铜工艺及工艺条件的影响进行了浅析,并结合工艺对电铸槽等关键部件进行了阐述.【期刊名称】《山西电子技术》【年(卷),期】2015(000)003【总页数】2页(P84-85)【关键词】电铸铜;电铸铜工艺;电铸槽【作者】常志;靳志强;张峰;王玉;郭帝江【作者单位】中国电子科技集团公司第二研究所,山西太原030024;中国电子科技集团公司第二研究所,山西太原030024;中国电子科技集团公司第二研究所,山西太原030024;中国电子科技集团公司第二研究所,山西太原030024;中国电子科技集团公司第二研究所,山西太原030024【正文语种】中文【中图分类】TQ153.4电铸是利用电沉积方法在作为阴极的原型进行加厚电镀,从而复制出与原型一样的制品方法,是电沉积技术的重要应用技术之一[1]。
电铸作为一种精密加工技术具有复制精度高和工艺简单等优点,电铸铜作为电铸的一个铸种,在具有以上优点的同时,还具有优良的导电性和导热性及延展性[2],在仪器仪表、塑料、铜版浮雕模、雕塑艺术创作、精密机械、模具制造、电子工业及纳米材料制备等方面获得广泛应用。
本文通过对电铸铜工艺及工艺条件影响的初步分析,获得工艺条件对电铸铜镀层影响规律,为进一步优化工艺及电铸槽的设计奠定了基础。
1 电铸铜工艺1.1 电铸铜的工艺流程原型表面预处理—清洗—电镀—电铸—纯水喷洗、氮气吹干—脱模。
在电铸铜工艺中原型表面预处理,对于非金属原型电铸铜,首先要进行表面修整后再进行表面金属化;如果原型为导电材料,造型和表面质量符合要求即可。
1.2 铜电铸液成分本设备铜电铸采用的为酸性硫酸铜镀液,该电铸液具有镀液稳定及在高电流密度下工作的优点,通过电铸添加剂,可获得高速及整平性好的光亮镀层,这种镀层的结晶细致,其内应力及硬度也可得到一定的控制。
铸造基本工艺参数对铸锭质量的影响
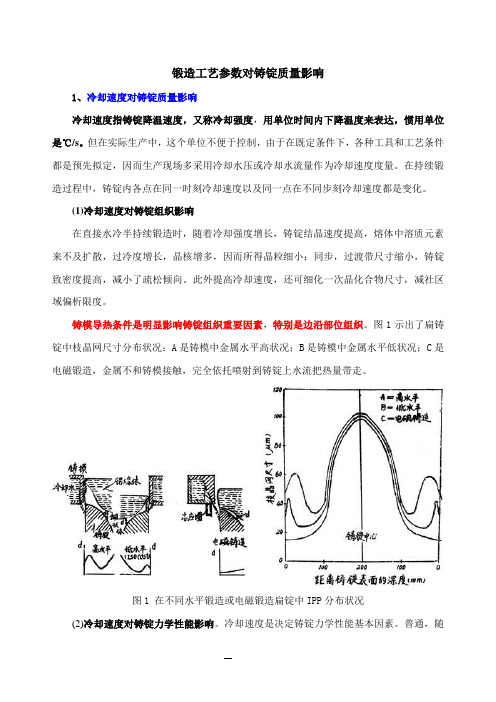
锻造工艺参数对铸锭质量影响1、冷却速度对铸锭质量影响冷却速度指铸锭降温速度,又称冷却强度,用单位时间内下降温度来表达,惯用单位是℃/s。
但在实际生产中,这个单位不便于控制,由于在既定条件下,各种工具和工艺条件都是预先拟定,因而生产现场多采用冷却水压或冷却水流量作为冷却速度度量。
在持续锻造过程中,铸锭内各点在同一时刻冷却速度以及同一点在不同步刻冷却速度都是变化。
(1)冷却速度对铸锭组织影响在直接水冷半持续锻造时,随着冷却强度增长,铸锭结晶速度提高,熔体中溶质元素来不及扩散,过冷度增长,晶核增多,因而所得晶粒细小;同步,过渡带尺寸缩小,铸锭致密度提高,减小了疏松倾向。
此外提高冷却速度,还可细化一次晶化合物尺寸,减社区域偏析限度。
铸模导热条件是明显影响铸锭组织重要因素,特别是边沿部位组织。
图1示出了扁铸锭中枝晶网尺寸分布状况:A是铸模中金属水平高状况;B是铸模中金属水平低状况;C是电磁锻造,金属不和铸模接触,完全依托喷射到铸锭上水流把热量带走。
图1 在不同水平锻造或电磁锻造扁锭中IPP分布状况(2)冷却速度对铸锭力学性能影响。
冷却速度是决定铸锭力学性能基本因素。
普通,随冷却速度增大,铸锭平均力学性能得到提高。
冷却速度这种作用重要是由下面两个因素引起:一是随冷却速度增大,铸锭结晶速度提高,晶内构造细化;二是随冷却速度增大,铸锭过渡带尺寸缩小,铸锭致密度提高。
此外,提高冷却速度,还可细化一次晶化合物尺寸,减社区域偏析限度。
但是,合金成分不同,冷却速度对铸锭力学性能影响限度是不同样,对变形铝合金而言,大体可分为四个基本类型:第一类是在所有温度下(从室温到熔点)均呈单相合金,如各种牌号高纯铝、工业纯铝、5A66、7A01等。
这些合金铸态力学性能同冷却速度关系不太强烈,冷却速度仅在能消除破坏金属持续性缺陷(疏松、气孔)极限速度之前有影响(见图2a)。
第二类是铸态呈多相,但在固溶热解决后变成固溶体合金,如5A12、5A13等。
镀覆孔的质量控制和检测方法
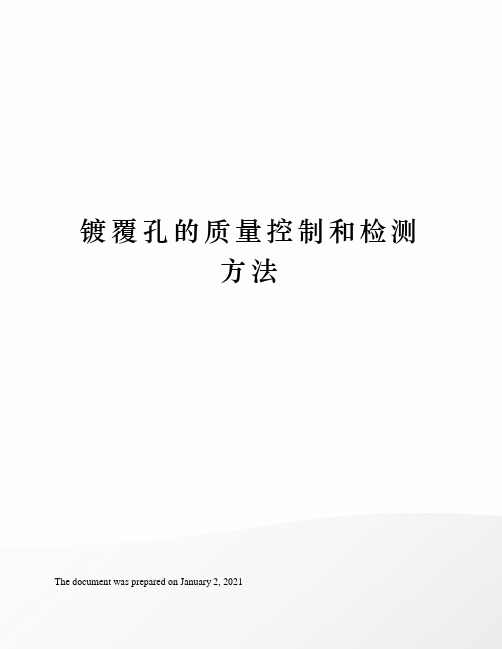
镀覆孔的质量控制和检测方法The document was prepared on January 2, 2021镀覆孔的质量控制和检测方法随着微电子技术的飞速发展,多层和积层印制电路板在电子工业中获得广泛的应用,并且对可靠性的要求越来越高.而镀覆孔作为贯穿连接多层与积层式印制电路板各层电路的导体,其质量的优劣对印制电路板的可靠性有着很大的影响.因此,在印制电路板生产过程中对镀覆孔的质量控制和质量检测,对镀覆孔的质量保证起着非常重要的作用.在印制电路板制造程序中,对镀覆孔质量影响较大的工序主要是数控钻孔、化学沉铜和电镀等.要实行质量跟踪与检测,就必须根据不同的工序的特点,制定与建立控制要点和设立控制点,并采取不同的工艺方法和检测手段,实现随机质量控制.为更加深刻地了解各工序的工艺特性,就需分别加以研究与讨论.一.钻孔质量的控制钻孔是印制电路板制造的关键工序之一.对于钻孔工序而言,影响孔壁质量的主要因素是钻头的转速和进刀速度.要设定正确的钻孔工艺参数,就必须了解所采用的基板材料的性质和特点.否则所设定的工艺参数:转速、进刀速度等所钻的孔就达不到技术要求,严重的就会造成孔壁环氧钻污或拉伤,以致在后工序沉铜或电镀过程中产生空洞、镀瘤等缺陷.根据这种情况,就必须采用工艺试验法,也就是将进厂的基板材料进行实验,设定不同的进刀速度和转速进行组合钻孔,再经化学沉铜后,采用金相剖切法对切片呈现的孔镀层图像与实物进行评估,确定最隹的工艺参数范围,以便在生产过程中根据不同厂家供应的基板材料调整工艺参数.当然,在钻孔工序中其它影响孔壁质量有因素也必须予以重视和控制.如钻头的质量及钻孔过程所使用的上盖板下垫板材料、钻孔过程的吸尘系统和叠层的数量等.二.沉铜工序的质量控制化学沉铜是镀覆孔过程的第一步,它的质量优劣直接影响电镀的质量.因此确保化学沉铜层的质量,是保证通孔电镀质量的基础.为此,必须严格地对化学沉铜槽液进行有效的控制和检测.这因为化学沉铜溶液在生产过程中溶液的各种成份会有很大的变化,除了实现自动控制系统的作用外,还应采取定期定时的抽查分析溶液中各种成份的含量是否符合工艺规范要求,以确保溶液正常工作.根据化学沉铜机理主要控制其沉积速率及沉积层的密实性.化学沉铜的沉积效果检测的主要项目是沉积速率和背光试验来进行.1沉铜速率的控制和检测根据化学沉铜的反应化学原理,对化学沉铜速率的主要影响因素有二价铜离子浓度、甲醛浓度、PH值、添加剂、温度和溶液搅拌等.所以,每当溶液工作一段时间时间的长短由溶液的负载量来决定,就采用一块试验板带有孔随产品流过沉铜生产线,以测试其沉铜速度是否符合工艺技术指标与要求.如符合工艺要求,产品板还必须使用检孔镜对产品板进行检查后转入下道工序.如未符合工艺要求,就必须进行背光实验作进一步的测试与判断.测试沉铜沉积速率和背光试验的具体工艺方法如下:1.沉积速率的测定:首先将剥掉铜的基板,剪裁成尺寸为100×100mm即1dm2在试验板上一排小孔,留着背光试验用.测定沉积速率的板沉铜前后均在120℃下烘1小时再称重.沉铜速率可通过下式计算:S=W2-W1/t×式中:S-沉铜速率m/minW1-沉铜前试验板重量gW2-沉铜后试验板重量gT-沉铜时间min-每沉积1克铜新增加铜层厚度m2.背光实验的检测:主要检测沉铜层的致密度.评定的标准要根据所采用的供应商提供的标准而定.德国先灵公司将沉铜层的致密度分为12个背光等级,最高为5 级,最低为级;其它公司所提供的等级标准各有不同,都有评定的合格标准,如背光等级低于合格标准,就说明沉铜层的致密度差,其最终的电镀质量也就无法保证.其具体的方法就是将试验板切一块带有孔的基板材料作试样,经过锯切或磨制到孔中心位置即中心线上.测试时利用光从底面射入,然后使用100倍放大镜进行检查即可.通过上述两种控制沉铜质量的工艺方法,就可以进一步确定孔壁质量的可靠性,当转入下道工序-进行电镀铜时,只要能够严格的控制电镀工艺参数就可以达到最终的技术标准和技术要求.三.电镀铜层质量的控制通孔电镀铜层质量控制是非常重要的,因为多层或积层板向高密度、高精度、多功能化方向的发展,对镀铜层的结合力、均匀细致性、抗张强度及延伸率等要求越来越严,也越来越高,因此对通孔电镀的质量控制就显得特别重要.为确保通孔电镀铜层的均匀性和一致性,在高纵横比印制电路板电镀铜工艺中,大多都是在优质的添加剂的辅助作用下,配合适度的空气搅拌和阴极移动,在相对较低的电流密度条件下进行的,使孔内的电极反应控制区加大,电镀添加剂的作用才能显示出来,再加上阴极移动非常有利于镀液的深镀能力的提高,镀件的极化度加大,镀层电结晶过程中晶核的形成速度与晶粒长大速度相互补偿,从而获得高韧性铜层.当然,电流密度的设定是根据被镀印制电路板的实际电镀面积而定.从电镀原理解度分析,电流密度的取值还必须依据高酸低铜电解液的主盐浓度、溶液温度、添加剂含量、搅拌程度等因素有关.总之,要严格控制电镀铜的工艺参数和工艺条件,才能更能确保孔内镀铜层的厚度符合技术标准的规定.但必须通过评定,做法如下:1孔壁镀铜层厚度的测定根据标准规定,孔壁镀铜层的厚度应25微米.镀铜层过薄会导致孔电阻超标,而且还有可能经红外热熔或热风整平过程中出现孔壁铜层的破裂.具体的测定方法就是利用金相切片,选择孔壁镀层内最薄的部位不同位置三个测点,进行测试,将其测试结果取平均值.2孔壁铜层热应力的测试孔壁在电镀过程中,镀层会有应力产生.特别当电镀液洁净度不高的情况下,孔壁镀铜层的应力就大,通过热应力的试验 ,孔口处会因为应力集中而产生开裂;如果电镀质量高的话,其产生的应力就很小,通过热应力试验后,其金相部切的结果,孔口未开裂.通过测试结果就可以确定其生产还是停产.上述所谈及的有关镀覆孔质量的控制问题,是最普遍采用的工艺措施和方法.随着高科技的发展,新的控制系统就会出现,特别全封闭式水平生产流水线上采用“反脉冲技术”的供电方式逐步取代直流供电形式,达到解决深导通孔与深盲孔电镀问题已取得更加明显的经济和技术效果.高纵横比导通孔电镀技术印制电路板制造业越来越需要高纵横比、小孔印制电路板的电镀工艺.它是推动高层数多层印制电路板制造技术发展的动力.因为孔镀层的可靠性,对印制电路板的运用起到了关键性的作用.如何确保高纵横比深孔电镀问题,是所有印制电路工作者的科技任务,是必须面临的最重要问题.为此,很多研究部门着手进行有计划的研制和开发.从当前的科技资料报导推芨的方法很多,其中有脉冲电镀技术、化学气相沉积技术、溶液冲击电镀技术、全化学镀铜技术和改进型高酸低铜的空气搅拌技术等.现将这部分技术分别简介如下:一.脉冲电镀工艺技术脉冲电镀技术,早已运用于电铸成型工艺中,是比较成熟的技术.但运用在高纵横比小孔电镀还必须进行大量的工艺试验.因脉冲电源不同于一般的直流电源,它是通过一个开关元件使整流器以US的速度开/关,向阴极提供脉冲信号,当整流器处于关的状态时,它比直流电更有效地向孔内的边界层补充铜离子,从而使高纵横比的印制电路板沉积层更加均匀.目前已研制的脉冲整流器运用在全封闭式水平电镀生产流水线上,使用的效果取得极为明显的经济和技术成效.采用了“定时反脉冲”按照时间使电流在供电方式上忽而正镀忽而反镀即阳极溶解按照时间比例交替进行,使电度铜的沉积很难在常规供电方式取得相应的铜层厚度而得以解决.当阴极上的印制电路板处于反电流时,就可以将孔口高电流密度区铜层迅速得到迅速的溶解,由于添加剂的作用,对低电流密度区影响却很微,因而将逐渐使得孔内铜层厚度与板面铜的厚度趋向于均等.反脉冲技术应用到印制电路板生产中,很好的解决了多层板与积层板上面的深孔或深盲孔纵横比为1:1以上-指盲孔而言电镀的难题.它与常规的供电方式电镀铜进行比较,其数据列表如下:表4 直流与脉冲对深孔镀铜的比较样板孔长mm孔径mm纵横比电流密度ASD脉冲电镀铜直流电镀铜反波/正波电流比%正反时间比ms分布力%全程时分分布力%全程时间分A8:1310 20/ 92 5875 113:125020/784570-7570二.化学气相沉积技术化学气相沉积是沉铜工艺方法之-,它是将气相中的一种组份或多种组份聚积于基体上,并在基体上发生反应,产生固相沉积层.而化学气相沉积属于原子沉积类,其基本原理是沉积物以原子、离子、分子等原子尺度的形态在材料表面沉积,形成外加覆盖层,如果覆盖层是通过化学反应形成的,则称为化学气相沉积CVD,其过程包括三个阶段即:物料气化、运到基材附近的空间和在基体上形成覆盖层.该技术发展很快,它所得以迅速发展,是和它的本身的特点分不开的,其特点是:沉积物众多,它可以沉积金属;能均匀涂覆几何形状复杂的零件,这是它具有高度的分散性;涂层与基体结合牢固;设备简单操作方便.采用CVD新技术的目的在于解决高纵横比小孔电镀问题,提高生产效率和镀层的均匀性和物化性能及使用帮命.最常用CVD的新技术有脉冲CVD法、超声波CVD等.化学气相法沉积技术的应用,还必须做大量的工艺试验,使该项新技术,能在解决高纵横比深孔或积层式的深盲孔电镀上起到应有的作用.三.溶液冲击电镀铜工艺技术它是和电镀金生产线高速流动的金液冲击印制电路板插头的表面进行电镀的原理同样的工艺方法.其具体的实施方法就是在电镀槽中安装2个5马力的的马达,迫使阴极附近的溶液以-1.12kg/cm2的压力喷出管道上孔径为12.7mm的孔,射向印制电路板的一边,然后从印制电路板的另一边流出,电镀通孔的进出口压力不同,两管道平行放置,溶液以150-250克/分钟的流速循环通过管道,这提高板面镀层的均匀性,阴极并以50.8MM的半径旋转,而不是平行来回移动,冲击电镀与常规的空气搅拌电镀相类似,都依赖于化学特性和电气特性.这一种类型的工艺方法,给槽体系统的制造带来一些系列的因难,因为要适应这种工艺方法的需要,还必须设计一套复杂的专用泵、特殊的夹具和电镀槽的结构形式,能否很快地运用到解决高纵横比小孔电镀铜问题,这需很长一段时间,但从原理分析,应是可行的,但需要作很大的改进.四.全化学镀铜工艺技术全化学镀铜工艺方法解决深孔电镀问题以是一种途径,它是利用化学催化作用,而不是电气作用来沉积铜,由于不需要施加电流,因而也就不存在由于电流分布不均匀而导致的镀层分布不均匀的问题.全化学镀铜的沉积速率为-m/hr,按照这个速率沉积30m的铜层需要18小时以上,生产效率很低,但它的工作负载高达-平方英尺/4.5升-平方米/升而电化学方法的工作负载只有平方米/升,其化学组份采用自动分析仪来控制,在生产过程中沉积速度可以采用沉积速度试验板来定期监控.如把此种类型的工艺技术用生产自动流水线上,仅需要在现有的化学沉铜线上增加一个10%弱腐蚀槽和一个全化学沉铜槽就可以了.但从试验报告中获知,此种类型的工艺方法,对通孔电镀能力很强,表面与孔镀层厚度比接近1:1,但它的最大缺陷就铜层的最重要的物性-延伸率只有2-3%,离标准差距较大,而且镀层脆,特别是经热冲击后铜镀层容易产生破裂.五.改进型空气搅拌电镀技术空气搅拌电镀体系,此种类型的工艺方法已被诸多厂家运用于生产流水线上,取得较明显的技术效果.该工艺体系是采用印制电路板来回移动搅拌溶液,使孔内的溶液得到及时交换,同时又采用高酸低铜的电解液,通过提高酸浓度增加溶液的电导率,降低铜浓度达到减小孔内溶液的欧姆电阻,并借助优良的添加剂的配合,确保高纵横比印制电路板电镀的可靠性和稳定性.根据电解液的特性,要使得深孔电镀达到技术要求,就必限制电流密度的取值,原因是因为欧姆电阻的直接影响,而不是物质的传递.重要的是确保孔内要有足够的电流,使电极反应的控制区扩大到整个孔内表面,使铜离子很快的转化成金属铜,为此应把常规使用的电流密度值降低到50%使电镀通孔内的过电位比高电流密度电镀时,孔内可以获得足够的电流.以上所介绍的工艺方法,其中有些技术现已经运用在生产高纵横比的印制电路板电镀铜上,取得很好的效果.目前较为成熟的脉冲电镀技术,经过研制和开发,采用“定时反脉冲”工艺技术运用到多层和积层多层印制电路板的深孔或深盲孔电镀铜上,制造出适应脉冲电镀的反脉冲整流器,使此种类型的工艺方法定会处到普遍应用.全板镀金镀层起层与色变的原因分析及控制在型号研制生产过程中,其控制系统中的四层板需全板镀金,该板的特点是密度高,导线细、间距窄只有0.05mm导线宽度0.30 mm.为确保金-镍-铜层的结合力,对所经过的工序都进行分析和处理,使各种类型的处理溶液处于最隹状态,首先排除各类溶液对三者之间结合强度的直接影响.但稍为不慎就会产生镍层从铜层上分离开来或者金镀层从镍镀层表面脱落,其原因经过多次试验,有以下三个方面:一镀层分层的原因分析1.经光亮镀铜后,没有进行彻底地的清除表面膜,因此清洗后直接转入镍镀槽内进行电镀作业.因此镀后镍层从铜的表面分离.为什么会产生微薄膜呢因为光亮镀铜溶液含有一定量的添加剂如光亮剂、整平剂、润湿剂等,也就指少量的添加剂,它在电解液内不会明显地改变镀液的性质,但会显着的改善镀层的性质,但镀层表面会吸附有此类添加剂等有机物质,这些有机物质在经过镀铜的表面吸附的很牢,很难使用一般的流动清洗水除去,必须配有专用的处理溶液进行一定时间的清除处理,方能达到满意的表面效果.就是因为这些看不见的透明薄膜,直接影响镍镀层与铜表面的结合强度.2.铜表面还必须进行微粗化处理,使铜表面形成微粗糙的表面,以增加铜层与镍层的结合强度.因为镍镀层具有一定的应力,这种应力特别在光亮的铜表面就会形成拉应力,而从铜的表面分离,微粗化的目的就是增加与镍镀层的结合力.由于粗化处理不当,造成铜层表面不均匀状态,使镍镀层的分布的一致性受到直接影响,造成局部结合力好,星星点点的部位差,而发生镍层从铜的表面上分层.3.铜的表面经过处理后,清洗的时间不易过长,因为清洗水也含有一定的酸性物质尽管其含量微弱,但对铜的表面影响不能掉以轻心,应严格按照工艺规范规定的时间进行清洗作业.4.金层从镍层表面脱洛的主要原因,就是镍的表面处理的问题.镍金属表面活性差很难取处令人满意的效果.镍镀层表面易在空气中产生钝化膜,如处理不当,就会使金层从镍层表面分离.如活化不当就会在进电镀金时,金层就会从镍层表面脱离即起皮脱落.第二方面的原因是因为活后,清洗的时间过长,造成镍表面从新生成钝化膜层,然后再去进行镀金,必然会产生镀层脱落的疵.以上分析了三种镀层间产生质量缺陷的主要原因.解决此种类型的质量问题,就必须针对其表面特点,采取不同的工艺方法进行处理.根据光亮镀铜表面的特性分析,要获得高质量的镀层品质,就必须采取镀后进行弱腐蚀处理,以除去表面由于添加剂造成的表面膜,使用稀硫酸水溶液进行处理,使铜表面呈现激化状态,立即带电转入镍槽内,根据被镀面积选取适当的电流密度进行电镀.镀镍后立即经过新盐酸活化处理,经清洗后立即进行金槽内进行镀金.经过这样的处理后,三者镀层的之间的结合力才能达到规定的工艺技术指标.二金层颜色不正或变色的原因分析酸性镀硬金所使用的电流密度很小,控制不好镀层就会发黑或发红,这就说明使的电流密度不当,当电流的设定值确定后,金层表面仍然显示不出金的本色,这主要原因是溶液的温度选择不当.这是控制方面选择不当所造成的镀层颜色不正常.另一方面由于柠檬酸盐镀其溶液的粘度增高,镀金后回收槽清洗后,再用流动水冲洗表面没有冲洗干净,当暴露于空气中而变色.所以,镀金后的表面清洗要严格按照工艺规范进行,以确保镀层质量的可靠性和稳定性.三镀金工艺规范中规定的电流密度很窄,所以控制时要非常严格,稍为电流密度控制失灵,金层质量就无法保证.根据这种工艺特性,最好采用“面积测定法”即进行严格而又精确的计算的圆面积,安装导电挂具,将不需要镀的部位用绝缘物保护起来,只留下规定的电流密度抽需的电镀面积,使电流密度保持在规定的工艺范围内.采用此种工艺措施就能确保镀金部位所需要的电流,使金层质量有很大的提高.因此,无论是全板镀金或局部镀金,首先要确保表面无沾污、金层表面处于激活状态和严格地控制工艺规范所提供的工艺参数及槽液成份正常的情况下,才能镀出高质量的光亮的金黄色金层.。
电解过程影响因素

电解过程影响因素电解过程是指通过外加电流使电解质在电解槽中发生化学反应的过程。
在电解过程中,有很多因素会对反应的进行产生影响。
本文将从电解质的种类、浓度、温度、电流强度以及电解槽的设计等方面进行探讨。
电解质的种类是影响电解过程的重要因素之一。
不同的电解质在电解过程中会产生不同的化学反应。
例如,在氯化钠溶液中,正极会产生氯气,负极会产生氢气和氢氧化钠溶液。
而在硫酸铜溶液中,正极会产生氧气,负极会产生铜沉积。
因此,选择合适的电解质对于所需的反应非常重要。
电解质的浓度也会影响电解过程的进行。
一般来说,电解质的浓度越高,电解过程的速度越快。
这是因为在高浓度的电解质溶液中,离子的浓度较高,电导率较大,电流可以更容易地通过电解质溶液。
因此,在实际应用中,可以根据需要调整电解质的浓度来控制反应速率。
温度也是影响电解过程的重要因素之一。
一般来说,提高温度可以加快电解反应的速率。
这是因为在高温下,溶液的粘度会降低,离子的迁移速率加快,电解质中的化学反应速率也会增加。
然而,过高的温度也会引发副反应或者导致电解质的分解,因此在实际应用中需要控制好温度的范围。
电流强度也会对电解过程产生影响。
一般来说,电流强度越大,电解过程的速度越快。
这是因为电流强度决定了单位时间内通过电解质溶液的电量,而电量与化学反应的速率直接相关。
因此,在实际应用中,可以通过调整电流强度来控制反应速率。
电解槽的设计也会对电解过程产生影响。
电解槽的形状和尺寸会影响电流的分布以及反应物质的扩散速率。
因此,在电解槽的设计中需要考虑电流的均匀分布和反应物质的有效接触。
一般来说,采用合适的电解槽设计可以提高反应的效率。
电解过程受到多个因素的影响,包括电解质的种类、浓度、温度、电流强度以及电解槽的设计等。
在实际应用中,需要根据具体情况调整这些因素,以达到所需的反应速率和效果。
通过合理地控制这些影响因素,可以实现电解过程的高效进行。
电镀铜原理概

电镀铜(二)3.4操作条件的影响温度温度对镀液性能影响很大,温度提高,会导致允许的电流密度提高,加快电极反应速度,但温度过高,会加快添加剂的分解,使添加剂的消耗增加,同时镀层光亮度降低,镀层结晶粗糙。
温度太低,虽然添加剂的消耗降低,但允许电流密度降低,高电流区容易烧焦。
一般以20-300C为佳。
3.4.2电流密度当镀液组成,添加剂,温度,搅拌等因素一定时,镀液所允许的电流密度范围也就一定了,为了提高生产效率,在保证镀层质量的前提下,应尽量使用高的电流密度。
电流密度不同,沉积速度也不同。
表8-5给出了不同电流密度下的沉积速度(以阴极电流效率100%计)。
表8-5 电流密度与沉积速度时间( 分) 镀层厚度(μm)6 9 12 24 36 电流密度(A/dm2)1 28 41 54 1082 14 21 28 56 823 9 14 19 37 55 镀液的最佳电流密度一定,但由于印制电板的图形多种多样,难以估计出准确的施镀面积,也就难以得出一个最佳的电流值。
问题的症结在于正确测算图形电镀的施镀面积。
下面介绍三种测算施镀面积的方法。
1)膜面积积分仪:此仪器利用待镀印制板图形的生产底版,对光通过与阻挡不同,亦即底版黑色部分不透光,而透明部分光通过,将测得光通量自动转换成面积,再加上孔的面积,即可算出整个板面图形待镀面积。
需指出的是,由于底片上焊盘是实心的,多测了钻孔时钻掉部分的面积,而孔壁面积只能计算,孔壁面积S=πDH,D一孔径,H一板厚,每种孔径的孔壁面积只要算出一个;再乘以孔数即可。
此法准确,但价格较贵,在国外已推广使用,国内很多大厂家也在使用。
2)称重计量法:剪取一小块覆铜箔单面板,测量出一面的总面积,将板子在800C烘干1小时,干燥冷至室温,用天平称取总重量(Wo).在此板上作阴纹保护图形,蚀掉电镀图形部分的铜箔,清洗后按上法烘干称重,得除去电镀图形铜箔后的重量(W1),最后全部蚀刻掉剩余铜箔,清洗后按上法干燥称重,得无铜箔基体的净重(W2),按下式可算出待电镀图形的面积S:S=S0X(W0-W1)/(W0-W2)式中:S0 覆铜箔板的面积。
热处理对铜合金材料导电性能的影响分析

热处理对铜合金材料导电性能的影响分析热处理是一种通过控制材料的加热和冷却过程来改变其结构和性能的方法。
在铜合金材料的制备过程中,热处理常常被用来优化材料的导电性能。
本文将对热处理对铜合金材料导电性能的影响进行分析,并探讨其原理和影响因素。
一、热处理方法常见的铜合金材料热处理方法包括退火、淬火和时效处理。
退火是通过加热材料至一定温度后,保持一定时间,然后缓慢冷却至室温。
淬火是将材料加热至高温后迅速冷却至室温。
时效处理是将材料在一定温度下保持一定时间,然后冷却至室温。
二、热处理对导电性能的影响1. 晶粒尺寸热处理过程中,晶粒尺寸会发生变化,这将直接影响铜合金材料的导电性能。
通过合适的热处理方法,可以实现晶粒尺寸的细化,从而提高材料的导电性能。
2. 晶界及析出物晶界是指晶粒之间的边界,也是电子在材料中传导的主要通道。
热处理会对晶界的结构和化学成分产生影响,进而影响材料的导电性能。
此外,热处理还可能导致材料中出现析出物,如奥氏体相、金属间化合物等,这些析出物的形成也会对导电性能产生影响。
3. 化学成分铜合金材料的化学成分也会对导电性能产生重要影响。
在热处理过程中,通过调整材料的化学成分,可以进一步改善其导电性能。
三、热处理的优化方法针对不同的铜合金材料和导电性能要求,可以采取不同的热处理优化方法。
以下是几种常用的方法:1. 温度控制热处理过程中的温度控制非常重要。
合适的退火温度、淬火温度和时效温度可以有效控制晶粒尺寸和晶界结构,从而达到最佳的导电性能。
2. 时间控制热处理时间也是影响导电性能的重要因素。
适当的保温时间和冷却时间可以实现晶粒尺寸的细化和析出物的形成,进而提高导电性能。
3. 合金元素调整通过调整铜合金材料的化学成分,可以改变其晶界结构和析出物的类型和数量,从而改善导电性能。
例如,添加少量的镍、锡等元素可以降低导电材料的电阻率,提高导电性能。
四、实际应用热处理对铜合金材料导电性能的影响已经广泛应用于实际生产中。
对铜热电动势率

对铜热电动势率
铜热电动势率是指铜在温度变化下产生的热电动势的变化速率。
铜是一种重要的导电材料,具有良好的热电性能。
在温度变化时,铜材料会产生热电动势,这是由于热量引起的电子在材料内部的移动所致。
铜热电动势率的大小与温度变化的快慢有关。
当温度变化较慢时,铜热电动势率较小;而当温度变化较快时,铜热电动势率较大。
这是因为温度变化快时,铜内部电子的移动速度增加,从而导致热电动势的变化速率增大。
铜热电动势率的大小对于一些特定的应用非常重要。
例如,在温度传感器中,铜热电动势率可以用来测量温度的变化。
通过测量铜热电动势率的变化,我们可以准确地知道温度的变化情况,并进行相应的控制。
铜热电动势率的研究也对于热电材料的开发具有重要意义。
热电材料是一类能够将热能转换为电能的材料,具有广泛的应用前景。
通过研究铜热电动势率的变化规律,我们可以更好地了解热电材料的性能,并为热电材料的设计与制备提供参考。
铜热电动势率是一个重要的物理量,它描述了铜在温度变化下产生的热电动势的变化速率。
铜热电动势率的研究对于温度传感器的应用和热电材料的开发具有重要意义。
通过深入研究铜热电动势率的
变化规律,我们可以更好地理解铜材料的热电性能,并为相关领域的研究和应用提供有益的参考。
- 1、下载文档前请自行甄别文档内容的完整性,平台不提供额外的编辑、内容补充、找答案等附加服务。
- 2、"仅部分预览"的文档,不可在线预览部分如存在完整性等问题,可反馈申请退款(可完整预览的文档不适用该条件!)。
- 3、如文档侵犯您的权益,请联系客服反馈,我们会尽快为您处理(人工客服工作时间:9:00-18:30)。
F
善 叠 善
0
100
200 400
600
800 1 000
阴极移动速度/(mm·B-1)
图3 阴极移动速度对极限电流密度的影响
1.2影响电化学反应(电子转移)过程的因素 当电极浸入镀液,未通电前如电极处于平衡状
态,电位为虹,电极与溶液之间不断进行着金属离 子的交换,而且氧化反应和还原反应的速率相等,用 i。表示。实验表明:i。越大,说明电化学反应越容 易,通电后越不容易在电极上积累剩余电荷,电化学 极化也就越小;相反,i。越小,说明电化学反应越困 难,通电后越容易在电极上积累剩余电荷,电极电位 也就偏离虹越远,电化学极化也就越大。由塔菲 尔(Tafel)公式C11:I△乒I=口+b log i(口,b为常数)可 知,极化度与通过的电流i有关。据理论推导,n与 i。有关,可将上式改写为l△乒I一--b log i。+b log i 或I酗l—b log(i/i。)。实验测得Cu2+在1 mol/L CuSO。溶液中的i。约为103 A/dm2,比很多金属在 同等条件下的i。要大几十、几百甚至上千倍。根据 公式可以推断酸铜工艺中在一定电流通过电极时, 电化学极化非常小,说明电化学反应速率非常快。 研究影响电化学反应速率的因素,对提高电铸铜质 量非常有价值。 1.2.1 Cu2+的质量浓度
I竺l 胡 王瑞祥.钢铁基体上碱性无氰镀铜[J].电镀与涂饰,2005,
24(7)l 13-15. ∞ 幻 高琛,尹国光,张自广,等.碱性无氰镀铜工艺研究[J].
I竺l 阳
福建化工,2005(1)117-20. 蔡爱清,王建华。曹相锋.碱性无氰镀铜工艺研究[J].电镀 与精饰,2007,29(3):45-47.
部地区不可能长得过快,所获得的晶粒自然就比较
细小,从而得到细致光滑的电镀层。这时表面扩散
步骤的速度比放电步骤快得多[1],所以电化学反应
速率就成了控制整个电结晶速率的因素之一。
,
以上可看出,电流密度增加时,反而使吸附原子
的扩散步骤变得容易了。因此,电结晶过程的速率
可以随电流密度的提高、阴极极化的增加有很大程
传质速度大得很多,所以有机添加剂对电结晶速率
的影响可以不考虑。有机添加剂的吸附作用能增大
阴极的电化学极化,因而有利于晶核的形成,获得细
小的晶粒;另一方面,有机添加剂可优先吸附在某些
活性较高、生长速率较快的晶面,使得吸附原子进入
万方数据
·1 6· Mar.2008
Electroplating&Pollution Control
酸性硫酸盐镀铜工艺因其成分简单、维护方便、 电流效率高、极限电流密度相对较大、废水处理容 易、成本低等优点,是理想的电铸铜工艺的选择。本 文以酸铜工艺为例,就影响电铸速率的因素进行 分析。
1影响电铸速率的因素
电铸铜属于电镀工艺的范畴。研究镀铜速率的 影响因素,便能制定合理的电铸铜工艺。
电镀速率主要受三个过程的影响[1]: (1)液相传质过程反应粒子自溶液中向电极 表面附近传输; (2)电化学反应(电子转移)过程 反应粒子在 电极与溶液界面间得失电子; (3)新相形成的过程 在阴极表面形成新相
(如结晶)。 1.1影响液相传质过程的因素
通电前溶液中各个部分的Cu2+的浓度都是均 匀的,通电后阴极表面的Cu2+会被迅速消耗,溶液 中的Cu2+就会通过电迁移、扩散和对流三种方式向 阴极表面传输。但这三种方式的传输速度都是有限 的,这就造成了电极的浓度极化。如果电极上通过 的电流密度过大,超过了极限电流密度,溶液中的 Cu2+未能及时进行补给,使电极的极化过电位达到 或超过H+的析出电位,H+就会在阴极上被还原, 使阴极表面溶液的pH值迅速升高,就会形成金属 离子的氢氧化物沉淀,并夹杂在镀层中,造成“烧焦” 现象。在酸铜工艺中,液相传质过程是控制电镀速 率的主要因素。相对于其他两个过程而言,这是一 个基元因素,加快传质过程的速度能有效地提高极 限电流密度,对提高镀速有重大意义。 1.1.1 Cu2+的质量浓度
o 胡 温青,邓正平,高中平.无氰碱性镀铜清洁生产工艺的研
究口].电镀与涂饰,2005,24(11)t36—39.
口刀
奚兵.新型碱性无氰镀铜工艺口].腐蚀与防护,2005,26 (1)137-38.
D胡
袁诗璞.路漫漫兮,无氰碱铜[J].电镀与涂饰,2006,25 (8):51—53.
收稿日期,2007—09—17
在电镀铜工艺中,电极的电化学极化度很小,电 化学反应速率极快。为了得到优良的电镀层,我们 必须提高电化学极化度。当镀液中加入相应的有机 添加剂后,由于它们在电极表面的吸附,增大了电化 学反应的阻力,使金属离子的还原反应变得困难,电 化学极化增大。因而有利于晶核的形成,使晶核的 形成速率大于晶体的生长速率,有利于获得细小的 晶粒。
由于浓度极化是由反应物在电极表面的传质速 度受到限制所引起的,因此,提高镀液的温度能很大 程度上提高反应物粒子自由能,加快扩散传质速度, 对降低浓度极化有相当大的作用。温度对极限电流 密度的影响,如图2所示。提高温度同时能有效提 高硫酸铜的溶解度,避免硫酸铜结晶析出;但温度也 不能过高,否则添加剂的消耗量会过大,有些中间体
子,形成在晶体表面上可以自由移动的吸附原子。
然后吸附原子在金属表面上移动寻找能量较低的位
置,在脱去全部水化膜的同时进入晶格,完成电结晶 过程。
在电极电位偏离平衡电位不远,电流密度很小
的情况下,金属离子在电极上还原的数量不多,吸附
原子的浓度较小,而且晶体表面上存在的“生长点”
也不多,吸附原子在电极表面的扩散相当困难。于
2008年3月
电镀与环保
第28卷第2期(总第160期) ·13·
的影响FJ].表面技术,2006,35(4);40一45. [27]蔡梅英,倪步高.缩二脲无氰碱性镀铜方法,中国,1 183485
[P1.1998—06—03. [28]辽宁兴城东华机械厂.草酸镀铜工艺的改进[J].材料保护,
1990,23(II):33-34. [293程 良.三乙醇胺碱性光亮镀铜[J].材料保护,1988,21
虽然有机添加剂在电镀过程中增大了电化学极
化度,阻碍了电化学反应速率。但由于酸铜工艺中
电极的电化学反应速率非常快,传质速度才是一个
基元因素。有机添加剂的加人不会对总体的电镀速
率产生不利影响,反而对得到优良镀层有非常大的
价值。
1.3影响新相成的过程因素
在电镀过程中形成的金属镀层几乎都是晶体。
当金属离子失去部分水化膜,在电极表面上获得电
Electroplating&Pollution Control
V01.28 No.2
流密度的影响,如图1所示。但硫酸铜的质量浓度 的提高受其溶解度的限制,故工艺温度也相应提高。 为消除溶解度的影响,硫酸铜的质量浓度不宜超过 300 g/L。
8
,、6 呷
差4
荨
2
0
50
100
150 200 250 300
图2温度对极限电流密度的影响
也会分解失去作用;故需要寻求耐高温型的中间体 配制添加剂,以满足生产需要。目前有几种添加剂 在55℃下仍具有优良的性能,受到市场的欢迎。 1.1.4搅拌或高速阴极移动
由费克定律可知,扩散速度与扩散层厚度成反 比关系。如能有效地降低扩散层的厚度,对提高扩 散速度是有利的。加强搅拌或提高阴极移动速度就 是很好的方法。它不仅能有效降低扩散层的厚度, 还能提高对流速度;对提高极限电流密度,作用非常 显著。而对挂镀而言,阴极移动很难实现高速电镀。 可以通过改变工件电镀的方式来实现,如凹印制版 就是通过版辊的高速旋转(线速度能达到1 m/s)来 实现高速电镀(电流密度可达到30 A/dm2)。阴极 移动的速度与极限电流密度的关系,如图3所示。
是有条件从容不迫进入晶格,晶粒长得就比较大;在
这种条件下表面扩散步骤控制着整个电结晶速率。
当电流密度增大时,电极电位变得更负,吸附原子的
浓度逐渐变大,晶体表面上存在的“生长点”也大大
增多。由于吸附原子表面扩散距离缩短,表面扩散
变得容易,刚刚形成的吸附原子来不及规则地排列
在原有晶格上,而是聚集起来形成新的晶核,使得局
p(CuS04·5t120Y(g·L-1)
图I硫酸铜对极限电流密度的影响
1.1.2硫酸的质量浓度 硫酸是强电解质,能有效降低镀液的电阻,使初
次电流分布趋向均匀。如果硫酸的质量浓度过低, 槽电压升高,分散能力相应降低,阳极则容易钝化。 硫酸的质量浓度过高,一方面,会因同离子效应降低 硫酸铜的溶解度,使硫酸铜结晶析出;另一方面,硫 酸在镀液中属于不参加电极反应的局外电解质,会 影响Cu2+在电场作用下的迁移数量,降低液相传质 速度。若工件不是太复杂,硫酸的质量浓度不宜超 过80 g/L。 1.1.3温度
V01.28 No.2
这些位置有困难,使这些晶面的生长速率下降。这 样就可以使各个晶面的生长速率趋向均匀,形成结 构致密、定向排列整齐的晶体。 1.3.2温度
在化学、电化学、物理化学等领域,温度是影响 各种反应进程的重要因素之一,对反应进程有很大 的推动作用。同样在电化学结晶过程中,温度升高 能提高吸附原子的扩散自由能,提高扩散速度,以更 短的时间进入晶格或形成晶核,加快电结晶速率。 1.4阳极的影响
在电流作用下,紧靠阴极表面的Cu2+的浓度最 小,随着与电极距离的增大,Cu2+的质量浓度也在 变大,最后达到溶液的本体浓度。这个有浓度差的 溶液层称为扩散层(一般0.5 mm左右)。可以通过 提高酸铜溶液中的Cu2+的质量浓度来提高扩散流 量,从而提高液相传质速度。标准条件下对极限电
万方数据
.1 4· Mar.2008
铸铜生产中增加硫酸铜的浓度,能加快电化学反应 的进程。
啤
甜
t
(1)铜电极在0.5 mol/L CuSO·溶液中的极化曲线