低碳烯烃低压羰基合成工艺的技术进展
低压羰基合成丁辛醇工艺技术

低压羰基合成丁辛醇工艺技术摘要:低压羰基合成法是目前生产丁辛醇的主要方法。
世界上羰基合成丁醛装置中,低压羰基合成工艺技术占55%。
丁辛醇装置以丙烯、合成气为原料,采用Davy/DOW低压羰基合成工艺技术生产2-乙基己醇和正丁醇,同时副产异丁醇,设计年运行时间为8000小时,操作弹性为60%~110%。
关键词:低压羰基;丁辛醇;工艺技术;分析引言:丁辛醇装置采用世界较为先进的LP OxoSM SELECTORSM 10液体循环技术,生产2-乙基己醇(俗称辛醇)和正丁醇,它以丙烯和合成气为原料,在铑、三苯基膦催化剂的作用下,发生羰基合成反应生成混合丁醛,丁醛经过丁醛异构物分离得到高纯度正丁醛,在0.2×10-2mol的NaOH溶液作用下,发生缩合反应生成辛烯醛,辛烯醛在铜催化剂作用下与H2发生加氢反应生成粗辛醇,再经过精制后得到产品辛醇;混合丁醛加氢后得到粗混合丁醇,经过预精馏和精馏系统进入丁醇异构物塔。
丁醇异构物塔顶分离出的混合丁醛也可直接进行异构物分离得到正丁醛和异丁醛,异丁醛直接外送至界外,正丁醛经加氢、精制后,得到产品正丁醇。
1.低压羰基合成丁辛醇技术七十年代中期,美国UCC公司、英国DAVY公司和J.M公司合作开发了铑膦催化体系─低压羰基合成工艺。
压力1.6-1.8MPa,正异比高达10:1~12:1,基建投资和生产成本均低于高、中压羰基合成技术。
1.1气相法将催化剂加入并联的两台反应器中,丙烯、合成气按一定比例分别从反应器和分馏塔底部进入。
产品由循环气带出,经冷凝、分离后,由分馏塔底部采出,过量气体循环进入反应系统,催化剂留在反应器内直至失效取出再生。
因该羰基合成反应为气相反应,故称气相法。
1.2液相法液相法是以丙烯、合成气为原料,以铑为催化剂生产丁辛醇的低压羰基合成法,是低压羰基合成的进一步改进。
其优点是:一是反应器容积小,产率高;二是原料单耗降低;三是成本及能耗降低;四是催化剂使用形式为活性循环型;五是反应温度低,可用于生产高碳醇。
以乙烯和丙烯为代表的低碳烯烃是重要的基础有机化工原料

以乙烯和丙烯为代表的低碳烯烃是重要的基础有机化工原料。
随着化学工业的发展,对低碳烯烃的需求日益增长。
目前的工业生产中,低碳烯烃的生产基本上依赖石油资源。
在世界范围内,石油资源贮量愈来愈少,通过煤或天然气为原料经由甲醇或二甲醚制取乙烯和丙烯等低碳烯烃工艺(MTO/MTP)近年来受到广泛关注。
甲醇制取低碳烯烃研究主要包括以乙烯和丙烯为主要产物的MTO技术和以丙烯为主要产物的MTP技术。
MTO工艺使用催化剂以SAPO-34分子筛为主,MTP工艺使用催化剂以ZSM-5分子筛为主,通过所使用分子筛的不同择形性能调控甲醇裂解产物中乙烯与丙烯的相对含量。
甲醇制取低碳烯烃是一强放热反应,生成低碳烯烃过程中产生大量的反应热,导致催化剂积炭失活速率加快,须使用具有催化剂连续再生的流化床反应器(如MTO工艺),或将甲醇原料部分转化为二甲醚以降低反应过程中的热效应(如MTP工艺)。
实际生产中,常用,尺等稀释剂对原料进行稀释,以降低整个反应的热效应,大量的水汽化和冷凝,增加能耗,同时降低生产效率。
在石油烃蒸汽裂解生产乙烯与炼油厂的催化裂化过程中,C4及C4以上烯烃是主要的副产物,针对目前乙烯和丙烯紧缺的现状,通过催化裂解将其转化为低碳烯烃(乙烯和丙烯)成为综合利用C4及C4以上烯烃的主要研究方向。
C4及C4以上烯烃催化裂解所用催化剂以ZSM-5分子筛为主,该过程是一较强吸热反应,为保持整个反应过程的平稳进行,常在原料中加入水蒸汽作为稀释剂或热载体。
甲醇制取低碳烯烃反应与C4及以上烯烃裂解所用催化剂均是以分子筛为主的固体酸催化剂,且二者目的产物相同,如果将这2个反应放在同一反应器中进行,则可以将甲醇裂解所释放的反应热提供给C4及以上烯烃裂解反应,从而使能量得到有效利用,避免二者单独反应时存在的热量移出与供入问题。
二者的共裂解会减轻反应系统的热负荷,对提高反应系统的稳定性和改善催化剂使用寿命有利,还可省掉或减少反应系统中水蒸汽用量。
煤制烯烃国内外研究进展综述
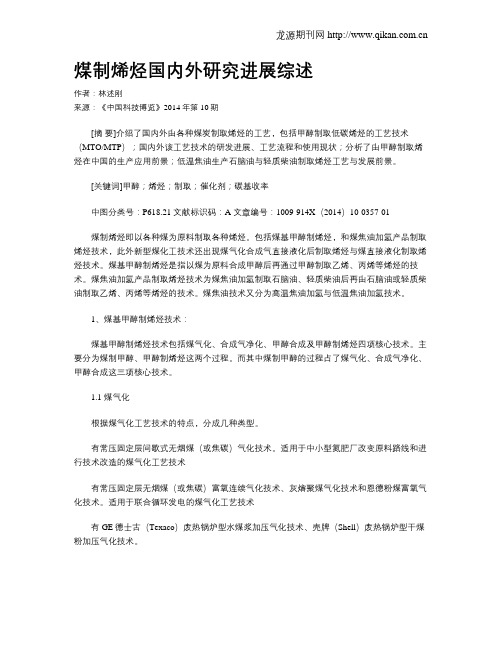
煤制烯烃国内外研究进展综述作者:林述刚来源:《中国科技博览》2014年第10期[摘要]介绍了国内外由各种煤炭制取烯烃的工艺,包括甲醇制取低碳烯烃的工艺技术(MTO/MTP);国内外该工艺技术的研发进展、工艺流程和使用现状;分析了由甲醇制取烯烃在中国的生产应用前景;低温焦油生产石脑油与轻质柴油制取烯烃工艺与发展前景。
[关键词]甲醇;烯烃;制取;催化剂;碳基收率中图分类号:P618.21 文献标识码:A 文章编号:1009-914X(2014)10-0357-01煤制烯烃即以各种煤为原料制取各种烯烃。
包括煤基甲醇制烯烃,和煤焦油加氢产品制取烯烃技术,此外新型煤化工技术还出现煤气化合成气直接液化后制取烯烃与煤直接液化制取烯烃技术。
煤基甲醇制烯烃是指以煤为原料合成甲醇后再通过甲醇制取乙烯、丙烯等烯烃的技术。
煤焦油加氢产品制取烯烃技术为煤焦油加氢制取石脑油、轻质柴油后再由石脑油或轻质柴油制取乙烯、丙烯等烯烃的技术。
煤焦油技术又分为高温焦油加氢与低温焦油加氢技术。
1、煤基甲醇制烯烃技术:煤基甲醇制烯烃技术包括煤气化、合成气净化、甲醇合成及甲醇制烯烃四项核心技术。
主要分为煤制甲醇、甲醇制烯烃这两个过程。
而其中煤制甲醇的过程占了煤气化、合成气净化、甲醇合成这三项核心技术。
1.1 煤气化根据煤气化工艺技术的特点,分成几种类型。
有常压固定层间歇式无烟煤(或焦碳)气化技术。
适用于中小型氮肥厂改变原料路线和进行技术改造的煤气化工艺技术有常压固定层无烟煤(或焦碳)富氧连续气化技术、灰熔聚煤气化技术和恩德粉煤富氧气化技术。
适用于联合循环发电的煤气化工艺技术有GE德士古(Texaco)废热锅炉型水煤浆加压气化技术、壳牌(Shell)废热锅炉型干煤粉加压气化技术。
有两段式干煤粉加压气化技术,四喷嘴对置式干粉煤加压气化技术。
国内外已有多套商业化装置在长周期正常运转,煤气化能力达投煤量1000-2000t/d,适用于大型化的煤气化工艺技术有GSP干煤粉加压气化技术。
甲醇制烯烃技术及进展
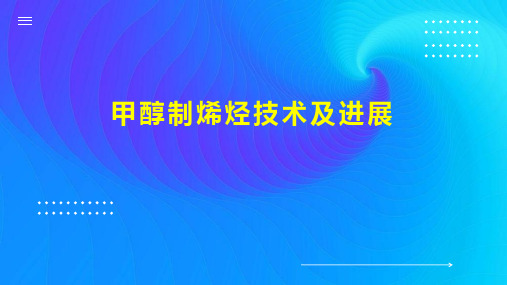
甲醇制烯烃技术概述
甲醇制烯烃技术是将甲醇通过一系列反应转化为低碳烯烃的过程。根据反应 条件和催化剂的不同,甲醇制烯烃技术主要分为两大类:直接法和间接法。直接 法是指在高温高压条件下,甲醇直接转化为烯烃;间接法则包括甲醇脱水生成二 甲醚,然后二甲醚断裂为烯烃。反应原理和主要过程如图1所示。
图1.甲醇制烯烃反应原理及主要 过程
结论
甲醇制烯烃技术作为一种高效、环保的石油替代技术,已引起了广泛和深入 研究。该技术在技术工艺、催化剂、反应条件等方面取得了显著进展,并且已在 石油替代、材料制造、医药等领域得到广泛应用。然而,甲醇制烯烃技术仍然存 在一些挑战和问题,如催化剂活性、选择性和稳定性有待进一步提高,反应条件 还需要进一步优化等。
未来,需要继续深入研究甲醇制烯烃技术,提高其效率和稳定性,降低生产 成本,以更好地满足市场需求并推动可持续发展。
谢谢观看
甲醇制烯烃技术及进展
01 引言
目录
02 甲醇制烯烃技术概述
03 图1.甲醇制烯烃反应 原理及主要过程
04 甲醇制烯烃技术进展
05 甲醇制烯烃技术应用
06 结论引言来自随着全球石油资源的日益枯竭和环境保护意识的增强,寻求替代石油的可持 续资源已成为迫切需求。甲醇制烯烃技术作为一种高效、环保的石油替代技术, 引起了广泛。本次演示将详细介绍甲醇制烯烃技术的分类、原理、进展及其在各 个领域中的应用,并探讨该技术的未来发展方向。
3、反应条件的优化
反应条件对甲醇制烯烃技术的效率和产物分布有着重要影响。近年来,研究 者们通过调控制反应温度、压力、物料流量等参数,进一步优化了反应条件。此 外,还开发了一些新型的能源回收和余热利用技术,降低了整个工艺过程的能耗。
4、产业化的前景
9煤制烯烃碳四深加工项目情况介绍——王爽

其中原料混合丁烯来自上游MTO装置副产的C4馏分,经
过MTBE单元,丁二烯加氢单元和丁烯-1单元进行原料预 处理,除去混合碳四中的异丁烯和丁二烯,副产MTBE和 丁烯-1。处理后的混合碳四经2-PH单元生产出2-PH产品。
MTBE
煤化工 混合碳 四产品
制品中禁止使用DOP;日本国内DOP 作为塑料助剂仅限
于在工业塑料制品中应用。
近年来,欧美、日韩等国纷纷出台限制甚至禁止DOP等增
塑剂的使用,从而促使以DPHP等新型的增塑剂市场的快 速增长,进一步拉动增塑剂用醇类使用量的直接增长。国 际市场上近年来2-丙基庚醇、异庚醇、十二碳醇等小品种 增塑剂醇消费需求增长率均超过10%。
技术来源
产品
方案1
Lummus的CPT(共聚
单体生产)技术
年产6.75万吨的丁烯-1,
同时副产2.66万吨的剩余 C4和0.96万吨的异丁烯产
品
方案2 术 Dow/Davy低压羰基技 年产7万吨的2-PH,同 时副产2万吨的MTBE和2
万吨的丁烯-1产品
Lummus的CPT技术
Lummus的CPT技术能够将丁烯-2异构化并转化为丁烯-1,从 混合C4产品中得到更多的丁烯-1产品。该技术已经于 2002~2004年在天津石化实现了1500吨/年的商业化运行,同时 2007年签订了一套规模为4万吨/年的丁烯-1装置的技术转让协
同时提出了由2-PH制备DPHP的方法并取得了专利权。在
之后的很长一段时间内,2-PH和DPHP并没有真正投入工
业化生产,增塑剂及相应醇长期被DOP和2-EH所垄断。
直到九十年代,伴随着增塑剂醇向更高碳数发展的潮流, 2-PH和DPHP被重新提起。
甲醇制低碳烯烃研究进展

景 。文章介绍了 甲醇制烯烃技术的 国内外研究水平 和发展趋势 。 关键词 : 甲醇 ; 低碳烯烃 ; O; T MT M P 中图分类号 :Q 2 .2 T 2311 文献标识码 : A 文章编号 :0 8- 4 1 2 1 ) 2- 0 6一 4 10 9 1 (0 2 0 00 o
景。
目 前非石油资源合成低碳主要有 3 种方法 : 1 () 甲醇法( T 、 T ) 5; 2 M O M P - ( )费一托合成法 (F — ]
T ) ;3 甲 烷 氧 化 偶 联 法 (O M) 。其 中 , () C J O M 工艺 在 甲烷 氧化偶 联制 取 乙烯 过 程 中 , 甲烷 C 当
甲醇是重 要 的有机原 料 , C 化学 工业 的基础 是 1
维 、 成橡胶 、 成塑 料 ( 乙烯 及 聚 氯 乙 烯 ) 合 成 合 合 聚 、
产品 , 然而其 自身价位较低 , 附加值不高。甲醇的深
加 工与 工业应 用是许 多 国家竞 相开 发 的一个 重 要领 域 , 甲醇工业 的发 展 在 很 大 程度 上 取 决 于 甲醇工 且
—
丙烯用量最大的是生产聚丙烯 , 另外丙烯可制 丙烯腈、 异丙醇、 苯酚和丙酮 、 丁醇和辛醇、 丙烯酸及 其脂类 以及制环氧丙烷和丙二醇 、 环氧氯丙烷 和合 成甘 油等 。 近年 来 , 由于丙烯 下游 产 品快 速 发 展 , 大 促进 极 了中 国丙 烯需 求 量 快 速增 长 I】 00年 , 国新 3。2 1 中
合成气直接制取低碳烯烃可描述为一氧化碳和 氢气在催化剂作用下 , 通过 F— T合成法制得碳原子 数小于或等于 4 烯烃的过程。通常情况下 , F— 由 T 反应所得产物碳数分布服从 Shl— o 规律 , eu f r z ly 因 而使得由合 成气直接制 取低碳烯烃 的选择受 到限 制。为了获得高选择性低碳烯烃 , 需限制碳链 的增 长 , 甲烷生成及阻止碳烯烃发生二次反应 , 抑制 并保 证所开发的催化剂具有较高催化活性 。常用方法是
对甲醇低压羰基合成醋酸工艺的几点思考
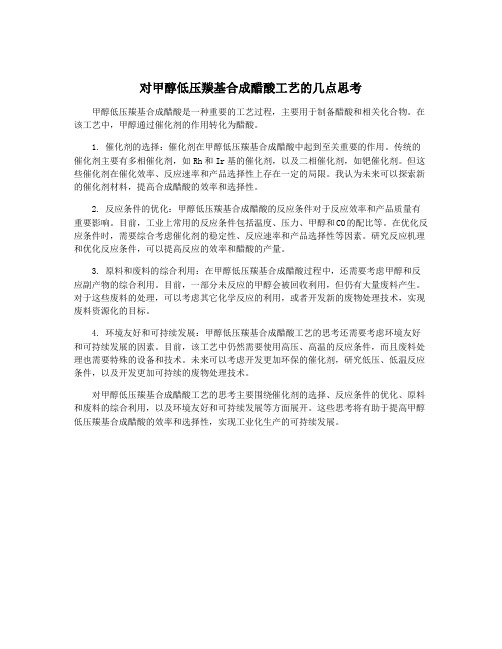
对甲醇低压羰基合成醋酸工艺的几点思考甲醇低压羰基合成醋酸是一种重要的工艺过程,主要用于制备醋酸和相关化合物。
在该工艺中,甲醇通过催化剂的作用转化为醋酸。
1. 催化剂的选择:催化剂在甲醇低压羰基合成醋酸中起到至关重要的作用。
传统的催化剂主要有多相催化剂,如Rh和Ir基的催化剂,以及二相催化剂,如钯催化剂。
但这些催化剂在催化效率、反应速率和产品选择性上存在一定的局限。
我认为未来可以探索新的催化剂材料,提高合成醋酸的效率和选择性。
2. 反应条件的优化:甲醇低压羰基合成醋酸的反应条件对于反应效率和产品质量有重要影响。
目前,工业上常用的反应条件包括温度、压力、甲醇和CO的配比等。
在优化反应条件时,需要综合考虑催化剂的稳定性、反应速率和产品选择性等因素。
研究反应机理和优化反应条件,可以提高反应的效率和醋酸的产量。
3. 原料和废料的综合利用:在甲醇低压羰基合成醋酸过程中,还需要考虑甲醇和反应副产物的综合利用。
目前,一部分未反应的甲醇会被回收利用,但仍有大量废料产生。
对于这些废料的处理,可以考虑其它化学反应的利用,或者开发新的废物处理技术,实现废料资源化的目标。
4. 环境友好和可持续发展:甲醇低压羰基合成醋酸工艺的思考还需要考虑环境友好和可持续发展的因素。
目前,该工艺中仍然需要使用高压、高温的反应条件,而且废料处理也需要特殊的设备和技术。
未来可以考虑开发更加环保的催化剂,研究低压、低温反应条件,以及开发更加可持续的废物处理技术。
对甲醇低压羰基合成醋酸工艺的思考主要围绕催化剂的选择、反应条件的优化、原料和废料的综合利用,以及环境友好和可持续发展等方面展开。
这些思考将有助于提高甲醇低压羰基合成醋酸的效率和选择性,实现工业化生产的可持续发展。
羰基化研究及在化工生产中的应用新进展

路线 。迄 今为 止 , 最重 要 的羰 基 化学 品是 正 丁 醛 , 其 次是 增 塑剂 醇用 C , , 醛 和 清 洁剂 醇用 异 丁醛 和
的烃类 化合 物 拓展 到 醇 、 酚、 环 氧化 物 、 硝 基 化合 物 、 胺 类 化合 物 、 有 机 卤化 物 等 。 除合 成醛 、 醇、 酸、
酯外 , 也可 以用 来 合成 酸 酐 、 酰胺 、 酮、 内酯 醌等 其 它一 系列 含 氧化 合物 。羰 基合 成技 术 已成 为 C 化 学 化 工 与石 油 化 工 紧 密结 合 的桥 梁 , 因具 有 “ 原 子 经济 性 ” 反应 的高 选 择性 和 对 环 境 友好 而 备 受 学 术及 工 业 界 的关 注 [ 1 - 2 , 6 1 。
产前 景 的反 应 实例进 行 了较 为详 细 的讨 论 .如 :环 氧化 合 物 经环 状 碳 酸 酯合 成 乙二 醇并 联 产 D MC, 环化 物 氢 酯基化 合 成 3 一 羟 基羧 酸 酯 , 丁烯 氢 甲酰 化合 成 戊 醛 , 异 丁烯羰 基 化 合 成特 戊 酸 ,
甲醇羰基 化 生产 醋酸 和醋 酐 , 丁二烯 羰 基化合 成 己二 酸等 。另 外 , 对 该领 域的 一些 新型催 化 剂的
低 碳 烯 烃 的羰 基 合 成 主 要 以丙 烯 合 成 丁 醛 为 代 表 。U n i o n C a r b i d e等 开 发 的 以 铑 一 苯 基 膦 ( T P P ) 为催 化剂 的工 艺 , 具有 低 温 、 低压 、 反应 速率 快 、 副 反应 少 和节 省 投资 等优 点 , 是 日前应 用最 为
低压羰基合成丁辛醇工艺技术

Ab s t r a c t:L o w— p r e s s u r e c a r b o n y l s y n t h e s i s o f o c t a n o l t e c h n o l o g y i s a v e r y i mp o r t a n t t e c h n o l o g y, i t s s y n t h e s i s o f b u t a n o l a n d o c t a n o l h a s a v e r y wi d e r a n g e o f u s e s . Ho we v e r , Ch i n a ’S t e c h n o l o g y r e s e a r c h f o r t h e s t a r t o f s o me l a t e ,b u t i n t h e c o n t i n u o u s e x p l o r a t i o n , ma d e a v e r y b i g p r o g r e s s . T h i s p a p e r f u r t h e r e x p l o r e d t h e t e c h n o l o g i c a l p r o c e s s o f l o w p r e s s u r e c a r b o n y l a t i o n o f b u t a n o l , a n d g a v e a d e t a i l e d a n a l y s i s o n t h e p r e s e n t s i t u a t i o n o fs y n t h e s i s t e c h n o l o g y o f b u t y l o c t a n o l a n d t h e p r o g r e s s o f t h e s y n t h e s i s o f b u t a n o 1 . Ke y wo r d s:l o w p r e s s u r e;c a r b o n y l; b u t a n o l; p r o c e s s t e c h n o l o g y
上海石化院合成气直接制低碳烯烃研究取得进展

报道数据,进一步提高 CO转化率至 45%以上时, 低碳烯烃选择性仍保持 80%以上。该催化剂对 反应条件的适应性强,在苛刻条件下仍然可以保 持低碳烯烃的高选择性,其转化率和选择性的跷 跷板系数极低,且在反应 500h内,反应性能稳 定。这是目前公开报道的最具竞争力的 STO工 艺结果,有望实现合成气制烯烃技术的工业应用。
近年来,中国科学院大连化学物理研究所提 出了氧化物分子筛耦合的新催化剂研发思路,实 现了 C2~C4的高选择性合成,打破了传统费托过 程的理论极限 58%,但是较低的 CO转化率会造 成大量的产物分离和循环能耗,不利于其工业推 广;副产物中,大量低碳烷烃也直接制约着该过程 的经济性。在现有的催化剂体系中,提高 CO转 化率会带来烯烃选择性的大幅下降,而如何摆脱 这种此消彼长的跷跷板效应,是亟需解决的难题。
optimization
櫵櫵櫵櫵櫵櫵櫵櫵櫵櫵櫵櫵櫵櫵櫵櫵櫵櫵櫵櫵櫵櫵櫵櫵櫵櫵櫵櫵櫵櫵櫵櫵櫵櫵櫵櫵
上海石化院合成气直接制低碳烯烃研究取得进展
一步法制低碳烯烃一直是合成气转化的研究 热点。传统研究思路是基于费托合成催化剂的改 性和优化来实现,然而,受限于其反应机理,该过 程低碳产物(C2 ~C4)的 选 择 性 低,限 制 了 其 工 业 应用。
研究表明:分子筛的拓扑结构和酸性特征直 接决定耦合催化体系中的最终产物分布。从反应 机理出发,耦合体系实质上是一种串联反应,合成 气先在氧化物表面转化生成 C1中间体甲醇,再迁 移到分子筛酸性位上进行 C—C偶联,生成烯烃产 物。然而由于氧化物催化剂上甲醇生成速率较低, 分子筛上过量的酸性位会导致烯烃进一步加氢生 成烷烃,从而导致产物中烯烃选择性的降低。团队 通过大量研究,精准控制合成了低硅的 AlPO-18 分子筛,发现其是实现高烯烃选择性的关键。此 外,这种 AEI结 构 的 分 子 筛 上 的 氢 转 移 过 程 较 弱,也是烷烃选择性大幅降低的原因。
甲烷脱氢制备低碳烯烃的研究
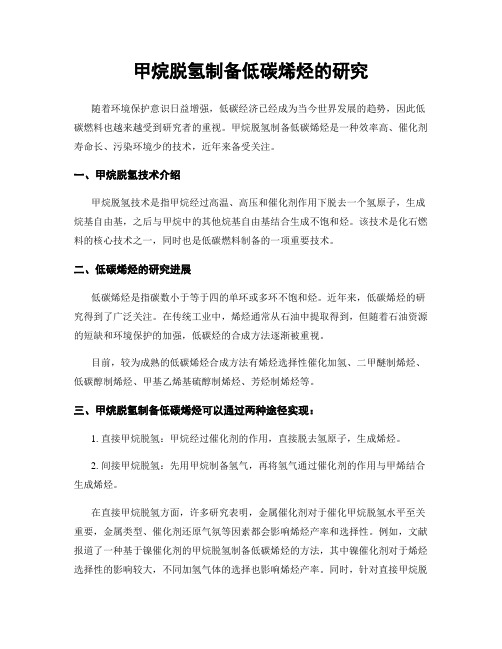
甲烷脱氢制备低碳烯烃的研究随着环境保护意识日益增强,低碳经济已经成为当今世界发展的趋势,因此低碳燃料也越来越受到研究者的重视。
甲烷脱氢制备低碳烯烃是一种效率高、催化剂寿命长、污染环境少的技术,近年来备受关注。
一、甲烷脱氢技术介绍甲烷脱氢技术是指甲烷经过高温、高压和催化剂作用下脱去一个氢原子,生成烷基自由基,之后与甲烷中的其他烷基自由基结合生成不饱和烃。
该技术是化石燃料的核心技术之一,同时也是低碳燃料制备的一项重要技术。
二、低碳烯烃的研究进展低碳烯烃是指碳数小于等于四的单环或多环不饱和烃。
近年来,低碳烯烃的研究得到了广泛关注。
在传统工业中,烯烃通常从石油中提取得到,但随着石油资源的短缺和环境保护的加强,低碳烃的合成方法逐渐被重视。
目前,较为成熟的低碳烯烃合成方法有烯烃选择性催化加氢、二甲醚制烯烃、低碳醇制烯烃、甲基乙烯基硫醇制烯烃、芳烃制烯烃等。
三、甲烷脱氢制备低碳烯烃可以通过两种途径实现:1. 直接甲烷脱氢:甲烷经过催化剂的作用,直接脱去氢原子,生成烯烃。
2. 间接甲烷脱氢:先用甲烷制备氢气,再将氢气通过催化剂的作用与甲烯结合生成烯烃。
在直接甲烷脱氢方面,许多研究表明,金属催化剂对于催化甲烷脱氢水平至关重要,金属类型、催化剂还原气氛等因素都会影响烯烃产率和选择性。
例如,文献报道了一种基于镍催化剂的甲烷脱氢制备低碳烯烃的方法,其中镍催化剂对于烯烃选择性的影响较大,不同加氢气体的选择也影响烯烃产率。
同时,针对直接甲烷脱氢产生的高氢流失问题,也有研究利用甲烷转化制氢副产物与甲烯合成低碳烯烃,达到了较高的产率。
在间接甲烷脱氢方面,催化剂也是至关重要的。
研究表明,贵金属催化剂具有很好的选择性,同时活性较高,可以在较低反应温度下增加烯烃产率。
例如,英国威廉姆斯公司研发出一种以金属双酸盐为主催化剂,利用甲烷转化制氢与甲烯合成三碳烯烃,不仅达到了较高的烯烃产率,并且催化剂可以重复使用。
总体而言,甲烷脱氢制备低碳烯烃技术产率高,催化剂寿命长,同时其所产生的废弃物少,符合低碳经济与环保理念,是未来低碳燃料的重要来源之一。
羰基合成的发展趋势

羰基合成的发展趋势
羰基合成是有机合成中一种重要的化学反应,用于构建酰基化合物。
它的发展趋势主要体现在以下几个方面:
1. 催化剂的发展:羰基合成常使用的催化剂包括酸、碱和金属催化剂等。
随着催化剂的研发和优化,对反应条件的选择范围更广,催化效率更高,催化剂的稳定性也得到了提升。
2. 反应体系的改进:为了提高合成效率和减少副反应,人们不断改进反应体系,如采用无水条件、使用溶剂的优化选择和添加助剂等措施,以提高产率和纯度。
3. 环境友好性:在羰基合成中,人们越来越注重反应的环境友好性,采用绿色合成的方法和废物处理的方法来减少对环境的污染。
4. 新的反应类型和途径:人们不断探索新的羰基合成反应类型和途径,以应对特定的合成需求。
例如,环脂化反应、噻唑化反应等新的反应类型正在得到广泛研究和应用。
5. 应用拓展:羰基合成在有机合成中的应用范围越来越广泛,涉及药物合成、天然产物合成、材料合成等领域。
人们将不断探索新的应用领域,并进一步提高合成效率和反应选择性。
低碳烯烃合成工艺技术73页PPT

1、不要轻言放弃,否则对不起自己。
2、要冒一次险!整个生命就是一场冒险。走得最远的人,常是愿意 去做,并愿意去冒险的人。“稳妥”之船,从未能从岸边走远。-戴尔.卡耐基。
梦 境
3、人生就像一杯没有加糖的咖啡,喝起来是苦涩的,回味起来却有 久久不会退去的余香。
低碳烯烃合成工艺技术 4、守业的最好办法就是不断的发展。 5、当爱不能完美,我宁愿选择无悔,不管来生多么美丽,我不愿失 去今生对你的记忆,我不求天长地久的美景,我只要生生世世的轮 回里有你。
Hale Waihona Puke 6、最大的骄傲于最大的自卑都表示心灵的最软弱无力。——斯宾诺莎 7、自知之明是最难得的知识。——西班牙 8、勇气通往天堂,怯懦通往地狱。——塞内加 9、有时候读书是一种巧妙地避开思考的方法。——赫尔普斯 10、阅读一切好书如同和过去最杰出的人谈话。——笛卡儿
低碳烯烃合成方法
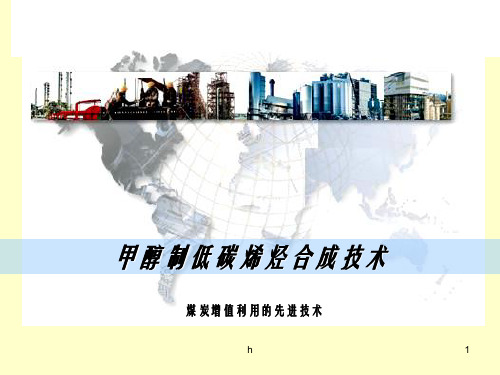
烯烃质量分数,%
乙烯 乙烯+丙烯 乙烯+丙烯+丁烯
34~46 76~79 85~90
49 >79 约87
﹡ 原料消耗:指生产每吨混h 合烯烃所消耗的原料吨数。
12
MTO合成工艺
• 甲醇转化为低碳烯烃传统工艺特点:
– 放热反应; – 催化剂因积炭致使活性很快衰退; – 通常需要采用多台固定反应器,并且反应和再
气相产物(质量分数) /%
7.47
19.17 39.92 38.45 41.41
气相中的烃 类分布 (质量 分数)
/%
CH4 C2H6 C2H4 C3H8 C3H6 C4H10 大C于4HC8 5
h
0.58 0.23 35.9 4.55 36.92 4.24 13.55 2.92
1.07 0.44 27.06 3.32 29.79 2.11 10.18 23.25
27
MTP&MTO工艺比较
项目
MTP工艺
MTO工艺
产品
丙烯,并附产LPG和汽油
乙烯和丙烯,并附产LPG、丁 烯、碳五及以上产品
反应器特征
采用固定床反应器,结构简单, 投资较低。
反应结焦少,催化剂无磨损,可 就地再生。 反应温度控制比流化床难。
采用流化床反应器,结构复杂, 投资较大。
项目
数值
原料中水含量(质 量分数)/%
0
74
84
90
温升 /℃
120 100 60 35
转化率 /%
100 100 100 100
生成油 /g
32 0.58 0.15 0.38
C2H6 18 40 45 48
气相产物 C3H6 24 25 25 25
合成气一步法制备低碳烯烃工艺技术路线

未来煤化工中煤制烯烃发展新趋势
低碳烯烃(乙稀、丙稀和丁稀,C2=~C4=)是化学工业生产中重要的基础有机化工原料,其可以用于制造高附加值的化学品,如:聚合物、塑料、化妆品、有机溶剂、洗涤剂和药品等。
低碳烯烃生产主要来源于传统的石油路线工艺,包括石脑油的蒸汽裂解工艺和催化裂化增产烯烃工艺。
非石油路线工艺包括甲醇制烯烃(MTO)、甲醇制丙烯(MTP)、丙烷脱氢、乙醇脱水制烯烃、C3/C4烷烃混合脱氢制烯烃、煤基合成气制低碳烯烃等工艺。
目前,生产低碳烯烃的工艺朝着多元化方向发展,并不断推向工业化应用,体现出较强的竞争力。
从煤基合成气出发制烯烃工艺包括的工艺有很多种,其中间接法主要有两种:一是指合成气先制成甲醇,再经甲醇制丙烯(Methanol to Propylene, MTP)或低碳烯烃(Methanol to Olefin, MTO);二是合成气先制成二甲醚,再经二甲醚制备低碳烯烃(Syngas/Dimethyl ether to Olefins, SDTO)。
直接法是指合成气一步转化制低碳烯烃(Syngas to Olefin, STO)。
其中MTO工艺己经实现工业化,是目前合成气间接法制烯烃最成熟的工艺路线。
煤基合成气直接制备低碳烯烃的工艺路线尚未工业化应用,且催化剂研究现处于实验室研发阶段。
但是,合成气通过费托合成制低碳烯烃工艺具有较好的原料供应保障和产品市场需求,且与传统蒸汽裂解和经甲醇制烯烃(MTO)工艺相比,具有原料价格优势,工艺技术路线短,并副产高附加值油品,在经济性上具有较强的竞争力,应用前景广阔。
煤基合成气一步法制备低碳烯烃烯
烃工艺路线将是今后煤化工发展的新趋势,请大家拭目以待!。
低压羰基化法

低压羰基化法
摘要:
一、低压羰基化法的概念
二、低压羰基化法的反应原理
三、低压羰基化法的应用领域
四、低压羰基化法与其他羰基化法的比较
五、低压羰基化法的发展前景与挑战
正文:
低压羰基化法是一种在低压条件下进行的羰基化反应,具有条件温和、选择性高、副反应少等优点,广泛应用于有机合成领域。
低压羰基化法的反应原理是利用金属铑、钌等催化剂,在低压条件下,将一氧化碳与有机化合物进行反应,生成羰基化合物。
在这个过程中,催化剂起到降低反应活化能、提高反应速率的作用。
低压羰基化法在有机合成领域的应用非常广泛,包括羰基化反应、羰基加成反应、羰基取代反应等。
其中,羰基化反应是最常见的应用之一,例如在酮、酯、酰胺等化合物的合成中都有应用。
此外,低压羰基化法还可以用于生物质转化、精细化工品生产等方面。
低压羰基化法与其他羰基化法相比,具有反应条件温和、选择性高、副反应少等优点。
例如,与高压羰基化法相比,低压羰基化法不需要使用高压设备,降低了生产成本和安全风险;与常压羰基化法相比,低压羰基化法具有更高的选择性,可以获得更为纯净的产物。
尽管低压羰基化法具有很多优点,但仍然面临着一些挑战和发展前景。
例如,催化剂的活性和稳定性需要进一步提高,以满足工业化生产的需求;此外,研究新型低压羰基化反应体系,拓宽应用领域,也是未来发展的一个重要方向。
总之,低压羰基化法作为一种高效、环保的有机合成方法,具有广泛的应用前景和发展潜力。
催化裂解制低碳烯烃工艺的应用前景及发展趋势
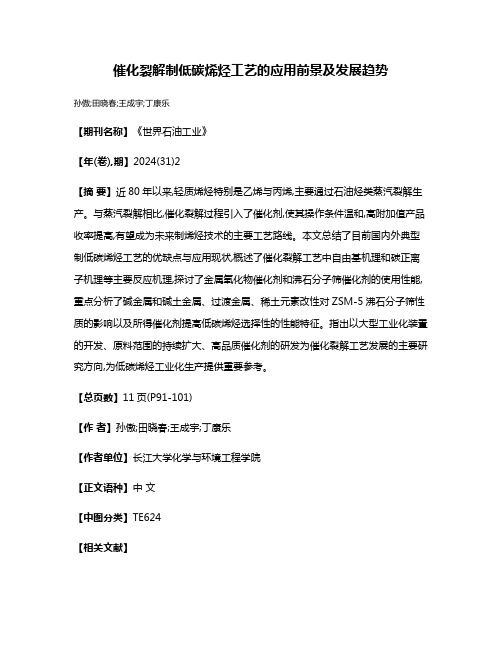
催化裂解制低碳烯烃工艺的应用前景及发展趋势
孙傲;田晓春;王成宇;丁康乐
【期刊名称】《世界石油工业》
【年(卷),期】2024(31)2
【摘要】近80年以来,轻质烯烃特别是乙烯与丙烯,主要通过石油烃类蒸汽裂解生产。
与蒸汽裂解相比,催化裂解过程引入了催化剂,使其操作条件温和,高附加值产品收率提高,有望成为未来制烯烃技术的主要工艺路线。
本文总结了目前国内外典型制低碳烯烃工艺的优缺点与应用现状,概述了催化裂解工艺中自由基机理和碳正离子机理等主要反应机理,探讨了金属氧化物催化剂和沸石分子筛催化剂的使用性能,重点分析了碱金属和碱土金属、过渡金属、稀土元素改性对ZSM-5沸石分子筛性质的影响以及所得催化剂提高低碳烯烃选择性的性能特征。
指出以大型工业化装置的开发、原料范围的持续扩大、高品质催化剂的研发为催化裂解工艺发展的主要研究方向,为低碳烯烃工业化生产提供重要参考。
【总页数】11页(P91-101)
【作者】孙傲;田晓春;王成宇;丁康乐
【作者单位】长江大学化学与环境工程学院
【正文语种】中文
【中图分类】TE624
【相关文献】
1.碳四烯烃催化裂解制低碳烯烃反应性能的研究
2.HZSM-5催化剂在烃类催化裂解制低碳烯烃中的应用研究进展
3.石油烃类催化裂解制低碳烯烃工艺条件及技术分析
4.石蜡基原油直接催化裂解制低碳烯烃新型炼化工艺的开发
5.工艺条件对轻烃原料催化裂解制低碳烯烃反应的影响
因版权原因,仅展示原文概要,查看原文内容请购买。
低压羰基合成法 丙醛

低压羰基合成法丙醛以低压羰基合成法丙醛为标题,写一篇文章。
丙醛是一种重要的化工原料,广泛应用于医药、农药等行业。
在工业上,丙醛的合成方法有多种,其中低压羰基合成法是一种常用且有效的方法。
低压羰基合成法是通过将甲醇和一氧化碳在催化剂的作用下反应生成羰基合成气体,然后将气体通过反应器进行进一步的反应,从而得到丙醛的方法。
甲醇和一氧化碳作为原料被混合进入反应器。
在反应器中,原料与催化剂发生反应,生成羰基合成气体。
催化剂的选择对于反应的效果起着至关重要的作用,常用的催化剂有氧化钯、氧化铼、氧化钯钼等。
这些催化剂能够加速反应速率,提高反应效率。
接下来,羰基合成气体进入反应器进行进一步的反应。
在反应器中,羰基合成气体经过一系列的化学反应,逐步生成丙醛。
反应过程中需要控制反应温度和压力,以保证反应能够顺利进行。
反应温度一般在150-200摄氏度之间,反应压力一般在1-5兆帕之间。
同时,反应器的设计也需要考虑到反应物的流动性和热平衡等因素,以确保反应的高效进行。
反应产物经过分离和提纯,得到纯度较高的丙醛。
分离和提纯的方法有多种,常用的包括蒸馏、结晶、萃取等。
这些方法能够有效地分离丙醛与其他杂质,提高丙醛的纯度。
低压羰基合成法具有反应条件温和、反应效率高的特点,因此在工业上得到了广泛应用。
与其他合成方法相比,低压羰基合成法具有较低的能耗和操作成本,能够大规模生产丙醛,满足市场需求。
低压羰基合成法是一种常用且有效的丙醛合成方法。
通过控制反应条件和选择合适的催化剂,能够高效地合成丙醛。
随着化工技术的不断进步,低压羰基合成法在丙醛生产中的应用前景将更加广阔。
- 1、下载文档前请自行甄别文档内容的完整性,平台不提供额外的编辑、内容补充、找答案等附加服务。
- 2、"仅部分预览"的文档,不可在线预览部分如存在完整性等问题,可反馈申请退款(可完整预览的文档不适用该条件!)。
- 3、如文档侵犯您的权益,请联系客服反馈,我们会尽快为您处理(人工客服工作时间:9:00-18:30)。
为了便于产物丁醛与催化剂的分离 , 20世纪 80 年代 , R uh rchem ie公司开发了以水溶性铑为催化剂 的两相 工 艺 , 该 工 艺 以 三 苯 基 膦 - 三 间 磺 酸 盐 ( TPPTS )为催化剂配体 。这种催化剂溶解于水相 中 ,与产物丁醛分离方便 , 催化剂回收容易 , 丁醛的 正异构比高 。由于丙烯在水中的溶解度较低 , 因此 催化剂的活性不高 , 反应速率慢 , 需要较高的操作 压力 ( 4~5 M Pa)和温度 (高于 125 ℃) 。采用水溶
D avy - D ow 工艺采用双釜串联 , 反应产物通过 高 、低压蒸发实现催化剂与产物的分离 , 将催化剂 溶液返回 反 应 釜 中 。反 应 液 中 铑 的 质 量 分 数 为 ( 2~3) ×10 - 4 , TPP的质量分数约为 12% 。两个反 应釜的工艺条件不同 , 第一反应釜的温度为 90 ℃、 压力 约 1. 8 M Pa; 第 二 反 应 釜 的 温 度 为 100 ~ 110 ℃、压力为 1. 7 M Pa。该工艺丙烯转化率较高 , 反应循环气量少 , 生产能力高 ; 催化剂的分离温度 低 ,延长了催化剂的使用寿命 ; 失活催化剂可以现 场活化 ,降低了生产成本 。产品丁醛的正异构比为 7~10。 1. 1. 2 三菱工艺
BA S F工艺采用单台塔式反应器 , 反应器液相 出料经过闪蒸 ,将未反应的丙烯和产物丁醛与催化 剂分离 ,然后丙烯和丁醛经精馏分离 , 丙烯通过压 缩机返回反应器 ,部分混和丁醛与反应器的气相出 料在汽提塔中逆向接触 , 充分回收未反应的丙烯 。 BA S F工艺的反应温度约 100 ℃, 压力约 2 M Pa, 丙 烯的转化率较高 ,产物丁醛的正异构比为 8~9。
[ Abstract] S eve ra l im p o rtan t low p ressu re oxo p rocesses fo r hyd rofo rm y la tions of p rop y lene and bu ty lenes w e re rev iew ed. The d iscuss ion conce rn ing p rop y lene p rocess focused on the w ide ly app lied p rocess w ith R h2trip heny lp hosp h ine as ca ta lys t, R uh rchem ie p rocess w ith w a te r2so lub le ca ta lyst, w h ich fea tu red in conven ience of sep a ra tion and recyc le of the ca ta lyst, and the m o re advanced D avy2D ow p rocess w ith h igh ly ac tive R h2p hosp h ite ca ta lyst. D iffe ren t low p ressu re oxo p rocesses of bu ty lenes w e re a lso d iscussed. The advan tages of the p rocesses w e re com p a red and the deve lopm en ts in recen t yea rs w e re in troduced. The deve lopm en t d irec tion of low p ressu re oxo p rocess w as sugges ted. [ Keywords] o lef in; low p ressu re oxo p rocess; rhod ium; p hosp h ite ligand; p rop y lene; bu ty lene
图 5 采用水溶性催化剂的 R uh rchem ie工艺流程 F ig. 5 F low sheet of R uh rchem ie p rocess w ith w ater2soluble catalyst.
图 4 BA SF工艺流程 Fig. 4 Flow sheet of BA SF p rocess.
·570·
石 油 化 工
PETRO CH EM ICAL TECHNOLO G Y
2009年第 38卷
工艺的是 ,反应产物先经过汽提塔回收未反应的烯 烃 ,然后再通过精馏塔来分离产物丁醛与催化剂 。 三菱工艺的反应温度为 100~120 ℃, 压力为 1. 7~ 1. 8 M Pa,催化剂活性较高 , 产物丁醛的正异构比为 8~10。但该工艺丙烯消耗定额高 ,装置的维护成本 较高 。 1. 1. 3 BA S F工艺
·568·
பைடு நூலகம்
石 油 化 工
PETRO CH EM ICAL TECHNOLO G Y
2009年第 38卷第 5期
进展与述评
低碳烯烃低压羰基合成工艺的技术进展
陈 和
(中国石油化工股份有限公司 北京化工研究院 ,北京 100013)
[摘要 ] 对近年来国内外低碳烯烃低压羰基合成醇的工艺进行了综述 。分别介绍了丙烯和丁烯的羰基合成工艺 ,其中丙烯羰基合 成工艺重点介绍了采用铑 - 三苯基膦油溶性催化剂的工艺 、R uh rchem ie 公司采用的水溶性铑催化剂的两相工艺 、D avy - D ow 公 司采用的高性能铑 - 双亚磷酸酯催化剂的新工艺 , 同时还介绍了丁烯羰基合成的几种工艺 , 分析了各工艺的技术特点及进展状 况 ,并对今后的发展方向进行了展望 。 [关键词 ] 烯烃 ; 低压羰基合成 ; 铑 ; 膦配体 ; 丙烯 ; 丁烯 [文章编号 ] 1000 - 8144 ( 2009) 05 - 0568 - 07 [中图分类号 ] TQ 224. 12 [文献标识码 ] A
烯烃的羰基合成反应 , 即氢甲酰化反应 , 是烯 烃与合成气在催化剂作用下生成比原料烯烃高一 个碳原子的醛的反应 。自 1938 年罗兰发现羰基合 成反应至今 ,该反应已经成为石化生产中重要的有 机化工工艺 , 每年生产的醛 、醇产量近 10 M t[ 1 ] , 并 被广泛应用于增塑剂 、表面活性剂 、药物中间体 、溶 剂及香料等精细化工领域 [ 2 ] 。国内羰基合成工艺 集中在以丙烯为原料生产丁醇和辛醇 , 主要用于合 成增塑剂 、丙烯酸酯和二元醇醚 。目前国内丁醇和 辛醇的总产能占世界总产能的 10%左右 。近年来 , 由于传统增塑剂产品邻苯二甲酸二辛酯 (DO P ) 具 有毒害性 ,因此国外已开发出低毒性的增塑剂 [ 3~5 ] 。
根据烯烃碳原子数的不同 , 它们的物化性能也 不相同 ,因此 , C4以下的低碳烯烃与高碳烯烃的羰 基合成工艺也有所区别 。其中丙烯的羰基合成工
艺的发展经历了高压钴法 、改性钴法和低压铑法 。 目前 ,工业上高碳烯烃的羰基合成工艺仍以高压钴 法为主 [ 6, 7 ] 。
本文主要介绍了低碳烯烃羰基合成工艺的进 展情况 。
[收稿日期 ] 2008 - 12 - 02; [修改稿日期 ] 2009 - 02 - 10。 [作者简介 ] 陈和 ( 1978—) , 男 , 江西省德兴市人 , 博士 , 工程师 , 电 话 010 - 59202578,电邮 chenhe@ b rici. ac. cn。
第 5期
陈和 1低碳烯烃低压羰基合成工艺的技术进展
三菱工艺 [ 14, 15 ]以羰基氢铑为催化剂前体 、甲苯 为溶剂 。该工艺具有反应液黏度低 、传热效果好 、 催化剂活性稳定 、金属铑的损失少等优点 。但该工 艺在回收催化剂时需结晶和离心过滤 , 同时溶剂甲 苯也需要专门的回收装置 。国内采用三菱工艺的 厂家只有北京化工四厂 。三菱工艺流程见图 3。
·569·
Johnson - M a they公司联合开发了以铑 - 三苯基膦 ( TPP)为催化剂的工艺 , 该工艺具有低温 、低压 、反 应速率快 、副反应少 、节省投资等优点 , 是目前应用 最广泛的工艺 [ 9, 10 ] 。20世纪 80年代 R uh rchem ie公 司开发了使用水溶性铑催化剂的两相工艺 [ 11 ] , 降低 了贵金属铑的损失 , 产物与催化剂易分离 , 但该催 化剂的活性较低 , 反应需要较高的温度和压力 。20 世纪 90年代 , U n ion C a rb ide公司和 D avy M ckee公 司又开发了以铑 - 双亚磷酸酯为催化剂的第四代 工艺 [ 12 ] 。该催化剂的活性高于铑 - TPP催化剂 , 烯 烃的转化率较高且不必循环 , 该工艺适用于丙烯和 丁烯的羰基合成 ,产品醛的正构体与异构体的摩尔 比 (简称正异构比 )高达 30 ∶1,反应条件更加温和 , 其投资费用也低于传统的以铑 - TPP为催化剂的工 艺 ,具有良好的发展前景 。 1. 1 以铑 - TPP为催化剂的工艺
D avy - D ow 工艺是目前应用最广泛的工艺 , 国 内中国石化齐鲁石化分公司 、中国石油吉化集团公 司及中国石油大庆石化公司均采用该工艺 。该工
图 3 三菱工艺流程 F ig. 3 F low sheet of M itsub ishi p rocess.
三菱工艺采用单反应釜 , 不同于 D avy - D ow
国内 采 用 BA SF 工 艺 的 厂 家 为 扬 子 石 化 BA S F有限责任公司 。BA S F工艺 [ 16~18 ]以醋酸铑为 催化剂前体 、丁醛与丁醛三聚物的混合物为溶剂 , 添加催化剂时需先将催化剂溶解在甲醇中 , 然后加 入到反应体系中 。BA S F工艺流程见图 4。
性催化剂的 R uh rchem ie工艺流程见图 5。