原料组成和燃耗对烧结矿强度影响的试验研究
影响烧结矿强度的因素分析及改进措施

烧结强度攻关分析一、影响烧结矿强度的因素分析1、烧结矿中FeO含量:过高直接还原增加,过低强度不好;碳高时容易还原生成FeO,形成强度很好但还原性很差的铁橄榄石和钙铁橄榄石,因此生产时既要保证有一定的还原性,又要保证机械强度。
2、烧结矿化学成份:MgO、Al2O3的影响。
3、烧结混合料混匀程度:圆筒混合机中的三种运动状态——翻动、滚动、滑动,其中滑动对混料是没有效果的,需要控制;混合后碳粒的存在形式有三种——被矿粉包裹在中心形成的颗粒、与矿粉一起包裹在核表面形成的颗粒、单独存在的颗粒,因此要防止第一、三种状态,产生第二种混合颗粒。
4、烧结矿烧结工艺参数:点火温度1150~1250℃等;5、烧结矿的碱度:根据烧结矿强度分析,碱度在1.7~1.8时强度最好,加入的生石灰起粒化促进剂的作用。
6、固相反应有利于提高烧结矿的强度质量:在高碱度烧结条件下,主要是产生铁酸钙,甚至是铁酸二钙,铁酸三钙,都有较好的强度和还原性。
7、抽入的空气温度越低,抽风速度越快,则烧结矿气孔越薄,强度也就较差。
8、原料成分和矿相的影响:软熔温度的影响,结晶水的影响,粒度比例的影响。
二、【小知识】降低烧结矿FeO 对提高烧结矿产、质量和高炉生产有什么好处?烧结矿中FeO不是单独存在的,由于燃烧层高温的作用,使很大一部分FeO 与SiO2和CaO结合生成铁橄榄石和钙铁橄榄石。
此物质较多的烧结矿呈多孔蜂状,具有一定的强度但发脆,此种物质还原性很差。
该物质生成温度高,需配碳也多,也起烧结燃烧带变宽,阻力增大,影响烧结机台时产量提高。
同时由于生成温度高,因而燃料消耗也多,据日本试验和生产的经验数据统计,烧结矿FeO 增减1%,影响固体燃料消耗增减2~5kg/t。
对高炉的影响也是很大的,根据生产统计数据和经验数据表明,FeO 波动1%,影响高炉焦比1~1.5%,影响产1~1.5%。
因此在保证烧结矿强度的情况下,应尽量降低烧结矿FeO。
现在我国重点厂烧结矿FeO在10%左右,有个别厂达到7%。
MgO对烧结过程及烧结矿性能影响的试验研究

i n v e s t i g a t i o n , a n d i t i s r e g a r d e d t h a t t h e r e a s o n a b l e Mg O c o n t e n t( W f Mg O ) )i n s i n t e r e d o r e s h a l l b e 2 . 5 %.
3 1 . 3 4 3 0 . 5 3 2 9 . 4 2 2 7. 8 7 2 8 33 2 8. 8 9 2 9 . 46
试验 用原 料理 化 性能及 配 矿 比例见 表 1 。 2 . 2 试 验 与数 据统 计 试 验 在 3 0 0 mm烧 结 杯 中进 行 ,料 层 6 0 0 m m,点 火 进 行 抽风 烧 结 ,测定 烧 成 的 烧 结矿 落 下 指数 、转 鼓 指 数 及 粒 度 组 成 ,做 化 学 成 分 分 析 ,并 测 定 低 温还 原 粉 化 率 、还 原 度 及 熔 滴 性 能等 冶金性 能 数据 。 具体 试 验方 案 见表 2 ,在 保证 原 料结 构 以及
2 l 每 镰 _ 、 荨
l ■
Mg O对烧结过程及烧结矿性能影响的试验研究
张 中中 阮志勇 罗秀传 王子宏 陈伟 兰
摘 要 :试验 研 究 Mg O 对 烧 结过 程 及 烧 结矿 性 能的 影 响程 度 ,认 为烧 结 矿 中合理 的 Mg O 含 量
( w f Mg O) )为 2 . 5 %。
M g O 含 量是 烧结 矿质 量 的 主要控 制 指标 。对 高 炉 冶 炼 而 言 ,适 量 的 Mg O可 以改 善 炉 渣 的 流 动 性 、稳 定 性 及 冶 金 性 能 ,同 时 ,炉 渣 镁 铝 比 ( m( Mg O ) / m( A 1 0 3 ) ) 对 高 炉 冶炼 过 程 、脱 s反 应 都 有 很 大 影 响 。历 年 来 ,针对 烧 结 矿 中 Mg O含 量 对 烧 结 过 程 、烧 结 矿 理 化及 冶 金 性 能 影 响 的 研 究 较 少 ,烧 结 矿 Mg O含 量 的控 制 多 以控 制 矿 石 A 1 : 0 含 量 及 炉渣 镁 铝 比为 主 。因此 ,柳钢 于
烧结矿的矿物组成和显微结构对其质量的影响

烧结矿的矿物组成和显微结构对其质量的影响这里所说烧结矿的质量,主要指其机械强度和还原性而言。
烧结矿的机械强度和还原性与组成烧结矿的矿物性质、含量、晶粒大小及其相互之间的分布情况有着直接的关系。
一、烧结矿中不同矿物组成和显微结构对其强度的影响1.烧结矿个各种矿物自身强度对烧结矿强度的影响烧结矿中的磁铁矿、赤铁矿、铁酸一钙、铁橄榄石有较高的抗压强度,其次则为钙铁橄榄石及铁酸二钙,在钙铁橄榄石中,当x小于等于1.0时,钙铁橄榄石的抗压性、耐磨性及脆性的指标均与前一类接近或超过,当x=1.5时,钙铁橄榄石强度相当低,而且易产生裂纹,它的晶格常数接近于2Cao·SiO 2。
其中玻璃质具有最低的强度。
因此在烧结矿的结构中应尽量减少玻璃质的形成,这对提高烧结矿强度是非常有利2.冷却结晶过程中产生的内应力对烧结矿强度的影响矿物组成对烧结矿强度的影响不仅仅局限于烧结矿中分离出来的结晶个体和玻璃质的强度作用,在很多情况下它还取决于烧结矿的矿物组成以及它在冷却时产生的内应力。
烧结矿在冷却过程中,产生不同的内应力:(1)由于烧结矿块表面与中心存在温差而产生的热应力。
这种热应力主要取决于冷却条件,可用缓慢冷却或热处理的方法来消除。
(2)烧结矿中各种矿物相具有不同热膨胀系数,因而引起各矿物相之间的应力。
研究防止这种矿物相之间的应力的产生,对提高熔剂性烧结矿的强度具有重要的意义。
(3)硅酸二钙在冷却过程中的多晶转变所引起的相变应力。
通常在烧结矿中主要出现β—C2S和γ—C2S。
当β—C2S在自然冷却转变为γ—C2S时,由于体积膨胀产生根大应力,这是导致高硅磁铁矿精矿烧结熔剂性烧结矿在自然冷却时产生自动粉化的根本原因。
例如,使用迁安高硅磁铁矿精矿(TFe60—62%,SiO2 10—12%)生产碱度为1.15的烧结矿,由于在其中生成少量的C2S ,当此烧结矿在冷却到300度以后时,发生由β—C2S向γ—C2S的相转变,因而导致烧结矿在冷却时产生严重的碎裂和粉化。
矿物组成、结构及其对烧结矿质量的影响
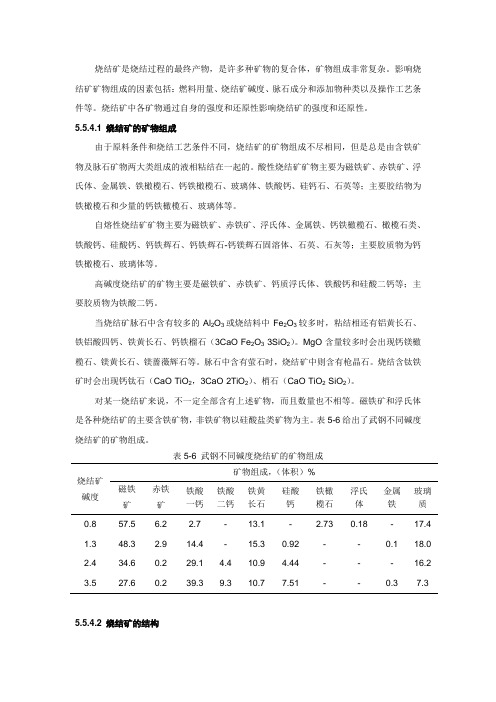
烧结矿是烧结过程的最终产物,是许多种矿物的复合体,矿物组成非常复杂。
影响烧结矿矿物组成的因素包括:燃料用量、烧结矿碱度、脉石成分和添加物种类以及操作工艺条件等。
烧结矿中各矿物通过自身的强度和还原性影响烧结矿的强度和还原性。
5.5.4.1 烧结矿的矿物组成由于原料条件和烧结工艺条件不同,烧结矿的矿物组成不尽相同,但是总是由含铁矿物及脉石矿物两大类组成的液相粘结在一起的。
酸性烧结矿矿物主要为磁铁矿、赤铁矿、浮氏体、金属铁、铁橄榄石、钙铁橄榄石、玻璃体、铁酸钙、硅钙石、石英等;主要胶结物为铁橄榄石和少量的钙铁橄榄石、玻璃体等。
自熔性烧结矿矿物主要为磁铁矿、赤铁矿、浮氏体、金属铁、钙铁橄榄石、橄榄石类、铁酸钙、硅酸钙、钙铁辉石、钙铁辉石-钙镁辉石固溶体、石英、石灰等;主要胶质物为钙铁橄榄石、玻璃体等。
高碱度烧结矿的矿物主要是磁铁矿、赤铁矿、钙质浮氏体、铁酸钙和硅酸二钙等;主要胶质物为铁酸二钙。
当烧结矿脉石中含有较多的Al2O3或烧结料中Fe2O3较多时,粘结相还有铝黄长石、铁铝酸四钙、铁黄长石、钙铁榴石(3CaO·Fe2O3·3SiO2)。
MgO含量较多时会出现钙镁橄榄石、镁黄长石、镁蔷薇辉石等。
脉石中含有萤石时,烧结矿中则含有枪晶石。
烧结含钛铁矿时会出现钙钛石(CaO·TiO2,3CaO·2TiO2)、梢石(CaO·TiO2·SiO2)。
对某一烧结矿来说,不一定全部含有上述矿物,而且数量也不相等。
磁铁矿和浮氏体是各种烧结矿的主要含铁矿物,非铁矿物以硅酸盐类矿物为主。
表5-6给出了武钢不同碱度烧结矿的矿物组成。
表5-6 武钢不同碱度烧结矿的矿物组成烧结矿碱度矿物组成,(体积)%磁铁矿赤铁矿铁酸一钙铁酸二钙铁黄长石硅酸钙铁橄榄石浮氏体金属铁玻璃质0.8 57.5 6.2 2.7 - 13.1 - 2.73 0.18 - 17.41.3 48.32.9 14.4 - 15.3 0.92 - - 0.1 18.02.4 34.6 0.2 29.1 4.4 10.9 4.44 - - - 16.23.5 27.6 0.2 39.3 9.3 10.7 7.51 - - 0.3 7.3 5.5.4.2 烧结矿的结构烧结矿的结构包括宏观结构和显微结构。
燃料配加工艺对烧结矿成分及性能的影响

摘
要: 采用现场工业试验 的方法 , 探索 了不 同的燃 料配) r 艺对烧结矿 中 F O S Ja u e 、 及残 C 沿料层厚度 方向的分布规律与变
化趋势 , 以及对烧结矿低 温冶金性能 的影 响。结果表 明 , 在燃料全 部外加的新工 艺条件下 , 结矿中 F O S 残碳沿料层 烧 e 、及 厚 度方 向的分布趋 于更加均 匀 , 其标 准偏差分 别为 0 9 0 0 %和 0 0 %, 差分别 为0 9 O 0 %和0 0 %; D . %、. 3 3 0 .3 极 0 . %、 . 9 9 0 .4 R L 0 (4 0 、17 . %) 7 . %)R (8 0 明显改 善。分析认为 , 9 9 主要是新工艺 的燃 料配加方式使烧 结料层 的热量分 布趋于合理 , 各处 透气性 更加均匀 , 对烧结 生产产 生有 利影响。 关键词 : 燃料配/ r 艺 ; J u a 烧结 矿 ; 均匀性 ; 成分 低温冶金性能
中图分 类号 :F 4 . T 0 64 文献标识码 : A 文章编号 :0 4 4 2 (0 10 — 0 7 0 10 — 6 0 2 1 )3 0 2 — 3
1 前
言
置样 品 中残 碳 的平 均 值 ( 、 准 偏 差 ( 与 极 差 )标 ) ( 等 特征值 , ) 分析焙 烧过程 的 内在 特征 。
烧结矿某些化学成分的稳定性及分布规律 , 一
方面 是重 要 的理 化指 标 , 另一 方 面也 直接 反应 焙烧
3 燃料 配加工 艺对烧结 矿 的影 响
3 1 对 F O含量 的影 响 . e 在 不 同的燃 料配 加 方式 工艺 条 件下 , 照试 验 按
影响烧结矿强度的因素分析及其改善举措

影响烧结矿强度的因素分析及其改善举措许满兴罗玉强(北京科技大学山西建邦集团有限公司)摘要本文论述了烧结矿强度的重要价值、影响烧结矿强度的因素分析及提高烧结矿强度的技术举措关键词烧结矿强度影响因素技术举措1.前言烧结矿强度是烧结矿质量的重要指标之一,由于烧结矿强度(包括低温还原强度)是影响高炉上部顺行的限制性环节,故烧结矿强度是高炉炼铁对烧结矿质量的一项重要要求。
且不同容积级别的高炉对烧结矿强度的要求不同,高炉有效容积越大,对烧结矿的强度指标要求越高。
众所周知,烧结过程是一个及其复杂的物理化学变化过程,影响烧结矿强度的因素是多方面的,有矿种及烧结基础特性的影响、矿粉粒度组成和表面形态的影响、碱度及化学成分的因素,燃料和熔剂质量及粒度的影响、返矿粒度及数量的影响、料层厚度、配C配水、混合料透气性等烧结主要工艺参数的影响、矿物组成对强度的影响等等。
正因为影响烧结矿强度的因素有如此之多,要改善和提高烧结矿强度的技术措施也必然是多方面的、全方位的。
2.影响烧结矿强度的因素分析2.1 矿种及铁矿粉基础特性对烧结矿强度的影响用于烧结生产的铁矿石的种类主要有磁铁矿、赤铁矿、褐铁矿和菱铁矿四种,四种不同铁矿粉用于烧结生产,其成品矿的强度是不同的。
褐铁矿矿粉组织疏松、堆密度小,用于烧结生产成品率低、强度差;菱铁矿在烧结生产中CO2被分解析出,体积收缩大,也是成品率低、强度差;磁铁矿粉分子式为Fe3O4,在烧结过程中需要氧化气氛,氧化为Fe2O3+FeO,比不上赤铁矿粉可以在一定化学成分和温度条件下生成铁酸钙(CaO·Fe2O3)。
不同矿种烧结成品矿强度的高低排序为:赤铁矿>磁铁矿>褐铁矿>菱铁矿。
即便同样是赤铁矿由于Fe2O 3含量不同,在烧结过程中生成SFCA的机率不同,也会导致成品矿的强度不同。
巴西和南非的粉矿的Fe2O3含量均>85%,且有一定含量的SiO2,易与配入熔剂中的CaO反应生成铁酸钙,特别是南非的1~0.25mm的准颗粒比例低,制粒后混合料的透气性好,有利于成品矿的强度提高;而同为赤铁矿印度矿粉的Fe2O3含量比巴西和南非的低10%左右,在烧结过程中形成铁酸钙的机率低,因此印度粉不大可能烧出很好的烧结矿。
烧结矿能耗研究

烧结矿能耗研究烧结矿是一种重要的铁矿石,在钢铁工业中占有重要地位。
然而,在烧结矿生产过程中,能源消耗一直是一个不可忽视的问题。
因此,研究烧结矿的能源消耗,对于提高钢铁工业的生产效率和降低生产成本具有非常重要的意义。
烧结矿的生产过程主要有三个环节:前处理、配料和烧结。
在前处理环节中,矿石经过破碎、筛分、洗涤等工序,将大块矿石变成小块,使其更易于加工和烧结。
在配料环节中,矿石、焦炭、石灰石等原料按一定比例混合,然后进入烧结机进行烧结。
在烧结环节中,原料在高温条件下烧结成烧结矿,用于钢铁制造。
能源消耗在烧结矿的生产过程中占据重要地位。
因此,降低能源消耗是提高烧结矿生产效率和降低成本的有效途径。
能源消耗的主要途径是烧结机烧结过程中的自身热损失和散热。
解决这个问题的方法是采用多种节能措施。
首先,降低烧结机的热损失是重点。
一个常见的方法是通过在烧结机的烟气排出系统中安装余热回收装置来回收烟气中的热能。
这种方法可以在热能不被利用的情况下回收烟气中的热能,并在之后的生产过程中重复利用它。
此外,采用隔热材料对烧结机进行隔热,可以减少热传递和损失。
其次,通过优化烧结机的操作和管理来实现节能。
这主要是通过改善空气的供给和调节烧结机的温度、风压等参数,使烧结过程达到最佳效果,同时减少能量消耗。
对于生产工艺的设计和控制技术,进行优化,是进一步实现能源节约和环保的关键。
总之,研究烧结矿的能耗是一个非常重要的课题。
钢铁工业的发展需要降低烧结矿的生产成本和提高生产效率,而能耗的降低是实现这些目标的必要条件。
通过“节能降耗”的措施,可以实现减少能耗、提高效率的目标。
在探索更细致、更高效的节能措施的同时,也应该发挥好国家政策的引导作用,推动整个行业向着能耗低、效率高、环保、可持续发展的方向走。
探究水泥生料成分及烧成热耗分析

探究水泥生料成分及烧成热耗分析摘要水泥配料工艺方案一般从原材料、燃料化学成分、熟料热耗选择等方面分析,石灰质原料、黏土质原料、硅质原料,生料配料中常掺入少量铁质原料,以补充所需的氧化铁成分。
我国回转窑、分解炉普遍采用煤粉作为燃料,燃料的充分的燃烧决定着水泥熟料的质量、强度等级,所以配料中需要考虑煤灰掺入量和成分以及热效率。
即原材料越好烧出的熟料就越好,并且还可降低矿山资源和煤炭能源的消耗,把水泥行业建设成“环境材料型”产业,走可持续发展道路。
关键词:强度、安定性、施工、热效率一、原、燃料化学成分分析(一)原料化学成分分析1.石灰石原料的优劣是决定水泥产品质量好坏的关键因素,并且预分解窑系统对原(燃)料中的有害成分(碱、氯离子等)很敏感,所以生料的化学组分非常重要,生产中使用最主要的石灰质原料是石灰石,石灰石主要提供CaO,有利于形成硅酸盐矿物,对水泥强度起主导作用。
当高品位石灰石的CaO含量越高,则煅烧的难度就越高,容易造成反应不完全,导致 f-Cao含量的增加,从而影响水泥的安定性。
低品位石灰石CaO含量过低,则MgO、R2O等有害成分高,碱含量较高,对配料和煅烧都会造成影响,MgO会影响水泥的安定性,因此可以通过提高煤粉细度或提高生料均化程度的新型干法水泥生产线来控制碱含量。
若所用的石灰石原料品质好可以搭配低品位石灰石使用提高矿山的利用率,获得更多的经济效益2.砂岩和页岩黏土质原料主要选用砂岩和页岩,可以提供SiO2,其次是Al2O3,在高温下与CaO形成硅酸盐矿物,影响水泥的强度,当CaO含量一定时,SiO2含量高,易生成较多的未饱和C2S,则C3S的含量会减少,水泥的凝结速度变慢,同时SiO2含量高,则Al2O3、Fe2O3含量减少,熔剂性矿物减少,也不利于C3S的形成,水泥的早期强度会降低。
若SiO2含量低,熟料中的硅酸盐矿物就少,其含量不足会导致水泥强度低,过多的熔剂性矿物会造成液相量大,容易结大块,影响窑操作。
烧结厂降低固体燃耗的研究与实践

烧结厂降低固体燃耗的研究与实践
烧结厂是钢铁生产过程中不可或缺的重要环节,但同时也是一个能源消耗量较大的环节。
其中固体燃料是烧结过程中能源消耗的主要来源。
因此,降低固体燃料的消耗量,是烧结厂节能减排的重要措施。
以下是烧结厂降低固体燃耗的研究与实践:
1.提高烧结热效率。
对于烧结工艺中的热能损失,可以通过提高烧结热效率来减少固体燃耗。
其中一种有效的方法是采用先进的热交换技术,将热能回收用于制热或发电。
2.优化烧结原料。
烧结原料中的品位高低、组成结构等因素都会影响其热值,因此在烧结原料的选择和配比方面,可以优化烧结原料的组成和品位,从而减少固体燃料的消耗量。
3.制定科学的烧结参数。
在烧结过程中,通过调节烧结参数来控制烧结过程中的不同阶段,可以减少固体燃料的消耗。
例如,在烧结的初期阶段,通过增加还原气体的流量,可以提高还原反应的速率和效率,从而减少固体燃料的消耗。
4.加强热工装备的维护和改造。
在烧结厂的热工装备中,存在一定的能源浪费或能源利用不充分的情况。
例如,在热风炉的运行中,热能的回收利用率不高,通过加强热工装备的维护和改造,可以提高热能的利用率,从而减少固体燃料的消耗。
综上所述,烧结厂的固体燃料消耗问题,需要采取多方面的措施来解决。
随着技术的进步和工艺的不断完善,相信在未来,烧结厂的能耗将实现更加高效、节能和环保的目标。
烧结矿矿物组成对其强度的影响

烧结矿矿物组成对其强度的影响1.烧结矿的显微结构介绍烧结矿中矿物组成主要有赤铁矿、磁铁矿、铁酸钙、硅酸钙和少量的非晶态的玻璃相。
烧结矿中的矿物组成及其相互间的结构特征,对烧结矿的机械强度有直接的影响。
所以研究烧结矿的质量应与其内部的矿物组成与显微结构特征联系起来。
烧结矿中常见的显微结构:(1)粒状结构:烧结矿中先结晶出的自形晶、半自形晶或其他形晶的磁铁矿,与粘结性矿物晶粒相互组成粒状结构。
(2)斑状结构:烧结矿中自形晶程度较强的磁铁矿斑状晶体与较细的粘结相矿物结合成斑状结构。
(3)骸晶结构:烧结矿中早期结晶的磁铁矿呈骨架状的自形晶中,常有粘结性的矿物填充其内,仍大致保持磁铁矿原来的结晶外形和边缘部分,形成骸晶结构。
(4)共晶结构:在烧结矿中磁铁矿呈圆点状在橄榄石的晶体内,或赤铁矿呈圆点状晶体分布在硅酸盐晶体中。
(5)熔蚀结构:在烧结矿中磁铁矿多为熔蚀残余他形晶,晶粒较小,多为浑圆形状,与铁酸钙形成熔蚀结构。
此种类型在高碱度烧结矿中常见,也是高碱度烧结矿的结构特点。
通过对烧结矿矿物组成和显微结构特征的研究,可以得知烧结矿中出现哪些矿物对提高其质量有利,出现哪些矿物不利。
2.烧结矿矿物组成对其强度的影响烧结矿各种矿物自身的强度对烧结矿强度的影响:烧结矿中的磁铁矿、赤铁矿、铁酸一钙、铁橄榄石有较高强度,其次为钙铁橄榄石及铁酸二钙,玻璃质具有最低的强度。
因此烧结矿的结构中应尽量减少玻璃质的形成,这对提高烧结矿的强度非常有利。
烧结矿中矿物组分对烧结矿强度的影响:(1)非自溶性烧结矿:其显微结构为斑状或共晶结构。
其中大量的磁铁矿斑晶被铁橄榄石和少量玻璃相所胶结,它的主要胶结物铁橄榄石机械强度较大,胶结磁铁矿能力较强,因而具有良好的强度。
(2)自熔性烧结矿:它的显微结构为斑晶或斑晶玻璃状结构。
其中的磁铁矿斑晶或晶粒被玻璃质和钙铁橄榄石所胶结,并且后二者含量居多,强度较差。
(3)高碱度烧结矿:其显微结构为溶蚀或共晶结构,由铁酸钙和磁铁矿构成。
烧结矿强度和粒级组成影响因素分析

烧结矿强度和粒级组成影响因素分析2008年全国炼铁技术交流会论文集烧结矿强度和粒级组成影响因素分析刘福泉王树立顾爱军(宣钢炼铁厂)摘要:本文结合宣钢炼铁厂及相关单位的研究成果,综合分析了影响烧结矿强度和粒度组成的因素和对策。
关键词:烧结矿强度粒度组成1 前言烧结矿强度及粒级组成是烧结矿质量的重要内容,没有合格的强度和适宜的粒级组成,就很难谈得上烧结矿的质量,烧结矿强度及粒级组成对高炉冶炼有着明显的影响,根据日本、前苏联、首钢、本钢的生产统计,烧结矿-5mm粒级每增加1%,将影响高炉焦比0.5%,影响高炉产量0.5-1.0%。
根据一些专家研究成果表明,烧结矿强度及粒级组成的影响因素是多方面的和复杂的,既有碱度和矿物组成,SiO、MgO和AlO等化学成分方面的影响,又有配碳量和FeO含量,热返矿粒度和返223矿量、熔剂和燃料粒度、配矿及反应性的影响,还有料层厚度、抽风负压和冷却速度等工艺操作参数方面的影响。
2 宣钢炼铁厂烧结矿强度及粒级组成与同类型企业比较表1烧结矿粒级组成 %碱度 2厂家烧结机面积m FeO% 强度% 倍 +40 40-25 25-16 16-10 10-5 -5 柳钢 50 1.70 6.03 20.85 27.51 39.41 12.21 69.5湘钢 50 2.0 6.70 4.46 14.24 17.96 28.63 28.56 6.07三明24×5 8.5 10.72 15.19 4 8.17 22.47 3.45 67.61唐钢60×3 5.6 20.3 56.30 13.70 4.1 78.30济钢36×2 8.03 24.62 52.53 10.34 4.66 85.81 太钢一烧 90 9.54 27.69 28.92 18.61 13.01 12.51 4.06 69.87 太钢二烧 90 9.39 22.50 18.81 11.64 14.47 25.00 9.33 73.058台累 1.90 7.48 13.59 21.78 23.09 17.63 17.68 5.21 77.08 武钢烧结厂入炉粒级 8.69 12.65 50.42 25.81 2.43 首钢二烧 78 1.91 9.12 13.36 21.70 38.23 23.29 3.42 87.37 宣钢一烧86×2 2.30 9.32 7.98 17.95 28.51 28.68 13.13 3.75 78.60 宣钢二烧64×2 2.30 9.28 6.53 15.97 27.15 30.93 15.87 3.55 78.20 宣钢三烧36×4 2.30 7.47 20.71 25.52 22.56 16.81 6.93 80.6 宣钢四烧36×2 24.09 33.22 20.81 12.48 6.85 2.54 81.2说明由于各烧结厂家测定烧结矿强度、粒级的地点、采样方法不统一,数据可比性不强。
炼铁原料对烧结矿的影响

本科毕业论文(设计)炼铁原料对烧结矿的影响作者姓名:殷彤指导教师:**学院名称:东北大学专业名称:冶金工程2014年3月23日毕业设计(论文)任务书摘要随着钢铁工业的发展,天然含铁富矿从产量和质量上都不能满足高炉冶炼的要求,而大量含铁贫矿和多金属共生矿经选矿获得含铁量高的铁精矿粉以及天然含铁富矿粉都不能直接入炉冶炼。
为了解决这一矛盾,人们通过人工方法,将这些矿粉制成块状的人造富矿,共高炉使用。
这样既解决了天然富矿的不足,开辟和利用了铁矿资源,又通过改善人造富矿的冶金性能,为进一步发展钢铁工业开创了新的优质原料的途径。
但是由于钢铁市场的没落,炼铁原料的低成本成为了钢铁企业继续发展的基础。
本文介绍了炼铁厂在原燃料烧结生产中采取的有效措施,如铁矿物的选矿,混匀料的处理、烧结矿生产、焦炭要求以及烧结生产的自动化配置。
通过这些工作的开展,为炼铁生产提供良好的原料条件,实现烧结、高炉稳定高效生产并实现降本增效。
关键词:原燃料处理,厚料层烧结,自动化控制,烧结矿,焦炭目录毕业设计(论文)任务书 (1)摘要 (2)绪论 (5)一、铁矿物的选矿及要求 (6)(一)选矿的目的和意义 (6)(二)选矿前的准备作业 (6)1、矿石的破碎 (6)2、矿石的筛分 (6)3、细磨与分级 (6)(三)选矿方法 (6)1、重力选矿法 (6)2、磁力选矿法 (6)3、浮游选矿法 (6)(四)含铁原料的分类 (7)1、磁铁矿 (7)2、赤铁矿 (7)3、褐铁矿 (7)4、菱铁矿 (8)(五)烧结生产对含铁原料的要求 (8)(六)铁矿粉的技术经济评估 (9)二、烧结矿形成过程 (9)(一)烧结矿层 (10)(二)燃烧层 (10)(三)预热层 (10)(四)干燥层 (10)(五)过湿层 (10)三、实现稳产优质的措施 (11)(一)做好含铁原料的配比优化及预知预控 (11)(二)保证固体燃料的化学性能及粒度 (11)1、燃料的化学成分 (11)2、燃料的粒度 (11)(三)加强配料操作,提高稳定性 (12)(四)改善烧结料层的透气性 (13)1、加强烧结料准备 (13)2、增加通过烧结料层的有效风量 (13)(五)强化混合操作,稳定水分 (14)(六)执行厚料层烧结 (15)(七)烧结终点的判断与控制 (15)(八)完善烧结过程的自动化控制 (16)1、配料的控制 (17)2、混合料湿度的控制 (17)3、矿槽料位的自动控制 (17)4、布料厚度的控制 (17)四、严格控制各技术指标 (17)结束语 (18)参考文献 (18)绪论2014年,钢铁业继续在寒冬中煎熬,在产能过剩、价格下滑的现状下,钢铁冶炼的目光只好转向了“经济料”冶炼上,烧结机作为钢铁热线头道工序中的重要工艺,担当了重要的职责。
烧结矿能耗研究

烧结矿能耗研究报告1. 研究目标本研究的目标是深入研究烧结矿的能耗情况,通过对烧结矿生产过程中的能源消耗和能耗特征进行分析,找出有效降低烧结矿能耗的方法和措施,以提高能源利用效率和环境效益。
2. 方法为达到上述目标,我们采用以下方法进行研究:2.1 数据收集收集烧结矿生产过程中的能源消耗数据,包括用于原料预处理、烧结矿烧结和冷却、烧结废气处理等各个环节的能源消耗情况。
2.2 能耗分析对数据进行统计和分析,计算各个环节的能耗占比,找出能耗高峰期和低谷期。
2.3 影响因素分析分析烧结矿能耗的影响因素,包括原料成分、烧结设备状态、燃烧条件等。
通过相关性分析和回归分析,确定各个因素对能耗的贡献度。
2.4 能耗优化方案制定基于能耗分析和影响因素分析的结果,制定能耗优化方案。
包括优化工艺流程、改进设备能效、调整原料配比等措施。
2.5 方案实施与效果评估根据制定的优化方案,进行实施并监测效果。
通过对比优化前后的能耗情况,评估优化效果。
3. 发现根据研究结果,我们得出以下发现:1.烧结矿生产过程中,能耗占比最高的环节是烧结矿烧结和冷却,约占总能耗的60%。
2.烧结矿能耗呈现出明显的季节性变化,冬季能耗明显高于夏季,可能与环境温度和供暖设备使用有关。
3.烧结矿的原料成分对能耗有明显影响,特别是矿石含铁量和灰分含量。
提高矿石质量和控制灰分含量是降低能耗的关键点。
4.燃烧条件的优化可以有效降低烧结矿能耗。
通过调整燃烧参数和改进燃烧设备,可以提高燃烧效率和节能效果。
5.优化烧结废气处理设备和工艺,可以减少能耗,并同时降低对环境的影响。
4. 结论基于上述发现,我们得出以下结论:1.烧结矿能耗的降低是可行的,通过优化烧结工艺和设备,可以有效提高能源利用效率和节能效果。
2.烧结矿的原料质量和成分控制是降低能耗的关键点,应重视原料选择和控制。
3.燃烧条件的优化可以显著降低能耗,需要加强燃烧技术研究和设备改进。
4.烧结废气处理设备和工艺的改进不仅可以减少能耗,还可以降低环境污染。
烧结矿质量的影响及分析

烧结矿质量的影响及分析⼯艺参数对烧结矿质量的影响及分析张爽⾸钢矿业公司烧结⼚摘要⾼炉炼铁所使⽤的主要含铁原料是烧结矿,近⼏年,我国⽣铁产量不断上升,烧结矿⽤量⼤幅增加。
烧结⽣产是⼀个复杂的物理化学过程,这就决定了烧结过程具有⼯艺参数变化⼤,影响烧结矿质量的因素多,各参数和变量之间的关系极其复杂的特性。
因此,难以⽤数学模型的⽅法来达到优化控制的⽬的,只能借助⼈⼯智能和专家系统来实现对烧结过程的优化控制。
提⾼烧结矿的质量、降低消耗、节约能源、保护环境在烧结⽣产中显得越来越重要,也是烧结⽣产⼯艺技术发展的永恒课题和⽅向。
本⽂介绍了烧结⼯业的发展概况及⾸钢360平⼤型烧结机的建设背景,详细阐述了烧结的定义和烧结⼯艺概况,论述了正确认识烧结⼯艺参数对搞好烧结⽣产的意义,介绍了烧结⼯艺参数及其相互关系和烧结主要⼯艺参数对其烧结矿质量的影响,提出了对烧结⼯艺参数认识的⼏点结论性意见以及改进⼯艺流程,优化烧结矿质量的措施。
关键词烧结⼯艺参数相互关系烧结矿质量1前⾔解放前我国钢铁⼯业⼗分落后,到1937年底,共有⼗台烧结机,⾯积为33平⽅⽶,年产烧结矿仅⼗⼏万吨。
解放后,我国钢铁⼯业有了很⼤的发展,⼀⼤批钢铁企业建⽴了现代化的原料⼚,进⼝矿粉的使⽤改善了烧结⽤料,使含铁原料得到了优化,所⽣产的烧结矿不但产量⾼、质量好,环保也有所改善,⼯序能耗也低。
⽬前我国⼴泛采⽤的是带式烧结机,因为它具有⽣产效率⾼,原料适应性强,⾃动化程度⾼,劳动条件好和便于⼤型化、⾃动化,所以世界上有90%的烧结矿是这种⽅法⽣产的。
烧结机⼤型化已普遍受到认同,新上烧结机普遍⼤型化。
1.1本⽂研究的⽬的及意义烧结⽣产是⼀个复杂的物理化学过程,这就决定了烧结过程具有⼯艺参数变化⼤,影响烧结矿质量的因素多,各参数和变量之间的关系极其复杂的特性。
因此,造成采⽤传统定量⽅法的数学模型的应⽤受到了⼀定的限制,难以⽤数学模型的⽅法来达到优化控制的⽬的,只能借助⼈⼯智能和专家系统来实现对烧结过程的优化控制。
烧结固体燃料粒度对烧结矿质量的影响

烧结固体燃料粒度对烧结矿质量的影响摘要:本钢烧结矿生产的原燃料结构条件下固体燃料粒度对烧结矿产质量的影响,通过改变固体燃料粒度中<1 mm的比例进行烧结杯试验。
结果表明,随着固体燃料粒度中<1 mm比例的降低,垂直烧结速度加快,烧结矿成品率、利用系数、转鼓强度、平均粒径等指标明显改善,对降低固体燃料、烧结内返粉和高炉槽下返粉将起到重要作用。
生产中应稳定四辊操作,适当放宽输出粒度范围。
关键词:烧结;固体燃料;粒度铁矿石烧结过程是一个氧化还原兼有的复杂过程,固体燃料的燃烧在这个过程中提供了主要的反应动力,了解燃料的反应过程,就成为解决烧结中一系列问题的关键。
大量研究表明,燃料的配加量、粒度组成和燃烧性质直接影响烧结料层的温度与热量分布,燃烧带的厚度以及料层的透气性,烧结气氛等各个方面,当燃料的种类、配加量固定时,燃料粒度的大小就成为烧结过程的决定性因素。
一、慨述烧结过程中,固体碳的燃烧反应为液相生成和其他反应的进行提供了必要的热量和气氛条件,对烧结矿产质量有很大影响。
固体碳的燃烧需要不断地供给足够的氧,而且反应首先是在燃料表面进行。
因此,其反应速度(燃料燃烧速度)取决于两个因素:一是碳与氧的化学反应速度;二是氧(气体)向燃料表面的扩散速度。
燃烧过程的总速度就取决于这两个因素中最慢的一个速度[1]。
大量的动力学研究和对燃烧层厚度的探索性研究表明,烧结过程中的燃料燃烧受扩散控制。
因此,烧结混合料中固体燃料的燃烧速度及燃烧层的厚度与燃料颗粒的直径、气流的流速和料层的透气性有关。
在其他条件一定时,颗粒的大小就成为烧结过程的决定性因素。
高负压状态为燃烧带固体碳的燃烧提供了充足的氧量,在燃料粒度变细时,燃烧速度加快,从而使燃烧层变薄,来不及产生足够的液相,导致烧结矿出矿率降低,返矿量增大,配碳量提高,能耗增大。
由此可见,适当增大燃料粒度,降低燃烧速度,可以提高液相产生量,改善烧结矿强度。
由于燃料粒度偏细,导致<1 mm粒级燃料所占的比例升高,在高负压条件下,<1 mm 粒级的燃料被气流抽走,堵塞了混合料的空隙,造成料层的透气性下降,垂直烧结速度降低,烧结矿产量下降。
炼铁原料对烧结矿的影响

炼铁原料对烧结矿的影响炼铁原料是指用于冶炼铁和钢的原始材料,包括铁矿石、焦炭、石灰石和其他添加剂。
其中,铁矿石是最重要的原料,它通过经过矿石的磨碎、磁选和浮选等处理后,转化为烧结矿。
烧结矿是炼铁过程中的主要原料之一,由粉状或颗粒状的铁矿石、焦炭和其他添加剂混合而成。
烧结矿在高温下经过烧结反应,生成具有一定机械强度和适合炼铁工艺要求的块状矿料。
炼铁原料对烧结矿的影响是多方面的,主要包括原料的性质、成分和添加剂的选择。
首先,原料的性质直接影响烧结矿的质量和性能。
例如,粒度分布、比表面积和孔隙度等物理性质,以及矿石的矿物相组成和化学成分等,都会对烧结矿的烧结性能、结构和机械强度产生影响。
其次,炼铁原料中的成分也会对烧结矿的性能产生重要影响。
铁矿石中的主要矿物有赤铁矿、磁铁矿、褐铁矿等,而不同的矿物对烧结过程和产物的形成具有不同的影响。
例如,赤铁矿和褐铁矿富含Fe2O3,可以提供铁的含量,但分解产生的氧化亚铁和氧化铁会增加烧结过程中氧化焦炭和其他还原剂的耗氧量;磁铁矿富含Fe3O4,其磁性和矿物颗粒的结构会影响烧结矿的结构和烧结性能。
此外,炼铁原料中添加的其他剂也对烧结矿产生重要影响。
其中最常见的添加剂是焦炭和石灰石。
焦炭是炼铁过程中最常用的燃料,它能提供热量和还原剂,促进烧结反应的进行;石灰石则作为一种烧结助剂,可以提供CaO和MgO等氧化物,调节烧结矿中的成分和性能。
总的来说,炼铁原料对烧结矿的影响是多方面的,它直接决定了烧结矿的质量和性能。
因此,在炼铁过程中,科学地选择和调整原料的配比、成分和添加剂,能够优化烧结过程和烧结矿的性能,提高铁矿石资源的利用效率和炼铁工艺的经济效益。
- 1、下载文档前请自行甄别文档内容的完整性,平台不提供额外的编辑、内容补充、找答案等附加服务。
- 2、"仅部分预览"的文档,不可在线预览部分如存在完整性等问题,可反馈申请退款(可完整预览的文档不适用该条件!)。
- 3、如文档侵犯您的权益,请联系客服反馈,我们会尽快为您处理(人工客服工作时间:9:00-18:30)。
第1期
杨光亮 ,等 :原料组成和燃耗对烧结矿强度影响的试验研究
11
示 ;通过改变石灰石的用量调整碱度分别为 1. 84 、1. 97 、2. 10 倍 ;燃料的配比 ( %) 为 6. 0 、6. 5 、7. 0 ;水份 ( %)
1
3
2
17 6
2
1
3
18 6
3
2
1
原料 FeO
5. 65 5. 56 5. 46 4. 27 4. 20 4. 13 2. 87 2. 82 2. 83 5. 87 5. 89 5. 79 4. 54 4. 46 4. 47 3. 14 3. 14 3. 09
转鼓 指数
77. 55 74. 60 75. 28 77. 91 77. 27 76. 91 74. 33 76. 16 78. 44 78. 79 79. 71 79. 45 74. 27 77. 73 78. 54 75. 62 74. 06 78. 21
Ig 3. 62
2. 81 6. 24 4. 72 5. 49 14. 59 46. 17 43. 16 0. 610
粒度/ %
> 10mm 5 - 10mm 3 - 5mm 1. 5 - 3mm < 1. 5mm 2. 13 11. 53 15. 47 10. 80 60. 07
0
0
0
2
77. 36 76. 59 76. 36 77. 05
3
76. 31 77. 81 76. 75 76. 35
4 79. 32
5 76. 85
6 75. 96
R
3. 51 1. 40 1. 34 1. 06
2005 年
R′ 2. 25 1. 78 1. 71 1. 35
由表 4 的折算极差值可知 ,铁料搭配方案对烧结矿强度影响较大 , 碱度和燃耗对其影响相当 , 水分对强 度的影响较小 。 2. 1 铁料搭配对烧结矿强度的影响
摘 要 :应用正交试验方法 ,研究了不同原料组成和燃耗对烧结矿强度的影响 ,得出了原料组 成方案和高碱度 、低燃耗的试验结果 ,对合理搭配原料种类 ,提高烧结矿强度 ,降低固体燃耗具 有重要的意义 。 关键词 :原料组成 ;燃耗 ;烧结矿强度 中图分类号 : TF124. 5 文献标识码 :A
2 试验结果及分析
试验结果及烧结矿的理论成分见表 3.
表 3 正交试验结果及烧结矿理论成分
序号 铁料 碱度 燃耗 水份
1
1
1
1
1
2
1
2
2
2
3
1
3
3
3
4
2
1
1
2
5
2
2
2
3
6
2
3
3
1
7
3
1
2
1
8
3
2
3
2
9
3
3
1
3
10 4
1
3
3
11 4
2
1
1
12 4
3
2
2
13 5
1
2
3
14 5
2
3
1
15 5
3
1
2
16 6
铁料搭配水平为 4 时 ,烧结矿转鼓指数较高 。一般来说 ,烧结矿的转鼓指数随烧结料中 FeO 含量的升 高而增大 , FeO 含量在 5. 46 % - 5. 56 %时 ,烧结矿的强度较低 。烧结原料 (主要是含铁原料) 是烧结矿中 FeO 的主要来源 ,烧结料中的 FeO 随 A 矿和 B 矿用量的增加而增加 。烧结料原始 FeO 含量较低时 ,在烧结 过程中 Fe2O3 较易保持原始形态 ,并能与 CaO 生成铁酸钙 ;当烧结料原始 FeO 含量较高时 ,其在烧结料中的 含量高 ,会使烧结矿中的 FeO 含量升高 ,原料中的 Fe2O3 可能会被还原成 Fe3O4 或富氏体 FexO ,而与 SiO2 生成较多的铁橄榄石 (2 FeO·SiO2) ,降低硅酸钙和玻璃质的生成量 ,而铁料水平 4 中含有较高的 MgO ,可以 抑制硅酸钙晶型转变造成的强度降低 ,使烧结矿的强度升高[3 - 5 ] 。由表 1 可以看出铁料搭配水平为 4 时 ,烧 结原料中的 FeO 含量最高 。 2. 2 石灰石用量对烧结矿强度的影响
SiO2
5. 07 5. 05 5. 02 5. 00 4. 97 4. 95 4. 92 4. 89 4. 89 5. 06 5. 06 5. 03 5. 00 4. 97 4. 97 4. 92 4. 91 4. 89
R
1. 84 1. 97 2. 13 1. 82 1. 97 2. 11 1. 82 1. 97 2. 06 1. 87 1. 97 2. 12 1. 84 1. 98 2. 08 1. 83 1. 94 2. 08
Al2 O3
2. 82 2. 80 2. 77 2. 76 2. 73 2. 71 2. 69 2. 67 2. 66 2. 71 2. 71 2. 68 2. 65 2. 63 2. 62 2. 58 2. 58 2. 55
%
MgO
3. 23 3. 22 3. 20 3. 24 3. 22 3. 21 3. 24 3. 23 3. 23 3. 67 3. 67 3. 65 3. 68 3. 66 3. 66 3. 68 3. 68 3. 66
文章编号 :100920193 (2006) 0120010204
原料组成和燃耗对烧结矿强度影响的试验研究
杨光亮1 ,2 ,杨碧能3 ,张金柱1 ,邓海亮1 ,赵跃萍1
(1. 贵州大学 材料科学与冶金工程学院 ,贵州 贵阳 550003 ;2. 水城钢铁 (集团) 有限责任公司 培训中心 ,贵 州 水城 553028 ;3. 水城钢铁 (集团) 有限责任公司 技术处 ,贵州 水城 553028)
1 试验方法
本试验根据水城钢铁公司烧结厂现行原料结构和工艺 ,合理的搭配使用国内和国外的铁矿石 。试验用 铁料 、燃料 、熔剂的化学成分及其粒度组成如表 1 所示 。
表 1 原燃料和熔剂化学组成成分及其粒度组成
矿名 TFe FeO
进口矿 62. 46 0. 15
A 矿 59. 27 20. 92
第230506卷年第2
1期 月
贵 州 工 业 大 学 学 报 (自然科学版) J OU RNAL OF GU IZHOU UN IV ERSIT Y OF TECHNOLO GY
(Natural Science Edition)
Vol. 35 No. 1
Fedruary. 2006
0
0
12. 08 22. 27 64. 93
0
0
18. 4
19. 07 62. 53
以铁料 、碱度 、燃耗 、水份为因素 ,应用 L18 (6 ×36) 正交试验表进行试验 。 铁料中 C 矿 、D 矿 、E 矿和返矿的配比 ( %) 分别固定为 3 、8 、6 和 20 ,进口矿 、A 矿和 B 矿的配比如表 2 所
为 7. 0 、7. 5 和 8. 0 ;白云石配比固定为 6 %.
表 2 铁料搭配方案
kg
矿 名
水平号
1
2
3
4
5
6
进口矿 26 32 38 23 29 35
A矿
18 12 6 18 12 6
B矿
9
9
9 12 12 12
采用Φ145 mm ×560 mm 的烧结杯试验 ,料层高 540 mm ,压料 20 mm ,点火温度 (1323 ±50) K ,点火时 间 1 min ,点火时抽风负压 6000 Pa ,烧结时抽风负压 11000 Pa. 在冷却阶段 ,当废气温度降至 433 K 时 ,停止 抽风 。然后做落下试验 、筛分烧结矿粒级和转鼓试验 。并计算各个试验号的烧结矿理论成分 。
0 引 言
随着高炉炼铁产量的提高和炉前“精料”技术的发展 ,高炉对入炉原料的质量要求越来越高 。目前高炉 的熟料率达到 85 %以上 ,烧结矿作为高炉炼铁基本原料之一 ,其质量的好坏对高炉炼铁起着至关重要的作 用 。强度是烧结矿的主要质量指标 ,高强度的烧结矿可以显著改善高炉的冶炼工艺 。
在烧结过程中 ,通过点火 、预热和固体燃料的燃烧 ,将粒状烧结料的温度升高达到局部熔化并生成一定 的液相 ,在随后的冷却过程中 ,液相结晶或凝固成不同的矿相 ,将烧结料粘结到一起而成为烧结矿[1 ] 。烧结 过程的热量主要是通过燃烧分散在混合料中的碳粒而产生的 。烧结原料的化学成分和热分布状况明显影 响烧结矿质量 。由于水城钢铁公司烧结厂的原料来源较广 ,燃耗与同行业相比较高 。因此 ,研究原料组成 和燃耗对烧结矿强度的影响 ,实现合理的原燃料搭配是烧结生产降低成本的基础 。
烧结过程中必要的高温条件是由烧结料中燃料的燃烧提供的 ,燃料的用量明显影响烧结矿强度 。由表 4 的分析发现 ,随燃料配比的增加 ,烧结矿的转鼓指数降低 。当燃料配比为 6. 0 %时 ,烧结矿的转鼓指数较 高 。根据厚料层烧结理论 ,低水 、低碳有利于烧结矿强度的提高[9 ] 。燃料配入量为 6. 0 %时 ,烧结在氧化的 气氛下进行 ,Fe3O4 氧化生成 Fe2O3 ,使强度和还原性较好的铁酸钙生成量增加 。随燃料用量的增加而出现 了剩余 ,过剩的燃料会消耗空气中的氧 ,烧结料大量熔融 ,料层透气性变差 ,烧结在还原的气氛下进行 ,不利 于 Fe2O3 的存在 ,降低铁酸钙的生成量 ,使强度较差的玻璃相含量增加 ,烧结矿强度降低 。根据钢铁企业“降 耗提效”的宗旨 ,使用低燃料烧结符合钢铁企业发展的方向 。