异常分析对策表
外饰件喷漆异常分析及对策

失光
现象
有光泽涂层干燥后没有达到应有的光泽或涂装后不久出现光泽 下降、雾状朦胧现象
可能引起的原因
涂料方面:
• 颜料的选择、分散和混合比不适当 • 树脂的混溶性差 • 涂料的溶剂选配不当
涂装方面:
• • • • • 被涂面对涂料的吸收量大,且不均匀 被涂面粗糙,且不均匀 漆雾干扰或补漆造成 在高温高湿下或极低温的环境下涂装 2C1B湿喷湿体系,底层未指触干即喷涂面涂,造成清漆渗透
处置
●将大颗粒打磨,进行局部修补 ●小颗粒研磨后抛光处理
桔皮
<现象及原因> ●涂面如桔子表皮状 凹凸不平 ●在涂液形成涂膜过 程中,溶剂蒸发时在 涂膜内部产生对流现 象。如果其流动过早 停止则会引起漆膜表 面凹凸
引起的主要原因
●环境原因 ○温度高; ○风速强 ●设备、机器原因 ○喷枪口径小; ○压缩空气压力低 ○喷枪不佳或清扫不良,导致雾化不良 ●涂装作业时的原因 ○车体温度高; ○涂膜过薄 ○喷涂压力低; ○吐出量过少 ○喷枪速度快; ○喷枪距离远 ○晾干时间短 ●材料导致的原因 ○稀释剂挥发速度过快; ○涂料粘度高 ○涂料流平性不好
处置
●轻度流挂,用砂纸研磨后抛光或修补 ●全面流挂,应彻底打磨流挂痕,再重新涂装
针孔
现象及原因
●涂膜上产生针刺状孔或象皮 革的毛孔样现象 ●涂膜中的溶剂在表面干燥过 程中快速蒸发,其痕迹成孔 残留,工件的边角等,为容 易产生部位。
引起的主要原因
●环境原因 ○温度高; ○风速快 ○湿度高 ●设备、机器原因 ○升温过急、表面干燥过快 ●涂装作业时的原因 ○吐出量大; ○涂膜过厚 ○腻子的底孔 ●材料导致的原因 ○稀释剂挥发过快 ○涂料的流动性差 ○涂料中混入水分等异物
SMT异常分析和改善报告
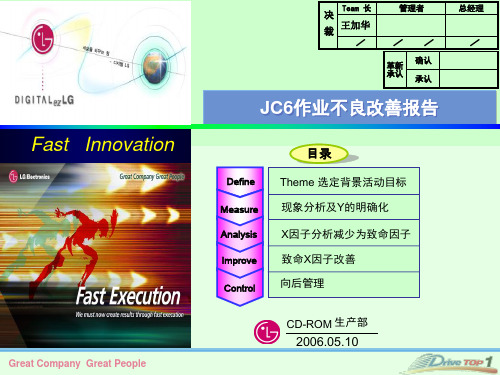
2006.05.10
Great Company Great People
Background Output
D
M
A
I
C
通过4月份工程不良数据分析发现作业不良占比率高,特选定作业不良为活动主题.
4月不良细部分析( PPM )
作业不良改善
TDR改善中
生产规模的迅速扩大,品质控制的
力度相对不足.
1236
修定 叠板 未检SET堆机现象严重
采用JIG放板
未检SET固定车放置 邀请生技,PM进行维修
PCB作业 不良
元件脱落
过桥掉机
修理叠板现象严重
修理不良追加JIG放置 作业者教育数量减少
投入位叠板
线路断
切板JIG不良 作业者修坏
设备重新更换改善 作业者教育数量减少
XS7 XS8
Two-proportions P-Value = 0.038 <0.05
改善前
1,236 1,246 1,123
改善后
作业不良率 改善目标
1,400 1,200 1,000 800 600 400 200 0
1,146
1,023
986 798
1,240
320
4月实绩 5月1日 5月2日 5月3日 5月4日 5月5日 5月6日 5月7日 5月8日
246
5月9日
235
155
13270 1930 2271 4月实际 部品
2435
1498
作业不良给品质,市场不良埋下了
很大的隐患.急需改善.
作业
MD
拆装
其他
不良细部分析( PPM )
Pareto Chart of 作业不良 _1
异常分析对策表(word表格)

策 省
低材料供商之影响
月
主管_____________
担当_____________
单位:制造部(生管课)
异常分析对策表
1. 扩大仓库之储放空间。
○○年 1 月
重 管 项
要 理 目 把
● 60 50 40 30 ● 20 10 00/11 00/12 01/1 01/2 01/3 01/4 01/5 00/12 月高达 65 件属异常
主管_____________ 担当_____________
反 策
基 准
30 件
周 期 月
因
真因:1.仓库空间不足,材料无法分类归位, 多种类似之材料以堆叠方式,易造 成盘点之失误. 2.材料种类繁多,协助人员未完全认 识所有材料造成误盘. 3.仓库人员未依照发料规定依单发 料,造成料帐不符.
制造部生管课异常分析对策表年3001100120பைடு நூலகம்010102010010401053023025201510001100120101010201030104010501020103差异交期太短采购疏失交通因素1物控疏失1114已进入市场旺季紧急订单增加而材料交期无法配合厂商本身之产能不足无法准时交货
单 位 : 制造部 ( 生管课 ) ○○年 3 月
异常分析对策表
30 25 20 ● 15 ● 10 5
重 管 项
要 理 目 把
再 1.物控提出材料预估
● ● ●
发 处 防 止
库存缩短材料交期
2. 建立供应商资料库
原物料未 能及时入 厂件数
基 准 期
10 件
00/11 00/12 01/01 01/02 01/03 01/04 01/05
质量异常响应及水平展开程序(含表格)
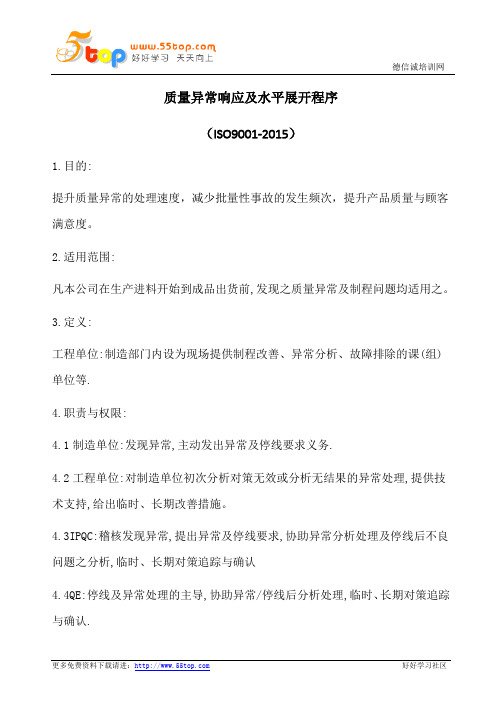
质量异常响应及水平展开程序(ISO9001-2015)1.目的:提升质量异常的处理速度,减少批量性事故的发生频次,提升产品质量与顾客满意度。
2.适用范围:凡本公司在生产进料开始到成品出货前,发现之质量异常及制程问题均适用之。
3.定义:工程单位:制造部门内设为现场提供制程改善、异常分析、故障排除的课(组)单位等.4.职责与权限:4.1制造单位:发现异常,主动发出异常及停线要求义务.4.2工程单位:对制造单位初次分析对策无效或分析无结果的异常处理,提供技术支持,给出临时、长期改善措施。
4.3IPQC:稽核发现异常,提出异常及停线要求,协助异常分析处理及停线后不良问题之分析,临时、长期对策追踪与确认4.4QE:停线及异常处理的主导,协助异常/停线后分析处理,临时、长期对策追踪与确认.4.5IQC:负责来料不良异常/停线的临时对策、长期对策的提供.4.6PMC单位:负责缺料而停线的问题解决。
4.7行政部:负责因停电与停气造成停线之问题解决。
5.文件内容:5.1异常的种类:材料异常指进料检验或制程中发现的材料不能满足产品特性及工艺要求(进料检验按AQL抽检)制程异常指在首件板外观、功能、性能验证、流动板外观、功能、性能验证以及正常量产中产品外观、功能、性能检查等不能满足产品特性要求成品检验异常:QA按AQL抽检发现的在外观、功能、性能等不能满足产品特性要求或客户要求5.2异常处理的时效:5.2.1材料异常:A、进料检验:检验后立即提报异常,QE在2小时内取证并将异常提交给供应商。
及时联络供应商回复处理方案。
B、制程中发现材料异常:生产部在工序检验中发现制程不良率超过2%后提交异常,工程分析为材料异常,生产部门将异常单提交给品质后,QE在1小时内取证,并将异常提交给供应商。
要求供应商在1小时内回复处理方案。
在取证过程中,如发现材料异常条件不充分,需进一步验证,生产及工程部门需配合。
C材料异常在供应商回复需要克服使用或挑选使用时,由品质部QE组织MRB会议,由生产、品质、工程、PMC讨论、制造部副总经理裁决是否同意要求执行。
异常处理及操作流程

异常中断。
异常管一理、:就异是常对所说发明生及、发流现程的各种显在的、
潜在的、持久的或者突发的异常进展分析、对 策处置的整个过程〔异常的不一定就是有问题 的〕,异常其实在我们身边无处不在,异常的 开掘要靠我们的注意力,从日常工作中,查出 任何细小的异常,以提升管理水准。要能擅长 用自己的五官〔视觉、嗅觉。听觉、触觉、味 觉〕及直接去觉察。
务忽略所致之异常。 作忽略所致之异常。
4、各部门影响消费问题的原因
消费车间:
品管部:
〔1〕工作安排不当,造 成零件损坏。
〔1〕 检验标准﹑标准 错误。
〔2〕操作设备仪器不当, 〔2〕 进料检验合格,但
造成故障。
实际上线不良。
〔3〕 设备保养不力。
〔3〕 进料检验延迟。
〔4〕 作业未依标准执行, 〔4〕 上工段品管检验合
3、分 类
消费异常分类
(1)方案异常:因消费方案临时 变更或安排失误等导致的 异常
(2) 物料异常:因物料供给不 及〔断料〕导致的异常.
(3) 设备异常:因设备故障或 水,气,电等原因此导致的 异常.
(4)品质异常:因制程中发生, 发现品质问题而导致的异 常.
(5) 技术异常:因产品设计或 其他技术问题而导致的异 常.
10、平日工作总结〔10问〕
•人
•机
• 1.新进员工入职培训是否有效? 1.设备管理职责清楚吗?
• 2.多能工培训方案有施行吗? 2.设备点检运作有落实没有?
Байду номын сангаас
• 3.员工可以有资格分级吗?
3.怎么减少设备磨损?
• 4.现场人员有共同遵守规那么吗? 4.设备预防怎么做?
• 5.岗位交接清楚?
供货品质异常分析及改善报告模板
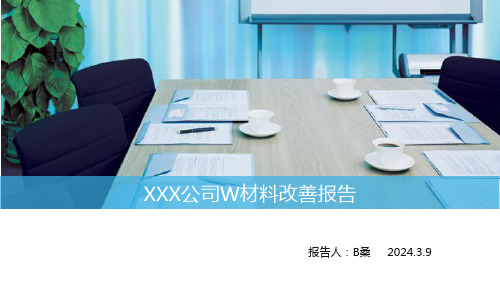
M材料改善报告---P4: 根本原因分析(Root Cause Analysis)
可能原因
现象特征匹配
发生站点匹配
发生概率匹配
再现验证匹配
设备故障
√
√
√
√
说明
该原因导致的不良现象和异常现象是否一致
LILY
2024年3月11日
采购中
M材料改善报告---P6:效果确认(effect confirmation)
设备走动机构报修后,当日已经修好,因此其他M材料没有此种情况;经过本次与现场使用人员沟通,我们待改进设备的行走稳定性,用以实现M材料涂层的更加均匀。此机构的优化计划在本月底以前完成,届时,将提供完善后的产品状态照片。
3D 临时对策
4D 原因分析及验证
5D 改善措施及验证
6D 改善执行及效果确认
7D 预防措施
JACK
工艺
★
★
★
★
LILY
品质
★
★
★
★
★
★
SURE
工程
★
★
★
LUCY
生产
★
★
★
★
★
JULY
业务
★
★
★
M材料改善报告—P3:临时对策(Temporary countermeasures)
现象描述 成立小组 临时对策 原因分析 永久措施 有效验证 措施标准化 客户确认
位置
数量
处理方法
处理结果
完成日期
备注
客户端
1
退回补货
根据客户安排
在库
油封缺陷分析及对策表
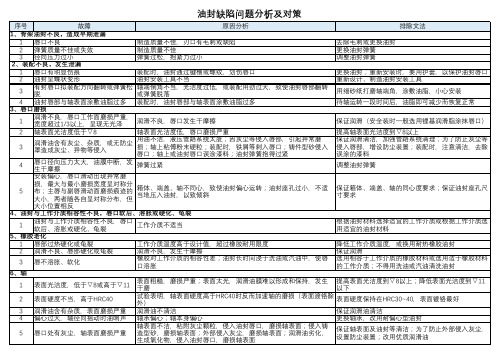
保证箱体、端盖、轴的同心度要求;保证油封座孔 尺寸要求
根据油封材料选择适宜的工作介质或根据工作介质 选用适宜的油封材料 降低工作介质温度,或换用耐热橡胶油封 保证润滑 选用相容于工作介质的橡胶材料或选用适于橡胶材 料的工作介质;不得用洗油或汽油清洗油封 提高表面光洁度到▽8以上;降低表面光洁度到▽ 11以下 表面硬度保持在HRC30~40,表面镀铬最好 保证润滑油清洁
偏心过大,轴径向摇动时油响声 轴承偏心;轴本身偏心 轴表面不洁,粘附灰尘颗粒,侵入油封唇口,磨损轴表面;侵入 5 唇口处有灰尘,轴表面磨损严重 铸造型砂,磨损轴表面;外部侵入灰尘,磨损轴表面;润滑油劣 化,生成氧化物,侵入油封唇口,磨损轴表面 轴表面有工艺性龟裂或腐蚀点等,加剧磨损而泄漏;轴表面的伤 6 轴的滑动表面有伤痕或砂眼 痕、砂眼等与油封唇口之间形成间隙而泄漏;轴表面划伤或碰伤 轴表面的滑动部分有方向性的加 轴表面留有微细螺纹旋槽等车削或磨削工痕迹,形成泵吸作用而 7 工痕迹 泄漏 五、骨架油封安装注意事项 1 2
装配时,油封通过键槽或螺纹,划伤唇口 油封安装工具不当 轴端倒角不当,光洁度过低,或装配用劲过大,致使油封唇部翻 3 有封唇口拟装配方向翻转或弹簧松脱 转或弹簧脱落 4 油封唇部与轴表面涂敷油脂过多 装配时,油封唇部与轴表面涂敷油脂过多 3、唇口磨损 润滑不良,唇口工作面磨损严 1 润滑不良,唇口发生干摩擦 重,宽度超过1/3以上,呈现无光 2 轴表面光洁度低于▽8 轴表面光洁度低,唇口磨损严重 用油不洁,液压管路系统太脏;因灰尘等侵入唇部,引起异常磨 润滑油含有灰尘、杂质,或无防 3 损;轴上粘傅粉末硬粒;装配时,铁屑等刺入唇口;铸件型砂侵 尘罩造成灰尘、异物等侵入 入唇口;轴上或油封唇口误涂漆料;油封弹簧抱得过紧 唇口径向压力太大,油膜中断, 4 弹簧过紧 发生干摩擦 安装偏心,唇口滑动出现异常磨 损,最大与最小磨损宽度呈对称 箱体、端盖、轴不同心,致使油封偏心运转;油封座孔过小,不 5 分布;主唇与副唇滑动面磨损痕 适当地压入油封,以致倾斜 迹的大小,两者随各自呈对称分 布,但大小位置相反 4、油封与工作介质相容性不良,唇口软后、溶胀或硬化、龟裂 油封与工作介质相容性不良,唇 1 工作介质不适当 口软后、溶胀或硬化、龟裂 5、橡胶老化 1 唇部过热硬化或龟裂 工作介质温度高于设计值,超过橡胶耐用限度 2 润滑不良、唇部硬化或龟裂 润滑不良,发生干摩擦 橡胶对工作介质的相容性差;油封长时间浸于洗油或汽油中,使 3 唇不溶胀、软化 唇口溶胀 6、轴 表面粗糙,磨损严重;表面太光,润滑油膜难以形成和保持,发 1 表面光洁度,低于▽8或高于▽11 生干磨 试验表明,轴表面硬度高于HRC40时反而加速轴的磨损(表面渡铬 2 表面硬度不当,高于HRC40 除外) 3 润滑油含有杂质,表面磨损严重 润滑油不清洁
客诉异常改善对策效果确认表

/
塑模 课
A
1、 客户处
36.4KP厂内库存 提报客户,方便客
人收货作业-------
----2011.3.22完
成;
(Insertmoding)尺寸大
0.01~0.02MM,导致模具作
业过程定位时产生干涉,
3/22 9:00
而把端子下压,形成端子 PIN下弯和胶跑到端子表面 的现象;
并测量MYLAR的厚度、宽 度。附改善前、改善后 对比图片,如附件PI胶带 对比测试报告(胶厚、 初粘力、剥离力)。 2 、 改善后的MYALR在制 程中上线使用时没有进 行擦拭MYLAR的动作,第 一次验证2400PCS经过 100%目视没有溢胶不良 (6月6日已送1200PCS给 客人确认没有溢胶), 第二次验证时间为6月6 日全检2400PCS产品存放 恒温恒湿仓6天再重新 200%目视全检没有发现 溢胶不良,故6月13日起
象,导致打
MINI USB 8P
2011.07.1 3
件抛料; 2、检验时
发现产品表
位置未作重点防控,引
张美群
发盖带压载带齿孔不良 。3、 残胶及粘在载带
上吸不出来,经分析原
/
面有残胶及
因是,裁切冲压MYLAR的
粘在载带上
治具刀口经长时间的裁
吸不出来。
切作业粘有胶,导致有
残胶粘在产品表面及边
S
制造 品保 采购
1、 要求供应商减少背
胶量,此部分已在5月16
日改后MYLAR样品,裁切
后MYLAR无溢胶的现象如
改善前后对比图5-1a。
从即日起,供应商交货
时每批附送PI胶带测试
报告,IQC检验时依供应
QC七手法(含对策表)

实施步骤
收集数据、绘制散布图、观察并 分析数据点的分布规律、判断变 量间的关系。
直方图法
定义
直方图法是通过绘制直方图,展示数据分布情况的方法。
应用场景
适用于了解数据的分布规律,判断其是否符合正态分布或其他分布 类型。
实施步骤
收集数据、确定组数及组距、绘制直方图、观察并分析数据分布情 况。
qc七手法(含对策表)
目录
CONTENTS
• 引言 • qc七手法概述 • qc七手法详解 • 对策表在qc七手法中的应用 • qc七手法与对策表的结合实践 • qc七手法(含对策表)的总结与展望
01 引言
CHAPTER
目的和背景
提高产品质量
01
通过QC七手法,可以系统地分析和解决质量问题,从而提高产
实施效果
通过运用QC七手法,企业能够及时发现并解决生产过程中的问题,减少不良品率,提高生产效率,降低 成本,增强市场竞争力。
qc七手法(含对策表)的展望与未来发展
发展趋势
挑战与对策
前景展望
随着科技的进步和市场需求的变化, QC七手法将不断发展和完善。未来 ,更多的智能化技术将被应用于质量 管理中,如机器学习、大数据分析等 ,以提高质量管理的效率和准确性。
持续改进
通过对实施对策的效果进行评估和反馈,不 断完善和改进质量管理方法和体系。
qc七手法的历史与发展
起源
qc七手法起源于20世纪60年代的日本,当时日本企业为了应对国际市场竞争和提高产品 质量,开始引入并广泛应用这些方法。
发展
随着全球化和市场竞争的加剧,qc七手法逐渐被世界各国企业所采用和改进,不断发展和 完善。同时,新的质量管理方法和工具也不断涌现,为企业提供了更多的选择和手段。
质量异常响应及水平展开程序(含表格)
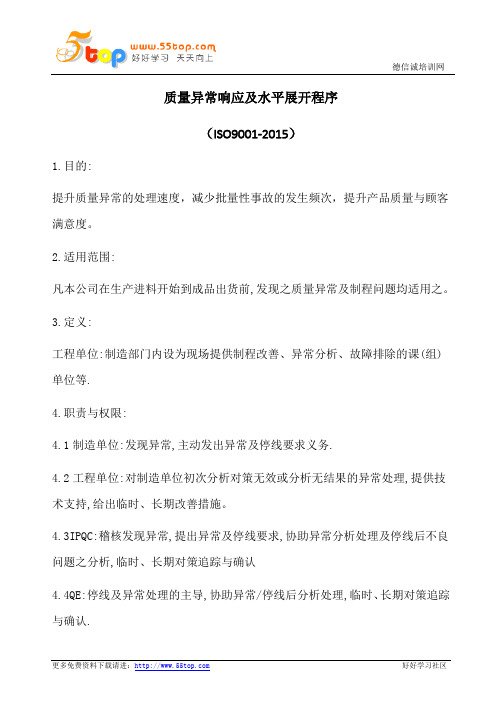
质量异常响应及水平展开程序(ISO9001-2015)1.目的:提升质量异常的处理速度,减少批量性事故的发生频次,提升产品质量与顾客满意度。
2.适用范围:凡本公司在生产进料开始到成品出货前,发现之质量异常及制程问题均适用之。
3.定义:工程单位:制造部门内设为现场提供制程改善、异常分析、故障排除的课(组)单位等.4.职责与权限:4.1制造单位:发现异常,主动发出异常及停线要求义务.4.2工程单位:对制造单位初次分析对策无效或分析无结果的异常处理,提供技术支持,给出临时、长期改善措施。
4.3IPQC:稽核发现异常,提出异常及停线要求,协助异常分析处理及停线后不良问题之分析,临时、长期对策追踪与确认4.4QE:停线及异常处理的主导,协助异常/停线后分析处理,临时、长期对策追踪与确认.4.5IQC:负责来料不良异常/停线的临时对策、长期对策的提供.4.6PMC单位:负责缺料而停线的问题解决。
4.7行政部:负责因停电与停气造成停线之问题解决。
5.文件内容:5.1异常的种类:材料异常指进料检验或制程中发现的材料不能满足产品特性及工艺要求(进料检验按AQL抽检)制程异常指在首件板外观、功能、性能验证、流动板外观、功能、性能验证以及正常量产中产品外观、功能、性能检查等不能满足产品特性要求成品检验异常:QA按AQL抽检发现的在外观、功能、性能等不能满足产品特性要求或客户要求5.2异常处理的时效:5.2.1材料异常:A、进料检验:检验后立即提报异常,QE在2小时内取证并将异常提交给供应商。
及时联络供应商回复处理方案。
B、制程中发现材料异常:生产部在工序检验中发现制程不良率超过2%后提交异常,工程分析为材料异常,生产部门将异常单提交给品质后,QE在1小时内取证,并将异常提交给供应商。
要求供应商在1小时内回复处理方案。
在取证过程中,如发现材料异常条件不充分,需进一步验证,生产及工程部门需配合。
C材料异常在供应商回复需要克服使用或挑选使用时,由品质部QE组织MRB会议,由生产、品质、工程、PMC讨论、制造部副总经理裁决是否同意要求执行。
品质异常分析与预防(超完善)

No
-
8
提出报告
ቤተ መጻሕፍቲ ባይዱ
改善进行/ 改善证据
FACA Report (Normal) 8D Report
9
结果确认
改善报告
-
10
报告整合
11
回复客户
12
结案
讨论: a) 怎么对策“客户抱怨”? b) 怎样处理“客户退货”? c) 怎样应对“客户验厂”? d) 怎样调查“客户满意”?
FACA Report (Normal) 8D Report 客诉登记表
Y
在 ERP 进行过账处理
Kunshan Myzy Technology Co., Ltd
四、品质异常相关处理流程
Dept Step 制造
产线正常生产
品保
工程
SQE
仓库
Key Point
Form
制程发现异常
*制程异常,QC开立异常处理单 *保留不良品,记录不良数据 不良品
异常处理单
良品
异常判定
*依客户由ENG/QE要求进行判定 *电子方面由EE进行判定
NMRB
品保
不合格品处理 联络单 NMRB IQC 报表
整理与记录
特采
退货
重工/挑选
Y
仓库
进料验收单
入库
IQC 报表 讨论: 进料检验报告 a) 所有物料都检验吗? 依“文件数据与记录管制 不合格品处理 程序”执行 b) 急料可以免验吗? 联络单 NMRB 外箱粘贴检验标签 c) IQC检验不合格时,是否一定 IQC 报表 退货? 粘贴检验标签 进料验收单 d) 进行不合格的责任一定是供应 商的吗?
How 方法
5W2H
Who 何人
制程品质异常处理程序(含表格)
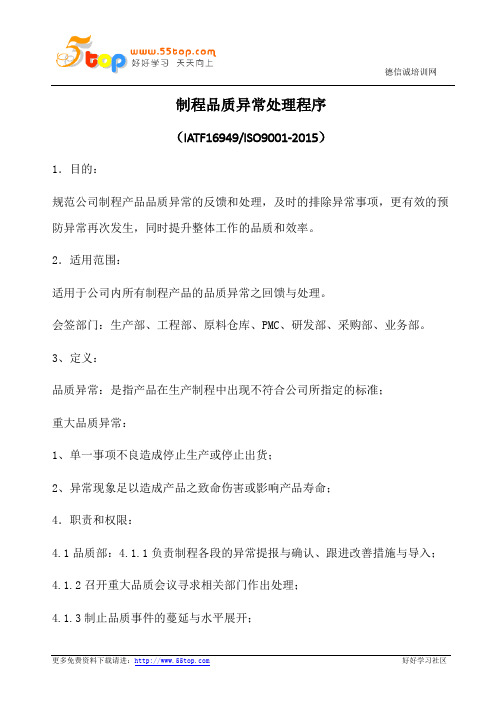
制程品质异常处理程序(IATF16949/ISO9001-2015)1.目的:规范公司制程产品品质异常的反馈和处理,及时的排除异常事项,更有效的预防异常再次发生,同时提升整体工作的品质和效率。
2.适用范围:适用于公司内所有制程产品的品质异常之回馈与处理。
会签部门:生产部、工程部、原料仓库、PMC、研发部、采购部、业务部。
3、定义:品质异常:是指产品在生产制程中出现不符合公司所指定的标准;重大品质异常:1、单一事项不良造成停止生产或停止出货;2、异常现象足以造成产品之致命伤害或影响产品寿命;4.职责和权限:4.1品质部:4.1.1负责制程各段的异常提报与确认、跟进改善措施与导入;4.1.2召开重大品质会议寻求相关部门作出处理;4.1.3制止品质事件的蔓延与水平展开;4.1.4对实施的对策做复核,发出最终的改善结果;4.2生产部:负责品质异常提出及初步的原因排除,执行技术部门给出的对策;4.3工程部:对制程的异常进行原因分析,给出有效的改善措施;4.4研发部:因设计不符合对制程产生的品质异常做出调整,并给出有效的改善对策;当出现重大品质事件协助查找不良原因;4.5PMC:根据品质异常处理状况对订单评估与调整;4.6采购部:掌握品质异常之材料影响程度,跟进进料品质状况和协助制程中出现异常处理;4.7业务部:因品质造成影响出货暂停出货或让步出货,以及修改出货计划;4.8仓库:根据因品质不良产品做出区分和标示;5、参考数据<成品检验规范><SOP作业指导书>6.作业程序:6.1制程品质异常确定6.1.1当在生产过程中,生产各段发现或经工程PE分析确认同一材料和工站出现不良数出现5PCS,一批总不良率超出3%时由品质IPQC提报异常单进行处理;6.1.2当生产各工段出现不良率达到100%或在接线、测试段直接烧机事件,跟线品质IPQC并立即要求生产源头停止下拉和不良标示以及发出停线报告,签核到品质中心主管后并以OA通知到相应部门,同时做生产的调整;6.1.3出货检验中出现不良率超出BJH-QU-ETS-007、BJH-QU-ETS-160标准值,由OQC提报异常由部门主管签核后转至生产包装负责人确认并通知工程PE到现场进行分析,按6.2执行;如急需出货并上升到中心主管审核通过或业务员与客户确认OK方可做让步接收出货;品质做单据保存以其客户使用状况的跟进;6.2正常制程品质异常处理6.2.1当产线出现异常达到6.1.1规定值时由跟线IPQC现场确认现场可改善或者由部门主管以上级确认可生产,将有效改善对策以及确认信息给到跟线的拉长执行,跟据生产对策实施IPQC再次确认改善效果,OK后按正常生产流程作业,NG时再返回对策实施;6.2.2当产线出现异常达到6.1.1规定值时由跟线IPQC现场确认现场不能改善时,及时开始品质异常处理单并填写发生异常工序、生产数量、不良现象、标准值、不良值、不良率等状况,由制程品质组长和主管签核后附带不良品转至跟线PE工程师并要求跟线人员以其IPQC到现场做进一步分析;6.2.3工程PE工程师接到品质开出的异常处理单并到异常发生工段做进一步分析确认,同时在30分钟内给出可执行的临时对策给到生产执行和现场指导,生产可恢复正常生产,若临时对策因设计、材料所至需生产挑选、加工使用由生产进行统计无效工时由责任归属承担,需要做实验验证分析结果跟进实验时间给出临时对策但总体时间不能超出8小时以外;6.2.4PE工程师在完成异常分析将分析状况填写至品质异常处理单上,同时给出临时对策、责任归属部门返回跟线IPQC转至到制程品质QE确认原因分析及责任归属,当责任归属对工程所分析的结果有异议时,品质QE主导对异常分析结果异议部门到现场进行确认,品质QE做最终判定。
全面质量管理的常用七种分析工具

全面质量管理的常用七种分析工具所谓全面质量管理常用七种工具,就是在开展全面质量管理活动中,用于收集和分析质量数据,分析和确定质量问题,控制和改进质量水平的常用七种方法。
这些方法不仅科学,而且实用,作为班组长应该首先学习和掌握它们,并带领工人应用到生产实际中。
一、统计分析表法和措施计划表法ﻫ质量管理讲究科学性,一切凭数据说话.因此对生产过程中的原始质量数据的统计分析十分重要,为此必须根据本班组,本岗位的工作特点设计出相应的表格。
常用的统计分析表有以下几种,供参考。
1.不良项目调查表某合成树脂成型工序使用的不良项目调查表如下.每当发生某种不良时,工人就可在相应的栏目里画上一个调查符号,这样,下班时哪些不良项目发生了多少,立即可知。
2.零件尺寸频数分布表此表与不良项目调查表属同一类型。
第二栏为零件尺寸的分组,第四栏的“ ”与不良项目调查表中的“正"是相同的符号。
工人每加工完一个零件,经检测后,将所得零件尺寸在第二栏“组距”中找到相应的尺寸组,然后再在第四栏中记录符号,待到下班或完工时,再统计第五栏.这样的图既直观、又明确、有助于掌握零件尺寸的分布情况。
3。
汽车油漆缺陷统计表ﻫ该表的特点是直观,而且将每个缺陷的部位表示出来了。
4。
不良原因调查表要分清不良的发生原因,可接设备、操作者、时间等标志进行分层调查,填写不良原因调查表。
下表为调查了甲、乙两位工人5天生产塑料勺不良原因的调查表。
5。
不合格品分类统计分析表ﻫ下表为某工序同时生产三种规格的轴承,按不良项目分别统计.表的右侧和下边的合计栏均画作虚线,表示可根据需要取舍.需要注意的是“尺寸精度”和“旋转精度"作为总目,下面还细分若干细目,这是表格设计的一种技巧,与此对应,下边合计栏也应合理设计。
6。
措施计划表ﻫ措施计划表,又称对策表.在制订一个具体的改进措施计划后,所有对策编制成计划表的形式。
下表为某照相机厂生产一种自拍照相机,为了解决自拍质量问题,针对所分析的原因,制订的改进措施计划表。
品质异常原因分析及对策报告

0.不具合情報(現象・件数・内容など)1.事実の把握(現品の確認結果・要因分析・生産品の品質状況)--1.現品確認結果※良品や図面と比較して何が悪いのかを明記する3.ロット追跡と変化点調査※対象範囲とその前後の4M変化点調査1.批次追溯年6月18日年6月2日台依客户OCD 反馈的现品票信息,该异常品对应批次的工程生△产日期及数量如下:※品質保証責任者(社内責任の場合は部署の長)コメント台殿 2.4M 变化点调查殿不具合詳細説明(発見状況・事象・写真等):年月日 2.工程の説明※工程のフローと、発生・流出対象工程を明確化する4.要因分析※決め事と実際の事実により問題点を抽出する1、通过对比通常品与异常品的成分分析,虽然两者的成分检测结果都满足SPHC原材料的标准要求,但同时也发现两者的发生工程C含量有明显的差异対策書の処置 □ 来社報告 □ 対策書のみ □受領 □再提出□ その他( 月 日)标准要求: ≤0.12記 事2、进一步对热处理生产履历记录表进行调查,发现2020-1-6对象批次的制品硬度实测值偏低,通常品一般硬度在HRB35以上,而异常批次对应制品的硬度为RHB24/27不具合コード流出工程综上分析,推断本回异常可能是在热处理过程中因制品加热及総数台NG数台保温时间过长而导致的偶发性的脱碳不良;进而推断如下原因:①制品在热处理框内因卡住而滞留在框内进行了二次或多次的热处理加工,从而导致其脱碳不良;②制品因锻造异常而进行返热处理,且同时与第一回热处理的制品混为进行。
2.原因の究明(再現テスト・発生のメカニズム・直接原因・なぜなぜ分析)3.適切な対策(対策内容)5.水平展開(類似部品・類似工程への展開)1.再現テスト※原因の判定をする 3.不具合発生/原因 1.発生対策(担当)(期限)有無(水平展開の概要、「無」の場合は展開しない理由を明記)相关类似品之FC制品,均无需经过热处理加工2.発生のメカニズム 4.不具合流出原因参见附件:热处理炉操作及热处理作业手顺书 6.効果予測(※実績は対策フォローにて報告)教育训练签到及考核表 2.流出対策原因コード03020199 4.源流へのフィードバック(標準・仕組み・ルールへの反映内容)歯止め発工程FMEA 6/2012345コントロールプラン6/20生作業標準類2/25流設備/治具/12345記録類6/20出教育記録2/25Q-2131-424.4.24改訂△80.008方法1.硬度实测值<55HRB2.锻造工程无该项目的检查内容C 含量通常品异常品0.042冷锻冲床SPHC 8.0 敝司于2020年2月13日和14日分别采 用普通退火炉以及真空退火炉,在 相同的热处理条件下进行热处理, 结果如下:→硬度测量值、切削后外观、表 面处理后外观等均无异常发现 由此推断:本回异常无法再现, 属于偶发性异常制品在热处理过程中加热及保温时 间过长导致偶发性的脱碳不良参见附件:分析报告(通常品) 分析报告(异常品)1、因该异常现象需要切削后才能发现,广州二宫工 程内无法检出;2、异常发生前,客户OCD及敝司双方均对该异常现象 的检查和判定基准不明确,且经成分分析和晶粒 度分析与通常品无明显差异,所以将该异常误判为OK品,从而导致该异常品流出至最终客户处。
人的不安全行为分析及对策
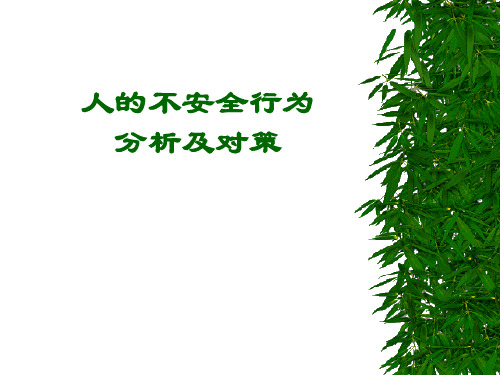
三、影响职工安全行为的心理分析
麻痹心理
其特点是作业者事先知道自己行为可能引发事故, 但由于各方面条件好,工作较顺利,就往往疏忽大意, 放松应有的警惕,产生麻痹心理。 在这种心理状态支配下,操作者往往认为这是“我常 干的工作”、“不知干过多少次”、“绝对不会有危
险”等而没有进行正常的检查或检查不细,按照老
五、预防不安全行为的对策
管理对策
劳动组织的合理化。 防止工作负荷过重引起的疲劳。 创造融洽和谐的人际工作环境。 加强班组安全建设,如班组安全自主管理的推进。
积极实施推广职业安全卫生管理体系。
加强安全生产责任制度的建立。
五、预防不安全行为的对策
法制对策
为预防生产事故,国家制定了一系列法规,企业
生理的影响
科学研究表明,人体的体力、情绪、智力呈正 弦曲线形式进行周期性变化。 所以当人的生理状态处于“低潮期”时,就应 该注意观察其行为是否执行各项规章制度,并
督促其严格按标准作业,以防事故发生。
做为管理者,应从群体的角度考虑, 而对一个群体的行为特征, 管理至关重 要。为了搞好太钢的安全工作,对事故 易发、多发区强化管理(C级以上危险源 点),消除不安全条件,对违章者加强教 育,杜绝“三违”,这样能产生好的效 果,减少安全事故的发生。
生产作业工过程事故人的不安全行为物的不安全状态管理失误事故隐患环境因素的影响事故模型图精神不集中麻痹大意好奇乱动不佩戴或不正确佩戴劳动防护用品使用不安全的工具不按规定的速度进行作业超速作业超速行车超速传递在不安全处逗留电力高压区起重机下高辐射区在狭窄的场所进行作业绑扎车皮狭窄的检修区域拜金心理侥幸心理侥幸型心理泛指人们在实际生产过程中图省事怕麻烦走捷径置安全法律法规和规程规章制度于不顾违章操作企图获得成功的心理状态
- 1、下载文档前请自行甄别文档内容的完整性,平台不提供额外的编辑、内容补充、找答案等附加服务。
- 2、"仅部分预览"的文档,不可在线预览部分如存在完整性等问题,可反馈申请退款(可完整预览的文档不适用该条件!)。
- 3、如文档侵犯您的权益,请联系客服反馈,我们会尽快为您处理(人工客服工作时间:9:00-18:30)。
对
反
周 期 月
1. 生管物控人员应随时注意各项料品库存之情 避免购入过量之库存, 况,避免购入过量之库存, 避免购入过量之库存 且控制各项材料入厂 之时机,缩短材料库存之时间。 之时机,缩短材料库存之时间。 2. 加强仓库管理人员之职能教育使其能依规定 收发料品。 收发料品。
因
真因:1.仓库空间不足,材料无法分类归位, 多种类似之材料以堆叠方式,易造 成盘点之失误. 2.材料种类繁多,协助人员未完全认 识所有材料造成误盘. 3.仓库人员未依照发料规定依单发 料,造成料帐不符.
● ●
10 5
00/11 00/12 01/01 01/02 01/03 01/04 01/05
处
发 2.建立供应商资料库,增加供料来源 避免单一供料 建立供应商资料库 增加供料来源 建立供应商资料库 增加供料来源,避免单一供料 所产生之问题。 所产生之问题。 防 止
握
交期太短 厂商缺失 采购疏失 交通因素 物控疏失 合 计
握
00/12 月高达 65 件属异常
真
基 准
30 件
漏 盘 误 盘 登帐错误 合 计
11 月 15 10 9 34
12 月 30 25 10 65
差异 15 15 1 31
理
盘点前召开盘点说明会,让协盘人员能充分了 防 3. 盘点前召开盘点说明会 让协盘人员能充分了 解认识每项材料。 解认识每项材料。 止 4. 每月定期施行仓管人员职能教育。 每月定期施行仓管人员职能教育。
异常分析对策表
●
○○年 ○○年 1 月
重 要 管 理 项 目 把 仓库原物 料盘点料 帐不符
60 50 40 30 ● 20 10
1. 扩大仓库之储放空间。 扩大仓库之储放空间。 再 处 发 2. 重新规划仓库储放方式。 重新规划仓库储放方式。
00/11 00/12 01/1 01/2 01/3 01/4 01/5
01/02 5 3 3 11 01/03 8 4 2 14 差异 3 1
理 1. 业务能加强订单之跟催 使客户能提前了解市 业务能加强订单之跟催,使客户能提前了解市 反 场状况增加长期订单之比率,使物控及采购有 场状况增加长期订单之比率 使物控及采购有 充足之备料时间. 充足之备料时间 2. 工程部加强对材料之开发 增加材料之来加材料之来源 低材料供商之影响度。 低材料供商之影响度。 省
策
省
主管_____________ 主管 担当_____________ 担当
真
基 准
10 件
对
-1 3
周 期 月
因
策
真 因 :1. 已 进 入 市 场 旺 季 , 紧 急 订 单增加,而材料交期无法配合 2. 厂商本身之产能不足,无法准 时交货.
主管_____________ 主管
担当_____________ 担当
单位:制造部 生管课 单位 制造部(生管课 制造部 生管课)
单位:制造部 生管课 单位 制造部(生管课 制造部 生管课)
异常分析对策表
30 25 20 15 ● ● ●
○○年 ○○年 3 月
重 要 管 理 项 目 把 原物料未 能及时入 厂件数
1.物控提出材料预估用量, 物控提出材料预估用量, 物控提出材料预估用量 请厂商提前备料建立库 再 存缩短材料交期。 存缩短材料交期。