3新型干法回转窑设计参数节能优化及传动功率计算分析探讨(会议投稿)
新型干法回转窑系统的节能提产改造
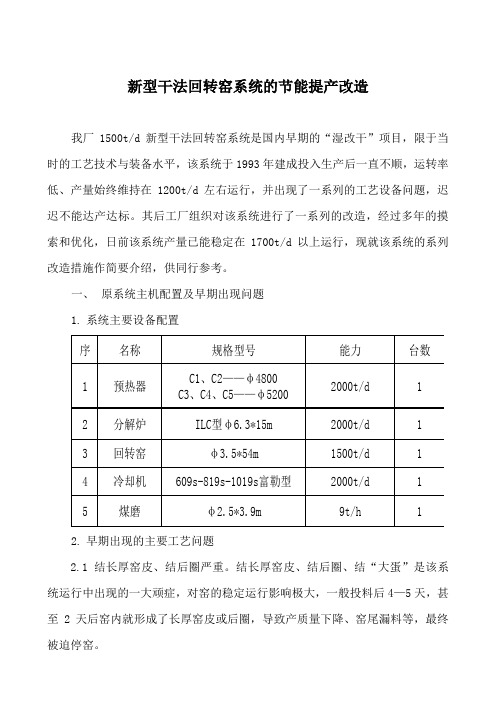
新型干法回转窑系统的节能提产改造我厂1500t/d新型干法回转窑系统是国内早期的“湿改干”项目,限于当时的工艺技术与装备水平,该系统于1993年建成投入生产后一直不顺,运转率低、产量始终维持在1200t/d左右运行,并出现了一系列的工艺设备问题,迟迟不能达产达标。
其后工厂组织对该系统进行了一系列的改造,经过多年的摸索和优化,日前该系统产量已能稳定在1700t/d以上运行,现就该系统的系列改造措施作简要介绍,供同行参考。
一、原系统主机配置及早期出现问题1.系统主要设备配置2.早期出现的主要工艺问题2.1 结长厚窑皮、结后圈严重。
结长厚窑皮、结后圈、结“大蛋”是该系统运行中出现的一大顽症,对窑的稳定运行影响极大,一般投料后4—5天,甚至2天后窑内就形成了长厚窑皮或后圈,导致产质量下降、窑尾漏料等,最终被迫停窑。
2.2 窑尾上升烟道结皮严重,严重影响了窑内通风。
2.3 一级筒出口温度高,通常达到370℃以上;气体粉尘浓度大,高达215g/Nm3。
2.4 篦冷机冷却效果差、运转率低、自身故障频繁,出篦冷机熟料温度高达150℃以上。
2.5 喂煤不稳定,波动幅度大且频繁,常出现断煤。
2.6 熟料产质量较差。
二、改造措施1.篦冷机的改造利用原有的水平推动式篦冷机框架及主梁,改为充气梁式篦冷机。
在高温区采用“固定式充气梁”装置最大的优点是大大降低了热端篦床的机械故障率,充分保证了篦冷机的运转率。
由于对窑下料口区域的篦床采用“固定式充气梁"装置,热熟料易于堆积,虽可调节冷却风量来对积料厚度加以控制,但为了防止堆“雪人”和大块熟料的堆积,在端墙安装了一组空气炮,按实际需要间断开炮,适时清理过多的积料,保证篦冷机安全稳定运行。
采用充气梁式冷却机,冷却风分布更为均匀,避免了“红河”现象,其热效率由原来的50—60%提高了到70%以上,三次风温提高了300℃左右。
2.分解炉的改造分解炉的改造与窑尾、冷却机等系统是密不可分的,因为原分解炉(如图1)的结构缺陷,物料在炉内停留时间过短,入窑分解率低,同时只靠窑尾废气不能把四级筒的来料完全带入炉内,一部分直接短路入窑,而为保证熟料质量,窑头必然加大燃煤量,这样又造成了窑尾温度过高、上升烟道结皮、窑内结后圈、窑内通风不良等不正常现象。
回转窑技术参数
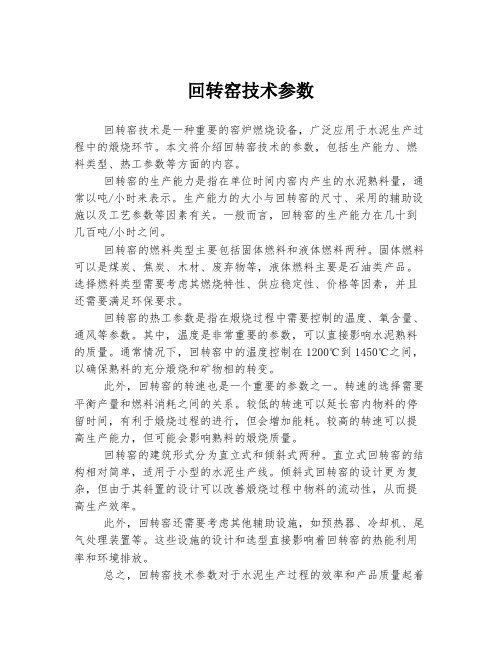
回转窑技术参数回转窑技术是一种重要的窑炉燃烧设备,广泛应用于水泥生产过程中的煅烧环节。
本文将介绍回转窑技术的参数,包括生产能力、燃料类型、热工参数等方面的内容。
回转窑的生产能力是指在单位时间内窑内产生的水泥熟料量,通常以吨/小时来表示。
生产能力的大小与回转窑的尺寸、采用的辅助设施以及工艺参数等因素有关。
一般而言,回转窑的生产能力在几十到几百吨/小时之间。
回转窑的燃料类型主要包括固体燃料和液体燃料两种。
固体燃料可以是煤炭、焦炭、木材、废弃物等,液体燃料主要是石油类产品。
选择燃料类型需要考虑其燃烧特性、供应稳定性、价格等因素,并且还需要满足环保要求。
回转窑的热工参数是指在煅烧过程中需要控制的温度、氧含量、通风等参数。
其中,温度是非常重要的参数,可以直接影响水泥熟料的质量。
通常情况下,回转窑中的温度控制在1200℃到1450℃之间,以确保熟料的充分煅烧和矿物相的转变。
此外,回转窑的转速也是一个重要的参数之一。
转速的选择需要平衡产量和燃料消耗之间的关系。
较低的转速可以延长窑内物料的停留时间,有利于煅烧过程的进行,但会增加能耗。
较高的转速可以提高生产能力,但可能会影响熟料的煅烧质量。
回转窑的建筑形式分为直立式和倾斜式两种。
直立式回转窑的结构相对简单,适用于小型的水泥生产线。
倾斜式回转窑的设计更为复杂,但由于其斜置的设计可以改善煅烧过程中物料的流动性,从而提高生产效率。
此外,回转窑还需要考虑其他辅助设施,如预热器、冷却机、尾气处理装置等。
这些设施的设计和选型直接影响着回转窑的热能利用率和环境排放。
总之,回转窑技术参数对于水泥生产过程的效率和产品质量起着重要的作用。
了解回转窑技术参数的基本原理,对于提高生产效率、降低能耗以及减少环境污染具有重要的意义。
新型干法回转窑的设计与增产节能的参数选择

新型干法回转窑的设计与增产节能——从技术进步谈回转窑设计操作参数的合理选择前言:从上世纪80年代我们研究新型干法(NSP)回转窑产量和规格参数的合理选择时,一般采用国内外相关窑型的产量和规格参数进行数学回归法或统计分析等方法,结合国情、厂情来比较选择确定。
早期在2000t/d窑外分解系统技术引进报价中,国外公司对窑规格、参数报价差异较大。
(见表一)国内外部分厂商日产2000t/d窑报价规格参数表一当时国产第一台(江西)2000t/d水泥生产线,其窑的规格为φ4.0×60m,L/D=15,斜度3.5%,最高转速3.2r/min,单位有效容积产量3.27t/m3·D。
经过20多年的努力,至今我国窑外分解系统生产工艺技术装备已趋于成熟,同规格窑系统产量不断突破,目前φ4.0×60m窑保证产量为2500t/d,实际可达到2700~2800t/d,系统产量提高35~40%,单位有效容积产量达到4.59t/m3·D,相关的斜度、转速、装机功率及窑内物料负荷率、物料在窑内停留时间等设计参数均有较大变化,笔者在实践-认识-再实践的基础上,对窑的合理设计、操作参数等作一些探讨。
1、回转窑在新型干法烧成系统中的地位和作用首先,回转窑是NSP烧成系统中的一个组成部分,它的作用是把在预热器、分解炉内已经大部分分解的生料进行煅烧,生成合格的水泥熟料。
从物理、化学反应来说:生料在窑尾预热器、分解炉系统中完成预热、脱水和绝大部分分解反应后进入回转窑内,在一定的高温条件下完成形成各种熟料矿物的化学反应和物理化学反应(固相反应),并使晶体得到一定程度的发育生长,再稍经冷却后排出窑外。
从传热学的角度来说,窑内物料因入窑生料表观分解率为90~95%,分解吸热反应所需的热量很少,公斤熟料约200~100千焦,物料升温吸热量约为450~500千焦,而熟料矿物形成是以放热反应为主,设熟料中C2S占0.20,C3S占0.60,C3A占0.08,C4AF占0.10,反应过程放热量约为655千焦。
新型干法水泥回转窑工艺及设备概述
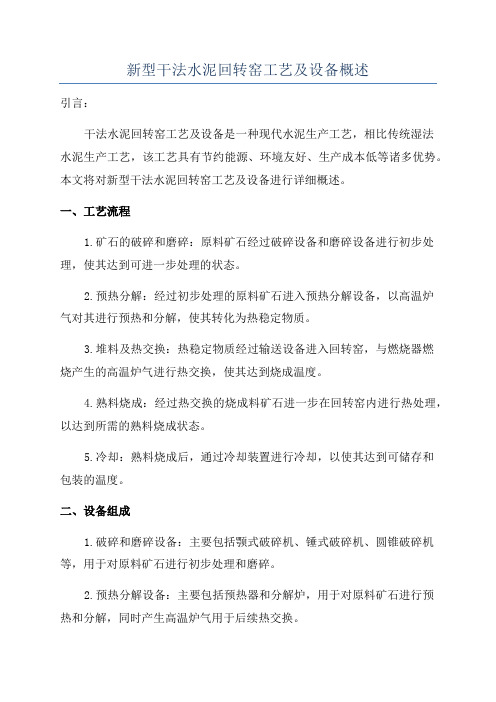
新型干法水泥回转窑工艺及设备概述引言:干法水泥回转窑工艺及设备是一种现代水泥生产工艺,相比传统湿法水泥生产工艺,该工艺具有节约能源、环境友好、生产成本低等诸多优势。
本文将对新型干法水泥回转窑工艺及设备进行详细概述。
一、工艺流程1.矿石的破碎和磨碎:原料矿石经过破碎设备和磨碎设备进行初步处理,使其达到可进一步处理的状态。
2.预热分解:经过初步处理的原料矿石进入预热分解设备,以高温炉气对其进行预热和分解,使其转化为热稳定物质。
3.堆料及热交换:热稳定物质经过输送设备进入回转窑,与燃烧器燃烧产生的高温炉气进行热交换,使其达到烧成温度。
4.熟料烧成:经过热交换的烧成料矿石进一步在回转窑内进行热处理,以达到所需的熟料烧成状态。
5.冷却:熟料烧成后,通过冷却装置进行冷却,以使其达到可储存和包装的温度。
二、设备组成1.破碎和磨碎设备:主要包括颚式破碎机、锤式破碎机、圆锥破碎机等,用于对原料矿石进行初步处理和磨碎。
2.预热分解设备:主要包括预热器和分解炉,用于对原料矿石进行预热和分解,同时产生高温炉气用于后续热交换。
3.回转窑:为整个工艺的核心设备,主要由筒体、支承装置、传动装置、燃烧装置等组成。
回转窑内的烧成料矿石在高温环境下进行热处理。
4.冷却设备:主要包括冷却机和冷却器,用于对熟料烧成后的产物进行冷却。
除了上述核心设备外,还需要配套的输送设备、除尘设备、燃料供应系统等进行辅助。
三、优势与前景1.节能环保:相比于传统湿法水泥生产工艺,新型干法水泥回转窑工艺具有更低的能耗和排放,减少了燃料的消耗和烟气排放量,符合现代环保要求。
2.生产成本低:新型干法水泥回转窑工艺采用了高温炉气热交换的方式,可以充分利用烟气热能,降低能源消耗,从而降低生产成本。
3.适应性强:新型干法水泥回转窑工艺适用于不同原料的水泥生产,可以根据不同的原料特性进行调整和优化,提高生产效率和产品质量。
4.市场前景广阔:在国家加大环保政策的背景下,新型干法水泥回转窑工艺将成为水泥生产的主流工艺,具有广阔的市场发展前景。
(整理)回转窑技术参数.

(整理)回转窑技术参数.回转窑是用于生产水泥、石灰、铁精矿和活性石灰等物料的重要设备。
它具有体积大、适用范围广、热量利用率高等特点,被广泛应用于建材、冶金、化工等行业。
回转窑的技术参数涉及到其结构、尺寸、能耗、生产能力等方面,下面我们来详细介绍一下。
1. 结构和尺寸:回转窑的结构主要包括筒体、轴承、齿轮环、轴承座等部件。
筒体通常采用直径较大的圆筒形状,长度根据生产需要而定。
一般来说,回转窑的直径在2.5米到7米之间,长度可以达到70米以上。
2. 制备能耗:回转窑的能耗主要包括燃烧燃料所需的热量和电力消耗。
不同的燃料和物料具有不同的热值和消耗量。
一般来说,燃烧煤粉需要的热量约为2800-3000千卡/千克,燃烧重油约为10000千卡/千克,燃烧天然气约为8300千卡/立方米。
而电力消耗根据生产能力和设备配置而定,一般为50-70千瓦时/吨物料。
3. 生产能力:回转窑的生产能力主要受到物料性质、窑筒尺寸和转速等因素的影响。
一般来说,水泥产线上的回转窑生产能力为1000-8000吨/天,石灰产线上的回转窑生产能力为100-1000吨/天。
生产能力还可通过改变生产线的运行时间和窑筒转速来调节。
4. 窑筒转速:回转窑的转速对于物料煅烧的均匀性和产量具有重要影响。
一般来说,水泥生产中回转窑的转速为0.3-2转/分钟,石灰生产中的回转窑转速为0.25-0.5转/分钟。
转速过高会导致物料不充分煅烧,转速过低则会影响生产效率。
5. 窑炉热效率:回转窑的热效率是评估其能耗高低和燃料利用率的重要指标。
热效率取决于回转窑的结构设计、燃料种类和燃烧系统的性能等因素。
一般来说,回转窑的热效率可达到60%-80%。
总结:回转窑是一种常见的重要工业设备,其技术参数包括结构和尺寸、能耗、生产能力、窑筒转速和热效率等方面。
了解这些参数可以帮助我们更好地使用和选择回转窑,提高生产效率和降低能耗。
同时,不同行业和不同生产要求可能会有一些特殊的技术参数,需要根据实际情况进行调整和优化。
日产6500吨新型干法水泥回转窑结构设计

新型干法水泥回转窑结构设计1. 引言新型干法水泥回转窑作为水泥生产中的关键设备,其结构设计直接影响到生产效率和产品质量。
本文将从深度和广度两个方面,全面评估日产6500吨新型干法水泥回转窑的结构设计,并据此撰写一篇有价值的文章。
2. 结构设计概况日产6500吨新型干法水泥回转窑的结构设计应考虑以下几个方面:- 转筒结构:转筒是回转窑的主体部分,其结构设计应考虑到耐磨、耐高温、耐腐蚀等因素。
- 带式环节:带式环节作为转筒的内衬部分,其结构应具有良好的耐磨性和耐高温性。
- 驱动装置:驱动装置是确保回转窑正常运转的关键部分,其结构设计应保证稳定、高效、节能。
3. 结构设计深度探讨对于转筒结构的设计可以考虑使用耐火材料进行内衬,以增加其耐磨和耐高温性能。
在结构设计中可以加入冷却装置,以降低转筒温度,延长使用寿命。
带式环节的结构设计可以采用防火防爆材料,以提高其耐磨性和耐高温性能。
对于驱动装置的设计,则可以考虑使用先进的液力偶合器和交流变频调速技术,以保证其运转稳定、高效、节能。
4. 结构设计广度探讨从广度方面来看,新型干法水泥回转窑结构设计不仅需要考虑到生产设备本身的性能,还需要考虑到与其他生产设备的配套性能。
在结构设计中,可以考虑与生料磨机、熟料磨机等设备的衔接和配合,以最大程度地提高生产效率和产品质量。
5. 总结和回顾日产6500吨新型干法水泥回转窑的结构设计需要全面考虑转筒、带式环节和驱动装置的设计,并且还需要考虑到与其他生产设备的配套性能。
在实际生产中,需要密切关注结构设计的耐磨性、耐高温性、耐腐蚀性,并不断改进和优化结构设计,以适应水泥生产的需求。
6. 个人观点和理解作为水泥生产设备的重要组成部分,新型干法水泥回转窑的结构设计直接影响到水泥生产的效率和产品质量。
在结构设计中,应充分考虑到不同材料的性能及其在高温、高压条件下的表现,以确保设备的长期稳定运行。
还需要不断引入先进的技术和材料,以提高设备的性能和效率。
5新型干法回转窑设计参数优化及图解应用
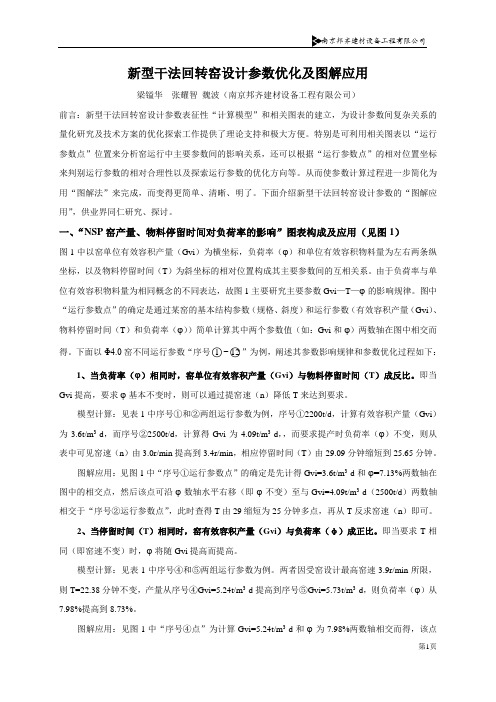
新型干法回转窑设计参数优化及图解应用梁镒华张耀智魏波(南京邦齐建材设备工程有限公司)前言:新型干法回转窑设计参数表征性“计算模型”和相关图表的建立,为设计参数间复杂关系的量化研究及技术方案的优化探索工作提供了理论支持和极大方便。
特别是可利用相关图表以“运行参数点”位置来分析窑运行中主要参数间的影响关系,还可以根据“运行参数点”的相对位置坐标来判别运行参数的相对合理性以及探索运行参数的优化方向等。
从而使参数计算过程进一步简化为用“图解法”来完成,而变得更简单、清晰、明了。
下面介绍新型干法回转窑设计参数的“图解应用”,供业界同仁研究、探讨。
一、“NSP窑产量、物料停留时间对负荷率的影响”图表构成及应用(见图1)图1中以窑单位有效容积产量(Gvi)为横坐标,负荷率(φ)和单位有效容积物料量为左右两条纵坐标,以及物料停留时间(T)为斜坐标的相对位置构成其主要参数间的互相关系。
由于负荷率与单位有效容积物料量为相同概念的不同表达,故图1主要研究主要参数Gvi—T—φ的影响规律。
图中“运行参数点”的确定是通过某窑的基本结构参数(规格、斜度)和运行参数(有效容积产量(Gvi)、物料停留时间(T)和负荷率(φ))简单计算其中两个参数值(如:Gvi和φ)两数轴在图中相交而得。
下面以Φ4.0窑不同运行参数“序号○1~○12”为例,阐述其参数影响规律和参数优化过程如下:1、当负荷率(φ)相同时,窑单位有效容积产量(Gvi)与物料停留时间(T)成反比。
即当Gvi提高,要求φ基本不变时,则可以通过提窑速(n)降低T来达到要求。
模型计算:见表1中序号①和②两组运行参数为例,序号①2200t/d,计算有效容积产量(Gvi)为3.6t/m3·d,而序号②2500t/d,计算得Gvi为4.09t/m3·d,,而要求提产时负荷率(φ)不变,则从表中可见窑速(n)由3.0r/min提高到3.4r/min,相应停留时间(T)由29.09分钟缩短到25.65分钟。
回转窑技术参数3篇

回转窑技术参数第一篇:回转窑技术概述及原理回转窑是一种重要的烧结设备,广泛应用于水泥、冶金、化工等行业。
其原理是将生料进入回转窑内进行高温烧结,使之变为熟料。
回转窑的生产能力较高,烧成的熟料质量稳定,且可适应多种生料的烧结要求。
下面就回转窑的技术参数进行详细介绍。
1. 回转窑的结构回转窑由筒体、支撑装置、驱动装置、尾气处理装置和控制系统等组成。
筒体为柱体形,内部衬有隔热层和烧成层,长度一般为50-200米,直径为3-6米。
2. 回转窑的烧成过程回转窑烧成分为预热、分解、煅烧和冷却四个阶段。
生料通过燃烧室和预热器进入窑筒,在预热器中进行预热,再进入回转窑。
窑内温度约为1450℃,生料煅烧至熟料形成,然后经过冷却区域进行冷却抛出。
3. 回转窑的运行参数(1)生料的进料速度:生料进料速度是回转窑操作的一个关键参数,其值一般控制在75-100 t/h。
当生料进入窑筒,窑速一定要与生料进料速度匹配,以保证在窑内停留的时间达到烧成的需要。
(2)回转窑转速:回转窑转速是影响烧成质量的另一个参数。
正常情况下,回转窑的转速为0.5~4.0 rpm。
通常建议粘结性较强的下料采用中速,而粘结性弱的下料采用高速,以避免生料坠落、结块等现象。
(3)窑筒倾角:窑筒倾角指与水平面的夹角,是影响回转窑烧成质量的重要参数之一。
窑筒倾角通常为1~3°,过小或过大都会影响烧成质量和烧结稳定性。
(4)烟气流量:烟气流量和氧气含量是回转窑烧成过程的控制参数之一,其值应约为生料进料量的1~2倍。
过小会导致熟料不完全烧成,过大会降低热量利用率。
第二篇:回转窑的控制系统回转窑的控制系统包括回转窑的自动化控制、设备监控、生产过程管理、统计分析和数据通信等。
下面列举了回转窑的主要控制参数。
1. 序列化控制系统回转窑的控制系统采用序列化控制系统,主要是通过PLC 控制,将所有的控制接口、传感器及控制参数进行程序化,以实现自动化控制和高精度的调节。
对新型干法水泥窑合理操作的浅谈(周李镇毕业论文第二次)

a料变窑速变。 入窑生料波动大,当料于耐火窑内煅烧困难时,应适当减料,放慢窑速,以防止熟料欠烧甚至窜生料,当料易烧,窑内熟料结粒粗大,窑前发亮,窑电流升高时,应及时加料将窑速提起,特别应注意加料时要首先提窑速,才能保证系统热工稳定,保持窑内适当的物料填充率。
b薄料快转。在正常的生产情况下,应保持薄料快转,以增加物料的翻动频率,有利于热交换;同时降低窑内物料填充率,减少窑内通风阻力,有利于煤粉完全燃烧,减少窑尾烟室缩口结皮。
毕业论文
对新型干法水泥窑合理操作的浅谈
摘要:新型干法水泥生产中,窑外预分解窑系统的生产正常与优化烧成系统的操作、强化系统的工艺管理有关,影响热工制度的可变因素较多,系统操作要有预见性,前后兼顾,熟悉并了解设计中所设置的操作控制手段的目的和意义,针对生产中出现的问题及时、正确地去调节,从而使整个系统尽快恢复正常,达到优质、高产、低耗的目的。中材萍乡水泥有限公司现拥有Ф4*60m带五级预分解系统日产2500吨熟料及Ф4.8*72m带五级双系列预分解系统日产4500吨熟料的新型干法生产线二条,本文针对中材萍乡水泥有限公司预分解窑生产过程中出现的典型异常情况进行了合理操作处理,并提出一些体会。
关键词:预分解窑、工艺管理、喷煤管、操作处理
绪论ﻩ
1.系统用风ﻩ3
2.煤的比例ﻩ4
5、风、煤、料和窑速的兼顾调整ﻩ5
二、优化烧成系统操作5
回转窑技术参数范文

回转窑技术参数范文回转窑是一种常用于生产水泥的设备,其通过回转的方式将原料均匀地加热到高温,完成煅烧过程。
以下是回转窑的一些常见的技术参数。
1.技术性能参数:(1)回转窑的直径:回转窑的直径通常在3-6米之间,根据生产能力的不同可以选择不同尺寸的回转窑。
(2)回转窑的长度:回转窑的长度通常在40-200米之间,长度的选择也取决于生产能力和所需的煅烧时间。
(3)回转窑的倾角:回转窑的倾角是指回转窑与水平面的夹角,倾角的选择通常在3-5度之间,它直接影响窑内的物料流动和煅烧效果。
(4)回转窑的转速:回转窑的转速通常在0.1-2转/分钟之间,转速的选择需要根据生产过程的要求和窑内物料的特性来确定。
2.燃料和能源参数:(1)燃料类型:回转窑可以使用多种燃料来提供热能,包括煤、天然气、重油等。
不同的燃料具有不同的能量含量和燃烧特性,需要根据实际情况选择。
(2)燃料消耗量:燃料消耗量是生产单位水泥所需的燃料量,通常以千克燃料/吨水泥的形式来表示。
不同的燃料消耗量直接影响到生产成本和环境影响。
(3)能耗:能耗指的是生产单位水泥所需要的能量,通常以千焦耳/吨水泥的形式来表示。
回转窑的能耗主要与燃料的选择、窑体结构和煅烧过程的控制有关。
3.生产能力参数:(1)生产能力:生产能力是指设备每天可以生产的水泥量,通常以吨/天或吨/小时来表示。
回转窑的生产能力取决于窑体的尺寸和煅烧过程的控制。
(2)生产效率:生产效率是指在单位时间内完成的生产任务,通常以吨/小时或吨/焦耳来表示。
提高生产效率可以降低生产成本和能耗。
(3)煅烧时间:煅烧时间是指窑内物料从进入回转窑到完成煅烧所经历的时间,通常在20-200分钟之间。
煅烧时间的选择需要根据原料的特性和生产任务来确定。
以上是回转窑常见的技术参数,不同的回转窑型号和制造商可能会有细微的差别,实际应用中需要根据具体情况进行选择和调整。
回转窑技术参数

回转窑技术参数回转窑是一种常见的水泥生产设备,广泛应用于熟料的烧结过程。
它以其高效、节能、环保等特点而受到业界的普遍好评。
本文将从不同的角度详细介绍回转窑的技术参数,帮助读者更好地了解和使用这一设备。
首先,我们来介绍一下回转窑的结构。
回转窑一般由筒体、滑轮、传动装置、排烟机、燃烧设备等组成。
其中,筒体是回转窑的主体部分,它具有一定的倾角,并通过滑轮和传动装置实现旋转。
排烟机负责排除烟气,燃烧设备则提供燃料和热能。
这样的结构保证了回转窑的正常运转。
回转窑的技术参数包括长度、直径、回转速度等。
长度是指回转窑的整体长度,直径则是指回转窑的外径。
这两个参数通常与生产规模相关,不同规模的水泥生产线会有不同的长度和直径。
而回转速度则决定了熟料在回转窑内的停留时间,进而影响熟料的烧结质量。
回转窑的回转速度一般由电机和减速器控制,具体数值需要根据实际情况进行调整。
除了长度、直径和回转速度,回转窑的倾角也是一项重要的技术参数。
倾角决定了熟料在回转窑内的流动方式和停留时间。
合理的倾角可以保证熟料充分与燃料接触,从而提高燃烧效率和熟料的烧结质量。
通常情况下,回转窑的倾角会根据生产需要进行调整,最佳倾角可以通过实验和经验来确定。
此外,回转窑的烧成温度也是一个重要的技术参数。
熟料的烧结温度直接影响水泥的质量和性能。
过低的烧成温度会导致熟料未完全烧结,降低水泥的强度和耐久性;过高的烧成温度则可能导致水泥中的矿物质发生异常相变,影响水泥的品质。
因此,回转窑的烧成温度需要严格控制,常用的方法是通过调整燃料的供给量和燃烧器的设置来实现。
最后,回转窑的产能也是衡量其技术参数的一个重要指标。
产能通常用熟料的生产量或水泥的生产量来表示。
回转窑的产能受到多种因素的影响,包括回转窑的尺寸、燃烧设备的性能、熟料的组成等。
提高回转窑的产能是提高生产效率的关键之一,可以通过优化生产工艺、提高设备的使用率等方式来实现。
综上所述,回转窑的技术参数涉及长度、直径、回转速度、倾角、烧成温度和产能等多个方面。
回转窑技术参数范文
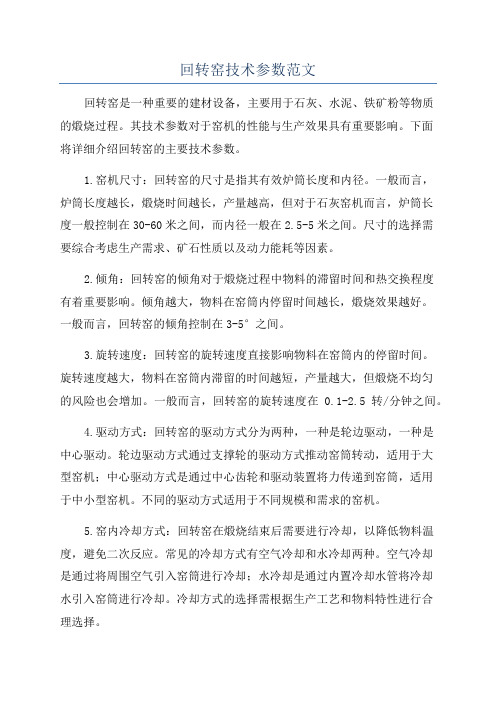
回转窑技术参数范文回转窑是一种重要的建材设备,主要用于石灰、水泥、铁矿粉等物质的煅烧过程。
其技术参数对于窑机的性能与生产效果具有重要影响。
下面将详细介绍回转窑的主要技术参数。
1.窑机尺寸:回转窑的尺寸是指其有效炉筒长度和内径。
一般而言,炉筒长度越长,煅烧时间越长,产量越高,但对于石灰窑机而言,炉筒长度一般控制在30-60米之间,而内径一般在2.5-5米之间。
尺寸的选择需要综合考虑生产需求、矿石性质以及动力能耗等因素。
2.倾角:回转窑的倾角对于煅烧过程中物料的滞留时间和热交换程度有着重要影响。
倾角越大,物料在窑筒内停留时间越长,煅烧效果越好。
一般而言,回转窑的倾角控制在3-5°之间。
3.旋转速度:回转窑的旋转速度直接影响物料在窑筒内的停留时间。
旋转速度越大,物料在窑筒内滞留的时间越短,产量越大,但煅烧不均匀的风险也会增加。
一般而言,回转窑的旋转速度在0.1-2.5转/分钟之间。
4.驱动方式:回转窑的驱动方式分为两种,一种是轮边驱动,一种是中心驱动。
轮边驱动方式通过支撑轮的驱动方式推动窑筒转动,适用于大型窑机;中心驱动方式是通过中心齿轮和驱动装置将力传递到窑筒,适用于中小型窑机。
不同的驱动方式适用于不同规模和需求的窑机。
5.窑内冷却方式:回转窑在煅烧结束后需要进行冷却,以降低物料温度,避免二次反应。
常见的冷却方式有空气冷却和水冷却两种。
空气冷却是通过将周围空气引入窑筒进行冷却;水冷却是通过内置冷却水管将冷却水引入窑筒进行冷却。
冷却方式的选择需根据生产工艺和物料特性进行合理选择。
6.燃料类型:回转窑的煅烧过程需要燃料提供热源。
常见的燃料类型有煤粉、石油焦、天然气等。
选用合适的燃料类型可以有效保证窑机的稳定性和生产效率。
7.动力消耗:回转窑的动力消耗是评估其性能的重要指标。
动力消耗包括机械动力、燃料消耗以及冷却系统的动力消耗。
优化回转窑技术参数可以有效降低动力消耗,提高生产效益。
除了上述技术参数外,回转窑的整体结构、进料方式、出料方式等也是需要考虑的因素。
回转窑有关参数计算方法

回转窑有关参数计算方法回转窑是水泥生产过程中的主要设备,其参数计算方法对于保证设备的正常运行和水泥生产的质量有着重要的影响。
下面我将从回转窑的设计参数、烧成过程中的参数计算以及操作参数的选择这三个方面,分别介绍回转窑的有关参数计算方法。
1.回转窑的设计参数计算回转窑的设计参数计算包括尺寸、转速和斜度等方面。
首先需要确定窑的内径,根据生产规模、水泥品种和材料性质等因素进行初步估算。
然后根据回转窑的长度和转速,计算膛线速度。
膛线速度是指窑身烧成区内壁表面上每单位长度的平均周向速度,是保证熟料在窑内能够停留足够时间进行热交换的重要参数。
通常,在一定的生产条件下,最佳的膛线速度范围为3.5-5.0 m/min,可以根据窑内原料的烧失率进行调整。
最后,根据回转窑的设计尺寸和转速,计算出窑体的最大斜度,以确保料层在回转窑内能够顺利前进,并最终产生熟料。
2.烧成过程中的参数计算烧成过程中的参数计算主要包括窑内燃烧状态的分析和熟料的烧成度计算。
燃烧状态的分析主要是为了保证窑内燃烧反应的正常进行和稳定燃烧的实现。
通过计算窑头处的剩余炭含量和窑尾处的氧含量,可以判断燃烧状态是否正常,并根据需要进行调整。
熟料的烧成度计算是评价烧成过程的关键指标之一,可以根据窑内熟料的大气侧质量、窑内热量补给和窑内大气侧质量流量等因素进行计算。
烧成度的计算结果可以帮助调整窑的操作参数,以达到最佳的烧成效果。
3.操作参数的选择回转窑的操作参数选择包括供料量、风量和回转窑的停留时间等方面。
供料量的选择要根据窑的设计尺寸、原料的粒度和特性以及烧成度的要求进行计算。
在供料量不变的情况下,适当调整物料的分层厚度可以改善窑内的热传导和物料的烧成情况。
风量的选择要根据窑内气氛状态、物料的烧成度和粉煤灰的含量等因素进行计算。
通过调整风量,可以改变窑内气氛的酸碱度,进而调整物料的烧成度和烧成质量。
而窑内停留时间的选择则要根据原料的性质、窑的设计参数和烧成过程的需求进行计算。
对新型干法回转窑系统的初步理解
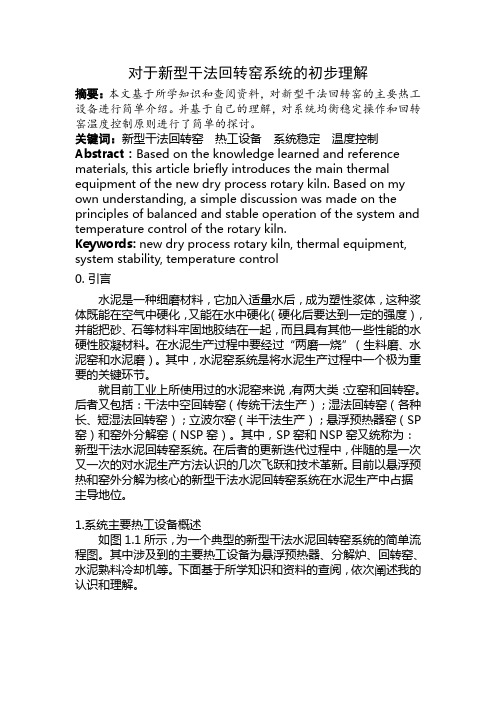
对于新型干法回转窑系统的初步理解摘要:本文基于所学知识和查阅资料,对新型干法回转窑的主要热工设备进行简单介绍。
并基于自己的理解,对系统均衡稳定操作和回转窑温度控制原则进行了简单的探讨。
关键词:新型干法回转窑热工设备系统稳定温度控制Abstract:Based on the knowledge learned and reference materials, this article briefly introduces the main thermal equipment of the new dry process rotary kiln. Based on my own understanding, a simple discussion was made on the principles of balanced and stable operation of the system and temperature control of the rotary kiln.Keywords: new dry process rotary kiln, thermal equipment, system stability, temperature control0.引言水泥是一种细磨材料,它加入适量水后,成为塑性浆体,这种浆体既能在空气中硬化,又能在水中硬化(硬化后要达到一定的强度),并能把砂、石等材料牢固地胶结在一起,而且具有其他一些性能的水硬性胶凝材料。
在水泥生产过程中要经过“两磨一烧”(生料磨、水泥窑和水泥磨)。
其中,水泥窑系统是将水泥生产过程中一个极为重要的关键环节。
就目前工业上所使用过的水泥窑来说,有两大类:立窑和回转窑。
后者又包括:干法中空回转窑(传统干法生产);湿法回转窑(各种长、短湿法回转窑);立波尔窑(半干法生产);悬浮预热器窑(SP 窑)和窑外分解窑(NSP窑)。
其中,SP窑和NSP窑又统称为:新型干法水泥回转窑系统。
回转窑技术参数
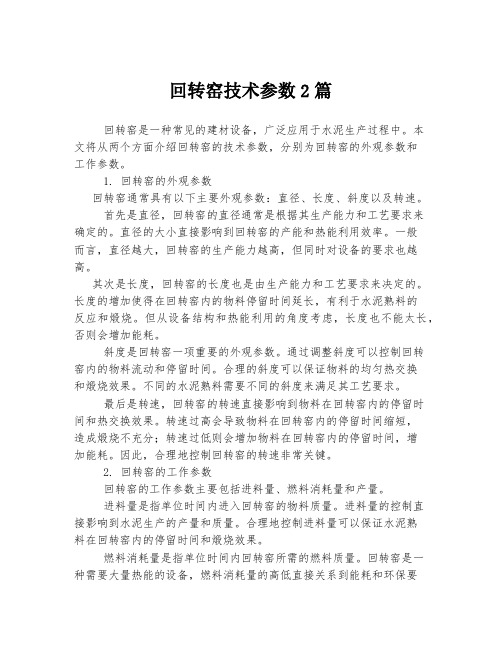
回转窑技术参数2篇回转窑是一种常见的建材设备,广泛应用于水泥生产过程中。
本文将从两个方面介绍回转窑的技术参数,分别为回转窑的外观参数和工作参数。
1. 回转窑的外观参数回转窑通常具有以下主要外观参数:直径、长度、斜度以及转速。
首先是直径,回转窑的直径通常是根据其生产能力和工艺要求来确定的。
直径的大小直接影响到回转窑的产能和热能利用效率。
一般而言,直径越大,回转窑的生产能力越高,但同时对设备的要求也越高。
其次是长度,回转窑的长度也是由生产能力和工艺要求来决定的。
长度的增加使得在回转窑内的物料停留时间延长,有利于水泥熟料的反应和煅烧。
但从设备结构和热能利用的角度考虑,长度也不能太长,否则会增加能耗。
斜度是回转窑一项重要的外观参数。
通过调整斜度可以控制回转窑内的物料流动和停留时间。
合理的斜度可以保证物料的均匀热交换和煅烧效果。
不同的水泥熟料需要不同的斜度来满足其工艺要求。
最后是转速,回转窑的转速直接影响到物料在回转窑内的停留时间和热交换效果。
转速过高会导致物料在回转窑内的停留时间缩短,造成煅烧不充分;转速过低则会增加物料在回转窑内的停留时间,增加能耗。
因此,合理地控制回转窑的转速非常关键。
2. 回转窑的工作参数回转窑的工作参数主要包括进料量、燃料消耗量和产量。
进料量是指单位时间内进入回转窑的物料质量。
进料量的控制直接影响到水泥生产的产量和质量。
合理地控制进料量可以保证水泥熟料在回转窑内的停留时间和煅烧效果。
燃料消耗量是指单位时间内回转窑所需的燃料质量。
回转窑是一种需要大量热能的设备,燃料消耗量的高低直接关系到能耗和环保要求。
通过优化燃料选择和燃烧控制,可以降低燃料消耗量,提高能源利用效率。
产量是指回转窑生产水泥熟料的质量和数量。
产量的提高需要在保证煅烧质量的前提下,通过优化工艺和设备参数来实现。
合理的工艺参数和设备运行可以提高水泥生产的产量和效益。
综上所述,回转窑的技术参数主要包括外观参数和工作参数。
外观参数包括直径、长度、斜度和转速,而工作参数包括进料量、燃料消耗量和产量。
新型干法水泥回转窑系统

在分解炉上部设置了一个涡流室, 使炉气呈螺旋形出炉。 将分解炉与预热器之间的联接管道延长---相当于增加了分解炉的容积),其效果是延长了生料在分解炉内的停留时间,使得碳酸盐的分解程度更高,更重要的是有利于使用燃烧速度较慢的一些燃料。
主要改进:
(2) RSP型炉:
RSP型炉: 结构:左部:混合室(MC室) 右部:上部旋风预燃室(SB炉) 下部涡旋分解室(SC炉) 特点: 燃料:在旋风预燃室喷入,与热空气直接接触而燃烧, 燃烧效果好。 生料:从SC室喂入,被三次风分散。 气体: 窑气经上升管道喷腾进入,热空气从SC炉的内侧 以切线方向送入,两股气流一起进入混合室。 优点:对燃料适应性强 缺点:结构比较复杂,系统通风调节比较困难,流动阻力损失大。
旋风筒改进的几个方面: 1)旋风筒入口或出口处增设导向叶片; 2)旋风筒筒体结构的改进; 3)旋风筒进风口与排气管(内筒)结构的改进; 4)旋风筒下料口结构的改进 5)旋风筒旋流方式的改进
特点:进风口截面由矩形改为多边形,筒体改为双柱双锥的组
单击此处添加小标题
合,柱体直径相对减小,内筒直径加大,插入深度减小等。
02
燃烧带单位截面面积、单位时间内所承受的热量
3)回转窑内燃烧带的截面热力强度(燃烧带的截面热负荷):
01
Qsh---水泥熟料理论热耗(在没有热量损失和物损失时,由0℃的干生料烧成1kg水泥熟料所需要的热量(kJ/kg熟料)
6)回转窑内燃烧带的空气过剩系数 根据生产经验以煤粉为燃料的水泥回转窑 α范围较合理 7)回转窑内的热效率
单击添加大标题
1.2悬浮预热器
旋风预热器的工作原理 生料粉在废气中分散与悬浮 气、固之间换热 (在联结管道内完成) 气、固相的分离,生料粉的收集 (在旋风筒内完成)
回转窑传动功率计算
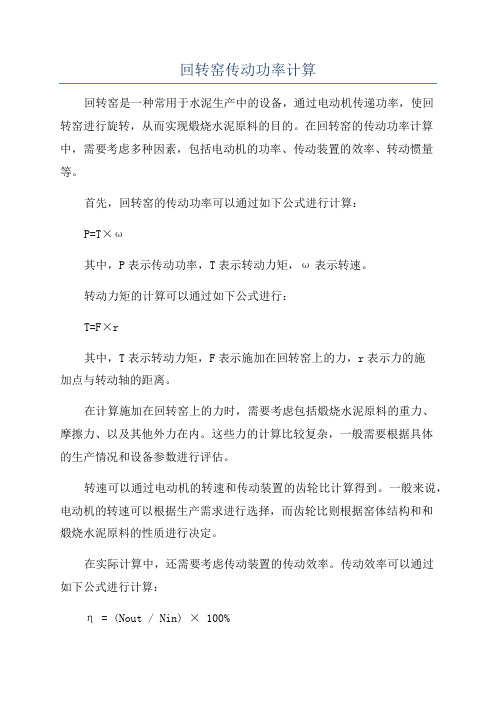
回转窑传动功率计算回转窑是一种常用于水泥生产中的设备,通过电动机传递功率,使回转窑进行旋转,从而实现煅烧水泥原料的目的。
在回转窑的传动功率计算中,需要考虑多种因素,包括电动机的功率、传动装置的效率、转动惯量等。
首先,回转窑的传动功率可以通过如下公式进行计算:P=T×ω其中,P表示传动功率,T表示转动力矩,ω表示转速。
转动力矩的计算可以通过如下公式进行:T=F×r其中,T表示转动力矩,F表示施加在回转窑上的力,r表示力的施加点与转动轴的距离。
在计算施加在回转窑上的力时,需要考虑包括煅烧水泥原料的重力、摩擦力、以及其他外力在内。
这些力的计算比较复杂,一般需要根据具体的生产情况和设备参数进行评估。
转速可以通过电动机的转速和传动装置的齿轮比计算得到。
一般来说,电动机的转速可以根据生产需求进行选择,而齿轮比则根据窑体结构和和煅烧水泥原料的性质进行决定。
在实际计算中,还需要考虑传动装置的传动效率。
传动效率可以通过如下公式进行计算:η = (Nout / Nin) × 100%其中,η表示传动效率,Nout表示输出功率,Nin表示输入功率。
传动装置一般采用齿轮传动,其效率可以在90%以上。
同时,还需要考虑到传动装置自身的转动惯量,以及回转窑本身的转动惯量。
转动惯量可以通过以下公式进行计算:J=m×r^2其中,J表示转动惯量,m表示物体的质量,r表示质心到转轴的距离。
在回转窑传动功率计算中,还需要考虑煅烧过程中的能量损失,包括机械振动、传热过程中的能量损失等。
这些能量损失的计算需要根据具体的工艺条件和设备参数进行评估。
总之,回转窑传动功率的计算涉及到多个因素的综合考虑,包括转动力矩、转速、传动效率、转动惯量以及能量损失等。
计算的结果可以用于电动机功率的选择、传动装置的设计以及生产过程中的能源消耗评估等方面。
再谈新型干法回转窑技术进步

再谈新型干法回转窑技术进步——提高过渡带升温速率优化烧成热工制度梁镒华、魏波(南京邦齐建材设备工程有限公司)新型干法回转窑内熟料煅烧过程的质量控制是整个生产过程中决定熟料产、质量的关键和中心环节。
而窑内合理的热工制度又是使物料完成各种化学反应和获得良好熟料矿物晶体结构是质量控制的重中之重。
怎样的窑型热工制度更适合优质熟料的生产呢?当前有传统观点认为:斜度大物料运动速度快,斜度小转速快物料翻动有利物料温度均匀是起决定作用的,反之不均匀会影响熟料烧成效果,因此建议斜度还是3.5%为好。
对长径比认为窑长一点更稳妥,产量也有保证;而新的设计理念提出是“大斜度、大直径、小长径比”能更好满足熟料烧成要求,特别对节能更为有利,前文已作论证,下面我们再从窑内烧成热工制度来分析。
现代新型干法窑内熟料煅烧过程主要化学反应和熟料矿物生成机理研究成果表明:随技术进步入窑物料分解率的提高达95%以上,分解带很短甚至逐步消失,过渡带升温速率对后续快速烧成和快速冷却对生产优质熟料具有至关重要的影响。
因为在该带固相反应生成的初生态C2S微晶和存在大量新生态CaO具有高活性和很强的反应能力,如果不能迅速升温滞留时间过长,延时进入烧成带则这些发育不完全的晶体会有充分时间和温度条件发育成为完整的大晶体,使活化能和反应能力下降,给后续烧成向C3S转化带来困难。
操作工为减少出窑熟料中f-CaO含量,就必须提高烧成带温度和延长停留时间,这样烧出的熟料矿物晶体往往大而完整,从而导致熟料强度和易磨性变差并伴随能耗的增加。
另有实验研究表明,物料升温速率对熟料矿物形成的影响:当采用600~800℃/min的升温速率硅酸盐水泥熟料矿物C3S可在1300℃左右形成,如果急速升温到1450℃则可能缩短熟料矿物的烧成时间,山东引进日产1000吨流化床生产线,烧成温度仅1300℃,熟料品质与新型干法窑相当。
这些都说明物料升温速率对熟料烧成的产、质量和能耗有重要影响。
新型干法回转窑的设计与增产节能_从技术进步角度谈回转窑设计操作参数的合理选择

1 早期新型干法回转窑产量和规格参数的选择
负荷率, 以及物料在窑内停留时间等设计参数均有 较大变化。在实践—认识—再实践的基础上,笔者对
从 20 世纪 80 年代我们研究新型干法(NSP)回 转窑产量和规格参数的合理选择时, 一般采用国内 外相关窑型的产量和规格参数进行数学回归法或统
窑的合理设计、操作参数等作一些探讨。 2 回转窑在新型干法烧成系统中的地位和作用
3 提高 NSP 窑系统产量的技术路径
稳定回转窑的热工制度、提高窑速和快转率,均 衡稳定、 薄料快烧等等这些都是实现 NSP 窑高产、 优质、低耗的重要工艺原则和主要技术路径。 其中, 以稳定回转窑热工制度为中心, 需要以下多项先进 技术的系统工程予以保证。
(1) 原料矿山合理开采、矿石搭配进厂并加强 进厂原、燃料的科学管理;
4 NSP 窑设计中应该考虑的主要参数
4.1 物料在窑内的停留时间 T 从操作上看, 决定熟料产量和质量的二个重要
条件就是窑内高温条件和物料在烧成带足够的停留 时间。物料在窑内所需停留时间与窑的类型有关,前 期统计资料介绍: 悬浮预热器窑 (即 SP 窑) 为 45~ 600min,预分解窑(即 NSP 窑)为 25~300min。 经验计 算式如下:
料 在 窑 内 最 短 停 留 19.5 min ( 见 表 2 中 方 案 2);
覫3.30m×510m 、斜度 3.5% NSP 窑(改造)、最高窑速 4.70r/min、负荷率 5.2%时,物料在窑内停留最短时间 仅为 19.30min(见表 2 方案 7)。
-8-
2009年第 3 期
梁镒华:新型干法回转窑的设计与增产节能
好的熟料质量。目前通过提高产量的生产实践证明:
覫4.0 m×60 m、 斜 度 3.5% NSP 窑 、 最 高 窑 速 3.9
- 1、下载文档前请自行甄别文档内容的完整性,平台不提供额外的编辑、内容补充、找答案等附加服务。
- 2、"仅部分预览"的文档,不可在线预览部分如存在完整性等问题,可反馈申请退款(可完整预览的文档不适用该条件!)。
- 3、如文档侵犯您的权益,请联系客服反馈,我们会尽快为您处理(人工客服工作时间:9:00-18:30)。
新型干法回转窑设计参数节能优化及传动功率计算分析探讨南京邦齐建材设备工程有限公司梁镒华郝景歆前言:作者早期曾参与部分湿法、干法短窑和NSP窑的工艺、设备开发,为新设备开发提供荷载资料等。
在工作中对窑内物料荷载负荷率计算比较粗略,按保守的最大值提,至于生产中窑内物料负荷率是一个随窑型、转速和产量变化的变量关注研究较少,对窑的研究较多注意在热工方面,而对设计参数如斜度、长径比等对窑经济运行的影响有所忽略或重视不够。
因此工作中存在一定的盲目性,有些参数的确定,往往参照外国公司现有同类窑型设计数据或根据实际情况做少量调整参照使用,所以会存在Φ4.0×60m斜度3.5%使用30年不变,设计中有随意加大长径比的情况。
随着技术装备引进和后期技术进步,NSP窑产量大幅提高,传动功率逐步加大,近年来由于有NC院Φ4.0×60m斜度4%传动功率由315kw改为280kw的启发,以及早期日产2000吨技术引进中国外各公司报价资料回转窑设计参数和装机功率差异很大,一直未能深入研究搞清所以然,以致引起笔者着手研究NSP窑设计参数和功率的计算问题,拟建立一个表征性数学模型做一些探索性工作。
前面发表两文[1][2],是关于NSP窑设计节能优化和新窑型的探索,本文拟把NSP窑设计参数优化及功率计算方法介绍给大家供研究探讨。
一、NSP窑设计参数计算1、物料停留时间(T)计算窑内物料停留时间是NSP窑设计的主要参数之一。
一般意义上讲,停留时间是保证物料在窑内高温热工制度下完成多种物理化学反应所需的时间。
停留时间不足熟料“欠烧”影响产品质量性能,时间过长熟料“过烧”,使熟料晶体生长过大,且结构致密而影响熟料的易磨性并造成动力消耗和热耗增大,因此缩短物料停留时间“薄料快烧”是优质、高产和节能的重要工艺原则。
这里研究物料停留时间除一台窑在日常操作中的改变窑速来调节物料停留时间达到物料烧成的目的外,主要是研究新设计或改造窑型可通过设计参数优化和缩短物料停留时间来达到NSP窑运行节能的要求。
1.1 缩短窑内物料停留时间的理论依据NSP窑的技术进步经验告诉我们:缩短物料在窑内的停留时间“薄料快烧”是实现优质、高产、低能耗的重要工艺手段之一。
缩短物料在窑内停留时间的理论依据是:NSP窑入窑物料经预分解系统已快速完成95%以上的碳酸钙分解,物料内含有大量CaO、SiO2等均为新生态物质,入窑后分解带很短能迅速升温至1100~1200℃,即有效进行固相反应,生成新生态C2S与之同时存在的CaO 晶体尺寸都<2μm,反应表面积大,微晶体缺陷多、活性高。
进入烧成带后易溶于熟料液相,化学反应扩散迁移速度较快,反应能力强,更有利于熟料主要矿物C3S的形成,且因烧成带“合理控制”烧结反应,熟料矿物C3S微晶和再结晶的C3A、C4AF等晶体生成尺寸小,结构较疏松,能提高熟料质量,且易磨性好。
因此,NSP窑在满足主要化学反应时间要求的基础上,尽量缩短窑内物料停留时间是可行的。
1.2 窑内物料主要物理化学反应过程和停留时间以KHD超短窑为例说明窑内主要物理化学反应过程和物料停留时间。
经预分解系统入窑物料碳酸钙表观分解率达到95%以上,入窑后尚需完成<5%的碳酸钙分解反应和升温,分解带很短物料能迅速升温至950℃吸热量168kj/t·cl,接着过渡带物料升温950~1300℃及部分液相出现,吸热量约448kj/t·cl,此间1100~1200℃时固相反应生成C3A、C4AF、C2S和钙离化子(Ca+)达到最大值,反应以放热约485kj/t·cl(设熟料矿物组成:C3A0.08、C4AF0.10、C2S0.20和C3S0.60),过度带吸、放热两项抵消后呈微放热状态约37kj/t·cl,过度带需时约6分钟。
分解、过度带约占窑长53%左右。
烧成带液相增加微吸热55 kj/t·cl,通过液相烧结由C2S吸收Ca+最终形成熟料主要矿物碳酸三钙(C3S),反应放热量约279kj/t·cl,因此入窑物料化学反应和升温需吸热量较少,主要化学反应以放热反应为主,窑内熟料形成热基本为负值。
由于窑内水泥物料是个多组分、多离子的混合体,各组分、离子对液相量和粘度有较大影响,进而影响生成C3S的反应速率和熟料矿物组成,另外温度对C3S形成速率的影响和C3S晶格形成和微晶生长的热、动力学因素均需要有一定的反应距离和停留时间来保证反应完成。
烧成带约占窑长40%左右,需时约10分钟,而冷却带很短约占窑长7%,出料温度>1300℃,需时仅1~2分钟。
因此,窑内物料总停留时间仅为19~20分钟。
表1 超短窑内各带物料主要化学反应过程及停留时间1.3窑设计中物料停留时间的合理选择合理确定物料停留时间很重要,随NSP的技术进步,我们逐步探索到合理物料停留时间的相关规律。
首先我们进行国内外公司部分NSP窑物料停留时间的计算统计,结果列于下表。
表2 部分NSP窑物料停留时间计算统计上表可见:(1)由80年代的25~30分钟(如万年、冀东、柳州和日本宇部报价资料等)到80年代后期90年代初的20~25分钟(如宁国、顺昌、天津院等)。
(2)KHD的选择。
KHD对停留时间有个探索过程,体现在最初超短窑,如:斯伯纳厂配最高转速3.5r/min,实际操作转速3.0r/min,计算停留时间为16.6和19.4分钟;80年代鲁南报价装机最高转速3.2r/min,计算停留时间为19.1分钟;后来台湾花莲配装机最高转速3.0r/min,实际操作转速2.5r/min,计算停留时间为21.1和25.4分钟;江苏京阳配装机最高转速3.2r/min,实际按此转速操作,计算停留时间为21.1分钟。
(3)NC的选择。
南京院90年代对最高转速配置均考虑物料停留时间<20分钟的可能,如:华润5000t/D配最高4.2r/min,计算停留时间为18.5分钟;江苏联合超短窑配最高3.8r/min,操作转速3.5r/min ,计算停留时间为17.7和19.3分钟,比京阳超短窑缩短了2.2分钟,负荷率降低0.7%,体现了“薄料快烧”的运行效果。
(4)笔者建议。
实践证明物料停留时间有随原燃料条件和窑系统工艺、装备的技术进步、生产管理控制水平的提高有缩短的趋势,因此我们在窑的设计时应给窑速配置留一定的余地。
笔者建议:设计中最高操作转速按目前生产水平控制在19~20分钟左右,装机最高转速可按~18分钟左右考虑,是合理可行的。
1.4 物料停留时间(T )计算nD P L a T i m ⋅⋅⋅=77.1 min (1)式中: i D ;L —分别为窑有效内径和长度,m ;P —窑斜度(度),其中3.5% (2.0º),4.0%(2.3º),4.5%(2.58º); n —窑转速,r/min ; m a —物料休止角,(º),全窑平均一般取35°计算公式(1)建立起停留时间(T )与长径比成正比和斜度(P )、内径(D i )、转速(n )成反比的关系,即:在同转速下,窑的长径比大、斜度小物料在窑内停留时间延长;而大斜度,小长径比将缩短物料在窑内停留时间。
若两台窑停留时间相同,能达到降低转速而节能。
当设计参数i D 、L 、P 确定后代入上式可得计算简式(2)如下: T=K 1·n -1(min ) (2)式中:K 1——窑型时间系数,即K 1=10.4715L/PD i 2、物料负荷率(ϕ)计算负荷率ϕ为窑内物料的容积与窑有效容积的百分比。
由于窑各带物料性质、状态和运动速度不同,物料负荷率ϕ各不相同,这里所指的是平均负荷率的概念,它是个虚拟表征性指标。
据资料介绍,NSP 窑一般ϕ=5%~13%,目前窑产量大幅提高并有向“薄料快烧”发展则ϕ=6%~9.0%左右(见图1)。
这里研究负荷率ϕ除对具体某窑,因产量提高窑速调节后计算物料负荷率外,主要研究新设计窑设计参数斜度、直径选择和产量对负荷率、物料量和节能的影响。
100785.0667.12cl ⨯=mi L D RTG γϕ(%) (3) 式中:[]1)55.0(21+-=λs k R 取1.0625 s k —料耗 kg·s/ kg·cl 取1.62 λ—入窑物料表观分解率,% 取0.90()()3cl kg 085.127.19.02121m s m ==++=γγγ(根据日本水泥协会数据计算) G cl —窑小时熟料产量,t/h将公式(1)和参数R 、m γ代入后得下式(4):100P 7757.213⨯=nD G i 熟料ϕ(%) (4) 为使用方便将窑规格设计参数代入公式(4)可得计算简式(5)如下: =ϕK 2·G cl ·n -1(%) (5)式中:K 2——窑型物料系数 即K 2=21.7757/ PD i 3计算公式建立起负荷率与产量成正比,而与斜度、转速和直径三次方成反比的关系,即负荷率随窑产量提高而加大,随斜度、直径和转速加大而减小。
这些结论从图1中都能得到印证。
3、窑内物料量(G w )计算窑内物料量和运动状态速度是构成物料运动功耗的两个组成部分,正常状态下,物料运动功耗约占据窑实际运动功耗的70~75%左右,因此在窑设计中,力求降低窑内物料量是节能降耗要考虑的主要因素之一。
窑内物料量可通过窑内平均负荷率查“园截面积内弓形函数表”如下表【见水泥工厂设计手册(下册)第871页】。
表3 窑内负荷率与园截面积内弓形函数表窑内物料量G w 可根据计算负荷率ϕ从表三中查取A 值,用下式(6)进行计算。
G w =A×2i D ×m γ×L (t ) (6)式中:i D —窑有效内径(m ),m γ—物料平均容重取1.085,A —弓面积查上表二、NSP 窑传动功率(N )计算正确计算选择传动功率很重要。
如果电机选型小了则会使传动电机过载过热影响生产正常进行和产量的提高,有时甚至会因过载而烧坏电动机;如果电动机选型过大,不但增加投资造成资源浪费,而且电动机长期低负荷运转会降低传动效率而浪费能源,为此许多人都在研究,探讨回转窑传动功率的计算方法。
随着NSP 窑技术进步,窑产量大幅度提高,主传动功率配置选型不断加大,特别是各种不同设计参数窑型在能耗和对窑产量能力研判上的差异,往往造成额定功率配置不合理而导致使用过程中再行改造。
因此,正确合理计算选择主传动功率显得尤为重要。
(见图2NSP 窑的斜度、长径比对能耗的影响。
)笔者根据国内早期Φ4.0×60斜度3.5%日产2000吨时的部分研究成果,结合当前实际生产数据探索传动功率的计算方法如下。