多组分精馏专
多组分精馏的简捷计算和逐板计算举例

0.59842 0.000984
w
lg 6.24
1
4.6
塔釜温度17℃,利用气相中的烷烃冷凝提供塔釜中需要的热 量,可以认为是塔顶部分冷凝,塔釜泵厢式循环。
最小回流比:
ibzi 1 q
ib
ib xdi
ib
Rm
1
其中需要注意的问题: zi是题面中的数据;1-q=0.36;采用牛顿迭代法;b组分选 取(i—C40挥发度最小);采用全塔平均温度-39℃和压力
C10 : yn1 0.3026xn 0.5279
C2 : yn1 0.3026xn 0.1353
C20 : yn1 0.3026xn 0.0204
相 平 衡 方 程 中 的 ib 是 精 馏 段 平 均 温 度 下 的
值: 95 60 77.50C ,(进料温度与塔顶温度的平均值)
⑦逐板计算 相平衡方程与操作线方程交替运用。
精馏段相平衡方程:xi
yi ib yi ib
xi 1
手算 0.005,计算机计算 0.0001
精馏段操作线方程:yn1,i
R R
1
xn,i
1 R
1
xd
,i
R 0.434
yn1,i 0.3026xn,i 0.6974xd,i
H2 : yn1 0.3026xn 8.7175103
⑥确定进料位置 因为是气液相进料,可以采用芬斯克公式计算精馏段塔板数 塔顶温度:-95℃;进料温度:-60℃;塔釜温度:17℃ 从塔顶温度与进料温度相差不大,可以判断精馏段塔板数不 会太多,采用全塔的平均温度计算误差会很大。所以,采用 塔顶温度和进料温度的平均值 95 60 77.50C 来计算。
yi ib
化工分离过程(第7讲)(3.2多组分精馏过程分析)
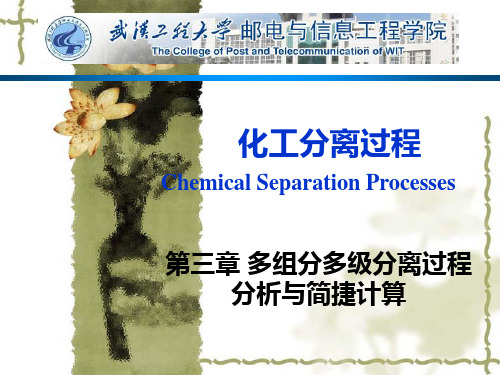
x1
y2 y 1
* TB
1.0 B7
3.2.1 多组分精馏过程分析
精馏是多次简单蒸馏的组合。
精馏塔底部是加热区,
温度最高;塔顶温度最低。
精馏结果,塔顶冷凝收 集的是低沸点组分,高沸 点组分则留在塔底。
8
3.2.1 多组分精馏过程分析
1 从塔的中间O点进料; 2 组分B的液、汽相组 成分别为 x3 和 y3; 3 每层塔板都经历部分 汽化和部分冷凝过程;T
4
3.2.1 多组分精馏过程分析
简单蒸馏以及二组分精馏的原理图 关键组分(Key Components) 清晰分割 多组分精馏过程的复杂性
二组分精馏实例:苯-甲苯 三组分精馏实例:苯(LK)-甲苯(HK)-异丙苯 四组分精馏实例:苯-甲苯(LK)-二甲苯(HK)-异丙苯
多组分精馏与二组分精馏在浓度分布上的区别
22
3.2.1 多组分精馏过程分析
2、关键组分
①若无LNK:HK分别在二段出现两个最高点,LK 表现像LNK。 (图3-7) ②若无HNK:LK分别在二段出现两个最高点,HK 表现像HNK。 (图3-8) ③有LNK、HNK,且都不同时出现在顶、釜时: LK在精馏段出现一个最大值,然后降到所规定的浓度; HK在提馏段出现一个最大值,然后降到所规定的浓度。 (图3-9)
甲苯为LK,二甲苯为HK,两 者的浓度分布曲线变化规律相 同,方向相反。 在 塔 底 处 , 主 要 分 离 HK 和 HNK,所以此处HK浓度向上 增大;同理,在塔顶处,主要 分离LK和LNK,所以此处LK 浓度向上减小。
图3-9 苯-甲苯(LK)-二甲苯(HK)-异丙 苯液相浓度分布
苯为LNK,在进料板以下浓度 快速减小,最终全部进入塔顶; 异丙苯为HNK,在进料板以上 浓度快速减小,最终全部进入 21 塔釜。
多效精馏的原理及应用

多效精馏的原理及应用1. 原理介绍多效精馏是一种利用多个分馏塔进行级联操作的精馏工艺,可以在相对低能耗的前提下实现高效的分离和提纯。
其主要原理包括以下几个方面:•级联操作:多效精馏将多个分馏塔有机地串联在一起,通过逐级分离和提纯的方式实现高效的分离效果。
每个分馏塔都将前一级塔的馏分作为进料,继续进行精细的分离过程。
•蒸馏原理:多效精馏依靠蒸发和冷凝的原理进行分离。
在各个分馏塔中,液体在加热的作用下蒸发成气体,然后通过冷凝器冷凝回液体。
不同组分在不同的温度下沸腾和冷凝,从而实现分离和提纯。
•温度梯度:多效精馏中的每个分馏塔都会设置不同的温度梯度,以便在每个级别上实现特定组分的分离。
较低温度区域主要用于提纯较轻的馏分,而较高温度区域则用于提纯较重的馏分。
2. 应用场景多效精馏在化工、石油、食品等行业有广泛的应用,主要包括以下几个方面:2.1 石油化工在石油化工领域,多效精馏常用于石油产品的提纯和分离。
例如,原油在精炼过程中需要通过多效精馏来提取不同沸点范围内的馏分,从而得到高纯度的汽油、柴油、润滑油等产品。
2.2 化学工程化学工程中,多效精馏被广泛应用于有机合成和分离纯化过程。
通过多效精馏技术,可以实现对化学反应产物的高效提纯,得到所需的纯净化合物。
2.3 食品加工在食品加工行业,多效精馏常用于酒精、香精、食用油等食品原料的提炼和脱水处理。
通过多效精馏,可以有效去除杂质和水分,提高产品品质和纯度。
2.4 环境工程多效精馏还可以应用于环境工程中的废水处理和污染物回收。
通过多效精馏,可以将废水中的有价值物质进行分离和回收,实现资源的有效利用和环境保护。
3. 优势与挑战多效精馏相较于传统的单效精馏有以下优势:•高效分离:多效精馏的级联操作使得每个分馏塔都能充分利用热能和组分差异,从而实现更高效的分离和提纯效果。
•节能环保:多效精馏相对于传统的单效精馏来说,能耗更低,排放更少,有利于减少能源消耗和环境污染。
多组分精馏和特殊精馏

核算式
对HNK:C3,iC4,nC4进行核算: C3:d0.6448,xD0.017 C4:xD0
\ 清晰分割假设对 C 3不成立,须调整
5.调整
以前面结果为初值,进行试差
设 d 0 .6 4 4 8 , 其 它 不 变 , 重 复 1 4 步
计 算 , 至 前 后 二 次 结 果 相 近 为 止 。
3. 核实清晰分割的合理性
对
于LNK
,
核
实w
,看
i
是
否xi
,W
0
核实式: fi di wi;
fd ( w )i ( w )i 1
\ wi fi 1 (wd )i
将
(d ) wi
i
h
N
m(d )代 wh
入
上
式
有:
wi
1i
fi h N m(wd )h
核算式
对 于 甲 烷 , w 9 .6 1 0 5 0 ; x W 1 .5 1 0 6
结果:第二次dC3 0.635 与第一次相近
例3-3 苯(B)-甲苯(T)-二甲苯(X)-异丙苯 (C)的混合物送入精馏塔分离,进料组成(摩尔 分数)为:zB=0.2,zT=0.3, zX=0.1, zC=0.4。相对 挥发度数据:αB=2.25,αT=1.00,αX=0.33,αC= 0.21。分离要求:馏出液中异丙苯不大于0.15%;釜 液中甲苯不大于0.3%(摩尔)。计算最少理论板和 全回流下的物料分配。
1.000 0.025 0.901 0.0167 1.000 - 1.325 0.901 1.325
故
Rm 1.306
返回
3.1.3 最少理论板数和组分分配
1、最少理论板数 全 回 流 R 时 操N , 作 N m
多组分精馏简述 2

第三章 多组分精馏在化工原理课程中,对双组分精馏和单组分吸收等简单传质过程进行过较详尽的讨论。
然而,在化工生产实际中,遇到更多的是含有较多组分或复杂物系的分离与提纯问题。
在设计多组分多级分离问题时,必须用联立或迭代法严格地解数目较多的方程,这就是说必须规定足够多的设计变量,使得未知变量的数目正好等于独立方程数,因此在各种设计的分离过程中,首先就涉及过程条件或独立变量的规定问题。
多组分多级分离问题,由于组分数增多而增加了过程的复杂性。
解这类问题,严格的该用精确的计算机算法,但简捷计算常用于过程设计的初始阶段,是对操作进行粗略分析的常用算法。
§3-1分离系统的变量分析设计分离装置就是要求确定各个物理量的数值,但设计的第一步还不是选择变量的具体数值,而是要知道在设计时所需要指定的独立变量的数目,即设计变量。
一、设计变量1.设计变量⎩⎨⎧-=:可调设计变量固定设计变量a x c v i N N N N N :v N :描述系统所需的独立变量总数。
c N :各独立变量之间可以列出的方程式数和给定的条件,为约束关系数。
要确定i N ,需正确确定v N 和c N ,一般采用郭慕孙发表在AIchE J (美国化学工程师学会),1956(2):240-248的方法,该法的特点是简单、方便,不易出错,因而一直沿用至今。
郭氏法的基本原则是将一个装置分解为若干进行简单过程的单元,由每一单元的独立变量数e v N 和约束数e c N 求出每一单元的设计变量数e i N ,然后再由单元的设计变量数计算出装置的设计变量数E i N 。
在设计变量i N 中,又被分为固定设计变量x N 和可调设计变量a N ,x N 是指确定进料物流的那些变量(进料组成和流量)以及系统的压力,这些变量常常是由单元在整个装置中的地位,或装置在整个流程中的地位所决定,也就是说,实际上不要由设计者来指定,而a N 才是真正要由设计者来确定的,因此郭氏法的目的是确定正确的a N 值。
第三章精馏3-1多组分精馏
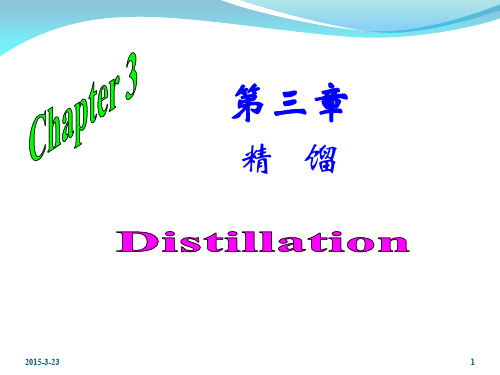
轻关键组分(LK):相对易挥发的组分;
多
组 重关键组分(HK):相对不易挥发的组分。
分 精
轻关键组分在塔釜液中,该组分的浓度
馏 有严格限制,并在进料液中比该组分轻的
组分及该组分的绝大部分应从塔顶采出。
重关键组分, 塔顶 重 塔釜
2015-3-23
14
(1) 关键组分
② 非关键组分
3.1
关键组分以外的组分称为非关键组分
2015-3-23
7
精馏操作流程
3.1
多 组 分 精 馏
2015-3-23
8
精馏操作流程
3.1
多 组 分
精 馏 段
精
馏
提
馏
段
塔顶产品 原料 塔釜产品
简单塔
2015-3-23
9
精馏操作流程
精馏
3.1 多
物化 基础
必要 条件
工程 措施
设备
组
分 精 馏
相对挥 发性差 异
多次部 分汽化、 多次部 分冷凝
进料级。
2015-3-23
32
小结
★组成分布
3.1 3. 关键组分 变化复杂 若只有HNK而无LNK时: HK分别在二段
多
出现两个最高点, LK表现象LNK。
组 分
若只有LNK而无HNK时:LK分别在二段出
精
现两个最高点, HK表现象HNK。
馏 有LNK、HNK, 且都不同时出现在顶、釜
2015-3-23
苯、甲苯、异丙苯 精馏塔内温度分布
# 26
3.1
多 组 分 精 馏
苯、甲苯、异丙苯精 馏塔内液相浓度分布
2015-3-23
多组分精馏的简捷计算和逐板计算举例
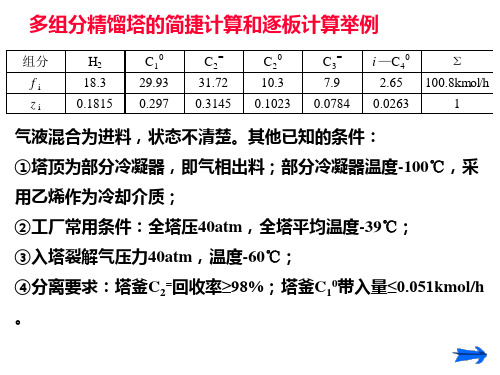
d
xh xl
lg lh
w
lg
0.6120 0.01298
d
0.59842 0.000984
w
lg 6.24
1
4.6
塔釜温度17℃,利用气相中的烷烃冷凝提供塔釜中需要的热 量,可以认为是塔顶部分冷凝,塔釜泵厢式循环。
950C T塔釜 390C 2
T塔釜 170C
考虑全塔的阻力降可以忽略,仍然认为全塔压力为40atm。
在塔釜温度17℃和塔压为40atm的情况下,采用泡点方程
来验证塔釜温度。
ki xi 1 0
组分
H2
C10
C2=
C20
C3=
i—C40
Σ
ki
0
3.9
1.26
0.9
0.34 0.135
顶底分布:
d
w
C10
ห้องสมุดไป่ตู้
585.86
C2=塔顶: dC2 31.72 1 0.98 0.034kmol / h
塔釜: wC2 31.086kmol / h
顶底分布:
d w C2
1.094 103
Ⅱ:工厂常用条件:全塔压40atm,全塔平均温度
最小回流比:
ibzi 1 q
ib
ib xdi
ib
Rm
1
其中需要注意的问题: zi是题面中的数据;1-q=0.36;采用牛顿迭代法;b组分选 取(i—C40挥发度最小);采用全塔平均温度-39℃和压力
为40atm的相对挥发数据。(注意换算到 ib)
3.1 多组分精馏过程
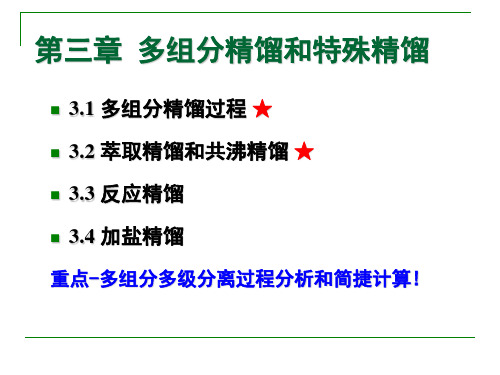
轻组分恒浓区
24
3.1.2 最小回流比(Rm)
(2)重组分为非分配组分,轻组分为分配组分:
(3)重组分为分配组分,轻组分为非分配组分:
25
3.1.2 最小回流比(Rm)
(4)轻、重组分均为分配组分:
最小回流比条件下会出 现恒浓区,区内无分离 效果,需无穷多理论板。 如何计算最小回流比?
26
3.1.2 最小回流比(Rm)
3.1.2 最小回流比(Rm)
为完成某一分离任务,所需的理论塔板数为无穷多
时的回流比称为最小回流比。
二组分精馏:
最小回流比下,进料板上下出现恒浓区或称夹点。
恒浓区
多组分精馏:
最小回流比下,也有恒浓区,但由于非关键组分
的存在,恒浓区出现的部位要较二组分精馏复杂。
23
3.1.2 最小回流比(Rm)
一、关键组分(Key Components)
串级数(2) 分配器(1) 侧线采出(0) 传热单元(2)
Na=5
F
已被指定的可调变量:
余下的2个可调
(1)进料位置;(2)回流比;
(3)全凝器饱和液体回流或冷凝器 的传热面积或馏出液温度。
设计变量往往用来 指定组分在馏出液 和釜液中的浓度。
4
3.1.1 多组分精馏过程分析
第三章 多组分精馏和特殊精馏
3.1 多组分精馏过程 ★ 3.2 萃取精馏和共沸精馏 ★ 3.3 反应精馏
3.4 加盐精馏
重点-多组分多级分离过程分析和简捷计算!
3.1 多组分精馏过程
3.1 多组分精馏过程
3.1.1 多组分精馏过程分析
1 、关键组分 2、 组分在塔顶、塔底产品中的预分配 3 、多组分精馏过程特征
化工分离工程第3章 多组分精馏2

FLGC
3.3.6 共沸与萃取精馏比较
共同点: 加入溶剂S, 萃取精馏的优点:
12 / s
(1) 因萃取精馏溶剂沸点高,溶剂可从塔顶或附近加入,使
全塔的相对挥发度都得到提高。
(2) 萃取精馏溶剂在塔内基本上不挥发,能量消耗少。而共
沸精馏中共沸剂与原料组分同时气化,消耗能量。
(3) 共沸精馏由于必须形成共沸物,因而可供选择的共沸剂
FLGC
特殊精馏
• 普通精馏不适合于以下状况的物料: 1、相对挥发度接近1的组分; 2、待分离组分间形成共沸物; 3、待分离组分是热敏物质; 4、待分离组分是难挥发组分,且含量低。
特殊精馏——利用加入热能和质量分离剂以增加原有组 分间的相对挥发度值的精馏方法。
FLGC
常用的特殊精馏方法
• 共沸精馏——如果加入的第三组分能和被分离物系中一个 或几个组分形成共沸物时,第三组分以共沸物的形式从精 馏塔塔顶蒸出。所加入的新组分称为共沸剂。
方案2:选择丙酮的同系物,则塔顶产物为甲醇,塔釜为丙酮及同
系物
哪个更好?
FLGC
(2)从分子结构相似(或极性相似)的概念选择溶剂 常见有机化合物按极性增加的顺序排列为: 烃→醚→醛→酮→醇→二醇→水 应选择在极性上更类似于重关键组分的化合物为溶剂, 可以有效的减小重关键组分的挥发度!
同样如甲醇(沸点64.7)—丙酮(沸点56.5)体系 选烃为溶剂,烃与丙酮极性相似,塔顶产物为甲醇,塔
FLGC
萃取精馏的注意事项:
(1)由于加入的萃取剂是大量的(一般要求xs>0.6),因此塔内下 降液量远大于上升蒸汽量,造成汽液接触不佳,故萃取精馏塔 的塔板效率低,大约为普通精馏的一半左右(回收段不包括在 内)。设计时要考虑塔板及流体动力情况。
多组分分离基础及多组分精馏-现代化工分离技术

人工智能和大数据等先进技术 的应用将为多组分分离技术提 供新的解决方案,实现智能化和技术开发将得到加强,以适 应不同化工领域的需求。
绿色化学和可持续发展理念将 进一步渗透到多组分分离技术 的研究和应用中,推动化工行 业的可持续发展。
平衡分离
当混合物达到热力学平衡时,各组分的组成不再发生变化,此时可以通过一定 的操作手段,如改变温度、压力或加入第三组分等,使混合物中各组分得以分 离。
非平衡分离
在某些情况下,混合物无法达到热力学平衡,但为了实现分离,可以采用一些 非平衡分离技术,如吸附、结晶、离子交换等。
分离过程的动力学基础
扩散系数
按操作目的分类
可分为精馏、吸收、萃取、吸附等。精馏是根据混合物中各组分的沸点不同,通过加热、冷凝实现分离;吸收是 根据混合气体中各组分在吸收剂中的溶解度不同实现分离;萃取是根据混合物中各组分在两种不混溶溶剂中的溶 解度不同实现分离;吸附则是利用固体吸附剂对不同组分的吸附能力不同实现分离。
分离过程的热力学基础
06 结论
分离技术的重要地位
分离技术是现代化工生产中的关键环 节,对于提高产品质量、降低能耗和 实现绿色生产具有重要意义。
随着化工行业的发展,多组分分离技 术成为研究和应用热点,对于解决复 杂混合物分离难题具有重要作用。
未来发展方向与展望
高效、节能、环保的多组分分 离技术将是未来的研究重点, 如新型吸附剂、萃取剂和精馏
03 多组分精馏技术
多组分精馏的原理
精馏原理
多组分精馏基于溶液的相平衡原 理,通过加热和冷凝操作将溶液 分成多个纯组分。
组分性质
多组分精馏中,各组分的沸点、 蒸汽压、溶解度等性质对分离效 果有重要影响。
多组分精馏简述

第三章 多组分精馏在化工原理课程中,对双组分精馏和单组分吸收等简单传质过程进行过较详尽的讨论。
然而,在化工生产实际中,遇到更多的是含有较多组分或复杂物系的分离与提纯问题。
在设计多组分多级分离问题时,必须用联立或迭代法严格地解数目较多的方程,这就是说必须规定足够多的设计变量,使得未知变量的数目正好等于独立方程数,因此在各种设计的分离过程中,首先就涉及过程条件或独立变量的规定问题。
多组分多级分离问题,由于组分数增多而增加了过程的复杂性。
解这类问题,严格的该用精确的计算机算法,但简捷计算常用于过程设计的初始阶段,是对操作进行粗略分析的常用算法。
§3-1分离系统的变量分析设计分离装置就是要求确定各个物理量的数值,但设计的第一步还不是选择变量的具体数值,而是要知道在设计时所需要指定的独立变量的数目,即设计变量。
一、设计变量1.设计变量⎩⎨⎧-=:可调设计变量固定设计变量a x c v i N N N N N :v N :描述系统所需的独立变量总数。
c N :各独立变量之间可以列出的方程式数和给定的条件,为约束关系数。
要确定i N ,需正确确定v N 和c N ,一般采用郭慕孙发表在AIchE J (美国化学工程师学会),1956(2):240-248的方法,该法的特点是简单、方便,不易出错,因而一直沿用至今。
郭氏法的基本原则是将一个装置分解为若干进行简单过程的单元,由每一单元的独立变量数e v N 和约束数e c N 求出每一单元的设计变量数e i N ,然后再由单元的设计变量数计算出装置的设计变量数E i N 。
在设计变量i N 中,又被分为固定设计变量x N 和可调设计变量a N ,x N 是指确定进料物流的那些变量(进料组成和流量)以及系统的压力,这些变量常常是由单元在整个装置中的地位,或装置在整个流程中的地位所决定,也就是说,实际上不要由设计者来指定,而a N 才是真正要由设计者来确定的,因此郭氏法的目的是确定正确的a N 值。
多组分共沸混合物精馏工艺流程的研究

多组分共沸混合物精馏工艺流程的研究1、萃取精馏的原理在基本有机化工生产中,经常会遇到组分的相对挥发度比较接近,组分之间也存在形成共沸物的可能性。
若采用普通精馏的方法进行分离,将很困难,或者不可能。
对于这类物系,可以采用特殊精馏方法,向被分离物系中加入第三种组分,改变被分离组分的活度系数,增加组分之间的相对挥发度,达到分离的目的。
如果加入的溶剂与原系统中的一些轻组分形成最低共沸物,溶剂与轻组分将以共沸物形式从塔顶蒸出,塔底得到重组分,这种操作称为共沸精馏;如果加入的溶剂不与原系统中的任一组分形成共沸物,其沸点又较任一组分的沸点高,溶剂与重组分将随釜液离开精馏塔,塔顶得到轻组分,这种操作称为萃取精馏。
2、溶剂甄选原理由于萃取精馏混合物多为强非理想性的系统,所以工业生产中选择适宜溶剂时主要应考虑以下几点:(1)选择性:溶剂的加人必须使待拆分组分的相对溶解度提高明显,即为建议溶剂具备较低的选择性,以提升溶剂的利用率;2)溶解性:要求溶剂与原有组分间有较大的相互溶解度,以防止液体在塔内产生分层现象,但具有高选择性的溶剂往往伴有不互溶性或较低的溶解性,因此需要通过权衡选取合适的溶剂,使其既具有较好的选择性,又具有较高的溶解性;(3)沸点:溶剂的沸点应当低于原进料混合物的沸点,以避免构成溶剂与组分的共沸物。
但也无法过低,以防止导致溶剂回收塔釜梅过低。
目前提炼减压蒸馏溶剂甄选的方法存有实验法、数据库查阅法、经验值方法、计算机辅助分子设计法用实验法甄选溶剂就是目前应用领域最广泛的方法,可以获得较好的结果,但是实验花费很大,实验周期较长。
实验法存有轻易法、沸点仪法、色谱法、气论调等。
实际应用领域过程中往往须要几种方法融合采用,以延长吻合目标溶剂的时间。
溶剂甄选的通常过程为:经验分析、理论指导与计算机辅助设计、实验检验等。
若文献资料和数据不全系列,则只有实行最基本的实验方法,或者实行极具应用领域前景的计算机优化方法以谋求最佳溶剂。
第三章 多组分精馏

层理论塔板才能满足分离要求所需的回流比,
称为最小回流比。多组分精馏计算中,必须用
解析法求最小回流比。
23
常用的是恩德伍德法,推导该式的基本假设是:
1) 体系中各组分的相对挥发度为常数;
2) 塔内气相和液相均为恒摩尔流。
根据物料平衡及相平衡表示,利用恒浓区的 概念,恩德伍德推导出最小回流比的两个联 立公式:
清晰分割时非关键组分在塔顶和塔底产品
中的分配用物料衡算求得。
11
12
总物料衡算 苯的衡算 乙苯的衡算
甲苯的衡算
13
(2) 非清晰分割
如果轻重关键组分不是相邻组分,则塔顶和塔 底产品中必有中间组分。 如果进料液中非关键组分的相对挥发度与关键 组分相差不大,则塔顶产品中就含有比重关键 组分还重组分,塔底产品中含有比轻关键组分
37
应用:实验制备的小批量物质分离、石油产 品评价、高效填料的性能测定、精细化工产
品的提纯、同位素产品的精制等。
计算:难以采用图解方法求解理论板数,通常
采用解析方法或简捷法确定理论板数、进料位
置等。计算中,精密精馏通常按二元混合物处
理。
38
3.5.3
盐溶精馏(加盐精馏)
一种采用特殊萃取剂的萃取精馏,用于难分 离混合物的分离。 例:乙醇-水 、丙醇-水、水-醋酸等的分离
5
对于双组分精馏;
塔顶:xDA 已确定 xDB =1- xDA ;
塔釜:xWB已确定 xWB =1- xWA ;
也就是塔顶、塔釜组成全部确定。
对于多组分精馏:Na=5 ,与组分数无关。
除规定全凝器饱和液体出料:2) R; 3)D/F外只
关键组分在多组分精馏分离的作用
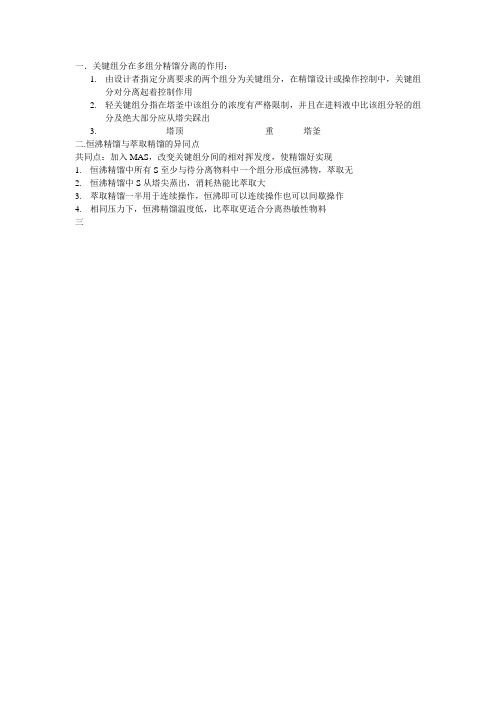
一.关键组分在多组分精馏分离的作用:
1.由设计者指定分离要求的两个组分为关键组分,在精馏设计或操作控制中,关键组
分对分离起着控制作用
2.轻关键组分指在塔釜中该组分的浓度有严格限制,并且在进料液中比该组分轻的组
分及绝大部分应从塔尖踩出
3.---------------------塔顶----------------------------重----------塔釜
二.恒沸精馏与萃取精馏的异同点
共同点:加入MAS,改变关键组分间的相对挥发度,使精馏好实现
1.恒沸精馏中所有S至少与待分离物料中一个组分形成恒沸物,萃取无
2.恒沸精馏中S从塔尖蒸出,消耗热能比萃取大
3.萃取精馏一半用于连续操作,恒沸即可以连续操作也可以间歇操作
4.相同压力下,恒沸精馏温度低,比萃取更适合分离热敏性物料
三。
多组分精馏

I区:提馏段分离区。将塔釜产品提浓到分离要求,使轻关键组分B的浓度打到xWL。
精馏段——
IV区:上加料区。由于重非分配组分D不在塔顶出现,进料板上必须紧接着有若干板使DA组分降到零,由IV区完成。因此恒浓区向上推移。
V区:上恒浓区。组分A、B、C的浓度恒定,没有分离效果。
可见,直接顺序在塔釜需要的外加热量和塔顶需要的外加冷量都比间接顺序的要少。
2.设备进行精馏操作的主要设备有塔、再沸器和冷凝器。从上面的讨论已知,直接顺序与间接顺序相比,在塔釜要汽化的组分和在塔顶要冷凝的组分都要少,因此:
①直接顺序塔内气体量少,故塔径要小;
②直接顺序塔釜再沸器和冷凝器传热面积要小。
综合上述从能量和设备两方面考虑,直接顺序比间接顺序优。
求 根据清晰分割,比T还重的组分在塔顶不出现,所以 ,
求 述三式可解出:
三、芬斯克(Fenske)公式求最小理论塔板数Nm
(一)操作线方程(回顾——由物料衡算求)
1、精馏段操作线方程
如图,以红框为物衡范围。
总物衡:
i组分物衡:
联立解得精馏段操作线方程:
令
(A)
5.产品质量要求高的组分从塔顶采出
因为塔顶为汽相,杂质少;塔釜为液相,杂质较多。
6.侧线采出可节省设备
对纯度要求高的组分在塔顶采出的同时,对于纯度要求不是很高的组分,可以采用侧线采出,减少设备。
以上概述了讨论了多组分精馏的特点及其分离先后顺序的选取原则。下面将学习多组分精馏的计算。
3.2.2多组分精馏简捷算法
在《化工原理》课程中对双组分液态混合物的精馏进行了讨论,但是在实际出产中所遇到的待进行精馏分离的液态混合物往往为多组分。
化工原理多组分精馏

化工原理多组分精馏简介多组分精馏是一种常见的化工分离技术,广泛应用于石油、化工、药品等行业中。
本文将介绍多组分精馏的基本原理、设备和操作、影响因素,以及应用案例等内容。
基本原理多组分精馏是通过不同组分的挥发性差异实现分离的一种方法。
在一个精馏塔中,原料液体进入塔顶,经过加热后蒸发,蒸汽上升并与冷却剂进行接触,冷却后变为液体,得到精馏液。
根据不同的沸点,各组分在塔内得到部分蒸发和凝结,最后在塔顶和塔底得到不同组分的纯化产品。
设备和操作多组分精馏通常由以下设备组成:1.精馏塔:用于将混合物分离成多个组分的关键设备。
塔内通常有填料或板式反应器,以增加传质效果。
2.热交换器:用于加热和冷却原料和冷却剂。
3.冷凝器:用于将蒸汽冷却成液体,以获取精馏液。
4.回流器:用于控制精馏液的回流或提供塔顶的回流液。
在操作多组分精馏塔时,需要注意以下几点:1.控制塔顶温度:通过调节加热和冷却剂的流量,控制塔顶温度,确保所需组分能够得到纯化。
2.控制回流比:回流比是回流液与塔顶出口流量的比值。
通过调节回流比,可以改变塔内的传质效果,影响分离效果。
3.利用塔内温度梯度:塔内温度从塔底到塔顶逐渐增加,利用温度差异来实现组分的分离。
影响因素多组分精馏的效果受到多个因素的影响,以下是几个重要的影响因素:1.组分挥发性差异:组分之间的沸点差异越大,精馏效果越好。
2.塔设计:塔的高度、填料或板式的选择,对传质效果和分离效果有直接影响。
3.温度梯度:塔内温度梯度越大,分离效果越好。
4.回流比:适当的回流比可以改善传质效果,提高精馏效果。
5.操作参数:加热剂和冷却剂的流量、操作压力等参数的调节,会直接影响精馏过程的效果。
应用案例多组分精馏在化工领域有着广泛的应用。
以下是几个常见的应用案例:1.石油炼油:通过多组分精馏,将原油中的各种烃类分离出来,得到汽油、柴油、煤油等产品。
2.药品制造:制药工业中,多组分精馏被用于纯化药物原料,去除杂质,提高药品的纯度和品质。
第三章多组分精馏

轻非关键组分(LNK),轻组分
多组分精馏物系组成:
轻关键组分(LK) 中间组分
重关键组分(HK)
重非关键组分(HNK),重组分
根据组分是否在精馏塔的两端都出现, 可分为分配组分和非分配组分。
清晰分割: 馏出液中除了重关键组分之外,没有其它
f d b
iቤተ መጻሕፍቲ ባይዱ
i
i
d i
b i
d r
b r
ir
Nm
f d b
i
i
i
(1) (2)
bi
fi
1
dr br
ir Nm
di
f i
dr br
ir
Nm i
1
dr br
ir
N m
i为非关键组分,r为重关键组分或参考组分
[例3-4]
设计一个脱乙烷塔,从含有 6 个轻烃 的混合物中回收乙烷,进料组成、各组 分的相对挥度和对产物的分离要求见设 计条件表。试求所需最少理论板数及在 全回流条件下馏出液和釜液的组成。
图3-10 Erbar-Mddox
适宜进料板位置的确定原则:
(1)在操作回流比下精馏段与提馏段理 论板数之比等与在全回流下用Fenske方 程分别计算得到的精馏段与提馏段理论 板数之比。
(2) Kirkbride 经验式:
P79 例[3-5]
最小回流比和操作回流比下的理论板数 的计算 : 应用例 3-4的已知条件和计算结果进行 下列计算:(a) 使用Underwood法确定最 小回流比;(b) 使用Erbar-Maddox图求 R=1.5Rm的理论板数;(c) 使用Kikbride 法确定进料位置。
普通多组分精馏的原理

普通多组分精馏的原理普通多组分精馏是一种常用的物理分离技术,用于将多种组分按照其沸点的差异进行分离和纯化。
其基本原理是利用不同组分的沸点差异,通过加热液体混合物,使其中一个或多个组分蒸发,然后再将蒸汽冷凝,得到纯净的组分。
普通多组分精馏过程中涉及到一系列的操作和装置,其中最基本的装置是精馏塔。
精馏塔通常由一个高度较高的塔筒和一系列水平安装的塔板组成,塔板上设有大量密布的塔板孔和下料孔。
液体混合物通过上部喷淋塔板进入塔筒内,然后在塔板孔的作用下形成多个液滴。
从塔顶向下流动的反流液体与从塔底向上流动的精馏液体相接触,通过蒸汽-液体平衡,发生质量传递和传热过程。
在普通多组分精馏中,通常会选择一种组分作为轻组分,其沸点较低,而将其他组分作为重组分,其沸点较高。
加热后,轻组分蒸发,并被吸附到塔顶的冷凝器中,冷凝成液体,被称为顶产品。
剩余的液体在精馏塔内逐渐升温,重组分逐渐蒸发,与轻组分的冷凝液发生交替相接触,通过多次汽液平衡,使得各组分逐渐富集。
普通多组分精馏的效率受到一系列因素的影响。
首先是加热方式,通常可以选择直接加热或间接加热。
直接加热是通过将加热介质直接接触到精馏塔内,实现对液体的加热,优点是传热效率高,但缺点是介质可能会与组分发生反应。
间接加热是通过介质流经换热器,间接传递热量给液体,优点是可控性好,但传热效率较低。
其次是塔板设计和操作参数的选择。
塔板设计要考虑到液滴的传递和分离,以及液体和气体的接触效率。
操作参数包括物料负荷、回流比、塔板孔的尺寸等,这些参数对精馏的效率和分离效果有着重要影响。
最后是冷凝器的设计。
冷凝器通过将蒸汽冷却并凝结,改变气体和液体之间的相态,从而实现组分的分离。
冷凝器的设计应考虑到冷却介质的选择、冷凝速率以及顶部温度等因素。
普通多组分精馏是一种常见的分离技术,在石油化工、化学工程等领域具有广泛应用。
根据不同的需求,可以选择不同的操作策略和装置设计,以实现高效的分离和纯化。
多组分普通精馏

多组分普通精馏概述按被分离混合物中组分的数目可分为两组分精馏和多组分精馏。
工业生产中,绝大多数为多组分精馏,但两组分精馏的原理及计算原则同样适用于多组分精馏,只是在处理多组分精馏过程时更为复杂些,因此常以两组分精馏为基础。
精馏操作流程精馏分离过程可连续操作,也可间歇操作。
精馏装置系统一般都应由精馏塔、塔顶冷凝器、塔底再沸器等相关设备组成,有时还要配原料预热器、产品冷却器、回流泵等辅助设备。
图3-3精馏塔中物料流动示意图精馏原理工业上是将每个单级分离器做成一块;或在一个圆形的塔内装有一定高度的填料。
板上液层或填料表面是汽液两相进行传热和传质的场所。
如图所示为一精馏塔。
下面由加热釜(再沸器)供热,使釜中残液部分汽化后蒸汽逐板上升,塔中各板上液体处于沸腾状态。
顶部冷凝得到的馏出液部分作回流入塔,从塔顶引人后逐板下流,使各板上保持一定液层。
上升蒸汽和下降液体呈逆流流动,在每块板上相互接触进行传热和传质。
原料液于中部适宜位置处加入精馏塔,其液相部分也逐板向下流入加热釜,汽相部分则上升经各板至塔顶。
由于塔底部几乎是纯难挥发组分,因此塔底部温度最高,而顶部回流液几乎是纯易挥发组分,因此塔顶部温度最低,整个塔内的温度,由下向上逐渐降低。
双组分和多组分精馏的异同第一节 设计变量 一、基本概念(一)、公式(郭氏法)N ν——描述系统所需的独立变量数N c ——各独立变量之间的约束数(这些变量之间可以列出的方程数以及给定的条件∴N i = N ν-N c相同点:基本原理一致主要工具相同:物料,衡算,热衡,相平衡关系不同点:双组份常用图解法多组份常用简捷法严格计算法(计算机算)cviNN N -=N i——设计变量数(二)、计算根据相律确定每一物流的对变量数任一处于平衡态的物系 f(自由度)=c-π+2c——组分数π——相数∴单相系 f=c+1两相系 f=c自由度也是描述系统所需的独立变量数。
应当注意:相律所指的独立变量是指强度性质,即温度、压力、浓度,是与系统的量无关的性质。
- 1、下载文档前请自行甄别文档内容的完整性,平台不提供额外的编辑、内容补充、找答案等附加服务。
- 2、"仅部分预览"的文档,不可在线预览部分如存在完整性等问题,可反馈申请退款(可完整预览的文档不适用该条件!)。
- 3、如文档侵犯您的权益,请联系客服反馈,我们会尽快为您处理(人工客服工作时间:9:00-18:30)。
3.3 最少理论板数 Nmin
精馏塔在操作过程中,将塔顶蒸气全部冷凝, 精馏塔在操作过程中,将塔顶蒸气全部冷凝,其 凝液全部返回塔顶作为回流,称此操作为全回流, 凝液全部返回塔顶作为回流,称此操作为全回流,回 流比R为无穷大(R=∞)。 此时通常不进料,塔顶、 流比R 为无穷大( R=∞) 此时通常不进料, 塔顶 、 塔底不采出。故精馏塔内气、液两相流量相等, 塔底不采出 。 故精馏塔内气 、 液两相流量相等 , L = 两操作线效率均为1 并与对角线重合。 V,两操作线效率均为1,并与对角线重合。由于全回 流操作时,使每块理论板分离能力达到最大, 流操作时,使每块理论板分离能力达到最大,完成相 同的分离要求,所需理论板数最少, 同的分离要求,所需理论板数最少,并称其为最小理 论板数Nmin 。
即
ϕ l=DxD,l/Fzl
某精馏塔进料中含n-C600.33, n[ 例 ] : 某精馏塔进料中含 , C700.33, n-C800.34。 要求馏出液中 , 。 要求馏出液中n- C70 含量不大于0.011,釜液中 含量不大于 ,釜液中n-C60含量不大于 0.015(以上均为摩尔分数 。 若进料流率为 以上均为摩尔分数)。 以上均为摩尔分数 100kmol/h,试求馏出液和釜液的流量及 / , 组成。 组成。
W,x W,i ,w i
总物料衡算式: 总物料衡算式: F=D+W 组分物料衡算式: 组分物料衡算式: fi=di+wi 对于轻组分i w =0; 对于轻组分i: i=0;di=fi 对于重组分j:j=0;wj=fj 对于重组分j d =0; 馏出液的流量 D=∑di+dl+dh=∑fi+dl+dh 塔釜液流量 W=∑wj+wl+wh=∑fj+wl+wh 1≤i≤l- 1≤i≤l-1 h+1≤j≤c
在一精馏塔中分离苯(B)、 甲苯(T)、 例 、 在一精馏塔中分离苯 、 甲苯 、 二甲苯(X)和异丙苯 四元混合物。 和异丙苯(C)四元混合物 二甲苯 和异丙苯 四元混合物 。 进 料量为100kmol/h,进料组成为 B=0.2, 料量为 , 进料组成为z , zT=0.3,zX=0.1,zC=0.4。塔顶采用全凝 , , 。 饱和液体回流。规定二甲苯(X)在馏 器,饱和液体回流。规定二甲苯 在馏 出液中的含量不大于0.015(以上均为摩 出液中的含量不大于 ( 尔浓度) 在塔底的回收率为93.4% 。 尔浓度 ) , 在塔底的回收率为 % 试按清晰分割法计算馏出液、釜液组成。 试按清晰分割法计算馏出液 、 釜液组成 。
分离要求: 分离要求: (1) 给定馏出液中轻关键组分的摩尔分数xD,l 给定馏出液中轻关键组分的摩尔分数 x 和塔釜液中重关键组分摩尔分数x 和塔釜液中重关键组分摩尔分数xW,h。 重关键组分的物料衡算为: 轻、重关键组分的物料衡算为: D=∑di+dl+dh=∑fi+dl+dh F=D+W
(2)给定馏出液中重关键组分的摩尔分数 D,h和 给定馏出液中重关键组分的摩尔分数x 给定馏出液中重关键组分的摩尔分数 塔釜液中轻关键组分的摩尔分数x 塔釜液中轻关键组分的摩尔分数 W,l。
3、精馏操作流程
4、双组分和多组分精馏的异同 基本原理一致 相同点: 相同点: 主要工具相同:物衡,热衡, 主要工具相同:物衡,热衡,相 平衡关系 不同点: 不同点: 双组分常用图解法 简捷法 多组分常用 严格计算法( 严格计算法(计算 机算) 机算)
最小回流比R 3.2 最小回流比 min(Rm) 1. 回流比 对精馏的影响 回流比R对精馏的影响 回流比R是精馏过程的设计和操作的重 回流比 是精馏过程的设计和操作的重 要参数。 直接影响精馏塔的分离能力和系 要参数。R直接影响精馏塔的分离能力和系 统的能耗,同时也影响设备的结构尺寸。 统的能耗,同时也影响设备的结构尺寸。
E
图3-4 回流比对理论塔板数的影响
2.最小回流比 m 最小回流比R 最小回流比 有若干方法可用来计算最小回流比, 有若干方法可用来计算最小回流比 , 其中最 常用的是恩特伍德法( 常用的是恩特伍德法(underwood),推导该 ) 式时所用的假设: 式时所用的假设: (1)塔内汽相和液相在各块板上为恒摩尔流率 ) (2)各组分的相对挥发度均为常数 )
根据分离要求,可假定为清晰分割。 解:根据分离要求,可假定为清晰分割。 设n-C60(1)为轻关键组分,n-C70为重关 )为轻关键组分, 键组分, 为重组分。 键组分,则n-C80为重组分。 总物料衡算式 F=D+W=100 = 对于组分1 f1=DxD,1+WxW,1 对于组分 )+0.015W 即 100×0.33=D(1-0.011)+ × = ( - )+ 可解得: 可解得: D=32.34(kmol/h) ( ) W=67.66(kmol/h) ( ) 对于组分2 对于组分 f2=DxD,2+WxW,2 即 100×0.33=32.34×0.011+67.66xW,2 × = × + 解得 xW,2=0.482
非清晰分割: 非清晰分割: 重关键组分是非相邻的, 轻、重关键组分是非相邻的,组分间的组分 在塔顶、底出现。 在塔顶、底出现。 或:两关键组分相对挥发度相差较小
分配组分与非分配组分 在塔顶和塔底产物中同时出现的组分叫分 配组分, 配组分,只在塔顶或塔底出现的组分叫非分配 组分。 组分。
2.清晰分割的物料衡算 2.清晰分割的物料衡算 fi=F×xF,i × di=D×xD,i × D,xD,i,di F,x F,i ,f i wi=W×xW,i ×
清晰分割与非清晰分割 清晰分割: 清晰分割: 若馏出液中除了重关键组分外没有其它 重组分( 重组分(或比重关键组分还重的组分全部从 塔底排出) 塔底排出),而釜液中除了轻关键组分外没 有其它轻组分( 有其它轻组分(或比轻关键组分还轻的轻组 分全部从塔顶馏出液中采取) 分全部从塔顶馏出液中采取),这种分离称 为清晰分割。这是一种理想状态。 为清晰分割。这是一种理想状态。 适用:两关键组分相对挥发度相差较大, 适用:两关键组分相对挥发度相差较大, 且两者为相邻组分。 且两者为相邻组分。
αi,j (xD,i )m ∑ α -θ = Rm + 1 i=1 i,j
c
αi,jzi - ∑α -θ = 1 q i= i,j 1
c
参数;方程式的根。 θ — 参数;方程式的根。对 于c个组分的系统 个根, 的那一个根。 将有 c个根,只取 α l,k > θ > α h,k的那一个根。 q — 进料热状态参数,其 值由下式决定: 进料热状态参数, 值由下式决定: H m-H m,F q= H m hm - H m —离开进料级气相摩尔焓 ; H m,F — 进料摩尔焓; 进料摩尔焓; h m — 进入进料级液相摩尔焓
如下图示: 如下图示:
1.几个概念 1.几个概念 关键组分与非关键组分 对于多组分精馏来说,一个精馏塔, 对于多组分精馏来说,一个精馏塔,根据 工艺要求,通常指定两个组分的分离要求, 工艺要求 , 通常指定两个组分的分离要求 , 那么我们把被分离要求 分离要求的组分称为关键组 那么我们把被 分离要求 的组分称为关键组 其它未被指定分离要求 分离要求的组分称为非 分 , 其它未被指定 分离要求 的组分称为非 关键组分。由于挥发度总是有差别的, 关键组分 。 由于挥发度总是有差别的 , 所 以把易挥发的关键组分称为轻关键组分, 以把易挥发的关键组分称为轻关键组分 , 把不易挥发的关键组分称重关键组分。 把不易挥发的关键组分称重关键组分。
对于甲苯(T): 对于甲苯 :dT+wT=fT=30(kmol/h) dT=D-dB-dX=44-20-0.66=23.34(kmol/h) ∴wT=fT-dT=30-23.34=6.66(kmol/h) ∴W=∑wi=6.66+9.34+40=56(kmol/h) ∵xDi= di/D ∴xDB=20/44=0.455; xDT=23.34/44=0.530; xDC=0 ∑xDi=1.000
∵xWi=wi/W ∴xwB=0; xwT=6.66/56=0.119; xWX=9.34/56=0.167; xWC=40/56=0.714 ∑xWi=1.000
3. 最少理论板数 最少理论板数由以下芬斯克方程求得: 最少理论板数由以下芬斯克方程求得:
3. 回流比的选择 精馏总成本最低的回流比为最优回流比。 精馏总成本最低的回流比为最优回流比 。 总成 本为投资费用和操作费用之和。 本为投资费用和操作费用之和 。而回流比变化对精 馏同时存在正、 负两方面的影响, 如回流比为R 馏同时存在正 、 负两方面的影响 , 如回流比为 Rmin, 其塔为无穷高, 投资费用直线上升为无穷大。 其塔为无穷高 , 投资费用直线上升为无穷大 。 当 R 适当提高时,投资费用很快下降为有限大小, 适当提高时 ,投资费用很快下降为有限大小 ,总成 本下降。当回流比继续增大时,则能耗随之增大, 本下降 。当回流比继续增大时 ,则能耗随之增大 , 则操作费用迅速增大, 增到一定程度, 则操作费用迅速增大 , R 增到一定程度 , 设备费用 开始升高,如塔径增大等,将使总成本开始上升。 开始升高, 如塔径增大等 ,将使总成本开始上升 。 为此,回流比存在一优化的问题。 为此,回流比存在一优化的问题。
第三章 多组分精馏过程 3.1 概述 1、多组分精馏 、 按被分离混合物中组分的数目可分为两组分 按被分离混合物中组分的数目可分为两组分 精馏和多组分精馏。 精馏和多组分精馏。 工业生产中,绝大多数为多组分精馏, 工业生产中,绝大多数为多组分精馏, 但两组分精馏的原理及计算原则同样适用于 多组分精馏, 多组分精馏,只是在处理多组分精馏过程时 更为复杂些,因此常以两组分精馏为基础。 更为复杂些,因此常以两组分精馏为基础。
2、精馏原理示意图
多次部分气化和多次部分冷凝