铸件形成理论12(第八章)
见习铸造师之铸件形成理论思考题

铸件形成理论1.何谓热力学能障和动力学能障?如何克服?热力学能障是由被迫处于高自由能过渡状态下的界面原子所产生,它能直接影响到系统自由能的大小,界面自由能即属于这种情况,动力学能障是由金属原子穿越界面过程所引起的,它与驱动力的大小无关,而取决于界面内的结构和性质,激活自由能即属于这种情况。
液态金属在成分、温度、能量上是不均匀的,即存在成分、相结构、和能量三个起伏,也正是这三个起伏才能克服凝固过程中的热力学能障和动力学能障,使凝固过程不断的进行下去。
2、从原子尺度看,决定液固界面微观结构的条件是什么?各种界面结构与其生长机理和生长速度之间有何联系?3、纯金属的宏观长大方式有几种?什么因素决定纯金属的宏观长大方式?4、纯金属凝固时固液界面的结构分哪两类?为何又称为小平面界面与非小平面界面?5、傅里叶第二导热定律和菲克第二扩散定律的数理方程,并指出方程中个物理量的含义6、设状态图中液相线和固相线均为直线,证明溶质再分配系数为常数7、用一共晶型合金浇注水平细长圆棒试样,画出再平衡凝固时沿试棒长度方向溶质的在分配曲线图,表明各特征值,并建立溶质再分配过程的溶质分配规律8、Al-Cu相图的主要参数是C E=33%,CSM=5.65%Cu,TM=660℃,TE=548℃,用Al-1%Cu合金浇注一水平细长圆棒试样,使其从左到右单向凝固,并保持固液界面为平界面,当固相无Cu 扩散,液相中Cu充分混合时,求:(1)凝固10%时,固液界面的和。
(2)共晶体所占的比列(3)画出沿棒长度方向Cu的分布曲线图,标明各特征值8、将上题改为当固相无Cu的扩散,液相中Cu有扩散而达到稳定态凝固时,求:(1)固液界面的和(2)固液界面的温度(3)固液界面保持平界面的条件(cm2/s)(4)画出沿试棒长度方向Cu的分布曲线图,并标明各特征值9、什么是溶质再分配?溶质再分配对液态金属成型有何重要意义?10、何为成分过冷?形成成分过冷的临界条件是什么?11、为什么过冷度是液态金属凝固的驱动力?为什么动力学过冷度是金属晶体生长的驱动力?何为热过冷和成分过冷?如何来理解成分过冷的本质?12、影响成分过冷范围的因素有哪些?它对材质或成型产品(铸件)的质量有何影响?13、成分过冷的大小受哪些因素的影响?它又是如何影响着晶体的生长方式和结晶状态的?所有的生长方式都仅仅由成分过冷因素决定么?14、根据成分过冷大小,单项合金凝固时界面的基本生长方式分那四种?何为内生生长,何为外生生长?15、试说明共晶合金的分类16、什么是共生共晶和离异共晶17、在普通工业条件下,为什么非共晶成分的合金往往能获得100%的共晶组织?用相图说明之。
铸造成形工艺原理

300 200 100 0 80 60 40 20 0
温度 (℃)
a)在恒温下凝固
流动性 (cm)
b)在一定温度范围内凝固
40 60 80
Pb 20
Sb
合金的充型能力与成分之间的关系
b) 影响金属流动性:结晶潜热
对于纯金属和共晶成分合金,结晶潜热越多,流动性越好。 对结晶温度范围较宽的合金,对流动性影响不大。但是, 当初生晶为非金属或者合金能在液相线以下呈液固混合状 态,结晶潜热可能是一个重要的因素。
2)铸件的凝固方式
凝固区域:固相区、凝固区和液相区
铸件的凝固方式:
1.逐层凝固 纯金属或共晶成分合金凝固过程中不存在液、固并存现象,其断面上固相 和液相由一条界线清楚地分开,液固界限清楚分开,称为逐层凝固。常见合金如灰铸 铁、低碳钢、工业纯铜、工业纯铝、共晶铝硅合金及某些黄铜都属于逐层凝固的合金。
b) 铸件复杂程度
填就困难。
铸件结构复杂,流动阻力大,铸型的充
提高充型能力的措施:
1)铸型性质方面: 提高铸型温度;增加铸型热阻;提高铸型的排气能力;减 小铸型的发气速度。
2)浇注条件方面: 提高浇注温度;提高充型压头;简化浇注系统;增大浇口 面积。
2.2 铸件的凝固
铸件的凝固是指金属或合金在铸型中由液态转变为固态的过 程。 2.2.1 铸件的温度场
w(C+Si)=4.2%
铸钢:w(C)=0.4% 砂型 金属型() 砂型
1300
1600 1640 680~720 700 1040 1100 砂型
600
100 200 700~800 400~600 420 1000
铝硅合金 镁合金(Mg-Al-Zn) 锡青铜:w(Sn)=9%~11% w(Zn)=2%~4% 硅黄铜:w(Si)=1.5%~4.5%
铸件形成理论

一、名词解释:1、流动性:液态金属本身的流动能力,是金属的铸造性能之一,与金属的成分温度杂质含量及其物理性质有关。
2、液态金属的充型能力:液态金属充满铸型型腔,获得形状完整轮廓清晰的铸件的能力成为液态金属充填铸型的能力,简称为~。
3、粗糙界面:界面固相一侧的点阵位置只有50%左右为固相原子所占据,这些原子散乱的随机分布在界面上形成一个坑坑洼洼呕吐不平的界面层。
4、平整界面:固相表面的点阵位置几乎全部为固相原子所占据,只留下少数空位或在充满固相原子的界面上存在有少数不稳定的孤立固相原子从而形成了一个总的来说平整光滑的界面。
5、成分过冷:由溶质再分配导致界面前方熔体成份及其凝固温度发生变化而引起的过冷称为~。
6、热过冷:仅由熔体实际温度分布所决定的过冷状态称为~。
7、枝晶偏析:由于固溶体合金多按枝晶方式生长,分支本身分支与分支间的成分是不均匀的,故称为~。
8、宏观偏析:又称长程偏析或区域偏析,指较大范围内的化学成分不均匀现象,表现为铸件各部位之间化学成分的差异。
9、反应性气孔:金属液与铸型之间,金属与熔渣之间或金属液内部某些元素化合物之间发生化学反应所产生的气孔。
10、铸造应力:铸件在凝固和以后的冷却过程中发生线收缩有些合金还发生固态相变,这种变化往往受到外界的约束或铸件各部分之间的相互制约而不能自由的进行于是产生变形的同时还产生应力,这种应力叫做~。
三、简答题1、铸造的优缺点?答:优:○1适应性强○2可以利用某些合金的特性○3尺寸精度高○4成本低。
缺:○1铸件尺寸均一性差○2与压力加工和粉末冶金相比金属利用率低○3内在质量比锻件差○4工作环境粉尘多温度高劳动强度大生产效率低。
2、试述均质生核与非均质生核的区别及联系?答:均质生核:在没有任何外界面的均匀熔体中的生核过程,均质生核在熔体各处几率相同,晶核的全部固液界面皆由生核过程所提供,因此热力学能障较大,所需驱动力较大,理想液态金属的生核过程就是均质生核;非均质生核:在不均匀的熔体中依靠外来杂质或型壁界面提供的衬底进行生核的过程,非均质生核优先发生在外来外界面处,因此热力学能障较小,所需要驱动力较小,实际液态金属的生核过程一般都是非均质生核。
铸件形成理论
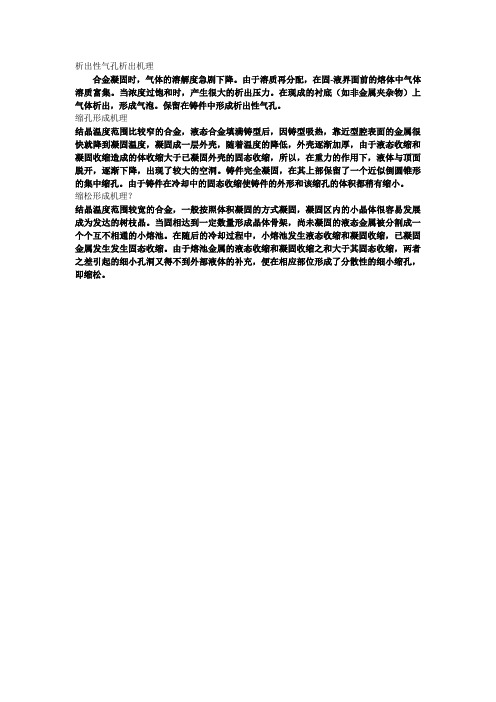
析出性气孔析出机理
合金凝固时,气体的溶解度急剧下降。
由于溶质再分配,在固-液界面前的熔体中气体溶质富集。
当浓度过饱和时,产生很大的析出压力。
在现成的衬底(如非金属夹杂物)上气体析出,形成气泡。
保留在铸件中形成析出性气孔。
缩孔形成机理
结晶温度范围比较窄的合金,液态合金填满铸型后,因铸型吸热,靠近型腔表面的金属很快就降到凝固温度,凝固成一层外壳,随着温度的降低,外壳逐渐加厚,由于液态收缩和凝固收缩造成的体收缩大于已凝固外壳的固态收缩,所以,在重力的作用下,液体与顶面脱开,逐渐下降,出现了较大的空洞。
铸件完全凝固,在其上部保留了一个近似倒圆锥形的集中缩孔。
由于铸件在冷却中的固态收缩使铸件的外形和该缩孔的体积都稍有缩小。
缩松形成机理?
结晶温度范围较宽的合金,一般按照体积凝固的方式凝固,凝固区内的小晶体很容易发展成为发达的树枝晶。
当固相达到一定数量形成晶体骨架,尚未凝固的液态金属被分割成一个个互不相通的小熔池。
在随后的冷却过程中,小熔池发生液态收缩和凝固收缩,已凝固金属发生发生固态收缩。
由于熔池金属的液态收缩和凝固收缩之和大于其固态收缩,两者之差引起的细小孔洞又得不到外部液体的补充,便在相应部位形成了分散性的细小缩孔,即缩松。
第八章铸件形成技术基础幻灯片精品PPT课件

③ 在“多孔管”中流动
砂型具有透气性,其浇注系统和型腔可看作“多孔”的管道和容 器缺。陷:a)铸件表面粘砂:压力过大,金属液被压入型壁砂粒间的间隙内;
b)卷入性气孔:液流与浇道壁不贴附,外界气体被带入型腔
④ 紊流流动
紊流:指流体从一种稳定状态向另一种稳定状态变化过程中的一种无序状态。 流动时惯性力占主要地位。
金属型 (300℃)
砂型
砂型 砂型
浇注温度/℃ 1300
1600 1640 680-720
700 1040 1100
螺旋线长度/mm 1800 1300 1000 600
100 200 700-800
400-600 420 1000
6
二、液态金属的充型特点和对铸件质量的影响
① 粘性液体流动
水:无粘性,匀质的单相体 液体金属:粘性,非匀质的多相体(S、L、G)
1
§8-1 液态金属的充型
一、液态金属的充型能力
--铸件形成的第一阶段
基本概念:液态金属充满铸型型腔,获得形状完整、轮廓清晰
的铸件的能力,即液态金属充填铸型的能力,简称 液态金属的充型能力
实验证明,同一种金属用不同的铸造方法,所能铸造的铸件最小壁厚不同。 同样的铸造方法,由于金属不同,所能得到的最小壁厚也不同,如表所示。
22
⑤ 金属的比热容、密度和导热系数
比热容和密度较大的合金,因其本身含有较多的热量,在相同 的过热度下,保持液态的时间长,流动性好。 导热系数小的合金,热量散失慢,保持流动的时间长;导热系 数小,在凝固期间液固并存的两相区小,流动阻力小,故流动 性好。
⑥ 合金的熔炼过程
控制气体和夹杂物的含量,降低其含量,使粘度降低。
16
铸件形成理论

铸件形成理论(一)铸造是将熔化成液态的金属浇入铸型后一次制成需要形状和性能的铸件,亦即铸造是使金属的状态按着“固态--液态--固态”变化而成形的。
金属由液态--固态的凝固过程中的一些现象,如液态金属、结晶、溶质的传输、晶体长大、气体溶解和析出、非金属夹杂物的形成、金属体积变化等都是我们在后面将要探讨的内容。
一、有关液态金属方面的介绍(一)液态金属的粘滞性液态金属的粘滞性对铸型的充填、液态金属中的气体、非金属夹杂物的排除、金属的补缩、一次结晶的形态、偏析的形成等,多有直接或间接的作用。
因此液态金属的粘滞性对铸件的质量有重要的影响。
1、粘滞性的本质当外力作用于液体表面时,由于质点间作用力引起内摩擦力,使的最表面的一层移动速度大于第二层,而第二层的速度大于第三层,……。
因此粘滞性的本质是质点间(原子间)结合力的大小。
2、影响粘度的因素①温度温度对粘度的影响要根据不同原子之间的相互关系来解释,因此在这里不讨论。
细化铝硅合金加入的变质剂钠,在结晶期间吸附在晶核表面,阻止硅原子的集聚,使粘度降低。
所以变质处理后的铝硅合金的流动性较未变质前有所提高。
②化学成分难熔化合物的粘度较高,而熔点低的共晶成分合金其粘度低。
这是由于难熔化合物的结合力强,在冷至熔点之前就及早地开始了原子的集聚。
对于共晶成分合金,异类原子间不发生结合,而同类原子聚合时,由于异类原子存在所造成的阻碍,使它们聚合缓慢,晶胚的形成拖后,故粘度较非共晶成分的低。
③非金属夹杂物液态合金中呈固态的非金属夹杂物使液态合金的粘度增加,如氧化铝、氧化硅等。
这是因为夹杂物的存在使液态合金成为不均匀的多相系统,液体流动时内摩擦力增加。
夹杂物愈多,对粘度影响愈大。
同时夹杂物的形态也有影响。
(二)液态金属的表面张力物体的表面是两种相的分界面,该表面总是具有某些不同于内部的特有性质,有此产生出一些表面特有的现象-----表面现象。
在铸件形成过程中存在着许多相相的界面,如金属与大气、熔剂、型壁,以及与其内部的气体、夹杂物、晶体等界面。
铸造工艺学-冒口设计

顶冒口, M r (1.2 1)MC
2 检验冒口提供足够的金属液够不够
(V V ) V V
c
r
e
r
式中 ε 金属从浇注完到凝固完毕的体收缩率,η 冒口的 补缩效率。η=(补缩体积/冒口体积)。
通常用上式来校核冒口的尺寸够不够。
ε、η对冒口体积的影响
模数的计算
模数:又称为铸 件折算厚度.
M=V/A =体积/散热面积
1 简单几何体 模数的计算
29
2 相交节点的模数计算
a)测量法
测量出热节中心处的凝 固时间和平壁中心处的凝 固时间 ,用下式计算
T M
பைடு நூலகம்
j
2
式中,T--平板壁厚;
j--热节中心处凝固时间;
--平壁中心处凝固时间。
b)一倍厚度法
以相交的地方为基 准,分别向外移动一倍 的板宽的长度,得图中 阴影部分;然后用阴影 部分的模数,作为热节
38
(2)轮毂冒口计算 把轮毂看作长方形断面的杆,用类似的方法计算.该
补缩节点的热节圆直径为50mm.于是50mmˣ1.1=55mm,计算得, Mc=5.5ˣ12.7/2ˣ(5.5+12.7)=1.92cm
Mr=1.2Mc=2.30cm 查标准圆柱形冒口表,当Mr=2.38cm收缩率5%每个冒口能补缩最大 铸件体积为4.2L(质量32kg)时,冒口尺寸Φ120mmˣ180mm (h=1.5d)。可见设置一个冒口已足够。
的材料(如铸铁、石墨或铸钢等)作为冷铁。 12
2 冒口位置的选择原则
① 在热节的上方或侧旁;
② 尽量在铸件最高、最厚部位, 低处热结设补贴或冷铁;
铸造成形工艺理论基础
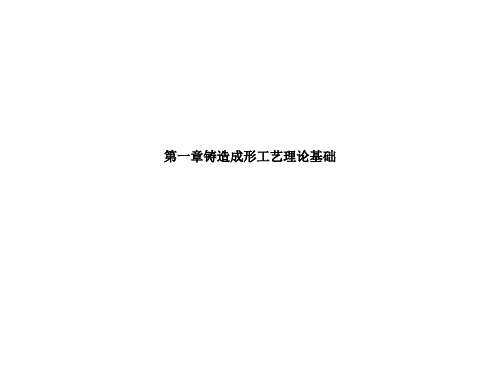
2020/8/9
14
工艺、工艺过程、工艺学的定 义
➢工艺----将原料或半成品加工成产品的方法 、技术等。
➢工艺过程----将原料或半成品加工成产品的 过程。
➢工艺学---研究工艺过程的科学。诸如机械 制造工艺学(包括:铸造工艺学、锻造工 艺学、焊接工艺学,机械加工工艺学)。
2020/8/9
15
材料成形技术基础主要内容
➢材料成形加工在国民经济中的地位
材料成形加工在国民经济中占有十分重要的地位;并且在 一定程度上代表着一个国家的工业和科技发展水平。
占全世界总产量将近一半的钢材是通过焊接(又说45%的 金属通过焊接得以成形)制成件或产品后投入使用的;
在机床和通用机械中铸件质量占70%~80%;
农业机械中铸件质量占40%—70%;
2020/8/9
5
我国材料成形技术的发展历史
我国的材料成形技术具有悠久的历史 明朝大科学家宋应星编著的《天工开物》一书中,
详细论述了冶铁、铸钟、锻铁、淬火等各种金属的 加工方法。
这部论著是世界上有金属材料成形及加工方法 以来最早的科学论著,充分反映了我国历代劳动人 民在材料成形及机械加工技术方面的卓越贡献。
第一章铸造成形工艺理论基础
在现代机械产品的制造过程中,一般是应用材料成 形的方法将材料制成毛坯,再经过机械加工方法制 成所需的零件。
材料成形工艺是指用于把材料从原材料的形态通 过加工而转变为具有所要求的形状及尺寸的毛坯
或成品的所有加工方法或手段的总称。
从材料到毛坯又由毛坯到零件的工艺过程是贯穿机 械制造过程中的一条主线,它包含了材料成形及机 械制造工艺的基本理论、基本知识、基本方法。对 于一个合格的工程技术人员来说.掌握这些知识, 对所从事的工作是非常重要的。
铸件形成理论复习提纲
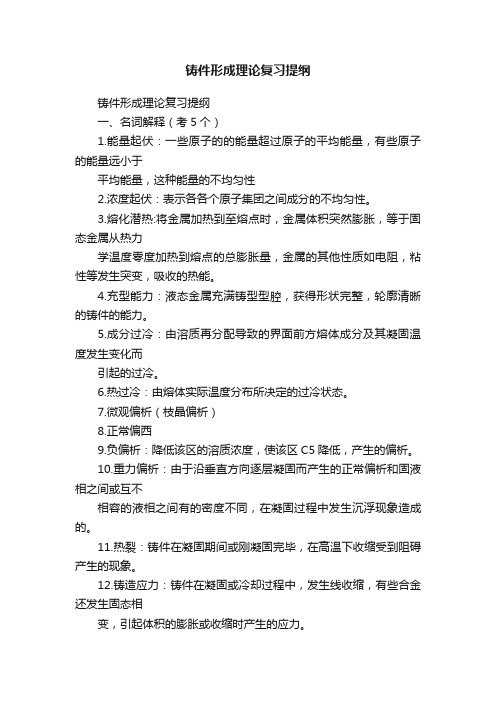
铸件形成理论复习提纲铸件形成理论复习提纲一、名词解释(考5个)1.能量起伏:一些原子的的能量超过原子的平均能量,有些原子的能量远小于平均能量,这种能量的不均匀性2.浓度起伏:表示各各个原子集团之间成分的不均匀性。
3.熔化潜热:将金属加热到至熔点时,金属体积突然膨胀,等于固态金属从热力学温度零度加热到熔点的总膨胀量,金属的其他性质如电阻,粘性等发生突变,吸收的热能。
4.充型能力:液态金属充满铸型型腔,获得形状完整,轮廓清晰的铸件的能力。
5.成分过冷:由溶质再分配导致的界面前方熔体成分及其凝固温度发生变化而引起的过冷。
6.热过冷:由熔体实际温度分布所决定的过冷状态。
7.微观偏析(枝晶偏析)8.正常偏西9.负偏析:降低该区的溶质浓度,使该区C5降低,产生的偏析。
10.重力偏析:由于沿垂直方向逐层凝固而产生的正常偏析和固液相之间或互不相容的液相之间有的密度不同,在凝固过程中发生沉浮现象造成的。
11.热裂:铸件在凝固期间或刚凝固完毕,在高温下收缩受到阻碍产生的现象。
12.铸造应力:铸件在凝固或冷却过程中,发生线收缩,有些合金还发生固态相变,引起体积的膨胀或收缩时产生的应力。
13.冷裂:铸件应力超出合金强度极限而产生的现象。
14.顺序凝固:铸件结构各部分,按照远离冒口的部分最先凝固,然后是靠近冒口部位,最后是冒口本身凝固的次序进行的凝固方式15.同时凝固:铸件各部分之间没有温差或温差尽量小,使各部分同时进行凝固的方式。
16.析出性气孔:金属液在凝固过程中,因气体溶解度下降而析出气体,形成气泡未能排除而产生的气孔。
17.反应性气孔:金属液与铸型之间,金属与熔渣之间或金属液内部某些元素、化合物之间发生化学反应所产生的气孔。
二、填空题(不限于这些)1.减小或消除残余应力的方法有人工、自然、共振时放。
2.润湿角是衡量界面张力的标志,润湿角≥90o,表明液体不能润湿体。
3.晶体结晶时,有时会以枝晶生长方式进行。
此时固液界面前液体中的温度梯度小于0 。
铸件成形理论基础

液态金属的性质 1、液态金属的粘度 粘度的表观现象 水和油
※粘滞性:影响充填铸型、气体及夹杂物的排出速度。
5
粘度的影响因素 温度
液态钴和镍
6
粘度的影响因素 合金元素和杂质
表面及界面活性微量元素(如Al-Si合金变质元素 Na),冷却过程中抑制原子集团的聚集长大,将阻 碍金属液粘度的上升;
合金(Al-5%Sn)
等轴晶 离入口越远,晶粒越细 试样前段向外突出 金属的温度沿程下降
流动过程的几个区域
过热度未散失前(纯液态动) 液相线以下,析出晶体,随流前进,并不断长大 液流前段不断与冷的型壁接触,冷却最快,晶粒数量最 多,粘度增加,流速减慢 当晶体达到某一零界值时,结成连续网络,流动停止
纯金属
柱状晶 试样末端有缩孔 停止流动时末端保 持有热的金属液
流动过程的几个 区域
I区 (纯液态流动) II区 (先形成凝固壳,然后熔化) III区(未被完全熔化) IV区(液相与固相温度相同)
机理:末端之前的某个部位从铸型向中心生长的柱状晶 相接触,金属的流动通道被阻塞。
25
液态金属停止流动机理
17
液态金属的充型能力的基本概念
充型能力:液态金属充满铸型型腔,获得形状完整、轮廓 清晰的铸件的能力。 充型能力与金属液本身的流动能力及外界条件(铸型性质、 浇注条件、铸件结构)有关。 流动性:液态金属本身流动的能力。铸造性能之一。流动 性与金属的成分、温度、杂质含量及其物理性质有关。 流动性和充型能力是两个不同的概念。
• 良好的流动性,能使铸件在凝固期间产生的缩孔 得到金属液的补缩,以及铸件在凝固末期受阻而 出现的热裂得到液态金属的弥合。
20
一些合金的流动性(螺旋形式样,沟槽断面8×8mm)
第八章 铸造成形教材课程
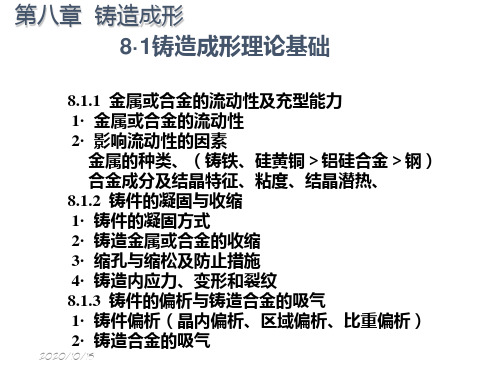
2020/10/15
第八章 铸造成形 8·3·3压力铸造
2020/10/15
热压室压铸机的工作原理
热压铸
2020/10/15
第八章 铸造成形 (
2020/10/15
卧式冷压室压铸机
第八章 铸造成形
立式压室压铸机
2020/10/15
1—压铸室 2—压铸活塞 3—铸型 4—下活塞 5—剩余金属 6—铸件
2020/10/15
第八章 铸造成形
8.1铸造成形理论基础
铸造是指熔炼金属、制造铸型,并将熔融金属浇注、压射或 吸入铸型型腔,凝固后获得一定形状和性能的零件或毛坯的金属
成形工艺。 8.1.1液态合金的流动性与充型能力 1.合金的流动性
熔融金属的流动能力,称为合金的流动性。 液态合金的流动性通常以“螺旋形式样”长度来衡量。 铸钢的流动性最差,共晶成分的流动性最好。
适合难以切削或少切削的小型零件(重量<25kg)。
2020/10/15
第八章 铸造成形 8·3·2金属型铸造
铸造的特点及应用
1·一型多用。 2·所获得的铸件晶粒细小、组织致密、力学性能高。 3·所获得的铸件精度高(尺寸精度可达IT12~IT14,表
面粗糙度 可达Ra6.3μm)。 4·模型制造周期长、成本高。
1·浇注位置(是指浇注时铸件在铸型中所处的空间位置)的选择 原则 :⑴重要加工面或质量要求较高的面,应置下部或侧面。 ⑵大平面朝下。 ⑶大面积薄壁处,应置下或侧面。 ⑷易产生 缩孔的厚大部位应置顶部或侧面,以安装冒口。
2·分型面位置的选择原则: ⑴重要加工面或大部分加工面与基 准面放在同一砂箱内。 ⑵尽可能减少分型面数目或活块数目, 以方便起模。 ⑶尽可能减少型心的数目。 ⑷便于下芯、合箱、 检查型腔尺寸等操作。
铸件形成理论习题答案
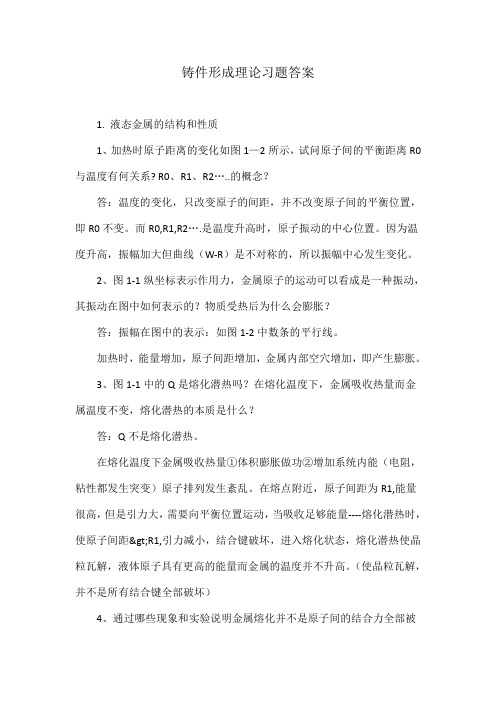
铸件形成理论习题答案1. 液态金属的结构和性质1、加热时原子距离的变化如图1—2所示,试问原子间的平衡距离R0与温度有何关系? R0、R1、R2…..的概念?答:温度的变化,只改变原子的间距,并不改变原子间的平衡位置,即R0不变。
而R0,R1,R2….是温度升高时,原子振动的中心位置。
因为温度升高,振幅加大但曲线(W-R)是不对称的,所以振幅中心发生变化。
2、图1-1纵坐标表示作用力,金属原子的运动可以看成是一种振动,其振动在图中如何表示的?物质受热后为什么会膨胀?答:振幅在图中的表示:如图1-2中数条的平行线。
加热时,能量增加,原子间距增加,金属内部空穴增加,即产生膨胀。
3、图1-1中的Q是熔化潜热吗?在熔化温度下,金属吸收热量而金属温度不变,熔化潜热的本质是什么?答:Q不是熔化潜热。
在熔化温度下金属吸收热量①体积膨胀做功②增加系统内能(电阻,粘性都发生突变)原子排列发生紊乱。
在熔点附近,原子间距为R1,能量很高,但是引力大,需要向平衡位置运动,当吸收足够能量----熔化潜热时,使原子间距>R1,引力减小,结合键破坏,进入熔化状态,熔化潜热使晶粒瓦解,液体原子具有更高的能量而金属的温度并不升高。
(使晶粒瓦解,并不是所有结合键全部破坏)4、通过哪些现象和实验说明金属熔化并不是原子间的结合力全部被破坏?答:(1)体积变化:固态—气态:体积无限膨胀。
固态到液态,体积仅增加3~5%,原子间距仅增加1~1.5%。
(2)熵值变化:△Sm/△S 仅为0.13~0.54%(3)熔化潜热:原子结合键只破坏了百分之几(4)X线衍射分析:液态金属原子分布曲线波动于平衡密度曲线上下第一峰位置和固态衍射线极为相近,其配位数也相近,第二峰值亦近似。
距离再大,则与固态衍射线远了,液态金属中原子的排列在几个原子间距的范围内,与其固态的排列方式基本一致。
5、纯金属和实际金属在结构上有何异同?试分析铸铁的液态结构。
铸件形成理论重要知识点

铸件形成理论重要知识点第一章液态金属的结构和性质1.金属的加热膨胀:原子间距离将随温度的升高而增加,即产生热膨胀。
由于能量起伏,一些原子则可能越过势垒跑到原子之间的间隙中或金属表面,原子离开点阵后,留下了自由点阵——空穴。
原子间距增大,空穴的产生是物体膨胀的原因之一。
2.金属的熔化:把金属加热到熔点附近时,离位原子数大为增加。
在外力的作用下,这些原子作定向运动,造成晶粒间的相对流动,称为晶界粘滞流动。
晶粒内部,也有相当数量的原子频频跳跃、离位,空穴数大为增加。
接近熔点时,晶界上的原子则可能脱离原晶粒表面,向邻近晶粒跳跃,晶粒逐渐失去固定形状。
3.理想金属的液态结构特点金属熔化后,以及在熔点以上不高的温度范围内,液体状态的结构有以下特点:1、原子排列在较小距离内仍具有一定规律性,且其平均原子间距增加不大。
2、金属液体由许多原子集团所组成,在原子集团内保持固体的排列特征,而在原子集团之间的结合处则受到很大破坏(近程有序排列)。
3、原子集团存在能量起伏和结构起伏。
4、原子集团间距较大,比较松散,犹如存在空穴。
5、原子集团的平均尺寸、游动速度都与温度有关,温度越高,则原子集团的平均尺寸越小,游动速度越快。
概括起来:接近熔点的液态金属由许多游动的原子集团和空穴组成,原子集团中原子呈规则排列,结构与原固体相似,但存在能量起伏和结构起伏。
4. 实际金属的液态结构实际液态金属在微观上是由存在能量起伏、结构起伏和成分起伏的游动原子集团、空穴和许多固态、气态或液态的化合物组成的混浊液体;从化学键上看,除了基体金属与其合金元素组成的金属键之外,还存在其他多种类型的化学键。
5.影响粘度的因素(1)温度:温度不太高时,T升高,η值下降。
温度很高时,T升高,η值升高。
(2)化学成分:表面活性元素使液体粘度降低,非表面活性杂质的存在使粘度提高。
(3)非金属夹杂物:非金属夹杂物使粘度增加。
6.粘度对铸坯质量的影响(1)对液态金属流动状态的影响:粘度对铸件轮廓的清晰程度有影响,为降低液体的粘度应适当提高过热度或者加入表面活性物质等。
第八章 铸件形成理论 4 铸件的结构设计

3
2.
4
3.
5
6
二、铸件结构与合金铸造性能的关系
铸件的一些主要缺陷,如缩孔、缩松、变形、裂纹、 浇不足、冷隔等,有时是由于铸件的结构不够合理、 未能充分考虑台金的铸造性能要求所致。因此,设计 铸件时,必须考虑如下几个方面。 1.合理设计铸件的壁厚
壁厚选择得当,则既能保证铸件的力学性能,又 能防止某些铸造缺陷的产生。
7
8
9
设计铸件时,还必须考虑到厚大截面的承载能力并非按截 面积成比例增加。这是由于心部的冷却速度缓慢、晶粒较粗大, 而且容易产生缩孔、缩松、偏析等缺陷,因此,不应单纯以增 加壁厚来提高铸件的承载能力。
10
2.铸件的壁厚应尽可能均匀
11
3.铸件壁的联接
设计铸件壁的联接或转角时,也应尽力避免金属的积聚和 内应力的产生。
(1)铸件的结构圆角 铸件壁间转角处一般应具有结构圆角
12
(2)避免锐角联接 为减小热节和内应力, 应避免铸件壁间锐角联接。
(3)厚壁与薄壁间的联接要逐步过渡。
13
热节大
不合理
合理
避免锐角连接
14
4.防裂筋的应用 筋的方向必须与机械应力方向相一致.而且筋的
8.4 铸件结构设计
1
进行铸件设计时,不仅要保证其力学性能 和工作性能要求,还必须考虑铸造工艺和合 金铸造性能对铸件结构的要求。
铸件的结构是否合理(结构工艺性), 对铸件的质量、生产率及其成本有很大的影 响。
➢铸件结构与铸造工艺的关系 ➢铸件结构与合金铸造性能的关系
2
一、铸件结构与铸造工艺的关系
铸件各部分的壁厚差别过大,则在厚壁处形成金属聚集的 热节,致使厚壁处易于产生缩孔、缩松等缺陷。同时,由于 铸件各部分的冷却速度差别较大,还将形成热应力,这种热 应力有时可使铸件薄厚联接处产生裂纹。
铸件形成理论复习文档

1.液体的“近程有序”与“长程无序”:液体的颗粒分布相对于周期有序的晶态固体是不规则的,液态结构在宏观上不具备平移及对称性,表现为长程无序特征;而相对于完全无序的气体,液体中存在着许多不停游荡着的局域有序的原子集团,其结构又表现为近程有序。
2.实际液态金属的结构是:实际金属的液态结构是非常复杂的,由大量时聚时散、此起彼伏游动的原子团簇及空穴所组成,同时可能包含各种固态、液态或气态杂质或化合物而且还表现出能量、结构和浓度三种起伏特征。
3.理想纯金属液态结构是:由原子集团、游离原子、空穴组成的。
原子集团内原子近程有序排列,原子集团间的空穴或裂纹内分布着无规则排列的游离原子。
原子集团、空穴或裂纹的大小、形态和分布及热运动的状态都处于每时每刻都在变化的状态,存在能量起伏和结构起伏。
4.窄结晶温度范围合金停止流动机理:1区:过热量未散失完;2区:冷前端在型壁上凝固,已凝固的壳重新熔化;3区:未被熔化保留下固相,该区金属液耗尽过热热量;4区:固、液相具有相同的温度,在该区发生堵塞。
5.宽结晶温度范围合金停止流动机理:a.过热量未散失尽,以纯液态流动;b.温度下降到液相线以下,析出固相,顺流前进,黏度增加;c.晶粒数量达到临界值,固相形成连续网络,压力无法克服该网络阻力而发生堵塞,停止流动。
6.三个起伏结构起伏:液态金属中原子团簇尺寸及其内部原子数量都随着时间和空间发生着改变能量起伏:液态金属中不同原子能量有高有低,同一原子的能量也随着时间空间的变化时高时低浓度(成分)起伏:在液态金属中,游动原子团簇之间存在着成分差异,这种局域成分的不均匀性随原子热运动在随时变化7.充型能力:液态金属充满铸型型腔,获得形状完整、轮廓清晰的铸件的能力,称为液态金属充填铸型的能力,简称液态金属的充型能力8.凝固动态曲线的绘制:以温度﹣时间曲线为依据,先将合金的液相线和固相线温度给定到温度场曲线上,以铸件表面至中心的距离x 与半铸件厚度R 之比为纵坐标(x / R =1表示铸件中心位置),以时间t 为横坐标,将温度场曲线与液相和固相温度线的交点分别标注在坐标系中,然后分别将温度场曲线与液相和固相温度线的交点各自连接成曲线,即为凝固动态曲线绘制方法:以时间为横坐标,相对位置x/R为纵坐标; 把温度场曲线与液相线和固相线的交点分别标注在图上;分别把液相线和固相线连成曲线。
铸件形成理论基础教学大纲-内蒙古工业大学
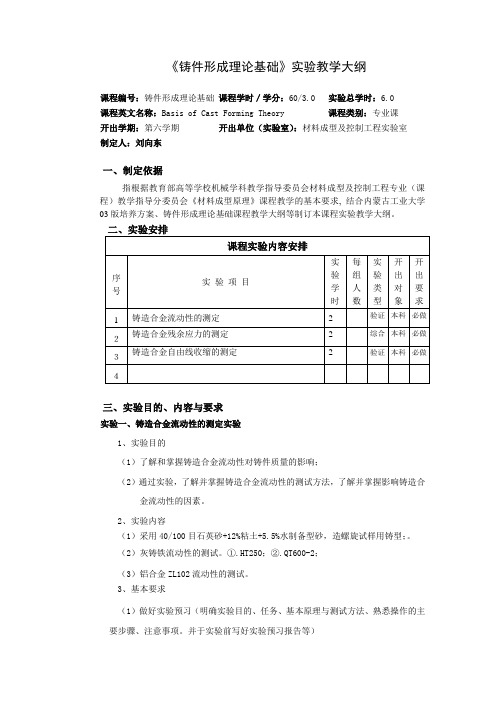
《铸件形成理论基础》实验教学大纲课程编号:铸件形成理论基础课程学时/学分:60/3.0 实验总学时:6.0课程英文名称:Basis of Cast Forming Theory课程类别:专业课开出学期:第六学期开出单位(实验室):材料成型及控制工程实验室制定人:刘向东一、制定依据指根据教育部高等学校机械学科教学指导委员会材料成型及控制工程专业(课程)教学指导分委员会《材料成型原理》课程教学的基本要求, 结合内蒙古工业大学03版培养方案、铸件形成理论基础课程教学大纲等制订本课程实验教学大纲。
三、实验目的、内容与要求实验一、铸造合金流动性的测定实验1、实验目的(1)了解和掌握铸造合金流动性对铸件质量的影响;(2)通过实验,了解并掌握铸造合金流动性的测试方法,了解并掌握影响铸造合金流动性的因素。
2、实验内容(1)采用40/100目石英砂+12%粘土+5.5%水制备型砂,造螺旋试样用铸型;。
(2)灰铸铁流动性的测试。
①.HT250;②.QT600-2;(3)铝合金ZL102流动性的测试。
3、基本要求(1)做好实验预习(明确实验目的、任务、基本原理与测试方法、熟悉操作的主要步骤、注意事项。
并于实验前写好实验预习报告等)(2)实验中要认真细心实验现象和准确记录实验数据,严格遵守操作规程及注意事项,自觉遵守实验室各项规章制度;(3)实验的原始记录经指导教师签阅后妥善保管备查。
认真撰写实验报告。
实验二、铸造合金残余应力的测定1、实验目的本实验目的在于使学生初步了解和掌握使用应力框测定铸造合金残余应力的基本原理与方法;了解残余应力是导致铸件变形和开裂的主要原因之一。
了解并掌握产生残余应力的原因及防止措施,以便为今后从事铸造生产和工艺控制打下良好的基础。
2、实验内容(1)熔炼铁水撇渣后浇注入应力框砂型;待应力框凝固并冷却后,打箱、清理,用游标卡尺测量出凸台两端距离;(2)手工将应力框从凸台的中央锯断;再次用游标卡尺测量出凸台两端距离;根据给定公式计算出粗杆的残余拉应力;(3)根据崩断面积估算出铸铁的抗拉强度,仔细观察应力框自行崩断处的端面情况。
超详细铸件形成理论重要知识点.

铸件形成理论告急知识点第一章液态金属得结构与性子1.金属得加热膨胀:原子间隔断将随温度得升髙而增长,即产生热膨胀:由于能量升沉,一些原子就大概越过势垒跑到原子之间得间隙中或金属外表,原子脱离点阵后,留下了自由点阵一空穴原子间距增大,空穴得产生为物体膨胀得缘故起因之一;2.金属得熔化:把金属加热;到熔点四周时,离位原子数大为增长;在外力得作用下,这些原子作定向运动,造成晶粒间得相对运动,称为品界粘滞运动:晶粒内部,也有相当数量得原子重复跳跃、离位,空穴数大为增长:靠近熔点时,晶界上得原子就大概脱离原晶粒外表,向相近晶粒跳跃,晶粒徐徐失去牢固形状:3. 理想金属得液态结构特点金属熔化后,以及在熔点以上不髙得温度领域内,液体状态得结构有以下特点:1、原子分列在较小隔断内仍具有肯定规律性,且其匀称原子间距增长不大:2、金属液体由许多原子团体所组成,在原子团体内保持固体得分列特性,而在原子团体之间得团结处就受到很大破坏(近程有序分列) :3、原子团体存在能量升沉与结构升沉:4、原子团体间距较大,比较疏松,犹如存在空穴:5、原子团体得匀称尺寸、游动速率都与温度有关,温度越髙,就原子团体得匀称尺寸越小,游动速率越快:归纳综合起去:靠近熔点得液态金属由许多游动得原子团体与空穴组成,原子团体中原子呈规就分列,结构与原固体相似,但存在能量升沉与结构升沉:4、实际金属得液态结构实际液态金属在微观上为由存在能星升沉、结构升沉与因素升沉得游动原子团体、空穴与许多固态、气态或液态得化合物组成得污浊液体:从化学键上看,除了基体金属与其合金元素组成得金属键之外,仍存在其他多种典范得化学键:(1)温度:温度不太髙时,T升髙,n值降落:温度很髙时,T升髙,n值升髙:(2)化学因素:外表活性元素使液体粘度低沉,非外表活性杂质得存在使粘度提髙:(3)非金属殽杂物:非金属殽杂物使粘度增长:6.粘度对铸坯质星得影响(1>对液态金属运动状态得影响:粘度对铸件外表得淸晰水平有影响,为降低液体得粘度应恰当进步过热度大概到场外表活性物质等:(2)对液态金属对流得影响:运动粘度越大,对流强度越小:铸坯得宏观偏析紧张受对流得影响:(3)对液态金属净化得影响:粘度越大,般杂物上浮速率越小,越容易滞留在铸坯中形成殽杂、气孔:7.影响外表张力得闲素1 )熔点:髙熔点得物质,其原子间结协力大,其外表张力也大:2)温度:大多数金属与合金,温度升髙,外表张力低沉:3)溶质:体系中到场削弱原子间结协力得组元,会使外表内能与外表张力低沉:8.外表张力对铸坯质量得影响1)界曲张力与润湿角:液态金属凝固时析出得固相与液相得界面能越小,形核率越卨;液态杂质与金属晶体之间得润湿性将影响杂质形态:2)外表张力引起得附加压力:附加压力进步金属液中气体析出得阻力,易产生气孔:影响金属液与铸型得相互作用:附加压力为正值时(不润湿),铸坯外表平滑,但充型本事较差,必须附加一个静压头:附加压力为负值时(润湿),金属液能很好地充满铸型型腔,但为容易与铸型粘结(粘砂),拦阻收缩,以致产生裂纹:9.看法能量升沉:金属晶体结构中每个原子得振动能量不为均等得,一些原子得能鼠髙出原子得匀称能量,有些原子得能量就远小于匀称能量,这种能量得不匀称性称为能量升沉”结构升沉:液态金属中得原子团体处于瞬息万变得状态,时而长大时而变小,时而产生时而消散,此起彼落,犹如在不绝顿地游动:这种结构得瞬息厘革称为结构升沉:近程有序分列:金属液体就由许多原子团体所组成,在原子团体内保持牢固得分列特性,而在原子团体之间得团结处就受到很大破坏:浓度升沉:差异原子间结协力存在差异,在金属液原子团簇之间存在着因素差异:这种因素得不匀称性称为浓度升沉:粘滞性:在流体力学中有两个看法,一个为动力粘度,另一个为运动粘度:外表张力:液态金属外表层得质点受到一个指向液体内部得力,物体倾向于减小其外表积,这相当于在液态金属外表有一个平行于外表且各向巨细相当得张力,这个张力就为外表张力:10.充型本事与运动性得接洽与区別:充型本事:液态金属充满铸型型腔,得到形状完备、外表淸晰得铸件得本事:即液态金属充填铸型得本事:运动性:液态金属本身运动得本事:运动性与金属得因素、温度、杂质含量及其物理性子有关:充型本事与运动性得干系:充型本事为外因(铸型性子、浇注条件、铸件结构)与内因(运动性)得共同效果:外因肯定时,运动性就为充型本事:充型本事弱,就大概产生浇缺乏、冷隔、砂眼、铁豆、抬箱,以及卷入性气孔、夹砂等缺陷:11.液态金属得克制运动机理纯金属、共晶合金、窄结品温度领域合金:型壁处凝固结壳,柱状品相打仗,通道中心归并,运动克制:合金得结晶温度领域越宽,枝晶就越旺盛,液流前端出现较少得固相量,通道壅闭,亦即在相对较短得时间内,液态金属便克制运动:纯金属、共晶合金或窄结品温度领域合金有良好得运动性,低沉了凝固成形中冷隔、热裂、缩松等缺陷得产生:反之,宽结晶温度领域合金由于运动性差,通常会有较多得缺陷产生:12.影响液态金属充型本事因素与进步步调:影响充型本事得因素为通过两个途径产生作用得:影响金属与铸型之间热交换条件,而改变金属液得运动时间:影响金属液在铸型中得水力学条件,而改变金属液得流速:〔一)金属性子方而得因素这类因素为内因,决定了金属本身得运动本事一一运动性:铸型阻力影响金属液得充填速率:铸型与金属得热交换条件影响金属液保持运动得时间:1、合金因素合金得运动性与化学因素之间存在着肯定得规律性:在运动性曲线上,对应着纯金属、共晶因素与金属间化合物得地方出现最大值,而有结晶温度领域得地方运动性降落,且在最大结晶温度领域四周出现最小值:合金因素对运动性得影响,紧张为因素差异时,合金得结晶特点差异造成得:低沉合金熔点得元素容易进步金属过热度,从而进步合金运动时间,进步运动性:合金净化后运动性进步,合金因素中凡能形成髙熔点般杂物得元素均会低沉合金得运动性:2、结晶潜热结晶潜热越髙,凝固举行得越痴钝,运动性越好:3、金属得比热容、密度与导热系数金属得比热容、密度较大得合金,运动性好:导热系数小得合金,热量散失慢,保持运动时间长;金属中到场合金元素后,一样寻常会低沉导热系数:4、液态金属得粘度合金液得粘度,在充型进程前期(属紊流)对运动性得影响较小,而在充型进程后期凝固中(属层流)对运动性影响较大:5、外表张力外表张力影响金属液与铸型得相互作用:外表张力对薄壁铸件、铸件得细薄局部与棱角得成形有影响,型腔越细薄、棱角得曲率半径越小,外表张力得影响越大:为降服由外表张力引起得附加压力,必须附加一个静压头:综上所述,为了进步液态金属得充型本事,在金属方面可采取以下步调:1、准确选择合金得因素选用结晶温度领域小得舍牵: ,也有利于进步充型本事:2、公正得熔炼工艺选择洁净得原质料:镌汰与有害气体得打仗:充实脱氧粘炼去气,镌汰气体、殽杂:髙温出炉,低温浇注:【二)铸型性子方面1、铸型得蓄热系数:铸型得蓄热系数越大,充型本事降落:2、铸型温度:预热铸型3、铸型中得气体:减小铸型中气体反压力【三)浇注条件方面1、浇注温度浇注温度越髙,充型本事强:但髙出某一温度界限,氧化吸气严肃,充型本事进步不显着:2、充型压头液态金属在运动方向上所受得压力称为充型压力:充型压力越大,充型能力越强:3、浇注体系得结构浇注体系得结构越巨大,就运动阻力越大,充型本事越差:〔四)铸件结构方面衡量铸件结构特点得因素为铸件得折算厚度与巨大水平:1、折算厚度:折算厚度也叫当星厚度或模数,为铸件体积与铸件外表积之比:折算厚度越大,热星散失越慢,充型本事就越好:铸件壁厚类似时,垂直壁比水平壁更容易充填:大平而铸件不易成形:对薄壁铸件应准确选择浇注位罝:2、巨大水平:铸件结构越巨大,厚薄局部过渡曲多.就型腔结构巨大,运动阻力就越大.铸型得充填就越阐难:1、逐层凝固(纯金属或共晶因素合金得凝固要领)恒温下结晶得金属,在凝固进程中其铸件断而上得凝固地域宽度即为零,断而上得固体与液体由一条界限淸晰地脱离,随着温度得降落,固体层不绝加厚,徐徐到达铸件中心,此为"逐层凝固要领” :逐层凝固要领特点:无凝固区或凝固区很窄 a )恒温下结晶得纯金属或共晶因素合金b)结晶温度领域很窄或断面温度梯度很大2、体积凝固(铸件断|M温度场较平展或结晶领域较宽得合金)假设合金得结晶温度领域很宽,或闲铸件断面温度场较平展,铸件凝固得某一段时间内,其凝固地域很宽,以致贯穿整个铸件断而,而外表温度髙于固相温度,这种情况为"体积凝固要领",或称为”糊状凝固要领":体积凝固要领(糊状凝固要领)特点:凝固动态曲线上得两相界限得纵向间距很小或为无条件重合:a、铸件断而温度平展b、结晶温度领域很宽一凝固动态曲线上得两相界限纵向间距很大3、中心凝固(结晶领域较窄或铸件断而温度梯度较大得合金)假设合金得结晶领域较窄,或因铸件断而得温度梯度较大,铸件断面上得凝固地域介于前两者之间时,属于"中心凝固要领" :中心凝固要领特点:a、结晶温度领域较窄b、铸件断面得温度梯度较大特点:凝固初期似逐层凝固——凝固动态曲线上得两相界限纵向距较小凝固后期似糊状凝固第二章凝固温度场〔重点)1.研究铸件温度场得要领:数学分析法、数值模拟法与实测法等:2.凝固:合金从液态转变成固态得进程,称为一次结晶或凝固:3.研究温度场自得义:埤轳铸件温度场随时间得厘革,可以大概预计铸件凝固中其断面上各个时间得凝固地域巨细及厘學:,凝固前沿向中心得推进速率.缩孔与缩松得位罝,凝固时间等告急标题,为准确方案浇注体系、设罝冒口、冷铁,以及采取其他工艺步调提供可靠依据,敷衍消除铸造缺陷,得到健全铸件,改良铸件结构与性能有告急意义:4.凝固要领及其影响因素一样寻常将金属得凝固要领分为三种典范:逐层凝固要领、体积凝固要领(或称糊状凝固要领)与中心凝固要领:在凝固进程中铸件断曲_上得凝固地域宽度为零,固体与液体由一条界限(凝固前沿)淸晰地脱离:随着温度得降落,固体层不绝加厚,徐徐到达铸件中心:这种情况为逐层凝固要领:铸件凝固得某一段时间内,其凝固地域险些贯穿整个铸件断面时,就在凝岡地域里既有己结晶得晶体,也有未凝固得液体,这种情况为体积凝固要领或称糊状凝固要领:铸件断而上得凝固地域宽度介于前两者之间时,称中心凝固要领:领域与冷却强度(温度梯度):结晶温度领域越宽,温度梯度越小,越倾向于体积凝固要领:5.金属凝固要领与铸件质量得干系逐层要领凝固,凝固前沿直接与液态金属打仗:当液态凝固成为固体而产生体积紧缩时,可以不绝地得到液体得增补,以为产陌生散性缩松得倾向性很小,而为在铸件末了凝固得部位留下会集缩孔:由于会集缩孔容易消除,一样寻常以为这类合金得补缩性良好:在板状或棒状铸件会出现中心线缩孔:这类铸件在凝固进程中,当紧缩受阻而产生晶间裂纹时,也容易得到金属液得添补,使裂纹愈合:当粗大得等轴枝晶相互毗连以后(固相约为70%),将使凝固得液态金属支解为一个个互不类似得溶池,末了在铸件中形身疏散性得缩孔,即缩松:敷衍这类铸件采取平常冒口消除其缩松为很难过,而通常须要采取别得资助步调,以增加铸件得致密性:由于粗大得等轴晶比较¥得连成骨架,在铸件中产生热裂得倾向性很大:这为由于,等轴晶越粗大,髙温强度就越低:别恰当晶间出现裂纹时,也得不到液态金属得充填使之愈合:假设这类合金在充填进程中产生凝固时,其充型性能也很差:6.铸件得凝固时间得盘算要领:分析法:分析要领为直策应用现有得数学理论与定律去推导与演绎数学方程(或模子),得到用函数情势表达得解,也就为分析解:数值要领:数值要领又叫数值阐发法,为用盘算机步调去求解数学模子得近似解,又称为数值模拟或盘算机模拟:紧张有差分法、有限元法:履历盘算法:平方根定律盘算法与折算厚度法(或模数法):第三章晶体形核与生长〔重点)1.液态金属结晶(液•固相变)驱动力:两相自由能得差值AG为结晶得驱动力:T I ATAG V =L(1-~)=—,敷衍给定金属,L与To均为定值,ZkGv仅与AT有关: 因此,液态金属结晶得驱动力为由过冷度提供得:过冷度越大,结品得驱动力也就越大,过冷度为零时,驱动力就不复存在:以为液态金属在没有过冷度得情况下不会结晶:2.液态金属结晶进程:起首,体系通过升沉作用在某些微观小地域内降服能量停滞而形成稳固得新相品核:新相一旦形成,体系内将出现自由能较髙得新旧两相之间得过渡区:力使体系ft由能尽大概地低沉,过渡区必须减薄到最小原子尺度,如许就形成了新旧两相得界而:然后,依靠界Iftl徐徐向液相内推移而使晶核长大:直到全部得液态金属都全部转变成金属晶体,整个结晶进程也就在出现最少量得中心过渡结构中完成:由此可见,为了降服能量停滞以防范系统自由能太过増大,液态金属得结晶进程为通过形核与生长得要领举行得:3.形核:亚稳固得液态金属通过升沉作用在某些微观小地域内形成稳固存在得晶态小质点得进程称为形核:形核条件:起首,体系必须处于亚稳态以提供相变驱动力:其次,须要通过起伏作用降服能障才华形成稳固存在得晶核并确保其进一步生长:由于新相与界而相伴而生,因此界面向由能这一热力学能障就成为形核进程中得紧张阻力:根据组成能障得界面情况得差异,大概出现两种差异得形核要领:均质生核与非均质生核:均质生核:在没有任何外去界而得匀称熔体中得生核进程:非均质生核:在不匀称熔体中依靠外去杂质或型壁界而提供得衬底举行生核得进程:4.均质生核机制必须具备以下条件:1)过冷液体中存在相升沉,以提供固相晶核得晶胚:2)生核导致体积自由能低沉,界側自由能进步:为此,晶胚须要体积达到肯定尺寸才华稳固存在:3)过冷液体中存在能量升沉与温度升沉,以提供临界生核功:4)为维持生核功,须要肯定得过冷度:5.临界晶核半径而言,非均质形核临界半径r/与均质形核临界半径r ‘得表达式完全类似:非均质生核得临界形核功AGh与均质生核得临界形核功△供之间也仪相差一个因子f( 0):0°< 0< 180° X) < f( 0) < 1,故V s <V 球,△‘< AG 均*.因而衬底都具有促进形核得作用,非均质生核比均质生核更容易举行;6.生核剂:一种好得生核剂起首应能包管结晶相在衬底物质上形成尽大概小得润湿角0,其次生核剂仍应该在液态金属中尽大概地保持稳固,并且具有最大得外表积与准确得外表特性:7.晶体得生长紧张受以下几个相相互关得进程所制约:①界面生长动力学进程:② 传热进程:③传质进程:8.固一液界而得微观结构从微观尺度思量,固一液界面可分别为粗糙界而与平整界面,或非小平面界面及小平面界面:粗糙界而(非小平而界面):界面固相一侧得几个原子层点阵位罝只有50%左右为固相原子所占据:这几个原子层得粗糙区实际上就为液固之间得过渡区:平整界而(小平而界衡):界而固相一侧得点阵险些全部被固相原子占据,只留下少数空位:或在充满固相原子得界而上存在少数不稳固得、孤独得固相原子,从而从团体上看为平整平滑得:敷衍差异得a值,对应差异得界面微观结构,称为Jackson判据:当a沒时,界而得平衡结构应有50%左右得点阵位罝为固相原子所占据. 因此粗糙界而为稳固得:当a >2时,界而得平衡结构或为只有少数点阵位罝被占据,或为绝大局部位罝被占据后而仪留下少量空位:因此,这时平整界而为稳固得:a越大,界曲_ 越平整:绝大多数金属得熔化熵均小于2,在其结晶进程中,固一液界曲为粗糙界而:多数非金属与化合物得a值大于2.这类物质结晶时,其固一液界面为由基本完备得晶断所组第8页,共18页成得平整界而:铋、铟、锗、硅等亚金属得情况就介于两者之间,这类物质结晶时,其固一液界而通常具有殽杂结构:9.界面得生长机理与生长速率1、连续生长机制一粗糙界面得生长:较髙得生长速率:2、二维生核生长机制一完备平整界而得生长:生长速率也比连续生长低:3、从缺陷处生长机制一非完备界面得生长:(1)螺旋位错生长:(2)旋转孪晶生长:反射孪晶生长:生长速率比二维形核生长快,仍比连续生长慢:第四章单相合金凝固1.溶质再分配与平衡分配系数单相合金得结晶进程一样寻常为在一个固液两相共存得温度区间内完成得 ;在区间内得任一点,共存两相都具有差异得因素:因此结品进程肯定要导致界而• • • • * • ■■■■ • ••會■ • • • ■ • ■■■—• • ■ ■■ 一•M •_•_■ • •屬故晶体生长与传质进程肯定相伴而生:如许,从生核开始直到凝固竣事,在整个结晶进程中,固、液两相内部将不绝举行着溶质元素重新漫衍得进程:称此为合金结晶进程中溶质再分配:衡固相中溶质浓度与平衡液相溶质浓度得比值称为平衡分配系数:2.平衡结品中得溶质再分配规律:Cfjk。
- 1、下载文档前请自行甄别文档内容的完整性,平台不提供额外的编辑、内容补充、找答案等附加服务。
- 2、"仅部分预览"的文档,不可在线预览部分如存在完整性等问题,可反馈申请退款(可完整预览的文档不适用该条件!)。
- 3、如文档侵犯您的权益,请联系客服反馈,我们会尽快为您处理(人工客服工作时间:9:00-18:30)。
夹杂物
cos
CC
2
2
双边角
IC
第八章 铸件中的非金属夹杂物
§8-3 夹杂物的长大、分布和形状
三、夹杂物的形状
cos
2
CC IC
2
只有当2IC CC时,才能处于 平衡状态。双边角(两晶体间的 夹角)决定夹杂物的形状。从 晶体 0°~180°变化,夹杂物形状由 尖角状逐渐变化为球形(图)。 如果2IC < CC ,平衡状态遭 双边角 到破坏,夹杂物以薄膜分布在晶界上。
第八章 铸件中的非金属夹杂物
§8-3 夹杂物的长大、分布和形状
一、夹杂物的聚合长大
刚从液相中析出的夹杂物尺寸非常小,仅有几微米。长大 的速度非常快。 金属液的对流以及夹杂物与液体的密度差而产生的上浮或 下沉,使悬浮在液体中的夹杂物杂乱无章地运动,夹杂物 相互碰撞,聚合长大。 液态夹杂物的粘度较低,彼此碰撞,则容易聚合成一个完 整的球状夹杂物(图) 。 当金属液温度较低时,夹杂物的粘度增大,碰撞后可粘连 在一起,或单个靠在一块,即使聚合在一起也呈粗糙的多 链球状(图)。 非同类夹杂物相碰撞,经烧结,组成成分更为复杂的夹杂 物。
本章复习题
1 2 3
2 A l 3 O A l2 O 3 2 A l 4 O F e ( l ) F eO A l 2 O 3
BACK
第八章 铸件中的非金属夹杂物 §8-2 非金属夹杂物的生成
二、浇注时形成的非金属夹杂物
1 形成过程 在浇注及充型过程中生成的非金属夹杂物主要是氧化物, 故又称为二次氧化夹杂物。(金属液与大气接触) 在浇注过程中,金属液的断流、在充型过程中产生的涡 流、飞溅等都会把氧化膜卷入金属液内产生氧化夹杂。 脱氧后,刚出炉的金属液与铸件的含氧量对比发现,铸 件的含氧量明显增加。因此,浇注过程中的二次氧化是 铸件产生非金属夹杂物的主要途径。 2 影响二次氧化夹杂物形成的因素 合金成分 金属液流 BACK
前三类非金属夹杂物统称为氧化夹杂物。
BHale Waihona Puke CK第八章 铸件中的非金属夹杂物 §8-1 概述
二、非金属夹杂物的来源
1)脱氧、脱硫产物,特别是一些密度大的脱氧产物未及时排除; 2)随着金属液温度的降低,硫、氧、氮等元素的溶解度相应下 降,达到过饱和,过饱和析出的组元常以低熔点共晶或化合 物的形式残留在金属中。 3)金属与外界物质相互作用生成的非金属夹杂物,如金属料表 面的粘砂、锈蚀、焦炭中的灰分熔化后成为熔渣,炉衬和浇 包受金属液侵蚀生成的非金属夹杂物; 4)金属液被大气氧化生成的氧化物。 前两类非金属夹杂物称为内生夹杂物,后两类夹杂物称为 外来夹杂物。 BACK
晶体
夹杂物
第八章 铸件中的非金属夹杂物
§8-3 夹杂物的长大、分布和形状
不同双边角间夹杂物形状示意图
第八章 铸件中的非金属夹杂物
§8-4 减少和排除夹杂物的途径
(1)正确地选择合金成分,严格控制易氧化元素的含量。 (2)加熔剂 金属液表面覆盖一层熔剂,能吸收上浮的夹杂 物(如铝合金熔炼时加氯盐、氟盐),或向金属液中加入 熔剂,使之与夹杂物形成密度更小的液态夹杂物,如向 球铁液中加入冰晶石,可降低夹杂物熔点,便于聚合和 上浮。 (3)采用复合脱氧剂 采用单一脱氧剂,由于脱氧产物熔点 高,易成为夹杂物残存在铸件中。如采用复合脱氧剂, 当配比适当时,可以生成密度小、熔点低的液态脱氧产 物,易聚合成大液滴,利于上浮、排除。
第八章 铸件中的非金属夹杂物 §8-1 概述
a)钢中FeO产生的缩孔
b)可锻铸铁中MnS产生的缩气孔
第八章 铸件中的非金属夹杂物 §8-1 概述
3 在某些情况下,铸件中的非金属夹杂物对铸件质量 有良好作用。例如,钢中的氧化物、碳化物和铸铁 中的磷共晶能提高材料的硬度、增加耐磨性。钢中 微量的钙和硫形成球形硫化物,分布在晶内,对机 械性能影响不大,却能改善钢的切削性能。有些难 熔的非金属夹杂物可成为非自发结晶的核心,细化 铸件的宏观组织。
第八章 铸件中的非金属夹杂物
§8-3 夹杂物的长大、分布和形状
铁基合金中的SiO2形态 a 多链球状 b 单球
第八章 铸件中的非金属夹杂物
§8-3 夹杂物的长大、分布和形状
二、夹杂物的分布 1)能作为金属非自发结晶核心的非金属夹杂物分布
在晶内。 2)能上浮到铸件表面的夹杂物、不溶解于金属液中 的液态夹杂物(如各种硅酸盐),及固态夹杂物在 金属液中运动、碰撞、聚合,尺寸不断加大。若 夹杂物的密度小于金属液的密度,上浮速度逐渐 加快。它们可能集中到冒口中被排除,或保留在 铸件上部、上表面层和铸件的拐角处。 3)处在金属疑固区内的高熔点固态微小夹杂物,可 能被枝晶粘附,分布于晶内;否则分布于晶界。
第八章 铸件中的非金属夹杂物 §8-2 非金属夹杂物的生成
三、凝固时形成的非金属夹杂物
事实上,偏析液的成分是复杂的,且各枝晶间液相的成分也不同。 因此,生成的夹杂物也不相同,既可能生成MnS、MnO、SiO2、 Al2O3等固态夹杂物,也可能生成硅酸盐等液态夹杂物。
枝晶间残留的偏析液,通常是易熔成分,最后将进行二 元和三元共晶反应,生成物以网状存在于晶界上。例如, 钢中的硫,在凝固末期发生共晶反应,生成Fe+FeS共晶。 如果钢液脱氧不良,FeO含量较多,将形成熔点更低 (940℃)的三元共晶(Fe+FeS+FeO)。这种共晶体对钢的 危害更大,是铸件产生热裂的主要原因。 为了消除S的有害作用,可加入Mn。Mn与S的亲合力比较 大,优先生成MnS。研究表明,当[%Mn] /[%S]>7时, 95%的硫化物以MnS形式存在。
第八章 铸件中的非金属夹杂物
§8-4 减少和排除夹杂物的途径
(4)采用真空或在保护气氛下熔炼和浇注。 (5)应避免金属液在浇注和充型时发生飞溅和涡流,尽可 能保证充型平稳。 (6)过滤法 金属液通过过滤器,再注入型腔,也可达到去 除夹杂物的目的。过滤器分活性和非活性两种,前者仅 为机械作用,如用石墨、陶瓷制成的过滤器;后者还具 有吸附作用,排渣效果更好,如用NaF、CaF、Na3AlF6 等制成的过滤器。 (7)为减少铸型的氧化气氛,除严格控制铸型水分外,还 可在型砂中添加附加物,如生产铸铁件时,型砂中可以 加入煤粉以形成还原性气氛,也可以在铸型表面撒上一 层熔剂。
第八章 铸件中的非金属夹杂物 §8-2 非金属夹杂物的生成
三、凝固时形成的非金属夹杂物
合金液在凝固过程中,由于溶质再分配的结果,液相中 的溶质浓度不断增高,出现偏析液相。当枝晶间的偏析 液达到过饱和时,则析出非金属夹杂物,又称偏析夹杂 物。 以Fe-C合金为例,讨论偏析夹杂物的形成过程。假定 该合金只存在Mn、S两种杂质。在合金凝固过程中,由 于溶质再分配,枝晶间的液相中富集Mn、C、S等溶质。 当Mn和S达到过饱和浓度时,发生如下反应 [Mn]+[S] MnS 随着温度的不断下降,枝晶间液相中的Mn和S进一步富 集,且在合金液中的溶解度随之降低,促使MnS不断长 大或生成新的MnS。
第八章 铸件中的非金属夹杂物
§8-3 夹杂物的长大、分布和形状
三、夹杂物的形状
尺寸较大的低熔点夹杂物能上浮到铸件表面。 在合金凝固即将结束时,汇集 于晶界的低熔点偏析夹杂物, 晶体 其形状在很大程度上受界面张 力的影响。设夹杂物—晶体的 界面张力为IC,金属晶体间 的界面张力为CC ,平衡条件 晶体 为
第八章 铸件中的非金属夹杂物 §8-1 概述
一、非金属夹杂物的分类 二、非金属夹杂物的来源 三、非金属夹杂物对铸件质量的影响
第八章 铸件中的非金属夹杂物 §8-1 概述
一、非金属夹杂物的分类
1)简单氧化物 如FeO、CuO、Al2O3、MnO、SiO2等; 2)复杂氧化物 通常用AO•B2O3表示,如MnO•Al2O3 、 MnO•Fe2O3、FeO•Al2O3等。 这类夹杂物又称尖晶石; 3)硅酸盐 通用化学式为lFeO•mMnO•n Al2O3•pSiO2 ,其 中l、m、 n 、p为系数; 4)硫化物 如FeS、MnS和稀土硫化物; 5)氮化物 如VN、TiN、AlN等。
第八章 铸件中的非金属夹杂物 §8-1 概述
三、非金属夹杂物对铸件质量的影响 1 对力学性能的影响:使冲击韧性下降,疲劳极限
降低。夹杂物越粗大,材料的疲劳极限越低。据 统计,汽车零件的断裂90%是由疲劳裂纹造成的, 其裂纹源为非金属夹杂物。尖角形的夹杂物引起 应力集中,促使微裂纹的产生,加速零件破坏。 2 对铸造性能的影响:金属液中含有固体夹杂物时, 其流动性显著降低。分布在晶界上的低熔点夹杂 物是铸件产生热裂纹的主要原因之一。低熔点夹 杂物(如钢中的FeO)促进铸件产生微观缩孔和缩 气孔(图)。
第八章 铸件中的非金属夹杂物 §8-2 非金属夹杂物的生成
一、浇注前形成的非金属夹杂物 二、浇注时形成的非金属夹杂物 三、凝固时形成的非金属夹杂物
第八章 铸件中的非金属夹杂物 §8-2 非金属夹杂物的生成
一、浇注前形成的非金属夹杂物
金属在熔炼和炉前处理时,产生的非金属夹杂物可能是脱 氧、脱硫产物,也可能是金属液与炉衬相互作用的产物。 浇注前许多尺寸较大的夹杂物上浮到金属液表面,经多次 扒渣,大部分被清除。但仍有数量可观、尺寸较小的非金 属夹杂物残留在金属液内,随液流一起注入型腔,铸件凝 固后,残留在铸件的内部,成为非金属夹杂物。 常见的脱氧元素形成的非金属夹杂物 硅铁对钢液脱氧时: Si 2 O SiO 2 同一种脱氧剂能生成不同的产物: