SC1205中文资料
IRFR1205中文资料

IRFR/U1205HEXFET ®Power MOSFETDescription5/11/98ParameterMax.UnitsI D @ T C = 25°C Continuous Drain Current, V GS @ 10V 44 I D @ T C = 100°C Continuous Drain Current, V GS @ 10V 31 A I DMPulsed Drain Current 160P D @T C = 25°C Power Dissipation 107W Linear Derating Factor 0.71W/°C V GS Gate-to-Source Voltage± 20V E AS Single Pulse Avalanche Energy 210mJ I AR Avalanche Current25A E AR Repetitive Avalanche Energy 11mJ dv/dt Peak Diode Recovery dv/dt 5.0V/ns T J Operating Junction and-55 to + 175T STGStorage Temperature RangeSoldering Temperature, for 10 seconds300 (1.6mm from case )°CAbsolute Maximum RatingsParameterTyp.Max.UnitsR θJC Junction-to-Case––– 1.4R θJA Junction-to-Ambient (PCB mount) **–––50°C/WR θJAJunction-to-Ambient–––110Thermal ResistanceD -P AK T O -252AA I-PA K TO -251AAl Ultra Low On-Resistance l Surface Mount (IRFR1205)l Straight Lead (IRFU1205)l Fast SwitchinglFully Avalanche RatedFifth Generation HEXFETs from International Rectifier utilize advanced processing techniques to achieve the lowest possible on-resistance per silicon area. This benefit, combined with the fast switching speed and ruggedized device design that HEXFET Power MOSFETs are well known for, provides the designer with an extremely efficient device for use in a wide variety of applications.The D-PAK is designed for surface mounting using vapor phase, infrared, or wave soldering techniques.The straight lead version (IRFU series) is for through-hole mounting applications. Power dissipation levels up to 1.5 watts are possible in typical surface mount applications.PD - 91318BIRFR/U1205IRFR/U1205IRFR/U1205IRFR/U1205IRFR/U1205IRFR/U1205IRFR/U1205IRFR/U1205IRFR/U1205。
汶川地震抗震救灾志地震灾害志

附件三《汶川地震抗震救灾志·地震灾害志》“第九篇商业和服务业破坏,第四章建筑业与房地产业破坏”收集资料要求“第九篇商业和服务业破坏,第四章建筑业与房地产业破坏”收集资料包括文字、图片及说明等内容。
具体要求如下。
一、工作区及其深入程度汶川地震产生房屋破坏的地区,为本篇开展资料收集的工作区。
1.省份本篇收集资料的省份为:四川省、甘肃省、陕西省、重庆市、宁夏自治区和云南省。
2.市(州)在上述省份范围内,本篇收集资料的工作区仅限于汶川地震产生房屋破坏的市(州)(含副省级市)管辖范围,如表3-表8。
3.县、区在上述市(州)范围内,本篇收集资料的工作区仅限于汶川地震产生房屋破坏的县和县级市管辖范围,如表2-表8。
省、市(州)、县区均要统计,逐级汇总,下级统计资料作为上一级统计资料的基础。
统计资料一式两份,一份电子文件,一分为纸质文档,纸质文档需行政主管部门盖章,以便存档。
二、资料的内容收集资料须统计企业各种损失。
统计资料起至时间为:2008年5月12日-2008年10月8日。
1.企业经济损失2.企业建筑物损失房屋结构破坏分为三级:1) 倒塌和严重破损(不可修复)2) 中等破损3) 轻微破损和基本完好。
由于各地情况不同,震后统计数据中对房屋破坏的分类不尽相同。
如有与上述方法不同的分类方式,请按上述方式进行重新归类和统计,并附原始统计材料。
要强调的是:在统计数据中,必须包括基本完好等级。
即一个地区的统计数据包含破坏的和未破坏的所有房屋数据。
3.企业设备等损失4.企业人员伤亡情况5.其它损失三、需要统计的建筑业企业及篇章节编号建筑业(04090401)【】勘察企业(0409040101)【】设计企业(0409040102)【】监理企业(0409040103)【】施工企业(0409040104)【】其他建筑业(0409040105)房地产业(04090402)【】房地产开发企业(0409040201)【】物业管理企业(0409040202)【】房地产中介服务企业(0409040203)【】其他房地产企业(0409040204)四、地名编号1. 地名编号表1-表6中的省、地(市)、县编号是本篇的统一编号。
SC500操作手册说明书

11/2014 Revised 07/2017(C)9099974000DeutschFrançaisEnglishNederlands9087400020, 9087401020, 9087402020See previous manual for the models no.:9087350020, 9087351020, 9087355020INSTRUCTIONS FOR USE ENGLISH9099974000 - SC500111/2014revised 07/2017TABLE OF CONTENTSINTRODUCTION (2)MANUAL PURPOSE AND CONTENTS ..........................................................................................................................................2TARGET ...........................................................................................................................................................................................2HOW TO KEEP THIS MANUAL .......................................................................................................................................................2DECLARATION OF CONFORMITY ................................................................................................................................................2IDENTIFICATION DATA ...................................................................................................................................................................2OTHER REFERENCE MANUALS ...................................................................................................................................................2SPARE PARTS AND MAINTENANCE .............................................................................................................................................2CHANGES AND IMPROVEMENTS ................................................................................................................................................2OPERATION CAPABILITIES ...........................................................................................................................................................3CONVENTIONS (3)UNPACKING/DELIVERY .................................................................................................................................................3SAFETY (3)VISIBLE SYMBOLS ON THE MACHINE .........................................................................................................................................3SYMBOLS THAT APPEAR ON THIS MANUAL ...............................................................................................................................4GENERAL INSTRUCTIONS (4)MACHINE DESCRIPTION (6)MACHINE STRUCTURE .................................................................................................................................................................6CONTROL PANEL ...........................................................................................................................................................................8ACCESSORIES/OPTIONS .. (9)TECHNICAL DATA (9)WIRING DIAGRAM (10)USE/OPERATION (11)MAGNETIC SMART KEY ...............................................................................................................................................................11BATTERY CHECK/SETTING ON A NEW MACHINE .....................................................................................................................11BATTERY INSTALLATION ..............................................................................................................................................................11BEFORE MACHINE START-UP ....................................................................................................................................................12MACHINE START AND STOP .......................................................................................................................................................14MACHINE OPERATION (SCRUBBING/DRYING) .........................................................................................................................15TANK EMPTYING ..........................................................................................................................................................................17AFTER USING THE MACHINE .....................................................................................................................................................17MACHINE LONG INACTIVITY (17)MAINTENANCE (18)SCHEDULED MAINTENANCE TABLE .........................................................................................................................................18BATTERY CHARGING ..................................................................................................................................................................19SUPERVISOR KEY (yellow) ..........................................................................................................................................................20SQUEEGEE CLEANING ...............................................................................................................................................................22SQUEEGEE BLADE CHECK AND REPLACEMENT ....................................................................................................................22CLEANING THE BRUSH ...............................................................................................................................................................23RECOVERY TANK CLEANING .....................................................................................................................................................23SOLUTION FILTER CLEANING ....................................................................................................................................................24MACHINE TRACKING ADJUSTMENT ..........................................................................................................................................24DETERGENT TANK CLEANING ...................................................................................................................................................25DRAINING THE ECOFLEX SYSTEM............................................................................................................................................26FUSE CHECK/REPLACEMENT . (26)TROUBLESHOOTING ...................................................................................................................................................27SCRAPPING (28)ENGLISH INSTRUCTIONS FOR USE 2SC500 - 909997400011/2014revised 07/2017INSTRUCTIONS FOR USE ENGLISH9099974000 - SC500311/2014revised 07/2017ENGLISH INSTRUCTIONS FOR USE 4SC500 - 909997400011/2014revised 07/2017INSTRUCTIONS FOR USE ENGLISH9099974000 - SC500511/2014revised 07/2017ENGLISH INSTRUCTIONS FOR USE 6SC500 - 909997400011/2014revised 07/2017INSTRUCTIONS FOR USE ENGLISHrevised 07/2017ENGLISH INSTRUCTIONS FOR USE 8SC500 - 909997400011/2014revised 07/2017LMK50INSTRUCTIONS FOR USE ENGLISH9099974000 - SC500911/2014revised 07/2017ACCESSORIES/OPTIONSIn addition to the standard components, the machine can be equipped with the following accessories/options, according to the machine specific use:–GEL batteries–Electronic battery charger –Brushes of different materials–Pads of different materials–Splash guard–Natural rubber squeegee blades –EcoFlex–USB portFor further information concerning the optional accessories, contact an authorised Retailer.TECHNICAL DATAModelNilfisk SC500 53 BNilfisk SC500 53R BSolution tank capacity 45 litres Recovery tank capacity 45 litresMachine length1,277 mm1,302 mm Machine width with squeegee 720 mmMachine width without squeegee 532 mm538 mmMachine height 1,063 mm Cleaning width 530 mm Driving wheel diameter200 mm Driving wheel specific pressure on the floor 0.7 N/mm 2Rear wheel diameter80 mm Rear wheel specific pressure on the floor 2.1 N/mm 2Brush/pad diameter530/508 mmBrush pressure with extra pressure function turned off 15 kg 22 kg Brush pressure with extra pressure function turned on 30 kg 30 kgSolution flow values0.75 cl/m / 1.5 cl/m 3.0 cl/m / 2.8 l/min0.38 cl/m / 0.75 cl/m 1.5 cl/m / 2.8 l/minEcoFlex system detergent percentage0.25 % ÷ 3 %Sound pressure level at workstation (ISO 11201, ISO 4871, EN 60335-2-72) (LpA)63 ± 3 dB(A)65 ± 3 dB(A)Sound pressure level at workstation in silent mode (LpA)60 ± 3 dB(A)61 ± 3 dB(A)Machine sound power level (ISO 3744, ISO 4871, EN 60335-2-72) (LwA)81 dB(A)83 dB(A)Vibration level at the operator’s arms (ISO 5349-1, EN 60335-2-72)< 2.5 m/s 2Maximum gradient when working 2 %Drive system motor power 200 W Drive speed (variable)0 - 5 km/h Vacuum system motor power 280 W Vacuum system circuit capacity 760 mm H 2OBrush motor power 450 W 670 W Brush rotation speed 155 rpm-Total absorbed power (*)500 W IP protection class X4Protection class (electric)III (I for the battery charger)Battery compartment size 350x350x260 mmSystem voltage 24 V Standard batteries (2)12 V 105 AhC5Battery charger 24 V 13 A Work autonomy (*)3.5 hourWeight without batteries and with empty tanks 83 kg85 kg (full package)88 kg Gross vehicle weight (GVW)207 kg210 kg Shipping weight114 kg192 kg (full package)119 kg(*) Values reflect standard operating conditions (EN 60335-2-72)icon (50), wait until the brush is lowered onto the floor.0,75 cl/m OFF 1,5 cl/m3,0 cl/m2,8 l/min0,38 cl/m0,75 cl/m1,5 cl/mOFFFigure 7Press the EcoFlex push-button (46) when stronger washing power is needed temporarily.With the EcoFlex system activated (LED flashing), increased solution flow, activation of the extra pressure of the brush and an increase in the solution detergent concentration (level 2 if the level was set to 1 - level 1 if the level was set to 0) is obtained. Press the EcoFlex push-button (46) again, to restore the original settings (LED on).If the push-button (46) is not pressed again, the original settings are restored automatically after 60 seconds.All of the above solution flow and detergent concentration values are factory settings.To change these settings, see the Supervisor key paragraph in Maintenance chapter.Press and hold the One-Touch push-button (43) for more than 1 second. The extra pressure function activation is shown by LED which turns from green to red, and by the iconTo return to normal pressure, press and hold the One-Touch push-button (43) for more than 1 second.appears on the display (50), contact an authorised Nilfisk Service Centre for scheduled maintenance.FFigure 8Figure 9 Figure 10 Figure 11DETERGENT TANK CLEANING(For machines with EcoFlex system)Clean the detergent tank (25) as follows.1. Drive the machine to the appointed disposal area.2. Ensure that the machine is off and the user key (51) has been removed.3. Lift the cover (34) and check that the recovery tank (33) is empty; if not, empty it using the drain hose (12).4. Close the cover (19).5. Grasp the handle (16) and carefully lift the tank (33).6. Unscrew the cap (A, Fig. 15) from the detergent tank (B).7. Remove the tank.8. Rinse and wash out the tank with clean water in the appointed disposal area.9. Replace the detergent tank (B) as shown in the figure, then refit the plug (A).10. When the detergent tank has been drained, it may be necessary to drain the EcoFlex system too (see procedure in followingsection).ABFigure 15P100853SCRAPPINGHave the machine scrapped by a qualified scrapper.Before scrapping the machine, remove and separate the following materials, which must be disposed of properly according to the Law in force:–Batteries–Brushes–Plastic hoses and components–Electrical and electronic components (*)(*) Refer to the nearest Nilfisk Center especially when scrapping electrical and electronic components.Machine material composition and recyclabilitySC500 weight percentageType RecyclablepercentageAluminium100 %7 %Electric motors - various29 %29 %Ferrous materials100 % 2 %Wiring harness80 % 2 %Liquids100 %0 %Plastic - non-recyclable material0 % 2 %Plastic - recyclable material100 %7 %Polyethylene92 %48 %Rubber20 % 2 %。
笔记本常用芯片大全

ADP3168笔记本电脑供电控制芯片)
ADP3170主板CPU供电控制芯片
ADP3180主板CPU供电控制芯片
ADP3181笔记本电脑CPU供电芯片
ADP3203笔记本电脑CPU供电芯片
ADP3421笔记本电脑CPU供电芯片
ADP3806笔记本电脑电池充/放电控制芯片
笔记本IO芯片大全PC87591E (-VPCI01),(VPCQ01)/PC 97551-VPC/PC 87570-ICC/VPC
笔记本IO芯片大全PC87391VGJ/TB6807F/W83L950D/LPC47N249-AQQ/PCI4510/PC8394T
笔记本IO芯片大全PC87392/PC87541L/PC87541V/LPC47N253-AQQ/PC87591E-VLB
笔记本电源管理芯片ADP3421/ADP3410/ADP3205/ADP3180/ADP3806/ADP3203/ADP3020
笔记本电源管理芯片ADP3170/ADP3188/ADP3181/ADP3166/ADP3163/ADP3165/ADP3168
笔记本电源管理芯片ADP3169/ADP3415/ADP3416/ADP3417/ADP3418/ADP3155/ADP3422
电源管理芯片大全RT9227A/RT9228/RT9238/RT9248A/RT9173/RT9202/RC5051M
电源管理芯片大全5090MTC/RC5093MTC/5098MTC/SC1470/SC1205/SC1214TS
电源管理芯片大全SC1155CSW/SC1154CSW/SC1153CSW/SC1189SW//SC1185ACSW
CRS1215中文资料

CRD dual output DC/DC converters offer excellent regulation and isolation in an industry standard DIP package. Available in 5 or 12 Volt input versions, the CRD is perfect for industrial and EDP applications.The CRD features short circuit protection and 500VDC isolation. Please see the CRS series for single output applications.CRD SERIES - DUAL OUTPUT, 0.5 WATT•5V and 12V Inputs •Input Pi Filter•Regulated Outputs •500V IsolationFEATURESDESCRIPTION•Industry Standard Package•Industry Standard Pinout•85°C Case Operation •Note: For model options, see the last page of this file .OPTIONSWhen ordering equipment options, use the following suffix information. Select the option(s) that you prefer and add them to the model number. Example ordering options are located below the options table.OPTION SUFFIX APPLICABLE SERIES REMARKSNegative Logic N HAS, HBD, HBS, HES, LES, QBS,QES, TES, TQD TTL “Low” Turns Module ON TTL “High” Turns Module OFFLucent Compatible Trim T HAS, HBD, HBS, HES, QBS, QES Terminal Strip TS XWS, XWD, XWTTrim1IAS, LESEnable2IAD, IAS, LES, SMSTrim and Enable3IAS, LESCurrent Share4SMSHeaderless Y Encapsulated EWS, IWS, OWSPIN LENGTH AND HEATSINK OPTIONS Standard Pin Length is 0.180”(4.6mm)0.110” (2.8mm) Pin Length8All Units (Except SMS)0.150” (3.8mm) Pin Length9All Units (Except SMS)0.24” (6.1mm) Horizontal Heatsink1H All Units (Except DIP, SIP, and SMPackages)Includes Thermal Pad0.24” (6.1mm) Vertical Heatsink1V All Units (Except DIP, SIP, and SMPackages)Includes Thermal Pad0.45” (11.4mm) Horizontal Heatsink 2H All Units (Except DIP, SIP, and SMPackages)Includes Thermal Pad0.45” (11.4mm) Vertical Heatsink2V All Units (Except DIP, SIP, and SMPackages)Includes Thermal Pad0.95” (24.1mm) Horizontal Heatsink 3H All Units (Except DIP, SIP, and SMPackages)Includes Thermal Pad0.95” (24.1mm) Vertical Heatsink3V All Units (Except DIP, SIP, and SMPackages)Includes Thermal PadExample Options:HBS050ZG-ANT3V = HBS050ZG-A with negative logic, Lucent compatible trim, and0.95” vertical heatsink.LES015YJ-3N = LES015YJ with optional trim and enable, negative logic.QBS066ZG-AT8 = QBS066ZG-A with Lucent compatible trim and 0.110” pin length.NUCLEAR AND MEDICAL APPLICATIONS Power-One products are not authorized for use as critical components in life support systems, equipment used in hazardous environments, or nuclear control systems without the express written consent of the President of Power-One, Inc. TECHNICAL REVISIONS The appearance of products, including safety agency certifications pictured on labels, may change depending on the date manufactured. Specifications are subject to change without notice.。
SCB变压器与SC变压器的区别

SCB变压器与SC变压器的区别一、线圈绕制方面:SCB型产品低压线圈采用箔绕:(1)绕组结构:采用铜箔单层缠绕,层间材料用含有潜伏性固化剂的环氧树脂及F级复合箔。
(2)绕组材料:采用导电率极佳的无氧铜,含铜量99.99%。
SC型产品低压线圈采用线绕:(1)绕组结构:圆筒式线圈(2)多根普通玻璃丝包扁铜线。
二、抗突发短路事故方面:(1)SCB型产品低压采用铜箔式结构,电抗高度即为绕组高度,与高压线圈等同,从而在变压器产生突发短路条件下,产生较小的轴向短路力。
另外,由于整个绕组采用一张宽而薄的箔材,抗轴向拉断能力较强。
(2)SC型产品由于采用多根并绕,端部螺旋角极大,产生很强的端部漏磁场,在变压器遭受突发短路状态下,产生极大的短路力,如果结构方面没有充分加强,则很容易造成轴向损坏。
三、在变压器低压温升方面由于低压绕组靠近铁芯散热较困难,SCB型产品采用箔式低压绕组结构,可以方便的设置散热面,加大通风量,从而保证线圈产生的热量及时散发。
而SC型产品采用线绕式低压绕组,达到上述目的较为困难。
变压器的低压温升,箔绕结构要比线绕结构平均下降5—7K。
可提高变压器的过负载能力和使用寿命。
四、在变压器的负载损耗方面由于SCB型产品低压箔式结构采用无氧铜箔,同电压等级,同规格的变压器,SCB型产品比SC型产品,由于集肤效应造成的,附加损耗平均降低5%。
(5)绝缘性能方面SCB型产品低压箔式结构采用低压箔式结构,低压绕组内各层间的电压梯度很低,SCB型产品与SC型产品相比具有更高的绝缘强度。
由于其匝间电容较大,从而提高产品抗过电压及雷电冲击强度。
SCB9-3150/35±2x2.5%/0.4kV,Uk%=8 Y,d11请问这个变压器参数具体都是什么意思?这是环氧树脂干式变压器:其意义如下:S-三相;C-环氧树脂浇注型B-为铜箔线圈9-设计序号9型代表损耗标准(这是目前比较差的)3150kVA-是变压器的额定容量35kV-是变压器的输入额定电压(高压)+-2*2.5%-是高压的分接调压范围:高压有36750、35875、35000、34125、33250V五档电压可以调节。
贴片三极管丝印型号对照手册

npn dtr R1 22k 50V 100mA
fT12GHz npn 4V 5mA
06
Gali-6
06
DTC144TE
06
DTC144TUA
06
DTC144TKA
-06
PMSS3906
t06
PMBS3906
020
SSTPAD20
050
SSTPAD50
Roh
N
SC70
04
DTC114TKA
Roh
N
SC59
04
MRF5211L
04
Gali-4
-04
PMSS3904
t04
PMBS3904
05
Gali-4
05
DTC124TE
Mot
X SOT143
MC
AZ SOT89
Phi
N SOT323
Phi
N
SOT23
MC
AZ SOT89
Roh
N
EMT3
05
DTC124TUA
npn dtr R1 10k 50V 100mA
npn dtr R1 10k 50V 100mA
npn dtr R1 10k 50V 100mA
pnp RF MRF521 DC-4GHz MMIC amp 17.5 dBm
2N3904 2N3904 DC-4GHz MMIC amp 18 dBm o/p npn dtr R1 22k 50V 100mA
AZ SOT89
N
EMT3
N
SC70
N
SC59
N SOT323
ADS1205中文资料
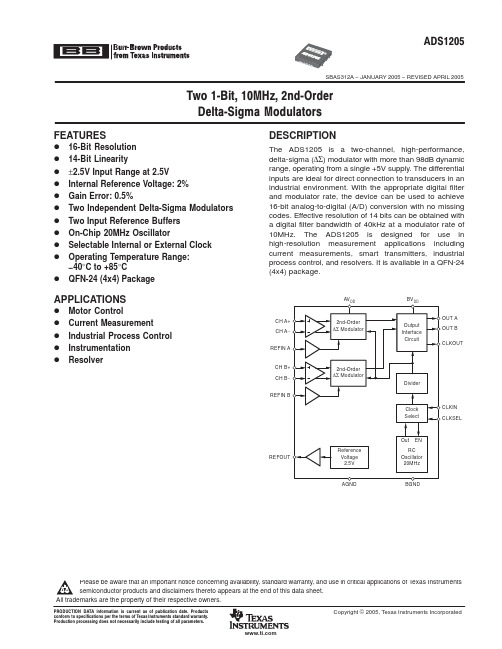
ESD damage can range from subtle performance degradation to complete device failure. Precision integrated circuits may be more susceptible to damage because very small parametric changes could cause the device not to meet its published specifications.Figure 20Frequency (kHz)02468101214161819Figure 21Frequency (kHz)02468101214161819EFFECTIVE NUMBER OF BITSvs DECIMATION RATIO1001k9886746250382614Sinc 2FilterSinc 3FilterPOWER−SUPPLY CURRENTvs TEMPERATURE40−2020406080100Temperature (_C)CLKSEL =1CLKSEL =0,CLKIN =20MHzCLKSEL =0,CLKIN =32MHzPACKAGING INFORMATIONOrderable Device Status (1)Package Type Package Drawing Pins Package Qty Eco Plan (2)Lead/Ball Finish MSL Peak Temp (3)ADS1205IRGER ACTIVE QFN RGE 243000Green (RoHS &no Sb/Br)CU NIPDAU Level-2-260C-1YEAR ADS1205IRGERG4ACTIVE QFN RGE 243000Green (RoHS &no Sb/Br)CU NIPDAU Level-2-260C-1YEAR ADS1205IRGET ACTIVE QFN RGE 24250Green (RoHS &no Sb/Br)CU NIPDAU Level-2-260C-1YEAR ADS1205IRGETG4ACTIVEQFNRGE24250Green (RoHS &no Sb/Br)CU NIPDAULevel-2-260C-1YEAR(1)The marketing status values are defined as follows:ACTIVE:Product device recommended for new designs.LIFEBUY:TI has announced that the device will be discontinued,and a lifetime-buy period is in effect.NRND:Not recommended for new designs.Device is in production to support existing customers,but TI does not recommend using this part in a new design.PREVIEW:Device has been announced but is not in production.Samples may or may not be available.OBSOLETE:TI has discontinued the production of the device.(2)Eco Plan -The planned eco-friendly classification:Pb-Free (RoHS)or Green (RoHS &no Sb/Br)-please check /productcontent for the latest availability information and additional product content details.TBD:The Pb-Free/Green conversion plan has not been defined.Pb-Free (RoHS):TI's terms "Lead-Free"or "Pb-Free"mean semiconductor products that are compatible with the current RoHS requirements for all 6substances,including the requirement that lead not exceed 0.1%by weight in homogeneous materials.Where designed to be soldered at high temperatures,TI Pb-Free products are suitable for use in specified lead-free processes.Green (RoHS &no Sb/Br):TI defines "Green"to mean Pb-Free (RoHS compatible),and free of Bromine (Br)and Antimony (Sb)based flame retardants (Br or Sb do not exceed 0.1%by weight in homogeneous material)(3)MSL,Peak Temp.--The Moisture Sensitivity Level rating according to the JEDEC industry standard classifications,and peak solder temperature.Important Information and Disclaimer:The information provided on this page represents TI's knowledge and belief as of the date that it is provided.TI basesits knowledge and belief on information provided by third parties,and makes no representation or warranty as to the accuracy of such information.Efforts are underway to better integrate information from third parties.TI has taken and continues to take reasonable steps to provide representative and accurate information but may not have conducted destructive testing or chemical analysis on incoming materials and chemicals.TI and TI suppliers consider certain information to be proprietary,and thus CAS numbers and other limited information may not be available for release.In no event shall TI's liability arising out of such information exceed the total purchase price of the TI part(s)at issue in this document sold by TI to Customer on an annual basis.PACKAGE OPTION ADDENDUM21-Jun-2005Addendum-Page 1元器件交易网IMPORTANT NOTICETexas Instruments Incorporated and its subsidiaries (TI) reserve the right to make corrections, modifications, enhancements, improvements, and other changes to its products and services at any time and to discontinue any product or service without notice. Customers should obtain the latest relevant information before placing orders and should verify that such information is current and complete. All products are sold subject to TI’s terms and conditions of sale supplied at the time of order acknowledgment.TI warrants performance of its hardware products to the specifications applicable at the time of sale in accordance with TI’s standard warranty. T esting and other quality control techniques are used to the extent TI deems necessary to support this warranty. Except where mandated by government requirements, testing of all parameters of each product is not necessarily performed.TI assumes no liability for applications assistance or customer product design. Customers are responsible for their products and applications using TI components. T o minimize the risks associated with customer products and applications, customers should provide adequate design and operating safeguards.TI does not warrant or represent that any license, either express or implied, is granted under any TI patent right, copyright, mask work right, or other TI intellectual property right relating to any combination, machine, or process in which TI products or services are used. Information published by TI regarding third-party products or services does not constitute a license from TI to use such products or services or a warranty or endorsement thereof. Use of such information may require a license from a third party under the patents or other intellectual property of the third party, or a license from TI under the patents or other intellectual property of TI.Reproduction of information in TI data books or data sheets is permissible only if reproduction is without alteration and is accompanied by all associated warranties, conditions, limitations, and notices. Reproduction of this information with alteration is an unfair and deceptive business practice. TI is not responsible or liable for such altered documentation.Resale of TI products or services with statements different from or beyond the parameters stated by TI for that product or service voids all express and any implied warranties for the associated TI product or service and is an unfair and deceptive business practice. TI is not responsible or liable for any such statements. Following are URLs where you can obtain information on other Texas Instruments products and application solutions:Products ApplicationsAmplifiers Audio /audioData Converters Automotive /automotiveDSP Broadband /broadbandInterface Digital Control /digitalcontrolLogic Military /militaryPower Mgmt Optical Networking /opticalnetwork Microcontrollers Security /securityTelephony /telephonyVideo & Imaging /videoWireless /wirelessMailing Address:Texas InstrumentsPost Office Box 655303 Dallas, Texas 75265Copyright 2005, Texas Instruments Incorporated。
AD2S1205WSTZ中文资料

One Technology Way, P.O. Box 9106, Norwood, MA 02062-9106, U.S.A.
Tel: 781.329.4700
Fax: 781.326.8703 © 2006 Analog Devices, Inc. All rights reserved.
• System Fault Detection: A fault detection circuit will detect any loss of resolver signals, out of range input signals, input signal mismatch, or loss of position tracking.
笔记本电源管理芯片

笔记本电源管理芯片,i/o(2009-11-06 22:23:06)转载标签:杂谈笔记本电源管理芯片大全:ADP3421/ADP3410/ADP3205/ADP3180/ADP3806/ADP3203/ADP3020电源管理芯片大全RT9237/RT9237CS/RT9231/RT9241/RT9231A/RT9241A/RT9241B电源管理芯片大全RT9221/RT9600/RT9602/RT9603/RT9222/RT9224/RT9224A/RT9223电源管理芯片大全RT9227A/RT9228/RT9238/RT9248A/RT9173/RT9202/RC5051M 电源管理芯片大全5090MTC/RC5093MTC/5098MTC/SC1470/SC1205/SC1214TS电源管理芯片大全SC1155CSW/SC1154CSW/SC1153CSW/SC1189SW//SC1185ACSW电源管理芯片大全SC1402ISS/SC2422ACS//SC1164CSW/SC1150/ISL6524CB/RC5053M电源管理芯片大全/ISL6522CB/ISL6556BCB/ISL6566CRZ/4500M/HIP6501ACB电源管理芯片大全HIP6521CB/HIP6502/HIP6016CB/HIP6017CB/HIP6018BCB/HIP6019BCB电源管理芯片大全HIP6020CB/HIP6021CB/HIP6601/HIP6602BCB/HIP6603CB/HIP6004ECB电源管理芯片大全HIP6620BAB/HIP6301CB/HIP6520/HIP6302CB/HIP6303CS/SC1163电源管理芯片大全SC1159/SC1486/ST75185C/SC2434SW/SC1480/SC1403/SC1404 电源管理芯片大全SC1485/SC1486/SC1474/SC1476/SC1211/SC451/SC1470电源管理芯片大全IRU3013/IRU3004CW/IRU3055CQTR/IRU1150CM/MS-5/MS-7/5322电源管理芯片大全CS5301/L6916D/L6917CB/LM2637M/LM2638M/ICE2AS01/KA7500B笔记本电源管理芯片ADP3421/ADP3410/ADP3205/ADP3180/ADP3806/ADP3203/ADP3020笔记本电源管理芯片ADP3170/ADP3188/ADP3181/ADP3166/ADP3163/ADP3165/ADP3168笔记本电源管理芯片ADP3169/ADP3415/ADP3416/ADP3417/ADP3418/ADP3155/ADP3422笔记本电源管理芯片ADP3207/MAX3243/MAX1902/MAX1999/MAX785/MAX786/MAX1717笔记本电源管理芯片MAX1604/MAX1987/MAX1887/ISL6223/ISL6565/ISL6225/ISL6218笔记本电源管理芯片ISL6566/ISL6568/ISL6563笔记本电源管理芯片MAX1904(SSOP)/MAX1904(BGA的)/MAX1634/MAX1710/MAX1711笔记本电源管理芯片MAX1904/MAX1714/MAX1715/MAX1718/MAX1772/MAX1773/MAX1901笔记本电源管理芯片MAX1908/MAX1632/MAX1545/MAX1535/MAX1631/MAX1909/MAX1977笔记本电源管理芯片MAX1504/MAX1845/MAX1844/MAX1980/MAX1532/MAX1907/MAX1617笔记本电源管理芯片MAX8734/MAX8743/MAX8724/MAX1644/MAX1645/ISL6207/ISL6559CB笔记本电源管理芯片ISL6217/ISL6264/ISL6227/ISL6255/SC1485/SC1404笔记本电源管理芯片LT3728LX/LTC1709/LTC1439/LTC3735/LTC1628/LTC1707/LTC1736笔记本电源管理芯片MB3887/MB3878/LTC1778/LTC1511/LTC1709/LTC1439/LM8463笔记本电源管理芯片LM2729/LM2641/VT8235/LTC3728/SC1476/SC1474/SC1404/SC451笔记本电源管理芯片SC1403/SC1470/SC1486/TPS51120/TPS51020/PU2211A/VT6105笔记本电源管理芯片VT8235/VT1612/VT8237/VT8233/VT8235(BGA的)/LTC3707/LTC3716笔记本IO芯片大全PC87591S(VPCQ01)/PC 87591L(VPC01)/PC 97317IBW/PC 87393 VGJ笔记本IO芯片大全TB62501F/TB62506F/TB6808F/KB910QF/KB910QB4/KB910LQF/KB910LQFA1笔记本IO芯片大全KB3910QB0/KB910SFC1/KB3910SF/PC87591E-VLB/IT8510E/PS5130笔记本IO芯片大全PC87591E (-VPCI01),(VPCQ01)/PC 97551-VPC/PC87570-ICC/VPC笔记本IO芯片大全PC87391VGJ/TB6807F/W83L950D/LPC47N249-AQQ/PCI4510/PC8394T笔记本IO芯片大全PC87392/PC87541L/PC87541V/LPC47N253-AQQ/PC87591E-VLB笔记本IO芯片大全LPC47N250-SD/LPC47N252-SG/LPC47N254-AQQ。
RTS-1205中文资料

ECONOLINE - DC/DC-Converter
RTS/RTD Series, 2 Watt, SMD (Single & Dual Output) Package Style and Pinning (mm)
Dual Output Single Output
3rd angle projection
Efficiency at Full Load Short Circuit Protection Operating Temperature Range Storage Temperature Range Package Weight
元器件交易网
Specifications (Core Operating Area) and Operating Temperature / Derating-Graph
Input Voltage Range Output Voltage Accuracy Rated Power Isolation Voltage Isolation Resistance (Viso = 500VDC) Isolation Capacitance Ripple and Noise (20MHz BW) Line Voltage Regulation Load Voltage Regulation (10% to 100% full load) 3.3V output type 5V output type 9V, 12V, 15V output types 24V output type ±10% ±5% 2W 1000VDC min. 10 GΩ min. 40pF min./115pF max. 150mVp-p max. 1.2%/1% of Vin 20% max. 15% max. 10% max. 10% max. 70% min. 1 Second -40°C to +71°C -55°C to +125°C Single output types Dual output types August 2002 2.1g 2.5g EC 49
MC33035资料

MC33035, NCV33035 Brushless DCMotor ControllerThe MC33035 is a high performance second generation monolithic brushless DC motor controller containing all of the active functions required to implement a full featured open loop, three or four phase motor control system. This device consists of a rotor position decoder for proper commutation sequencing, temperature compensated reference capable of supplying sensor power, frequency programmable sawtooth oscillator, three open collector top drivers, and three high current totem pole bottom drivers ideally suited for driving power MOSFETs.Also included are protective features consisting of undervoltage lockout, cycle−by−cycle current limiting with a selectable time delayed latched shutdown mode, internal thermal shutdown, and a unique fault output that can be interfaced into microprocessor controlled systems.Typical motor control functions include open loop speed, forward or reverse direction, run enable, and dynamic braking. The MC33035 is designed to operate with electrical sensor phasings of 60°/300° or 120°/240°, and can also efficiently control brush DC motors. Features•10 to 30 V Operation•Undervoltage Lockout•6.25 V Reference Capable of Supplying Sensor Power•Fully Accessible Error Amplifier for Closed Loop Servo Applications•High Current Drivers Can Control External 3−Phase MOSFET Bridge•Cycle−By−Cycle Current Limiting•Pinned−Out Current Sense Reference•Internal Thermal Shutdown•Selectable 60°/300° or 120°/240° Sensor Phasings•Can Efficiently Control Brush DC Motors with External MOSFET H−Bridge•NCV Prefix for Automotive and Other Applications Requiring Site and Control Changes•Pb−Free Packages are Available241P SUFFIXPLASTIC PACKAGECASE 724DW SUFFIXPLASTIC PACKAGECASE 751E(SO−24L)See detailed ordering and shipping information in the package dimensions section on page 27 of this data sheet.ORDERING INFORMATIONSee general marking information in the device marking section on page 27 of this data sheet.DEVICE MARKING INFORMATIONRepresentative Schematic DiagramThis device contains 285 active transistors.1.The input common mode voltage or input signal voltage should not be allowed to go negative by more than 0.3 V.2.The compliance voltage must not exceed the range of −0.3 to V ref.3.NCV33035: T low = −40°C, T high = 125°C. Guaranteed by design. NCV prefix is for automotive and other applications requiring site and changecontrol.4.MC33035: T A = −40°C to +85°C; NCV33035: T A = −40°C to +125°C.5.Maximum package power dissipation limits must be observed.ERROR AMPLIFIER Output Voltage SwingHigh State (R L = 15 k to Gnd) Low State (R L = 15 k to V ref)V OHV OL4.6−5.30.5−1.0VV s a t , O U T P U T S A T U R A T I O N V O L T A G E (V )5.0 µs/DIVA V = +1.0No Load T A = 25°C, O U T P U T V O L T A G E (V )O 4.53.01.51.0 µs/DIVA V = +1.0No Load T A = 25°C3.053.02.95I O , OUTPUT LOAD CURRENT (mA)f, FREQUENCY (Hz)562202001801601401201008060−−16−08.0162432404840240A V O L , O P E N L O O P V O L T A G E G A I N (d B )E X C E S S P H A S E (D E G R E E S ),φT A , AMBIENT TEMPERATURE (°C)−55−4.0−2.02.01254.01007550250−25f O S C O S C I L L A T O R F R E Q U E N C Y C H A N G E (%),∆1001.0R T , TIMING RESISTOR (k Ω)100010010010f O S C O S C I L L A T O R F R E Q U E N C Y (k H z ),Figure 1. Oscillator Frequency versusTiming Resistor Figure 2. Oscillator Frequency Changeversus TemperatureFigure 3. Error Amp Open Loop Gain andPhase versus Frequency Figure 4. Error Amp Output SaturationVoltage versus Load CurrentFigure 5. Error Amp Small−SignalTransient Response Figure 6. Error Amp Large−SignalTransient Response1.02.00− 0.8−1.61.60.8 5.04.03.00V , O U T P U T V O L T A G E (V )O VI Sink , SINK CURRENT (mA)0−40−20−4020, N O R M A L I Z E D R E F E R E N C E V O L T A G E C H A N G E (m V )∆V r e f 0−−−−− 12− 16V r e f , R E F E R E N C E O U T P U T V O L T A G E C H A N G E (m V )∆Figure 11. Bottom Drive Response Time versusCurrent Sense Input Voltage Figure 12. Fault Output Saturationversus Sink Current0CURRENT SENSE INPUT VOLTAGE (NORMALIZED TO V th )50100150200250t H L , B O T T O M D R I V E R E S P O N S E T I M E (n s )1.0O U T P U T V O L T A G E (%)−40I O , OUTPUT LOAD CURRENT (mA)02.0806020, O U T P U T S A T U R A T I O N V O L T A G E (V )s a t V 50 ns/DIV V CC = 20 V V C = 20 V C L = 1.0 nF T A = 25°C100 ns/DIVV CC = 20 V V C = 20 V R L = 1.0 k C L = 15 pF T A = 25°CFigure 13. Top Drive Output SaturationVoltage versus Sink CurrentFigure 14. Top Drive Output WaveformFigure 15. Bottom Drive Output Waveform Figure 16. Bottom Drive Output WaveformI Sink , SINK CURRENT (mA)0.40.81.2V s a t , O U T P U T S A T U R A T I O N V O L T A G E (V )Figure 17. Bottom Drive Output SaturationVoltage versus Load Current 50 ns/DIVV CC = 20 V V C = 20 V C L = 15 pF T A= 25°CFigure 18. Power and Bottom Drive SupplyCurrent versus Supply Voltage, P O W E R S U P P L Y C U R R E N T (m A )C C , I 05.01015202530C I V CC , SUPPLY VOLTAGE (V)1000100100O U T P U T V O L T A G E (%)O U T P U T V O L T A G E (%)INTRODUCTIONThe MC33035 is one of a series of high performance monolithic DC brushless motor controllers produced by Motorola. It contains all of the functions required to implement a full−featured, open loop, three or four phase motor control system. In addition, the controller can be made to operate DC brush motors. Constructed with Bipolar Analog technology, it offers a high degree of performance and ruggedness in hostile industrial environments. The MC33035 contains a rotor position decoder for proper commutation sequencing, a temperature compensated reference capable of supplying a sensor power, a frequency programmable sawtooth oscillator, a fully accessible error amplifier, a pulse width modulator comparator, three open collector top drive outputs, and three high current totem pole bottom driver outputs ideally suited for driving power MOSFETs. Included in the MC33035 are protective features consisting of undervoltage lockout, cycle−by−cycle current limiting with a selectable time delayed latched shutdown mode, internal thermal shutdown, and a unique fault output that can easily be interfaced to a microprocessor controller. Typical motor control functions include open loop speed control, forward or reverse rotation, run enable, and dynamic braking. In addition, the MC33035 has a 60°/120°select pin which configures the rotor position decoder for either 60° or 120° sensor electrical phasing inputs. FUNCTIONAL DESCRIPTIONA representative internal block diagram is shown in Figure 19 with various applications shown in Figures 36, 38, 39, 43, 45, and 46. A discussion of the features and function of each of the internal blocks given below is referenced to Figures 19 and 36.Rotor Position DecoderAn internal rotor position decoder monitors the three sensor inputs (Pins 4, 5, 6) to provide the proper sequencing of the top and bottom drive outputs. The sensor inputs are designed to interface directly with open collector type Hall Effect switches or opto slotted couplers. Internal pull−up resistors are included to minimize the required number of external components. The inputs are TTL compatible, with their thresholds typically at 2.2 V. The MC33035 series is designed to control three phase motors and operate with four of the most common conventions of sensor phasing. A 60°/120°Select (Pin 22) is conveniently provided and affords the MC33035 to configure itself to control motors having either 60°, 120°, 240° or 300° electrical sensor phasing. With three sensor inputs there are eight possible input code combinations, six of which are valid rotor positions. The remaining two codes are invalid and are usually caused by an open or shorted sensor line. With six valid input codes, the decoder can resolve the motor rotor position to within a window of 60 electrical degrees.The Forward/Reverse input (Pin 3) is used to change the direction of motor rotation by reversing the voltage across the stator winding. When the input changes state, from high to low with a given sensor input code (for example 100), the enabled top and bottom drive outputs with the same alpha designation are exchanged (A T to A B, B T to B B, C T to C B). In effect, the commutation sequence is reversed and the motor changes directional rotation.Motor on/off control is accomplished by the Output Enable (Pin 7). When left disconnected, an internal 25 µA current source enables sequencing of the top and bottom drive outputs. When grounded, the top drive outputs turn off and the bottom drives are forced low, causing the motor to coast and the Fault output to activate.Dynamic motor braking allows an additional margin of safety to be designed into the final product. Braking is accomplished by placing the Brake Input (Pin 23) in a high state. This causes the top drive outputs to turn off and the bottom drives to turn on, shorting the motor−generated back EMF. The brake input has unconditional priority over all other inputs. The internal 40 kΩ pull−up resistor simplifies interfacing with the system safety−switch by insuring brake activation if opened or disconnected. The commutation logic truth table is shown in Figure 20. A four input NOR gate is used to monitor the brake input and the inputs to the three top drive output transistors. Its purpose is to disable braking until the top drive outputs attain a high state. This helps to prevent simultaneous conduction of the the top and bottom power switches. In half wave motor drive applications, the top drive outputs are not required and are normally left disconnected. Under these conditions braking will still be accomplished since the NOR gate senses the base voltage to the top drive output transistors.Error AmplifierA high performance, fully compensated error amplifier with access to both inputs and output (Pins 11, 12, 13) is provided to facilitate the implementation of closed loop motor speed control. The amplifier features a typical DC voltage gain of 80 dB, 0.6 MHz gain bandwidth, and a wide input common mode voltage range that extends from ground to V ref. In most open loop speed control applications, the amplifier is configured as a unity gain voltage follower with the noninverting input connected to the speed set voltage source. Additional configurations are shown in Figures 31 through 35.OscillatorThe frequency of the internal ramp oscillator is programmed by the values selected for timing components R T and C T. Capacitor C T is charged from the Reference Output (Pin 8) through resistor R T and discharged by an internal discharge transistor. The ramp peak and valley voltages are typically 4.1 V and 1.5 V respectively. To provide a good compromise between audible noise and output switching efficiency, an oscillator frequency in the range of 20 to 30 kHz is recommended. Refer to Figure 1 for component selection.Figure 19. Representative Block DiagramNOTES:1.V = Any one of six valid sensor or drive combinations X = Don’t care.2.The digital inputs (Pins 3, 4, 5, 6, 7, 22, 23) are all TTL compatible. The current sense input (Pin 9) has a 100 mV threshold with respect to Pin 15.A logic 0 for this input is defined as < 85 mV, and a logic 1 is > 115 mV.3.The fault and top drive outputs are open collector design and active in the low (0) state.4.With 60°/120°select (Pin 22) in the high (1) state, configuration is for 60°sensor electrical phasing inputs. With Pin 22 in low (0) state, configurationis for 120° sensor electrical phasing inputs.5.Valid 60° or 120° sensor combinations for corresponding valid top and bottom drive outputs.6.Invalid sensor inputs with brake = 0; All top and bottom drives off, Fault low.7.Invalid sensor inputs with brake = 1; All top drives off, all bottom drives on, Fault low.8.Valid 60° or 120°sensor inputs with brake = 1; All top drives off, all bottom drives on, Fault high.9.Valid sensor inputs with brake = 1 and enable = 0; All top drives off, all bottom drives on, Fault low.10.Valid sensor inputs with brake = 0 and enable = 0; All top and bottom drives off, Fault low.11.All bottom drives off, Fault low.Figure 20. Three Phase, Six Step Commutation Truth Table (Note 1)Pulse Width ModulatorThe use of pulse width modulation provides an energy efficient method of controlling the motor speed by varying the average voltage applied to each stator winding during the commutation sequence. As C T discharges, the oscillator sets both latches, allowing conduction of the top and bottom drive outputs. The PWM comparator resets the upper latch, terminating the bottom drive output conduction when the positive−going ramp of C T becomes greater than the error amplifier output. The pulse width modulator timing diagram is shown in Figure 21. Pulse width modulation for speed control appears only at the bottom drive outputs.Current LimitContinuous operation of a motor that is severely over−loaded results in overheating and eventual failure. This destructive condition can best be prevented with the use of cycle−by−cycle current limiting. That is, each on−cycle is treated as a separate event. Cycle−by−cycle current limiting is accomplished by monitoring the stator current build−up each time an output switch conducts, and upon sensing an over current condition, immediately turning off the switch and holding it off for the remaining duration of oscillator ramp−up period. The stator current is converted to a voltage by inserting a ground−referenced sense resistor R S (Figure 36) in series with the three bottom switch transistors (Q4, Q5, Q6). The voltage developed across the sense resistor is monitored by the Current Sense Input (Pins 9 and 15), and compared to the internal 100 mV reference. The current sense comparator inputs have an input common mode range of approximately 3.0 V. If the 100 mV current sense threshold is exceeded, the comparator resets the lower sense latch and terminates output switch conduction. The value for the current sense resistor is:R S+0.1I stator(max)The Fault output activates during an over current condition. The dual−latch PWM configuration ensures that only one single output conduction pulse occurs during any given oscillator cycle, whether terminated by the output of the error amp or the current limit comparator.Figure 21. Pulse Width Modulator Timing Diagram Current Sense Input Capacitor C T Error Amp Out/PWMInput Latch Set"Inputs Top Drive Outputs Bottom DriveOutputsFault OutputReferenceThe on−chip 6.25 V regulator (Pin 8) provides charging current for the oscillator timing capacitor, a reference for the error amplifier, and can supply 20 mA of current suitable for directly powering sensors in low voltage applications. In higher voltage applications, it may become necessary to transfer the power dissipated by the regulator off the IC. This is easily accomplished with the addition of an external pass transistor as shown in Figure 22. A 6.25 V reference level was chosen to allow implementation of the simpler NPN circuit, where V ref − V BE exceeds the minimum voltage required by Hall Effect sensors over temperature. With proper transistor selection and adequate heatsinking, up to one amp of load current can be obtained.Figure 22. Reference Output BuffersThe NPN circuit is recommended for powering Hall or opto sensors, where the output voltage temperature coefficient is not critical. The PNP circuit is slightly more complex, but is also more accurate over temperature. Neither circuit has current limiting.V V and Sensor Power6.25 VUndervoltage LockoutA triple Undervoltage Lockout has been incorporated to prevent damage to the IC and the external power switch transistors. Under low power supply conditions, it guarantees that the IC and sensors are fully functional, and that there is sufficient bottom drive output voltage. The positive power supplies to the IC (V CC ) and the bottom drives (V C ) are each monitored by separate comparators that have their thresholds at 9.1 V . This level ensures sufficient gate drive necessary to attain low R DS(on) when driving standard power MOSFET devices. When directly powering the Hall sensors from the reference, improper sensor operation can result if the reference output voltage falls below 4.5 V . A third comparator is used to detect this condition. If one or more of the comparators detects an undervoltage condition, the Fault Output is activated, the top drives are turned off and the bottom drive outputs are held in a low state. Each of the comparators contain hysteresis to prevent oscillations when crossing their respective thresholds.Fault OutputThe open collector Fault Output (Pin 14) was designed to provide diagnostic information in the event of a system malfunction. It has a sink current capability of 16 mA and can directly drive a light emitting diode for visual indication.Additionally, it is easily interfaced with TTL/CMOS logic for use in a microprocessor controlled system. The Fault Output is active low when one or more of the following conditions occur:1)Invalid Sensor Input code 2)Output Enable at logic [0]3)Current Sense Input greater than 100 mV4)Undervoltage Lockout, activation of one or more of the comparators5)Thermal Shutdown, maximum junction temperature being exceededThis unique output can also be used to distinguish between motor start−up or sustained operation in an overloaded condition. With the addition of an RC network between the Fault Output and the enable input, it is possible to create a time−delayed latched shutdown for overcurrent. The added circuitry shown in Figure 23 makes easy starting of motor systems which have high inertial loads by providing additional starting torque, while still preserving overcurrent protection. This task is accomplished by setting the current limit to a higher than nominal value for a predetermined time.During an excessively long overcurrent condition, capacitor C DLY will charge, causing the enable input to cross its threshold to a low state. A latch is then formed by the positive feedback loop from the Fault Output to the Output Enable.Once set, by the Current Sense Input, it can only be reset by shorting C DLY or cycling the power supplies.Drive OutputsThe three top drive outputs (Pins 1, 2, 24) are open collector NPN transistors capable of sinking 50 mA with a minimum breakdown of 30 V. Interfacing into higher voltage applications is easily accomplished with the circuits shown in Figures 24 and 25.The three totem pole bottom drive outputs (Pins 19, 20, 21) are particularly suited for direct drive of N−Channel MOSFETs or NPN bipolar transistors (Figures 26, 27, 28 and 29). Each output is capable of sourcing and sinking up to 100 mA. Power for the bottom drives is supplied from V C (Pin 18). This separate supply input allows the designer added flexibility in tailoring the drive voltage, independent of V CC. A zener clamp should be connected to this input when driving power MOSFETs in systems where V CC is greater than 20 V so as to prevent rupture of the MOSFET gates.The control circuitry ground (Pin 16) and current sense inverting input (Pin 15) must return on separate paths to the central input source ground.Thermal ShutdownInternal thermal shutdown circuitry is provided to protect the IC in the event the maximum junction temperature is exceeded. When activated, typically at 170°C, the IC acts as though the Output Enable was grounded.Figure 23. Timed Delayed Latched Over Current ShutdownFigure 24. High Voltage Interface withNPN Power TransistorsTransistor Q1 is a common base stage used to level shift from V CC to the high motor voltage, V M. The collector diode is required if V CC is present while V M is low.[R DLY C DLY Inǒ6.25–(20x10–6R DLY)1.4–(20x10R DLY)ǓFigure 25. High Voltage Interface withN−Channel Power MOSFETsFigure 26. Current Waveform Spike SuppressionFigure 27. MOSFET Drive Precautions Figure 28. Bipolar Transistor DriveSeries gate resistor R g will dampen any high frequency oscillations caused by the MOSFET input capacitance and any series wiring induction in the gate−source circuit. Diode D is required if the negative current into the Bot-tom Drive Outputs exceeds 50 mA.The totem−pole output can furnish negative base current for enhanced tran-sistor turn−off, with the addition of capacitor C.Figure 29. Current Sensing Power MOSFETs Figure 30. High Voltage Boost SupplyVirtually lossless current sensing can be achieved with the implementation of SENSEFET power switches.[R S @I pk @R DS(on)r DM(on))RS= 200 Ω, 1/4 W Pin 9 ≈ 0.75 I pkControl Circuitry Ground (Pin 16) and Current Sense Inverting Input (Pin 15)must return on separate paths to the Central Input Source Ground.This circuit generates V Boostfor Figure 25.Figure 31. Differential Input Speed Controller Figure 32. Controlled Acceleration/DecelerationV V A VPin 13+V A ǒR 3)R 41)R 2Ǔ R 23 *ǒR 43V B ǓResistor R 1 with capacitor C sets the acceleration time constant while R 2controls the deceleration. The values of R 1 and R 2 should be at least ten times greater than the speed set potentiometer to minimize time constant variations with different speed settings.This circuit can control the speed of a cooling fan proportional to the difference between the sensor and set temperatures. The control loop is closed as the forced air cools the NTC thermistor. For controlled heating applications, ex-change the positions of R1 and R2.Figure 35. Closed Loop Temperature ControlSYSTEM APPLICATIONSThree Phase Motor CommutationThe three phase application shown in Figure 36 is a full−featured open loop motor controller with full wave, six step drive. The upper power switch transistors are Darlingtons while the lower devices are power MOSFETs. Each of these devices contains an internal parasitic catch diode that is used to return the stator inductive energy back to the power supply. The outputs are capable of driving a delta or wye connected stator, and a grounded neutral wye if split supplies are used. At any given rotor position, only one top and one bottom power switch (of different totem poles) is enabled. This configuration switches both ends of the stator winding from supply to ground which causes the current flow to be bidirectional or full wave. A leading edge spike is usually present on the current waveform and can cause a current−limit instability. The spike can be eliminated by adding an RC filter in series with the Current Sense Input. Using a low inductance type resistor for R S will also aid in spike reduction. Care must be taken in the selection of the bottom power switch transistors so that the current during braking does not exceed the device rating. During braking, the peak current generated is limited only by the series resistance of the conducting bottom switch and winding.I peak+V M)EMFswitch)R windingIf the motor is running at maximum speed with no load, the generated back EMF can be as high as the supply voltage, and at the onset of braking, the peak current may approach twice the motor stall current. Figure 37 shows the commutation waveforms over two electrical cycles. The first cycle (0° to 360°) depicts motor operation at full speed while the second cycle (360° to 720°) shows a reduced speed with about 50% pulse width modulation. The current waveforms reflect a constant torque load and are shown synchronous to the commutation frequency for clarity.Figure 36. Three Phase, Six Step, Full Wave Motor ControllerFigure 37. Three Phase, Six Step, Full Wave Commutation WaveformsRotor Electrical Position (Degrees)100000001011111110100000001011111110720660600540480420360300240180120600S AS B S C CodeS C S B CodeS ASensor Inputs60°/120°Select PinOpenSensor Inputs60°/120°Select Pin GroundedA BB B Q 2 + Q 6C BQ 2 + Q 4Q 3 + Q 4Q 3 + Q 5Q 1 + Q 5Q 1 + Q 6Bottom DriveOutputsQ 2 + Q 6Q 2 + Q 4Q 3 + Q 4Q 3 + Q 5Motor DriveCurrentBFwd/Rev = 1C−O +−O +Conducting Power Switch TransistorsQ 1 + Q 5Top Drive OutputsQ 1 + Q 6AB T A TC T−O +100110001011001011110100010010101101Figure 38 shows a three phase, three step, half wave motor controller. This configuration is ideally suited for automotive and other low voltage applications since there is only one power switch voltage drop in series with a given stator winding. Current flow is unidirectional or half wave because only one end of each winding is switched. Continuous braking with the typical half wave arrangement presents a motor overheating problem since stator current is limited only by the winding resistance. This is due to the lack of upper power switch transistors, as in the full wave circuit, used to disconnect the windings from the supply voltage V M. A unique solution is to provide braking until the motor stops and then turn off the bottom drives. This can be accomplished by using the Fault Output in conjunction with the Output Enable as an over current timer. Components R DLY and C DLY are selected to give the motor sufficient time to stop before latching the Output Enable and the top drive AND gates low. When enabling the motor, the brake switch is closed and the PNP transistor (along with resistors R1 and R DLY) are used to reset the latch by discharging C DLY. The stator flyback voltage is clamped by a single zener and three diodes.Figure 38. Three Phase, Three Step, Half Wave Motor ControllerThree Phase Closed Loop ControllerThe MC33035, by itself, is only capable of open loop motor speed control. For closed loop motor speed control, the MC33035 requires an input voltage proportional to the motor speed. Traditionally, this has been accomplished by means of a tachometer to generate the motor speed feedback voltage. Figure 39 shows an application whereby an MC33039, powered from the 6.25 V reference (Pin 8) of the MC33035, is used to generate the required feedback voltage without the need of a costly tachometer. The same Hall sensor signals used by the MC33035 for rotor position decoding are utilized by the MC33039. Every positive or negative going transition of the Hall sensor signals on any of the sensor lines causes the MC33039 to produce an output pulse of defined amplitude and time duration, as determined by the external resistor R1 and capacitor C1. The output train of pulses at Pin 5 of the MC33039 are integrated by the error amplifier of the MC33035 configured as an integrator to produce a DC voltage level which is proportional to the motor speed. This speed proportional voltage establishes the PWM reference level at Pin 13 of the MC33035 motor controller and closes the feedback loop. The MC33035 outputs drive a TMOS power MOSFET 3−phase bridge. High currents can be expected during conditions of start−up, breaking, and change of direction of the motor.The system shown in Figure 39 is designed for a motor having 120/240 degrees Hall sensor electrical phasing. The system can easily be modified to accommodate 60/300 degree Hall sensor electrical phasing by removing the jumper (J2) at Pin 22 of the MC33035.Figure 39. Closed Loop Brushless DC Motor Control Using The MC33035 and MC33039。
SC1205_04中文资料

θJC
Thermal Resistance Junction to Ambient
θJA
Operating Temperature Range
TJ
Storage Temperature Range
TSTG
Lead Temperature (Soldering) 10 Sec.
TLEAD
NOTE: (1) Specification refers to application circuit in Figure 1.
Features
Fast rise and fall times (15ns typical with 3000pf
load) 3 Amp peak drive current 14ns max Propagation delay (BG going low) Adaptive Non-overlapping Gate Drives provide
AC Operating Specifications
Parameter
Symbol
Conditions
Min
High Side Driver
Rise Time
Fall Time
Propagation Delay Time, TG Going High Propagation Delay Time, TG Going Low Low-Side Driver
of small inductors and low cost caps in place of electrolytics High efficiency portable computers Battery powered applications
SC1202中文资料

Notes: (1) C1 needed if device is far from filter capacitors (2) C2 minimum value required for stability
Revision 8/30/2000
1
SC1202 & SC1202A
Typical Application Circuits
Fixed Voltage Regulator
U1 VIN > 4.75V 3 IN
SC1202-3.3 2 TAB OUT
VOUT = 3.3V
+
C1 10uF Tant.
+ GND 1
C2 10uF Tant.
Adjustable Voltage Regulator
Pin Descriptions
Pin N umber 1 Pin N ame AD J GND 2 3 OUT IN Pin Function Thi s pi n i s the negati ve si de of the reference voltage for the devi ce. Transi ent response can be i mproved by addi ng a small bypass capaci tor from the adjust pi n to ground. Thi s pi n i s the bottom end of the i nternal resi stor feedback chai n for fi xed output voltage parts, and should be connected to ground. Thi s i s the power output of the devi ce, and i s electri cally connected to the TAB. Thi s i s the i nput supply pi n for the devi ce.
贴片三极管型号对照表
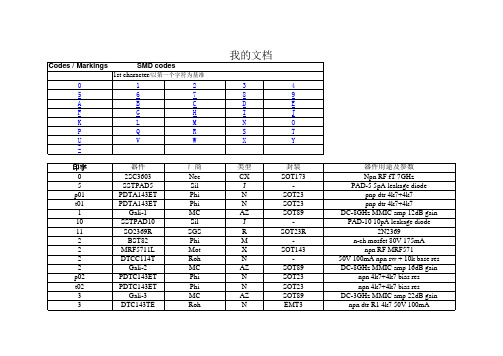
X
SOT143
A
SOT346
C
SOT346
O
SOT89
X
SOT143
DP
SOT363
N
SOT416
N
SOT23
N
SOT23
npn dtr R2 100k 50V 100mA npn dtr R2 100k 50V 100mA
dual pnp dtr 22k+22k dual pnp dtr 47k+47k dual pnp dtr 10k+47k dual pnp dtr R1 10k dual pnp dtr R1 4k7 dual pnp dtr 1k0+1k0 dual pnp dtr 2k2+2k2 dual pnp dtr 4k7+4k7 dual pnp dtr 4k7+47k dual pnp dtr 22k+47k dual pnp dtr 2k2+47k
N
EMT3
npn dtr R1 22k 50V 100mA
N
SC70
npn dtr R1 22k 50V 100mA
N
SC59
npn dtr R1 22k 50V 100mA
WQ
-
fT12GHz npn 4V 5mA
AZ
SOT89
DC-4GHz MMIC amp 115 dBm o/p
N
EMT3
npn dtr R1 47k 50V 100mA
pnp dtr pnp dtr pnp dtr
我的文档
11A
PZM11NB2A
Phi
11A
MMBD1501A
AD2S1205中文资料

12-Bit R/D Converterwith Reference Oscillator Preliminary Technical Data AD2S1205Rev.PrB_10/06Information furnished by Analog Devices is believed to be accurate and reliable.However, no responsibility is assumed by Analog Devices for its use, nor for anyinfringements of patents or other rights of third parties that may result from its use. Specifications subject to change without notice. No license is granted by implication or otherwise under any patent or patent rights of Analog Devices. Trademarks and registered trademarks are the property of their respective owners.One Technology Way, P.O. Box 9106, Norwood, MA 02062-9106, U.S.A. Tel: Fax: 781.326.8703© 2006 Analog Devices, Inc. All rights reserved.FEATURESComplete monolithic R/D converterParallel and serial 12-bit data portsSystem fault detectionAbsolute position and velocity outputs Differential inputs±11 arc minutes of accuracy1,250 rps maximum tracking rate, 12-bit resolution Incremental encoder emulation (1,024 pulses/rev) Programmable sinusoidal oscillator on-board Compatible with DSP and SPI® interface standards 204.8 kHz square wave outputSingle-supply operation (5.00 V ± 5%)−40°C to +125°C temperature rating44-lead LQFP package4 kV ESD protection GENERAL DESCRIPTIONThe AD2S1205 is a complete 12-bit resolution tracking resolver-to-digital converter, integrating an on-board programmable sinusoidal oscillator that provides sine wave excitation for resolvers. An external crystal is recommended to provide a precision time reference.The converter accepts 3.15 V p-p ± 27% input signals, in the range of 10 kHz to 20 kHz on the Sin and Cos inputs. A Type II servo loop is employed to track the inputs and convert the input Sin and Cos information into a digital representation of the input angle and velocity. The maximum tracking rate of the converter is set internally by the input clock frequency. The nominal clock frequency is 8.192MHz which allows a tracking rate of 1,000rps. However by increasing the clock frequency to 10.24MHz a maximum tracking rate of 1,250 rps can be achieved.FUNCTIONAL BLOCK DIAGRAMFigure 1.AD2S1205Preliminary Technical DataRev.PrB | Page 2 of 25APPLICATIONSElectric power steering Electric vehiclesIntegrated starter generator/alternator Encoder emulationAutomotive motion sensing and controlPRODUCT HIGHLIGHTS•Complete Resolver-to-Digital Interface: The AD2S1205 provides the complete solution for digitizing resolver signals (12-bit resolution) with on-board programmable sinusoidal oscillator.•Ratiometric Tracking Conversion: This technique provides continuous output position data without conversion delay. It also provides noise immunity and tolerance of harmonic distortion on the reference and input signals.•Triple Format Position Data: Absolute 12-bit angular binary position data accessed either via a 12-bit parallel port or via a 3-wire serial interface. Incremental encoder emulation in standard A QUAD B format, with direction output is available.•Digital Velocity Output: 12-bit signed digital velocity, twos complement format, accessed either via a 12-bit parallel port or via a 3-wire serial interface.•Programmable Excitation Frequency : Excitation fre-quency easily programmable to 10 kHz, 12 kHz, 15 kHz, or 20 kHz by using the frequency select pins.•System Fault Detection: A fault detection circuit will detect any loss of resolver signals, out of range inputsignals, input signal mismatch, or loss of position tracking.Preliminary Technical DataAD2S1205Rev. PrB | Page 3 of 25TABLE OF CONTENTSAD2S1205–Specifications................................................................4 Absolute Maximum Ratings............................................................6 ESD Caution..................................................................................6 Pin Configuration and Function Descriptions.............................7 Resolver Format Signals...................................................................8 Principle of Operation......................................................................9 Fault Detection Circuit.................................................................9 Connecting the Converter.........................................................11 Absolute Position and Velocity Output....................................12 Parallel Interface..........................................................................12 Serial Interface.............................................................................14 Incremental Encoder Outputs...................................................16 On-Board Programmable Sinusoidal Oscillator.....................17 Supply Sequencing and Reset....................................................17 Charge Pump Output.................................................................18 Circuit Dynamics............................................................................19 AD2S1205 Loop Response Model............................................19 Sources of Error...........................................................................20 Clock Requirements...................................................................21 Connecting to the DSP...............................................................21 Outline Dimensions........................................................................22 Ordering Guide (22)AD2S1205 Preliminary Technical Data AD2S1205–SPECIFICATIONS1 The voltages Sin, SinLO, Cos, and CosLO relative to AGND must always be between 0.2 V and AV DD.Rev.PrB | Page 4 of 25Preliminary Technical Data AD2S1205 Parameter Min Typ Max Unit Conditions/CommentsFAULT DETECTION BLOCK (CONT.)DOSSin/Cos Threshold 4.0 4.09 4.2 V p-p DOS goes low when Sin or Cos exceeds threshold.Sin/Cos Mismatch 385 420 mV DOS latched low when Sin/Cos amplitude mismatchexceeds the threshold.Angular Accuracy (Worst Case) 33 Degrees DOS indicated before angular output error exceedslimit.Angular Latency (Worst Case) 66 Degrees Maximum electrical rotation before DOS is indicated.Time Latency 125 μsLOTTracking Threshold 5 Degrees LOT goes low when internal error signal exceedsthreshold. Guaranteed by design.Time Latency 1.1 msHysteresis 4 Degrees Guaranteed by designVOLTAGE REFERENCEREFOUT 2.39 2.47 2.52 V ±IOUT = 100 μADrift 70 ppm/°CPSRR −60 dBCHARGE PUMP OUTPUT (CPO)Frequency 204.8 kHz Square wave outputDuty Cycle 50 %POWER SUPPLYI DD Dynamic 18 mAELECTRICAL CHARACTERISTICSV IL Voltage Input Low 0.8 VV IH Voltage Input High 2.0 VV OL Voltage Output Low 0.4 V 2 mA loadV OH Voltage Output High 4.0 V −1 mA loadI IL Low Level Input Current 10 μAI IH High Level Input Current −10 μAI OZH High Level Three-State Leakage −10 μAI OZL Low Level Three-State Leakage 10 μARev. PrB | Page 5 of 25AD2S1205Preliminary Technical DataRev.PrB | Page 6 of 25ABSOLUTE MAXIMUM RATINGSTable 2.Parameter Rating Supply Voltage (V DD ) −0.3 V to +7.0 V Supply Voltage (AV DD ) −0.3 V to + 7.0 V Input Voltage −0.3 V to V DD + 0.3 V Output Voltage Swing −0.3 V to V DD + 0.3 V Operating Temperature Range (Ambient) −40°C to +125°C Storage Temperature Range −65°C to +150°C Lead Temperature SolderingVapor Phase (60 sec) 215°C Infrared (15 sec)220°CStresses above those listed under Absolute Maximum Ratingsmay cause permanent damage to the device. This is a stress rating only; functional operation of the device at these or any other conditions above those indicated in the operational sections of this specification is not implied. Exposure to absolute maximum ratings for extended periods may affect device reliability.ESD CAUTIONESD (electrostatic discharge) sensitive device. Electrostatic charges as high as 4000 V readily accumulate on the human body and test equipment and can discharge without detection. Although this product features proprietary ESD protection circuitry, permanent damage may occur on devices subjected to high energy electrostatic discharges. Therefore, proper ESD precautions are recommended to avoid performancedegradation or loss of functionality.Preliminary Technical DataAD2S1205Rev. PrB | Page 7 of 25PIN CONFIGURATION AND FUNCTION DESCRIPTIONS04406-0-002DV DD 1RD 2CS 3SAMPLE 4RDVEL 5SOE 6DB11/SO 7DB10/SCLK 8DB99DB810DB711RESET 33FS232FS131LOT 30DOS 29DIR 28NM 27B 26A25CPO 24DGND23D B 612D B 513D B 414D B 315D G N D16D V D D17D B 218D B 119D B 020X T A L OU T21C L K I N22R E F O U T44R E F B Y P43A G N D42C o s41C o s L O40A V D D39S i n L O38S i n37A G N D36E X C35E X C34AD2S1205TOP VIEW (Not to Scale)Figure 2. Pin Configuration44-Lead Low Profile Quad Flat Package [LQFP] (ST-44)AD2S1205Preliminary Technical DataRev.PrB | Page 8 of 25RESOLVER FORMAT SIGNALS04406-0-003V b = V s × Sin(ϖt)× Sin(θ)(A) CLASSICAL RESOLVERV b = V s × Sin(ϖt)× Sin(θ)(B) VARIABLE RELUCTANCE RESOLVERs × Sin(ϖt)× Cos(θ)Figure 3. Classical Resolver vs. Variable Reluctance ResolverA resolver is a rotating transformer typically with a primary winding on the rotor and two secondary windings on the stator. In the case of a variable reluctance resolver, there are no wind-ings on the rotor as shown in Figure 3. The primary winding is on the stator as well as the secondary windings, but the saliency in the rotor design provides the sinusoidal variation in the secondary coupling with the angular position. Either way, the resolver output voltages (S3–S1, S2–S4) will have the same equations as shown in Equation 1.AmplitudeExcitation Rotor E FrequencyExcitation Rotor t Sin AngleShaft Cos t Sin E S S Sin t Sin E S S ===×=−×=−0004213ωθθωθω Equation 1.The stator windings are displaced mechanically by 90° (see Figure 3). The primary winding is excited with an ac reference. The amplitude of subsequent coupling onto the stator secon-dary windings is a function of the position of the rotor (shaft) relative to the stator. The resolver, therefore, produces two output voltages (S3–S1, S2–S4) modulated by the Sine and Cosine of shaft angle. Resolver format signals refer to the signals derived from the output of a resolver as shown in Equation 1. Figure 4 illustrates the output format.04406-0-0040°90°180°θ270°360°Figure 4. Electrical Resolver RepresentationPreliminary Technical DataAD2S1205Rev. PrB | Page 9 of 25PRINCIPLE OF OPERATIONThe AD2S1205 operates on a Type II tracking closed-loop principle. The output continually tracks the position of the resolver without the need for external convert and wait states. As the resolver moves through a position equivalent to the least significant bit weighting, the output is updated by one LSB. The converter tracks the shaft angle θ by producing an output angle ϕ that is fed back and compared to the input angle θ, and the resulting error between the two is driven towards 0 when the converter is correctly tracking the input angle. To measure the error, S3–S1 is multiplied by Cosϕ and S2–S4 is multiplied by Sinϕ to give423100S to S Sin Cos t Sin E S to S Cos Sin t Sin E φθωφθω××The difference is taken, giving)(0φθ−φθ×ωSin Cos Cos Sin t Sin EEquation 2.This signal is demodulated using the internally generated synthetic reference, yielding)(0φθφθSin Cos Cos Sin E −Equation 3.Equation 3 is equivalent to E 0 Sin (θ − ϕ), which isapproximately equal to E 0 (θ − ϕ) for small values of θ − ϕ, where θ − ϕ = angular error.The value E 0 (θ − ϕ) is the difference between the angular error of the rotor and the converter’s digital angle output.A phase-sensitive demodulator, integrators, and a compensation filter form a closed-loop system that seeks to null the error signal. When this is accomplished, ϕ equals the resolver angle θ within the rated accuracy of the converter. A Type II tracking loop is used so that constant velocity inputs can be tracked without inherent error.For more information about the operation of the converter, see the Circuit Dynamics section.FAULT DETECTION CIRCUITThe AD2S1205 fault detection circuit will detect loss of resolver signals, out of range input signals, input signal mismatch, or loss of position tracking. In these cases, the position indicated by the AD2S1205 may differ significantly from the actual shaft position of the resolver.Monitor SignalThe AD2S1205 generates a monitor signal by comparing the angle in the position register to the incoming Sin and Cos signals from the resolver. The monitor signal is created in a similar fashion to the error signal described in the Principle of Operation section. The incoming signals Sin θ and Cos θ are multiplied by the Sin and Cos of the output angle, respectively, and then added together as shown below:φ×θ×+φθ×=Cos Cos A Sin x Sin A Monitor 21Equation 4.Where A1 is the amplitude of the incoming Sin signal (A1 × Sin θ), A2 is the amplitude of the incoming Cos signal (A2 × Cos θ), θ is the resolver angle, and ϕ is the angle stored in the position register. Note that Equation 4 is shown after demodula-tion, with the carrier signal Sin ωt removed. Also note that for matched input signal (i.e., no-fault condition), A1 = A2. When A1 = A2 and the converter is tracking (θ = ϕ), themonitor signal output has a constant magnitude of A1 (Monitor = A1 × (Sin 2 θ + Cos 2 θ) = A1), independent of shaft angle. When A1 ≠ A2, the monitor signal magnitude varies between A1 and A2 at twice the rate of shaft rotation. The monitor signal is used as described in the following sections to detect degradation or loss of input signals.Loss of Signal DetectionLoss of signal (LOS) is detected when either resolver input (Sin or Cos) falls below the specified LOS Sin/Cos threshold bycomparing the monitor signal to a fixed minimum value. LOS is indicated by both DOS and LOT latching as logic low outputs. The DOS and LOT pins are reset to the no fault state by a rising edge of SAMPLE . The LOS condition has priority over both the DOS and LOT conditions, as shown in Table 4. LOS is indicated within 45° of angular output error worst case.AD2S1205Preliminary Technical DataRev.PrB | Page 10 of 25Signal Degradation DetectionDegradation of signal (DOS) is detected when either resolver input (Sin or Cos) exceeds the specified DOS Sin/Cos threshold by comparing the monitor signal to a fixed maximum value. DOS is also detected when the amplitude of the input signals Sin and Cos mismatch by more than the specified DOS Sin/ Cos mismatch by continuously storing the minimum andmaximum magnitude of the monitor signal in internal registers, and calculating the difference between the minimum andmaximum. DOS is indicated by a logic low on the DOS pin, and is not latched when the input signals exceed the maximum input level. When DOS is indicated due to mismatched signals, the output is latched low until a rising edge of SAMPLE resets the stored minimum and maximum values. The DOS condition has priority over the LOT condition, as shown in Table 4. DOS is indicated within 30° of angular output error worst case.Loss of Position Tracking DetectionLoss of tracking (LOT) is detected for three separate conditions: • When the internal error signal of the AD2S1205 has exceeded 5°• When the input signal exceeds the maximum tracking rate of 60,000 rpm (1,000 rps)•When the internal position (at the position integrator) differs from the external position (at the position register) by more than 5°LOT is indicated by a logic low on the LOT pin, and is not latched. LOT has a 4° hysteresis, and is not cleared until the internal error signal or internal/external position mismatch is less than 1°. When the maximum tracking rate is exceeded, LOT is cleared when both the velocity is less than 1,000 rps and the internal/external position mismatch is less than 1°. LOT can be indicated for step changes in position (such as after a RESET signal is applied to the AD2S1205), or for accelerations >~85,000 rps 2. LOT is useful as a built-in test (BIT) that the tracking converter is functioning properly. The LOT condition has lower priority than both the DOS and LOS conditions as shown in Table 4. The LOT and DOS conditions cannot be indicated at the same time.Table 4. Fault Detection DecodingCondition DOS LOT Priority Loss of Signal0 0 1 Degradation of Signal 0 1 2 Loss of Tracking 1 0 3 No Fault1 1Responding to a Fault ConditionIf any fault condition (LOS, DOS, or LOT) is indicated by the AD2S1205, the output data must be presumed to be invalid. This means that even if a RESET or SAMPLE pulse releases the fault condition, the output data may be corrupted, even though a fault may not be immediately indicated after the RESET / SAMPLE event. As discussed earlier, there are some fault conditions with inherent latency. If the device fault is cleared, there could be some latency in the resolver’s mechanical position before the fault condition is re-indicated.When a fault is indicated, all output pins will still provide data, although the data may or may not be valid. The fault condition will not force the parallel, serial, or encoder outputs to a known state.Response to specific fault conditions is a system-levelrequirement. The fault outputs of the AD2S1205 indicate that the device has sensed a potential problem with either the internal or external signals of the AD2S1205. It is the responsibility of the system designer to implement theappropriate fault-handling schemes within the control hardware and/or algorithm of a given application based on the indicated fault(s) and the velocity or position data provided by the AD2S1205.False Null ConditionResolver-to-digital converters that employ Type II tracking loops based on the error equation (Equation 3) presented in the Principle of Operation section can suffer from a condition known as “false null.” This condition is caused by a metastable solution to the error equation when θ − ϕ = 180°. The AD2S1205 is not susceptible to this condition because its hysteresis is implemented externally to the tracking loop.Because of the loop architecture chosen for the AD2S1205, the internal error signal always has some movement (1 LSB per clock cycle), and so, in a metastable state, the converter will always move to an unstable condition within one clock cycle, causing the tracking loop to respond to the false null condition as if it were a 180° step change in input position (the response time is the same as specified in Dynamic Performance section of Table 1). Therefore, it is impossible to enter the metastable condition any time after the startup sequence as long as the resolver signals are valid.Preliminary Technical DataAD2S1205Rev. PrB | Page 11 of 25CONNECTING THE CONVERTERRefer to Figure 5. Ground should be connected to the AGND pin and DGND pin. Positive power supply V DD = +5 V dc ± 5% should be connected to the AV DD pin and DV DD pin. Typical values for the decoupling capacitors are 10 nF and 4.7 μF, respectively. These capacitors should be placed as close to the device pins as possible, and should be connected to both AV DD and DV DD . If desired, the reference oscillator frequency can be changed from the nominal value of 10 kHz using FS1 and FS2. Typical values for the oscillator decoupling capacitors are 20 pF. Typical values for the reference decoupling capacitors are 10 μF and 0.01 μF, respectively.Figure 5. Connecting the AD2S1205 to a ResolverThe gain of the buffer depends on the type of resolver used. Since the specified excitation output amplitudes are matched to the specified Sin/Cos input amplitudes, the gain of the buffer is determined by the attenuation of the resolver.In this recommended configuration, the converter introduces a V REF /2 offset in the Sin, Cos signals coming from the resolver. Of course, the SinLO and CosLO signals may be connected to a different potential relative to ground, as long as the Sin and Cos signals respect the recommended specifications. Note that since the EXC/EXC outputs are differential, there is an inherent gain of 2×.For example, if the primary to secondary turns ratio is 2:1, the buffer will have unity gain. Likewise, if the turns ratio is 5:1, the gain of the buffer should be 2.5×. Figure 6 suggests a buffer circuit. The gain of the circuit is)1/2(R R Gain −=and ⎟⎠⎞⎜⎝⎛×−⎟⎠⎞⎜⎝⎛⎟⎠⎞⎜⎝⎛+×=IN REF OUT V R R R R V V 12121V REF is set so that V OUT is always a positive value, eliminating theneed for a negative supply.Figure 6. Buffer CircuitSeparate screened twisted cable pairs are recommended for analog inputs Sin/SinLO and Cos/CosLO. The screens should terminate to REFOUT. To achieve the dynamic performance specified, an 8.192 MHz crystal must be used.AD2S1205Preliminary Technical DataRev.PrB | Page 12 of 25ABSOLUTE POSITION AND VELOCITY OUTPUTThe angular position and angular velocity are represented by binary data and can be extracted either via a 12-bit parallel interface or a 3-wire serial interface that operates at clock rates up to 25 MHz. The chip select pin, CS , must be held low to enable the device. Angular position and velocity can be selected using a dedicated polarity input, RDVEL .SOE InputThe serial output enable pin, SOE , is held high to enable the parallel interface. The SOE pin is held low to enable the serial interface, which places pins (DB0–DB9) in the high impedance state, while DB11 is the serial output (SO), and DB10 is the serial clock input (SCLK).Data FormatThe digital angle signal represents the absolute position of the resolver shaft as a 12-bit unsigned binary word. The digital velocity signal is a 12-bit twos complement word, whichrepresents the velocity of the resolver shaft rotating in either a clockwise or a counterclockwise direction.Finally, the RD input is used to read the data from the output register and to enable the output buffer. The timingrequirements for the read cycle are illustrated in Figure 7.SAMPLE InputData is transferred from the position and velocity integrators respectively to the position and velocity registers following a high to low transition of the SAMPLE signal. This pin must be held low for at least t 1 ns to guarantee correct latching of the data. RD should not be pulled low before this time. Also, a rising edge of SAMPLE resets the internal registers that contain the minimum and maximum magnitude of the monitor signal.PARALLEL INTERFACEThe angular position and angular velocity are available on the AD2S1205 in two 12-bit registers, which can be accessed via the 12-bit parallel port. The parallel interface is selected holding the SOE pin high. Data is transferred from the velocity and position integrators, respectively, to the position and velocity registers following a high-to-low transition on the SAMPLE pin. The RDVEL polarity pin selects which register from the position or the velocity registers is transferred to the output register. The CS pin must be held low to transfer the selected data register to the output register. Finally, the RD input is used to read the data from the output register and to enable the output buffer. The timing requirements for the read cycle are shown in Figure 7.SAMPLE InputData is transferred from the position and velocity integrators, respectively, to the position and velocity registers following a high-to-low transition on the SAMPLE signal. This pin must be held low for at least t 1 ns to guarantee correct latching of the data. RD should not be pulled low before this time since data would not be ready. The converter will continue to operate during the read process. Also, a rising edge of SAMPLE resets the internal registers that contain the minimum and maximum magnitude of the monitor signal.CS InputThe device will be enabled when CS is held low.RDVEL InputRDVEL input is used to select between the angular position and velocity registers as shown in Figure 7. RDVEL is held high for angular position and low for angular velocity. The RDVEL pin must be set (stable) at least t 4 ns before the RD pin is pulled low.RD InputThe 12-bit data bus lines are normally in a high impedance state. The output buffer is enabled when CS and RD are held low. A falling edge of the RD signal transfers data to the output buffer. The selected data is made available to the bus to be read within t 6 ns of the RD pin going low. The data pins will return to high impedance state when the RD returns to high state, within t 7 ns. If the user is reading data continuously, RD can be reapplied a minimum of t 3 ns after it was released.Preliminary Technical Data AD2S1205Figure 7. Parallel Port Read TimingRev. PrB | Page 13 of 25AD2S1205Preliminary Technical DataRev.PrB | Page 14 of 25SERIAL INTERFACEThe angular position and angular velocity are available on the AD2S1205 in two 12-bit registers. These registers can be accessed via a 3-wire serial interface, SO, RD , and SCLK, that operates at clock rates up to 25 MHz and is compatible with SPI and DSP interface standards. The serial interface is selected by holding low the SOE pin. Data from the position and velocity integrators are first transferred to the position and velocity registers, using the SAMPLE pin. The RDVEL polarity pin selects which register from the position or the velocity registers is transferred to the output register. The CS pin must be held low to transfer the selected data register to the output register. Finally, the RD input is used to read the data that will be clocked out of the output register and will be available on the serial output pin, SO. When the serial interface is selected, DB11 is used as the serial output pin, SO, and DB10 is used as the serial clock input, SCLK, while pins DB0–DB9 are placed in the high impedance state. The timing requirements for the read cycle are described in Figure 8.SO OutputThe output shift register is 16-bit wide. Data is shifted out of the device as a 16-bit word under the control of the serial clock input, SCLK. The timing diagram for this operation is shown in Figure 8. The 16-bit word consists of 12 bits of angular data (position or velocity depending on RDVEL input), one RDVEL status bit and three status bits, a parity bit, degradation of signal bit, and loss of tracking bit. Data is read out MSB first (bit 15) on the SO pin. Bit 15 through bit 4 correspond to the angular information. The angular position data format is unsigned binary, with all zeros corresponding to 0 degrees and all ones corresponding to 360 degrees –l LSB. The angular velocity data format instead is twos complement binary, with the MSB representing the rotation direction. Bit 3 is the RDVEL status bit, 1 indicating position and 0 indicating velocity. Bit 2 is DOS, the degradation of signal flag (refer to the Fault Detection Circuit section). Bit 1 is LOT, the loss of tracking flag (refer to the Fault Detection Circuit section). Bit 0 is PAR, the parity bit: both position and velocity data are odd parity format; the data read out will always contain an odd number of logic highs (1s). SAMPLE InputData is transferred from the position and velocity integrators, respectively, to the position and velocity registers following a high-to-low transition on the SAMPLE signal. This pin must be held low for at least t 1 ns to guarantee correct latching of the data. RD should not be pulled low before this time since data would not be ready. The converter will continue to operate during the read process.CS InputThe device will be enabled when CS is held low.RD InputThe 12-bit data bus lines are normally in a high impedance state. The output buffer is enabled when CS and RD are held low. The RD input is an edge-triggered input that acts as frame synchronization signal and output enable. A falling edge of the RD signal transfers data to the output buffer and data will be available on the serial output pin, SO. RD must be held low for t 9 before the data is valid on the outputs. After RD goes low, the serial data will be clocked out of the SO pin on the falling edges of the SCLK (after a minimum of t 10 ns): the MSB will be already available at the SO pin on the very first falling edge of the SCLK. Each other bit of the data word will be shifted out on the rising edge of SCLK and will be available at the SO pin on the falling edge of SCLK for the next 15 clock pulses.The high-to-low transition of RD must happen during the high time of the SCLK to avoid MSB being shifted on the first rising edge of the SCLK and lost. RD may rise high after the falling edge of the last bit transmitted. Subsequent negative edges greater than the defined word length will clock zeros from the data output if RD remains in a low state. If the user is reading data continuously, RD can be reapplied a minimum of t 5 ns after it is released.RDVEL InputRDVEL input is used to select between the angular position and velocity registers. RDVEL is held high for angular position and low for angular velocity. The RDVEL pin must be set (stable) at least t 4 ns before the RD pin is pulled low.。
SC2415中文资料

Models Available Strobe Models White RedSC2415W SC2415 SC241575W SC241575SC2430W SC2430SC2475W SC2475SC2495W SC2495 SC24115W SC24115SC24177W SC24177Horn/Strobe Models White RedPC2415W PC2415 PC241575W PC241575PC2430W PC2430PC2475W PC2475PC2495W PC2495 PC24115W PC24115PC24177WPC24177Accessory Mounting PlatesWhite Red BBSCW BBSCSystem Sensor’s SpectrAlert ® ceiling mount series strobes and horn/strobes offer afresh approach to addressing the unique needs for ceiling mount applications.Technology. Like the original SpectrAlert, the SpectrAlert ceiling mount series offer significant current draw reductions over other ceiling mount strobes and horn/strobes.Installation. SpectrAlert’s compact design also offers installation savings. Thestrobe and horn/strobe models mount to a 4˝×4˝×11⁄2˝ back box, and take up little room in the back box, making connections easier. And with SpectrAlert’s round shape, it is not necessary to align the back box with the room’s walls. SpectrAlert always lines up.Flexibility. SpectrAlert ceiling mount strobes and horn/strobes are available inseven different candelas, including 177 candela for sleeping areas. The horn/strobe’s tones are field-selectable through the use of a three position switch located on the back of the unit. Selections include electromechanical and 3 KHz tones, temporal and non-temporal patterns, and high and low volume.Aesthetics. SpectrAlert ceiling strobes and horn/strobes offer a design that is sensi-tive to the aesthetic demands of ceiling mount applications. The round shape main-tains a low profile appearance, similar to that of a smoke detector and provides clearly visible “FIRE” identification from all angles.Lower current drawAvailable in 15, 15/75, 30, 75, 95, 115,and 177 candelaHorn/strobe models include a threeposition switch for field-selecting horn tones:- Electromechanical/3KHz - Temporal/Non-temporal - High/Low dBA outputCeiling-specific shape, profile, and aestheticsSynchronizable with MDL Sync•Circuit ™moduleMounts to 4˝× 4˝× 11⁄2˝ back box Round shape offers greater placement flexibilityProduct OverviewSC241575W PC2475WS40117135-1209:20461-00-E 144-00-E元器件交易网General Specifications SpectrAlert Mounting DiagramsStrobe or Horn/Strobe with Mounting PlateStrobe or Horn/Strobe with Accessory Back Box SkirtStrobeStrobe shall be a System Sensor SpectrAlert Model _________ listed to UL 1971 and be approved for fire protective ser-vice where ceiling mount strobes are permitted. The strobe shall be wired as a primary signaling notification appliance and shall flash at 1Hz over the strobe’s entire operating range. The strobe light shall consist of a xenon flash tube and associated lens/reflector system.Horn/Strobe CombinationHorn/strobe shall be a System Sensor SpectrAlert Model _________ listed to UL 1971 and UL 464 and be approved for fire protective service where ceiling mount horn/strobes are permitted. The horn/strobe shall be wired as a primary signaling notification appliance and shall flash at 1Hz over its entire operating range. The strobe light shall consist of a xenon flash tube and associated lens/reflector system. The horn shall have two tone options, two audibility options, and the option to switch between a temporal and a non-temporal continuous pattern. These options shall be selected by a multi-position switch. Strobes shall be powered independently of the sounder with the removal of factory installed jump-er wires. The horn on horn/strobe models shall operate on a coded or non-coded power supply.Note: The strobes must be powered continuously for the horn to operate.BBSCW4 × 4 × 21/8˝Table 1-A: SpectrAlert Strobe UL Max. Current Draw (mA RMS)Strobe Setting 16-33V FWR Operating Current – Strobe (mA RMS)16-33V DC Operating Current – Strobe (mA RMS)15686415/757778301071137519720595239274115298325177399489Table 1-B: Horn UL Max. Current Draw Measurements (mA RMS)16-33V (DC)16-33V (FWR)TemporalLow Volume Electromechanical 23233000 Hz Interrupted 3323High VolumeElectromechanical 53443000 Hz Interrupted 5740Non-TemporalLow Volume Electromechanical 37293000 Hz Interrupted 3233High VolumeElectromechanical 49493000 Hz Interrupted5658Notes:1. Full Wave Rectified (FWR) voltage is a non-regulated, time-varying power source that is used on some power supply and panel outputs.2. The MDL causes a one-volt voltage drop in the notification appliance circuit.Table 1-C: 24V DC Horn/Strobe UL Max. Current Draw Measurements (mA RMS)TemporalNon-TemporalLow VolumeHigh VolumeLow VolumeHigh VolumeCandela SettingElectromechanical3000 Hz Electromechanical3000 Hz Electromechanical3000 Hz Electromechanical3000 Hz 15737376787575818615/758989919289909698301261251281281251251311347522522222222221921922122295272270271271266265269270115297297296296291290292293177512504501496491493491496Explanation of Published Voltage, Current, and SPL SpecificationsDuring May 2004, UL also changed the way they list the voltage range of a device. All 12V products will be listed between 8 – 17.5V and all 24V products will be listed between 16 – 33V . Those devices are considered “regulat-ed”. Any product that does not operate within these ranges will be listed as a “special application” with its operating voltage specified on the device.Notes1. C urrent draw for strobe-only products is shown in Table 1-A.2. 24VDC 2-wire horn/strobe current draw is shown in Table 1-C.3.C urrent draw for other horn/strobe power supplies can be calculated by adding the strobe current in Table 1-A to the horn current in Table 1-B from the chosen settings.In May 2004 Underwriters Laboratories changed standard UL 1971 to require that operating current measuremments are made using RMS (root mean square) instead of peak or average values. RMS measurements more accurately predict the power consumption of a device since they take into account the entire current draw profile including surge, repetitive surge, and peak values. The published RMS cur-rent is the maximum operating current of that device within its operating voltage range. This current maximum may or may not occur at the endpoints of the voltage range.Similarly, UL tests the audibility of devices in accordance with UL 464 by measuring them across the operating volt-age range to determine the minimum sound pressure level produced at any particular setting.© 2005 System Sensor. The company reserves the right to change product specifications without notice. A05-1025-008•9/05•#1530SpectrAlert DimensionsSpectrAlert Ceiling Mount StrobeSpectrAlert Ceiling Mount Horn/Strobe6.8˝Ordering InformationModel No.DescriptionSC2415Ceiling-mount strobe, 24 volt, 15 candela, red SC2415W Ceiling-mount strobe, 24 volt, 15 candela, white SC241575Ceiling-mount strobe, 24 volt, 15/75 candela, red SC241575W Ceiling-mount strobe, 24 volt, 15/75 candela, white SC2430Ceiling-mount strobe, 24 volt, 30 candela, red SC2430W Ceiling-mount strobe, 24 volt, 30 candela, white SC2475Ceiling-mount strobe, 24 volt, 75 candela, red SC2475W Ceiling-mount strobe, 24 volt, 75 candela, white SC2495Ceiling-mount strobe, 24 volt, 95 candela, red SC2495W Ceiling-mount strobe, 24 volt, 95 candela, white SC24115Ceiling-mount strobe, 24 volt, 115 candela, red SC24115W Ceiling-mount strobe, 24 volt, 115 candela, white SC24177Ceiling-mount strobe, 24 volt, 177 candela, red SC24177W Ceiling-mount strobe, 24 volt, 177 candela, white PC2415Ceiling-mount horn/strobe, 24 volt, 15 candela, red PC2415W Ceiling-mount horn/strobe, 24 volt, 15 candela, white PC241575Ceiling-mount horn/strobe, 24 volt, 15/75 candela, redPC241575W Ceiling-mount horn/strobe, 24 volt, 15/75 candela, whitePC2430Ceiling-mount horn/strobe, 24 volt, 30 candela, red PC2430W Ceiling-mount horn/strobe, 24 volt, 30 candela, white PC2475Ceiling-mount horn/strobe, 24 volt, 75 candela, red PC2475W Ceiling-mount horn/strobe, 24 volt, 75 candela, white PC2495Ceiling-mount horn/strobe, 24 volt, 95 candela, red PC2495W Ceiling-mount horn/strobe, 24 volt, 95 candela, white PC24115Ceiling-mount horn/strobe, 24 volt, 115 candela, red PC24115W Ceiling-mount horn/strobe, 24 volt, 115 candela, whitePC24177Ceiling-mount horn/strobe, 24 volt, 177 candela, red PC24177WCeiling-mount horn/strobe, 24 volt, 177 candela, whiteAccessories MDL Sync•Circuit™ Module, red MDLW Sync•Circuit™ Module, white BBSC Surface-mount back box skirt, red BBSCWSurface-mount back box skirt, whiteSystem Sensor Sales and ServiceSystem Sensor Headquarters 3825 Ohio Avenue St. Charles, IL 60174 Ph: 800/SENSOR2 Fx: 630/377-6495 System Sensor Canada Ph: 905.812.0767 Fx: 905.812.0771System Sensor Europe Ph: 44.1403.276500 Fx: 44.1403.276501System Sensor in China Ph: 86.29.8832.0119 Fx: 86.29.8832.5119System Sensor in Singapore Ph: 65.6273.2230 Fx: 65.6273.2610System Sensor – Far East Ph: 85.22.191.9003 Fx: 85.22.736.6580System Sensor – Australia Ph: 613.54.281.142 Fx: 613.54.281.172System Sensor – IndiaPh: 91.124.237.1770 x.2700Fx: 91.124.237.3118System Sensor – Russia Ph: 70.95.937.7982Fx: 70.95.937.7983Horn Sound Measurements (dBA)Selectable Horn Tones16-33V TemporalLow VolumeElectromechanical 753000 Hz Interrupted75High VolumeElectromechanical 803000 Hz Interrupted81Non-TemporalLow VolumeElectromechanical 793000 Hz Interrupted79High VolumeElectromechanical 843000 Hz Interrupted86。
SC1205K1的规格书
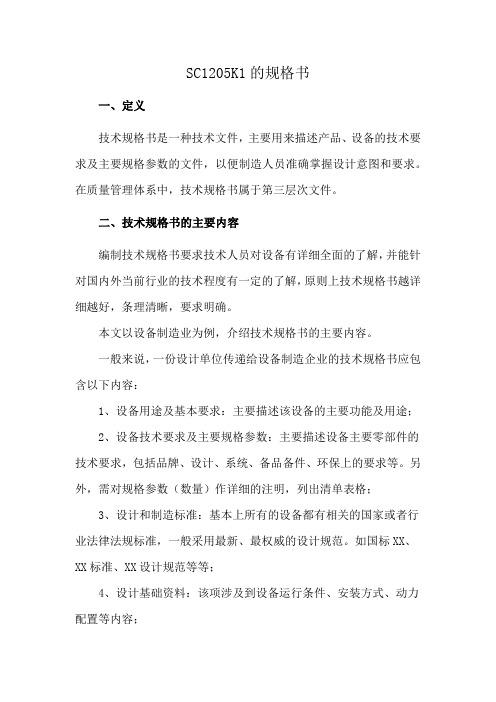
SC1205K1的规格书一、定义技术规格书是一种技术文件,主要用来描述产品、设备的技术要求及主要规格参数的文件,以便制造人员准确掌握设计意图和要求。
在质量管理体系中,技术规格书属于第三层次文件。
二、技术规格书的主要内容编制技术规格书要求技术人员对设备有详细全面的了解,并能针对国内外当前行业的技术程度有一定的了解,原则上技术规格书越详细越好,条理清晰,要求明确。
本文以设备制造业为例,介绍技术规格书的主要内容。
一般来说,一份设计单位传递给设备制造企业的技术规格书应包含以下内容:1、设备用途及基本要求:主要描述该设备的主要功能及用途;2、设备技术要求及主要规格参数:主要描述设备主要零部件的技术要求,包括品牌、设计、系统、备品备件、环保上的要求等。
另外,需对规格参数(数量)作详细的注明,列出清单表格;3、设计和制造标准:基本上所有的设备都有相关的国家或者行业法律法规标准,一般采用最新、最权威的设计规范。
如国标XX、XX标准、XX设计规范等等;4、设计基础资料:该项涉及到设备运行条件、安装方式、动力配置等内容;5、供货的主要要求、内容:该项内容可包括设备的几大系统控制等功能、设备品质保证、售后服务、验收标准及供货日期等。
三、技术规格书的用途一份内容完善的技术规格书,可以有效传递设计意图、反映产品制造要求,让制造人员充分掌握顾客要求,制造出满足法规标准和顾客要求的产品。
同时,技术规格书还对产品的运输、验收等质量相关内容提出要求,有助于提高产品的总体质量,确保完全满足顾客需求。
四、技术规格书与技术协议的区别有的朋友认为技术协议可以代替技术规格书,或者分不清这两份文件内容和性质的区别。
我们来仔细分析一下:1、编制时间不一样。
技术协议本质上是带有合同性质的文件,也就是说,是招标后编制的。
而技术规格书需要在招标前编制完成,并在招标过程中修改确认。
2、范围不一样。
技术规格书仅仅规定产品的规格型号、参数、依据的法规标准等;而技术协议包括的内容更广,如制造工艺、知识产权归属、培训和售后服务等。
- 1、下载文档前请自行甄别文档内容的完整性,平台不提供额外的编辑、内容补充、找答案等附加服务。
- 2、"仅部分预览"的文档,不可在线预览部分如存在完整性等问题,可反馈申请退款(可完整预览的文档不适用该条件!)。
- 3、如文档侵犯您的权益,请联系客服反馈,我们会尽快为您处理(人工客服工作时间:9:00-18:30)。
Symbol
VMAX5V VMAXBST-PGND VMAXBST-DRN VMAXDRN-PGN VMAXOVP_S-PGND
CO Pd
பைடு நூலகம்
Thermal Resistance Junction to Case θϑΧ
Thermal Resistance Junction to
Ambient
θJA
Operating Temperature Range Storage Temperature Range Lead Temperature (Soldering) 10 sec
PIN CONFIGURATION
FEATURES
• Fast rise and fall times (15ns typical with 3000pf
load)
• 2Amp peak drive current • 14ns max Propagation delay (BG going low) • Adaptive Non-overlapping Gate Drives provide
DESCRIPTION
The SC1205 is a cost effective Dual MOSFET Driver designed for switching High and Low side Power MOSFETs. Each driver is capable of driving a 3000pF load in 20ns rise/fall time and has a 20ns max propagation delay from input transition to the gate of the power FET’s. An internal Overlap Protection Circuit prevents shoot-through from Vin to GND in the main switching and synchronous MOSFET’s. The Overlap Protection circuit ensures the Bottom FET does not turn on until the Top FET source has reached a voltage low enough to prevent cross-conduction.
The high current drive capability (2A peak) allows fast switching, thus reducing switching losses at high (1MHz) PWM frequencies. The high voltage CMOS process allows operation from 5-25 Volts at top MOSFET drain, thus making SC1205 suitable for battery powered applications. Connecting Enable pin (EN) to logic low shuts down both drives and reduces operating current to less than 10uA.
4.15
5
1
UNDER-VOLTAGE LOCKOUT
Start Threshold Hysteresis Logic Active Threshold
VSTART VhysUVLO
VACT
4.2
4.4
0.05
MAX UNITS
6.0
V
ma
10
µA
4.6
V
V
1.5
V
© 1999 SEMTECH CORP.
VV_5 = 4.6V, VBG = 4V (src), or VLOWDR = 0.5V (sink)
1.0
Ω
© 1999 SEMTECH CORP.
3 652 MITCHELL ROAD NEWBURY PARK CA 91320
元器件交易网
HIGH SPEED SYNCHRONOUS POWER MOSFET DRIVER
An Under-Voltage-Lock-Out circuit is included to guarantee that both driver outputs are low when the 5V logic level is less than or equal to 4.4V (typ) at supply ramp up (4.35V at supply ramp down). An Internal temperature sensor shuts down all drives in the event of overtemperature. SC1205 is fabricated utilizing CMOS technology for low quiescent current. The SC1205 is offered in a standard SO-8 package.
PACKAGE TEMP. RANGE (TJ)
SO-8
0 - 125°C
Note: (1) Add suffix ‘TR’ for tape and reel.
BLOCK DIAGRAM
Top View
(SO-8) © 1999 SEMTECH CORP.
1 652 MITCHELL ROAD NEWBURY PARK CA 91320
CI = 3nF, VV_5 = 4.6V, TJ = 125°C
CI = 3nF, VV_5 = 4.6V, TJ = 125°C
CI = 3nF, VV_5 = 4.6V, TJ = 125°C, DRN < 1V
TOTP THYST
165
°C
10
°C
Peak Output Current Output Resistance
LOW-SIDE DRIVER
IPKH
2
A
RsrcTG
duty cycle < 2%, tpw < 100µs,
1
Ω
TJ = 125°C, VBST - VDRN = 4.5V,
RsinkTG
PARAMETER
SYMBOL
CONDITIONS
MIN TYP MAX UNITS
CO
High Level Input Voltage
VIH
Low Level Input Voltage
VIL
THERMAL SHUTDOWN
2.0
V
0.8
V
Over Temperature Trip Point Hysteresis HIGH-SIDE DRIVER
TJ TSTG TLEAD
NOTE:
(1) Specification refers to application circuit in Figure 1.
Conditions
Tamb = 25°C, TJ = 125°C Tcase = 25°C, TJ = 125°C
Maximum 7 30 7 25 10
of small inductors and low cost caps in place of electrolytics
• Portable computers • Battery powered applications
ORDERING INFORMATION
DEVICE(1) SC1205CS
元器件交易网
HIGH SPEED SYNCHRONOUS POWER MOSFET DRIVER
SC1205
PRELIMINARY - December 7, 1999
ABSOLUTE MAXIMUM RATINGS
Parameter VCC Supply Voltage BST to PGND BST to DRN DRN to PGND OVP_S to PGND Input pin Continuous Power Dissipation
trTG, tfTG tpdhTG tpdlTG
CI = 3nF, VBST - VDRN = 4.6V, TJ = 125°C
CI = 3nF, VBST - VDRN = 4.6V, TJ = 125°C
CI = 3nF, VBST - VDRN = 4.6V, TJ = 125°C
CI = 3nF, VBST - VDRN = 4.6V, TJ = 125°C
APPLICATIONS
• High Density sunchronous power supplies • Motor Drives/Class-D amps/Half bridge drivers • High frequency (to 1.2 MHz) operation allows use
2 652 MITCHELL ROAD NEWBURY PARK CA 91320
元器件交易网
HIGH SPEED SYNCHRONOUS POWER MOSFET DRIVER
SC1205
PRELIMINARY - December 7, 1999
ELECTRICAL CHARACTERISTICS (DC OPERATING SPECIFICATIONS) Cont.
元器件交易网
HIGH SPEED SYNCHRONOUS POWER MOSFET DRIVER
SC1205
PRELIMINARY - December 7, 1999
TEL:805-498-2111 FAX:805-498-3804 WEB: