钣金车身工艺-铸造-NC数模checklist流转单A1-2006
钣金模具课程设计

西安航空学院课程设计说明书(论文) 题目冲裁复合模课程名称钣金课程设计学院(部)飞行器学院专业飞行器制造工程班级学生姓名学号设计地点西安航空学院指导教师设计起止时间:2016年12月14日至2016年12月24日目录课程设计任务书 ............................................................................................................................... 4 一.原始数据 ................................................................................................................................... 7 二.工艺分析 ................................................................................................................................... 7 三.冲裁方案的确定 .. (7)①方案种类 ............................................................................................................................... 7 ②方案的比较 ........................................................................................................................... 8 ③方案的确定 ........................................................................................................................... 8 四.模具结构形式的确定 ............................................................................................................... 8 五.工艺尺寸计算 (8)①排样设计 (8)a. 排样方法的确定 ......................................................................................................... 8 b. 确定搭边值 ................................................................................................................. 9 c. 确定条料步距 ............................................................................................................. 9 d. 条料的利用率 ............................................................................................................. 9 e. 画出排样图 ................................................................................................................. 9 ②冲裁力的计算 (10)a. F 确定 (10)b. 卸料力X F .................................................................................................................. 10 c. 推件力T F ................................................................................................................... 10 d. 顶件力D F (10)③压力机公称压力的确定 ..................................................................................................... 11 ④冲裁压力中心的确定 ......................................................................................................... 11 ⑤刃口尺寸的计算 .. (11)a. 加工方法的确定。
钣金工艺流程表
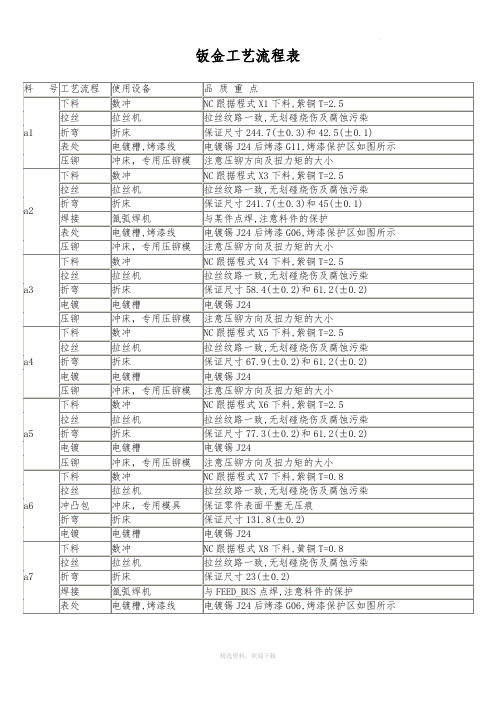
钣金工艺流程表钣金基础介绍(一),钣金业的发展非常迅速,所以应该了解一下钣金加工的基本常识.一.材料的选定.钣金加工一般用到的材料:有冷轧板(SPCC)、镀锌板(SECC)、铜板、铝板、不锈钢板、铝材等.其作用各不相同.至于如何选用,一般需从其用途及成本上来考虑.1.冷轧板.简称SPCC,用于表面处理是电镀五彩锌或烤漆件使用.2.镀锌板.简称SECC,用于表面处理是烤漆件使用.在无特别要求下,一般选用SPCC,可减少成本.3.铜板.一般用于镀镍或镀铬件使用,有时不作处理.跟据客户要求而定.4.铝板.一般用于表面处理是铬酸盐或氧化件使用.5.不锈钢板.分镜面不锈钢和雾面不锈钢,它不需要做任何处理.6.铝型材.一般用于表面处理是铬酸盐或氧化件使用.主要起支撑或连接作用,大量用于各种插箱中.二.钣金加工的工艺流程.对于任何一个钣金件来说,它都有一定的加工过程,也就是所谓的工艺流程.随着钣金件结构的差异,工艺流程可能各不相同,但总的不超过以下几点.1.设计并绘出其钣金件的零件图,又叫三视图.其作用是用图纸方式将其钣金件的结构表达出来.2.绘制展开图.也就是将一结构复杂的零件展开成一个平板件.3.下料.下料的方式有很多种,主要有以下几种方式:a.剪床下料.是利用剪床剪出展开图的外形长宽尺寸.若有冲孔、切角的,再转冲床结合模具冲孔、切角成形. b.冲床下料.是利用冲床分一步或多步在板材上将零件展开后的平板件结构冲制成形.其优点是耗费工时短,效率高,可减少加工成本,在批量生产时经常用到.c.NC数控下料.NC下料时首先要编写数控加工程序.就是利用编程软件,将绘制的展开图编写成NC数控加工机床可识别的程序.让其跟据这些程序一步一步的在一块铁板上,将其平板件的结构形状冲制出来.d.激光下料.是利用激光切割方式,在一块铁板上将其平板件的结构形状切割出来.4.翻边攻丝.翻边又叫抽孔,就是在一个较小的基孔上抽成一个稍大的孔,再在抽孔上攻丝.这样做可增加其强度,避免滑牙.一般用于板厚比较薄的钣金加工.当板厚较大时,如2.0、2.5等以上的板厚,我们便可直接攻丝,无须翻边.5.冲床加工.一般冲床加工的有冲孔切角、冲孔落料、冲凸包、冲撕裂、抽孔等加工方式,以达到加工目的.其加工需要有相应的模具来完成操作.冲凸包的有凸包模,冲撕裂的有撕裂成形模等.6.压铆.压铆就本厂而言,经常用到的有压铆螺柱、压铆螺母、压铆螺钉等,其压铆方式一般通过冲床或液压压铆机来完成操作,将其铆接到钣金件上.7.折弯.折弯就是将2D的平板件,折成3D的零件.其加工需要有折床及相应的折弯模具来完成操作.它也有一定的折弯顺序,其原则是对下一刀不产生干涉的先折,会产生干涉的后折.8.焊接.焊接就是将多个零件组焊在一起,达到加工的目的或是单个零件边缝焊接,以增加其强度.其加工方一般有以下几种:CO2气体保护焊、氩弧焊、点焊、机器人焊接等.这些焊接方式的选用是根据实际要求和材质而定.一般来说CO2气体保护焊用于铁板类焊接;氩弧焊用于铝板类焊接;机器人焊接主要是在料件较大和焊缝较长时使用.如机柜类焊接,可采用机器人焊接,可节省很多任务时,提高工作效率和焊接质量.9.表面处理.表面处理一般有磷化皮膜、电镀五彩锌、铬酸盐、烤漆、氧化等.磷化皮膜一般用于冷轧板和电解板类,其作用主要是在料件表上镀上一层保护膜,防止氧化;再来就是可增强其烤漆的附着力.电镀五彩锌一般用冷轧板类表面处理;铬酸盐、氧化一般用于铝板及铝型材类表面处理;其具体表面处理方式的选用,是根据客户的要求而定.10.组装.所谓组装就是将多个零件或组件按照一定的方式组立在一起,使之成为一个完整的料品。
汽车设计-汽车白车身数模验收规范模板
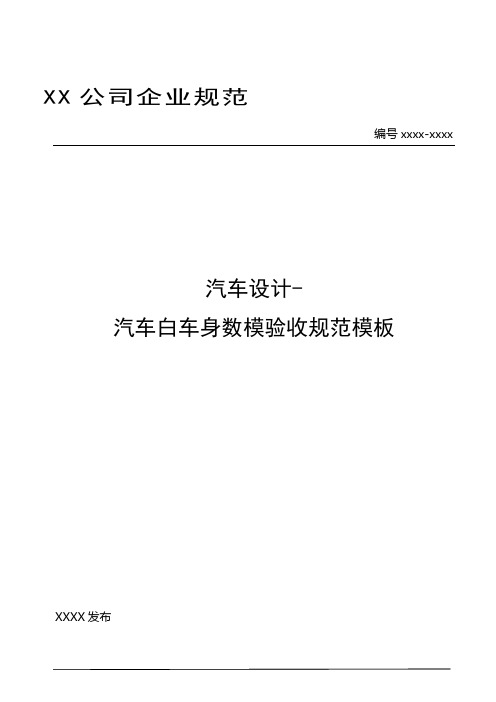
XX公司企业规范编号xxxx-xxxx汽车设计-汽车白车身数模验收规范模板XXXX发布白车身数模验收规范1范围本规范规定了本公司白车身各部件数模验收的一般要求。
本规范规定了本公司白车身各部件的冲压工艺性、焊接工艺性、涂装工艺性、装配工艺性的要求。
本规范规定了本公司白车身结构强度、各部件之间的密封、间隙及干涉的要求。
本规范规定了本公司白车身运动件运动分析的要求。
本规范规定了本公司白车身安全及法规要求。
本规范规定了本公司白车身车身轻量化设计要求。
2规范性引用文件下列文件对于本文件的应用是必不可少的。
凡是注日期的引用文件,仅注日期的版本适用于本文件。
凡是不注日期的引用文件,其最新版本(包括所有的修改单)适用于本文件。
GB 11566-2009 乘用车外部凸出物3定义3.1 白车身总成:是指包含车身骨架总成、左/右前门总成、左/右后门总成、发动机罩盖总成、后背门总成或行李箱盖总成、所有黑漆件在内的涂装之前的车身总成。
3.2 RPS定位点:含定位面、定位孔及所有定位点系统。
4规范4.1数模通用要求4.1.1零件编号规则要按照《汽车零部件编号规则》及研究院关于零件编号的规范执行;数模名称、编号与BOM表名称、代号一致;整车坐标系统一;结构设计数模外表面与A面数模完全符合。
4.1.23D数据按要求分层存放;交付数据不允许有未倒角的棱边和未倒圆的,除A 面外不可见的结构件型面及切边线要保证G1以上连续。
4.1.3 同一零件必须包含完整空间集合形态描述的无缝曲面、料厚指示线、圆孔法向指示线;型面不得有重叠、不允许有碎面及多余面线,同一型面一种颜色;料厚线起点要在零件数据型面上,数模可以沿料厚线偏移料厚;零件数据中要有实体数据.。
4.1.4任何两个相邻钣金零件,如果其料厚指示方向相反,则该两零件间的搭接边距离应该恒为零。
如果其料厚指示方向相同,两零件间的搭接边距离为其中一个零件的料厚;4.1.53D数据树状结构要采用研究院规定的标准形式。
(工艺流程)钣金工艺流程表
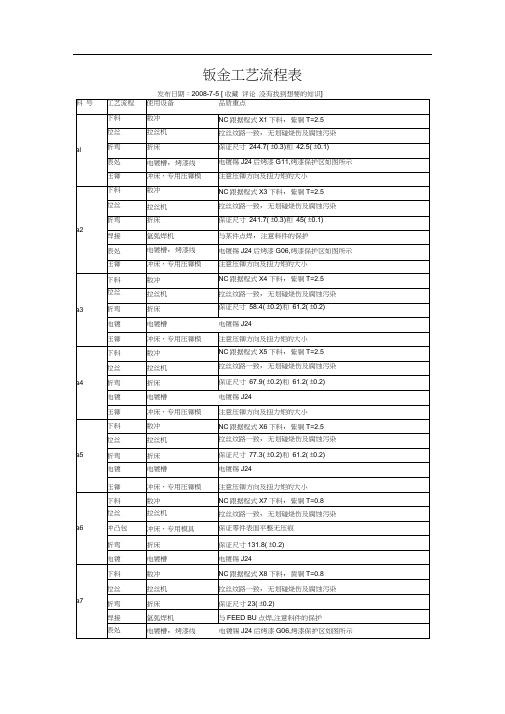
钣金工艺流程表各种钢材焊接知识要点(一)发布日期:2010-5-1 [ 收藏评论没有找到想要的知识]1 什么是焊接性?试述碳钢的焊接性。
焊接性是指材料在限定的施工条件下焊接成按规定设计要求的构件,并满足预定服役要求的能力。
焊接性受材料、焊接方法、构件类型及使用要求四个因素的影响。
碳钢是以铁元素为基础的,铁碳合金,碳为合金元素,其碳的质量分数不超过1% 此外,锰的质量分数不超过1.2%,硅的质量分数不超过0.5%,后两者皆不作为合金元素。
其它元素如Ni、Cr、Cu等均控制在残余量的限度以内,更不作为合金元素。
杂质元素如S、P、O N等,根据钢材品种和等级的不同,均有严格限制。
因此,碳钢的焊接性主要取决于含碳量,随着含碳量的增加,焊接性逐渐变差,其中以低碳钢的焊接性最好,见表1 O碳钢焊接性与含碳量的关系表把钢中合金元素(包括碳)的含量按其作用换自成碳的相当含量,称为该种钢材的碳当量,可作为评定钢材焊接性的一种参考指标。
碳钢中的元素除C外,主要是Mn和Si,它们的含量增加,焊接性变差,但其作用不及碳强烈。
国际焊接学会推荐的碳当量公式为Mn Cu+N6+ Mo+VCE(IIW)= C + ——+ ----------- + ----------------------- (质量分数)(%6 15 5随着碳当量值的增加,钢材的焊接性会变差。
当CE值大于0.4%〜0.6%寸,冷裂纹的敏感性将增大,焊接时需要采取预热、后热及用低氢型焊接材料施焊等一系列工艺措施。
3 利用碳当量值评价钢材焊接性有何局限性?碳当量值只能在一定范围内,对钢材概括地、相对地评价其焊接性,这是因为:1)如果两种钢材的碳当量值相等,但是含碳量不等,含碳量较高的钢材在施焊过程中容易产生淬硬组织,其裂纹倾向显然比含碳量较低的钢材来得大,焊接性较差。
因此,当钢材的碳当量值相等时,不能看成焊接性就完全相同。
2)碳当量计算值只表达了化学成分对焊接性的影响,没有考虑到冷却速度不同,可以得到不同的组织,冷却速度快时,容易产生淬硬组织,焊接性就会变差。
数理统计工具在车身配合工艺改进中的应用

下面根 据不 同改进 阶段 的工作 要求 ,分析各 阶段
并 无直接 联 系 ,这一缺 陷可 以认 为是普遍 性 问题 。
中数理 统计 工具 的具体应 用。
( 通过调查厂区内未出库的整车 ,编制统计表, 2)
同时应用排列 图 ( 帕累托 图 ) 对各类掉漆缺 陷进行排列
散布 图 、直 方 图、过程 能力 分析 、控 制图 等。结 合 本 案例 ,对 各类 要 因的工 艺 分析和验 证 如下 。 ( 左 前 翼 子板 安 装 孔 处走 料 因素 的 判定 。对 1)
用域 地
工 变 ,改量 位
环境 方法
/ 具 冲
焊 艺 堡 夹 骱廿 坐 装 具 工 垦
1 O O
流程 图 ,如 图4 。
8 O
1 0
8 6
4
6 0婺
4 蘸 0
2 O
O
O
缺 陷 来源 敲击钣金 调整损伤 工具划伤 未补 漆 其 他 1 7 4 累计频 率 4 67 2 67 1 33 67 67 百 分比 4 67 7 33 8 67 9 1 OO 33 O 累积 %
亮
车 身配合 类 问题 主要 指 由于焊 接结 构尺 寸偏 差 导 致 内外饰 件装配后产生 外观或功 能性 问题 ,由于影 响因 素 多 ,是车身制造控制难 点之一 。此类问题除采用 冲焊 工艺改进外 ,在数据 分析、制定 改进 措施 、效 果验 证 中 借助质 量工具有助于 问题; 确 定位 ,缩短 更改周期 。 隹
2 年 第2 01 0 期 汽车 q -艺 与 材 料 A& 2 TM l 7 J
.
生
产 琐 扬
子 板 匹配 不 良导 致 了 整车 油 漆 外 观 损伤 ),故 采用
汽车冲压件模具验收CHECKLIST
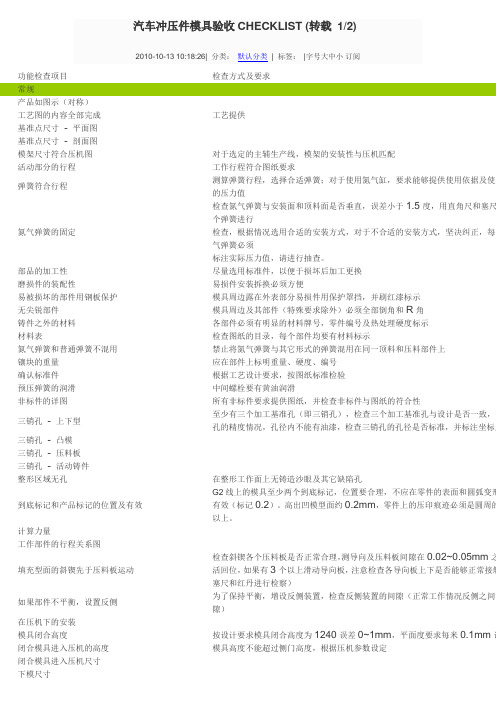
汽车冲压件模具验收CHECKLIST (转载1/2)2010-10-13 10:18:26| 分类:默认分类| 标签:|字号大中小订阅功能检查项目检查方式及要求常规产品如图示(对称)工艺图的内容全部完成工艺提供基准点尺寸- 平面图基准点尺寸- 剖面图模架尺寸符合压机图对于选定的主辅生产线,模架的安装性与压机匹配活动部分的行程工作行程符合图纸要求弹簧符合行程测算弹簧行程,选择合适弹簧;对于使用氮气缸,要求能够提供使用依据及使用的压力值氮气弹簧的固定检查氮气弹簧与安装面和顶料面是否垂直,误差小于1.5度,用直角尺和塞尺个弹簧进行检查,根据情况选用合适的安装方式,对于不合适的安装方式,坚决纠正,每个气弹簧必须标注实际压力值,请进行抽查。
部品的加工性尽量选用标准件,以便于损坏后加工更换磨损件的装配性易损件安装拆换必须方便易被损坏的部件用钢板保护模具周边露在外表部分易损件用保护罩挡,并刷红漆标示无尖锐部件模具周边及其部件(特殊要求除外)必须全部倒角和R角铸件之外的材料各部件必须有明显的材料牌号,零件编号及热处理硬度标示材料表检查图纸的目录,每个部件均要有材料标示氮气弹簧和普通弹簧不混用禁止将氮气弹簧与其它形式的弹簧混用在同一顶料和压料部件上镶块的重量应在部件上标明重量、硬度、编号确认标准件根据工艺设计要求,按图纸标准检验预压弹簧的润滑中间螺栓要有黄油润滑非标件的详图所有非标件要求提供图纸,并检查非标件与图纸的符合性三销孔- 上下型至少有三个加工基准孔(即三销孔),检查三个加工基准孔与设计是否一致,注孔的精度情况,孔径内不能有油漆,检查三销孔的孔径是否标准,并标注坐标尺三销孔- 凸模三销孔- 压料板三销孔- 活动铸件整形区域无孔在整形工作面上无铸造沙眼及其它缺陷孔到底标记和产品标记的位置及有效G2线上的模具至少两个到底标记,位置要合理,不应在零件的表面和圆弧变形有效(标记0.2)。
高出凹模型面约0.2mm,零件上的压印痕迹必须是圆周的以上。
钣金工艺流程单管理办法
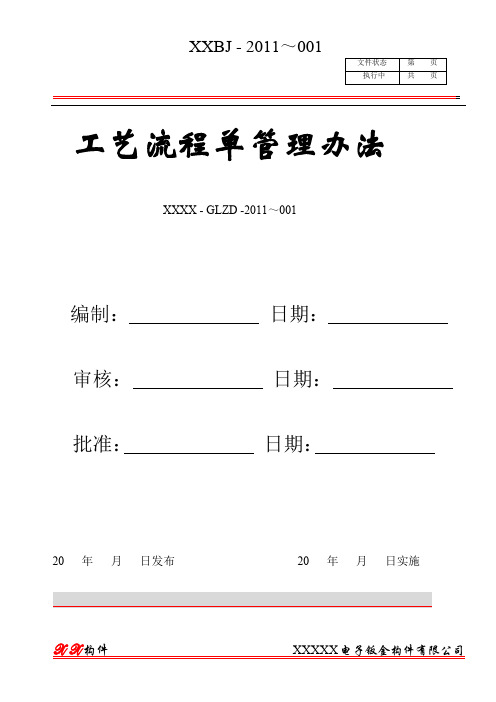
工艺流程单管理办法XXXX - GLZD -2011~001编制:日期:审核:日期:批准:日期:20 年月日发布20 年月日实施工艺流程单管理办法SCKD - GLZD -2010~001一. 适用范围1.1本办法适用于公司内各种产品的生产加工。
1.2 凡是被在公司内生产加工的产品必需有图纸和工艺流程单。
二. 工艺流程单的编写部门、人员2.1 主要由设计部对应图纸详细填制、审核工艺流程单。
2.2设计部所出图纸由设计部填制、审核工艺流程单。
2.3 生产部只有总图的单件、非标件由设计部或下单人员填制工艺流程单。
2.4 客户提供的图纸由设计部或负责此产品的技术人员填制工艺流程单。
2.5 其他散件产品也可由下单人员填制工艺流程单。
三. 工艺流程单的内容3.1在填制工艺流程单时必需对应图纸详细填写单位、零件名称、图号(图纸没有图号可不填写),材料、数量和每道工序的主要加工内容,加工先后顺序、重点保证的尺寸、公差,加工时需要特别注意的事项等。
3.2下料:3.2-1 剪床:材料、数量、板厚,下料的详细尺寸,公差。
3.2-2 锯床:材料、数量、大小,下料的详细尺寸,公差。
3.2-3其他下料工种所对应的内容。
3.3 数冲:材料、数量、板厚,要冲孔的形状、大小、数量、公差。
3.4 水切割、线切割、激光切割:材料、数量、板厚,要切割孔的形状、大小、数量、公差,以及切割时要确保的尺寸等。
3.5 普冲:材料、数量、板厚,要冲孔的形状、大小、数量、公差,切角、冲孔时要确保的尺寸,左右件等。
3.6 钻床:材料、数量、板厚,钻孔攻丝的大小、数量,孔位公差,左右件。
3.7 折弯:材料、数量、板厚,折弯时要确保的尺寸、公差,以及折弯时要确保的特殊角度等,左右件等。
3.8 车床:材料、数量、大小,要加工的主要内容、加工时要确保的尺寸,公差等。
3.9 铣床:材料、数量、大小,要加工的主要内容、加工时要确保的尺寸,公差等。
3.10 钳焊:材料、数量,所要焊接的零件名称、左右件,焊接时所要注意的事项,打磨、修锉、校正。
车身修复(钣金)比赛方案
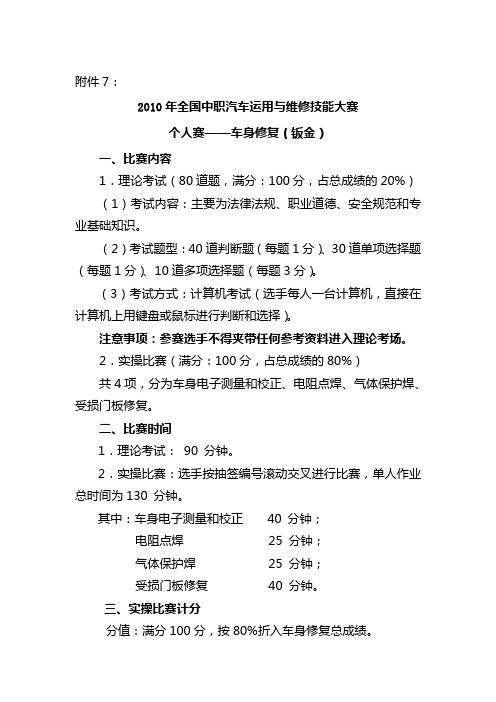
附件7:2010年全国中职汽车运用与维修技能大赛个人赛——车身修复(钣金)一、比赛内容1.理论考试(80道题,满分:100分,占总成绩的20%)(1)考试内容:主要为法律法规、职业道德、安全规范和专业基础知识。
(2)考试题型:40道判断题(每题1分)、30道单项选择题(每题1分)、10道多项选择题(每题3分)。
(3)考试方式:计算机考试(选手每人一台计算机,直接在计算机上用键盘或鼠标进行判断和选择)。
注意事项:参赛选手不得夹带任何参考资料进入理论考场。
2.实操比赛(满分:100分,占总成绩的80%)共4项,分为车身电子测量和校正、电阻点焊、气体保护焊、受损门板修复。
二、比赛时间1.理论考试: 90 分钟。
2.实操比赛:选手按抽签编号滚动交叉进行比赛,单人作业总时间为130 分钟。
其中:车身电子测量和校正 40 分钟;电阻点焊 25 分钟;气体保护焊 25 分钟;受损门板修复 40 分钟。
三、实操比赛计分分值:满分100分,按80%折入车身修复总成绩。
其中:(1)车身电子测量和校正 25分;(2)电阻点焊 20分;(3)气体保护焊 25分;(4)受损门板修复 30分。
四、比赛作业工件1.车身电子测量和校正:广汽丰田凯美瑞车身,前纵梁变形。
2.电阻点焊:焊片的厚度为1毫米,尺寸为125毫米×40毫米,材质为低碳普通冷轧钢板。
3.气体保护焊:焊片的厚度为1毫米,尺寸分别为125毫米×70毫米(无孔)和125毫米×70毫米(有1个8毫米的孔),材质为低碳普通冷轧钢板。
4.受损门板修复:已设置损伤的凯美瑞右后车门外板。
五、比赛作业内容及要求1.车身电子测量和校正项目(1)作业内容在40 分钟内,先对车身进行车身底部测量并记录(共6对12个测量点,分别为2对基准点,4对测量点),然后再对前纵梁进行测量、记录并校正。
(2)作业要求比赛提供3张不同测量点的车身图,选手抽签确定比赛用车身图。
12 车身、钣金与喷漆TOC--待审核-抽审OK
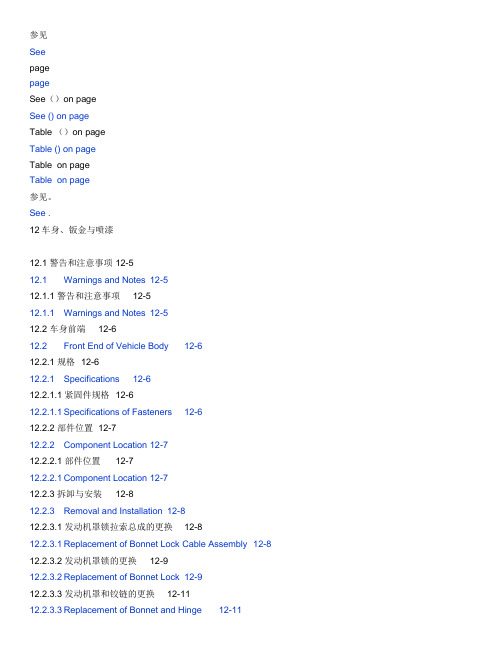
参见SeepagepageSee()on pageSee () on pageTable ()on pageTable () on pageTable on pageTable on page参见。
See .12车身、钣金与喷漆12.1 警告和注意事项 12-512.1 Warnings and Notes 12-512.1.1 警告和注意事项12-512.1.1 Warnings and Notes 12-512.2 车身前端12-612.2 Front End of Vehicle Body 12-612.2.1 规格12-612.2.1 Specifications 12-612.2.1.1 紧固件规格12-612.2.1.1 Specifications of Fasteners 12-612.2.2 部件位置12-712.2.2 Component Location 12-712.2.2.1 部件位置12-712.2.2.1 Component Location 12-712.2.3 拆卸与安装12-812.2.3 Removal and Installation 12-812.2.3.1 发动机罩锁拉索总成的更换12-812.2.3.1 Replacement of Bonnet Lock Cable Assembly 12-8 12.2.3.2 发动机罩锁的更换12-912.2.3.2 Replacement of Bonnet Lock 12-912.2.3.3 发动机罩和铰链的更换12-1112.2.3.3 Replacement of Bonnet and Hinge 12-1112.2.3.4 发动机罩支撑杆总成的更换12-1312.2.3.4 Replacement of Bonnet Stay Rod Assembly 12-1312.2.3.5 前翼子板的更换12-1412.2.3.5 Replacement of Front Fender 12-1412.3 车身后端12-2112.3 Rear End of Vehicle Body12-2112.3.1 规格12-2112.3.1 Specifications 12-2112.3.1.1 紧固件规格12-2112.3.1.1 Specifications of Fasteners 12-2112.3.2 部件位置12-2212.3.2 Component Location 12-2212.3.2.1 部件位置12-2212.3.2.1 Component Location 12-2212.3.3 拆卸与安装12-2312.3.3 Removal and Installation 12-2312.3.3.1 背门和背门铰链的更换12-2312.3.3.1 Replacement of Trunk Lid and Trunk Lid Hinge 12-2312.3.3.2 背门支撑气弹簧的更换12-2512.3.3.2 Replacement of Supporting Air Spring of Trunk Lid 12-2512.3.3.4 加油口盖开启手柄及拉索总成的更换12-2612.3.3.4 Replacement of Assembly-Fuel Filler Cap Release Handle and Cable 12-26 12.4 保险杠12-2812.4 Bumper 12-2812.4.1 规格12-2812.4.1 Specifications 12-2812.4.1.1 紧固件规格12-2812.4.1.1 Specifications of Fasteners 12-2812.4.2 部件位置12-2912.4.2 Component Location 12-2912.4.2.1 部件位置12-2912.4.2.1 Component Location 12-2912.4.3 拆卸与安装12-3012.4.3 Removal and Installation 12-3012.4.3.1 前保险杠的更换12-3012.4.3.1 Replacement of Front Bumper 12-3012.4.3.2 前保险杠支架的更换12-3212.4.3.2 Replacement of Front Bumper Bracket 12-3212.4.3.3 后保险杠的更换12-3312.4.3.3 Replacement of Rear Bumper 12-3312.4.3.4 后保险杠支架的更换12-3512.4.3.4 Replacement of Rear Bumper Bracket 12-3512.4.3.5 前横梁的更换12-3612.4.3.5 Replacement of Front Crossmember 12-3612.4.3.6 后横梁的更换12-3712.4.3.6 Replacement of Rear Crossmember 12-3712.5 车门12-3812.5 Door 12-3812.5.1 规格12-3812.5.1 Specifications 12-3812.5.1.1 紧固件规格12-3812.5.1.1 Specifications of Fasteners 12-3812.5.2 拆卸与安装12-3912.5.2 Removal and Installation 12-3912.5.2.1 车门和铰链的更换12-3912.5.2.1 Replacement of Door and Hinge 12-3912.5.2.2 车门限位器的更换12-4112.5.2.2 Replacement of Door Stopper 12-4112.5.2.3 车门外开启手柄的更换12-4212.5.2.3 Replacement of Exterior Door Release Handle 12-4212.5.2.4 车门内开启手柄的更换(1.8L车型)12-4412.5.2.4 Replacement of Interior Door Release Handle (Model 1.8L) 12-44 12.5.2.5车门内开启手柄的更换(2.0L车型)12-4612.5.2.5 Replacement of Interior Door Release Handle (Model 2.0L) 12-46 12.5.2.6 前车门锁芯的更换12-4812.5.2.6 Replacement of Front Door Lock Cylinder 12-4812.6 车架和车身底部 12-5212.6 Vehicle Frame and Vehicle Body Bottom 12-5212.6.1 规格12-5212.6.1 Specifications 12-5212.6.1.1 紧固件规格- 前车架和车身底部12-5212.6.1.1 Specifications of Fasteners- Front Vehicle Frame and Vehicle Body Bottom 12-52 12.6.1.2 紧固件规格- 后车架和车身底部12-5212.6.1.2 Specifications of Fasteners- Rear Vehicle Frame and Vehicle Body Bottom 12-52 12.6.2 描述和操作12-5312.6.2 Description and Operation 12-5312.6.2.1 车架和车身底部说明12-5312.6.2.1 Description of Vehicle Frame and Vehicle Body Bottom 12-5312.6.3 诊断信息和步骤12-5412.6.3 Diagnostic Information and Steps 12-5412.6.3.1 诊断信息和步骤12-5412.6.3.1 Diagnostic Information and Steps 12-5412.6.4 拆卸与安装12-5512.6.4 Removal and Installation 12-5512.6.4.1 车架的维修12-5512.6.4.1 Repair of Vehicle Frame 12-5512.6.4.2 前悬架横梁总成的更换12-5512.6.4.2 Replacement of Front Suspension Crossmember Assembly 12-5512.6.4.3 前悬架纵梁的更换12-5712.6.4.3 Replacement of Front Suspension Side Member 12-5712.6.4.4前副车架的更换(液压转向机)12-5912.6.4.4 Replacement of Front Sub-chassisframe (hydraulic steering gear) 12-5912.6.4.5前副车架的更换(电子助力转向机)12-6512.6.4.5 Replacement of Front Sub-chassisframe (electronic power steering gear) 12-65 12.6.4.6后副车架的更换12-7112.6.4.6 Replacement of Rear Sub-chassisframe 12-7112.6.4.7后副车架的更换12-7312.6.4.7 Replacement of Rear Sub-chassisframe 12-7312.7 座椅12-7412.7 Seats 12-7412.7.1 规格12-7412.7.1 Specifications 12-7412.7.1.1 紧固件规格12-7412.7.1.1 Specifications of Fasteners 12-7412.7.2 分解图12-7512.7.2 Breakdown View 12-7512.7.2.1 分解图12-7512.7.2.1 Breakdown View 12-7512.7.3 拆卸与安装12-7712.7.3 Removal and Installation 12-7712.7.3.1 前排座椅头枕的更换12-7712.7.3.1 Replacement of Front Seat Headrest 12-7712.7.3.2 前排座椅的更换12-7712.7.3.2 Replacement of Front Seats 12-7712.7.3.3 后排座椅的更换12-7812.7.3.3 Replacement of Rear Seats 12-7812.7.3.4 后排座椅支架的更换12-8112.7.3.4 Replacement of Rear Seat Support 12-8112.8 仪表台、仪表和控制台12-8312.8 Instrument Panel, Instrument and Control Panel 12-83 12.8.1 规格12-8312.8.1 Specifications 12-8312.8.1.1 紧固件规格12-8312.8.1.1 Specifications of Fasteners 12-8312.8.2 部件位置12-8412.8.2 Component Location 12-8412.8.2.1 部件位置12-8412.8.2.1 Component Location 12-8412.8.3 拆卸与安装12-8512.8.3 Removal and Installation 12-8512.8.3.1 仪表台总成的更换12-8512.8.3.1 Replacement of Instrument Panel Assembly 12-85 12.8.3.2 副仪表台总成的更换12-9312.8.3.2 Replacement of Console Assembly 12-9312.8.3.3 仪表台杂物箱的更换12-10412.8.3.3 Replacement of Glove Box of Instrument Panel 12-104 12.8.3.4 仪表台横梁的更换12-10612.8.3.4 Replacement of Crossmember of Instrument Panel 12-106 12.9 内饰12-11412.9 Interior Trims 12-11412.9.1 拆卸与安装12-11412.9.1 Removal and installation 12-11412.9.1.1 左/右车门槛内装饰板总成的更换12-11412.9.1.1 Replacement of Left/right Door Sill Interior Trim Panel Assembly 12-114 12.9.1.2 左/右前柱上装饰板总成的更换12-11612.9.1.2 Replacement of Left/right A Post Upper Trim Panel Assembly 12-116 12.9.1.3 左/右中柱装饰板总成的更换12-11712.9.1.3 Replacement of Left/right B Post Trim Panel Assembly 12-11712.9.1.4 车门框密封条及密封件的更换 12-12112.9.1.4 Replacement of Door Frame Seal and Sealing Part 12-12112.9.1.5 左/右后柱下装饰板总成的更换12-12312.9.1.5 Replacement of Left/right C Post Lower Trim Panel Assembly 12-123 12.9.1.6 左/右后柱上装饰板总成的更换12-12712.9.1.6 Replacement of Left/right C Post Upper Trim Panel Assembly 12-127 12.9.1.7 左前车门内装饰板的更换 12-13012.9.1.7 Replacement of Interior Trim Panel of Front Door LH 12-13012.9.1.8 右前车门内装饰板的更换 12-13212.9.1.8 Replacement of Interior Trim Panel of Front Door RH 12-13212.9.1.9 后车门内装饰板的更换12-13312.9.1.9 Replacement of Interior Trim Panel of Rear Door 12-13312.9.1.10 背门内装饰板的更换12-13512.9.1.10 Replacement of Interior Trim Panel of Trunk Lid 12-13512.9.1.11 顶盖内装饰板的更换12-13812.9.1.11 Replacement of Interior Trim Panel of Panel Roof 12-13812.9.1.12 车内地毯的更换12-14412.9.1.12 Replacement of Interior Carpet of Vehicle 12-14412.10 外饰12-14512.10 Exterior Trims 12-14512.10.1 拆卸与安装12-14512.10.1 Removal and installation 12-14512.10.1.1 前后徽标的更换12-14512.10.1.1 Replacement of Front and Rear Logos 12-14512.10.1.2 发动机罩隔音垫的更换12-14612.10.1.2 Replacement of NVH Pad, Bonnet 12-14612.10.1.3 通风盖板的更换12-14712.10.1.3 Replacement of Plenum Mounding 12-14712.10.1.4 背门饰条的更换12-15112.10.1.4 Replacement of Trunk Lid Trim Strip 12-15112.10.1.5 后门三角外装饰板的更换12-15312.10.1.5 Replacement of Triangular Exterior Trim Panel of Rear Door 12-15312.10.1.6 顶盖装饰条的更换12-15512.10.1.6 Replacement of Trim Strip of Panel Roof 12-15512.10.1.7 发动机底部左右护板的更换12-15612.10.1.7 Replacement of Left/right Shield of Engine Bottom 12-15612.10.1.8 前翼子板衬板的更换12-15712.10.1.8 Replacement of Front Fender 12-15712.10.1.9 后翼子板衬板的更换12-15912.10.1.9 Replacement of Rear Fender 12-15912.10.1.10 门槛下装饰板的更换12-16112.10.1.10 Replacement of Lower Trim Panel of Door Sill 12-16112.10.1.11 车门密封条的更换 12-16312.10.1.11 Replacement of Door Seal 12-16312.10.1.12 行李架的更换12-16512.10.1.12 Replacement of Parcel Shelf 12-16512.11 塑料面板信息及维修12-16712.11 Plastic Panel Information and Repair 12-16712.11.1 描述和操作12-16712.11.1 Description and Operation 12-16712.11.1.1 描述和操作12-16712.11.1.1 Description and Operation 12-16712.11.2 拆卸与安装12-16812.11.2 Removal and installation 12-16812.11.2.1 塑料件的维修注意事项12-16812.11.2.1 Notes for Repair of Plastic Parts 12-16812.11.2.2 热固性塑料凹坑的维修12-16812.11.2.2 Repair of the Pit of Thermosetting Plastic 12-16812.11.2.3 热固性塑料刮伤的维修12-16812.11.2.3 Repair of the Scratch of Thermosetting Plastic 12-16812.11.2.4 热固性塑料裂纹的维修(长度100 mm以下) 12-16912.11.2.4 Repair of the Crack of Thermosetting Plastic (less than 100 mm long) 12-169 12.12 碰撞维修12-17012.12 Impact Repair 12-17012.12.1 规格12-17012.12.1 Specifications 12-17012.12.1.1 碰撞维修材料12-17012.12.1.1 Impact Repair Material 12-17012.12.1.2 车身表面间隙/面差12-17112.12.1.2 Body Surface Gap/Flush 12-17112.12.1.3 车身尺寸12-17312.12.1.3 Vehicle Body Dimension 12-17312.12.2 描述和操作12-18412.12.2 Description and Operation 12-18412.12.2.1 安全注意事项12-18412.12.2.1 Safety Notes12-18412.12.2.2 零部件的状态12-18412.12.2.2 Parts State 12-18412.12.2.3 焊接种类说明12-18412.12.2.3 Welding Type Description 12-18412.12.2.4 防腐处理12-18412.12.2.4 Corrosion Prevention Treatment 12-18412.12.2.5 汽车报废件环保处理方法12-18412.12.2.5 Environmental Protection Treatment for Discarded Parts 12-184 12.12.3 分解图12-18512.12.3 Breakdown View 12-18512.12.3.1 车身总成12-18512.12.3.1 Vehicle Body Assembly 12-18512.12.3.2 车身总成(带天窗)12-18612.12.3.2 Vehicle Body Assembly (with sunroof) 12-18612.12.3.3 车身前地板12-18712.12.3.3 Vehicle Body Front Floor 12-18712.12.3.4 车身后地板12-18812.12.3.4 Vehicle Body Rear Floor 12-18812.12.3.5 地板隔热垫12-18912.12.3.5 Floor Heat Insulation Pad 12-18912.12.3.6 前挡风玻璃12-19012.12.3.6 Front Windshield 12-19012.12.3.7 前围挡板12-19112.12.3.7 Front Wall Baffle 12-19112.12.3.8 发动机舱12-19212.12.3.8 Engine Bay 12-19212.12.3.9 发动机下护板12-19312.12.3.9 Engine Lower Shield 12-19312.12.3.10 发动机罩12-19412.12.3.10 Bonnet 12-19412.12.3.11 前翼子板12-19512.12.3.11 Front Fender 12-19512.12.3.12 侧围12-19612.12.3.12 Side Wall 12-19612.12.3.13 车身前支柱12-19712.12.3.13 Vehicle Body Front Pillar 12-19712.12.3.14 车身中支柱12-19812.12.3.14 Vehicle Body Middle Pillar 12-198 12.12.3.15 车身后支柱12-19912.12.3.15 Vehicle Body Rear Pillar 12-19912.12.3.16 后挡泥板12-20012.12.3.16 Rear Splash Guard 12-20012.12.3.17 背门玻璃12-20112.12.3.17 Trunk Lid Glass 12-20112.12.3.18 背门12-20212.12.3.18 Trunk Lid 12-20212.12.3.19 顶盖12-20312.12.3.19 Panel Roof 12-20312.12.3.20 顶盖(带天窗) 12-20412.12.3.20 Panel Roof (with sunroof) 12-20412.12.4 诊断信息和步骤12-20512.12.4 Diagnostic Information and Steps 12-205 12.12.4.1 诊断信息和步骤12-20512.12.4.1 Diagnostic Information and Steps 12-205 12.12.5 拆卸与安装12-20612.12.5 Removal and Installation 12-20612.12.5.1 拆卸与安装12-20612.12.5.1 Removal and Installation 12-20612.13 油漆/涂层12-20712.13 Paint/Coat 12-20712.13.1 规格12-20712.13.1 Specifications 12-20712.13.1.1 规格12-20712.13.1.1 Specifications 12-20712.13.2 描述和操作12-20812.13.2 Description and Operation 12-20812.13.2.1 油漆涂层说明12-20812.13.2.1 Paint Coat Description 12-20812.13.2.2 汽车漆面日常保养12-20812.13.2.2 Daily Maintenance of Coat 12-20812.13.2.3 进行油漆调配和喷漆操作过程中的警告和注意事项 12-20812.13.2.3 Warning and Notes for Paint Mixing and Spraying 12-20812.13.2.4 罩光清漆保养、维修时的注意事项12-20812.13.2.4 Notes for Coating Varnish Maintenance and Repair 12-20812.13.2.5 进行防腐处理的注意事项12-20912.13.2.5 Notes for Anti-corrosion Treatment 12-20912.13.3 诊断信息和步骤12-21012.13.3 Diagnosis Information and Steps 12-21012.13.3.1 汽车漆面常见缺陷示例及处理方法12-21012.13.3.1 Normal Defect of Coat and Handling Method 12-21012.13.4 拆卸与安装12-21112.13.4 Removal and Installation 12-21112.13.4.1 常见漆膜缺陷处理工艺过程示例12-21112.13.4.1 Example of Normal Paint Film Defect Treatment Process 12-21112.13.4.2 常规研磨抛光美容处理工艺过程示例12-21212.13.4.2 Example of Normal Grinding and Polishing Process 12-21212.13.4.3 深度研磨抛光处理工艺过程示例12-21312.13.4.3 Example of Deep Grinding and Polishing Process 12-21312.13.4.4 刚性表面的油漆喷涂工艺12-21512.13.4.4 Paint Spraying Process for Rigid Surface 12-21512.13.4.5 进行钣金20修复后的刚性表面的油漆喷涂程序12-22112.13.4.5 Paint Spraying Process for Rigid Surface after Repairing the Metal Panel 20 12-221 12.13.4.6 塑料件表面的漆面修补程序12-22112.13.4.6 Paint Repair Procedure for Plastic Surface 12-221。
车身数模工艺性一般检查规范

车身数模工艺性一般检查规范1. 范围本规范规定了结构设计工艺性审查的若干要求和产品图样工艺性审查的主要因素。
本规范适用于上海同济同捷科技有限公司新设计和改进设计的产品系列。
2. 规范性引用文件指定加工零件公差手册3. 术语公差基准:在制造工程上极为重要的零件,指定其容许公差,以将它作为验收零件的基准,称为公差基准。
4. 数模检查若干规范在数模检查过程中,经常发现设计数模严格遵循参照钣金件点云及测量尺寸设计,这样纯逆向设计带来的问题是:以这样的数模加工制造时,得不到原有钣金件的制造水准与装配水准,其原因主要是在建模过程中未考虑到参照车型钣金件的制造偏差,从而使设计值出现偏差,甚至出现不合理的设计结构;所以,有必要通过公差分析的手段还原其设计值,并通过正向设计的理念优化钣金件的设计。
4.1 搭接边间隙宽度4.1.1 对接钣金件间隙一般情况下控制为2mm;对应其单个钣金件制造公差基准为±1.0;对地板钣金件制造公差基准为±1.5或±2.0,间隙控制在3.0~4.0 。
对于样件经常出现的对接间隙很小和无间隙的情况,实际情况是由生产控制调整造成的,通过公差控制以及移动公差控制使其安装间隙达到很小,同时也就达到很好的外观质量要求,如下图4.1-2、图4.1-3。
4.1.2 侧围钣金件搭接间隙图4.1-2样件实际装配状图4.1-3样件的公差基准;制造 工艺水平提高,费用提高侧围钣金件搭接间隙及制造公差一般控制如下图的规范图4.1-4中对应的单件钣金制造公差基准为:4.1.3 车身下部总成钣金件搭接间隙地板等钣金件搭接间隙及制造公差一般控制如下图的规范 ⅰ)对于质量控制比较高的地板钣金件图4.1-4 图4.1-5图4.1-6图4.1-7 对应的单件钣金制造公差基准为:4.2 车门、盖板包边设计规范 4.2.1 发动机罩球截面包边的规范图4.1-8 图4.1-9图4.2-14.2.2 车门包边的规范ⅰ)车门内板切边到外板内圆角距离保持1.5mmⅱ)车门复杂造型曲线切边处包边设计规范(外板钣金设计规范)ⅲ)车门、盖板类尖角处设计规范图4.2-2ⅳ)后背门内外板高度(推荐值)图4.2-7有后背门护板遮盖时,外板比内板高1mm(推荐);无后背门护板遮盖时,内板比外板高1mm (推荐);4.3 特征避让圆角设计规范ⅰ)特征避让圆角合理的间隙为1mm,最小极限为0.5mm图 4.3-1ⅱ)特征过渡配合时,间隙控制设计规范图4.3-2①圆角切点尺寸,最小控制在2mm。
车身钣金零件热成型-工艺科-hotstamping

车身钣金零件热成型-工艺科-hotstamping第一篇:车身钣金零件热成型-工艺科-hotstamping车身钣金零件热成型汽车用热成型高强钢高强度钢的热冲压成型是汽车制造领域的一项新技术,解决了传统高强度钢板成型在汽车车身制造中遇到的各种问题。
这项技术是指将钢板经过1000°C左右的高温加热之后一次拉伸成形,又迅速冷却从而全面提升了钢板强度。
图1为热成型生产线。
图1 热成型生产线热成型件的抗拉强度达到1500Mpa之高,屈服强度大于1000Mpa,每平方厘米能承受10吨以上的压力,而且消除回弹影响,提高制造精度。
图2为热成型件。
图2 B柱热成型冲压件热成型的主要工序(1)、落料、冲孔(预成型):主要是冲压出板材外轮廓,对于形状复杂或拉伸深度较大的制件则需要进行预成型。
(2)、板料热处理:包括加热和保温两个阶段。
这一工序的目的在于将钢板加热到一个合适的温度,使钢板完全奥氏体化,并且具有良好的塑性。
加热所使用的设备为专用的连续加热炉,钢板在加热到再结晶温度以上之后,表面很容易氧化,生成氧化皮,这层氧化皮会对后续的加工造成不利的影响。
为了避免或减少钢板在加热炉中的氧化,一般在加热炉内设置惰性气体保护机制,或者对板料进行表面防氧化处理。
(3)、转移:指的是将加热后的钢板从加热炉中取出放进热成形模具中去。
在这一道工序中,必须保证钢板被尽可能快地转移到模具中,一方面是为了防止高温下的钢板氧化,另一方面是为了确保钢板在成形时仍然处在较高的温度下,以具有良好的塑性。
(4)、冲压和淬火。
在将钢板放进模具之后,要立即对钢板进行冲压成形,以免温度下降过多影响钢板的成形性能。
成形以后模具要合模保压一段时间,一方面是为了控制零件的形状,另一方面是利用模具中设置的冷却装置对钢板进行淬火,使零件形成均匀的马氏体组织,获得良好的尺寸精度和机械性能。
研究表明,就目前常用的热冲压钢材而言,实现奥氏体向马氏体转变的最小冷却速率为27~30℃/s,因此要保证模具对板料的冷却速度大于此临界值。
推荐-垫片BS11F106 钣金成形工艺及模具设计 精品
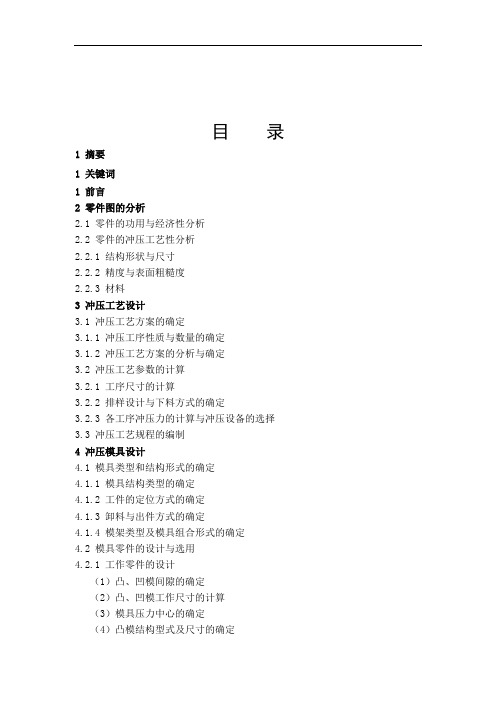
目录1 摘要1 关键词1 前言2 零件图的分析2.1 零件的功用与经济性分析2.2 零件的冲压工艺性分析2.2.1 结构形状与尺寸2.2.2 精度与表面粗糙度2.2.3 材料3 冲压工艺设计3.1 冲压工艺方案的确定3.1.1 冲压工序性质与数量的确定3.1.2 冲压工艺方案的分析与确定3.2 冲压工艺参数的计算3.2.1 工序尺寸的计算3.2.2 排样设计与下料方式的确定3.2.3 各工序冲压力的计算与冲压设备的选择3.3 冲压工艺规程的编制4 冲压模具设计4.1 模具类型和结构形式的确定4.1.1 模具结构类型的确定4.1.2 工件的定位方式的确定4.1.3 卸料与出件方式的确定4.1.4 模架类型及模具组合形式的确定4.2 模具零件的设计与选用4.2.1 工作零件的设计(1)凸、凹模间隙的确定(2)凸、凹模工作尺寸的计算(3)模具压力中心的确定(4)凸模结构型式及尺寸的确定(5)凹模结构型式及尺寸的确定4.2.2 定位零件的设计与选用4.2.3 卸料与出件装置的设计(1)卸料装置设计(2)推件装置设计(3)顶件装置设计4.2.4 支承固定零件的设计与选用(1)凸(凹)模固定板(2)垫板(3)模柄4.2.5 模架及其零件的选用4.2.6 紧固件的选用4.3 模具图样的绘制及压力机校核4.3.1 模具装配图的绘制4.3.2 模具零件图的绘制4.3.3 压力机技术参数的校核5 模具的工作原理与使用维护6 设计总结(设计的优缺点及其他需说明的问题,收获与体会)参考资料致谢垫片(BS11-F106)钣金成形工艺及模具设计摘要:本说明书以设计铁芯片零件模具为主线,主要阐述了冲裁零件的模具设计,模具各零件的加工工艺性及模具的总装配。
此制件为垫片,主要设计该件的冲孔落料模,材料为10号钢,其材料的力学性能比较好,经计算,此制件适合用冲孔、落料冲裁工艺生产。
设计这套模具首先分析材料是不是适合冲裁,选用冲裁工艺是否经济,是不是需要后续工序,如校平、整形等,然后计算冲压力选定压力机,最后确定模具的结构和工作零件的结构,并计算其工作零件的尺寸,其他的一些零件则在设计的时候尽量选用标准件,节约模具的制造成本,这些前提条件做好后,绘制模具总装图和零件图,编写总装过程和零件的加工工艺规程。
钣金工艺1
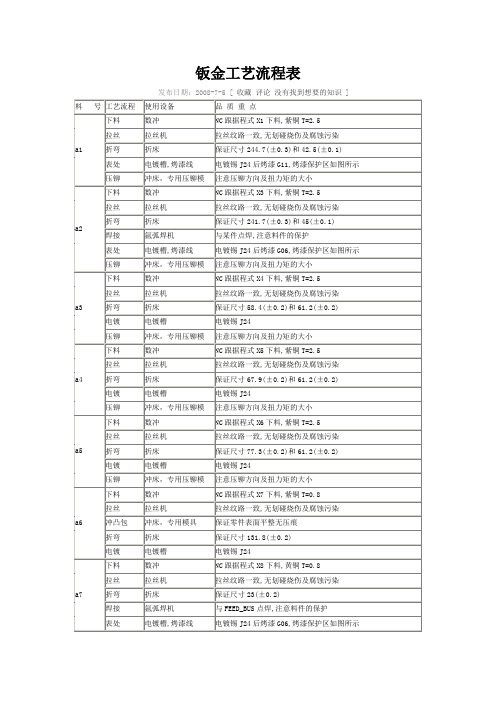
钣金工艺流程表发布日期:2008-7-5 [ 收藏评论没有找到想要的知识 ]钣金基础介绍(二)发布日期:2008-7-6 [ 收藏评论没有找到想要的知识 ]一.钣金所用材料常用材料有:冷轧板SPCC、电解板SECC、普通铝板及铝合金板AL3003-H14、AL5052-H32,不锈钢板、花纹板SGEC.最近开发的新材料:镀铝锌钢板.二.钣金加工方法1.下料方法下料是将厚材料按需要切成坏料,钣金下料的方法很多.按机床的类型和工作原理可分为剪切、铣切、冲切、氧气切割和激光切割.我司主要采用剪切、冲切及激光切割(LASER)1.1 剪切主要是用剪床剪裁直线边缘的板料,要求保证剪切表面的直线度和平行度.并尽量减少板材扭曲.1.2冲切下料主要利用数控冲床或普通冲床及落料模进行下料.1.3激光切割利用激光切割设备对板材进行连续切割,它的特点是效率高、精度高.2.手工成形随着生产的不断发展的技术进步,绝大多数的成形工艺是在机器上完成的.手工方法往往作为补充加工或修整工作.但在单件生产情况下,或一些形状比较复杂的零件,仍离不开手工操作及加工.手工成形主要是利用一些简单的胎型、靠模和各种各样的工夹具来完成.手工成型主要采取以下方法:弯曲、放边、收边、拔缘、拱曲、卷边、缝的校正.3.工模具成形工模具成形是利用冲床、折床等机器及各种各样的模具来完成板料的成型.可分为:弯曲、拉延、局部成型和翻边、缩口、缩颈、扩口和胀形、成形、拉弯成形、旋压成形和校平.我司主要采用弯曲(折弯)、校平或成形等工艺.弯曲(折弯)是钣金加工的主要方法之一.三.钣金联接方法钣金联接主工采用焊接、螺纹联接、铆接和粘接.我司采用的联接方式:焊接、螺纹联接和铆接.1.焊接是对焊件进行局部或整体加热或使焊件产生塑性变形,或加热与塑性变形同时进行,实现永久连接的工艺方法.可分为:手工电弧焊、气体保护电弧焊、激光焊、气焊、段焊和接触焊.我司主工采用气体保护焊和接触焊.1.1气体保护电弧焊在进行气体保护电弧焊时,电极电弧区及焊接熔池都处在保护气体的保护下.采用氩气保护焊缝表面没有氧化物及夹杂物.可以在任何空间位置施焊,可以用肉眼观察焊缝的成形过程并进行调整生产效率高.二氧气体保护焊则成本相当低.1.2接触焊接触焊是瞬时加热连接部位在熔化状态或非熔化状态下对被焊件加压形成焊接接头的焊接方法.它可分为对焊、点焊和缝焊.2.螺纹联接螺纹联接具有安装容易、拆卸方便、操作简单等优点,常用于可拆的钢结构连接.它可分为螺钉联接和螺栓联接.3.铆接铆接是用铆钉将金属结构的零件或组合件连接在一起的方法,铆钉种类较多,我司常用的铆钉有封闭形圆头抽芯铆钉、封闭形沉头抽芯铆钉及开口型圆头抽芯铆钉、开口型沉头抽芯铆钉。
汽车钣金工艺流程

钣金工艺流程之杨若古兰创作汽车车身概况操纵的钣金修复普通要经过几个过程.首先,对送修车辆进行检查,确定其车身结构类型,然后根据受损部位的情况确定修复方式,最初,按请求对分歧的部位安插合理的补缀工艺.一、根据车身结构确定补缀工艺1、车身校订固定,对于车身的拔拉索引校订,必须包管车身固定,否则,在拉力感化下会发生全体位移,达不到索引校订的目的.2、车身校订程序●了解设备的功能及平安使用措施●对车身损伤作出分析判断,确定牵拉方案●初步校订基础的固定点●批改定位点,检查校订后果,按计划牵拉校订3、在进行牵拉校订之前,应对车身内部和内部进行如下呵护●尽量取出内部部件,如坐位,仪表台,车垫等●焊接时用隔热材料盖住玻璃,坐位,仪表台等部件,以防烧伤●裁撤车身里面部件,并用棉布或呵护带呵护好车身,防止擦伤●如果油漆概况擦破,必须修睦,防止锈蚀4、车身前端损坏的修复●车身前端损坏主如果前端受碰撞(如追尾事故)构成的.损坏的部位包含前部的横梁一侧的挡泥板,侧梁和另侧的前翼板等相干区域●整修前端要从前挡泥板一侧梁开始,首先,须要修复支持结构件,选择须要更换部件的一侧进步前辈行侧梁的牵拉5、车身后部损坏的修复●校订时,将夹钳或钩子接到后侧梁的后部,后地板或后顶盖,侧板后端部,一边牵拉,一边测量车身上面每一部分的尺寸,观察车身板的配合间隙来确定须要的补缀程度●当后侧梁被严重碰撞,影响到后门框变形开关不畅时,但能靠牵拉侧梁来清除后顶盖侧板的应力二、根据车身概况损伤程度确定补缀工艺1、凹凸概况的整修●小范围局部凸起的整形:用垫铁贴紧凸起的反面,手锤敲击凸起部位,使凸起部分被紧缩到本来外形.操纵时,请求捶击力量要轻巧,以每秒2次的频率连续冲击,并做到捶击点均匀分布●局部凹陷的整形:与凸起的修整分歧的是,捶击点不在垫铁顶面上方,而是在铁皮的凸起部位.将垫铁贴紧最低处,用铁锤敲击附近凸起处即可●撬起凹陷,利用修平刀修整凹陷,车门概况某处有凹陷,将修平刀作垫铁用,采取捶击概况凸起部位的法子,可将凹陷修复2、概况收缩整形●金属板上变形部位的收缩用焊炬火焰将最凸或最凹点(伸张中间)加热无樱红色.加热大小与伸张程度有关加热后急速敲击红晕区域的四周,并逐步向加热点的中间包抄,?便金属组织紧缩.敲击时,要用垫铁在部件背部,用木锤敲击,冷却后再用铁锤轻轻敲击整平如果收缩一点不克不及达到整平的目的,可用同样方法在该点四周适当地位进行多点收缩,但此时加热范围要小一些所有收缩点冷却以后,进行一次全面敲平,敲击力要轻三、根据锈蚀程度确定补缀工艺车身概况锈蚀程度分歧,其钣金补缀方法也不不异1、概况漆层隆起是因为金属面生锈形成的,应将此处漆层清除干净,露出金属层,并用除锈剂清除铁锈,再按照喷漆请求处理,从头涂漆2、穿透性锈蚀,普通会使大面积的漆面隆起,此时,应将这部分生锈的金属全切除,经补焊一块金属块整修以后,再按喷漆请求处理,从头喷漆3、概况漆层被刮蹭是较罕见的损伤,应将刮蹭部位附近的漆层用专门的砂纸打磨,直至显现金属,然后对金属面按喷漆请求处理,从头涂装ZK施工流程工件概况:龟裂、零落、老化1、打磨2、除锈 P800-127除锈水(切勿用于镀锌板上)化学洗锈,对重锈渍需先打磨后清洗3、打磨干磨砂纸P180,机磨砂纸P180,水磨砂纸P3204、除油 P850-14除油剂(快干),P850-1402除油剂(热天用)以清洁布浴湿除油剂擦抹于工作概况,并马上用另一清洁布抹干5、底漆磷化底漆P565-597,1份活化剂P275-61,1份喷涂一道于裸金属概况并马上喷半途底漆或:超快干环氧底漆P565-895,4份固化剂P210-93819,1份喷涂2-3道,干燥后可以刮灰或喷半途底漆6、刮灰P551-1050/9988/6288原子灰(腻子)(不成使用于镀锌板概况)P551-1052全能腻子(可使用于镀锌板上)建议薄涂于完整磨透之金属概况,ZK漆面或原厂烤漆概况,可溶性漆面建议脱漆再刮灰7、打磨干磨P180后细磨P280,机磨P280后,细磨P280水磨P220后细磨P320(不适合裸金属概况)8、微填P083-60白色填眼灰,微填针眼,砂纸痕及刮痕,填补后概况建议干磨9、贴护根据喷涂须要进行当心,严谨的贴护,除油及除尘10、中涂尺度工序:ZK高固含量厚膜底漆P565-510,1份ZK固化剂P210-938/9,1份喷涂2-3层,每层相隔5-15分钟,并喷上研磨唆使图免磨工序:ZK超能免磨底漆P565-777,或ZK透明底漆P210-668,2份ZK固化剂P210-938/9,1份ZK浓缩剂P850-1492/3,40%喷涂2层,每层相隔5-10分钟11、打磨如面涂为单工序纯色漆,建议使用P600号水砂纸完整打磨,如面涂为底色漆系列时,建议P800号水砂纸作完整打磨(如有须要可用P083-60快干补土微填小沙眼)12、面涂前处理除水:气压清除车身藏水,贴护,更换贴护纸除油:除油剂除油,黏土,粘尘布除尘如需节省时间,可使用P210-790ZK超快干固化剂但不排除需抛光可能性13、面漆水纯色面漆 ZK单工序金属色漆P420一系列,2份 P421系列,2份P210-938/9,1份 P210-938/9,1份P80-1492/3,5-15% P850-1492/3,30-40%喷涂2次单层,每层喷涂3次单层,每层相隔10-15分钟相隔10-15分钟烤干60C30分钟烤干60C30分钟风干20C16小时风干20C16小时ZK双工序底色P422一系列银底色,1份纯底色,1份珍珠色,1份P850-1492/3,1份喷涂3次单层,每层相隔5-10分钟ZK三工序底色漆P422珍珠色,1份P850-1492/3,1份每次喷涂单层,不竭检查色彩,每层相隔5-10分钟P422底色,1份P850-1492/3,1份喷涂2次单层,每层相隔5-10分钟工作概况:裸金属概况1、清洁2、打磨3、除油4、底漆5、刮灰6、打磨7、微填8、贴护9、半途10、打磨11、面涂前处理12、面漆13、打蜡14、打蜡:P1500号水砂纸磨平尘点,或小垂流的地方(如有须要)P971-399用打磨亮丽蜡399机械或手工打磨砂纸痕并抛光P971-9若有须要,用油蜡作最初,漆膜呵护层(也可用机械打油蜡)。
汽车-车身开发工艺工程-9-夹具及检具(焊装总成)设计
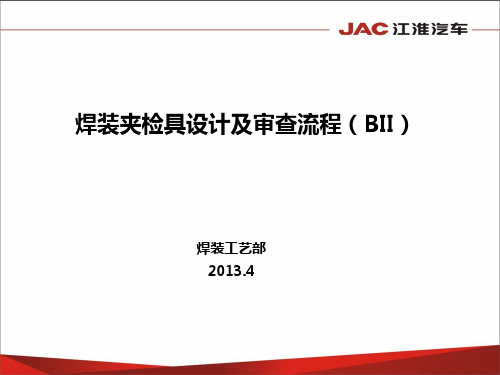
3 工作开展过程
2.2 夹紧元: 03 气缸:施力及传导功能。
标准气缸
带导杆气缸
薄型缸
夹紧功能
常配销使用,保 证精度要求
受限空间使用
3 工作开展过程
2.2 夹紧单元: 04 气缸连接板:支撑气缸带动的压臂功能,及旋转机构。
M6/M 9
Φ8
三孔结构
宽32/50 厚8/10
四孔结构
25mm系 列
内径2: 14mm 顶厚 3.5mm
3 工作开展过程
2.2 夹紧单元: 09 铜套:用于连接支撑板与气缸连接板(18-12),压臂与气缸(14-12), 减小摩擦,提高精度,增加使用寿命的作用。
长度:15.5/18.5mm
内径:12mm
外径:14/18mm
3 工作开展过程
2.2 夹紧单元: 10 压臂:用于连接夹紧型块与气缸,起到定位夹紧的作用,属非 标件,根据时间尺寸需求设计。
连接气缸连接板
连接型块
连接气缸
3 工作开展过程
2.2 夹紧单元: 11 上型块:与压臂相连,用于夹紧板件,起到定位的作用,属非 标件,根据时间尺寸需求设计。
上型 块
压臂 板件
3 工作开展过程
2.2 夹紧单元: 12 下型块:与支撑板相连,用于支撑板件,起到定位的作用,属非标 件,根据时间尺寸需求设计。
3 工作开展过程
步骤二:夹检具基本结构及标准件名称(以夹具为例)
手持夹具:一般上件数量为2个,且工 件尺寸较小
1.夹具分类
手动夹具:一般夹持点在5个以内
自动夹具
气控式:普通夹持点在5个以上的 夹具,采用方向控制阀控制夹紧打 开状态
电控式:主线、侧围等生产线, 集成于生产线电控系统中
钣金工艺数据库及其应用系统技术方案-任国辉

钣金材料数据库及其应用系统技术方案一、项目背景基础性科学数据作为科技活动发展的基础和成果,是科学技术滚动发展的平台。
一个好的科学思想、理论假说和应用技术,必须在掌握大量前人资料和科学数据的基础上才能形成,同时也必须在大量相关数据的支撑下才能被证实。
而对科学数据进行系统化的综合分析,进而促进新的科学思维的产生,是实现科技创新的重要方式,并推动交叉学科的发展。
当代高新技术的发展趋势明显呈现出大科学、定量化和注重过程研究等特点,越来越依赖于系统的、高可信度的基本科学数据及其衍生的数据产品。
近年来,钣金工艺在我国航空航天及其他工业领域的应用不断扩大,已逐渐成为构建产品的基础性材料之一,因此,创建一个内容丰富、使用便利、并能够通过电子网络方式提供服务的钣金工艺数据数据库,并广泛应用于研究部门和生产场所,就成为亟待解决的问题。
在这个大背景下,航材院作为航空企业中钣金工艺研究的龙头单位,承接了国防科工委高新工程项目,主要研究航空钣金工艺的数据库支撑技术以及航空钣金工艺制品的数字化制造技术。
最终,建立一个钣金工艺数据管理和应用系统,提供钣金工艺性能的数据测试、分析、存储和应用的统一平台,支持钣金工艺制件的数字化设计、数字化制造、模拟仿真和验证,使之成为国防科技工业创新研究和可持续发展的重要基础。
通过一段时间的工作,航材院基本完成了钣金工艺性能表征及其标准化和测试技术的标准,这些是建立钣金工艺数据库的主要基础。
但是,由于产品研发工作比较紧张,数据库专业人员比较缺乏,在接下来的数据库构建过程中,进度受到了影响。
中航伊萨公司作为航材院的控股单位,具有丰富的数据库工程经验,为多个国防单位提供过相关服务。
因此,双方通过紧密合作、各展所长,将会大大加快数据库建立的速度,确保整个项目的顺利进行。
二、用户需求材料数据本身是一种资源,先进国家如美国非常重视材料数据管理和应用系统的建设和维护,到目前为止,美国已建设了13个国家级的数据系统,形成了庞大的国防工业数据管理和应用体系,为美国国防工业保持其世界领先的竞争力和可持续发展做出了巨大的贡献。
产品制造工艺、检验流转卡
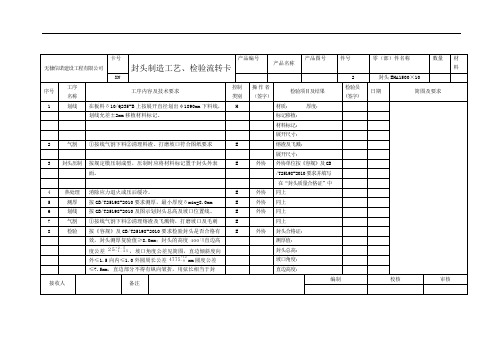
产品名称
产品图号
件号
零(部)件名称
数量
材料
XN
序号
工序
名称
工序内容及技术要求
控制
类别
操作者
(签字)
检验项目及结果
检验员
(签字
日期
简图及要求
1
划线
在板料δ10/Q235-B上展开直径划出Φ1890mm下料线,
H
材质: 厚度:
划线允差±2mm移植材料标记。
标记移植:
材料标记:
外协
展开尺寸:
2
气割
外协
封头合格证:
效,封头测厚复验值≥8.0mm;封头的高度 直边高
测厚值:
度公差 ,坡口角度公差见简图,直边倾斜度向
封头总高:
外≤1.5向内≤1.0外圆周长公差 mm圆度公差
坡口角度:
≤7.5mm,直边部分不得有纵向皱折,用弦长相当于封
直边高度:
接收人
备注
编制
校核
审核
本卡流程路线:技术部→生产部→车间→操作者→检验员→总装→质检部存档
产品编号
产品名称
产品图号
件号
零(部)件名称
数量
材料
XN
2
封头EHA1500×10
序号
工序
名称
工序内容及技术要求
控制
类别
操作者
(签字)
检验项目及结果
检验员
(签字
日期
简图及要求
间隙样板,检查封头内表面的形状偏差,其值:外凸≤
外圆周长:
18.75内凹≤9.3
圆度:
直边倾斜度:
直边皱折:
内表面的形状偏差:
外凸:
- 1、下载文档前请自行甄别文档内容的完整性,平台不提供额外的编辑、内容补充、找答案等附加服务。
- 2、"仅部分预览"的文档,不可在线预览部分如存在完整性等问题,可反馈申请退款(可完整预览的文档不适用该条件!)。
- 3、如文档侵犯您的权益,请联系客服反馈,我们会尽快为您处理(人工客服工作时间:9:00-18:30)。
白车身数模质量要求 白车身数模质量要求 白车身数模质量要求 白车身数模质量要求
24 25 26 27 28 29 30 31 32 33
34 35 NC数模应包含实体数模 失效模式: 1代表不可原谅错误 2代表严重错误 3代表一般错误
外表面符合性检查 白车身数模质量要求 结构符合焊接工艺性 焊接总成焊点分布合理 白车身零部件工艺性审查规定 凸焊螺母、凸焊螺栓工艺可行性 白车身零部件工艺性审查规定 孔功能描述报告符合性检查,不漏孔,无多余孔 安装孔孔位与硬点报告的符合性检查 凸焊螺母和螺栓底孔孔径满足企业要求,凸焊螺母底 孔孔径比螺母规格(公称直径)大1mm,凸焊螺栓底孔 孔径比螺栓公称直径大0.5mm(长城企业标准) 装配密集断面检查,干涉量不得大于0.1mm,安装关系 正确,间隙正确 运动干涉和运动间隙检查满足要求 过孔满足过孔规定:逆向时,过孔按照样车设计;新 设计时,过孔直径在安装孔的直径基础上逐层加大2mm 或3mm 涂装工艺孔及切口的设计及分布是否合理
P P P P P P P P P P P P
P P P P P P P P P P P P
P P P P P P P P P P P P
P P P P P P P P P P P P
P P P P P P P P P P P P
P P P P P P P P P P P P
1 2 2 2 2 2 2 2 2 2 2 1
ZB•Q•0004/03.02
A1-2006 项目 失效 总监 模式 P 1 3 2 3 2 2 2 P P P P P P P P P P P P P P P P P P P 3 3 2 2 2 2 2 2 2 2 2 2 3 1 1 1
自检 校对 审核 质检 总布置 总师 P P P P P P P P P P P P P P P P P P P P P P P P P P P P P P P P P P P P P P P P P P P P P P P P P P P P P P P P P P P P P P P P P P P P P P P P P P P P P P P P P P P P P P P
三维数模设计规范 文件命名和层设置
P P
白车身数模质量要求 白车身设计规则 白车身设计规则 白车身设计规则 白车身零部件工艺性审查规定 白车身零部件工艺性审查规定 白车身零部件工艺性审查规定 白车身零部件工艺性审查规定 白车身设计规则 白车身零部件工艺性审查规定 白车身零部件工艺性审查规定
P P P P P P P P P P P P P P P P P P
钣金车身工艺/铸造/NC数模 Checklist流转单
项目代码: 序 号 1 2 3 4 5 6 7 8 9 10 11 12 13 14 15 16 17 18 19 20 21 22 23 检查内容 是否根据确定方案进行设计 数模分层符合公司标准 明细表中的件号、数模是否对应 电子文档命名、版本控制是否符合规范 零部件的坐标系的统一性(模型一律采用整车坐标 系) 对钣金件检查有无料厚线,并按明细表核对料厚线长 度是否正确 料厚线方向是否正确:原则上规定外板走向为向内, 内板走向为向外 数模的焊接面是否为offset面 数模是否干涉,根据料厚判断间隙是否正确 冲压方向是否合理 拉延最大相对深度是否合理 工艺缺口是否合理 拉延圆角是否合理 孔边距是否合理 焊接边宽度是否合理 焊点间距是否合理 板材层数及料厚比是否合理 检查数模是否存在负角 检查孔的设计是否合理 数模包含的信息是否全面,其中应包括倒角的数模以 及料厚线,并保留未倒角的数模 焊接关系是否与主断面符合 密封结构是否与主断面符合 断面结构是否与主断面符合 编号: 参照标准(企业标准、国家标准)标准号 版本