粗轧区支承辊过跨车功能描述-Rev_00
粗轧操作规范----常见问题及处理办法
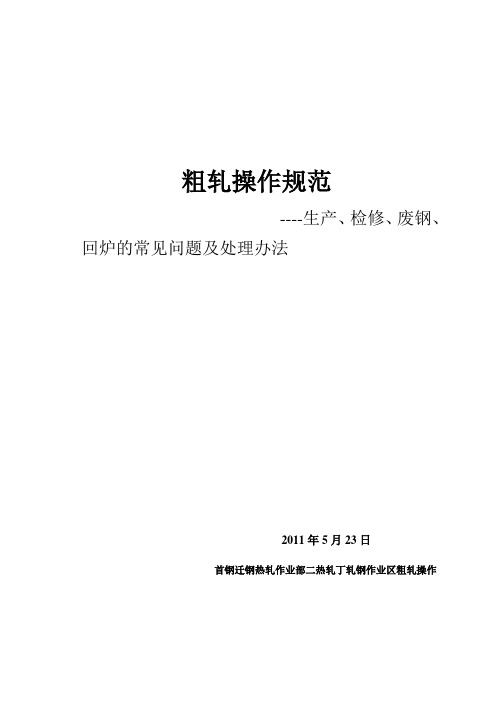
粗轧操作规范----生产、检修、废钢、回炉的常见问题及处理办法2011年5月23日首钢迁钢热轧作业部二热轧丁轧钢作业区粗轧操作摘要目前钢铁企业市场的不景气和竞争愈演愈烈,避免操作类回炉和废钢是减少停机时间、增加机时产量、节能降耗降成本的一项重要举措,作为粗轧操作人员更应规范化操作,以主人公自居。
本文阐述粗轧区域人员在生产、检修、回炉及废钢时出现的常见问题及操作规范。
关键字:粗轧常见问题操作规范ABSTRACTThe current slump in the steel business market and competition intensified, reducing scrap is recycled and reduce downtime, increase machine production, energy saving is an important cost reduction initiatives, as a rough rolling operation the operator should be standardized to the hero itself .In this paper, the regional staff in the production of rough rolling, maintenance, recycled and scrap and common problems that occur when practices.Keywords: Rough Mill,Frequently questions,Operating目录第一章生产中注意事项及常见问题处理方法1.1出炉板坯数据确认 (5)1.2二级设定常见问题处理预案....... ............ (6)1.3粗轧轧制注生产中意事项 (9)1.4 板坯扣翘头控制......... ..... .......... ..... .. (11)1.5板型及RT2温度控制................. . (11)1.5.1 RT2温度控制 (11)1.5.2 板型控制 (11)1.6冷宽控制................................... ..... . (12)第二章检修、恢复及换辊常见问题2.1 停机、停泵操作规范 (13)2.1.1 停机 (13)2.1.2 停泵 (13)2.2更换R1、R2工作辊操作规程及常见问题处理预案 (14)2.2.1 更换R1工作辊 (14)2.2.2 更换R2工作辊 (15)2.2.3 更换R2支撑辊 (16)2.2.4 换辊常见问题及注意事项 (16)2.3 检修恢复操作注意事项 (17)2.3.1恢复转车操作流程 (17)2.3.2恢复转车注意事项 (19)2.4输入辊单、标定及压铜棒操作规范............... .... (19)2.4.1输入辊单......。
RM单词汇总
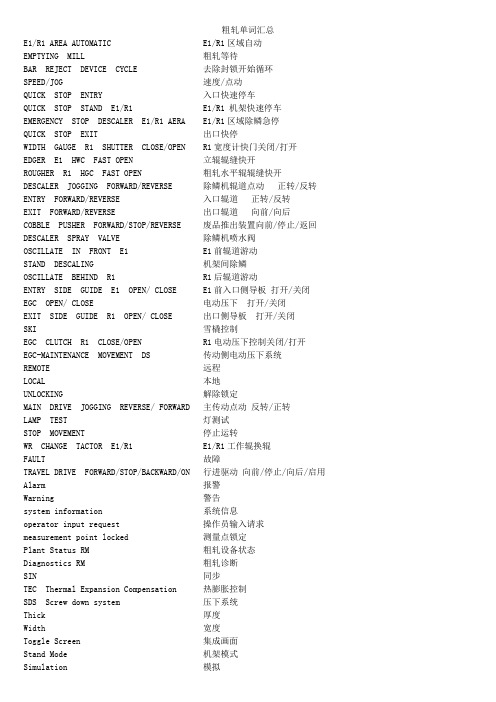
粗轧单词汇总E1/R1 AREA AUTOMATIC E1/R1区域自动EMPTYING MILL 粗轧等待BAR REJECT DEVICE CYCLE 去除封锁开始循环SPEED/JOG 速度/点动QUICK STOP ENTRY 入口快速停车QUICK STOP STAND E1/R1 E1/R1 机架快速停车EMERGENCY STOP DESCALER E1/R1 AERA E1/R1区域除鳞急停QUICK STOP EXIT 出口快停WIDTH GAUGE R1 SHUTTER CLOSE/OPEN R1宽度计快门关闭/打开EDGER E1 HWC FAST OPEN 立辊辊缝快开ROUGHER R1 HGC FAST OPEN 粗轧水平辊辊缝快开DESCALER JOGGING FORWARD/REVERSE 除鳞机辊道点动正转/反转ENTRY FORWARD/REVERSE 入口辊道正转/反转EXIT FORWARD/REVERSE 出口辊道向前/向后COBBLE PUSHER FORWARD/STOP/REVERSE 废品推出装置向前/停止/返回DESCALER SPRAY VALVE 除鳞机喷水阀OSCILLATE IN FRONT E1 E1前辊道游动STAND DESCALING 机架间除鳞OSCILLATE BEHIND R1 R1后辊道游动ENTRY SIDE GUIDE E1 OPEN/ CLOSE E1前入口侧导板打开/关闭EGC OPEN/ CLOSE 电动压下打开/关闭EXIT SIDE GUIDE R1 OPEN/ CLOSE 出口侧导板打开/关闭SKI 雪橇控制EGC CLUTCH R1 CLOSE/OPEN R1电动压下控制关闭/打开EGC-MAINTENANCE MOVEMENT DS 传动侧电动压下系统REMOTE 远程LOCAL 本地UNLOCKING 解除锁定MAIN DRIVE JOGGING REVERSE/ FORWARD 主传动点动反转/正转LAMP TEST 灯测试STOP MOVEMENT 停止运转WR CHANGE TACTOR E1/R1 E1/R1工作辊换辊FAULT 故障TRAVEL DRIVE FORWARD/STOP/BACKWARD/ON 行进驱动向前/停止/向后/启用Alarm 报警Warning 警告system information 系统信息operator input request 操作员输入请求measurement point locked 测量点锁定Plant Status RM 粗轧设备状态Diagnostics RM 粗轧诊断SIN 同步TEC Thermal Expansion Compensation 热膨胀控制SDS Screw down system 压下系统Thick 厚度Width 宽度Toggle Screen 集成画面Stand Mode 机架模式Simulation 模拟Jogging Selection 点动选择Pass counter 道次数Release Drives 传动释放Ski Adjustment 雪橇调整功能ACK Fault Acknowledeg 故障确认Work roll cooling 工作辊冷却Feed roll cooling 机架辊冷却Backup roll cooling 支承辊冷却Calibration 标定Measured value 测量值Correction value 偏差值AWC 自动宽度控制roll change preselect 换辊预选择service 服务Current 电流media systems 介质系统position control 位置控制THC thickness control 厚度控制Descaler unit table 除鳞箱辊道Entry Extend table 入口延伸辊道Entry work roll table 入口工作辊道HWC Hydraulic Width Control 液压宽度控制Force transducer 压力传感器Servo valves 伺服阀Check valves 截止阀SSC Short Stroke control 短行程控制Head/tail 头/尾Collapsed 收缩Automatic/ Manual 自动/手动HGC Hydraulic gap control 液压辊缝控制Clutch open 离合器打开Compensation 补偿Set point position 设定位置Balance 平衡Tracking Reset 跟踪复位Work roll balancing 工作辊平衡Slag flushing water 冲渣水Exit side-spray 出口侧喷Hysteresistest 刚度测试Bending force 弯辊力Relative position 相对位置Cm 物料模数Cg 轧机模数Position transducer 位移传感器Limit switch 极限开关Block valve 封锁阀Relief valve 泄压阀Single POS 单侧位置Filter clogged 过滤塞Brake closed 制动系统关闭Low voltage 低电压Spindle balancing 接轴平衡WR change sequence 工作辊换辊顺序Spindle head supporting 接轴头部提升Load cell 压头Hard ware 硬件Communication 通讯Inactive 未激活Maintenance 维护Reference 参考CLS central lubrication system 中央润滑系统Roll Diameters 辊径Speed Parameters 速度参数Reset transd.error 传感器故障复位Tilting 倾斜TRANSFER BAR 中间坯BUR TRANSFER CAR 支承辊过跨车。
粗轧机R2工作辊窜动分析与治理

79中国设备工程Engineer ing hina C P l ant中国设备工程 2018.05 (上)攀钢西昌钢钒公司2050mm 热轧生产线于2009年开始动工,历时两年多,于2011年12月投产,粗轧机R2为四辊轧机,采用往复式轧制方式将板坯轧薄。
投产后,时常发生在轧制过程中工作辊轴向窜动的问题,最大窜动量达4mm,导致大电机止推瓦异常磨损,严重影响轧机大电机的稳定运行和生产的正常进行。
1 工作辊轴向窜动的影响1.1 工作辊窜动对设备产生的危害大电机通过十字万向接轴将轧制力矩传递给工作辊,十字万向接轴由剖分轴承支撑。
工作辊窜动时,剖分轴承将承受较大的轴向力,当其超出使用极限时,剖分轴承就会发生损坏,引起3天左右的停机。
工作辊窜动量过大时,该轴向力还会通过十字万向节轴传递到大电机导致大电机转子发生轴向位移。
当轴向窜动大于3mm 时,过大的作用力将直接作用于巴氏合金止推瓦,导致巴氏合金止推瓦受损,严重时可能直接将其烧损,甚至造成大电机损坏;此情况在粗轧机的运行中已有所发生,如2012年9月30日某热轧带钢厂1780线R2下辊主电机,由于轧钢时轴向窜动大将止推盘和止推瓦损坏,影响生产29小时31分钟,给企业带来了很大损失。
1.2 工作辊窜动对产品质量的影响在轧制过程中,由于工作辊的轴向窜动,使板坯在上下工作辊间的变形多样化,在生产中极易发生跑偏,产生中间轧废,甚至引起事故,如板坯将中间坯推钢机推头撞坏的事故曾多次发生和撞坏R2出口工作辊道电机。
当粗轧工作辊窜辊现象比较严重时,轧出的中间坯容易出现单边或双边厚度超差,同时还会对板形产生影响,如镰刀弯、S 弯等严重影响产品质量的问题;由于板形的遗传性,产品经精轧机组轧制时无法完全消除其粗轧产生的镰刀弯、S 弯等,轻者造成成品浪形,重者直接导致精轧废钢。
1.3 工作辊窜动对轧制成本的影响由于工作辊窜动超标引起废钢和产品质量不合格问题严重影响到轧制成本。
粗轧机区域1

粗轧机(工)换辊程序
选择粗轧机换辊模式。 接轴定位并关闭轧辊冷却水。 打开上下工作辊清辊器(WIPER),下工作辊平衡卸荷。 压下螺丝抬升至上限(上辊系和接轴平衡同时抬升),支撑辊安全锁栓 锁紧。 上接轴抬升到位并锁定。 工作辊换辊轨道抬升(下接轴平衡同时抬升)。 下接轴夹紧缸夹紧,下接轴平衡缸卸荷。 工作辊推拉缸推至轧机后挂钩并将下工作辊轴端挡板打开。
电动小车
移动行程:
约20m 移动速度: 17.8m /s 传动功率: 15kW@580rpm 速比: 47.4:1 工作辊直接由电动小车送入轧辊间
支撑辊换辊系统
推拉缸行程:
系统压力:
换辊速度:
约6500mm 160bar 最小35 mm /s 最大70 mm /s
系统压力: 160bar 操作速度: 25mm/s l 轨道的提升和下降由液压缸完成 l 轨道上装有耐磨衬板
工作辊,工作辊轴承座及轴承
辊子直径:
l l l l l
最大1200mm 最小1080mm 辊身长度: 1750 mm 辊子材质: 无限冷硬球磨铸铁 辊子硬度: 60-65肖氏硬度 轴承座材质: 铸钢 轴承类型: 4列圆锥滚子轴承 工作辊材质为无限冷硬复合球墨铸铁 工作辊轴承座由铸钢制成,装有可更换耐磨衬板 工作辊轴承采用四列圆锥滚子轴承 非传动侧的工作辊下轴承座上,装有与换辊油缸连接的卡座 轴承的润滑为手动干油润滑
支撑辊,支撑辊轴承座及轴承
l 支撑辊材质为锻钢
l 支撑辊轴承座为铸钢件
l 支撑辊轴承为摩根轴承 l 轴承座表面润滑由集中干油润滑系统提供 l 油膜轴承通过快速接头与稀油润滑系统连接 粗轧机和精轧机的支撑辊和油膜轴承完全相同,可以互换
精轧区板形功能说明

选择检修 HMI选择手动模式 在轧机咬钢后 两侧(入口侧和出口侧)窜量偏差过大报警 窜量极限位 急停 快停 自动模式下,上下辊、入口侧出口侧保证液压同步。 检修模式 在HMI上选择检修模式后,窜辊液压缸会自动回到零位。 急停快停模式 在发生紧急情况或设备失控时,需立即拍下急停或者快停: 拍下快停/急停:窜辊液压缸会自动锁定,保持在当前位置。
冷却影响模型得到的板形平直度良好条件。
平直度偏差信号是目标平直度与实测平直度的差,通过模式识别后
确定板形平直度缺陷的类型和大小。
根据平直度偏差信号反馈调节弯辊力。
弯辊力反馈调节增量的计算公式为:
式中
BF = KBFF(FLATT - FLATM)
FLATT:目标平直度(根据带钢张力补偿和温度分布补偿以及层流对 平直度冷却影响模型得到的板形平直度良好条件)
2.1 F1-F7工作辊弯辊
2.1.1 弯辊功能
通过向工作辊施加液压弯辊力,使轧辊产生附加弯曲,来瞬时地
改变轧辊的有效凸度,从而改变承载辊缝形状和轧后带钢的延伸沿横向
的分布,以补偿由于轧制压力等工艺因素的变化而产生的辊缝形状的变
化。
工作辊弯辊和平衡是同一个液压缸,由伺服阀液压系统(板形控
制器)和开关阀液压系统(换辊控制器)来控制,任意时刻只能由其中
2.1.5 工作辊弯辊的操作
HMI操作 弯辊投入选择:HMI上选择需要投入弯辊的机架,如果液压 系统正常,并且换辊控制器允许投入弯辊,那么选择的机架 进入弯辊方式。
操作台操作 弯辊力手动调节:在操作台上通过“弯辊力增大/减小”按钮调 节弯辊力,自动模式下操作台手动调整优先。 急停快停操作:拍下精轧快停/急停时,自动切换到平衡方 式。
粗轧篇
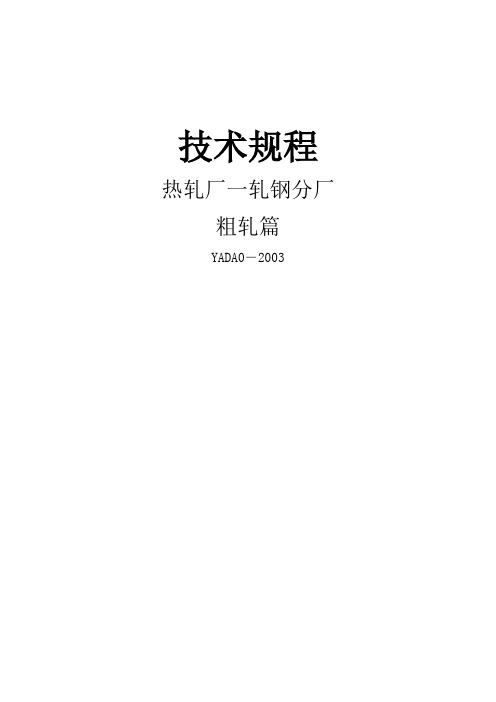
3)最大轧制力和轧辊开度 机架 最大轧制力 t 行程 mm 4)轧辊尺寸范围 机架 Rl R2 R3 R4
R1 3000 350
R2 4000 350
R3 4000 350
R4 4000 350
工作辊Φmm*Lmm (1350-1200)*2050 (1200-1080)*2050 (1200-1080)*2050 (1200-1080)*2050
1.功能说明 除鳞系统主要作用是通过高压除鳞水进行板坯粗大氧化铁皮的去除,确保后道工序轧制 时产品表面质量。 2.除鳞设备及工艺参数 1)除鳞设备的布置 在 El 前的辊道上有一个除鳞箱,箱内上下各有两根集管,改造后上下集管前后错开分 布。 在 E1 前侧面,每侧有两个喷嘴(用于坯侧面除鳞) 在 Rl 前,上下各有一根集管。 在 R2 前,上下各有一根集管。 在 R2 后,上下各有一根集管。 在 E3 前,上下各有一根集管。 在 E4 前,上下各有一根集管。 2)除鳞设备参数(参数说明见示意图) a)1#除鳞箱 每根集管喷嘴数 20 个 喷嘴间距(约) 100 mm 坯与喷嘴垂直间距(约) 200 mm 水嘴型号:694.807。 散射角(α):27-30°。 偏转角(λ):15°。 倾斜角(β):15°。 b)机架间除鳞 集管喷嘴数:R1:2*17 个,R2:2*18 个,R3:上 15 个/下 19 个,R4:上 13 个/下 19 个. 喷嘴间距(约) R1: 118mm, 111mm, 上 133mm/下 105mm, 上 154mm/下 105mm. R2: R3: R4: 水嘴型号:R1:694.847,R2:694.807,R3R4 上:694.727,R3R4 下:694.887。 散射角(α):27-30°。 偏转角(λ):15°。 倾斜角(β):15°。 垂直高度(约) :R1:H 上 360mm,H 下 160mm, R2:H 上 230mm,H 下 210mm, 1. R3:H 上 395mm,H 下 210mm, R4:H 上 400mm,H 下 200mm. 3)除鳞水压力 160bar 4)水嘴更换周期 a) 除鳞箱、R1 前、R3R4 前:一年。 b) R2 前:四个月。 c) R2 后:二年。
1 一、粗轧主要设备及功能

在轧机运行或停车状态均可进行R1轧机的标 定,因工作辊直径较小时轧机上下接轴在工作辊 压靠状况会出现干涉,故要求当R1工作辊直径小 于915mm时采用静态清零,当R1工作辊直径大于 915mm时采用动态清零。
减 速 开 始
抛 钢 速 度
减 速 停 转
时间
三角形速度制度图
17
三、粗轧机的速度制度
• 3、轧制速度的给定 手动轧制时 手动轧制时,水平轧制速度由脚踏主令控制器控制,既 当“主机速度选择旋钮”选至一定档位时,脚踏主令控制 器可在该档位能达到的最高速度范围内控制轧机速度;立 辊轧机随水平轧机联动。 半自动轧制时 自动轧制时,操作工在操作台面选定速度档位后,水平 轧机和立辊轧机速度由PLC控制。 自动轧制时 自动轧制时粗轧机的速度由二级模型给出,但操作工可 以在L2HMI跟踪画面通过速度升降按钮选择需要的轧制速 度。
第三道次定位完成
R2第三道次带坯头部 经 HMD210 检得, R2 速度基准由热卷箱给 出,直到R2抛钢
R2轧制结束
侧压、压下、侧导板自动 定位到安全位置,以待钢 速度等待下一块钢的轧制
14
三、粗轧机的速度制度
• 粗轧机根据所轧带坯的长短有梯形和三角 形两种速度制度,如果所轧带坯的长度超 过临界长度时为梯形速度制度,当所轧带 坯长度小于临界长度时为三角形速度制度, 其速度制度图如下:
25
六、粗轧轧制时常见的异常情况
• 2、机架内堆钢 原因:
1)由于侧压、侧导板开口度基准或侧压误动作引起侧压、 侧导板开口度过小,偶道次轧制带坯不能顺利通过立辊轧机、 侧导板,导致带坯在立辊轧机、水平轧机间堆钢。 2)偶道次板形严重不良,带坯侧弯撞击立辊轧机导卫装置, 撞击机前侧导板或辊道边板引起带坯在立辊轧机、水平轧机间 堆钢。 3)偶道次扣头、翘头严重,偶道次的头部撞击机架内设备 引起立辊轧机、水平轧机间堆钢。 4)机架内护板过高、水梁位置过低,偶道次轧制带坯头部 撞击护板或水梁引起立辊轧机、水平轧机间堆钢。 5)奇道次轧制由于立辊与水平辊速度不匹配,立辊速度高 于水平辊速度引起立辊轧机、水平轧机间堆钢。
热轧带钢设备及控制(粗轧平辊轧机) ppt课件
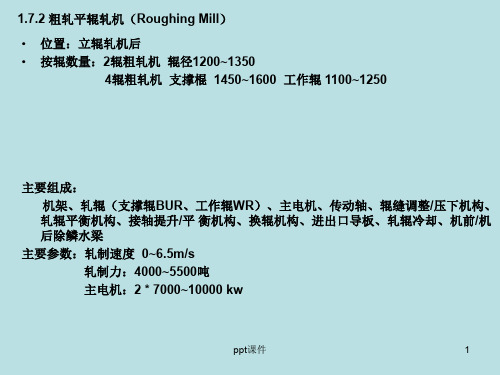
HMD
314
402A/B
301
HMD
13,150
207
HMD
302A/B
11,700
304 13,450
HMD 303A/B
HMD 305
HMD 306
HMD 307
HMD 308
HMD 309
HMD 310
HMD 311
HMD 312
11.225
HMD
HMD 315A/B
313455 36
7.置
HMD 314
HMD 315A/B
E2/R2 SECTIONAL VIEW
11,225 9,425
7,625 E2
11,850
R2
4550
HMD 401A/B
DESCALING
WG
COUNTER SPRAY
SPRAY
DESCALING
HOOD
WG
900 900
1,550
8,190
8,190
8,190 10,900 25 00 00 10,900 9327.5 8,190 8,190 8,190
HSB SP
ppt课件
10
粗轧区传感器、仪表布置
HMD HMD HMD HMD HMD HMD HMD 201 202 203 204 205 206 207
HMD
HMD
HMD
NO.1 F'CE
C6 C7 D1 D2
OSCILATION D3 D4 D5 G1 G2 G3 G4 G5 G6 G7 G8
H1 H2 H3 H4 H5
HSB
SP
E2 R2
OSCILATION H6 H7 H8 H9 H10 H11 H12 H13 FSB
粗轧机功能描述-rev01

Job 0053 ContractualitemZY-2004-66-NE-4-1ERZHONG item(04)325301TitleRoughing Mill Functional DescriptionApprovalsRemarks02 05-01-0501 04-12-8 ERZHONG ISSUE OF DETAIL DESIGNPHASEHu YiGe XianyuLu Qingchun Qi Xiaohu00 04-07-22 ERZHONG ISSUE OF DESIGN PHASE Hu YiGe XianyuLu Qingchun Qi XiaohuRev. File Date Revisions description Drawn Checked Approved1设备总体概况3 2设备分项说明32.132M2005-2021粗轧机本体(13253.204) (3)2.1.132M2005: R1 - MILL SPINDLE HEAD HOLDER (13253.204.11) (3)2.1.1.1设备概况 (3)2.1.1.2设备结构及传动示意图 (3)2.1.1.3技术参数 (3)2.1.1.4控制要求 (3)2.1.1.5电机和电器工艺检测仪表 (3)2.1.1.6液压控制系统电磁阀动作表及相关信息 (3)2.1.234M2006: Electromechanical Screwdown(13253.204.03) (3)2.1.2.1设备概况 (3)2.1.2.2设备结构及传动示意图 (3)2.1.2.3技术参数 (3)2.1.2.4控制要求 (3)2.1.2.5电机和电器工艺检测仪表 (3)2.1.332M2007: R1 - CLAMPING MECHANISM (13253.204.01) (3)2.1.3.1设备概况 (3)2.1.3.2设备结构及传动示意图 (3)2.1.3.3技术参数 (3)2.1.3.4控制要求 (3)2.1.3.5电机和电器工艺检测仪表 (3)2.1.3.6液压控制系统电磁阀动作表及相关信息 (3)2.1.432M2008: R1 W.R. RAILS LIFTING(13253.204.06) (3)2.1.4.1设备概况 (3)2.1.4.2设备结构及传动示意图 (3)2.1.4.3技术参数 (3)2.1.4.4控制要求 (3)2.1.4.5电机和电器工艺检测仪表 (3)2.1.4.6液压控制系统电磁阀动作表及相关信息 (3)2.1.532M2009: R1 W.R. BALANCE(13253.204.01) (3)2.1.5.1设备概况 (3)2.1.5.2设备结构及传动示意图 (3)2.1.5.3技术参数 (3)2.1.5.4控制要求 (3)2.1.5.5液压控制系统电磁阀动作表及相关信息 (3)2.1.632M2010: R1 BUR. BALANCE(13253.204.04) (3)2.1.6.1设备概况 (3)2.1.6.2设备结构及传动示意图 (3)2.1.6.3技术参数 (3)2.1.6.4控制要求 (3)2.1.6.5电机和电器工艺检测仪表 (3)2.1.6.6液压控制系统电磁阀动作表及相关信息 (3)2.1.732M2011: R1 HAGC (13253.204.12) (3)2.1.832M2002: R1 AC MAIN DRIVE(13253.205) (3)2.1.8.1设备概况 (3)2.1.8.2设备结构及传动示意图 (3)2.1.8.3技术参数 (3)2.1.8.4控制要求 (3)2.1.8.5电机和电器工艺检测仪表 (3)2.1.8.6液压控制系统电磁阀动作表及相关信息 (3)2.1.932M2013: R1 阶梯垫调整及支承辊换辊滑台 (13253.204.07) (3)2.1.9.1设备概况 (3)2.1.9.2设备结构及传动示意图 (3)2.1.9.3技术参数 (3)2.1.9.4控制要求 (3)2.1.9.5电机和电器工艺检测仪表 (3)2.1.9.6液压控制系统电磁阀动作表及相关信息 (3)2.1.1032M2015: R1 ENTRY /EXIT STRIPPERS AND GUIDES (13253.204.05) (3)2.1.10.1设备概况 (3)2.1.10.2设备结构及传动示意图 (3)2.1.10.3技术参数 (3)2.1.10.4控制要求 (3)2.1.10.5电机和电器工艺检测仪表 (3)2.1.10.6液压控制系统电磁阀动作表及相关信息 (3)2.1.1132M2016: R1 – ENTRY/EXIT FEED ROLLERS (13253.204.08) (3)2.1.11.1设备概况 (3)2.1.11.2设备结构及传动示意图 (3)2.1.11.3技术参数 (3)2.1.11.4控制要求 (3)2.1.11.5电机和电器工艺检测仪表 (3)2.1.1232M2013:油膜轴承润滑监测系统 (3)2.1.12.1控制要求 (3)2.1.12.2电机和电器工艺检测仪表 (3)2.1.1332M2021:工作辊冷却装置 (3)2.1.13.1设备概况 (3)2.1.13.2设备结构及传动示意图 (3)2.1.13.3技术参数 (3)2.1.13.4控制要求 (3)2.1.13.5电机和电器工艺检测仪表 (3)5) 32.1.1432M2021:支承辊冷却装置 (3)2.1.14.1设备概况 (3)2.1.14.2设备结构及传动示意图 (3)2.1.14.3技术参数 (3)2.1.14.4控制要求 (3)2.1.14.5电机和电器工艺检测仪表 (3)2.232M2101: R1-W.R.CHANGING SYSTEM (13253.206) (3)2.2.132M2101: R1-W.R.CHANGING SYSTEM (3)2.2.1.1设备概况 (3)2.2.1.2设备结构及传动示意图 (3)2.2.1.3技术参数 (3)2.2.1.4换工作辊步序 (3)2.2.232M2101:工作辊液压缸推拉装置 (3)2.2.2.1设备概况 (3)2.2.2.2设备结构及传动示意图 (3)2.2.2.3技术参数 (3)2.2.2.4控制要求 (3)2.2.2.5电机和电器工艺检测仪表 (3)2.2.2.6液压控制系统电磁阀动作表及相关信息 (3)2.2.332M2101:工作辊横移装置 (3)2.2.3.1设备概况 (3)2.2.3.2设备结构及传动示意图 (3)2.2.3.3技术参数 (3)2.2.3.4控制要求 (3)2.2.3.5电机和电器工艺检测仪表 (3)2.2.3.6液压控制系统电磁阀动作表及相关信息 (3)2.2.432M2101工作辊推拉缸翻转装置 (3)2.2.4.1设备概况 (3)2.2.4.2设备结构及传动示意图 (3)2.2.4.3技术参数 (3)2.2.4.4控制要求 (3)2.2.4.5电机和电器工艺检测仪表 (3)2.2.4.6液压控制系统电磁阀动作表及相关信息 (3)2.2.532M2101:工作辊轨道摆动装置 (3)2.2.5.1设备概况 (3)2.2.5.2设备结构及传动示意图 (3)2.2.5.3技术参数 (3)2.2.5.4控制要求 (3)2.2.5.5电机和电器工艺检测仪表 (3)2.2.5.6液压控制系统电磁阀动作表及相关信息 (3)2.332M2102: R1支承辊换辊系统(13253.206) (3)2.3.1.1设备概况 (3)2.3.1.2设备结构及传动示意图 (3)2.3.1.3技术参数 (3)2.3.1.4控制要求 (3)2.3.1.5电机和电器工艺检测仪表 (3)2.3.1.6液压控制系统电磁阀动作表及相关信息 (3)1 设备总体概况R1四辊可逆粗轧机是设置在热连轧带钢生产线粗轧区的关键设备,R1四辊可逆粗轧机位于E1立辊轧机之后、粗轧机输出辊道之前,与E1立辊轧机、粗轧机前后工作辊道、侧导板配合完成从连铸坯料轧制到中间坯的轧制过程。
热轧粗轧区工艺设备介绍
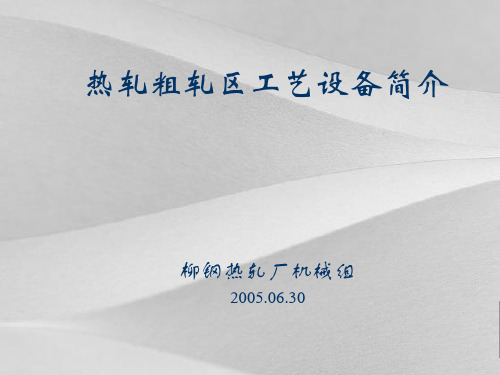
英国Lackenby厂外貌
C
O
R
米德克尔利斯夫兰堡--雷 德卡郡
精轧精 精电轧 轧气电 电室气 气室 室
26 2266
29 2299
30 3300
除鳞除除箱鳞鳞箱箱
粗轧粗粗机轧轧机机 测宽测测仪宽宽仪仪
板头板板整头头形整整形形
测厚测测仪厚厚仪仪
75t 7755tt
F1 FF11 F2 FF22 F3 FF33 F4 FF44 F5 FF55 F6 FF66
飞剪飞 飞剪 剪除鳞除 除箱鳞 鳞箱 箱
产品名称
碳素结构钢 优质碳素结
构钢 低合金结构
钢 管线钢
合计
代表钢种 Q215、Q235、
Q255 08Al、20
Q345
X60
产品规格,mm
2.0~25×600~ 1840
2.0~25×600~ 1840
2.0~25×600~ 1840
2.0~12×600~ 1840
计划年产 量,(t/a) 600,000
热轧粗轧区工艺设备简介
柳钢热轧厂机械组
2005.06.30
目录
英国Lackenby厂设备拆运概述 粗轧区工艺流程 粗轧区主要设备概况 其他设备 利旧设备修配改 工程建设情况
第一部分 设备拆运概述
英国Lackenby厂概况
CORUS英国有限公司Lackenby热轧卷板厂位于
英国中部东海岸Redcar镇。 该厂于二十世纪六十年代建成,七十年代初由万
粗轧机工作原理

粗轧机工作原理全文共四篇示例,供读者参考第一篇示例:粗轧机是钢铁行业中常用的一种设备,它主要用于将热轧坯料进行初步压制和变形,以便后续进一步加工。
粗轧机的工作原理是通过辊子的转动和下压,将坯料进行压扁和延展,使得坯料的形状和尺寸得到初步调整。
下面我们一起来详细了解一下粗轧机的工作原理。
粗轧机由机架、辊子、传动机构、压下机构和控制系统等部分组成。
机架是整个设备的支架,辊子通过传动机构连接到电动机,并可以通过控制系统控制辊子的转动和下压。
压下机构则用于调整辊子的下压力,以适应不同的坯料厚度和材质。
在工作时,坯料首先经过加热炉进行加热,使其达到适合进行轧制的温度。
然后,坯料被送入粗轧机的进料口,并通过辊子的运转和下压,逐渐被压扁和延展。
辊子的设计和排列方式会使得坯料在经过不同辊子组合的过程中得到不同程度的压制和变形,从而实现对坯料形状和尺寸的调整。
通过连续的轧制过程,坯料经过粗轧机后会变得更加平整和延展,同时也会减小其厚度和宽度。
这样处理后的坯料可以进一步送入中轧机和精轧机进行进一步加工,最终得到符合要求的板材或型材。
粗轧机的工作原理可以总结为:通过辊子的转动和下压,将坯料进行压制和变形,从而使其形状和尺寸得到初步调整。
粗轧机在钢铁生产过程中起到至关重要的作用,不仅能提高生产效率,还可以提高产品质量和减少生产成本。
通过不断优化和改进粗轧机的设计和工艺流程,可以进一步提升钢铁行业的竞争力和生产效益。
粗轧机作为钢铁生产中的重要设备,其工作原理简单而有效。
通过合理的设计和操作,粗轧机可以对坯料进行有效的初步加工和准备,为后续加工工艺奠定基础。
希望通过本文的介绍,读者能对粗轧机的工作原理有更加深入的了解,从而更好地应用于生产实践中。
【字数超过2000】第二篇示例:粗轧机是金属材料生产中常用的一种机械设备,其作用是对金属材料进行初步的轧制和塑性加工,将原料进行初步的压缩和变形,为后续的加工工序做好准备。
粗轧机主要应用于钢铁、有色金属等材料的轧制加工,广泛用于冶金、建筑、机械制造等领域。
2250热轧板厂120t钢卷过跨车控制系统改进
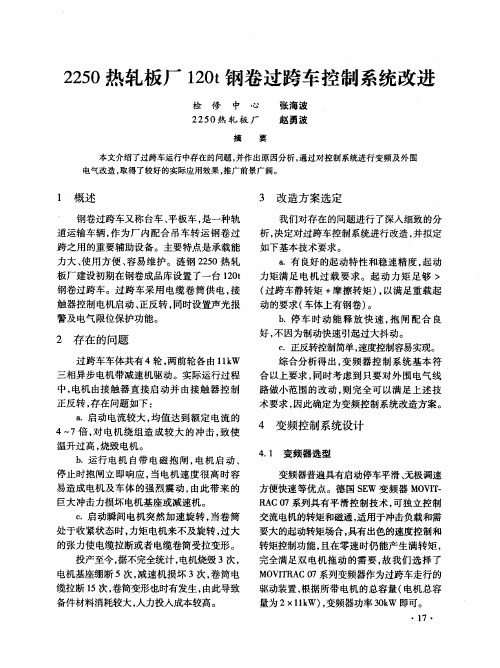
P0 8 8=接 通 (4 2 V输 出电压 ) 。
时外围监控信号不多 , 控制元器件稀少 , 无需 P C直接采用端子源 控制方式来控制 变频 L
器, 既简单又经济。具体变频控制原理 图如
4— 倍 , 电机绕组造成 较大 的冲击 , 使 7 对 致 温升 过 高 , 毁 电机 。 烧 4 1 变 频器 选型 . b .运 行 电 机 自带 电 磁 抱 闸 , 机 启 动 、 电 停止 时 抱 闸立 即响 应 , 电机 速 度很 高 时 容 当 变频 器普遍具 有启动停车平滑 、 极调速 无
由于过跨车车体轮距大约 2米, 较短 , 速 度控制要求精度不高, 因此变频控制采用一 台变频器驱动两台电机 即一拖二的方式 , 同
P 0 =1 端子分配: 62 ( 使能) ;
P0 4 端子分配 : 63= ( 转速 1 ; ) P0 64=5 端子分 配 : 速 2 ; ( 转 ) 一
a 为了保证控制 电源的稳定性 , . 所有 的
控制 电源都 由增加 的西 门子稳 压 电源 ST P IO 提供 。 b .改造 前 抱 闸 电源 直 接 由电 机 电缆 线 上取 30 改 造 时增 加 一 控 制 接 触 器 , 设 8V, 增 2根 单独 的抱 闸 电缆 线 , 同时 对 抱 闸 的打 开 释放 时间进 行 控制 , 加 了一个 断 电延 时 继 增 电器 , 这样 避免 了停 车抱 闸立 即 动作 导 致 的
备件 材料消耗较 大 , 人力投 入成本较 高 。
交流电机的转矩和磁通, 适用于冲击负载和需 要大的起动转矩场合, 具有出色的速度控制和 转矩控制功能, 且在零速时仍能产生满转矩 ,
支承辊支撑着工作辊

对轧辊制造提出要求,是为了保证轧辊的机械强度、带钢的 表面质量和轧辊的安装精度。
(1)保证轧辊机械强度所规定的技术要求。保证轧辊材料的 化学成分及力学性能;轧辊铸造时,不允许有铸造缺陷,如气孔、 砂眼、裂纹、夹渣及偏析等;锻造轧辊的坯料必须经多方均匀锻 压,锻压比不得小于3;热处理后的残余应力应最小;保证轧辊 接触强度所需的表面硬度。
冷轧过程中,轧辊表面承受着很大的挤压应力和强烈的磨损,高 速轧制时,卡钢、过烧等会造成辊面裂纹。因此,冷轧工作辊应具 有极高而均匀的硬度,一定深度的硬化层,以及良好的耐磨性与抗 裂性。轧辊具有良好的耐过烧、抗裂性是延长轧辊寿命的主要因素。 降低轧辊硬度,虽能改善抗裂性,但耐磨性降低。因此,必须正确 选择轧辊的表面硬度。
——几何形状:无论张开或缩起,必须为一整圆不能有缺口。
30
——稳定性:对于大张力薄带卷取,有产生塌卷的可能,这是不能允许 的。
——纠偏控制:一般采用光电元件——伺服阀,进行在线纠偏。
2.2 冷带卷取机的结构
一般以卷筒的结构进行分类。
(1)实心卷筒卷取机:其结构最简单,刚度大,可受大 张力;但无法胀缩故无法卸卷。
按张力的大小,可分为:轧制及平整线上的大张力卷取机及精整线(退 火、酸洗、涂层作业线)上的卷取机。其卷筒大多是棱锥式、弓形块式。 也有用实心卷筒的。 2.1.2工艺特点 ——张力:σ0以可逆式轧机为最高,比张力最大达0.5~0.8。而精整线为 0.05~0.10最低(比张力定义为张力与相对应材料的屈服极限之比)。
冷轧机械设备
因轧薄和板形控制的需要,出现了各种各样的板带冷轧机
中国二重支承辊使用维护手册2012-11-6版
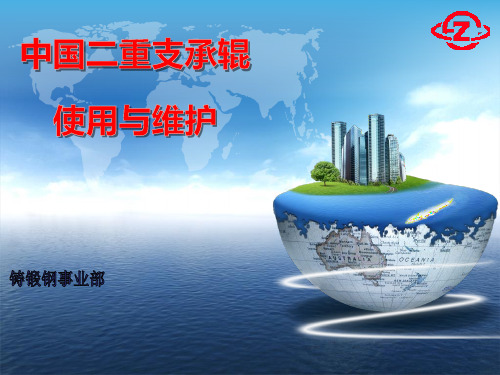
❖ 轧制工艺尽量控制轧制力 ; ❖ 合理的辊型曲线 ; ❖ 提高表面光洁度; ❖ 防腐、防锈; 2、制定合理的换辊周期 3、磨辊彻底 ❖ 每次磨辊应将疲劳层、
加工硬化层磨削清除。
一、控制应力
❖1、制定轧制工艺时,在保证轧材质量的基 础上,尽量降低轧制力,禁止超载荷运行 。
❖2、磨辊过程中,提高卸载区的表面光洁度, 光洁度要求Ra0.8。
磨辊车间设备要求
❖3、无损检测设备
超声波探伤(UT)、 磁粉探伤(MT)、 渗透检测(PT )或涡流探伤是支承辊使用 维护过程中的重要无损检测仪器,支承辊 每次磨辊后,均需进行无损检测,确保辊 身表面无残留裂纹,支承辊只有在无损检 测没有裂纹的条件之下才能继续上机使用。 同时,MT或PT能针对支承辊打磨凹坑,在 涡流探伤无法检测时进行无损检测,确保 凹坑无残余裂纹,并且准确度高,操作简 单。
支承辊的存放
❖ 支承辊存储的环境温度应≥0℃,低于此 温度存储支承辊,由于低温脆性转变,在 一定程度上将降低支承辊工作层质量。同 时,支承辊不应露天存放。支承辊长时间 未使用时,表面须刷涂防锈涂料,包装好 后按要求存放,并定期检查防锈涂料情况, 必要时重新刷涂防锈涂料。
支承辊的使用范围
❖ 支承辊应在设计允许的工作条件下使用, 防止轧制力超过设计允许范围。与支承辊 配合的工作辊,其硬度与支承辊的硬度差 应≤15HSC(四辊轧机),如果超出此范围, 将加速支承辊产生疲劳层,从而降低支承 辊的单次轧制量。如果支承辊比工作辊硬 度低HS25而上机使用,将极易导致支承辊 产生裂纹、剥落等失效情况。
就越短。
支承辊换辊周期的制定原则
❖ 因支承辊的使用情况不同,所以换辊 周期也不相同。换辊周期同样是一个数据 积累、摸索、不断改善进步的过程,以下 几个方面给出支承辊换辊周期的制定原则:
R1粗轧机说明书

mm热带连轧机R1四辊可逆轧机产品安装调试及使用说明书编号51226MSS集团有限公司设计研究院2004年7月MS1.用途:R1粗轧机是粗轧区的关键设备,与E1组成万能可逆轧机,当连铸坯经加热炉加热好后,除去氧化铁皮,由机前工作辊道送至E1R1机前,由机前推床将钢坯推正、对中轧线,经E1立辊轧边,再送入R1,经来回可逆轧制5~7道次,将厚度160的坯料轧制到规定的厚度、宽度,中间坯再由机后工作辊道送往热卷箱、飞剪区进行热卷及切头切尾,之后进入精轧机区进行轧制。
本设备工艺号为42,图号为51226.00。
相关设备有:支承辊换辊装置59294(工艺号43)工作辊换辊装置59312(工艺号43)E1立辊轧机51225(工艺号41)机前工作辊道53235(工艺号34,35,36,37,38,39)机后工作辊道53236(工艺号46,47,48,49)机前推床5277(工艺号40)机后推床5278(工艺号45)2.技术性能与基本参数坯料规格:160X750~1400X7200~12000mm(厚X 宽X长)中间坯规格:17~30(40)X750~1400X~最大长113mMS坯料最大重量:21t工作辊直径X辊身长:φ1050/φ980 X1550mm支承辊直径X辊身长:φ1350(最大)/φ1250(最小)X1500mm工作辊轴承:4列圆锥φ660.4Xφ812.8X365mm 支承辊轴承:Morgan48 X75 KL型油膜轴承最大轧制压力:3500KN最大轧制力矩:2X2000KN.m轧制速度:2.75~5.5m/s主电机型号:BPT6000-12交流变频电机2台主电机功率:6000KW主电机转速:50/100r/min轧辊最大开口度:新辊270mm压下速度:5-15-25mm/s压下电机型号:ZKSL-315-41压下电机功率:150KW压下电机转速:385/770r/min压下蜗轮副中心距:A=711.2mm压下蜗轮副速比:i=1.125X18.33=20.64 ZC1型压下螺丝规格:S508X48(P=24)mm双头锯齿型螺纹压下止推轴承:φ609.6 X204.01mm满装锥形滚子止MS推轴承松卡电机型号:ZZJ-808松卡电机功率:37.3 KW松卡电机转速:575/1150 r/min松卡蜗轮副速比:i=50 zc1型单线蜗轮付主平衡液压缸规格:φ380(400) X610 柱塞型mm主平衡液压缸工作压力:7Mpa主平衡液压缸换辊时压力:16Mpa工作辊平衡压靠液压缸规格:8 X120 X400上辊/120下辊mm工作辊平衡压靠液压缸工作压力:7Mpa塞机架辊规格:2Xφ450X1360mm机架辊传动电机:交流变频45KWX370 r/min,YGP355M1-16机架牌坊外形尺寸:高X宽X厚=9660X4700X1435mm 牌坊单片净重:147t牌坊立柱断面:760X980=7448cm2上下工作辊装配件重量:53.56t上支承辊装配件重量: 56t下支承辊装配件重量: 46t支承辊更换移出行程:5280 mmMS支承辊更换移出速度:70 mm/s工作辊更换移出行程:6250 mm工作辊更换移出速度:100 mm/s主传动接轴型式:C型十字头万向接轴主传动接轴规格:φ960/φ1200X9830mm主传动接轴平衡液压缸:上轴φ200/φ110X450mm下轴用φ200/φ110X200mm主传动接轴平衡液压缸工作压力:7Mpa接轴换辊及抱紧液压缸:2Xφ125/φ90X260mm,16Mpa支承辊、工作辊轴向卡板缸:6Xφ80/φ56X80mm,16Mpa上导卫护板摆动气缸规格:φ200X550-MP4 mm下导卫护板摆动气缸规格:φ200X250-MP4 mm工作辊冷却水喷嘴数量/总耗量:4X19=76(个),250t/h 工作辊冷却水压力:8-10bar,浊环水支承辊冷却水喷嘴数量/总耗量:4X19=76(个),137t/h 支承辊冷却水压力:3-4bar,浊环水轧机本体总重量:820t3.设备外形图3.1机列图MS3.2本体外形图3.3压下原理图3.4轧辊窗口位置图4.结构及工作原理说明:4.1机列组成:轧机本体(51226.04—51226.11) ;主接轴及平衡(51226.01-51226.03)主电机及中间轴 J7002(东电图)工作辊换辊装置 59312支撑辊换辊装置 592944.2轧机本体:本轧机本体由机架、轧辊系统、压下及平衡装置、轧辊传动装置、上下导卫护板、轧辊水冷装置、机架辊装置、平台走梯、配管、及电气行程开关布置等组成。
棒材轧机区设备功能说明介绍模板之欧阳历创编

轧机区设备控制功能说明书2007年4月30日项目代号水平轧机 C.S.001立式轧机 C.S.002平立转换轧机 C.S.0036V轧机后的飞剪(1号飞剪) C.S.00412V轧机后的飞剪(2号飞剪) C.S.005中轧后辊道 C.S.006精轧后辊道 C.S.007立式活套器 C.S.008夹送辊 C.S.00918H/V轧机后的飞剪(3号飞剪) C.S.010轧机区设备控制功能说明书C.S. 001水平轧机1.概述水平轧机共9架●1H、3H为Φ610mm轧机●5H为Φ530mm轧机●7H、9H、11H为Φ470mm轧机●13H、15H、17H为Φ380mm轧机每架轧机由以下几部分组成:●底座●拉扞和轧辊组(机架)●锁紧装置●横移液压缸,布置在轧机传动侧●液压马达(手动)压下机构●上下辊弹性阻尼减振器平衡●万向接轴托架装置2.电气元件详见电机表及各分项描述3.功能描述换孔型的工作过程●机架锁紧液压缸松开;●横移液压缸动作,驱动轧机在底座上水平移动以对中孔型;●机架锁紧缸闭合,锁紧轧机。
换机架的工作过程轧机主电机停转;轧机锁紧缸松开;轧机横移液压缸动作推动轧机横移到操作侧换辊位置;万向接轴托架插销缸插销缩回;轧机横移液压缸动作拉动万向接轴托架横移到传动侧极限位置;(此时,轧辊轴头与万向接轴辊端轴套脱开)吊车将轧机机架整体吊走,新轧机机架吊入;轧机横移液压缸动作推动万向接轴托架横移到操作侧换辊位置;(此时,轧辊轴头与万向接轴辊端轴套重合)万向接轴托架插销缸插销伸出;轧机横移液压缸动作拉动轧机横移对中孔型使轧机处于正常轧钢位置;轧机锁紧缸闭合。
此即水平轧机的完整换辊过程。
换孔型或换机架过程的连锁:只有当轧机锁紧缸松开,轧机才能横移;只有当轧机锁紧缸锁紧轧机,主电机才能工作;只有当主电机停止时,才能进行换辊操作。
机架锁紧1.电气元件9个锁紧缸电磁阀,每个机架1个,为双线圈电磁阀2.功能描述每架轧机设4个锁紧缸,2个在入口侧,2个在出口侧锁紧缸有杆腔进油时,机架被松开并可移动锁紧缸无杆腔进油时,机架被锁紧每架轧机的锁紧缸由一个双电控阀控制3.操作工的控制装置在主操作室上:仅设定“就地操作”方式选择主操作室不进行操作“机架未锁紧”指示(CRT)无线遥控操作箱1个选择开关,用于“机架”及“机旁闭锁”选择1个“锁紧”按钮1个“松开”按钮“锁紧”、“松开”指示机架横移电气元件9个双线圈电磁阀,每个机架1个功能描述双线圈中的一个得电,机架“推进”;另一个得电,机架“拉出”3. 操作工的控制装置在主操作室上:仅设定“就地操作”方式选择不进行操作无线遥控操作箱:1个选择开关,用于“机架”和“机旁闭锁”选择1个按钮,机架“推进”1个按钮,机架“拉出”接轴托架与轧机机架的联接电气元件9个双线圈电磁阀,控制插销缸,每架轧机1个功能描述每个接轴托架上设1个液压插销缸轧机工作和机架横移时,插销杆必须处于伸出状态,将机架与接轴托架联接在一起只有在机架“推出”轧线进行换辊时,活塞杆方可收回;此时,机架与接轴托架“松开”操作工的控制装置A.主操作室上不进行操作仅设定“就地操作方式”设9个指示灯,“插销缸未伸出”(CRT)B.无线遥控操作箱1个机架选择开关1个按钮“缸伸出”1个按钮“缸收回”“收回”显示轧辊压下装置电气元件9个双线圈电磁阀,每个机架1个功能描述通过压下机构实现上辊的径向调整液压马达压下液压马达设在轧机传动侧3. 操作工的控制装置在主操作室上不进行操作仅设定“就地操作”方式选择无线遥控操作箱1个选择开关,用于“机架”和“机旁闭锁”选择1个按钮“抬起”1个按钮“压下”轧机齿轮箱稀油润滑电气元件•9个电接点压力表,每架轧机1个•9个油流信号器,每架轧机1个功能描述•用于稀油润滑低压报警轧机区设备控制功能说明书C.S.002立式轧机1.概述立式轧机共7架●2V、4V为Φ610mm轧机●6V为Φ530mm轧机●8V、10V、12V为Φ470mm轧机●14V为Φ380mm轧机每架立式轧机由以下几部分组成:●底座●换辊小车●拉扞和轧辊组(机架)●锁紧装置●横移液压缸,布置在轧机传动侧(上方)●液压马达(手动)压下机构●上下辊弹性阻尼减振器平衡●万向接轴托架装置2.电气元件详见电机表及各分项描述3.功能描述换孔型的工作过程●机架锁紧液压缸松开;●横移液压缸动作,驱动轧机在底座上下移动以对中孔型;●机架锁紧缸闭合,锁紧轧机。
粗轧区域设备参数
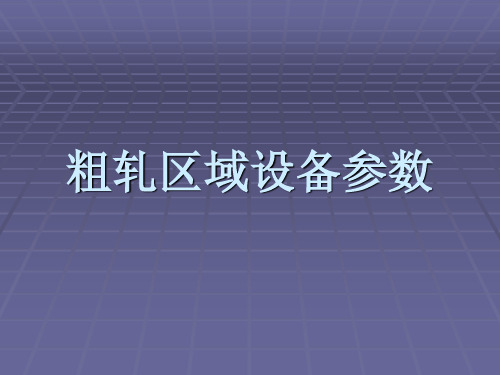
R1/R2轧机前后推床动作方式 R1/R2轧机前后推床动作方式
推床是由液压缸驱动上齿条,上齿条通过齿轮传动下齿轮, 推床是由液压缸驱动上齿条,上齿条通过齿轮传动下齿轮, 使左右推板同步动作,一侧推板的两个推杆机械同步, 使左右推板同步动作,一侧推板的两个推杆机械同步,实现 轧件对中,通过编码器实现开口度设定及对钢件测宽。 轧件对中,通过编码器实现开口度设定及对钢件测宽。
R1轧机前后工作辊道 R1轧机前后工作辊道
R1轧机前后工作辊道由:联轴器、冷却水系 R1轧机前后工作辊道由:联轴器、 轧机前后工作辊道由 甘油系统、螺栓紧固、电机等部分组成。 统、甘油系统、螺栓紧固、电机等部分组成。 简要性能:型式:交流单独传动 简要性能:型式:
辊子尺寸:Φ450x1780mm 辊子尺寸: 辊子数量:机前18根、机后18根 辊子数量:机前18根 机后18根 辊距: 辊距:800mm 传动电机:AC22kW160r/min调速 传动电机:AC22kW160r/min调速 辊面线数度: 辊面线数度:0~3.7m/s 辊子为实心锻钢辊,辊身为喷水冷却,辊颈为喷水冷却( 辊子为实心锻钢辊,辊身为喷水冷却,辊颈为喷水冷却(分 别单独控制) 别单独控制)
R1/R2轧机前后推床作用 R1/R2轧机前后推床作用
推床位于热连轧生产线粗轧机机前、 推床位于热连轧生产线粗轧机机前、机后工作辊道上方其作用是把在辊道 运输中跑偏的钢坯推正,对中轧制线并送入粗轧机进行多道次轧制, 运输中跑偏的钢坯推正,对中轧制线并送入粗轧机进行多道次轧制,以减 少或避免钢坯出现镰刀弯,对粗轧机轧制板型的好坏起着重要作用。 少或避免钢坯出现镰刀弯,对粗轧机轧制板型的好坏起着重要作用。推床 采用电气或液压伺服阀控制,当推板在完成对坯料对中的功能后,可以迅 采用电气或液压伺服阀控制,当推板在完成对坯料对中的功能后, 速退开, 速退开,以防止由于镰刀弯过大或不规整钢坯在轧制时对推板产生过大侧 向力而使推杆弯曲, 向力而使推杆弯曲,破坏设备。
CVC串辊功能简单描述
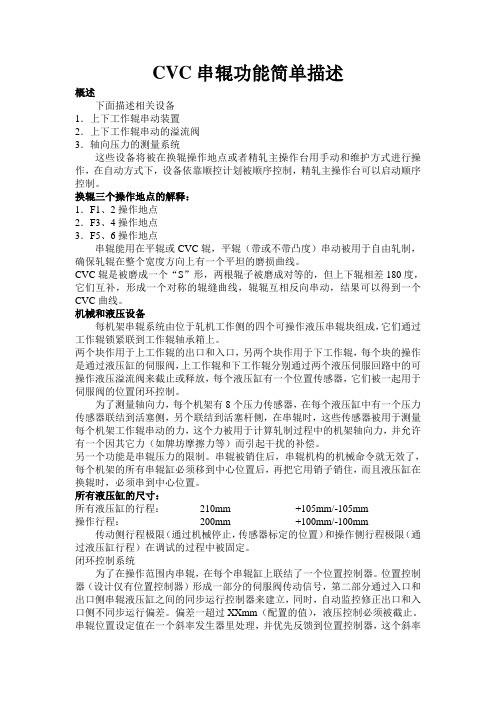
CVC串辊功能简单描述概述下面描述相关设备1.上下工作辊串动装置2.上下工作辊串动的溢流阀3.轴向压力的测量系统这些设备将被在换辊操作地点或者精轧主操作台用手动和维护方式进行操作,在自动方式下,设备依靠顺控计划被顺序控制,精轧主操作台可以启动顺序控制。
换辊三个操作地点的解释:1.F1、2操作地点2.F3、4操作地点3.F5、6操作地点串辊能用在平辊或CVC辊,平辊(带或不带凸度)串动被用于自由轧制,确保轧辊在整个宽度方向上有一个平坦的磨损曲线。
CVC辊是被磨成一个“S”形,两根辊子被磨成对等的,但上下辊相差180度,它们互补,形成一个对称的辊缝曲线,辊辊互相反向串动,结果可以得到一个CVC曲线。
机械和液压设备每机架串辊系统由位于轧机工作侧的四个可操作液压串辊块组成,它们通过工作辊锁紧联到工作辊轴承箱上。
两个块作用于上工作辊的出口和入口,另两个块作用于下工作辊,每个块的操作是通过液压缸的伺服阀,上工作辊和下工作辊分别通过两个液压伺服回路中的可操作液压溢流阀来截止或释放,每个液压缸有一个位置传感器,它们被一起用于伺服阀的位置闭环控制。
为了测量轴向力,每个机架有8个压力传感器,在每个液压缸中有一个压力传感器联结到活塞侧,另个联结到活塞杆侧,在串辊时,这些传感器被用于测量每个机架工作辊串动的力,这个力被用于计算轧制过程中的机架轴向力,并允许有一个因其它力(如牌坊摩擦力等)而引起干扰的补偿。
另一个功能是串辊压力的限制。
串辊被销住后,串辊机构的机械命令就无效了,每个机架的所有串辊缸必须移到中心位置后,再把它用销子销住,而且液压缸在换辊时,必须串到中心位置。
所有液压缸的尺寸:所有液压缸的行程:210mm +105mm/-105mm操作行程:200mm +100mm/-100mm 传动侧行程极限(通过机械停止,传感器标定的位置)和操作侧行程极限(通过液压缸行程)在调试的过程中被固定。
闭环控制系统为了在操作范围内串辊,在每个串辊缸上联结了一个位置控制器。
- 1、下载文档前请自行甄别文档内容的完整性,平台不提供额外的编辑、内容补充、找答案等附加服务。
- 2、"仅部分预览"的文档,不可在线预览部分如存在完整性等问题,可反馈申请退款(可完整预览的文档不适用该条件!)。
- 3、如文档侵犯您的权益,请联系客服反馈,我们会尽快为您处理(人工客服工作时间:9:00-18:30)。
Title
BUR TRANSFER CAR Functional Description
Approvals Remarks
00 2008-1-24 ERZHONG ISSUE OF DESIGN PHASE Huang liaodong
Rev. File Date Revisions description Drawn Checked Approved
Table of content
1设备总体概况 (3)
2技术参数/ Characteristics (3)
3设备结构及传动示意图 (3)
4控制要求 (4)
4.1工作方式 (4)
4.2操作方式 (4)
4.3联锁要求 (4)
5电机和电器工艺检测仪表 (4)
1 设备总体概况
位于磨辊间和轧制跨之间;用于在轧制跨和磨辊间运输支承辊。
2 技术参数/C HARACTERISTICS
运载能力/ Capacity t 80
尺寸(L×W)/ Dimension (L X W) approx. m 6 x 3.04
运送行程/ Travelling stroke approx. m 30
最大运行速度(带负载)/ Max. car speed (loaded) m/min 10
电机减速器/ Motor No. 2
电机功率/ Power Kw 3.5
电机额定转速/ Motor Speed r/min 925
减速器传动比/ Drive ratio 1:45
3 设备结构及传动示意图
本设备为电动车轮式运输车。
该运输车在台面内承载轧辊,用于双向运行;该车车轮数为4个, 4个均为主动车轮,分别由两台电机驱动。
在运输车的极限位置设有接近开关,用于极限行程安全保护。
双电机同时驱动,采用电缆卷筒供电方式。
电控柜设置在车体上。
1) 过跨车采用手动操作。
4.2 操作方式
1) 机旁操作:过跨车前进、返回和停止由操作工通过按钮盒进行操作。
4.3 联锁要求
1)车上要求配备可靠的声光报警灯;
2)两台电机要求同时正反转;
3)两台电机要求同步。
5 电机和电器工艺检测仪表
Functional
item Product
item
名称型号技术参数
数
量
功能备注
32M2103 115M001
-M002
Motor
YZR132M2-6-
3.5
AC380
P=3.5KW
n=925/min
2 Car Drive MKL
32M2103 115H001 Vertical
type
acoustic
& optical
alarm
1
Alarm during
operation
32M2103 115S001 Proximity
Switch Ni15-M30-
AD4X
N-GS24 1
Limit position
end of the
mill shop
SBE
32M2103 115S002 Proximity
Switch Ni15-M30-
AD4X
N-GS24 1
Limit position
end of the
roll shop
SBE
32M2103 115Y001-
002
Motor
brake
YWZ5-
160/ED23/5
AC380 165W 2 YBM。