反溅射刻蚀试制过程
溅射镀膜操作过程
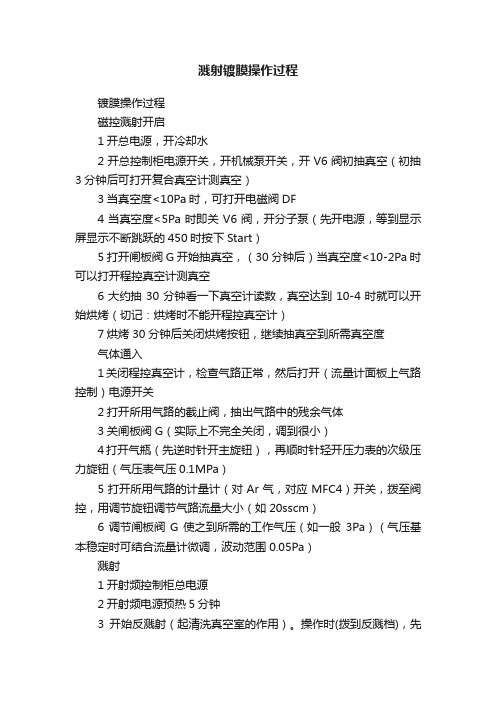
溅射镀膜操作过程镀膜操作过程磁控溅射开启1开总电源,开冷却水2开总控制柜电源开关,开机械泵开关,开V6阀初抽真空(初抽3分钟后可打开复合真空计测真空)3当真空度<10Pa时,可打开电磁阀DF4当真空度<5Pa时即关V6阀,开分子泵(先开电源,等到显示屏显示不断跳跃的450时按下Start)5打开闸板阀G开始抽真空,(30分钟后)当真空度<10-2Pa时可以打开程控真空计测真空6大约抽30分钟看一下真空计读数,真空达到10-4时就可以开始烘烤(切记:烘烤时不能开程控真空计)7烘烤30分钟后关闭烘烤按钮,继续抽真空到所需真空度气体通入1关闭程控真空计,检查气路正常,然后打开(流量计面板上气路控制)电源开关2打开所用气路的截止阀,抽出气路中的残余气体3关闸板阀G(实际上不完全关闭,调到很小)4打开气瓶(先逆时针开主旋钮),再顺时针轻开压力表的次级压力旋钮(气压表气压0.1MPa)5打开所用气路的计量计(对Ar气,对应MFC4)开关,拨至阀控,用调节旋钮调节气路流量大小(如20sscm)6调节闸板阀G使之到所需的工作气压(如一般3Pa)(气压基本稳定时可结合流量计微调,波动范围0.05Pa)溅射1开射频控制柜总电源2开射频电源预热5分钟3开始反溅射(起清洗真空室的作用)。
操作时(拨到反溅档),先把溅射电压调至50V。
量程按钮调到最大(2000,保护仪表不超过量程),调节功率到设定功率,反射读数调到最低。
按量程到200按钮,调节功率(电压)起辉反溅10分钟,关闭溅射电源4调节闸板阀到所需工作气压(如0.3Pa),开射频电源,电压调至50V,重复步骤3调节到所需功率,起辉预溅5~10分钟(转动挡板挡住样品)清洗靶材。
5移开挡板,打开偏压(设定好)开始溅射(注意把握好时间,到时间旋转挡板)溅射关闭1关射频功率源(旋钮至最低,OFF)2关偏压电源3关基片旋转控制电源(注意顺序)4关射频总控制电源5把旋钮打到反溅关闭气体1先将调节旋钮旋到最低,当流量显示<1.0时再把流量计开关档打到关闭2关闭气路的截止阀(对Ar气是V5)3打开闸板阀,关闭气瓶(先逆时针关次分压)真空系统关闭1关闭闸板阀G2继续抽真空到10-4数量级,关闭分子泵。
溅射镀膜

溅射镀膜介绍一: 溅射镀膜应用:溅射镀膜主要用于半导体生产的金属薄膜的生长.如下图的金属层1到金属层6都是运用溅射镀膜所生产.溅射镀膜到形成所需的金属线的过程为:溅射镀膜--→光照显影--→蚀刻(形成金属连接线)二: 溅射镀膜原理溅射淀积(溅射)是另一种老工艺,能够适应现代半导体制造需要。
它几乎可以在任何衬底上淀积任何材料,而且广泛应用在人造珠宝涂层,镜头和眼镜的光学涂层的制造。
在真空反应室中,由镀膜所需的金属构成的固态厚板被称为靶材(target)(图1),靶材接阴极,衬底接阳极并接地。
首先将氩气充入室内,并且电离成正电荷。
带正电荷的氩离子被不带电的靶吸引,加速冲向靶。
在加速过程中这些离子受到引力作用,获得动量,轰击靶材。
这样在靶上就会出现动量转移现象(momentum transfer)。
正如在桌球,球杆把能量传递到其他球,使它们分散一样,氩离子轰击靶,引起其上的原子分散。
被氩离子从靶上轰击出的原子和分子进入反应室。
这就是溅射过程。
从靶上轰击出原材料之后,氩离子、轰击出的原材料、气体原子和溅射工艺所产生的电子在靶前方形成一个等离子区域。
等离子区是可见的,呈现紫色。
而黑色区域将等离子区和靶分开,我们称之为暗区(dark space)。
图1 溅射工艺的原理被轰击出的原子或分子散布在反应室中,其中一部分渐渐地停落在晶圆上,形成薄膜,溅射工艺的主要特征是淀积在晶圆上的靶材不发生化学或合成变化。
形成薄膜的过程有如下几个过程(图2所示):1长晶2 晶粒成长3 晶粒聚集4 缝隙填补5 沉积膜的成长图2 溅射工艺的原理三:溅射镀膜相对于真空蒸发优点:1 靶材的成分不会改变。
这种特征的直接益处就是有利于合金膜和绝缘膜的淀积。
合金真空蒸发的问题在前一部分已作描述。
对于溅射工艺来说,含有2%铜的铝靶材就可以在晶圆上生长出含有2%铜的铝薄膜。
2 阶梯覆盖度也可以通过溅射改良。
蒸发来自于点源,而溅射来自平面源。
因为金属微粒被从靶材各个点溅射出来的,所以在到达晶圆承载台时,它们可以从各个角度覆盖晶圆表面。
刻蚀实验方案
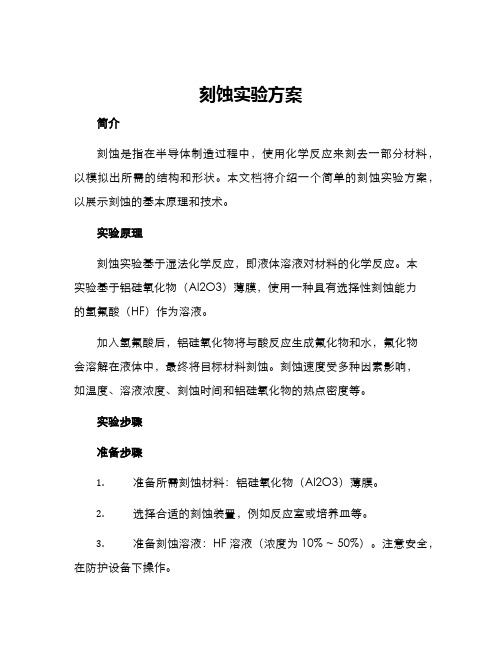
刻蚀实验方案简介刻蚀是指在半导体制造过程中,使用化学反应来刻去一部分材料,以模拟出所需的结构和形状。
本文档将介绍一个简单的刻蚀实验方案,以展示刻蚀的基本原理和技术。
实验原理刻蚀实验基于湿法化学反应,即液体溶液对材料的化学反应。
本实验基于铝硅氧化物(Al2O3)薄膜,使用一种具有选择性刻蚀能力的氢氟酸(HF)作为溶液。
加入氢氟酸后,铝硅氧化物将与酸反应生成氟化物和水,氟化物会溶解在液体中,最终将目标材料刻蚀。
刻蚀速度受多种因素影响,如温度、溶液浓度、刻蚀时间和铝硅氧化物的热点密度等。
实验步骤准备步骤1.准备所需刻蚀材料:铝硅氧化物(Al2O3)薄膜。
2.选择合适的刻蚀装置,例如反应室或培养皿等。
3.准备刻蚀溶液:HF溶液(浓度为10% ~ 50%)。
注意安全,在防护设备下操作。
实验步骤1.将反应室或培养皿加入足够的HF溶液,使得刻蚀液可以涵盖所有待刻蚀的铝硅氧化物薄膜。
2.检查HF溶液浓度,注意与第一步中提到的范围相匹配。
3.将铝硅氧化物薄膜放入刻蚀液中。
4.设置刻蚀时间,一般在数秒到数分钟之间。
由于刻蚀速率受多种因素影响,可以根据不同的需求进行调整。
5.取出铝硅氧化物薄膜,将其洗净并放入去离子水中浸泡数分钟以去除余留的刻蚀溶液和杂质。
6.用氮气将去离子水吹干铝硅氧化物薄膜。
注意事项•操作时应该戴好防护眼镜、颈部防护、铅手套和全棉工作服等。
•配制HF溶液时要非常小心,且必须在通风设备下进行。
•在操作溶液时不要将溶液撒到自己的身上,切勿碰到皮肤。
•操作过程中发现异常情况应立刻停止实验。
结论该实验实现了对铝硅氧化物(Al2O3)薄膜的刻蚀。
刻蚀的最终效果可因不同的参数设置而有所不同,本实验在刻蚀溶液浓度为10%,刻蚀时间为3分钟,温度为30度的条件下获得了较为理想的刻蚀效果,刻蚀深度约为20 nm。
刻蚀效果可通过扫描电镜(SEM)进行观察和评估。
结束语本文档介绍了使用氢氟酸对铝硅氧化物(Al2O3)薄膜进行刻蚀的基本原理和实验步骤。
蓝宝石刻蚀

The results of anodized experiments showed that best condition was the oxidation temperature below 15 °C, 40 V for the oxidation voltage, 50 min for bearizing. With this condition, anodic oxidation could successed produce a sub-wavelength structure with an aperture ratio of 0.6, a depth of 0.65 μ m and 0.08 μ m, a period of 0.1 μ m. Experimental results of solid phase epitaxy showed that the higher the temperature, the better the degree of crystallization. After the heattreatment at 450 °C for 24 h and 1000 °C for 3 h, the porous structure was preserved, the crystalline quality of alumina was good, and the crystal orientation was consistent with sapphire substrate.
真空双面溅镀工艺流程

真空双面溅镀工艺流程英文回答:Vacuum double-sided sputtering is a process used in the manufacturing of various electronic devices, such as solar cells, LED displays, and semiconductors. It involves depositing thin films of different materials onto both sides of a substrate using a vacuum chamber and sputtering targets.The process starts with the preparation of the substrate. The substrate can be made of various materials, such as glass or silicon. It is thoroughly cleaned to remove any impurities or contaminants that could affect the quality of the deposited films.Once the substrate is prepared, it is loaded into the vacuum chamber. The chamber is then evacuated to create a high vacuum environment. This is important to minimize the presence of any gas molecules that could interfere with thesputtering process.Next, sputtering targets are introduced into the chamber. These targets are made of the materials that will be deposited onto the substrate. For example, if the desired films are made of indium tin oxide (ITO), the sputtering targets would be made of indium and tin.The targets are bombarded with high-energy ions, typically generated by a radio frequency (RF) or direct current (DC) power source. This bombardment causes the atoms of the target material to be ejected and deposited onto the substrate.To ensure uniform deposition on both sides of the substrate, the chamber is equipped with multiple targets and the substrate is rotated during the sputtering process. This allows for a more even distribution of the deposited material.The deposition process continues until the desired thickness of the films is achieved. The thickness can becontrolled by adjusting the sputtering time and the power applied to the targets.Once the deposition is complete, the chamber is slowly vented to atmospheric pressure. The substrate is then unloaded and inspected for quality. Any defects or imperfections in the films can be identified at this stage.中文回答:真空双面溅镀是一种用于制造各种电子器件的工艺流程,例如太阳能电池、LED显示屏和半导体。
盖板玻璃AG蚀刻工艺详解

样品A
43.5
19.1
18.5
0.43
0.6
样品B
42.1
22.7
18.5
0.47
56.2
金 相 图
样品A
样品B
分析:样品A和样品B的雾度、 光泽度、粗糙度、颗粒大小 均接近,但它们的鲜映度却 相差很大。
结论:玻璃的DOI与玻璃表 面颗粒的形貌、大小及均匀 性等有很大关系。
5.4 蚀刻AG工艺流程图
感谢收看
目录
CONTENTS
1 何谓AG
2
常见AG工艺
3
AG相关性能测试
4
AG玻璃的应用
5 案例分享
3.1 常见测量仪器
雾度/透过率测试仪 光泽度测试仪
粗糙度测试仪 鲜映度测试仪
3.2 Aቤተ መጻሕፍቲ ባይዱ玻璃参数之间的关系
雾度(Haze):即光的扩散,以肉眼来判断就是模糊程度。雾度与清晰度呈反比,与防眩效果成正比; 雾度越高,防眩效果越好,但清晰度越差。
应合理选择各组分原料的类型和定量, 不同的组分,所达到的蒙砂效果也不 同,甚至蒙砂加工时间都有区别。
在蒙砂剂的配方中,一般可根据需要添加一些预期能产生溶解度较小的盐类,如氟化钙、钡、 铅盐和氟硅酸钾、钠、钙、钡盐,使其结晶于玻璃表面,形成起始晶核,并不断长大。玻璃 表面被结晶盐覆盖的部分,阻碍了其与蒙砂剂的接触和进一步反应;而玻璃表面微被覆盖的 部分,即结晶颗粒间的缝隙,仍暴露在蒙砂剂中,则受到侵蚀。覆盖部分处的盐结晶不断变 化,未覆盖的缝隙处玻璃继续被侵蚀,即玻璃表面表面受到非均匀侵蚀,形成凹凸不平的无 光泽表面。
①宝泰采用整面酸蚀(不避空)→物理抛光(前摄孔和IR孔),做出来产品不满足客户的要求。 ②兴利、睿冠、华玻采用孔避空处理→酸蚀→退镀→酸抛的方式,做出来的产品均能满足客户要求。
真空双面溅镀工艺流程

真空双面溅镀工艺流程英文回答:Vacuum double-sided sputtering is a process used in the manufacturing of thin film coatings. It involves depositing thin layers of material onto both sides of a substrate using a sputtering technique in a vacuum chamber. This process is widely used in various industries, including electronics, optics, and automotive.The process begins with the preparation of the substrate, which is usually made of glass or metal. The substrate is cleaned thoroughly to remove any impurities that may affect the quality of the coating. Once the substrate is clean, it is loaded into the vacuum chamber.Next, the chamber is pumped down to a high vacuum to create the necessary conditions for sputtering. This involves removing all air and other gases from the chamber to minimize the presence of contaminants. The vacuum levelis typically in the range of 10^-6 to 10^-8 Torr.After achieving the desired vacuum level, thesputtering process begins. Sputtering is a physical vapor deposition technique where atoms from a target material are ejected and deposited onto the substrate. This is achieved by bombarding the target material with high-energy ions, usually generated by a plasma discharge.The target material is chosen based on the desired properties of the coating. For example, if a reflective coating is required, a metal target such as silver or aluminum may be used. If a transparent conductive coatingis needed, a material like indium tin oxide (ITO) may be used.During the sputtering process, the target material is bombarded with ions, causing atoms to be ejected from the target surface. These ejected atoms travel in straightlines and deposit onto the substrate, forming a thin film coating. The thickness and composition of the coating can be controlled by adjusting the sputtering parameters, suchas the power applied to the target and the gas pressure in the chamber.Once the desired thickness and composition are achieved on one side of the substrate, the process is repeated on the other side. This ensures that both sides of the substrate have a uniform coating.After the sputtering process is complete, the coated substrate is carefully removed from the vacuum chamber. The coating may undergo further processing, such as annealing or etching, depending on the specific application requirements.中文回答:真空双面溅镀是一种用于制造薄膜涂层的工艺流程。
6-半导体加工技术-2-刻蚀

向低能级越变: XY∗→XY+hv(光子) 发光性(光学应用)
强碰撞分解:XY+e→X+Y+e
反应性(化学应用)
更强碰撞电离:XY+e→XY++2e
导电性(电学应用)
加速:电子和离子由电场加速
高速粒子(力学应用)
升温:粒子间冲击发热,与固体冲击 高温性(热学应用)
XY*为能级较高的激发态分子;
3、等离子体的应用
RF电源 气瓶
等离子体刻蚀装置
7、溅射刻蚀(sputter etching)
溅射:加速的离子轰击固体
表面,从固体表面溅出原子
的现象。
工件
电离气体:惰性气体(氩) 辉光放电电离: Ar+e→Ar++2e 固体原子获得的能量:
等离子体 电极
刻蚀气体 泵
E2 max
=
4m1m2 (m1 + m2 )
E0
E0为离子轰击前能量;m1和m2为离子与固体原子的质量。
能量
制造、材料
环境、宇宙
<电学应用> 热电子发电 MHD发电 核融合发电 闸流管 点火管
<光学应用> 照明用灯管 霓虹灯 气体激光 等离子体显示器 紫外线源 X射线源
<力学应用> 电子束/离子束源 粒子加速
<热学应用> 电弧焊接 放电加热 等离子体喷射 烧结 微粉体制造
<化学应用> 表面改质 等离子体CVD 等离子体刻蚀(太阳电 池、LSI、MEMS、 DRAM等制造)
• EDP、EPW:(ethylene diamine, pyrocatechol, water)
乙二胺(ethylene diamine): NH2-CH2-CH2-NH2 邻苯二酚(pyrocatechol): C6H4(OH)2 不易操作,有毒性,对SiO2、P++选择性好,气泡少。1.3μm/min(115°C)。
浅谈磁控溅射镀膜工艺中的反应溅射

浅谈磁控溅射镀膜工艺中的反应溅射信义玻璃(天津)有限公司陈大伟摘要:本文介绍了磁控溅射镀膜工艺、磁控溅射设备、非反应溅射与反应溅射:反应溅射是一个非常复杂的过程。
重点对反应溅射中的“直流氧化溅射”、“阳极消失效应”、“靶材中毒现象”、“磁滞效应现象”、“金属模式”、“过渡模式”、“反应模式”、“反应溅射磁滞效应特征曲线”进行分析。
在生产过程中,掌握反应溅射工艺的特点,合理控制溅射过程中的工艺参数,准确判断溅射工艺中的异常现象,利用有效的手段进行调整,才能达到高效的溅射速率以及高质量的膜层性能,防止不良溅射现象的出现。
0引言磁控溅射镀膜是目前离线镀膜玻璃生产最重要的方式之一.其生产溅射工艺非常复杂.其中包含直流和交流溅射的控制模式,平面阴极、旋转阴极的溅射设备,惰性和反应的工作气体以及适当的低气压环境等方面。
在生产过程中不同的磁控阴极、材料、气氛等又会有不同的工艺控制模式,其中包含非反应溅射以及反应溅射,而反应溅射中又涉及到靶材溅射的金属模式、磁滞效应、中毒模型等,这些均会影响到膜层组分、溅射效率、成膜质量及性能等方面。
在实际的生产过程中.掌握磁控溅射工艺的特点,合理控制溅射过程中的工艺参数,准确判断溅射工艺中的异常现象并做出及时的处理.对最终高质量高效率成膜控制具有重大意义。
1磁控溅射简介1.1溅射工艺磁控溅射是物理气相沉积(PVD)的一种,是一种十分有效的薄膜沉积方法。
上世纪70年代广泛发展起来的磁控阴极溅射法可以在玻璃上沉积出高质量的用于控制光线和太阳能的膜层。
简单地讲,就是在磁场约束及增强下的等离子体中的工作气体离子,在阴极电场的加速下,轰击刻蚀阴极上的靶材,使材料源的离子从靶材表面上脱离崩射出来,然后沉积附着在基片上。
溅射镀膜过程是将基片置-4-于有特殊设计的阴极和工作气体的真空腔室中来实现的,在阴极上施加负电压,当真空腔体内达到适当的条件进行等离子体辉光放电(图1)。
带正电的气体离子受到带负电的阴极靶材表面的吸引,正原子对负电位的靶材的撞击非常强烈,使得靶材上的原子从表面崩射出来并沉积在玻璃上,从而形成一层原子依次排列的薄膜(图2)。
上海反应磁控溅射步骤
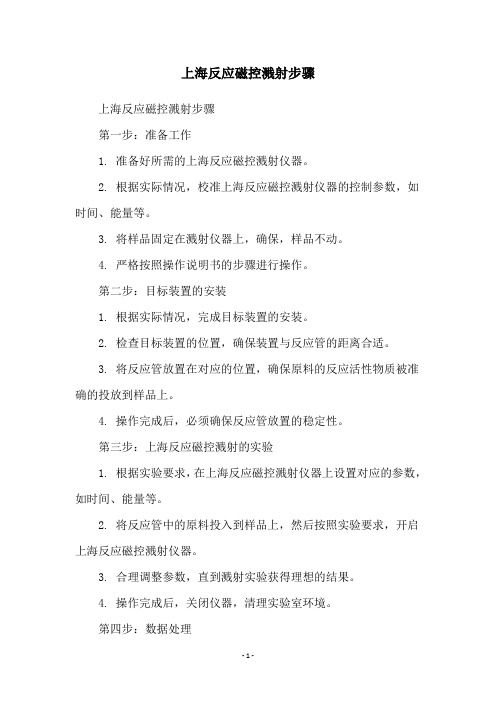
上海反应磁控溅射步骤
上海反应磁控溅射步骤
第一步:准备工作
1. 准备好所需的上海反应磁控溅射仪器。
2. 根据实际情况,校准上海反应磁控溅射仪器的控制参数,如时间、能量等。
3. 将样品固定在溅射仪器上,确保,样品不动。
4. 严格按照操作说明书的步骤进行操作。
第二步:目标装置的安装
1. 根据实际情况,完成目标装置的安装。
2. 检查目标装置的位置,确保装置与反应管的距离合适。
3. 将反应管放置在对应的位置,确保原料的反应活性物质被准确的投放到样品上。
4. 操作完成后,必须确保反应管放置的稳定性。
第三步:上海反应磁控溅射的实验
1. 根据实验要求,在上海反应磁控溅射仪器上设置对应的参数,如时间、能量等。
2. 将反应管中的原料投入到样品上,然后按照实验要求,开启上海反应磁控溅射仪器。
3. 合理调整参数,直到溅射实验获得理想的结果。
4. 操作完成后,关闭仪器,清理实验室环境。
第四步:数据处理
1. 根据实验结果,对数据进行处理,绘制出曲线图。
2. 计算出实验结果,并且分析结果的合理性。
3. 根据实验结果及分析,得出结论,如实验目的已经达到,反应机理等。
4. 保存处理后的数据,并给出相应的报告。
反溅射刻蚀试制过程

磁控反溅射刻蚀试验2006年公司提出准备上电子束钢带真空镀膜项目成立项目组。
于是开始进行查资料,学习相关知识的前期准备工作。
2007年项目正式投入生产计划,项目组开始做方案,然后进入方案论证和设计阶段。
至2010年初生产线装配和真空系统基本完成。
2010年4月溅射刻蚀第一个设计方案开始正式进入试验,一直到2011年底,进行了6次大的设计改进和试验(这中间小改不计其数),2011年11月基本定型,将新的定型方案投入生产,由于公司的原因,这个方案的外加工零件直到2014年底才回到公司。
经过开机验证,达到设计和应用的要求。
第一部分,摘自2009年《反溅射刻蚀预处理初步试验方案》:1 本试验的基本依据:1.1 阿登纳《连续试制线上使用PVD 新型钢带镀膜技术:加工工艺和镀膜发展》(2002):反转磁控溅射刻蚀:“这种设备在带材表面产生强度约为25mT的磁场,为了确保稳定的运行,将用于磁控技术中相似的中频电源用于溅射刻蚀工作站。
电流密度可以达到约10mA/cm2。
通过由稀土磁体组成的磁场系统,可以在厚度为0.9mm的钢带表面保持稳定的磁控放电,对钢带的刻蚀率达到15~20nm/s”。
(注:带宽300mm,速度30米/分)1.2 FEP《金属薄板和带的PVD镀膜(From FEP Annual Report 1999)》:The current pretreatment of metallic sheets and strips(当前的钢带预处理): “采用Pulse plasma Activated Treatment(脉冲等离子体激活处理。
注:基本原理和结构同阿登纳的反转磁控溅射刻蚀),刻蚀速率约15nm/s, The power feed for the discharge pulses unipolar(用单极脉冲放电电源)。
pulse frequencies in the range 10–30kHz(脉冲频率在10–30 kHz之间)”。
反溅工艺
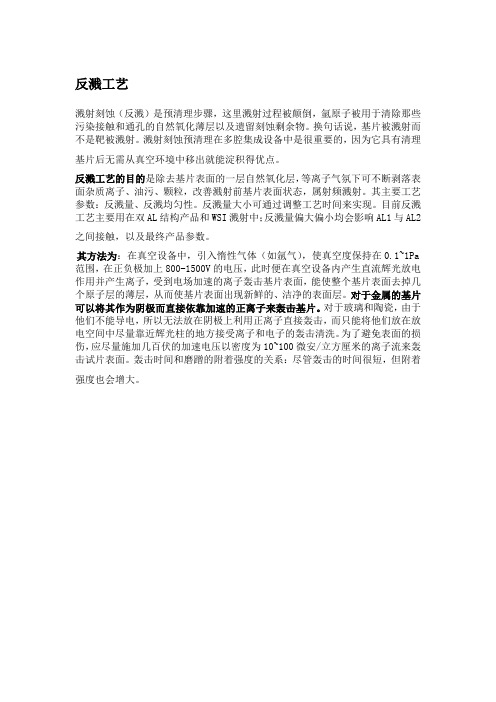
反溅工艺
溅射刻蚀(反溅)是预清理步骤,这里溅射过程被颠倒,氩原子被用于清除那些污染接触和通孔的自然氧化薄层以及遗留刻蚀剩余物。
换句话说,基片被溅射而不是靶被溅射。
溅射刻蚀预清理在多腔集成设备中是很重要的,因为它具有清理
基片后无需从真空环境中移出就能淀积得优点。
反溅工艺的目的是除去基片表面的一层自然氧化层,等离子气氛下可不断剥落表面杂质离子、油污、颗粒,改善溅射前基片表面状态,属射频溅射。
其主要工艺参数:反溅量、反溅均匀性。
反溅量大小可通过调整工艺时间来实现。
目前反溅工艺主要用在双AL结构产品和WSI溅射中;反溅量偏大偏小均会影响AL1与AL2
之间接触,以及最终产品参数。
其方法为:在真空设备中,引入惰性气体(如氩气),使真空度保持在0.1~1Pa 范围,在正负极加上800-1500V的电压,此时便在真空设备内产生直流辉光放电作用并产生离子,受到电场加速的离子轰击基片表面,能使整个基片表面去掉几个原子层的薄层,从而使基片表面出现新鲜的、洁净的表面层。
对于金属的基片可以将其作为阴极而直接依靠加速的正离子来轰击基片。
对于玻璃和陶瓷,由于他们不能导电,所以无法放在阴极上利用正离子直接轰击,而只能将他们放在放电空间中尽量靠近辉光柱的地方接受离子和电子的轰击清洗。
为了避免表面的损伤,应尽量施加几百伏的加速电压以密度为10~100微安/立方厘米的离子流来轰击试片表面。
轰击时间和磨蹭的附着强度的关系:尽管轰击的时间很短,但附着
强度也会增大。
溅射镀膜操作流程

JGP-560C双室磁控溅射沉积系统操作规范系统的气路图如图:一、前期准备:打开循环水(循环水能及时降温,主要是抽水泵能正常工作),打开墙上电源,打开总电源,打开控制电源注:循环水的有效降温同样是维持实验条件稳定和实验参数进行的有力保障。
其主要影响设备是抽水泵。
所以在确定水箱充有足够水的前提下还要确保泵的正常工作。
二、抽真空:1.开机械泵开关;2.开旁抽阀V1(V7),开复合真空计,对溅射真空室(进样室)进行抽真空(粗抽真空);3.当气压低于20 Pa时,关旁抽阀V1(V7);4.开电磁阀DF1(DF2),开闸板阀G2(G3),启动分子泵T1(T2);5.开电离真空计(细抽真空)。
注:真空区域可划分为五类:粗真空区域 1.103×105Pa—1.3×103Pa低真空区域 1.3×103Pa—1.3×10-1Pa高真空区域 1.3×10-1Pa—1.3×10-6Pa超真空区域 1.3×10-6Pa—1.3×10-12Pa极高真空区域<1.3×10-12Pa这种气体的量的变化也会对各类生产过程产生很大影响。
对镀膜过程也不例外。
例如物质在真空中的沸点比在大气中的低,在真空条件下可以降低物质大量蒸发所需的温度,因而在真空镀膜室内镀膜材料可以在较低的温度下大量蒸发。
在低真空区域中氧气相应少了,物质被氧化的可能性大大的变小,因而真空镀膜时能够得到纯度较高的有实用价值的镀膜层。
所以稳定的真空度能有效保证各实验参数的进行,保证镀膜质量。
三、装样1.检查闸板阀G3是否关闭,确认G1,V7,V5确实关闭;2.缓慢打开放气阀V6,向进样室充气;3.充气完成后,打开带窗活开门,将放好样品的样品托一一放入样品库内(一次可放置6个样品托);4.关闭放气阀V6,对样品室抽真空。
四、处理样品(进样室中,退火炉在上,反溅靶在下)1.用磁力传递杆取下样品托,将样品托放置在反溅靶表面;2.将复合真空计由自动调为手动;3.稍关闭闸板阀G3,打开截止阀V5;4.开流量计,预热3min;5.开气瓶开关,调节流量阀MFC3,通过调节流量以及闸板阀开关控制真空到3~5Pa;6.打开RF电源,预热5min,调节功率对样品进行反溅清洗;7.关闭RF电源,关气瓶开关,关闭流量阀MFC3,关闭V5,打开G3;8.取下样品托,放入退火炉托座;9.调节退火温度对样品热处理。
关于反应溅射工艺
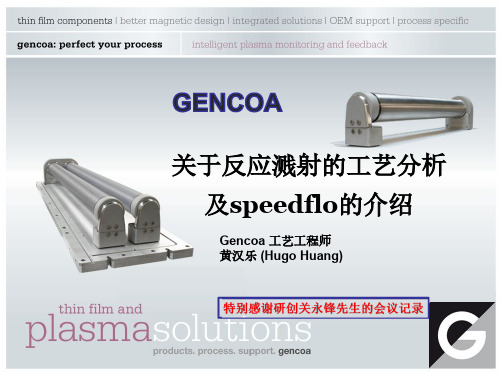
GENCOA 5排磁铁的旋转靶设计
但是这种设计就不会对基片加温,也会减少打火,因为两个靶管的等离子体 是完全独立的。上一种情况,通过观察窗口你会看到靶管背部也有辉光,那 就是leaks的那部分,这一个没有leaks的,靶管背部就不会辉光 。
解决靶材打火问题阴极磁场设计理念
另外无论是平面靶还是旋转靶,我们设 计磁场时,都应该让靶材表面的刻蚀面 积越大越好。 左上图,旋转靶的溅射面刚好到靶材的 顶端,这是最理想的状态,这样会大大 减少打火状态发生。溅射到顶端并不是 因为想让利用率更高点。而是让靶材表 面尽可能地干净。这样就会大大减小的 靶材表面结瘤和打火现象了。 左下图,平面靶也一样,让中间的非刻 蚀区越小越好,这样靶材表面 更干净,而且靶材利用更高。 通常我们的平面靶利用40%到45% 旋转靶利用率75%到85%
关于反应溅射的工艺分析 及speedflo的介绍
Gencoa 工艺工程师 黄汉乐 (Hugo Huang)
GENCOA Key Company Facts
• GENCOA is a private limited company (Ltd) • 成立于 1995 by Dr Dermot Monaghan • 公司位于英国利物浦 •GENCOA是一个专业做阴极,离子源,以及speedflo的公司 •GENCOA目前员工38人 •(是目前全世界专业只做阴极配件最多人的公司) 6 design (Creo 3D CAD) 8 process development & simulation 14 assembly & test 4 sales & tech support (2 Asia based) 其中Hugo是亚洲的工艺/产品工程师 3 administration & accounts 3 hardware & software (Speedflo) • 全球销售阴极数量达3000多个 • 全球销售speedflo达1000台,在反应溅射控制市场占比95%以上
广州反应磁控溅射步骤
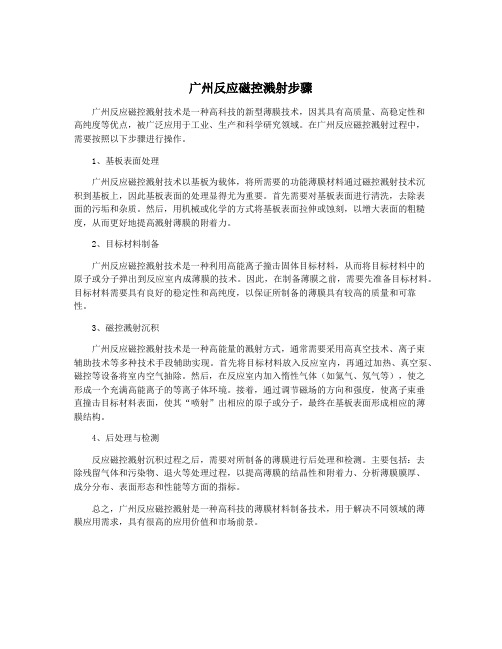
广州反应磁控溅射步骤广州反应磁控溅射技术是一种高科技的新型薄膜技术,因其具有高质量、高稳定性和高纯度等优点,被广泛应用于工业、生产和科学研究领域。
在广州反应磁控溅射过程中,需要按照以下步骤进行操作。
1、基板表面处理广州反应磁控溅射技术以基板为载体,将所需要的功能薄膜材料通过磁控溅射技术沉积到基板上,因此基板表面的处理显得尤为重要。
首先需要对基板表面进行清洗,去除表面的污垢和杂质。
然后,用机械或化学的方式将基板表面拉伸或蚀刻,以增大表面的粗糙度,从而更好地提高溅射薄膜的附着力。
2、目标材料制备广州反应磁控溅射技术是一种利用高能离子撞击固体目标材料,从而将目标材料中的原子或分子弹出到反应室内成薄膜的技术。
因此,在制备薄膜之前,需要先准备目标材料。
目标材料需要具有良好的稳定性和高纯度,以保证所制备的薄膜具有较高的质量和可靠性。
3、磁控溅射沉积广州反应磁控溅射技术是一种高能量的溅射方式,通常需要采用高真空技术、离子束辅助技术等多种技术手段辅助实现。
首先将目标材料放入反应室内,再通过加热、真空泵、磁控等设备将室内空气抽除。
然后,在反应室内加入惰性气体(如氦气、氖气等),使之形成一个充满高能离子的等离子体环境。
接着,通过调节磁场的方向和强度,使离子束垂直撞击目标材料表面,使其“喷射”出相应的原子或分子,最终在基板表面形成相应的薄膜结构。
4、后处理与检测反应磁控溅射沉积过程之后,需要对所制备的薄膜进行后处理和检测。
主要包括:去除残留气体和污染物、退火等处理过程,以提高薄膜的结晶性和附着力、分析薄膜膜厚、成分分布、表面形态和性能等方面的指标。
总之,广州反应磁控溅射是一种高科技的薄膜材料制备技术,用于解决不同领域的薄膜应用需求,具有很高的应用价值和市场前景。
反应离子刻蚀PPT课件
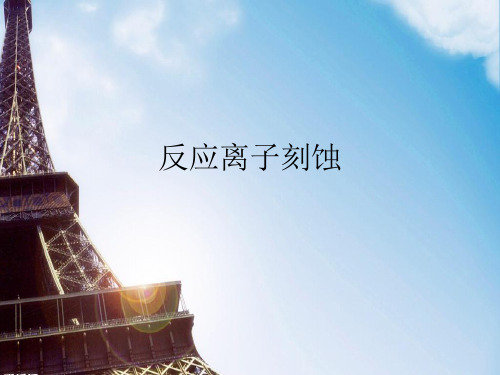
离子轰击的作用
A.离子轰击将被刻蚀材料表 面的原子键破坏使化学反应 增强。
B.再将淀积于被刻蚀表 面的产物或聚合物打掉
反 应 离 子 刻 蚀
在RIE设备中,使用非对称腔体。 为了保持电流连续性,小电极处应有更高 的电场(更高的RF电流密度)。
自由基反应各向同性刻蚀, 高能离子轰击各向异性刻蚀
光刻
反应离子刻蚀
刻蚀方法简介 RIE 刻 蚀 原 理 RIE 刻 蚀 术 语 RIE 刻蚀的工艺优化 RIE刻蚀不足与损伤 RIE 刻 蚀 机
刻蚀技术分类:
刻蚀技术
湿法 干法
化学刻蚀 电解刻蚀
离子束溅射刻蚀(物理作用) 等离子体刻蚀(化学作用) 反应离子刻蚀(物理化学作用)
干法刻蚀
特点: 利用刻蚀气体辉光放电形成的等离子体进行刻蚀。 优点: 各向异性好,选择比高,可控性、灵活性、重复性
RIE工艺参数的优化
刻蚀工艺参数:射频功率、腔体压强、气体流量等 1.若物理作用占主导则刻蚀损伤较大; 2.若化学作用占主导则刻蚀速度较慢,各项同性,表面 粗糙。 因此,选择最优的刻蚀参数的组合可以 在保证表面光 滑和一定的速率和方向性。
条件
待处理 材料
通入气体
SiO2
CHF3、O2
GaAs AlAs DBR
它有三个电极可以将等离子体的产生与离子的加 速分开控制。
磁场强化活性离子刻蚀机(MERIE)
在传统RIE的基础上加上永久性的磁铁或线圈, 产生与晶片平行、与电场垂直的磁场
刻
蚀
过
程
抑制剂沉积或形成
示
意
图
刻蚀
为了获得高度的各项异性,
通常利用侧壁钝化技术,即在刻蚀露出的侧壁上形 成聚合物或二氧化硅保抑护制剂膜沉,积或使形侧成 壁不受刻蚀
反应离子刻蚀实验

反应离子刻蚀硅阵列实验一、实验目的:1、掌握反应离子刻蚀的基本原理。
2、掌握利用单晶硅刻蚀硅阵列的实验流程。
3、了解刻蚀后的硅阵列的表征方法。
二、实验原理刻蚀技术分为湿法刻蚀和干法刻蚀。
湿法刻蚀是传统的刻蚀工艺,把硅片浸泡在一定的化学试剂或试剂溶液中,使没有被抗蚀剂掩蔽的那一部分薄膜表面与试剂发生化学反应而被除去,其优点是操作简便、对设备要求低、易于实现大批量生产,并且刻蚀的选择性也好。
但是,它具有各项同性的缺点,即在刻蚀过程不但有所需要的纵向刻蚀,还有不需要的横向刻蚀,因而精度差,线宽一般在3μm以上。
干法刻蚀是应大规模集成电路生产的需要而被开发出的精细加工技术,它具有各项异性的特点,在最大限度上保证了纵向刻蚀,还控制了横向刻蚀。
反应离子刻蚀(Reactive Ion Etching,RIE)是干法刻蚀的一种,是以物理溅射为主并兼有化学反应的过程,通过物理溅射实现纵向刻蚀,同时应用化学反应来达到所要求的选择比,其基本工作原理是刻蚀气体(主要是F基和Cl基的气体)在高频电场(频率通常为13.56MHz)作用下产生辉光放电,使气体分子或原子发生电离,形成“等离子体”(Plasma)。
在等离子体中,包含有正离子(Ion+)、负离子(Ion-)、游离基(Radical)和自由电子(e)。
游离基在化学上是很活波的,它与被刻蚀的材料发生化学反应,生成能够由气流带走的挥发性化合物,从而实现化学刻蚀。
而质量较大的正离子,被阴极附近带负电的鞘层电压有效的加速,垂直轰击放置于阴极表面的硅片,以较大的动量进行物理刻蚀,这种离子轰击可大大加快表面的化学反应及反应生成物的脱附,从而导致很高的刻蚀速率。
三、实验装置ME-3A型多功能磁增强反应离子刻蚀机四、实验内容和步骤1. 硅片的清洗:采用RCA标准清洗法进行硅片的清洗,具体步骤:(1)SPM清洗:去除硅片表面的有机污物和部分金属,(2)DHF清洗:去除硅片表面的自然氧化膜,(3)APM清洗(SC-1):去除硅片表面的颗粒和金属,(4)HPM清洗:去除硅表面的钠、铁、镁和锌等金属污染物。
- 1、下载文档前请自行甄别文档内容的完整性,平台不提供额外的编辑、内容补充、找答案等附加服务。
- 2、"仅部分预览"的文档,不可在线预览部分如存在完整性等问题,可反馈申请退款(可完整预览的文档不适用该条件!)。
- 3、如文档侵犯您的权益,请联系客服反馈,我们会尽快为您处理(人工客服工作时间:9:00-18:30)。
磁控反溅射刻蚀试验2006年公司提出准备上电子束钢带真空镀膜项目成立项目组。
于是开始进行查资料,学习相关知识的前期准备工作。
2007年项目正式投入生产计划,项目组开始做方案,然后进入方案论证和设计阶段。
至2010年初生产线装配和真空系统基本完成。
2010年4月溅射刻蚀第一个设计方案开始正式进入试验,一直到2011年底,进行了6次大的设计改进和试验(这中间小改不计其数),2011年11月基本定型,将新的定型方案投入生产,由于公司的原因,这个方案的外加工零件直到2014年底才回到公司。
经过开机验证,达到设计和应用的要求。
第一部分,摘自2009年《反溅射刻蚀预处理初步试验方案》:1 本试验的基本依据:1.1 阿登纳《连续试制线上使用PVD 新型钢带镀膜技术:加工工艺和镀膜发展》(2002):反转磁控溅射刻蚀:“这种设备在带材表面产生强度约为25mT的磁场,为了确保稳定的运行,将用于磁控技术中相似的中频电源用于溅射刻蚀工作站。
电流密度可以达到约10mA/cm2。
通过由稀土磁体组成的磁场系统,可以在厚度为0.9mm的钢带表面保持稳定的磁控放电,对钢带的刻蚀率达到15~20nm/s”。
(注:带宽300mm,速度30米/分)1.2 FEP《金属薄板和带的PVD镀膜(From FEP Annual Report 1999)》:The current pretreatment of metallic sheets and strips(当前的钢带预处理): “采用Pulse plasma Activated Treatment(脉冲等离子体激活处理。
注:基本原理和结构同阿登纳的反转磁控溅射刻蚀),刻蚀速率约15nm/s, The power feed for the discharge pulses unipolar(用单极脉冲放电电源)。
pulse frequencies in the range 10–30kHz(脉冲频率在10–30 kHz之间)”。
2005年FEP宝钢会议文章介绍:钢带1米带宽,30KW,20-50KHz,正弦波电源可以达到5—10纳米(1米/秒走带速度)刻蚀速率。
辊筒磁场组件钢带水冷阳极 磁控放电区域磁控放电俯视图氩气进口溅射电源磁控反溅射刻蚀原理示意图这是利用磁控溅射的基本原理,将基材(钢带)作为普通磁控溅射镀膜装置中的靶材来进行溅射刻蚀。
钢带作为磁控溅射靶的阴极,氩气离化后,氩离子带正电,必然以较快的速度和较大的能量冲向钢带,起到溅射清洁和活化金属表面,使电子束蒸镀到基材上的膜层更加牢固的一种工艺方法。
我们知道,由于蒸镀镀膜是用合适的热源将固体金属变成金属蒸汽,再附着到基材上。
而金属蒸汽是由膜材金属的原子或原子团组成,基本上呈电中性。
从坩埚里的靶材蒸腾到坩埚上方的钢带基材上,能量是不够附着牢固的。
要将微米甚至纳米级的膜材牢固的镀在钢带基材上,应该有三种工艺手段联合使用才能达到目的:1、用磁控溅射的方式,让电离后的氩离子去冲击钢带,起到清除钢带表面杂质、活化钢带表面的目的。
2、采用离化金属蒸汽方式,使金属蒸汽的原子变成离子。
目前有四种方式可以采用:无斑热弧离化装置,空心阴极阵列离化装置,棒状阴极离化装置和磁控对靶离化装置。
3、金属蒸汽离化后,用偏压电源给钢带加上负偏压,使金属离子获得更大的动能飞向钢带基材。
磁控反溅射刻蚀是钢带进入真空系统后预处理的第一个重要过程,为保障后续的工艺过程提供坚实的基础,所以其工作是否有成效,对整个镀膜过程还是比较关键的。
当钢带温度达到一个理想温度时(国外文献一般认为摄氏300度左右比较合适),可以增加钢带表面的活性,是镀层更加牢靠。
而磁控反溅射可以提高钢带温度,有可能节省专用的加热电子枪。
2 工艺条件范围及预订目标:2.1 本底真空度:工作时先将预处理真空室抽至真空度高于10-3Pa(即压强低于10-3Pa)。
然后通入氩气,使之达到下述的工作压强。
并记录对应的质量流量数值(单位:sccm,即“在标准大气压下的立方厘米/每分钟”)。
2.2 工作压强:3~8×10-1 Pa。
先做3×10-1 Pa、5×10-1 Pa、8×10-1 Pa共3点。
2.3 工作电压:300~600V。
此电压由电流强度和工作压强确定。
2.4 电流密度:11~55.5mA/cm2。
按放电区域15×60cm计算,溅射电源的电流输出为10~50A。
记录每组试验的电流强度和功率密度(W/cm2),功率密度为该试验点的电流电压乘积除以放电区域面积。
并依此计算出各点功率效率{(nm/min)/(W/cm2)}。
2.5 水平磁场感应强度:40~60mT。
根据加减调节磁轭后的磁感应强度做3点,首先做不加调节磁轭的一点(40mT),根据试验情况再做其它点。
不加调节磁轭的磁场系统实测数据:仪器:力田PFX-045A特斯拉计。
方法:特斯拉计探头测量面垂直于磁力线,测量磁场组件滚筒轴线区域磁力线平行于钢带表面的磁感应强度(B//)。
钢带厚度0.5mm,探头距钢带表面约5mm,两端按阳极装配好的距离放好不锈钢挡板。
测量结果:钢带中部约39mT,两端分别为39mT和42mT;两端挡板分别为26mT和27mT。
2.6 靶基距:调节范围60~120mm。
以10为调节步长,找到刻蚀效果最好的靶基距。
2.7 电源供给方式:依次使用直流、单极脉冲、双极脉冲进行试验,以确定最佳电源模式。
2.8 脉冲频率:10–30kHz。
以5kHz为步长,寻找合适的脉冲频率。
先做10、20、30kHz共3点。
2.9 占空比:10%~80%。
以10%为步长, 寻找合适的占空比。
先做10%、40%、60%、80%共4点。
2.10 预定目标:刻蚀率应达到15~20nm/s(按阿登纳300mm带宽)。
3 设备和材料:3.1 溅射电源的选择依据:见上述阿登纳和FEP文献摘录。
按放电区域15×60cm计算,30KW 电源平均33W/cm2;按工作电压600V计,电流50A,电流密度可达到55.5mA/cm2。
满足上述文献的范围。
3.2 溅射电源型号和参数:由于为试验阶段,故选择多用型电源。
采用成都普斯特MSM 30KW三用电源,空载电压≥800V,工作电压200~600V;工作方式(开关选定):A、直流,B、单极脉冲,C、双极脉冲;脉冲频率3KHz~30KHz连续可调,正负脉冲占空比10%~80%连续可调。
正负极性平均电流独立稳流,精度1%,直流稳流精度:1%,频率稳定度:1% 。
打火自动保护功能。
3.3 试样钢带(片)的规格和要求:3.3.1 试样应经过化学和物理清洗并烘干,为便于测量,表面应光滑平整并且不能有荷叶边。
尽量做到与实际镀膜时对钢带的要求一样。
3.3.2 静态溅射试样钢片规格:300×600×0.5mm。
数量:80张。
4 验证反溅射装置的结构和试选最佳电源模式:4.1 按设计要求安装好所有设备,用1000V摇表检查阳极与屏蔽罩间的绝缘不小于10MΩ。
将电源输出正极接阳极组件汇流排,电源负极接在磁场组件上。
按设备和电源使用要求接好冷却水(其中电源冷却水要求:进水温度20℃,水压 1.5-3.0Kg/cm2,应使用软水,防止电源水道结垢)。
4.2 电源模式初步选择:4.2.1 直流模式试溅射:磁场为不加调节磁轭的一点(0.5厚钢板,40mT),靶基距90mm。
抽本底真空大于10-3Pa(具体数值根据实际能达到的水平而定),充入氩气,将工作压强调到5×10-1 Pa。
开启溅射电源,调节电流电位器,输出电流和电压将随之增加,直到工作电压为600V(此时电流不应超过50A,否则应降低工作压强)。
观察起辉情况,在钢带区域是否均匀、有无打火现象。
如能正常运行,则可在此工艺条件进行计时刻蚀,测量此工艺条件的刻蚀速率。
并可继续进行后续试验,直到阳极绝缘层被铁镀层污染发生打火或短路为止。
如不能正常运行,则需根据情况改进后再试验。
4.2.2 单极脉冲模式溅射:以4.2.1条的磁场、靶基距、工作压强和工作电压,做3组脉冲频率和占空比:脉冲频率10kHz,占空比40%;脉冲频率20kHz,占空比60%;脉冲频率30kHz,占空比80%。
测量这3组工艺条件下的刻蚀速率。
4.2.3 双极脉冲模式溅射:以4.2.1条的磁场、靶基距、工作压强和工作电压,做3组脉冲频率和占空比:脉冲频率10kHz,占空比40%;脉冲频率20kHz,占空比60%;脉冲频率30kHz,占空比80%。
测量这3组工艺条件下的刻蚀速率。
比较3种溅射方式的刻蚀速率和工作稳定程度,选择最优的方式做进一步试验。
4.3 在以上试验过程中,铁原子(原子团)被溅射出来后会使阳极绝缘层表面被污染导电,有可能使实验不能继续进行下去。
当打火或短路使装置不能正常运行时应终止试验,观察绝缘层表面的铁镀层污染分布,改进绝缘结构后再继续进行后面的试验。
5 试验方法和步骤:5.1 确定电源模式后,可逐步确定本试验中的7个可变工艺参数:工作压强、电流、电压、磁场、靶基距、脉冲频率、脉冲占空比(如确定的是直流模式,则没有频率参数)。
相比之下,其中的电压、磁场、靶基距3个参数和其它参数的关系相对单纯,可以先确定。
5.1.1 确定溅射电压:设定工作压强=5×10-1 Pa、磁场=40mT、靶基距=90mm、脉冲频率=20kHz、占空比=60%。
调整电流使电压分别为400V、500V、600V做3张样片,用效果最好的一张样片确定电压值。
5.1.2 确定磁场:设定工作压强=5×10-1 Pa、靶基距=90mm、脉冲频率=20kHz、占空比=60%、调整电流使电压为5.1.1确定好的电压值。
在磁场为40mT、50mT、60mT条件下做3张样片,用效果好的一张确定磁场值。
5.1.3 确定靶基距:设定工作压强=5×10-1 Pa、脉冲频率=20kHz、占空比=60%、调整电流使电压为 5.1.1确定好的电压值、磁场为 5.1.2确定的磁场值。
在靶基距=60mm、70mm、80mm、100mm、110mm、120mm条件下做6张样片,用效果最好的一张确定靶基距。
5.1.4 其余4个参数均先取适当的点做所有组合,然后根据试验情况再调整。
工作压强:3×10-1Pa、5×10-1 Pa、8×10-1 Pa共3点。
电流:在5.1.1确定好的电压值条件下,记录不同组合下的电流值。
脉冲频率:10kHz、20kHz、30kHz共3点。
脉冲占空比:10%、40%、60%、80%共4点。
共做样片36张。
第二部分,实际试验:磁场部分是沿用普通磁控靶结构简化而成,基本没有改动过。