热处理对模具失效的影响与对策
模具热处理的变形问题与防范措施的分析(标准版)

( 安全技术 )单位:_________________________姓名:_________________________日期:_________________________精品文档 / Word文档 / 文字可改模具热处理的变形问题与防范措施的分析(标准版)Technical safety means that the pursuit of technology should also include ensuring that peoplemake mistakes模具热处理的变形问题与防范措施的分析(标准版)模具的形状很复杂、品种也比较多、表面比较粗糙,所以制造难度是很大的。
模具经过热处理后会产生严重的变形,这将对模具的使用寿命和质量造成严重的影响。
所以,在模具热处理的过程中要预防和减少模具的变形。
下面主要讲了模具热处理的变形的影响因素和它的预防措施。
模具热处理中的影响因素和变形原因1.1模具材料的影响1.1.1模具材质的影响某工厂有一些结构比较复杂的模具,这些模具都是带有¢60mm圆孔的,这些模具经过热处理之后,一些相邻的模具圆孔会发生椭圆的变形,从而使模具出现报废。
这种钢是微变形钢的一种,按常理来说,不会发生严重变形的现象。
所以,我们对这些变形比较严重的模具进行研究,发现了许多共晶碳化物存在于模具钢中,分布形状呈块状和带状。
1.1.1.1模具发生变形的原因模具钢中有着一些碳化物,这些碳化物是不均匀的,而且按一定的方向呈现,钢的基体组织高于这些碳化物膨胀系数的30%,所以在模具加热的时候,这些碳化物会减小模具圆孔的膨胀,在模具冷却的时候,这些碳化物又会减少模具内孔发生收缩的现象,从而使模具圆孔发生严重变形的现象,就是指这些模具的圆孔产生椭圆的现象。
1.1.2模具选材的影响某工厂从模具的热处理简便的方面考虑,选择了一些截面尺寸相差很大的钢,它的硬度要求比较高,在淬火后模具变形较小。
模具热处理质量影响因素及预防路径思考
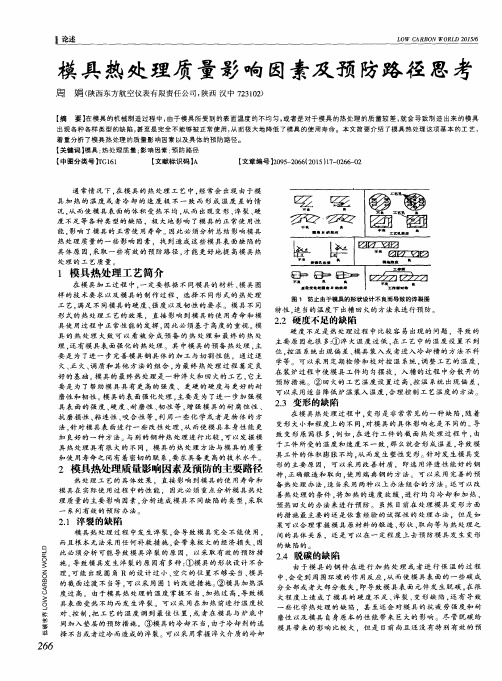
主要 原 因 也很 多: ① 淬 火 温度 过 低 , 在 工 艺 中 的 温度 设 置 不 到
具表面的强度 、 硬度 、 耐磨性 、 韧性等 , 增 强模 具 的 耐 腐 蚀 性 、 抗磨损性 、 粘连性 、 咬合性 等, 利 用 一 些 化 学或 者 是 物 体 的 方 法. 针对模具表面进行一些改性处理 , 从 而使 模 具 本 身 性 能 更
和 使 用 寿命 之 间 有 着 密切 的联 系, 要 求 具备 更 高 的技 术水 平 。
2 模具热处理质量影响因素及预 防的主要路径
热 处 理 工 艺 的 具 体 效 果 .直 接 影 响 到 模 具 的使 用 寿命 和 模 具 在 实 际使 用 过 程 中的 性 能 , 因此 必 须重 点分 析 模 具 热 处
加 良好 的 一 种 方 法 。与 别 的 钢种 热 处理 进 行 比较 。 可 以发 掘 模 具 热 处 理 具 有很 大 的 不 同 .模 具 的 热 处 理 方 法与 模 具 的质 量
2 . 3 变形 的缺 陷
在模 具热处理过程 中. 变形 是 非 常 常 见 的 一 种 缺 陷 , 随 着
幂 ^
t
^
一 ■ t J  ̄ , l l t / , V
^
羊童
工 靠^董 廊
^
眨z = =
[
矗
具 体 原 因, 采 取 一 些 有 效 的 预 防路 径 , 才 能 更 好 地提 高 模 具 热
处 理 的 工 艺 质 量
餐● 毳 位量 鼻 膏 -蕴 琏
-
1 模 具热 处理工艺简介
理. 还 有模 具 表 面强 化 的 热 处理 。其 中模 具 的预 备 热 处 理 , 主 位, 控 温 系统 出现 偏 差 、 模 具 装 入 或 者进 入 冷 却 槽 的 方 法 不 科 要 是 为 了进 一 步 完 善 模 具 钢 具 体 的 加 工 与 切 割 性 能 ,通 过 退 学 等 。 可 以 采 用 定期 检 修 和校 对控 温 系统 , 调 整 工 艺 的 温度 , 火、 正 火、 调 质 和 其他 方 法 的 组 合 , 为最终热处理过 程奠定 良 在 装 炉 过程 中使 模 具 工件 均 匀 摆放 ,入 槽 的 过 程 中分 散 开 的 好 的基 础 。 模 具 的 最终 热 处 理 是 一 种 淬 火 和 回 火 的 工 艺 , 它 主
模具失效及解决方法实例

模具失效及解决方法实例一、引言模具是工业生产中必不可少的工具,它能够成型出各种形状和尺寸的产品。
然而,模具在使用过程中会受到各种因素的影响,导致失效。
模具失效不仅会影响生产效率,增加生产成本,还会影响产品的质量。
因此,了解模具失效的原因和解决方法非常重要。
本文将介绍模具失效的类型、原因以及一些常见的解决方法实例。
二、模具失效类型1. 磨损:模具在使用过程中,其工作表面会与材料不断接触,导致工作表面磨损。
2. 腐蚀:模具受到化学或电化学作用,导致腐蚀损坏。
3. 塑性变形:材料在模具内塑性变形,导致模具变形。
4. 热疲劳:模具在工作过程中频繁冷热交替,导致热疲劳损坏。
5. 裂纹扩展:由于制造、使用过程中产生的裂纹在交变应力作用下扩展导致破坏。
三、模具失效原因1. 操作不当:如超负荷生产、材料硬度过高、材料中有杂质等都会导致模具过早磨损或腐蚀。
2. 维护不当:润滑不足、冷却系统不良等都会导致模具过热或腐蚀。
3. 材料问题:模具材料的选择不当,如硬度、耐腐蚀性、耐磨性等都会影响模具的使用寿命。
4. 制造问题:制造过程中的缺陷,如铸造缺陷、热处理不当等都会导致模具产生裂纹或塑性变形。
四、解决方法实例1. 磨损修复:对于磨损的模具,可以采用堆焊、喷涂等方法进行修复。
例如,对于磨损的凸轮表面,可以采用堆焊的方式进行修复,选择耐磨性好、焊前流动性好的合金堆焊焊条。
在修复过程中,需要注意控制热输入,避免热影响扩大。
同时,对于一些磨损严重的模具,还可以采用喷涂的方法进行修复,选择耐磨性好、耐腐蚀的涂层材料,如金属陶瓷、镍基涂层等。
2. 腐蚀防护:对于腐蚀的模具,可以采用镀层、表面处理等方法进行防护。
例如,对于受腐蚀的模具钢表面,可以采用镀铬或镀锌等防腐方法进行防护。
此外,还可以采用表面处理的方法提高模具表面的抗腐蚀性能,如采用氧化处理、磷化处理等。
3. 温度控制:对于塑性变形的模具,可以通过调整生产工艺、选择合适的材料等方法来降低模具工作时的温度。
影响模具热处理质量的因素及预防措施

m m。
I 模 具 热 处 理
影响模具热处理质量的因素及预防措施
日照市 技师学 院 ( 山东 2 7 6 8 2 6 ) 刘招 安
一
、
热处理工艺因素的影响及防止措施
和 加 热 温 度 不 同 , 向 炉 内 送 入 可 以 控 制 的 保 护 气
在 热 处 理 的 过 程 中 , 由 于 热 处 理 工 艺 控 制 不 当 ,使 工 件 产 生某 些 缺 陷 ,如 氧化 、脱 碳 、过 热 、 过烧 、硬 度 不 足 、 变形 与 开 裂 等 。对 热 处 理 质量 影 响很 大 ,甚 至 造 成 工件 报 废 。其 中氧 化 与 脱 碳 、变 形 与开 裂 是 最 常 见的 热 处理 缺 陷 。
氛 ,使工件表面不氧化 、脱碳 ,也不渗碳 。 ( 4 )采用真空炉加热 它不但能防止氧化与脱
碳 ,还 能 使 工件 净 化 ,提高 性 能 。但设 备 复 杂 ,应
用较 少 。
2 . 变形与开裂
淬火 中变形 与开裂主要是淬火 时形成的内应 力 引起的 。形成内应 力的原因主要是热应 力和相变应 力。热应力是 由于工件在加热和冷却时内外温度不
构 复 杂 ,曲面 较 多 ,淬 火 轨迹 多变 , 目前 国内 激 光 淬 火 过 程 中的 手 动采 点记 录 后进 行 简单 编程 的 方式
( 即示教模式 )不适用汽车模具生产对效率的极大
要 求 ,制 约 了激 光热 处 理 在 汽车 覆 盖 件 模具 制造 中 的推 广 应 用 ,无 论从 设 备 的 完善 ,软 件 的 配套 ,还
一
1 . 氧化与脱碳
氧化与脱碳是工件在加热时 ,由于加热炉 中介 质控制不好而 出现的缺陷。 钢在氧化介质中加热时 ,会发生氧化而在表面
模具热处理的主要缺陷与防止措施
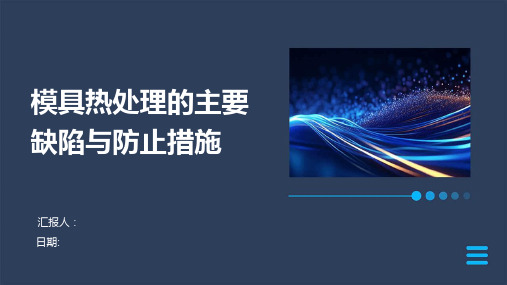
模具热处理的基本原理
将模具加热到一定的温度,并保 持一定的时间,以实现模具材料 的相变和晶粒细化等物理变化。
通过不同的加热、保温和冷却方 式,控制模具材料的组织结构和
性能特征。
ห้องสมุดไป่ตู้
在热处理过程中,需要注意控制 加热速度、保温时间和冷却速度 等参数,以避免模具出现裂纹、
变形和氧化等问题。
02
模具热处理的主要缺 陷
模具热处理的主要 缺陷与防止措施
汇报人: 日期:
目录
• 模具热处理概述 • 模具热处理的主要缺陷 • 防止措施 • 模具热处理的应用实例 • 总结与展望
01
模具热处理概述
模具热处理的目的和意义
提高模具的硬度和强 度,以满足模具的使 用性能要求。
改善模具的加工性能 ,以降低模具的加工 成本。
优化模具的韧性和耐 磨性,以提高模具的 使用寿命。
防止措施
采用合理的材料和热处理工艺,如淬火、回火和表面强化 处理等,提高模具的硬度和耐磨性;同时加强生产过程中 的质量检测,及时发现并处理问题。
实例二:注塑模具的热处理
01
模具类型
注塑模具是一种用于塑料制品成型的模具。
02
热处理要求
注塑模具的热处理需控制模具的硬度和耐腐蚀性,以确保制品的尺寸精
度和表面质量。
4. 通过采取适当的防止措施,可以减少模具在后 续使用中的磨损和损坏,提高模具的耐用性,降 低维修和更换成本。
未来研究与发展的展望
1. 进一步研究和开发新的热 处理技术和工艺,以提高模 具的性能和寿命。
2. 针对不同的模具材料和类 型,研究更合适的热处理工 艺和参数,以获得更好的处 理效果。
3. 进一步探索热处理过程中 的缺陷形成机制和防止措施 ,以减少或消除缺陷的产生 。
模具热处理缺陷及预防
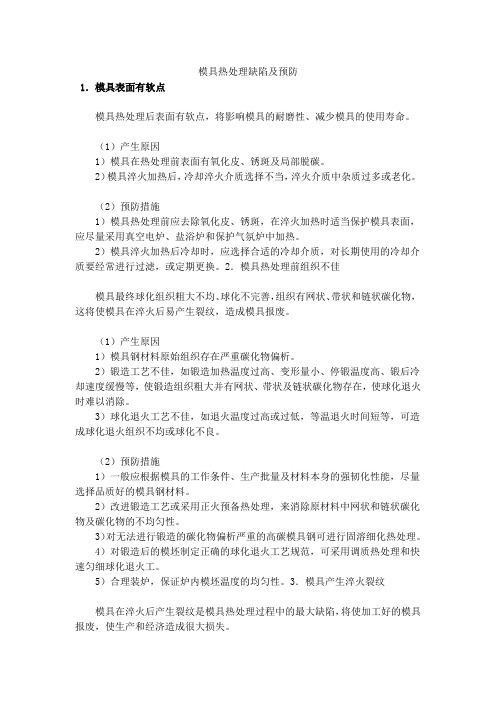
模具热处理缺陷及预防1.模具表面有软点模具热处理后表面有软点,将影响模具的耐磨性、减少模具的使用寿命。
(1)产生原因1)模具在热处理前表面有氧化皮、锈斑及局部脱碳。
2)模具淬火加热后,冷却淬火介质选择不当,淬火介质中杂质过多或老化。
(2)预防措施1)模具热处理前应去除氧化皮、锈斑,在淬火加热时适当保护模具表面,应尽量采用真空电炉、盐浴炉和保护气氛炉中加热。
2)模具淬火加热后冷却时,应选择合适的冷却介质,对长期使用的冷却介质要经常进行过滤,或定期更换。
2.模具热处理前组织不佳模具最终球化组织粗大不均、球化不完善,组织有网状、带状和链状碳化物,这将使模具在淬火后易产生裂纹,造成模具报废。
(1)产生原因1)模具钢材料原始组织存在严重碳化物偏析。
2)锻造工艺不佳,如锻造加热温度过高、变形量小、停锻温度高、锻后冷却速度缓慢等,使锻造组织粗大并有网状、带状及链状碳化物存在,使球化退火时难以消除。
3)球化退火工艺不佳,如退火温度过高或过低,等温退火时间短等,可造成球化退火组织不均或球化不良。
(2)预防措施1)一般应根据模具的工作条件、生产批量及材料本身的强韧化性能,尽量选择品质好的模具钢材料。
2)改进锻造工艺或采用正火预备热处理,来消除原材料中网状和链状碳化物及碳化物的不均匀性。
3)对无法进行锻造的碳化物偏析严重的高碳模具钢可进行固溶细化热处理。
4)对锻造后的模坯制定正确的球化退火工艺规范,可采用调质热处理和快速匀细球化退火工。
5)合理装炉,保证炉内模坯温度的均匀性。
3.模具产生淬火裂纹模具在淬火后产生裂纹是模具热处理过程中的最大缺陷,将使加工好的模具报废,使生产和经济造成很大损失。
(1)产生的原因1)模具材料存在严重的网状碳化物偏析。
2)模具中存在有机械加工或冷塑变形应力。
3)模具热处理操作不当(加热或冷却过快、淬火冷却介质选择不当、冷却温度过低、冷却时间过长等)。
4)模具形状复杂、厚薄不均、带尖角和螺纹孔等,使热应力和组织应力过大。
热处理技术对模具性能的影响
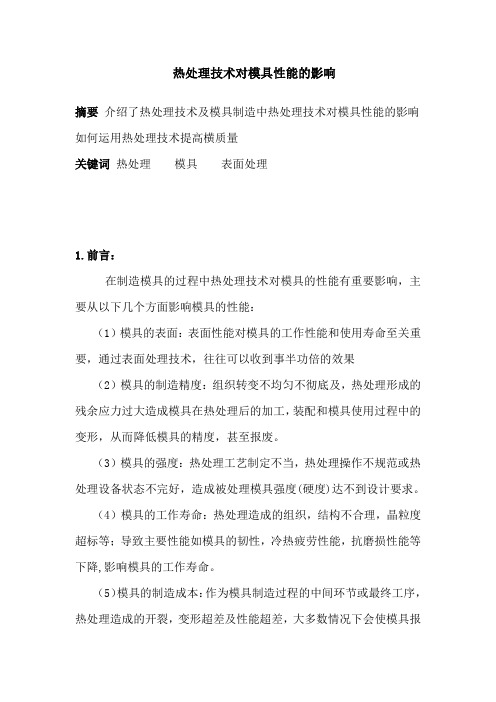
热处理技术对模具性能的影响摘要介绍了热处理技术及模具制造中热处理技术对模具性能的影响如何运用热处理技术提高横质量关键词热处理模具表面处理1.前言:在制造模具的过程中热处理技术对模具的性能有重要影响,主要从以下几个方面影响模具的性能:(1)模具的表面:表面性能对模具的工作性能和使用寿命至关重要,通过表面处理技术,往往可以收到事半功倍的效果(2)模具的制造精度:组织转变不均匀不彻底及,热处理形成的残余应力过大造成模具在热处理后的加工,装配和模具使用过程中的变形,从而降低模具的精度,甚至报废。
(3)模具的强度:热处理工艺制定不当,热处理操作不规范或热处理设备状态不完好,造成被处理模具强度(硬度)达不到设计要求。
(4)模具的工作寿命:热处理造成的组织,结构不合理,晶粒度超标等;导致主要性能如模具的韧性,冷热疲劳性能,抗磨损性能等下降,影响模具的工作寿命。
(5)模具的制造成本:作为模具制造过程的中间环节或最终工序,热处理造成的开裂,变形超差及性能超差,大多数情况下会使模具报废,即使通过修补仍可继续使用,也会增加工时,延长交货期,提高模具的制造成本。
因为模具的热处理对模具的性能影响很大,所以我们要对模具进行热处理。
2.模具热处理2.1热处理工艺金属热处理是机械制造中的重要工艺之一,与其他加工工艺相比,热处理一般不改变工件的形状和整体的化学成分,而是通过改变工件内部的显微组织,或改变工件表面的化学成分,赋予或改善工件的使用性能。
其特点是改善工件的内在质量,而这一般不是肉眼所能看到的。
为使金属工件具有所需要的力学性能、物理性能和化学性能,除合理选用材料和各种成形工艺外,热处理工艺往往是必不可少的。
热处理工艺一般包括加热、保温、冷却三个过程,有时只有加热和冷却两个过程。
这些过程互相衔接,不可间断。
常见的热处理方式:正火:将钢材或钢件加热到临界点的适当温度保持一定时间后在空气中冷却,得到珠光体类组织的热处理工艺。
退火:将亚共析钢工件加热至AC3以上20—40度,保温一段时间后,随炉缓慢冷却(或埋在砂中或石灰中冷却)至500度以下在空气中冷却的热处理工艺。
热处理工艺对H13模具钢组织和性能的影响
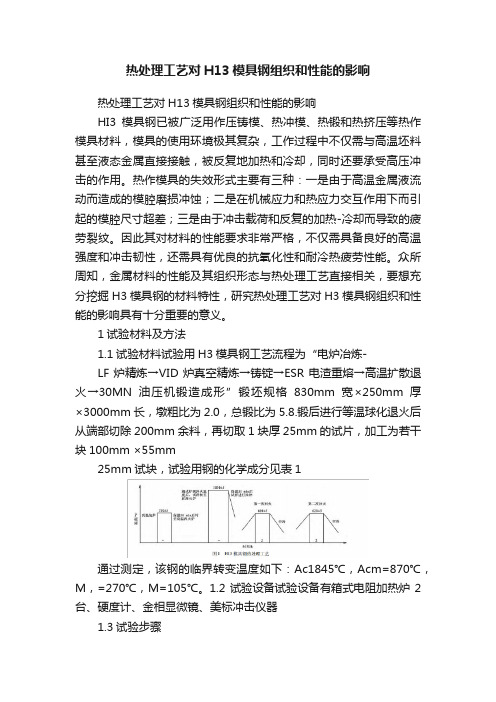
热处理工艺对H13模具钢组织和性能的影响热处理工艺对H13模具钢组织和性能的影响HI3模具钢已被广泛用作压铸模、热冲模、热锻和热挤压等热作模具材料,模具的使用环境极其复杂,工作过程中不仅需与高温坯料甚至液态金属直接接触,被反复地加热和冷却,同时还要承受高压冲击的作用。
热作模具的失效形式主要有三种:一是由于高温金属液流动而造成的模腔磨损冲蚀;二是在机械应力和热应力交互作用下而引起的模腔尺寸超差;三是由于冲击载荷和反复的加热-冷却而导致的疲劳裂纹。
因此其对材料的性能要求非常严格,不仅需具备良好的高温强度和冲击韧性,还需具有优良的抗氧化性和耐冷热疲劳性能。
众所周知,金属材料的性能及其组织形态与热处理工艺直接相关,要想充分挖掘H3模具钢的材料特性,研究热处理工艺对H3模具钢组织和性能的影响具有十分重要的意义。
1试验材料及方法1.1试验材料试验用H3模具钢工艺流程为“电炉冶炼-LF炉精炼→ⅥD炉真空精炼→铸锭→ESR电渣重熔→高温扩散退火→30MN油压机锻造成形”锻坯规格830mm宽×250mm厚×3000mm长,墩粗比为2.0,总锻比为5.8.锻后进行等温球化退火后从端部切除200mm余料,再切取1块厚25mm的试片,加工为若干块100mm ×55mm25mm试块,试验用钢的化学成分见表1通过测定,该钢的临界转变温度如下:Ac1845℃,Acm=870℃,M,=270℃,M=105℃。
1.2试验设备试验设备有箱式电阻加热炉2台、硬度计、金相显微镜、美标冲击仪器1.3试验步骤(1)淬火预热和淬火加热分别在两台箱式电阻炉内进行,首先将两台箱式电阻炉升至所规定的温度(2)将100mm×55mm×25mm试样放置在预热加热箱式电阻炉中保温30min(到温装炉);(3)保温结束后将试样转移至淬火加热的电阻炉中进行淬火温度保温30min(开关炉后,炉温降低,待电阻炉升至规定温度时开始计算保温时间)(4)保温结束后针对样块进行淬火(采用水或油淬方案,水或油温控制在30℃以下);(5)回火在箱式电阻炉内进行,按照规定的温度对试样进行回火;(6)回火结束后针对试样样块进行硬度检验并记录;(7)将试样加工至美标冲击要求尺寸后进行冲击试验并记录(8)金相组织检验。
模具热处理中失效变形的原因及其对策

回火 常规 热处 理 , 温度 要求 HR 5 , C 7 仅能 拉深 10 00 件 即早期 失 效 ,后 改 为 T O IA钢 采用 淬 火+ 中温 回 火 后 硬度 为 HR 5 , 均 寿命 达 4 0 C5平 0 0次 。 而后又 改 为 3 0 4 0 回火 , 其 硬 度 在 HR 4 , 寿命 8 ~ 0℃ 使 C8则 可 达 6 0 ~ 0 0次 。而 C l Mo 00 80 r2 V钢制 冲头 ,冲厚
识。
、
热 处 理 中 模 具 的 失 效 变 形 的 原 因 及 影 响
因素
由于模 具各 处 厚 薄不 均 及 存在 尖 锐 圆角 等 因 素 . 以在淬火 时 引起 模 具各部 位之 间 的热应力 和 所
组织 应力 的不 同 ,导 致各 部位体 积膨 胀 的不 同 , 使
模具 淬火后 产生 失效变 形 。 中常见 的模 具失效 的 其
管理 。
维普资讯
第2 2卷第 1 期
彭 刚 模 具 热 处 理 中 失 效变 形 的原 因 及其 对 策
6 1
正 确 的金 相 组织 , 而应 力 消 除程 度 又与 温 度 、 间 时 1 热 处理 对模 具 失效 变形 的影响 因素 . 热 处理 是 以“ 热—— 保 温—— 冷却 ” 大 隐 加 三 成 正 比关系 ( 图 1 。 见 )
形式 、 因如表 l 示 。 原 所
正 是 因为 热处 理 技 术与 模 具 质量 有 十 分密 切
表 1 模 具 失效的形 式 、 因及 对策 原
收稿 日期 :0 7 0 — 5 20 — 1 0 作者简介 : 刚( 9 9 )男 , 彭 1 5 一 , 湖南岳 阳人 , 阳工 业技 术学院一级实 习指导教师。主要研 究方 向: 岳 模具设计与制造及 工程
模具热处理的主要缺陷与防止措施

总结词
模具热处理过程中,由于加热和冷却过 程中与空气中的氧气接触,容易导致模 具氧化和脱碳。
VS
详细描述
模具氧化和脱碳会影响其表面质量和耐磨 性。氧化和脱碳的原因可能包括加热和冷 却速度过快、温度过高或过低、保护气氛 不足等。为了防止氧化和脱碳,需要控制 加热和冷却速度,并采用适当的温度和时 间,同时采用保护气氛或真空热处理技术 。
03
防止措施
变形防止措施
控制加热速度
采用合理的加热速度,避免模具局部过热,减少变形 。
均匀加热
确保模具各部分受热均匀,避免因温度梯度引起的变 形。
合理选择冷却方式
采用适当的冷却方式,如分级淬火、预冷淬火等,以 减少变形。
开裂防止措施
合理选择材料
选择具有适当强度和韧性的材料,以减少开裂 的可能性。
残余应力过大
总结词
模具热处理过程中,由于加热和冷却不均匀 或组织转变不充分,容易导致模具残余应力 过大。
详细描述
模具残余应力过大会影响其尺寸精度和稳定 性,进而影响产品质量。残余应力过大的原 因可能包括加热或冷却速度过快、温度过高 或过低、组织转变不充分等。为了防止残余 应力过大,需要控制加热和冷却速度,并采 用适当的温度和时间,同时对模具进行充分 的回火处理。
模具热处理的主要缺陷与防 止措施
汇报人: 2023-12-21
目录
• 模具热处理概述 • 模具热处理的主要缺陷 • 防止措施 • 实际应用案例分析
01
模具热处理概述
模具热处理的目的和意义
提高模具的硬度和耐磨性
通过热处理,模具的表面硬度可以提高,从而提高其耐磨性和使用 寿命。
改善模具的韧性
适当的热处理可以改善模具的韧性,使其在承受冲击和振动时不易 开裂或崩坏。
工模具零件热处理开裂分析与对策

工模具零件热处理开裂分析与对策热处理是金属制造加工过程中的重要环节之一,对于提高金属材料的机械性能和使用寿命具有重要作用。
然而,在热处理过程中,工模具零件往往会出现开裂的现象,严重影响产品质量和使用寿命。
因此,对工模具零件热处理开裂进行分析并提出对策是非常必要的。
首先,从材料因素的角度看,材料的化学成分和组织结构是导致开裂的关键因素。
例如,钢材中的含碳量过高,会导致材料的脆性增加,容易发生开裂。
另外,材料内部的非金属夹杂物和缺陷也会成为开裂的隐患。
其次,从工艺因素的角度看,热处理过程中的冷却速度、温度控制、保温时间等因素也会对零件开裂产生重要影响。
不合理的冷却速度或温度控制会导致零件内部应力过大,从而引发开裂。
保温时间过长或过短也会导致零件热变形和开裂。
针对以上问题,可以采取以下对策来解决工模具零件热处理开裂的问题。
首先,对材料的选择要慎重。
选择低含碳量且具有良好可焊性的钢材,可以降低材料脆性,减少开裂风险。
此外,还应对材料进行严格的质量把控,避免有过多的夹杂物和缺陷。
其次,优化工艺参数。
根据工模具零件的具体要求,控制好热处理的温度、冷却速度和保温时间等参数,以确保零件内部的应力得到恰当释放,避免过大的残余应力引发开裂。
再次,改进热处理工艺。
可以尝试采用一些特殊的热处理工艺,如缓慢升温、预冷却等方法,以减少热应力的产生,并保证材料的均匀加热和冷却,从而降低开裂的风险。
此外,对于一些特殊的工模具零件,可以考虑进行局部加热处理。
通过对零件的局部加热,可以减少整体的热应力,提高零件的抗开裂能力。
需要注意的是,以上对策仅仅是一些建议,具体的措施应根据具体情况来进行确定。
对于工模具零件热处理开裂问题,必须结合实际情况进行分析,并进行试验验证,以得出最佳的解决方案。
模具设计中的热处理问题探讨

模具设计中的热处理问题探讨模具热处理是模具制造中的关键环节之一。
在模具的制造过程中,热处理对于模具的性能、寿命甚至是整个模具工艺都有着至关重要的作用。
因此,模具设计师需要对模具的热处理问题有着较为深入的了解和掌握,以确保模具质量的稳定和优化。
1. 热处理的基本原理及步骤热处理是通过改变材料的组织结构和性能来提高材料的硬度、强度和耐磨性等性能的方法。
模具的热处理通常可分为以下几个步骤:预热、加热保温、冷却和回火。
预热阶段是为了消除模具中的工作应力、缓慢升温,同时发挥了加热场的效应。
加热阶段将模具加热至所需的温度,并保持一段时间,以使模具中的结构发生相应改变。
冷却阶段是为了迅速降低模具的温度,并在最短时间内固定模具的组织结构,使之达到所需的硬度。
回火阶段是为了消除模具中的残留应力和提高其强度,同时使硬度得到柔化。
2. 热处理对模具性能的影响及要求模具的热处理不同于常规工艺用钢的热处理,更多的是要求在较高的温度下保持一段时间,并在水中迅速冷却。
这种处理方式使模具得到了更高的硬度和抗磨损性能,但同时也容易引起模具的变形或开裂,甚至缩短其使用寿命。
因此,热处理质量的好坏决定了模具的使用性能和周期。
在模具的热处理中,要根据模具材料的性质和使用条件来选择对应的热处理工艺,并对热处理过程中的温度、时间、冷却速度、回火温度和时间等参数进行精确的控制和调节。
此外,还要严格遵守处理规程,避免操作失误和设备故障,从而保证模具的热处理质量。
3. 模具热处理应用技巧模具的热处理中还需要注意以下几点技巧:(1)合理选择模具合金及热处理工艺。
不同的模具合金适用于不同的热处理工艺。
例如,高速钢的热处理工艺与工具钢的热处理工艺不同,其处理温度范围、预热时间、残余应力处理方式也有所不同。
(2)控制加热速率和温度。
加热速率和温度对于热处理质量的影响极大。
加热速度过快或加热温度过高会引起材料内部结构的变化而导致材料机械性能的下降。
因此,加热速率和温度都需要严格控制。
模具热处理若干问题的探讨
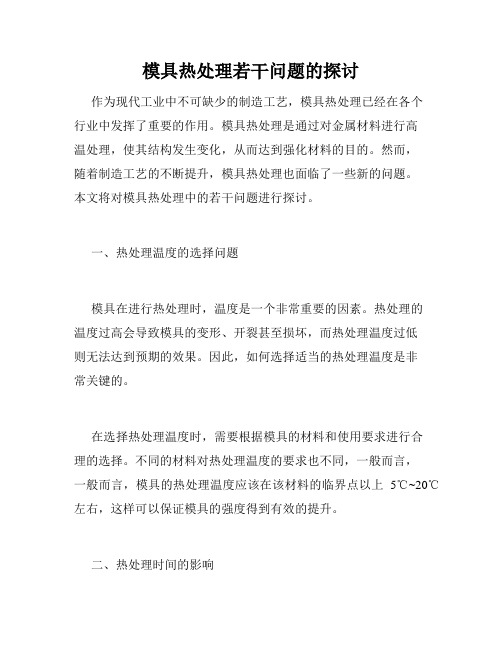
模具热处理若干问题的探讨作为现代工业中不可缺少的制造工艺,模具热处理已经在各个行业中发挥了重要的作用。
模具热处理是通过对金属材料进行高温处理,使其结构发生变化,从而达到强化材料的目的。
然而,随着制造工艺的不断提升,模具热处理也面临了一些新的问题。
本文将对模具热处理中的若干问题进行探讨。
一、热处理温度的选择问题模具在进行热处理时,温度是一个非常重要的因素。
热处理的温度过高会导致模具的变形、开裂甚至损坏,而热处理温度过低则无法达到预期的效果。
因此,如何选择适当的热处理温度是非常关键的。
在选择热处理温度时,需要根据模具的材料和使用要求进行合理的选择。
不同的材料对热处理温度的要求也不同,一般而言,一般而言,模具的热处理温度应该在该材料的临界点以上5℃~20℃左右,这样可以保证模具的强度得到有效的提升。
二、热处理时间的影响在热处理过程中,时间也是一个非常重要的因素。
热处理时间的长短直接影响到模具的强度和使用寿命。
一般而言,热处理时间长能够使材料结构更加致密,从而提高强度和耐磨性。
但是,过长的热处理时间也会导致模具变形、裂纹等问题。
因此,热处理时间的选择需要充分考虑模具的使用要求和工作环境等因素。
在具体实践中,需要根据不同的材料和使用要求选择合理的热处理时间,同时需要进行严格的控制和监测。
三、热处理工艺的优化为了解决模具热处理中的问题,许多制造企业开始尝试进行热处理工艺的优化。
通过改进热处理设备和技术,优化热处理流程,可以使模具的强度和耐磨性得到有效的提升,同时可以降低热处理过程中的变形和损伤。
具体而言,可以采用先进的热处理设备、精细的温度控制系统和科学的热处理流程,降低热处理过程中的变形风险。
此外,还可以采用特殊的热处理工艺,如真空热处理、气体淬火、盐浴淬火等,进一步提高材料性能。
四、后处理问题的解决在模具热处理完成之后,还需要进行后处理工作,如研磨、抛光、涂层等。
这些后处理工作同样非常重要,因为它们可以使模具表面光滑、整洁,延长模具的使用寿命。
热处理对模具失效的影响及对策
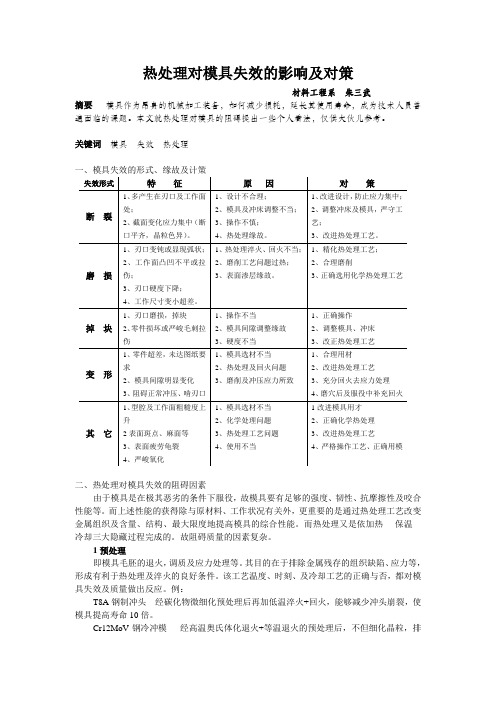
热处理对模具失效的影响及对策材料工程系朱三武摘要模具作为昂贵的机械加工装备,如何减少损耗,延长其使用寿命,成为技术人员普遍面临的课题。
本文就热处理对模具的阻碍提出一些个人看法,仅供大伙儿参考。
关键词模具失效热处理一、模具失效的形式、缘故及计策二、热处理对模具失效的阻碍因素由于模具是在极其恶劣的条件下服役,故模具要有足够的强度、韧性、抗摩擦性及咬合性能等。
而上述性能的获得除与原材料、工作状况有关外,更重要的是通过热处理工艺改变金属组织及含量、结构、最大限度地提高模具的综合性能。
而热处理又是依加热----保温---冷却三大隐藏过程完成的。
故阻碍质量的因素复杂。
1预处理即模具毛胚的退火,调质及应力处理等。
其目的在于排除金属残存的组织缺陷、应力等,形成有利于热处理及淬火的良好条件。
该工艺温度、时刻、及冷却工艺的正确与否,都对模具失效及质量做出反应。
例:T8A钢制冲头经碳化物微细化预处理后再加低温淬火+回火,能够减少冲头崩裂,使模具提高寿命10倍。
Cr12MoV钢冷冲模经高温奥氏体化退火+等温退火的预处理后,不但细化晶粒,排除碳化物不平均性,并使模具服役寿命提高1倍。
9SiCr钢滚丝模按常规处理,其晶粒度为8—9级,后经超细化预热处理能够达13~14级,抗弯强度及断裂强度分别提高30%和40%。
可有效地防止早期失效,寿命可提高1倍。
2、淬火由于加热温度较高,稍有不慎,即会发觉晶粒粗大、氧化脱碳、强度、钢性不佳等。
淬火中的快速冷却会形成应力隐患,导致模具在服役中早期失效。
例:4Cr5MoSiV钢制铝合金压铸模,在使用2000余次时发生疲劳开裂,经检测发觉模具表面强度为HRC40~44。
心部为HRC43~44,且裂纹处有0.1mm的贫碳区,呈粗针马氏体,故判为淬火温度过高,爱护不良,表面脱碳所为。
反之,淬火温度过低,易显现网状铁素体,形成沿铁素体的脆性断裂,如铬钢冲头在服役中断裂,镜分析呈马氏+铁素体组织,即加热不足所为。
模具热处理质量的影响因素分析及预防
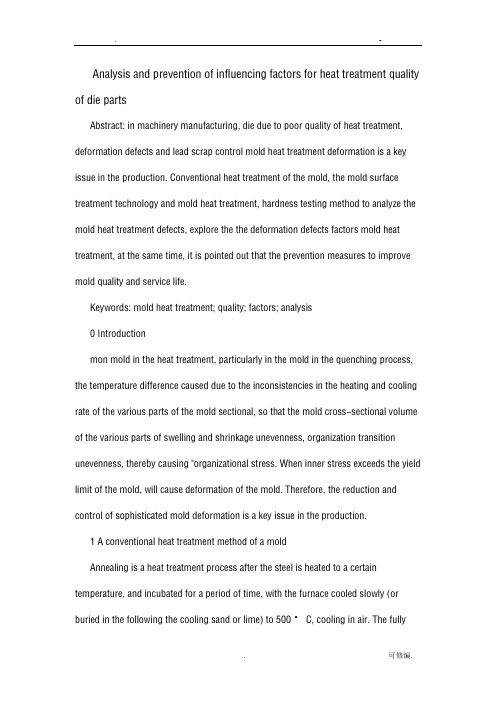
Analysis and prevention of influencing factors for heat treatment quality of die partsAbstract: in machinery manufacturing, die due to poor quality of heat treatment, deformation defects and lead scrap control mold heat treatment deformation is a key issue in the production. Conventional heat treatment of the mold, the mold surface treatment technology and mold heat treatment, hardness testing method to analyze the mold heat treatment defects, explore the the deformation defects factors mold heat treatment, at the same time, it is pointed out that the prevention measures to improve mold quality and service life.Keywords: mold heat treatment; quality; factors; analysis0 Introductionmon mold in the heat treatment, particularly in the mold in the quenching process, the temperature difference caused due to the inconsistencies in the heating and cooling rate of the various parts of the mold sectional, so that the mold cross-sectional volume of the various parts of swelling and shrinkage unevenness, organization transition unevenness, thereby causing "organizational stress. When inner stress exceeds the yield limit of the mold, will cause deformation of the mold. Therefore, the reduction and control of sophisticated mold deformation is a key issue in the production.1 A conventional heat treatment method of a moldAnnealing is a heat treatment process after the steel is heated to a certain temperature, and incubated for a period of time, with the furnace cooled slowly (or buried in the following the cooling sand or lime) to 500 ° C, cooling in air. The fullyannealed also known as recrystallization annealing, generally referred to as annealing, this annealing is mainly used for a variety of carbon and alloy steel forgings andhot-rolled profiles, the hypoeutectoid ingredients sometimes used for welding structure. monly as the final heat of the light quality of the workpiece atProcessing, or as a pre-heat treatment of certain workpieces. Ball annealing mainly used eutectoid carbon steel and alloy workersWith steel (such as: manufacture of cutting tools, measuring tools, mold steels). Its main purpose is to reduce the hardness, to improve the machinability, and to prepare for the subsequent quenching. Stress relief annealing, also known as low-temperature annealing (annealing or tempering this is mainly used to eliminate the residual stress of castings, forgings, weldments, hot-rolled and cold-drawn pieces, etc. If these stresses are not eliminated, will cause the steel deformed or cracks after a certain time, or in a subsequent machining process.Quenching is a process of heat treatment the steel is heated to a certain temperature, the incubation period of time, was cooled in a certain medium (water, oil, etc.). The most monly used cooling medium is a brine, water, and oil quenching. Brine quenching of the workpiece, and easy to get high hardness and smooth surface, not prone to quench hard soft spot, but easy to make the deformation of the workpiece serious, even cracking. Oil for quenching medium only apply to the stability of supercooled austenite alloy steel or carbon steel workpiece size large quenching.Normalizing is steel or steel is heated to a certain temperature or higher, the heat treatment process, to keep a certain time after the cooling in air.The tempering is heated through the hardening of the workpiece to the appropriate temperature below the critical point AC1 maintain a certain time followed by the method to meet the requirements of the cooling in order to obtain the desired microstructure and properties of the heat treatment process. The purpose of low-temperature tempering in the premise of maintaining the hardened steel of high hardness and high wear resistance, and reduces the quenching stress and brittleness, in order to avoid using chipping or prematurely damaged. It is mainly used for a variety of high-carbon cutting and cutting tools, measuring tools, Die, Rolling carburized parts, tempering hardness is generally 58 to 64 of H RC. The Tempers purpose is to obtain a high yield strength, the elastic limit and a high toughness. Therefore, it is mainly used for a variety of spring and hot mold processing, tempering hardness is generally 35 ~~ 5O HRC. High-temperature tempering (500 ~ 650 ℃) habits will be quenched bination ofhigh-temperature tempering heat treatment called quenching, its purpose is to obtain better mechanical properties of strength, hardness, ductility and toughness. Therefore, important structural parts are widely used in automobiles, tractors, machine tools, such as: connecting rods, bolts, gears and shafts. After tempering hardness of 200 ~ 330 HB. The purpose of tempering steel is to reduce brittleness, eliminate or reduce the internal stress, the presence of a large internal stress and brittleness in the steel after quenching, if not timely tempering, often make the steel deformed even cracking; workpiece by the required mechanical properties . The limitation is the alloy after heat treatment, left at room temperature or slightly above room temperature to maintain their performance over time, and changing phenomenon. Steel carbonitriding to the surface layer of thesteel at the same time into the process of carbon and nitrogen. Habits on the carbon and nitrogen permeation, also known as cyanide, permeation-temperature gas carbonitriding and low-temperature gas carbonitriding (ie gas soft nitriding) is widely used. Temperature gas carbonitriding the main purpose is to improve the hardness, wear resistance and fatigue strength of steel. The cryogenic gas carbonitriding Nitriding mainly, its main purpose is to improve the wear resistance and seizure resistance of the steel. Quenching and tempering treatment is a bination of quenching and high temperature tempering heat treatment. Quenching and tempering treatment is widely used in a variety of important structural parts, especially in the alternating load working rod, bolts, gears and shafts, etc.. Quenched and tempered sorbite body tissue, its mechanical properties than the same hardness normalizing sorbite organization was excellent. Its hardness depending on the high-temperature tempering temperature and is related to the stability of a tempering steel and the workpiece cross-sectional dimension, usually between 200 ~ 350 HB [1].2 die surface treatment technologyMold in addition claim substrate has a sufficiently high strength and toughness with a reasonable work, its surface properties the essential mold performance and service life. These surface features include: wear resistance, resistance to corrosion, friction factor and fatigue performance. Improve and enhance the improvement of the performance of the matrix material alone is very limited, it is not economical surface treatment technology, can achieve a multiplier effect, which is the reason for the rapid development of surface treatment technology. Mold surface treatment technology,surface coating, surface modification or posite processing technology to change the the mold surface morphology, chemical position, organizational structure and the stress state in order to obtain the desired surface properties of systems engineering. From the surface treatment can be divided into: chemical methods, physical methods, physical and chemical methods and mechanical methods. While increasing the mold surface properties of new processing technologies continue to emerge, but more mold manufacturing nitriding, carburizing and hardening film deposition.The nitriding process gas nitriding, ion nitriding and liquid nitriding, etc. way, each nitriding way has several kinds of the nitriding technology, can be adapted to the requirements of different workpieces of different kinds of steel. Due to the excellent performance of surface nitriding technology can form, and good coordination nitriding process and mold steel quenching process, nitriding temperature, without intense cooling after nitriding, very small deformation of the mold, so the mold surface hardening is an early adopter of nitriding technology, is the most widely used. Mold carburizing purposes, mainly in order to improve the overall strength and toughness of the mold, i.e. the working surface of the mold having a high strength and wear resistance, thereby introducing the technical idea is, the lower levelThe material, i.e., by carburizing and quenching instead of high-level material, thereby reducing manufacturing costs. Hardened film deposition technology is more mature, CVD, PVD. In order to increase the bonding strength of the coating layer of the workpiece surface, and now the development of a variety of enhanced CVD, PVD technology. Hardening of the earliest film deposition technology tools (cutting tools,cutting tools, measuring tools on the excellent results, a variety of knives have been hardened coating film as a standard process. Molds since the last century 8O, Began hardened coating film technology. Current technical conditions, the cost of the hardened film deposition technology (equipment), still only in the application on precision, long life die, hardened coating film costs will be greatly reduced if the establishment of heat, more mold using this technology, we can improve our overall level of mold manufacturing. Pre-hardened mold material, mold manufacturing process can be simplified to shorten the manufacturing cycle of the mold, mold manufacturing precision. It can be predicted that, with the advances in processing technology,pre-hardened mold material will be used for the mold type.3 die heat treatment hardness testingDie steel is the main material of the mold industry, according to the different mold conditions of service, the environment and the state of die steel should have different characteristics. Production in the life of mold and made part of the accuracy, quality, appearance and performance, in addition to mold design technology, manufacturing precision, and precision machine tools and manufacturing operations, is The correct selection of mold material and heat treatment process is also crucial. Hardness is an important performance indicators of the mold material and finished mold. The stress state of the mold in the work is plicated, such as: hot die is usually in the alternating temperature field exposed to alternating stress, and therefore, it should have good blocking mold into a relatively soft or plastic state capacity , and in thelong-term work environment, and still maintain the mold shape and dimensions of thesame accuracy. General hardness of the finished mold, cold mold often choose of 59 ~~ 60 HRC, the hot die often choose around 48 HR. Important performance indicators of wear resistance of the finished mold. Parts forming metal and the surface of the mold cavity when relative motion occurs, wear of the cavity surface, leading to change the size and shape of the mold, accuracy and surface roughness VALID. The wear resistance of the mold is by a heat treatment of the mold, especially surface heat treatment decisions, the evaluation of mold wearability is mainly based hardness. Mold steel hardness test for the three cases (1) mold steel hardness testing; (2) After the heat treatment of semi-finished mold hardness detection; (3) require high wear resistance of the surface of the mold after heat treatment, surface hardness testing . The surface heat treatment surface hardening heat treatment and chemical heat management, its hardness testing method is as follows. Surface hardening, heat treatment usually by induction heating, or flame heating. The main technical parameters of surface hardness, the local hardness and effective case depth. Hardness test Vickers hardness tester can be used, and may be used the Rockwell or surface Rockwell hardness. The choice of test force (ruler) of the effective case depth and surface hardness. Vickers hardness is an important means of testing heat treatment surface hardness, it can choose the test force of 0.5 to 100 kg, the test thin surface-hardened layer to a thickness of 0.05 mm, and its accuracy is the highest, can distinguish the heat-treated workpiece minor differences of the surface hardness. Effective hardened layer depth but also by the Vickers hardness meter to detect the surface heat treatment or a large number of units of the workpiece surface heat treatment with a Vickers hardness tester is necessary.Mold heat treatment quality and the use of performance usually hardness as the basis of the judgment. In order to take care of other properties such as toughness, the mold hardness range is a relatively narrow range, therefore, how in the field using portable instruments quickly and accurately test the hardness of the mold, mold manufacture and use of the unit has a very important significance. It can enhance the the mold product quality and mold manufacturing technology level, to extend the life of the die.4 Mold heat treatment defects cause analysis and prevention(1) mold burst. Mold burst There are many reasons for the stamping process, different working conditions. Die life of different materials are often different. For this end, for the material of the die working parts, the two basic requirements: the use of properties of the material should have a high hardness and high strength, and having a high wear resistance and sufficient toughness, heat deformation small, certain thermosetting; Process Performance is good. The die working parts manufacturing The process is generally more plex, and therefore must have the adaptability to a variety of processes, such as: malleability, machinability, hardenability hardenability, quench cracking susceptibility and grinding, etc.. Generally, according to the stampings of the material properties, the production volume, and precision requirements, select the mold material with excellent performance, while taking into account And economy of the process.(2) The mold surface with a soft point. Soft point will affect the wear resistance of the mold, reducing the life of the mold surface mold heat treatment. Mold prior to heat treatment surface oxide scale, rust, and local decarburization; mold quenching, coolingimproper selection of quenching medium, quenching media of impurities too much or aging. Should be adopted in the descaling, rust, mold heat treatment before quenching appropriate to protect the surface of the mold, vacuum furnace, salt bath furnace and PaulCare atmosphere furnace heating; cooling after the heating of the mold quenching, should choose a suitable cooling medium, and long-term use of the cooling medium should always be filtered or periodic replacement.(3) poor mold before heat treatment organizations. Mold the final ball of the organization coarse uneven spheroidization imperfect, mesh, ribbon and chain carbide organization, which will allow the mold easily cracks after quenching, resulting in mold scrapped. Poor forging process, such as: forging heating temperature is too high, a small amount of deformation, stop forging temperature, slow cooling after forging the forging organizations coarse mesh, ribbon and chain carbide exists so spheroidization annealing is difficult to eliminate. The spheroidizing poor, such as: the annealing temperature is too high or too low, etc. isothermal annealing time, can cause uneven ball annealing organization or nodulizing. According to the working conditions of the mold, the Toughening performance of the production volume and the material itself, choose a good quality mold steel material.(4) molds produce quenching cracks. The mold cracks quenched mold heat treatment process defects lead to mold scrap production and great economic losses. Serious mold material mesh carbide segregation; machining or cold plastic deformation stress there is in the mold; mold improper heat treatment operations (heated or cooledtoo fast, improper selection of quenching medium, low cooling temperature and cooling time is too long. ); plex shape of the mold, and uneven thickness, with sharp corners and threaded holes, so that the thermal stress and stress is too large; mold quenching temperature is too high to produce hot or burning; mold after quenching and tempering is not timely or Tempering insufficient time; mold rework quenching, without intermediate annealing again heated quenching; improper mold heat treatment, grinding process; EDM mold after the heat treatment, the hardened layer has a high drawing stress and microcracks. Strict control mold of the originalIntrinsic quality of materials, improved forging and spheroidizing to eliminate mesh, ribbon, chain carbides, improve the uniformity of the ball of the organization; mold machining or cold plastic deformation should retreat to the stress ( > 600 ℃) and then heated quenching; asbestos plug screw holes should be used to the plex shape of the mold, bandaged dangerous section and thin-walled office, and grading quenching or austempering.(5) mold quenching coarse microstructure. The mold after quenching organizations coarse, will seriously affect the mechanical properties of the mold, the mold will crack, and seriously affect the life of the mold. Steel mold, confusion, the actual steel quenching temperature far below the requirements of the mold material the quenching temperature (the GCrl5 steel as the steel 3Cr2W8V); die steel quenched without correct the spheroidization treatment process, poor ball of the organization; mold quenching temperature improper placement of mold in the oven near the electrode or heating element region prone to overheating; inappropriate choice of the cross-section changesthe mold, the quenching process parameters, in thin sections and sharp corners overheating or long holding time; Steel storage should be strictly tested to strictly prevent steel confuse misplacing; mold quenching before the correct forging and ball annealing, to ensure a good ball of the organization; properly formulated mold quenching process specifications, strict control of quenching temperature and holding time; regular detection and correction Thermometer, to ensure the normal work of the instrument [2].5 mold heat treatment the deformation defects factors andDie heat treatment is an important process to ensure the performance of the mold, the molds heat treatment of poor quality will cause poor results following performance: (1) mold manufacturing precision: uneven organizational changes, thoroughly and heat treatment of residual stress caused by excessive mold deformation after heat treatment, machining, assembly and mold process, thereby reducing the accuracy of the mold, or even scrapped. (2) the strength of the mold: heat treatment process is not appropriate heat treatment operations are not standardized or heat treatment equipment status is not intact, causing the handle mold strength (hardness) reach the design requirements.(3) the working life of the mold short: heat treatment due to the organizational structure is unreasonable, excessive grain size, resulting in major performance, such as: mold toughness, thermal fatigue performance and wear resistance performance decline, affectingThe working life of the mold. (4) mold manufacturing costs: intermediate links as mold manufacturing process or final process, the heat caused by cracking,distortion-tolerance and performance of ultra poor will die scrap most cases, even if the repair can continue to use, also increased working hours, to extend the delivery time, improve the manufacturing cost of the mold. Deformation of the mold heat treatment is one of the major defects of the mold processing, sophisticated mold, often due to the heat treatment deformation scrapped to control sophisticated mold deformation heat treatment production has been a key issue. Is well known, the mold during the heat treatment, particularly in the quenching process, the temperature difference caused due to the inconsistencies in the heating and cooling rate of the various parts of the mold sectional, coupled unequal organizational changes and other reasons, so that the mold cross-section of each portion of the volume swelling and shrinkage uneven uneven, organizational changes, causing thermal stress caused by the tissue stress and mold temperature difference between inside and outside. When inner stress exceeds the yield limit of the mold, will cause deformation of the mold. Mold deformation after heat treatment is generally considered to be caused by cooling, which is not correct. Mold particularly plex mold, the processing is correct or not on the deformation of the mold tend to have a greater impact, the contrast of the mold heating process can be seen, the heating speed, to generate a large deformation. Any metal when heated to be inflated, due to the steel when heated, within the same mold, the temperature of each portion the unevenness would inevitably result in inconsistencies in the mold within the portion of the expanded, thereby forming the internal stresses due to uneven heating. Temperature below the transformation point of steel, uneven heating is mainly thermal stress is generated in excess of the phase-change temperature uneven heating, but also producetissue stress. Faster heating rate, the greater the difference of the temperature of the mold surface and the center portion, the greater the stress, the greater the deformation generated in the mold after the heat treatment. plex mold should be heated slowly heated transformation point, in general, the quenching is much less than the salt bath furnace heated mold vacuum heat treatment deformation. Using the warm-up, just the mold for high alloy can be used for low-alloy steel mold preheated (550 ~ 620 ℃); should be used secondary preheated (55O ~ 620 ℃and 800 - 850 ℃). Sophisticated mold deformation causes are often plex, but, as long as the grip of its deformation law, analysis of its causes, different methods for prevention, to reduce and control the deformation of the mold. Heat treatment deformation sophisticated mold can be taken to prevent this by sophisticated mold should choose material good micro deformation of steel (such as air quenching steel) should be reasonable forging die steel severe carbide segregation and the transfer of heat treatment, can not be larger and forging die steel heat treatment of the solid solution dual refinement. Mold structure design to be reasonable, the thickness should be uniform, the shape should be symmetrical to master for large deformation mold deformation law to set aside allowance posite structure can be used for large-scale, sophisticated mold. The sophisticated mold to pre-heat treatment, the elimination of the residual stress generated in the machining process. Reasonable choice of the heating temperature, control the heating rate can be taken, for sophisticated mold was slowly heated, preheated, and other balanced heating method of heat treatment to reduce the mold deformation. Maximize the use ofpre-cooling, grading cooling quenching or Austempering of mold hardness premise.Sophisticated mold, as far as conditions permit, using the vacuum heating after quenching and quenching cryogenic processing. Sophisticated mold can be used to pre-heat treatment and aging heat treatment and quenching and tempering nitride heat treatment to control the accuracy of the mold. Defect repair mold trachoma, porosity, wear, use cold welding heat affected small repair equipment, to avoid the generation of deformation in the repair process. In addition, the correct heat treatment process operation (such as: plugging the holes, tying the hole, the mechanical fixing, suitable heating method, the correct choice of the cooling of the mold direction and in the direction of movement of the cooling medium, etc.) as well as a reasonable heat treatment process is also reduced precision the plicated mold deformation measures [3].6 ConclusionHeat treatment technology and the quality of the mold there is a close correlation makes the technology together to improve and promote each other in the process of modernization. The the sophisticated mold heat deformation defects is plex, However, as long as the master of the law of its production, analysis of its causes, prevention takes a different approach to reduce and control the deformation of the mold heat treatment defects.References:[1] Shen hi Church. Automobile manufacturing mold materials and mold heat treatment technology intoExhibition [J]. Metal processing: thermal processing, 2008 (3) :21-25.[2] P. Chang, Zhang Zhigang. Mold heat treatment technology and its deformation prevention measures[J]. Mold manufacturing, 2006 (11) :81-86.[3] WU Bing. Mold heat treatment technology [J]. Mechanical workers: thermal processing,2002 (9) :39-4l.模具热处理质量的影响因素分析与预防摘要:在机械制造中,模具因热处理质量不佳,产生变形缺陷而导致报废,控制模具的热处理变形是生产中的关键问题。
热处理不当对模具的影响
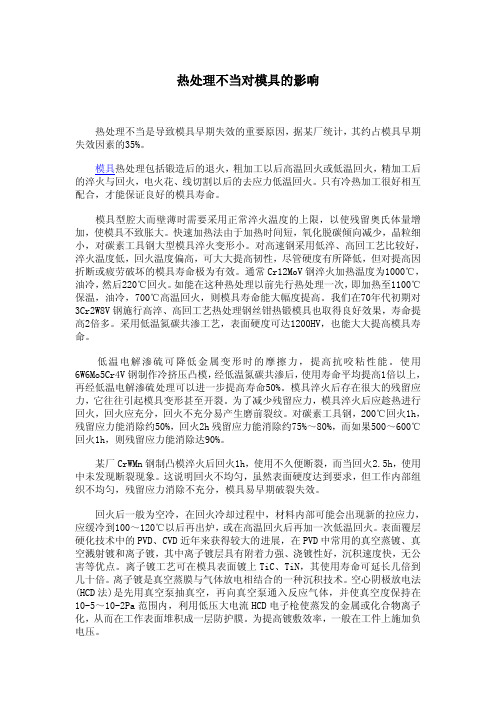
回火后一般为空冷,在回火冷却过程中,材料内部可能会出现新的拉应力, 应缓冷到100~120℃以后再出炉,或在高温回火后再加一次低温回火。表面覆层 硬化技术中的 PVD、CVD 近年来获得较大的进展,在 PVD 中常用的真空蒸镀、真 空溅射镀和离子镀,其中离子镀层具有附着力强、浇镀性好,沉积速度快,无公 害等优点。离子镀工艺可在模具表面镀上 TiC、TiN,其使用寿命可延长几倍到 几十倍。离子镀是真空蒸膜与气体放电相结合的一种沉积技术。空心阴极放电法 (HCD 法)是先用真空泵抽真空,再向真空泵通入反应气体,并使真空度保持在 10-5~10-2Pa 范围内,利用低压大电流 HCD 电子枪使蒸发的金属或化合物离子 化,从而在工作表面堆积成一层防护膜。为提高镀敷效率,一般在工件上施加负 电压。
锻模的表面处理技术国内应用不太多,这一领域大有开发的必要。整体模腔 的渗碳、渗氮、渗硼、碳氮共渗以及模腔局部的喷涂、刷镀和堆焊等表面硬化支 持都是很有发展前途的,突破这一领域将使我国制模技术得到很大提高。模具失 效以后的焊补技术,国内90年代初期就有工厂进行研究和应用,如青海锻造厂, 焊补后的锻模寿命可提高1倍
低温电解渗硫可降低金属变形时的摩擦力,提高抗咬粘性能。使用 6W6Mo5Cr4V 钢制作冷挤压凸模,经低温氮碳共渗后,使用寿命平均提高1倍以上, 再经低温电解渗硫处理可以进一步提高寿命50%。模具淬火后存在很大的残留应 力,它往往引起模具变形甚至开裂。为了减少残留应力,模具淬火后应趁热进行 回火,回火应充分,回火不充分易产生磨前裂纹。对碳素工具钢,200℃回火1h, 残留应力能消除约50%,回火2h 残留应力能消除约75%~80%,而如果500~600℃ 回火1h,则残留应力能消除达90%。
热处理对模具的影响
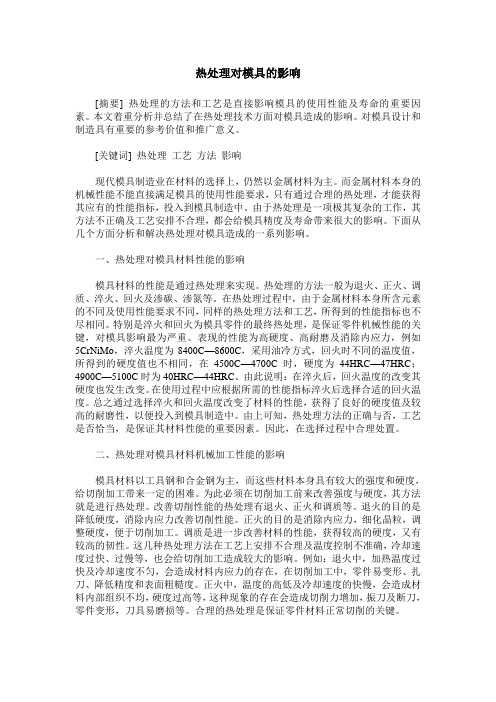
热处理对模具的影响[摘要] 热处理的方法和工艺是直接影响模具的使用性能及寿命的重要因素。
本文着重分析并总结了在热处理技术方面对模具造成的影响。
对模具设计和制造具有重要的参考价值和推广意义。
[关键词] 热处理工艺方法影响现代模具制造业在材料的选择上,仍然以金属材料为主。
而金属材料本身的机械性能不能直接满足模具的使用性能要求,只有通过合理的热处理,才能获得其应有的性能指标,投入到模具制造中。
由于热处理是一项极其复杂的工作,其方法不正确及工艺安排不合理,都会给模具精度及寿命带来很大的影响。
下面从几个方面分析和解决热处理对模具造成的一系列影响。
一、热处理对模具材料性能的影响模具材料的性能是通过热处理来实现。
热处理的方法一般为退火、正火、调质、淬火、回火及渗碳、渗氮等。
在热处理过程中,由于金属材料本身所含元素的不同及使用性能要求不同,同样的热处理方法和工艺,所得到的性能指标也不尽相同。
特别是淬火和回火为模具零件的最终热处理,是保证零件机械性能的关键,对模具影响最为严重。
表现的性能为高硬度、高耐磨及消除内应力,例如5CrNiMo,淬火温度为8400C—8600C,采用油冷方式,回火时不同的温度值,所得到的硬度值也不相同,在4500C—4700C时,硬度为44HRC—47HRC;4900C—5100C时为40HRC—44HRC。
由此说明:在淬火后,回火温度的改变其硬度也发生改变。
在使用过程中应根据所需的性能指标淬火后选择合适的回火温度。
总之通过选择淬火和回火温度改变了材料的性能,获得了良好的硬度值及较高的耐磨性,以便投入到模具制造中。
由上可知,热处理方法的正确与否,工艺是否恰当,是保证其材料性能的重要因素。
因此,在选择过程中合理处置。
二、热处理对模具材料机械加工性能的影响模具材料以工具钢和合金钢为主,而这些材料本身具有较大的强度和硬度,给切削加工带来一定的困难。
为此必须在切削加工前来改善强度与硬度,其方法就是进行热处理。
工程师文章发表模具热处理过程中存在的主要问题
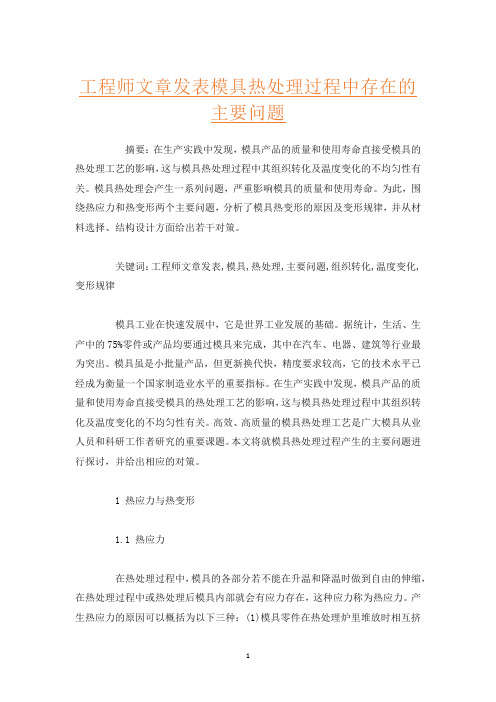
工程师文章发表模具热处理过程中存在的主要问题摘要:在生产实践中发现,模具产品的质量和使用寿命直接受模具的热处理工艺的影响,这与模具热处理过程中其组织转化及温度变化的不均匀性有关。
模具热处理会产生一系列问题,严重影响模具的质量和使用寿命。
为此,围绕热应力和热变形两个主要问题,分析了模具热变形的原因及变形规律,并从材料选择、结构设计方面给出若干对策。
关键词:工程师文章发表,模具,热处理,主要问题,组织转化,温度变化,变形规律模具工业在快速发展中,它是世界工业发展的基础。
据统计,生活、生产中的75%零件或产品均要通过模具来完成,其中在汽车、电器、建筑等行业最为突出。
模具虽是小批量产品,但更新换代快,精度要求较高,它的技术水平已经成为衡量一个国家制造业水平的重要指标。
在生产实践中发现,模具产品的质量和使用寿命直接受模具的热处理工艺的影响,这与模具热处理过程中其组织转化及温度变化的不均匀性有关。
高效、高质量的模具热处理工艺是广大模具从业人员和科研工作者研究的重要课题。
本文将就模具热处理过程产生的主要问题进行探讨,并给出相应的对策。
1 热应力与热变形1.1 热应力在热处理过程中,模具的各部分若不能在升温和降温时做到自由的伸缩,在热处理过程中或热处理后模具内部就会有应力存在,这种应力称为热应力。
产生热应力的原因可以概括为以下三种:(1)模具零件在热处理炉里堆放时相互挤压,受到这种约束,相应部分不能自由伸缩;(2)由于炉膛空间和模具零件大小的限制,不可能保证模具各部分完全均匀受热与冷却,导致模具的中心与边缘、厚处与薄处的伸缩量不同;(3)如果模具本身材质不均匀,在受热与冷却时,不同的组织所在的部分伸缩量也不相同,从而导致相应部分不能自由伸缩。
因为存在热应力,零件实际产生的热变形是指它受约束限制之后的热变形,因此与热应力的关系密不可分。
1.2 热变形1.2.1 热变形形成机理。
由于热处理过程中热应力的存在,模具在热处理过程中或在模具热处理后产生的几何形状上的变形,甚至是破坏,可称之为热变形。
- 1、下载文档前请自行甄别文档内容的完整性,平台不提供额外的编辑、内容补充、找答案等附加服务。
- 2、"仅部分预览"的文档,不可在线预览部分如存在完整性等问题,可反馈申请退款(可完整预览的文档不适用该条件!)。
- 3、如文档侵犯您的权益,请联系客服反馈,我们会尽快为您处理(人工客服工作时间:9:00-18:30)。
热处理对模具失效的影响及对策
材料工程系朱三武
摘要模具作为昂贵的机械加工装备,如何减少损耗,延长其使用寿命,成为技术人员普遍面临的课题。
本文就热处理对模具的影响提出一些个人看法,仅供大家参考。
关键词模具失效热处理
二、热处理对模具失效的影响因素
由于模具是在极其恶劣的条件下服役,故模具要有足够的强度、韧性、抗摩擦性及咬合性能等。
而上述性能的获得除与原材料、工作状况有关外,更重要的是通过热处理工艺改变金属组织及含量、结构、最大限度地提高模具的综合性能。
而热处理又是依加热----保温---冷却三大隐蔽过程完成的。
故影响质量的因素复杂。
1预处理
即模具毛胚的退火,调质及应力处理等。
其目的在于消除金属残存的组织缺陷、应力等,形成有利于热处理及淬火的良好条件。
该工艺温度、时间、及冷却工艺的正确与否,都对模具失效及质量做出反应。
例:
T8A钢制冲头经碳化物微细化预处理后再加低温淬火+回火,可以减少冲头崩裂,使模具提高寿命10倍。
Cr12MoV钢冷冲模经高温奥氏体化退火+等温退火的预处理后,不但细化晶粒,消除碳化物不均匀性,并使模具服役寿命提高1倍。
9SiCr钢滚丝模按常规处理,其晶粒度为8—9级,后经超细化预热处理可以达13~14级,抗弯强度及断裂强度分别提高30%和40%。
可有效地防止早期失效,寿命可提高1倍。
2、淬火
由于加热温度较高,稍有不慎,即会发现晶粒粗大、氧化脱碳、强度、钢性不佳等。
淬火中的快速冷却会形成应力隐患,导致模具在服役中早期失效。
例:
4Cr5MoSiV钢制铝合金压铸模,在使用2000余次时发生疲劳开裂,经检测发现模具表面强度为HRC40~44。
心部为HRC43~44,且裂纹处有0.1mm的贫碳区,呈粗针马氏体,故判为淬火温度过高,保护不良,表面脱碳所为。
反之,淬火温度过低,易出现网状铁素体,形成沿铁素体的脆性断裂,如铬钢冲头在服役中断裂,镜分析呈马氏+铁素体组织,即加热不足所为。
3.回火
回火在于消除因力,获得合理的硬度,均匀而正确的金相组织,而应力消除程度又与温度、时间成正比关系。
见图1:
下图2所示拉深零件,由于工作条件恶劣。
图1 回火温度与应力关系图2 材料Q235A
原为Cr12MoV钢经淬火+回火常规热处理,温度要求HRC57,仅能拉深1000件即早期失效,后改为T10A钢采用淬火+中温回火后硬度为HRC55。
平均寿命达4000件,而后又改为380~400℃回火,使其硬度在HRC48,则寿命可达6000~8000件。
而Cr12MoV钢制冲头,冲厚2.5mm的钢板,常规淬火+210℃回火硬度降至HRC58~62,寿命仅有1000件,后采用中温410℃回火,硬度降至HRC57~59。
不但克服了模具的早期失效,且冲件达到10000件,寿命提高10倍。
由此可见,回火温度和所获硬度对寿命有巨大影响,而且对应力的消除程度、变形等作出反映。
4。
软点
淬火加热中,因温度不均匀、保护不良、严重氧化或冷却介质中的污染等,均可造成硬度不均,而使模具强度受损,在模具使用中将出现塌角、变形、掉块等弊病,这对冷镦模、剪切模和中模尤为重要。
5。
硬化层
磨损失效除与模具硬度过低,或淬硬层过浅有关外,还与化学热处理硬化层有关,若热处理工艺不当,尤其是淬火温度、时间以及冷却介质能力和钢材选择等因素,均可影响淬硬度层导致刃口发钝、抗压强度下降、局部塌陷、变形等早期失效。
模具在渗碳、渗氮、渗硼、碳氮共渗化学热处理中由于工艺或配方不适,操作不当也会出现渗层、硬化层不均或过浅等弊端,出现刃口不锋利、咬合、啃刃口、粘模、塌陷、氧化
腐蚀和硬化层脱落等失效,严重影响模具的寿命。
三、防止模具失效的热处理对策
1、服役中的低温去应力回火
模具在长期服役中,尤其是热作模具在巨大的冲压力和和温度的双重应力作用下,将发生不均匀的塑性变形及金属组织的变化,从而产生可观的应力,当这种潜在应力聚集到极限时,金属将会出现开裂、崩块、变形等失效。
故小于500g的铝压铸模在使用1万次在模具服役一段时间后,应增加低温去应力回火处理,以防止早期失效。
如100g的铝压铸模在使用2.5万次,大于500g的铝压铸模在使用500次后,进行低温去应力回火与未去应力回火者有明显不同,前者较后者早期失效的下降25%。
2、精化热处理工艺
如φ175mm×233mm的3Cr2W8V钢热压模冲头,其被冲压坯料要在900℃中加热后,置于4000KN水压机中热压成形。
原冲头热处理工艺如图3所示,,平均寿命仅有1200件,即以开裂和磨损的形式失效,后改为图4所示热处理工艺,其平均寿命提高64%,以热疲劳失效。
图3 图4
还有W18Cr4V钢的电池冲压拉深模,原采用常规热处理工艺,仅能拉深锌筒2万件,表面因拉伤和脆断而失效。
后改为图5复合热处理工艺后,单头可拉深6万件,双头达10万件以上,节约制模材料、工时,具有明显经济效益。
图5
3、增加调质工序
调质在模具加工中不仅是获得良好力学性能,改善切削性能的手段,更重要的在于能改善金属部组织,获得均匀细小颗粒的碳化物,减少网状和带状碳化物偏析及其它缺陷等,这为模具成形后减少变形、防止开裂、减少应力、防止模具在热处理中及服役中的失效有一定作用,一般调质工序在下料→锻造→退火→粗加工成形→调质→精加工成形→淬火回火→磨刃口→装配流程中,调质后的高温回火,由于不要求索氏体组织及性能,故回火温度可高于常温回火温度,以顺利地精加工成形。
实践证明,经上述工艺流程的模具其变形量较小,即模具的最大变形发生在粗加工后、精加工成形前的调质中。
4、合理锻造
在锻造中依据材料选择加热温度,方式及加热时间和锻造次数、停锻温度等,并应采取反复横向锻拔、镦拔和多项镦拔、扁方锻造以及对角锻造等,使残余网状、带状碳化物消除,碳化物级别<2级。
经锻造后的钢材流线应合理分布,流线平行于型腔短轴或垂直于型腔端面,呈幅射状以最大限度减少应力和隐患,防止模具早期失效。
5、采用新钢种
模具用钢对其寿命影响甚大,因此选用一些具有良好的抗拉、抗弯强度和有较好淬透性的新型钢种对延长模具寿命有明显提高。
6、正确的电加工及磨削
该工序也是产生应力叠加造成失效的原因之一,故正确的电加工、磨削工艺是防止模具失效的又一途径。
7、改进模具设计结构
为减少模具在机加工、热处理及使用中的应力,模具在设计时应尽可能采取型腔对称法,截面均匀法、边孔最少法、尖角避免法及圆弧多用法的模具原则。