南钢高速线材生产线粗中轧机改造方案
高速无扭轧机产线材(盘条)的品质管理与持续改进实践

高速无扭轧机产线材(盘条)的品质管理与持续改进实践随着工业化进程的不断发展,钢铁行业作为基础产业之一扮演着重要的角色。
高速无扭轧机产线材(盘条)作为钢铁行业的重要产品之一,在生产中的品质管理与持续改进显得尤为重要。
本文将探讨高速无扭轧机产线材(盘条)在品质管理与持续改进方面的实践经验。
首先,品质管理是高速无扭轧机产线材(盘条)生产过程中的核心环节。
品质管理的目标是保证产品的质量符合市场需求和技术标准,并且持续提升产品的品质水平。
在品质管理方面,高速无扭轧机产线材(盘条)需要注意以下几个方面:1. 完善的生产工艺控制系统:高速无扭轧机产线材(盘条)生产过程多层次、多环节,需要建立完善的生产工艺控制系统。
这个系统包括对原材料的选择和质量控制、生产过程中各个环节的监控和控制、产品质量检测和分析等方面。
只有建立完善的生产工艺控制系统,才能从根本上保证产品的品质。
2. 严格的品质检测标准:高速无扭轧机产线材(盘条)需要建立一套严格的品质检测标准。
这个标准应该基于市场需求和技术标准,并且要具备可操作性和可实施性。
只有在严格的品质检测标准的指导下,才能保证产品的品质。
3. 持续的质量改进活动:高速无扭轧机产线材(盘条)的生产过程中,质量问题是难以避免的。
因此,持续的质量改进活动是必不可少的。
这包括对产品质量问题的分析和改进、对生产工艺的改进以及对人员技术能力的提升等方面。
只有通过持续的质量改进活动,才能不断提升产品的品质水平。
其次,持续改进是高速无扭轧机产线材(盘条)品质管理的关键。
持续改进是一个不断追求优化和进步的过程,能使企业在竞争激烈的市场中保持竞争力。
高速无扭轧机产线材(盘条)在持续改进方面需要注意以下几个方面:1. 建立改进机制:高速无扭轧机产线材(盘条)需要建立一个持续改进的机制。
这个机制应该包括信息收集和反馈、问题分析和解决、改进方案的制定和实施等环节。
只有建立了良好的改进机制,才能推动企业持续改进。
高标准轴承钢线材的开发

型线 开坯一坯 料检 验 、 修磨 处理一 合 格坯 料入 炉一
加热炉保 温一高压水 除鳞一粗 轧一 飞剪一 中轧一飞 剪一预精轧一初 冷水箱一 飞剪一 精轧一水 冷线一减
定 径 轧机 一 水 冷 线 一 吐丝 机 一 斯 太 尔 摩 风 冷 线 一 集 卷一 酸洗 检测 一 头尾 剪 切 一 打 捆 一 卸 卷 一 入 库
2 2 1 高标准轴承钢 内在及表面质量的要求 ..
高标准轴承钢 要求产 品的纯净 度 高 , 中残余 钢 元素如 T 、 i iN 等含量 低 , 夹杂 物 的含量低 ; 氧含量 小
于 8 P m P
2 1 年第 1 01 期
南钢 科 技 与管理
2 7
线材内部组织要求高 , 碳化物带状不大 于 20级 ; .
产线。高线厂 经过 充分 的研究 , 成功 开发 出不 同规 格的高标准轴 承钢 G r5一X 线 材 , Cl 1 得到 了用 户 的
2 2 高标 准轴 承钢 一x . 1的质 量要 求
高标 准轴 承钢 G r5一 1 于制造超静音轴 承 Cl X 用 滚动体 , 此 高标 准轴 承 钢 比普 通 高碳 铬 轴 承 钢 因
4 2 高 温扩 散 消除碳 化 物偏 析 .
2 22 轴承线材 的尺 寸要求较高 , .. 具体见表 2 。
表 2 高 标 准 轴 承 钢 的 尺 寸 要 求
为 了最大 限度地 消除高标准轴 承钢 连铸坯 中严 重的树枝状偏析 , 使共 晶碳 化物 中的碳 、 等碳化 物 铬 形 成元素充 分扩 散 均匀 , 降低 碳化 物偏 析 。南 钢 充 分 利用 中型线 开坯 过程 进行 高 温长 时 间扩散 , 有效 地 消除了连铸 坯 的偏析 , 高速 线材 厂采 取低 温终 为 轧 生产 出合格的高标准轴 承钢线材 打下 了坚 实 的基
高速线材粗中轧轧机调整

高速线材粗中轧轧机的调整【摘要】:本文详细叙述了高速线材粗中轧轧机的调整与操作以及在轧制过程中容易发生的一些轧制技术的分析与处理.通过本文的分析让读者对高速线材生产进一步了解。
在实践过程操作中对工艺流程所提出改进方法.【关键词】:调整轧辊导位操作方法企业的发展动力来源于员工的较高素质,轧钢工的专业知识与技能的熟练握是企业高效率生产及操作技能水平。
在生产中的炸鸡调整是操作的基础,也为将来的工作打下了坚实的基础。
无论是实际应用中。
还是在理论研究方面。
都尽量使它符合实际操作。
本文笔者比较侧重实际操作技能。
所以不断要求自己提高实际动手解决为体的能力。
使自己的工作水平更上个台阶以及对我国钢铁企业尽一份自己的微薄之力。
1、粗中轧区域的轧机1.1机架由两个两个框架状的轧机牌坊联结而成、轧机牌坊的敞开部分叫做“窗”,在这个“窗”中安装轧辊的轴承座。
通常高速线材粗轧机采用闭式机架,这是因为闭式轧机具有刚性大的优点。
二辊机架排放通常由铸钢铸造而成,也可用厚钢板焊接而成,后者的强度与刚性较好,并且具有体积小,重量轻的优点。
1.2轧辊基本结构分为三个部分:既辊身、辊颈、辊头,辊身是轧辊与轧件接触的工作部分,型钢轧机的轧辊辊身是圆柱体,上面车有孔槽.辊颈是轧辊的支撑部分,轧辊是依靠辊身两侧的辊颈而支撑在轴承上.辊身和辊颈交界处由于断面变化可能成为集中的地方,容易断裂.所以,为了提高轧辊强度,交界处应有适当的过渡圆角。
轧辊的辊头具有连接传动接轴.传递轧制力矩的作用。
轧辊直径:许轧机组轧辊辊身直径一般为轧件平均高度的4到5倍,这不仅是为了有足够的强度和刚度以及咬入能力,也是为了轧制时的变形渗透,以避免轧件端部出现由表面变形造成的双叉鱼尾状,而在继续轧制时发生顶撞入口导位的故障.1.3轧辊平衡装置:轧辊平衡装置起着平衡上辊及其轴承座重量的作用.b 轧辊水平调整装置:轧辊的水平调整包括轧机中心线的标高调整和上.下辊间距的调整.轧机中心线的标高通过改变下轧辊轴承座底部的垫块厚度来调整;上下辊的最大间距是由改变上辊平衡器的垫片厚度来设定.1.4 轧机的压下装置是实现上辊压下,调整辊缝的机构.压下装置的形式有电动压下、液压压下、气动压下和手动压下几种、在高速线材轧机上多采用电动压下或者气动压下形式,辅以手动压下.电动和气动压下装置的压下调整速度快、省事省力,用于辊缝的粗调;而手动压下是用于对辊缝进行微量的精确调整.不论采取何种方式,均要求调整后,轧辊两侧的辊缝相等、粗轧机轧辊径向调整量较大,一般为轧辊直径的15%左右。
南钢棒材厂全连轧线改造实践
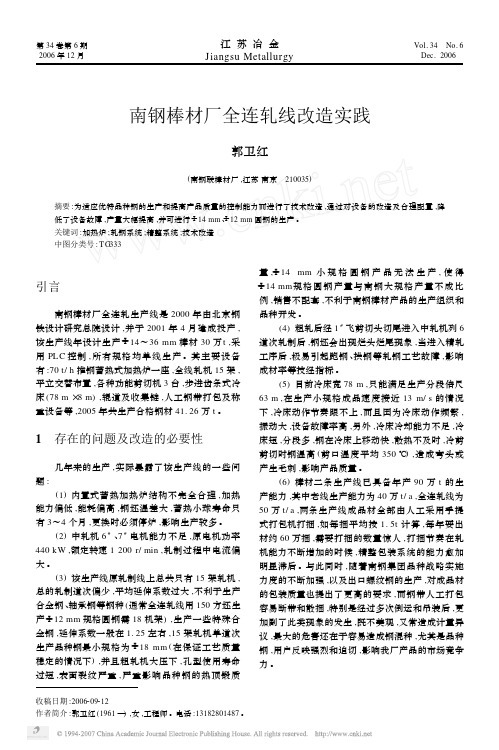
②由于上了 2 # 飞剪 ,设备工艺故障明显减少 , 轧机作业率提高 ,由原 70 %上升为 75 %。
③提高了孔型的共用性 ,减少了备辊工作量 , 缩短了品种规格更换时间 ,降低了换辊劳动强度 。
④精整系统的改造 ,使钢材收集包装能力明显 提高 ,与轧机能力相匹配 ,精整来不及的状况得到明 显改善 。
第 34 卷第 6 期 2006 年 12 月
江苏冶金 Jiangsu Metallurgy
Vol. 34 No . 6 Dec. 2006
南钢棒材厂全连轧线改造实践
郭卫红
(南钢联棒材厂 ,江苏 南京 210035)
摘要 :为适应优特品种钢的生产和提高产品质量的控制能力而进行了技术改造 ,通过对设备的改造及合理配置 ,降 低了设备故障 ,产量大幅提高 ,并可进行Φ14 mm 、Φ12 mm 圆钢的生产 。 关键词 :加热炉 ;轧钢系统 ;精整系统 ;技术改造 中图分类号 : T G333
收稿日期 :2006209212 作者简介 :郭卫红 (1961 —) ,女 ,工程师 。电话 :13182801487 。
4 8
江苏冶金
第 34 卷
2 改造内容及特点
(1) 将内置式蓄热加热炉改成外置蓄热烧嘴 式 ,并将推钢式加热炉改为步进梁式 ,以适应生产的 需要 。
(2) 将中轧机列 6 # 、7 # 电机替换为 650kW ,额定 转速 1 500 r/ min ,解决轧制过程中电流偏大的问题。
(6) 棒材二条生产线已具备年产 90 万 t 的生 产能力 ,其中老线生产能力为 40 万 t/ a ,全连轧线为 50 万 t/ a ,两条生产线成品材全部由人工采用手提 式打包机打捆 ,如每捆平均按 1. 5t 计算 ,每年要出 材约 60 万捆 ,需要打捆的数量惊人 ,打捆节奏在轧 机能力不断增加的时候 ,精整包装系统的能力愈加 明显滞后 。与此同时 ,随着南钢集团品种战略实施 力度的不断加强 ,以及出口螺纹钢的生产 ,对成品材 的包装质量也提出了更高的要求 ,而钢带人工打包 容易断带和散捆 ,特别是经过多次倒运和吊装后 ,更 加剧了此类现象的发生 ,既不美观 ,又常造成计量异 议 ,最大的危害还在于容易造成钢混种 ,尤其是品种 钢 ,用户反映强烈和迫切 ,影响我厂产品的市场竞争 力。
高线粗中轧立式轧机减速机输入轴寿命短的分析改进(201206正式投稿版)
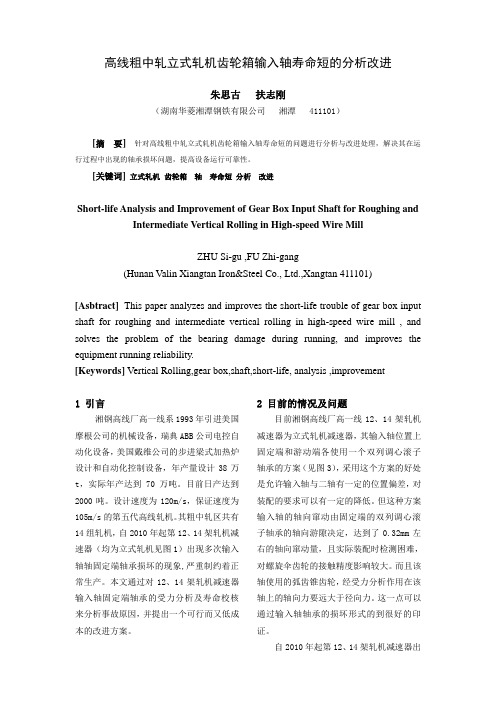
高线粗中轧立式轧机齿轮箱输入轴寿命短的分析改进朱思古扶志刚(湖南华菱湘潭钢铁有限公司湘潭 411101)[摘要]针对高线粗中轧立式轧机齿轮箱输入轴寿命短的问题进行分析与改进处理,解决其在运行过程中出现的轴承损坏问题,提高设备运行可靠性。
[关键词]立式轧机齿轮箱轴寿命短分析改进Short-life Analysis and Improvement of Gear Box Input Shaft for Roughing and Intermediate Vertical Rolling in High-speed Wire MillZHU Si-gu ,FU Zhi-gang(Hunan V alin Xiangtan Iron&Steel Co., Ltd.,Xangtan 411101)[Asbtract]This paper analyzes and improves the short-life trouble of gear box input shaft for roughing and intermediate vertical rolling in high-speed wire mill , and solves the problem of the bearing damage during running, and improves the equipment running reliability.[Keywords] V ertical Rolling,gear box,shaft,short-life, analysis ,improvement1 引言湘钢高线厂高一线系1993年引进美国摩根公司的机械设备,瑞典ABB公司电控自动化设备,美国戴维公司的步进梁式加热炉设计和自动化控制设备,年产量设计38万t,实际年产达到70万吨。
目前日产达到2000吨。
设计速度为120m/s,保证速度为105m/s的第五代高线轧机。
高速线材轧机的施工工法

高速线材轧机的施工工法中冶集团华冶资源公司天津工业设备安装分公司郭英昌焦健材沈洪斌朱博1 前言天钢高线东移技术改造工程新增加1#高线,采用全连续式无扭转轧制工艺,精轧最高轧制速度为135m/s。
该工程特点是设备先进,工艺系统复杂,自动化程度高。
安装要求精度高,施工工艺复杂,难度大,调试项目多要求严格,此安装调试技术在国内处于领先水平。
在这次工程施工过程中,结合以往在其它地方施工棒、线材设备的经验,总结了一套高速线材的施工工法。
2 工法的特点2.1精轧区设备整体联调中心、标高技术,安装中心、标高精度达到超过了国家标准。
2.2合理安排施工顺序,采用先安首尾设备,后安中间设备即先安粗中轧区设备、散卷风冷运输线设备,然后从首尾向精轧机方向推进的安装顺序。
精轧区设备,先安装精轧机组和吐丝机机组,后安装减定径机组设备的施工工序,确保了安装中心线和标高的精度。
2.3立式轧机底座的反顺序座浆垫板施工方法,比以往传统的安装方法提高了安装效率及安装质量。
2.4座浆垫板精找及垫板加工方法,提高了设备底座的安装效率。
3 适用范围本工法适用于棒、线材轧机生产线设备的安装,主要针对高速线材生产线设备的安装。
4 工艺原理4.1精轧区设备整体联调的施工工艺,该工艺有效的提高了安装精度及质量,具体操作要点,减定径机组的标高及中心线要依据精轧机组和吐丝机夹送辊的标高及中心线来确定,故减定径机组的安装要等到精轧机组及吐丝机夹送辊安装完成后进行,这样能保证该关键设备的安装精度及质量。
精轧区设备整体调整:精轧区设备安装完成后对设备进行整体检测设备的标高和中心线。
以最终检验设备的安装质量和保证试车的一次成功。
4.2立式轧机底座的反顺序座浆垫板施工工艺,操作步骤是先安装找正好立式轧机底座,然后根据底座进行座浆垫板的施工,比以往的先施工座浆垫板再进行轧机的底座安装工作提高了安装效率及安装质量。
5 施工工艺流程及操作要点5.1轧机的安装调整工艺轧机的安装是精品轧钢生产线设备安装工作中的重点,安装精度要求高,由于部分构件质量大、体积大,安装难度大,需按照下列程序进行安装。
南钢高线厂滚动化改造(续俊)
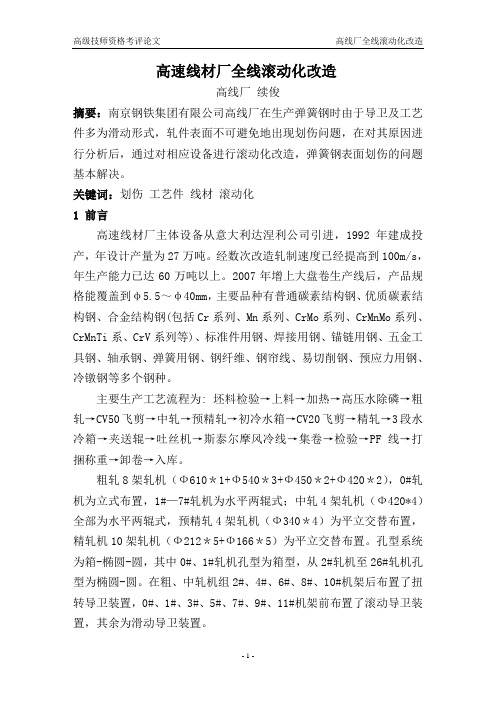
高速线材厂全线滚动化改造高线厂续俊摘要:南京钢铁集团有限公司高线厂在生产弹簧钢时由于导卫及工艺件多为滑动形式,轧件表面不可避免地出现划伤问题,在对其原因进行分析后,通过对相应设备进行滚动化改造,弹簧钢表面划伤的问题基本解决。
关键词:划伤工艺件线材滚动化1 前言高速线材厂主体设备从意大利达涅利公司引进,1992年建成投产,年设计产量为27万吨。
经数次改造轧制速度已经提高到100m/s,年生产能力已达60万吨以上。
2007年增上大盘卷生产线后,产品规格能覆盖到φ5.5~φ40mm,主要品种有普通碳素结构钢、优质碳素结构钢、合金结构钢(包括Cr系列、Mn系列、CrMo系列、CrMnMo系列、CrMnTi系、CrV系列等)、标准件用钢、焊接用钢、锚链用钢、五金工具钢、轴承钢、弹簧用钢、钢纤维、钢帘线、易切削钢、预应力用钢、冷镦钢等多个钢种。
主要生产工艺流程为: 坯料检验→上料→加热→高压水除磷→粗轧→CV50飞剪→中轧→预精轧→初冷水箱→CV20飞剪→精轧→3段水冷箱→夹送辊→吐丝机→斯泰尔摩风冷线→集卷→检验→PF线→打捆称重→卸卷→入库。
粗轧8架轧机(Ф610*1+Ф540*3+Ф450*2+Ф420*2),0#轧机为立式布置,1#—7#轧机为水平两辊式;中轧4架轧机(Ф420*4)全部为水平两辊式,预精轧4架轧机(Ф340*4)为平立交替布置,精轧机10架轧机(Ф212*5+Ф166*5)为平立交替布置。
孔型系统为箱-椭圆-圆,其中0#、1#轧机孔型为箱型,从2#轧机至26#轧机孔型为椭圆-圆。
在粗、中轧机组2#、4#、6#、8#、10#机架后布置了扭转导卫装置,0#、1#、3#、5#、7#、9#、11#机架前布置了滚动导卫装置,其余为滑动导卫装置。
2 改造的必要性2.1设备缺陷高线厂在当初设计时是以生产普碳钢线材为主,虽然经过数次技术改造,但是针对品种钢生产的改造并不多,除孔型进行过优化外轧机系统基本未动,粗中轧除0#外仍然为二棍水平闭口式轧机,导卫系统也没有太大的变化。
高速线材轧制工艺提升与优化

高速线材轧制工艺提升与优化高速线材轧制工艺是钢铁行业的关键技术之一,它对于提高产品质量、降低成本、提高生产效率等方面都起着非常重要的作用。
因此,高速线材轧制工艺的提升与优化一直是行业内的研究热点。
本文将从高速线材轧制的一些基本工艺流程出发,探讨如何提升与优化高速线材轧制工艺。
高速线材轧制工艺的基本工艺流程包括:原料预处理、预热、轧制、冷却、粗整形、自然冷却、细整形、钢卷切割等环节。
其中,轧制是整个工艺流程中最核心的环节之一。
轧制主要是将钢坯通过压延机组成卷轧,这样能够调整线材表面的结构、形状和尺寸。
轧制的关键因素有:轧辊几何参数、轧制力、轧辊表面状态、轧制温度等。
这些因素之间的关系比较复杂,因此,在工艺优化时需要综合考虑。
1.轧辊加工工艺轧辊是高速线材轧制工艺中最为重要的工具之一。
优化轧辊几何形状对于提高高速线材轧制工艺的质量和效率非常重要。
轧辊的主要加工工艺包括:轧辊材料的选择、轧辊热处理、轧辊加工技术等。
轧辊的材料选择应根据不同的轧制温度和应变率选择不同材料。
同时,轧辊表面热处理能够改善其表面状态,降低摩擦系数,提高轧制效率。
轧辊加工精度和表面平整度对于轧制工艺的效率和质量都有极大的影响。
2.轧制力的控制轧制力是通过轧制来实现金属塑性变形的驱动力。
轧制力的大小和分布对于轧制工艺的质量和效率都有很大的影响。
因此,在高速线材轧制工艺的优化中,控制轧制力是关键技术之一。
调整轧制力大小需要综合考虑金属的应变率、韧塑性、温度等因素,同时对于不同的钢种和规格需根据其特定性能进行不同的控制。
轧制温度是影响高速线材轧制质量的重要因素之一。
轧制温度过高会导致过度热处理,使得材料的塑性变得不足,导致表面裂纹和疏松;轧制温度过低则可能导致组织变硬,使得轧制难度增加,并且表面容易产生缺陷。
因此,控制轧制温度,使其处于最适温度范围区间之内,对于提升高速线材轧制工艺质量具有重要的意义。
1.优化轧辊几何形状轧辊是决定线材尺寸、形状和表面质量的关键因素。
轧钢厂生产线施工方案
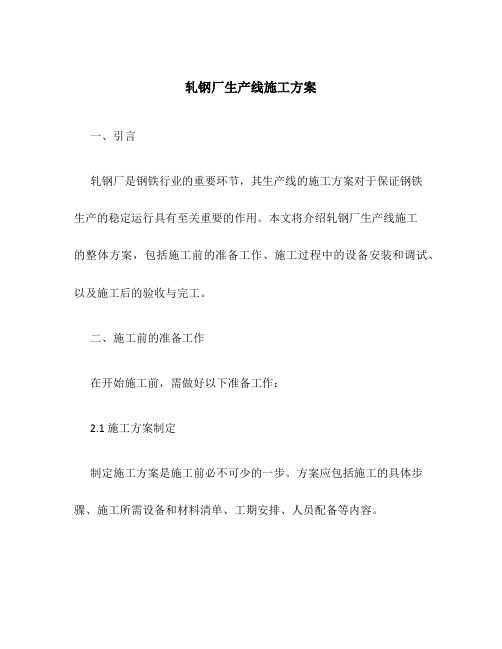
轧钢厂生产线施工方案一、引言轧钢厂是钢铁行业的重要环节,其生产线的施工方案对于保证钢铁生产的稳定运行具有至关重要的作用。
本文将介绍轧钢厂生产线施工的整体方案,包括施工前的准备工作、施工过程中的设备安装和调试、以及施工后的验收与完工。
二、施工前的准备工作在开始施工前,需做好以下准备工作:2.1 施工方案制定制定施工方案是施工前必不可少的一步。
方案应包括施工的具体步骤、施工所需设备和材料清单、工期安排、人员配备等内容。
2.2 设备采购与运输根据施工方案确定所需的设备,并提前进行采购。
在设备采购完成后,需做好设备的运输安排,保证设备能够按时到达施工现场。
2.3 施工现场准备施工现场应进行清理和整理,确保施工区域没有任何障碍物。
同时,还需确保施工现场的安全设施完善,包括防护网、警示标识等。
2.4 人员培训与安全教育在施工前,需要对所有参与施工的人员进行安全培训和教育,确保他们具备相关的安全意识和操作技能,以降低施工过程中的事故风险。
三、施工过程施工过程中,需要按照施工方案进行设备的安装和调试。
3.1 设备安装根据施工方案中的设备清单,按照相应的顺序进行设备安装。
在安装过程中,需要严格按照设备供应商提供的安装说明进行操作,确保设备安装正确、牢固。
3.2 设备调试设备安装完成后,需要进行设备的调试工作。
调试过程中,应根据设备的操作手册进行操作,检查设备的各项功能是否正常,并进行相应的调整,以确保设备能够正常运行。
3.3 设备联调在完成设备的单独调试后,需要进行设备的联调工作。
这需要确保各设备之间能够正常通信和协同工作,以实现整个生产线的正常运行。
3.4 安全检查在施工过程中,需要定期进行安全检查,确保施工现场的安全。
对于发现的安全隐患,及时采取相应的措施进行整改,以减少事故风险。
四、施工后的验收与完工施工完成后,需要进行验收和完工工作,以确保施工结果符合预期。
4.1 验收进行施工结果的验收,包括对设备安装质量的评估、设备性能的测试、设备联调情况的检查等。
高速线材轧制工艺提升与优化
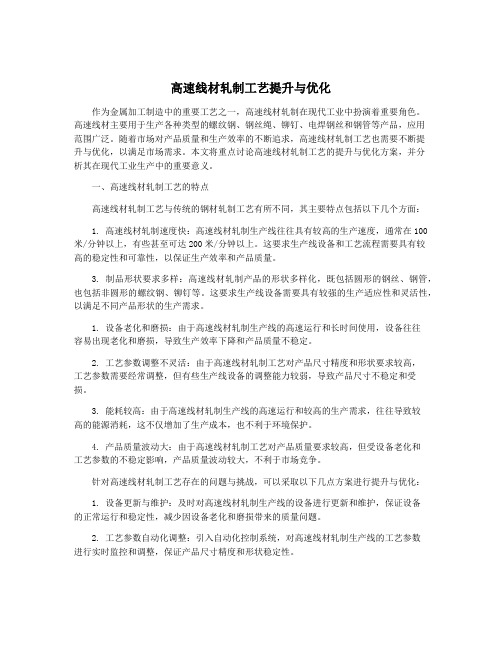
高速线材轧制工艺提升与优化作为金属加工制造中的重要工艺之一,高速线材轧制在现代工业中扮演着重要角色。
高速线材主要用于生产各种类型的螺纹钢、钢丝绳、铆钉、电焊钢丝和钢管等产品,应用范围广泛。
随着市场对产品质量和生产效率的不断追求,高速线材轧制工艺也需要不断提升与优化,以满足市场需求。
本文将重点讨论高速线材轧制工艺的提升与优化方案,并分析其在现代工业生产中的重要意义。
一、高速线材轧制工艺的特点高速线材轧制工艺与传统的钢材轧制工艺有所不同,其主要特点包括以下几个方面:1. 高速线材轧制速度快:高速线材轧制生产线往往具有较高的生产速度,通常在100米/分钟以上,有些甚至可达200米/分钟以上。
这要求生产线设备和工艺流程需要具有较高的稳定性和可靠性,以保证生产效率和产品质量。
3. 制品形状要求多样:高速线材轧制产品的形状多样化,既包括圆形的钢丝、钢管,也包括非圆形的螺纹钢、铆钉等。
这要求生产线设备需要具有较强的生产适应性和灵活性,以满足不同产品形状的生产需求。
1. 设备老化和磨损:由于高速线材轧制生产线的高速运行和长时间使用,设备往往容易出现老化和磨损,导致生产效率下降和产品质量不稳定。
2. 工艺参数调整不灵活:由于高速线材轧制工艺对产品尺寸精度和形状要求较高,工艺参数需要经常调整,但有些生产线设备的调整能力较弱,导致产品尺寸不稳定和受损。
3. 能耗较高:由于高速线材轧制生产线的高速运行和较高的生产需求,往往导致较高的能源消耗,这不仅增加了生产成本,也不利于环境保护。
4. 产品质量波动大:由于高速线材轧制工艺对产品质量要求较高,但受设备老化和工艺参数的不稳定影响,产品质量波动较大,不利于市场竞争。
针对高速线材轧制工艺存在的问题与挑战,可以采取以下几点方案进行提升与优化:1. 设备更新与维护:及时对高速线材轧制生产线的设备进行更新和维护,保证设备的正常运行和稳定性,减少因设备老化和磨损带来的质量问题。
2. 工艺参数自动化调整:引入自动化控制系统,对高速线材轧制生产线的工艺参数进行实时监控和调整,保证产品尺寸精度和形状稳定性。
高速线材轧制工艺提升与优化
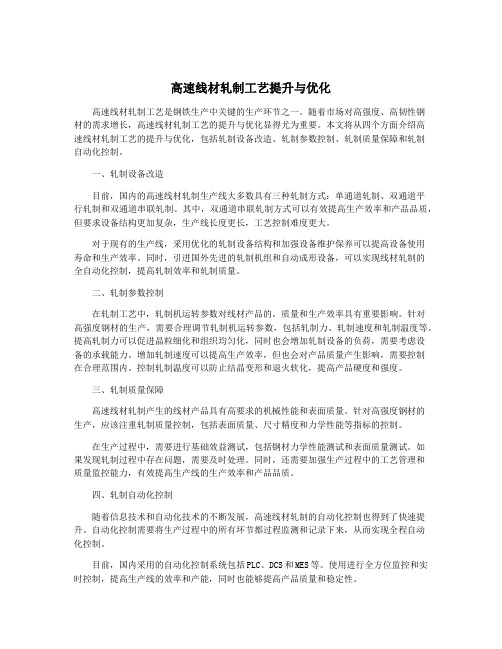
高速线材轧制工艺提升与优化高速线材轧制工艺是钢铁生产中关键的生产环节之一。
随着市场对高强度、高韧性钢材的需求增长,高速线材轧制工艺的提升与优化显得尤为重要。
本文将从四个方面介绍高速线材轧制工艺的提升与优化,包括轧制设备改造、轧制参数控制、轧制质量保障和轧制自动化控制。
一、轧制设备改造目前,国内的高速线材轧制生产线大多数具有三种轧制方式:单通道轧制、双通道平行轧制和双通道串联轧制。
其中,双通道串联轧制方式可以有效提高生产效率和产品品质,但要求设备结构更加复杂,生产线长度更长,工艺控制难度更大。
对于现有的生产线,采用优化的轧制设备结构和加强设备维护保养可以提高设备使用寿命和生产效率。
同时,引进国外先进的轧制机组和自动成形设备,可以实现线材轧制的全自动化控制,提高轧制效率和轧制质量。
二、轧制参数控制在轧制工艺中,轧制机运转参数对线材产品的。
质量和生产效率具有重要影响。
针对高强度钢材的生产,需要合理调节轧制机运转参数,包括轧制力、轧制速度和轧制温度等。
提高轧制力可以促进晶粒细化和组织均匀化,同时也会增加轧制设备的负荷,需要考虑设备的承载能力。
增加轧制速度可以提高生产效率,但也会对产品质量产生影响,需要控制在合理范围内。
控制轧制温度可以防止结晶变形和退火软化,提高产品硬度和强度。
三、轧制质量保障高速线材轧制产生的线材产品具有高要求的机械性能和表面质量。
针对高强度钢材的生产,应该注重轧制质量控制,包括表面质量、尺寸精度和力学性能等指标的控制。
在生产过程中,需要进行基础效益测试,包括钢材力学性能测试和表面质量测试。
如果发现轧制过程中存在问题,需要及时处理。
同时,还需要加强生产过程中的工艺管理和质量监控能力,有效提高生产线的生产效率和产品品质。
四、轧制自动化控制随着信息技术和自动化技术的不断发展,高速线材轧制的自动化控制也得到了快速提升。
自动化控制需要将生产过程中的所有环节都过程监测和记录下来,从而实现全程自动化控制。
高速无扭轧机产线材(盘条)的技术改进与创新实践
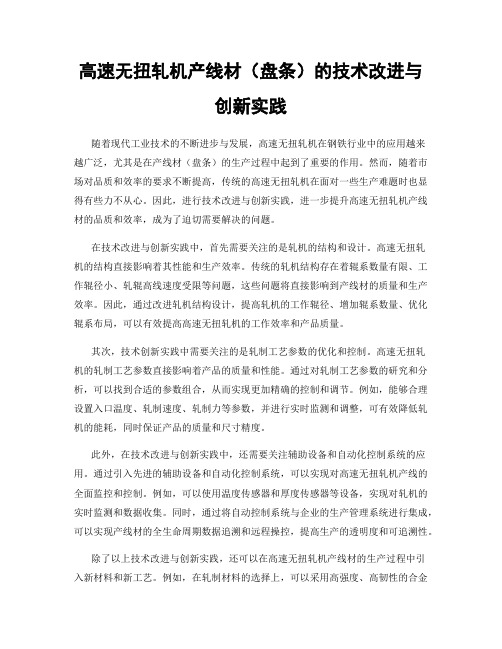
高速无扭轧机产线材(盘条)的技术改进与创新实践随着现代工业技术的不断进步与发展,高速无扭轧机在钢铁行业中的应用越来越广泛,尤其是在产线材(盘条)的生产过程中起到了重要的作用。
然而,随着市场对品质和效率的要求不断提高,传统的高速无扭轧机在面对一些生产难题时也显得有些力不从心。
因此,进行技术改进与创新实践,进一步提升高速无扭轧机产线材的品质和效率,成为了迫切需要解决的问题。
在技术改进与创新实践中,首先需要关注的是轧机的结构和设计。
高速无扭轧机的结构直接影响着其性能和生产效率。
传统的轧机结构存在着辊系数量有限、工作辊径小、轧辊高线速度受限等问题,这些问题将直接影响到产线材的质量和生产效率。
因此,通过改进轧机结构设计,提高轧机的工作辊径、增加辊系数量、优化辊系布局,可以有效提高高速无扭轧机的工作效率和产品质量。
其次,技术创新实践中需要关注的是轧制工艺参数的优化和控制。
高速无扭轧机的轧制工艺参数直接影响着产品的质量和性能。
通过对轧制工艺参数的研究和分析,可以找到合适的参数组合,从而实现更加精确的控制和调节。
例如,能够合理设置入口温度、轧制速度、轧制力等参数,并进行实时监测和调整,可有效降低轧机的能耗,同时保证产品的质量和尺寸精度。
此外,在技术改进与创新实践中,还需要关注辅助设备和自动化控制系统的应用。
通过引入先进的辅助设备和自动化控制系统,可以实现对高速无扭轧机产线的全面监控和控制。
例如,可以使用温度传感器和厚度传感器等设备,实现对轧机的实时监测和数据收集。
同时,通过将自动控制系统与企业的生产管理系统进行集成,可以实现产线材的全生命周期数据追溯和远程操控,提高生产的透明度和可追溯性。
除了以上技术改进与创新实践,还可以在高速无扭轧机产线材的生产过程中引入新材料和新工艺。
例如,在轧制材料的选择上,可以采用高强度、高韧性的合金材料,以提高产品的力学性能和使用寿命。
同时,在表面处理工艺上,可以采用先进的涂层技术,增加产品的防腐性能和耐磨性。
中厚板粗轧机改造期间精轧机单机生产方案--轧钢车间
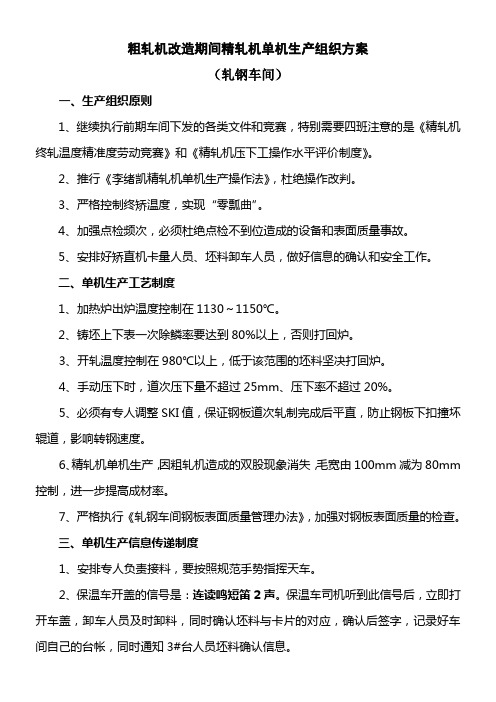
粗轧机改造期间精轧机单机生产组织方案(轧钢车间)一、生产组织原则1、继续执行前期车间下发的各类文件和竞赛,特别需要四班注意的是《精轧机终轧温度精准度劳动竞赛》和《精轧机压下工操作水平评价制度》。
2、推行《李绪凯精轧机单机生产操作法》,杜绝操作改判。
3、严格控制终矫温度,实现“零瓢曲”。
4、加强点检频次,必须杜绝点检不到位造成的设备和表面质量事故。
5、安排好矫直机卡量人员、坯料卸车人员,做好信息的确认和安全工作。
二、单机生产工艺制度1、加热炉出炉温度控制在1130~1150℃。
2、铸坯上下表一次除鳞率要达到80%以上,否则打回炉。
3、开轧温度控制在980℃以上,低于该范围的坯料坚决打回炉。
4、手动压下时,道次压下量不超过25mm、压下率不超过20%。
5、必须有专人调整SKI值,保证钢板道次轧制完成后平直,防止钢板下扣撞坏辊道,影响转钢速度。
6、精轧机单机生产,因粗轧机造成的双股现象消失,毛宽由100mm减为80mm 控制,进一步提高成材率。
7、严格执行《轧钢车间钢板表面质量管理办法》,加强对钢板表面质量的检查。
三、单机生产信息传递制度1、安排专人负责接料,要按照规范手势指挥天车。
2、保温车开盖的信号是:连读鸣短笛2声。
保温车司机听到此信号后,立即打开车盖,卸车人员及时卸料,同时确认坯料与卡片的对应,确认后签字,记录好车间自己的台帐,同时通知3#台人员坯料确认信息。
3、坯料必须轻轻落到IC出口辊道上,禁止落在其他区域。
4、坯料卸到IC出口辊道上后,必须对坯料质量和信息进行二次确认:1)确认铸坯表面质量,是否存在裂纹等缺陷。
2)3#台专人观察测宽仪显示数值,并与MES坯料宽度核对。
3)开始轧制前用机前推床抱钢时,必须查看坯料宽度是否与MES信息一致。
4)用机前推床导板比对坯料厚度,必须杜绝坯料厚度出现任何错误,防止坯料厚度错误导致的设备事故。
以上四点必须做到,必须把坯料信息层层把关,任何坯料信息不对应的,必须拒轧。
生产线改善方案

生产线改善方案以下是 7 条关于生产线改善方案:1. 咱得让生产线动起来更高效呀!就好比跑步,原来你慢悠悠地跑,现在得加把劲冲刺啦!比如说,咱们可以增加一些自动化设备来帮忙,就像给生产线安上了翅膀,那效率不得蹭蹭往上涨?这样一来,咱们是不是就能快速完成更多任务啦?例子:现在人工操作多费时费力呀,要是有个自动传输带,东西直接就运到下一个环节了,多棒啊!2. 你知道不,工人的工作环境也很重要啊!就像咱自己,要是在一个乱糟糟的地方干活,心情能好吗?所以呀,咱们得好好整理一下生产线周边,让大家舒舒服服地工作。
这就像给自己的小窝整理得干干净净,多舒坦呀!这样他们是不是能更有干劲啦?例子:你看那堆杂物都堆在一起,工人走路都不方便,赶紧清理清理呀!3. 培训可不能少哇!给工人多充充电,就像给汽车加油一样。
让他们掌握新技能,那干活不就更得心应手啦?这不是一举两得的事儿嘛!难道你不想看到工人们个个技艺高超吗?例子:咱要是安排个专业的师傅来教教大伙,那大家的操作水平肯定能上一个台阶!4. 沟通也是关键呀!就像身体里的血管一样,各个环节得通畅才行。
大家随时交流,有问题就说出来,一起想办法解决。
这不就像朋友之间聊天一样自然嘛!这样效率能不提高吗?例子:上次那个问题,如果大家早点沟通,不就不会拖那么久了嘛!5. 质量把控得严格点呀!咱不能只求速度不求质量呀,这就像做蛋糕,外表好看,里面却是空心的可不行哟!咱们得确保每个产品都杠杠的。
这样客户才会信任咱呀,对吧?例子:要是质量不过关,客户退货了,那不就白干啦,多闹心呀!6. 创新不能少哇!老是那一套可不行,得时不时来点新花样。
就像每天吃一样菜会腻,偶尔得换换口味。
想想看,有新的方法新的思路,生产线是不是能变得更有意思呀?例子:咱可以试试那种新的生产流程,说不定效果出奇地好呢!7. 要时刻关注市场动态呀!生产线可不能脱离市场需求。
就像船在海上航行,得根据风向调整方向。
了解客户想要啥,咱们就生产啥。
项目六 高速线材粗中轧操作教案

掌握导卫安装与调整方法。
能分析典型生产事故并提出解决措施。
重点
难点
粗中轧区域操作和各项参数
教学环节时间分配
3课时
教学手段、教学方法和实施步骤
多媒体
授课内容:
任务一:粗、中轧区的设备布置与参数
一、粗中轧轧制工艺与机组布置
1.粗、中轧的主要功能
粗轧是使坯料得到初步压缩和延伸,得到温度合适、断面形状正确、尺寸合格、表面良好、端头规矩、长度适合工艺要求的轧件。中轧的作用是继续缩减粗轧机组轧出的轧件断面。
(2)参照原孔型高度设定新孔型的辊缝值。
(3)调整冷却水管的位置,使冷却水能准确地浇在新轧槽上。
(4)横移轧机使新的在用轧槽处在轧制线位置上
三、粗、中轧机组轧制过程中的轧机调整操作
1.导卫操作
(1)辊式导卫的辊间距调整
原则:辊间距的设定是通过标准试棒进行的,以试棒在两导辊间能推拉带动两辊同时转动为合适。
(4)轧辊对装入机架辊头调整后,轧辊对即可被装入机架,涂抹润滑油。
(5)轧辊轴向定位、紧固与辊缝初步设定经常对轧机牌坊内侧的衬板,以及基准轧辊的垫板进行检查,更换必要的磨损件。在安装轧辊时,要用水平尺对基准辊进行水平度的测量。
2.导卫安装与调整
(1)导板梁标高的找正关系到轧制能否稳定进行
(2)导卫横梁移动通过横移导卫横梁来实现
5.粗轧后切头、尾
轧件头尾两端的散热条件不同于中间部位,轧件头尾两端温度较低,塑性较差;同时轧件端部在轧制变形时由于温度较低,宽展较大,同时变形不均造成轧件头部形状不规则,这些在继续轧制时都会导致堵塞入口导卫或不能咬入。为此在经过道次粗轧后必须将端部切去。通常切头切尾长度为70~200mm。
生产线改造方案
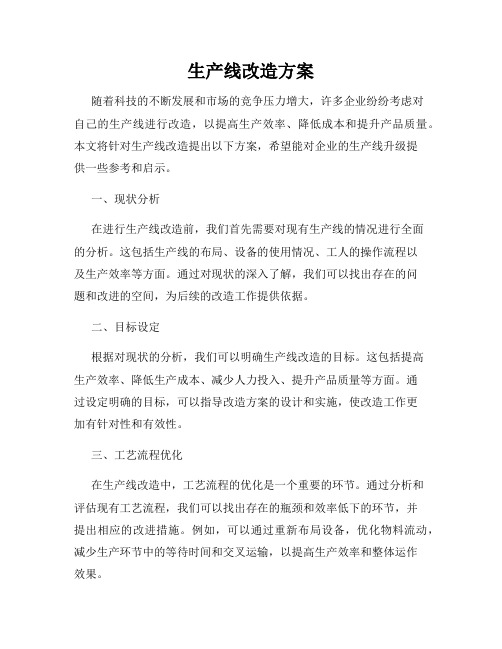
生产线改造方案随着科技的不断发展和市场的竞争压力增大,许多企业纷纷考虑对自己的生产线进行改造,以提高生产效率、降低成本和提升产品质量。
本文将针对生产线改造提出以下方案,希望能对企业的生产线升级提供一些参考和启示。
一、现状分析在进行生产线改造前,我们首先需要对现有生产线的情况进行全面的分析。
这包括生产线的布局、设备的使用情况、工人的操作流程以及生产效率等方面。
通过对现状的深入了解,我们可以找出存在的问题和改进的空间,为后续的改造工作提供依据。
二、目标设定根据对现状的分析,我们可以明确生产线改造的目标。
这包括提高生产效率、降低生产成本、减少人力投入、提升产品质量等方面。
通过设定明确的目标,可以指导改造方案的设计和实施,使改造工作更加有针对性和有效性。
三、工艺流程优化在生产线改造中,工艺流程的优化是一个重要的环节。
通过分析和评估现有工艺流程,我们可以找出存在的瓶颈和效率低下的环节,并提出相应的改进措施。
例如,可以通过重新布局设备,优化物料流动,减少生产环节中的等待时间和交叉运输,以提高生产效率和整体运作效果。
四、设备更新与智能化升级生产线改造过程中,设备的更新和智能化升级是至关重要的。
新一代的设备通常拥有更高的自动化程度和更强的生产能力,可以大大提高生产效率。
例如,可以引入机器人自动化生产,替代部分重复性劳动,降低工人的工作强度和错误率。
同时,还可以通过互联网、大数据和人工智能技术实现智能化监控和控制,提高生产线的稳定性和可靠性。
五、人员培训与技能提升在生产线改造的过程中,人员培训与技能提升同样不可忽视。
新的技术和设备的引入,往往需要工人具备相应的操作和维护技能。
因此,企业应该加强对员工的培训,提高他们的技术水平和综合素质。
通过这样的方式,可以确保新的生产线能够顺利运行,并发挥出最佳的效益和效果。
六、质量控制与持续改进改造后的生产线需要建立适应性强、灵活性高的质量控制体系。
通过实施全面的质量管理,及时发现和解决问题,不断改进和提高生产线的质量水平。
线材粗中轧轧机传动改造
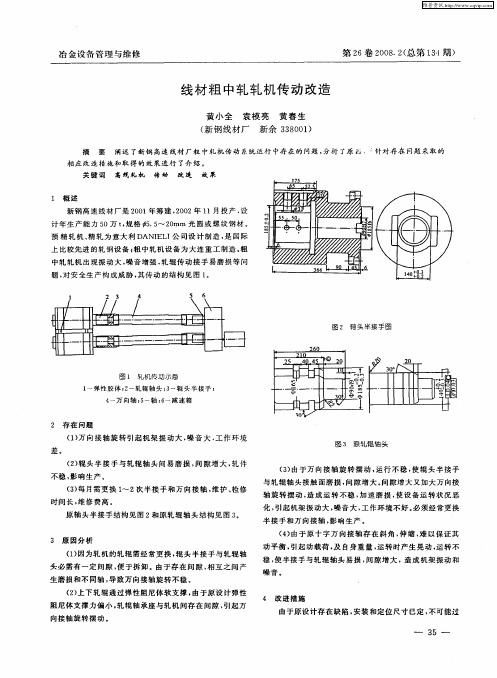
关键词 工 作辊 捷 移 液 压 缸 格来 圈 斯 特 封
1 概 述
工 作 辊 横 移 装 置 工 作 原 理 :横 移 装 置 主 要 由操 作 侧 移 动 块 、 动侧 移 动 块 、 作 辊 横 移 缸 等 组 成 。操 作 侧 移 动 块 传 工
() 3 由于 万 向 接 轴 旋 转 摆 动 , 行 不 稳 , 辊 头 半 接 手 运 使 与 轧 辊 轴 头 接触 面 磨 损 , 隙 增 大 。 隙增 大 又加 大 万 向接 问 问 轴 旋 转 摆 动 , 成 运 转 不 稳 , 速 磨 损 , 设 备 运 转 状 况 恶 造 加 使
动平衡 , 引起动载荷 , 自身重量 , 及 运转时产生晃动 , 运转不
稳 , 半 接 手 与 轧 辊 轴头 易 损 , 隙 增 大 , 成 机 架 振 动 和 使 问 造
噪音 。
生磨损和不 同轴 , 导致 万向接轴旋 转不稳 。
( ) 下 轧 辊 通 过 弹 性 阻尼 体 软 支 撑 , 于原 设 计 弹 性 2上 由 阻 尼 体 支 撑 力 偏 小 , 辊 轴 承座 与 轧 机 问 存 在 间 隙 , 轧 引起 万 向接 轴 旋 转 摆 动 。
李 涛 刘成刚 栗 露 张 磊
( 鞍钢设 备检 修协力 中心
鞍 山 14 2 ) 1 0 1
摘
要
针 对 AS P精 轧 机 组 工 作 辊 横 移 装 置 液 压 缸 经 常 发 生 内外 泄 、 液压 缸扁 头 与 缸 杆 连接 螺 纹 退 扣 、 缸
杆断等故障, 致使 横 移 功 能 不 能 正 常运 用 , 频 繁 更 换 液 压 缸 维持 生 产 的 问题 , 须 分析 了产 生 问题 的 原 因 , 出 了 改 提