高速线材生产车间设计
年产90万吨高速线材车间设计压下规程

炉外精练这种新技术得到迅猛发展的原因是:
(1)提高韧烁炉生产率。电弧炉生产率提高25%左右,可提高超高功率电炉生产率50%—10%。
(2)降低产品成本。对于精炼超低碳不锈钢,可降低成本500—1000元/吨;
(3)提高产品内在质量、扩大产品品种。当钢中氢含量低于某含量时可以避免白点的形成:钢的纯治度大大提高、同时钢的化学成分均匀稳定,偏析减轻;钢的综合力学性能得到显著提高,品种也得到扩大,从而满足了用户的要求。
3)根据现场实习并进行设备、工艺分析,工艺设计与设备选择,工艺参数计算,
计算机软件绘图,完成毕业设计任务。
2设计要达到的目标
1)进一步巩固,加深对所学基本理论、基本技能和专业知识的掌握,使之系统
化、综合化。
2)初步掌握科学研究的基本方法和能力。包括调查研究、查阅文献和搜集资料
的能力,理论分析和制定设计方案的能力,设计计算和制图的能力等。3)树立严谨、负责、实事求是、刻苦钻研、勇于探索、敢于创新的科学研究精
1研究方法
1)收集线材车间设计相关资料,查阅文献,确定线材车间的生产规模、品种,;
生产方案、建厂地址及厂区范围,资源利用状况、各种材料供应、运输等要求,需要达到的技术水平,经济及社会效益,环保要求等。
年产量40万吨高速线材车间设计_毕业设计

┊┊┊┊┊┊┊┊┊┊┊┊┊装┊┊┊┊┊订┊┊┊┊┊线┊┊┊┊┊┊┊┊┊┊┊┊┊年产量40万吨高速线材车间设计摘要根据设计要求拟建一个优碳年产40万吨的高速线材生产车间。
它的最高轧制速度为120m/s,保证速度为100m/s,产品规格为φ5.5~φ12mm,盘卷单重约2吨。
连铸坯在步进梁式加热炉中使用煤气加热,侧进侧出,加热能力为75t/h。
加热炉由微机控制,出炉温度为900℃~1050℃。
该套轧机采用全连轧无扭工艺,连铸坯为120×120mm,长约为12m,单重约为1.3t的方坯。
在12架平立-交替布置的粗轧机和中轧机之后,布置了4架预精轧机,8架精轧机,4架的减定径机组。
轧后冷却通过水冷箱和一套斯太尔摩冷却运输线(120m)来完成。
该套斯太尔摩冷却运输系统采用延迟型冷却装置,可对成品轧材的最终性能控制如抗拉强度及产品的金相组织和氧化铁皮厚度进行最终控制。
计算机系统用于控轧和控冷,无张力轧制,最佳剪切尺寸控制和缺陷检测。
本设计采用的工艺技术及选用的设备代表了当今世界上较为成熟的主流先进技术。
关键词:车间设计线材轧机高速线材┊┊┊┊┊┊┊┊┊┊┊┊┊装┊┊┊┊┊订┊┊┊┊┊线┊┊┊┊┊┊┊┊┊┊┊┊┊AbstractIn this design, a new single line high speed wire mill with the output of 400000 ton per year will be built. This maximum rolling speed reaches 120m/s, guarantee speed reaches 100m/s. The specification of the products fromφ5.5 toφ12mm diameter and each coil is about 2 ton. .The billets are heated by mix coal gas in a controlled atmosphere walking-beam furnace which is controlled by computer .The heating capacity is 75t/h,and its exit temperature is from 900℃~1050℃.The rolling mill adopts 120-mm sqare, 12-m long ,and 1.3-ton weight billets which casted by continuation casting machine.After 12 H-Vhorizontal roughing and intermediate stands,a rod-wire process line are arranged .This line consists of 4cantilevered prefinishing stands and a 8-stand Morgan No Twist finishing block.at last,for guarantee its qualtity every wire though off a 4-stand Reducing/size Mill.Post-rolling cooling is achieved by water-cooling conveyor adopts tardy cooling device which carry final control of metallurgical properties such as tensile strength and scale thickness.The computer system is used for controlled rolling and cooling, no-tension rolling, optimum cutting, gage-controll and defect detection, etc.The technology and fracilities this design stands for the prime advanced-technology nowadays.Keywords :work-shop design wire mill high speed wire┊┊┊┊┊┊┊┊┊┊┊┊┊装┊┊┊┊┊订┊┊┊┊┊线┊┊┊┊┊┊┊┊┊┊┊┊┊目录摘要 (1)Abstract (2)第一章概述 (1)第二章车间产品大纲和金属平衡表 (2)2.1车间产品大纲 (2)2.1.1产品方案表 (2)2.1.2产品交货的技术条件 (2)2.1.3产品的性能 (3)2.1.4产品国内国际销售应符合以下标准 (3)2.2原料及其质量要求 (3)2.2.1原料规格 (3)2.2.2钢坯的技术条件 (3)2.3金属平衡表 (4)第三章设计方案 (5)3.1方案的比较及选择 (5)3.1.1轧制速度的确定 (5)3.1.2线数的确定 (5)3.1.3总机架数的确定 (5)3.2高线生产的主要设备的特点及其选用 (6)3.2.1高线生产的主要设备概况 (6)第四章工艺流程 (13)4.1生产工艺流程说明 (13)4.1.1上料与加热 (13)4.1.2高压水除鳞 (13)4.1.3轧制 (13)4.1.4控制冷却 (14)4.1.5精整 (14)4.1.6剪切、废钢及氧化铁皮清除 (14)4.2生产工艺流程 (15)4.2.1生产工艺流程简 (15)┊┊┊┊┊┊┊┊┊┊┊┊┊装┊┊┊┊┊订┊┊┊┊┊线┊┊┊┊┊┊┊┊┊┊┊┊┊第五章孔型设计及速度制度 (16)5.1孔型系统的选择 (16)5.1.1粗轧、中轧孔型系统选择 (16)5.1.2预精轧、精轧机组孔型的选择 (17)5.2主要参数的计算 (18)5.2.1箱型孔型(K1,K2)设计系数的确定 (18)5.2.2各道次延伸系数的确定 (19)5.3摩擦系数的确定 (19)5.4孔型设计 (20)5.4.1孔型设计说明 (20)5.4.2各孔型计算方法 (20)5.5孔型设计步骤: (22)第六章轧机力能参数计算及电机设备校 (26)6.1轧制压力的计算 (27)6.1.1平均单位压力的计算 (27)6.1.2总轧制压力P (28)6.2轧辊强度校核 (28)6.2.1孔型在轧辊上的配置 (28)6.2.2 轧辊强度校核 (31)6.2.3危险断面尺寸的确定 (31)6.2.4轧辊强度校核 (31)6.3传动力矩计算 (34)6.3.1轧制力矩M (34)6.3.2摩擦力矩 (34)6.3.3空转力矩 (34)6.3.4动力矩 (35)6.4电机校核 (35)6.4.1电机校核 (35)第七章生产能力计算 (38)7.1各规格产品轧制时间,间隙时间的确定 (38)7.1.1各种轧制时间,间隙时间的确定 (38)┊┊┊┊┊┊┊┊┊┊┊┊┊装┊┊┊┊┊订┊┊┊┊┊线┊┊┊┊┊┊┊┊┊┊┊┊┊7.2加热炉小时生产能力计算 (39)7.3工作制度及年工作时间的确定 (40)7.4轧机负荷率及轧机年产量计算 (41)7.4.1轧机负荷率 (41)7.4.2轧机年产量 (41)7.5加热炉的生产能力计算 (41)7.5.1设计条件 (41)7.5.2加热炉生产能力计算 (41)第八章厂房平面布置和起重运输设备 (43)8.1厂房平面布置 (44)8.1.1主轧跨 (44)8.1.2成品跨 (44)8.1.3轧辊及导卫轴承加区域 (44)8.1.4车间原料及成品跨面积计算 (44)8.2 P/F线运输能力验算 (45)第九章高线车间主要经济指标 (47)9.1高线车间主要经济指标 (47)第十章环境保护及综合治理 (49)10.1编制依据 (49)10.2主要污染物及治理措施 (49)致谢 (50)参考文献 (51)附录A 轧机力能参数计算及电机设备校核程序[11] (52)附录B φ6.5mm孔型图[14] (57)附录C 英文翻译 (70)第一章概述按设计任务书的要求,本设计在综合考虑国内外线材生产和发展的基础上,主要参考马钢新高线厂[2] ,[3]以及山东石横高线厂[1]的生产及技术条件,拟建一年40万吨优质碳素钢的高速线材厂,采用单线轧制工艺。
年产60万吨高速线材车间工艺设计毕业设计(可编辑)(正规版)
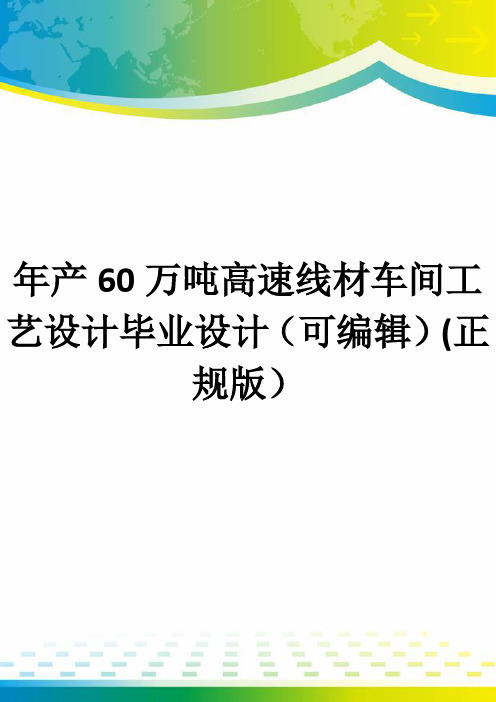
年产60万吨高速线材车间工艺设计毕业设计(可编辑)(正规版)课题:年产60万吨高速线材车间工艺设计毕业设计(论文)原创性声明和使用授权说明原创性声明本人郑重承诺:所呈交的毕业设计(论文),是我个人在指导教师的指导下进行的研究工作及取得的成果。
尽我所知,除文中特别加以标注和致谢的地方外,不包含其他人或组织已经发表或公布过的研究成果,也不包含我为获得及其它教育机构的学位或学历而使用过的材料。
对本研究提供过帮助和做出过奉献的个人或集体,均已在文中作了明确的说明并表示了谢意。
作者签名: 日期:指导教师签名: 日期:使用授权说明本人完全了解大学关于收集、保存、使用毕业设计(论文)的规定,即:按照学校要求提交毕业设计(论文)的印刷本和电子版本;学校有权保存毕业设计(论文)的印刷本和电子版,并提供目录检索与阅览效劳;学校可以采用影印、缩印、数字化或其它复制手段保存论文;在不以赢利为目的前提下,学校可以公布论文的局部或全部内容。
作者签名: 日期:湖南冶金职业技术学院毕业设计任务书设计题目:年产60万吨高速线材车间工艺设计一、主要内容及根本要求主要内容: 1、确定产品方案的编制和金属平衡表,及有关技术条件。
2、确定产品的生产工艺流程和车间平面布置。
3、典型产品的工艺设计方案(原料选取、压下规程、温度制度、速度制度等)。
4、选择主要设备与辅助设备,并确定其参数。
5、轧制力能参数的计算与强度校核各道次力能参数、咬入条件、轧辊强度、和电机发热校核等。
6、轧制图表和生产能力的计算。
7、绘制主要零件图、车间平面布置图。
根本要求: 1、要求设计方案合理、可行。
2、设计过程中要求独立思考,不得相互抄袭。
3、设计期间要求学生严守学校纪律,不得做与设计无关的事情。
4、设计图纸要求整洁、规范、线条流畅、布局合理以及数据齐全。
5、要求按设计指导老师规定的设计进度完成整个设计。
6、设计说明书字数在30000以上,要求用A4纸打印。
二、重点研究的问题1、生产工艺及技术参数确定。
高速线材车间设计设计

目录任务书 ............................................................................................................... 错误!未定义书签。
摘要 ..................................................................................................................... 错误!未定义书签。
第1章绪论 (1)1.1 设计背景及意义 (1)1.1.1 国际市场 (1)1.1.2 国内市场 (2)1.1.3 中国线材行业生产的现状 (4)1.2 设计任务 (6)1.3 厂址选择 (6)1.3.1 区域优势 (6)1.3.2 交通优势 (7)1.3.3 成本优势 (7)1.3.4 政策优势 (7)第2章产品方案的确定与编制金属平衡表 (9)2.1 产品方案的确定 (9)2.2 确定金属平衡表 (10)2.2.1 确定计算产品的成品率 (10)2.2.2 金属平衡表 (10)2.3 计算产品的选择 (11)2.3.1 计算产品选择的原则 (11)2.3.2 计算产品的技术标准 (11)第3章生产工艺流程的制订 (13)3.1 制订生产工艺流程 (13)3.1.1 制订生产工艺流程的依据 (13)3.1.2 工艺流程简介 (13)第4章设备选择 (15)4.1 加热炉 (15)4.1.1 炉型选择 (15)4.1.2 炉子尺寸的确定 (15)4.2 主轧机 (16)4.2.1 轧机的组成 (16)4.2.2 轧机的主要技术参数的确定 (16)4.3 控制冷却线 (18)4.3.1 水冷装置 (18)4.3.2 精轧机后夹送辊 (18)4.3.3 吐丝机 (19)4.3.4 斯太尔摩运输机 (19)4.4 剪机 (19)4.5 盘卷收集和处理系统 (20)第5章工艺计算 (21)5.1 坯料选择 (21)5.2 坯料加热制度确定 (21)5.2.1 加热温度确定 (21)5.2.2 加热速度的确定 (22)5.2.3 加热时间的确定 (23)5.3 计算产品的孔型设计 (23)5.3.1 选择孔型系统 (24)5.3.2 确定轧制道次数 (24)5.3.3 各道次延伸系数的分配 (25)5.3.4 各孔型及轧件尺寸的确定 (26)5.4 延伸系数校核 (32)5.5 充满度的校核 (32)5.6 轧制力的计算 (33)5.6.1 各机组的温度制度 (33)5.6.2 孔型轧制力系数 (33)5.6.3 轧件的变形抗力 (35)5.6.4 轧制力的计算公式 (36)5.7 主电机传动轧辊所需力矩及功率 (37)5.7.1 传动力矩的组成 (37)5.7.2 轧制力矩的确定 (37)5.7.3 附加摩擦力矩的确定 (37)5.7.4 空转力矩的确定 (38)5.8 轧制程序表 (39)第6章轧辊及电机校核 (41)6.1 轧辊强度校核 (41)6.1.1 校核辊身强度 (41)6.1.2 辊颈强度 (42)6.1.3 辊头校核 (42)6.2 电机校核 (43)6.2.1 等效力矩计算 (44)6.2.2 电机的过热过载校核 (44)第7章设备生产能力的计算 (46)7.1 绘制轧制图表 (46)7.1.1 轧制图表 (46)7.1.2 确定纯轧制时间、间隙时间、轧制节奏 (46)7.2 轧机生产能力计算 (48)7.2.1 轧机小时生产能力 (48)7.2.2 年产量的计算 (48)7.2.3 轧机负荷率的计算 (49)第8章车间平面布置 (50)8.1 车间平面布置的原则 (50)8.1.1 车间整体平面设计内容 (50)8.2 金属流程线的确定 (51)8.2.1 设备间距的确定 (51)8.2.2 车间内仓库设施的布置 (51)8.2.3 其它设施的布置 (52)8.3 车间厂房参数 (52)第9章安全技术及环保 (53)9.1 安全技术 (53)9.2 环境保护 (53)第10章车间主要经济指标和经济效益分析 (55)10.1 车间劳动组织 (55)10.2 主要经济技术分析 (55)10.2.1 资金来源以及投资费用 (55)10.2.2 产品成本预算 (56)10.2.3 主要经济技术指标 (57)10.2.4 车间效益估算 (58)第11章专题 (59)11.1 前言 (59)11.2 飞剪的启动信号控制 (59)11.3 飞剪的速度曲线的建立 (60)11.3.1 剪速度的要求 (60)11.3.2 飞剪的速度曲线 (60)11.3.3 飞剪制动状态与位置调节状态的转换 (61)11.4 飞剪电气自动控制系统 (62)11.4.1 剪控制系统主回路 (62)11.4.2 飞剪控制程序分析 (63)11.5 常见故障与处理 (65)11.6 结束语 (65)参考文献 (66)致谢 (67)第1章绪论1.1设计背景及意义随着全球经济形势的持续回暖,全球经济逐步走出低谷,钢铁产品产能和需求都恢复增长态势。
年产量65万吨高速线材车间设计(致谢)
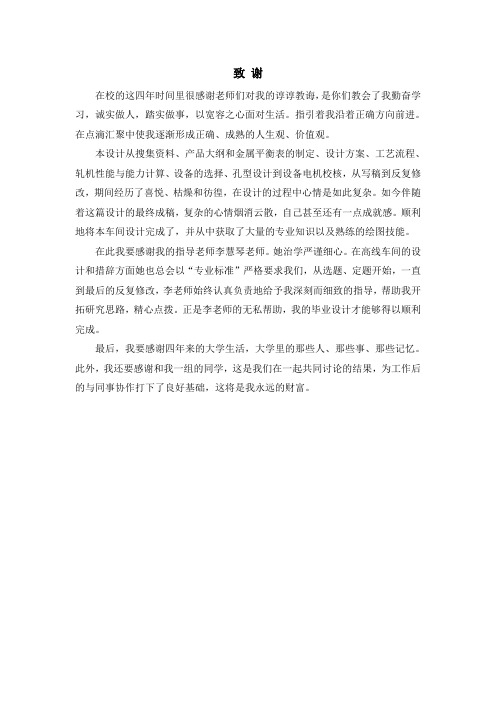
致谢
在校的这四年时间里很感谢老师们对我的谆谆教诲,是你们教会了我勤奋学习,诚实做人,踏实做事,以宽容之心面对生活。
指引着我沿着正确方向前进。
在点滴汇聚中使我逐渐形成正确、成熟的人生观、价值观。
本设计从搜集资料、产品大纲和金属平衡表的制定、设计方案、工艺流程、轧机性能与能力计算、设备的选择、孔型设计到设备电机校核,从写稿到反复修改,期间经历了喜悦、枯燥和彷徨,在设计的过程中心情是如此复杂。
如今伴随着这篇设计的最终成稿,复杂的心情烟消云散,自己甚至还有一点成就感。
顺利地将本车间设计完成了,并从中获取了大量的专业知识以及熟练的绘图技能。
在此我要感谢我的指导老师李慧琴老师。
她治学严谨细心。
在高线车间的设计和措辞方面她也总会以“专业标准”严格要求我们,从选题、定题开始,一直到最后的反复修改,李老师始终认真负责地给予我深刻而细致的指导,帮助我开拓研究思路,精心点拨。
正是李老师的无私帮助,我的毕业设计才能够得以顺利完成。
最后,我要感谢四年来的大学生活,大学里的那些人、那些事、那些记忆。
此外,我还要感谢和我一组的同学,这是我们在一起共同讨论的结果,为工作后的与同事协作打下了良好基础,这将是我永远的财富。
年产量65万吨高速线材车间设计(工艺设计)

第三章生产工艺流程制定3.1制定生产工艺流程合理的生产工艺流程应该是在满足产品技术条件的前提下,要尽可能低的消耗,最少的设备、最小的车间面积、最低的产品成本,并且根据车间具体的技术经济条件确定车间机械化和自动化程度,以利于产品质量和产量的不断提高和使工人具有较好的劳动条件。
3.1.1制订生产工艺流程的依据根据生产方案的要求:由于产品的产量、品种、规格及质量的不同,所采用的生产方案就不同,那么主要工序就有很大的差别。
因此生产方案是编制生产工艺流程的依据;根据产品的质量要求:为了满足产品技术条件,就要有相应的工序给予保证,因此,满足产品标准的要求是设计生产工艺流程的基础。
根据车间生产率的要求:由于车间的生产规模不同,所要求的工艺过程复杂程度也不同。
在生产同一产品情况下,生产规模越大的车间,其工艺流程也越复杂。
因此,设计时生产率的要求是设计工艺流程的出发点。
3.1.2工艺流程简介钢坯的准备:连铸坯150×150×1200mm装炉加热:将钢坯加热到奥氏体温度,以利于轧制。
高压水除鳞:坯料在加热炉加热之后,进入粗轧机组之前,需高压水除鳞,破除坯料表面的氧化铁皮和次生氧化铁皮,以免压下表面产生缺陷。
粗、中、精轧机组轧制:使轧件轧成成品的尺寸,其中,粗轧机组6架,中轧机组6架,预精轧机组4架,精轧机组10架,这条生产线上共有26架轧机。
飞剪切头尾:轧件进入每组轧机之前都要进行切头尾工作,目的是为了除去温度过低的头部以免损伤辊面,并防止轧件头部卡在机架间导卫装置中,卡断剪用于中轧机组、预精轧机组和精轧机组前,在事故状态下碎断轧件。
穿水冷却:为了降低进入精轧机组的轧件温度,在精轧机组之前设置水箱,以控制终轧温度。
吐丝成卷:轧出的线材在穿水冷却后,通过吐丝成卷形成散卷。
斯太尔摩散卷冷却:控冷线按不同的钢种和产品用途,控制其冷却速度,以得到相应的成品质量。
精整与运输:包括集卷、修整、检查、取样、捆轧、称重挂标牌,用集卷装置收集散卷,并将其挂到P-S运输线上的C形钩上,依次完成集卷、修整、检查、取样、捆轧、称重挂标牌等工序,之后卸卷入库。
年产32万吨高速线材车间设计
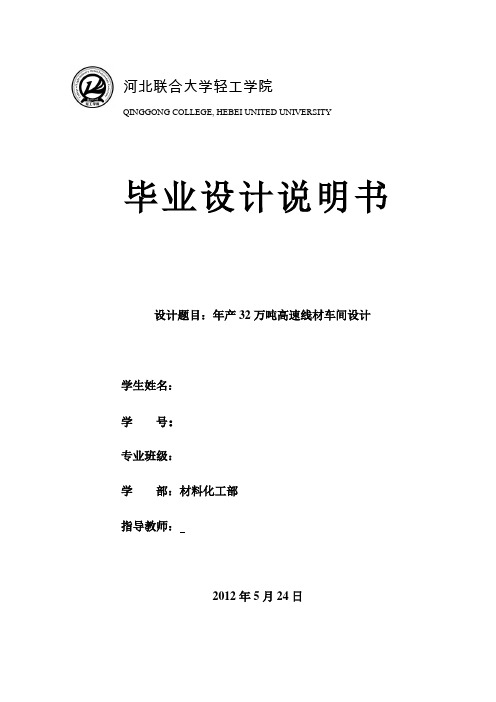
河北联合大学轻工学院QINGGONG COLLEGE, HEBEI UNITED UNIVERSITY毕业设计说明书设计题目:年产32万吨高速线材车间设计学生姓名:学号:专业班级:学部:材料化工部指导教师:2012年5月24日摘要本设计为年产32万吨高速线材车间工艺设计。
产品规格为Ф5.5~Ф10.0mm 的圆钢盘条,主要钢种有碳素结构钢、优质碳素结构钢、低合金钢。
成品线材以盘卷状态经压紧打捆后交货,盘卷质量约1600Kg。
产品质量执行现行国家标准。
根据产品规格选择尺寸为150mm×150mm×12000mm 的连铸坯为原料。
加热炉为步进式加热炉。
本设计采用全连续无头轧制生产工艺技术,全线共有轧机28架,其中粗、中轧机平立交替布置,精轧机为45°悬臂辊环式轧机,终轧最大保证速度为120m/s。
轧后控制冷却线由穿水冷却和斯泰尔摩散卷冷却线两部分组成。
精整区采用P/F运输线。
关键词:高速线材,车间设计,孔型设计AbstractThis design is an annual output of 320000 tons of high speed wire rod plant process design. Product specifications for the diameter5.5 ~10.0mm round steel wire diameter, there are major steel carbon structural steel, carbon structural steel, low alloy steel. Finished wire to the coil state through packing and bundling after delivery, coil quality about 1200Kg. Product quality of the implementation of the current national standard. According to the product specification and size of 150mm x150mm x 16000mm continuous casting billet as raw material. Heating furnace for reheating furnace. This design uses a continuous endless rolling production technology, all of the mill frame 28, wherein the coarse, medium mill alternation of horizontal and vertical arrangement, finishing mill of 45 DEG cantilever roller ring rolling mill, rolling the maximum guarantee rate of 120m / s.Key words:High speed wire, workshop design ,roll pass design目录摘要 (I)ABSTRACT (II)目录.......................................................................................................................... I II 引言. (1)第一章文献综述 (2)1.1概况 (2)1.2新技术、新装备 (3)1.2.1轧前工序 (3)1.2.2蓄热式燃烧技术 (3)1.2.3精密轧制 (3)1.2.4低温轧制技术 (4)1.2.5无头轧制技术 (4)1.2.6其他 (4)1.3现有生产线装备水平 (5)1.3.1具有领先水平的生产线 (5)1.3.2具有二流水平的生产线 (6)1.3.3一般水平的生产线 (6)1.3.4较落后的生产线 (6)1.4存在的主要问题 (6)1.5高速线材的发展及其需要解决的问题 (7)第二章产品大纲制定及金属平衡表 (9)2.1编制产品方案的原则及方法 (9)2.1.1国民经济发展对产品的要求 (9)2.1.2产品的平衡 (9)2.1.3建厂地区的条件 (9)2.1.4产品方案的制定 (9)2.2选择计算产品 (10)2.3金属平衡表 (10)第三章生产工艺流程制定 (12)3.1工艺流程图如下 (12)3.2工艺过程简述 (12)3.2.1坯料的选择 (12)3.2.2坯料的表面处理 (12)3.2.3坯料的加热 (13)3.2.4轧制过程 (13)3.2.5控制冷却过程 (15)3.2.6盘卷收集过程 (15)第四章轧钢机的选择 (17)4.1轧钢机的选择的主要依据 (17)4.2选择的内容 (17)4.2.1轧钢机的布置形式 (17)4.2.2轧机机架数量的确定 (18)4.2.3粗轧机组的选择 (18)4.2.4中轧机组的选择 (18)4.2.5预精轧机组的选择 (19)4.2.6精轧机组的选择 (19)4.3主机列介绍 (20)第五章孔型设计 (21)5.1孔型设计概述 (21)5.1.1孔型设计的内容 (21)5.1.2孔型设计的基本原则 (21)5.2孔型系统的选取 (22)5.2.1粗轧机孔型系统的选取 (22)5.2.2中轧、预精轧、精轧及减定径轧机孔型系统的选取 (23)5.3孔型设计计算 (23)5.3.11#孔型(平箱)尺寸设计及计算 (23)5.3.22#孔型(立箱)尺寸设计及计算 (23)5.3.3分配各道次延伸系数 (24)5.3.4孔型设计计算 (25)5.4孔型在轧辊上的配置 (26)5.4.1孔型在轧辊上的配置原则 (26)5.4.2孔型在轧辊上的配置 (27)5.5确定轧辊的平均工作直径及机架的连轧常数 (27)5.5.1轧辊的平均工作直径 (27)5.5.2孔型在轧辊上的配置原则 (28)第六章力学参数计算及校核 (30)6.1力能参数计算 (30)6.1.1轧制温度 (30)6.1.2轧制压力 (32)6.2电机功率的校核 (36)6.2.1传动力矩的组成 (36)6.2.2各种力矩的计算 (37)6.2.3电机校核 (39)6.2.4第一道次电机功率校核举例 (39)6.3轧辊强度的校核 (40)6.3.1强度校核 (40)6.3.2第一架轧机轧辊强度校核举例 (42)第七章年产量计算 (45)7.1轧制节奏图表 (45)7.2典型产品的小时产量计算 (45)7.2.1典型产品轧机小时产量: (45)7.2.2轧钢机的平均小时产量 (46)7.3典型产品的年产量计算 (46)7.3.1工作制度、工作小时书的确定 (46)7.3.2年产量计算 (47)第八章辅助设备的设计及选择 (48)8.1加热炉 (48)8.1.1选型 (48)8.1.2加热炉的尺寸 (49)8.2飞剪 (49)8.2.1选型 (50)8.2.2飞剪的基本参数 (50)8.3高线散卷冷却设备 (51)8.3.1吐丝机: (51)8.3.2斯泰尔摩冷却运输机 (52)8.3.3起重运输设备的选择 (52)8.4其它辅助设备 (53)8.4.1钢坯上料台架 (53)8.4.2固定挡板 (53)8.4.3入炉辊道 (54)8.4.4推钢机 (54)8.4.5出钢机 (54)8.4.6高压水除鳞装置及前后辊道 (54)8.4.7出炉辊道 (55)8.4.8钢坯剔除装置 (55)8.4.9夹送辊 (55)8.4.10卡断剪 (55)8.4.11活套器 (55)8.4.12吐丝机前夹送辊 (56)8.4.13集卷站 (56)8.4.14P/F运输机 (56)8.4.15盘卷秤 (56)8.4.16压紧打捆机 (56)8.4.17卸卷站 (57)第九章车间平面图 (58)9.1车间平面布置得原则 (58)9.2车间平面布置得内容 (58)9.2.1布置简图 (58)9.2.2可为车间以后发展各部分的具体布置 (59)第十章综合经济技术指标 (60)10.1日历作业率 (60)10.2有效作业率 (60)10.3成材率 (60)10.4劳动生产率 (60)总结 (63)参考文献 (64)致谢 (65)引言线材是指成卷交货的圆、扁小断面长材。
2023年年产万吨高速线材车间及工艺设计模板

工艺优化
高速线材车间 生产工艺流程
"工艺优化是企业提 升竞争力的关键要 素之一,可以提高 生产效率和质量。"
设备选型与布局优化
低效操作
参数优化与控制策略 改进
瓶颈环节
02
生产工艺改进
Production process improvement
优化车间布局
1. 设备布局:根据高速线材的生产工艺和工序要求,合 理规划设备的摆放位置。例如,将主要设备按照生产流 程依次排列,以减少物料和半成品的运输距离,提高生 产效率。同时,根据设备的运行特点和安全要求,合理 划分设备之间的间距,确保设备操作和维护的便利性。2. 动 线 设 计 : 设计合理的生产动线,以提高工作效率和人员 流动性。如设置合理的进料和出料通道,确保原材料和 成品的顺畅流动。同时,考虑将相邻工序之间的距离尽 量缩短,减少物料搬运和等待时间,提高生产效率。此 外,还应合理安排办公、休息和通道空间,以确保员工 的工作环境舒适和人流的通畅。
吨高速线材的目标。
流程控制
质量控制与检测
设计并建立完善的质量控制体系, 通过在线检测和自动化仪器,对线 材的尺寸、表面质量和力学性能等 进行实时监测和评估,以保证建立自动化控制系统,通过自动化设备和传感器 监测和控制生产过程中的关键参数,例如温度、速度和 张力等,以确保线材的质量和尺寸准确性。使用先进的 PLC(可编程逻辑控制器)技术,实现生产流程的实时 监控和调整,提高生产效率和稳定性。引入远程监控和 控制技术,实现对车间生产过程的远程监控和操作,提 高生产管理的便捷性和灵活性。
空间利用
1. 布局优化:通过合理布局和空间规划,充分利用车间内部 的空间资源。例如,设计合理位置的设备摆放,以减少设备 之间的距离,提高生产效率。另外,合理布置工作区域和通 道,使得物料的流动更加顺畅,减少搬运和等待时间。2. 收 纳 与 仓 储 : 设计适当的收纳系统和仓储空间,使得零部件和 工具等物品能够有序摆放和分类存放。合理安排仓库的位置 和大小,以提高物料的取用效率,并充分考虑物料的流动路 径,减少不必要的运输和处理时间。3. 空间扩展与灵活性: 考虑到未来可能的发展和生产需求,设计具有一定扩展性的 车间空间。例如,合理安排机械设备的位置,以便在需要时 能够方便地增加或调整设备。同时,设计灵活的工作区域, 能够适应不同生产线或工艺的变化,提高车间的适应性和生 产效率。通过以上的空间利用方面的考虑,能够有效提高高速线材车间的生产效率及运营效益,实现年产50万
- 1、下载文档前请自行甄别文档内容的完整性,平台不提供额外的编辑、内容补充、找答案等附加服务。
- 2、"仅部分预览"的文档,不可在线预览部分如存在完整性等问题,可反馈申请退款(可完整预览的文档不适用该条件!)。
- 3、如文档侵犯您的权益,请联系客服反馈,我们会尽快为您处理(人工客服工作时间:9:00-18:30)。
1 我国高速线材生产工艺1.1 前言线材是热轧材中断面尺寸最小的一种,由于轧钢厂需将线材在热状态下圈成盘卷并以此交货,故又称之为盘条。
线材是钢铁工业的重要产品之一。
它广泛用于机械、建筑和金属制品行业。
从线材轧机的发展历史来看,20世纪60年代以前轧制速度达到40m/s之后就很难再提高了。
但是人们追求更为高效的生产工艺以提高轧制速度和成品精度的目标却一直没有停止。
在这一思想的指导下,1996年世界上第一台由美国摩根公司研制成功的高速线材轧机正式生产,给线材生产领域带来了革命性的变化,揭开了高速线材工业化生产的序幕。
高速线材不仅用途很广而且用量也很大,它在国民经济各部门中占有重要地位。
高速线材的用途概括起来可分为两大类:一类是高速线材产品直接被利用,主要用在钢筋混凝土的配筋和焊接结构件方面。
另一类是将高速线材作为原料,经再加工后使用,主要是通过拉拔成为各种钢丝,再经过捻制成为钢丝绳,或再经编制成为钢丝网;经过热锻或冷锻成铆钉;经过冷锻及滚压成螺栓,以及经过各种切削加工及热处理制成机器零件或工具;经过缠绕成型及热处理制成弹簧等等。
1.2 我国高速线材发展状况我国1987年开始生产高速线材,受消费结构不断升级的影响和消费市场强劲拉动的作用,生产线越建越多,产量快速增长,呈现了在装备上追求高速、单线、无扭、微张力组合,在产品上追求高质量、高品质、大盘重等特点。
目前我国已成为世界上拥有高速线材生产线最多、产量最大的国家,2003年全国线材总产量4007万t,其中高速线材2704.75万t,占67.5%;2004年线材总产量4940.98万t,其中高速线材占75%左右。
线材生产发展的总趋势是提高轧速、增加盘重、提高精度及扩大规格范围。
自60年代第一台全新结构的摩根450高速线材无扭精轧机问世后,引起了线材领域的革命性变化。
线材轧制速度突破了以往的极限,达到42m/s。
经过几十年不断的改进和更新换代,特别是80年代以后由于各项制造技术、自动化控制技术的发展,检测技术的进步,使轧制速度突破100m/s大关,最大达到120m/s。
坯料断面尺寸扩大到150mm×150mm~160mm×160mm,个别使用180mm×180mm,盘重达到2t以上,线材规格上限扩大到Φ20mm~25mm。
一般可按速度将高速线材轧机分为六代,其主要指标见表1:在今后一段时期内,由于经济仍处于高速发展阶段,全国的基础设施建设、住房建设、以及西部开发将增大对线材的需求。
目前我国高速线材产品的主要品种有普碳钢、优碳钢、焊条钢、焊丝钢、弹簧钢、轴承钢、碳结钢、不锈钢、高速工具钢、冷墩钢、低合金钢等。
宝钢、武钢、马钢、酒钢等还可生产一部分钢帘线。
产品规格一般为Φ5.5mm~Φ12mm的圆钢,邢钢还可上产大规格的盘卷。
目前我国高速线材产品大多数为建筑用材,其次为金属制品焊、焊条和各类标准件用钢。
高速线材制成的各类用途金属制品见表2。
虽然我国已是线材生产大国,但与先进国家相比仍有很大差距,主要表现在高线比低、硬线及合金等高附加值线比低、控冷线材比低、总体质量水平低等。
因此,线材生产面临着结构调整的繁重任务,必须优化工艺结构、产品结构,才能增加市场竞争力。
1.3 我国高速线材生产线特点概括目前,我国正在生产的77条高速线材生产线的装备水平大致可划为四个等级,即具有世界领先水平的生产线,世界二流水平的生产线,一般水平的生产线,较落后水平的生产线。
1.3.1具有世界领先水平的生产线这类生产线主要以宝钢、马钢、新疆八一、安钢、酒钢、杭钢、青钢等高速线材生产线为代表,其主要特点是:1)均从德国西马克或意大利达涅或美国摩根或奥钢联引进。
或以点菜拼盘方式汇集了20世纪90年代后期世界线材生产的最新装备而建成。
大都在21世纪初(2001~2003年)正式投产。
2)坯料采用连铸坯短流程热装热送工艺,热装温度可达500~7500C,加热炉采用蓄热式燃烧技术。
3)轧制的保证温度达110~120m/s。
4)采用超重型精轧机组和减定径机组,实现了完全意义上的精密轧制。
5)采用了温度闭环控制系统,实现了真正意义上的控扎孔冷。
6)采用了全数字控制及交流变频调速,并设有在线测径和在线探伤装置。
7)生产效率和产品质量都能得到保障,完全具备了生产高品质产品的条件。
1.3.2 具有世界二流水平的生产线这类生产线的主要特点是:1)大都是20世纪90年代中期建成,部分生产线全引进,部分生产线中的主要装备引进。
2)部分生产线实现了热送,采用了先进的蓄热式加热炉。
3)轧制的保证速度在90~105 m/s。
4)精轧机前设有冷却水箱并采用延迟型风冷线,能实现控温轧制。
5)精整装备较先进,自动化程度较高。
6)生产线整体装备能满足高品质产品的工艺要求。
这类生产线主要以沙钢、包钢、湘钢、武钢、昆钢、天钢、北台、邢钢、鄂钢、萍乡等高速线材生产线为代表。
1.3.3 一般水平的生产线这类生产线的主要特点是:1)大都是在20世纪80年代末期至90年代初期建成或由经过改造的二手设备组成。
2)轧制速度一般在70~90 m/s左右。
3)采用热装热送工艺的少。
4)基本上没有采用20世纪90年代兴起的各种装备和技术。
5)采用了延迟型或标准型风冷段,能生产一般等级的产品。
6)由于投产时期都在15年以上,所以对这类生产线的设备使用,工艺应用等方面都很熟悉,且积累了一套行之有效的生产经验,目前,这类生产线运行成本较低,生产效率较高。
由于产品的市场是分层次和等级的,在对应等级的市场中,这类生产线生产的产品销路仍然看好。
1.3.4 较落后的生产线这类生产线是对原有的复二重轧机改造而成,或是20世纪80年代末至90年代初建成,由于当时的起点和市场定位就不高,所以装备水平和技术水平都低。
轧制速度一般在50~70m/s左右,只能生产一般水平的建筑用钢。
这类生产线目前约占77条生产线中的1/6左右,随着产品结构调整步伐的加快和市场竞争压力的增大,以及装备精良的新生产线在近几年将不断地投入使用,这类落后的生产线退出舞台将是必然的。
1.4 我国当前线材生产中应用的主要新技术、新设备1.4.1 轧前工序为了获得优质的钢水从而最终保证线材的质量,不少生产厂尽量扩大转炉容量,增加精炼,钢坯在进加热炉前设置或预留“抛丸-超声波探伤”或“磁粉探伤-修磨”工序。
一些采用超高功率电炉的企业增加了300m3级别的高炉,将热铁水兑入废钢中冶炼,不仅改善了钢质的纯净度,而且减少了电耗。
高线生产线采用连铸坯为原料后与采用初轧坯相比,炼钢到成材,能耗可降低80kg/t标煤,金属收得率提高10%。
由于节能的需要,有条件自供坯料的生产线均力求采用热送钢坯。
1.4.2 蓄热式燃烧技术我国20 世纪90年代初期以前建的用于高线生产线的加热炉,大都采用步进底式加热炉,为了使钢坯加热温度更均匀,90年代中期以后建设的加热炉大都采用侧进侧出的全梁式步进炉。
它的主要特点是步距可调,采用新型的低NOx 型烧嘴,侧烧嘴则采用带中心风的调焰烧嘴。
调节比可达1:10。
20世纪90年代中期,日本工业炉公司在开发新技术时使蓄热体在单位体上的需热能力取得突破性进展,研发的蓄热式燃烧技术在高线生产线钢坯加热过程中得到广泛的应用。
目前,我国大部分全梁式步进炉均运用了蓄热式燃烧技术。
蓄热式燃烧系统由蓄热室和换向装置组成,可将空、煤气同时预热至10000C 左右,可使用高炉煤气等低热值燃料。
采用此项技术的加热炉,不仅平均节能约35%。
且缩短了加热时间,降低了烧损。
1.4.3 应用先进的轧机进行精密轧制(A)减定径轧机为了提高线材的轧制精度,满足用户对产品尺寸精度、表面质量、机械性能等的要求,20世纪90年代初,美国摩根公司和意大利达涅利公司相继开发了减定径机组。
它由2台减经、2台定径机架与一套组合变速箱传动系统组成成组更换机架。
用减定径机进行精轧的主要优点在于:1)采用小压下量轧制,保证了产品尺寸的高精度,可达到±0.1mm的精度偏差;2)可以进行7500C~8000C的低温轧制,改善了产品性能,达到细化晶粒的效果;3)采用了快速换辊装置,减少了换辊时间,可提高轧机利用率10%~15%;4)只需1套精轧机组孔型,即可生产Φ5.0mm~Φ20mm范围内的所有规格的产品;5)减定径机组轧制后,头尾可不切除,提高了收得率。
目前,我国引进的具备世界领先水平的生产线如宝钢、马钢、酒钢、安钢、杭钢等都采用了此项装备和技术。
(B)双模块轧机该机是达涅利公司20世纪90年代中期开发的,它的主要特点是4个精轧机架分成独立的2组,每组由单独的电机变速齿轮箱传动,2台电机实现电气联锁,设于无扭精轧机后的水冷装置与吐丝机之间,通常将原有的10架无扭精轧机改为8架。
双模块轧机与减定径轧机采用的结构不同,但两者的优越性基本相同。
目前我国约有5条生产线在精密轧制中采用的是双模块轧机技术,如具有世界领先水平的新疆八一钢厂的高速线材生产线等。
1.4.4 低温轧制技术低温轧制技术主要是指轧件在轧制时,将温度控制在常化温度或热机轧制温度范围内。
低温轧制技术一方面可降低燃料消耗,减少脱碳,减少烧损;另一方面轧件在低温条件下轧制、变形、延伸使晶粒产生细化,可获得更均匀、更细的微观组织,使产品的屈服强度,抗疲劳强度大大提高。
低温轧制通常在最后2道次或4 道次进行,采用2道次时,最后2道次累计压下率24%~31%;采用4道次时,最后4道次累计压下率46%~57%。
由于低温轧制时对轧机的轧制速度、强度、电机功率等要求高,轧制负荷增大,所以低温轧制技术需在20世纪90年代中期开发的重型或超重型精轧机上进行。
我国近几年引进美国摩根公司的几套100m/s级精轧机均为重负荷型,适应了低温轧制技术对轧机的要求。
1.4.5 无头轧制技术应用于高线生产的无头轧制技术是20世纪90年代中期分别由当时日本的NKK公司和意大达涅利公司开发的。
该技术的主要优点在于可提高成材率,降低消耗并使轧制过程中各项参数处于稳定状态。
其主要是将刚出加热炉的钢坯头部与前一根在粗轧机第一架的钢坯的尾部焊接起来进行无头轧制,提高了轧机生产率,减少了切头和切废,即使在盘条打捆时也不需要切去头尾,提高了成材率。
1.4.6 其他1)大部分生产线配置了辊道式大风量延迟型控冷线,辊道分段有加速与落差,使线圈冷却更均匀。
2)在精轧机后或定精机后设置了热态在线测径仪及涡流探伤装置,对线材产品从头到尾的尺寸精度和表面情况进行检测,可及时发现轧制配件的缺陷和不合格品。
3)采用性能更好的夹送辊和吐丝机。
夹送辊可进行自动调整夹送压力并提供全长、头部、尾部的加减速夹送。
吐丝机的吐丝管结构与形状较20世纪90年代末时有了新的改进,主要表现为振动减小,吐丝管寿命延长并能快速更换;在吐丝管入口设置了用压缩空气吹扫氧化铁皮装置,可及时对吐丝管进行清理,在吐丝机前设置了可监视温度和振动状况的仪器,确保了吐丝机处于正常良好的工作状态。