年产量65万吨高速线材车间设计(工艺设计)
年产量65万吨高线车间设计(轧制速度计算)
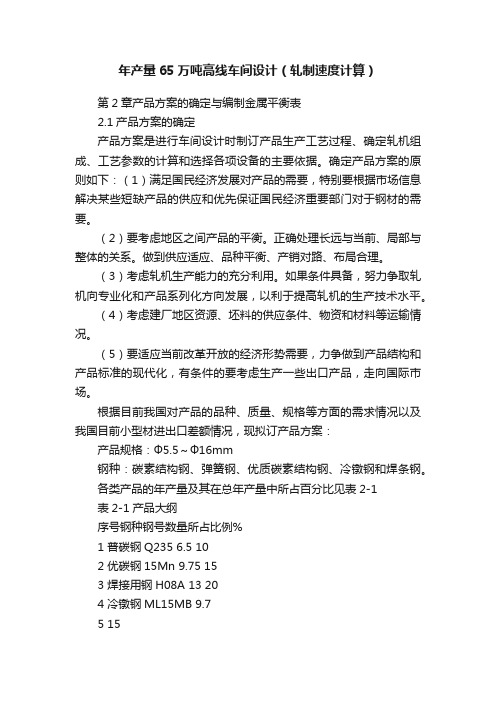
年产量65万吨高线车间设计(轧制速度计算)第2章产品方案的确定与编制金属平衡表2.1产品方案的确定产品方案是进行车间设计时制订产品生产工艺过程、确定轧机组成、工艺参数的计算和选择各项设备的主要依据。
确定产品方案的原则如下:(1)满足国民经济发展对产品的需要,特别要根据市场信息解决某些短缺产品的供应和优先保证国民经济重要部门对于钢材的需要。
(2)要考虑地区之间产品的平衡。
正确处理长远与当前、局部与整体的关系。
做到供应适应、品种平衡、产销对路、布局合理。
(3)考虑轧机生产能力的充分利用。
如果条件具备,努力争取轧机向专业化和产品系列化方向发展,以利于提高轧机的生产技术水平。
(4)考虑建厂地区资源、坯料的供应条件、物资和材料等运输情况。
(5)要适应当前改革开放的经济形势需要,力争做到产品结构和产品标准的现代化,有条件的要考虑生产一些出口产品,走向国际市场。
根据目前我国对产品的品种、质量、规格等方面的需求情况以及我国目前小型材进出口差额情况,现拟订产品方案:产品规格:Ф5.5~Ф16mm钢种:碳素结构钢、弹簧钢、优质碳素结构钢、冷镦钢和焊条钢。
各类产品的年产量及其在总年产量中所占百分比见表2-1表2-1产品大纲序号钢种钢号数量所占比例%1 普碳钢Q235 6.5 102 优碳钢15Mn 9.75 153 焊接用钢H08A 13 204 冷镦钢ML15MB 9.75 155 不锈钢1Cr18Ni9Ti 16.25 256 弹簧钢60Si2MnA 6.5 107 轴承钢GCr6 3.25 5合计65 1002.2确定金属平衡表2.2.1确定计算产品率成品率是一项重要的技术经济指标,成品率的高低反映了生产组织管理及生产技术水平的高低。
成品率是指成品质量与投料量之比的百分数。
%100QWQ A -=式中 A -成品率,%Q -投料量(坯料原料重量),t W -金属损失重量,t影响成品率的因素:(1)烧损:金属在高温状态下的氧化损失称为烧损,其中约占0.9%。
年产万吨热轧线材车间设计

┊┊┊┊┊┊┊┊┊┊┊┊┊装┊┊┊┊┊订┊┊┊┊┊线┊┊┊┊┊┊┊┊┊┊┊┊┊年产63万吨热轧线材车间设计摘要凭据结业设计的要求,设计年产63万吨的热轧高速线材生产车间,采取单线轧制方法。
产物规格为Φ5.5~16mm,单卷盘重约2吨。
本设计产物包罗碳素结构钢和优质碳素钢。
本车间设计的内容主要有:产物大纲和金属平衡表的制定;设计工艺方案和工艺流程;事情制度简直定及轧机生产能力阐发;主要设备的选择;帮助设备的选择及盘算;车间平面摆设及起重运输;车间技能经济指标;情况掩护;孔型设计;轧机力能参数盘算及电机设备校核等。
本设计原料采取连铸坯,以淘汰金属的损失,并且连铸坯的组织结构较好,这也提高了产物的质量;还可以淘汰轧制间隙时间,提高生产率。
加热炉为步进梁式加热炉,进出料方法采取侧进侧出,以包管炉子的严密性,加热能力为120t/h。
加热炉由微机控制,出炉温度为1050~1250°C。
轧机采取高速线材轧机,全线均为无扭轧制,终轧包管速度为100 m/s,最高轧制速度为120m/s。
为改进产物微观组织,轧后采取控制冷却技能,轧后冷却通过水冷箱和一套斯太尔摩冷却运输系统来完成。
斯太尔摩冷却运输系统采取延迟型冷却运输装置,它适用于冷却种种碳钢,具有较好的冷却效果。
总之,上述先进工艺技能和设备是本设计的产物高质量的重要包管;同时也为高线生产车间设计提供了一个很好的样板。
要害词:车间设计高速线材线材轧机控制轧制┊┊┊┊┊┊┊┊┊┊┊┊┊装┊┊┊┊┊订┊┊┊┊┊线┊┊┊┊┊┊┊┊┊┊┊┊┊A workshop of new hot rolled high-speed wire with the outputof 630,000 t/aAbstractAccording to the requirements of graduation design, a new single line of high-speed wire rod workshop with the output of 630,000 t / a will be built.Product specifications are for 5.5~16 mm diameter, each coil weighs about 2 tons. The products in this design include the carbon structural steel and high-quality carbon steel.The main contents of the design are mainly as follows, formulation of products scheme and metal balance, design of technological plan and process, the determination of work routine and production capacity analysis of rolling mill, choice of the main equipment, choice and calculation of the auxiliary equipment, the grooves design, the layout of workshop and hoisting and conveying equipment, check of roll strength and motor power, technical and economic indicators of the workshop and environmental protection etc.The continuous casting billet is used as raw materials in this design to reduce the metal loss. The better microstructure of the billets can also improve the quality of the product and reduce the rolling gap time to increase productivity.The reheating furnace is a walking beam type furnace which is side entry and side exit to ensure the tightness of the furnace. The heating capacity is 120t / h. The furnace is controlled by the computer. The exit temperature is 1050~1250°C.The high-speed wire rod mill is used in this workshop.No twist rolling is realized across the rolling line. The finishing ensure speed is 100 m / s, maximum rolling speed of 120m / s.The controlled cooling technology is used after rolling through the cooling water box and a Stelmor cooling conveyor system to improve product microstructure. Stelmor transportation system by the delayed cooling type cooling transport devices, which applies to various carbon steels and has better cooling effect.In short, the advanced technology and equipment, the design of the product is an important guarantee of high quality and providing a good model for the high speed wire production workshop designing.目录引言 (1)1 产物方案和金属平衡 (4)1.1 车间产物大纲 (4)1.2 产物质量执行标准及产物交货条件 (4)执行标准 (4)交货条件 (4)1.3 原料 (5)原料来源和年需要量 (5)钢坯尺寸和质量要求 (5)1.3.3 连铸坯的化学身分 (5)1.4 金属平衡表 (5)2 设计方案 (6)2.1 轧机数量简直定 (7)2.2 轧机摆设方案 (7)3 工艺流程 (9)3.1 工艺流程图 (9)3.2 生产工艺流程简述 (10)坯料的选择及加热 (10)坯料的除鳞 (10)坯料的轧制 (10)冷却 (10)后期事情 (11)4 事情时间及轧机生产能力阐发 (11)4.1 车间事情制度和年事情小时 (11)4.2 轧机生产能力阐发 (12)5 主要设备的选择 (13)5.1 加热炉 (13)炉型选择 (13)加热炉尺寸简直定 (14)5.2 轧机形式以及轧辊材质的选择 (15)轧机的选择 (15)轧辊尺寸参数简直定 (15)5.3 粗轧机组 (17)5.4 中轧机组 (17)5.5 预精轧机组 (17)5.6 精轧机组 (17)5.7 减定径机组 (18)6 帮助设备的选择及盘算 (18)6.1 P/F线运输能力验算 (18)形钩的运输周期 (18)形钩数量确定 (18)6.2 斯太尔摩冷却运输线的选择 (19)6.3 其它帮助设备的选择 (20)7 车间平面及起重运输 (23)7.1 车间平面摆设 (23)车间平面摆设的原则 (23)平面摆设的内容 (24)轧制设备间距简直定 (25)7.2 车间原料和制品库能力的盘算 (25)有效方法 (25)原料库和制品库堆放面积的负荷盘算 (25)7.3 起重运输设备的选择和性能参数 (26)7.4 其它设施的摆设 (26)8 孔型设计(Φ7.0mm) (27)8.1 孔型设计的准备盘算 (27)延伸系数的分派 (27)道次孔型系统选择 (28)8.2减定径及精轧机组孔型设计 (29)圆孔型设计 (29)椭圆孔型设计 (32)8.3 预精轧机组孔型设计 (36)圆孔型设计 (36)椭圆孔型设计 (37)8.4 中轧机组孔型设计 (39)圆孔型设计 (39)椭圆孔型设计 (41)8.5 粗轧机组孔型设计 (43)9 轧机力能参数盘算及电机设备校核 (49)9.1 轧制压力的盘算 (49)平均单位压力盘算 (49)总轧制压力 (50)9.2 轧辊强度校核 (50)孔型在轧辊上的配置 (50)轧辊强度校核 (51)危险断面尺寸简直定 (51)轧辊强度校核 (51)9.3 传动力矩盘算 (53)轧制力矩 (53)摩擦力矩 (53)空转力矩 (54)动力矩 (54)9.4 电机校核 (54)种种轧制时间及间隙时间简直定 (54)电机校核 (54)10 车间技能经济指标及情况掩护 (55)10.1 车间技能经济指标 (55)10.2情况掩护 (56)体例依据 (56)本设计中对污染的防治及综合治理 (56)致谢 (58)参考文献 (59)附录A各道次孔型图 (60)附录B程序 (64)引言1. 线材的根本状况线材是指直径为5~22mm的热轧圆钢大概相当此断面的异形钢。
李志强——年产60万吨高速线材
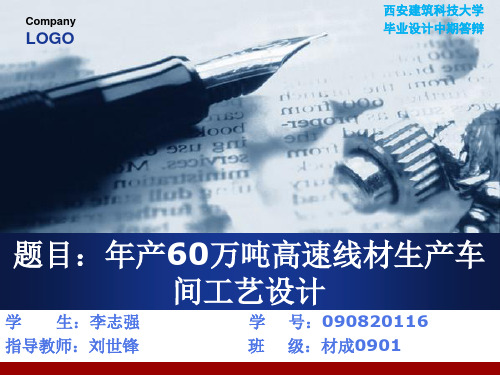
设备选择
年产60万吨高速线材生产车间工艺设计
加热炉
1. 炉子的宽度 主要根据坯料长度确定,公式如下: 式中:l —坯料的最大长度,mm; n —坯料排列数; —钢坯和炉墙以及钢坯和钢坯之间的间隔,一般取0.15~0.3m 已知l =12000 mm=12.0m,取n=1, =0.25 则:B =1×12.0+2×0.25 =12.5m 2.炉子的长度 主要根据加热炉产量决定,公式如下
西安建筑科技大学
设备选择
年产60万吨高速线材生产车间工艺设计
主轧机参数
西安建筑科技大学
设备选择
年产60万吨高速线材生产车间工艺设计
斯太尔摩冷却线
为避免当线材盘卷在800℃~1050℃高温下自然冷却时,因盘 卷内外温差大而导致表面严重氧化、盘卷内部不符合要求、机 械性能低、拉拔性能差等问题,为此目前新建的高线都选择了 斯太尔摩冷却线,斯太尔摩冷却线有三种形式:标准型、缓慢 型、延迟型,具体比较见下表
西安建筑科技大学
具体设计内容——产品大纲
年产60万吨高速线材生产车间工艺设计
金属平衡表
计算方法
粗略按以下计算:金属烧损氧化一般占坯重的1.2%,轧废约 占1.5%,粗轧切头、精轧前切头、成品切头等切损约占0.5%
典型产品
西安建筑科技大学
生产工艺流程
年产60万吨高速线材生产车间工艺设计
西安建筑科技大学
孔型参数的计算
年产60万吨高速线材生产车间工艺设计
孔型设计
螺纹钢的孔型系统与圆钢非常相似,两者之间的差别仅在于 成品孔和成品前孔。在实际生产中,除K1和K2孔外,各轧钢 厂相同规格的圆钢和螺纹钢都是公用一套孔型的,所以螺纹钢 延伸孔型系统设计与圆钢相同.其精轧孔型系统一般为:方一椭 圆一螺或圆一椭圆—螺。
年产60万吨高速线材车间工艺设计毕业论文

年产60万吨高速线材车间工艺设计毕业论文目录1产品方案及金属平衡表 (1)1.1产品方案的编制1.2产品的技术标准1.3钢铁产品化学成分及力学性能1.4金属平衡表的确定2高速线材生产设备及工艺 (13)2.1坯料2.2钢坯的加热炉和钢坯的加热2.3轧机2.4飞剪设备及工艺2.5QTB控制冷却工艺及设备2.6线材的精整、运输与成品库2.7水箱技术参数表2.8工艺流程3型钢孔型设计 (22)3.1概述3.2孔型系统3.3连轧机孔型设计4轧制压力计算 (24)4.1轧制压力计算的公式4.2轧制的速度制度4.3典型产品孔型轧制压力的计算5轧辊强度的校核 (29)5.1型钢轧辊的强度校核5.2典型产品轧辊强度校核6电机的校核和咬入条件校核 (35)6.1电机的校核6.2典型产品电机的校核6.3咬入条件校核7型钢生产车间的生产能力计算及技术经济指标 (38)7.1轧制工作图表7.2典型产品的轧机小时产量7.3轧机年可轧制时间8典型产品孔型设计 (40)8.1规格为5.5mm产品孔型设计8.2其它规格孔型参数列表1产品方案及金属平衡表1.1产品方案的编制产品方案是指所设计的工厂或车间拟生产的产品名称.品种.规格.状态及年计划产量,是进行车间设计的主要依据,根据产品方案可以选择设备和确定生产工艺.。
编制产品方案的原则:1).国民经济发展对产品的要求.根据国民经济各部门对产品数量.质量和品种等方面的需要情况,及考虑当前的急需,又要考虑将来发展的需要.为此.,设计着必须进行产品的社会调查.。
2).产品的平衡.考虑全国生产的布局和配套加以平衡.。
3).建厂地区的条件.生产资源.自然条件.投资等的可能性。
.在进行产品方案编制时,要以以上三点为依据,全面考虑,三者不可偏废.。
对于各类产品的分类.编组.牌号.化学成分.品种.规格尺寸及公差.交货状态.生产技术调件.机械性能要求.验收规格.试样及包装方法等,均按标准规定。
若没有标准,就由生产单位和用户共同订立协仪。
年产量65万吨高速线材车间设计的可行性

年产量65万吨高速线材车间设计的可行性1设计背景及意义随着全球经济形势的持续回暖,全球经济逐步走出低谷,钢铁产品产能和需求都恢复增长态势。
其主要市场空间不仅来自发达国家,还来自于发展中国家的强劲需求。
2 可行性研究目前,我国钢铁行业区域布局存在不合理现象,钢铁工业“北重南轻”的布局长期未能改善,环渤海地区钢铁产能近4亿吨,50%以上产品外销,从而增加了运输成本,造成整个行业物流的成本非常高。
2012年2月,国务院批复同意了《西部大开发“十二五”规划》这是国务院批复的第三个西部大开发五年规划。
此次规划首次提到产业布局要考虑“物流配套能力”。
由于,钢材具有典型的销售半径,产品一般只能覆盖300-500公里的需求。
假如布局不合理,产品远途倒运必然增大物流成本。
2012年以来,西部地区,特别是四川、新疆等地螺纹钢价格明显高于上海地区300-400元/吨。
随着《西部大开发“十二五”规划》的正式批复,西部地区将迎来基础建设高潮,也必将带动大量钢材需求。
2.1 中国线材行业生产的现状中国目前正在生产的77条高速线材生产线的装备水平大致分为四个等级:(1)具有世界领先水平的生产线。
这类生产线主要特点是:单线轧制,盘重大,可进行热机轧制,轧制保证速度达120米/秒,采用超重型精轧机组和减定径机组,尺寸精度控制在±0.10毫米以内,全线控轧控冷。
(2)具有世界二流水平的生产线。
这类生产线主要特点是:单线轧制,盘重较大,轧制速度可达到90米/秒以上,尺寸精度可以控制在±0.15毫米以内,采用延迟型风冷线,能实现控温轧制。
(3)一般水平的生产线。
这类生产线的主要特点是:多线轧制,盘重较小,轧制速度一般在70米/秒以上,尺寸精度可以满足B级要求,采用了延迟型或标准型风冷段。
(4)较落后的生产线。
这类生产线是对原有的复二重横列式轧机改造而成,或是20世纪80年代末至90年代初建成,由于当时的起点和市场定位就不高,所以装备水平和技术水平都低。
年产60万吨高速线材车间工艺设计毕业设计(可编辑)(正规版)
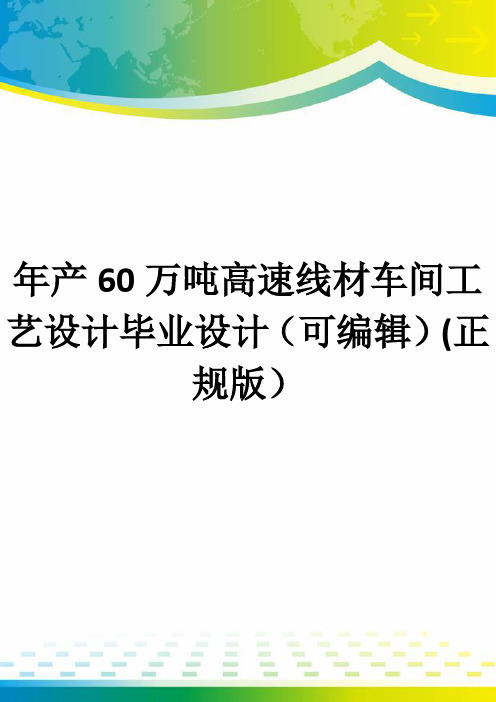
年产60万吨高速线材车间工艺设计毕业设计(可编辑)(正规版)课题:年产60万吨高速线材车间工艺设计毕业设计(论文)原创性声明和使用授权说明原创性声明本人郑重承诺:所呈交的毕业设计(论文),是我个人在指导教师的指导下进行的研究工作及取得的成果。
尽我所知,除文中特别加以标注和致谢的地方外,不包含其他人或组织已经发表或公布过的研究成果,也不包含我为获得及其它教育机构的学位或学历而使用过的材料。
对本研究提供过帮助和做出过奉献的个人或集体,均已在文中作了明确的说明并表示了谢意。
作者签名: 日期:指导教师签名: 日期:使用授权说明本人完全了解大学关于收集、保存、使用毕业设计(论文)的规定,即:按照学校要求提交毕业设计(论文)的印刷本和电子版本;学校有权保存毕业设计(论文)的印刷本和电子版,并提供目录检索与阅览效劳;学校可以采用影印、缩印、数字化或其它复制手段保存论文;在不以赢利为目的前提下,学校可以公布论文的局部或全部内容。
作者签名: 日期:湖南冶金职业技术学院毕业设计任务书设计题目:年产60万吨高速线材车间工艺设计一、主要内容及根本要求主要内容: 1、确定产品方案的编制和金属平衡表,及有关技术条件。
2、确定产品的生产工艺流程和车间平面布置。
3、典型产品的工艺设计方案(原料选取、压下规程、温度制度、速度制度等)。
4、选择主要设备与辅助设备,并确定其参数。
5、轧制力能参数的计算与强度校核各道次力能参数、咬入条件、轧辊强度、和电机发热校核等。
6、轧制图表和生产能力的计算。
7、绘制主要零件图、车间平面布置图。
根本要求: 1、要求设计方案合理、可行。
2、设计过程中要求独立思考,不得相互抄袭。
3、设计期间要求学生严守学校纪律,不得做与设计无关的事情。
4、设计图纸要求整洁、规范、线条流畅、布局合理以及数据齐全。
5、要求按设计指导老师规定的设计进度完成整个设计。
6、设计说明书字数在30000以上,要求用A4纸打印。
二、重点研究的问题1、生产工艺及技术参数确定。
年产Φ5.5~Φ10mm圆钢盘条65万t高速线材车间工艺设计毕业论文

年产Φ5.5~Φ10MM圆钢盘条65万T高速线材车间工艺设计毕业论文目录前言 (1)ABSTRACT (2)1 综述 (10)1.1 概况 (11)1.2 当前生产中应用的主要新技术、新装备 (11)1.2.1 轧前工序 (12)1.2.2 蓄热式燃烧技术 (12)1.2.3 应用先进的轧机进行精密轧制 (12)1.2.4 低温轧制技术 (13)1.2.5 无头轧制技术 (13)1.2.6 其他 (13)1.3 现有生产线装备水平 (14)1.3.2 具有世界二流水平的生产线 (15)1.3.3 一般水平的生产线 (15)1.3.4 较落后的生产线 (15)1.4 存在的主要问题 (16)1.5 高速线材的发展及其需要解决的问题 (16)2 产品大纲的制定及金属平衡 (17)2.1 编制产品方案的原则及方法 (17)2.1.1 国民经济发展对产品的要求 (18)2.1.2 产品的平衡 (18)2.1.3 建厂地区的条件、生产资源、自然条件、投资等的可能性 (18)2.2 产品方案的制定 (18)2.3 选择计算产品 (19)2.4 金属平衡表 (19)3 生产工艺流程及过程简述 (21)3.1 工艺流程图如下 (21)3.2 工艺过程简述 (21)3.2.2 坯料的表面处理 (21)3.2.3 坯料的加热 (22)3.2.4 轧制过程 (22)3.2.5 控制冷却过程 (24)3.2.6 盘卷收集过程 (25)3.2.7 废钢及氧化铁皮清除 (25)4 轧钢机的选择 (26)4.1 轧钢机的选择的主要依据 (26)4.2 选择的容 (26)4.2.1 轧钢机的布置形式 (26)4.2.2 轧机机架数量的确定 (27)4.2.3 轧钢机结构参数的确定 (27)4.3 孔型在轧辊上的配置 (29)4.3.1 一般应遵循以下原则 (29)4.3.2 分配校核道次的孔型 (30)5 孔型系统的设计与计算 (31)5.2 确定轧制道次 (31)5.3 精轧孔型设计 (31)5.3.1 确定成品孔的孔型尺寸 (31)5.3.2 确定成品孔前圆孔的孔型尺寸 (32)5.3.3 椭圆前圆孔型的构成 (32)5.4 延伸孔型系统的确定 (33)5.4.1 分配各道的延伸系数 (33)5.4.2 确定各中间扁轧件的断面尺寸 (34)5.5 计算轧辊转速及轧制速度 (37)5.6 力能参数计算 (37)5.6.1 确定各道次的轧制温度 (37)5.6.2 确定各道次的接触弧长 (38)5.6.3 各道的接触面积 (38)5.6.4 轧制压力的计算 (39)5.6.5 轧制力矩的计算 (39)5.6.6 确定空转力矩 (39)5.6.8 确定静力矩 (41)5.6.9 确定纯轧时间 (41)6 主电机的选择 (43)6.1主电机类型的选择 (43)6.2初选主电机 (43)6.2.1 初选电机所采用公式 (43)6.2.2 电机的额定转矩计算 (43)6.2.3 主电机轴上的附加摩擦力矩计算 (44)6.2.4 空转力矩的确定 (44)6.2.5 总力矩 (44)7 轧辊强度校核 (46)7.1轧辊选择 (46)7.2轧辊校核 (46)7.3 电机校核 (49)7.3.1 计算等效力矩 (49)7.3.2 电动机功率的计算 (50)8 轧机产量的计算 (50)8.1 绘制轧机负荷图 (50)8.2 轧机工作图表的制定 (51)8.3 计算轧机小时产量 (51)8.4 计算车间年产量 (51)8.5 计算轧机负荷率 (52)9 辅助设备的选择与计算 (52)9.1 加热炉 (52)9.1.1 选型 (53)9.1.2 加热炉的尺寸 (54)9.2 飞剪 (54)9.2.1 选型 (55)9.2.2 飞剪的基本参数 (56)9.3 高线散卷冷却设备 (57)9.3.1 吐丝机: (57)9.3.2 斯泰尔摩冷却运输机 (57)9.3.3 起重运输设备的选择 (58)9.4 其它辅助设备 (58)9.4.1 钢坯上料台架 (58)9.4.2 固定挡板 (59)9.4.4 推钢机 (59)9.4.5 出钢机 (60)9.4.6 高压水除鳞装置及前后辊道 (60)9.4.7 出炉辊道 (60)9.4.8 钢坯剔除装置 (60)9.4.9 夹送辊 (61)9.4.10 卡断剪 (61)9.4.11 活套器 (61)9.4.12 吐丝机前夹送辊 (61)9.4.13 集卷站 (61)9.4.14 P/F运输机 (62)9.4.15 盘卷秤 (62)9.4.16 压紧打捆机 (62)9.4.17 卸卷站 (62)10 车间平面布置 (63)10.1 轧钢车间平面布置依据的原则 (64)10.2.1 原料库面积 (64)10.2.2 成品库面积 (64)10.3 其它设施的布置 (65)10.3.1 操作台 (65)10.3.2 主电室 (65)10.3.3 轧辊的堆放 (65)10.4 运输通道的确定 (65)10.5 设备间距 (66)10.5.1 加热炉到轧机的距离: (66)10.5.2 轧机机列间的距离 (66)10.5.3 轧机到剪切机的距离 (66)10.6 厂房的设计 (66)10.6.1 厂房跨度布置 (67)10.6.2 厂房跨度大小 (67)10.6.3 柱距尺寸 (67)10.6.4 吊车轨面标高 (67)1. 日历作业率 (68)2. 有效作业率 (68)3. 成材率 (68)4. 劳动生产率 (68)年产65万吨高速线材车间工艺设计专业:金属材料工程学生:石小兰指导老师:西成摘要本设计为年产65万吨高速线材车间工艺设计。
年产量65万吨高速线材车间设计(致谢)
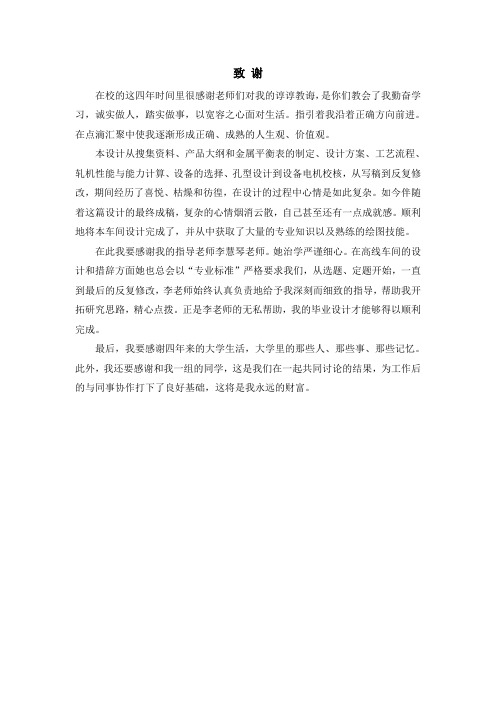
致谢
在校的这四年时间里很感谢老师们对我的谆谆教诲,是你们教会了我勤奋学习,诚实做人,踏实做事,以宽容之心面对生活。
指引着我沿着正确方向前进。
在点滴汇聚中使我逐渐形成正确、成熟的人生观、价值观。
本设计从搜集资料、产品大纲和金属平衡表的制定、设计方案、工艺流程、轧机性能与能力计算、设备的选择、孔型设计到设备电机校核,从写稿到反复修改,期间经历了喜悦、枯燥和彷徨,在设计的过程中心情是如此复杂。
如今伴随着这篇设计的最终成稿,复杂的心情烟消云散,自己甚至还有一点成就感。
顺利地将本车间设计完成了,并从中获取了大量的专业知识以及熟练的绘图技能。
在此我要感谢我的指导老师李慧琴老师。
她治学严谨细心。
在高线车间的设计和措辞方面她也总会以“专业标准”严格要求我们,从选题、定题开始,一直到最后的反复修改,李老师始终认真负责地给予我深刻而细致的指导,帮助我开拓研究思路,精心点拨。
正是李老师的无私帮助,我的毕业设计才能够得以顺利完成。
最后,我要感谢四年来的大学生活,大学里的那些人、那些事、那些记忆。
此外,我还要感谢和我一组的同学,这是我们在一起共同讨论的结果,为工作后的与同事协作打下了良好基础,这将是我永远的财富。
- 1、下载文档前请自行甄别文档内容的完整性,平台不提供额外的编辑、内容补充、找答案等附加服务。
- 2、"仅部分预览"的文档,不可在线预览部分如存在完整性等问题,可反馈申请退款(可完整预览的文档不适用该条件!)。
- 3、如文档侵犯您的权益,请联系客服反馈,我们会尽快为您处理(人工客服工作时间:9:00-18:30)。
第三章生产工艺流程制定3.1制定生产工艺流程合理的生产工艺流程应该是在满足产品技术条件的前提下,要尽可能低的消耗,最少的设备、最小的车间面积、最低的产品成本,并且根据车间具体的技术经济条件确定车间机械化和自动化程度,以利于产品质量和产量的不断提高和使工人具有较好的劳动条件。
3.1.1制订生产工艺流程的依据根据生产方案的要求:由于产品的产量、品种、规格及质量的不同,所采用的生产方案就不同,那么主要工序就有很大的差别。
因此生产方案是编制生产工艺流程的依据;根据产品的质量要求:为了满足产品技术条件,就要有相应的工序给予保证,因此,满足产品标准的要求是设计生产工艺流程的基础。
根据车间生产率的要求:由于车间的生产规模不同,所要求的工艺过程复杂程度也不同。
在生产同一产品情况下,生产规模越大的车间,其工艺流程也越复杂。
因此,设计时生产率的要求是设计工艺流程的出发点。
3.1.2工艺流程简介钢坯的准备:连铸坯150×150×1200mm装炉加热:将钢坯加热到奥氏体温度,以利于轧制。
高压水除鳞:坯料在加热炉加热之后,进入粗轧机组之前,需高压水除鳞,破除坯料表面的氧化铁皮和次生氧化铁皮,以免压下表面产生缺陷。
粗、中、精轧机组轧制:使轧件轧成成品的尺寸,其中,粗轧机组6架,中轧机组6架,预精轧机组4架,精轧机组10架,这条生产线上共有26架轧机。
飞剪切头尾:轧件进入每组轧机之前都要进行切头尾工作,目的是为了除去温度过低的头部以免损伤辊面,并防止轧件头部卡在机架间导卫装置中,卡断剪用于中轧机组、预精轧机组和精轧机组前,在事故状态下碎断轧件。
穿水冷却:为了降低进入精轧机组的轧件温度,在精轧机组之前设置水箱,以控制终轧温度。
吐丝成卷:轧出的线材在穿水冷却后,通过吐丝成卷形成散卷。
斯太尔摩散卷冷却:控冷线按不同的钢种和产品用途,控制其冷却速度,以得到相应的成品质量。
精整与运输:包括集卷、修整、检查、取样、捆轧、称重挂标牌,用集卷装置收集散卷,并将其挂到P-S运输线上的C形钩上,依次完成集卷、修整、检查、取样、捆轧、称重挂标牌等工序,之后卸卷入库。
3.2坯料选择连铸坯是用钢水直接浇铸而成的。
连铸工艺与模铸开坯相比具有减少钢锭再加热的切头切尾、金属回收率高、能源消耗少、产品成本低、基建投资和生产费用少、劳动定员少、劳动条件好等一系列优点,使连铸坯成为轧钢生产的主要供坯方式。
3.2.1坯料规格(1)连铸坯尺寸的边长和允许偏差:连铸坯断面尺寸150×150mm;连铸坯长度12000mm边长公差±4mm;对角线长度偏差≤6mm;圆角半径R>8mm;连铸坯单根重约为2.3 t吨。
连铸方坯和矩形坯标准:GB2011-98;(2)钢坯标准长度为12000mm;短尺钢坯最短长度为10000mm;每批(炉)短尺钢坯重量不大于全部钢坯重量的10%。
(3)钢坯的弯曲度在12000mm内不大于100mm;但不允许在钢坯两端,两端最大50mm.(4)钢坯扭转在12000mm内为6°.(5)钢坯端部因剪切变形而造成的局部宽度不大于边长的10%.切头毛刺应清除.端部因剪切变形而造成的局部弯曲不得大于20mm.剪切端面应与钢坯长度方向轴线垂直;端面弯斜量不得大于边长的6%.3.2.2对连铸坯表面质量要求(1)连铸坯表面缺陷最为常见的是表面氧化结疤和针孔。
严重时报废。
(2)严格控制冶炼及浇铸过程,消除表面缺陷,得到符合生产要求的连铸坯。
3.2.3对连铸坯内部质量要求(1)减少连铸坯的偏析现象。
偏析是连铸坯的一个重要的质量问题,连铸坯尺寸越小则偏析越严重。
(2)控制中心偏析。
中心偏析是连铸小方坯的代表性缺陷。
其控制方法主要有:1)扩大连铸坯尺寸。
2)严格控制钢水的过热度,防止产生严重的中心偏析。
3)降低钢种设计中的磷、锰、硫含量,以减少高碳钢盘条的中心偏析。
4)采用电磁搅拌技术,有助于减低固液界面与心部区域的温度梯度,从而减少合金成分的中心偏析。
(3)控制裂纹的产生。
3.3确定加热温度钢的加热温度是指钢加热终了时出路的温度。
不同碳素钢的加热温度见表3-1.表3-1 不同碳钢的加热温度和过烧温度钢种加热温度/C°过烧温度/C°碳素钢1.5%C 1050 1140碳素钢1.1%C 1080 1180碳素钢0.9%C 1120 1220碳素钢0.7%C 1180 1280碳素钢0.5%C 1250 1350碳素钢0.2%C 1320 1470碳素钢0.1%C 1350 1490每单位时间的板坯加热速率一般铸坯表面温度的上升速度,单位℃/ h时,在实际生产中,钢坯的厚度被加热到所需的时间温度(min/cm)的每单位时间或加热一预定单元钢坯的厚度(cm/min)来表示。
由大小和传热条件加热炉的热负荷速度,钢坯尺寸和热扩散系数的大小的影响。
加热速度大时,炉内的全部加热容量可以是短的时间在炉中,钢坯的燃烧速率。
因此,在可能的条件和内部产生过大的温差,否则钢坯将会产生弯曲和由热应力引起的内裂。
碳素结构钢和低合金钢一般不限制加热速度,加热时间越短。
但大截面钢坯和高碳,高合金钢,必须控制升温速度,以免造成铸坯内部缺陷。
线材所用的中型钢坯在步进式加热炉中加热时,情况得到很大改善,步进式加热炉可以使钢坯得到全方位上的加热。
各钢种在步进式加热炉中平均加热速度的经验数据如表2 表3-2在步进式加热炉中各钢种的平均加热速度3.4加热时间确定加热时间指金属装炉后加热到加工要求温度所需要的时间。
加热时间同钢种、坯料尺寸与形状、坯料在炉中的方法、炉形结构及装炉温度等因素有关。
连续式加热炉:7(+05=.0DT)D式中T-加热时间,timeD-钢坯厚度或钢坯直径,cm7(=⨯.0T取T=2h05=+15)m i n.25151163.5钢材的冷却与精整1、钢材的冷却经热轧成形的钢材仍处在一个较高的温度范围,尚有800~900℃的温度,需要经过冷却使钢材温度降至常温。
由于钢在热轧后冷却到常温,钢材经历相变和再结晶的过程;在应力作用下可能出现内部裂纹和外部裂纹,得采取缓冷等措施。
另外还可利用轧件扎后的余热进行控制冷却,以获得所需要的金相组织和力学性能,这就是钢材的冷却制度。
冷却方法分为自然冷却和控制冷却:自然冷却是把轧后的钢材在冷床上自然冷却。
对组织及性能无特殊要求的钢材,可采用这种冷却方式。
控制冷却是把轧后的轧件进行冷却过程进行有目的人为控制,使产品达到预期的内部组织和力学性能。
2、其它精整工序除了上述各工序外,精整内容还包括成品的热处理、各种涂层和表面精加工及成品检验等内容,成品的质量检验内容包括化学成分分析、低倍组织及显微组织、机械性能检验等。
第四章车间工艺设计4.1确定轧机类型及布置形式轧钢机是完成金属轧制变形的主要设备,是代表车间生产技术水平。
因此,选择的是否合理对车间生产具有非常重要的影响。
4.1.1轧钢机选择原则轧钢机选择的主要依据是车间生产的钢材的钢种、产品品种和规格、生产规模的大小以及由此确定的产品生产工艺过程。
在选择轧钢机时一般要注意考虑下列原则;(1)满足产品方案的前提下,使轧机组成合理,布置紧凑;有较高的生产效率和设备利用系数;有利于轧机机械化、自动化的实现,有助于工人劳动条件的改善;(2保证获得质量良好的产品,并考虑到生产新产品的可能;轧机结构型式先进合理,制造容易,操作简单,维修方便;由于采用的生产方案就不同,所以产品的产量、品种、规格及质量的不同,那么主要工序就有很大差距。
因此生产方案是编制生产工艺流程的依据。
(1)生产规模大小由于车间生产规模不同,所要求的工艺过程复杂程度也不同。
在同一生产产品情况下,生产规模越大的车间,其工艺过程也越复杂。
设计时生产率的要求是设计工艺过程的出发点。
(2)产品成本成品是生产效果的综合反映,是各种因素影响的结果。
一般钢的加工工艺性能愈差,产品的技术要求愈高,其生产工艺过程就愈复杂,生产过程中金属、燃料、电力、劳动力等各种消耗也愈高,产品成本必然会相应提高。
反之,则产品成本下降。
工艺过程中采用的工序必须保证生产安全,不危及劳动者的身体健康,不造成环境污染。
否则,应采取妥善的防护措施。
选择轧钢机时除遵循上述的一般原则之外,要从产品的工艺要求出发,根据不同产品的生产特点和具体要求来确定轧机的结构型式、主要技术参数和它们的布置形式4.1.2轧钢机类型线材轧机多为二辊式,布置形式很多,主要有横列式、连续式、高速无扭整体式由于设计产量较高可采用45°全程无扭轧机,例如美国摩根公司的高速无扭线材精轧机其特点是:(1)工艺布置优化,全线18架轧机呈平立轧制交替布置,轧件在整个轧制过程中无扭转;(2)高速轧制,成品轧机的最高轧制速度为120米/秒;(3)引进新一代超重型V型轧机,轧机的功率、负荷、刚度都优于标准型轧机;(4)产品的高化,可生产直径5.5~20毫米规格线材;(5)产品盘重大,利用一锭一坯一成品,成品每盘单重达2.2吨;(6)产品性能优质化,采用美国摩根公司最新开发的大风量斯太尔摩控制冷却设备,成品线材可以直接拉成高强度钢丝;(7)自动控制系统数字化提高了轧制过程的控制精度、可靠性和易操作性。
轧机布置形式、轧机布置形式可采用摩根式45°无扭整体机座的高速线材轧机为二辊式,辊轴中心线与水平成45°角,而相邻轧辊轴线成90°角交替配置,轧制中轧件没有扭转,轧机集体传动,一般简称为45°无扭线材轧机。
4.1.3轧机数量的确定本设计产品的最小规格为Φ5.5mm,故在确定轧机数目时,以最小直径Φ5.5坯料规格为150×150×12000mm连铸坯计算得:F0=150×150=22500 mm2F n=π(D/2)2=23.75mm2上式中:F0——连铸坯料原始面积F n——成品断面面积则总延伸系数:μz=F0/F c =22500/23.75=947.3取平均延伸系数:μc=1.28则轧机数:N=㏑μz/㏑μc=27.61取N=284.1.4轧机的组成(1)粗轧机组的选择粗轧机是使坯料得到初步的压缩和延伸,得到温度合适、断面形状正确、尺寸合格、表面质量良好、长度合适的工艺要求的轧件。
本设计选用6架平-立辊交替布置的二辊无牌坊式粗轧机组,采用上传动和下传动方式。
(2)中轧机组的选择中轧机组的作用是继续缩减从粗轧机组的轧件断面,为精轧提供形状正确、尺寸精确的中间料为保证足够的压下量。
本设计采用6架平-立交替布置的、双支点、长辊身、多孔型无牌坊轧机。
(3)预精轧机组的选择预精轧机组继续缩减从中轧机组轧出来的轧件断面,为后来的精轧机组轧机提供尺寸精确和形状正确的轧件。