高速线材车间设计说明
年产万吨热轧线材车间设计

┊┊┊┊┊┊┊┊┊┊┊┊┊装┊┊┊┊┊订┊┊┊┊┊线┊┊┊┊┊┊┊┊┊┊┊┊┊年产63万吨热轧线材车间设计摘要凭据结业设计的要求,设计年产63万吨的热轧高速线材生产车间,采取单线轧制方法。
产物规格为Φ5.5~16mm,单卷盘重约2吨。
本设计产物包罗碳素结构钢和优质碳素钢。
本车间设计的内容主要有:产物大纲和金属平衡表的制定;设计工艺方案和工艺流程;事情制度简直定及轧机生产能力阐发;主要设备的选择;帮助设备的选择及盘算;车间平面摆设及起重运输;车间技能经济指标;情况掩护;孔型设计;轧机力能参数盘算及电机设备校核等。
本设计原料采取连铸坯,以淘汰金属的损失,并且连铸坯的组织结构较好,这也提高了产物的质量;还可以淘汰轧制间隙时间,提高生产率。
加热炉为步进梁式加热炉,进出料方法采取侧进侧出,以包管炉子的严密性,加热能力为120t/h。
加热炉由微机控制,出炉温度为1050~1250°C。
轧机采取高速线材轧机,全线均为无扭轧制,终轧包管速度为100 m/s,最高轧制速度为120m/s。
为改进产物微观组织,轧后采取控制冷却技能,轧后冷却通过水冷箱和一套斯太尔摩冷却运输系统来完成。
斯太尔摩冷却运输系统采取延迟型冷却运输装置,它适用于冷却种种碳钢,具有较好的冷却效果。
总之,上述先进工艺技能和设备是本设计的产物高质量的重要包管;同时也为高线生产车间设计提供了一个很好的样板。
要害词:车间设计高速线材线材轧机控制轧制┊┊┊┊┊┊┊┊┊┊┊┊┊装┊┊┊┊┊订┊┊┊┊┊线┊┊┊┊┊┊┊┊┊┊┊┊┊A workshop of new hot rolled high-speed wire with the outputof 630,000 t/aAbstractAccording to the requirements of graduation design, a new single line of high-speed wire rod workshop with the output of 630,000 t / a will be built.Product specifications are for 5.5~16 mm diameter, each coil weighs about 2 tons. The products in this design include the carbon structural steel and high-quality carbon steel.The main contents of the design are mainly as follows, formulation of products scheme and metal balance, design of technological plan and process, the determination of work routine and production capacity analysis of rolling mill, choice of the main equipment, choice and calculation of the auxiliary equipment, the grooves design, the layout of workshop and hoisting and conveying equipment, check of roll strength and motor power, technical and economic indicators of the workshop and environmental protection etc.The continuous casting billet is used as raw materials in this design to reduce the metal loss. The better microstructure of the billets can also improve the quality of the product and reduce the rolling gap time to increase productivity.The reheating furnace is a walking beam type furnace which is side entry and side exit to ensure the tightness of the furnace. The heating capacity is 120t / h. The furnace is controlled by the computer. The exit temperature is 1050~1250°C.The high-speed wire rod mill is used in this workshop.No twist rolling is realized across the rolling line. The finishing ensure speed is 100 m / s, maximum rolling speed of 120m / s.The controlled cooling technology is used after rolling through the cooling water box and a Stelmor cooling conveyor system to improve product microstructure. Stelmor transportation system by the delayed cooling type cooling transport devices, which applies to various carbon steels and has better cooling effect.In short, the advanced technology and equipment, the design of the product is an important guarantee of high quality and providing a good model for the high speed wire production workshop designing.目录引言 (1)1 产物方案和金属平衡 (4)1.1 车间产物大纲 (4)1.2 产物质量执行标准及产物交货条件 (4)执行标准 (4)交货条件 (4)1.3 原料 (5)原料来源和年需要量 (5)钢坯尺寸和质量要求 (5)1.3.3 连铸坯的化学身分 (5)1.4 金属平衡表 (5)2 设计方案 (6)2.1 轧机数量简直定 (7)2.2 轧机摆设方案 (7)3 工艺流程 (9)3.1 工艺流程图 (9)3.2 生产工艺流程简述 (10)坯料的选择及加热 (10)坯料的除鳞 (10)坯料的轧制 (10)冷却 (10)后期事情 (11)4 事情时间及轧机生产能力阐发 (11)4.1 车间事情制度和年事情小时 (11)4.2 轧机生产能力阐发 (12)5 主要设备的选择 (13)5.1 加热炉 (13)炉型选择 (13)加热炉尺寸简直定 (14)5.2 轧机形式以及轧辊材质的选择 (15)轧机的选择 (15)轧辊尺寸参数简直定 (15)5.3 粗轧机组 (17)5.4 中轧机组 (17)5.5 预精轧机组 (17)5.6 精轧机组 (17)5.7 减定径机组 (18)6 帮助设备的选择及盘算 (18)6.1 P/F线运输能力验算 (18)形钩的运输周期 (18)形钩数量确定 (18)6.2 斯太尔摩冷却运输线的选择 (19)6.3 其它帮助设备的选择 (20)7 车间平面及起重运输 (23)7.1 车间平面摆设 (23)车间平面摆设的原则 (23)平面摆设的内容 (24)轧制设备间距简直定 (25)7.2 车间原料和制品库能力的盘算 (25)有效方法 (25)原料库和制品库堆放面积的负荷盘算 (25)7.3 起重运输设备的选择和性能参数 (26)7.4 其它设施的摆设 (26)8 孔型设计(Φ7.0mm) (27)8.1 孔型设计的准备盘算 (27)延伸系数的分派 (27)道次孔型系统选择 (28)8.2减定径及精轧机组孔型设计 (29)圆孔型设计 (29)椭圆孔型设计 (32)8.3 预精轧机组孔型设计 (36)圆孔型设计 (36)椭圆孔型设计 (37)8.4 中轧机组孔型设计 (39)圆孔型设计 (39)椭圆孔型设计 (41)8.5 粗轧机组孔型设计 (43)9 轧机力能参数盘算及电机设备校核 (49)9.1 轧制压力的盘算 (49)平均单位压力盘算 (49)总轧制压力 (50)9.2 轧辊强度校核 (50)孔型在轧辊上的配置 (50)轧辊强度校核 (51)危险断面尺寸简直定 (51)轧辊强度校核 (51)9.3 传动力矩盘算 (53)轧制力矩 (53)摩擦力矩 (53)空转力矩 (54)动力矩 (54)9.4 电机校核 (54)种种轧制时间及间隙时间简直定 (54)电机校核 (54)10 车间技能经济指标及情况掩护 (55)10.1 车间技能经济指标 (55)10.2情况掩护 (56)体例依据 (56)本设计中对污染的防治及综合治理 (56)致谢 (58)参考文献 (59)附录A各道次孔型图 (60)附录B程序 (64)引言1. 线材的根本状况线材是指直径为5~22mm的热轧圆钢大概相当此断面的异形钢。
高速线材工艺的设计说明

高速线材车间工艺设计及帘线钢质量控制技术摘要本设计是依据鞍钢线材厂设计的年产量55万吨的高速线材车间工艺。
典型产品为Q235、Φ6mm的线材。
设计说明书包括文献综述,车间工艺设计,专题三个部分。
在综述部分叙述了线材的基本知识和当前线材生产的状况。
设计部分(从第二章到第九章)主要包括产品方案及工艺流程的设计及制定、生产设备的选择、工艺参数的计算及校核、年产量计算、导位装置及轧机调整、车间平面布局设计及图纸绘制,还有技术经济指标与环保措施。
专题部分主要阐述了对帘线钢质量控制的方法及研究。
关键词:高速线材;生产方案;孔型设计;校核;帘线钢High-speed wire rod plant process design and quality control of steel cordAbstractThis design which is based on Anshan Iron and Steel Wire Factory is planted 550,000 t annual workshop for high-speed wire rod plant technology. Typical produce is the Q235,Φ6mm wire. Design specification includs literature review, workshop process design andproject. The literature review part describes the basic knowledge of wire rod production andthe current situation. Design part (from chapter to chapter IX) describes the main program andthe process of product design and development, production and equipment selection, process parameter calculation and checking, annual basis, the guide position adjusting device andmill,shop flat design and layout drawings, as well as technical and economic indicators and environmental protection measures. The major topics describes method and technology in quality control of steel cord.Keyword:High-speed wire; production program; pass design; check;Steel Cord目录 摘要............................................................................................................................................I Abstract...................................................................................................................................II 1文献综述..............................................................................................................................1 1.1线材生产的基本知识...................................................................................................1 1.1.1线材的定义.........................................................................................................1 1.1.2线材的种类.........................................................................................................1 1.1.3线材的品种与用途.............................................................................................1 1.2生产工艺.......................................................................................................................4 1.2.1线材的生产工艺流程.........................................................................................4 1.2.2线材的生产特点.................................................................................................4 1.2.3线材生产轧机布置.............................................................................................5 1.3产品的质量控制...........................................................................................................6 1.3.1坯料控制.............................................................................................................6 1.3.2加热控制.............................................................................................................7 1.3.3轧制控制.............................................................................................................8 1.3.4冷却控制.............................................................................................................8 1.4生产的发展...................................................................................................................9 1.4.1轧制速度进一步提高.........................................................................................9 1.4.2采用减径定径机组...........................................................................................10 1.4.3无扭轧机...........................................................................................................12 1.4.4低温轧制技术...................................................................................................12 1.4.5采用控制轧制和控制冷却...............................................................................12 1.4.6无头轧制...........................................................................................................13 1.4.7采用低温轧制和温控轧制技术.......................................................................13 1.4.8广泛采用在线测径及涡流探伤仪...................................................................13 1.4.9高线轧机的其他新设备...................................................................................13 1.5本设计的目的和意义.................................................................................................14 2产品大纲及金属平衡表制定......................................................................................15 2.1产品方案的确定.........................................................................................................15 2.1.1产品方案...........................................................................................................15 2.1.2产品大纲...........................................................................................................15 2.2坯料的确定.................................................................................................................15 2.2.1坯料的选择.......................................................................................................15 2.2.2坯料的技术条件...............................................................................................16 2.2.3对表面质量与部质量的要求.......................................................................17 2.3生产方案的确定.........................................................................................................18 2.4金属平衡表的制定.. (19)3主要设备选择及其参数设定......................................................................................20 3.1加热炉.........................................................................................................................20 3.2轧机参数.....................................................................................................................22 3.2.1粗轧机组设备参数...........................................................................................22 3.2.2中轧机组设备参数...........................................................................................23 3.2.3预精轧机组设备参数.......................................................................................24 3.2.4精轧机组设备参数...........................................................................................25 3.3冷却设备.....................................................................................................................26 3.4辅助设备性能参数.....................................................................................................28 3.4.1飞剪、摆动剪、卡断剪...................................................................................28 3.4.2吐丝机...............................................................................................................28 3.4.3集卷筒...............................................................................................................29 3.4.4立活套、侧活套...............................................................................................29 4产品工艺制度制定.........................................................................................................30 4.1生产工艺流程.............................................................................................................30 4.2加热制度的制定.........................................................................................................31 4.2.1加热目的...........................................................................................................31 4.2.2加热温度...........................................................................................................31 4.2.3钢坯的加热速度和加热时间 (32)4.3轧制温度的确定.........................................................................................................33 4.4延伸系数的确定.........................................................................................................34 4.4.1轧制道次的确定...............................................................................................34 4.4.2各道次延伸量的确定.......................................................................................34 4.5冷却工艺的确定.........................................................................................................35 5孔型设计............................................................................................................................36 5.1孔型设计的基本容.................................................................................................36 5.1.1孔型设计的容...............................................................................................36 5.1.2孔型设计的要求...............................................................................................36 5.1.3孔型的分类.......................................................................................................36 5.1.4孔型设计的原则...............................................................................................36 5.2线材生产中的孔型系统.............................................................................................37 5.2.1孔型类型...........................................................................................................37 5.2.2线材中孔型系统选择分析...............................................................................37 5.3孔型设计.....................................................................................................................38 5.3.1圆孔型设计.......................................................................................................38 5.3.2椭圆孔型设计...................................................................................................39 5.3.3箱型孔型设计...................................................................................................40 5.3.4连轧常数及轧制速度.......................................................................................40 6轧制力能参数及设备校核. (42)6.1摩擦系数确定.............................................................................................................42 6.2轧制力计算.................................................................................................................42 6.3咬入能力校核.............................................................................................................44 6.4轧辊强度校核.............................................................................................................45 6.4.1粗轧机组轧辊强度校核...................................................................................46 6.4.2中轧机组轧辊强度校核...................................................................................47 7年产量计算.......................................................................................................................50 7.1轧机工作图表的绘制.................................................................................................50 7.1.1轧制节奏时间的确定.......................................................................................50 7.1.2轧机工作图表的绘制.......................................................................................51 7.2轧机年产能力计算.....................................................................................................52 7.2.1轧机平均小时产量...........................................................................................52 7.2.2车间年产量计算...............................................................................................53 7.3加热炉生产能力计算.................................................................................................53 7.4仓库面积计算.............................................................................................................54 8车间平面布置及主要技术经济指标........................................................................55 8.1车间平面布置.............................................................................................................55 8.1.1主要设备间距的确定.......................................................................................55 8.1.2车间原料仓库和成品仓库面积的确定...........................................................55 8.2 车间主要技术经济指标和环保 (56)8.2.1车间主要技术经济指标...................................................................................56 8.2.2能源消耗...........................................................................................................56 8.3环境保护对车间设计的要求.....................................................................................58 9专题 帘线钢的质量控制技术.............................................................................60 9.1生产工艺.....................................................................................................................60 9.1.1钢帘线的生产工艺...........................................................................................60 9.1.2钢帘线钢的生产技术.......................................................................................61 9.2对钢帘线钢的质量要求及控制措施.........................................................................61 9.2.1钢帘线钢的化学成分.......................................................................................61 9.2.2夹杂物控制.......................................................................................................62 9.2.3中心偏析...........................................................................................................62 9.2.4有害气体含量及残余元素的控制...................................................................63 9.2.5表面质量及部缺陷.......................................................................................63 9.2.6结构特性...........................................................................................................63 9.3钢帘线钢生产的现状和展望.....................................................................................63 9.3.1国外部分钢厂生产钢帘线钢的概况...........................................................63 9.3.2钢帘线钢高强度化的努力方向.......................................................................64 9.3.3钢帘线钢生产今后的展望...............................................................................64 9.4结论.............................................................................................................................65 附录A 计算机C 程序代码 (66)附录B 孔型图 (70)参考文献 (73)结束语...................................................................... (74)1文献综述1.1线材生产的基本知识1.1.1线材的定义线材是热轧型钢中断面尺寸最小的一种。
年产60万吨高速线材车间工艺设计毕业设计(可编辑)(正规版)
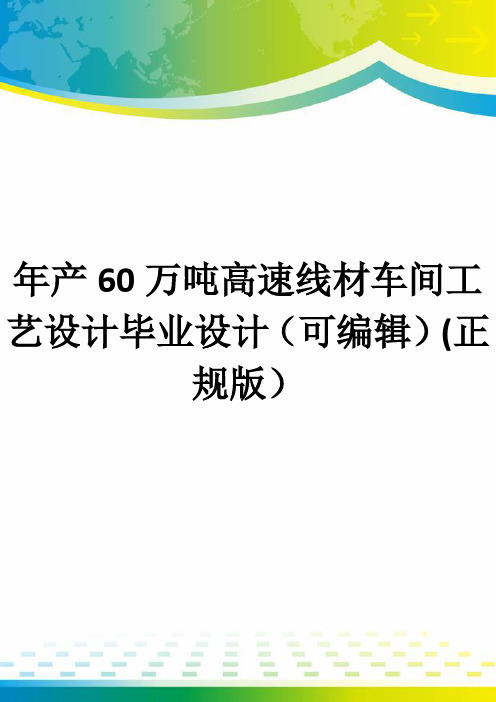
年产60万吨高速线材车间工艺设计毕业设计(可编辑)(正规版)课题:年产60万吨高速线材车间工艺设计毕业设计(论文)原创性声明和使用授权说明原创性声明本人郑重承诺:所呈交的毕业设计(论文),是我个人在指导教师的指导下进行的研究工作及取得的成果。
尽我所知,除文中特别加以标注和致谢的地方外,不包含其他人或组织已经发表或公布过的研究成果,也不包含我为获得及其它教育机构的学位或学历而使用过的材料。
对本研究提供过帮助和做出过奉献的个人或集体,均已在文中作了明确的说明并表示了谢意。
作者签名: 日期:指导教师签名: 日期:使用授权说明本人完全了解大学关于收集、保存、使用毕业设计(论文)的规定,即:按照学校要求提交毕业设计(论文)的印刷本和电子版本;学校有权保存毕业设计(论文)的印刷本和电子版,并提供目录检索与阅览效劳;学校可以采用影印、缩印、数字化或其它复制手段保存论文;在不以赢利为目的前提下,学校可以公布论文的局部或全部内容。
作者签名: 日期:湖南冶金职业技术学院毕业设计任务书设计题目:年产60万吨高速线材车间工艺设计一、主要内容及根本要求主要内容: 1、确定产品方案的编制和金属平衡表,及有关技术条件。
2、确定产品的生产工艺流程和车间平面布置。
3、典型产品的工艺设计方案(原料选取、压下规程、温度制度、速度制度等)。
4、选择主要设备与辅助设备,并确定其参数。
5、轧制力能参数的计算与强度校核各道次力能参数、咬入条件、轧辊强度、和电机发热校核等。
6、轧制图表和生产能力的计算。
7、绘制主要零件图、车间平面布置图。
根本要求: 1、要求设计方案合理、可行。
2、设计过程中要求独立思考,不得相互抄袭。
3、设计期间要求学生严守学校纪律,不得做与设计无关的事情。
4、设计图纸要求整洁、规范、线条流畅、布局合理以及数据齐全。
5、要求按设计指导老师规定的设计进度完成整个设计。
6、设计说明书字数在30000以上,要求用A4纸打印。
二、重点研究的问题1、生产工艺及技术参数确定。
高速线材孔型设计说明

目录1设计说明 (2)1.1孔型设计概述 (2)1.1.1孔型设计的容 (2)1.1.2孔型设计的基本原则 (2)2孔型系统的选择及依据 (3)2.1孔型系统的选取 (3)2.1.1粗轧机孔型系统的选取 (3)2.1.2中轧、预精轧及精轧轧机孔型系统的选取 (3)3确定轧制道次 (4)3.1轧机的选择 (4)4分配各道次延伸系数 (5)4.1孔型设计计算 (5)4.1.1确定各道次延伸系数 (5)5确定各道次出口的断面面积 (6)5.1确定各道次轧件的断面面积 (6)6各道次孔型尺寸 (7)6.1孔型设计计算 (7)7孔型在轧辊上的配置 (8)7.1孔型在轧辊上的配置原则 (8)7.1.1孔型在轧辊上的配置 (9)7.2轧辊的平均工作直径及轧辊转速的确定 (9)7.2.1工作辊径的确定 (9)7.2.2轧辊转速的确定 (10)8力能等效计算 (13)8.1力能参数计算 (13)8.1.1轧制温度 (13)8.1.2轧制力计算 (15)8.1.3轧辊辊缝计算 (20)9校核轧辊强度 (21)9.1轧辊强度的校核 (21)9.1.1强度校核 (21)9.1.2第一架轧机轧辊强度校核举例 (24)10电机的选择及校核 (26)10.1电机功率的校核 (26)10.1.1传动力矩的组成 (26)10.1.2各种力矩的计算……………………………………………….....26.10.1.3电机校核 (28)10.1.4第一道次电机功率校核举例 (28)11各孔型图及轧制图表 (30)11.11. 设计说明1.1 孔型设计概述钢坯要在所设计的孔型中轧制若干道次才能获得所要求的断面形状和尺寸,同时孔型设计还与所轧产品的性能、质量及轧机的生产能力、金属消耗、能耗、产品成本、劳动条件都直接相联,所以孔型设计是车间设计重要一环。
1.1.1 孔型设计的容孔型设计是型钢生产的工具设计。
孔型设计的全部设计和计算包括三个方面:1. 断面孔型设计根据原料和成品的断面形状和尺寸及对产品性能的要求,确定孔型系统、轧制道次和各道次的变形量,以及各道次的孔型形状和尺寸。
高速线材车间设计设计

目录任务书 ............................................................................................................... 错误!未定义书签。
摘要 ..................................................................................................................... 错误!未定义书签。
第1章绪论 (1)1.1 设计背景及意义 (1)1.1.1 国际市场 (1)1.1.2 国内市场 (2)1.1.3 中国线材行业生产的现状 (4)1.2 设计任务 (6)1.3 厂址选择 (6)1.3.1 区域优势 (6)1.3.2 交通优势 (7)1.3.3 成本优势 (7)1.3.4 政策优势 (7)第2章产品方案的确定与编制金属平衡表 (9)2.1 产品方案的确定 (9)2.2 确定金属平衡表 (10)2.2.1 确定计算产品的成品率 (10)2.2.2 金属平衡表 (10)2.3 计算产品的选择 (11)2.3.1 计算产品选择的原则 (11)2.3.2 计算产品的技术标准 (11)第3章生产工艺流程的制订 (13)3.1 制订生产工艺流程 (13)3.1.1 制订生产工艺流程的依据 (13)3.1.2 工艺流程简介 (13)第4章设备选择 (15)4.1 加热炉 (15)4.1.1 炉型选择 (15)4.1.2 炉子尺寸的确定 (15)4.2 主轧机 (16)4.2.1 轧机的组成 (16)4.2.2 轧机的主要技术参数的确定 (16)4.3 控制冷却线 (18)4.3.1 水冷装置 (18)4.3.2 精轧机后夹送辊 (18)4.3.3 吐丝机 (19)4.3.4 斯太尔摩运输机 (19)4.4 剪机 (19)4.5 盘卷收集和处理系统 (20)第5章工艺计算 (21)5.1 坯料选择 (21)5.2 坯料加热制度确定 (21)5.2.1 加热温度确定 (21)5.2.2 加热速度的确定 (22)5.2.3 加热时间的确定 (23)5.3 计算产品的孔型设计 (23)5.3.1 选择孔型系统 (24)5.3.2 确定轧制道次数 (24)5.3.3 各道次延伸系数的分配 (25)5.3.4 各孔型及轧件尺寸的确定 (26)5.4 延伸系数校核 (32)5.5 充满度的校核 (32)5.6 轧制力的计算 (33)5.6.1 各机组的温度制度 (33)5.6.2 孔型轧制力系数 (33)5.6.3 轧件的变形抗力 (35)5.6.4 轧制力的计算公式 (36)5.7 主电机传动轧辊所需力矩及功率 (37)5.7.1 传动力矩的组成 (37)5.7.2 轧制力矩的确定 (37)5.7.3 附加摩擦力矩的确定 (37)5.7.4 空转力矩的确定 (38)5.8 轧制程序表 (39)第6章轧辊及电机校核 (41)6.1 轧辊强度校核 (41)6.1.1 校核辊身强度 (41)6.1.2 辊颈强度 (42)6.1.3 辊头校核 (42)6.2 电机校核 (43)6.2.1 等效力矩计算 (44)6.2.2 电机的过热过载校核 (44)第7章设备生产能力的计算 (46)7.1 绘制轧制图表 (46)7.1.1 轧制图表 (46)7.1.2 确定纯轧制时间、间隙时间、轧制节奏 (46)7.2 轧机生产能力计算 (48)7.2.1 轧机小时生产能力 (48)7.2.2 年产量的计算 (48)7.2.3 轧机负荷率的计算 (49)第8章车间平面布置 (50)8.1 车间平面布置的原则 (50)8.1.1 车间整体平面设计内容 (50)8.2 金属流程线的确定 (51)8.2.1 设备间距的确定 (51)8.2.2 车间内仓库设施的布置 (51)8.2.3 其它设施的布置 (52)8.3 车间厂房参数 (52)第9章安全技术及环保 (53)9.1 安全技术 (53)9.2 环境保护 (53)第10章车间主要经济指标和经济效益分析 (55)10.1 车间劳动组织 (55)10.2 主要经济技术分析 (55)10.2.1 资金来源以及投资费用 (55)10.2.2 产品成本预算 (56)10.2.3 主要经济技术指标 (57)10.2.4 车间效益估算 (58)第11章专题 (59)11.1 前言 (59)11.2 飞剪的启动信号控制 (59)11.3 飞剪的速度曲线的建立 (60)11.3.1 剪速度的要求 (60)11.3.2 飞剪的速度曲线 (60)11.3.3 飞剪制动状态与位置调节状态的转换 (61)11.4 飞剪电气自动控制系统 (62)11.4.1 剪控制系统主回路 (62)11.4.2 飞剪控制程序分析 (63)11.5 常见故障与处理 (65)11.6 结束语 (65)参考文献 (66)致谢 (67)第1章绪论1.1设计背景及意义随着全球经济形势的持续回暖,全球经济逐步走出低谷,钢铁产品产能和需求都恢复增长态势。
课程设计:年产万吨的高速线材生产车间

摘要凭据设计要求拟建一个优碳年产80万吨的高速线材生产车间。
它的最高轧制速度为110m/s,产物规格为φ5.5~φ12mm,盘卷单重约2吨。
连铸坯在步进梁式加热炉中使用煤气加热,侧进侧出,加热能力为75t/h。
加热炉由微机控制,出炉温度为900℃~1050℃。
该套轧机采取全连轧无扭工艺,连铸坯为150×150mm,长约为12m,单重约为2.3t的方坯。
在13架平立-瓜代摆设的粗轧机和中轧机之后,摆设了2架预精轧机,13架精轧机。
轧后冷却通过水冷箱和一套斯太尔摩冷却运输线(120m)来完成。
该套斯太尔摩冷却运输系统采取延迟型冷却装置,可对制品轧材的最终性能控制如抗拉强度及产物的金相组织和氧化铁皮厚度进行最终控制。
盘算机系统用于控轧和控冷,无张力轧制,最佳剪切尺寸控制和缺陷检测。
要害词:高速线材;生产方案;孔型设计;校核目录第一章绪论 (1)第二章车间产物大纲和金属平衡表....................................... 错误!未定义书签。
2.1车间产物大纲............................ 错误!未定义书签。
产物方案表........................................................ 错误!未定义书签。
产物交货的技能条件................................................ 错误!未定义书签。
产物的性能........................................................ 错误!未定义书签。
产物国内国际销售应切合以下标准.................................... 错误!未定义书签。
2.2原料及其质量要求........................ 错误!未定义书签。
原料规格.......................................................... 错误!未定义书签。
80万吨高速线材生产线工程方案设计

80万吨高速线材生产线工程方案设计摘要本设计是依据鞍钢线材厂设计的年产量80 万吨的高速线材车间工艺。
典型产品为Q235、Φ6.5mm 的线材。
设计说明书包括文献综述,车间工艺设计,专题三个部分。
在综述部分叙述了线材的基本知识和当前线材生产的状况。
设计部分主要包括产品方案及工艺流程的设计及制定、生产设备的选择、工艺参数的计算及校核、年产量计算、车间平面布局设计及图纸绘制,还有技术经济指标关键词:高速线材;生产方案;孔型设计;校核;帘线钢目录任务书 .................................................................................................................. 错误!未定义书签。
摘要 ........................................................................................................................ 错误!未定义书签。
第1章绪论 (1)1.1 线材生产的基本知识 (1)1.1.1 线材的定义 (1)1.1.2 线材的种类 (1)1.1.3 线材的品种与用途 (2)1.1.4 高速线材生产特点 (6)1.2 国内外线材生产的兴起与发展 (8)1.3 国内外线材生产的现状与展望 (11)1.3.1 国外线材生产现状 (11)1.3.2 国内线材生产现状 (12)1.3.3 对我国线材发展的几点看法 (12)第2章产品大纲及金属平衡表制定 (13)2.1 产品方案的确定 (13)2.1.1 产品方案 (13)2.1.2 产品大纲 (14)2.2 确定金属平衡表 (15)2.2.1 确定计算产品的成品率 (15)2.2.2 金属平衡表 (17)2.3 计算产品的选择 (17)2.3.1 计算产品选择的原则 (18)2.3.2 计算产品的技术标准 (18)2.4 生产工艺流程的制定 (19)2.4.1 制订生产工艺流程的 (19)2.4.2 制定生产工艺流程的依据 (20)2.4.3 工艺流程简介 (20)第1章综述1.1线材生产的基本知识1.1.1线材的定义线材是断面周长很小,可以卷起来的金属材料称之为线材。
年产量65万吨高速线材车间设计(工艺设计)

第三章生产工艺流程制定3.1制定生产工艺流程合理的生产工艺流程应该是在满足产品技术条件的前提下,要尽可能低的消耗,最少的设备、最小的车间面积、最低的产品成本,并且根据车间具体的技术经济条件确定车间机械化和自动化程度,以利于产品质量和产量的不断提高和使工人具有较好的劳动条件。
3.1.1制订生产工艺流程的依据根据生产方案的要求:由于产品的产量、品种、规格及质量的不同,所采用的生产方案就不同,那么主要工序就有很大的差别。
因此生产方案是编制生产工艺流程的依据;根据产品的质量要求:为了满足产品技术条件,就要有相应的工序给予保证,因此,满足产品标准的要求是设计生产工艺流程的基础。
根据车间生产率的要求:由于车间的生产规模不同,所要求的工艺过程复杂程度也不同。
在生产同一产品情况下,生产规模越大的车间,其工艺流程也越复杂。
因此,设计时生产率的要求是设计工艺流程的出发点。
3.1.2工艺流程简介钢坯的准备:连铸坯150×150×1200mm装炉加热:将钢坯加热到奥氏体温度,以利于轧制。
高压水除鳞:坯料在加热炉加热之后,进入粗轧机组之前,需高压水除鳞,破除坯料表面的氧化铁皮和次生氧化铁皮,以免压下表面产生缺陷。
粗、中、精轧机组轧制:使轧件轧成成品的尺寸,其中,粗轧机组6架,中轧机组6架,预精轧机组4架,精轧机组10架,这条生产线上共有26架轧机。
飞剪切头尾:轧件进入每组轧机之前都要进行切头尾工作,目的是为了除去温度过低的头部以免损伤辊面,并防止轧件头部卡在机架间导卫装置中,卡断剪用于中轧机组、预精轧机组和精轧机组前,在事故状态下碎断轧件。
穿水冷却:为了降低进入精轧机组的轧件温度,在精轧机组之前设置水箱,以控制终轧温度。
吐丝成卷:轧出的线材在穿水冷却后,通过吐丝成卷形成散卷。
斯太尔摩散卷冷却:控冷线按不同的钢种和产品用途,控制其冷却速度,以得到相应的成品质量。
精整与运输:包括集卷、修整、检查、取样、捆轧、称重挂标牌,用集卷装置收集散卷,并将其挂到P-S运输线上的C形钩上,依次完成集卷、修整、检查、取样、捆轧、称重挂标牌等工序,之后卸卷入库。
- 1、下载文档前请自行甄别文档内容的完整性,平台不提供额外的编辑、内容补充、找答案等附加服务。
- 2、"仅部分预览"的文档,不可在线预览部分如存在完整性等问题,可反馈申请退款(可完整预览的文档不适用该条件!)。
- 3、如文档侵犯您的权益,请联系客服反馈,我们会尽快为您处理(人工客服工作时间:9:00-18:30)。
目录任务书 (I)摘要 .......................................................................................................................... I I 第1章绪论 (1)1.1设计背景及意义 (1)1.1.1国际市场 (1)1.1.2 国市场 (2)1.1.3 中国线材行业生产的现状 (4)1.2 设计任务 (6)1.3 厂址选择 (6)1.3.1 区域优势 (6)1.3.2 交通优势 (7)1.3.3 成本优势 (7)1.3.4 政策优势 (7)第2章产品方案的确定与编制金属平衡表 (9)2.1 产品方案的确定 (9)2.2 确定金属平衡表 (10)2.2.1 确定计算产品的成品率 (10)2.2.2 金属平衡表 (10)2.3 计算产品的选择 (11)2.3.1 计算产品选择的原则 (11)2.3.2 计算产品的技术标准 (11)第3章生产工艺流程的制订 (13)3.1 制订生产工艺流程 (13)3.1.1 制订生产工艺流程的依据 (13)3.1.2 工艺流程简介 (13)第4章设备选择 (15)4.1 加热炉 (15)4.1.1 炉型选择 (15)4.1.2 炉子尺寸的确定 (15)4.2 主轧机 (16)4.2.1 轧机的组成 (16)4.2.2 轧机的主要技术参数的确定 (16)4.3 控制冷却线 (18)4.3.1 水冷装置 (18)4.3.2 精轧机后夹送辊 (18)4.3.3 吐丝机 (19)4.3.4 斯太尔摩运输机 (19)4.4 剪机 (19)4.5 盘卷收集和处理系统 (20)第5章工艺计算 (21)5.2 坯料加热制度确定 (21)5.2.1 加热温度确定 (21)5.2.2 加热速度的确定 (22)5.2.3 加热时间的确定 (23)5.3 计算产品的孔型设计 (23)5.3.1 选择孔型系统 (24)5.3.2 确定轧制道次数 (24)5.3.3 各道次延伸系数的分配 (25)5.3.4 各孔型及轧件尺寸的确定 (26)5.4 延伸系数校核 (32)5.5 充满度的校核 (32)5.6 轧制力的计算 (33)5.6.1 各机组的温度制度 (33)5.6.2 孔型轧制力系数 (33)5.6.3 轧件的变形抗力 (35)5.6.4 轧制力的计算公式 (36)5.7 主电机传动轧辊所需力矩及功率 (37)5.7.1 传动力矩的组成 (37)5.7.2 轧制力矩的确定 (37)5.7.3 附加摩擦力矩的确定 (37)5.7.4 空转力矩的确定 (38)第6章轧辊及电机校核 (41)6.1 轧辊强度校核 (41)6.1.1 .................................................................................... 校核辊身强度416.1.2 辊颈强度 (42)6.1.3 辊头校核 (42)6.2 电机校核 (43)6.2.1 等效力矩计算 (44)6.2.2 电机的过热过载校核 (44)第7章设备生产能力的计算 (46)7.1 绘制轧制图表 (46)7.1.1 轧制图表 (46)7.1.2 确定纯轧制时间、间隙时间、轧制节奏 (46)7.2 轧机生产能力计算 (48)7.2.1 轧机小时生产能力 (48)7.2.2 年产量的计算 (48)7.2.3 轧机负荷率的计算 (49)第8章车间平面布置 (50)8.1 车间平面布置的原则 (50)8.1.1 车间整体平面设计容 (50)8.2 金属流程线的确定 (51)8.2.1 设备间距的确定 (51)8.2.2 车间仓库设施的布置 (51)8.2.3 其它设施的布置 (52)8.3 车间厂房参数 (52)第9章安全技术及环保 (53)9.1 安全技术 (53)9.2 环境保护 (53)第10章 ............................ 车间主要经济指标和经济效益分析55 10.1 ........................................................................... 车间劳动组织55 10.2 ..................................................................... 主要经济技术分析5510.2.1 ...................................................................... 资金来源以及投资费用5510.2.2 .................................................................................. 产品成本预算5610.2.3 ............................................................................ 主要经济技术指标5710.2.4 .................................................................................. 车间效益估算58第11章 ................................................................... 专题59 11.1 ........................................................................................前言59 11.2 ................................................................. 飞剪的启动信号控制59 11.3 .............................................................. 飞剪的速度曲线的建立6011.3.1 .................................................................................. 剪速度的要求6011.3.2 ............................................................................... 飞剪的速度曲线6011.3.3 ................................................... 飞剪制动状态与位置调节状态的转换6111.4 .............................................................. 飞剪电气自动控制系统6211.4.1 ............................................................................ 剪控制系统主回路6211.4.2 ............................................................................ 飞剪控制程序分析63 11.5 ........................................................................ 常见故障与处理65 11.6 .................................................................................... 结束语65参考文献 (66)致 (67)第1章绪论1.1设计背景及意义随着全球经济形势的持续回暖,全球经济逐步走出低谷,钢铁产品产能和需求都恢复增长态势。
其主要市场空间不仅来自发达国家,还来自于发展中国家的强劲需求。
1.1.1国际市场(1)美国经济。
美国商务部(Commerce Department)28日公布,2010年第四季度美国实际国生产总值(GDP)按年率计算增长3.2%,快于第三季度的2.6%,但略低于分析师3.5%的增速预期。
为去年最强劲季度增长。
这不仅确认了去年年底以来美国经济复势头已增强,也激起了今年经济增长将更为强劲的希望。
美国经济形势的好转得益于政府庞大的货币与财政刺激方案。
(2)欧元区及欧盟。
相对于美国经济的乐观期待,欧元区经济形势仍没有达到乐观的程度。
IMF预计2011年欧元区经济增长1.5%,欧盟统计局公布的预估数据显示,欧元区和欧盟2010年国生产总值均增长1.7%。
预估统计数字表明,欧元区和欧盟2010年第四季度国生产总值分别比上个季度增长0.3%和0.2%,低于2010年第三季度的增幅。
与2009年同期相比,欧元区和欧盟2010年第四季度国生产总值分别增长2%和2.1%。
(3)从近期欧洲工业生产情况看,在09年8-9月份大幅回升后,10月份工业生产均是收缩态势。
其中欧元区16国下降了0.6%,欧盟27国则下降了0.7%。
但从同比的角度看,欧元区和欧盟的工业生产均呈现出恢复的迹象,降幅明显收窄。
对比5月份。
欧元区16国和欧盟27国工业生产降幅分别收窄了6.6个百分点。
(4)日本。
日本经济增长出现持续增长趋势。
日本公布2010年一季度经济数据GDP同比增长4.9%,受国需求和出口稳步复的影响,日本连续4个季度实现正增长,经济复势头更趋明显。
遭受金融危机打击后的全球钢铁行业正在逐渐恢复生产能力,粗钢产量呈现为前低后高的增长态势。
这当然与全球经济回暖带来的需求增长有直接的关系。
但更值得关注的是,中国不再扮演全球粗钢产量增长的领军角色,因为扣除中国以外的其他国家和地区的粗钢产量增长速度已明显超过了中国。
对比08年12月份粗钢日均产量水平,全球11月份累计增长了31.0%,同期中国大陆粗钢日均产量增长了25.1%,扣除中国以外其他国家和地区粗钢产量大幅增长36.0%,粗钢生产的扩幅度超过中国10.9%。
IMF预测2011年全球经济将持续增长,但2011年全球经济增速料略低于去年的4.8%。
相比较2009年的1.4%负增长,无疑还是令人充满振奋和期待的。
美国第三季度经济增长了2.6%,为去年最强劲季度增长。
也是自2007年年底步入衰退以来的最好表现。