水位传感器说明书
KSONIK MICRO LP 超声水位传感器操作说明书

KSONIK MICRO LP Ultrasonic Level Transmitter“Loop powered” ultrasonic leveltransmitterK-TEK ProductsIntroductionThis operating instruction manual provides the following information:–Quick start guide - see page 3–Instructions on changing parameters -see page 4–Installation instructions - see page 5–Configuration guidelines - see page 6Table Of Contents1.0 Introduction (3)2.0 Quick Start for the KSONIK MICRO LP (3)3.0 Changing Parameters (5)4.0 Installation (5)5.0 Key Description (6)6.0 Configuration for KSONIK MICRO LP (6)7.0 Example - Level Measurement for KMICRO LP (8)8.0 Fault Finding (8)9.0 Terminal Connections (9)10.0 Dimensions (9)11.0 Customer Support (10)11.1 ABB RMA Form (11)12.0 Declaration of Conformity (12)13.0 Warranty (13)2 KSONIK MICRO LP Ultrasonic Leve Transmitter | Operating instruction manualThe KMICRO LP range works on the non-contact principle of ultrasonics. A pulse of energy emits from the Transducer at the speed of sound and is detected on its return. The Transmitter can distinguish the difference between the correct echo and other ambient noise. When the signal returns, the KMICRO LP measures the time period, and then knowing the speed of sound, it can accurately calculate the distance from the material to the Transducer. The Microprocessor will adjust the display and 4-20 mA output accordingly.2.0 Quick Start for the KSONIK MICRO LPInitially, the default unit of measurement (meters) must be changed to feet. Refer to page 5 for the method of changing parameters and select “ft” in the “Unit” parameter, “ENTER” it and press “RUN”.-IK MICRO LP without the aid of a complicated source code book. There are no references to any codes in KSONIK MICRO LP. The set up procedure is all menu driven.KSONIK MICRO LP Wiring ConnectionsSimply connect the regulated power supply to positive and negative terminals. A multi-meter can be placed in series with the positive supply to measure the mA output.Aim the transducer at a wall about 3 ft. away and check the display. It should read the following:If the reading is below 13.00 ft., then move the transducer closer to the wall. If the reading is above 13.00 ft., then move the transducer away from the wall. You may now proceed and check other distances.1.0 IntroductionOperating instruction manual | KSONIK MICRO LP Ultrasonic Level Transmitter 34 KSONIK MICRO LP Ultrasonic Leve Transmitter | Operating instruction manual3.0 Changing ParametersBefore any parameters can be changed, the security code must first be entered in order to gain access to the param -eters.Step 1: Simply SCROLL and the SECURITYCODE prompt will be displayed.Step 2: Then enter the code 5159 by pressing the UP and DOWN keys.Step 3: Press Enter.Code has been accepted.Code not accepted, please try again.The display will indicate that it has accepted the code by displaying “ACC” and then it will display “ED” empty distance. If you would like to carry on programming, the configuration list is on page 6 for the KSONIK MICRO LP .UpDown Enter RunScrollUpDown Enter RunOperating instruction manual | KSONIK MICRO LP Ultrasonic Level Transmitter 54.0 InstallationKMICRO LP is protected to IP65. The Transmitter is dust and waterproof so it can be mounted outside. The LCD display should not face full sunlight as this can cause the display to fail. KMICRO COMPACT LP should be fixed to a chassis plate using a plastic nut to tighten the 2-inch NPT thread.DO NOT INSTALL KMICRO LP in areas of high vibration as this may cause failure.DO NOT INSTALL KMICRO LP in the close vicinity of electrical cable, SCR’s or variable speed drives.The installation of KMICRO LP is the most important section of this manual and has been driven up into 6 sub sections.1. KMICRO LP must be fitted at least 1.64 ft / 0.50 mabove the highest point of level.2. Always use the plastic nut . KMICRO LP must be fittedto a rigid support. Use mild steel or a suitable plastic. Do not use stainless steel as this can cause ringing.3. KMICRO LP must be perpendicular to the material itis measuring with a clear line of sight and must not beabove beams or filling points.INCORRECTCORRECTThis is INCORRECT as the filling point is obscuring the KSONIK’sline of sight This is CORRECT as the filling point is NOT obscuring the KSONIK’sline of sightTransducer perpendicular to liquid level.6 KSONIK MICRO LP Ultrasonic Leve Transmitter | Operating instruction manual4. If KMICRO LP is in a coned vessel, it must be positioned overthe cone. This ensures that the Transducer receives the true echo and not one from the sides of the cone.5. When a standpipe is being used it must be as wide as possible; i.e. the pipe diameter must be at least double its height, preferably made ofplastic. The base MUST have a 45° chamber to reduce the echo size from the bottom of the standpipe. No welding should be present on the inside of the pipe as this causes false echoes.6. If any large electrical equipment is installed in the vicinity, then earthedsteel conduit must be used.5.0 Key DescriptionKMICRO LP is “user friendly” having only 5 keys and a menu driven display. The keys are listed below with their ap-propriate functions.This is used to initially access the programming and then to run through the various commands.This key is used to INCREASE the value in the various commands.This key is used to INCREASE the value in the various commands.When the value has been selected it can be accepted by pressing the ENTER key.When programming is complete, press RUN to return KSONIK MICRO back to the run mode.SECURITY CODETo advance to the programming mode, the correct security code must be entered. The factory default code is 5159.6.0Configuration for KSONIK MICRO LPSECURITY CODESecurity code to advance to programming.DEFAULT 5159EMPTY DISTANCEThis is the distance from the face of the transducer to the bottom of the tank.DEFAULT 16.42 ft.SPANThis figure is the measuring range of the instrument i.e. distance from the bottom of the tank to the highest point being measured. Remember, the material must not approach within 16.4 ft. of the transducer face.DEFAULT 15.42 ft.RATE OF CHANGEThis is used to set up the rate of change of the level output. Increase the number if the level moves faster than 3.28 ft. / min and decrease it if a more stable output is required.DEFAULT 3.28 ft. / minLOSSIf a loss of echo condition is reached then the 4-20 mA output will follow the configured settings 3,6 mA (LO), 21 mA (HI), or hold the last recognized echo.DEFAULT HOLDLOSS OF ECHO DELAY TIMEThis sets up the time period from the time the KSONIK MICRO does not receive a good echo to the time it goes into the loss of echo routine.DEFAULT 300 SECFACTORY RESETThis prompt will reset all the values entered back to the factory setting except the password. Please write down all set-tings before using this function.DEFAULT NOZERO ADJUSTShould there be a small zero offset in the measurement this function can correct it up to -1.97 in. / -50 mm and +1.97 in. / 50 mm.DEFAULT 0 INOperating instruction manual | KSONIK MICRO LP Ultrasonic Level Transmitter 78 KSONIK MICRO LP Ultrasonic Leve Transmitter | Operating instruction manualThe KSONIK MICRO LP is monitoring the level in an open tank and sending back to the control room a 4-20mA signal. The tank is 8.20 ft / 2.50 m high and the transducer is mounted 1.64 ft / 0.50 m above the tank. The actual level is at 6.56 ft / 2.00 m which would make the output 16.8 mA.Below is what KSONIK MICRO LP will display on the above application. The analog output should be approximately 16.8 mA.7.0Example - Level Measurement for KMICRO LPSECURITY CODE 5159EMPTY DISTANCE (ED)9.84 FT / 3.00 M SPAN 8.20 FT / 2.50 M LOSSHOLDThere are three categories of possible faults. The malfunction of the instrument, loss of echo and wrong reading. The biggest problem is to identify the malfunction. If the instrument is not working satisfactorily then remove the transmitter to the workshop. Connect the power and aim the KSONIK MICRO to a wall about 6.00 ft away, making sure that it is perpendicular to the wall. Now reset the instrument by the factory reset prompt. Change the unit of measurement back to feet. The Instrument should now read about 9.85. If it does not read the above then there is a malfunction with the instrument and it should be returned for repair. If the above works and it still does not work in the field then there are many possible problems. Please check below for possibilities.Loss of EchoCheck that the KSONIK MICRO is not being used on a solid or agitated surface, as agitated surfaces and solids do not reflect as much signal as flat surfaces. Aim the Transducer straight down. Check if the Transducer face is dirty.Wrong reading, always reading close to the transducer.Do not reduce the blanking distance below 1.64 ft / 0.50 m unless consultation has been made with ABB. Electrical noise can cause this error. Remove noise.Wrong reading, anywhere in tank.Check to see if there is a reflection from the wall. Please note that a piece of wire across a tank can be a big enough echo to be accepted. Are the parameters correct? Reset to factory default and check that KSONIK MICRO reads cor-rectly. If the factory settings are OK then your parameters need changing. Re-check them with a tape measure.8.0 Fault FindingOperating instruction manual | KSONIK MICRO LP Ultrasonic Level Transmitter 99.0 Terminal ConnectionsConnections - KSONIK MICRO LPPower Supply and Output- Negative 4-20 mA and power+ Positive 4-20 mA and power10.0Dimensions10 KSONIK MICRO LP Ultrasonic Leve Transmitter | Operating instruction manual11.0 Customer SupportEmail:****************************.com Website: /levelABBPhon e: (86)21 6105 6666Fax: (86)21 6105 6992No.5, Lane 369, Chuangye Road, KangQiao Town, Pudong District,Shanghai, 201319, P. R. China11.1ABB RMA Form*** IMPORTANT CUSTOMER NOTICE: PLEASE READ PRIOR TO RETURNING PRODUCTS TO ABB***Operating instruction manual | KSONIK MICRO LP Ultrasonic Level Transmitter 1112.0 Declaration of ConformityThe KMICRO COMPACT LP range complies with conformity in accordance with the following tests. Electromagnetic CompatibilityEN801-2,3,4,Susceptibility:EN50082-1ENV50204EN50082-2ENV50140ENV50141EN61000-4-2EN61000-4-4EN55011Emission: EN50081-2EN50081-1EN55022 EN60555-2,3 BSEN61010-1Safety:CE Conformity DeclarationThe KMICRO LP is in accordance with EN50081-2 1993 and EN50082-2 1995.Prairieville, Louisiana December 20, 2002Eric FauveauEric Fauveau, V.P. R & DABB12 KSONIK MICRO LP Ultrasonic Leve Transmitter | Operating instruction manual13.0 Warranty5 YEAR WARRANTY FOR:KM26 Magnetic Liquid Level Gauges; MagWave Dual Chamber System; LS Series Mechanical Level Switches (LS500, LS550, LS600, LS700, LS800 & LS900); EC External Chambers, STW Stilling Wells and ST95 Seal Pots.3 YEAR WARRANTY FOR:KCAP300 & KCAP400 capacitance switches. BETA Pressure and Temperature Switches have a limited factory guarantee, excluding wetted parts & consumables.2 YEAR WARRANTY FOR:AT100, AT100S and AT200 series transmitters; RS80 and RS85 liquid vibrating fork switches; RLT100 and RLT200 reed switch level transmitters; TX, TS, TQ, IX and IM thermal dispersion switches; IR10 and PP10 External Relays; MT2000, MT5000, MT5100 and MT5200 radar level transmitters; RI100 Repeat Indicators; KP paddle switches; A02, A75 & A77 RF capacitance level switches and A38 RF capacitance level transmitters; Buoyancy Level Switches (MS50, MS10, MS8D & MS8F); Magnetic Level Switches (MS30, MS40, MS41, PS35 & PS45).1 YEAR WARRANTY FOR:KM50 gauging device; AT500 and AT600 series transmitters; LaserMeter and SureShot series laser transmitters; LPM200 digital indicator; DPM100 digital indicators; APM100 analog indicators; KVIEW series digital indicators and controllers; SF50 and SF60 vibrating fork switches, KB Electro-Mechanical Continuous Measuring Devices, KSONIK ultrasonic level switches, transmitters & transducers, ChuteMaster Microwave Transmitter / Receiver and TiltMaster Switches.SPECIAL WARRANTY CONSIDERATIONS:ABB does not honor OEM warranties for items not manufactured by ABB (i.e. Palm Pilots). These claims should be handled directly with the OEM.ABB will repair or replace, at ABB’s election, defective items which are returned to ABB by the original purchaser within the period-fects in materials or workmanship which arose only under normal use and service and which were not the result of either alterations, misuse, abuse, improper or inadequate adjustments, applications or servicing of the product. ABB’s warranty does not include onsite repair or services. Field service rates can be supplied on request.If a product is believed to be defective, the original purchaser shall notify ABB and request a Returned Material Authorization be-fore returning the material to ABB, with transportation prepaid by the purchaser. (To expedite all returns/repairs from outside of the UnitedStates,consultABB’scustomerserviceteam(********************)todetermineanoptimalsolutionforshippingmethod and turnaround time.) The product, with repaired or replaced parts, shall be returned to the purchaser at any point in the world with transportation prepaid by ABB for best-way transportation only. ABB is not responsible for expedited shipping charges. If the product is shipped to ABB freight collect, then it will be returned to the customer freight collect.If inspection by ABB does not disclose any defects in material or workmanship, ABB’s normal charges for repair and shipment shall apply (minimum 250.00 USD).compatibility of the materials for the application.THE FOREGOING WARRANTY IS ABB’S SOLE WARRANTY AND ALL OTHER WARRANTIES EXPRESSED, IMPLIED, OR STAT-UTORY, INCLUDING ANY IMPLIED WARRANTY OF MERCHANTABILITY OF FITNESS FOR A PARTICULAR PURPOSE, ARE EXCLUDED AND NEGATED TO THE MAXIMUM EXTENT PERMITTED BY LAW. NO PERSON OR REPRESENTATIVE IS AU-THORIZED TO EXTEND ANY OTHER WARRANTY OR CREATE FOR ABB ANY OTHER LIABILITY IN CONNECTION WITH THE SALE OF ABB’S PRODUCTS. THE REMEDIES SET FORTH IN THIS WARRANTY ARE EXCLUSIVE OF ALL OTHER REMEDIES AGAINST ABB. ABB SHALL NOT BE LIABLE FOR ANY CONSEQUENTIAL, INCIDENTAL, OR SPECIAL DAMAGES OF ANY KIND. ABB’S SOLE OBLIGATION SHALL BE TO REPAIR OR REPLACE PARTS (FOUND TO BE DEFECTIVE IN MATERIALS OR WORKMANSHIP) WHICH ARE RETURNED BY THE PURCHASER TO ABB.14.0 Customer SupportABBNo.5, Lane 369, Chuangye Road,KangQiao Town, Pudong District,Shanghai, 201319, P. R. ChinaTel: +86 21 6105 6666Fax: +86 21 6105 6992/levelOperating instruction manual | KSONIK MICRO LP Ultrasonic Level Transmitter 1314 KSONIK MICRO LP Ultrasonic Leve Transmitter | Operating instruction manualOperating instruction manual | KSONIK MICRO LP Ultrasonic Level Transmitter 15O I /K M I C R O L P -E N R e v . B 05.2013, C o p y r i g h t ©2013 A B BContact usNot eWe reserve th e right to make techn ical chang es or modif y th e cont ents of th is docum ent without pr ior notice. With regard to pu rchase orders, th e agreed part icula rs shal l prevail. ABB does not accept any responsibil it y whats oever for potent ial errors or possible lack of inf ormatio n in th is document.We reserve all rights in this do cume nt and in th e subject matter and ill ustr ations cont ained therein. An y reprodu ctio n, disclo sure to th ird parti es or ut iliz atio n of its cont ents - in wh ol e or in parts – i s forb idden without pr ior writt en consent of ABB.Copyri ght© 2013 ABB Al l rights reservedABB Engineering (Shanghai) Ltd.Phone: (86)21 6105 6666Fax: (86)21 6105 6992/levelNo.5, Lane 369, Chuangye Road, KangQiao Town, Pudong District,Shanghai, 201319, P. R. China。
海康威视水位传感器说明书

1. CHOOSE MODEThe standard modes available are selected by the jumpers A,B,C,D.•The snooze alarm means that the buzzer will be silenced onlytemporarily: after 30 minutes it will sound again and so on.2. POWER•The unit draws 110VAC power from the prongs of the piggyback plug. It isconverted to 12V by the waterproof power converter. All logic circuits includingthe cable connecting the two pipes are 12VDC.•The 15A dry contact relay switches power to the back (receptacle) side of the piggyback plug to turn on devices like pumps.•*********************************************************fieldreplaceable. For motors that have large current surges another larger relay isnecessary. The power cord is 14 AWG designed for 15A@110VAC service.3.OPERATIONSET DESIRED LEVEL POINTS•Loosen the thumbscrews to slide the tubes to desired level. Extra cable is stored in the long float pipe which can be pulled out by loosening the cord grip. When finished, tighten the thumbscrews to lock.PUSH BUTTON•During an alarm condition, the push button silences the buzzer whilethe LED continues to flash until the level is corrected.•When there is no alarm, (level is between the floats) the buttonallows manual control of the relay and testing of the buzzer. (pushingonce will turn the relay on, a second push turns it off, etc.) When thelevel reaches one of the floats the controller will resume correctlevel control automatically.EMERGENCY ALARMS•There is a third float switch that causes an alarm if activated. Inadditinon, tt also controls the relay to prevent overflow. For example,in a tank-filling application, if the high level float fails, the emergencyfloat switch would switch the relay in addition to sounding an alarm.•If the high and low float switches are in an unatural state (like thehigh floating high and the low is still low) an alarm is given.Sep 2, 2015LEVEL CONTROLLEREngineering2257 County Road 4, Building 3, Stanley, NY 14561 585-301-0970 LOW LEVEL FLOATINSIDE PIPEJUMPER JUMPER ON PINSJUMPER OFF PINS A NOT USEDNOT USED (FOR CUSTOM PROGRAMS)B 30 MIN. SNOOZE ALARMNO SNOOZE ALARM C TANK FILLINGTANK EMPTYTING DCONTINUOUS BUZZER INTERMITTENT BUZZER OUTPUT (WIRELESS)INSIDE THE ENCLOSUREEMERGENCY FLOATHIGH LEVEL FLOATGUARD REMOVED。
水位仪说明书
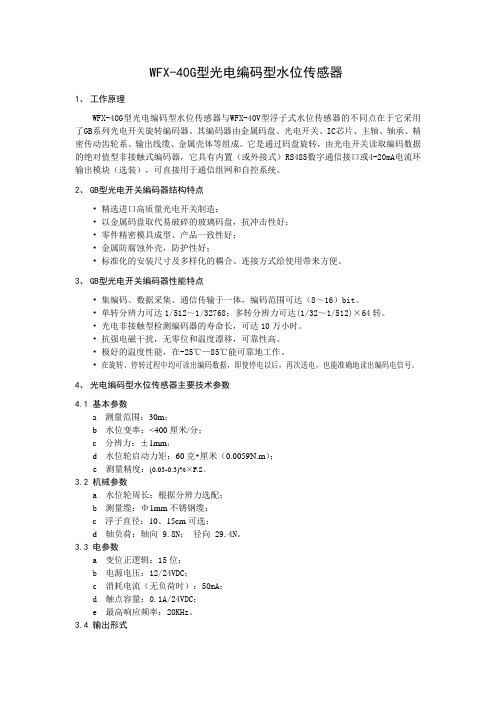
WFX-40G型光电编码型水位传感器1、工作原理WFX-40G型光电编码型水位传感器与WFX-40V型浮子式水位传感器的不同点在于它采用了GB系列光电开关旋转编码器。
其编码器由金属码盘、光电开关、IC芯片、主轴、轴承、精密传动齿轮系、输出线缆、金属壳体等组成。
它是通过码盘旋转,由光电开关读取编码数据的绝对值型非接触式编码器,它具有内置(或外接式)RS485数字通信接口或4-20mA电流环输出模块(选装),可直接用于通信组网和自控系统。
2、GB型光电开关编码器结构特点•精选进口高质量光电开关制造;•以金属码盘取代易破碎的玻璃码盘,抗冲击性好;•零件精密模具成型、产品一致性好;•金属防腐蚀外壳,防护性好;•标准化的安装尺寸及多样化的耦合、连接方式给使用带来方便。
3、GB型光电开关编码器性能特点•集编码、数据采集、通信传输于一体,编码范围可达(8~16)bit。
•单转分辨力可达1/512~1/32768;多转分辨力可达(1/32~1/512)×64转。
•光电非接触型检测编码器的寿命长,可达10万小时。
•抗强电磁干扰,无零位和温度漂移,可靠性高。
•极好的温度性能,在-25℃—85℃能可靠地工作。
•在旋转、停转过程中均可读出编码数据,即使停电以后,再次送电,也能准确地读出编码电信号。
4、光电编码型水位传感器主要技术参数4.1 基本参数a 测量范围:30m;b 水位变率:<400厘米/分;c 分辨力:±1mm;d 水位轮启动力矩:60克•厘米(0.0059N.m);e 测量精度:(0.03-0.3)%×F.S。
3.2 机械参数a 水位轮周长:根据分辨力选配;b 测量缆:Φ1mm不锈钢缆;c 浮子直径:10、15cm可选;d 轴负荷:轴向 9.8N;径向 29.4N。
3.3 电参数a 变位正逻辑:15位;b 电源电压:12/24VDC;c 消耗电流(无负荷时):50mA;d 触点容量:0.1A/24VDC;e 最高响应频率:20KHz。
VEGAPULS C 21 雷达水位传感器说明书

Specification sheetVEGAPULS C 21T wo-wire 4 … 20 mA/HARTRadar sensor for continuous level measurementApplication areaThe VEGAPULS C 21 is the ideal radar sensor for non-contact level measurement with high accuracy requirements in all standard applica-tions where a high degree of protection is required.It is particularly suitable for level measurement in water treatment, in pumping stations and rain overflow basins, for flow measurement in open channels, for level monitoring and for many other industrial areas.The sensor is suitable both for measuring liquids and for use on small bulk solids silos or bulk solids containers.Y our benefit• Maintenance-free operation due to non-contact 80 GHz radar tech-nology• Exact measurement results independent of medium properties and process conditions• High accuracy and universal measuring range. Maintenance-free operation due to non-contact measuring principle FunctionThe sensor emits a continuous radar signal through the antenna. The emitted signal is reflected by the medium and received as an echo by the antenna.The frequency difference between the emitted and received signal is proportional to the distance and depends on the filling height. The determined filling height is converted into a respective output signal and output as measured value.T echnical data Measuring range up to 15 m (49.21 ft)Deviation ≤ 2 mm Beam angle8°Measuring frequency W-band (80 GHz technology)Output signal 4 … 20 mA/HARTProcess fittingThread G1½, 1½ NPT , R1½Mounting connection Thread G1, 1 NPT , R1Process pressure -1 … +3 bar (-100 … +300 kPa/-14.5 … +43.51 psig)Process temperature -40 … +80 °C (-40 … +176 °F)Ambient temperature -40 … +80 °C (-40 … +176 °F)Bluetooth standard Bluetooth 5.0Effective range typ. 25 m (82 ft)Operating voltage 12 … 35 V DCProtection ratingIP66/IP68 (3 bar, 24 h) acc. to IEC 60529, T ype 4X/6P acc. to UL 50MaterialsThe wetted parts of the instrument are made of PVDF . The process seal is made of FKM. The connection cable is PUR insulated.A complete overview of the available materials and seals can be found on our homepage under " Products " and " Configure & Order ". Housing versionsThe housing is optimized for applications in the water/waste water industry and manufactured of PVDF . Due to the encapsulated cable gland, protection rating IP66/IP68 (3 bar) is achieved.Electronics versionsThe instruments are available in different electronics versions. Apart from the two-wire electronics with 4 … 20 mA/HART , two digital ver-sions with SDI-12 and Modbus/Levelmaster protocol are possible.ApprovalsWorldwide approvals are available for VEGA instruments, e.g. for use in hazardous areas, on ships or in hygienic applications.The technical data in the respective safety instructions are valid for ap-proved instruments (e.g. with Ex approval). In some cases, these data can differ from the data listed herein.Y ou can find detailed information on the existing approvals with the ap -propriate product on our homepage.AdjustmentAdjustment via the signal cableThe adjustment of the instrument is carried out via the interface adapterVEGACONNECT and a PC with the adjustment software PACT wareand corresponding DTM.Wireless adjustment via BluetoothThe Bluetooth version of the device enables wireless connection tosmartphones/tablets (iOS/Android) or Windows PCs.Wireless connection to standard operating devicesOperation is via a free app from the " Apple App Store", the " Goog-le Play Store" or the " Baidu Store". Alternatively, adjustment can alsobe carried out via PACT ware/DTM and a Windows PC.Adjustment via PACT ware or appAdjustment via remote systemsFurther adjustment options are possible via a HART Communicator aswell as manufacturer-specific programs such as AMS™ or PDM.Electrical connection123Wire assignment in permanently connected connection cable1Brown (+) to voltage supply or to the processing system2Blue (-) to voltage supply or to the processing system3ShieldingY ou can find details on electrical connection in the instrument operatinginstructions at /downloads.DimensionsDimensions VEGAPULS C 211Thread G1½2Thread 1½ NPT3Thread R1½Mounting accessoriesFor the VEGAPULS C 21 the suitable mounting accessories for ceilingor wall mounting is available.Example mounting strap - wall mounting with adjustable sensor holderY ou can find further information on the mounting accessory on ourhomepage.InformationY ou can find further information on the VEGA product line on our home-page.In the download section on our homepage you'll find operatinginstructions, product information, brochures, approval documents,instrument drawings and much, much more.Software accessories such as the current device software and the ap-propriate operating software are also available there.Instrument selectionOn our homepage under " Products" you can select the suitable meas-uring principle and instrument for your application.There you will also find detailed information on the available deviceversions.ContactY ou can find your personal contact person at VEGA on our homepageunder " Contact".。
LVLK500型号的地下水水位传感器说明书
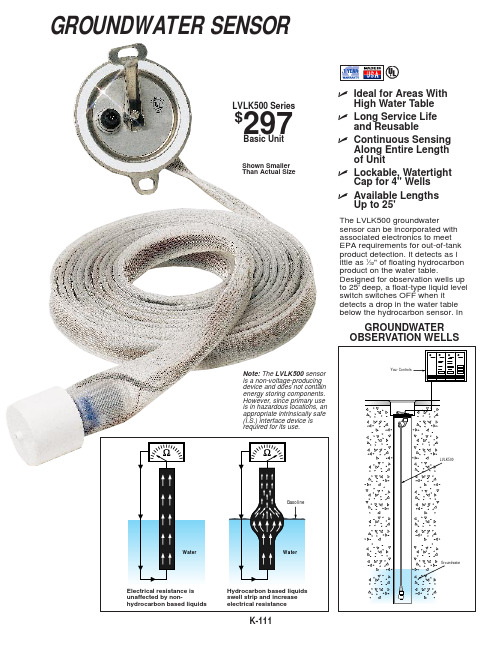
GROUNDWATER SENSORߜIdeal for Areas WithHigh Water TableߜLong Service Lifeand ReusableߜContinuous SensingAlong Entire Lengthof UnitߜLockable, WatertightCap for 4" WellsߜAvailable LengthsUp to 25'The LVLK500 groundwatersensor can be incorporated withassociated electronics to meetEPA requirements for out-of-tankproduct detection. It detects as little as 1⁄32" of floating hydrocarbonproduct on the water table.Designed for observation wells upto 25' deep, a float-type liquid levelswitch switches OFF when itdetects a drop in the water tablebelow the hydrocarbon sensor. InGROUNDWATEROBSERVATION WELLS Shown SmallerThan Actual SizeLVLK500 Series$297Basic UnitNote: The LVLK500sensoris a non-voltage-producingdevice and does not containenergy storing components.However, since primary useis in hazardous locations, anappropriate intrinsically safe(I.S.) interface device isrequired for its use.K-111K-112SPECIFICATIONSWetted Materials:PVC, Polyester, Polysulfone,Polypropylene, Nitrile, Epoxy Operating Temperature:-28.9 to 65.5°C (-20 to 150°F)Polymer Base Resistance:0.8 to 3.0 k Ω/Ft.Approvals:UL for Class I, Group D,Hazardous Locations When Powered by a SBG22445 Intrinsically Safe (I.S.) Relay.Federal register Vol. 53 No 185, rules and regulations.3.Designed for 4' schedule 40 PVC (per ASTM D 1785-64T) with an inside diameter of 3.980" to4.026"Comes with complete operator’s manual.Ordering Example:LVLK503groundwater sensor with 20 ft. sensor length, $416.addition, a polymer strip is incorporated into theLVLK500 to also indicate the presence of hydrocarbons.The LVLK500 responds to gasoline within ten minutes.Response time for other hydrocarbons, the C 5to C 16range, takes longer. For example, response time for diesel is up to one hour. (Heavier hydrocarbons can take several hours.)A watertight cap prevents spilled fuel from entering the well.The entire unit is easily removed for periodic inspection.If the probe comes in contact with hydrocarbon, simply allow it to air out and reuse. These units arerecommended for installation in non-contaminated sites only; they are not designed for remediation applications.To detect liquid hydrocarbon, LVLK500 well monitoring sensors incorporate an innovative polymer strip that continuously conducts electricity when voltage is applied. Extending longitudinally within the unit’sprotective braiding, the polymer strip physically swells on contact with liquid hydrocarbons anywhere along its length. The swelling causes a dramatic increase in the electrical resistance of the polymer, and may be used as a switch when incorporated with associated system electronics. When allowed to recover, outside the well,the polymer reverts to its normal conductive state for reuse. In absence of hydrocarbons, the polymer strip has a base resistance of 0.8 to 3.0 k Ω/ft.WIRING DIAGRAMCANADA www.omega.ca Laval(Quebec) 1-800-TC-OMEGA UNITED KINGDOM www. Manchester, England0800-488-488GERMANY www.omega.deDeckenpfronn, Germany************FRANCE www.omega.frGuyancourt, France088-466-342BENELUX www.omega.nl Amstelveen, NL 0800-099-33-44UNITED STATES 1-800-TC-OMEGA Stamford, CT.CZECH REPUBLIC www.omegaeng.cz Karviná, Czech Republic596-311-899TemperatureCalibrators, Connectors, General Test and MeasurementInstruments, Glass Bulb Thermometers, Handheld Instruments for Temperature Measurement, Ice Point References,Indicating Labels, Crayons, Cements and Lacquers, Infrared Temperature Measurement Instruments, Recorders Relative Humidity Measurement Instruments, RTD Probes, Elements and Assemblies, Temperature & Process Meters, Timers and Counters, Temperature and Process Controllers and Power Switching Devices, Thermistor Elements, Probes andAssemblies,Thermocouples Thermowells and Head and Well Assemblies, Transmitters, WirePressure, Strain and ForceDisplacement Transducers, Dynamic Measurement Force Sensors, Instrumentation for Pressure and Strain Measurements, Load Cells, Pressure Gauges, PressureReference Section, Pressure Switches, Pressure Transducers, Proximity Transducers, Regulators,Strain Gages, Torque Transducers, ValvespH and ConductivityConductivity Instrumentation, Dissolved OxygenInstrumentation, Environmental Instrumentation, pH Electrodes and Instruments, Water and Soil Analysis InstrumentationHeatersBand Heaters, Cartridge Heaters, Circulation Heaters, Comfort Heaters, Controllers, Meters and SwitchingDevices, Flexible Heaters, General Test and Measurement Instruments, Heater Hook-up Wire, Heating Cable Systems, Immersion Heaters, Process Air and Duct, Heaters, Radiant Heaters, Strip Heaters, Tubular HeatersFlow and LevelAir Velocity Indicators, Doppler Flowmeters, LevelMeasurement, Magnetic Flowmeters, Mass Flowmeters,Pitot Tubes, Pumps, Rotameters, Turbine and Paddle Wheel Flowmeters, Ultrasonic Flowmeters, Valves, Variable Area Flowmeters, Vortex Shedding FlowmetersData AcquisitionAuto-Dialers and Alarm Monitoring Systems, Communication Products and Converters, Data Acquisition and Analysis Software, Data LoggersPlug-in Cards, Signal Conditioners, USB, RS232, RS485 and Parallel Port Data Acquisition Systems, Wireless Transmitters and Receivers。
SOR Inc. T21点水位传感器说明书
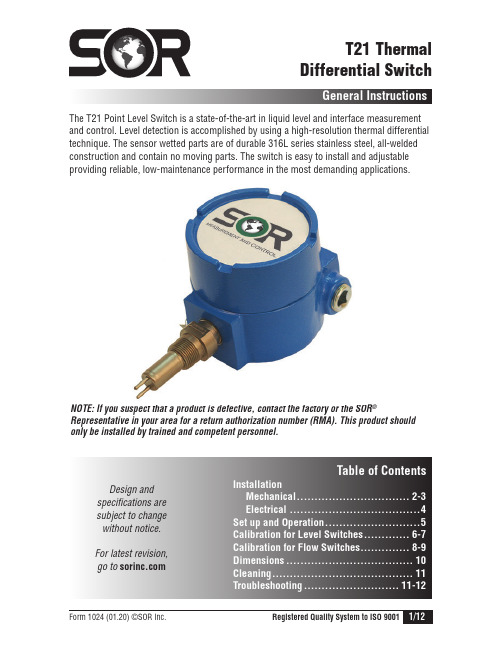
The T21 Point Level Switch is a state-of-the-art in liquid level and interface measurement and control. Level detection is accomplished by using a high-resolution thermal differential technique. The sensor wetted parts are of durable 316L series stainless steel, all-welded construction and contain no moving parts. The switch is easy to install and adjustable providing reliable, low-maintenance performance in the most demanding applications. T21 Thermal Differential SwitchTable of ContentsInstallationMechanical ................................2-3 Electrical .....................................4Set up and Operation ...........................5Calibration for Level Switches .............6-7Calibration for Flow Switches ..............8-9Dimensions ....................................10Cleaning ........................................11Troubleshooting ...........................11-12Design and specifications are subject to change without notice. For latest revision, go to NOTE: If you suspect that a product is defective, contact the factory or the SOR ®Representative in your area for a return authorization number (RMA). This product shouldonly be installed by trained and competent personnel.able, low maintenance performance in the most demanding apt th t d t i d f ti t t th f t th SORThe T21 has a 3/4-inch MNPT mount (standard), designed for easy installation through a threaded port.Conduit is recommended for all wiring to the switch.Due to the pipe thread mounting, it may be necessary to make a trial fit, addor remove teflon tape or other pipe thread sealant and reinstall to achieve a satisfactory seal with the sensor properly oriented.Proper orientation is marked on the switch body for reference.It is generally recommended that the sensor tips be located at 1/4 of the pipe’sinside diameter (I.D.) assuming pipe is full. (See )Level ApplicationThe switch body MUST be oriented with the two sensor tips aligned paralled to theUse a 1-1/8”, open-end wrench to tighten at the HEX flats of the MNPT of a standard switch. Do not use the instrument head to tighten the switch to the mounting port. Rotation of the instrument head with respect to the sensor body may cause internal wiring damage.For level and flow applications the material you are monitoring MUST contact the two sensor tips at the same time .*Sensor LengthUnit can be mounted above or below pipe. Mounting on top of pipe is displayed above.1/4 of pipe I.D. (preferred insertion assuming pipe Thread *Sensor Length = Nozzle/Coupling length+ Pipe wall thickness+ 25% of pipe I.D. - Thread engagementFlowe 1/4 of pip a insertion a p p is full)Engagementn Remove the instrument enclosure lid by unscrewing in a counterclockwise direction. o Loosen the two, board-retaining captured screws.p Remove the printed circuit board by grasping the transformer on the center of the board and, while rocking gently back and forth, pull firmly outward.q Connect power and alarm relay wiring to Terminal Block TBB as shown in.r Reinstall the switch electronics and tighten the retention screws.NOTE: Connections to sensors are factory installed and should not be disconnected in the field. NOTE: For 24 VDC operation (factory prepared), connect +24 VDC to TBB7 and 24 VDC return to TBB8. For 115 VAC or 230 VAC operation, there is no polarity.NOTE: Connect ground wire to the ground screw located in back of instrument enclosure. A ground wire must be attached to the ground screw located inside and on the back of instrument head for proper operation.n Remove the instrument head cover. Turn counterclockwise to expose the electronics.o Turn on power at its source.p Observe that either the red or green LED illuminates.q If neither lamp illuminates, refer to the troubleshootIng section.L.E.D. and Relay Status Logic (Fail-Safe)The L.E.D.s (L1-Red and L2-Green) are an indication of the sensor status (dry or wet) and are not affected by the position of the fail-safe jumper J-2. The fail-safe jumper J-2 changes the relay activation status allowing the user to select the fail-safe, power-off condition most appropriate to the application. Refer to and , showing the logic conditions between the sensors, L.E.D. lights, relay coil and contacts for each position of the fail-safe jumper J-2.Pre-Operational CheckIf the switch is installed and product level is below sensor level, or there is no flow, use the following procedure to verify preliminary operation.The switch comes configured from the factory with thefollowing operation with the J-2 jumper in the B position. (Seeg, page 7)Alternate Operation (Field Selectable), page 7)Red LEDThe switch comes configured from the factory with the following operation with the J-2 jumper in the B position. (See, page 9)Flow Sensor StatusFor optimum operation, calibration must be accomplished at actual process temperature and pressure conditions. Using as a location guide, adjust the system as follows:n Remove the instrument enclosure lid by turning it counterclockwise.o Apply power to the T21. Allow 5 minutes for the T21 to warm up. Verify J1 jumper is in the level position (Factory Default).p Ensure that the tank liquid level is below the probe sensor tips and the tips are dry.q Set the trip adjust potentiometer to zero fully counterclockwise (ccw).r Adjust the dry adjust pot so that the red LED just illuminates. This is a 25-turn pot. If the green LED is on, turn the pot counterclockwise (ccw). If Red LED is on, turn the pot clockwise (cw).s Toggle the dry adjust pot back and forth until the switching point is well defined.Leave the red LED illuminated. To ensure best definition/performance, waitapproximately 30 seconds between toggles.t Raise the level of the liquid to be detected until the probe/sensor tips are submerged and wet (covered).u Set the trip adjust pot to 100 (fully clockwise).v Adjust the wet adjust pot so that the green LED just does illuminate. This is a 25-turn pot. If the green LED is on, turn the pot clockwise. If the red LED is on,turn the pot counterclockwisew Toggle the set adjust pot back and forth until the switching point is well defined.Leave the green LED illuminated. To ensure best definition/performance, waitapproximately 30 seconds between toggles.Adjust the trip adjust pot to 80 and the calibration is complete.Trip AdjustDryp tor wsPC Board Retention Screw (2)J1quPosition BPostion AHigh Flow/LevelLow FlowJ1NOTE: This adjustment may be done for tripping points between 10% and 90% of the span from no flow to max flow.Usingas a location guide, adjust the system as follows:n Remove instrument enclosure lid by turning it counterclockwise.o Apply power to the T21. Allow 5-minute warm-up. Verify J1 jumper is in low flow setting ifair/gas flow rate is approximately 20 f/s and below (factory default). For liquid or high air/gas flow rates, the jumper should be in high flow/level position.p Ensure that the pipeline is filled with fluid and at no or minimum flow.q Set trip adjust potentiometer to zero fully counterclockwise (ccw).r Adjust the no-flow pot so that red LED just illuminates. This is a 25-turn pot. If green LED ison, turn pot counterclockwise (ccw). If the red LED is on, turn the pot clockwise (cw).s Toggle no-flow pot back and forth until the switching point is well defined. Leave red LED illumi-nated. To ensure best definition/performance, wait approximately 30 seconds between toggles.t Adjust liquid or gas flow to maximum velocity. Ensure that flow is homogenous, constant and free of bubbles if a liquid.u Set trip adjust pot to 100 (fully clockwise).v Adjust the full-flow pot so the green LED just illuminates. This is a 25-turn pot. If green LEDis on, turn pot clockwise. If red LED is on, turn the pot counterclockwise.w Toggle full-flow pot back and forth until switching point is well defined. Leave green LED illuminated.To ensure best definition/performance, wait approximately 30 seconds between toggles. If the switch is to be used for flow - no flow, set the trip adjust pot to 50 and go to step 14. A more exact flow rate setting may be achieved by establishing flow at a desired rate with a separate flow meter and proceeding to step 13, to establish trip point.Adjust the trip adjust pot to obtain a trip as exhibited by a LED illumination. If a trip on decreasing flow is desired, set for red LED illumination. If a trip on increasing flow isdesired, set for green LED illumination.Verify the switch will reset by returning actual product flow to maximum or minimum flow rates.100Trip AdjustSpanZerop torv wsFuseF1J2PC Board Retention Screw (2)J1quHigh Flow/LevelLow FlowJ1NOTE: For use as Flow Switch1. Insertion Length should be approximately 1/4 Pipe I.D.2. The unit should be installed on a straight pipe run with at least 10 pipe diameters upstream and 5 pipe diameters downstream.J2Position BPostion AL1 Red “ON” for Dry/No FlowL2 Green “ON” for Wet/ Full FlowThe probe may be cleaned by soaking, spraying solvents or detergent and water onto the sensor tubes, or by ultrasonic cleaning.Lime deposits can be safely removed by soaking in 20% hydrochloric acid. Warming to 150°F is permissible to speed this process.For unusual cleaning problems, contact the SOR factory to determine the exact materials of construction and chemical compatibility before using strong acids or unusual cleansers. Do not sandblast or scour the sensing probes with abrasive cleaners.The sensing probes could be damaged by abrasives.General InformationEach unit is different. Settings may not be identical from unit to unitMoving the trip adjust pot closer to 100 produces- Slower “On” response- Faster “Off” responseSet span at maximum possible flow rate (as far above the span setting as possible) Once again, the catalog J1 jumper settings are a starting point onlyWhat do I do if...... my zero or span is shifiting during calibration?The probes have likely not warmed up sufficiently. Apply power, place the probes in the zero state process, and wait for 5 minutes. (In dry air, the heated probe may be too hot to touch.)... my setpoint has shifted shortly after calibration?The probes were likely not allowed to warm sufficiently during calibration. Apply power, place the probes in the zero state process, wait for 5 minutes, and repeat the calibration process. In dry air, the heated probe should be hot to the touch.... I cannot get the red light to illuminate when turning the zero pot?• Make certain the heated probe is heating properly.• Make certain the Trip Adjust pot is in the fully counter-clockwise position• Change J1 jumper position and try again• If calibrating for liquid flow, try performing the zero function in dry air• Reverse Hot and Cold sensor wires and retry... wire is the proper length for terminal assembly?• Reverse the wires: 1 and 3... I cannot get the green light to illuminate when turning the span pot?• Make certain the heated probe is heating properly.• Make certain the Trip Adjust pot is in the fully counter-clockwise position• Change J1 jumper position and try again• If calibrating for liquid flow, try performing the zero function in dry air• Reverse Hot and Cold sensor wires and retry• Turn the unit around so that the other side of the probes faces the flow- RTD’s have a front and a back. Sometimes turning the probes around so that the other side is facing the flow will produce better results... the unit calibrated well but at some later point my setpoint has shifted?• Make sure the process has not changed• Changes in the thermal properties of the fluid will affect set point accuracy• Check the probe tips for uneven build-up- If the build up on one probe (usually the hot) is much greater than the otherthen the thermal differential relationship is compromised.• Check inside of pipe for build-up- If the process sticks and builds-up on the inside of the pipe, the diameter can get smaller causing a change in process velocity.• If all else fails, check the integrity of the sensor and boards (for step-by-stepinstructions see the Thermal Differential Point Switch_1024 General Instruction Manual on )Power and Continuity Verificationn Turn the power off to the T21 Switch.o Remove the instrument enclosure cover.p Loosen the PC board capture screws. (See , page 4)q Unplug the PC board from the instrument enclosure by pulling straight out on the transformer. r Reapply power and verify correct voltage at pins 7 (positive for DC) and 8 (negative for DC) of TBB. (See , page 4)s If voltage is correct, verify the fuse (F1) on the PC board is not blown. (See , page 9) If fuse is not blown, proceed to Sensor/Electronics Functionality verification step 2.t If fuse is blown, replace with the appropriate fuse.Sensor/Electronics Functionality Verificationn Turn the power off to T21 Switch.o Allow a 5-minute cool down.p Measure the resistance of each RTD at pins 1 and 6 of TBA (See , page 4) for the first RTD, and pins 3 and 5 of TBA for the second RTD. These resistances should be 110 ± 10 ohms (with sensors at approximately 70°F) and within 5% of each other in value.q Measure the insulation resistance between pin 1 of TBA and the case of the Switch. It should be greater than 20 megohms.r If the switch sensor assembly resistances are not as specified above, the switch sensor assembly must be replaced.s If the switch sensor assembly resistances are as specified, the switch PC board913-888-2630。
PLS水位传感器操作指南和安装说明说明书
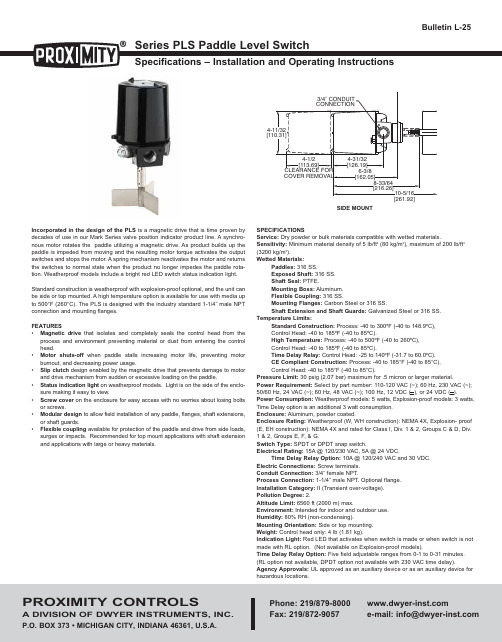
Incorporated in the design of the PLS is a magnetic drive that is time proven by decades of use in our Mark Series valve position indicator product line. A synchro-nous motor rotates the paddle utilizing a magnetic drive. As product builds up the paddle is impeded from moving and the resulting motor torque activates the output switches and stops the motor. A spring mechanism reactivates the motor and returns the switches to normal state when the product no longer impedes the paddle rota-tion. Weatherproof models include a bright red LED switch status indication light.Standard construction is weatherproof with explosion-proof optional, and the unit can be side or top mounted. A high temperature option is available for use with media up to 500°F (260°C). The PLS is designed with the industry standard 1-1/4˝ male NPT connection and mounting flanges.FEATURES•Magnetic drive that isolates and completely seals the control head from the process and environment preventing material or dust from entering the control head.•Motor shuts-off when paddle stalls increasing motor life, preventing motor burnout, and decreasing power usage.•Slip clutch design enabled by the magnetic drive that prevents damage to motor and drive mechanism from sudden or excessive loading on the paddle.•Status indication light on weatherproof models. Light is on the side of the enclo-sure making it easy to view.•Screw cover on the enclosure for easy access with no worries about losing bolts or screws.•Modular design to allow field installation of any paddle, flanges, shaft extensions, or shaft guards.•Flexible coupling available for protection of the paddle and drive from side loads, surges or impacts. Recommended for top mount applications with shaft extension and applications with large or heavy materials.SPECIFICATIONSService:Dry powder or bulk materials compatible with wetted materials. Sensitivity:Minimum material density of 5 lb/ft3(80 kg/m3), maximum of 200 lb/ft3 (3200 kg/m3).Wetted Materials:Paddles:316 SS.Exposed Shaft:316 SS.Shaft Seal:PTFE.Mounting Boss:Aluminum.Flexible Coupling:316 SS.Mounting Flanges:Carbon Steel or 316 SS.Shaft Extension and Shaft Guards:Galvanized Steel or 316 SS. Temperature Limits:Standard Construction:Process: -40 to 300ºF (-40 to 148.9ºC),Control Head: -40 to 185ºF (-40 to 85ºC).High Temperature:Process: -40 to 500ºF (-40 to 260ºC),Control Head: -40 to 185ºF (-40 to 85ºC).Time Delay Relay: Control Head: -25 to 140ºF (-31.7 to 60.0ºC).CE Compliant Construction:Process: -40 to 185°F (-40 to 85°C),Control Head: -40 to 185°F (-40 to 85°C).Pressure Limit:30 psig (2.07 bar) maximum for .5 micron or larger material. Power Requirement:Select by part number: 110-120 VAC (~); 60 Hz, 230 VAC (~);50/60 Hz, 24 VAC (~); 60 Hz, 48 VAC (~); 100 Hz, 12 VDC ( ), or 24 VDC ( ). Power Consumption:Weatherproof models: 5 watts, Explosion-proof models: 3 watts. Time Delay option is an additional 3 watt consumption.Enclosure:Aluminum, powder coated.Enclosure Rating:Weatherproof (W, WH construction): NEMA 4X, Explosion- proof (E, EH construction): NEMA 4X and rated for Class I, Div. 1 & 2, Groups C & D, Div.1 & 2, Groups E, F, & G.Switch Type:SPDT or DPDT snap switch.Electrical Rating:15A @ 120/230 VAC, 5A @ 24 VDC.Time Delay Relay Option:10A @ 120/240 VAC and 30 VDC.Electric Connections:Screw terminals.Conduit Connection:3/4˝ female NPT.Process Connection:1-1/4˝ male NPT. Optional flange.Installation Category:II (Transient over-voltage).Pollution Degree:2.Altitude Limit:6560 ft (2000 m) max.Environment:Intended for indoor and outdoor use.Humidity: 80% RH (non-condensing).Mounting Orientation:Side or top mounting.Weight:Control head only: 4 lb (1.81 kg).Indication Light:Red LED that activates when switch is made or when switch is not made with RL option. (Not available on Explosion-proof models).Time Delay Relay Option:Five field adjustable ranges from 0-1 to 0-31 minutes. (RL option not available, DPDT option not available with 230 VAC time delay). Agency Approvals:UL approved as an auxiliary device or as an auxiliary device for hazardous locations.SIDE MOUNTTOP MOUNTExample SeriesConstructionSwitchPower SupplyPaddleFlangeShaftExtension Material Protective ShieldShaft Extension and Shield LengthOptionsPLS-W-S-1-1-SSF-SS-SS-024-FCPaddle Level Switch Weatherproof Explosion-proofWeatherproof High Temperature Explosion-proof High Temperature SPDT DPDTDPDT Time Delay – 120 VAC DPDT Time Delay – 230 VAC 110-120 VAC 230 VAC 24 VAC 48 VAC 12 VDC 24 VDC230 VAC CE CompliantNo paddle for Motor Control Only Style Low Density Paddle (PDL-1)Medium Density Paddle (PDL-2)Bayonet Paddle (PDL-3)High Density Paddle (PDL-4)No Mounting FlangeCarbon Steel with Half Coupling (FLG-CSH)Carbon Steel with Full Coupling (FLG-CSF)316 SS with Half Coupling (FLG-SSH)316 SS with Full Coupling (FLG-SSF)None 1/4˝ NPS Galvanized Steel 1/4˝ NPS 316 SSNone 1-1/4˝ NPS Galvanized Steel 1-1/4˝ NPS 316 SS Specify length in inches. Minimum 6,Maximum 48. May go longer on custom ordered product.Reversed Light – light indication when paddlefree rotatingFlexible Coupling (CPL-FLX)PLS PLSW W E WH EHS S D TD1TD211234567101234SSF 0CSH CSF SSH SSFSS 0GS SS 024XXXFC RLFCFLEX COUPLING, MODEL CPL-FLX MODEL CHART SS 0GSSSPADDLESGeneralIf a control is mounted on the side wall of a bin, the conduit entry should be directed downwards. Also there should be ample clearance for cover removal. Paddles are secured to the extensions with a 1/4˝ NPT and 1/8˝ diameter roll pin. Care should be taken to press pins flush without damaging the bearings of the control.ElectricalMake electrical connections per the wiring diagram for output switch options select-ed. Wire in accordance with local codes. For hazardous locations, a sealing fitting must be located within 18˝ of the control.WiringAn external switch or circuit breaker should be added to during the installation as a disconnecting device. The switch or circuit breaker must meet the requirements of IEC 60947-1 and IEC 60947-3, shall disconnect all current carrying conductors, and shall not interrupt the protective earth ground. The disconnecting switch or circuit breaker must be marked or labeled with the symbols “I” for on and “O” for off, per IEC 60417-5007 & IEC 60417-5008 and shall be marked as “Disconnecting Device”. Do not position the PLS in a space where it is difficult to operate the disconnecting device that provides power. 300V @ 105°C 18 AWG/0.75 mm 2wiring with PVC or equivalent insulation with 94-V0 or FV-0 flammability rating is recommended for the switch out-puts and power.As a permanently installed piece of equipment, a power disconnect switch, circuit breaker, or other approved disconnect device must be installed in close proximity to the installed board and within easy reach of the operator. This disconnect device must include a label indicating its function as a mains disconnect. A 15amp circuit breaker or fuse device is recommended.Time DelayWith the DIP position 1 set to “off” the delay is upon energizing of the relay, and with it set to “on” the delay is upon de-energizing of the relay. Select delay range wanted from the chart and set the dip switches to the appropriate positions. Then adjust the one-turn (360˚) potentiometer for the exact time interval required within the selected delay range. Example: If a 5 minute delay is required, set DIP switches to 0-7 minute position. Then use potentiometer to adjust to 5 minute period.MAINTENANCEUpon final installation of the Series PLS Paddle Level Switch, no routine maintenance is required. A periodic check of system calibration is recommended. The Series PLS is not field serviceable and should be returned if repair is needed (field repair should not be attempted and may void warranty). Be sure to include a brief description of the problem plus any relevant application notes. Contact customer service to receive a return goods authorization number before shipping.©Copyright 2010 Dwyer Instruments, Inc.Printed in U.S.A. 6/10FR# 85-442245-00 Rev. 3STANDARD CONTROL WIRING DIAGRAMTIME DELAY OPTION WIRING DIAGRAMExplanation of Symbols:。
WFH水位计手册
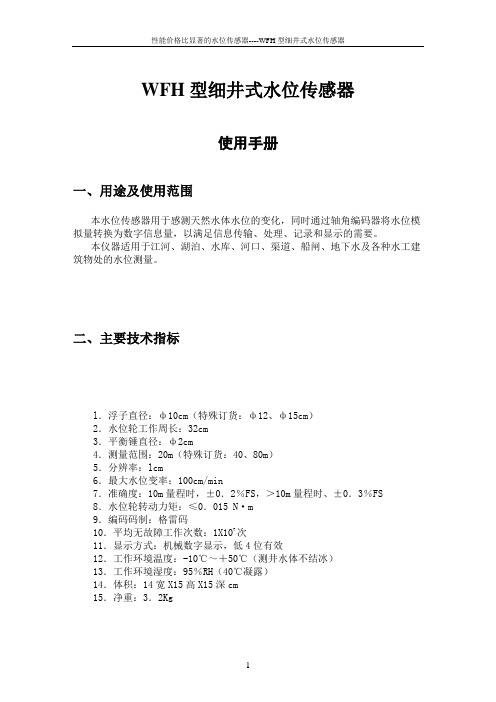
WFH型细井式水位传感器使用手册一、用途及使用范围本水位传感器用于感测天然水体水位的变化,同时通过轴角编码器将水位模拟量转换为数字信息量,以满足信息传输、处理、记录和显示的需要。
本仪器适用于江河、湖泊、水库、河口、渠道、船闸、地下水及各种水工建筑物处的水位测量。
二、主要技术指标l.浮子直径:ф10cm(特殊订货:ф12、ф15cm)2.水位轮工作周长:32cm3.平衡锤直径:ф2cm4.测量范围:20m(特殊订货:40、80m)5.分辨率:lcm6.最大水位变率:100cm/min7.准确度:10m量程时,±0.2%FS,>10m量程时、±0.3%FS8.水位轮转动力矩:≤0.015 N·m9.编码码制:格雷码10.平均无故障工作次数:1X107次11.显示方式:机械数字显示,低4位有效12.工作环境温度:-10℃~+50℃(测井水体不结冰)13.工作环境湿度:95%RH(40℃凝露)14.体积:14宽X15高X15深cm15.净重:3.2Kg三、工作原理本仪器是以浮子感测水位,轴角编码器编码的纯机械式水位传感器。
在水位测井中作为水位感测元件的浮子,灵敏地响应水位的涨落运动,并把此直线运动借助于悬索传递给水位轮,使水位轮产生圆周运动,使直线位移量转换为相应的角位移量。
水位轮枢轴就是轴角编码器的输入轴,当水位轮旋转的同时,轴角编码器将水位模拟量转换成相应的数字编码并以并行方式输出。
四、仪器结构由浮子感测系统和轴角编码器两部分组成。
1、浮子感测系统包括浮子、平衡锤、悬索、水位轮等。
(1)浮子浮子为实芯橡胶体,具有良好的耐腐、抗泄漏性能,可在含盐度高的河口,或具有腐蚀介质的测井中长期可靠地工作。
浮子的标准直径为ф10cm,中间有一配重及悬吊螺钉,供悬挂浮子。
直径为ф10cm的浮子推荐用于10m水位量程;ф15cm浮子推荐用于40m水位量程。
(2)平衡锤用于平衡浮子的重量,使浮子悬浮于水面。
SOR Inc. 1710水位传感器说明书

1710 is a horizontally oriented, float-operated level switch suitable for plant and OEMapplications where open or closed contacts are required to signal the presence or absence of liquid at a discrete level. The float extension arm moves a magnet which actuates (de-actuates) an electromechanical switching element.F e a t u r e s a n d B e n e fi t s• Five-year warranty • Low maintenance costs • Compact design • Worldwide approvals & certifications • Withstands temperatures up to 700o F (371o C)• Withstands pressures up to 1500 psig (103 bar)• External chambers available• ASME Section IX and AWS D2.1 qualified welding system• Designed to ANSI/ASME B31.1 and B31.3 guidelines• Stainless steel switching mechanisms• boilers• storage vessels • high or low alarmThe 1710 side mounted level switch is suitable for most pointlevel applications.The 1710 may be used on a wider variety of applications and process conditions than any other single model of mechanical level switch currently offered by SOR ®. The flexibility in this design is critical to customers all over the world in a wide variety of industries.• All stainless steel wetted parts • Quick worldwide delivery• Only ASTM grade materials with certified mill test reports used• ATEX, IECEx and CSA (US and Canada) certified for hazardous locations• GOST certified. Certifications available upon request• Safety Certified to IEC 61508 (SIL)SOR products are certified to IEC 61508 for non-redundant use in SIL1 and SIL2 Safety Instrumented Systems for most models. For more details or values applicable to a specific product, see the Safety Integrity Level QuickGuide (Form 1528).1710 Side Mounted Level SwitchSEE MORE AT Request QuoteSpecificationsLevel SwitchNote: For other variations please consult factory.*See page 3 for detailsWith External ChamberFor exact material description, see page 3.Maximum Operating Pressure Ratings*Level SwitchNotes:• “X” in model number indicates a special requirement. • For other variations please consult factory.How to Order* Requires use of EE or EG options. ** See page 2 for chamber details.*** Special conditions for safe use: When the equipment is installed,particular precautions shall be taken to ensure, taking into account the effect of the process temperature, that the ambient temperature of the overall liquid level control switch assembly is between -40°C to +80°C. **** Requires use of ZZ option.1710 A -G2A - C - A 1 - H1- ZZ PP C1Example Model No.How to OrderBelow is the SOR quick select model number tree that provides you with all the options to configure and order a product for your application. Y ou must select a designator for each component.CSA KOSHAAgency ApprovalsSpecificationsLevel SwitchLevel SwitchDimensionsThe 1710 unit allows for a smaller installation foot print, making it more compact and economical than most traditional vertical chambers. Although the 1710 is more compact, it provides the rugged reliability customers have come to expect from SOR.The design starts with a high pressure float counter-weighted with a magnet. The magnet is coupled with another magnet inside the housing which is attached to the switching mechanism. The key is that the two magnets are separated by a pressure retaining wall of non-magneticmaterial. The magnets interact with each other as the float goes up and down, providing a safe and reliable system you can depend on for the most critical of applications.COUNTERBALANCEATREGIONAL OFFICES ChinaSOR China | Beijing, China | ****************+86 (10) 5820 8767 | Fax +86 (10) 58 20 8770Middle EastSOR Measurement & Control Equipment Trading DMCC | Dubai, UAE ********************* | +971 4 278-9632 | Fax + 1 913 312 3596SOR Inc. | Lenexa, KS USA | 913-888-2630 | Fax 913-888-0767 |。
Dwyer 水位传感器产品说明说明书
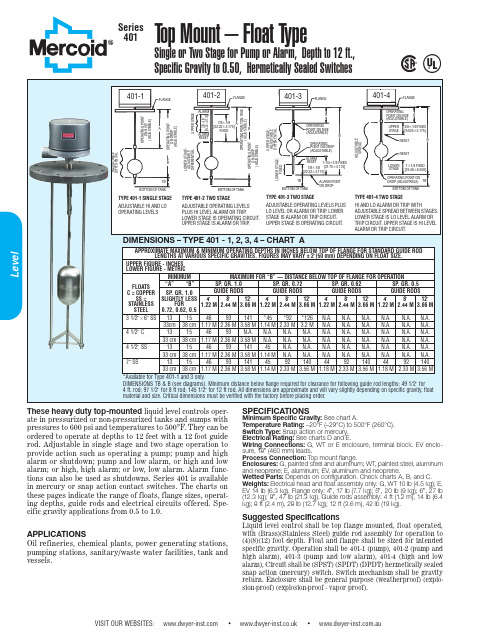
A D J U S T AB L E FLANGEAOPERATING POINT ON RI S E TABLE)3/8Ϯ1/8 FIXED [9.525Ϯ3.175]BRE S ET RE S ET 1Ϯ1/4 FIXED [25.40Ϯ6.350]TB OPERATING POINT ON DROP (ADJU S TABLE)BOTTOM OF TANKCALL TO ORDER: U.S. Phone 219 879-8000 • U.K. Phone (+44) (0)1494-461707 • Asia Pacific Phone 61 2 4272-2055127LevelFLANGE AND GUIDE ROD ASSEMBL Y FOR:31⁄2369(893152.4 mm) FLOAT – CHART CGUIDE RODGUIDE ROD FLANGE FLANGECODE CODESIZE LENGTH MATERIAL SIZE LENGTH MATERIAL 159125# CI 48(1.2 M)Brass 1369125# CI 48(1.2 M)Brass 259125# CI 88(2.4 M)Brass 1469125# CI 88(2.4 M)Brass 359125# CI 128(3.6 M)Brass 1569125# CI 128(3.6 M)Brass 459125# CI 48(1.2 M)303SS 1669125# CI 48(1.2 M)303SS 559125# CI 88(3.6 M)303SS 1769125# CI 88(2.4 M)303SS 659125# CI 128(3.6 M)303SS 1869125# CI 128(3.6 M)303SS 759150# CS 48(1.2 M)Brass 1969150# CS 48(1.2 M)Brass 859150# CS 88(2.4 M)Brass 2069150# CS 88(2.4 M)Brass 959150# CS 128(3.6 M)Brass 2169150# CS 128(3.6 M)Brass 1059150# CS 48(1.2 M)303SS 2269150# CS 48(1.2 M)303SS1159150# CS 88(2.4 M)303SS 2369150# CS 88(2.4 M)303SS 1259150# CS128(3.6 M)303SS 2469150# CS128(3.6 M)303SS401 1WT 7810XX A 1.0481UL CSA 2UL CSA 3UL CSA 4UL CSA G UL CSA WT UL E UL CSAEVUL48XX 48XX XX 78XX 78XX XX 78XXHM 98XX 98XXXXA 1.0481MODEL CHART – SERIES 401CONSTRUCTIONENCLOSURESCIRCUITS401-1-WT-7810-A-1.0-48-1 Single stage with adjustable deadband. Normally used for pump operation.Two stage. Lower stage has adjustable deadband. Upper stage has fixed deadband. Normally used for pump operation and high alarm or shutdown.Two stage. Upper stage has adjustable deadband. Lower stage has fixed deadband. Normally used for pump operation and low alarm or shutdown.Two stage. Each stage has fixed deadband with adjustable deadband between stages. Normally used for high and low alarm or shutdown.General purpose NEMA-1 enclosure.Water tight enclosure suitable for NEMA-1, 2, 3, 4,4X.Explosion proof enclosure, NEMA-7, 9. Class I Groups B, C, D. Class II Groups E, F , G. Division I and II.(CSA approved Groups C, D, E, F , G only).Explosion proof – vapor proof enclosure. NEMA-7, 9. Class I Groups B, C, D. Class II Groups E, F , G.Division I and II.Single stage. Mercury switch. See Chart D.Two stage. Mercury switch. See Chart D.Single stage. Snap switch. See Chart D.Two stage. Snap switch. See Chart E.Hermetically sealed snap switch. See Chart E.Single stage. High capacity DC snap switch. Use heat fins (HF) if process temperature exceeds 350°F (177°C). Do not exceed 450°F (232°C). See Chart E.Two stage. High capacity DC snap switch. Use heat fins (HF) if process temperature exceeds 350°F (177°C). Do not exceed 450°F (232°C). See Chart E.Float, float rod and stops. See Chart B.Specific gravity of process fluid. See Chart A on previous page for operating limits.Operating point. See Chart A for operating limits.Flange size, material, rating and guide rod assembly. See Chart CFLANGE AND GUIDE ROD ASSEMBL Y FOR: 41⁄29(114 mm) FLOAT –CHART CGUIDE ROD FLANGE CODE SIZE LENGTH MATERIAL 2569125# CI 48(1.2 M)Brass 2669125# CI 88(2.4 M)Brass 2769125# CI 128(3.6 M)Brass 2869125# CI 48(1.2 M)303SS 2969125# CI 88(2.4 M)303SS 3069125# CI 128(3.6 M)303SS 3169150# CS 48(1.2 M)Brass 3269150# CS 88(2.4 M)Brass 3369150# CS 128(3.6 M)Brass 3469150# CS 48(1.2 M)303SS 3569150# CS 88(2.4 M)303SS 3669150# CS128(3.6 M)303SSFLANGE AND GUIDE ROD ASSEMBL Y FOR:79(178 mm) FLOAT – CHART CGUIDE ROD FLANGE CODE SIZE LENGTH MATERIAL 3789125# CI 48(1.2 M)Brass 3889125# CI 88(2.4 M)Brass 3989125# CI 128(3.6 M)Brass 4089125# CI 48(1.2 M)303SS 4189125# CI 88(2.4 M)303SS 4289125# CI 128(3.6 M)303SS 4389150# CS 48(1.2 M)Brass 4489150# CS 88(2.4 M)Brass 4589150# CS 128(3.6 M)Brass 4689150# CS 48(1.2 M)303SS 4789150# CS 88(2.4 M)303SS 4889150# CS128(3.6 M)303SSFLOAT , FLOAT ROD AND STOPS – CHART BCODE SIZEMATERIALPRESS/TEMP MAX.ROD STOPS A 3 1/2936” (89 3152.4 mm)304SS Float 300 PSI (21 BAR) 500°F (260°C)303SS Rod Brass Stops B 3 1/2936” (89 3152.4 mm)304SS Float 300 PSI (21 BAR) 500°F (260°C)303SS Rod 316SS Stops C 4 1/29(114 mm)Copper Float 150 PSI (10 BAR) 300°F (149°C)303SS Rod Brass Stops D 4 1/29(114 mm)316SS Float 300 PSI (21 BAR) 500°F (260°C)303SS Rod 316SS Stops E 79(178 mm)304SS Float300 PSI (21 BAR) 500°F (260°C)303SS Rod316SS StopsELECTRICAL RATINGS IN AMPS ORDERING CODESWITCH SWITCH AC DC SINGLETWO STAGE TYPE ACTION 120V 240V 440V 30V 125V 250V STAGE LOWER UPPER CHART D SP-ST Open on level FALL 1053†105-4820-4820-21UL CSA SP-ST Open on level RISE 1053†105-4821-4821-20UL CSA SP-DT One Switch 421†42-4810-4810-10UL CSA SP-DT Two switches E.I.*1053†105-4815-4815-15UL CSA DP-ST Two switches E.I.*Open on level FALL 1053†105-4814-4814-13UL CSA DP-ST Two switches E.I.*Open on level RISE 1053†105-4813-4813-14UL CSA DP-DT Two SP-DT switches 421†42-4806-4806-06UL CSA CHART E SP-DT One switch 1253†0.5**0.25**-7810-7810-10UL CSA DP-DT Two SP-DT switches 1253†0.5**0.25**-7806-7806-06UL CSASP-DT One hermetically sealed switch 555**-7810HM -7810HM -10HM DP-DT Two hermetically sealed SP-DT switches 555**-7806HM -7806HM -06HM DP-DT Two SP-DT switches 10310‡3‡-9806-9806-06SP-DT One switch 10310‡3‡-9810-9810-10*Electrically Independent †Available on special order. Change 1st digit in Ordering Code from 4 to 5 or 7 to 8‡10 Amp inductive (Polarized) at 125 VDC i.e. -4820 becomes -5820, -7810 becomes -8810, etc.**ResistiveMercury Contacts SnapActionContacts ELECTRICAL CIRCUITS AND RATINGSEXAMPLE。
GUY10矿用投入式液位传感器水位传感器说明书
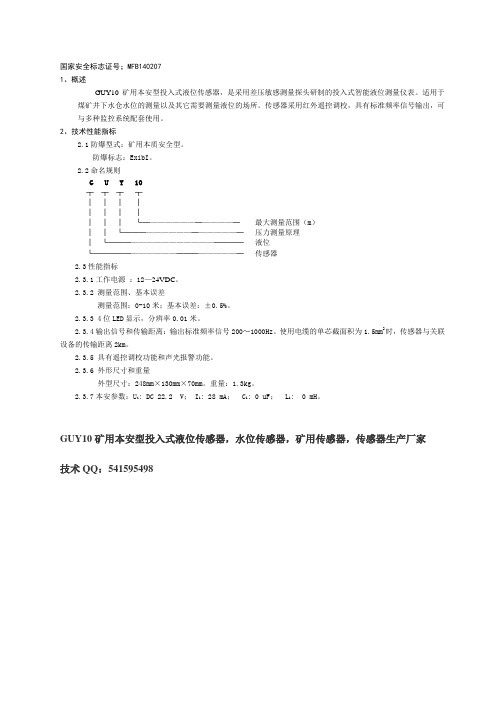
国家安全标志证号;MFB1402071、概述GUY10矿用本安型投入式液位传感器,是采用差压敏感测量探头研制的投入式智能液位测量仪表。
适用于煤矿井下水仓水位的测量以及其它需要测量液位的场所。
传感器采用红外遥控调校,具有标准频率信号输出,可与多种监控系统配套使用。
2、技术性能指标2.1防爆型式:矿用本质安全型。
防爆标志:ExibI。
2.2命名规则G U Y 10┬┬┬┬│││││││││││└─——————─————─最大测量范围(m)││└───——————─—————─压力测量原理│└───———————————────液位└─────——————───—————─传感器2.3性能指标2.3.1工作电源:12—24VDC。
2.3.2 测量范围、基本误差测量范围:0-10米;基本误差:±0.5%。
2.3.3 4位LED显示,分辨率0.01米。
2.3.4输出信号和传输距离:输出标准频率信号200~1000Hz。
使用电缆的单芯截面积为1.5mm2时,传感器与关联设备的传输距离2km。
2.3.5 具有遥控调校功能和声光报警功能。
2.3.6 外形尺寸和重量外型尺寸:248mm×130mm×70mm。
重量:1.3kg。
2.3.7本安参数:U i: DC 22.2 V; I i: 28 mA; C i: 0 uF; L i: 0 mH。
GUY10矿用本安型投入式液位传感器,水位传感器,矿用传感器,传感器生产厂家技术QQ:5415954981。
德特尔火爆水位传感器说明书

Flameproof Level Sensor (Flameproof F/S FP)Deeter HouseValley RoadHughenden ValleyBucks HP14 4LWTel: +44 (0)1494 566 046 Fax: +44 (0)1494 563 961 Email: sales@The Deeter F/S FP is magnetic float on a reed switch or Hall Effect sensor stem for control and indication of a liquid level while in a potentially explosiveatmosphere.II 1/2G 2DEx d IIC (*) Ga/GbEx t IIIC (*) Db IP68-20°C≤Ta≤+85°CII 2GDEx d IIC (*) GbEx t IIIC (*) Db IP68-20°C≤Ta≤+85°C* Temperature class options to suitenvironment and process temperaturesT5 / T100o C for process temperatures ≤ 85°CT4 / T135o C for process temperatures ≤ 125°CT3 / T200o C for process temperatures ≤ 190°CAtex Certificate: Sira 11ATEX1365IECEx Certificate: IECEx SIR 11.0159Refer to certificate for clarification ofdirective code and equipment protection level.Features include:•Custom length sensor stems up to 4 Metres.•Stainless steel 316L housing and wetted components.•Up to 7 switch points on one stem.•Custom made for mixed normally open/normally closed switches.•Atex and IECEx approved.•Suitable for gas and dust environments.•IP68 Ingress protection.•Voltage free reed switch contacts or Hall Effect sensing technology.•M20 or ½”NPT cable connections.•Custom mounting options available.•Narrow sensor stem and mounting for tanks without internal access.•Suitable for high liquid temperatures.Flameproof Level Sensor (Flameproof F/S FP)Deeter House Valley RoadHughenden Valley Bucks HP14 4LWTel: +44 (0)1494 566 046 Fax: +44 (0)1494 563 961 Email: sales@deeter Note 1: When this equipment is intended to be used in a liquid with a processtemperature above 85o C it is an essential requirement that the sensor head temperature is measured to determine if the ambient air cooling is sufficient to keep the head below 80o C. See installation manual for detail.Note 2: The F/S FP sensor float and tube can withstand the stated pressure when sealed inside a tank. The connection head and resin seal to the sensor stem must not be pressurised. The standard zone0 fittings are rated at 10bar, these fittings are not part of the certifiedflameproof seal and should not be considered as part of an explosion proof containment. Please call our technical sales department regarding sensors for liquid pressures up to 31bar.TypeSpecificationSensor technologyMagnetic float with reed switch or Hall Effect Sensor tube and wetted materials Stainless steel 316L Connection head materialStainless steel 316L IP rating with suitable cable gland IP68Approximate weight: Ø12mm stem Ø8mm stem 1Kg +process connector + 0.5Kg/Metre 1Kg +process connector + 0.3Kg/MetreFloat Diameter: Specific gravity: Ø12mm stem Ø8mm stem53mm : 0.65 30mm : 0.75Other floats available Maximum liquid temperature: Reed switch Hall Effect-20 to +85o C -10 to +45o C125o C/190o C on request Maximum head temperature -20 to +80o CNote 1 Maximum operating pressure 150PSI / 10Bar standard 450PSI / 31BarNote 2 Thread connection-Sensor tube ½”-14 NPTThread connection-Wiring port ½”-14 NPT or M20X1.5 Connection head height95mmPower supply: Reed switch Hall Effect Voltage free contacts 7 to 28Volts Switch rating:>4 point Reed switch <=4 point reed switch Hall effect0 to 50Vdc. 1Amp. 50Watts Max 0 to 240vac. 1Amp. 50Watts maxOpen collector 28Vdc Max. 50mA MaxNote 3Flameproof Level Sensor (Flameproof F/S FP)Deeter HouseValley RoadHughenden ValleyBucks HP14 4LWTel: +44 (0)1494 566 046 Fax: +44 (0)1494 563 961 Email: sales@Note 3: The sum current drawn by all switch points must not exceed 1Amp total.Ordering informationDue to the various options available please call our sales office to discuss your requirements. Options include: Probe length, Switch voltage, Switch point quantity, Switch point height, Threaded mounting/seal options, Reed/Hall Effect technology, float sizes, 8 or 12mm sensor tube, cable entry thread.Upon receipt of the above information a drawing and Deeter part No. will be issued to identify the options selected. This part No. will be required when making your order.All electrical equipment should be installed by a qualified/certified electrician.The Deeter Group follows a policy of continual development of its products and reserves the right to change specifications and/or features without notice.。
水位测量仪器使用说明书

水位测量仪器使用说明书一、产品概述水位测量仪器是一种用于测量液体或水位高度的设备。
它具有高精度、可靠性强、操作简便等特点,被广泛应用于工业生产、农业灌溉、水利工程等领域。
二、产品组成本产品由主机、传感器、显示屏、电源等组成。
三、产品特点1.高精度测量:采用先进的测量技术,具有极高的测量准确性和稳定性。
2.显示直观:配备显示屏,可实时显示当前测量值,并支持单位切换。
3.操作方便:仪器操作简便,一键启动、一键停止,用户友好。
4.多种应用场景:适用于不同的水体环境和工作条件,具有良好的适应性。
5.防水设计:外壳采用防水材料制造,可在水中长期使用,不会受损。
四、使用方法1.安装:将传感器固定在要测量水位的位置,确保传感器与液体接触良好。
2.开机:按下电源按钮,仪器将自动启动。
3.测量:测量过程中,仪器将自动采集数据并显示在屏幕上。
4.关闭:按下停止按钮,仪器将停止测量并关闭。
五、常见问题与解决方法1.仪器显示异常:可能是电池电量不足,需要更换电池。
2.测量误差较大:请确保传感器与液体接触良好,清洁传感器表面并重新安装。
3.仪器无法启动:请检查电源是否连接正确,并确保电源开关处于打开状态。
4.测量值不稳定:可能是液体波动引起的,可等待液体平稳后再进行测量或采用平均值。
六、安全警示和注意事项1.请勿将仪器浸入火源或其他有害物质中。
2.在使用过程中,避免剧烈震动或外力冲击,防止损坏。
3.请注意电池的正负极连接,避免反装。
4.不要随意拆卸或修改设备,以免影响正常使用和安全性能。
5.长时间不使用时,请及时关闭电源,并取出电池。
七、维护与保养1.定期清洁传感器表面,避免杂质等影响测量准确性。
2.确保仪器存放在防尘、干燥的环境中,避免受潮或受损。
3.不要将仪器暴露在高温、高湿、强磁、腐蚀性气体等环境中。
4.仪器长时间不使用时,请取出电池以免电池渗漏导致仪器受损。
八、售后服务本产品提供一年质保期,保修期内如出现质量问题,可免费维修或更换。
K-64 LV600级浮动水位传感器说明书

KPUMP UP/PUMP DOWN LEVEL CONTROLsNo Hazardous Mercury switches Required U U se One Switch for Differential or High/Low Control U A djustable Level Differential from15.2 cm to Over 30.5 m (6" to Over 100')U C ase and CableHermetically Sealed by Plastic Injection Molding U C ircular andRectangular DesignsThe LV600 Series unique float level switches provide an economicalmeans of pump-up/pump-down level control with just one level switch. The ON/OFF differential is set by adjusting the length of cable over which the LV600 is allowed to float. Depending on whether the LV600 is floating with the cable UP or DOWN (see drawing), the 15 amp relay is on or off. The relay changes state when the LV600 is above or below the fixed point by 80% of the cable length. For example, if the cable is fixed for 3 m (10') of free cable, the LV600 will trigger at 2.5 m (8') above and below the fixed point.SPeCIfICAtIONSMinimum fluid Specific Gravity: 0.62 for LV610; 0.72 for LV620Minimum/Maximum Level Differential:Approximately 152 mm (6") to 3', depending on cable lengthOperating temperatures: PVC Cable; Switch Rating: SPDT, 15 A @ 250 Vac, -25 to 50°C (-13 to 122°F); Neoprene Cable; -25 to 50°C (-13 to 122°F)Operating Pressure: 75 psig at21°C (70°F) Pressure rating decreases with increasing temperatureWetted Surfaces: Polypropylene body and PVC or Neoprene cable Counterweight: Polypropylene 50.8 mm diameter x 57.1 mm H (2" diameter x 2.25" H)Ordering Examples: LV621-P , circular level control, 0.75 lb weight, PVC cable, and LV600-CW, counterweight.LV611-N, rectangular level control, 0.75 lb weight, neoprene cable.LV600 SeriesShown with LV600-CW accessory counterweight.LV611-P shown smaller than actual size.Thus, turbulence will generally not cause false switching.The cable can be fixed to a pipe, or the accessory counterweight can be used by slipping it over the cable (see drawing). The mechanical SPDT switch has no potentially dangerous mercury, is rated for 15 A at 250 Vac, and can switch more than 100,000 times. The internal microswitch relay carries UL and CSA approvals.The case and cable are hermetically sealed by a two-step plasticinjection molding process to ensure a leak-tight seal.)Circular andRectangular Styles AvailableLV621-P shown smaller than actual size.LV611-P shown smaller than actual size.LV621-P shown smaller than actual size.LV610 SeriesCutaway View。
光电水位传感器说明书
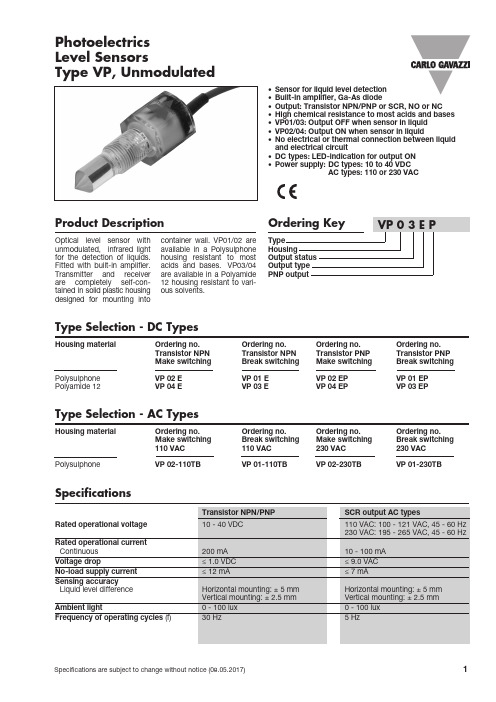
Specifications are subject to change without notice (08.05.2017)1• Sensor for liquid level detection • Built-in amplifier, Ga-As diode• Output: Transistor NPN/PNP or SCR, NO or NC • High chemical resistance to most acids and bases • VP01/03: Output OFF when sensor in liquid • VP02/04: Output ON when sensor in liquid• No electrical or thermal connection between liquid and electrical circuit• DC types: LED-indication for output ON • Power supply: DC types: 10 to 40 VDC AC types: 110 or 230 VACPhotoelectrics Product DescriptionOptical level sensor with un m odulated, infrared light for the detection of liquids. Fitted with built-in amplifier. Trans m itter and receiver are completely self-con-tained in solid plastic housing designed for mounting intocontainer wall. VP01/02 areavailable in a Polysulphone housing resistant to most acids and bases. VP03/04 are available in a Polyamide 12 housing resistant to vari-ous solvents. Type Selection - DC TypesHousing material Ordering no. Ordering no. Ordering no. Ordering no. Transistor NPN Transistor NPN Transistor PNP Transistor PNP Make switching Break switching Make switching Break switching Polysulphone VP 02 E VP 01 E VP 02 EP VP 01 EP Polyamide 12VP 04 EVP 03 EVP 04 EPVP 03 EPType Selection - AC TypesHousing material Ordering no. Ordering no.Ordering no. Ordering no. Make switching Break switching Make switching Break switching 110 VAC110 VAC 230 VAC 230 VAC Polysulphone VP 02-110TBVP 01-110TBVP 02-230TBVP 01-230TBSpecificationsLevel SensorsType VP, Unmodulated2Specifications are subject to change without notice (08.05.2017)DimensionsSpecifications (cont.)VP, unmodulatedMode of OperationThe sensor contains IR trans-mitter, receiver and amplifier with transistor or SCR output. The light source is a Ga-As diode emitting infrared light.The conical tip of the sensor forms an angle of 90ºC. This angle acts as a prism, i.e. the beam, emitted from theGa-As diode placed in one side of the sensor head, is reflected internally to the phototransistor placed in the other side of the sensorhead, provided that the tip of the sensor is si t uated in free air. If the sensor tip is immersed in a liquid, always having a refractive index dif-ferent from air, the beam willnot be refracted by the prism and the photo transistor will not receive any signal.The sensor types can operate in oil, waste water, aqueous solutions such as beer, wine, alcohol etc. without any kindof accessory.Wiring DiagramsVP01-...TB VP02-...TBVP01E, VP03EVP01EP, VP03EPBN BKBU BU BKBNVP02E, VP04E VP02EP, VP04EPBN BK BUBU BK BNBN BU BN BUSpecifications are subject to change without notice (08.05.2017)3VP, unmodulatedInstallation HintsRelief of cable strainProtection of the sensing faceSwitch mounted on mobile carrierTo avoid interference from inductive voltage/ current peaks, separate the prox. switch power cables from any other power cables, e.g. motor, contactor or solenoid cablesIncorrectCorrectThe cable should not be pulledA proximity switch should not serve as mechanical stopAny repetitive flexing of the cable should be avoided。
LBV301振动水位传感器说明书

LBV301Vibrating level switch Rugged, flexible and cleanable P r o d u c t i n f o r m a t i o nf L u i d s e n s o r s | s i c K8014462/2011-09-05Subject to change without notice2Product descriptionThe LBV family of level sensors features a vibrating fork sensor that provides overfill or dry-run signals for containers with bulk or powdered materials. The reli -able and accurate LBV301 level sensors signal full, empty, or demand states. The rugged, stainless steel sensor design prevents bulk materials from jamming. When the probe is covered with bulk ma -terial, the changing vibration amplitude is reliably detected and converted into a switching signal. In addition, the LBV301 features an easy-to-clean monoprobethat is immune to contamination, making it suitable for use in the food industry. While the LBV311 base version is mainly mounted horizontally, the LBV321 with a suspension cable and the LBV331 with a tube extension are mounted vertically to bridge switching distances of up to 80 m or 6 m respectively. With a variety of process connections for hygienic applica -tions, and several output options, the LBV301 can be used for nearly all appli -cations, even in explosive atmospheres.at a glance•Compact sensor from 1 in threaded •Monoprobe design prevents bulk ma -terials from sticking and jamming •Polished monoprobe for food applica -tions•Commissioning without filling•Process temperature up to 250 °C•ATEX versions (1D/2D/1G/2G) avail -able•Tube-extended version (LBV331) up to 6 m and rope-extended version (LBV321) up to 80 m available for vertical mountingYour benefits•Easy commissioning and no calibra -tion reduce setup time•Maintenance-free sensor, reduces downtime•On-site testing – no mounting re-quired, which reduces setup time•Flexible and rugged system suitablefor many types of applications•Vertical mounting in difficult installa-tion conditionsf L u i d s e n s o r s|s i c K 8014462/2011-09-05Subject to change without notice 3detailed technical dataMechanics Electronicsf L u i d s e n s o r s | s i c K8014462/2011-09-05Subject to change without notice4type codesLBV311approval XX Without approvalcX ATEX II 1G, 1/2G, 2G Ex ia IIC T6cK ATEX II 1,1/2,2G Ex ia IIC T6+1,1/2,2D Ex tD IP66 T*LX ATEX II 1/2G, 2G EEx d IIC T6GX ATEX II 1,1/2,2D Ex tD IP66 T*eZATEX II 3G Ex nA II T5...T1 X Version / Process temperature a Standard / –50 °C ... +150 °C B With adapter / –50 °C ... +250 °CcDetection of solids in water / –50 °C ... +150 °C Process fitting / materialGc thread G 1 (din 3852-a) Pn 16 / 316 LGr thread G 1 (din 3852-a) Pn 16 / 316 L, ra<0,8µm nc Thread 1” NPT (ASME B1.20.1) PN16 /316Lnr Thread 1” NPT (ASME B1.20.1) PN16 /316L, Ra<0,8µm cV tri-clamp 2'' / 316L, ra<0,8µmef flange dn 50 Pn 40 form c, din2501 / 316L Kf flange dn 80 Pn 40 form c, din2501 / 316L Zf flange dn 100 Pn 6 form c, din2501 / 316L Ha Flange 2‘‘ 150lb RF, ANSI B16.5 / 316L oa Flange 3‘‘ 150lb RF, ANSI B16.5 / 316L sa Flange 4‘‘ 150lb RF, ANSI B16.5 / 316L au flange dn 50 10K rf Jis / 316L Bu flange dn 80 10K rf Jis / 316L cu flange dn 100 10K rf Jis / 316Lelectronicsc Contactless electronic switch 20...253 V AC/DC r Relay (DPDT) 20...72 V DC/20...253 V AC (3A)tTransistor (NPN/PNP) 10...55 V DC n namur signalHousing / enclosure rate K Plastic / IP66/ IP67a Aluminium / IP66/ IP68 (0.2 bar)V Stainless steel (precision casting) 316L / IP66, IP67 (IP68, 0.2 bar)8Stainless steel (electro buffed) 316L / IP66, IP67 (IP68, 0.2 bar)cable entry / cable gland m M20x1,5 / withn½“ nPt / withoutLBV311-Xf L u i d s e n s o r s | s i c K 8014462/2011-09-05Subject to change without notice5LBV321approvalXX Without approvalcX ATEX II 1G, 1/2G, 2G Ex ia IIC T6cK ATEX II 1,1/2,2G Ex ia IIC T6+1,1/2,2D Ex tD IP66 T*GX ATEX II 1,1/2,2D Ex tD IP66 T*eZ ATEX II 3G Ex nA II T5...T1 XVersion / Process temperature t cable PUR / –20 °C ... +80 °C H cable FEP / –40 °C ... +150 °CcDetection of solids in water / –20 °C ... +80 °C Process fitting / materialXP without / mono probe 316L, ra<0,8µm Gc thread G 1 (din 3852-a) Pn 6 / 316LGr thread G 1 (din 3852-a) Pn 6 / 316L, tuning stick ra<0,8µm nc Thread 1“ NPT (ASME B1.20.1) PN 6 / 316Lnr Thread 1“ NPT (ASME B1.20.1) PN 6 / 316L, tuning stick Ra<0,8µm efflange dn 50 Pn 40 form c, din2501 / 316L Kf flange dn 80 Pn 40 form c, din2501 / 316L Zf flange dn 100 Pn 6 form c, din2501 / 316L Ha Flange 2" 150lb RF, ANSI B16.5 / 316L 0a Flange 3" 150lb RF, ANSI B16.5 / 316L sa Flange 4“ 150lb RF, ANSI B16.5 / 316L au flange dn 50 10K rf, Jis / 316L Bu flange dn 80 10K rf, Jis / 316L cu flange dn 100 10K rf, Jis / 316Lelectronicsc Contactless electronic switch 20...253 V AC/DC r Relay (DPDT) 20...72 V DC/20...253 V AC (3A)tTransistor (NPN/PNP) 10...55 V DC n namur signalHousing / enclosure rate K Plastic / IP66/ IP67a Aluminium / IP66/ IP67 (IP68, 0.2 bar)V Stainless steel (precision casting) 316L / IP66, IP67 (IP68, 0.2 bar)8Stainless steel (electro buffed) 316L / IP66, IP67 (IP68, 0.2 bar)cable entry / cable gland m M 20x1,5 / with n½“ nPt / withoutLBV321-Xf L u i d s e n s o r s | s i c K8014462/2011-09-05Subject to change without notice6LBV331approvalXX Without approvalcX ATEX II 1G, 1/2G, 2G Ex ia IIC T6cK ATEX II 1,1/2,2G Ex ia IIC T6+1,1/2,2D Ex tD IP66 T*GX ATEX II 1,1/2,2D Ex tD IP66 T*eZ ATEX II 3G Ex nA II T5...T1 XVersion / Process temperature t Kabel PUR / –20 °C ... +80 °C H Kabel FEP / –40 °C ... +150 °CcDetection of solids in water / –20 °C ... +80 °C Process fitting / materialGc thread G 1 (din 3852-a) Pn 16 /316LGr thread G 1 (din 3852-a) Pn 16 / 316L, ra<0,8µm nc Thread 1“ NPT (ASME B1.20.1) PN 16 / 316Lnr Thread 1“ NPT (ASME B1.20.1) PN 16 / 316L, Ra<0,8µm cVtri-clamp 2" / 316L, ra<0,8µmef flange dn 50 Pn 40 form c, din2501 / 316L Kf flange dn 80 Pn 40 form c, din2501 / 316L Zf flange dn 100 Pn 6 form c, din2501 / 316L Ha Flange 2" 150lb RF, ANSI B16.5 / 316L 0a Flange 3“ 150lb RF, ANSI B16.5 / 316L sa Flange 4“ 150lb RF, ANSI B16.5 / 316L auflange dn 50 10K rf, Jis / 316L Bu flange dn 80 10K rf, Jis / 316L cu flange dn 100 10K rf, Jis / 316Lelectronicsc Contactless electronic swi 20...253 V AC/DC r Relay (DPDT) 20...72 V DC/20...253 V AC (3A)tTransistor (NPN/PNP) 10...55 V DC n namur signalHousing / enclosure rate K Plastic / IP66/ IP67a Aluminium / IP66/ IP67V Stainless steel (precision casting) 316L / IP66, IP67 (IP68, 0.2 bar)8Stainless steel (electro buffed) 316L / IP66, IP67 (IP68, 0.2 bar)cable entry / cable gland m M 20x1,5 / with n½“ nPt / withoutLBV331-Xf L u i d s e n s o r s|s i c K 8014462/2011-09-05Subject to change without notice 7ordering informationThe part numbers below show a selection of our common configurations and represent only an extract of the product portfolio. LBV311•Process connection: G 1 A•Process temperature: –50 °C ... +150 °C•Process pressure: –1 bar ... +16 bar•Housing material: Plastic•electrical connection: M20 x 1,5•Probe length:160 mmLBV321•Process connection: G 1 A•Process temperature: –20 °C ... +80 °C•Process pressure: –1 bar ... 6 bar•Housing material: Plastic•electrical connection: M20 x 1,5•Probe length:1.000 mmLBV331•Process connection: G 1 A•Process temperature: –50 °C ... +150 °C•Process pressure: –1 bar ... 16 bar•Housing material: Plastic•electrical connection: M20 x 1,5•Probe length:1.000 mmf L u i d s e n s o r s | s i c K8014462/2011-09-05Subject to change without notice8dimensional drawingsProcess connections LBV311G 1 AAll dimensions in mm (inch)G 1 ½ AAll dimensions in mm (inch)Tri-clampAll dimensions in mm (inch)Temperature adapter –50 °C ... +250 °CAll dimensions in mm (inch)f L u i d s e n s o r s|s i c K 8014462/2011-09-05Subject to change without notice 9Process connections LBV321G 1 AAll dimensions in mm (inch)G 1 ½ AAll dimensions in mm (inch)f L u i d s e n s o r s | s i c K8014462/2011-09-05Subject to change without notice10Process connections LBV331G 1 AAll dimensions in mm (inch)G 1 ½ AAll dimensions in mm (inch)FlangeAll dimensions in mm (inch)f L u i d s e n s o r s|s i c K 8014462/2011-09-05Subject to change without notice 11Wiring planrelay outputWe recommend connecting LBV301 in such a way that the switching circuit is open when there is a level signal, line break or failure (safe condition).The relays are always shown in non-operative condition.LBV301 - Wiring plan, single chamber housing1 Relay output2 Relay output3 Voltage supplytransistor outputWe recommend connecting LBV301 in such a way that the switching circuit is open when there is a level signal, line break or failure (safe condition).The instrument is used to control relays, contactors, magnet valves, warning lights, horns as well as PLC inputs.LBV301 - Wiring plan, single chamber housing1 Voltage supply LBV301 Transistor output NPN actionLBV301 Transistor output PNP actionnamur outputFor connection of the amplifier according to NAMUR (IEC 60947-5-6, EN 50227). You can find further information in the …Technical data“.LBV301 - Wiring plan, single chamber housingf L u i d s e n s o r s | s i c K8014462/2011-09-05Subject to change without notice12contactless electronic switchWe recommend connecting LBV301 in such a way that the switching circuit is open when there is a level signal, line break or failure (safe condition).The contactless electronic switch is always shown in non-oper-ative condition.The instrument is used for direct control of relays, contac -tors, magnet valves, warning lights, horns etc. It must not be operated without an intermediately connected load, because the electronics would be destroyed if connected directly to the mains.It is not suitable for connection to low voltage PLC inputs. Do -mestic current is temporarily lowered below 1mA after switch -ing off the load so that contactors, whose holding current is lower than the constant domestic current of the electronics, are reliably switched off.LBV301 - Wiring plan, single chamber housing1 Shieldingrecommended accessoriesLock fittingf L u i d s e n s o r s|s i c K 8014462/2011-09-05Subject to change without notice 13mounting instructionsswitching pointIn general, LBV301 can be installed in any position. The instru-ment only has to be mounted in such a way that the vibrating element is at the height of the desired switching point.The only exception is vertical mounting of the tuning fork from below. In this position there is the danger of solid particles get-ting stuck between the fork tines.socketThe vibrating element should protrude into the vessel to avoid build-up. For that reason, avoid using mounting bosses for flanges and screwed fittings. This applies particularly to horizon-tal installation and use with adhesive products.filling openingInstall the instrument in such a way that the vibrating ele-ment does not protrude directly into the filling stream. Should such an installation location be necessary, mount a suitable baffle above or in front of the vibrating element, e.g. L80 x8 DIN 1028 (see Fig. Part …a.“). In abrasive solids, mounting according to fig. Part …b.“ has proven to be a good solution. The mound that forms in the concave baffle protects it from abrasion.a. Convex mountingb. Concave mountinginflowing mediumIf LBV301 is mounted in the filling stream, unwanted false measurement signals can be generated. For this reason, mount LBV301 at a position in the vessel where no disturbances, e.g. from filling openings, agitators, etc., can occur.Horizontal mountingTo achieve a very precise switching point, you can installLBV301 horizontally. However, if the switching point can have a tolerance of a few centimeters, we recommend mounting LBV301 approx. 20° inclined to the vessel bottom to avoid build-up. Orient the tuning fork of LBV301 so that the product cannot remain lying on the fork surface. There is a mark on the thread hexagon for aligning the fork. Make sure that the mark points upward. material coneTo achieve a very precise switching point, you can install LBV301 horizontally. However, if the switching point can have a tolerance of a few centimeters, we recommend mounting LBV301 approx. 20° inclined to the vessel bottom to avoid build-up.Orient the tuning fork of LBV301 so that the product cannot remain lying on the fork surface. There is a mark on the thread hexagon for aligning the fork. Make sure that the mark points upward.To compensate measurement errors caused by the material cone in cylindrical vessels, the sensor must be mounted at a distance of d/6 from the vessel wall.1 LBV3212 Emptying opening3 Filling openingf L u i d s e n s o r s | s i c K8014462/2011-09-05Subject to change without notice14tensile loadWith cable version, make sure that the max. permissible tensile load on the suspension cable is not exceeded. The danger of this happening exists particularly with very heavy solids and large meas. lengths. The max. permissible load is stated in chapter …Technical data“.agitatorsDue to filling or extraction forces, vibrations or similar, the level switch can be subjected to strong lateral forces. For this reason, do not use an overly long extension tube for LBV331, but check if a LBV311 level switch couldn‘t be used instead, mounted on the side of the vessel in horizontal position. Extreme vibration caused by the process or the equIP ment, e.g. by fluidization or beaters in the vessel, can cause theextension tube of LBV301 to vibrate in resonance. This leads to increased stress on the upper weld joint. Should a longer tube version be necessary, you can provide a suitable support or guy directly above the vibrating element to secure the extension tube.This measure applies mainly to applications in Ex areas. Make sure that the tube is not subject to bending stress due to this measure.If an installation from above is necessary, check if you can use a cable version. Over a longer period of time, strong vibration can damage the instrument electronics. You can decouple the electronics from the process by using a remote (displaced) housing.Baffle protection against falling rocksIn applications such as grit chambers or settling basins for coarse sediments, the vibrating element must be protected against damage with a suitable baffle.t i t L e|s i c K 8014462/2011-09-05Subject to change without notice 15Search online quickly and safely with the SICK “Finders”Efficiency – with SICK e-commerce toolsfind out prices and availabilityDetermine the price and possible delivery date of yourdesired product simply and quickly.Request or view a quoteYou can have a quote generated online here.Every quote is confirmed to you via e-mail.order onlineYou can go through the ordering process in just a fewsteps.Product finder: We can help you to quickly target the pro-duct that best matches your application.applications finder: Select the application description onthe basis of the challenge posed, industrial sector, or pro-duct group.Literature finder: Go directly to the operating instructions,technical information, and other literature on all aspectsof SICK products.These and other Finders at ProductServiceclearly structured: You can findeverything you need for your sensorplanning under the menu items Pro-ducts, Information, and My Account.available 24 hours a day: Regard-less of where you are in the world orwhat you’d like to know – everythingis just a click away at www.mysick.com.safe: Your data is password-pro-tected and only visible to you. Withthe individual user management,you define who can see what dataand who can execute what actions.8014462/2011-09-05 ∙ G W (2011-09) ∙ W B U S m o d i n t 37SICK AG | Waldkirch | Germany | Leading technologiesWith a staff of more than 5,000 and over 50 subsidiaries and representa -tions worldwide, SICK is one of the leading and most successful manufac -turers of sensor technology. The power of innovation and solution competency have made SICK the global market leader. No matter what the project and industry may be, talking with an expert from SICK will provide you with an ideal basis for your plans – there is no need to settle for anything less than the best.Unique product range•Non-contact detecting, counting, classifying, positioning and measur -ing of any type of object or media •Accident and operator protection with sensors, safety software and services•Automatic identification with bar code and RFID readers•Laser measurement technology for detecting the volume, position and contour of people and objects•Complete system solutions for analy -sis and flow measurement of gases and liquidsComprehensive services•SICK LifeTime Services – for safety and productivity•Application centers in Europe, Asia and North America for the develop-ment of system solutions under real-world conditions•E-Business Partner Portal – price and availabi-lity of products, requests for quotation and online orderssicK at a glanceWorldwide presence with subsidiaries in the following countries:australiaBelgium/Luxembourg Brasilceská republikacanada china danmark deutschland españa franceGreat Britain india israel italia JapanMéxico nederland norge Österreich Polska românia russia schweizsingapore slovenija south africasouth Korea suomi sverige taiwan türkiyeunited arab emirates usaPlease find detailed addresses and additional representatives and agencies in all major industrial nations at 。
生物科学领域的“SX”水位传感器产品介绍说明书

SENSORS FOR FOOD AND LIFE SCIENCES.“SX” Level TransmitterIntroductionThis line of sensors provide superior signal stability. The field tested performance of the “SX” transmitter means the elimination of expensive, repetitive re-calibrations along with protection against costly overflow/run-dry situations that can occur with less stable level transmitters. The 0.2% accuracy experienced at installation can now be expected a year later!We’ve also incorporated a new field calibration feature that provides “one-touch” sensor zeroing as well as simple range calibration, without the need for special tools and fixtures, pressure sources, or removal of the transmitter from the tank. This translates to real cost savings during installation or when adjusting for new application requirements.Of course the “SX” Transmitter is available in all standard fitting and range combinations you’ll need to fit any sanitary tank application. All variations are CE compliant, meet Intrinsically Safe requirements, 3-A Sanitary Standards, and are backed by a 2-year warranty.Complete specifications and ordering information are available on the reverse.For more information please visit our Web Site at , orcontact your local Authorized Anderson-Negele Distributor.2Kit -Field Wireable Connector and Receptacle with Dielectric Grease P/N:56642A0001Shield CordsetLoop+(red) wire Pin 1Loop-(black) wire Pin 2connected to nutShield (bare) wire - connected to nut0.17-0.26" Cable Sheath Diameter3S XSPAN RANGE5 0-30” min to 0-140” max6 0-140.1” to 0-415” max7 0-415.1” to 0-830” max8 0-830.1” to 0-1385” maxFITTING089 Anderson Flush Mount Long - with USP VI gasket(71060-A3, A5, A7, A9)088 Anderson Flush Mount Short - with USP VI gasket(71060-A4, A6, A8)091 Cherry Burrell Flush Mount Long(insulated tank)090 Cherry Burrell Flush Mount Short(uninsulated tank)092 King Gage Flush Mount Long(1777-3)093 King Gage Flush Mount Medium(1777-1, -6 Standard)094 King Gage Flush Mount Short(1777-2 non-insulated)097 Tank Mate Flush Mount Long 1(208WVE)096 Tank Mate Flush Mount Medium 1(205WVE)095 Tank Mate Flush Mount Short 1(200WVE)004 1-1/2” Tri-Clamp ®005 2” Tri-Clamp ®007 3” Tri-Clamp ®059 1-1/2” NPT 3141 Rosemount / Foxboro Sanitary Spud - Short 142 Rosemount / Foxboro Sanitary Spud - Long 154 Endress & Hauser Universal Adaptor - short 155 Endress & Hauser Universal Adaptor - long DIAPHRAGM1 SS-316L Electropolished2 Hastelloy “C”(N/A with King-Gage, Tank Mate, or Endress & Hauser Fittings)MOUNTING0 Horizontal 1 Vertical2 Other (specify angle fromvertical or from hoizontal)SENSOR WIRING00 Quick Disconnect Receptacle(QDR) w/No CableR0 QDR & 90° FWC w/No Cable01 QDR & Field Wireable Connector(FWC) w/No Cable05 QDR w/25 ft Standard Molded Cordset 10 QDR w/25 ft Standard Molded Cordset 20 QDR w/25 ft Standard Molded Cordset99 1/2" NPTNo QDR, no FWC and no Cable (No sensor warranty for water damage)2Note:Calibration of span is in units “inches water column”. Consult factory for assistance.3Not 3-A compliant1Requires Adapter:57200A0001 (insulated) 57200A0002 (uninsulated)Gaskets for Flush Mount Level Transmitters Anderson USP VI 44348A0002 Cherry Burrell 44292A0001 King Gage 36240S3212 Tank Mate 36240S3123 Continental 5658900000 Rosemount/Foxboro 36240E3341Sensor Calibration Adaptors Anderson fitting73198A0001 Cherry Burrell fitting 73198A0002 King Gage Fitting 73198A0003 Tankmate73198A0004 Cord SetsMolded w/25’ cable 42117K0025Molded w/50’ cable 42117K0050Molded w/100’ cable 42117K01005-Conductor w/25’ cable 42117H00255-Conductor w/50’ cable 42117H00505-Conductor w/100’ cable42117H0100ACCESSORIESAnderson Weld-In Shells for Flush Mount Level Transmitters 71060A0003 Insulated Vessel - Standard Flange - 316L 71060A0004 Uninsulated Vessel - Standard Flange - 316L 71060A0005 Insulated Vessel - Pressure Vessel Flange - 316L 71060A0006 Uninsulated Vessel - Pressure Vessel Flange - 316L 71060A0009 Insulated Vessel - H/D Press. Vessel Flange - 316L Shell AdaptorTank Mate, uninsulated 57200A0002 Tank Mate, insulated 57200A0001CALIBRATION##### Height in inches w.c. 2(to nearest tenth)00000 Field CalibratedExamples:10850 1,085.0 inches 0030530.5 inches4Tech. Support:*******************************Phone 800-833-0081CONTINENTAL SHELL TYPE"A"NON INSULA TED 2-5/32INSULA TED6-3/16。
SBLTX 潜水水位传感器说明书
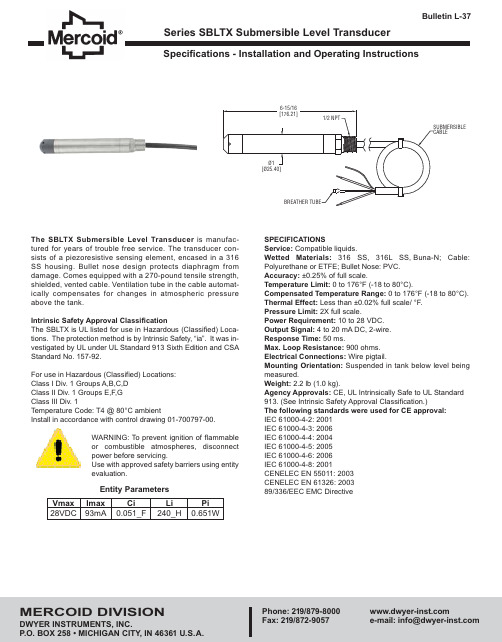
Install in accordance with control drawing 01-700797-00.WARNING: To prevent ignition of flammableor combustible atmospheres, disconnectpower before servicing.Use with approved safety barriers using entityevaluation.SPECIFICATIONS Service: Compatible liquids.Wetted Materials: 316 SS, 316L SS, Buna-N; Cable:Polyurethane or ETFE; Bullet Nose: PVC.Accuracy:±0.25% of full scale.Temperature Limit: 0 to 176°F (-18 to 80°C).Compensated Temperature Range:0 to 176°F (-18 to 80°C).Thermal Effect:Less than ±0.02% full scale/ °F.Pressure Limit: 2X full scale.Power Requirement: 10 to 28 VDC.Output Signal:4 to 20 mA DC, 2-wire.Response Time: 50 ms.Max. Loop Resistance: 900 ohms.Electrical Connections: Wire pigtail.Mounting Orientation: Suspended in tank below level being measured.Weight:2.2 lb (1.0 kg).Agency Approvals: CE, UL Intrinsically Safe to UL Standard 913. (See Intrinsic Safety Approval Classification.)The following standards were used for CE approval:IEC 61000-4-2: 2001IEC 61000-4-3: 2006IEC 61000-4-4: 2004IEC 61000-4-5: 2005IEC 61000-4-6: 2006IEC 61000-4-8: 2001CENELEC EN 55011: 2003CENELEC EN 61326: 200389/336/EEC EMC DirectiveCAUTION : Do not exceed specified supplyvoltage ratings. Permanent damage not cov-ered by warranty will result. This device is notdesigned for 120 or 240 volt AC operation.Use only on 10 to 28 VDC.INSTALLATION1. Location : Select a location where the temperature of the trans-ducer will be between 0 and 176°F (-18 to 80°C). Distance fromthe receiver is limited only by total loop resistance.2. Position : The transducer is not position sensitive. However allstandard models are originally calibrated with the unit in a positionwith the pressure connection downward. Although they can beused at other an g les, for best accuracy it is recommended thatunits be installed in the position calibrated at the factory.3. Mounting : The transducer can be mounted via several meth-ods. It can be suspended from the electrical cable, it can beplaced resting on the bottom of the tank in either horizontal or ver-tical orientation, or it can be attached to a pipe or hang wire by the1/2˝ NPT male connection on the top of the housing.4. Electrical ConnectionsWire Length - The maximum length of wire connecting the trans-ducer and receiver is a function of wire size and receiver resist-ance. Wiring should not contribute more than 10% of the receiverresistance to total loop resistance. For extremely long runs (over1000 feet), choose receivers with higher resistance to minimizethe size and cost of connecting leads. Where wiring length isunder 100 feet, wire as small as 22 AWG can be used. 5. Wiring An external power supply delivering 10-28 VDC with minimum current capability of 40 mA DC (per transducer) is required to power the control loop. See Fig. A for connection of the power supply, transducer and receiver. The range of appropriate receiver load resistance (RL) for the DC power supply voltage available is expressed by the formula:RL Max = Vps – 10V 20 mA DC Shielded cable is recommended for control loop wiring. Black wire is negative (-) and red wire is positive (+).MAINTENANCEAfter final installation of the pressure transducer and its compan-ion receiver, no routine maintenance is required. A periodic checkof system calibration is suggested. The Series SBLTX transducerare not field repairable and should be returned if repair is needed(field repair should not be attempted and may void warranty). Besure to include a brief description of the problem plus any relevantapplication notes. Contact customer service to receive a returngoods authorization number before shipping.Fig. A©Copyright 2009 Dwyer Instruments, Inc.Printed in U.S.A. 12/09FR# M2-443550-00 Rev. 2。
KSR Kuebler 水位传感器说明书
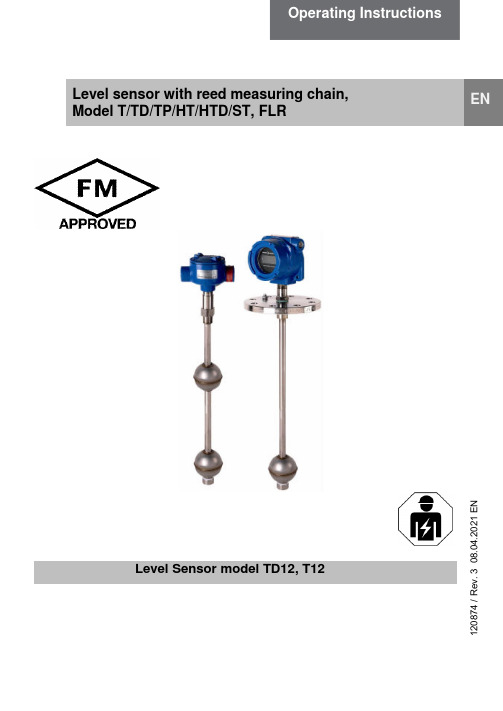
Operating InstructionsLevel sensor with reed measuring chain, Model T/TD/TP/HT/HTD/ST, FLR ENLevel Sensor model TD12, T12120874 / R e v . 3 08.04.2021 E NEN Operating Instructions, Model T/TD/TP/HT/HTD/ST, FLR © 2016 WIKA Alexander Wiegand SE & Co. KGAll rights reserved. / Alle Rechte vorbehalten.WIKA® and KSR® are registered trademarks in various countries.WIKA® and KSR® sind geschützte Marken in verschiedenen Ländern.Prior to starting any work, read the operating instructions!Keep for later use!Vor Beginn aller Arbeiten Betriebsanleitung lesen!Zum späteren Gebrauch aufbewahren!KSR Kuebler Niveau-Messtechnik GmbH Heinrich-Kuebler-Platz 169439 Zwingenberg am Neckar • Germany Tel. +49 6263/87-0Fax +49 6263/87-99******************** Gayesco-WIKA USA229 Beltway Green Boulevard Pasadena, Texas 77503 Tel. +1 713 475 0022Fax +1 713 475 0011********************2 KSR KUEBLER Operating Instructions – T/TD/TP/HT/HTD/ST, FLRContents1. General information 42. Design and function 53. Safety 64. Transport, packaging and storage 135. Commissioning, operation 136. Faults 197. Maintenance and cleaning 208. Dismounting, return and disposal 229. Specifications 23 KSR KUEBLER Operating Instructions – T/TD/TP/HT/HTD/ST, FLR 31. General information▪The magnetic Level sensors described in the operating instructions have been designed and manufactured using state-of-the-art technology. All components are subject to stringent quality and environmental criteria during production.Our management systems are certified to ISO 9001.▪These operating instructions contain important information on handling the in-strument. Working safely requires that all safety instructions and work instruc-tions are observed.▪Observe the relevant local accident prevention regulations and general safety re gulations for the instrument’s range of use.▪The operating instructions are part of the product and must be kept in the im-mediate vicinity of the instrument and readily accessible to skilled personnel at any time. Pass the operating instructions on to the next operator or owner of the instrument.▪Skilled personnel must have carefully read and understood the operating in-structions prior to beginning any work.▪The general terms and conditions contained in the sales documentation shall apply.▪Subject to technical modifications.▪Further information:Internet address: / Relevant data sheet: FLR / LM 20.024 KSR KUEBLER Operating Instructions – T/TD/TP/HT/HTD/ST, FLR2. Design and function2.1 Functional descriptionLevel sensors work on the float principle with magnetic transmission. A permanent magnet built into the float triggers, with its magnetic field, the resistance measur-ing chain built into the guide tube. The entire assembly corresponds to a 3-wire potentiometer circuit. The float changes its height with the level of the medium it is monitoring. The measured resistance signal is proportional to the level. The measurement voltage is very finely-stepped due to the contact separation of the resistance measuring chain and is thus virtually continuous.1 Connection housing2 Cable bushing3 Mounting thread4 Gasket5 Guide tube6 Float7 Teflon washer8 Float stop2.2 Scope of deliveryCross-check scope of delivery with delivery note.KSR KUEBLER Operating Instructions – T/TD/TP/HT/HTD/ST, FLR 56KSR KUEBLER Operating Instructions – T/TD/TP/HT/HTD/ST, FLR3. Safety3.1 SymbolsDANGER!... indicates an immediately hazardous situation which might result in death or severe injuries if it is not avoided.WARNING!... indicates an potentially hazardous situation which might result in death or severe injuries if it is not avoided.CAUTION!... indicates an potentially hazardous situation which might result in light or minor injuries or property or environmental damages if it is not avoided.Installation, electrotechnical expertise!For the installation particular electrotechnical expertise is required.Installation, mechanical expertise!For the installation particular mechanical expertise is required.Information... highlights useful tips and recommendations and infor-mation for efficient and fault-free operation.3.2 Proper intended useLevel sensors are solely intended for monitoring the liquid level of fluids. The area of use is based on the technical performance limits and materi-als.The fluids must not be contaminated nor contain coarse particles nor tend to crystallize. It must be ensured that the magnetic switch materi-als that come into contact with the media are sufficiently resistant to themonitored medium. Not suitable for dispersion, abrasive fluids, highly viscous media and paints.▪Compliance with the usage conditions specified in the operating instruc-tions is required.▪Do not operate the unit in direct proximity of ferro-magnetic environ-ments (distance min. 50mm).▪Do not operate the unit in direct proximity of strong electromagnetic fields or in direct proximity of facilities that can be impacted by magnetic fields (distance min. 1m).▪The level sensors must not be exposed to heavy mechanical strain (im-pact, bending, vibration).▪Compliance with the relevant safety regulations for the use is required. ▪Compliance with the technical specifications in these operating instruc-tions is required. Improper use or operation of the unit outside the tech-nical specifications requires immediate shut-down and inspection by an authorized KSR or WIKA service technician.Claims of any kind due to improper use are excluded.When working on containers, there is a risk of poisoningor suffocation. Work may only be performed using suitablepersonal safety equipment (e.g. respiratory protection,protective clothing, etc.).An explosive atmosphere may develop in a container.Measures must be taken to prevent sparking. Work insuch areas must be done by qualified personnel in ac-cordance with the relevant safety regulations and guide-lines.KSR KUEBLER Operating Instructions – T/TD/TP/HT/HTD/ST, FLR 73.3 Improper useAny use that exceeds the technical performance thresholds or that is in-compatible with the materials is considered improper use.Injury due to improper useImproper use of the unit can result in hazardous situationsand injuries.Do not modify the unit without authorizationAny use beyond the proper intended use or any other use is considered improper use.Do not use this unit in safety or emergency off equipment.3.4 Responsibility of the operatorThe unit is used in the industrial sector. The operator is therefore subject to statutory obligations with respect to occupational safety.Compliance with the safety instructions in these operating instructions and the applicable safety, accident prevention and environmental protection regulations for the area of use of the unit is required.In order to safely work on the unit, the operator must ensure▪the operating personnel is regularly trained in all matters pertaining to occupational safety, first aid and environmental conservation and is fa-miliar with the operating instructions and, in particular, the safety in-structions contained therein▪the unit is suitable for the application in accordance with the proper in-tended use (check for improper use).After check, improper use is excluded.8 KSR KUEBLER Operating Instructions – T/TD/TP/HT/HTD/ST, FLR3.5 Personnel qualificationRisk of injury due to insufficient qualificationsImproper use can result in significant personal injury andproperty damages.The activities described in these operating instructionsmay only be performed by specialist technicians withthe following qualifications.Specialist personnelThe specialist personnel authorized by the operator is capable of execut-ing the described work and autonomously detect potential hazards due their technical training, knowledge of measuring and control technology and their experience and knowledge of country-specific regulations, appli-cable standards and guidelines.3.6 Personal safety equipmentThe personal safety equipment serves to protect the technicians against hazards that might impact the safety or health while working. When exe-cuting the various tasks on and with the unit, the technicians must wear personal safety equipment.Comply with warning signs posted in the work area regarding per-sonal safety equipment!The required personal safety equipment must be provided by the operator.KSR KUEBLER Operating Instructions – T/TD/TP/HT/HTD/ST, FLR 94. Transport, packaging and storage4.1 TransportCheck the magnetic Level sensor for any damage that may have been caused by transport. Obvious damage must be reported immediately.Damage due to improper transportWith improper transport, a high level of damage to prop-erty can occur.▪Observe the symbols on the packaging.▪Handle packed goods with care4.2 Transport and storageDo not remove packaging until just before commissioning.5. Commissioning, operation▪Observe all instructions given on the shipment packaging for removing the transportation safety devices.▪Remove the magnetic Level sensor carefully from the packaging!▪When unpacking, check all components for any external damage.10 KSR KUEBLER Operating Instructions – T/TD/TP/HT/HTD/ST, FLR5.1 Functional checkPrior to installation, a functional test of the level sensor can be carried out with a resistance measuring instrument and manual movement of the float. The following table describes the measurements and the expected meas-ured values for the movement of the float, starting from the float stop in the direction of the tank opening.WARNING!Ensure that the functional check does not start any unin-tended processes.Functional tests must only be carried out with equipmentthat is approved for use in hazardous area. Tests must beconducted by qualified personnel in accordance with therelevant safety regulations and guidelines.5.2 Mounting preparationsEnsure that the sealing faces of the vessel or the level sensor are clean and do not show any mechanical damage.5.3 Mounting▪Observe the torque values of screws specified in pipefitting work.▪In the selection of the mounting material (seals, bolts, washers and nuts), take the process conditions into account. The suitability of the sealing must be specified with regard to the medium and its vapours. In addition, ensure it has corresponding corrosion resistance.▪Mount the level sensor either via mounting thread (3) or mounting flange (not illustrated).▪The guide tube (5) should not be inclined more than a maximum of 30° to the vertical.▪If the geometry of the float (6) does not fit through the process connec-tion, the float must be removed before mounting.▪Before removal, mark the position of the float stops with a waterproof pen▪Mark the mounting position of the floats (e.g. "Up")▪After the level sensor has been mounted, the float should be re-at-tached within the inside of the tank (pay attention to the mounting posi-tion!).▪Float stops (8) must then be re-attached at the marked points.5.4 Electrical connection▪The electrical connection must only be made by qualified skilled per-sonnel.▪Wire the level sensor in accordance with the connection diagram of the electrical output (see product label). The connection terminals are ap-propriately marked.▪Seal the cable gland at the connection housing.▪Install a pour-seal (conduit seal) fitting within 18 inches of the housing to prevent water from entering the housing and for compliance with the National Electrical Code.▪Transmitters with integral electronics (puck and/or display) must be connected in a series loop with the readout or data acquisition device and the power supply. Shielded cable must be used for noise immunity and for Intrinsically Safe applications an agency approved safety barrier must be installed. A ground wire must be provided and connected to the ground block inside the housing.▪To connect a transmitter with a built-in digital display, unscrew and re-move the housing cover and carefully remove the plastic label fromaround the display by grasping each side and pulling upwards. Remove the digital display by carefully pulling up on two diagonal sides of the display. The indicator is held in place by two banana plugs which plug into the baseboard where the 4 to 20 mA puck is mounted. Field wiring connections are made to a two point, compression type, terminal block located on the baseboard (see Fig. 2 for Explosion Proof or drawing 095-3201-001 Pg. 1 for Intrinsically Safe applications). Attach a ground wire directly to the ground screw inside the housing.▪To connect a transmitter without a built-in display, unscrew and remove the housing cover. Field wiring connections are made directly to the puck (see Fig 3 for Explosion Proof, drawing 095-3201-001 Pg. 2 for single puck Intrinsically Safe applications, or drawing 095-3201-001 Pg.4 for dual puck Intrinsically Safe applications). Attach a ground wire di-rectly to the ground screw inside the housing.WARNING!Malfunctions through voltage spikes due to running cables together with mains connection leads or due to large cable lengths.This can lead to a malfunction in the plant and thus lead to injury to personnel or damage to equipment. ▪ Use shielded connection leads▪ Ground connection leads at one endAlways observe the mounting and operating instructions of accessories when commissioning them.PCB layout and componentsWiring for transmitters with integral displayWiring for transmitters without integral display6. FaultsThe following table contains the most frequent causes offaults and the necessary countermeasures.FaultsLevel sensor cannot be mounted at the planned place on the vessel Process connection ofthe magnetic Level sen-sor does not match theprocess connection ofthe vessel.Modification of the vesselReturn to the factoryProcess connection atthe vessel defectiveRework the thread or re-place the screwed cou-plingMounting thread at themagnetic Level sensordefectiveReturn to the factoryNo signal, non-linear or undefined signal Electrical connection in-correctSee chapter 5.4 “Electricalconnection”. Check as-signment with the aid ofthe connection diagram. Measuring chain defec-tiveReturn to the factoryHead-mounted transmit-ter defectiveReturn to the factoryHead-mounted transmit-ter adjusted incorrectlyReturn to the factoryCAUTION!Physical injuries and damage to property and the environmentIf faults cannot be eliminated by means of the listedmeasures, the instrument must be taken out of operation immediately.▪ Ensure that there is no longer any pressure present and protect against being put into operation accidentally.▪ Contact the manufacturer.▪ If a return is needed, please follow the instructions given in chapter 8.2 “Return”.7. Maintenance and cleaning7.1 MaintenanceWhen used properly, the level sensors work maintenance-free. They must be subjected to visual inspection within the context of regular mainte-nance, however, and included in the vessel pressure test.DANGER!Work on vessels involves the danger of intoxication and suffocation. No work is allowed to be carried out unless by taking suitable personal protective measures (e.g. res-piratory protection apparatus, protective outfit etc.).Repairs must only be carried out by the manufacturer.Perfect functioning of the level sensors can only be guar-anteed when original accessories and spare parts are used.7.2 CleaningCAUTION!Physical injuries and damage to property and the en-vironmentImproper cleaning may lead to physical injuries and dam-age to property and the environment. Residual media in the dismounted instrument can result in a risk to persons, the environment and equipment.▪ Rinse or clean the removed instrument.▪ Sufficient precautionary measures must be taken.1. Prior to cleaning the unit, properly disconnect it from the process and the power supply.2. Carefully clean the unit with a damp cloth.3. Do not let electrical connections come into contact with moisture!CAUTION!Damage to propertyImproper cleaning may lead to damage to the instrument! ▪ Do not use any aggressive cleaning agents.▪ Do not use any pointed and hard objects for cleaning.8. Dismounting, return and disposalWARNING!Physical injuries and damage to property and the envi-ronment through residual mediaResidual media in the dismounted instrument can result in arisk to persons, the environment and equipment.Wash or clean the dismounted instrument, in order to protect persons and the environment from exposure to residual media.8.1 DismountingOnly disconnect the measuring instrument once the system has been de-pressurised and the power disconnected!8.2 ReturnWash or clean the dismounted magnetic Level sensor before returning it, in order to protect personnel and the environment from exposure to residual media.Information on returns can be found under the heading “Service” on our local website.8.3 DisposalIncorrect disposal can put the environment at risk.Dispose of instrument components and packaging materials in an environ-mentally compatible way and in accordance with the country-specific waste disposal regulations.9. SpecificationsModelsT12 Reed level sensor with guide tube 12 mmT14 Reed level sensor with guide tube 14 mmT18 Reed level sensor with guide tube 18 mmT48 Reed level sensor with guide tube 48 mmTD14 Reed level sensor with guide tube 14 mm, dual outputTD18 Reed level sensor with guide tube 18 mm, dual outputTD48 Reed level sensor with guide tube 48 mm, dual outputTP16 Reed level sensor with guide tube 16 mm, plastic design TP20 Reed level sensor with guide tube 20 mm, plastic design HT12 Reed level sensor with guide tube 12 mm,high temperature designHT14 Reed level sensor with guide tube 14 mm,high temperature designHT18 Reed level sensor with guide tube 18 mm,high temperature designHTD14 Reed level sensor with guide tube 14 mm, dual output, high temperature designHTD18 Reed level sensor with guide tube 18 mm, dual output, high temperature designST14 Reed level sensor with guide tube 14 mm, sanitary design ST18 Reed level sensor with guide tube 18 mm, sanitary design FLR-SBF Reed level sensor with guide tube 12, 14 or 18 mmMarkingT12T14T18T48FLR-SBF XPDIPNIXP / I / 1 / BCD / T6 Ta = 60°C,DIP / II,III / 1 / EFG / T6 Ta = 60°C,NI / I / 2 / ABCD / T4 Ta = 60°CType 4, 4XTD14 TD18 TD48 XPDIPNIXP / I / 1 / BCD / T6 Ta = 60°C,DIP / II,III / 1 / EFG / T6 Ta = 60°C,NI / I / 2 / ABCD / T4 Ta = 60°CType 4, 4XTP16 TP20 NI NI / I / 2 / ABCD / T4 Ta = 60°C Type 4, 4XHT12 HT14 HT18 XPDIPNIXP / I / 1 / BCD / T6 Ta = 60°C,DIP / II,III / 1 / EFG / T6 Ta = 60°C,NI / I / 2 / ABCD / T4 Ta = 60°CType 4, 4XHTD14 HTD18 XPDIPNIXP / I / 1 / BCD / T6 Ta = 60°C,DIP / II,III / 1 / EFG / T6 Ta = 60°C,NI / I / 2 / ABCD / T4 Ta = 60°CType 4, 4XST14 ST18 XPDIPNIXP / I / 1 / BCD / T6 Ta = 60°C,DIP / II,III / 1 / EFG / T6 Ta = 60°C,NI / I / 2 / ABCD / T4 Ta = 60°CType 4, 4X*) Ratings (FM-approved for the United States of America)XP: Explosionproof for Class I, Division 1, Groups B, C and DDIP: Dust-ignitionproof for Class II/III, Division 1, Groups E, F and G NI: Nonincendive for Class I, Division 2 Groups A, B, C and D hazard-ous (classified) locations, indoors and outdoors (Type 4, 4X)Type code T..For further specifications see data sheet FLR and LM 20.02.Type code FLR(1) (2) (3) (4) Type: - - -KSR KUEBLER Operating Instructions – T/TD/TP/HT/HTD/ST, FLR 31KSR Kuebler subsidiaries worldwide can be found online at . WIKA subsidiaries worldwide can be found online at .Manufacturer contact hergestellt von Sales contact Vertrieb durchKSR Kuebler Niveau-Messtechnik GmbH Heinrich-Kuebler-Platz 169439 Zwingenberg am Neckar • Germany Tel. +49 6263/87-0Fax +49 6263/87-99******************** WIKA Alexander Wiegand SE & Co. KG Alexander-Wiegand-Straße 3063911 Klingenberg • GermanyTel. +49 9372 132-0Fax +49 9372 132-406************www.wika.de32 KSR KUEBLER Operating Instructions – T/TD/TP/HT/HTD/ST, FLR。
- 1、下载文档前请自行甄别文档内容的完整性,平台不提供额外的编辑、内容补充、找答案等附加服务。
- 2、"仅部分预览"的文档,不可在线预览部分如存在完整性等问题,可反馈申请退款(可完整预览的文档不适用该条件!)。
- 3、如文档侵犯您的权益,请联系客服反馈,我们会尽快为您处理(人工客服工作时间:9:00-18:30)。
NRS1-7Betriebsanleitung 803966-07GESTRA Niveauschalter NRS 1-7Installation and Service Instructions 803966-07 GESTRA Level Switch NRS 1-7Instructions de montageet de mise en service 803966-07Commutateur de niveau GESTRA NRS 1-7Instrucciones de montaje y servicio 803966-07 Conmutador de nivel GESTRA NRS 1-7Manuale di istruzioni 803966-07Interruttore di livello NRS 1-7ࡅ╞╘╗╙Fig. 5Fig. 6Fig. 4BauteilkennzeichenTÜV · WB · 01-354; EG 01202931B010077 TÜV · WR/WB · 99-370 (NRG 16-36)EG 01202931B010075EingangVier Anschlüsse für eine Niveauelektrode. NRG 16-11, PN 40NRG 17-11, PN 63NRG 19-11, PN 160NRG 16-36, PN 40ENGLISHType-approval No.TÜV · WB · 01-354; EG 01202931B010077TÜV · WR/WB · 99-370 (NRG 16-36)EG 01202931B010075InputFour terminals for the connection of one level-control electrode typeNRG 16-11, PN 40NRG 17-11, PN 63NRG 19-11, PN 160NRG 16-36, PN 40FRANÇAISNuméro d’OhomologationTÜV · WB · 01-354; EG 01202931B010077TÜV · WR/WB · 99-370 (NRG 16-36)EG 01202931B010075EntréeQuatre connexions pour une électrode deniveau typeNRG 16-11, PN 40NRG 17-11, PN 63NRG 19-11, PN 160NRG 16-36, PN 40ESPAÑOLNo de registroTÜV · WB · 01-354; EG 01202931B010077 TÜV · WR/WB · 99-370 (NRG 16-36)EG 01202931B010075EntradaCuatro conexiones para un electrodo de nivel NRG 16-11, PN 40NRG 17-11, PN 63NRG 19-11, PN 160NRG 16-36, PN 40Omologazione n.TÜV · WB · 01-354; EG 01202931B010077 TÜV · WR/WB · 99-370 (NRG 16-36)EG 01202931B010075IngressoQuattro morsetti per il collegamento di un elettrodo di livelloNRG 16-11, PN 40NRG 17-11, PN 63NRG 19-11, PN 160NRG 16-36, PN 40803966-07/104cs · ©1991 GESTRA GmbH · Bremen · Printed in GermanyWir erklären hiermit, daß die GeräteNRS 1-7b und NRS 1-7c/dmit den Bestimmungen folgenderRichtlinien und Normen übereinstimmen:■73/23/EWG i. d. F . 93/68/EWG ■EN 50 081-1, EN 50 081-2,EN 50 082-1, EN 50 082-2,IEC 801-2, IEC 801-3, IEC 801-4,IEC 801-5Bei einer nicht mit uns abgestimmten Än-derung des Gerätes verliert dieseErklärung ihre Gültigkeit.DeutschWe hereby declare that the equipment NRS 1-7b and NRS 1-7c/dcomply with the regulations set out in thefollowing standards and guidelines:■73/23/EWG version 93/68/EWG■EN 50 081-1, EN 50 081-2,EN 50 082-1, EN 50 082-2,IEC 801-2, IEC 801-3, IEC 801-4,IEC 801-5This declaration is no longer valid if modifications are made to the equipmentwithout consultation with us.Français Nous déclarons, par la présente, que les appareils NRS 1-7b et NRS 1-7c/d correspondent aux dispositions en vigueur concernant les normes et les directives suivantes:■73/23/EWG d’après la version 93/68/EWG ■EN 50 081-1, EN 50 081-2,EN 50 082-1, EN 50 082-2,IEC 801-2, IEC 801-3, IEC 801-4,IEC 801-5Cette déclaration n’est plus valable sil’appareil subit des transformations n’étant pas mis au point par nos services.EnglishDipl.-Ing. Uwe BledschunLeiter Konstruktion Por la presente declaramos que los equipos NRS 1-7b y NRS 1-7c/d están conformes con las siguientes normas y reglamentos:■73/23/EWG en la versión 93/68/EWG ■EN 50 081-1, EN 50 081-2,EN 50 082-1, EN 50 082-2,IEC 801-2, IEC 801-3, IEC 801-4,IEC 801-5Esta declaración pierde su validez en caso que se realicen modificaciones en losequipo que no hayan sido acordadas connosotros.Español Dipl.-Ing. Lars Bohl QualitätsbeauftragterBremen, 8. Januar 2002GESTRA GmbHItaliano Dichiaramo con la presente gli strumenti NRS 1-7b e NRS 1-7c/d sono descritta è conforme alle norme delle direttive:■73/23/EWG nella versione 93/68/EWG ■EN 50 081-1, EN 50 081-2,EN 50 082-1, EN 50 082-2,IEC 801-2, IEC 801-3, IEC 801-4,IEC 801-5In caso di modifiche non coordinate con noi, questa dichiarazione perde la sua validità.GESTRA Gesellschaften ·GESTRA Companies ·Sociétés GESTRA ·Sociadades GESTRA ·Società GESTRA Vertretungen weltweit · Agencies all over the world · Représentations dans le monde entier · Representaciones en todo el mundo · Agenzie in tutto il mondo Italia Flowserve S.p.A.Divisione Italgestra Via Prealpi, 30 – 20032 Cormano (MI)Tel.003902/663251Fax 003902/66 32 55 60E-mail: infoitaly@GESTRA ESPAÑOLA S.A.Luis Cabrera, 86-88E-28002 Madrid Tel.003491/5152032Fax 003491/4136747; 5152036E-mail: gestra@gestra.es España Flowserve Flow Control S.A.S.10 Avenue du Centaure, BP 8263F-95801 CERGY PONTOISE CEDEXTél.00331/34432660Fax 00331/34432687E-mail: gnation@ FrancePortugal Flowserve Portuguesa, Lda.Av. Dr. Antunes Guimarães, 1159Porto 4100-082T el.0035122/6198770Fax 0035122/6107575E-mail: gestra@gestra.ptGreat BritainFlowserve Flow Control (UK) Ltd.Burrel Road, Haywards HeathWest Sussex RH 16 1TLTel.00 44 14 44 / 31 44 00Fax 00 44 14 44 / 31 45 40E-mail: sales@。